Unusual job on the bench today
Discussion
ecain63 said:
For the undercuts on the middle laws I used a burr. Easy way to make a nice groove. For the outers I use a hand saw to cut the grooves.
On round stones you can use a hammer handpiece without too many issues and a sharp pusher for the inner edge. For stones like the pear and marquis you have to be wary of the fragile points so a pusher and hammer combo is used to avoid too many shed tears. I'm not a dedicated setter so I'm sure there are flaws in my methods, but on the flipside a setter would struggle with the metalwork so unless I farm it out i have to the do the best I can with my own abilities and skills. Always learning, it never ends.
Thanks for the reply. I haven't had the opportunity to use a hammer handpiece yet but really want to, still doing all my bezel settings the old fashioned way with a pusher. I agree with the always learning and the more you learn, the more you seem to need to learn. Or maybe that is just me!On round stones you can use a hammer handpiece without too many issues and a sharp pusher for the inner edge. For stones like the pear and marquis you have to be wary of the fragile points so a pusher and hammer combo is used to avoid too many shed tears. I'm not a dedicated setter so I'm sure there are flaws in my methods, but on the flipside a setter would struggle with the metalwork so unless I farm it out i have to the do the best I can with my own abilities and skills. Always learning, it never ends.
ctrph said:
Thanks for the reply. I haven't had the opportunity to use a hammer handpiece yet but really want to, still doing all my bezel settings the old fashioned way with a pusher. I agree with the always learning and the more you learn, the more you seem to need to learn. Or maybe that is just me!
If you don't mind me asking, where are you doing your bench training? Did you find a job at a workshop or are you at college or doing courses?Is it something you want to do yourself as a business one day?
ecain63 said:
If you don't mind me asking, where are you doing your bench training? Did you find a job at a workshop or are you at college or doing courses?
Is it something you want to do yourself as a business one day?
I'm doing a course at the School of Jewellery in Birmingham. It is something I have wanted to learn for a while, I am a gemmologist and wanted to put my knowledge to use in a practical environment. Is it something you want to do yourself as a business one day?
I have set stones in silver that I have sold on but that is just to help cover my costs for equipment etc. My main business is bespoke jewellery at the higher end of the market but not sure I will have the confidence to set the more expensive stones.
ctrph said:
I'm doing a course at the School of Jewellery in Birmingham. It is something I have wanted to learn for a while, I am a gemmologist and wanted to put my knowledge to use in a practical environment.
I have set stones in silver that I have sold on but that is just to help cover my costs for equipment etc. My main business is bespoke jewellery at the higher end of the market but not sure I will have the confidence to set the more expensive stones.
If I can lend one bit of advice about the last bit of your comment: it's not confidence you need, it's the neck to just try it and see. There's always risk, no matter your experience but the more you wing it the better you get at flying close to the edge. I have set stones in silver that I have sold on but that is just to help cover my costs for equipment etc. My main business is bespoke jewellery at the higher end of the market but not sure I will have the confidence to set the more expensive stones.

Good luck with it

ecain63 said:
If I can lend one bit of advice about the last bit of your comment: it's not confidence you need, it's the neck to just try it and see. There's always risk, no matter your experience but the more you wing it the better you get at flying close to the edge. 
Good luck with it
Thank you for the advice, the more I do it the more I feel I can take that next step. It is just scary taking the leap from stones that cost a few pounds to those that cost a few hundred or more. Will just go for it at some point
Good luck with it

Morning 
This one is quite pic heavy so apologies if your internet takes a hit. Brief outline: Customer has very arthritic knuckles and is resigned to never wearing a ring again, unless it's made so big it swings round the finger. Queue the next job for ecain63 and his dirty fingers.
The lady has some rings left by her mother and grandmother, including one with a 0.75ct old cut diamond. There are half a dozen other small stones too as well as a mix of 18ct and 9ct yellow gold. We agree to keep the 18ct yellow to make the ring and swap / px the 9ct for another 0.50ct of small stone, making 14 stones in all. I bought some platinum and 18ct yellow tube and away we went. Here's the head building process:
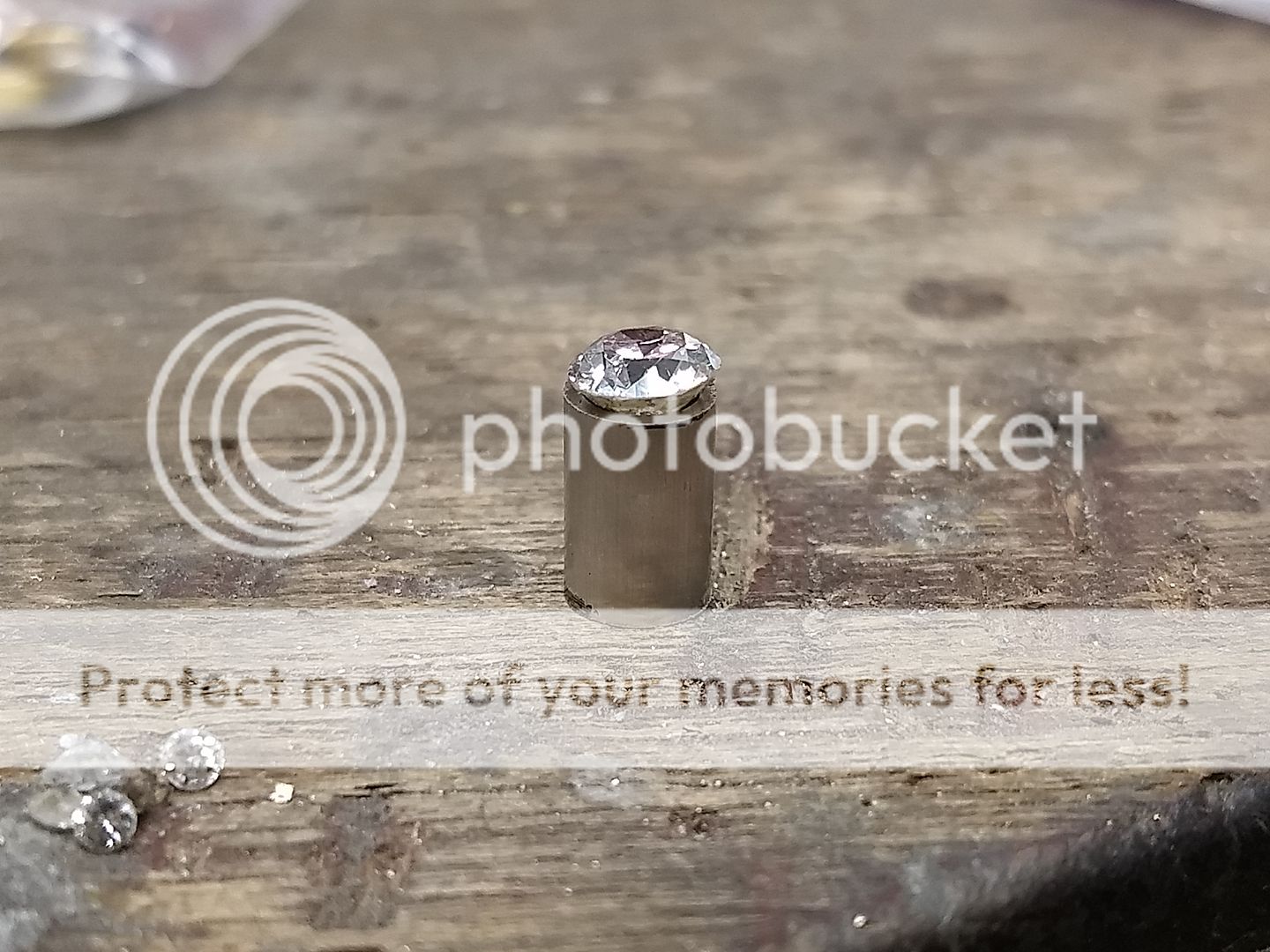
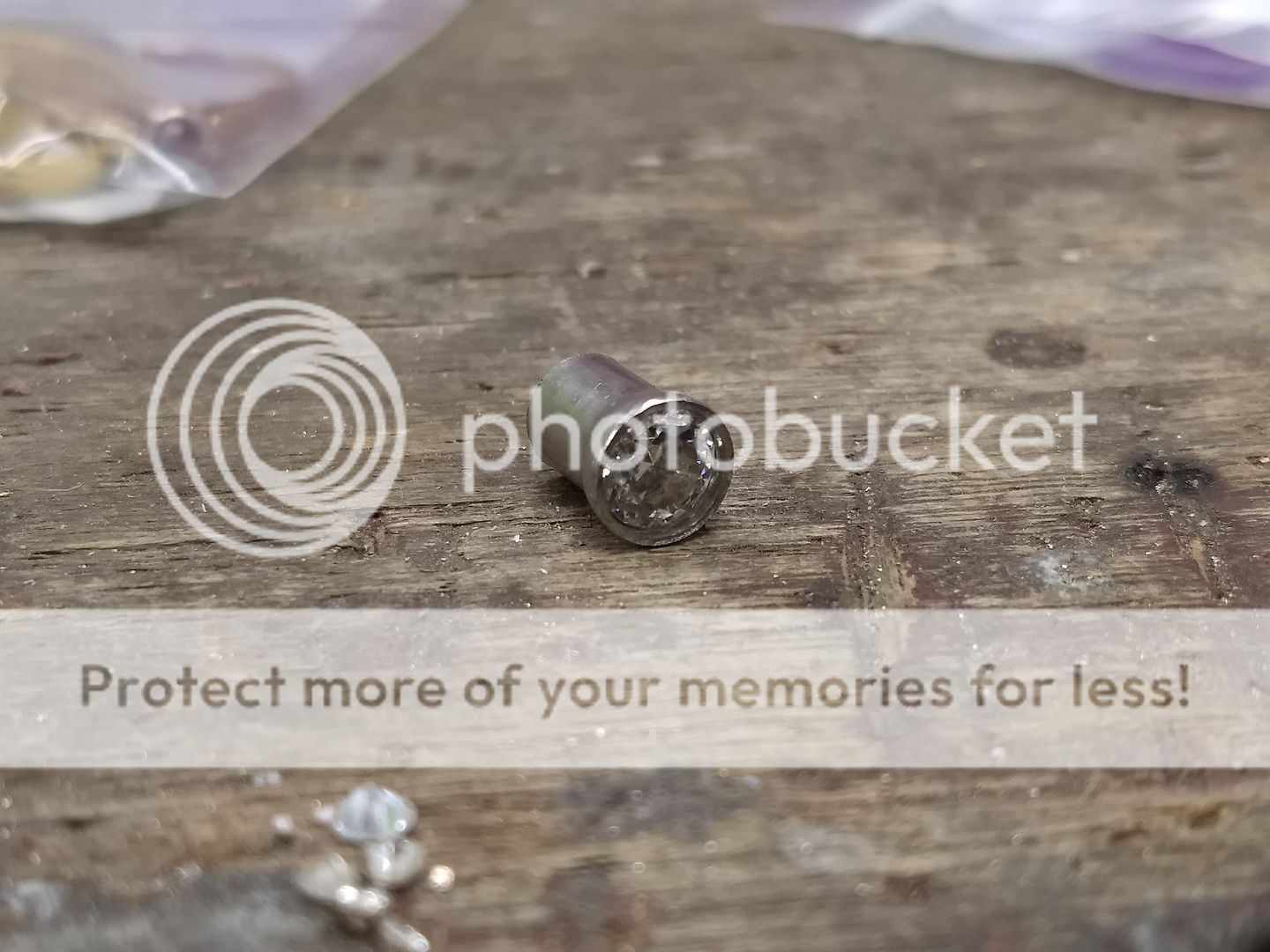
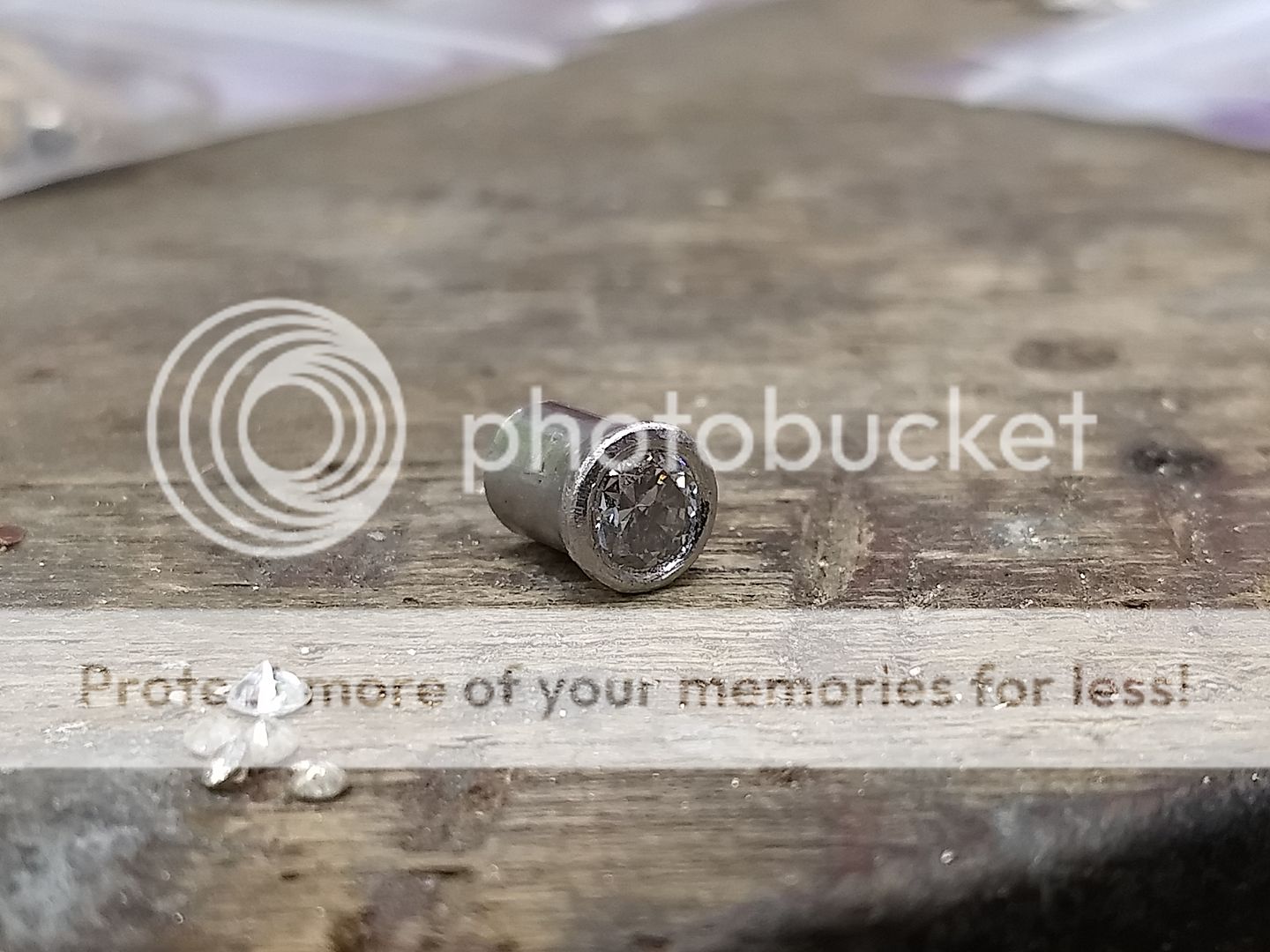
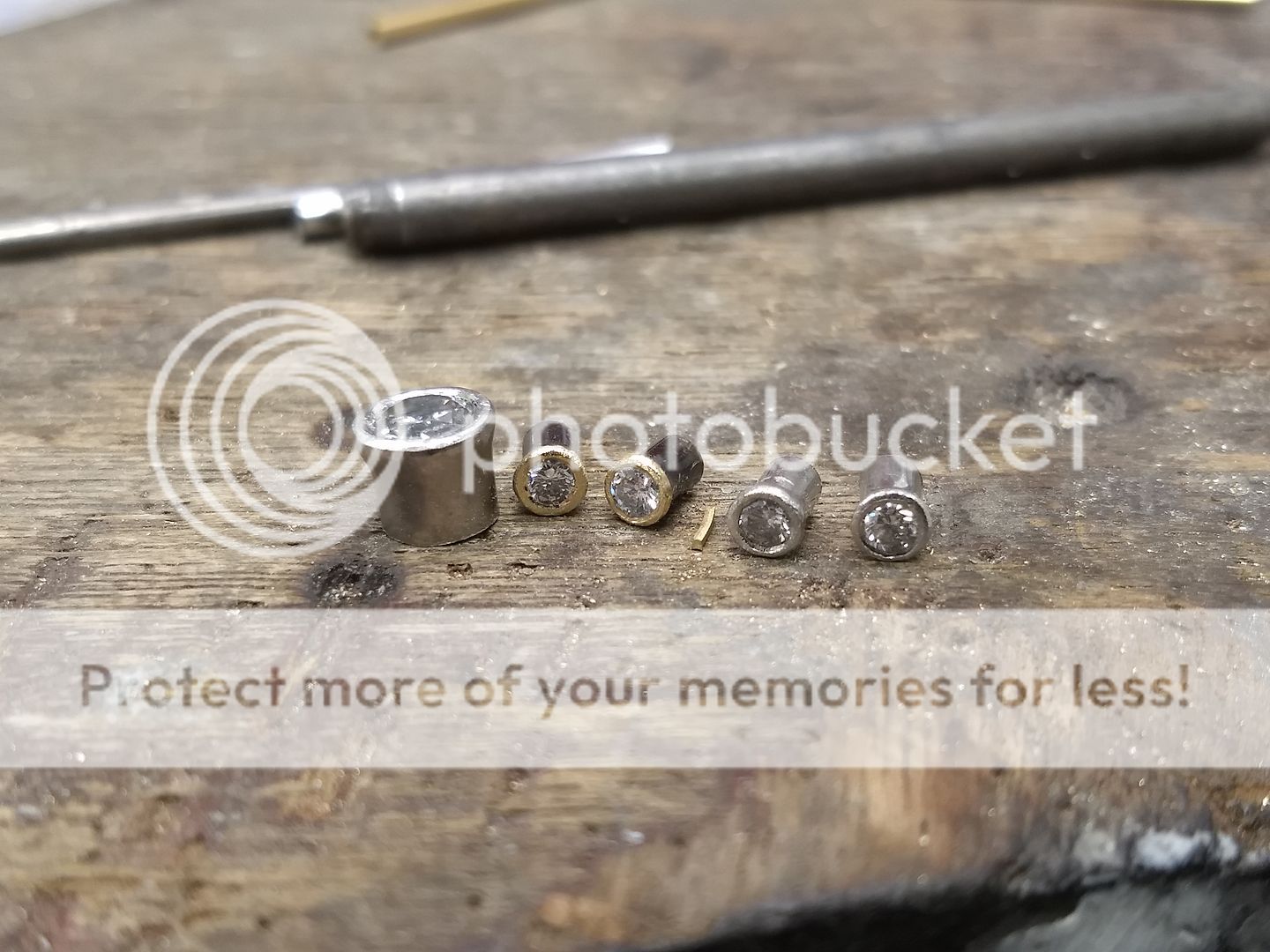
Reminds me of when that setting company did the diamonds on the inside of that Rolls Royce a couple of years back.
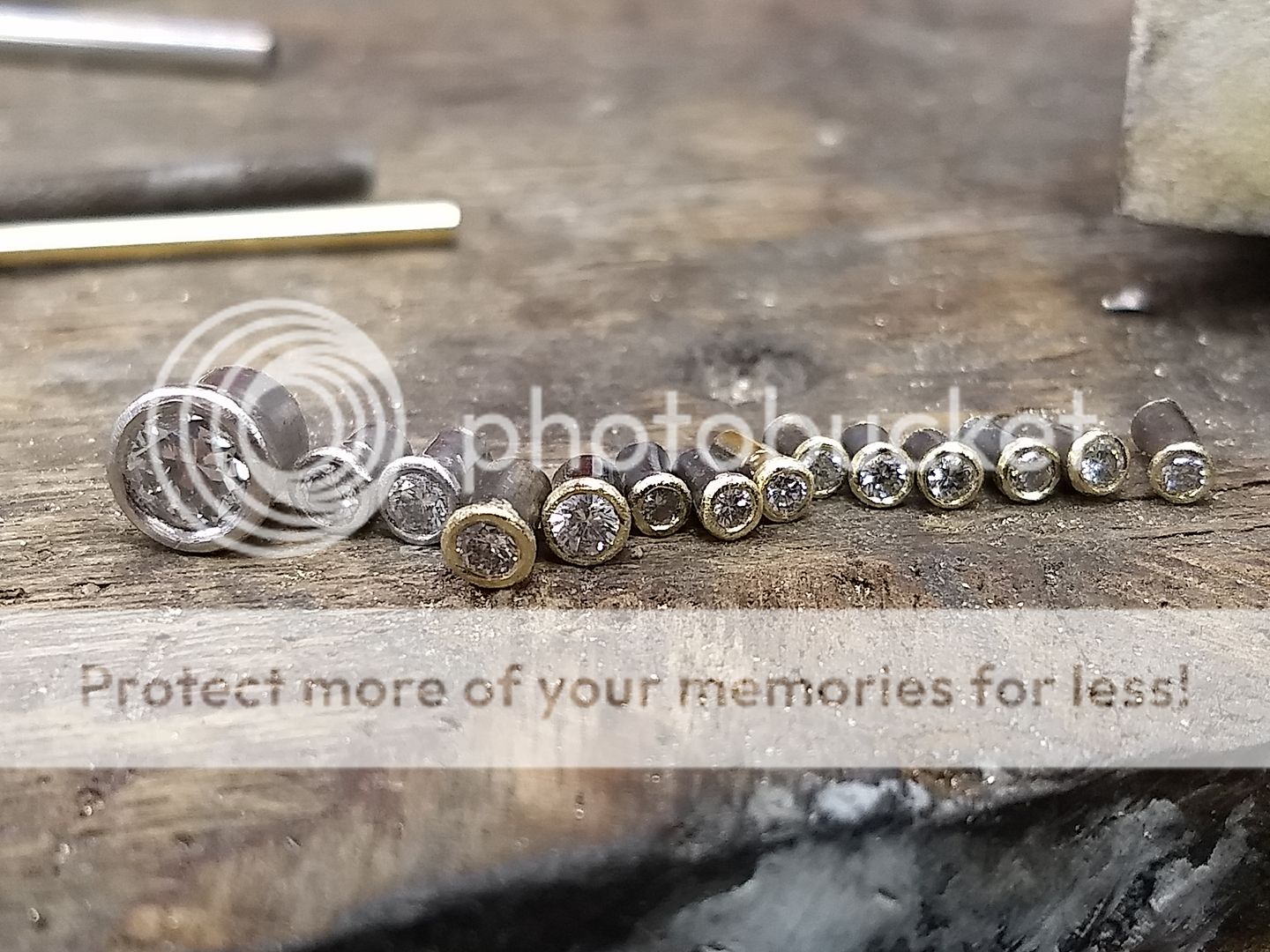
With the stones all set in their tubes we agree on a rough design:
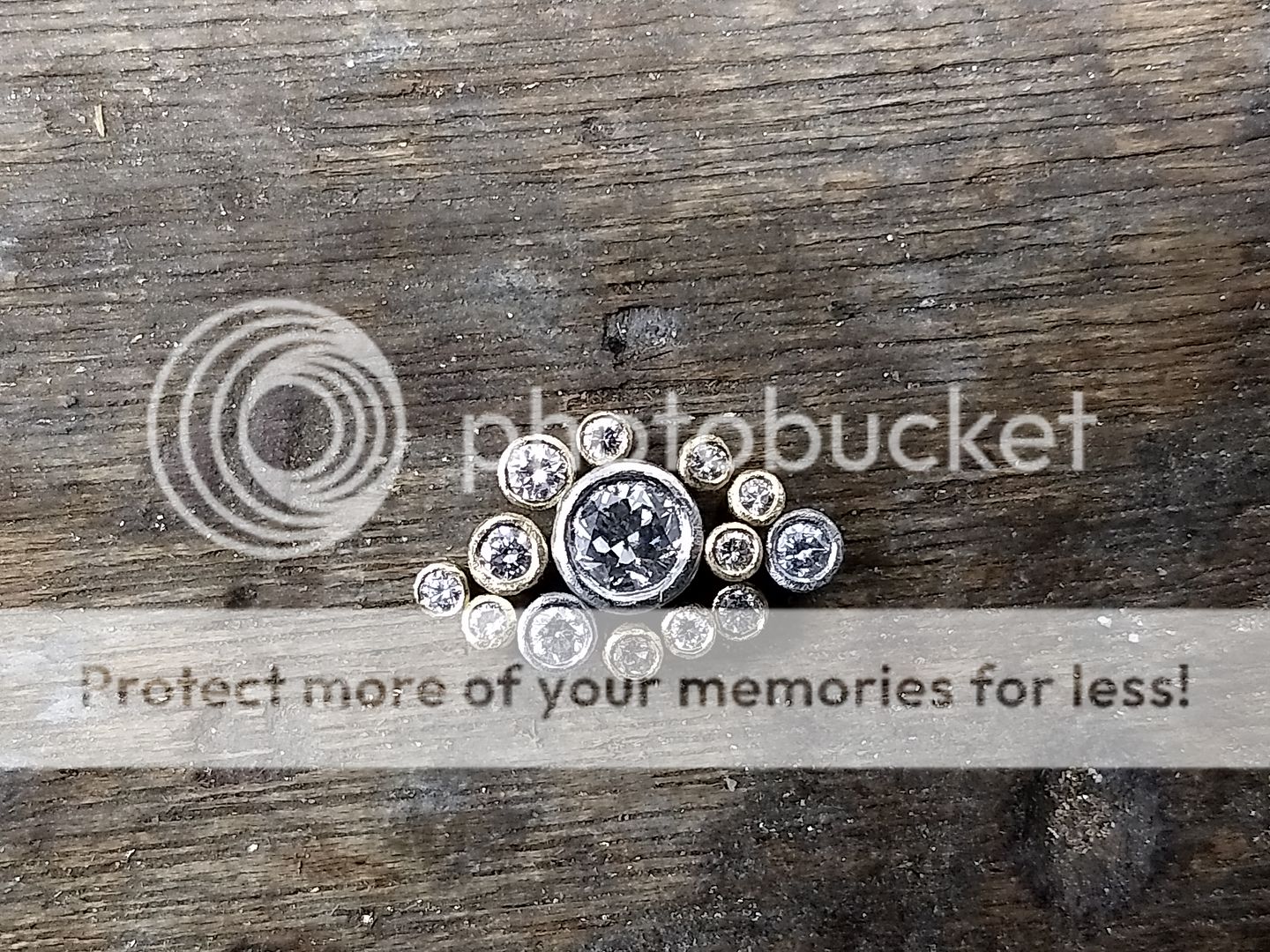

The next job is to make the shoulders and produce a complete head. Here we melt the 18ct scrap and begin the assembly process:
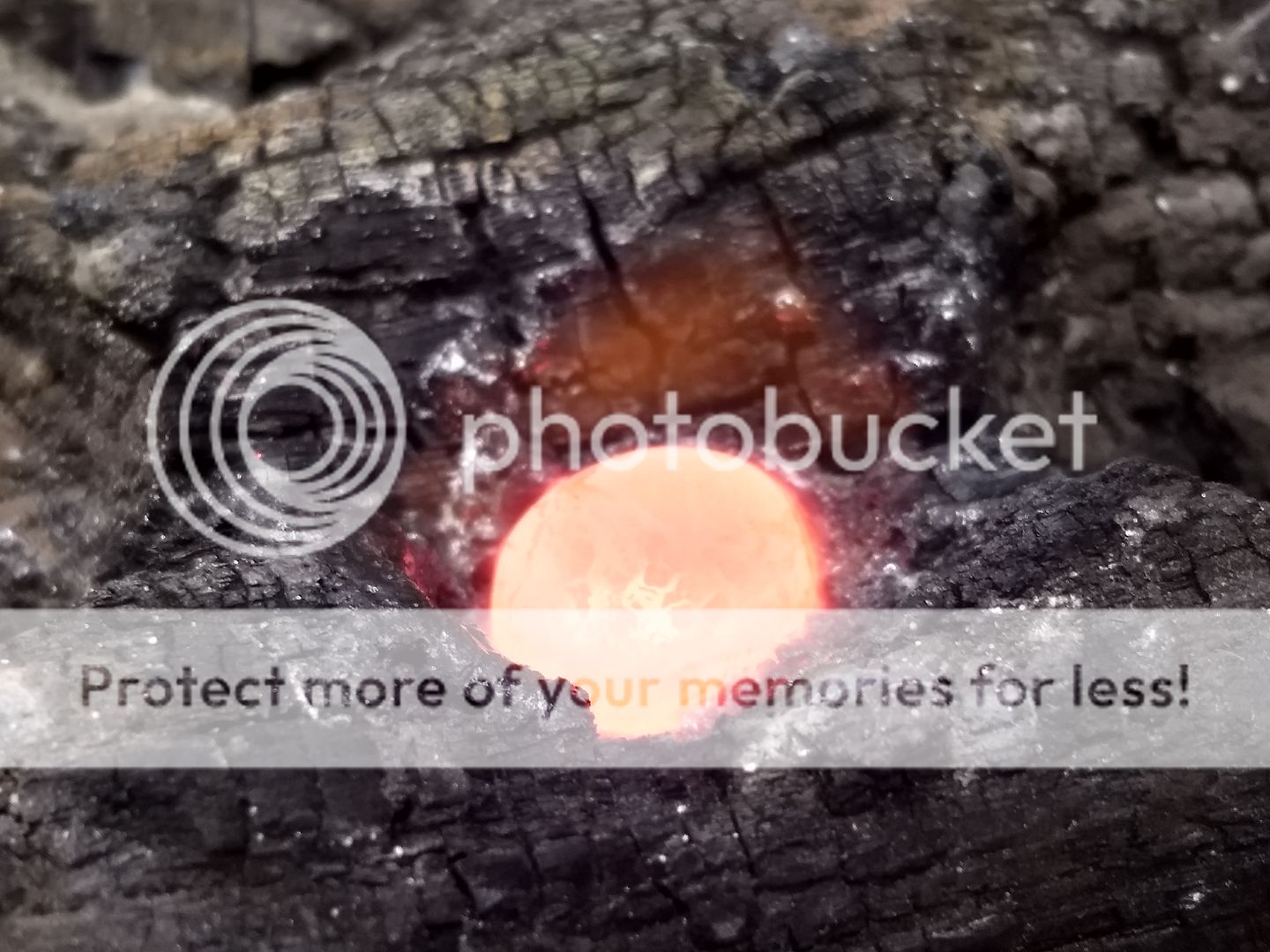
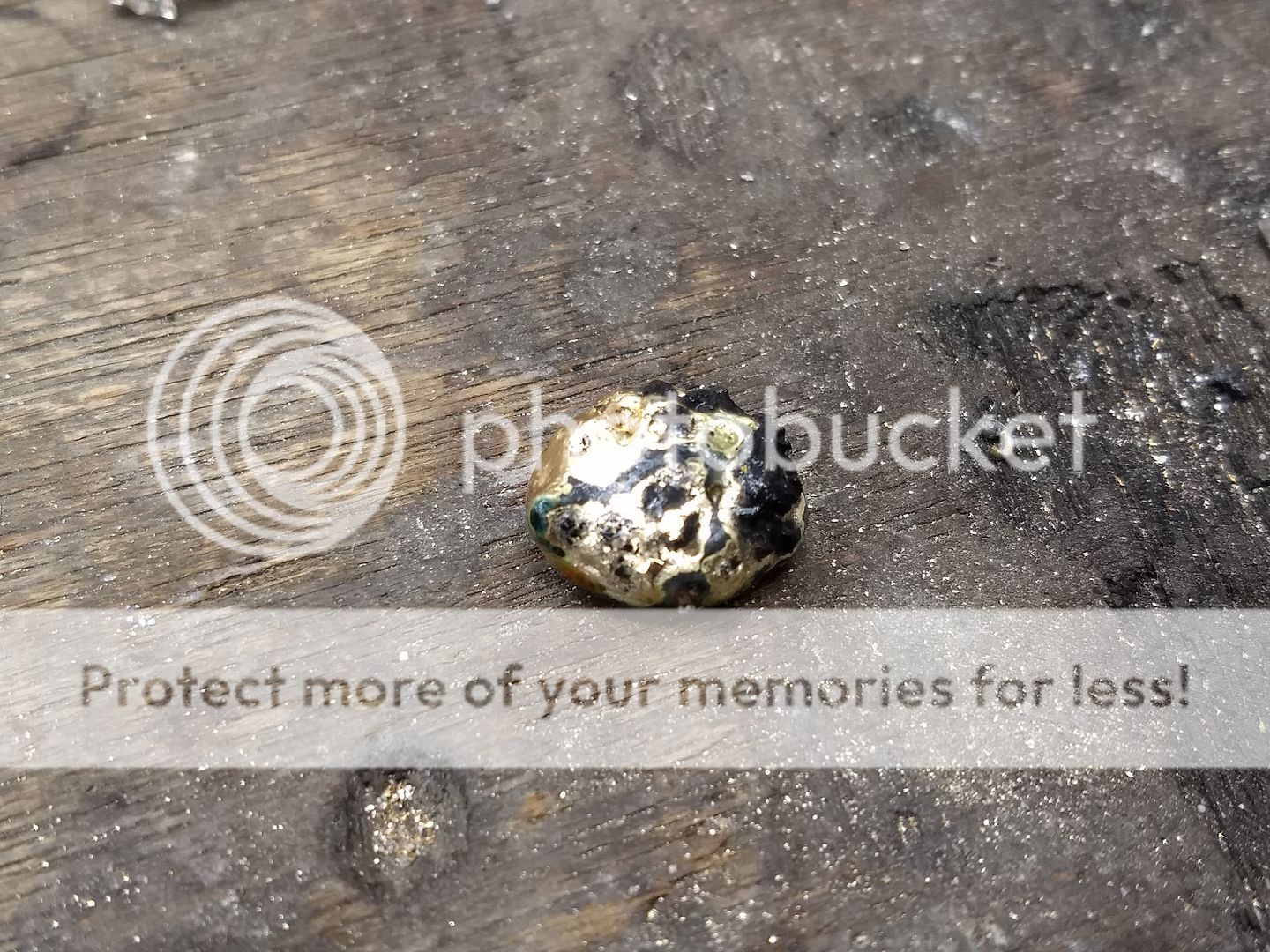
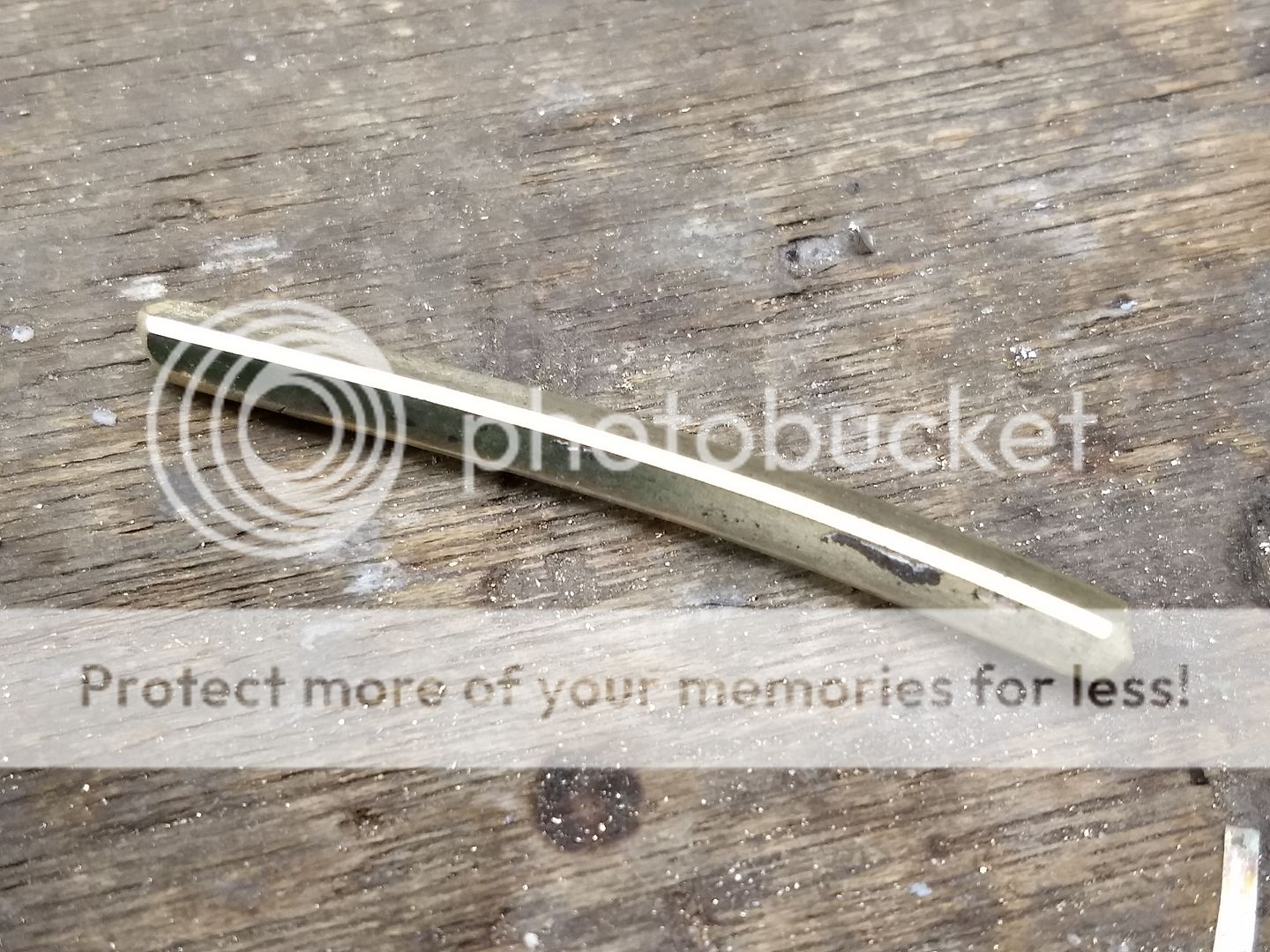
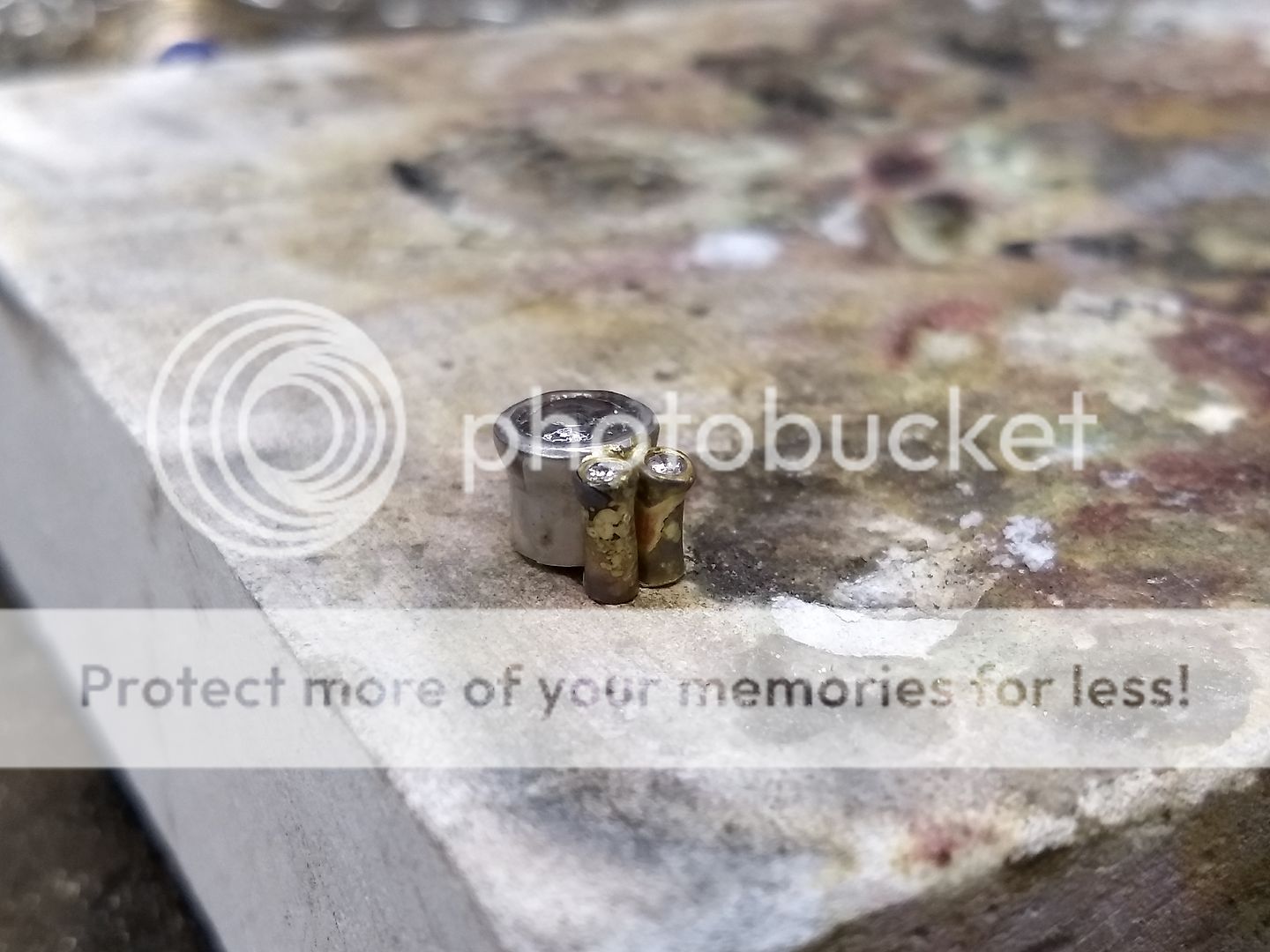
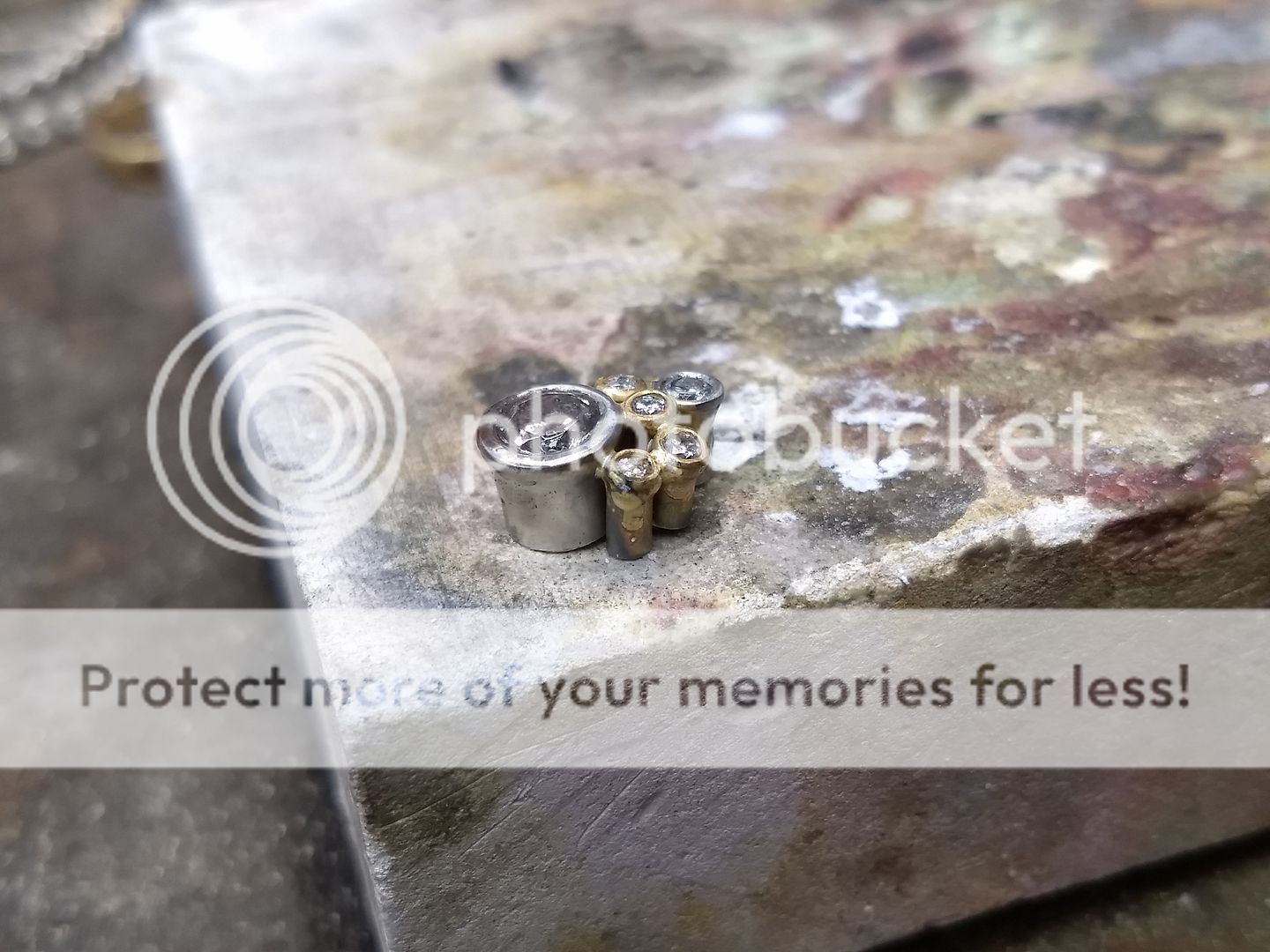
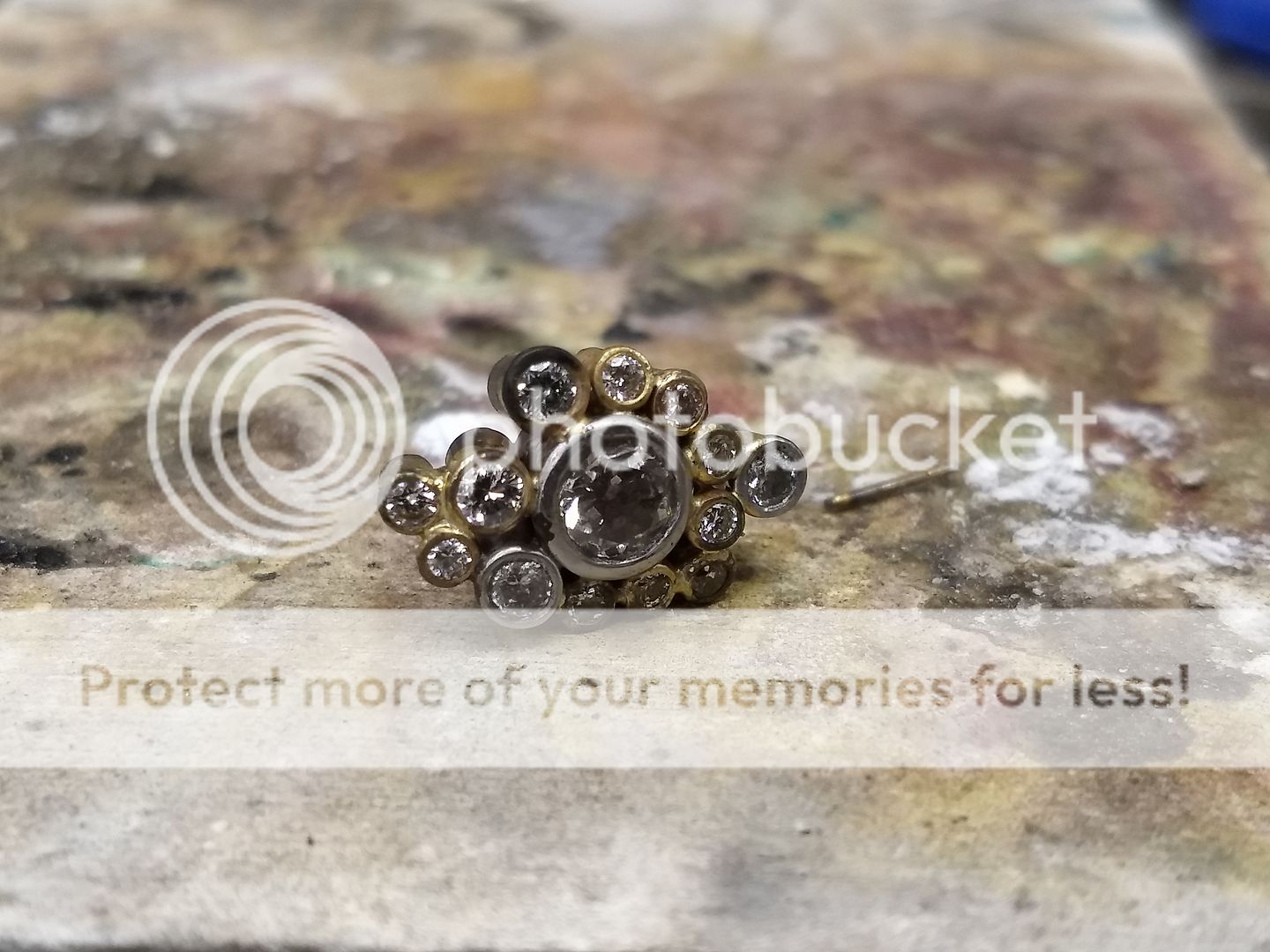
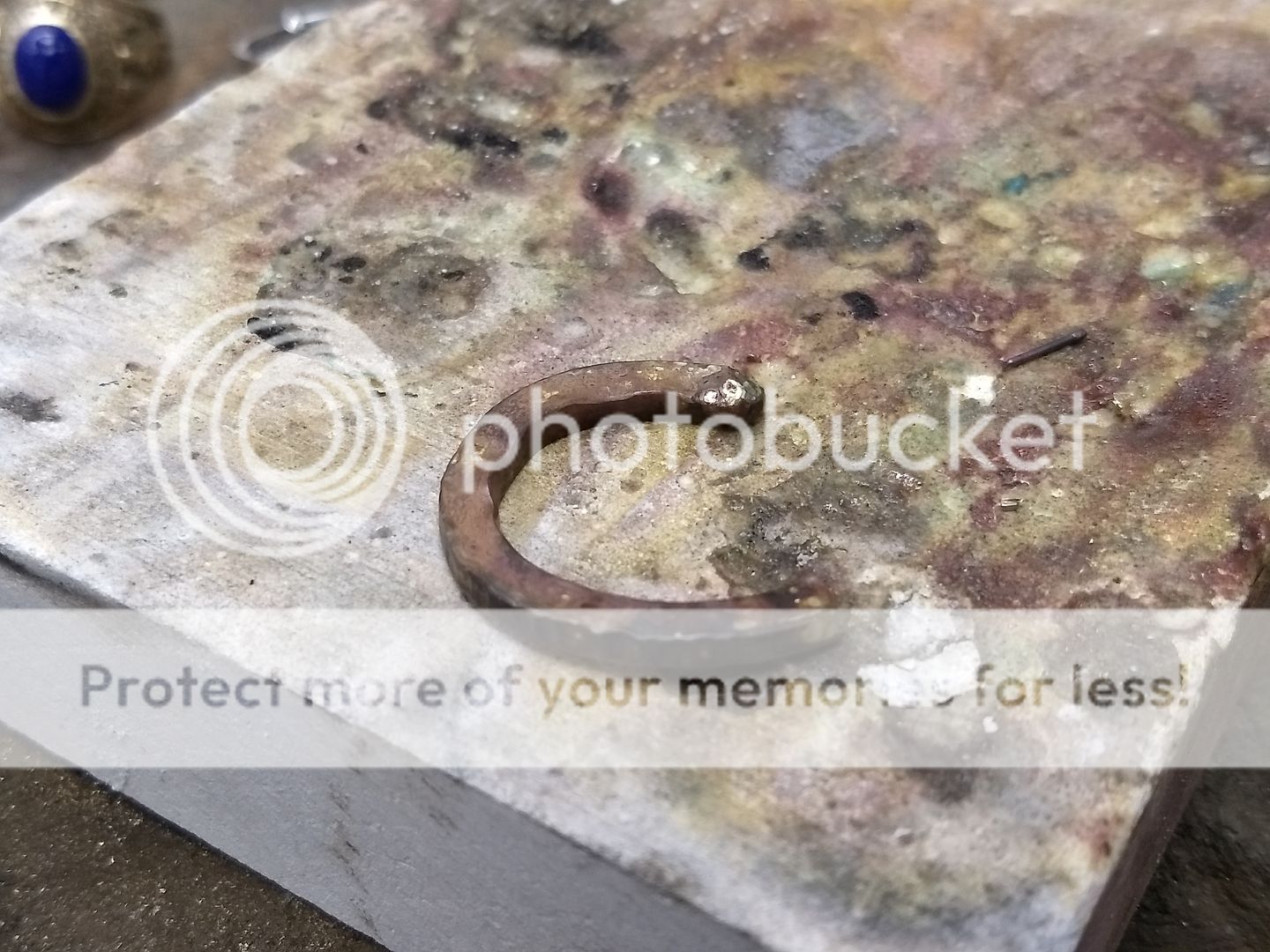
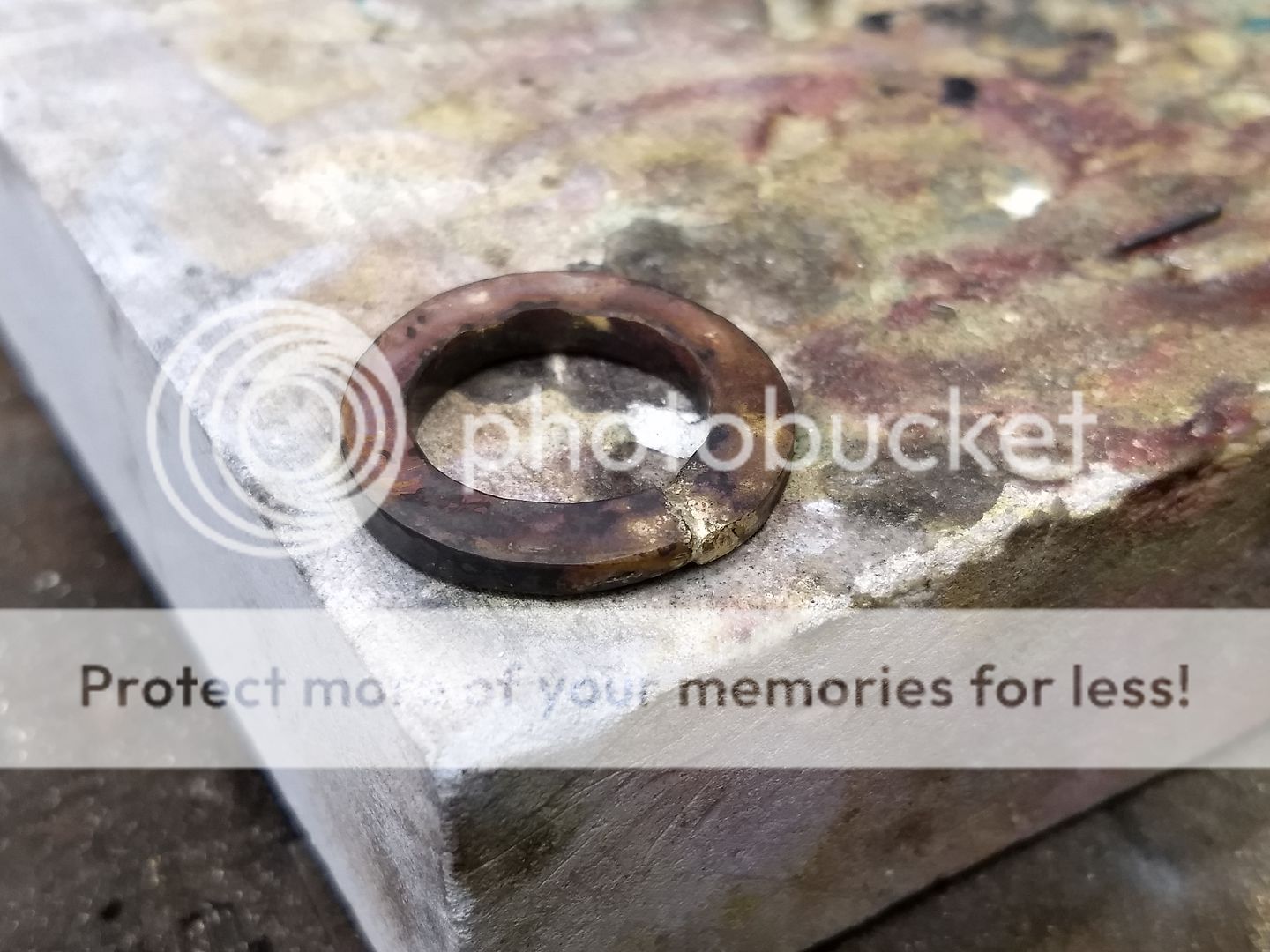
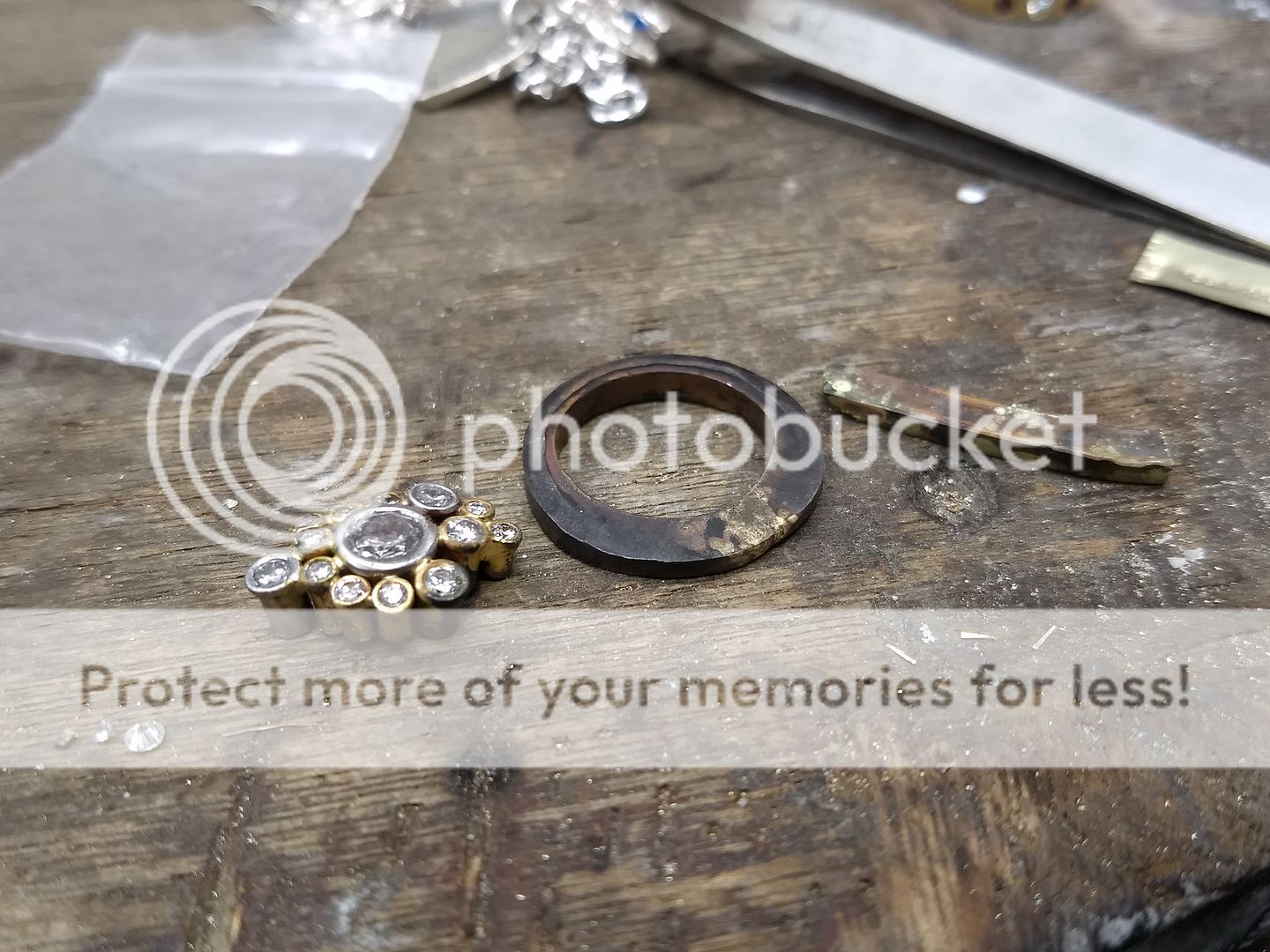
Skipped a pic here for some reason. The above is cleaned up and then split at the centre. The shoulders are shaped to make a twist:
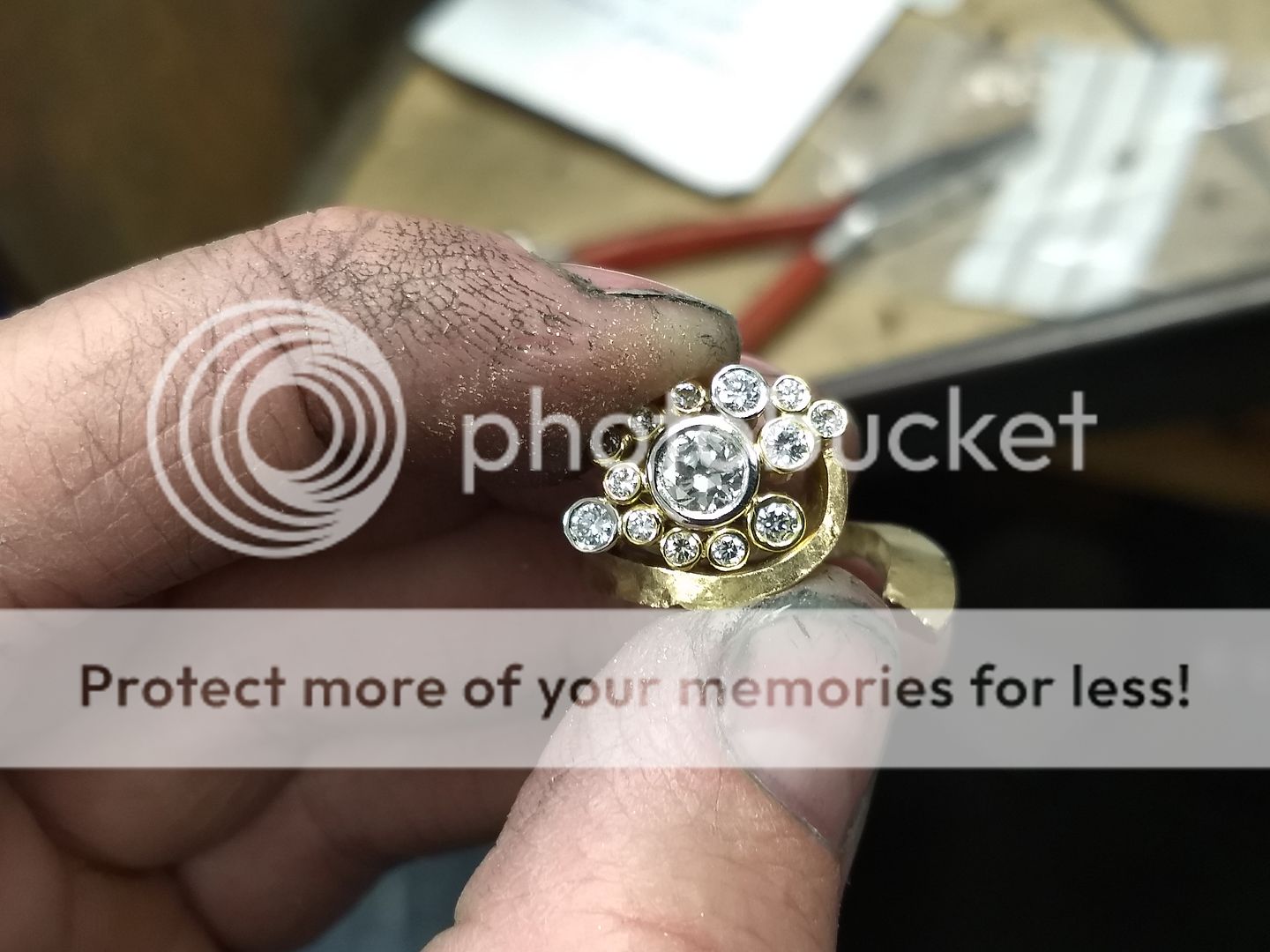
And test fitted on one side after a light file and clean up:
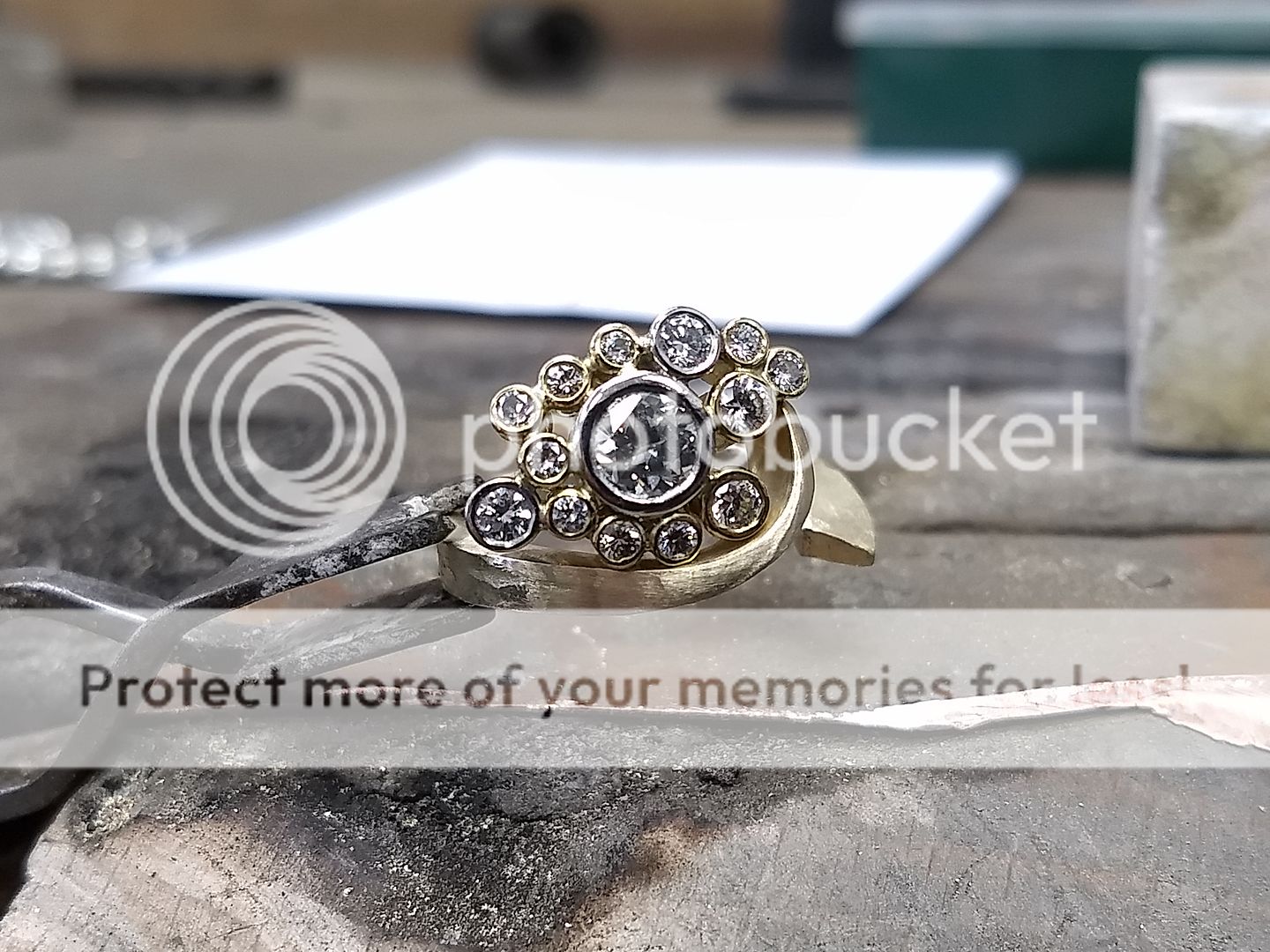
This shoulder is then removed from the other as they are both individually shaped and positioned:
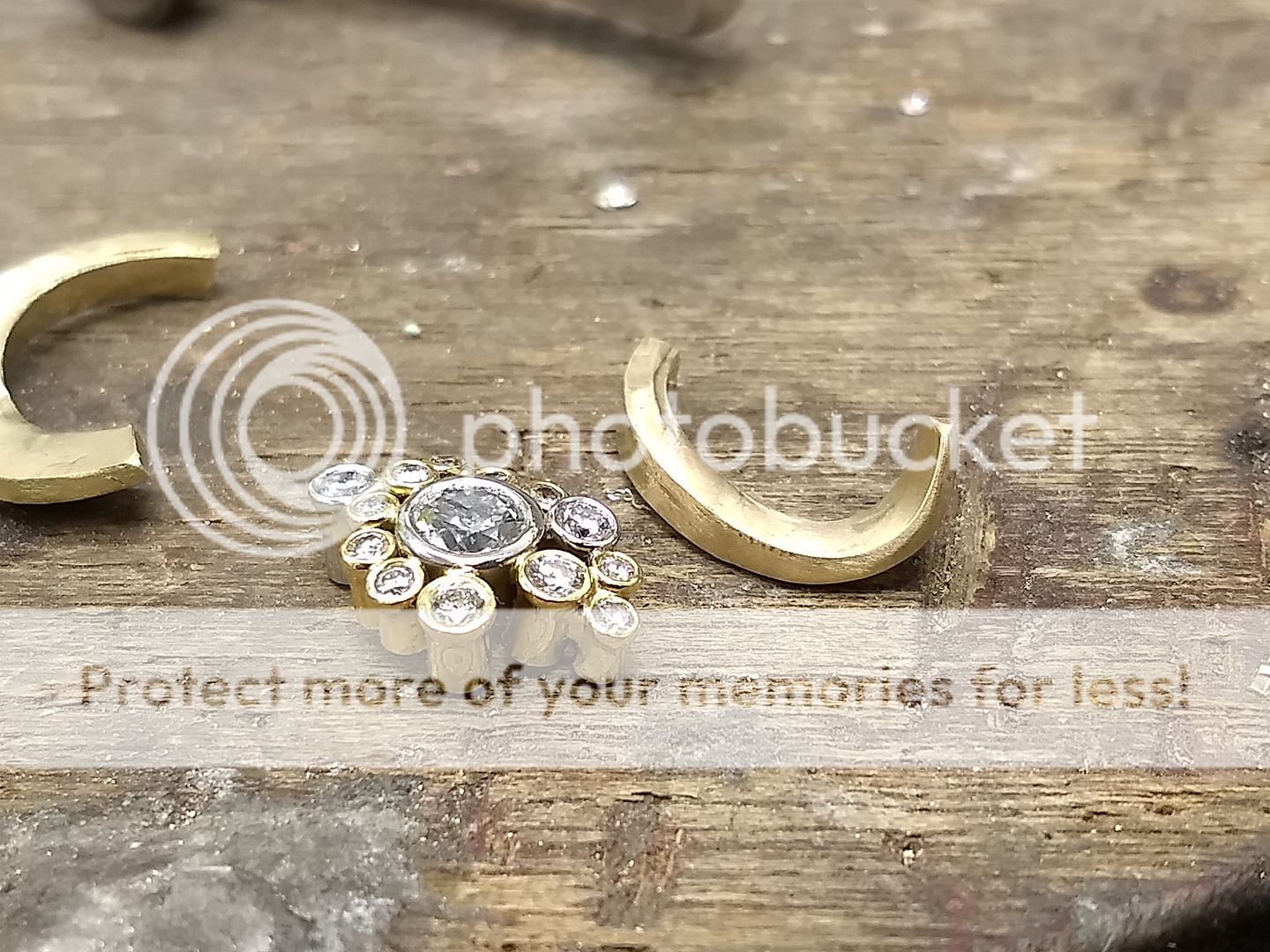
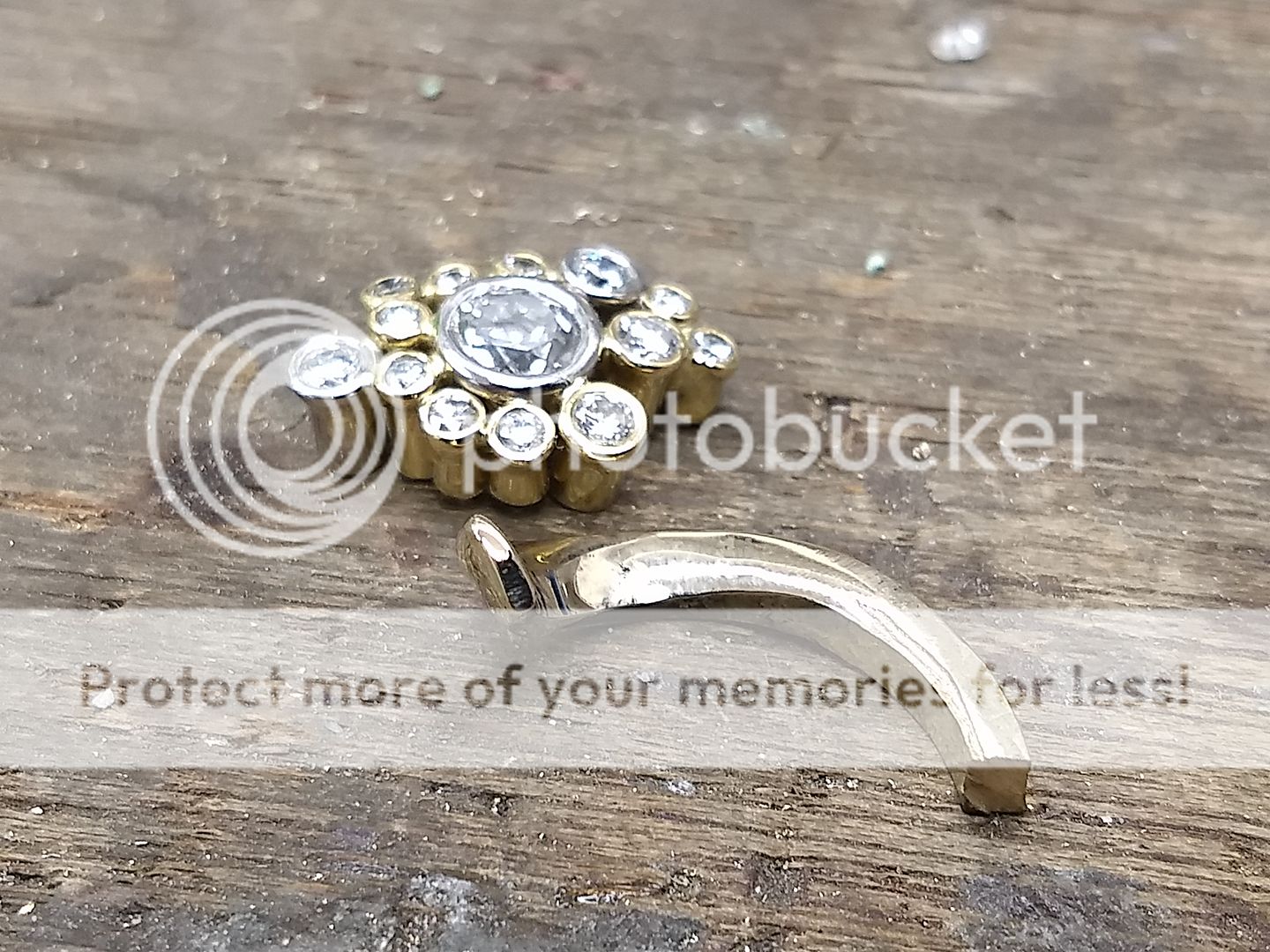
And it's then soldered in place:
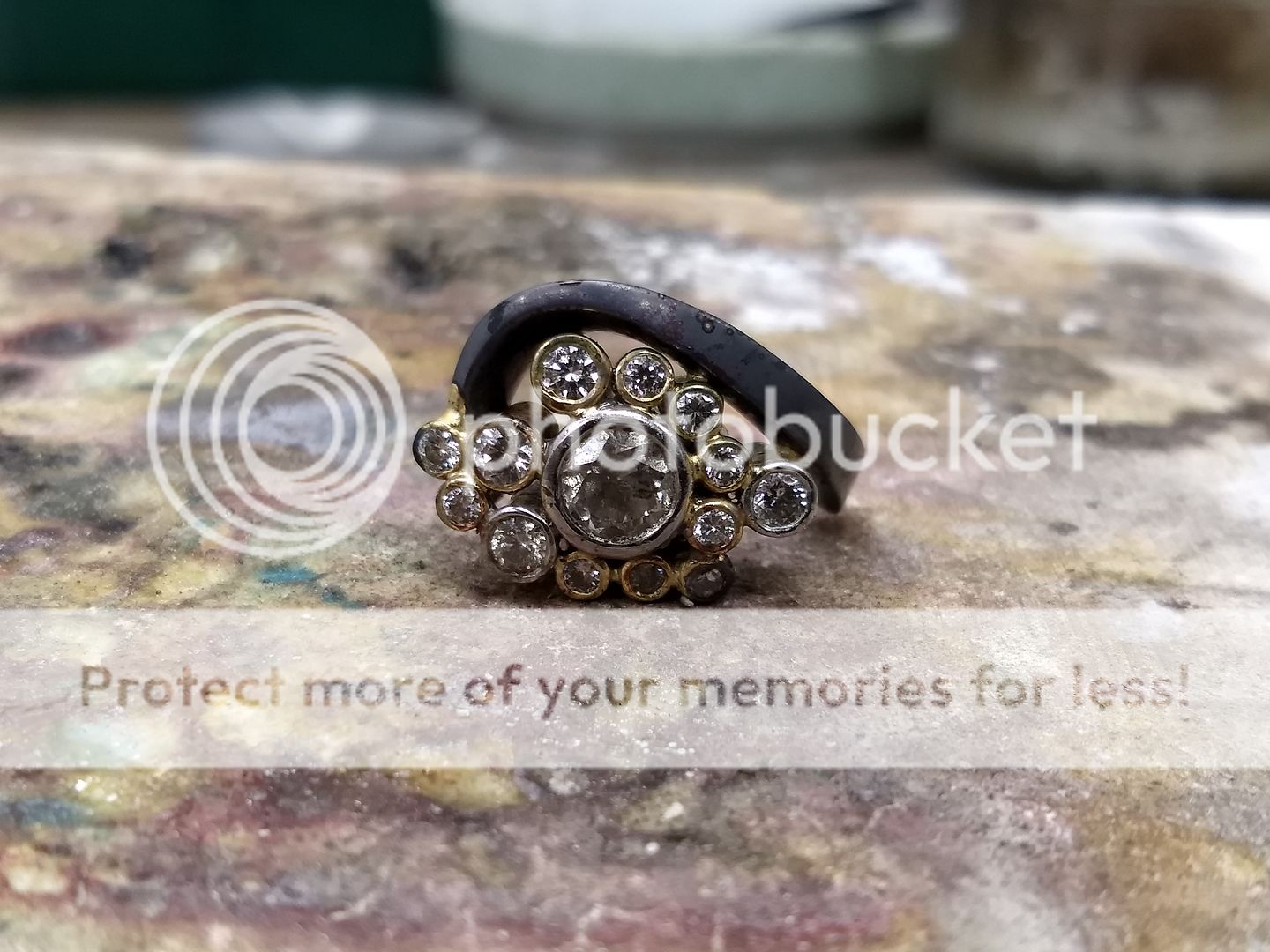
Shoulder number 2 is next:
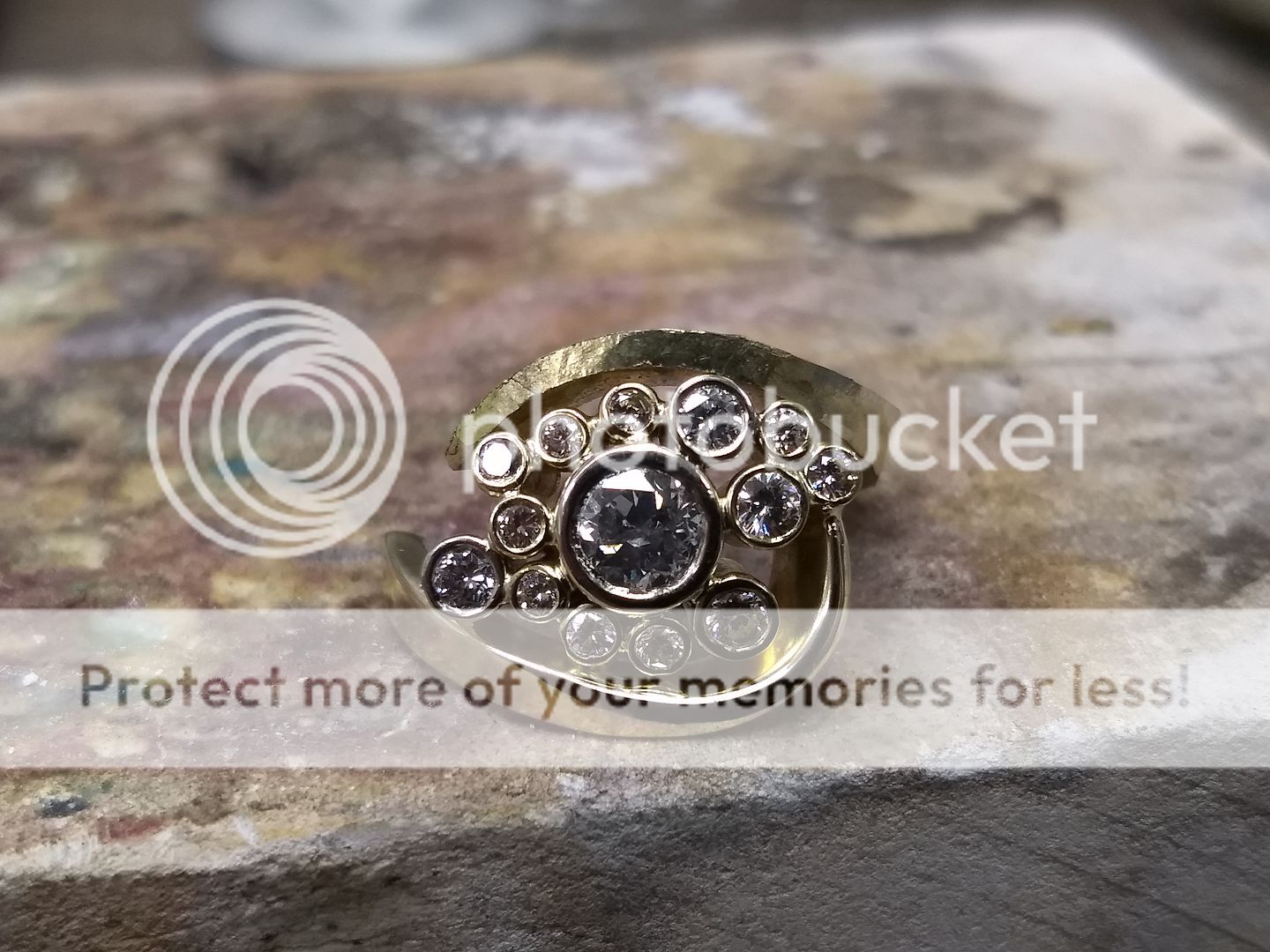
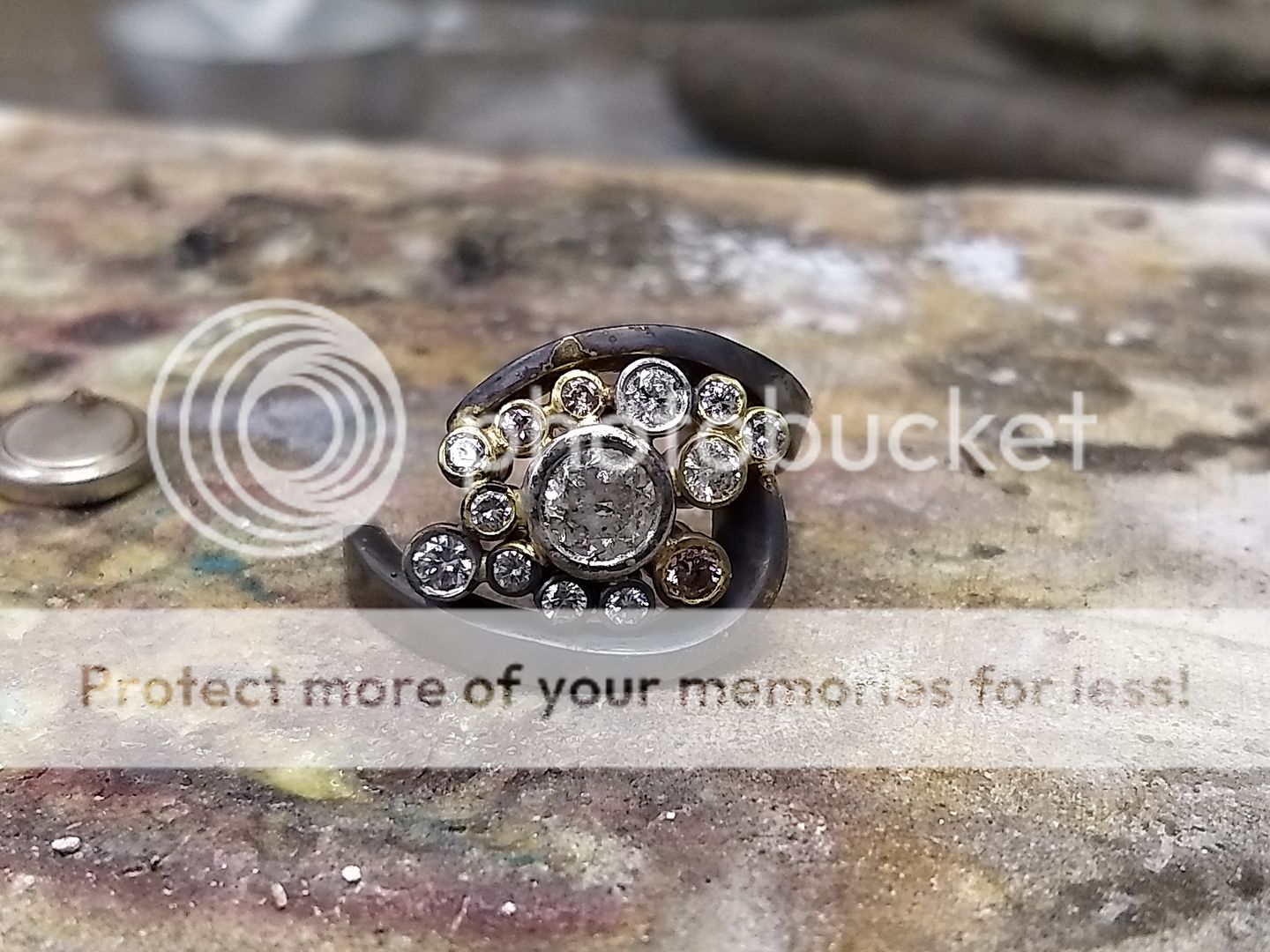
Almost looks like a ring now:
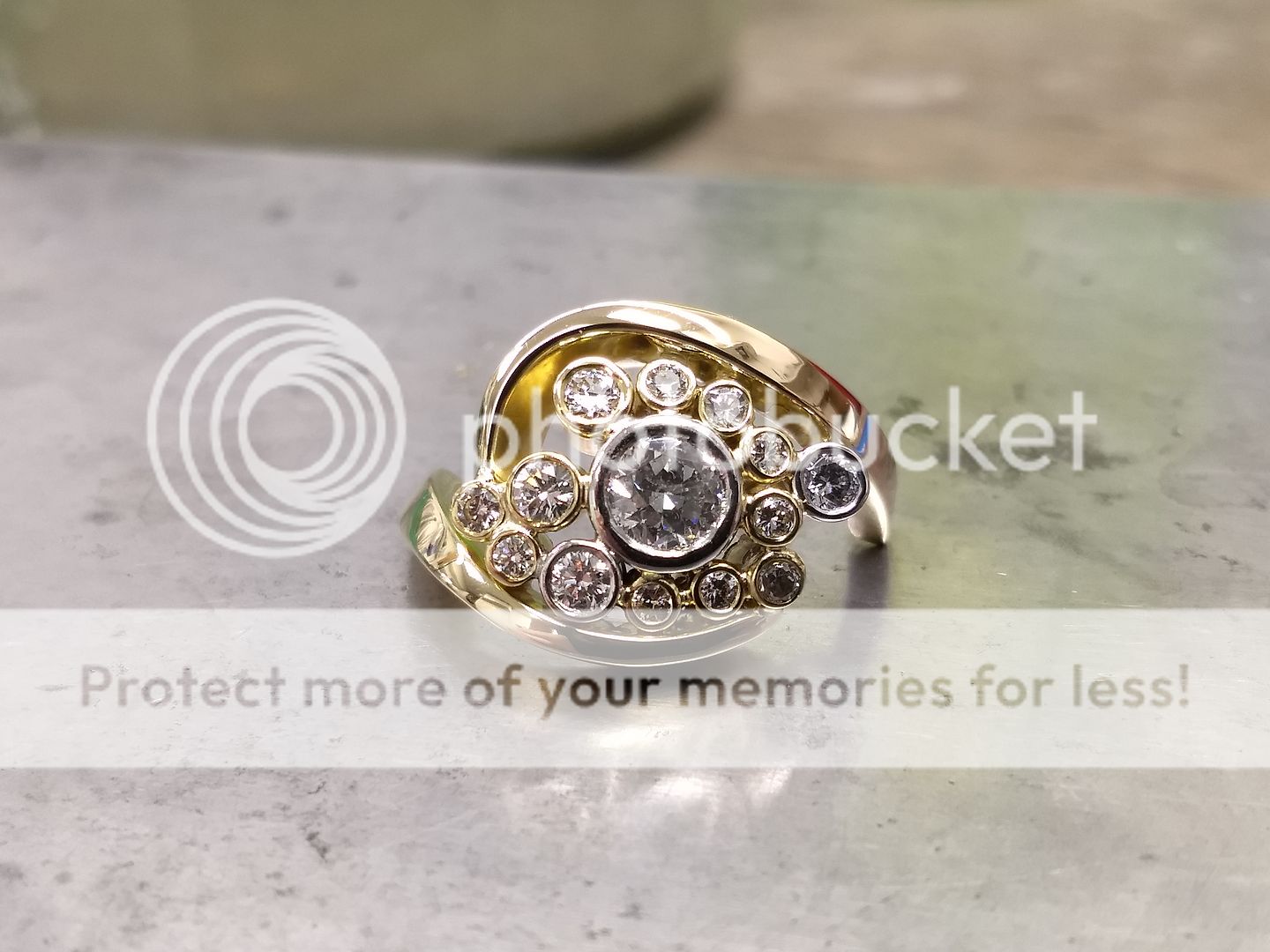
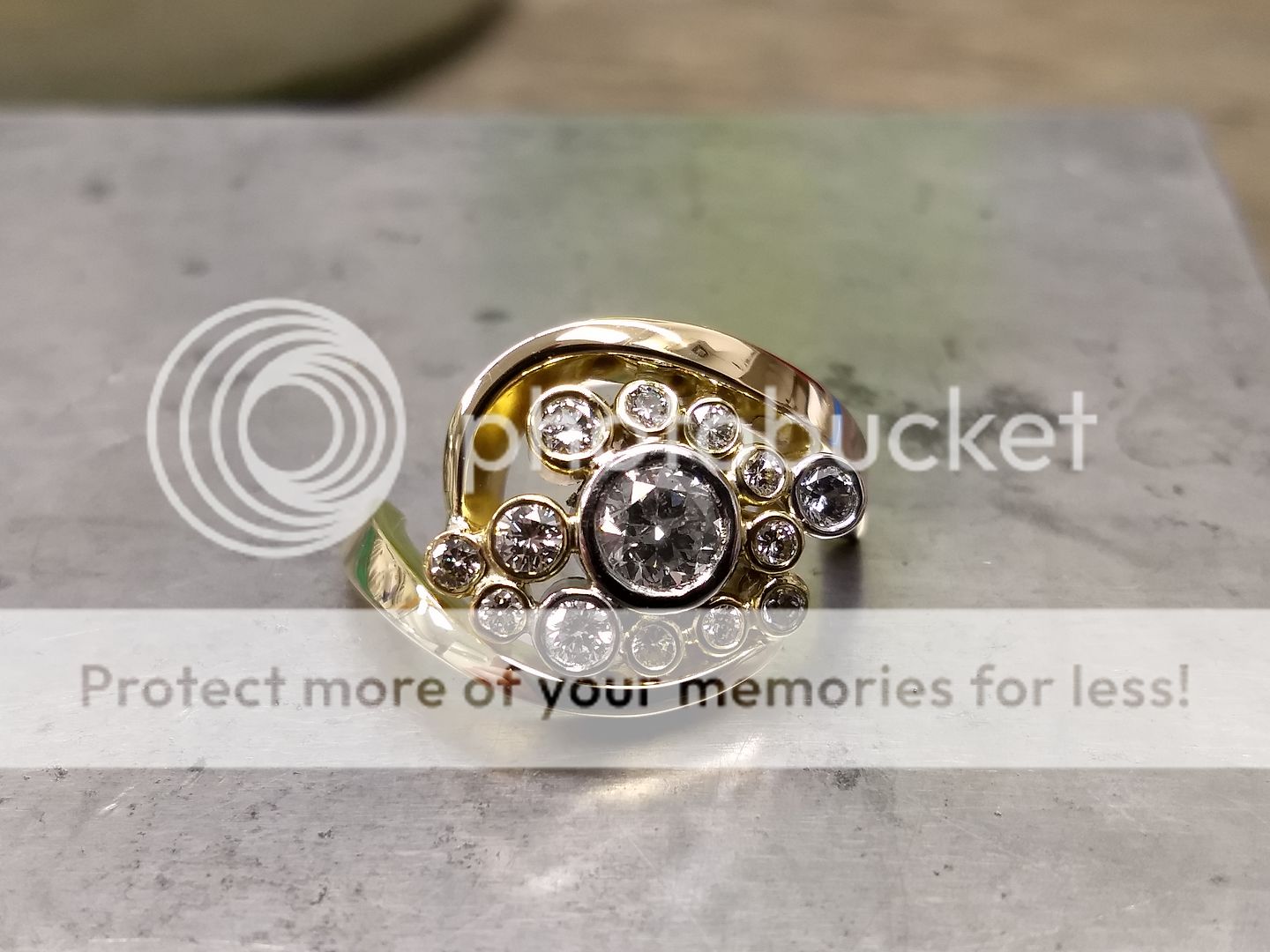
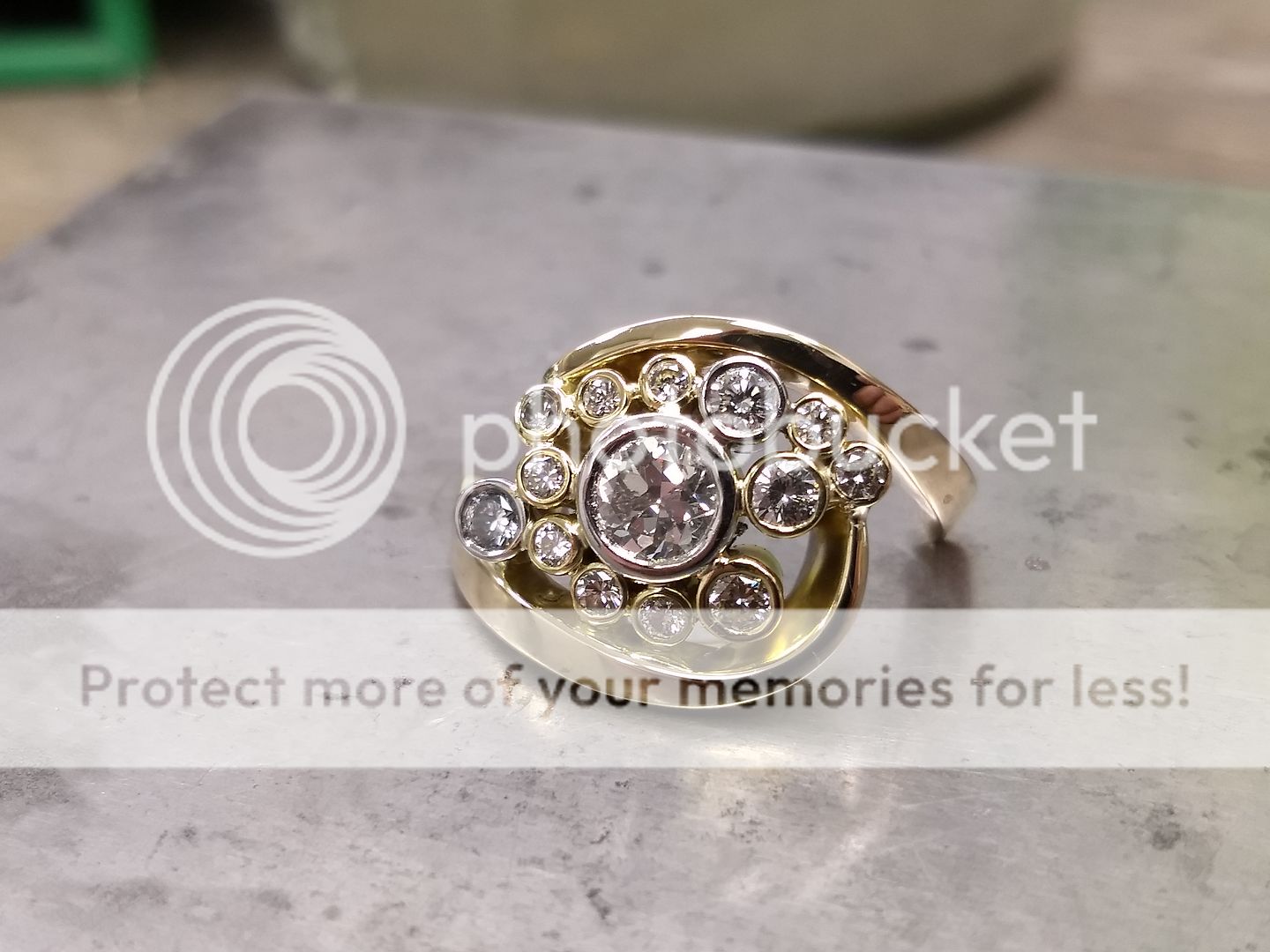
The remaining bar is then rolled out and marked with the material content.
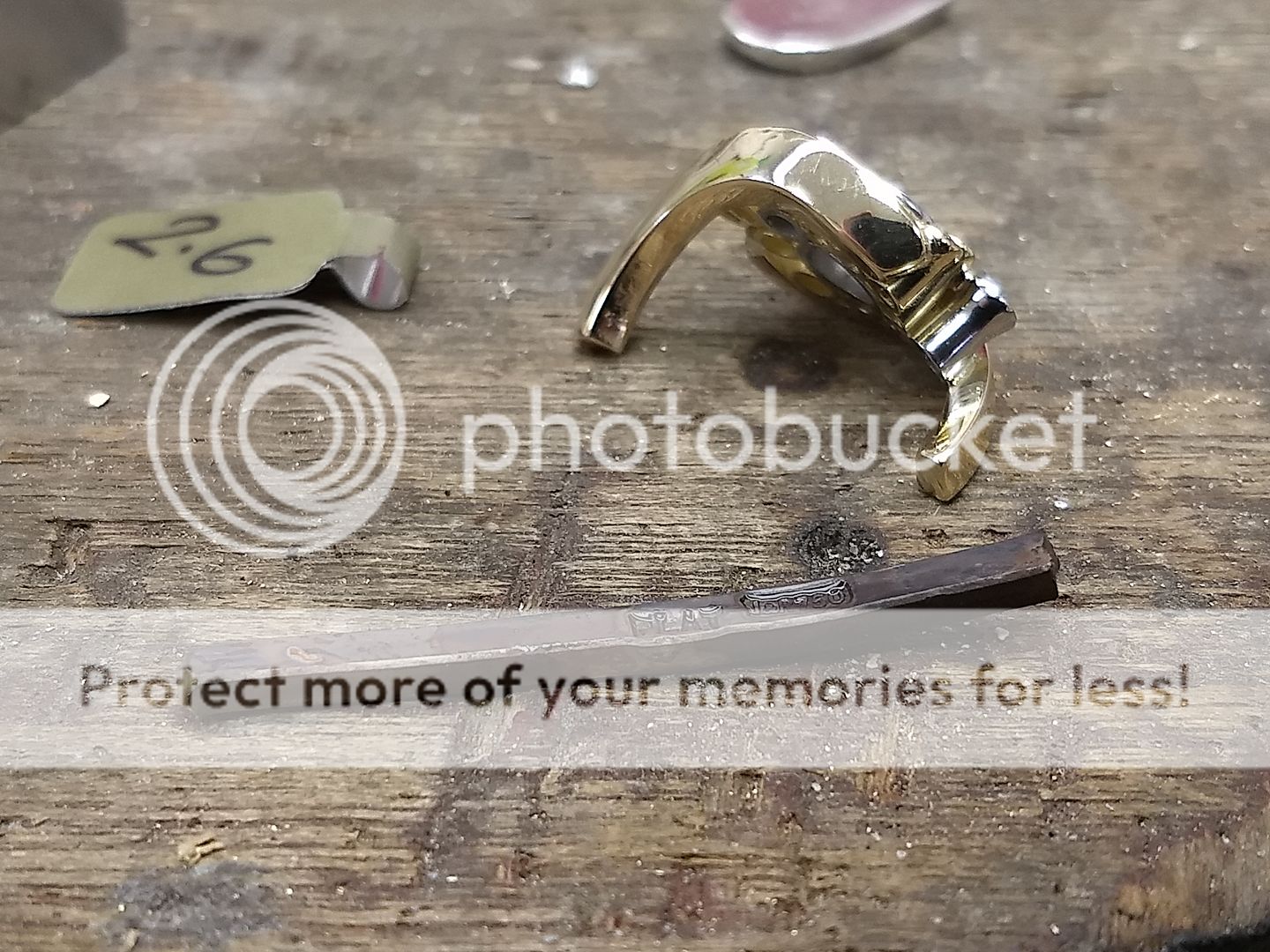
Using a digital gauge I worked out she's roughly a size N at the finger (not the knuckle) so bent the new shank to suit:
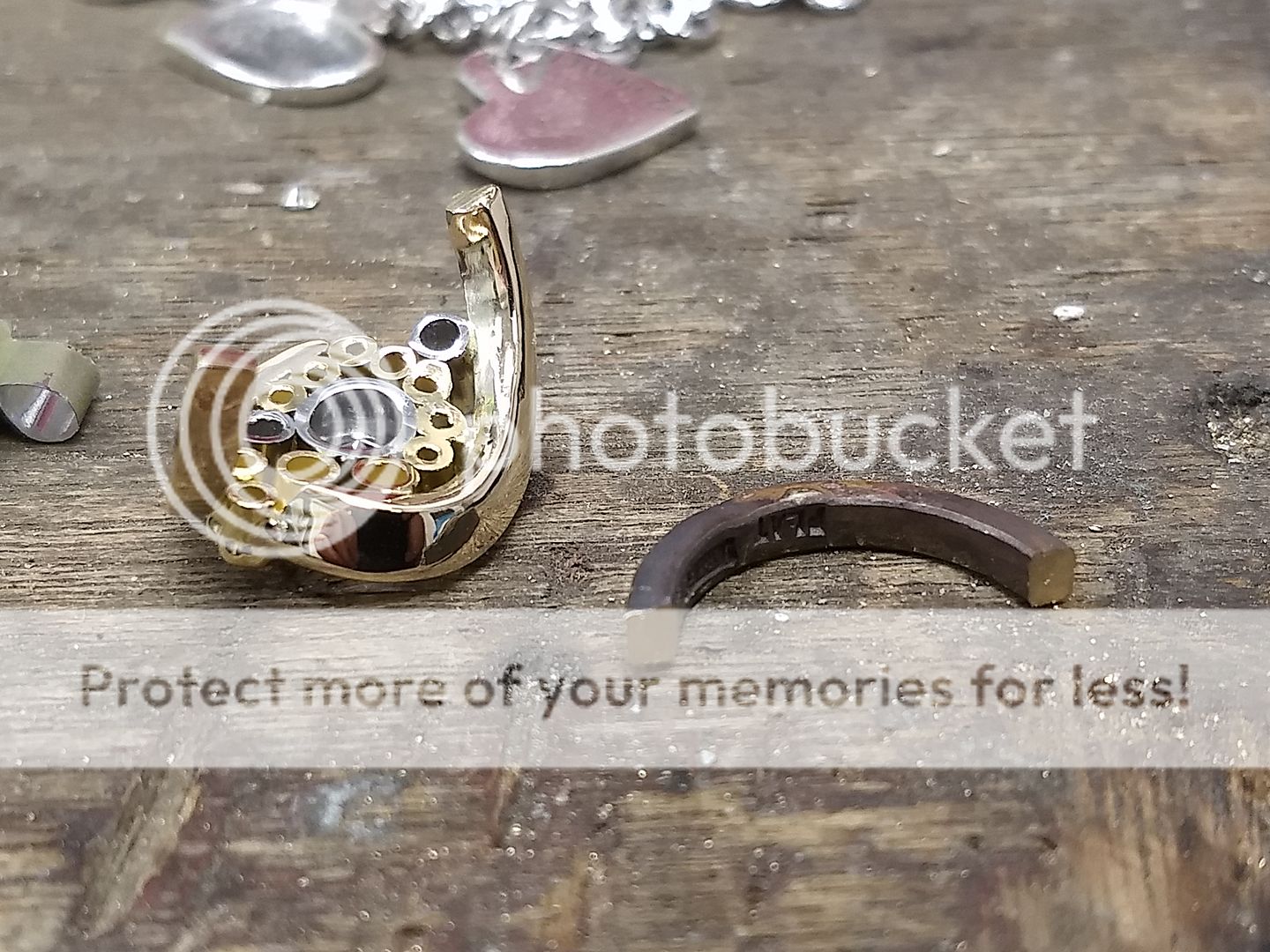
And then soldered it to the head so I could hammer it to the correct shape all round:
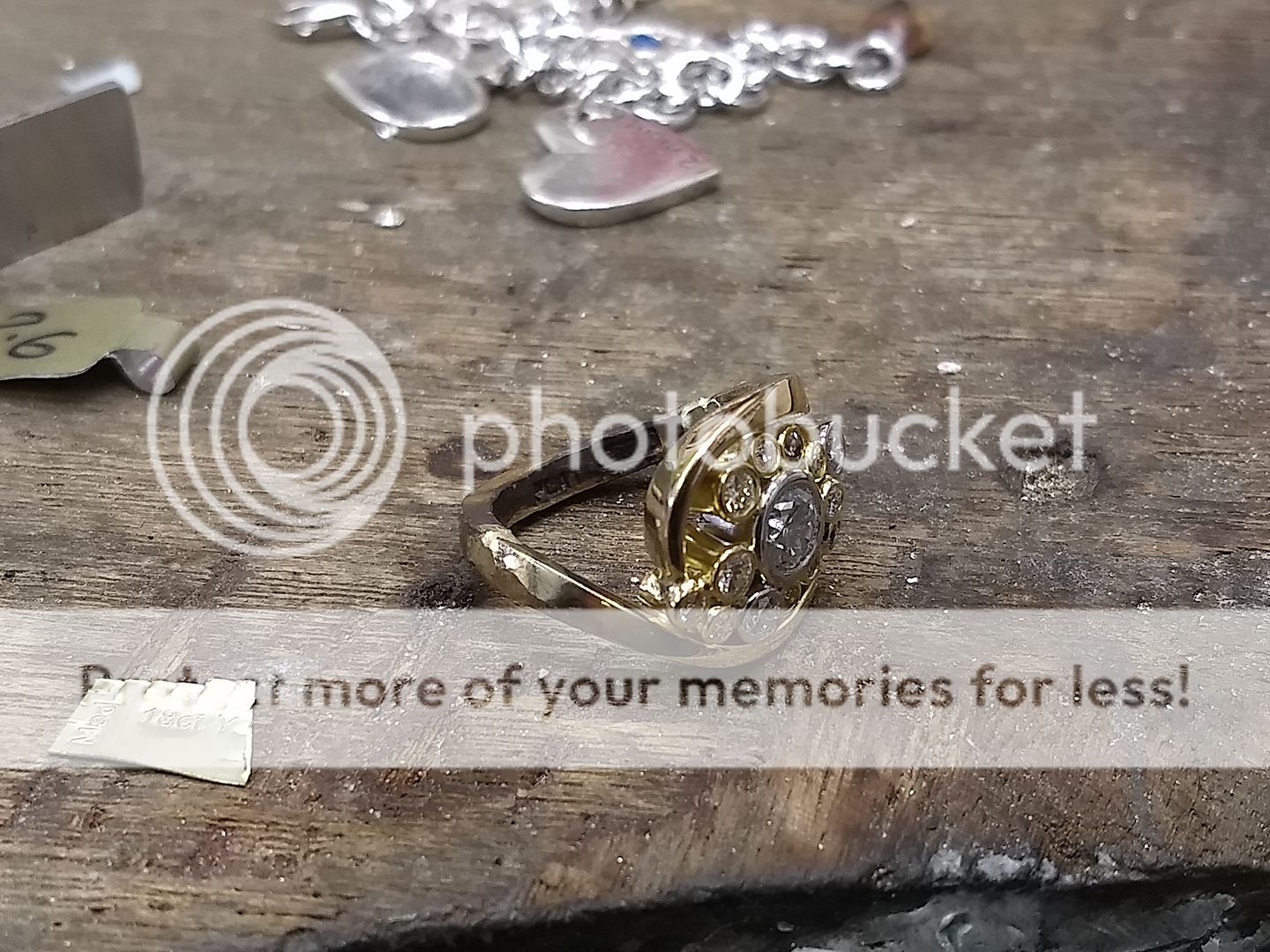
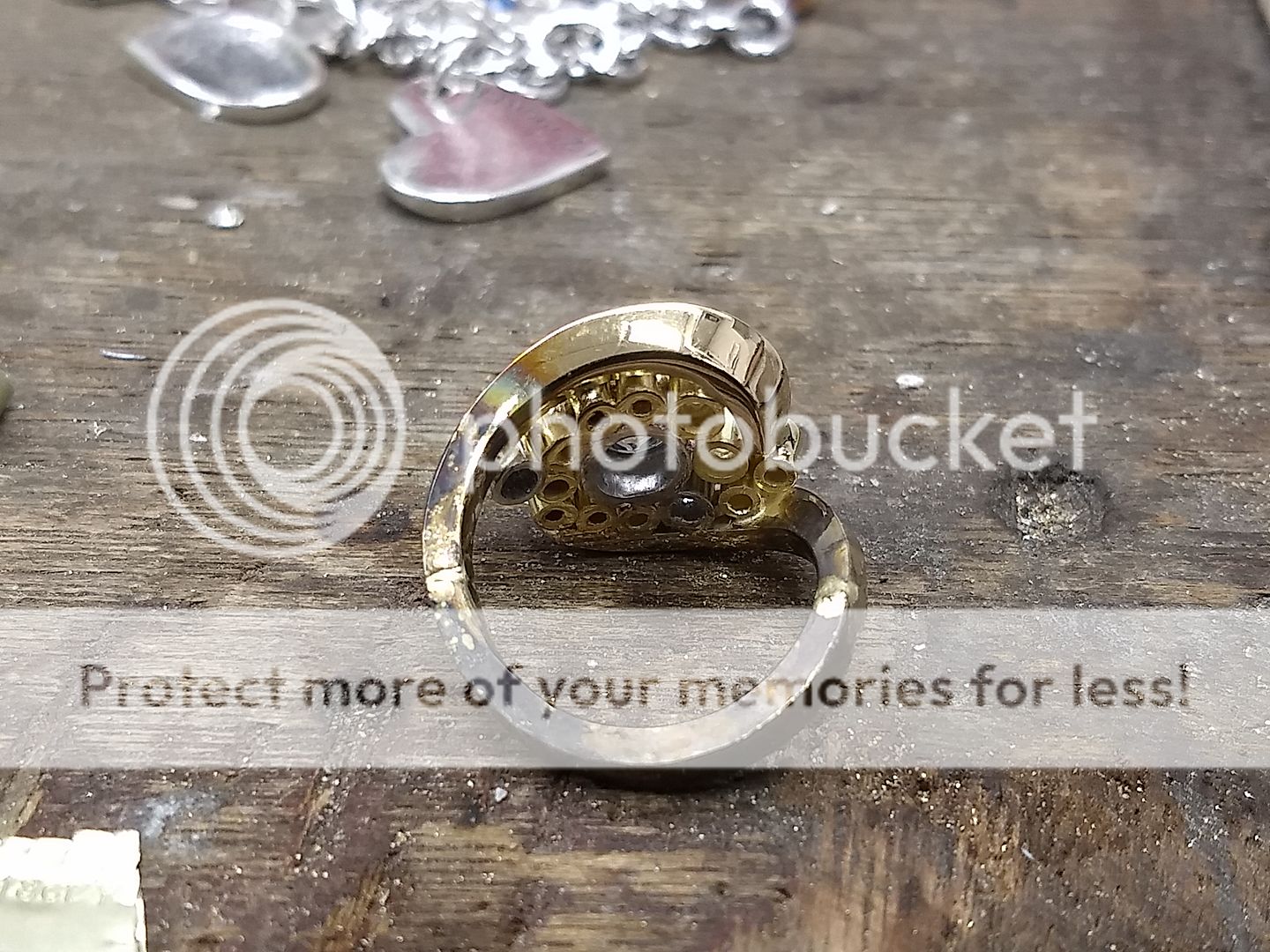
Now, obviously the ring won't go over her knuckle like this so I had to spend a while working out how the hell I was going to get it to fit. The clear answer was to hinge it, but how do we then secure the other end and make it durable?? Here's the hinge first:
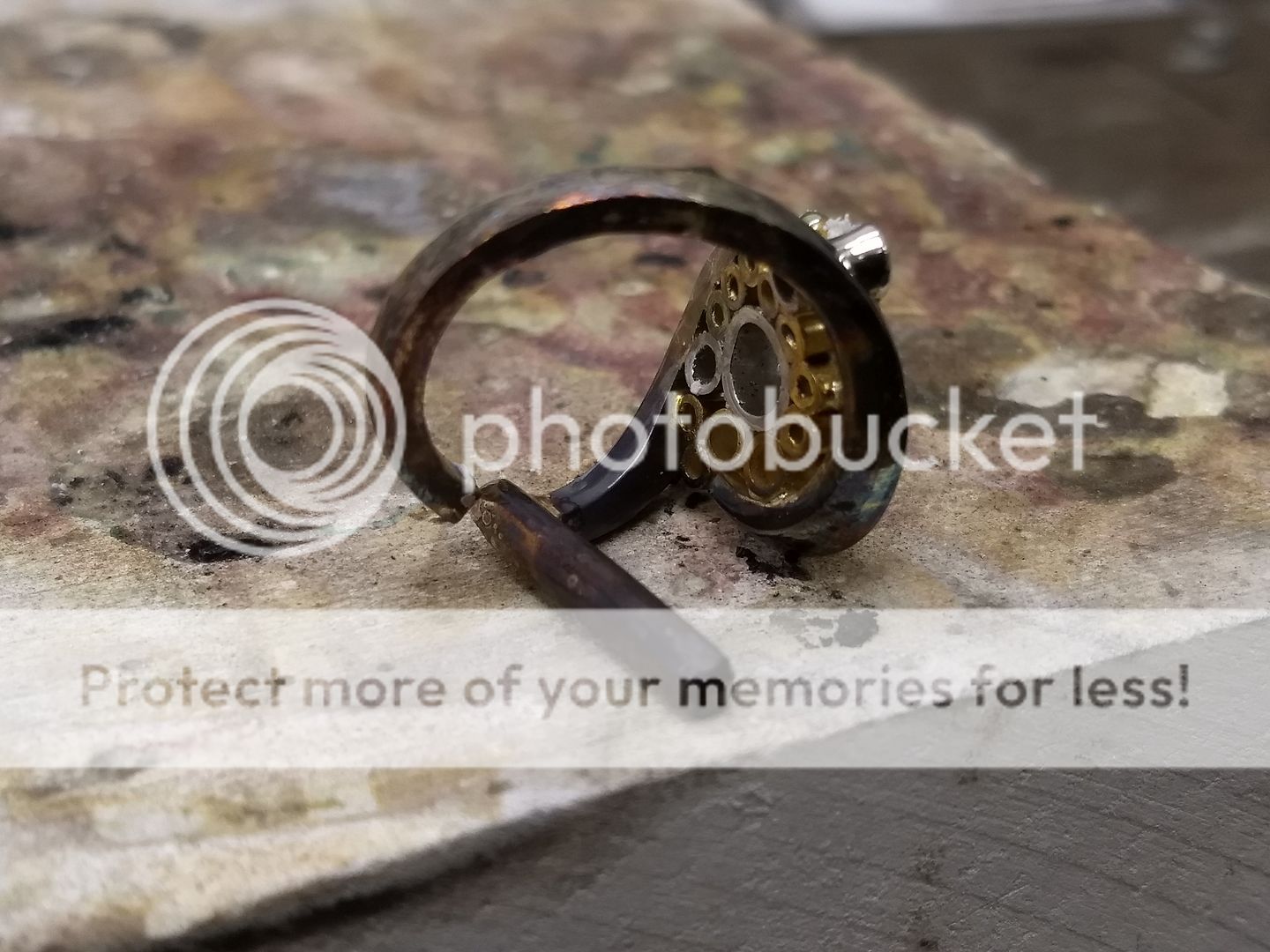
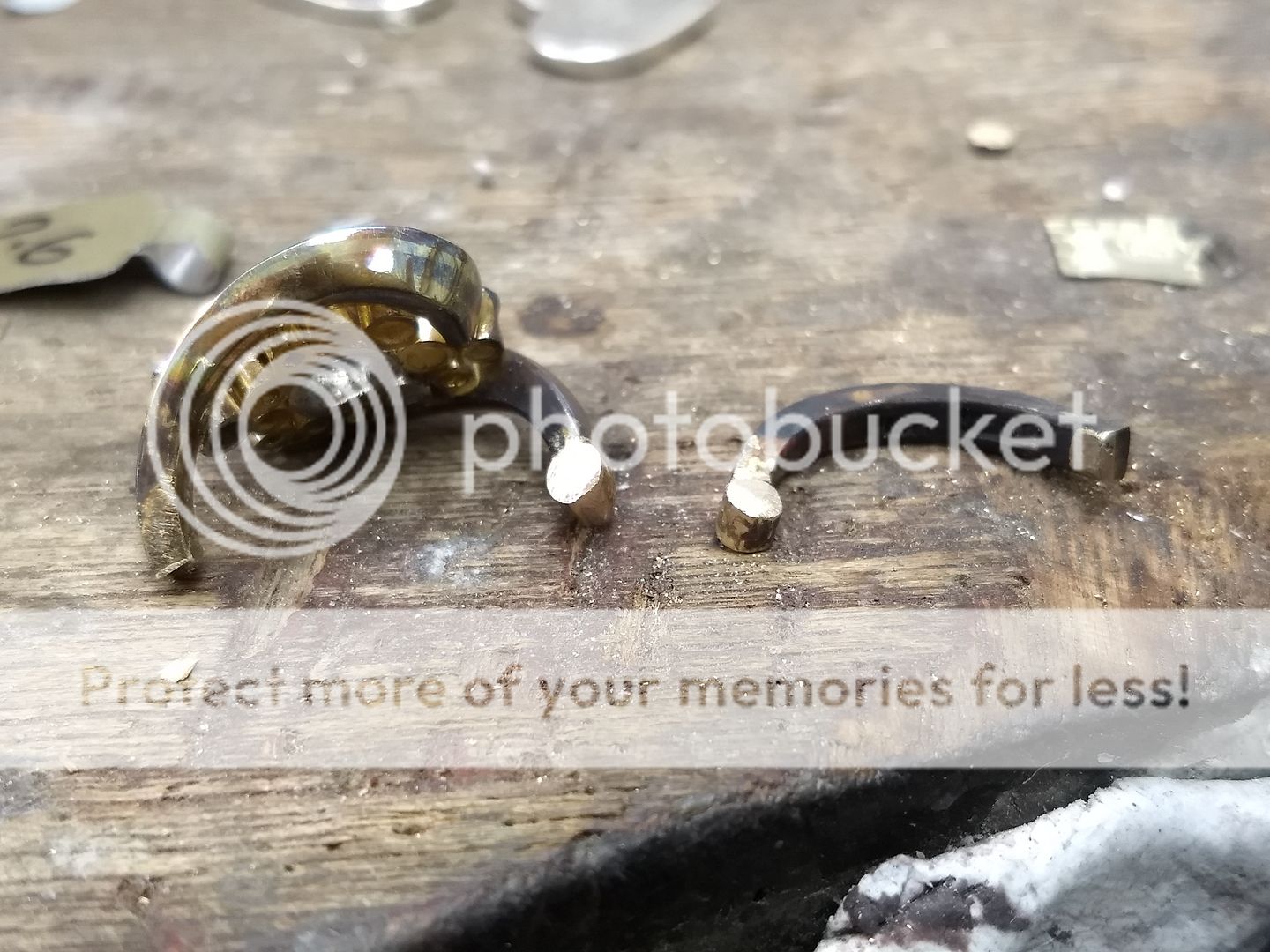
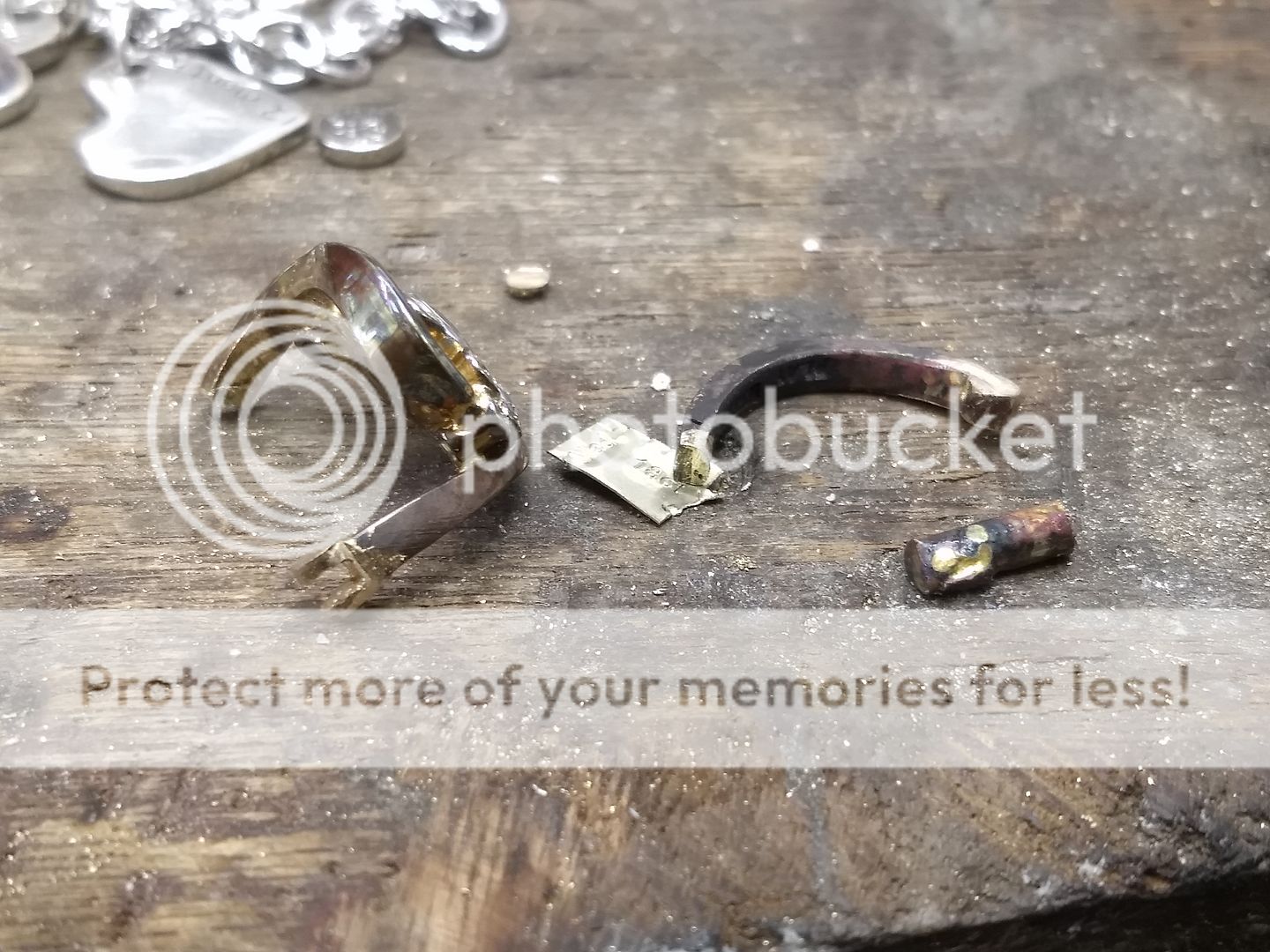
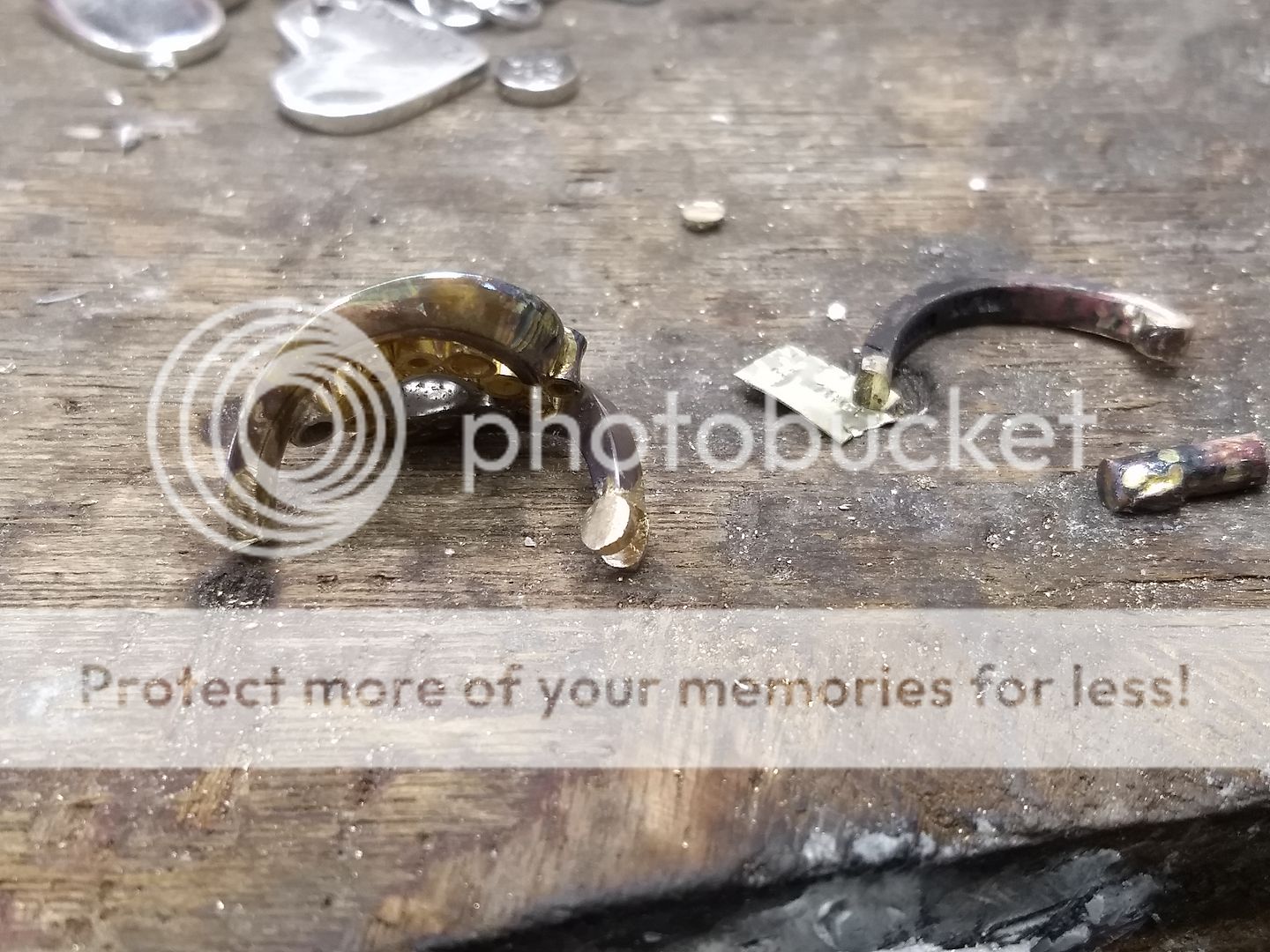
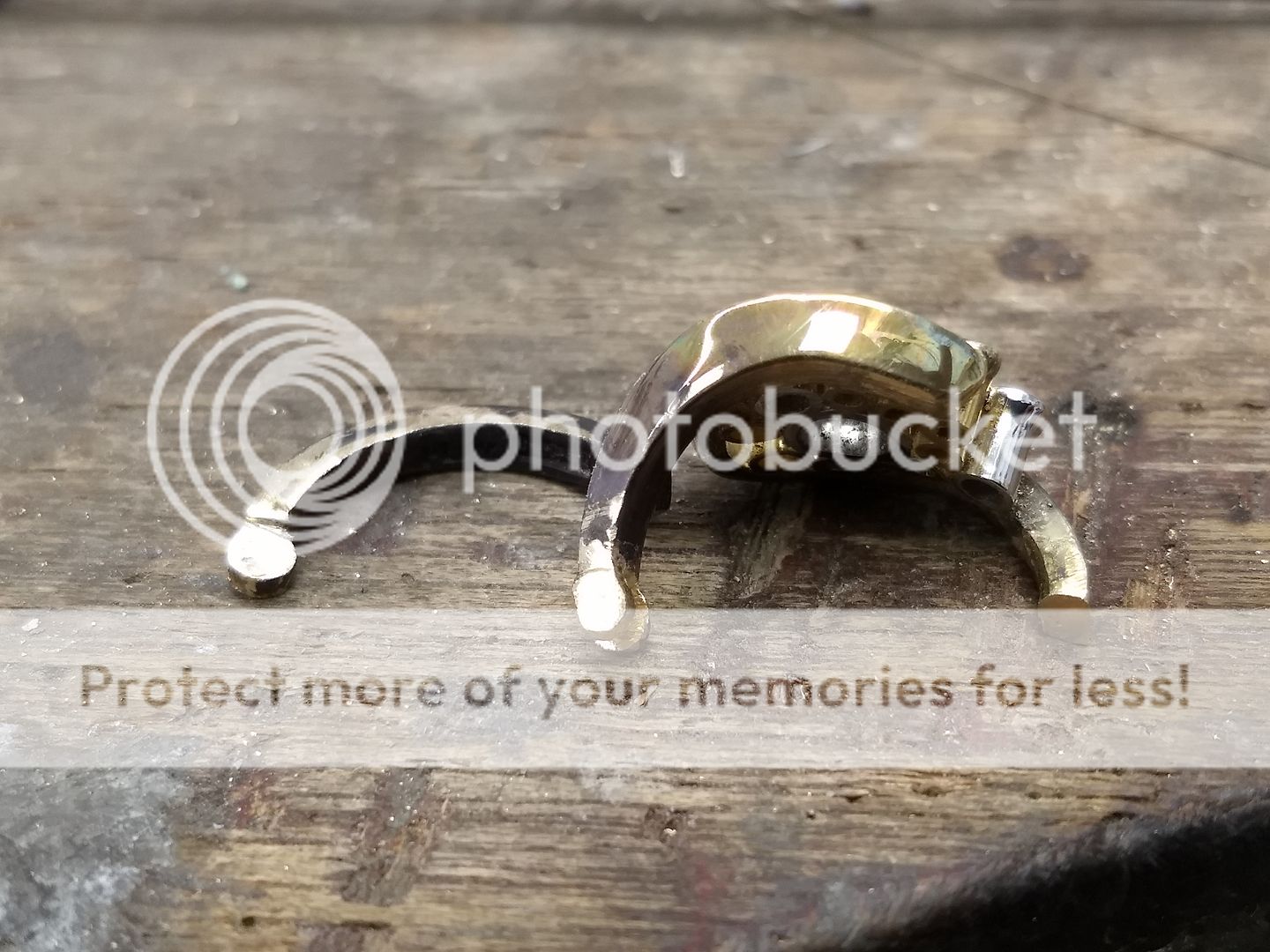
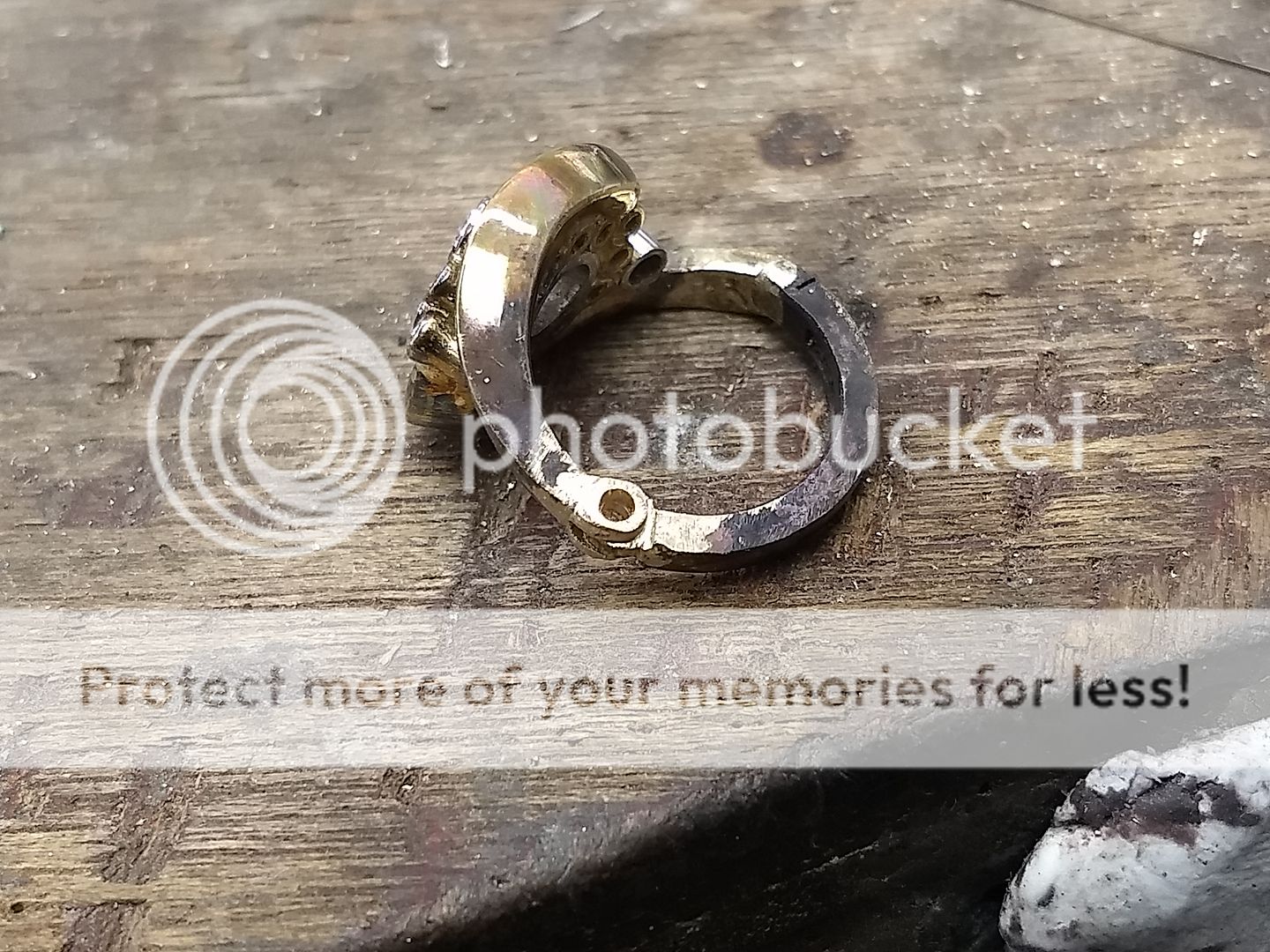
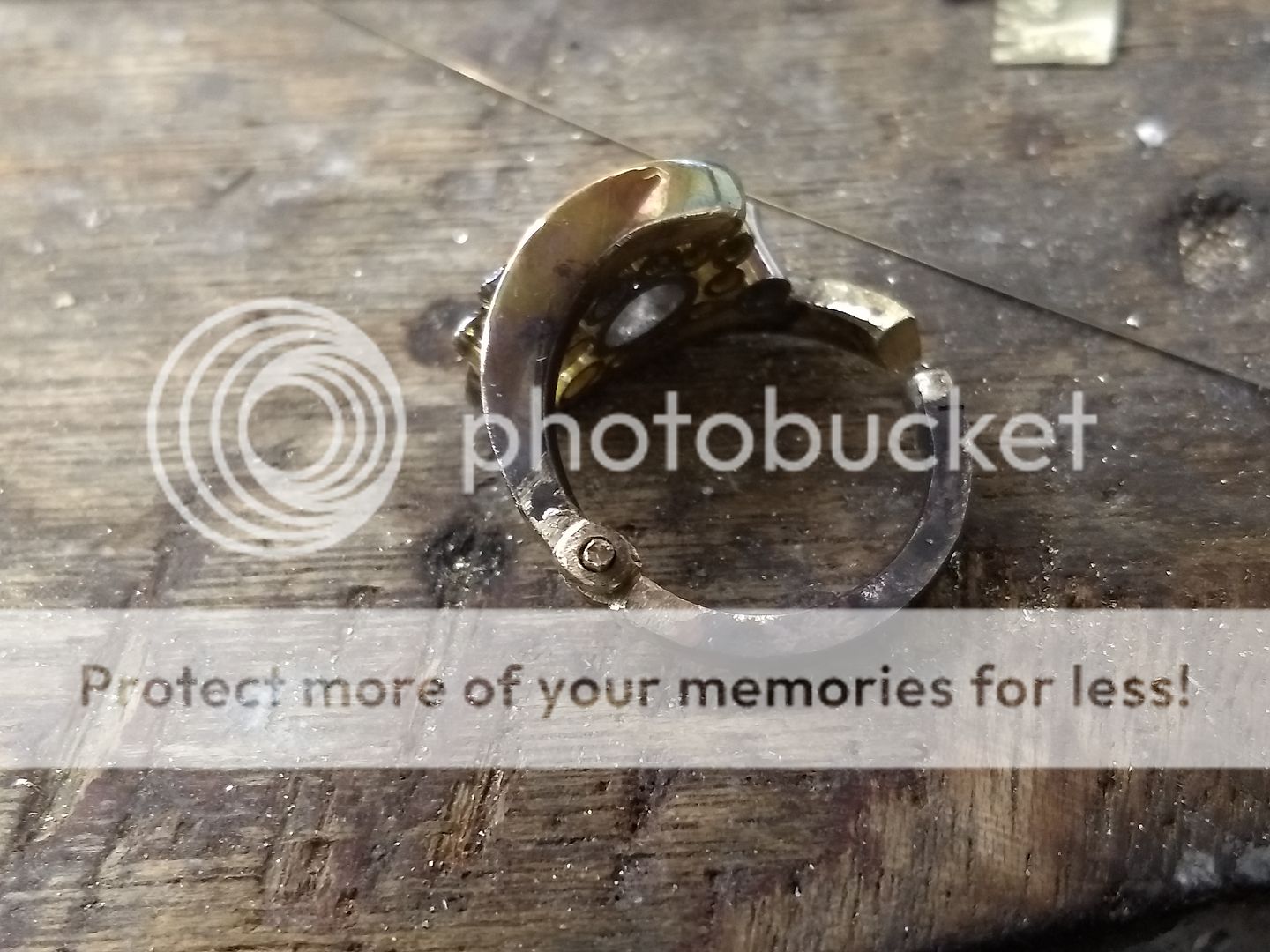
So, with the hinge fitted and functional what do we do about the other end? The shank is curved and doesn't come together in a way that a catch would work.... not reliably anyway. The only way to do it without worrying is to screw it shut. The solution: Make another hinge at the other end, but an angled one to allow for the way it closes and then instead of a hinge pin I'll use a grub screw to secure it. At this point it's trial and error but it's my best hope
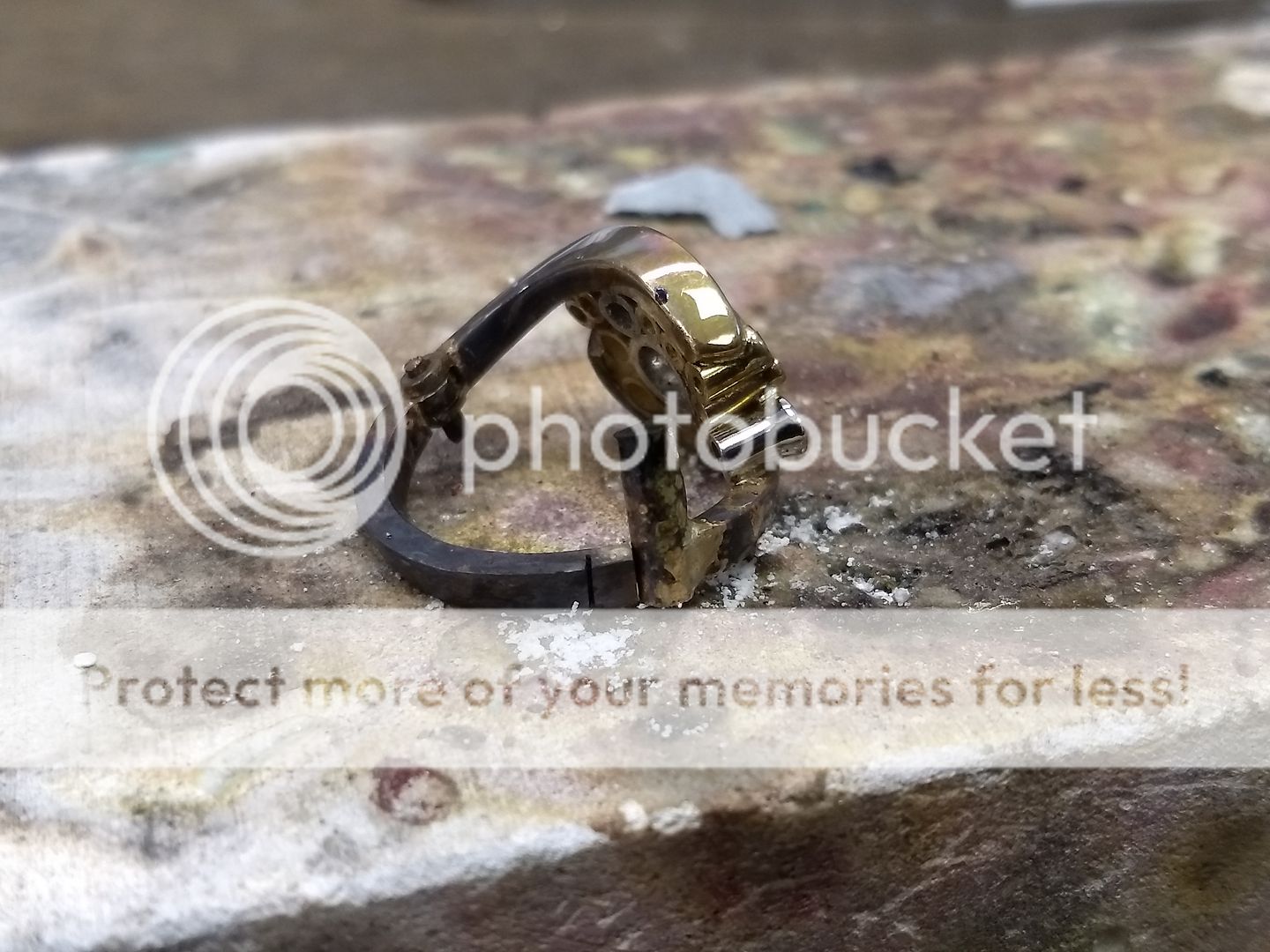
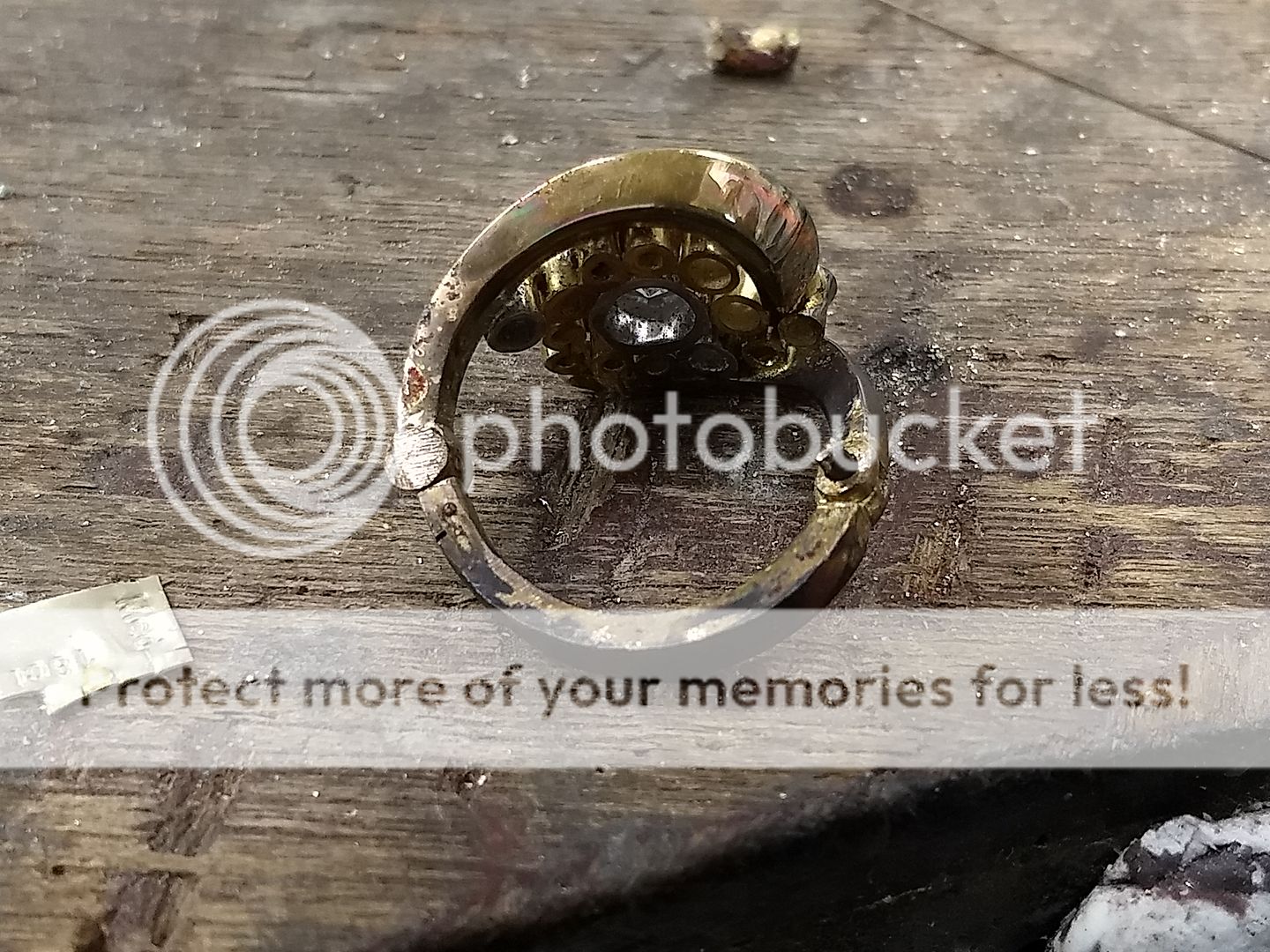
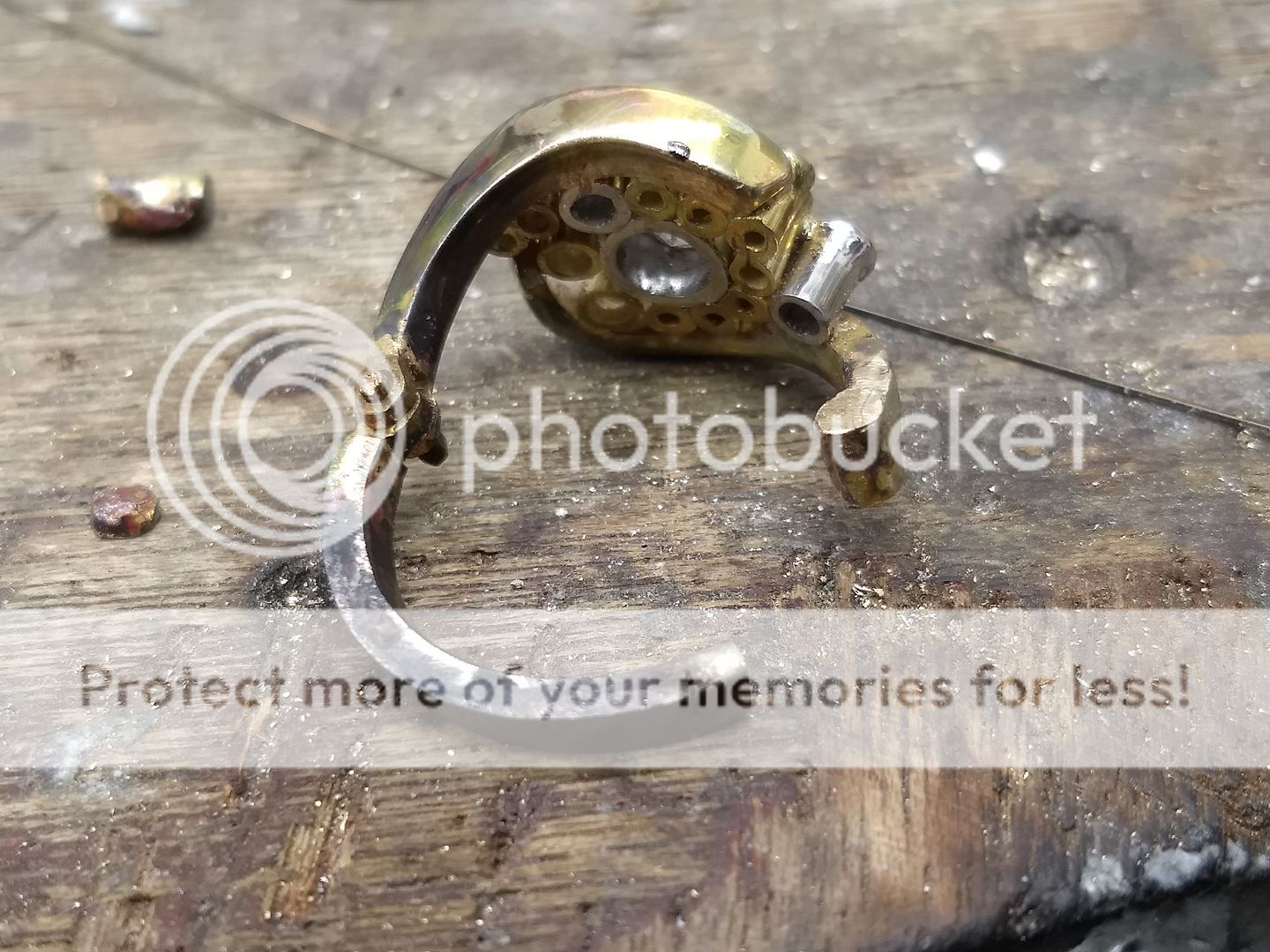
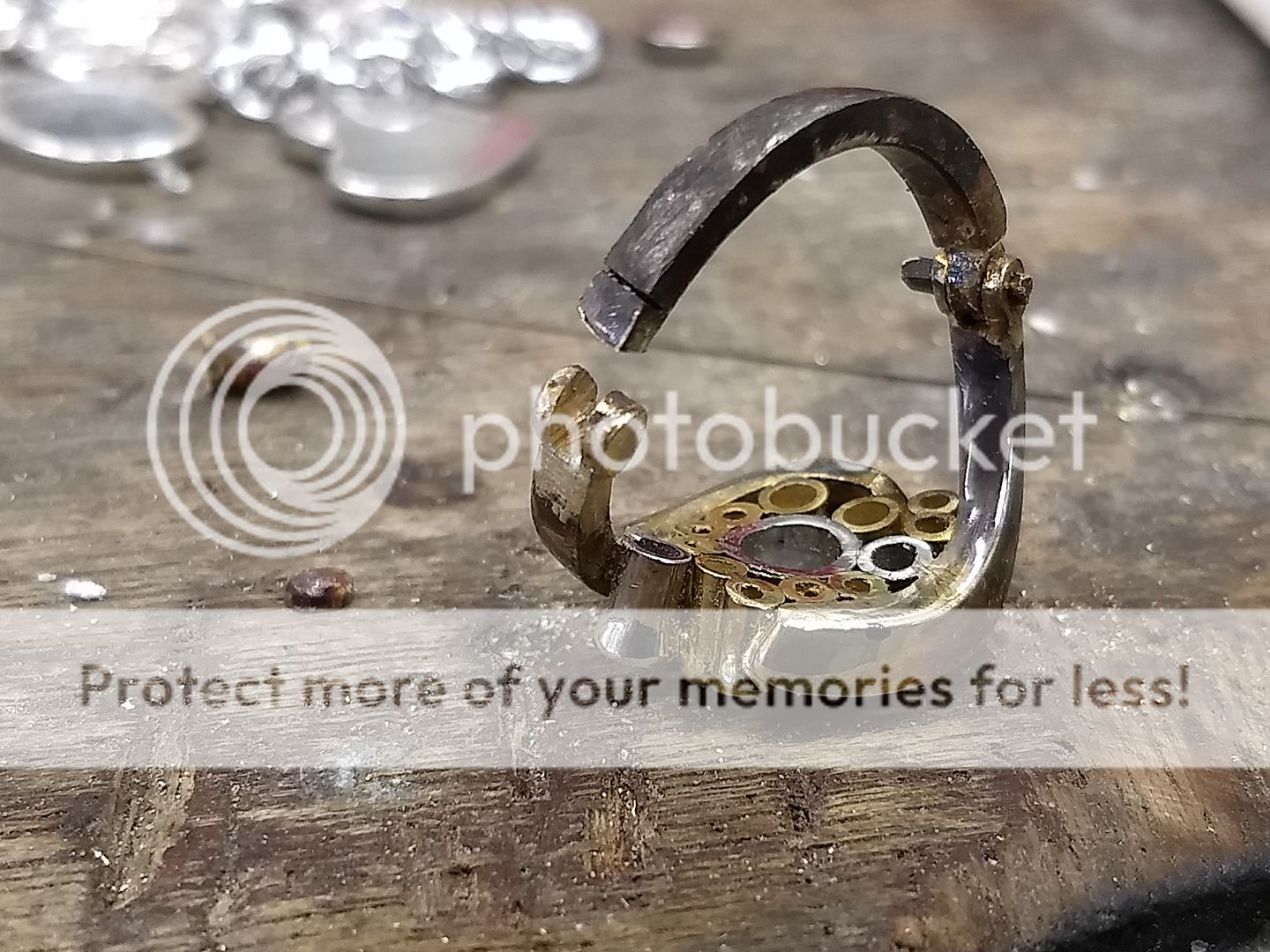
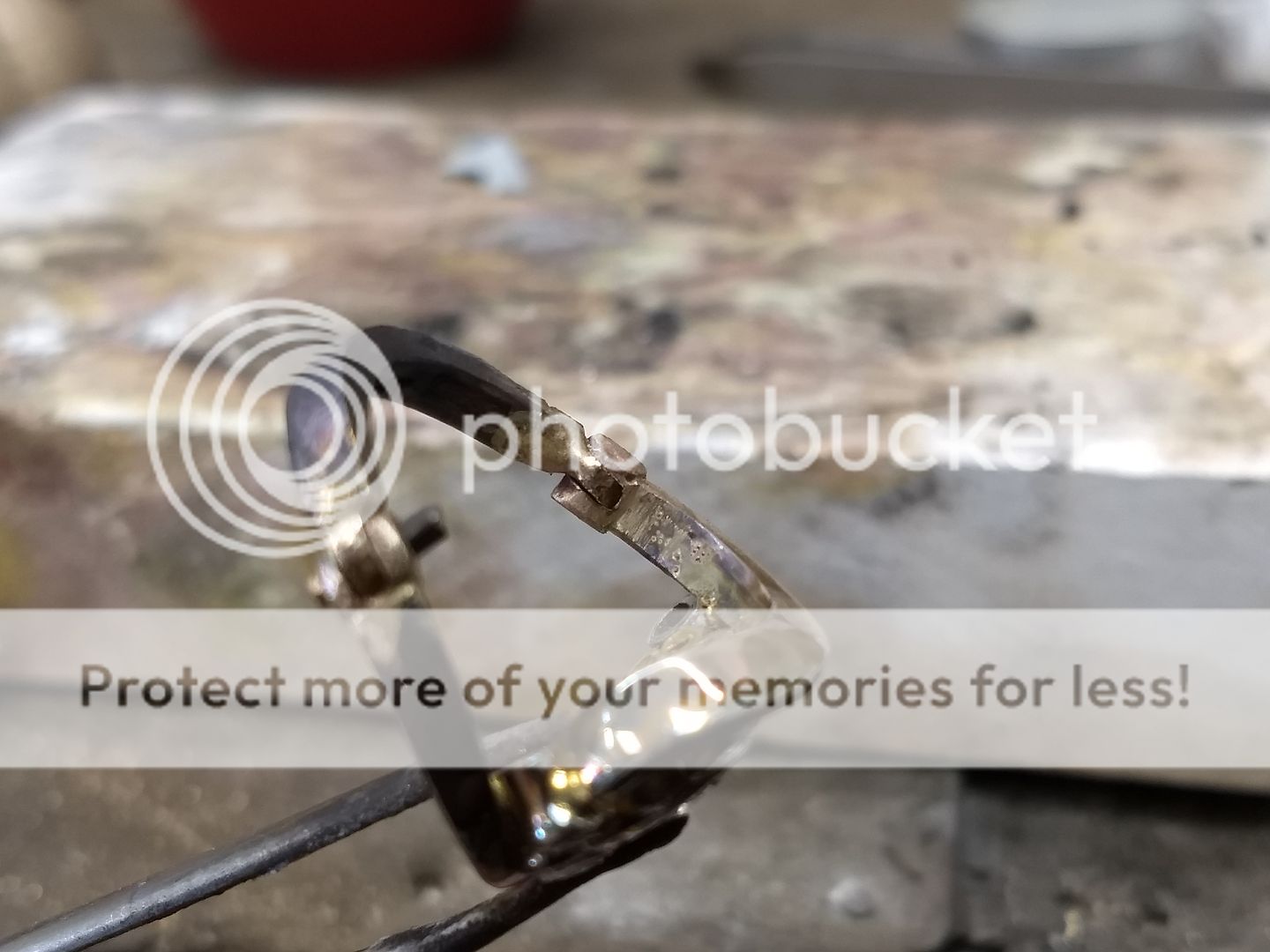
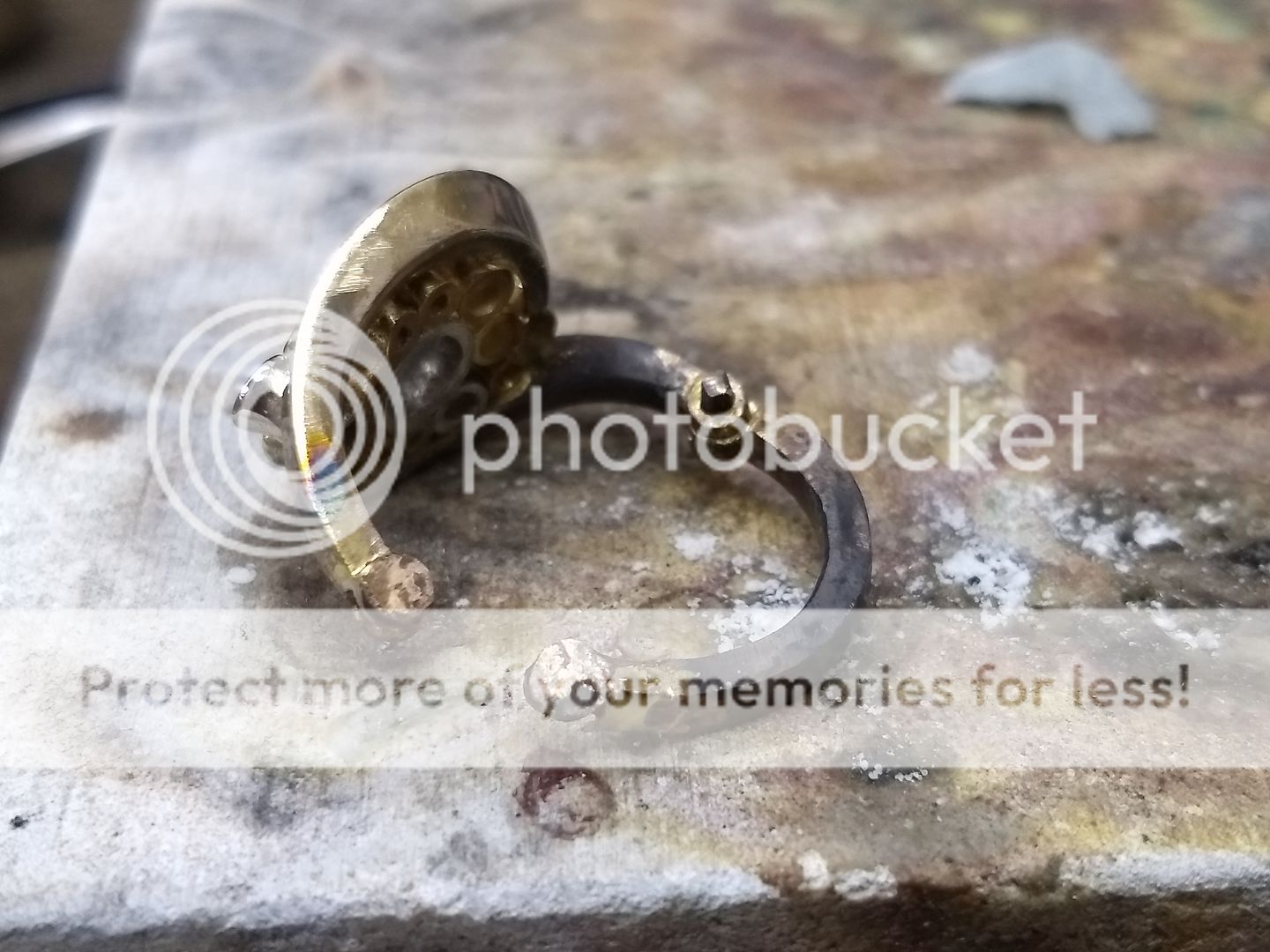
The hole is drilled only 4/5 the way through to stop the screw coming out.
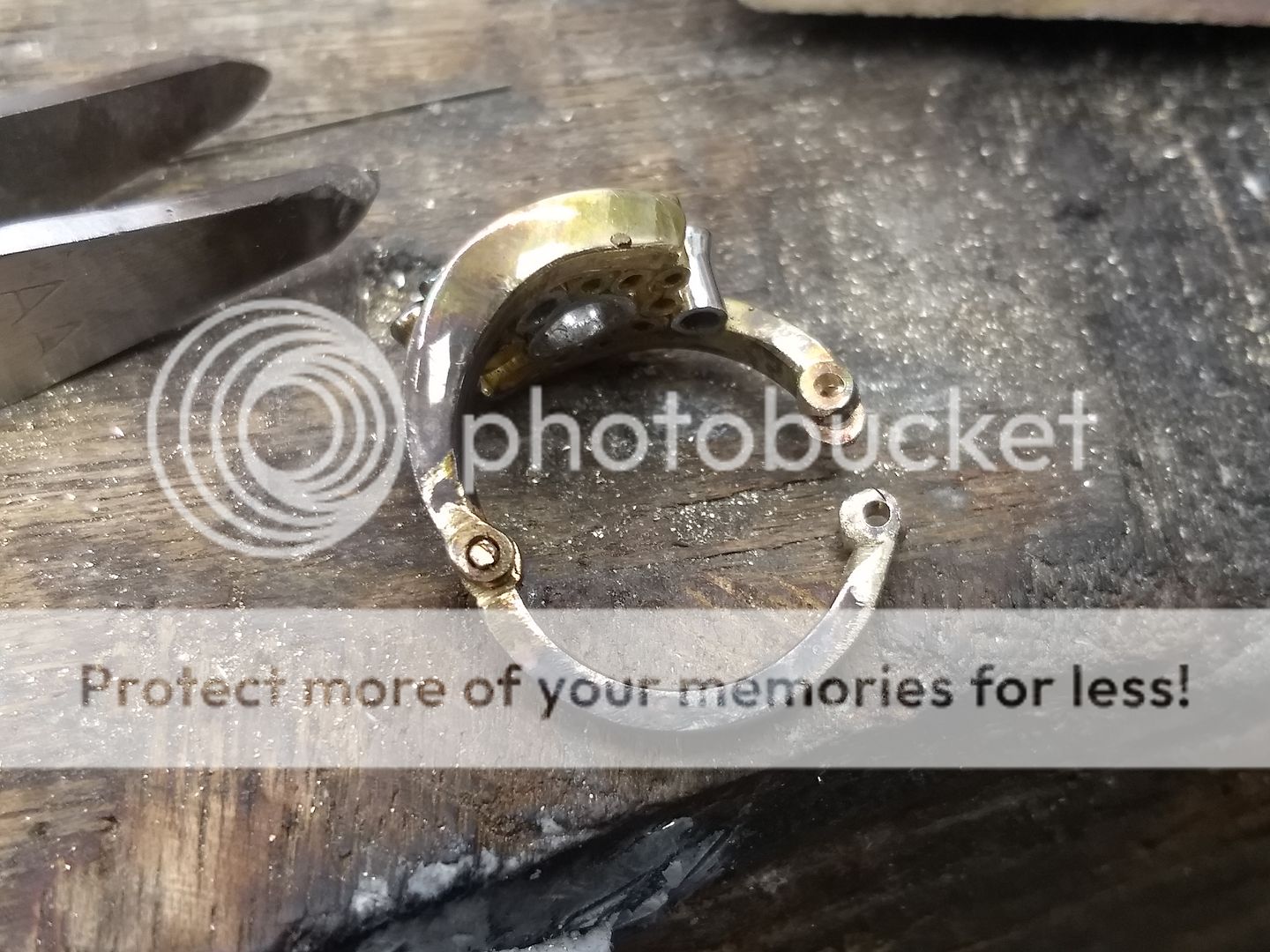
Test fit:
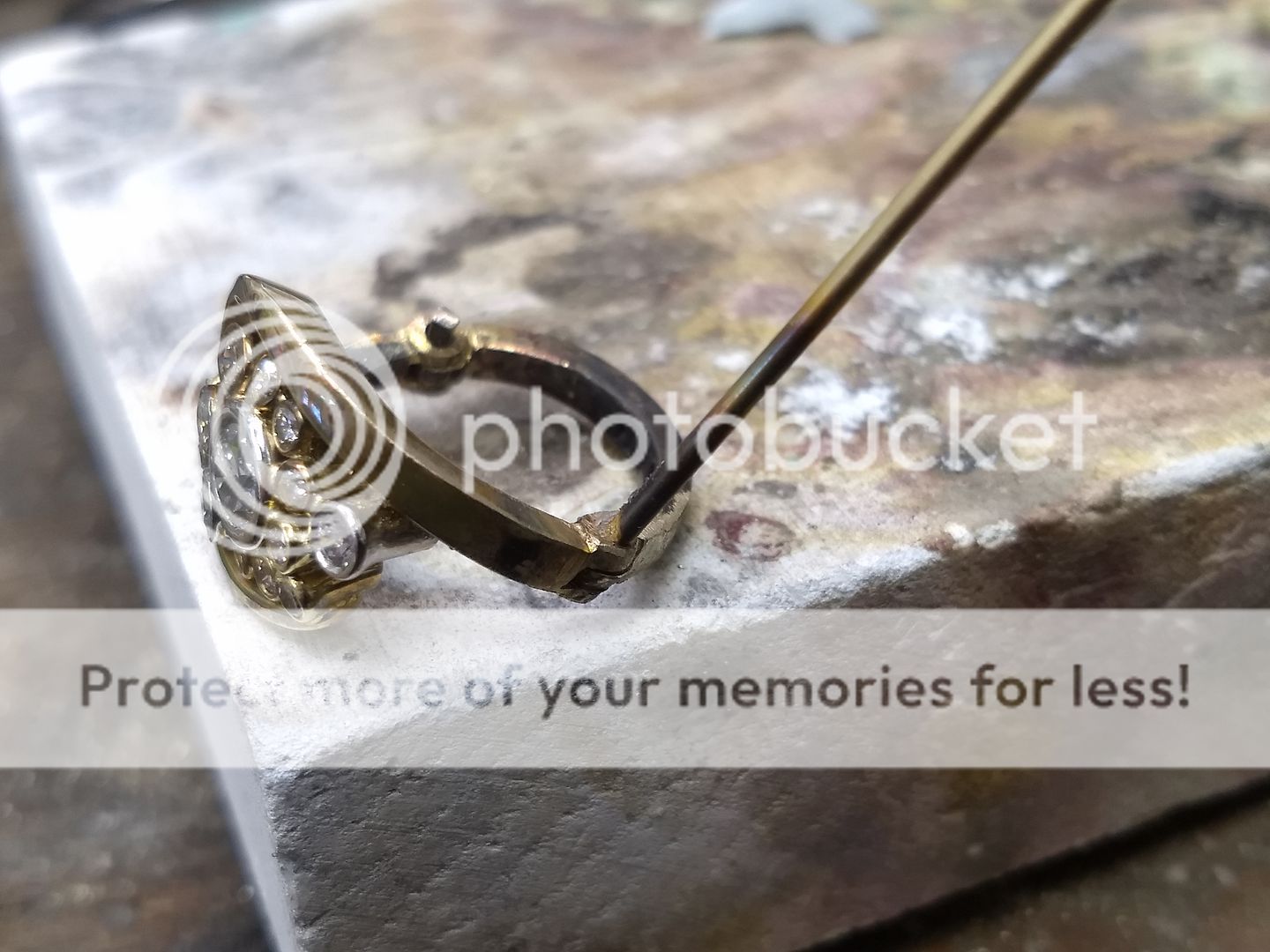
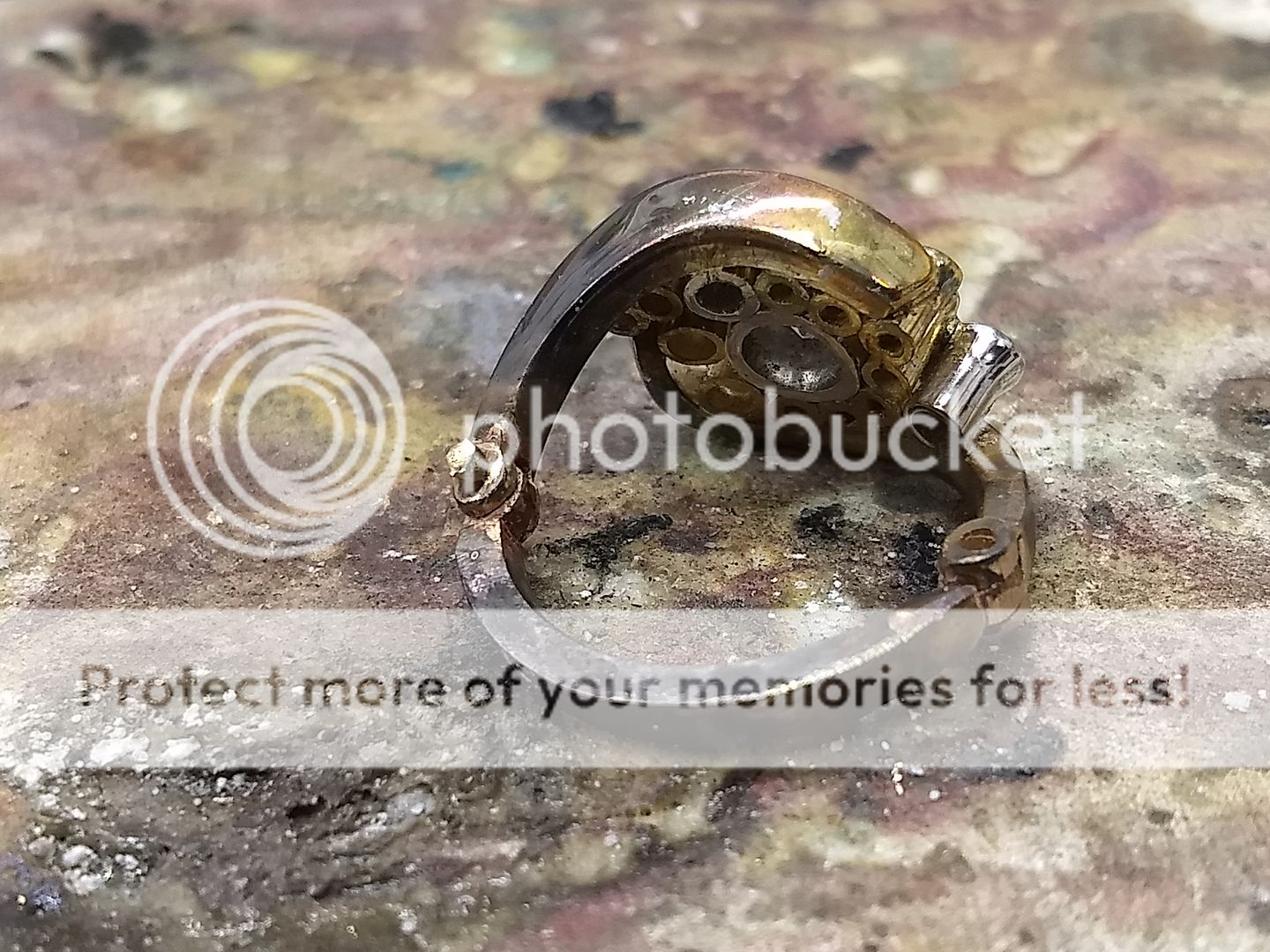
The hinge is then soldered to secure and the ring cleaned up:
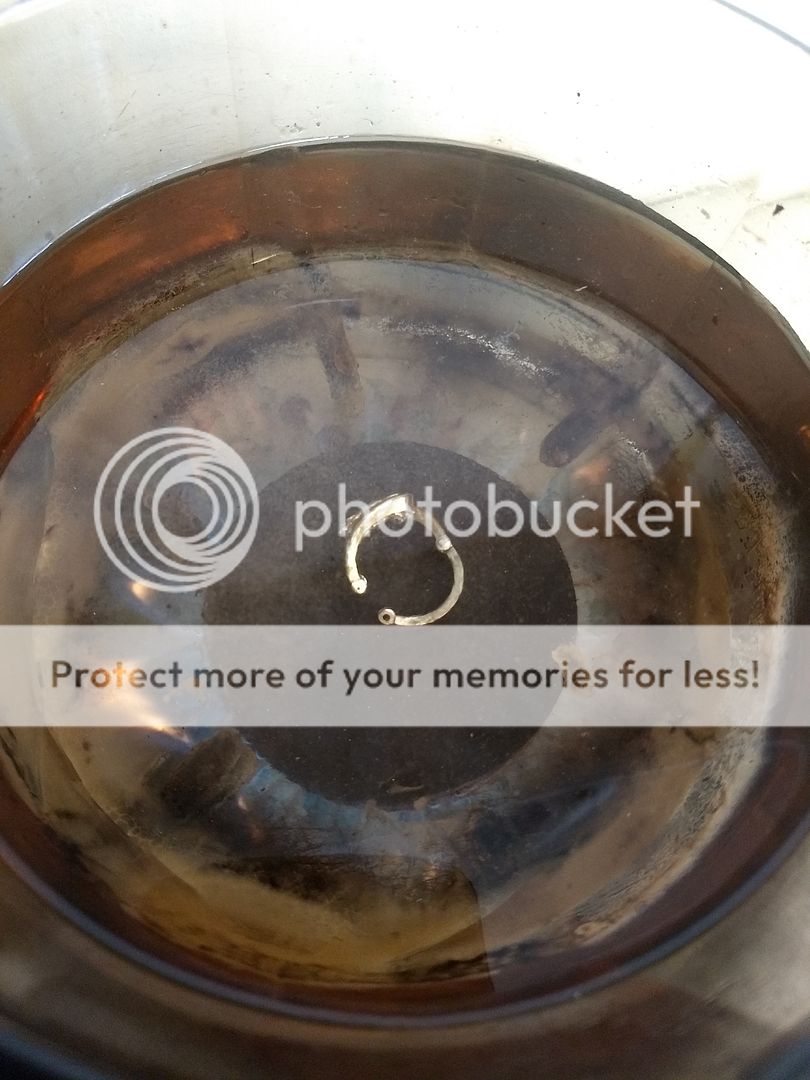
The little hole in the other end is there for a reason. I'll explain in a bit:
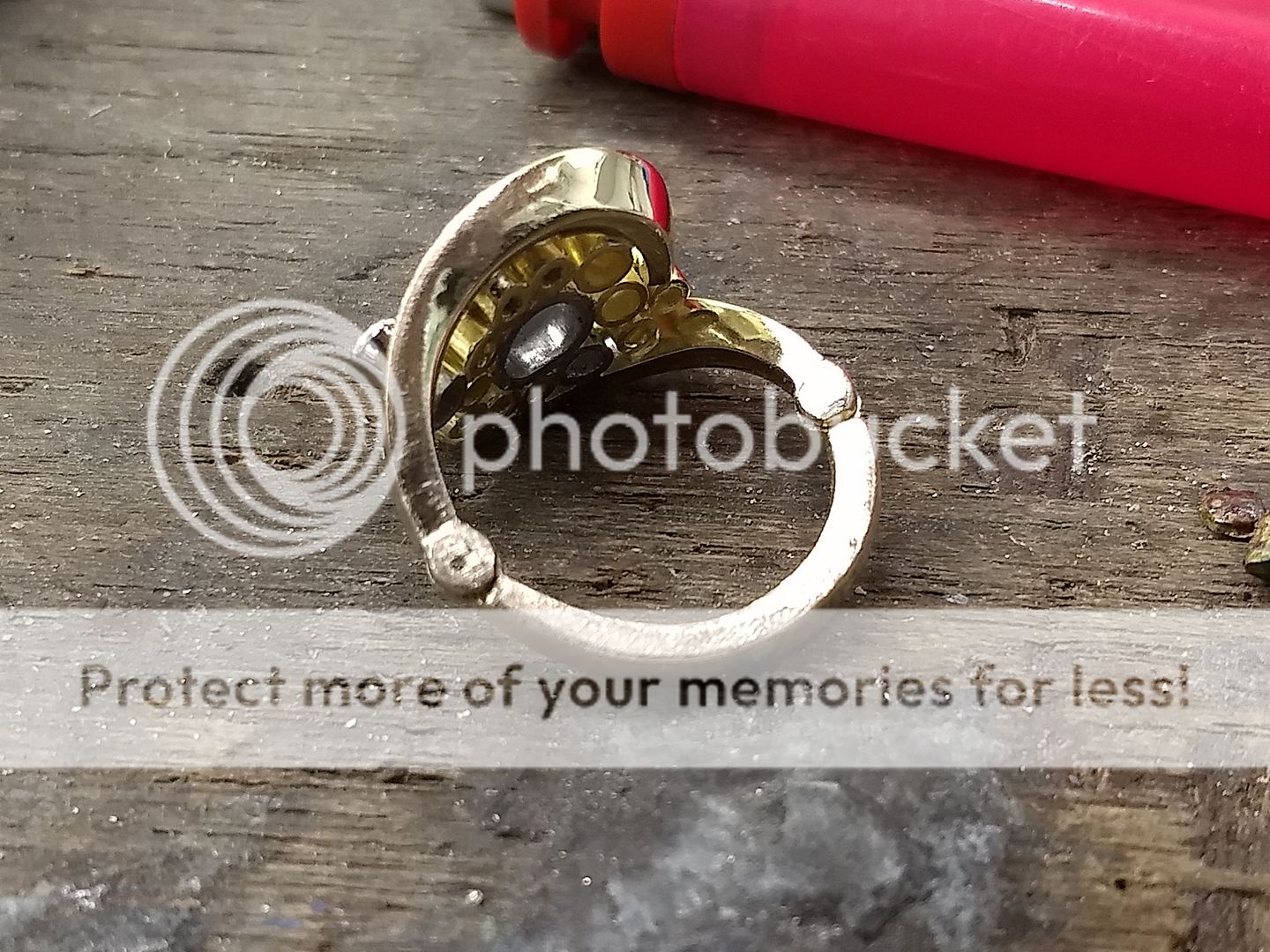
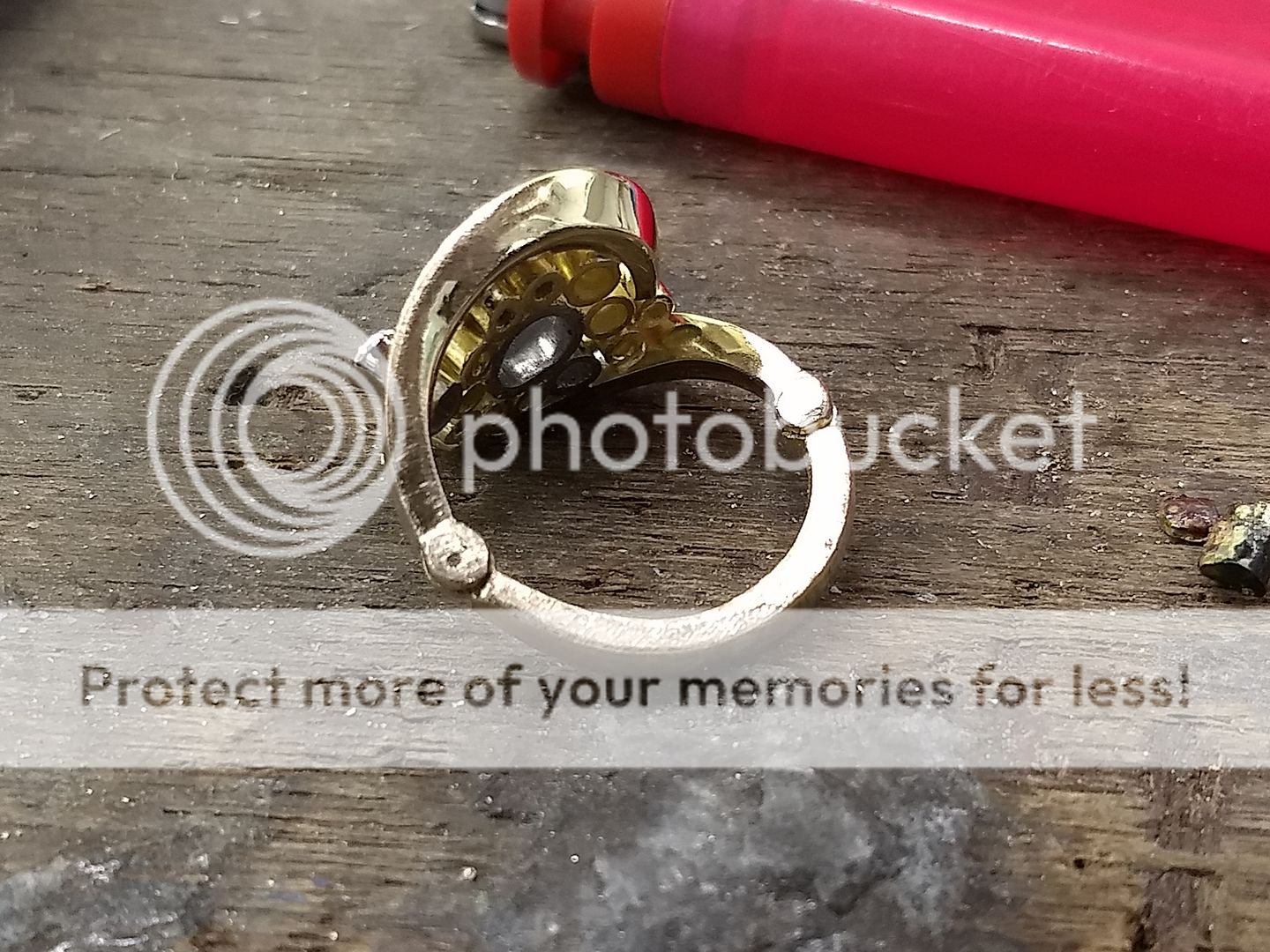
Sits ok
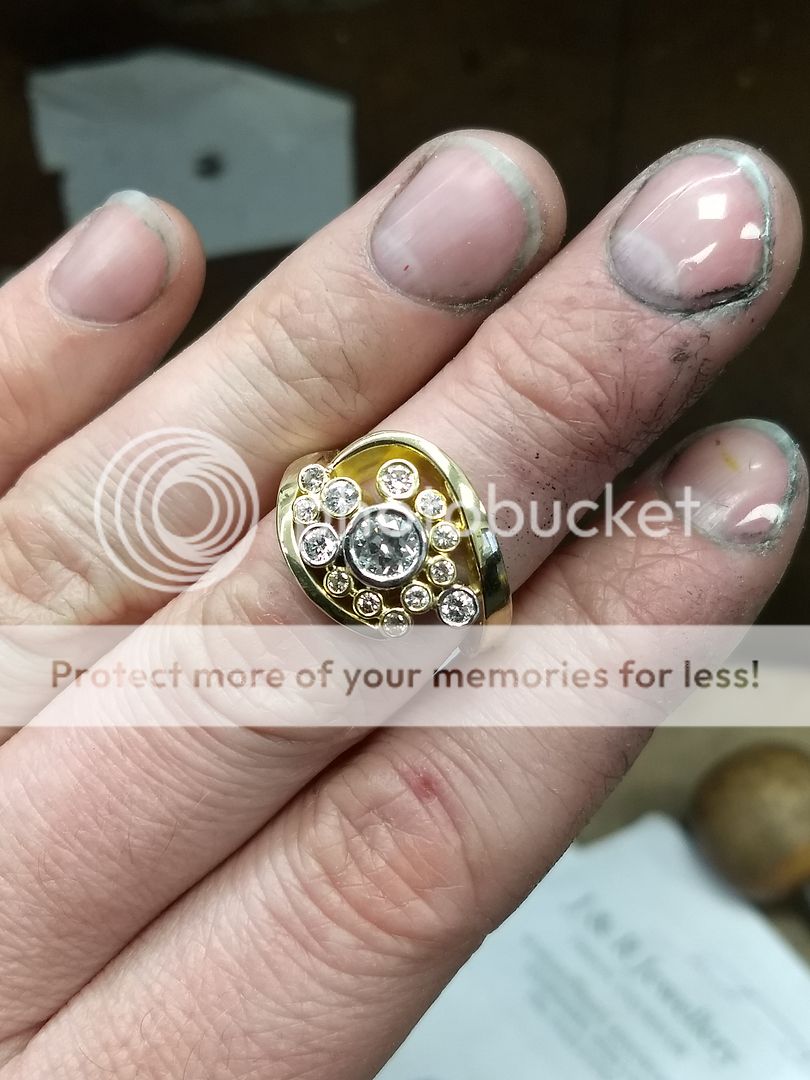
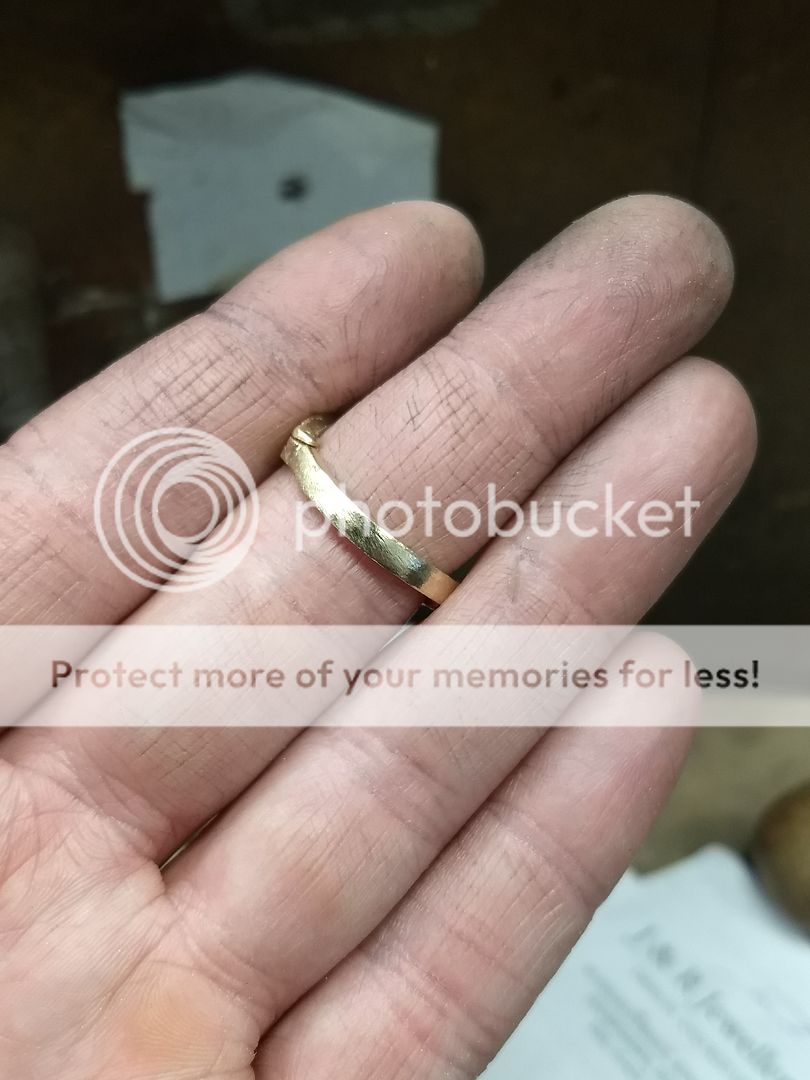
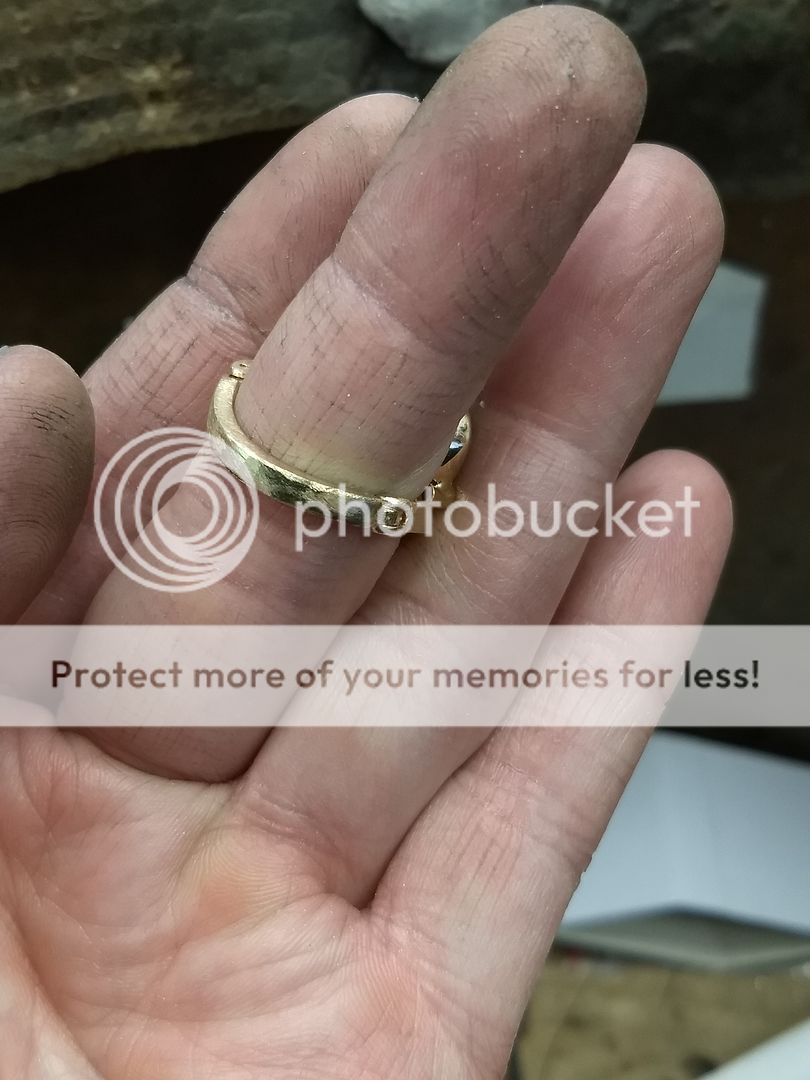
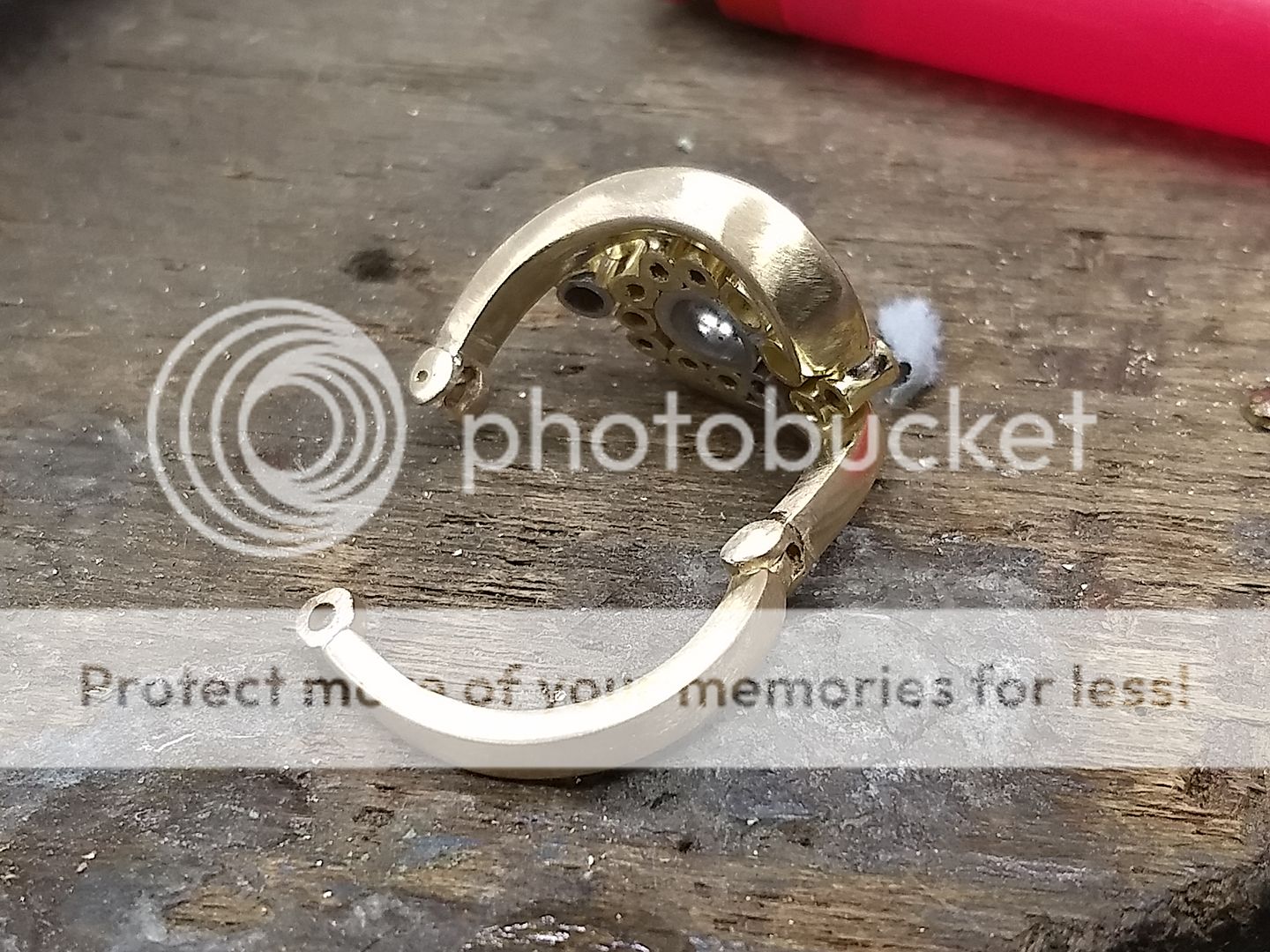

wrmc.jpg' target='_blank'/>
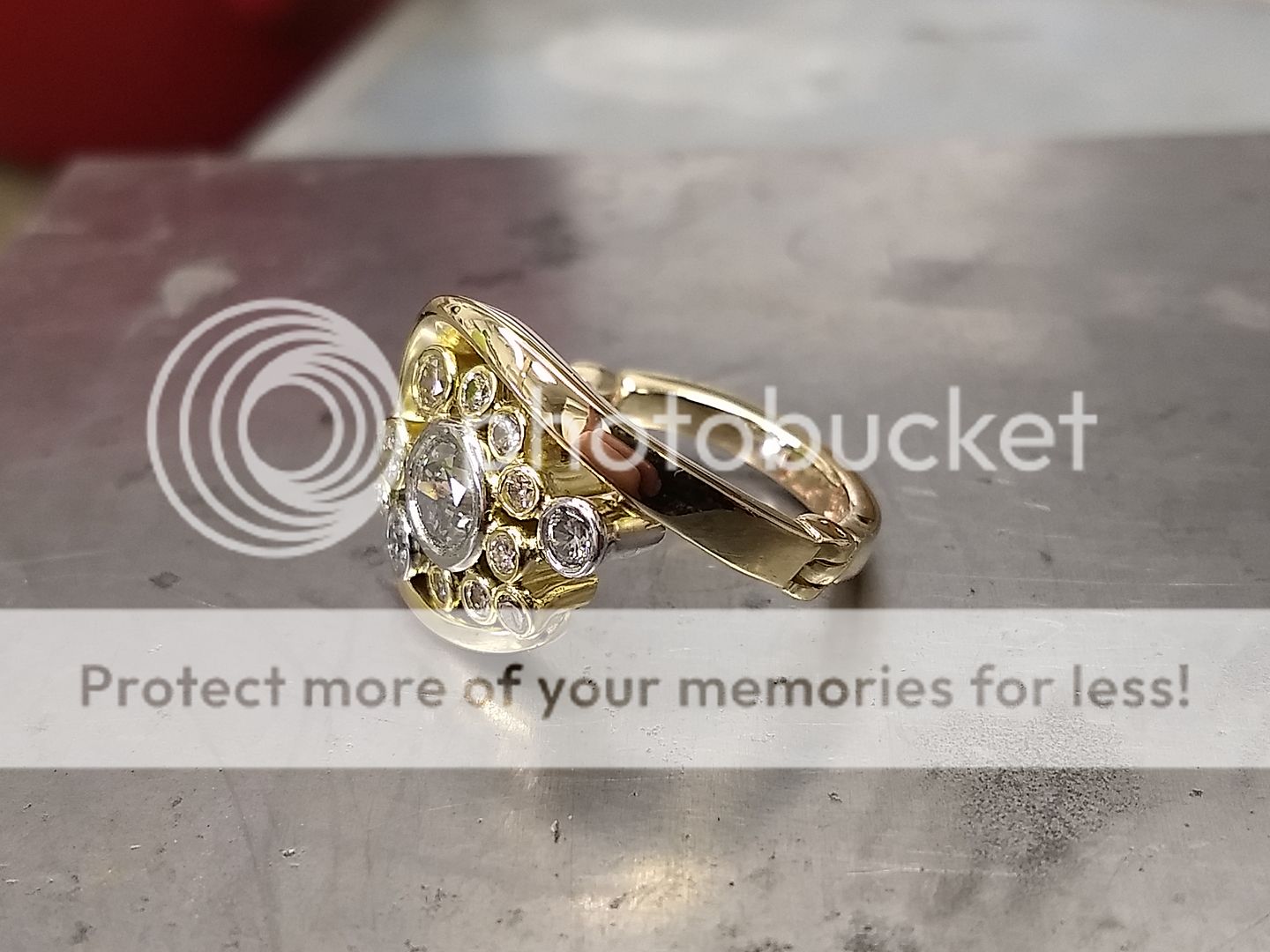
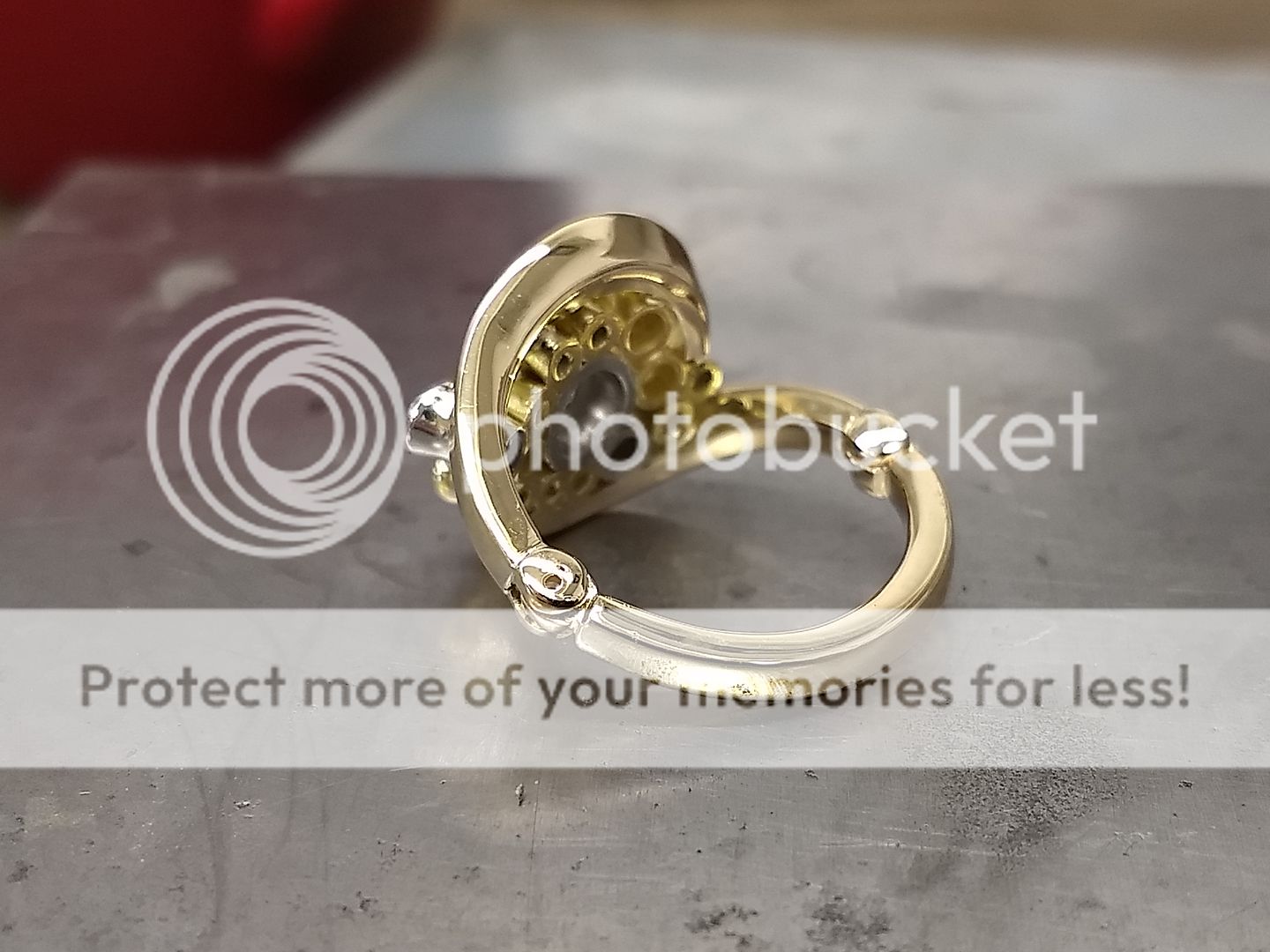
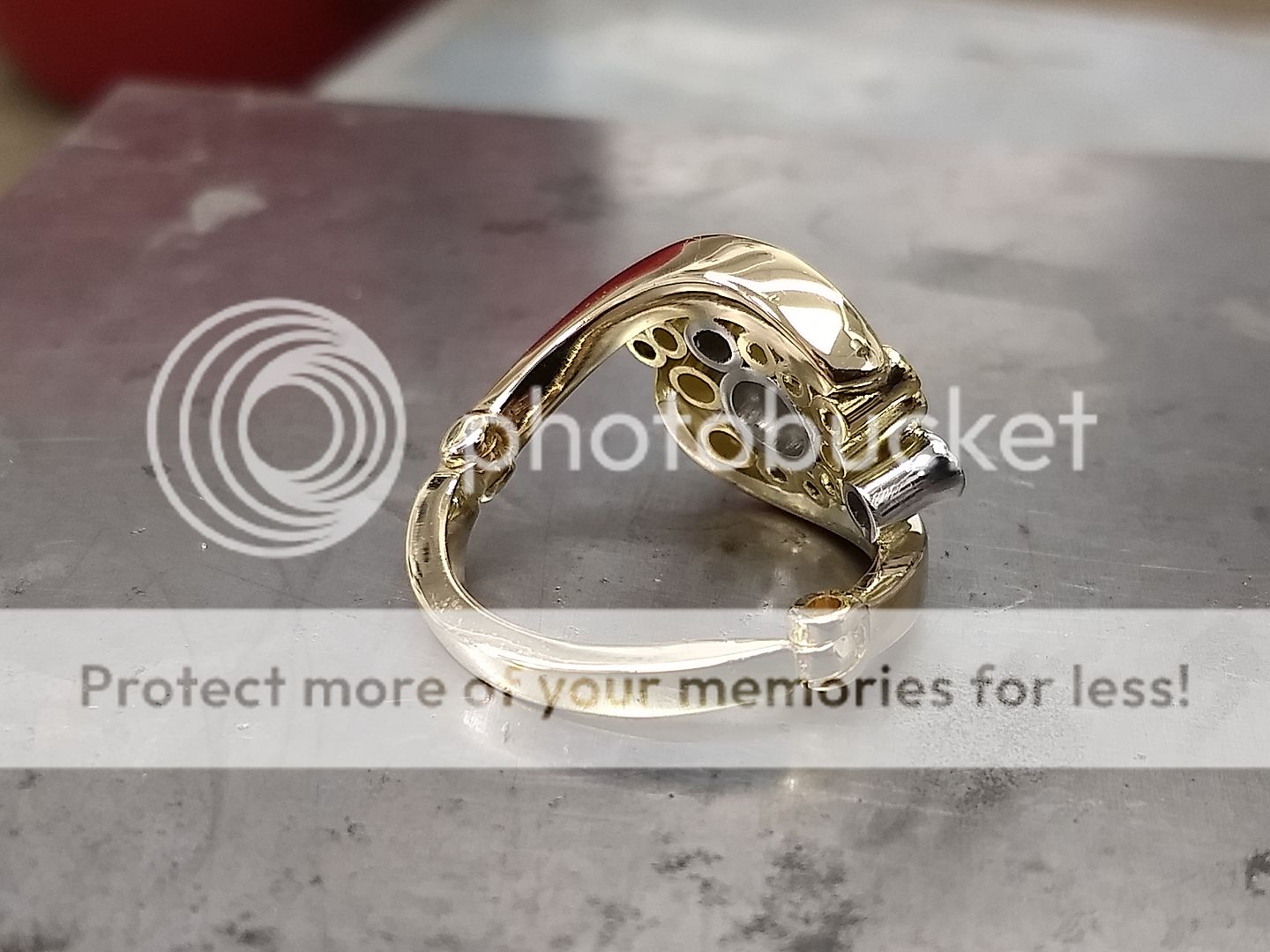
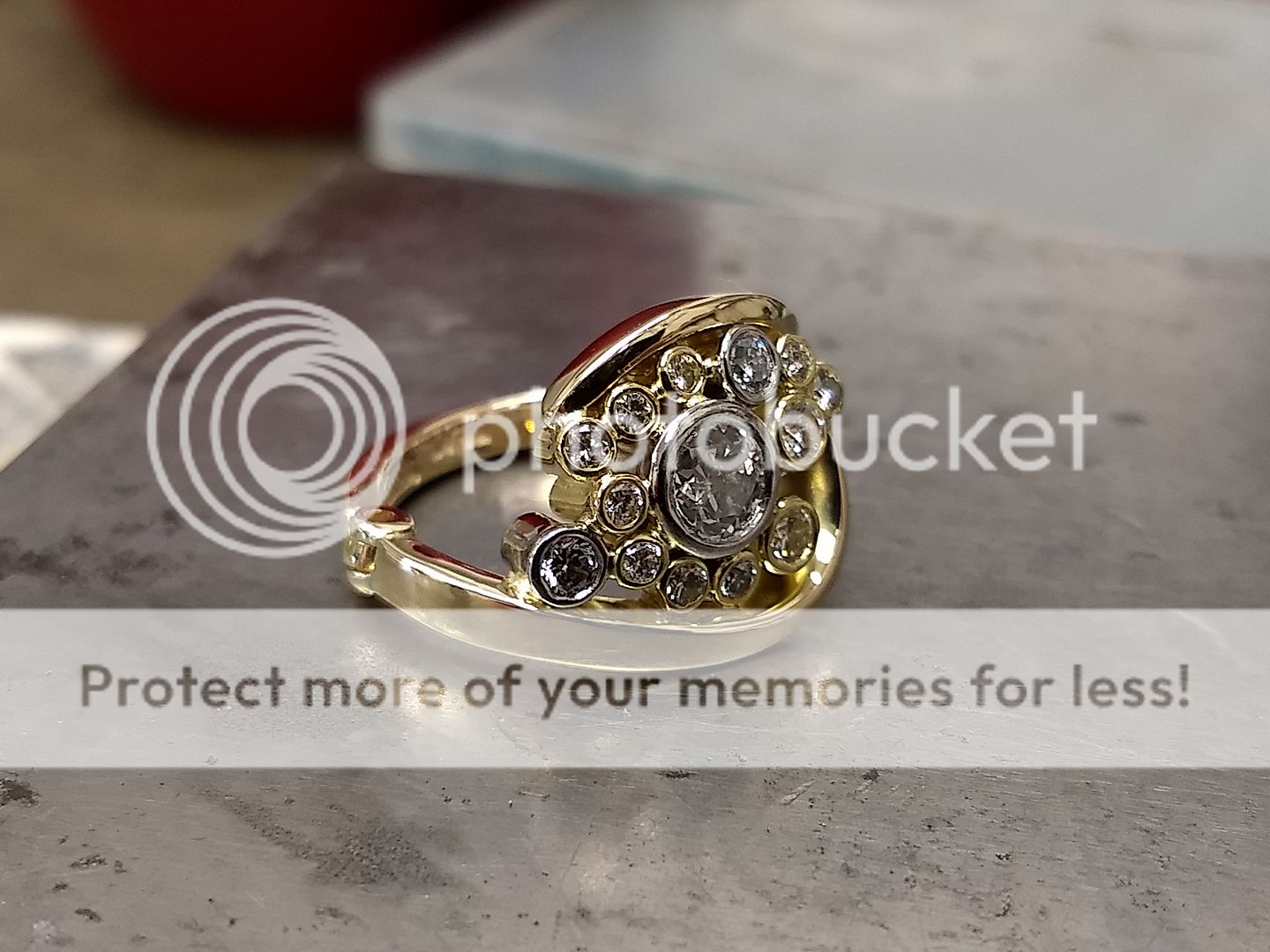
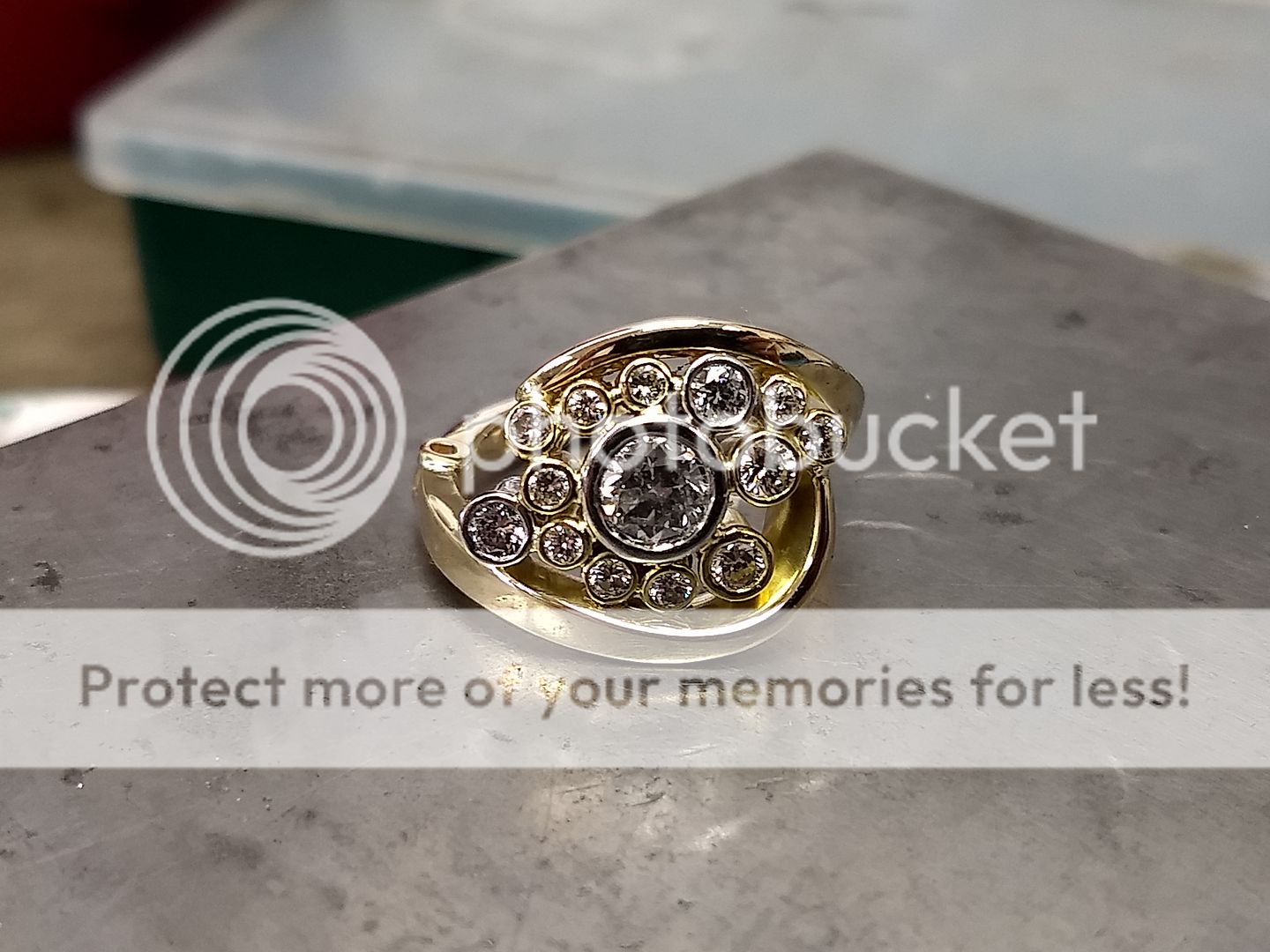
The grub screw: With the gold being soft I wanted something that wasn't going to damage the important bit..... the ring. So, I threaded some silver wire to make what is effectively a sacrificial, single use screw. She'll rarely take it off and as she's local she can come in to see me if it needed removing and refitting. It screws in fine and is snug enough to not come out, but once it's in the threads are destroyed. That little hole in the other side? It's to poke in a little threadlock to keep it secure long term. It's not strong enough that I can't screw it back out but it is firm enough that she and I don't have to worry about it. Pretty clever I reckon
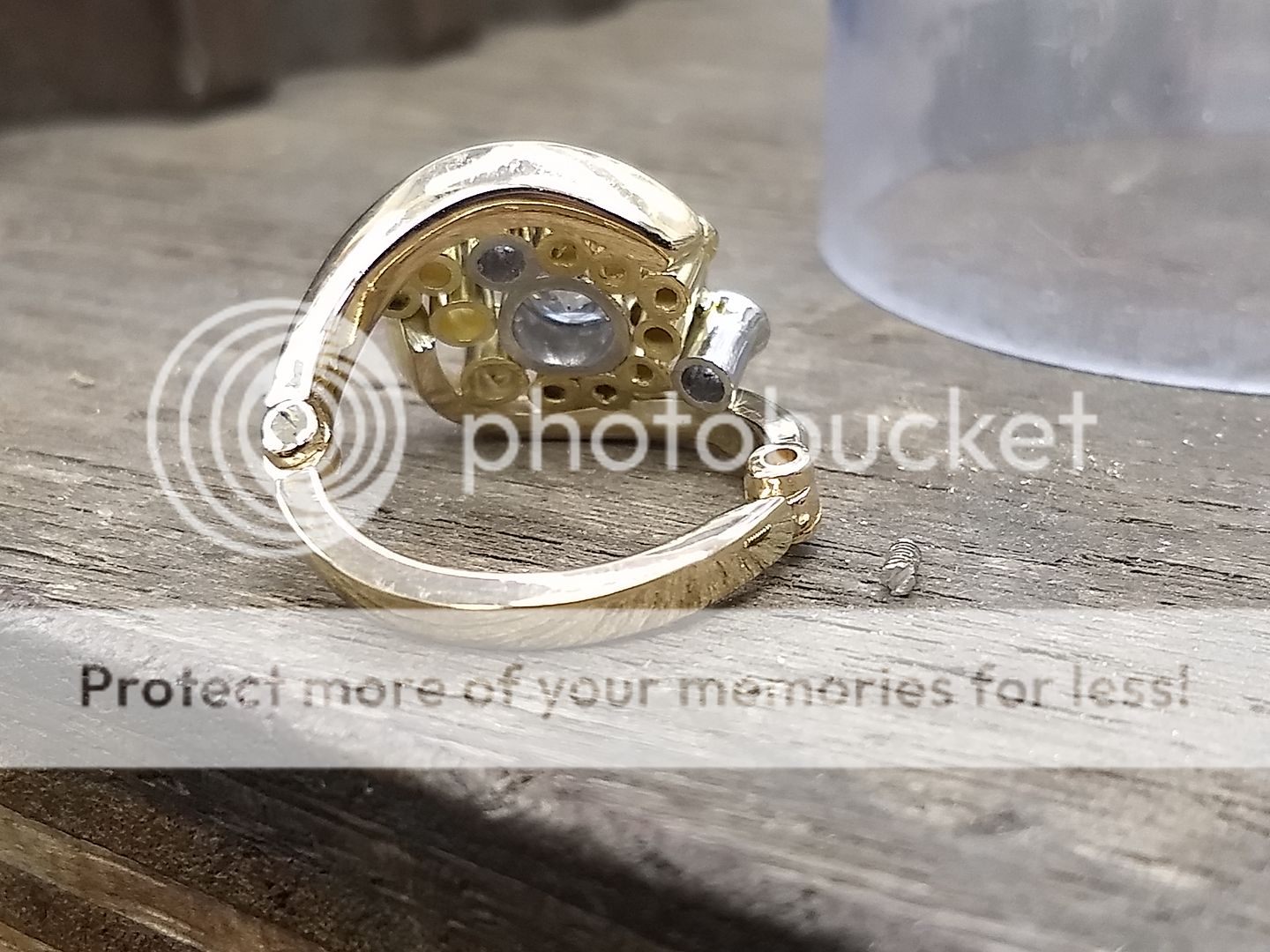
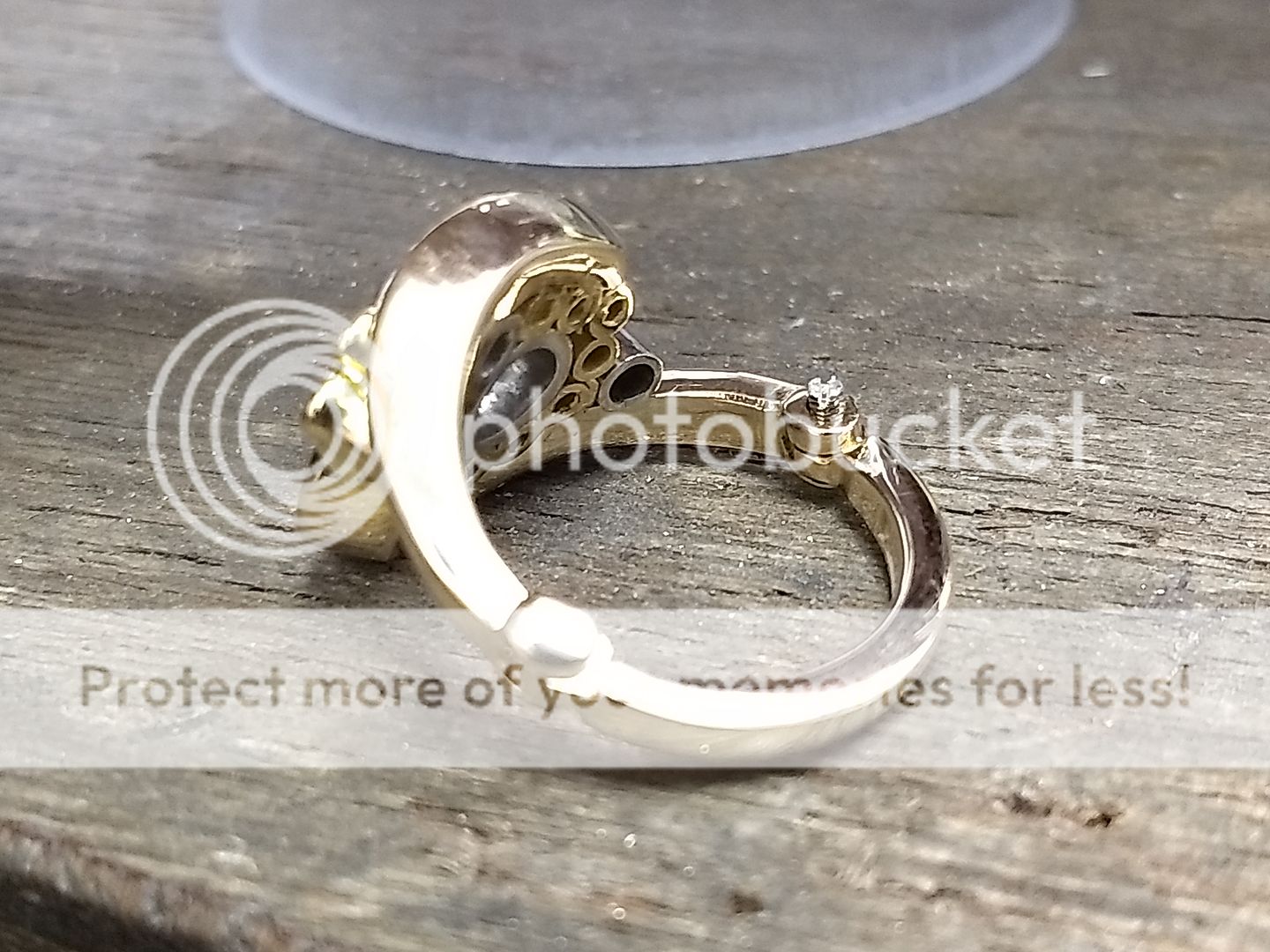
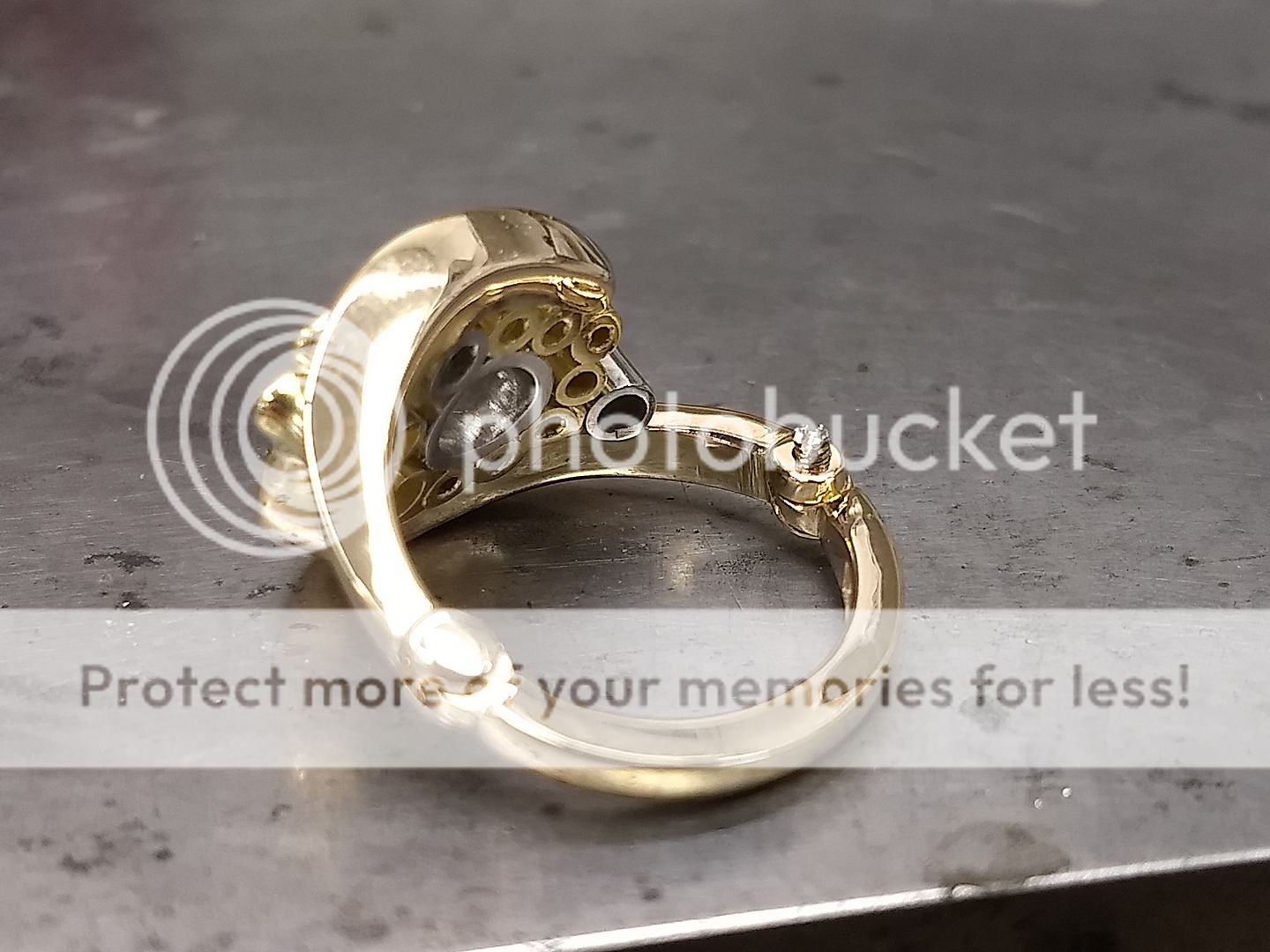
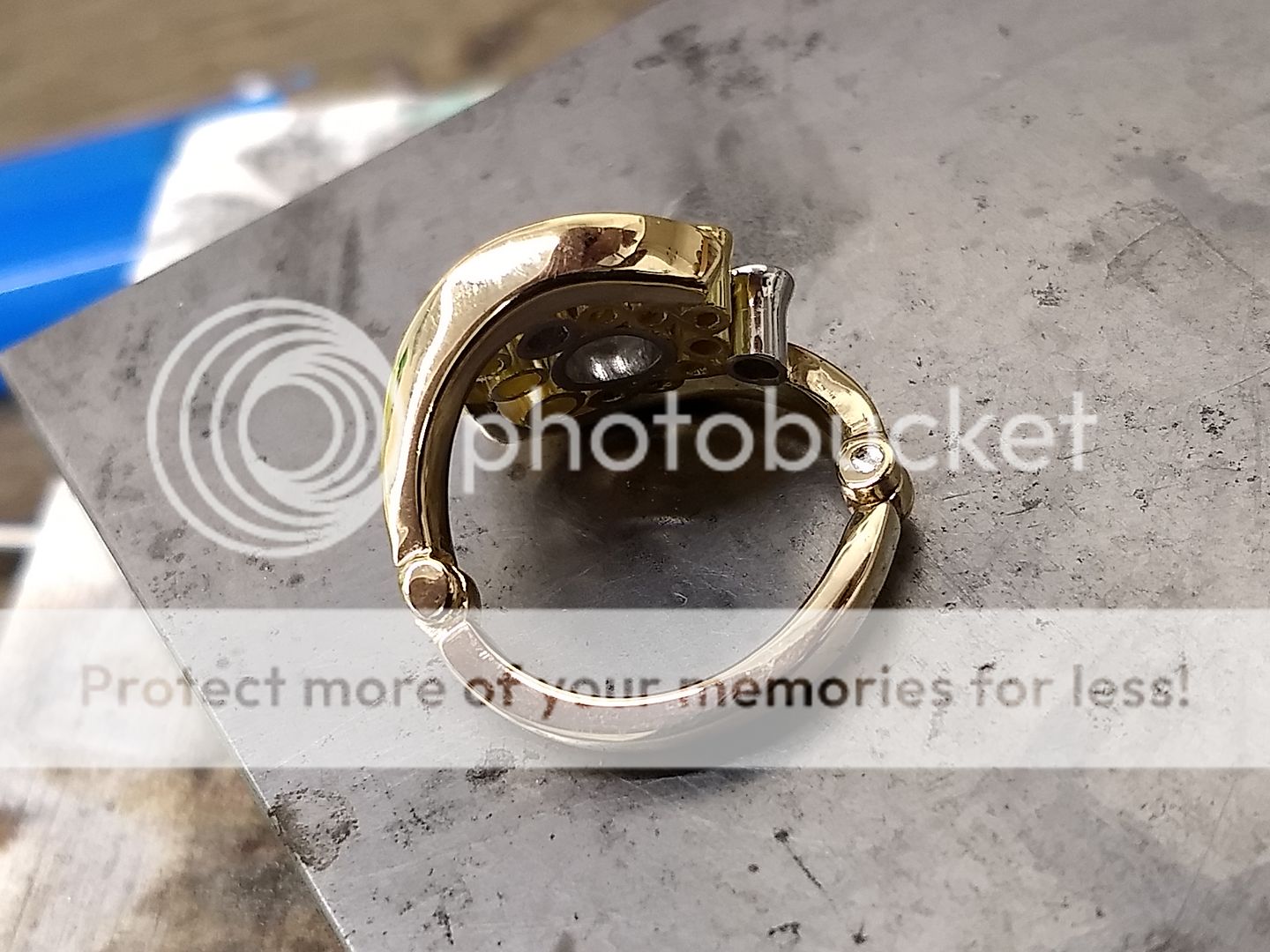
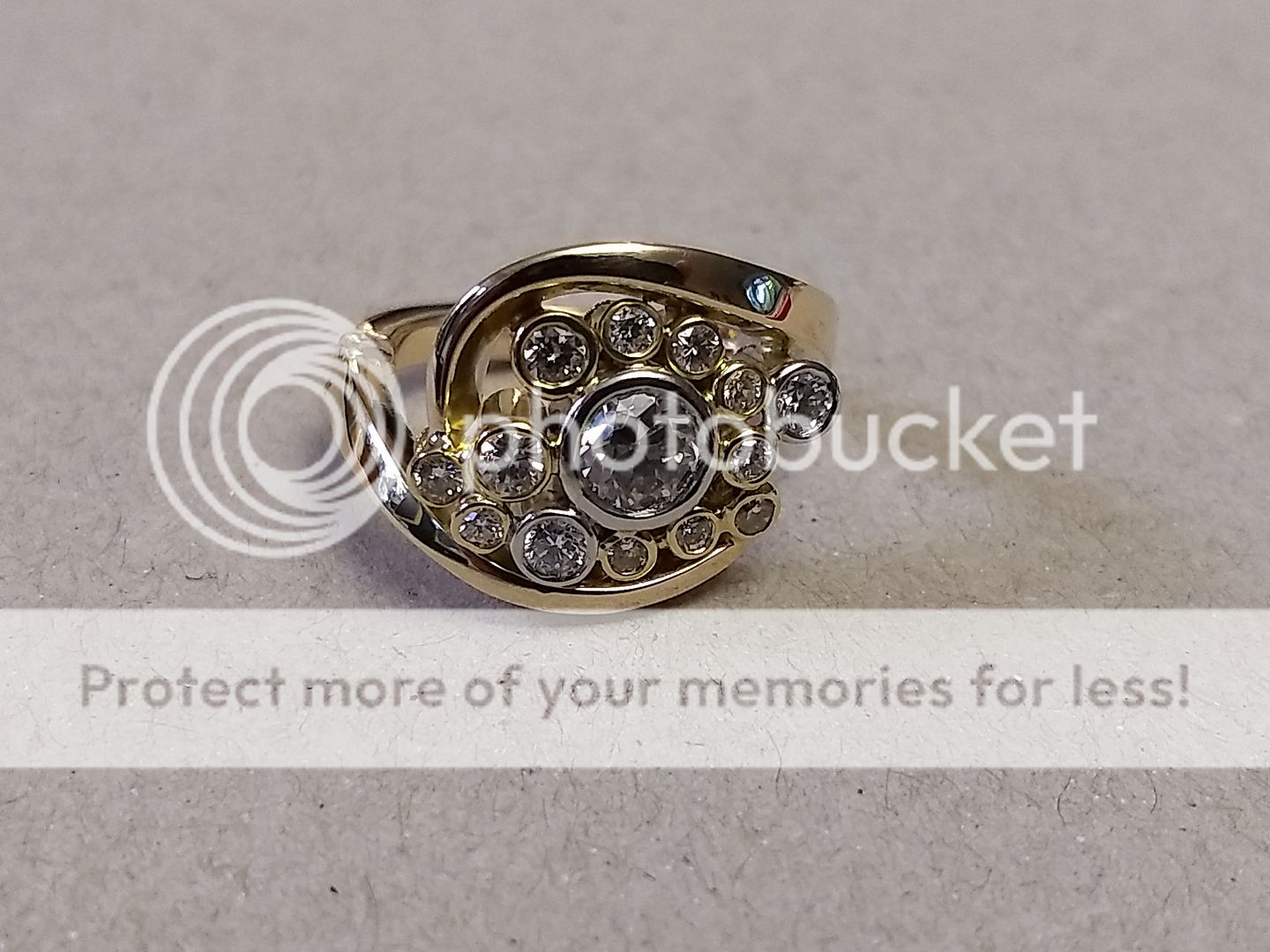
Thanks for looking

This one is quite pic heavy so apologies if your internet takes a hit. Brief outline: Customer has very arthritic knuckles and is resigned to never wearing a ring again, unless it's made so big it swings round the finger. Queue the next job for ecain63 and his dirty fingers.
The lady has some rings left by her mother and grandmother, including one with a 0.75ct old cut diamond. There are half a dozen other small stones too as well as a mix of 18ct and 9ct yellow gold. We agree to keep the 18ct yellow to make the ring and swap / px the 9ct for another 0.50ct of small stone, making 14 stones in all. I bought some platinum and 18ct yellow tube and away we went. Here's the head building process:
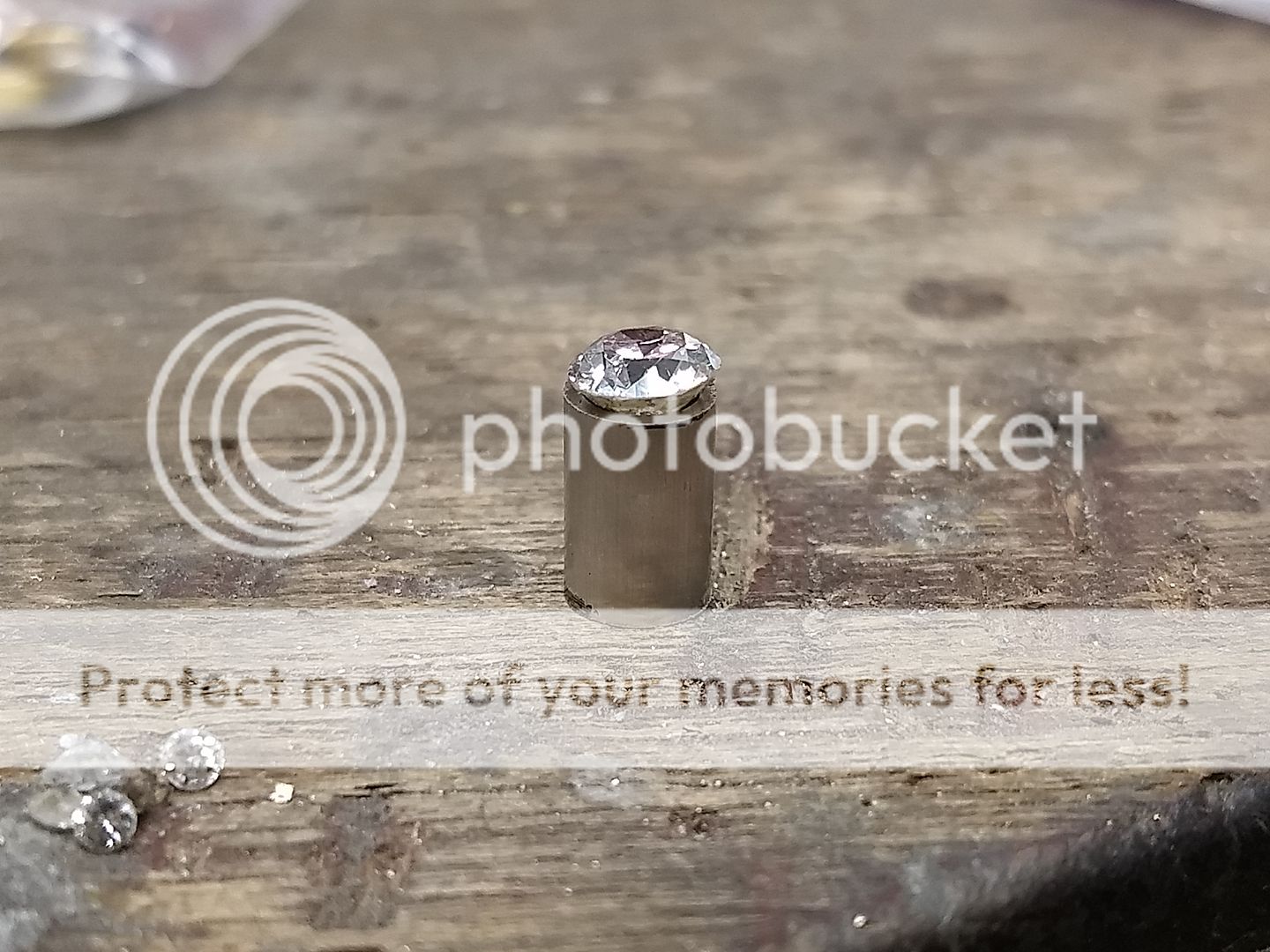
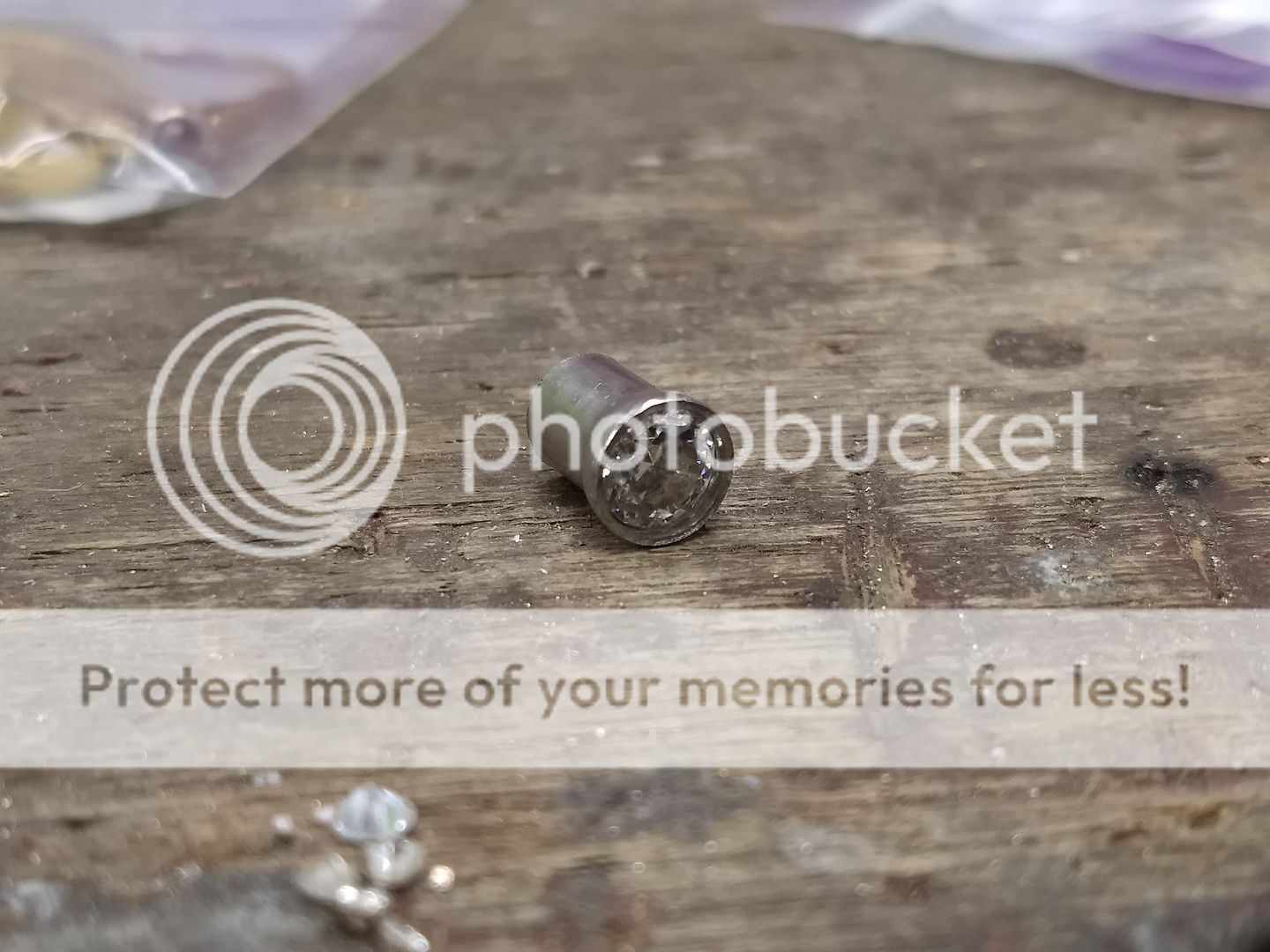
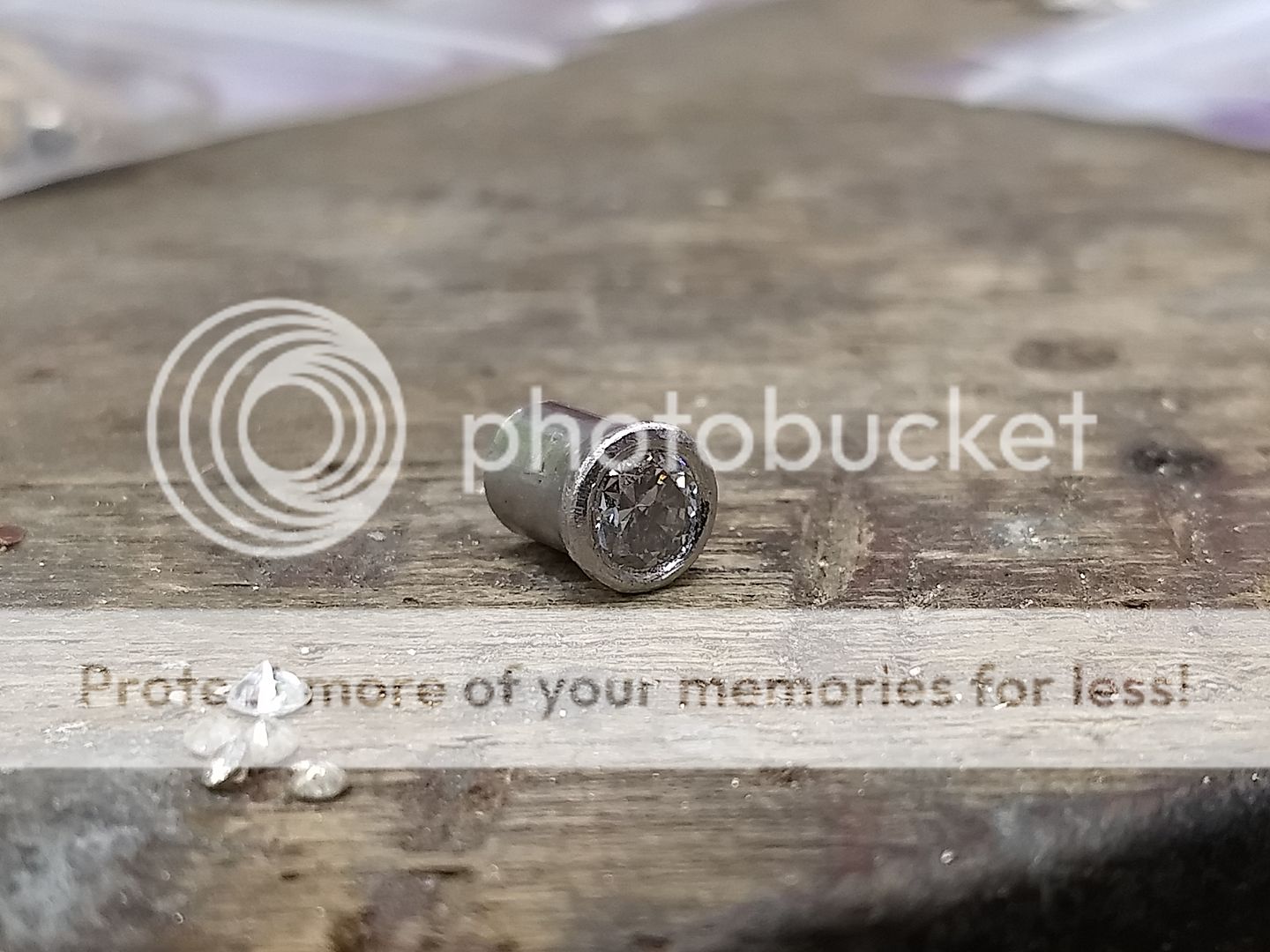
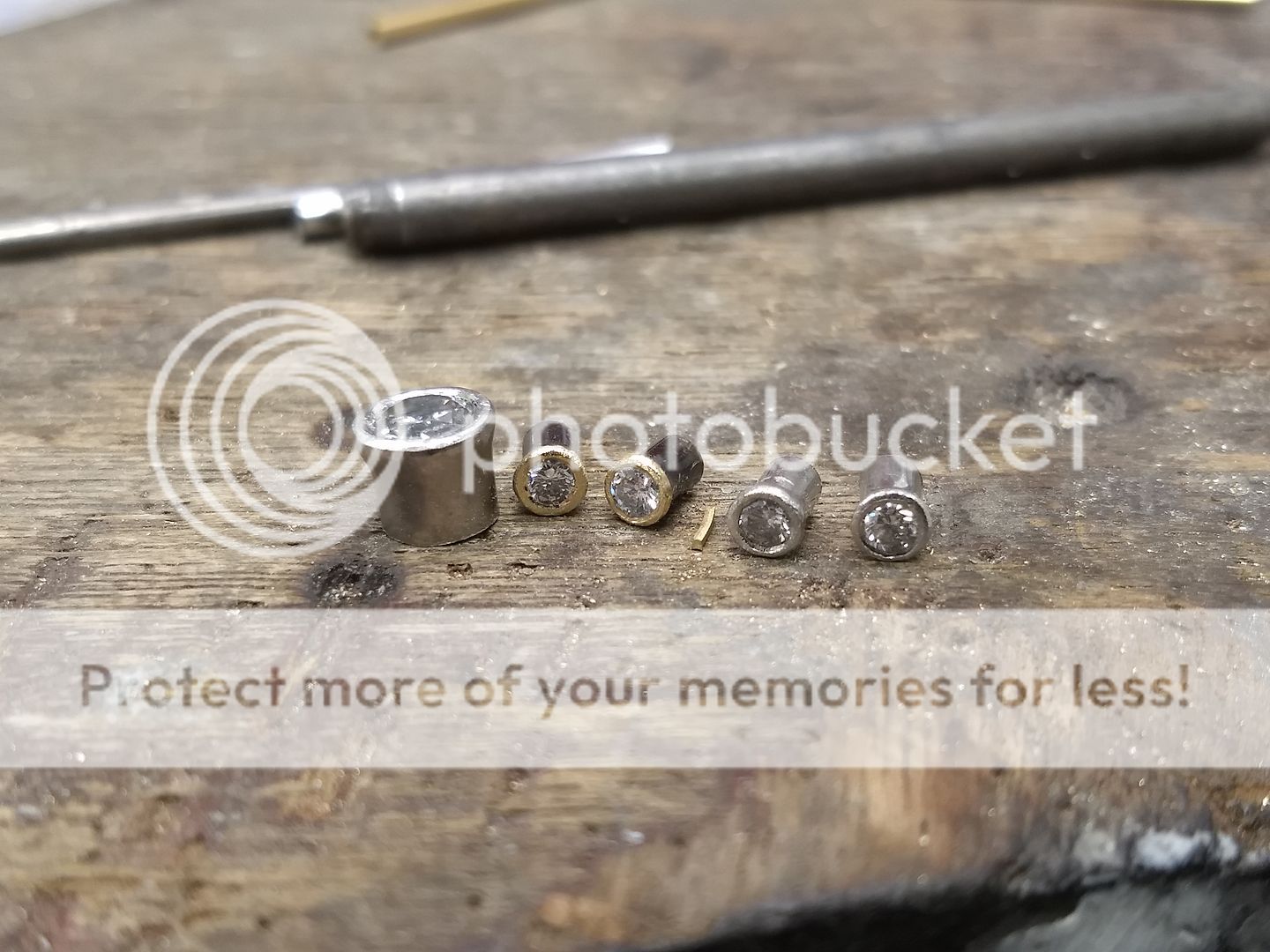
Reminds me of when that setting company did the diamonds on the inside of that Rolls Royce a couple of years back.
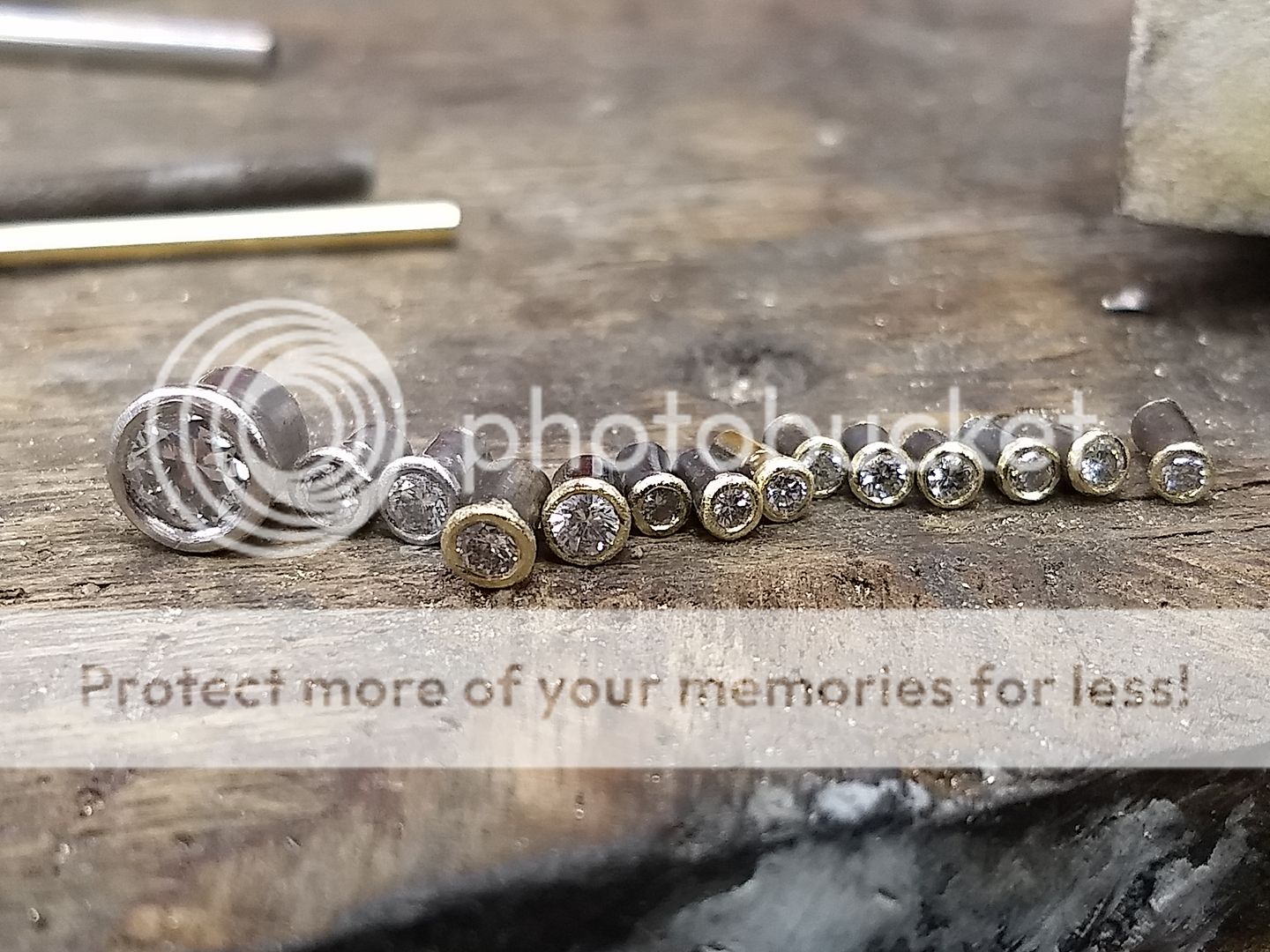
With the stones all set in their tubes we agree on a rough design:
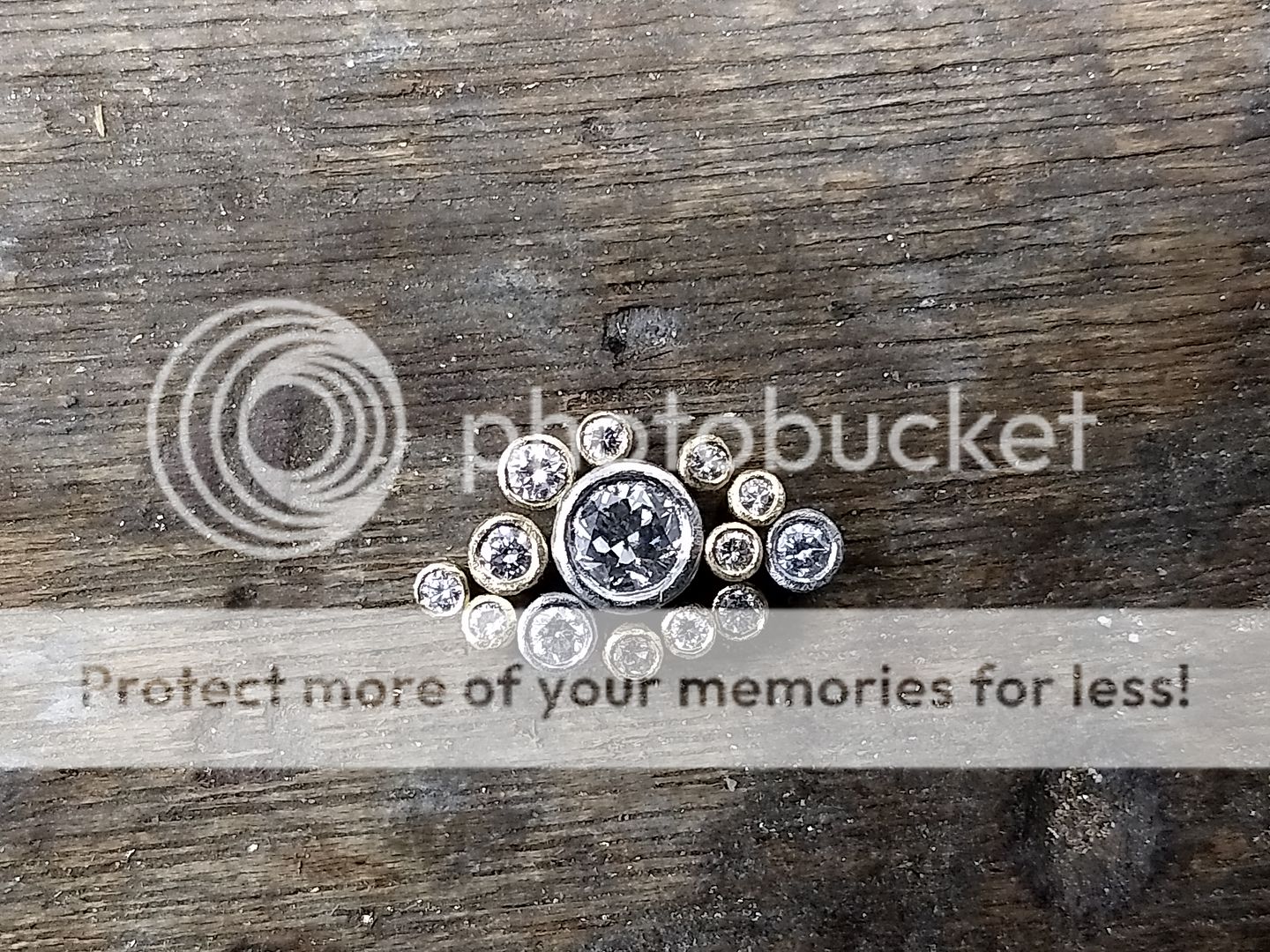

The next job is to make the shoulders and produce a complete head. Here we melt the 18ct scrap and begin the assembly process:
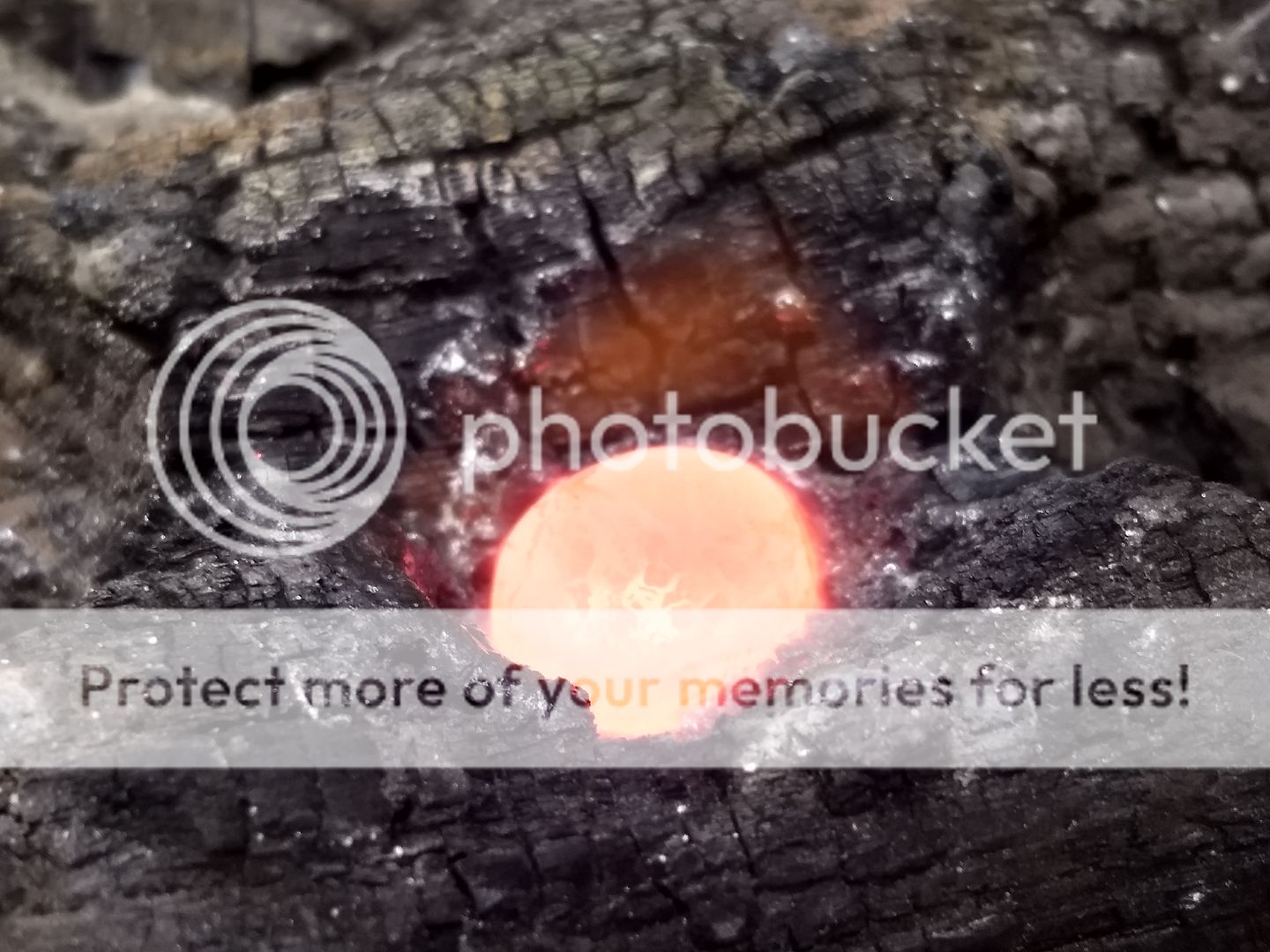
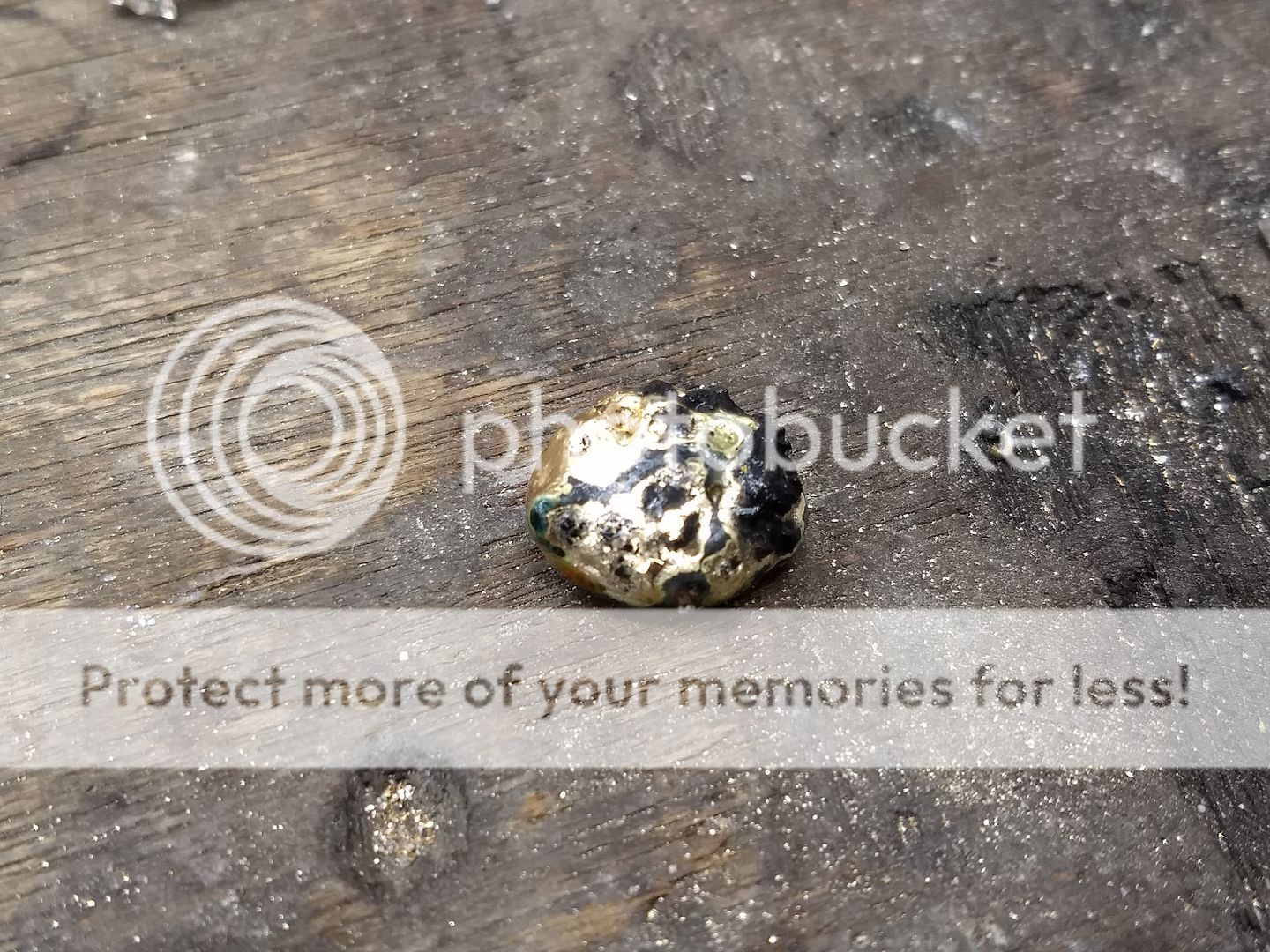
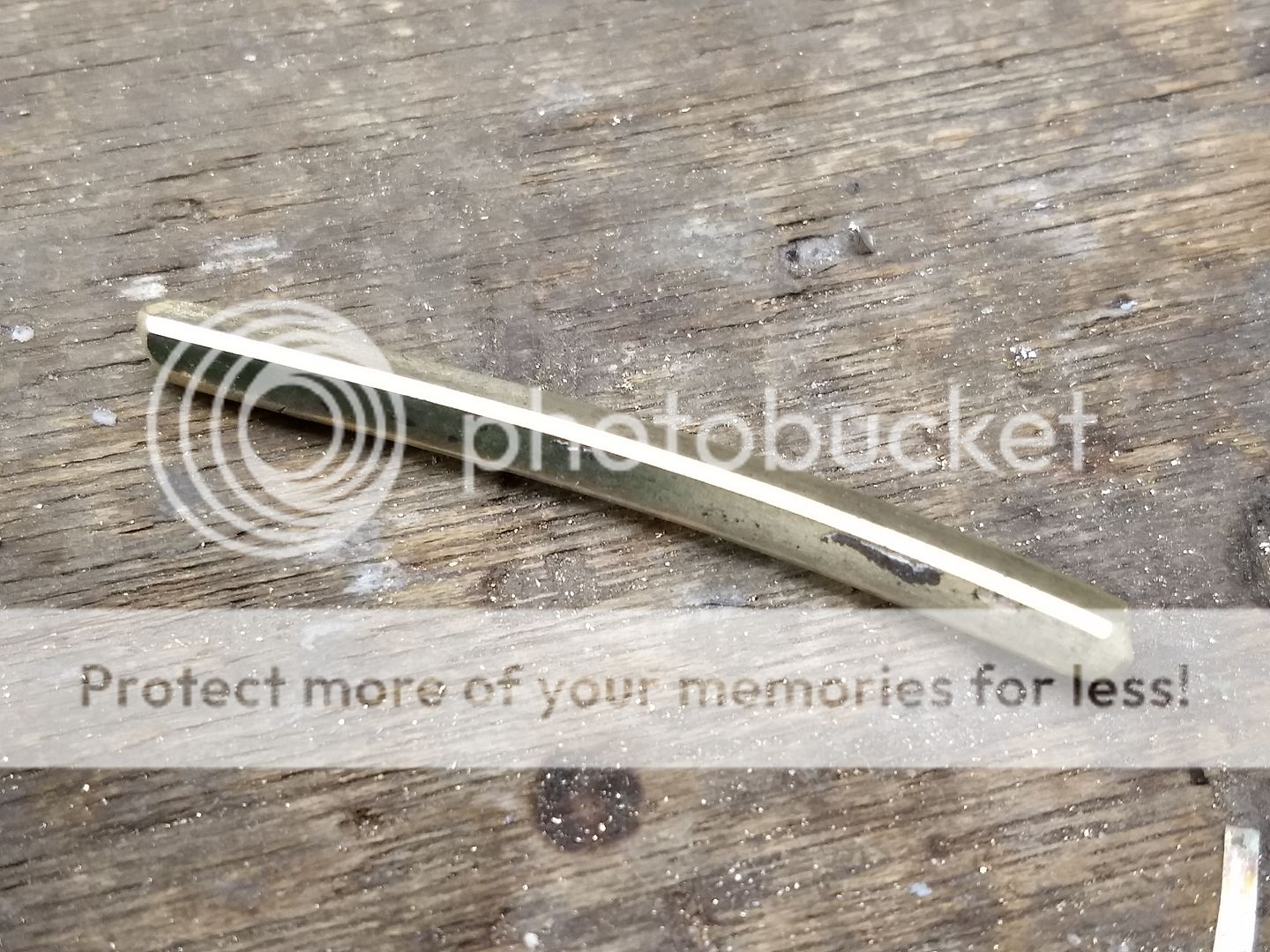
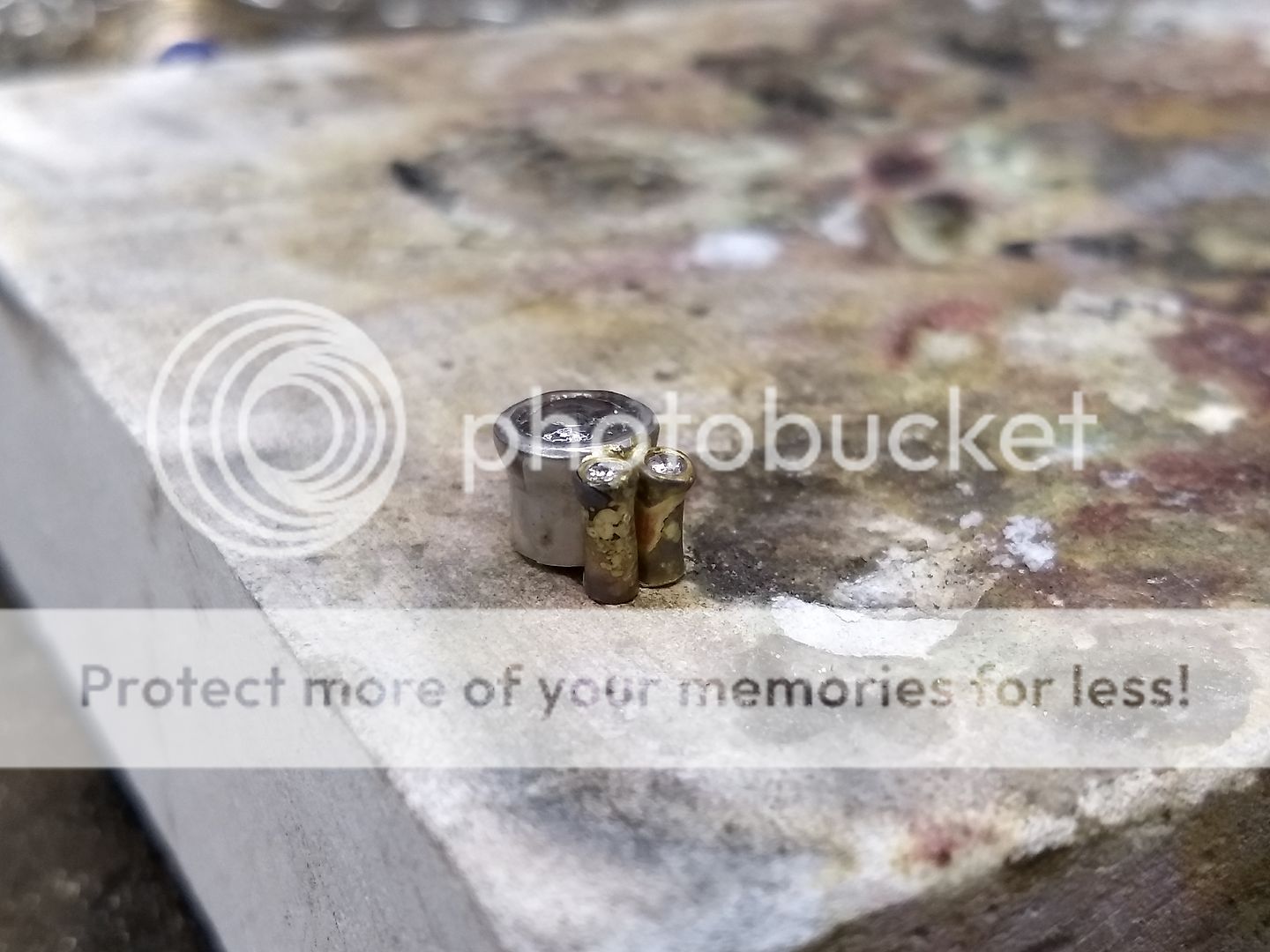
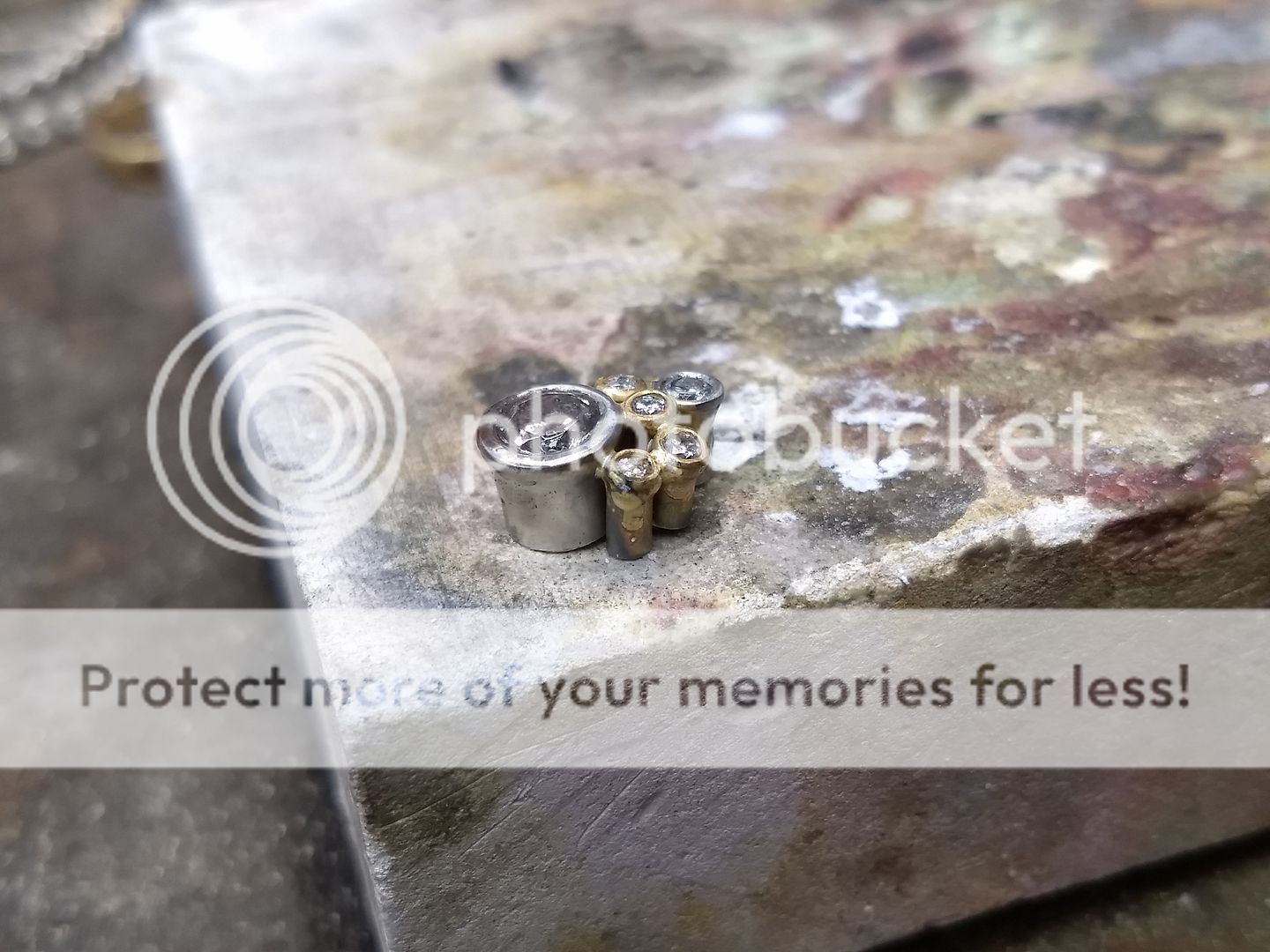
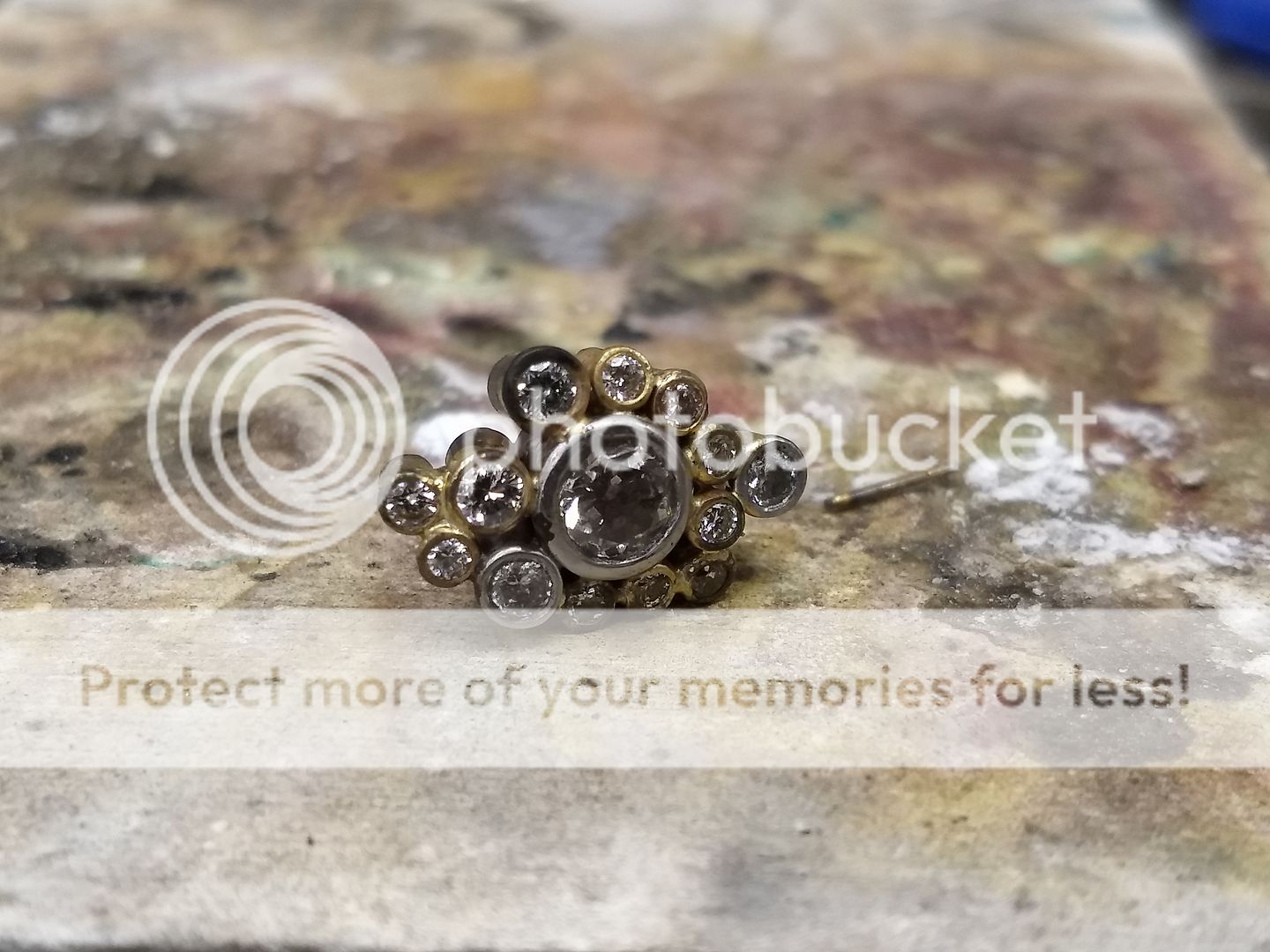
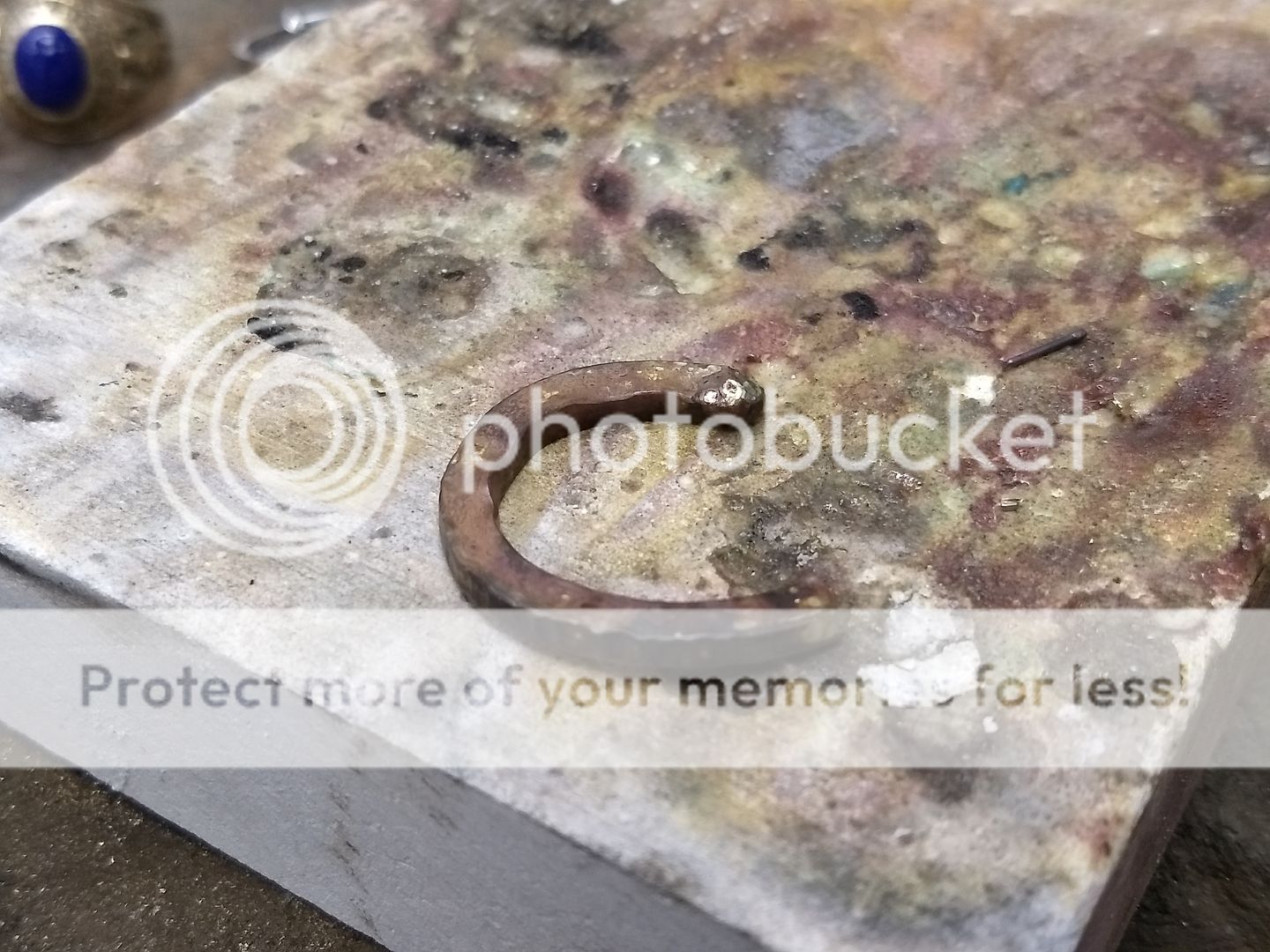
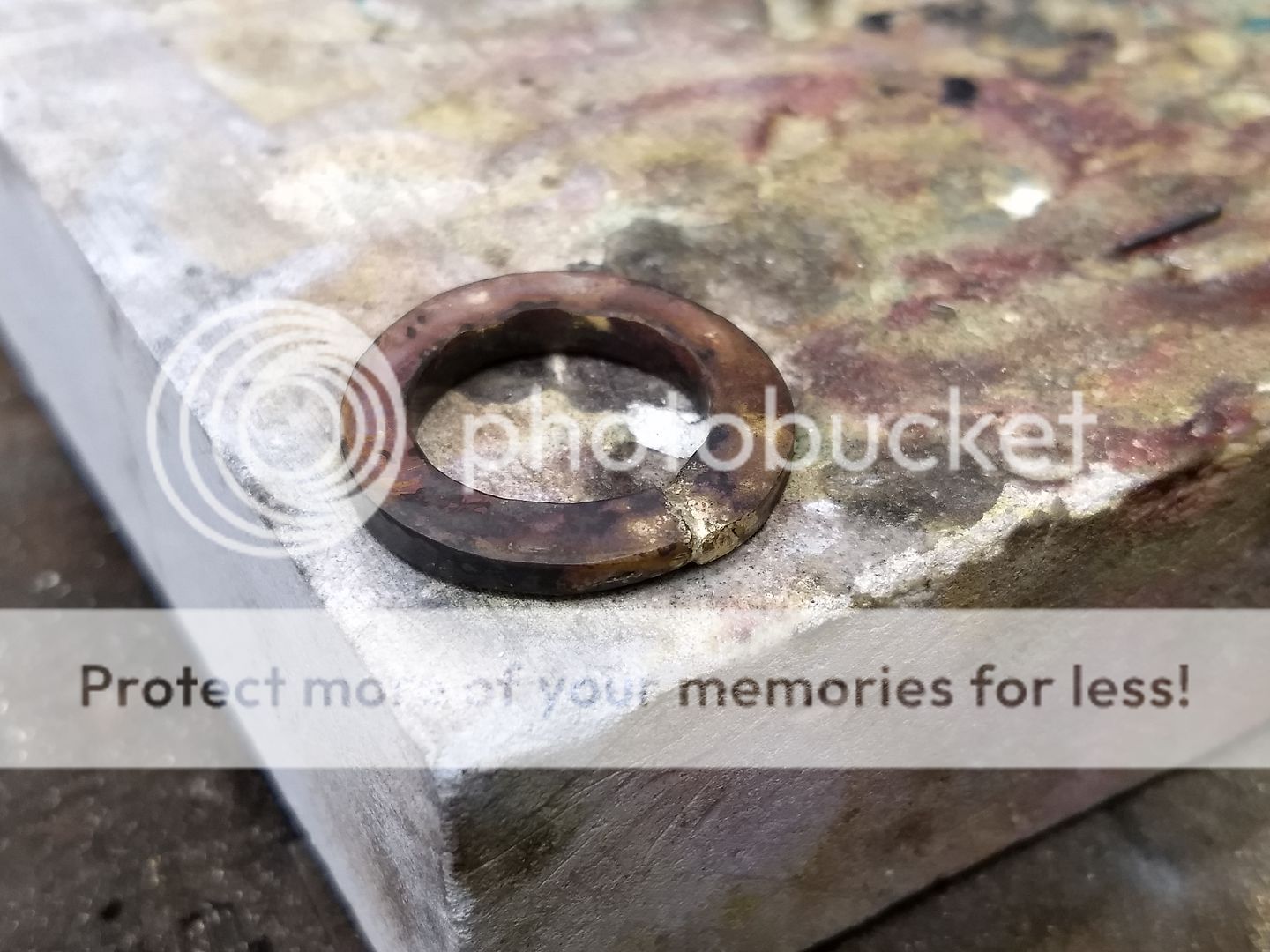
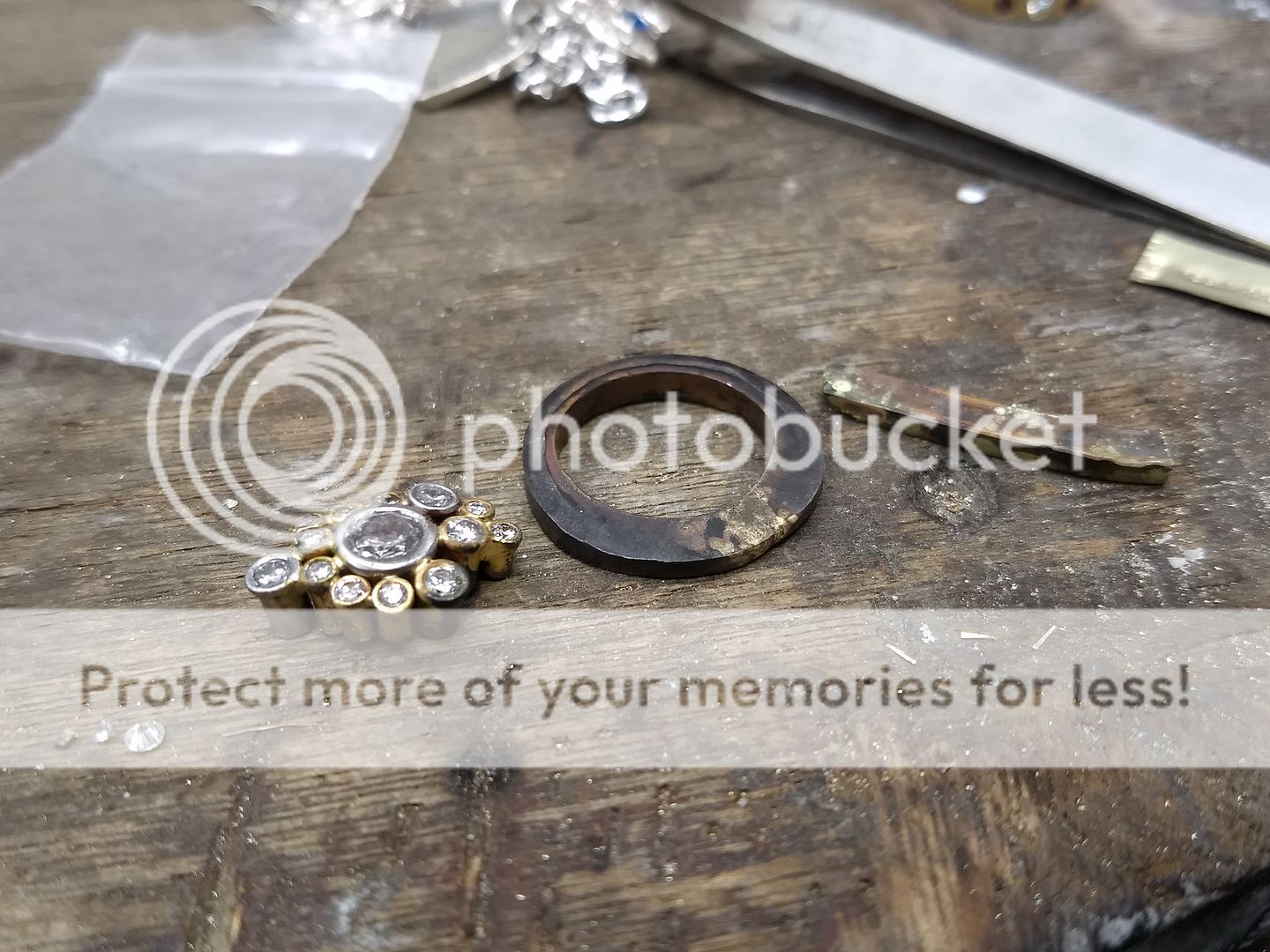
Skipped a pic here for some reason. The above is cleaned up and then split at the centre. The shoulders are shaped to make a twist:
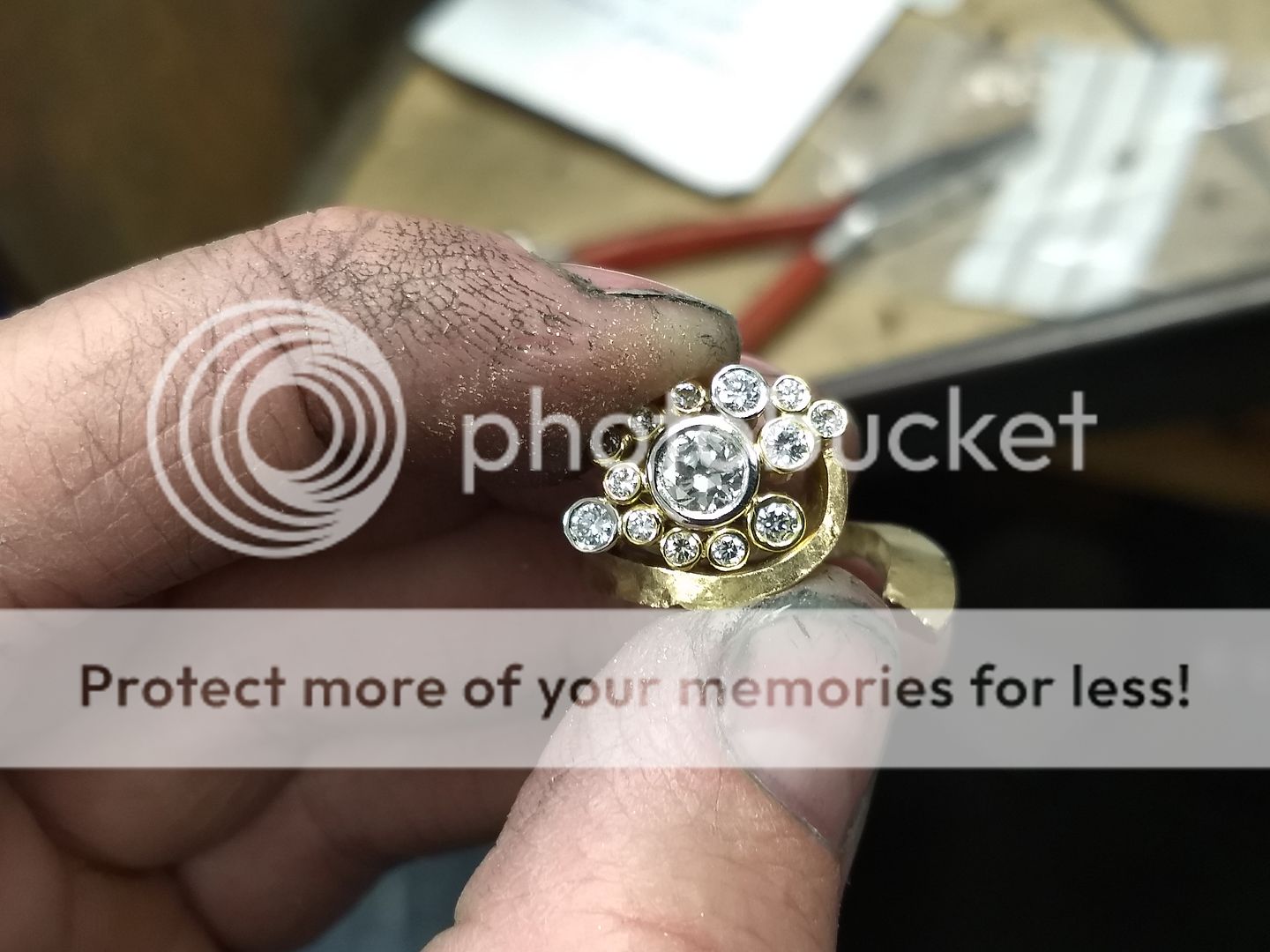
And test fitted on one side after a light file and clean up:
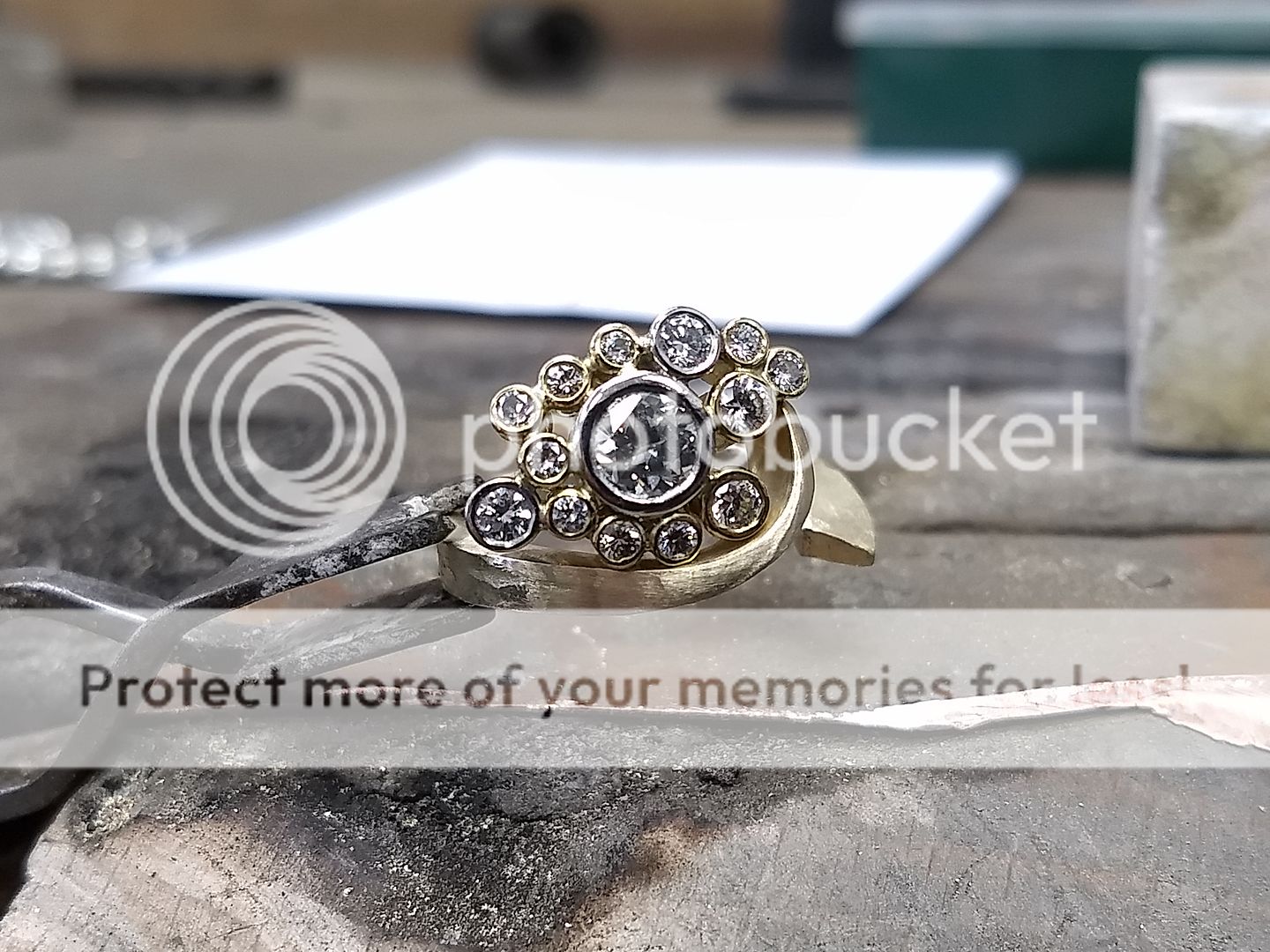
This shoulder is then removed from the other as they are both individually shaped and positioned:
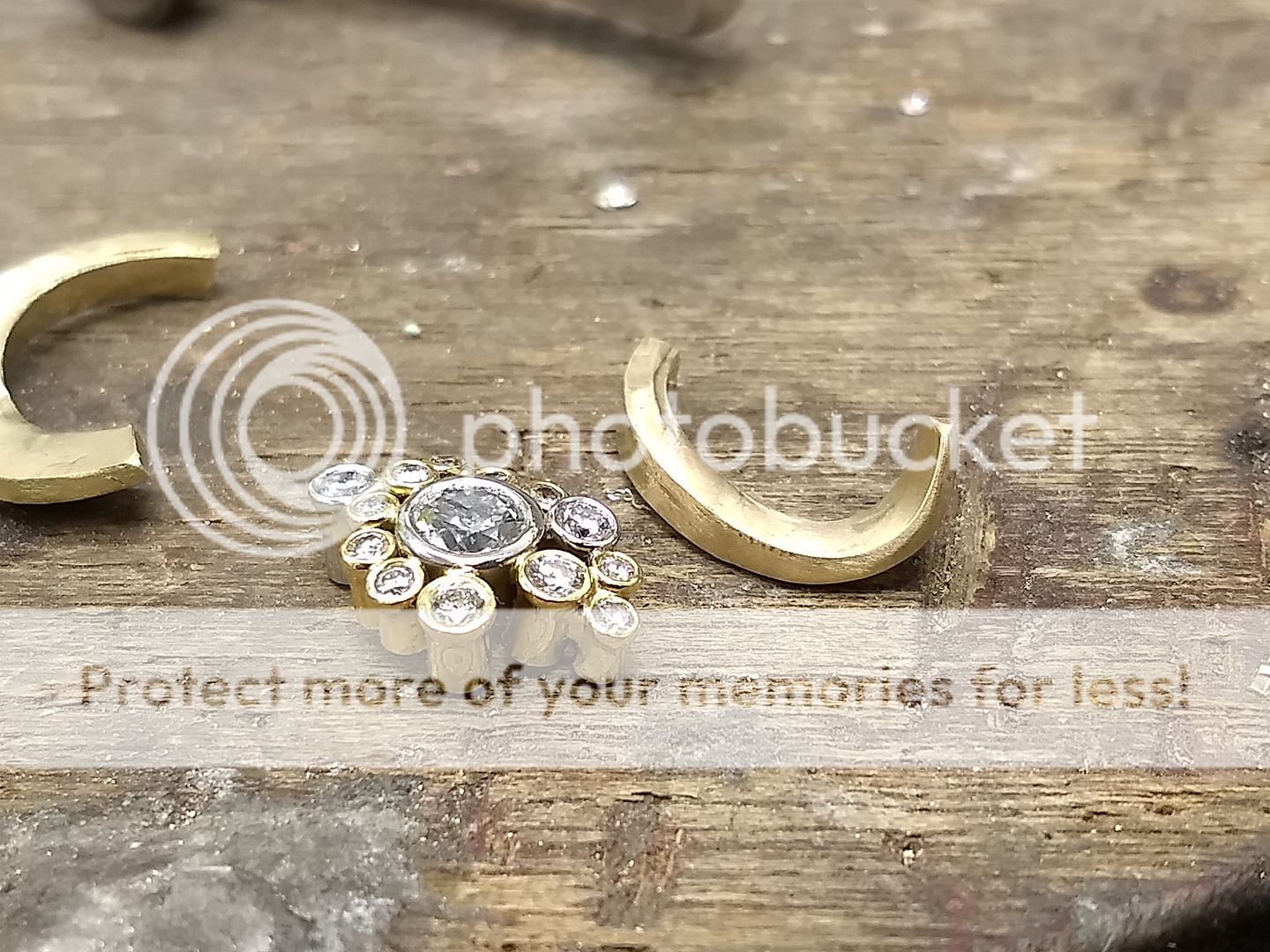
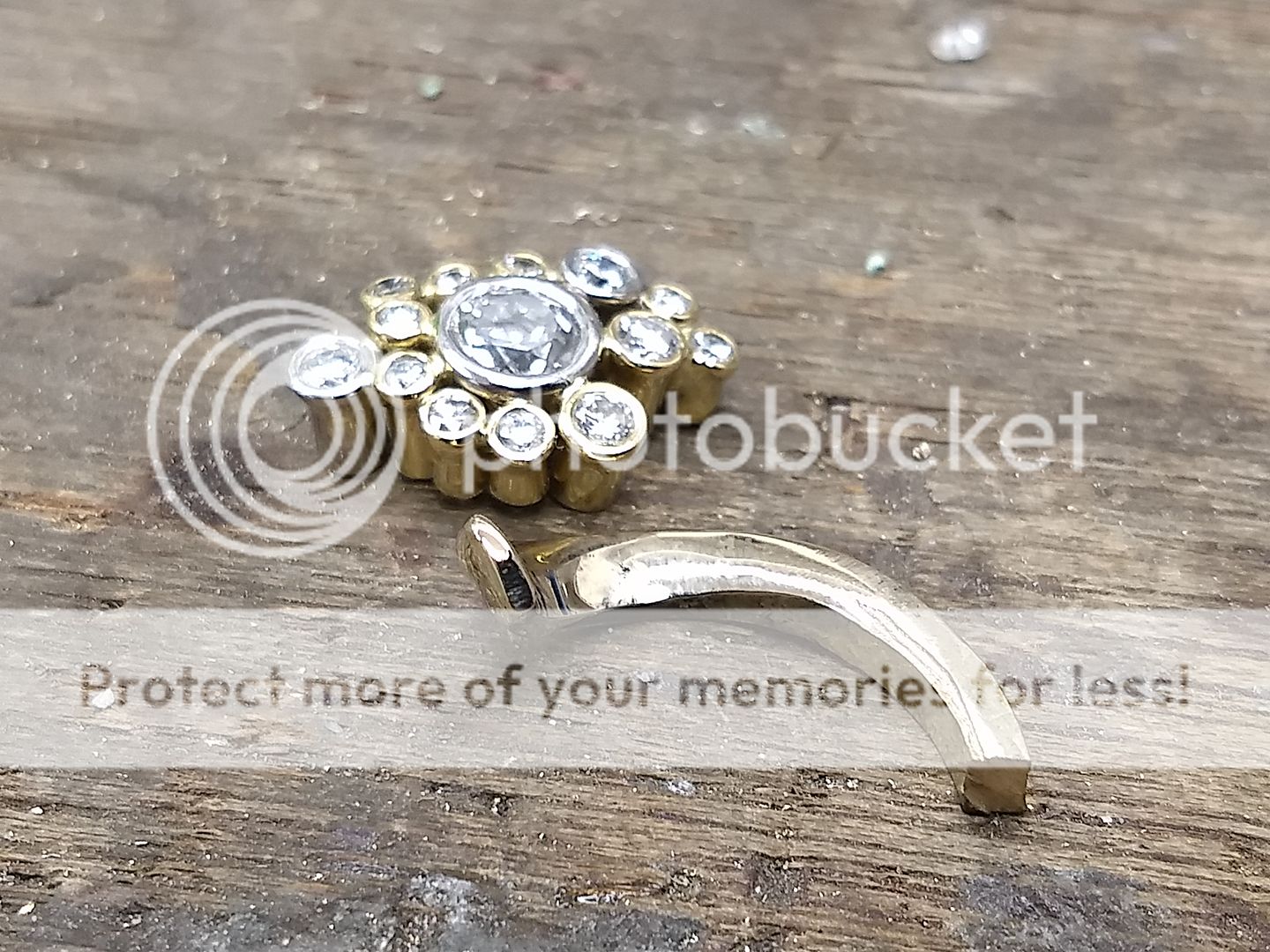
And it's then soldered in place:
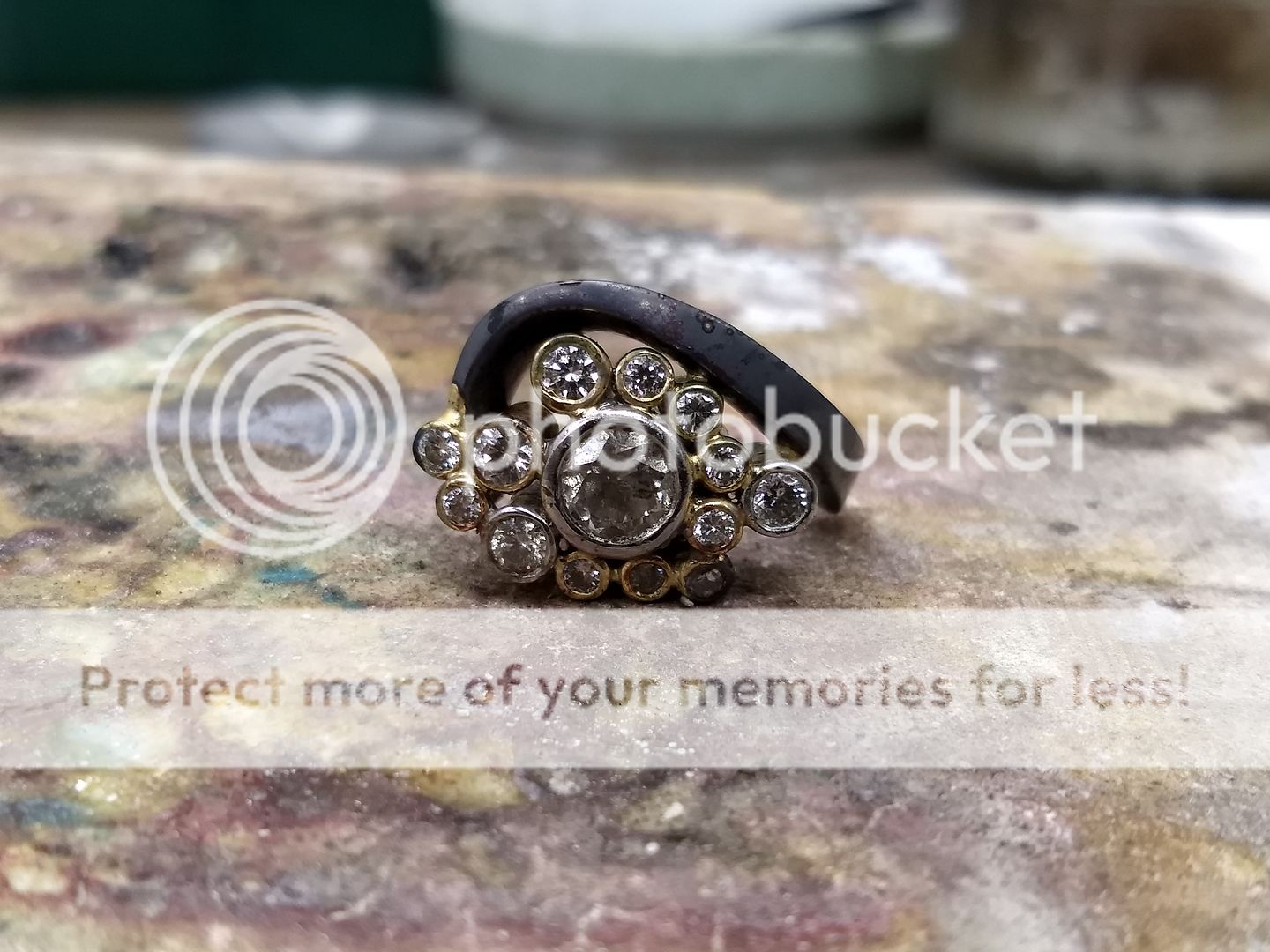
Shoulder number 2 is next:
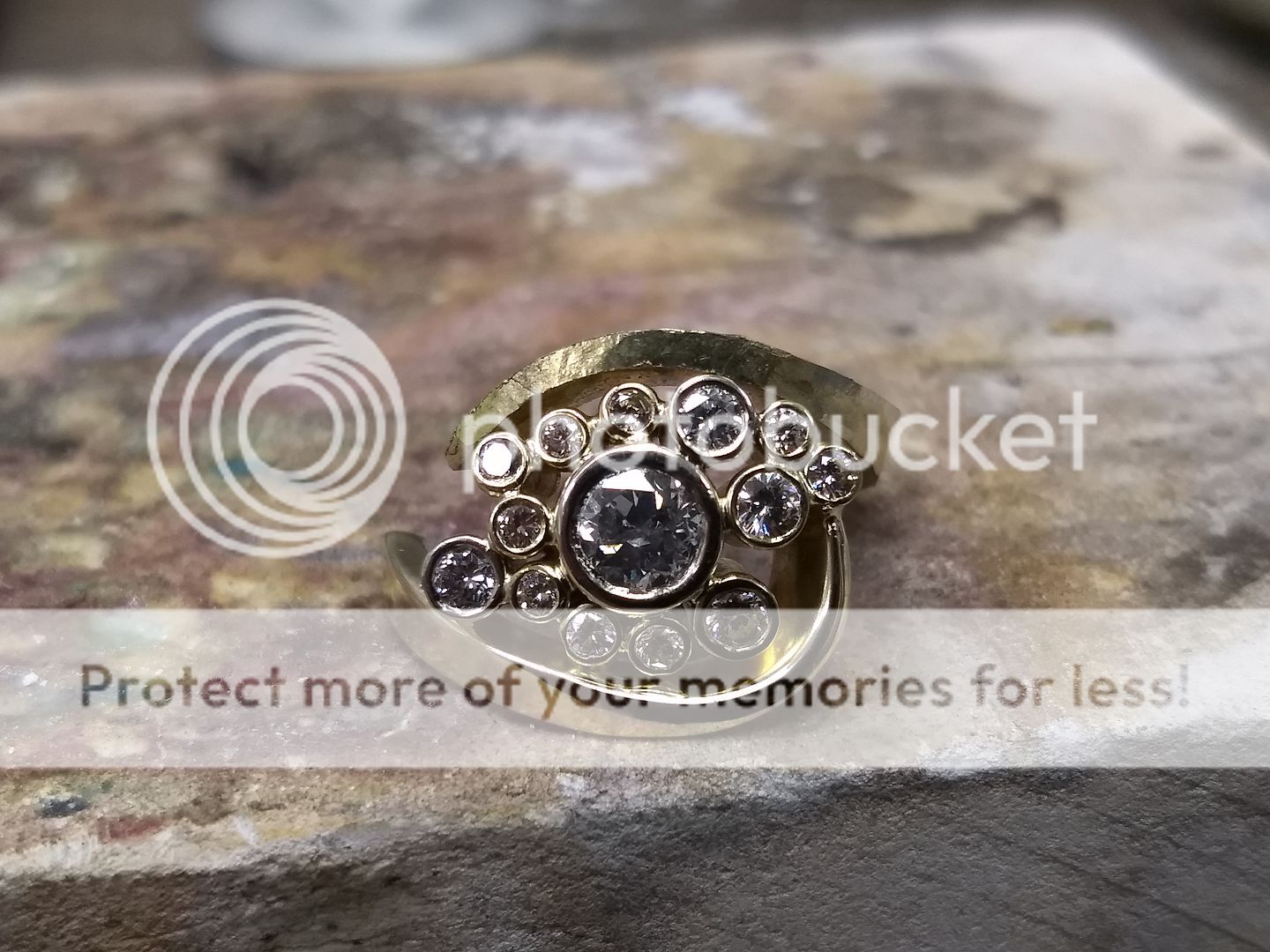
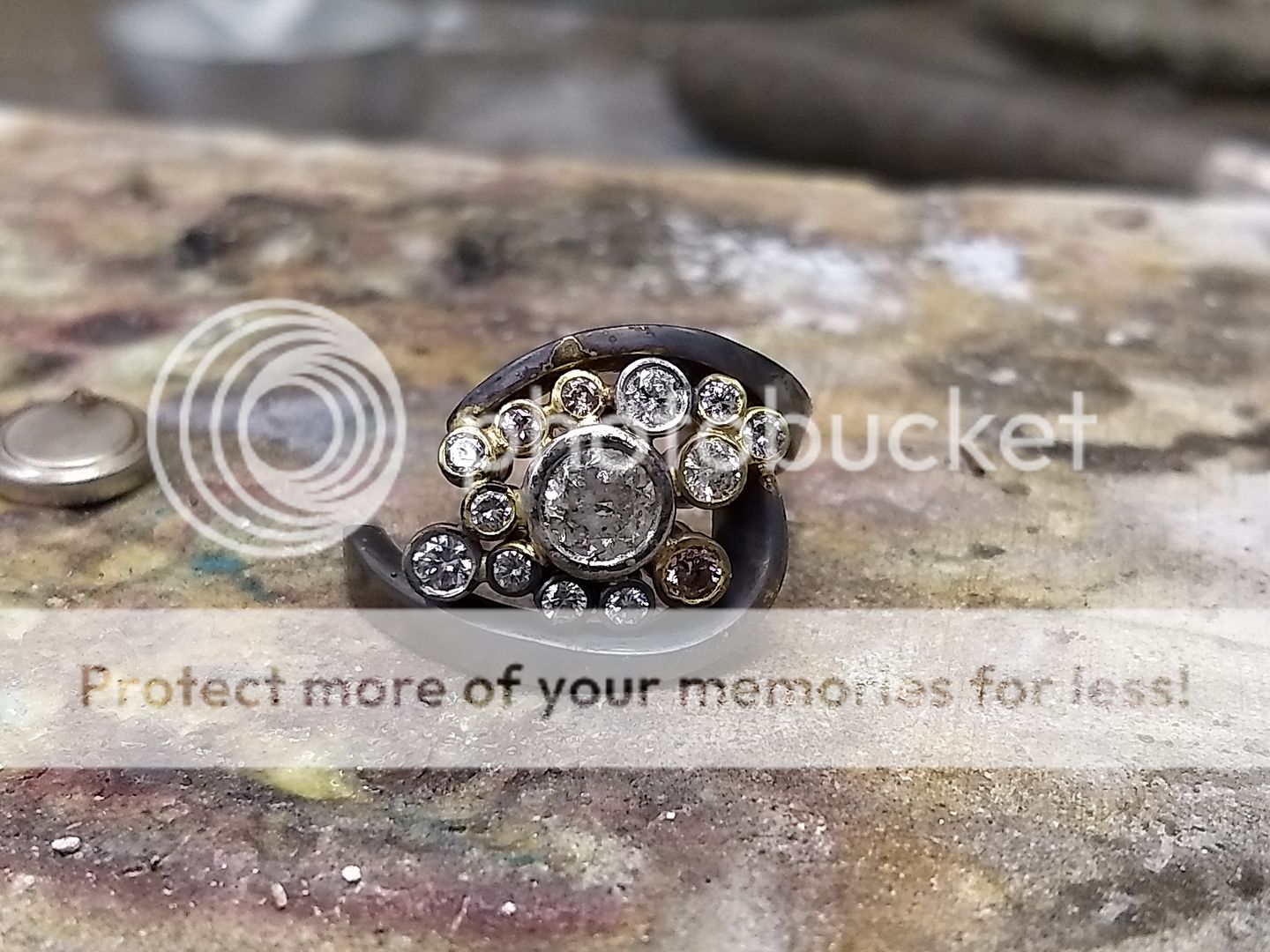
Almost looks like a ring now:
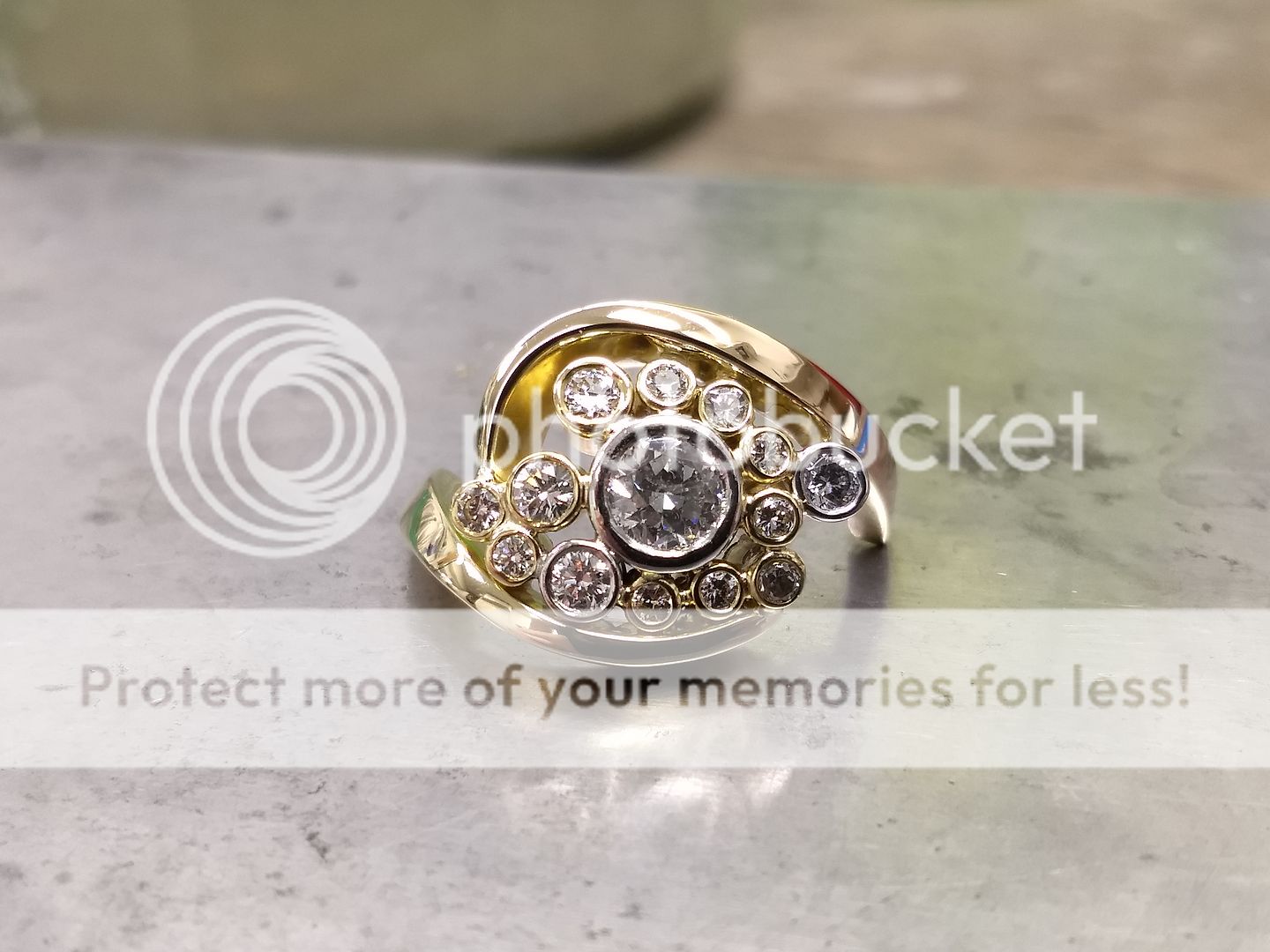
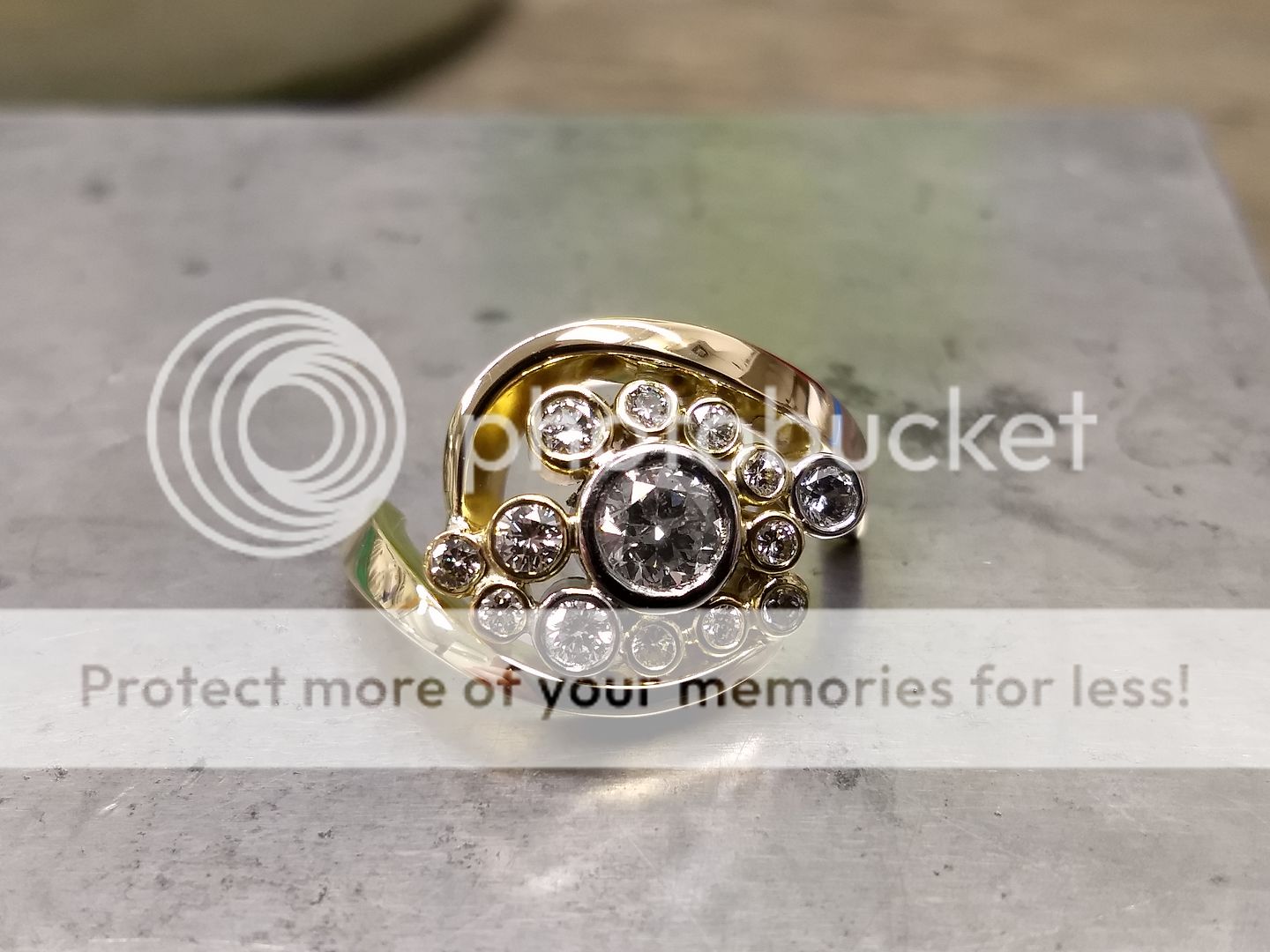
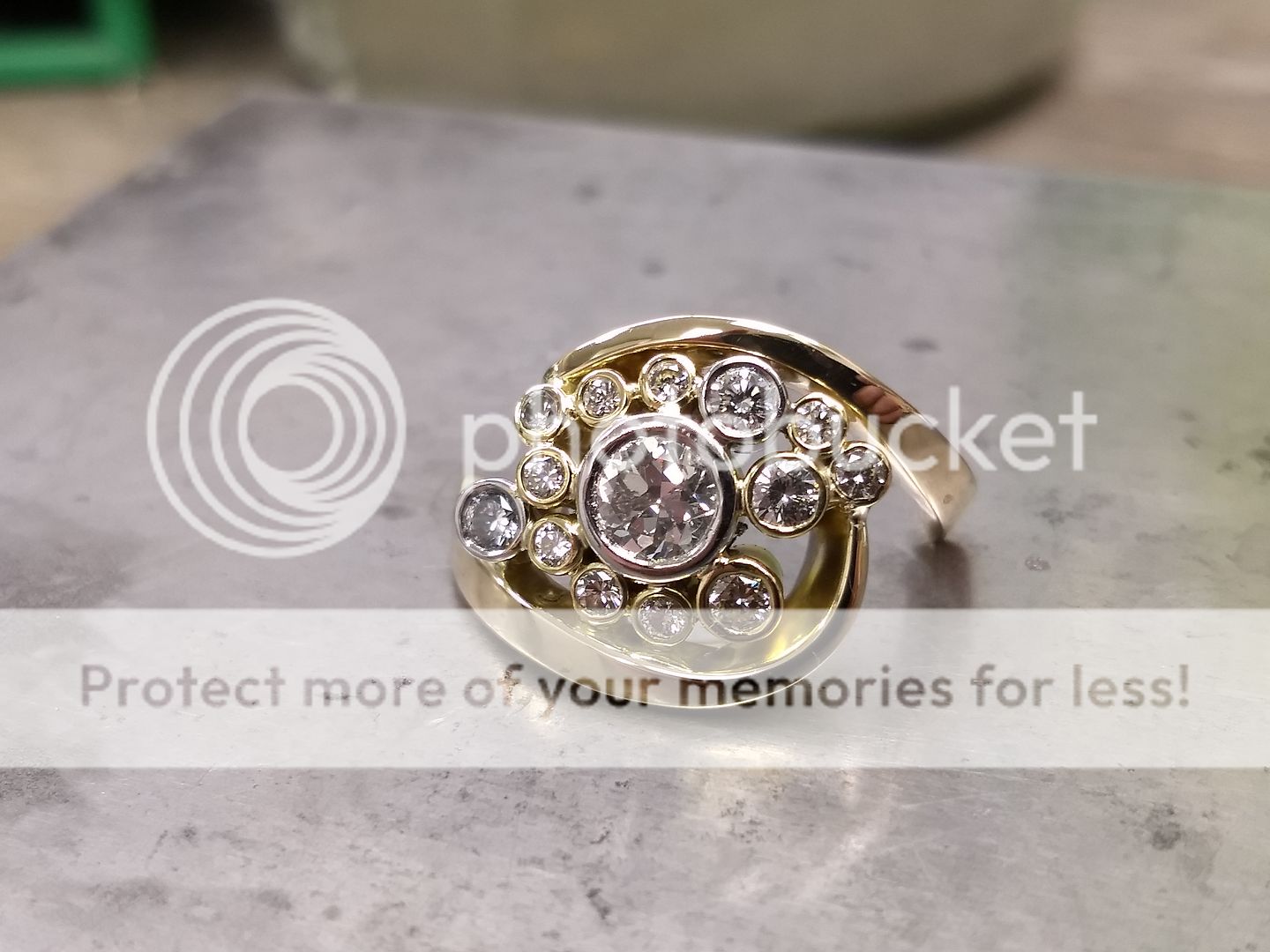
The remaining bar is then rolled out and marked with the material content.
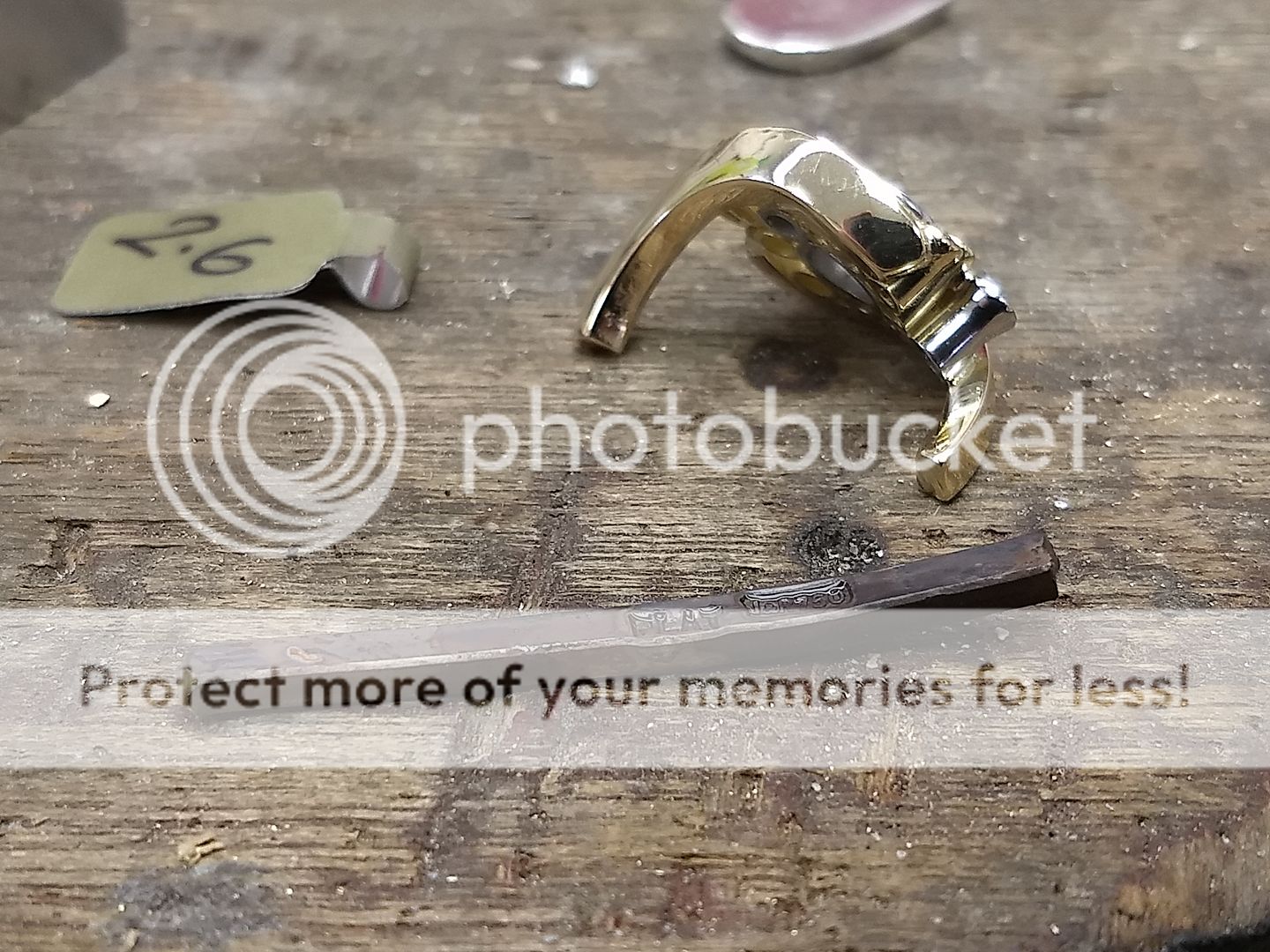
Using a digital gauge I worked out she's roughly a size N at the finger (not the knuckle) so bent the new shank to suit:
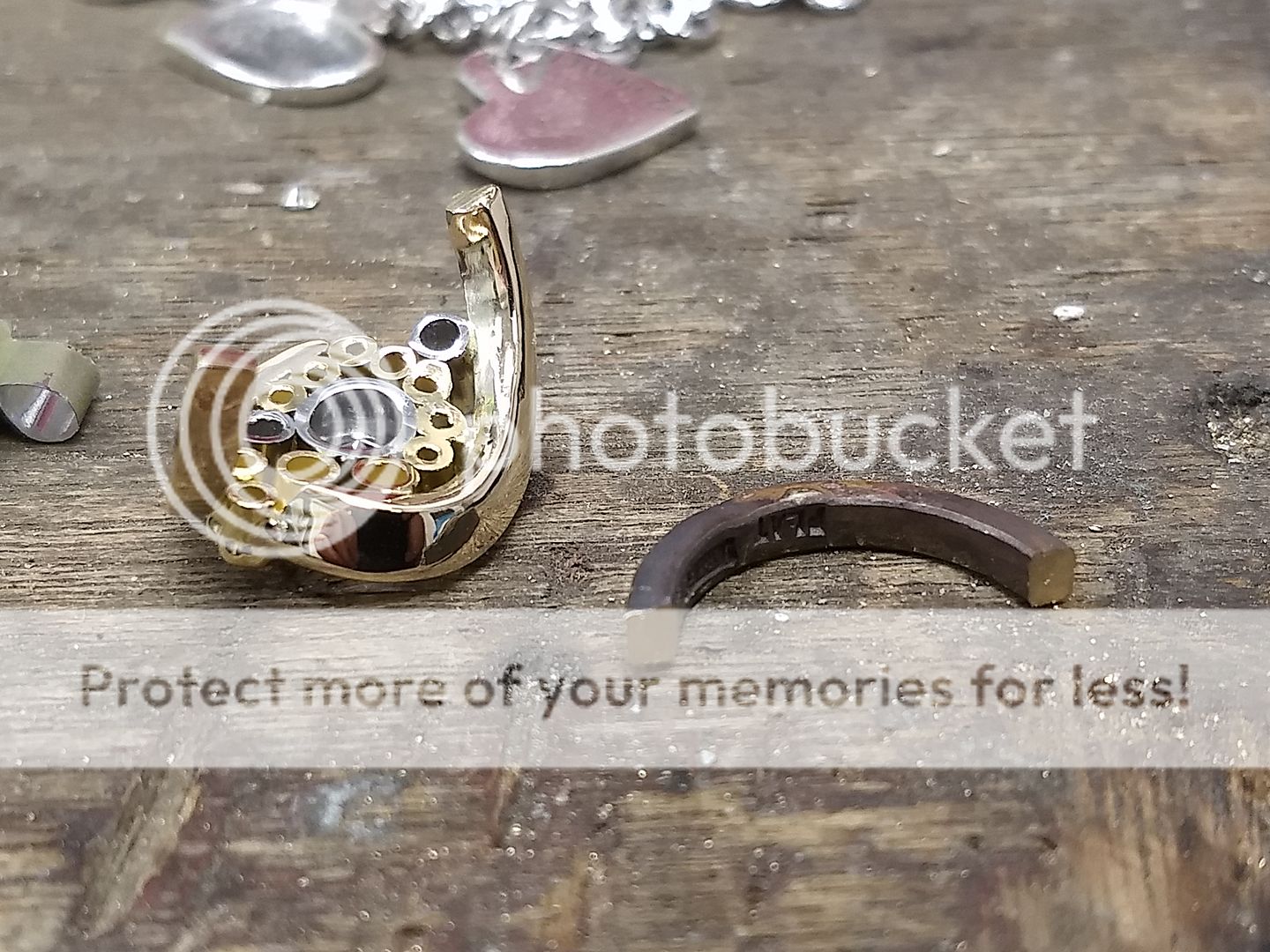
And then soldered it to the head so I could hammer it to the correct shape all round:
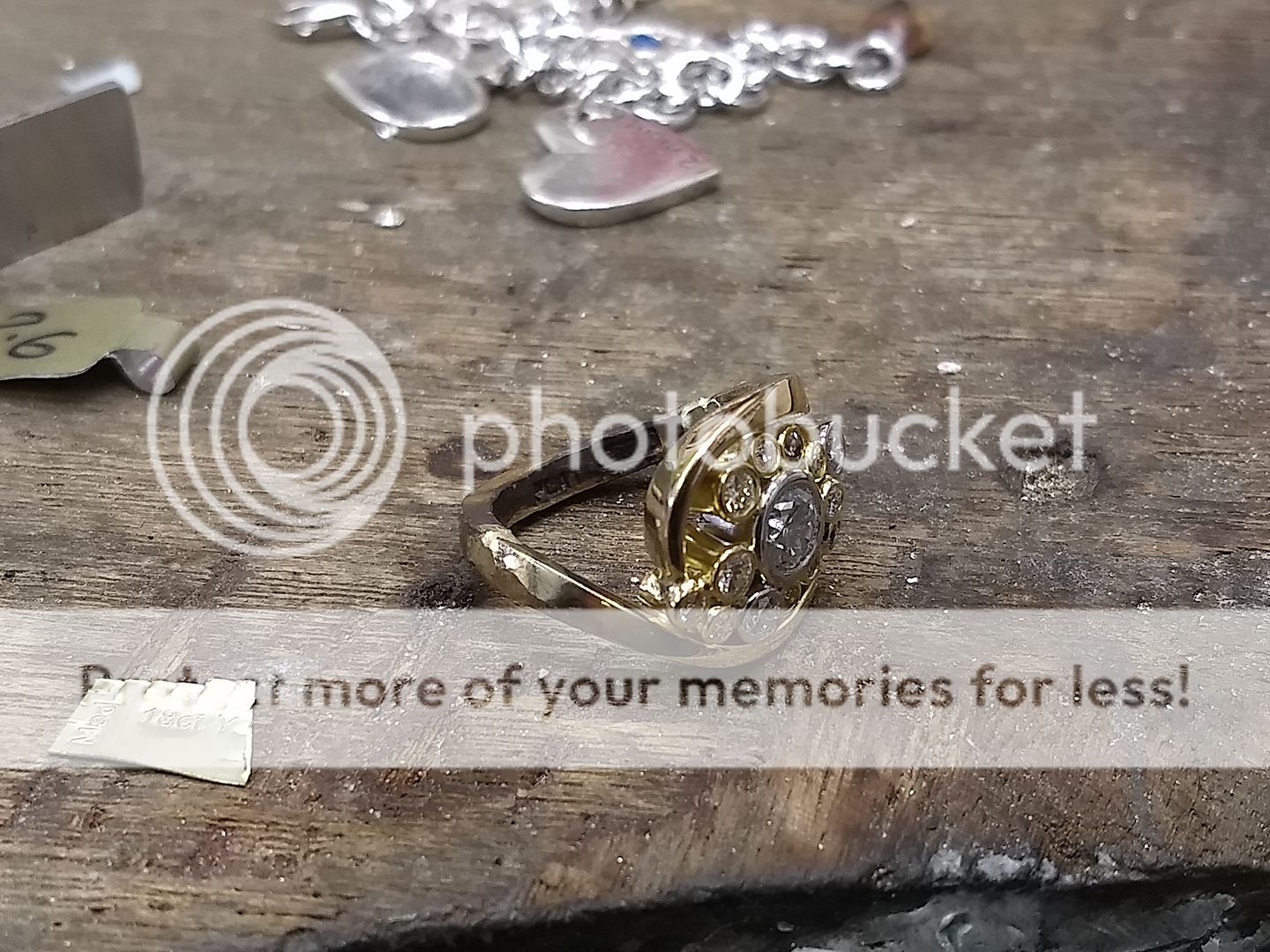
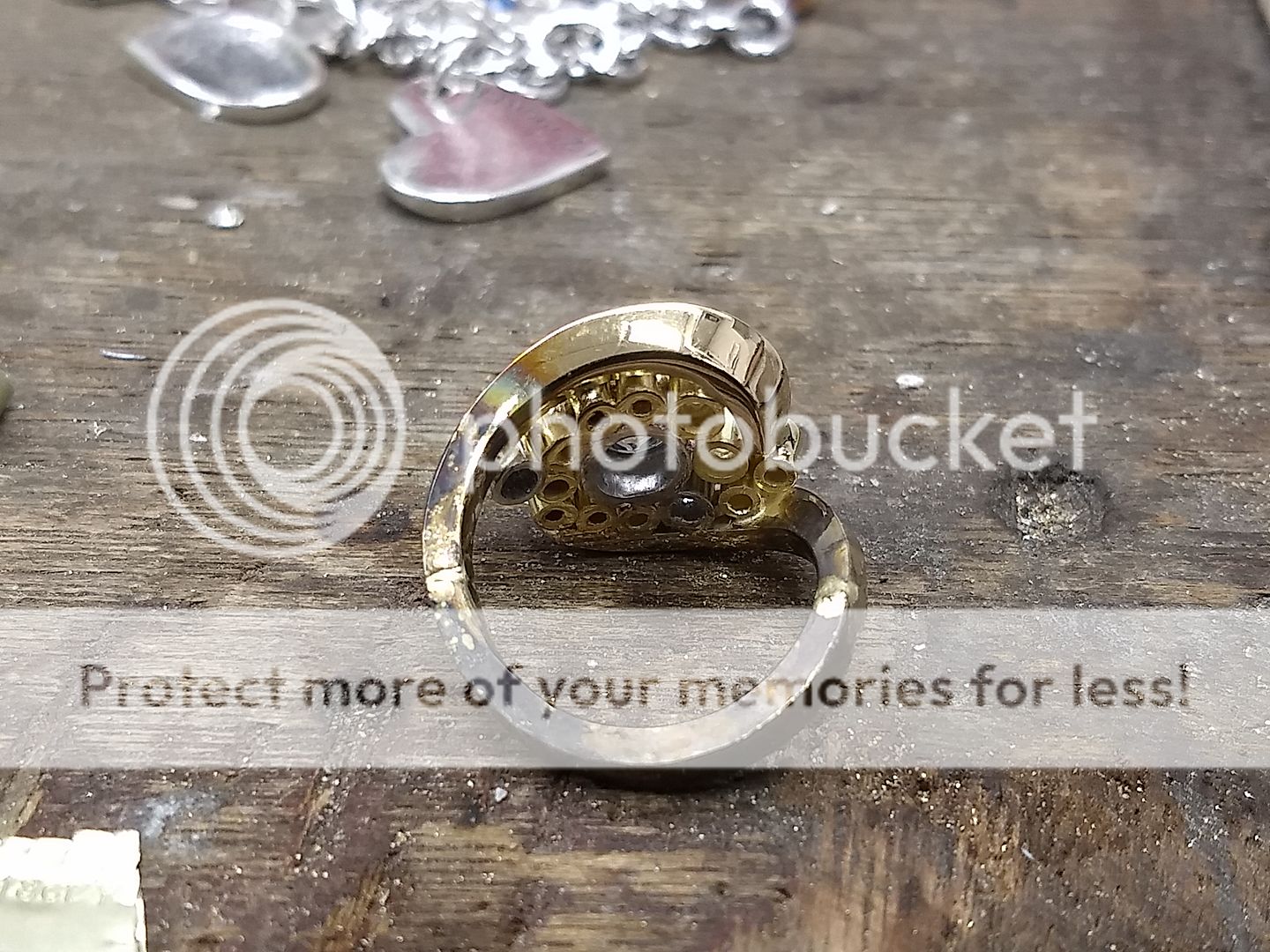
Now, obviously the ring won't go over her knuckle like this so I had to spend a while working out how the hell I was going to get it to fit. The clear answer was to hinge it, but how do we then secure the other end and make it durable?? Here's the hinge first:
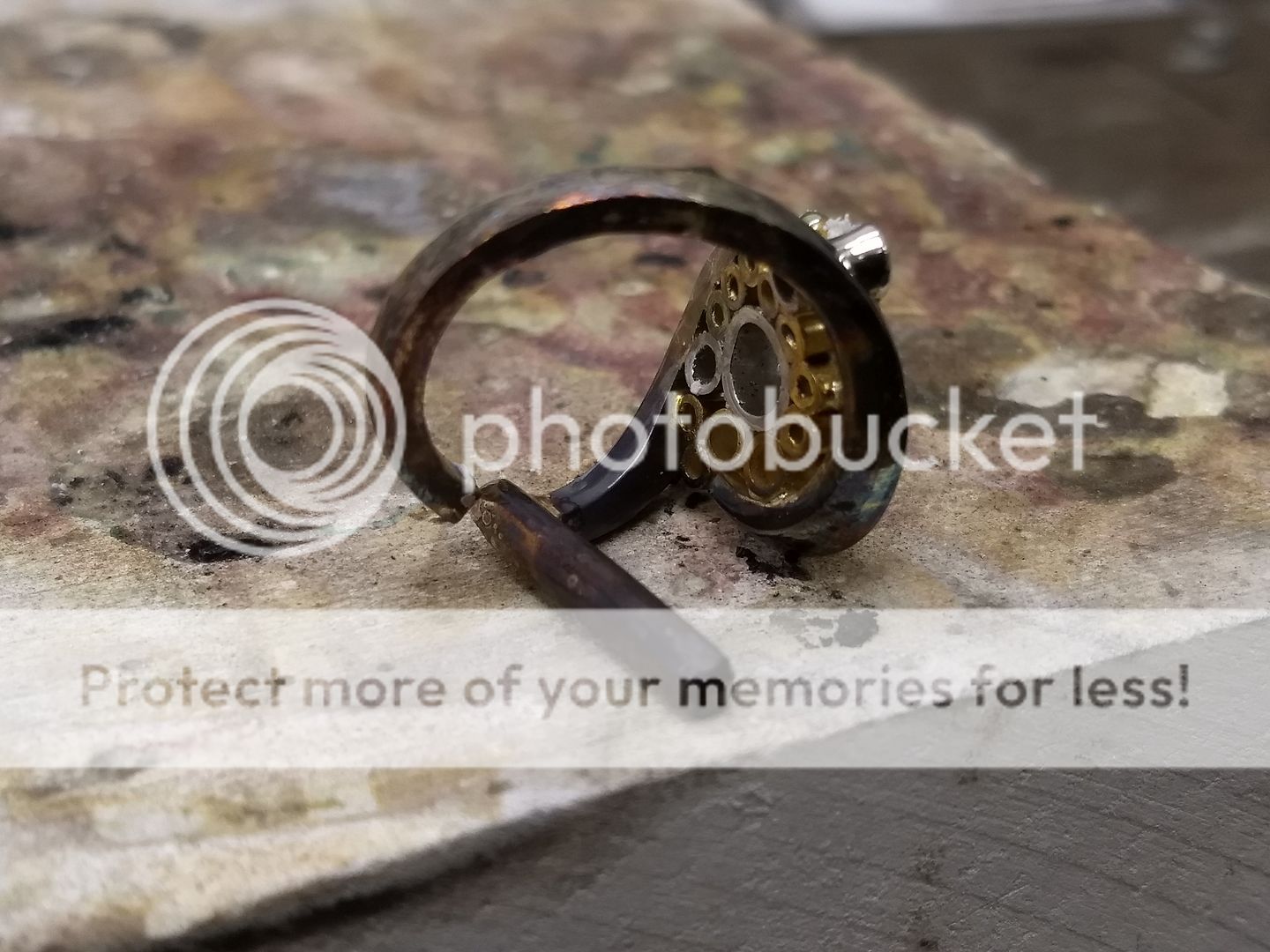
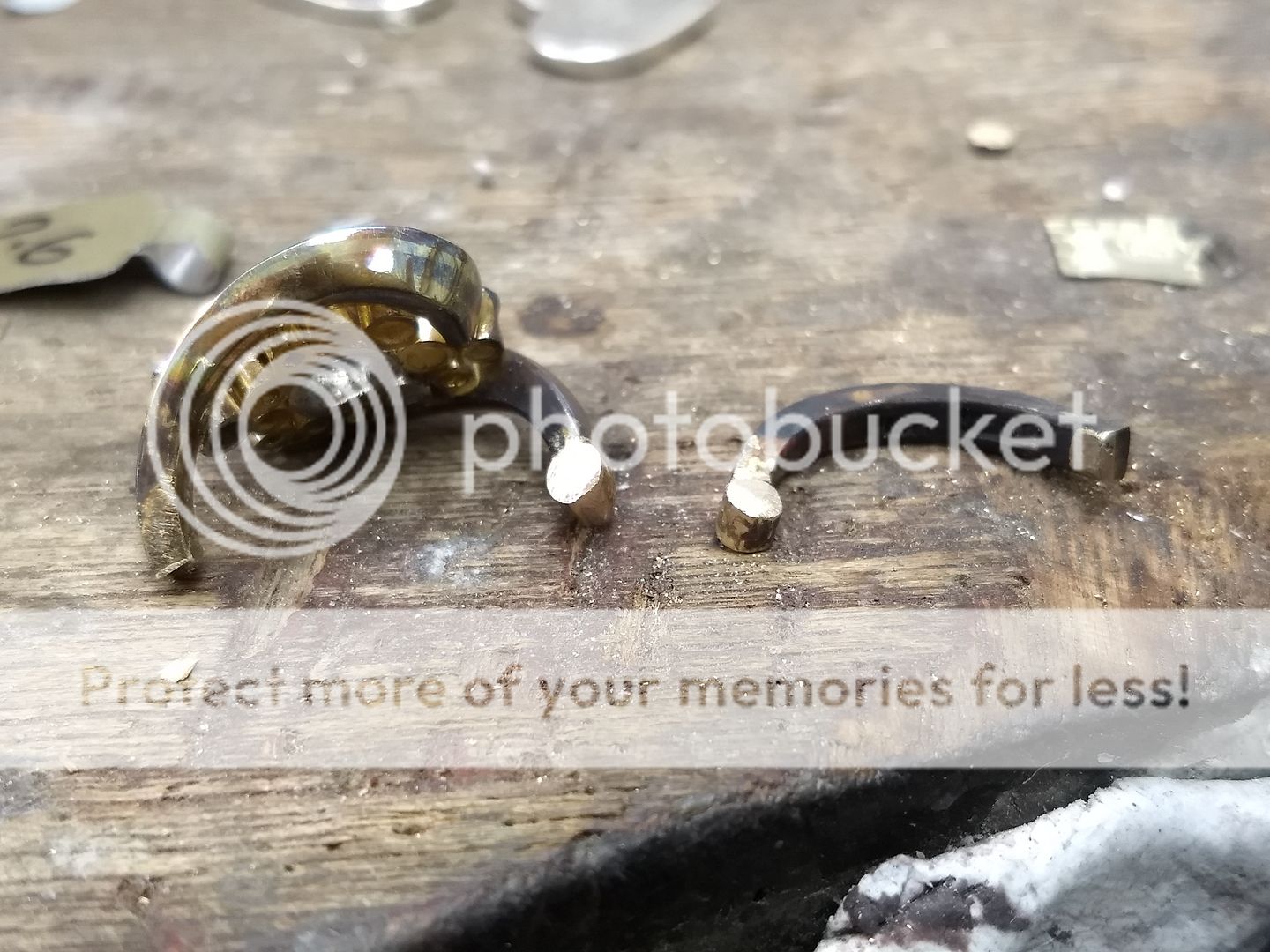
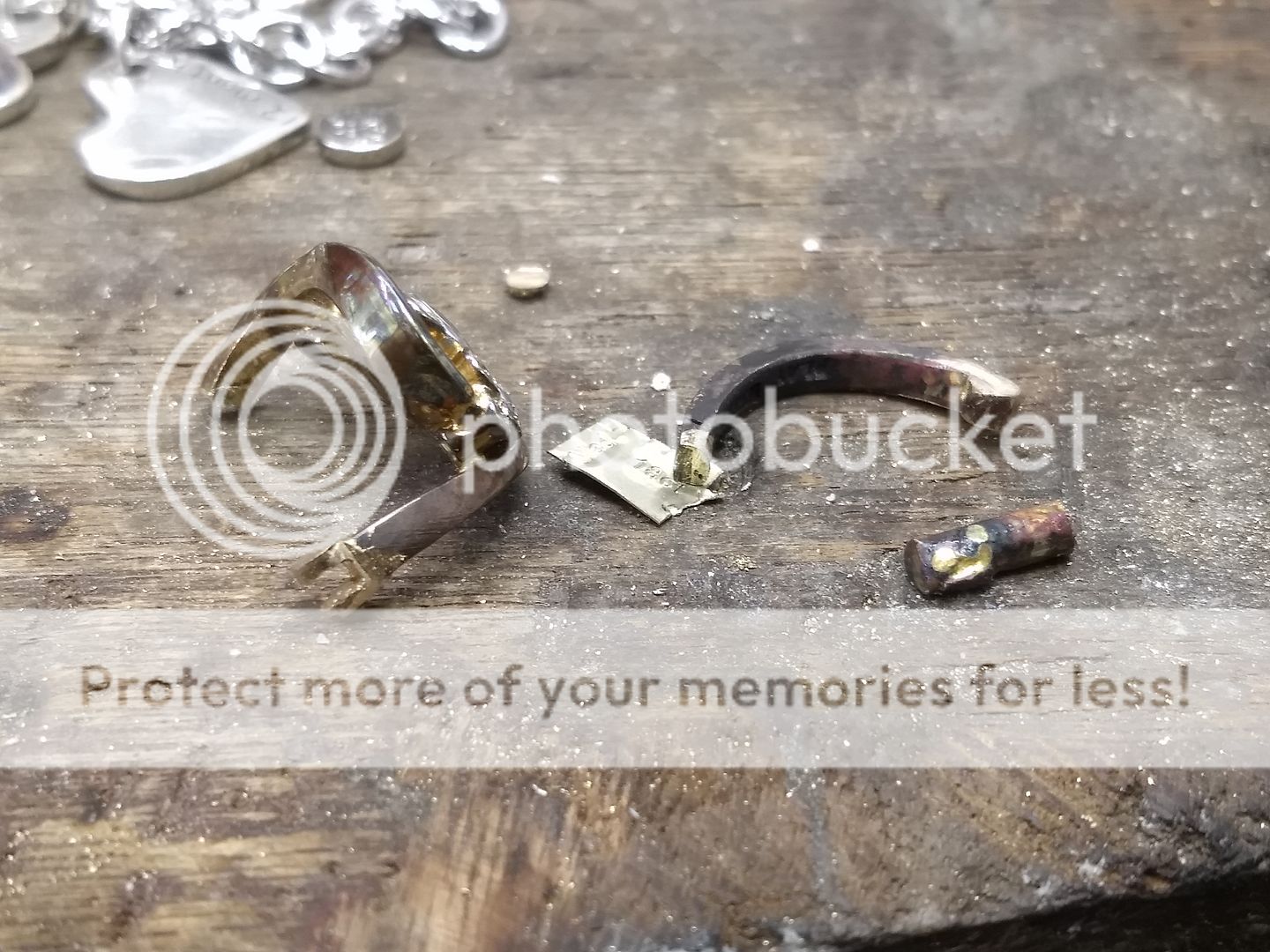
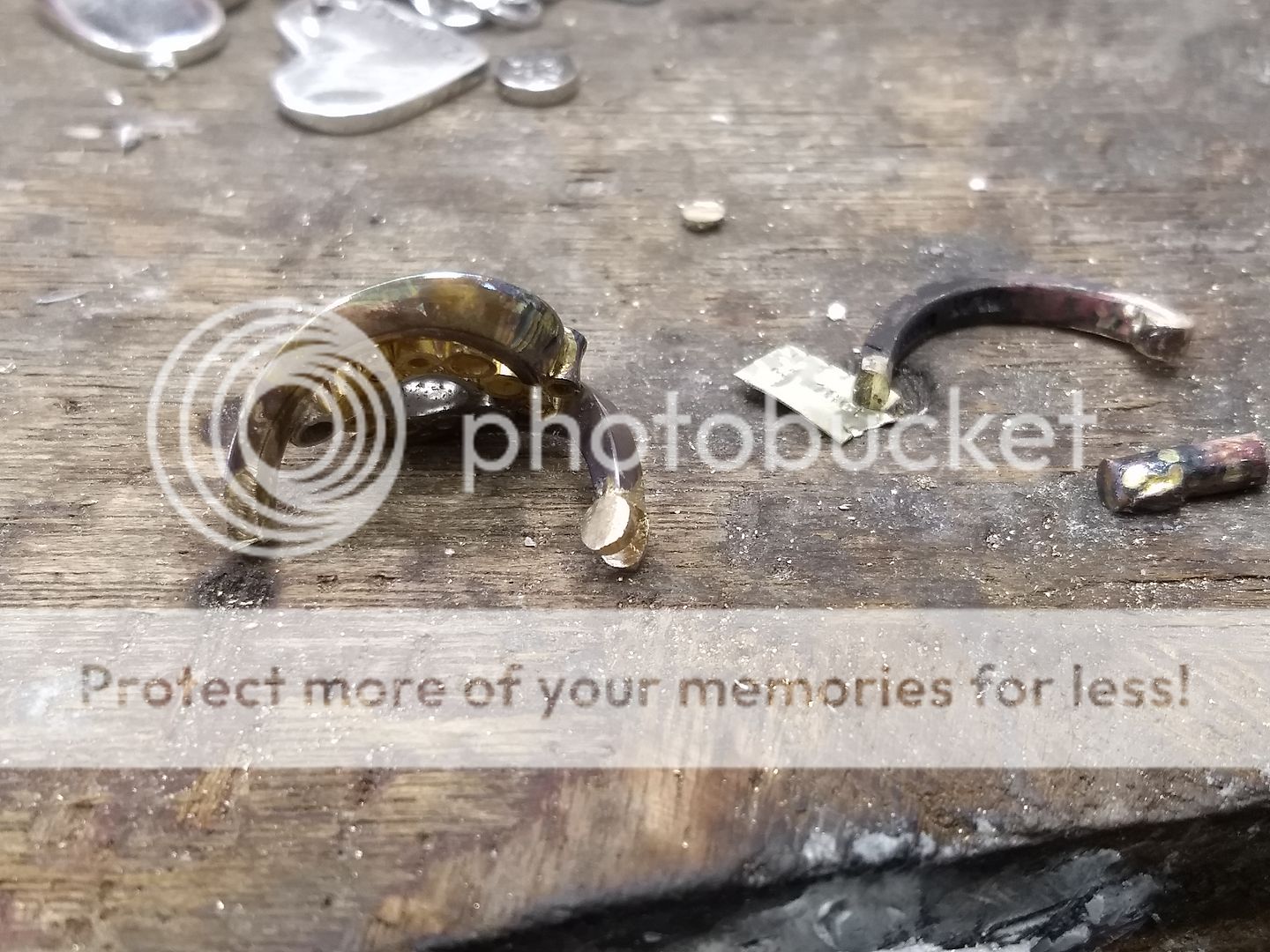
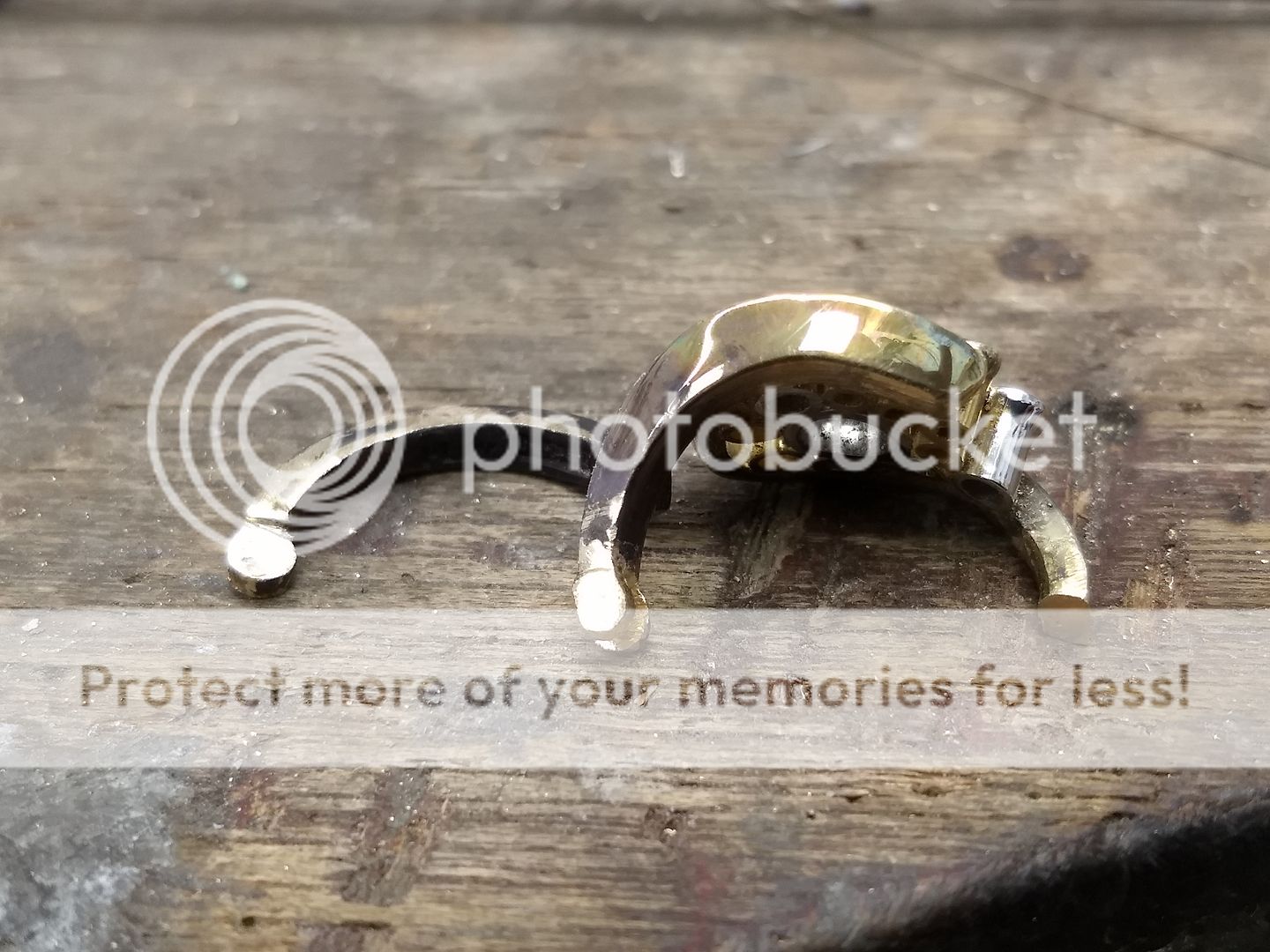
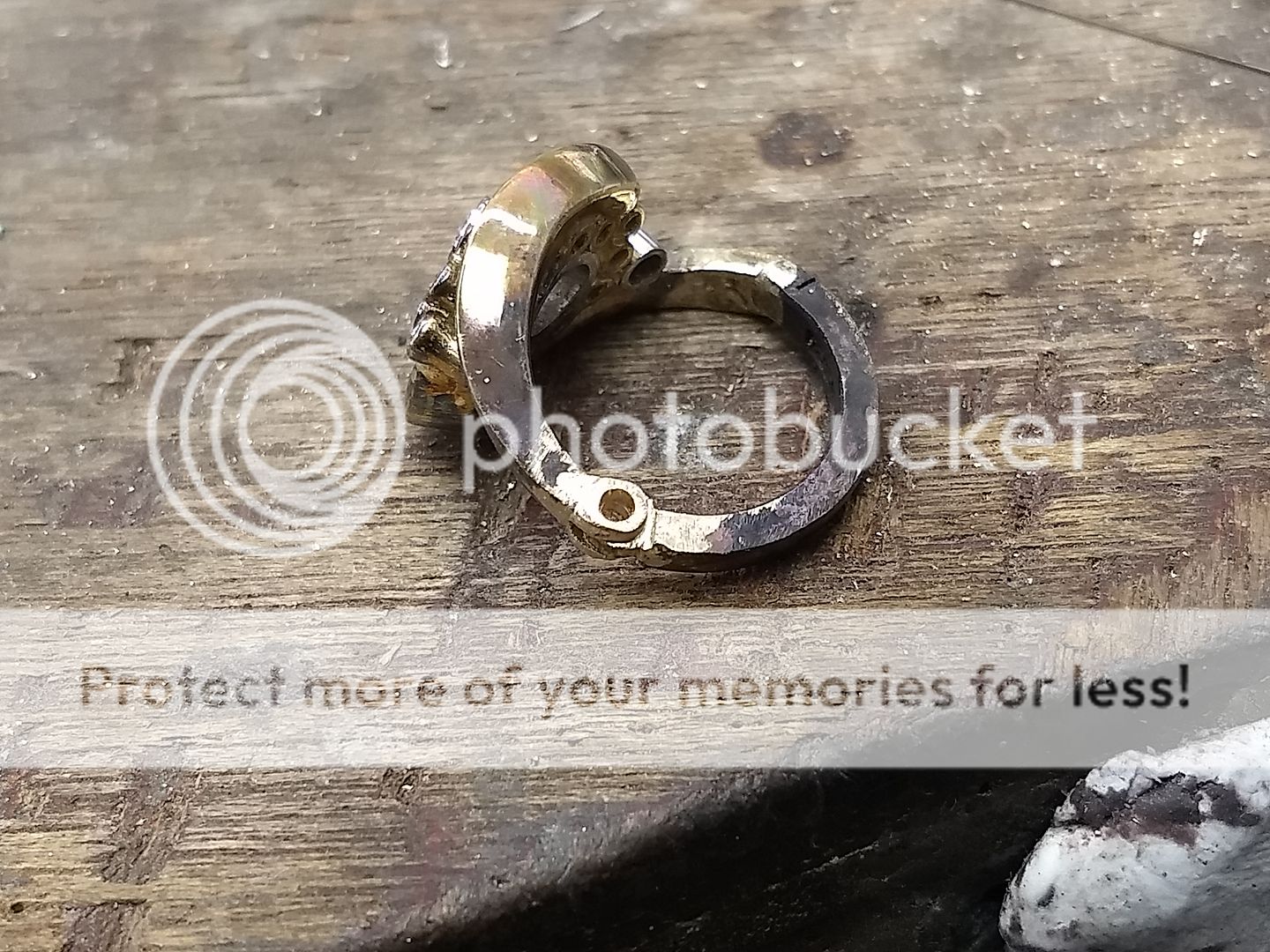
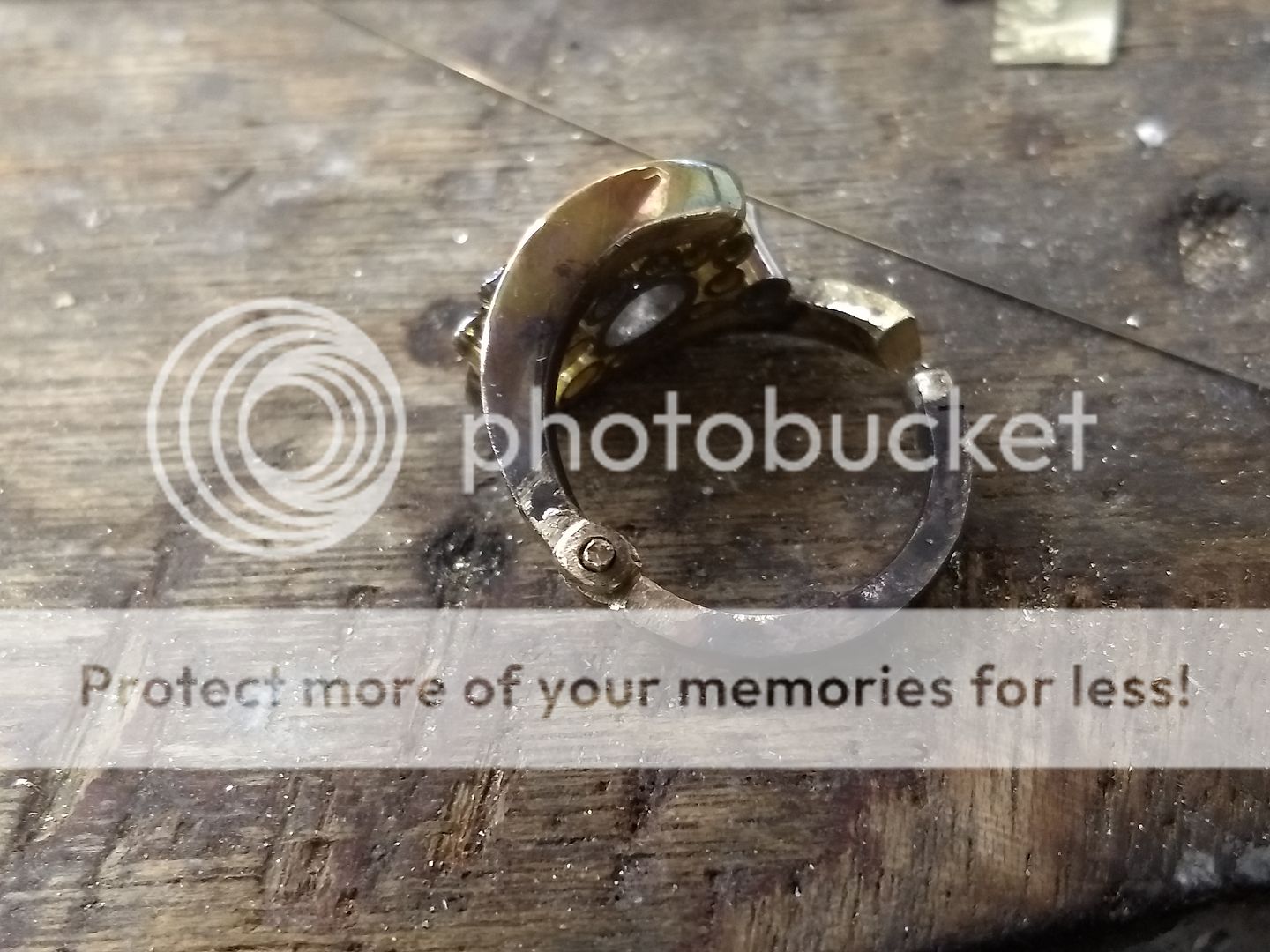
So, with the hinge fitted and functional what do we do about the other end? The shank is curved and doesn't come together in a way that a catch would work.... not reliably anyway. The only way to do it without worrying is to screw it shut. The solution: Make another hinge at the other end, but an angled one to allow for the way it closes and then instead of a hinge pin I'll use a grub screw to secure it. At this point it's trial and error but it's my best hope

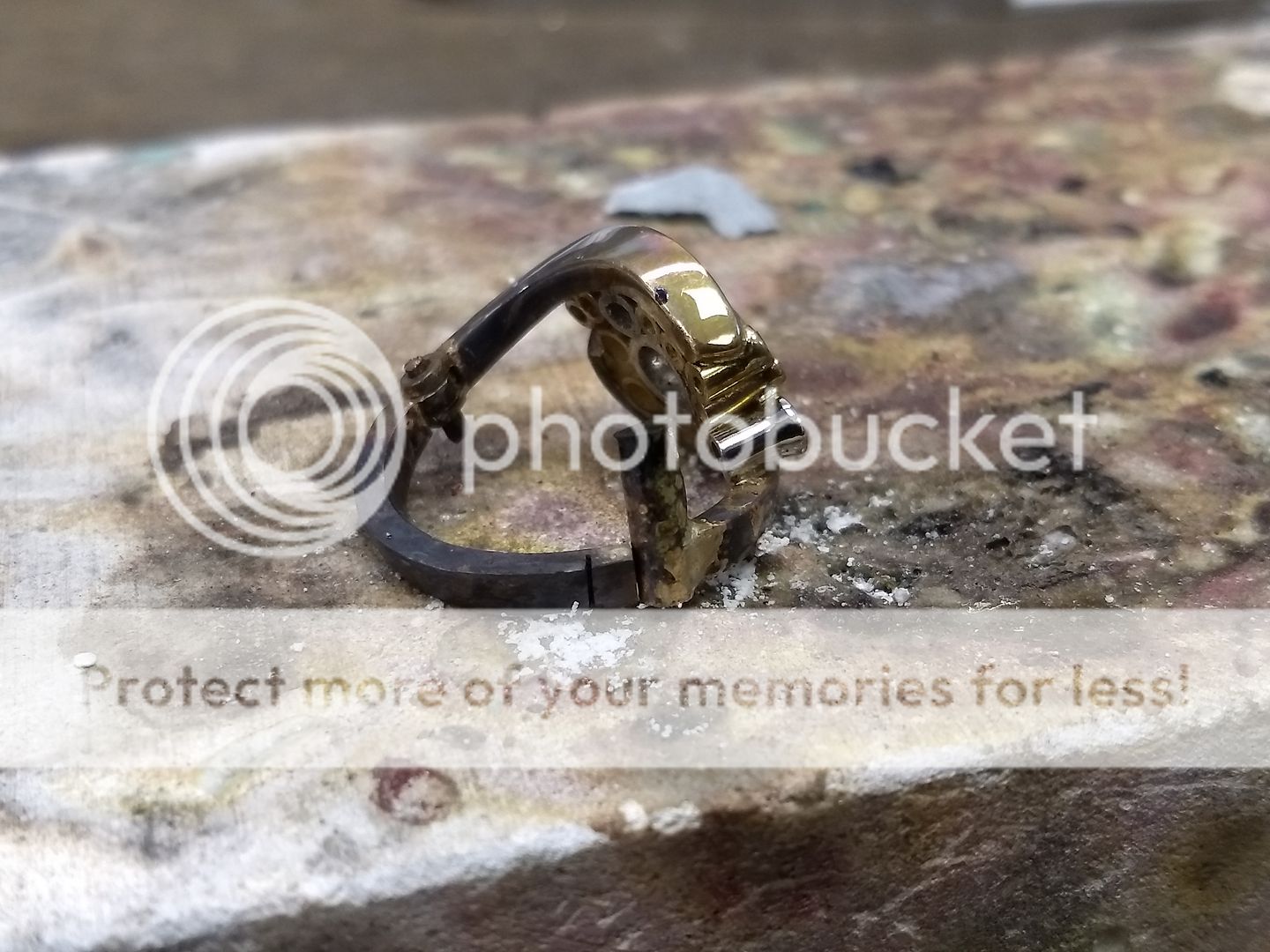
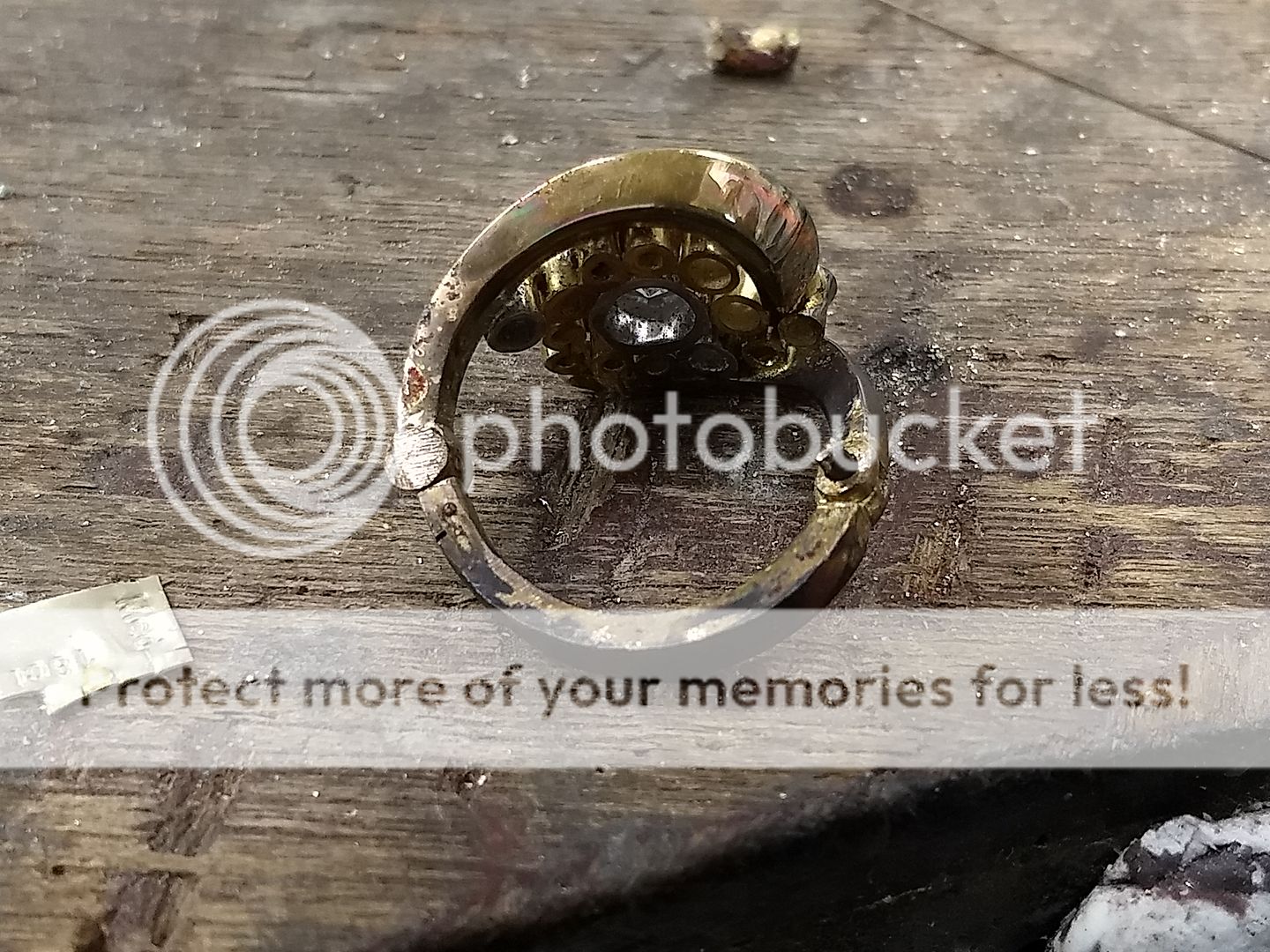
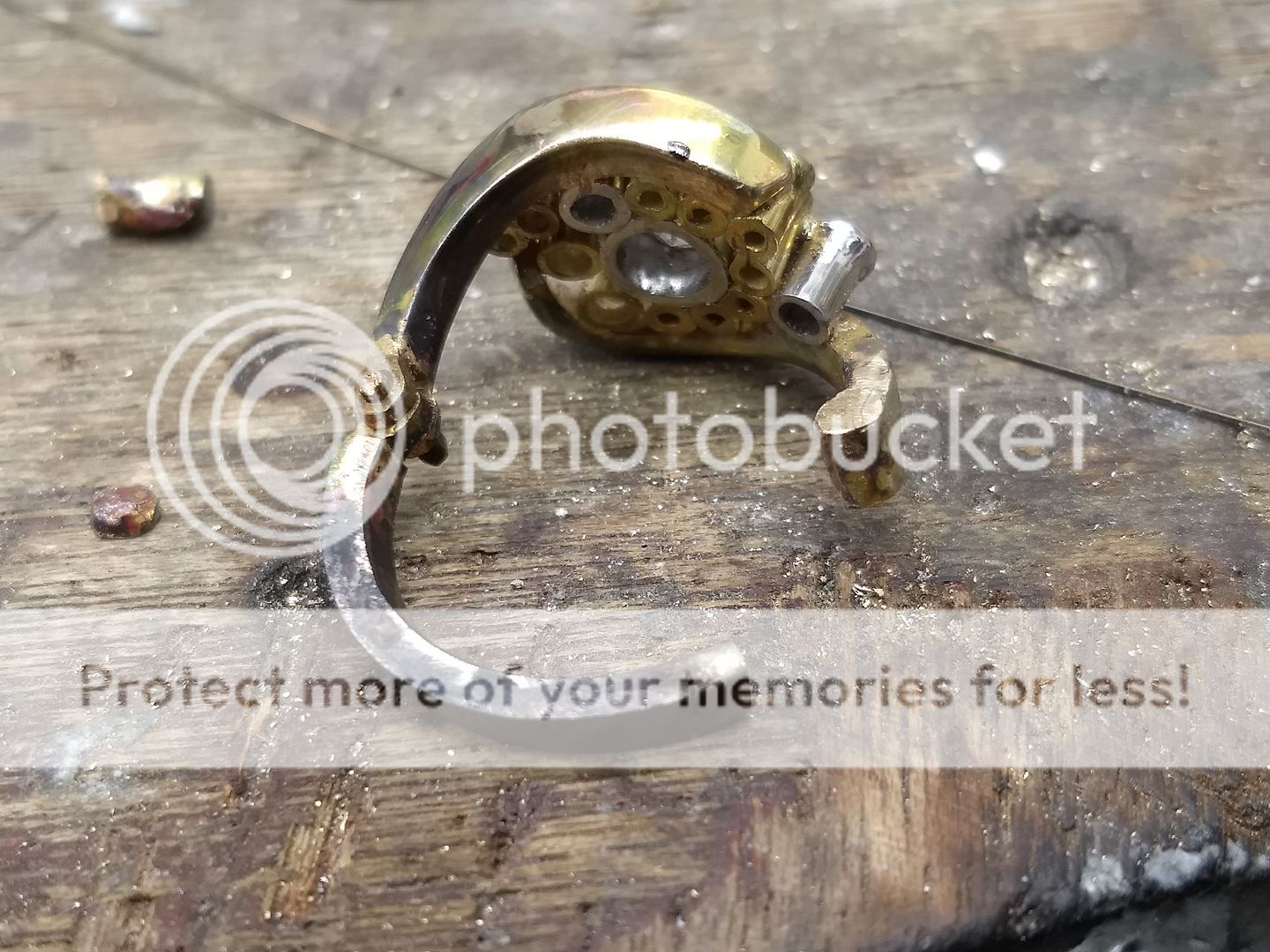
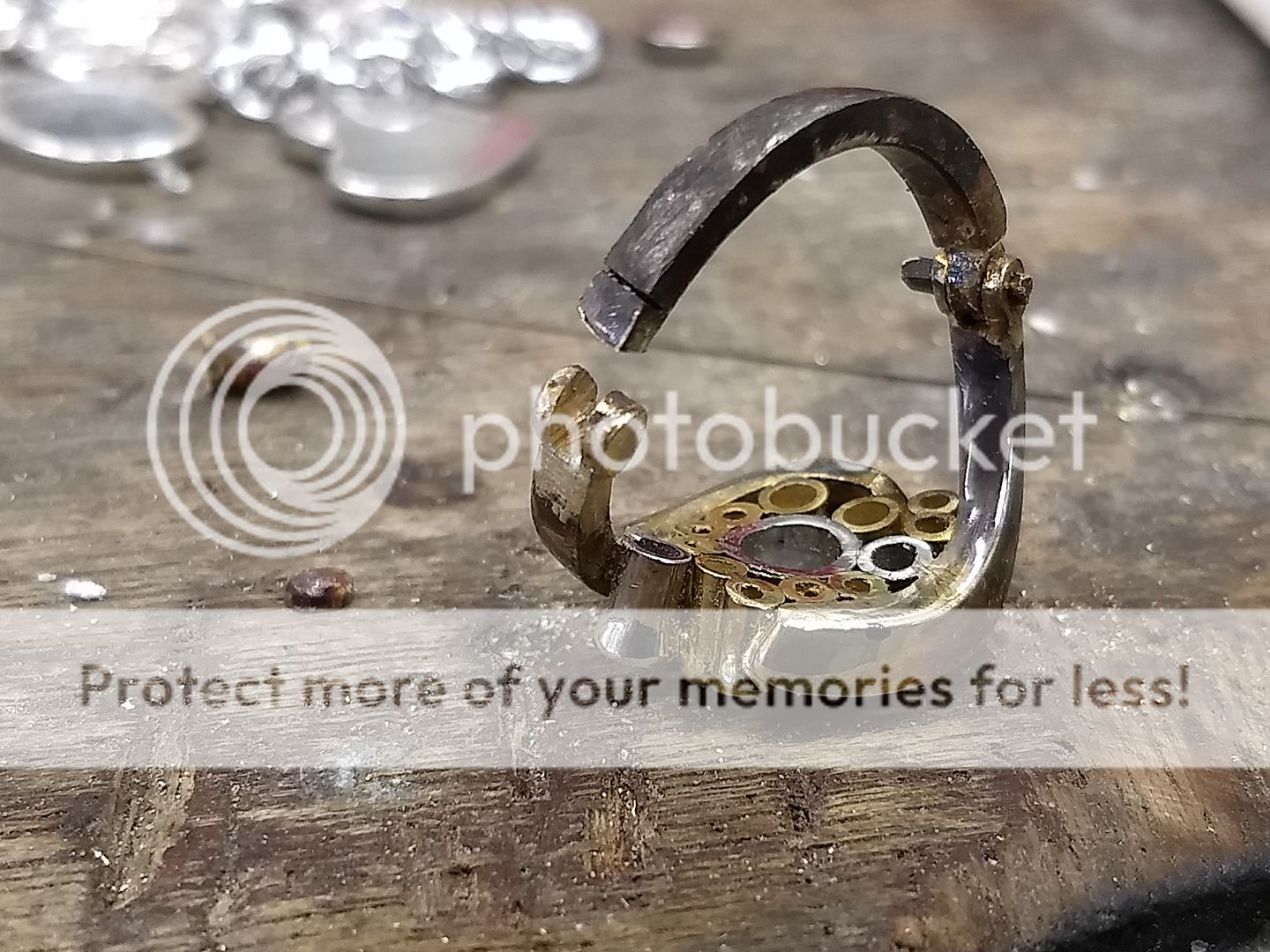
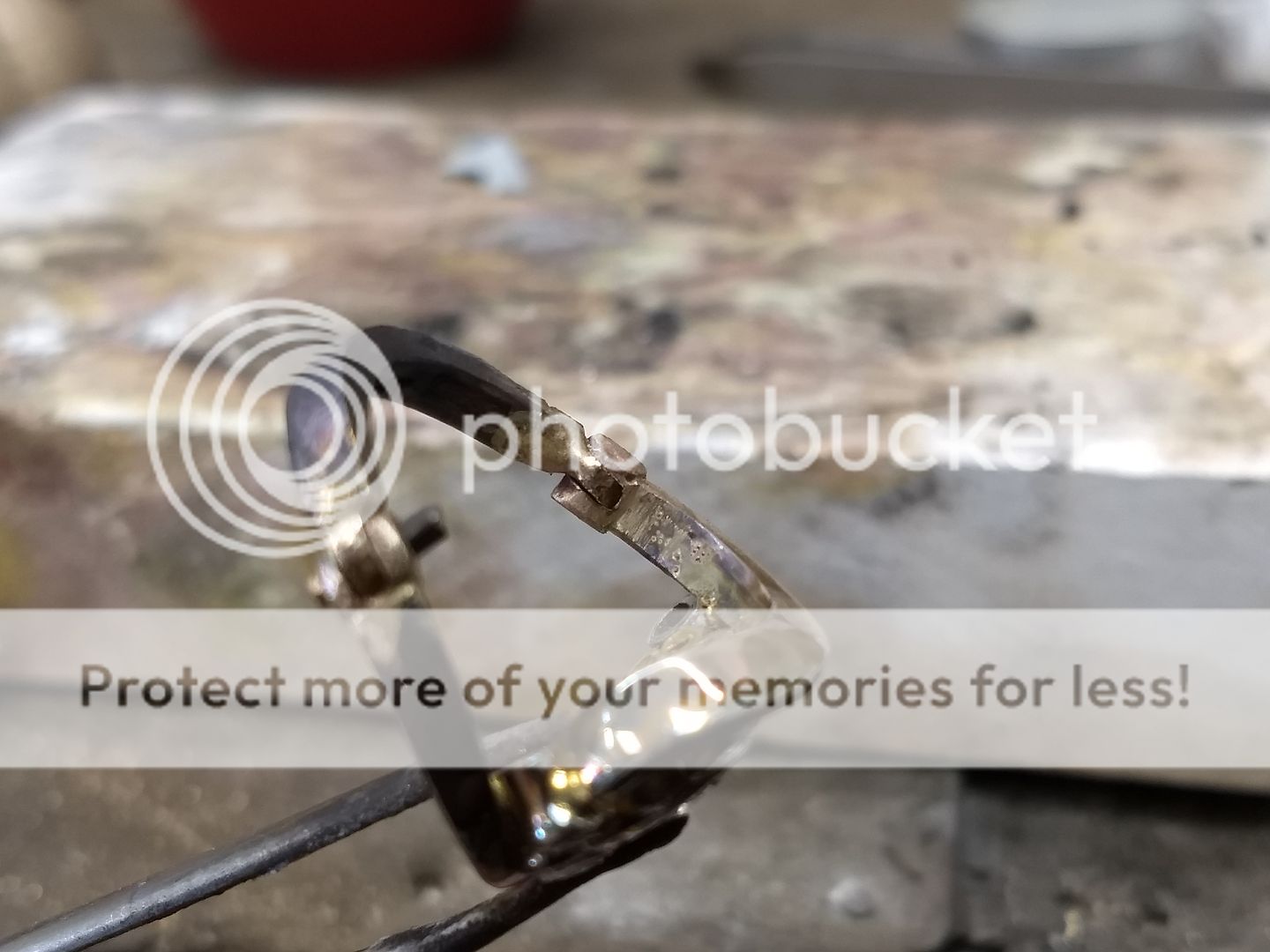
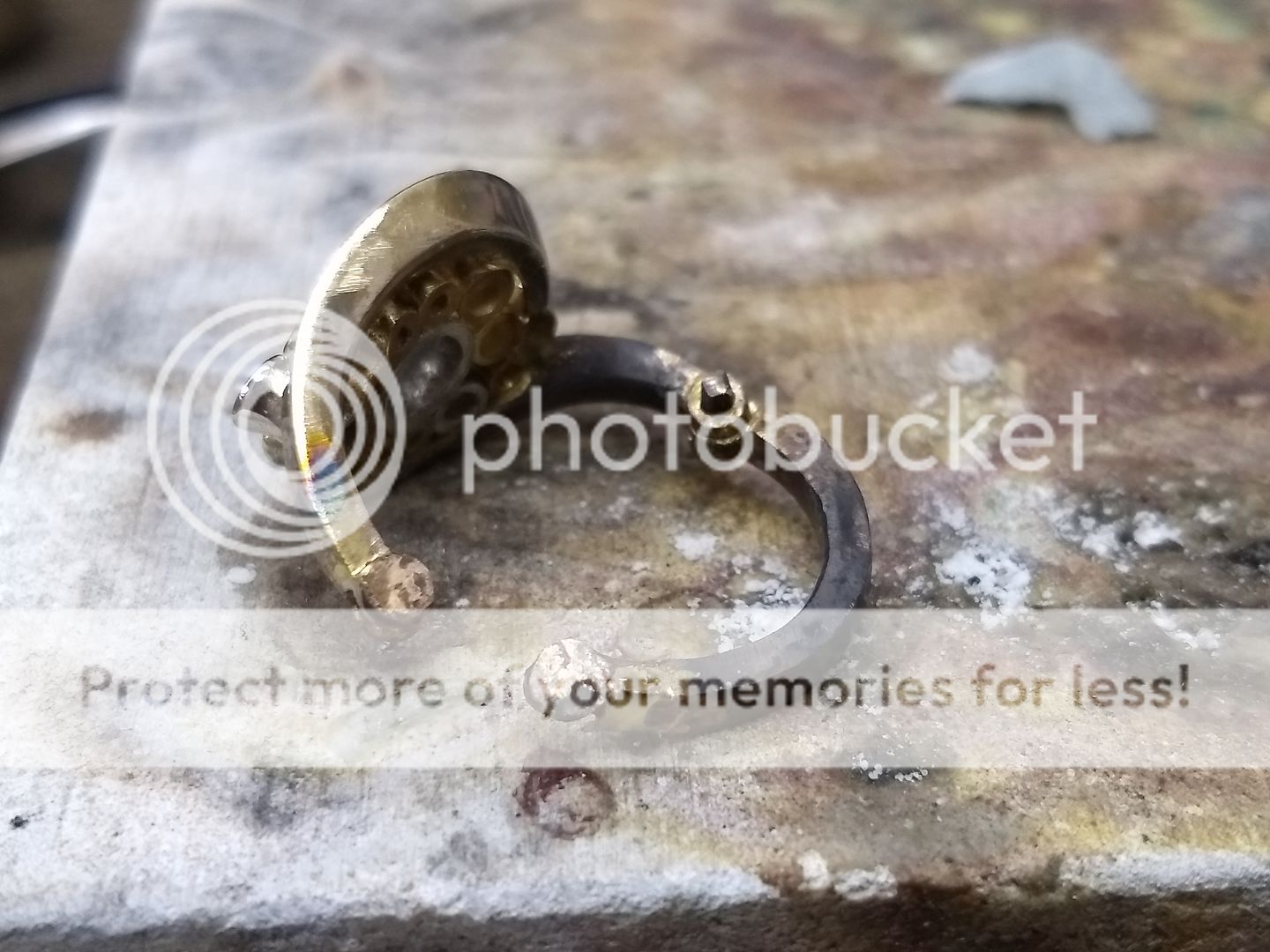
The hole is drilled only 4/5 the way through to stop the screw coming out.
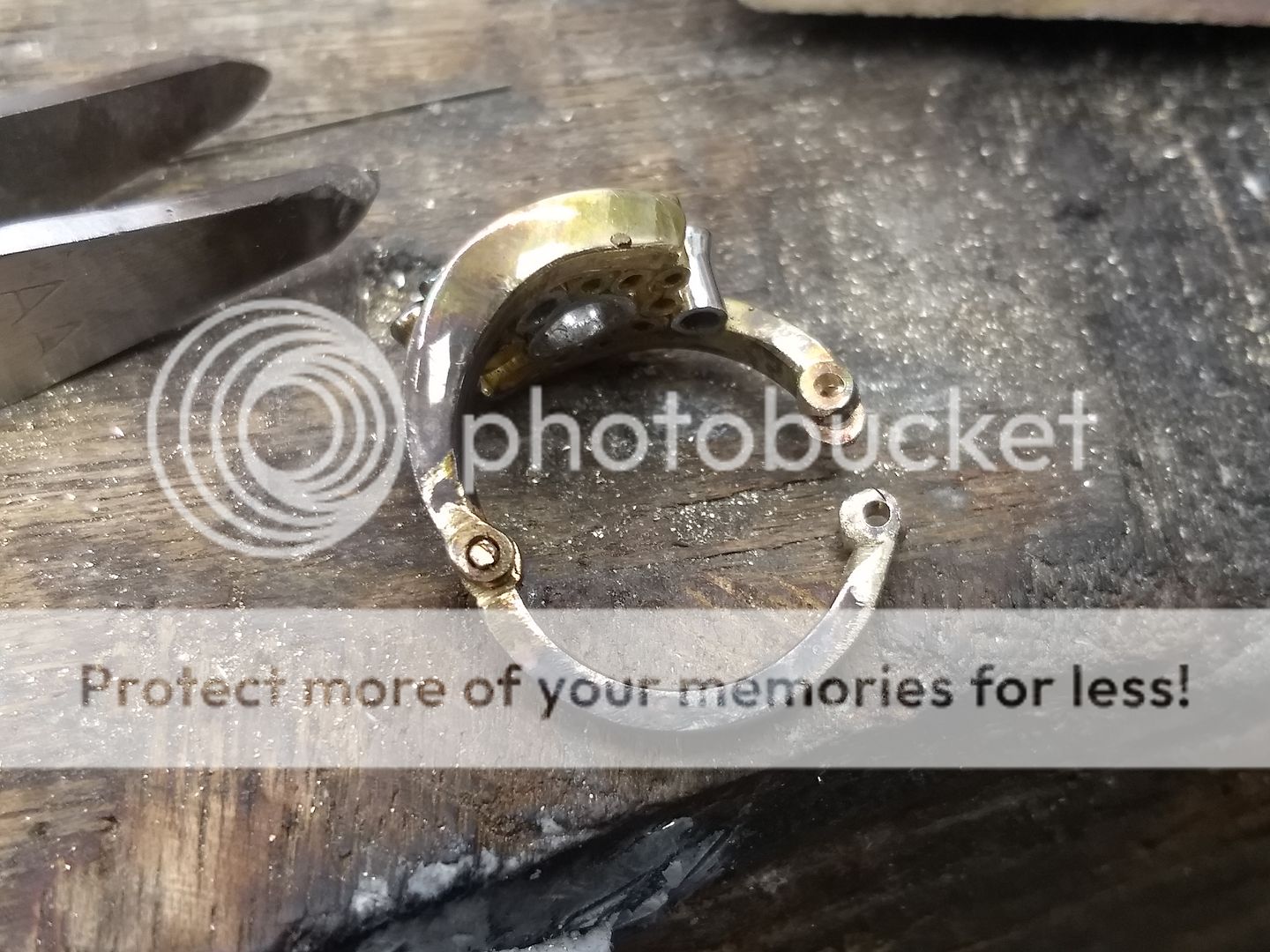
Test fit:
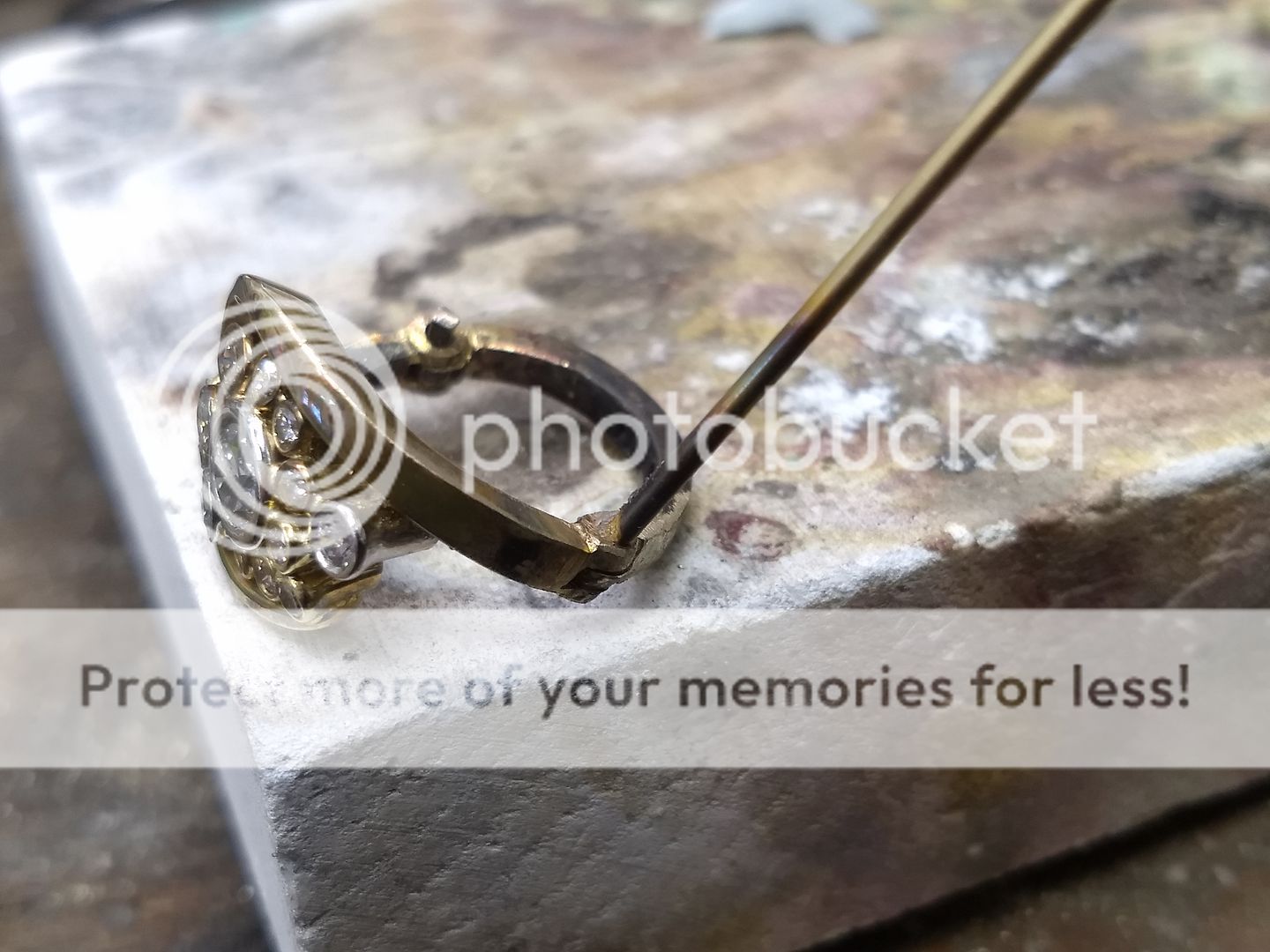
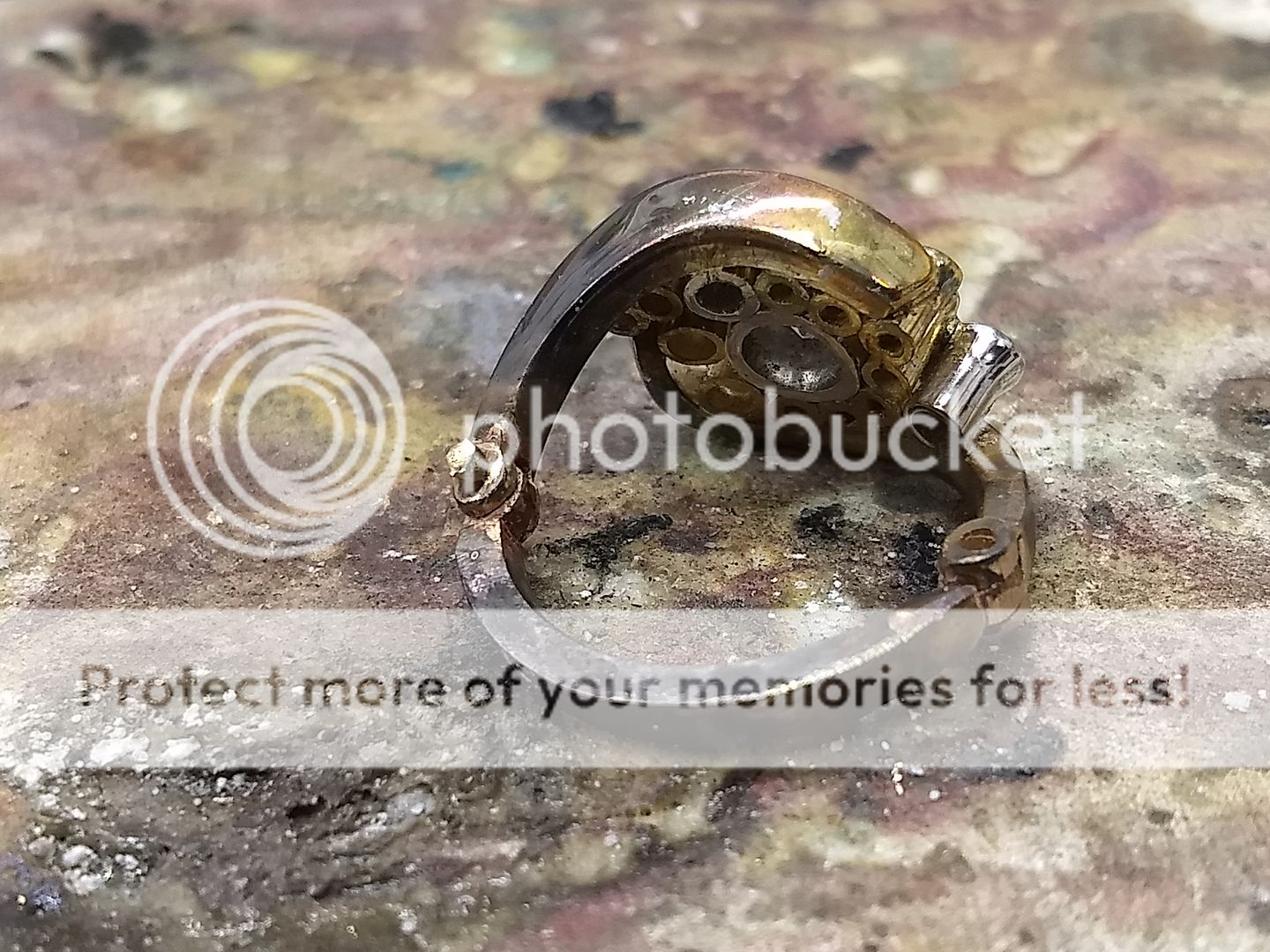
The hinge is then soldered to secure and the ring cleaned up:
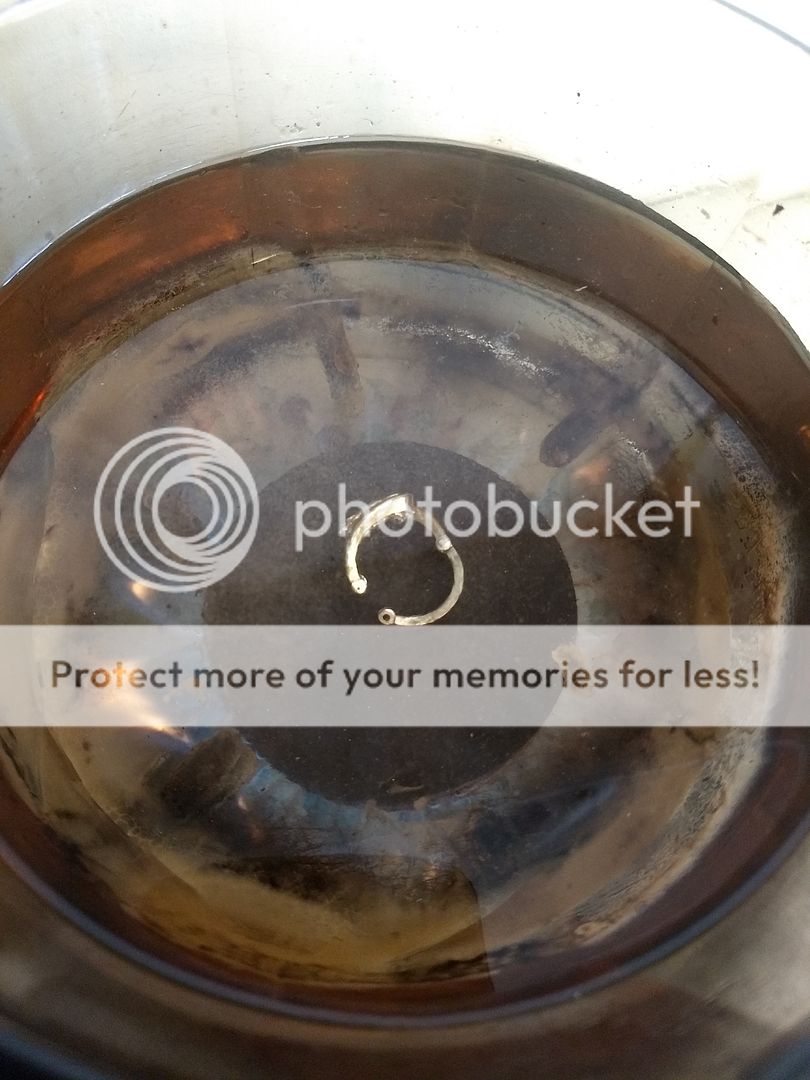
The little hole in the other end is there for a reason. I'll explain in a bit:
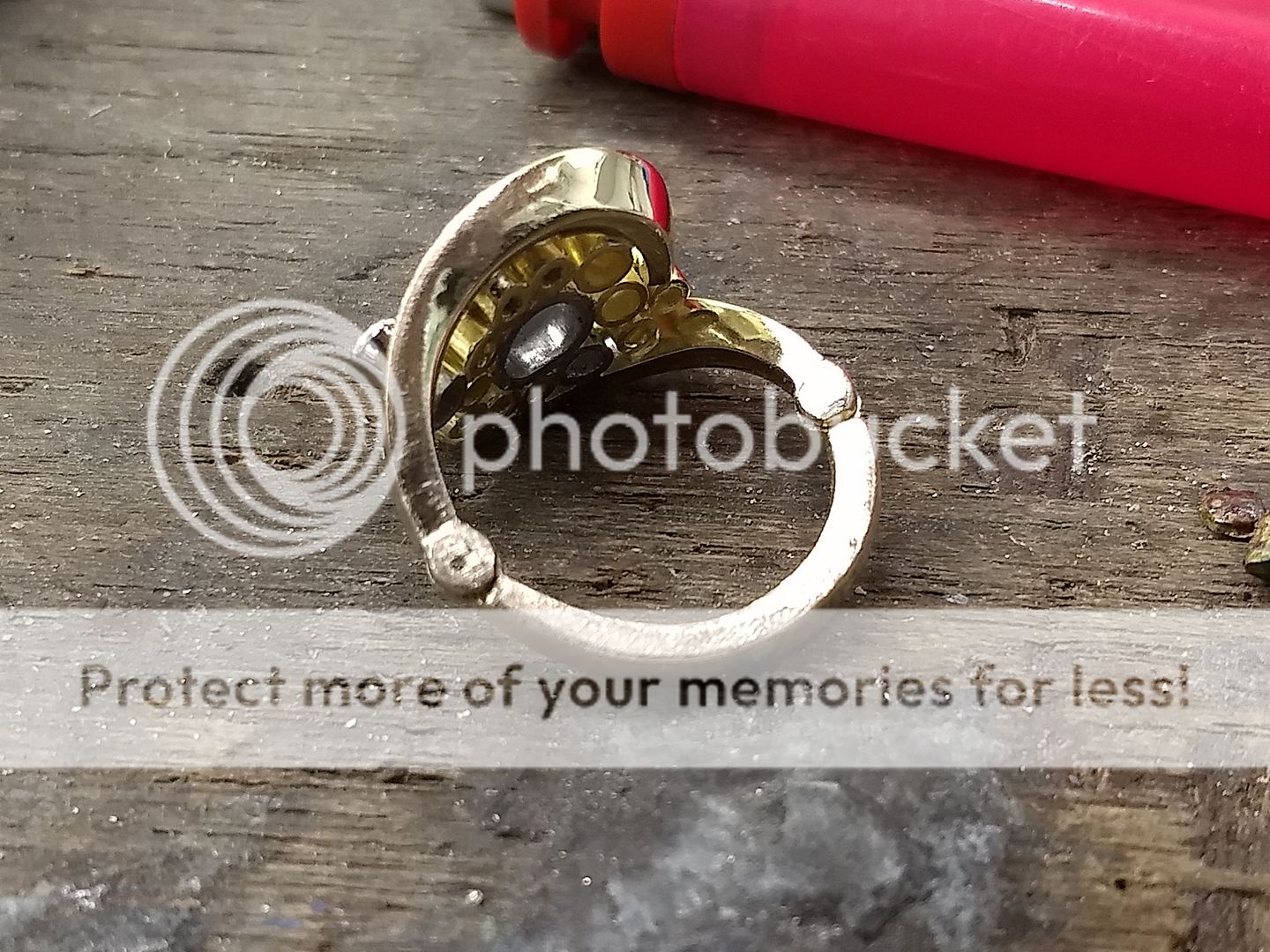
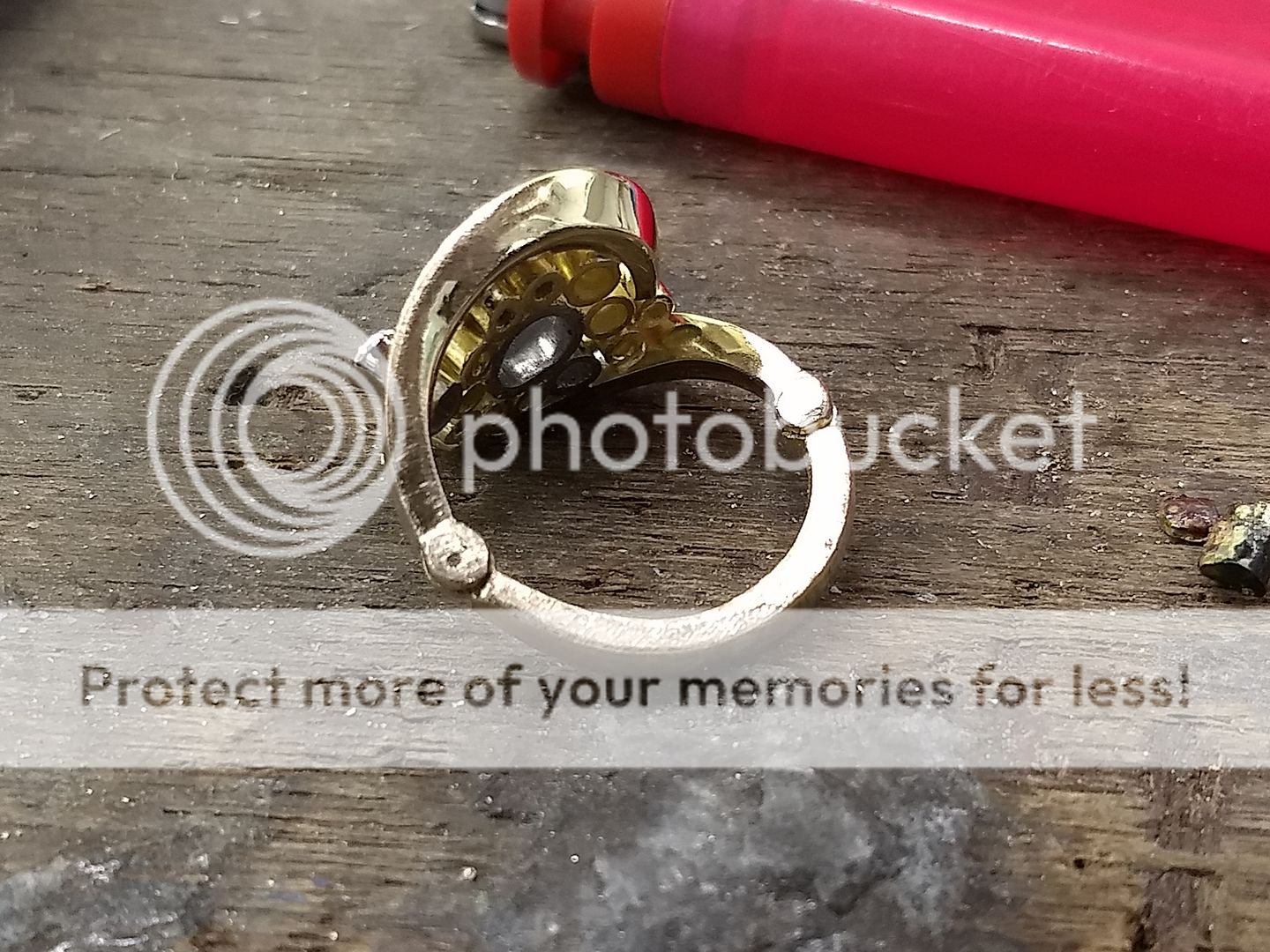
Sits ok

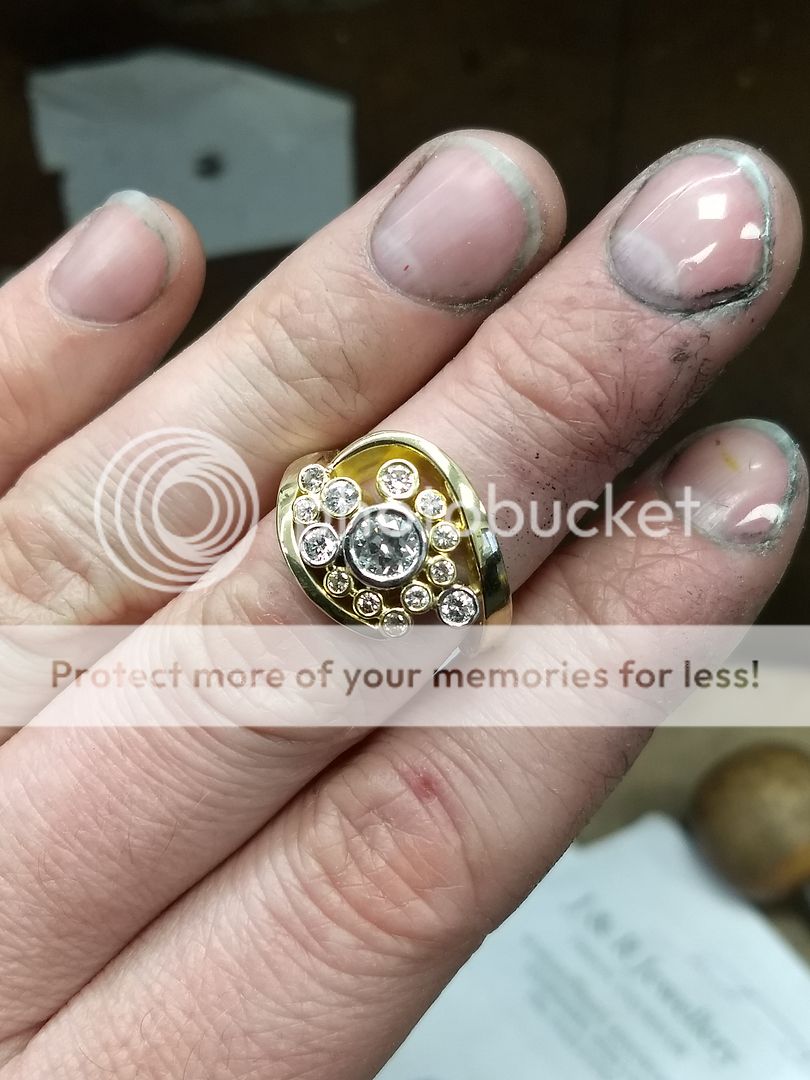
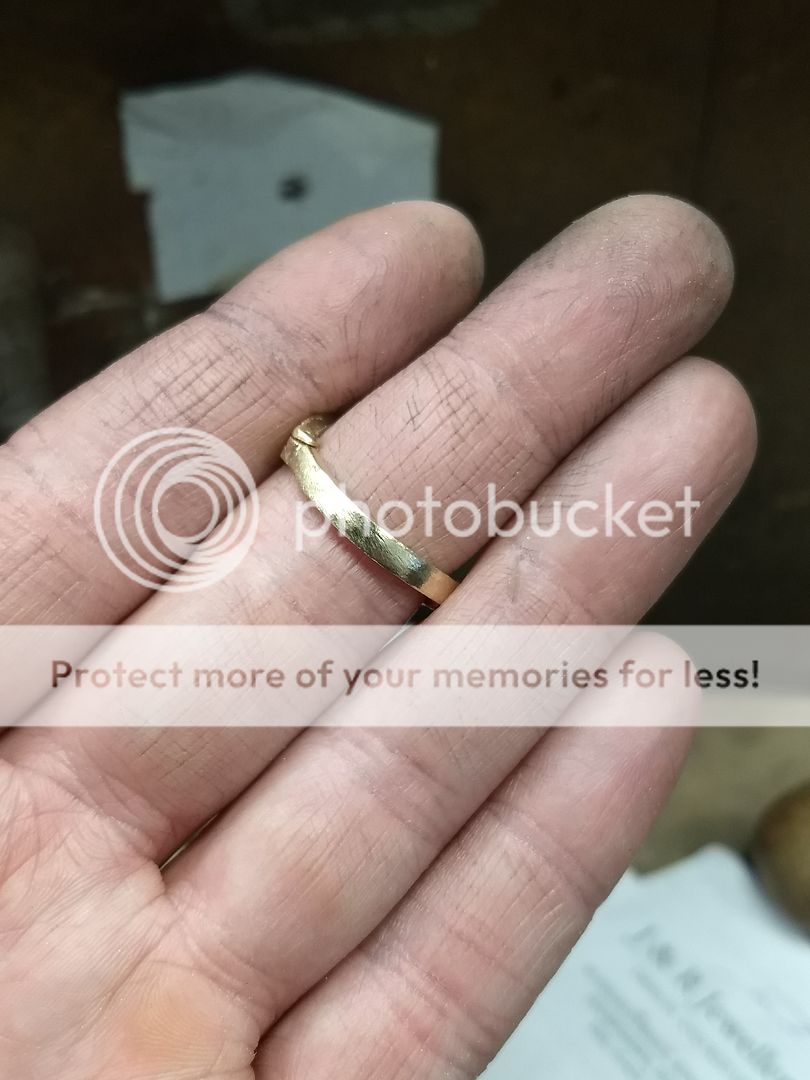
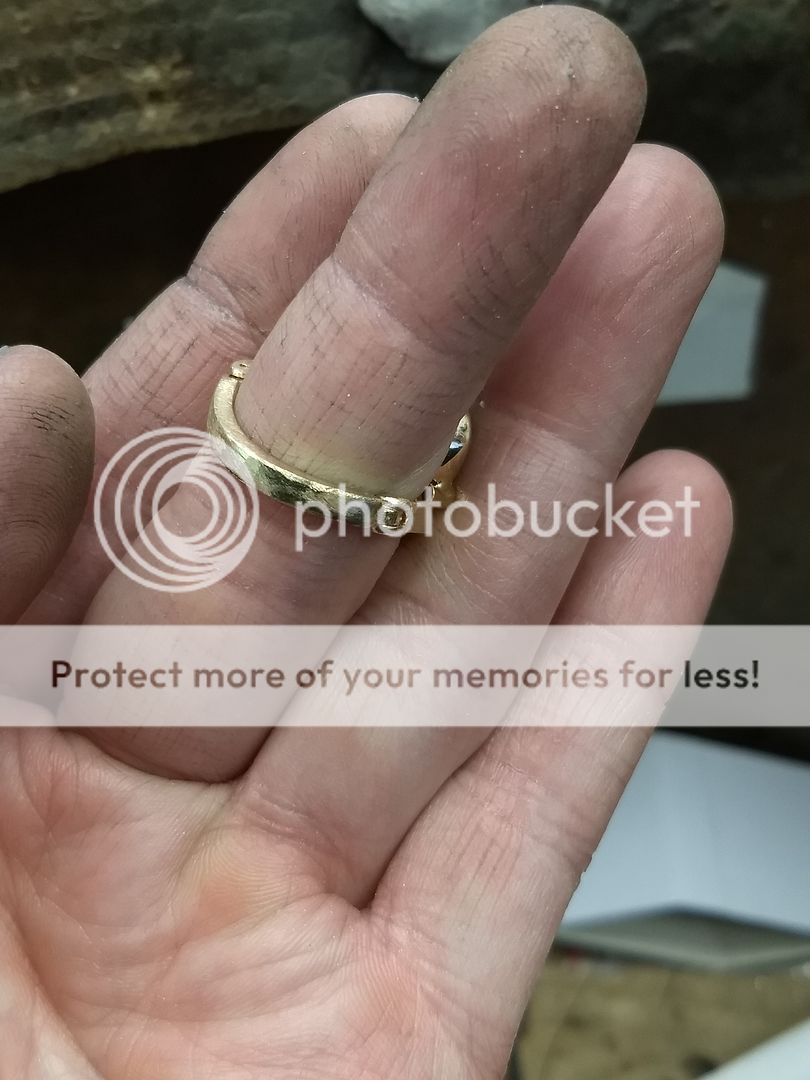
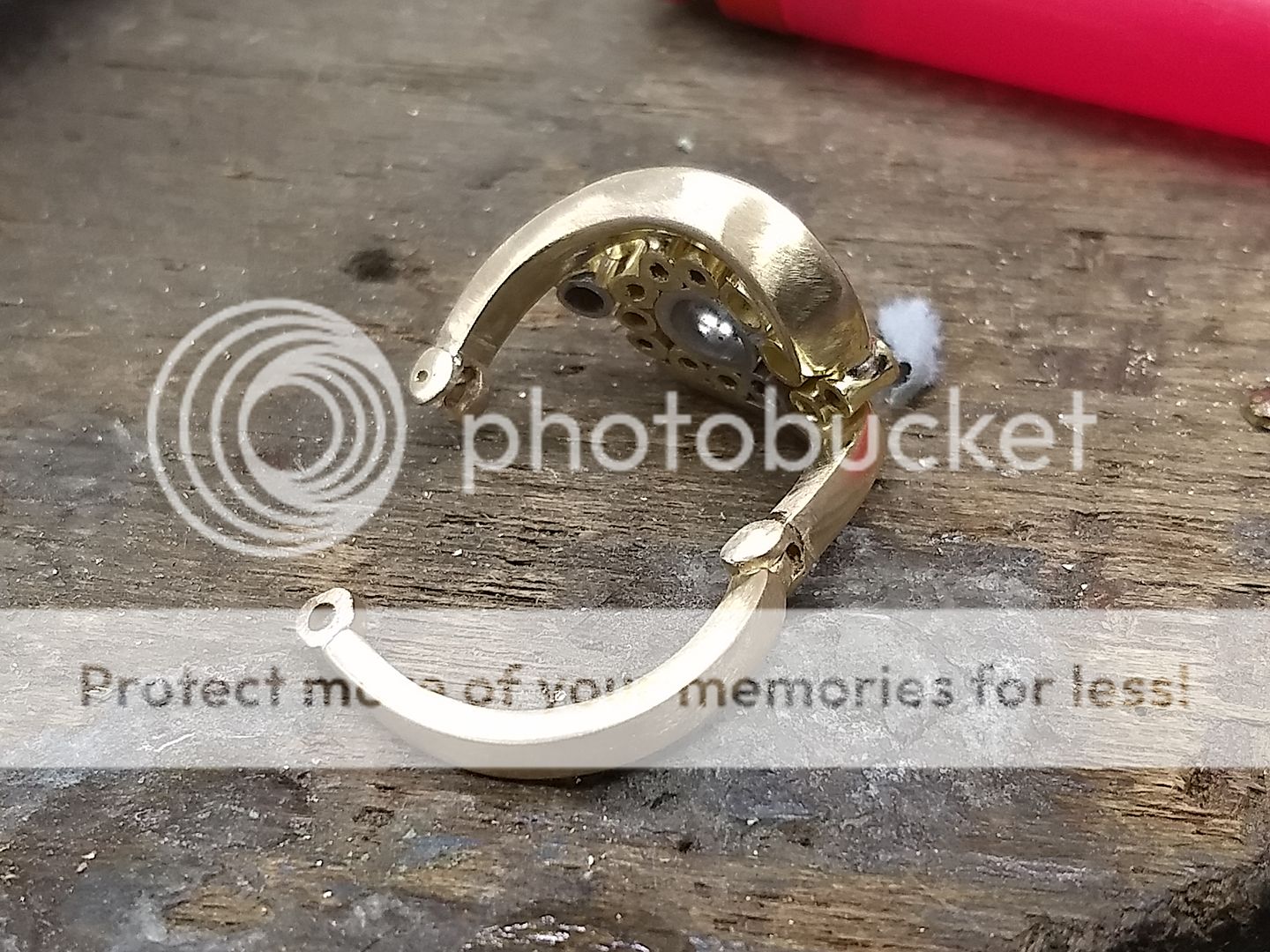

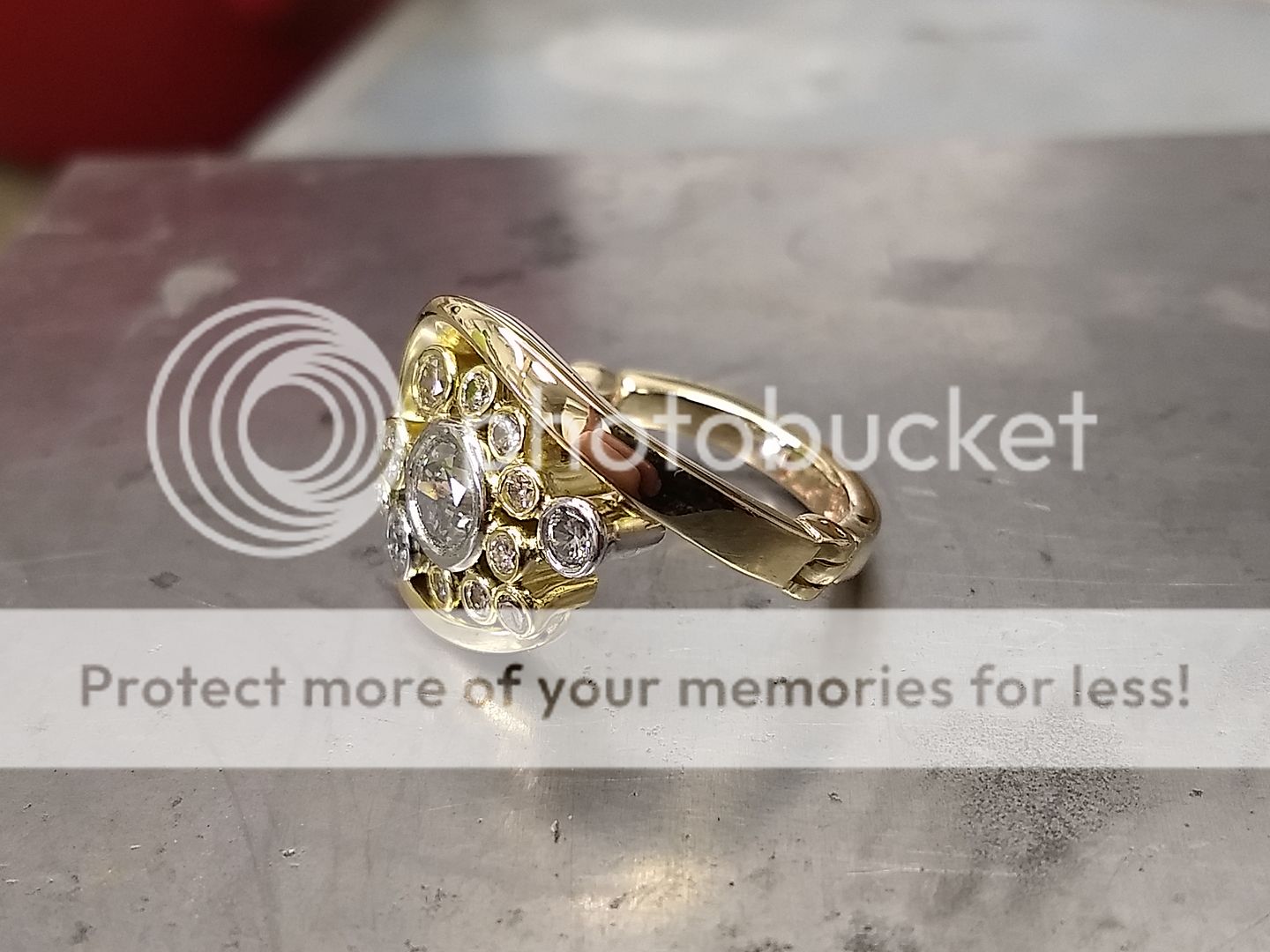
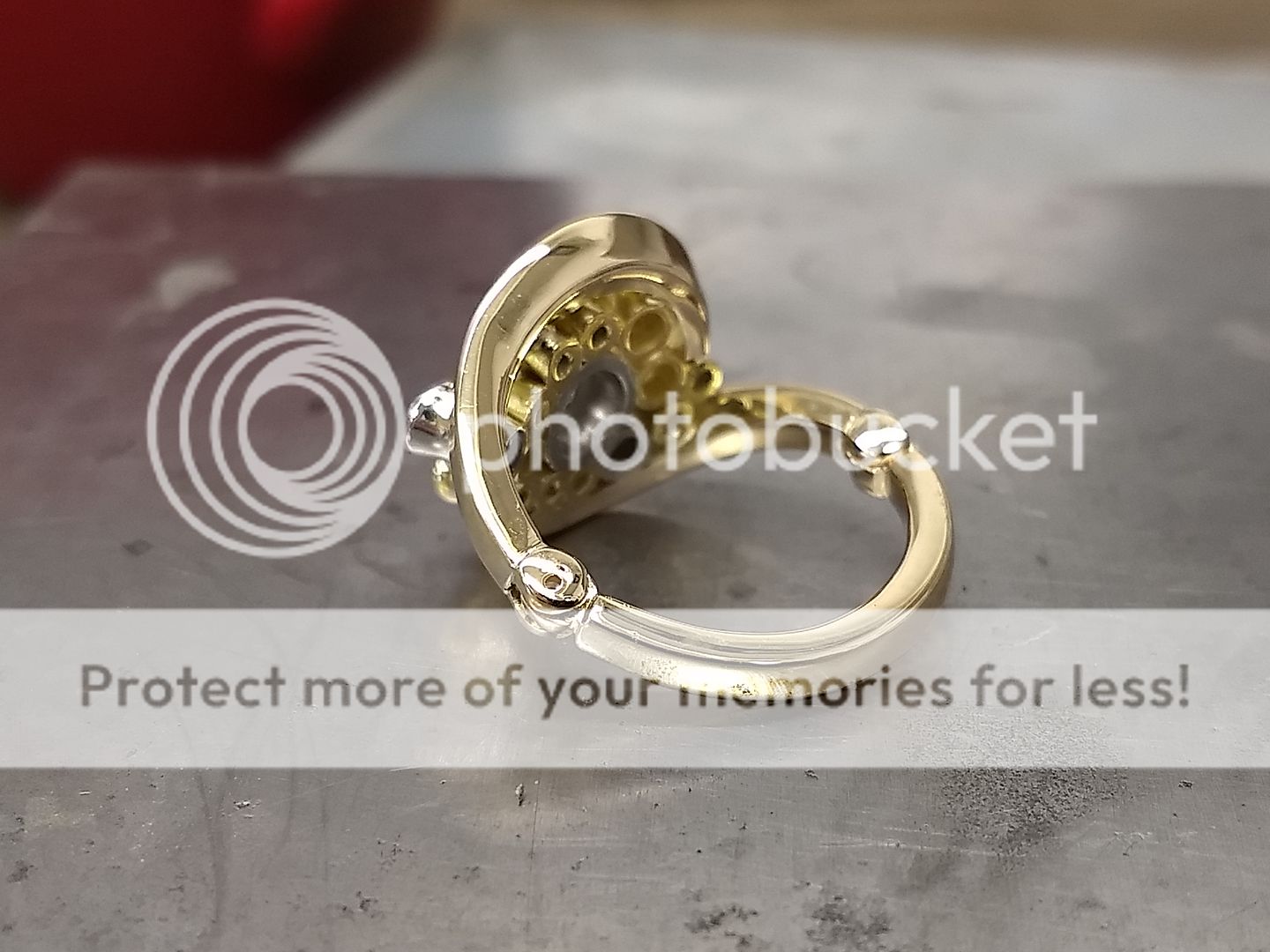
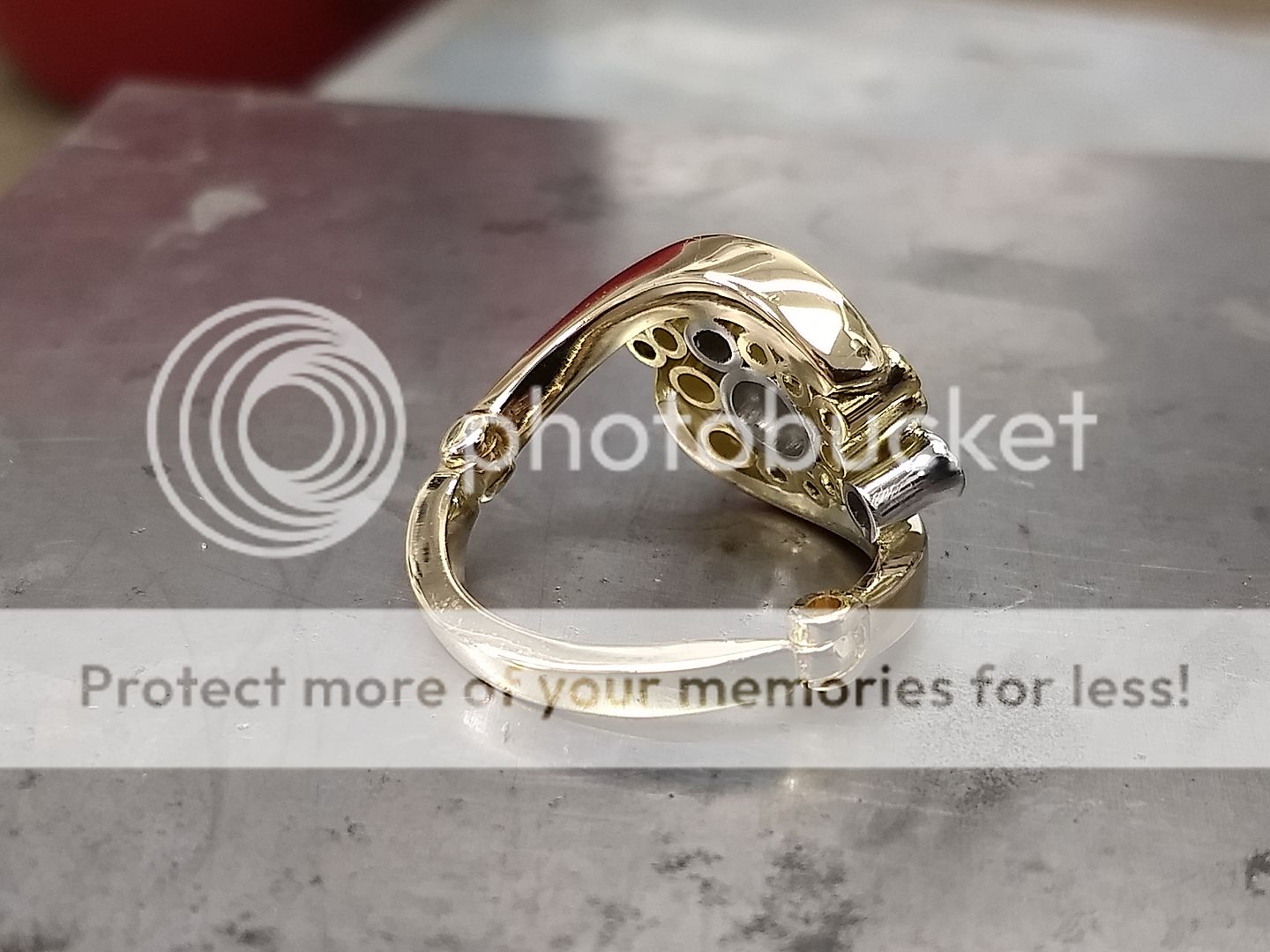
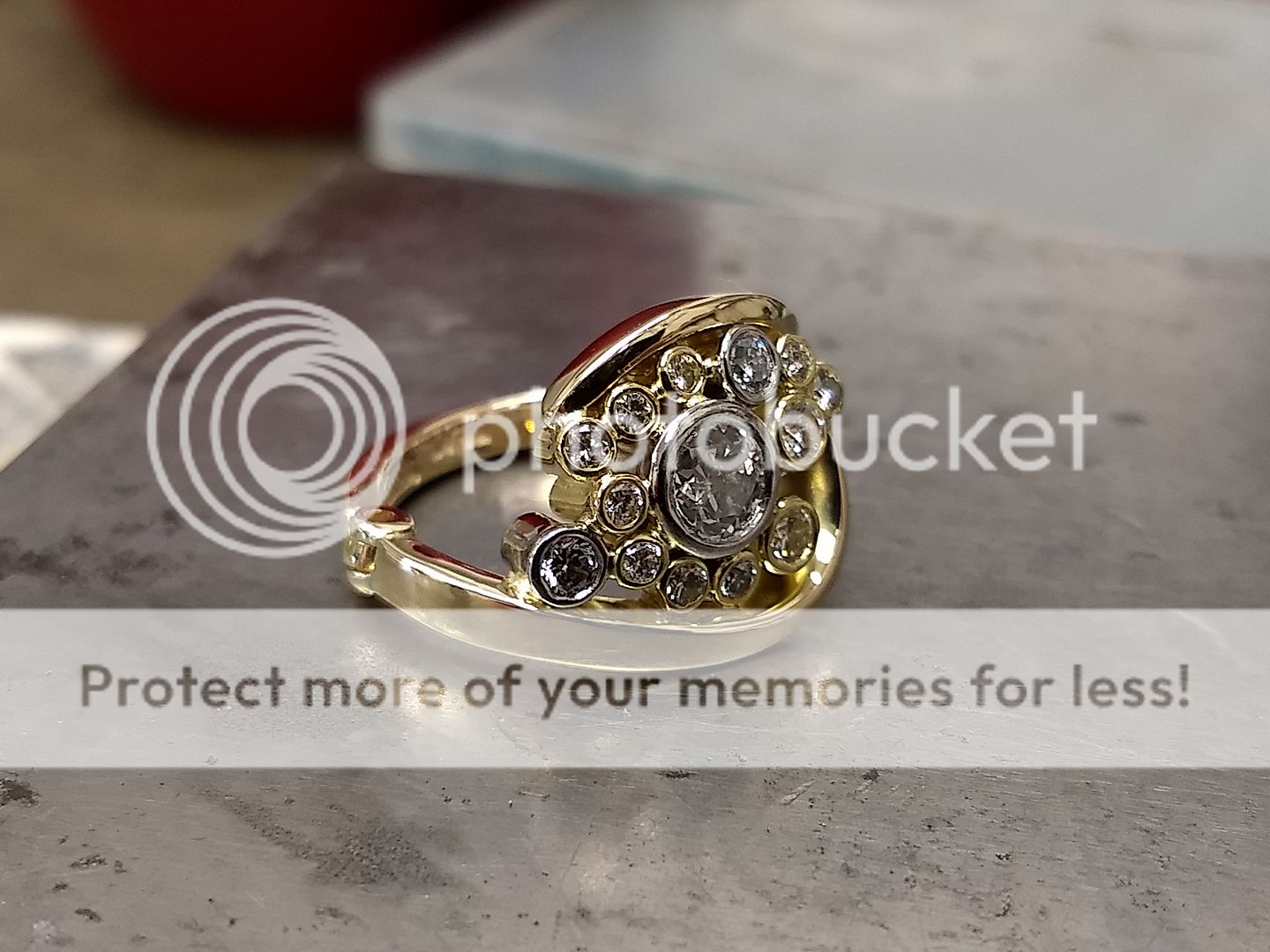
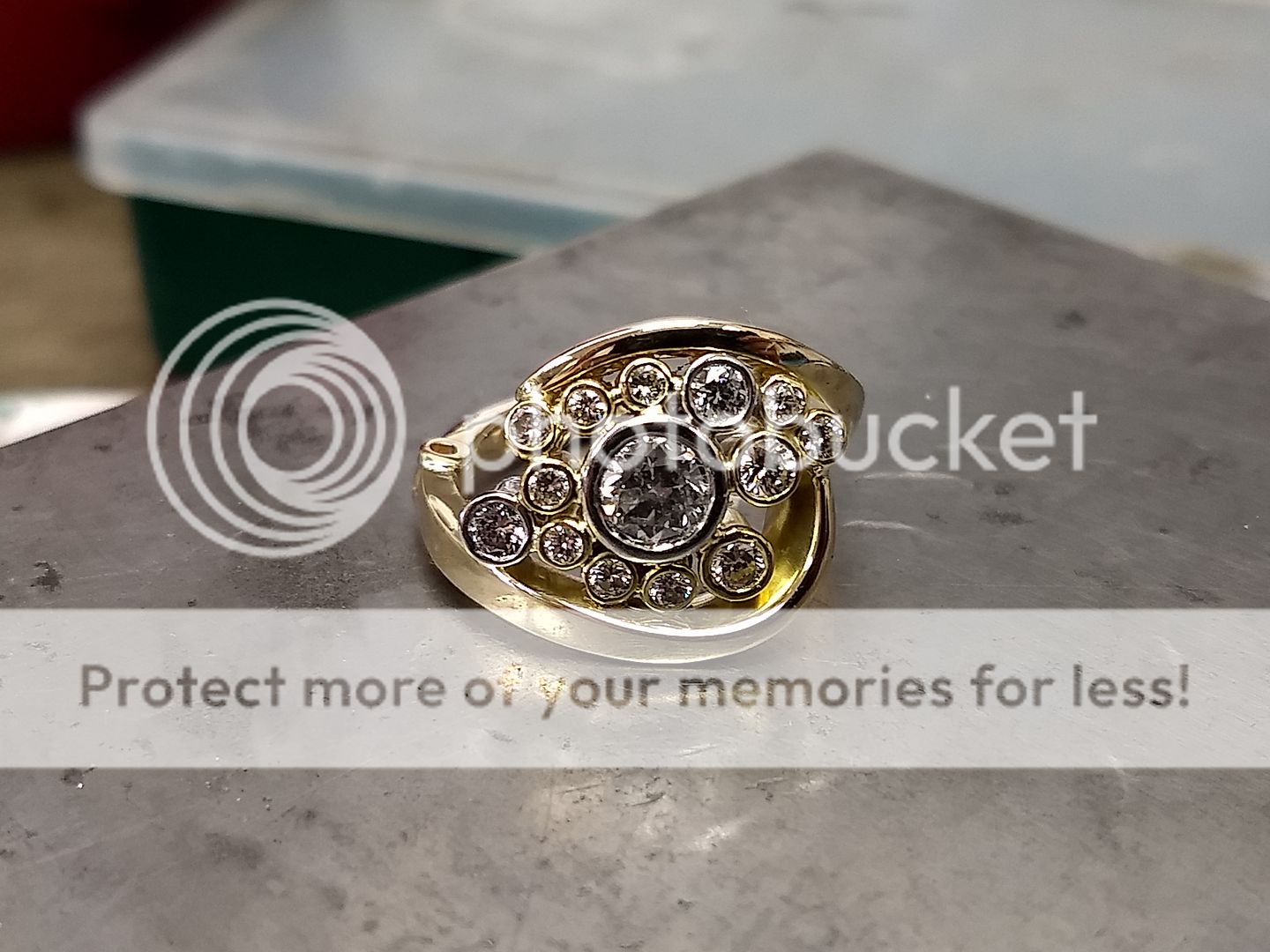
The grub screw: With the gold being soft I wanted something that wasn't going to damage the important bit..... the ring. So, I threaded some silver wire to make what is effectively a sacrificial, single use screw. She'll rarely take it off and as she's local she can come in to see me if it needed removing and refitting. It screws in fine and is snug enough to not come out, but once it's in the threads are destroyed. That little hole in the other side? It's to poke in a little threadlock to keep it secure long term. It's not strong enough that I can't screw it back out but it is firm enough that she and I don't have to worry about it. Pretty clever I reckon

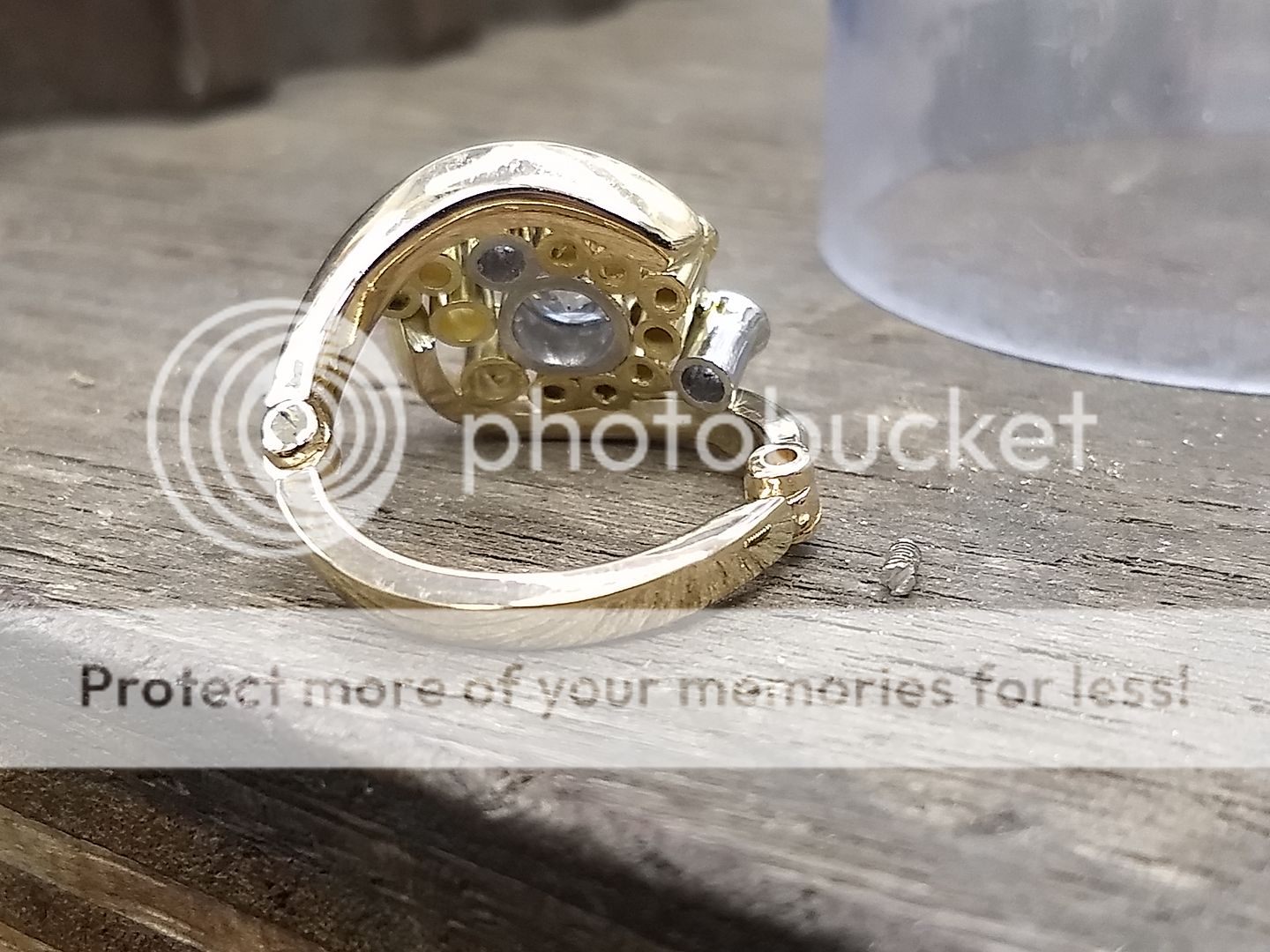
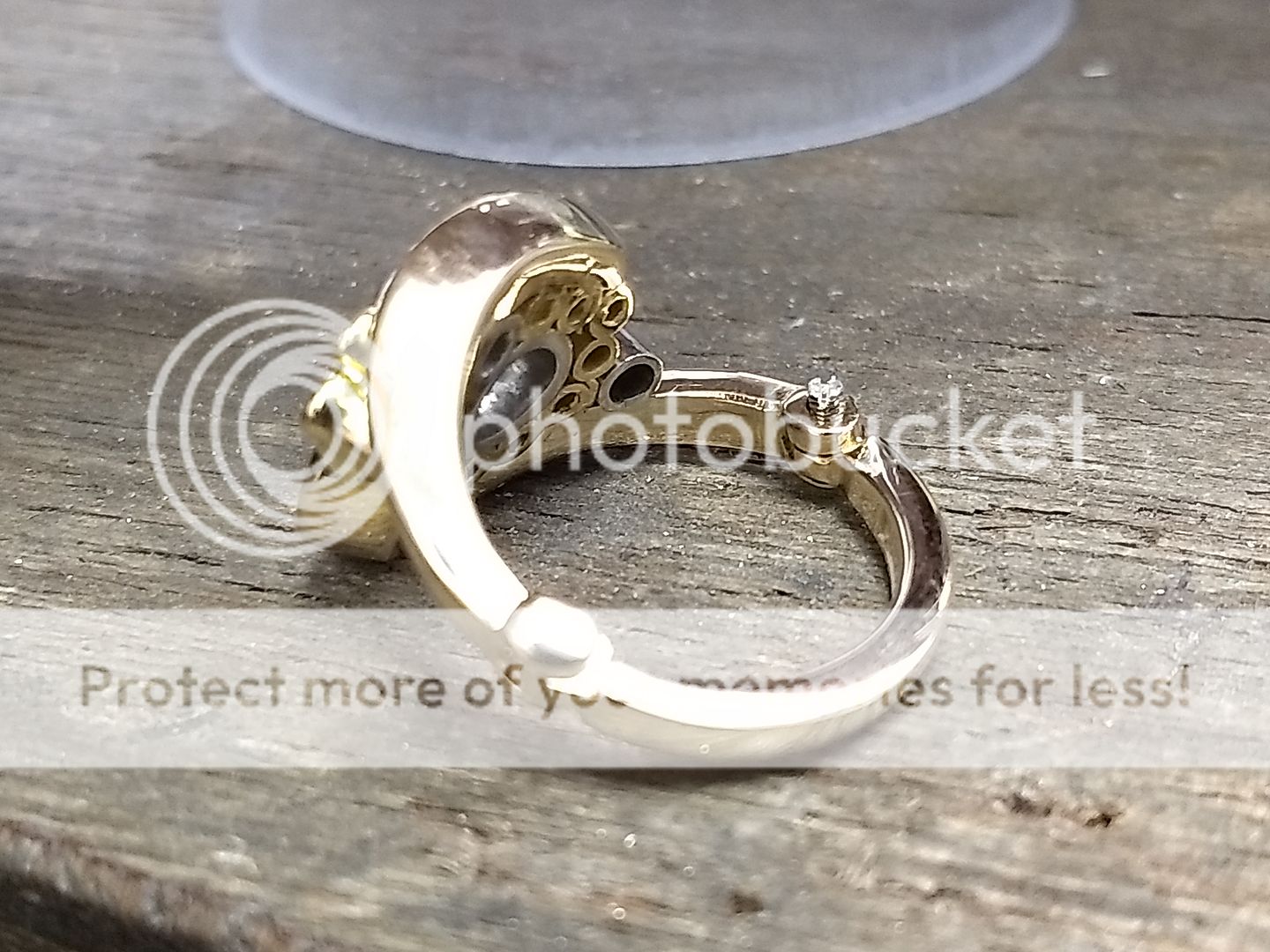
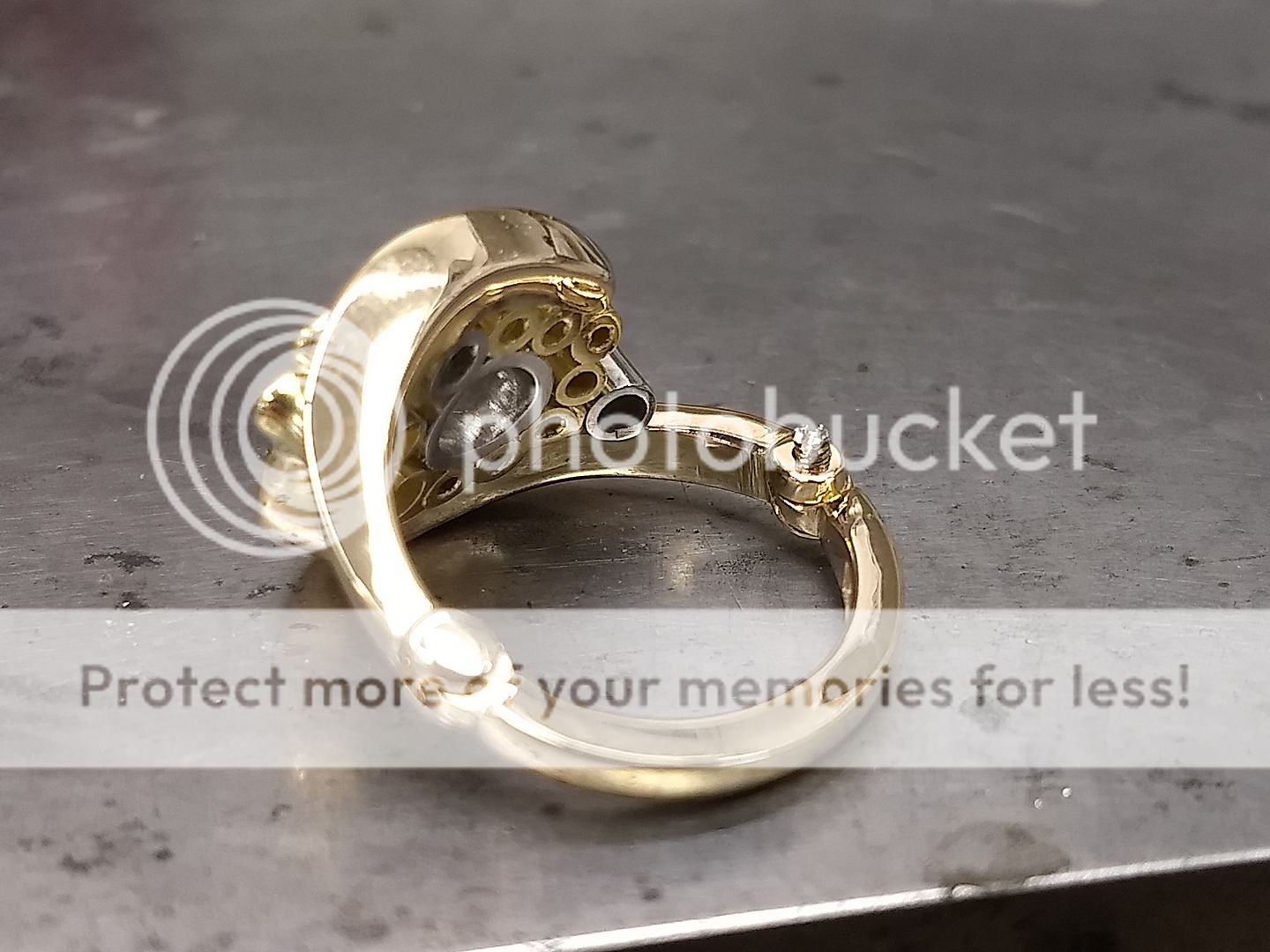
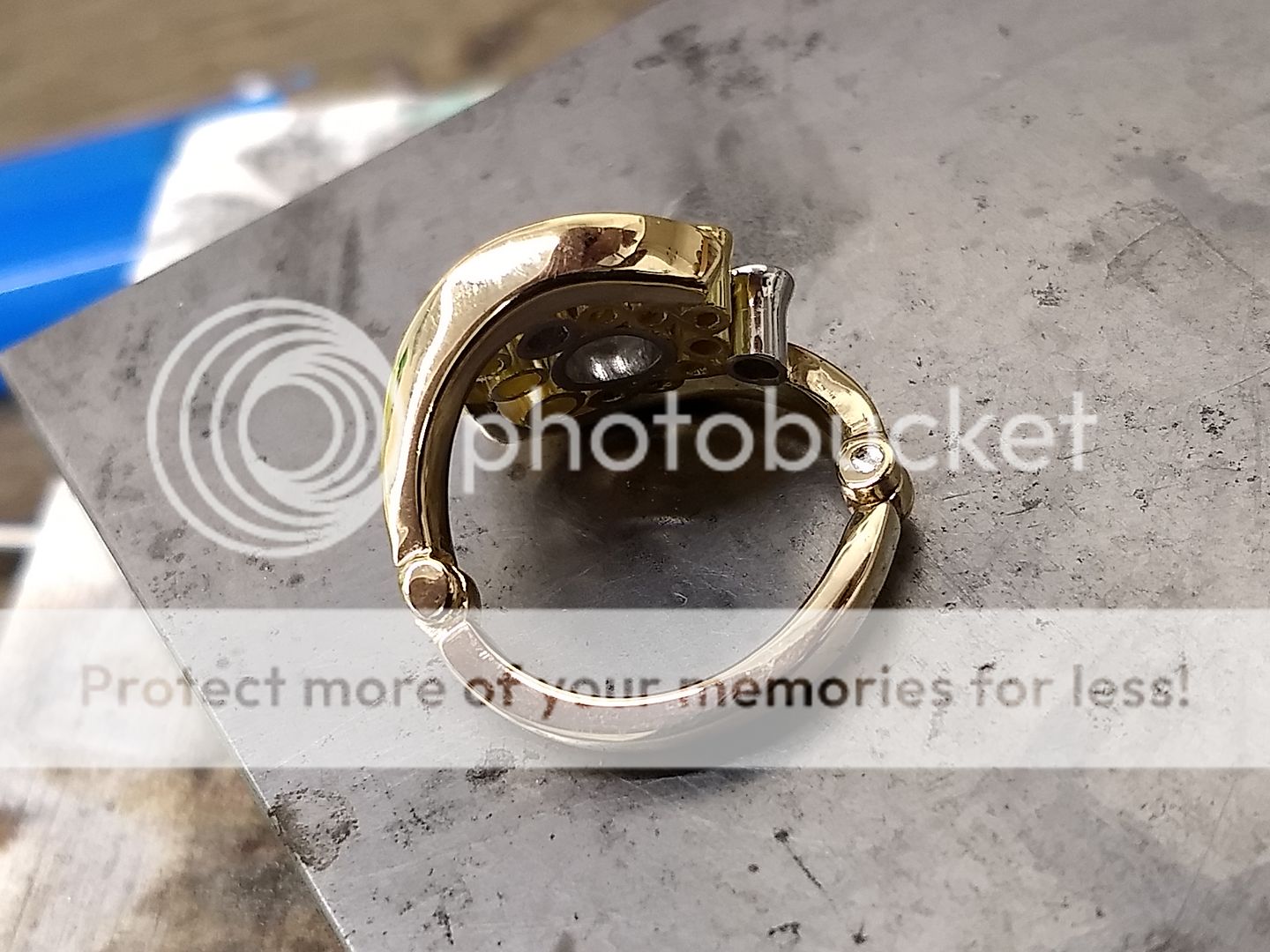
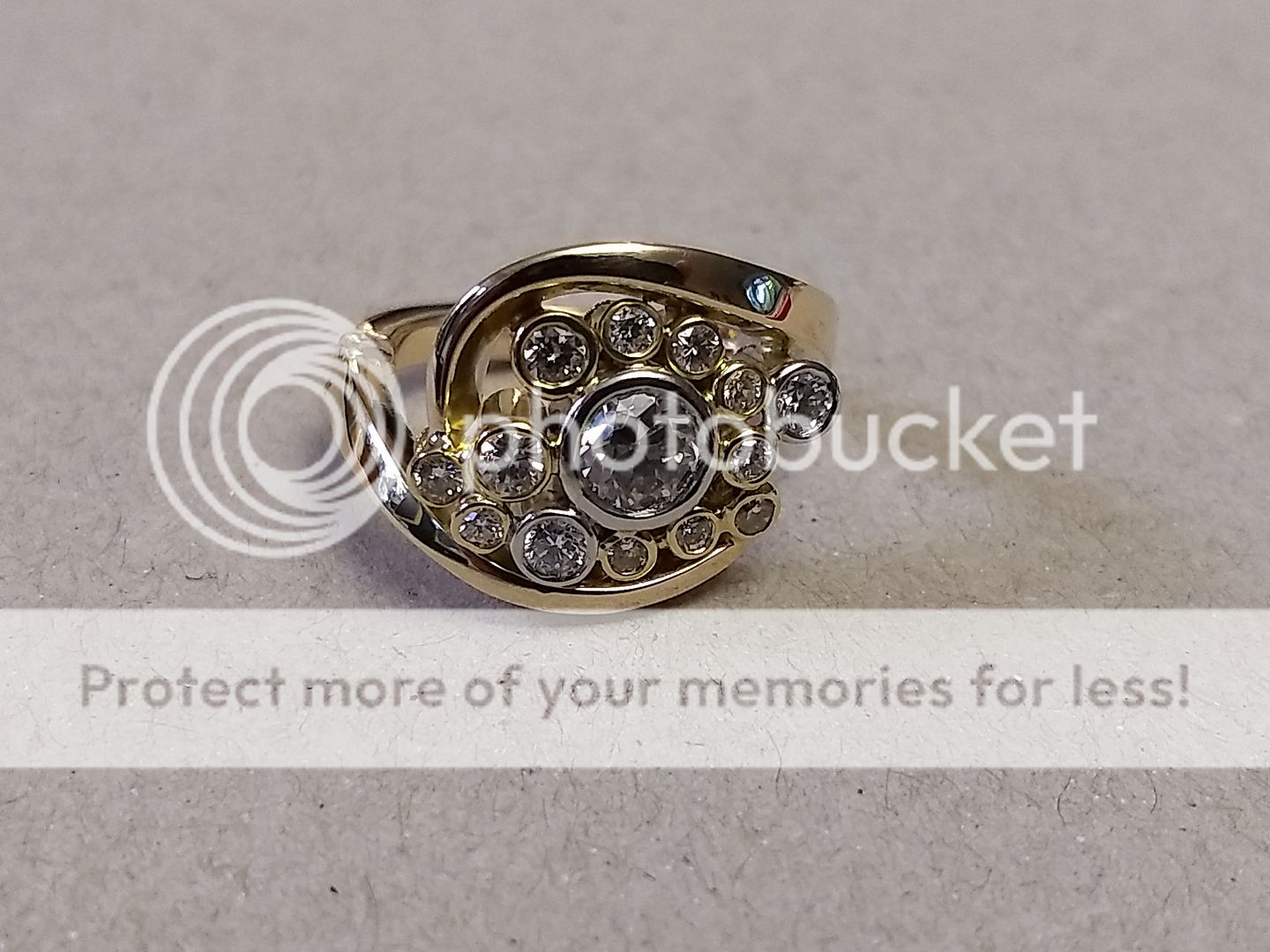
Thanks for looking

Edited by ecain63 on Friday 24th May 08:48
Edited by ecain63 on Friday 24th May 08:53
Edited by ecain63 on Friday 24th May 08:58
Great work as always.
A question from me, having seen what looks like you melting gold on some fairly burnt/carbonised wood; does the molten gold not pick up imperfections/carbon/bits of wood when it’s in its molten state? If so, how do you get rid of the “bits”, or is it just on the surface, so easy enough to file/polish away?
Sorry, that was more like two and a half questions!
A question from me, having seen what looks like you melting gold on some fairly burnt/carbonised wood; does the molten gold not pick up imperfections/carbon/bits of wood when it’s in its molten state? If so, how do you get rid of the “bits”, or is it just on the surface, so easy enough to file/polish away?
Sorry, that was more like two and a half questions!
Dibble said:
Great work as always.
A question from me, having seen what looks like you melting gold on some fairly burnt/carbonised wood; does the molten gold not pick up imperfections/carbon/bits of wood when it’s in its molten state? If so, how do you get rid of the “bits”, or is it just on the surface, so easy enough to file/polish away?
Sorry, that was more like two and a half questions!
Ha, yeah that's definitely more than one question A question from me, having seen what looks like you melting gold on some fairly burnt/carbonised wood; does the molten gold not pick up imperfections/carbon/bits of wood when it’s in its molten state? If so, how do you get rid of the “bits”, or is it just on the surface, so easy enough to file/polish away?
Sorry, that was more like two and a half questions!

To answer:it doesn't pick anything up from the wood. At that temperature, with borax thrown in the burn is very clean and if anything will burn off a tiny amount of the other metals, possibly increasing the carat slightly. Any surface rubbish will come off when quenching the metal and anything more stubborn will come off in the acid. Happy to help

s2tommi said:
Wow, that is incredible!
Do you cater for the man with a more modest budget?
So long as you're not in a rush, ha! Do you cater for the man with a more modest budget?

Work is absolutely bonkers at the moment. Lots on and even a waiting list. Send me a message and I'll take a look. Might take me a day or two to respond so apologies in advance if that's the case. I will respond though.
Here's a ring that I repaired today. Had been run over by a car and totally squashed. Full pics are on my Facebook
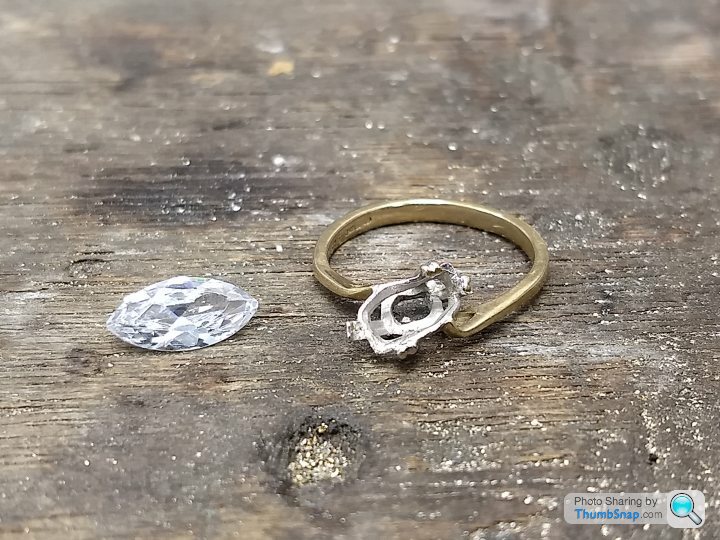
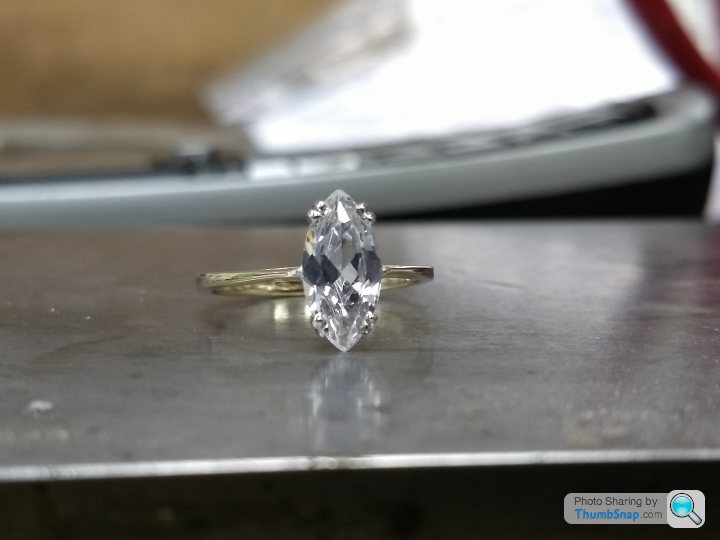
NDA said:
I can only assume the diamond was undamaged? They can chip can't they - despite their inherent strengths?
Diamonds do indeed chip and fracture. Hard as they are they are also brittle, more so in some cuts. Luckily this was a CZ ring so a cheap replacement if it did break. Fortunately the cz survived the experience 
Gassing Station | Watches | Top of Page | What's New | My Stuff