BMW 330CI E46 Build thread
Discussion
So with the build up to the Christmas period and the darkest of nights after work I've only been doing an hour or so here and there on the car. I don't plan on running the car out on track until about the beginning of March so not in the major rush to get a few little jobs done.
With the wet weather I've spent a little bit of time in the workshop working on making a few little parts for myself and friends. I like problem solving as well as making things from scratch especially when I can't buy something to do what I want off the shelf.
At the moment I am moving to a S54 Oil Filter housing to run an oil cooler, however with the filter housing only having two M12 take offs compared with the M54 housing which had 3 I've had to look at alternative locations for sensors. (ECU Temp & Vanos take off are already joined in a stainless adaptor with the Innovate Pressure going straight into the housing)
ECU Oil Temp
Innovate Gauge Temp
Innovate Gauge Pressure
Vanos take off
Because of the length of the probe below the thread (~20mm) on the Innovate Temp Sensor I have decided to move it into the oil cooler line pre cooler and make an inline housing for it.
Few minutes on CAD- AN10 on either end with flat on the top which will have an NPT or M12 Weld on fitting. This will give enough length to space the sensor up enough ensure the end of the Temp Sensor is just in the flow of oil without bottoming out on the other side. I've kept the ID of the whole fitting to be the same as the inside of the AN10 lines so now to reduce flow after going to the effort of blanking of the themostat, see below.

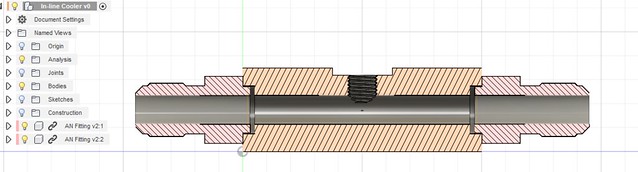
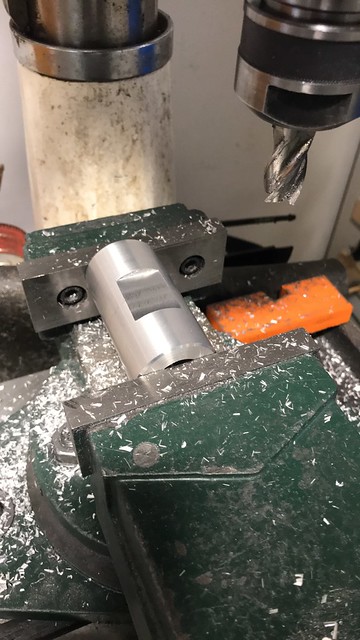
Finished product all welded together. Turned and bored on the lathe with a flat milled onto the top for the weld on fitting.
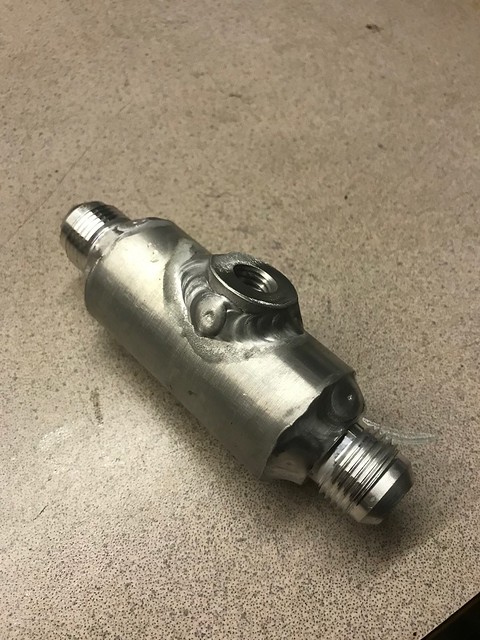
AN10 weld on fittings turned to the correct diameter of the S54 housing...
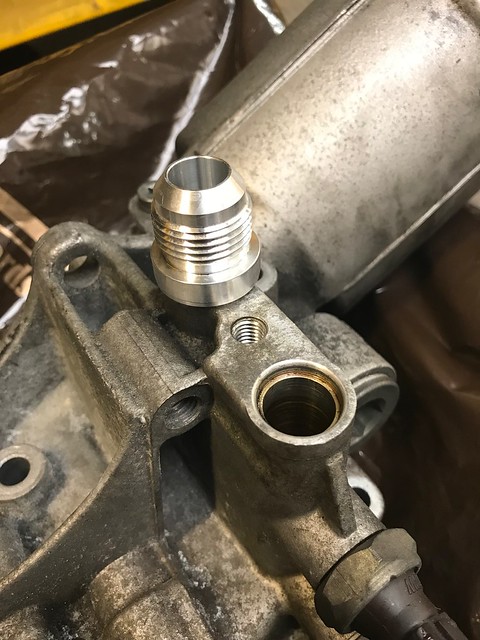
AN10 fittings all welded into place

Oil Thermostat blank turned on a lathe from Aluminium
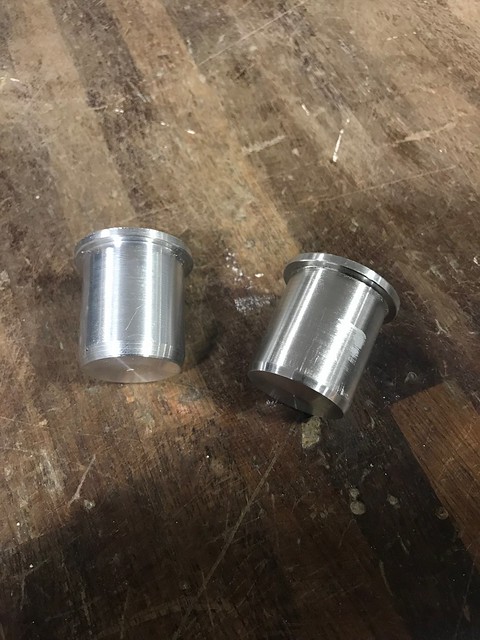
Fitted into place with the standard snap ring

So with the oil temps hitting 120' within 3 hardish laps at Oulton Park with am ambient temp of 10 degrees the cooling side of things needed something substantial to keep the temps under control. Knowing someone with pretty much exactly the same set up as this I've opted for a 19 row cooler and AN10 lines.
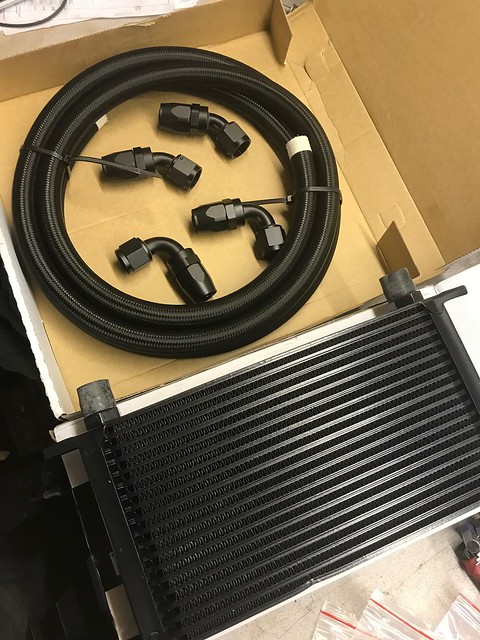
Front end of the car removed ready to fit everything into position
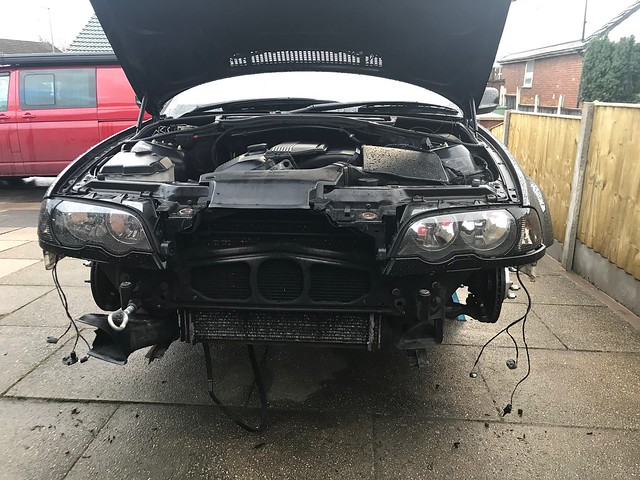
With the S54 filter housing being pretty much a bolt on solution to the M54 head the only major problem is that the offset on the power steering pump is different by 15mm. While I was at it I've made up some 15mm x 20mm OD spacers to bring the pump into the correct alignment. While I was at it I've also made some steering column spacers for my friends E36 steering column he's making.
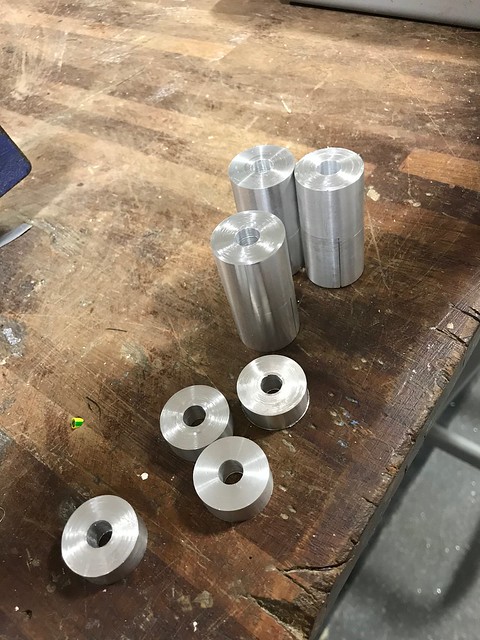
Finally one of the last jobs I got around to doing before Christmas was replacing the front left wheel bearing. This was replaced 1.5 track days ago but on the last day at Oulton I was suffering with judder under braking, the only thing I can find at the moment is noticeable play in the front left wheel bearing so that has been replaced and the old one send back under warranty. Will only be able to test it though when everything is put back together.

With the wet weather I've spent a little bit of time in the workshop working on making a few little parts for myself and friends. I like problem solving as well as making things from scratch especially when I can't buy something to do what I want off the shelf.
At the moment I am moving to a S54 Oil Filter housing to run an oil cooler, however with the filter housing only having two M12 take offs compared with the M54 housing which had 3 I've had to look at alternative locations for sensors. (ECU Temp & Vanos take off are already joined in a stainless adaptor with the Innovate Pressure going straight into the housing)
ECU Oil Temp
Innovate Gauge Temp
Innovate Gauge Pressure
Vanos take off
Because of the length of the probe below the thread (~20mm) on the Innovate Temp Sensor I have decided to move it into the oil cooler line pre cooler and make an inline housing for it.
Few minutes on CAD- AN10 on either end with flat on the top which will have an NPT or M12 Weld on fitting. This will give enough length to space the sensor up enough ensure the end of the Temp Sensor is just in the flow of oil without bottoming out on the other side. I've kept the ID of the whole fitting to be the same as the inside of the AN10 lines so now to reduce flow after going to the effort of blanking of the themostat, see below.

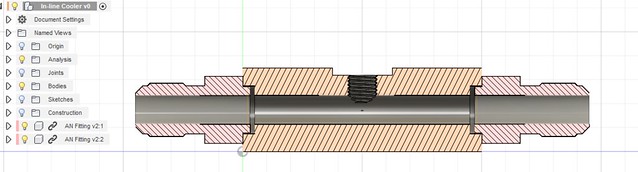
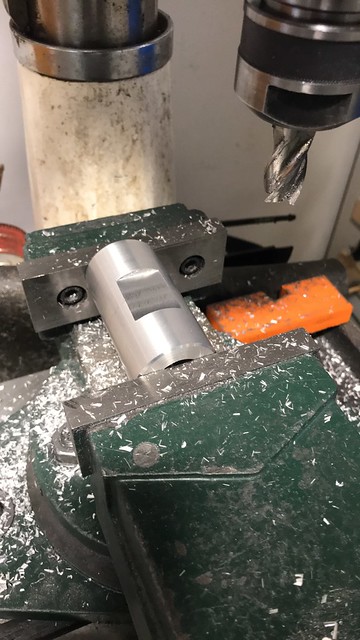
Finished product all welded together. Turned and bored on the lathe with a flat milled onto the top for the weld on fitting.
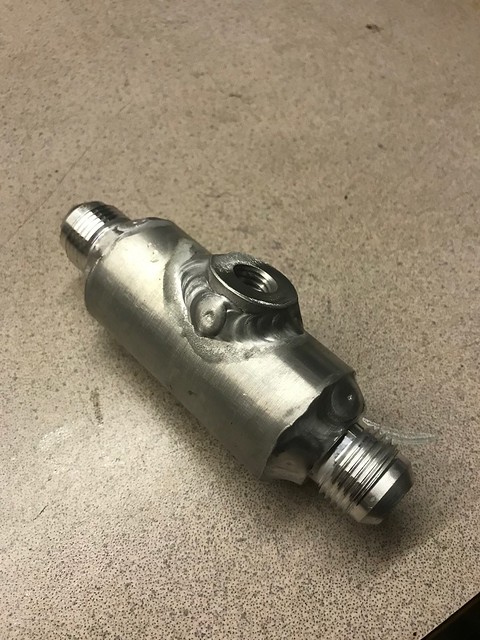
AN10 weld on fittings turned to the correct diameter of the S54 housing...
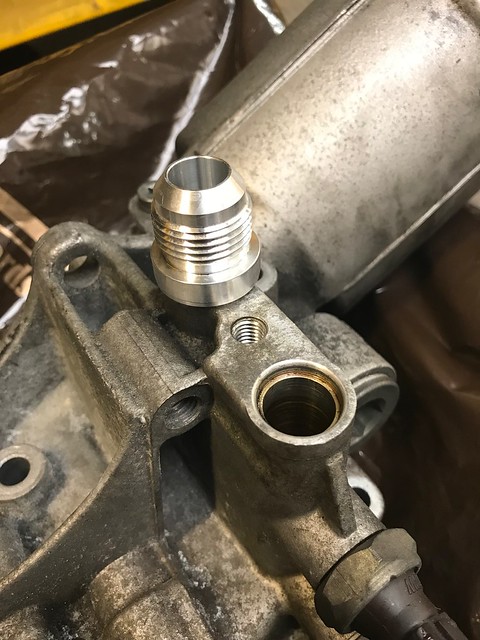
AN10 fittings all welded into place

Oil Thermostat blank turned on a lathe from Aluminium
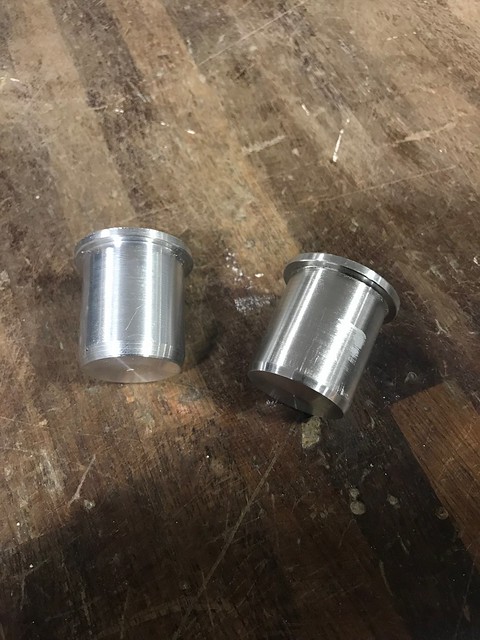
Fitted into place with the standard snap ring

So with the oil temps hitting 120' within 3 hardish laps at Oulton Park with am ambient temp of 10 degrees the cooling side of things needed something substantial to keep the temps under control. Knowing someone with pretty much exactly the same set up as this I've opted for a 19 row cooler and AN10 lines.
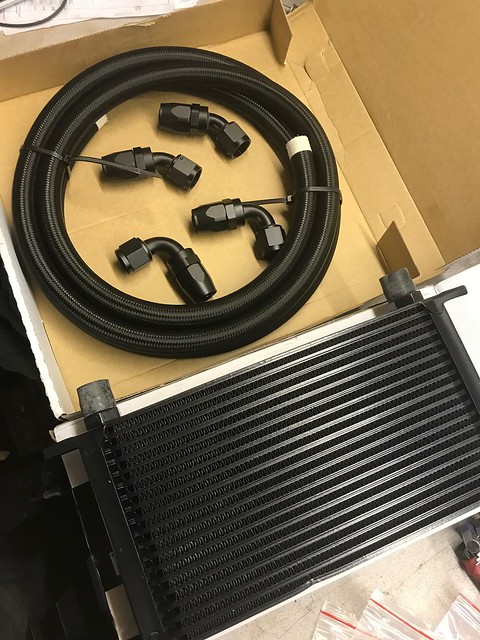
Front end of the car removed ready to fit everything into position
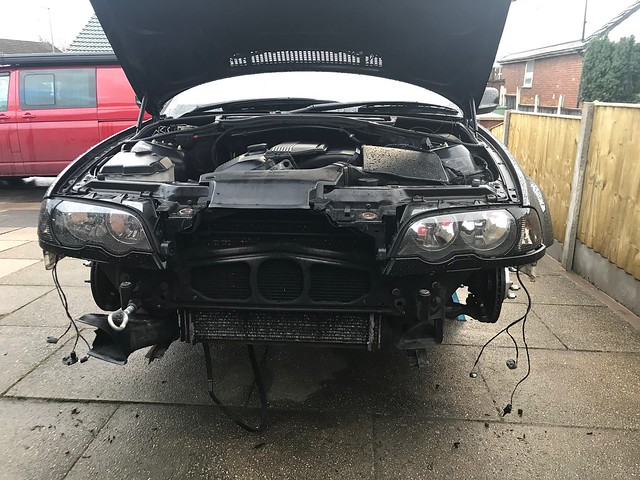
With the S54 filter housing being pretty much a bolt on solution to the M54 head the only major problem is that the offset on the power steering pump is different by 15mm. While I was at it I've made up some 15mm x 20mm OD spacers to bring the pump into the correct alignment. While I was at it I've also made some steering column spacers for my friends E36 steering column he's making.
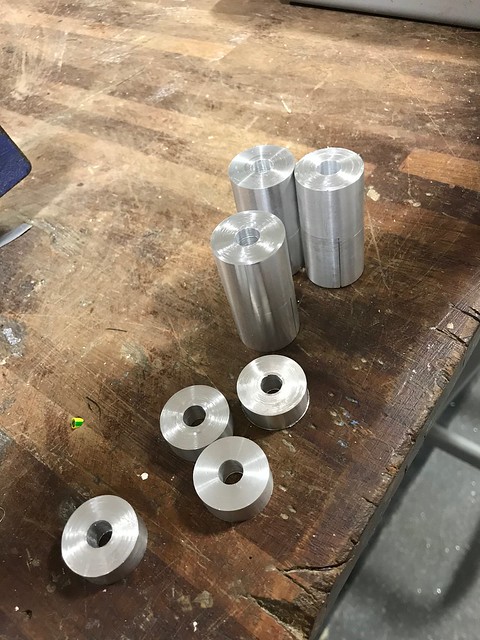
Finally one of the last jobs I got around to doing before Christmas was replacing the front left wheel bearing. This was replaced 1.5 track days ago but on the last day at Oulton I was suffering with judder under braking, the only thing I can find at the moment is noticeable play in the front left wheel bearing so that has been replaced and the old one send back under warranty. Will only be able to test it though when everything is put back together.

G600 said:
That was a good read and a nice set-up, I don't suppose you can remember the measurements for the brake bushes? I've got a Z4 with 330 brakes and access to a lathe so I've been meaning to make a set.
I've got the initial prototype I made knocking around in the garage so will measure that one tomorrow. Did a little more on the car today.
Finished making the lines to the correct length to run through to the cooler

Cooler mounted into position at the bottom to a solid piece of box section to support the weight of the cooler, You can see the inline temp sensor block mounted above the cooler in the feed line
Note - Still need to bend some steel to make the top cooler brackets to the two studs to the side, job for tomorrow.
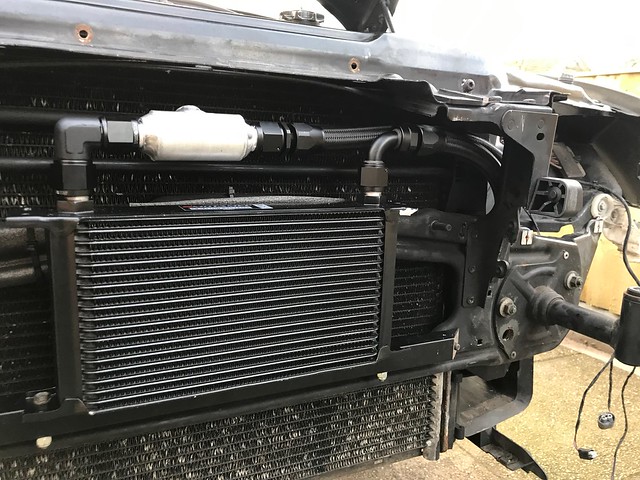
However as always trying to make everything as reliable as possible I've made the line long enough to able to remove the inline temp sensor and run an AN10 in line fitting should anything ever happen on a track day which requires it to be removed. I can only see this happening if the sensor was broken off and unable to plug the hole in the line. I thought of it when i was making it so easily added a solution to the spares box.
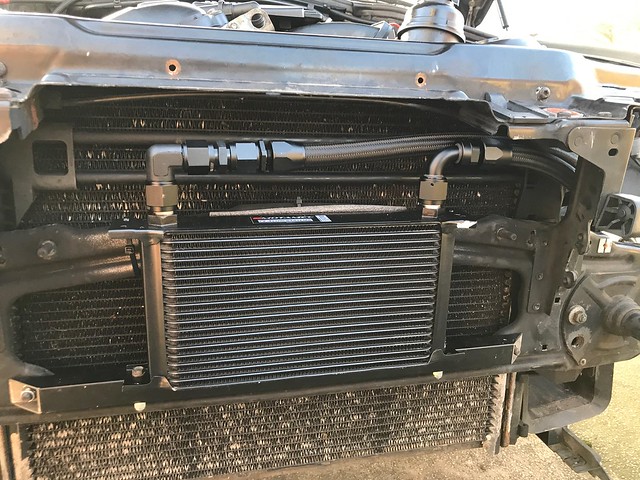
Mounted the power steering pump back to the housing. Had to drill out the threads on the pump to be able to bolt it to the S54 filter housing and used the 15mm spacers I machined for the job.
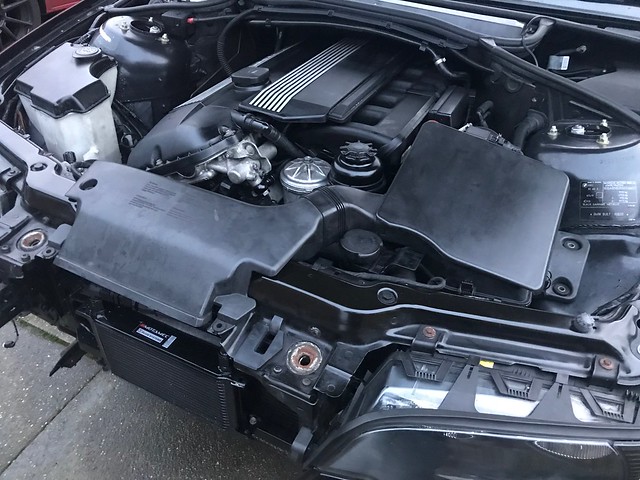
Modified the back of the headlight slightly to get more clearance on the oil lines where they run through and bolted the front end back together. Will run the car tomorrow and check all the fittings for leaks.
Also replaced the oil in their after the 3 track days, obviously needed to add more oil to take into consideration the extra volume in the lines and the cooler now so perfect time to do an oil change.
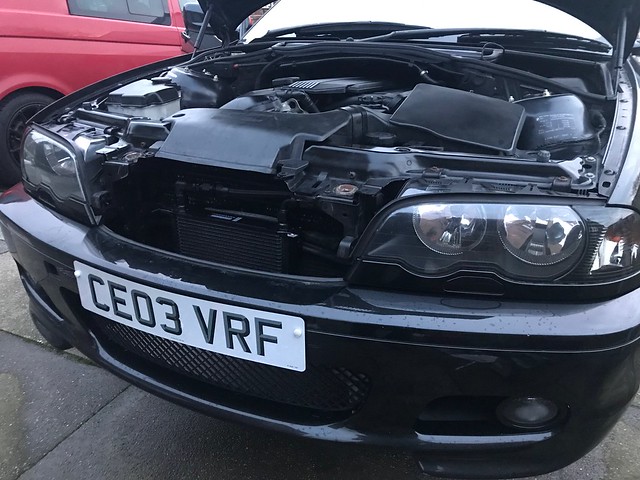
Nice build. Any thoughts of fitting a LSD ? I run a 325ti on track with 330 engine. It has good grip but feel a LSD would help it on tighter corners. You've also got me paranoid about oil temp. now ! I do 30-40 min stints on track with no apparent problems but have no oil temp gauge. If I use hidden dash functions coolant temp actually drops several degrees on track compared to on road. I know this might have little to do with oil temp. Keep up the good work and I'd be interested in your thoughts regarding a LSD 👍👍
330ti said:
Nice build. Any thoughts of fitting a LSD ? I run a 325ti on track with 330 engine. It has good grip but feel a LSD would help it on tighter corners. You've also got me paranoid about oil temp. now ! I do 30-40 min stints on track with no apparent problems but have no oil temp gauge. If I use hidden dash functions coolant temp actually drops several degrees on track compared to on road. I know this might have little to do with oil temp. Keep up the good work and I'd be interested in your thoughts regarding a LSD ????
I also have a 318ti with 330 conversion.I went with a Kaaz diff on a 3.38fd, the diff makes a lot of difference on track, the extra drive out of corners when it’s dry is amazing, tho in the wet it’s a drift machine

Mgd_uk said:
330ti said:
Nice build. Any thoughts of fitting a LSD ? I run a 325ti on track with 330 engine. It has good grip but feel a LSD would help it on tighter corners. You've also got me paranoid about oil temp. now ! I do 30-40 min stints on track with no apparent problems but have no oil temp gauge. If I use hidden dash functions coolant temp actually drops several degrees on track compared to on road. I know this might have little to do with oil temp. Keep up the good work and I'd be interested in your thoughts regarding a LSD ????
I also have a 318ti with 330 conversion.I went with a Kaaz diff on a 3.38fd, the diff makes a lot of difference on track, the extra drive out of corners when it’s dry is amazing, tho in the wet it’s a drift machine

330ti said:
Nice build. Any thoughts of fitting a LSD ? I run a 325ti on track with 330 engine. It has good grip but feel a LSD would help it on tighter corners. You've also got me paranoid about oil temp. now ! I do 30-40 min stints on track with no apparent problems but have no oil temp gauge. If I use hidden dash functions coolant temp actually drops several degrees on track compared to on road. I know this might have little to do with oil temp. Keep up the good work and I'd be interested in your thoughts regarding a LSD ????
Well it's funny you should bring this up... When you get a minute look at the bottom of this update....Regarding oil temp I'd seriously get an oil temp gauge in there as soon as possible. My coolent temp doesn't get that high to be honest but the oil temp rockets to the point withing 3 hard laps it's hitting 120 degrees. The car doesn't show any sign of it other than the fact the alarm on the temp gauge is flashing away. Will be interesting to see how the 19 Row brings to oil temps down. hopefully to high 90's-100 degrees consistently would be great so I can go back to doing 30-40 minutes stints on track without worrying about temps or having to do cool down laps for the oil.
With a little bit of spare time on my hands today I decided to give my other project a good wash after doing a few thousand miles since it was last detailed and waxed/protected for winter, just about to hit 6000 miles on this now since I bought it and converted it
I may come back and add more information and photos about this if it's of interest to anyone..
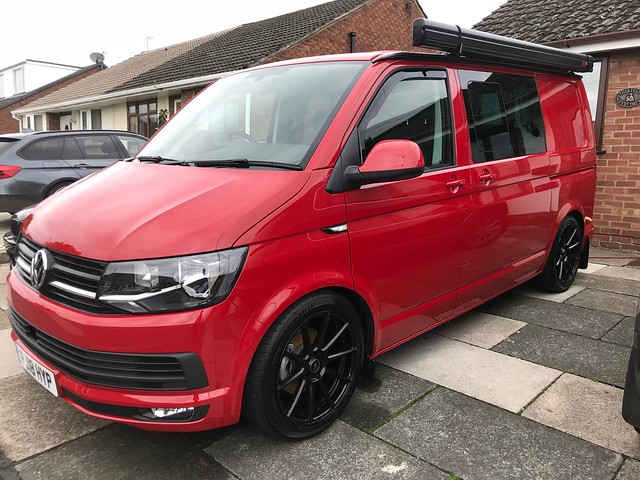
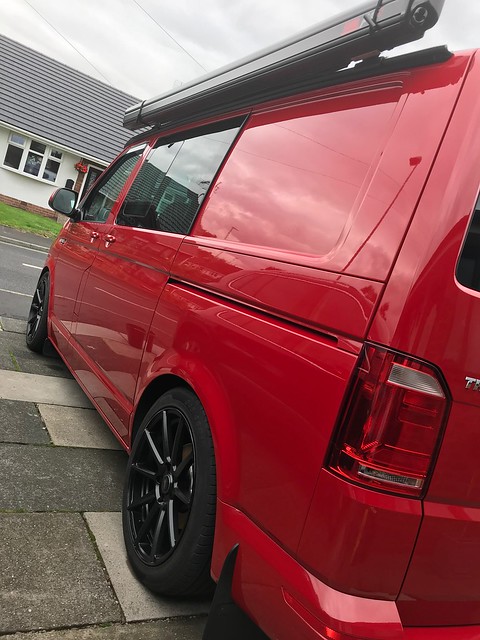
Back to the progress on the BMW... Once the car was cleaned I popped out to the garage to start to strip down a spare 3.38 FD Medium case diff I had knocking around from when the car was built back in the summer. Standard ratio is 2.9 which is longggg, 3.38 feels great on track at the moment so going to build an LSD into that casing. I had already done half a job earlier in the year cleaning up the casing and painting it silver as a temporary measure

Just as I was draining the oil from the diff casing the pulling out the old seals I got a message that my new diff had arrived, quickly packed up what I was doing and popped to pick it up from a friends unit.

Now It's taken me a lot of debating with myself and writing down fores and against regarding going to a Quaife. In the past In the clio I had a Gripper with a shorter final drive and that was fantastic, I also got to compare it against a very similar set up car which had a Quaife in it so have managed to compare the styles of diff against each other all be it in different platforms. FWD rather than RWD.
I have friends running Kaaz in E36 which have been great but when looking into it is seemed more work to get one to fit into the E46 diff casings to work with the FD I wanted to use, one person at Kaaz said they did one that worked, another said they didn't and only did them for E36 casing. In the end I started looking at other plated diffs. Gripper prices where extortionate compared with the price I was able to get a Quaife for. M Factory was another option but I'm not overly big on the idea of their diff's due to the quality and they're not exactly cheaper either! One of the final points for making this decision was that fact that from my own experience with plated diffs as well as friends in BMW's, plated diffs require a pump and cooler set up to be able to manage the oil temps inside the diffs. Because of the gear designed of the Quaife I wouldn't expect that I would need to run any sort of cooling because there isn't the heat generated compared with the plated diffs. I may however put a sensor into the diff casing and log the temps anyway to see what they get to on track. Overall I know the Quaife isn't as good as plated diffs in some situations on track but I decided it's very uncommon for me to be lifting a driving wheel on track and the Quaife set up worked out roughly £1k cheaper than going down the plated diff route by the time I had factored in the cooling required to do it properly. If it need to change in the future I can see this diff on built and build a plated diff into another 3.38 diff I have. Finally the Quaife is what was mandatory on the 330 Challenge cars, but they had to use the 2.9 FD so we'll see how it goes. Obviously leaps ahead of the open diff as we know.
I've booked onto Oulton Park for the 2nd of March so looking forward to getting all these bits sorted and getting back to test them out in March

Edited by tombate911 on Monday 31st December 18:43
Edited by tombate911 on Monday 31st December 18:45
330ti said:
Is that a 168 diff ? Mine is 188 medium case . Where did you get it from ? Cheers
Nope, mine is the 188k medium case also.Can you see this link?
https://imgur.com/gallery/NuipwU9
Edited by Mgd_uk on Monday 31st December 18:36
tombate911 said:
Back to the progress on the BMW... Once the car was cleaned I popped out to the garage to start to strip down a spare 3.38 FD Medium case diff I had knocking around from when the car was built back in the summer. Standard ratio is 2.9 which is longggg, 3.38 feels great on track at the moment so going to build an LSD into that casing. I had already done half a job earlier in the year cleaning up the casing and painting it silver as a temporary measure
If it turns out half as good as the Clio im sure it will be great work! Edited by tombate911 on Monday 31st December 18:43
G600 said:
That was a good read and a nice set-up, I don't suppose you can remember the measurements for the brake bushes? I've got a Z4 with 330 brakes and access to a lathe so I've been meaning to make a set.
I've drawn up the spare bush I had knocking around. When I measured my slider pins they where on average 11.8, I made a version with 11.9mm holes but when fitted there was too much binding on two bushes so settled at 12mm. Worth measuring your pins and calipers before making your own though as I've only measured my prototype bush and never had these fitted to anyone else's car other than my own. They're a push/press fit in to the calipers at that diameter too but also put a groove in them for a circlip just in case
Another couple of hours spent on the car in the evenings this week.
Removed the diff from the casing and pulled/pressed the old bearings off the BMW diff.
Two diff units side by side. Really happy with the quality of the Quaife so far.
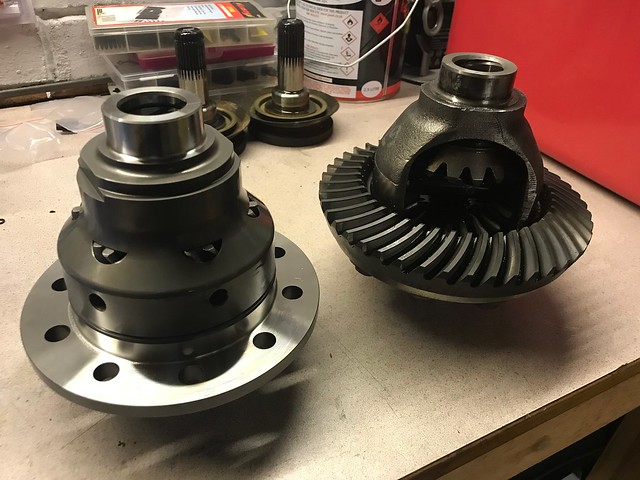
I then moved on to gripping the diff unit in the press to remove the crown wheel bolts.
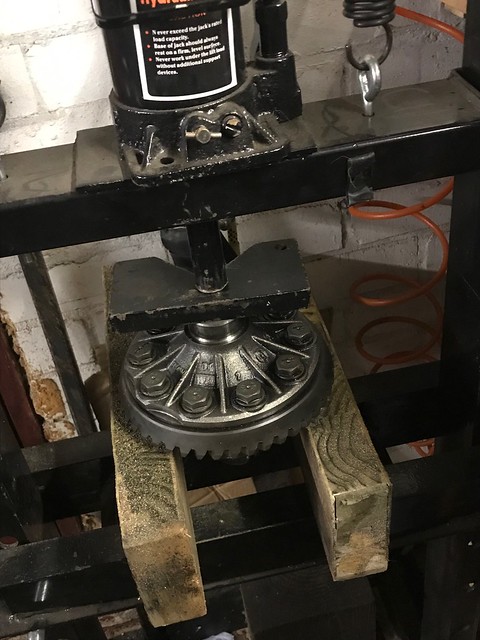
With the bolts undone the crown wheel was lightly pressed off the diff, it's a friction fit with the crown wheel being fitted after some heat has been applied to it to allow it to expand slightly.
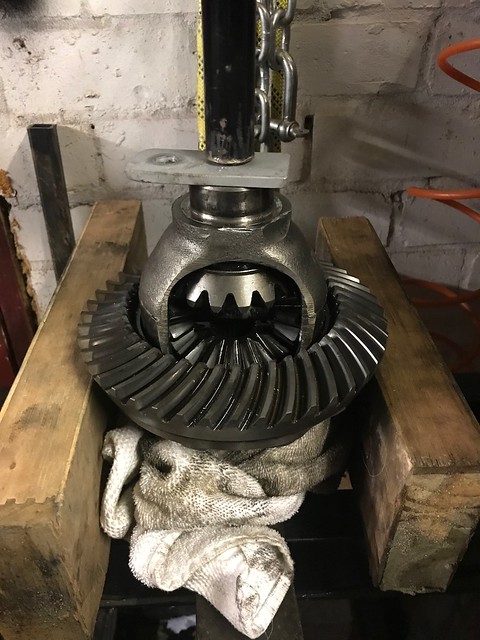
Everything stripped apart and cleaned, degreased ready to be reassembled together.

I've ordered a brand new bottle of Lock Tite for this job just to make sure, when that arrives this week I'll get to building up the diff and removing the old one off the car but it's too cold the past few days for working on the car.
Carrying on with the building of the diff while it's been too cold outside.
Started off by cleaning up the casing and giving it a fresh coat of silver paint and also painting the input shaft flange with some black paint too,

While that was drying I started with fitting the crown wheel to the diff. Put it in the oven at about 120degrees for about 15 minutes. Before carrying it outside wrapped in some towels to keep the heat in it.
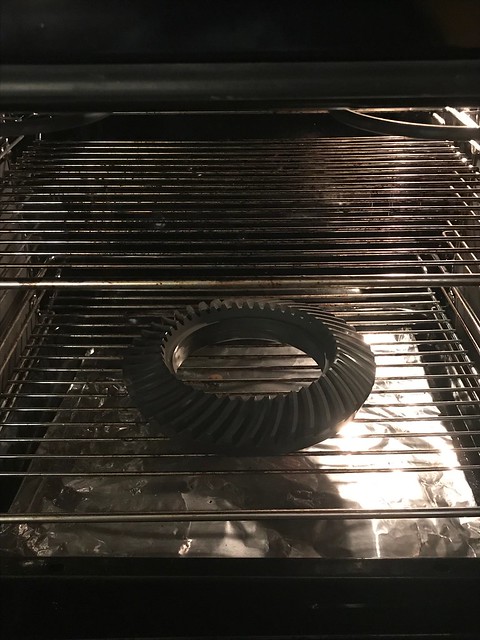
It was easier to rest the crown wheel on two blocks of wood and drop the diff through the centre hole so you could see easily where to align the bolt holes before it cooled. I dropped two bolts in to make sure it was correctly aligned before it cooled and gripped the diff housing
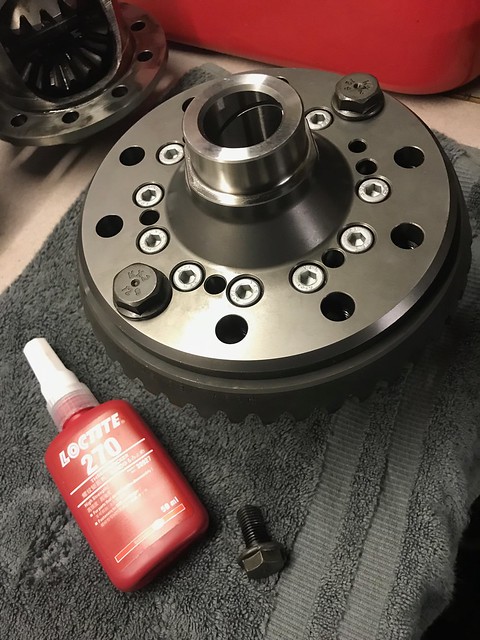
Strong Loctite 270 was applied to each of the bolts and torqued up to spec and marked ones then rechecked again when all the bolts were torqued to make sure they're all consistent and marked a second time.
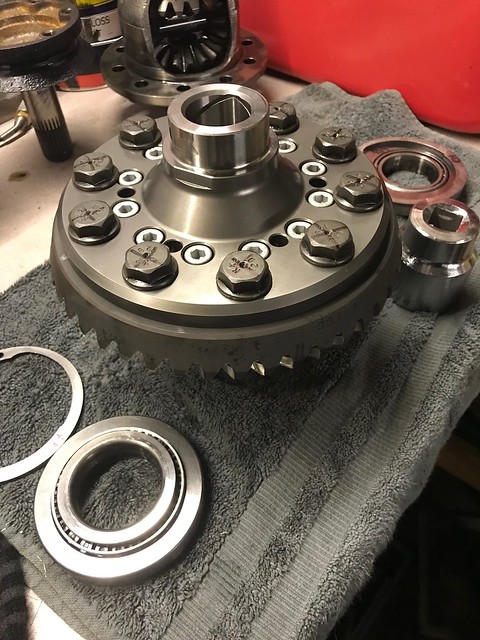
The first bearing being pressed onto to diff
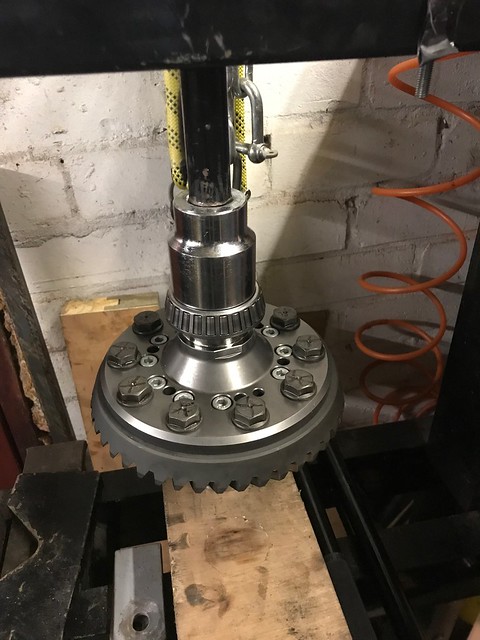
Little more rigging up in the press to make sure it was correctly supported when pressing on the second bearing.
I bought a 3/4" socket set 12 months ago and it is a god send for jobs like this using the press with up to ~60mm sockets.
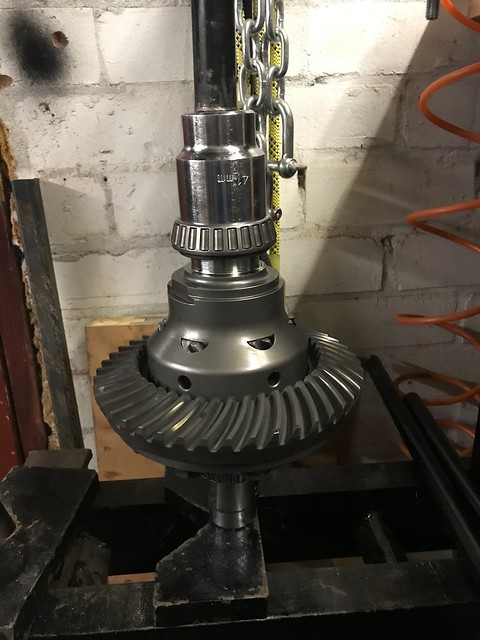
Finally the diff assembly all done and ready to be built up into the casing

When putting it back together I started by checking the preload on the input shaft bearing but because this hadn't been apart and it wasn't worn this was all fine and carried onto fitting the diff into the diff casing. Making sure when it was rebuilt that the same shims that came out of each side were fitting back into the same sides. Below you can see the circuit which acts as the preload spacer for the tapered bearings which hold the diff into position
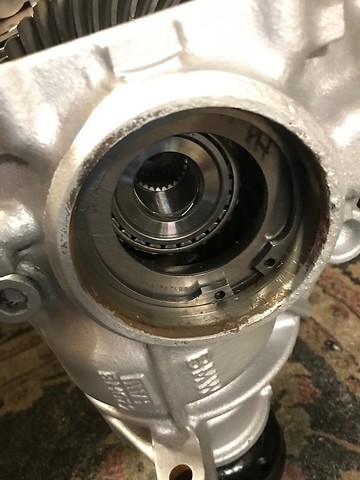
Repeating the same process on the left hand side with the circlip being refitted

At this point now you can check the additional preload on the bearings added onto the initial preload on the input shaft as well as measuring the backlash in the crown wheel and pinion. Back last in the gears was measured with a DTI, set to zero in the following picture

Holding the input shaft completely still and moving the diff/crown wheel back and forwards you can measure the backlash. Here it was showing 0.08mm. That's within tolerance for this so there was no need to start adjusting any shims to adjust the position of the diff in the casing.
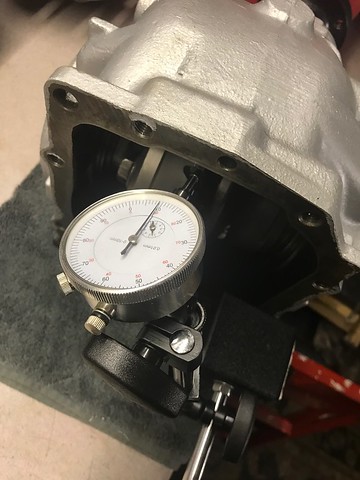
Gear paste added to the crown wheel to do a final check of the gear pattern
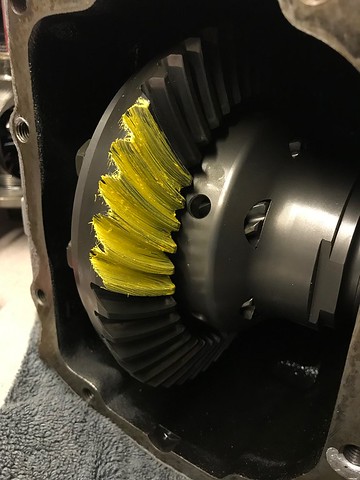
Nice and central gear pattern showing on the drive and coast side of the teeth. I then went on to keep running this around to check the pattern on all the teeth on the crown wheel
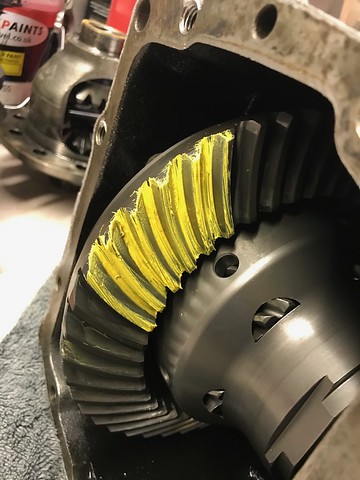
With all that checked and pretty happy with how it has gone so far, I could go ahead and seal on the back casing to the diff
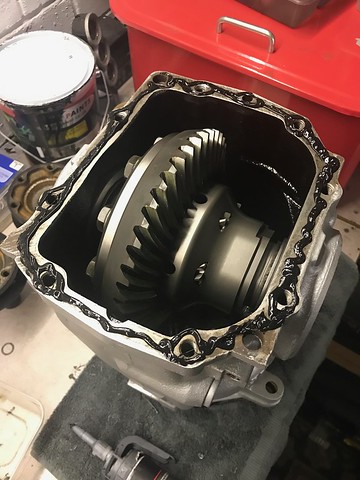
Done and dusted with new output flange seals fitted, ready to be fitted onto the car when I get time and some warmer weather.

When that's fitted I'll be able to get the car down off axle stands were it has been since the last track day and do a few miles in it on the road and check over everything that's been changed ready for the track day in March at Oulton Park. That's looking to be a great day with a large bunch of friends already booked on for it.
Started off by cleaning up the casing and giving it a fresh coat of silver paint and also painting the input shaft flange with some black paint too,

While that was drying I started with fitting the crown wheel to the diff. Put it in the oven at about 120degrees for about 15 minutes. Before carrying it outside wrapped in some towels to keep the heat in it.
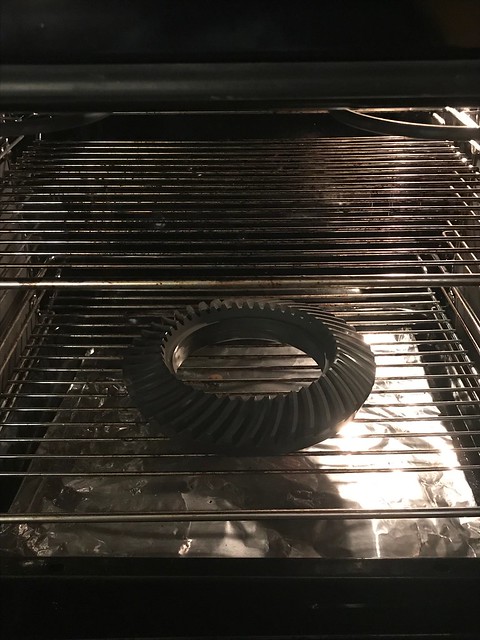
It was easier to rest the crown wheel on two blocks of wood and drop the diff through the centre hole so you could see easily where to align the bolt holes before it cooled. I dropped two bolts in to make sure it was correctly aligned before it cooled and gripped the diff housing
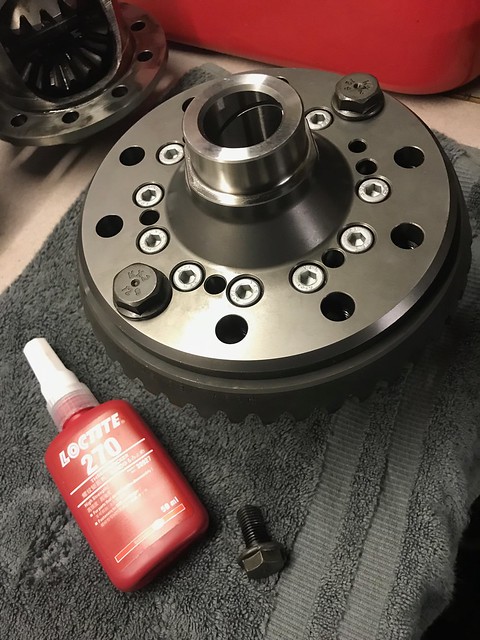
Strong Loctite 270 was applied to each of the bolts and torqued up to spec and marked ones then rechecked again when all the bolts were torqued to make sure they're all consistent and marked a second time.
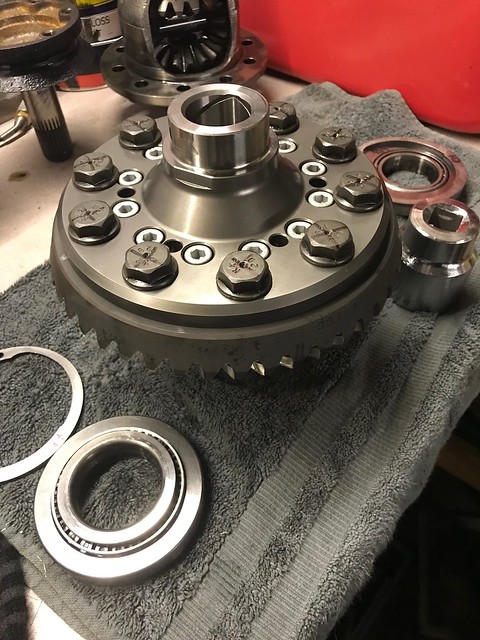
The first bearing being pressed onto to diff
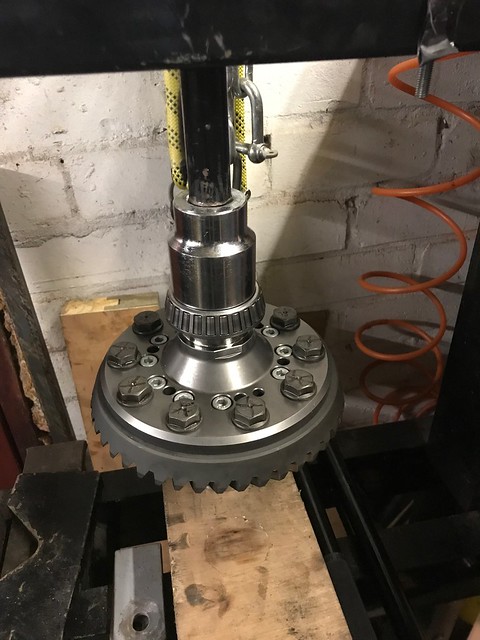
Little more rigging up in the press to make sure it was correctly supported when pressing on the second bearing.
I bought a 3/4" socket set 12 months ago and it is a god send for jobs like this using the press with up to ~60mm sockets.
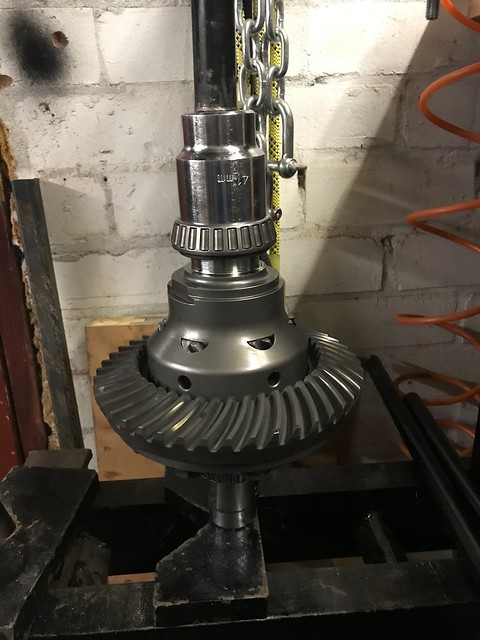
Finally the diff assembly all done and ready to be built up into the casing

When putting it back together I started by checking the preload on the input shaft bearing but because this hadn't been apart and it wasn't worn this was all fine and carried onto fitting the diff into the diff casing. Making sure when it was rebuilt that the same shims that came out of each side were fitting back into the same sides. Below you can see the circuit which acts as the preload spacer for the tapered bearings which hold the diff into position
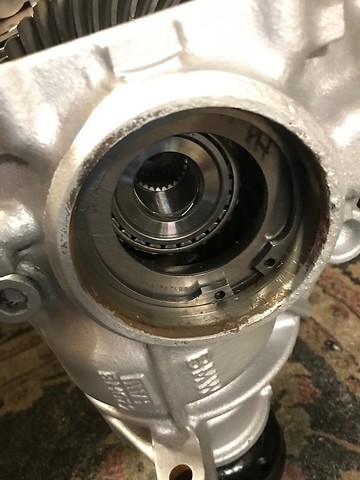
Repeating the same process on the left hand side with the circlip being refitted

At this point now you can check the additional preload on the bearings added onto the initial preload on the input shaft as well as measuring the backlash in the crown wheel and pinion. Back last in the gears was measured with a DTI, set to zero in the following picture

Holding the input shaft completely still and moving the diff/crown wheel back and forwards you can measure the backlash. Here it was showing 0.08mm. That's within tolerance for this so there was no need to start adjusting any shims to adjust the position of the diff in the casing.
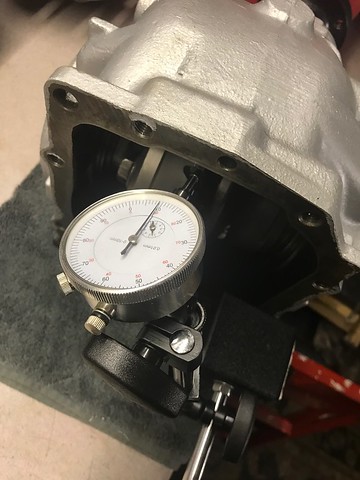
Gear paste added to the crown wheel to do a final check of the gear pattern
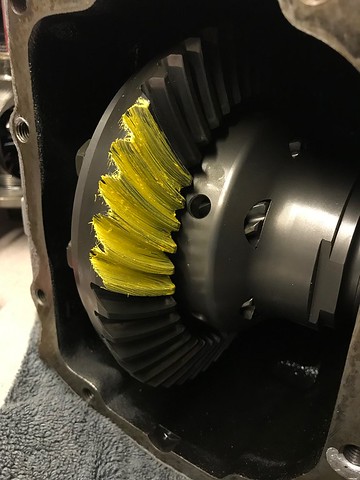
Nice and central gear pattern showing on the drive and coast side of the teeth. I then went on to keep running this around to check the pattern on all the teeth on the crown wheel
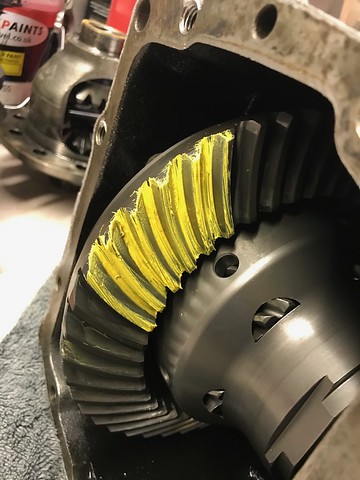
With all that checked and pretty happy with how it has gone so far, I could go ahead and seal on the back casing to the diff
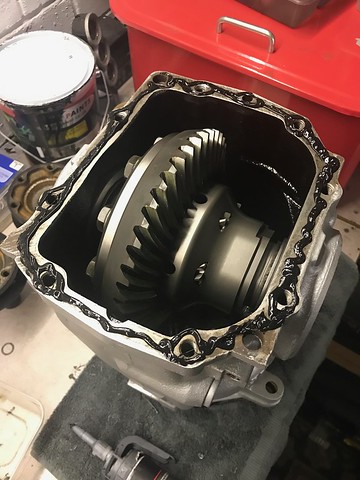
Done and dusted with new output flange seals fitted, ready to be fitted onto the car when I get time and some warmer weather.

When that's fitted I'll be able to get the car down off axle stands were it has been since the last track day and do a few miles in it on the road and check over everything that's been changed ready for the track day in March at Oulton Park. That's looking to be a great day with a large bunch of friends already booked on for it.
helix402 said:
Proper job. Never done any gearbox or diff rebuilds so I respect those who do.
Thanks! 5-6 years ago I never thought i’d be in the position to build a car like this or have the skill to be able to do the build never mind the technical knowledge for some of the other tasks. Amazing what a bit of time and effort put into learning something can do over a period of a few years! I’m always looking for the next challenge. To learn something new! Hopefully try and get the diff fitted at weekend and that car back on it’s wheels so everything can be tested. I’ve not really fancied doing it at the moment in the cold dark and wet!
Gassing Station | Readers' Cars | Top of Page | What's New | My Stuff