Race Car Rebuild
Discussion
Part 1
After many years of racing ZRTmotorsport have decided that after 7 hard years of racing, it is time to look at either re-shelling and rebuilding the Honda DC5 in advance of the 2017 Dubai 24Hrs or to buy another car.
We had considered opting for a new cars such as the Seat Cup racer, BMW 235i or Clio Cup but after running the DC5 for 4-years we came to have more spares than the Honda works teams! The work which went into acquiring the knowledge and stash of parts would be a huge undertaking to start again with a platform we were unfamiliar with. In addition considering the fact the Integra is a great platform to start with and the fact we are very stubborn the decision was taken to stick with what we know.
First step…. Find a shell
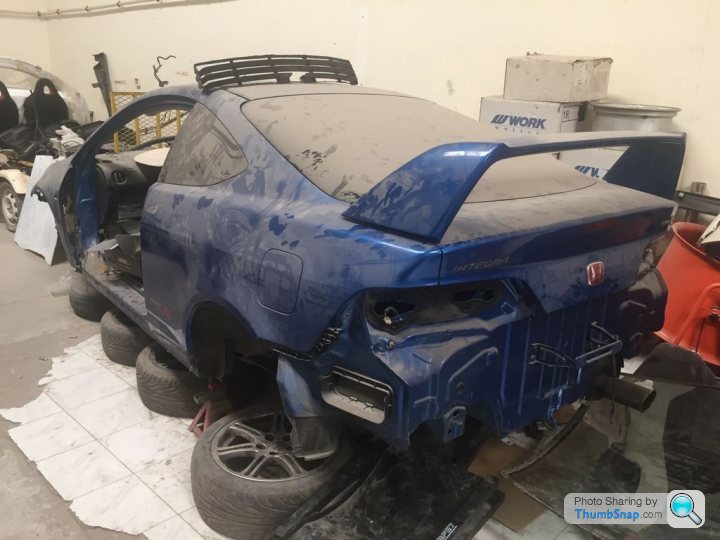
Our competitors and friends Lap 57 were able to assist and supply us with this clean (albeit dusty) 2007 shell.
The next step was to strip the shell and take it to Saluki Motorsport to agree the first stage of the project:
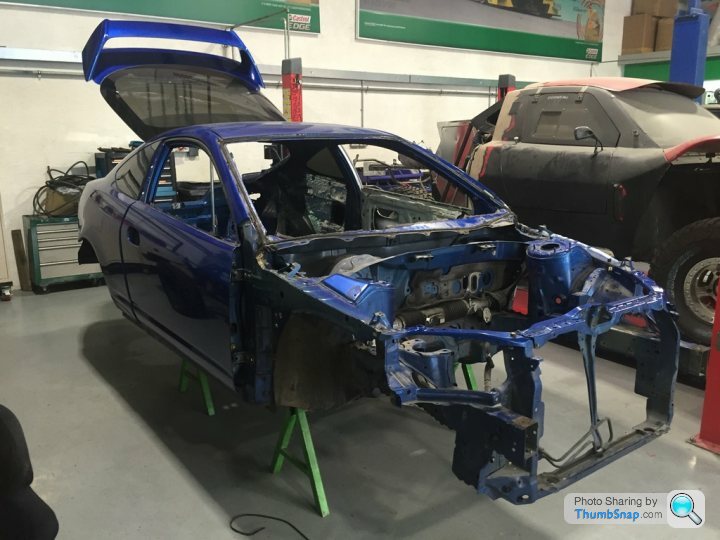
We agreed the following works with the guys at Saluki.
•Full FIA specification roll cage
•BTCC Spec enhancements for the front chassis
•Installation of seat rails
•Installation of air jacks brackets
•Removal of unnecessary brackets
•Provision for fuel cell installation
•Seem weld chassis
Stay tuned for part 2…
After many years of racing ZRTmotorsport have decided that after 7 hard years of racing, it is time to look at either re-shelling and rebuilding the Honda DC5 in advance of the 2017 Dubai 24Hrs or to buy another car.
We had considered opting for a new cars such as the Seat Cup racer, BMW 235i or Clio Cup but after running the DC5 for 4-years we came to have more spares than the Honda works teams! The work which went into acquiring the knowledge and stash of parts would be a huge undertaking to start again with a platform we were unfamiliar with. In addition considering the fact the Integra is a great platform to start with and the fact we are very stubborn the decision was taken to stick with what we know.
First step…. Find a shell
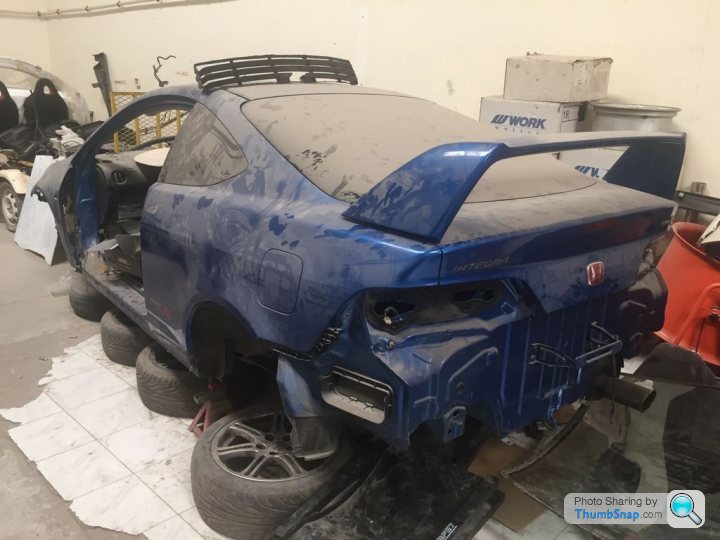
Our competitors and friends Lap 57 were able to assist and supply us with this clean (albeit dusty) 2007 shell.
The next step was to strip the shell and take it to Saluki Motorsport to agree the first stage of the project:
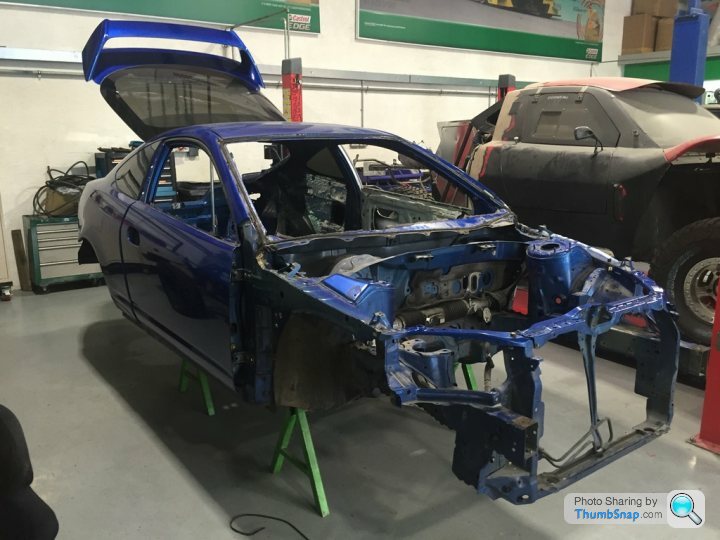
We agreed the following works with the guys at Saluki.
•Full FIA specification roll cage
•BTCC Spec enhancements for the front chassis
•Installation of seat rails
•Installation of air jacks brackets
•Removal of unnecessary brackets
•Provision for fuel cell installation
•Seem weld chassis
Stay tuned for part 2…
Edited by IanUAE on Thursday 26th May 05:20
Part 2
After agreeing the works to be carried out by Saluki, the first step was to shot blast the whole shell so that we uncover any surprises so that any metal work that required to be replaced could be replaced and secondly start with the best possible shell for seem welding.
So after shot blasting the good news was that the shell rust free and solid.
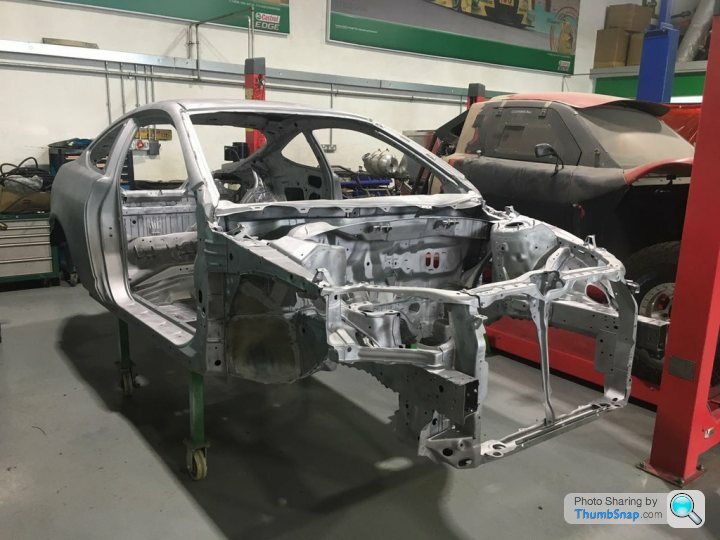
Saluki then got to work with the shell seam welding:
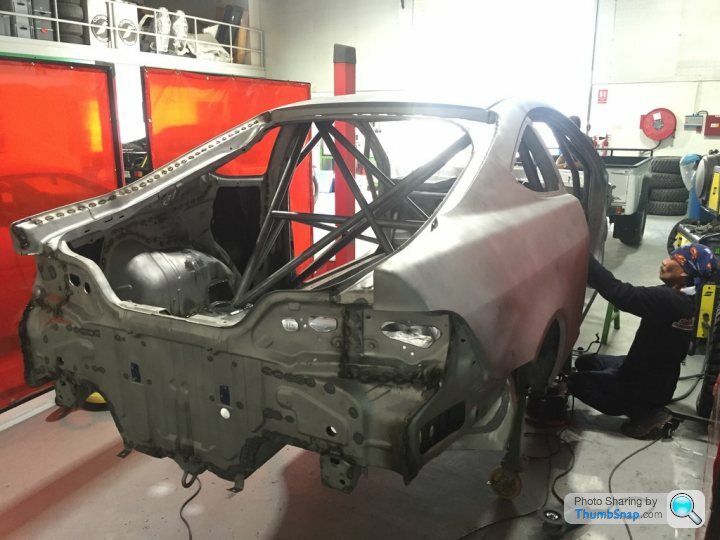
Front chassis is a critical part of the race car so seam welding was given detailed attention.
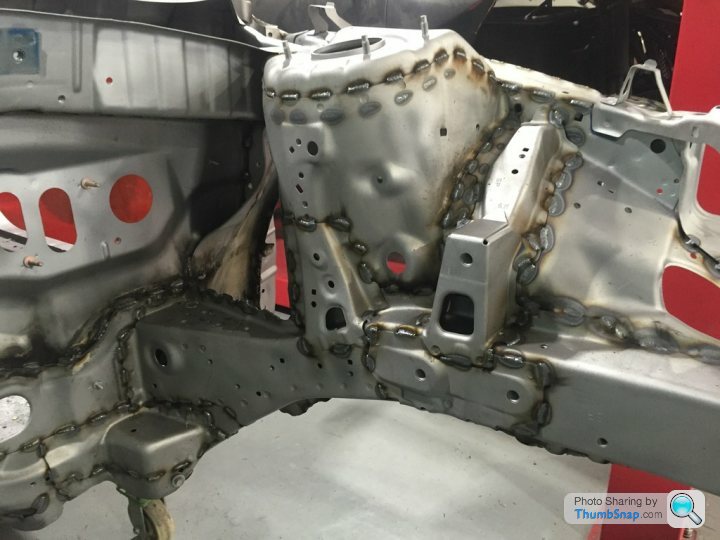
Stay tuned for part 3….
After agreeing the works to be carried out by Saluki, the first step was to shot blast the whole shell so that we uncover any surprises so that any metal work that required to be replaced could be replaced and secondly start with the best possible shell for seem welding.
So after shot blasting the good news was that the shell rust free and solid.
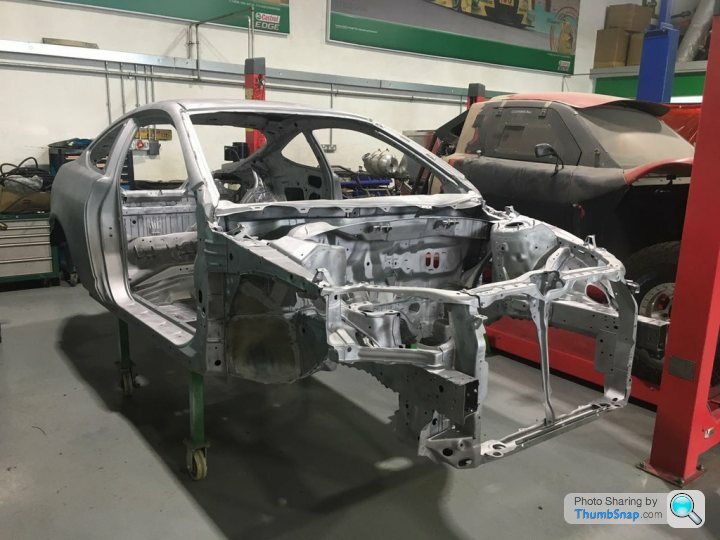
Saluki then got to work with the shell seam welding:
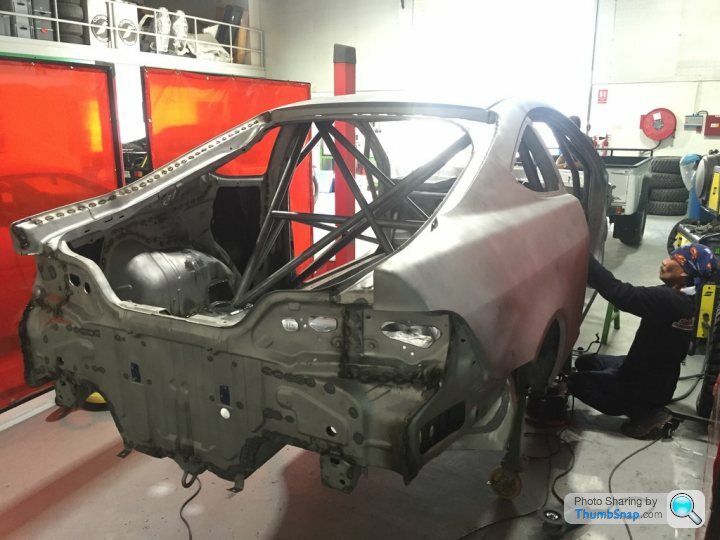
Front chassis is a critical part of the race car so seam welding was given detailed attention.
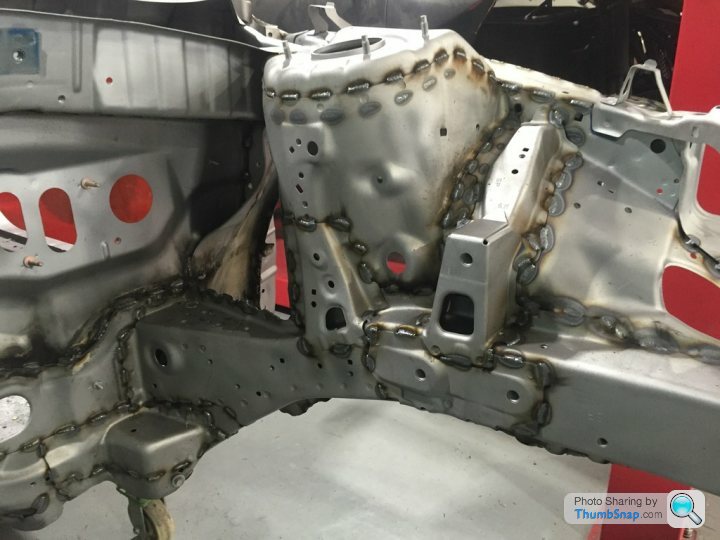
Stay tuned for part 3….
Edited by IanUAE on Thursday 26th May 05:20
Part 3
In our old shell we started facing a problem of windscreens cracking on the lower left of the screen. For anyone who has watched our documentary on Emirates Airline you will remember all too well what a problem this caused in 2015. Again since then a further 2-screens cracked. In the end we were unable to define exactly the cause but we suspect it is due to a weakness in the front chassis.
To combat this in the future and to eliminate the need for a strut brace this time we have replicated the roll cage design of the BTCC Touring cars similar to that of Peter England’s ex-BTCC astra here in Dubai. So in the below image you can see that the turret is strengthened in 4-ways.
1.Seam welding.
2.Triangulated bracing to the roll cage lateral bar at the dash.
3.Connection to the roll cage at the A-post. (Zoom in to see that one)
4.Double plate strengthening of the strut mounting.
We have also allowed for the provision of castor adjustment in the strut plate.
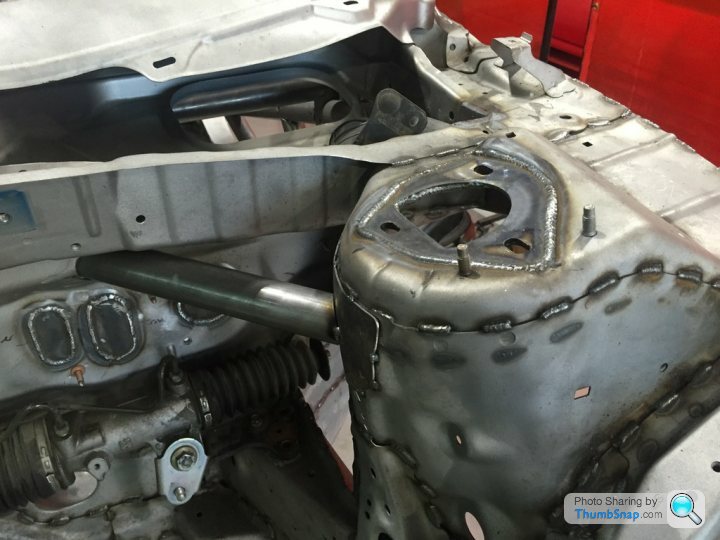
Those with a keen eye will also notice that the holes in the bulkhead (previous pic) have all been closed up as they are not needed on the race car. Most probably they were for water hoses to the heater/a-c but because we already have a car to work from we know they are not required in the build. They are therefore closed for safety and rigidity.
Stay tuned for part 4….
In our old shell we started facing a problem of windscreens cracking on the lower left of the screen. For anyone who has watched our documentary on Emirates Airline you will remember all too well what a problem this caused in 2015. Again since then a further 2-screens cracked. In the end we were unable to define exactly the cause but we suspect it is due to a weakness in the front chassis.
To combat this in the future and to eliminate the need for a strut brace this time we have replicated the roll cage design of the BTCC Touring cars similar to that of Peter England’s ex-BTCC astra here in Dubai. So in the below image you can see that the turret is strengthened in 4-ways.
1.Seam welding.
2.Triangulated bracing to the roll cage lateral bar at the dash.
3.Connection to the roll cage at the A-post. (Zoom in to see that one)
4.Double plate strengthening of the strut mounting.
We have also allowed for the provision of castor adjustment in the strut plate.
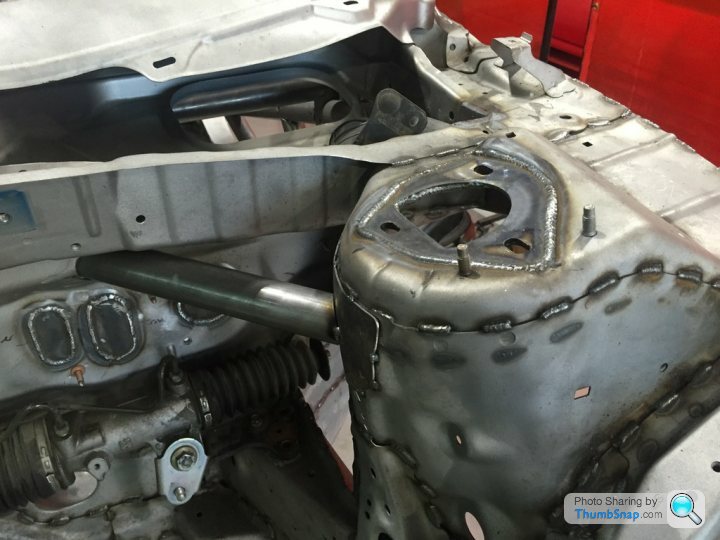
Those with a keen eye will also notice that the holes in the bulkhead (previous pic) have all been closed up as they are not needed on the race car. Most probably they were for water hoses to the heater/a-c but because we already have a car to work from we know they are not required in the build. They are therefore closed for safety and rigidity.
Stay tuned for part 4….
Part 4
Next up is to replace the OEM dash bar with an 38mm CDS section which will become an integral part of the roll cage. In the photo below you can see where the strut bracing sections are located and also its clear that Saluki have removed all unnecessary sections of steel from the floor and bulkhead reducing as much weight as possible.
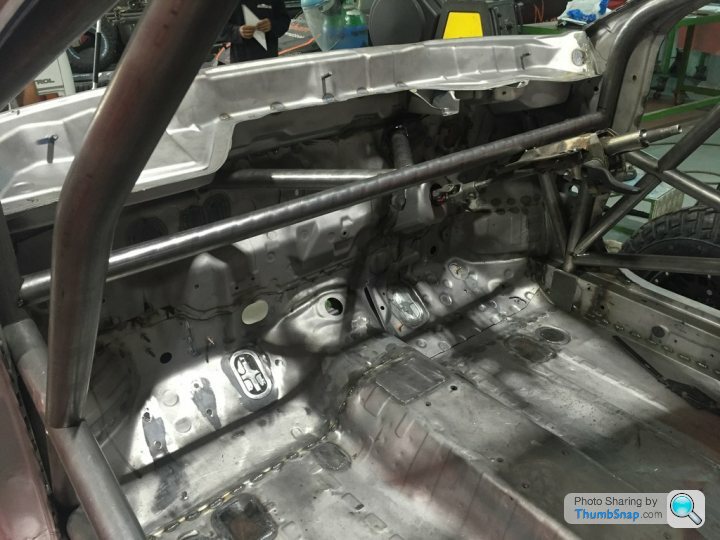
The cage will be built to the highest safety standards in accordance with the FIA regulations. With the cage partly mocked up and tacked into place the guys also start measuring precisely for the gusset reinforcement sections at the doors.

There will be 4 of these per door and the finished product looks like this:
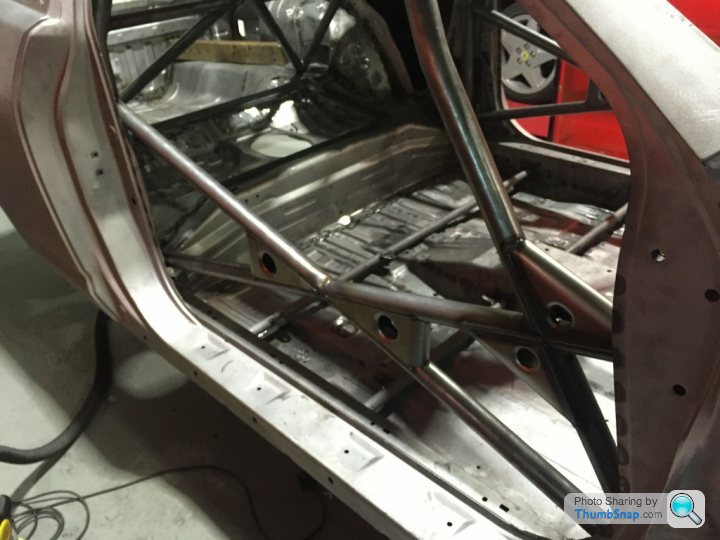
The cage is almost finished and we will post a few pics over the weekend showing the welding quality and explain how the guys weld the tops of the cage (The parts almost touching the roof) which incidentally were not properly welded in our previous car but still passed FIA scrutineering ??
With cars in Dubai 24hr reaching almost 300kph (not ours) we have to put safety as the no. 1 priority and now that we have the chance and expertise to do it we won’t take any shortcuts with the build.
Stay tuned for part 5…
More information about the team etc can be found on www.zrtmotorsport.com
Next up is to replace the OEM dash bar with an 38mm CDS section which will become an integral part of the roll cage. In the photo below you can see where the strut bracing sections are located and also its clear that Saluki have removed all unnecessary sections of steel from the floor and bulkhead reducing as much weight as possible.
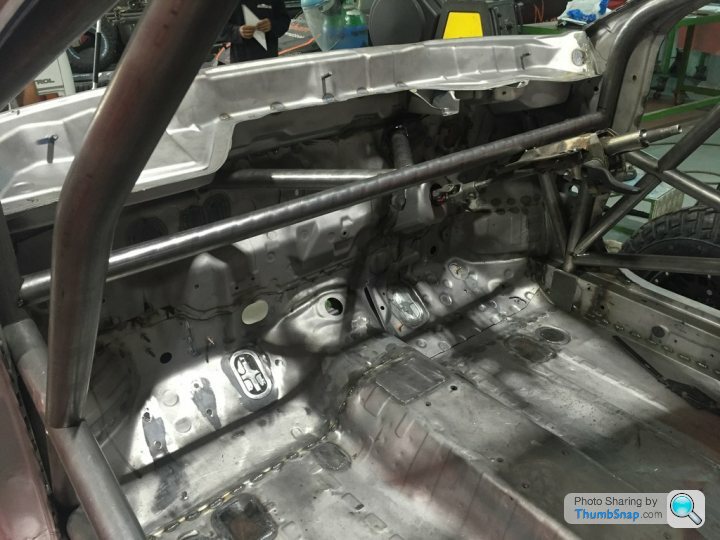
The cage will be built to the highest safety standards in accordance with the FIA regulations. With the cage partly mocked up and tacked into place the guys also start measuring precisely for the gusset reinforcement sections at the doors.

There will be 4 of these per door and the finished product looks like this:
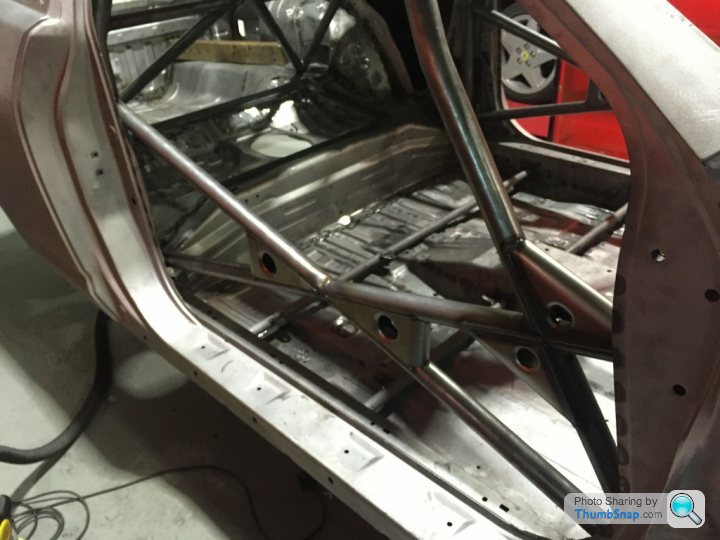
The cage is almost finished and we will post a few pics over the weekend showing the welding quality and explain how the guys weld the tops of the cage (The parts almost touching the roof) which incidentally were not properly welded in our previous car but still passed FIA scrutineering ??
With cars in Dubai 24hr reaching almost 300kph (not ours) we have to put safety as the no. 1 priority and now that we have the chance and expertise to do it we won’t take any shortcuts with the build.
Stay tuned for part 5…
More information about the team etc can be found on www.zrtmotorsport.com
Edited by IanUAE on Thursday 26th May 05:26
TacoExcellence said:
Looks like a Polaris RZR.
Correct. They are very common in the dunes over here and there is a category for them in the various desert rallies.IanUAE said:
This beast is a custom built desert rally car that runs an LS motor and Albans sequential gearbox, has onboard rear tyre deflation / inflation and 300mm of suspension travel (think of PhillipM car but on steroids http://www.pistonheads.com/gassing/topic.asp?h=0&a...Gassing Station | Readers' Cars | Top of Page | What's New | My Stuff