DIY Low Profile Ramps
Discussion
Hi PH
Another sleepless night in a hotel, thought I'd look at ramp options to get my 911 up a height relatively easily. I'm about to service my partner's CR-V so figured now would be the time to buy/build some ramps as my jacks are elsewhere. I came across Race Ramps on one of the usual 911 forums as the usual online suspects weren't getting much more than a 4" lift, however at £624 I could likely put that towards an actual hydraulic lift, which I don't have the space for yet (workshop extension pending).
https://www.raceramps.co.uk/product/67-race-ramp-x...
I decided to use the R&D done by the folks to make a design in Sketchup that I'm happy to open source - mostly to get some feedback from those familiar with working with timber to analyse the crush strength and work out if a £60 B&Q jobby is up to the task.
Proposed timber: https://www.diy.com/departments/essentials-smooth-...
(likely need 12 of those as a rough guesstimate)
The idea is this frame can be covered in plywood - likely 10mm - which will not only increase the strength but leave a smooth surface to drive on/off. One can bolt some batons onto the back of the ramps to provide a run off guide - and stop overdriving off the ramps. (I may as well just re-use the offcuts of some 4" legs I had made for the Ooni table I made out of a spare pallet).
Useful dimensions:
10"/254mm lift
11 degree climbing angle
20"/508mm Flat area
52.44"/ 1332mm climbing length
Overall length: 6ft
Link to SketchUp file: https://drive.google.com/file/d/1y-umUruru2PDblUk4...
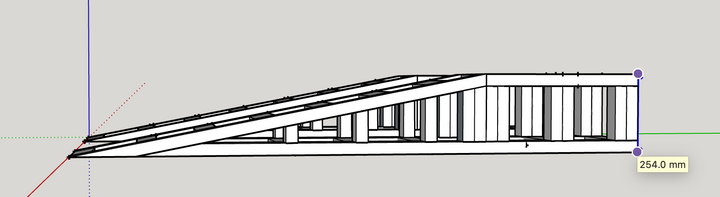
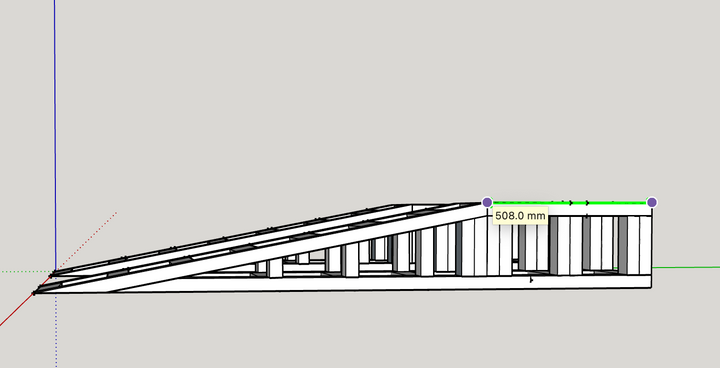
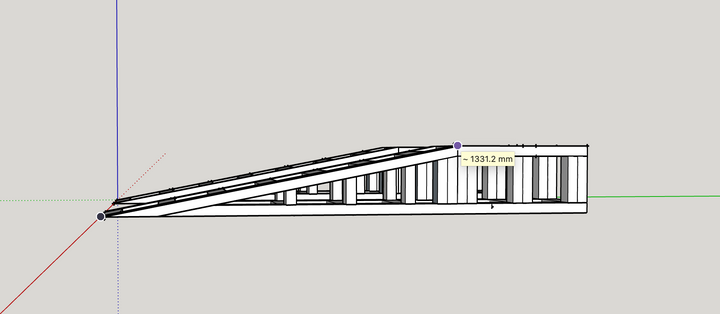
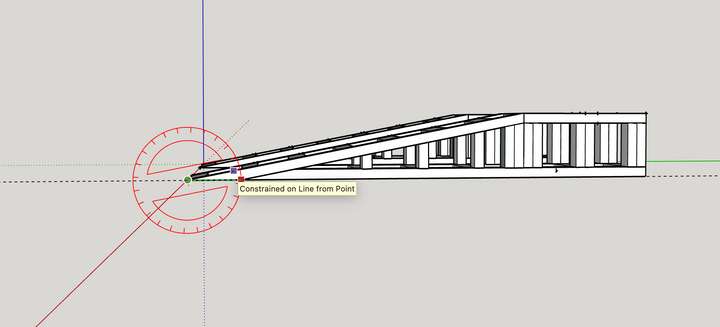
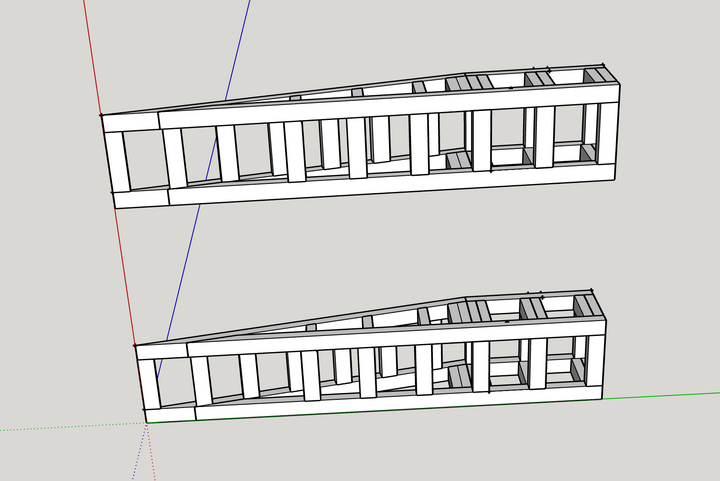
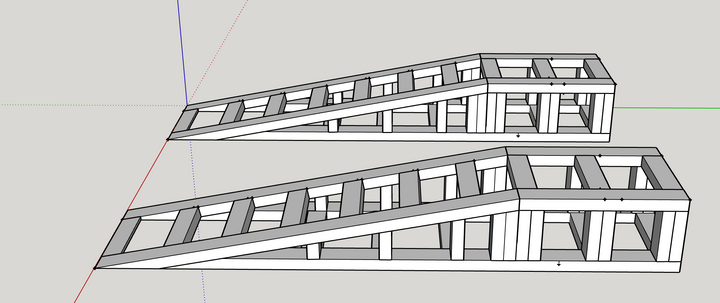
Another sleepless night in a hotel, thought I'd look at ramp options to get my 911 up a height relatively easily. I'm about to service my partner's CR-V so figured now would be the time to buy/build some ramps as my jacks are elsewhere. I came across Race Ramps on one of the usual 911 forums as the usual online suspects weren't getting much more than a 4" lift, however at £624 I could likely put that towards an actual hydraulic lift, which I don't have the space for yet (workshop extension pending).
https://www.raceramps.co.uk/product/67-race-ramp-x...
I decided to use the R&D done by the folks to make a design in Sketchup that I'm happy to open source - mostly to get some feedback from those familiar with working with timber to analyse the crush strength and work out if a £60 B&Q jobby is up to the task.
Proposed timber: https://www.diy.com/departments/essentials-smooth-...
(likely need 12 of those as a rough guesstimate)
The idea is this frame can be covered in plywood - likely 10mm - which will not only increase the strength but leave a smooth surface to drive on/off. One can bolt some batons onto the back of the ramps to provide a run off guide - and stop overdriving off the ramps. (I may as well just re-use the offcuts of some 4" legs I had made for the Ooni table I made out of a spare pallet).
Useful dimensions:
10"/254mm lift
11 degree climbing angle
20"/508mm Flat area
52.44"/ 1332mm climbing length
Overall length: 6ft
Link to SketchUp file: https://drive.google.com/file/d/1y-umUruru2PDblUk4...
Edited by geordiepingu on Wednesday 22 May 03:42
I had some feedback elsewhere that suggested I should be cross-bracing, which is a fair comment, so I've reflected that in an update of the design
https://drive.google.com/file/d/18Crt8E7m4g69EQ3eh...
It may be that if timber is wholly unsuitable then I can at least repurpose the design for steel and weld something up when I get my MAG setup out of storage. I want it to be lighter than railway sleepers being stacked on top of each other (that was my first thought)
v2: https://drive.google.com/file/d/18Crt8E7m4g69EQ3eh...
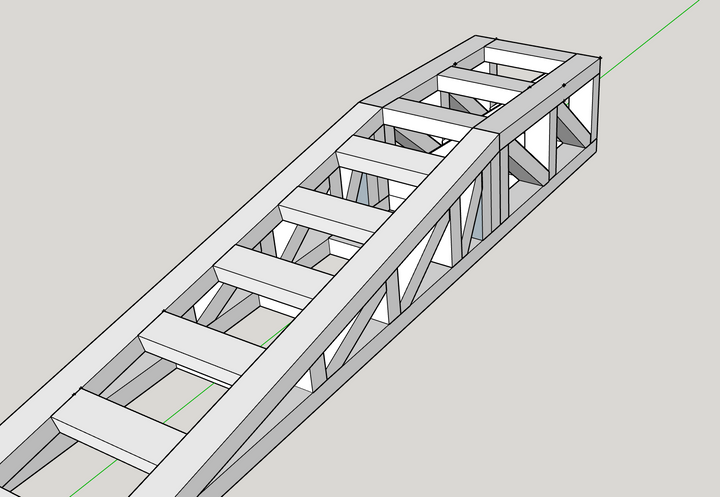
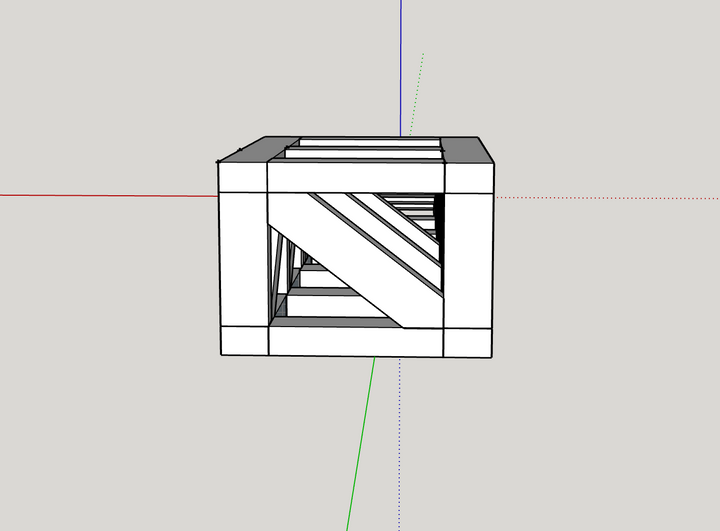
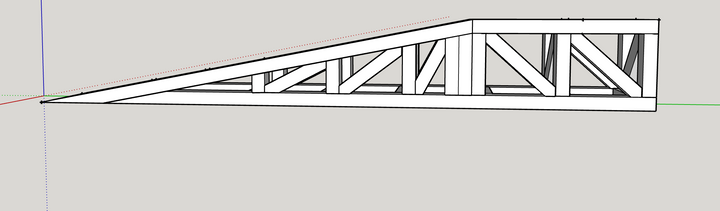
Suppose the other thought might be to re-use my run of the mill steel ramps and make some extensions for low profile use? Best of both words and can probably make it shorter than 6 ft long
My other thought is if I am going to use these reasonably long-term while I get my garage extension sorted, then I should probably be patient and just make them out of bent steel sheet. The big advantage of these over conventional ramps is the fact they're 14" wide.
Otherwise I'm back to looking for off the shelf alternatives if anyone has recommendations. Would like a reasonably good lift - at least 8"
https://drive.google.com/file/d/18Crt8E7m4g69EQ3eh...
It may be that if timber is wholly unsuitable then I can at least repurpose the design for steel and weld something up when I get my MAG setup out of storage. I want it to be lighter than railway sleepers being stacked on top of each other (that was my first thought)
v2: https://drive.google.com/file/d/18Crt8E7m4g69EQ3eh...
Suppose the other thought might be to re-use my run of the mill steel ramps and make some extensions for low profile use? Best of both words and can probably make it shorter than 6 ft long
My other thought is if I am going to use these reasonably long-term while I get my garage extension sorted, then I should probably be patient and just make them out of bent steel sheet. The big advantage of these over conventional ramps is the fact they're 14" wide.
Otherwise I'm back to looking for off the shelf alternatives if anyone has recommendations. Would like a reasonably good lift - at least 8"
Edited by geordiepingu on Wednesday 22 May 06:41
Alternatively buy some decent steel ramps, and a length of scaffold board or similar strong plank, cut board to suitable length after some measuring and using bolts and wing nuts or some other secure method secure one end of the board half way up each ramp to lengthen and therefore lessen the approach angle.
Make sure the boards are secure in the ramps because the driven wheels going up the ramp especially could spin a board out.
Make sure the boards are secure in the ramps because the driven wheels going up the ramp especially could spin a board out.
GreenV8S said:
E-bmw said:
Just get a couple of old scaffold boards & screw progressively shorter lengths on top of each other to make a pair of "stepped" ramps, much stronger.
That. Also, you can make the sloping part detachable, which makes it much easier to work around the car.Something like this... 225mmx38mm scaffy board on top, some C16 38mmx63mm stacked on the edges and some cut up scaffy board to hook into the rung of a metal ramp. Adjust length to suit the height of the ramps. I get the end piece would be end grain, but really it would be hooking on to the metal rung of the ramp so that would be bearing the weight
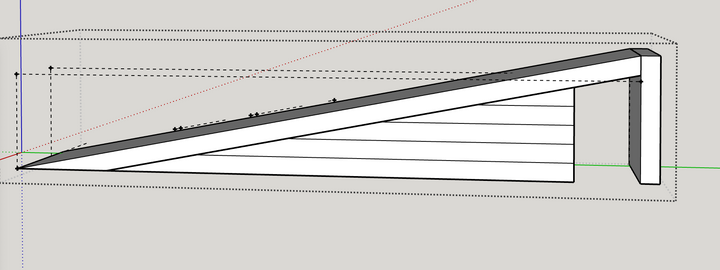
Not quite sure which surface of the surface area I use to calculate the compression strength of the C16 planks suspending the scaffy board, but seems reassuringly strong if I do the long side and longitudinally such that it compresses the grain rather than the end grain https://www.hitchcockandking.co.uk/h-k-news/c16-or...
Not quite sure which surface of the surface area I use to calculate the compression strength of the C16 planks suspending the scaffy board, but seems reassuringly strong if I do the long side and longitudinally such that it compresses the grain rather than the end grain https://www.hitchcockandking.co.uk/h-k-news/c16-or...
Edited by geordiepingu on Wednesday 22 May 19:10
Smint said:
Alternatively buy some decent steel ramps, and a length of scaffold board or similar strong plank, cut board to suitable length after some measuring and using bolts and wing nuts or some other secure method secure one end of the board half way up each ramp to lengthen and therefore lessen the approach angle.
Make sure the boards are secure in the ramps because the driven wheels going up the ramp especially could spin a board out.
That's how I worked on my Griff (very low). I used £150 drive up, hydraulic ramps like below, and then two half length scaff planks to smooth out/soften the approch angle. Worked a charm.Make sure the boards are secure in the ramps because the driven wheels going up the ramp especially could spin a board out.
Cheap, VERY high lift once you operate the jacks, and easy to put away. (stand on ends)
If going timber just lay the planks on top if each other with the ramp surface stepped.
I wouldn't trust bits of wood used as columns, guess I've seen too many US houses under construction just fall over.
And my ramps are made of plastic so it's not like I'm risk averse.
I wouldn't trust bits of wood used as columns, guess I've seen too many US houses under construction just fall over.
And my ramps are made of plastic so it's not like I'm risk averse.
Edited by ChocolateFrog on Thursday 23 May 14:21
geordiepingu said:
Something like this... 225mmx38mm scaffy board on top, some C16 38mmx63mm stacked on the edges and some cut up scaffy board to hook into the rung of a metal ramp. Adjust length to suit the height of the ramps. I get the end piece would be end grain, but really it would be hooking on to the metal rung of the ramp so that would be bearing the weight
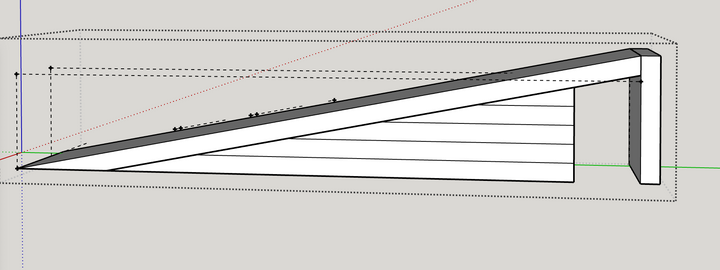
Not quite sure which surface of the surface area I use to calculate the compression strength of the C16 planks suspending the scaffy board, but seems reassuringly strong if I do the long side and longitudinally such that it compresses the grain rather than the end grain https://www.hitchcockandking.co.uk/h-k-news/c16-or...
Don't just screw them together, mind. Whilst you will almost certainly be fine if you do, "almost" isn't enough when it's keeping a car off your face. Glue them when you lay them up, clamp them together, then screw.Not quite sure which surface of the surface area I use to calculate the compression strength of the C16 planks suspending the scaffy board, but seems reassuringly strong if I do the long side and longitudinally such that it compresses the grain rather than the end grain https://www.hitchcockandking.co.uk/h-k-news/c16-or...
Edited by geordiepingu on Wednesday 22 May 19:10
You've gone to the effort of CAD so you might as well consider the end result as an engineer too.

I got a couple of 3 tonne 12v scissor jacks for around £40 each so I can lift the front/rear in unison. Once at height I pop a couple of jack stands under.
With a little to and fro I had my 996 around 500mm off the ground and very secure for working under.
This was when I fitted the stainless manifolds.
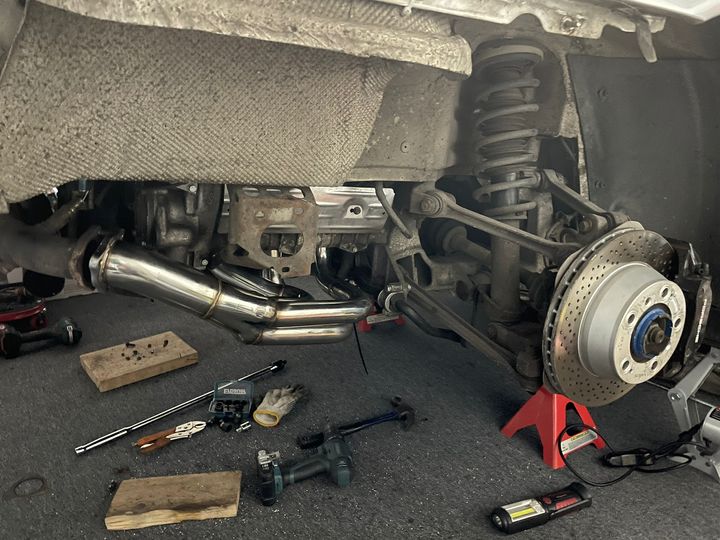
With a little to and fro I had my 996 around 500mm off the ground and very secure for working under.
This was when I fitted the stainless manifolds.
Gassing Station | Home Mechanics | Top of Page | What's New | My Stuff