What Engine for 500BHP
Discussion
eliot said:
Megaflow said:
Maybe I am being really thick here, but if the mapping table start at 0kPa, but that is a actually 100kPa atmospheric, is there any circumstances a turbo engine can get a vacuum in the plenum? I'm thinking suddenly slaming the throttle closed, where the engine is sucking against it or something, and if so what is the ECU supposed to do then?
Humans consider anything below 100Kpa a "Vacuum" and anything above 100KPA as "Boost" - but in reality its all just pressure. Sitting at my desk right now I'm enjoying 100kpa of "pressure" - hence why one of the suggestions in this thread was to turn the ignition on to see what pressure the ECU reported atmospheric as.Here are some spark and boost tables from a Megasquirt ECU, it uses MAP as the load measurement for both fuel and spark (as you should expect): (strictly speaking the right hand kpa columns should both go up to 200kpa - but I only run 10psi of boost which is around 150kpa from memory - but the idea is you ensure you cover the outliers as well)
I dug out my IAT Retard settings and it set to pull 1 degree of timing every 6'c increase in temperature only in boost (100kpa) and only when it exceeds 62'c - which in normal circumstances I wouldn't expect to see, so its just a safety net.
I fear the answer is it can't...
I said I'd post another sad tale of a turbo engine blowing up on the rollers. About 13 years ago I did an ultra big valve CVH head for a guy called Jim Hearne for the 2 litre Zetec/CVH hybrid (ZVH) engine he was building for his Quantum kit car. You can google him for the story although the website seems to be down at the moment.
ECU was a DTA I think and the maps were based on TPS position plus boost compensations for extra fueling and ignition retard. The rolling road guy was however very green and not familiar with the DTA system despite it being about the most common out there. He first held the wastegate open and mapped everything without any boost, put some boost compensations in and then started to see how it went in anger.
Unfortunately what he didn't realise was that the ignition retard table for boost on that ecu was not in degrees of ignition retard but percentages of the advance numbers in the base map. So for instance if he had the number 10 in the retard table at 1 bar of boost and the base map advance at a particular rpm was 30, the boost retard was only 3 degrees (10% x 30) rather than the 10 degrees he thought he was entering taking the total advance down to only 27 degrees BTDC instead of 20.
So it detonated like crazy as soon as the turbo kicked in. He increased the numbers in the boost retard table a bit but of course it made little difference. What he really needed was numbers like 30% plus in the retard table to get it right. So more det, more head scratching, even bigger numbers in the retard table until after several iterations of this the cylinder head gasket blew big style in a cloud of steam and oil and the car got trailered home on the back of an AA truck.
When the cylinder head came back to me it was pretty much swiss cheese. The aluminium wasn't just mottled or even pock marked, it had holes in it like the inside of an Aero chocolate bar. I sweated over it for days skimming the det out a few thou at a time trying not to remove any more metal than absolutely necessary and then opening up the chambers by hand to get the CR back to a sensible level. Fortunately I just managed to salvage it and after a rehone, new pistons and a proper set up by someone else it went beautifully and was totally reliable. Just a shame it cost so much to put the damage caused by the first mapping session right.
ECU was a DTA I think and the maps were based on TPS position plus boost compensations for extra fueling and ignition retard. The rolling road guy was however very green and not familiar with the DTA system despite it being about the most common out there. He first held the wastegate open and mapped everything without any boost, put some boost compensations in and then started to see how it went in anger.
Unfortunately what he didn't realise was that the ignition retard table for boost on that ecu was not in degrees of ignition retard but percentages of the advance numbers in the base map. So for instance if he had the number 10 in the retard table at 1 bar of boost and the base map advance at a particular rpm was 30, the boost retard was only 3 degrees (10% x 30) rather than the 10 degrees he thought he was entering taking the total advance down to only 27 degrees BTDC instead of 20.
So it detonated like crazy as soon as the turbo kicked in. He increased the numbers in the boost retard table a bit but of course it made little difference. What he really needed was numbers like 30% plus in the retard table to get it right. So more det, more head scratching, even bigger numbers in the retard table until after several iterations of this the cylinder head gasket blew big style in a cloud of steam and oil and the car got trailered home on the back of an AA truck.
When the cylinder head came back to me it was pretty much swiss cheese. The aluminium wasn't just mottled or even pock marked, it had holes in it like the inside of an Aero chocolate bar. I sweated over it for days skimming the det out a few thou at a time trying not to remove any more metal than absolutely necessary and then opening up the chambers by hand to get the CR back to a sensible level. Fortunately I just managed to salvage it and after a rehone, new pistons and a proper set up by someone else it went beautifully and was totally reliable. Just a shame it cost so much to put the damage caused by the first mapping session right.
Megaflow said:
What I was trying to understand is this, if the map table starts at 0kPa, which we have established, is actually 100kPa atmospheric, what happens when the MAP measures below atmospheric of 100kPa, or a negative value according to the map table, how is the ECU supposed to cope with that?
I fear the answer is it can't...
Struth. We've answered this specifically and in detail over and over again in the previous 3 pages. If you don't understand any of what's being written maybe you should stick to threads with more basic topics. I fear the answer is it can't...
Just for some comparison I looked in the default maps in the haltech software & dug out the one for a Subaru WRX.
That has the Fuel and ignition using MAP as load and both maps start at -100kpa.
I cant post pictures so the screen shots are here for the pats and air temp corrections.
http://www.turbonutter.net/apps/photos/album?album...
That has the Fuel and ignition using MAP as load and both maps start at -100kpa.
I cant post pictures so the screen shots are here for the pats and air temp corrections.
http://www.turbonutter.net/apps/photos/album?album...
stevesingo said:
Has to OP spoke to the guys responsible for the mapping yet?
Not spoke on the phone, as that is not the easiest thing to do, I did send them the photos & their comment was that there didnt appear to be any serious det doing on looking at the pistons and head & suggested to use a cometic head gasket and ARP studs.I have asked them last week about the scaling on the maps and as of now no reply...
Megaflow said:
What I was trying to understand is this, if the map table starts at 0kPa, which we have established, is actually 100kPa atmospheric, what happens when the MAP measures below atmospheric of 100kPa, or a negative value according to the map table, how is the ECU supposed to cope with that?
I fear the answer is it can't...
If the MAP table is scaled correctly 100kPa is atmospheric, < 100kPa is vacuum and > 100kPa is boost.I fear the answer is it can't...
All engines at some point in their operating range will operate in a state of vacuum. How? If the throttle is closed/partially open it is causing the engine (which is essentially a pump) a restriction. If the engine is not allowed to ingest the air it wants, pressure in the manifold will drop. In the case of a correctly scaled MAP table, the ECU will be calibrated to account for this reduction in flow/increase in vacuum. Broadly speaking, say we have a fuel value of 10 at 2000rpm 100kPa, in a closed/partially open throttle condition with a MAP value of 50kPa, we should have a fuel value of 5. As for ignition, we would need to calibrate the ign map on the dyno so we know what ign adv we need for a given MAP value at a given engine speed.
The problem with this calibration is that the ECU has been programmed to believe that there is no such thing as < 100kPa, in which case it cannot be calibrated for engine loads that create less than 100kPa.
Engines need more advance at lower MAP values as cylinder filling is reduced and therefore the combustion event is smaller/slower. This requires an earlier ignition of the charge so we have peak cylinder pressure occuring where it delivers best mechanical advantage on the piston,/rod/crank assembly.
turbonutter said:
Not spoke on the phone, as that is not the easiest thing to do, I did send them the photos & their comment was that there didnt appear to be any serious det doing on looking at the pistons and head & suggested to use a cometic head gasket and ARP studs.
What did they think had destroyed the top land of the piston? Mice? Woodworm?The trouble is in cases like this a County Court judge will understand nothing of the technicalities and will rely solely on independent expert evidence which is costly and beyond most people's willingness to push things that far. Hence it's almost unheard of for incompetent tuners to be made to pay up.
turbonutter said:
Just for some comparison I looked in the default maps in the haltech software & dug out the one for a Subaru WRX.
That has the Fuel and ignition using MAP as load and both maps start at -100kpa.
I cant post pictures so the screen shots are here for the pats and air temp corrections.
http://www.turbonutter.net/apps/photos/album?album...
that looks a good example of a decent amount of advance in the vacuum area ,and a safe amount of retard in the boost area .in fact you would probably have been better off if they had just loaded that .That has the Fuel and ignition using MAP as load and both maps start at -100kpa.
I cant post pictures so the screen shots are here for the pats and air temp corrections.
http://www.turbonutter.net/apps/photos/album?album...
I think yours may need a bit more timing on boost ,as long as the temps are sub 40c ,and your turbo has low tip. as inlet temps rise your can plonk in a correction to retard it.
stevesingo said:
If the MAP table is scaled correctly 100kPa is atmospheric, < 100kPa is vacuum and > 100kPa is boost.
All engines at some point in their operating range will operate in a state of vacuum. How? If the throttle is closed/partially open it is causing the engine (which is essentially a pump) a restriction. If the engine is not allowed to ingest the air it wants, pressure in the manifold will drop. In the case of a correctly scaled MAP table, the ECU will be calibrated to account for this reduction in flow/increase in vacuum. Broadly speaking, say we have a fuel value of 10 at 2000rpm 100kPa, in a closed/partially open throttle condition with a MAP value of 50kPa, we should have a fuel value of 5. As for ignition, we would need to calibrate the ign map on the dyno so we know what ign adv we need for a given MAP value at a given engine speed.
The problem with this calibration is that the ECU has been programmed to believe that there is no such thing as < 100kPa, in which case it cannot be calibrated for engine loads that create less than 100kPa.
Engines need more advance at lower MAP values as cylinder filling is reduced and therefore the combustion event is smaller/slower. This requires an earlier ignition of the charge so we have peak cylinder pressure occuring where it delivers best mechanical advantage on the piston,/rod/crank assembly.
That is what my mind was telling me, but it never hurts to have it confirmed.All engines at some point in their operating range will operate in a state of vacuum. How? If the throttle is closed/partially open it is causing the engine (which is essentially a pump) a restriction. If the engine is not allowed to ingest the air it wants, pressure in the manifold will drop. In the case of a correctly scaled MAP table, the ECU will be calibrated to account for this reduction in flow/increase in vacuum. Broadly speaking, say we have a fuel value of 10 at 2000rpm 100kPa, in a closed/partially open throttle condition with a MAP value of 50kPa, we should have a fuel value of 5. As for ignition, we would need to calibrate the ign map on the dyno so we know what ign adv we need for a given MAP value at a given engine speed.
The problem with this calibration is that the ECU has been programmed to believe that there is no such thing as < 100kPa, in which case it cannot be calibrated for engine loads that create less than 100kPa.
Engines need more advance at lower MAP values as cylinder filling is reduced and therefore the combustion event is smaller/slower. This requires an earlier ignition of the charge so we have peak cylinder pressure occuring where it delivers best mechanical advantage on the piston,/rod/crank assembly.
Thanks for that.
Pumaracing said:
Struth. We've answered this specifically and in detail over and over again in the previous 3 pages. If you don't understand any of what's being written maybe you should stick to threads with more basic topics.
Sadly, we can't all be born knowing everything and some of us have to learn it.Thanks for nothing.
Don't take this the wrong way op but why is the power level so important ??
I run a car with a few things in common , similar layout and weight with the same pwr cooler and ran compound charged system with nearly 500hp and it was just hard work to drive and suffered a few failures down to using stretch bolts for the head .
Now running a straight 2.3 turbo set up with decent rods/pistons and arp studs . Mapped for 480hp at 1.7 bar and runs 1 bar on spring pressure with around 300hp which is enough for 90% of the time on public roads .
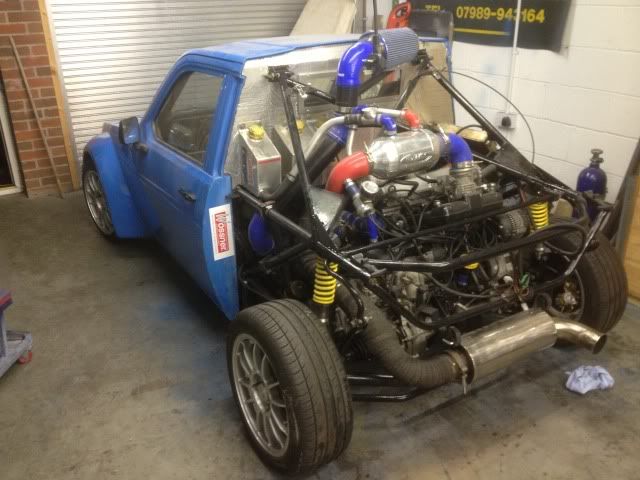
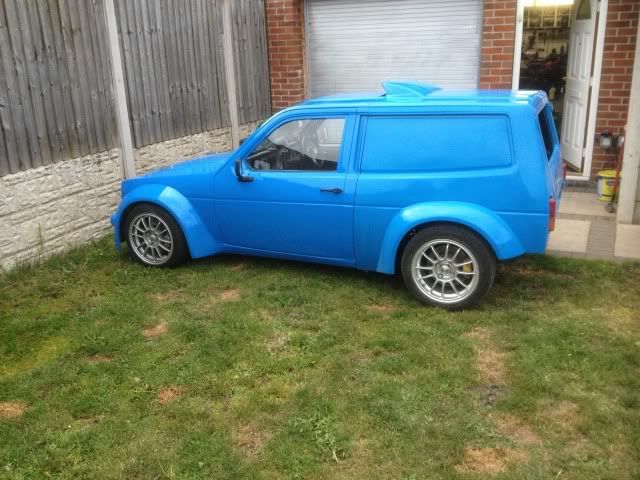
Probably another 50hp in there but at peak boost the cooler temps stay pretty constant and no det issues mainly down to the Saab knock sensing system .
I run a car with a few things in common , similar layout and weight with the same pwr cooler and ran compound charged system with nearly 500hp and it was just hard work to drive and suffered a few failures down to using stretch bolts for the head .
Now running a straight 2.3 turbo set up with decent rods/pistons and arp studs . Mapped for 480hp at 1.7 bar and runs 1 bar on spring pressure with around 300hp which is enough for 90% of the time on public roads .
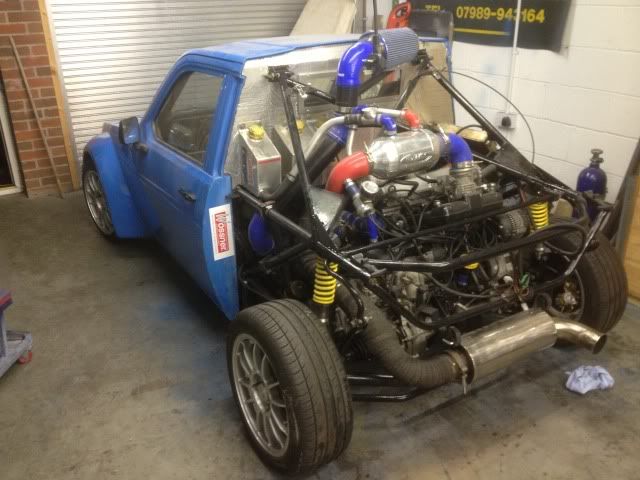
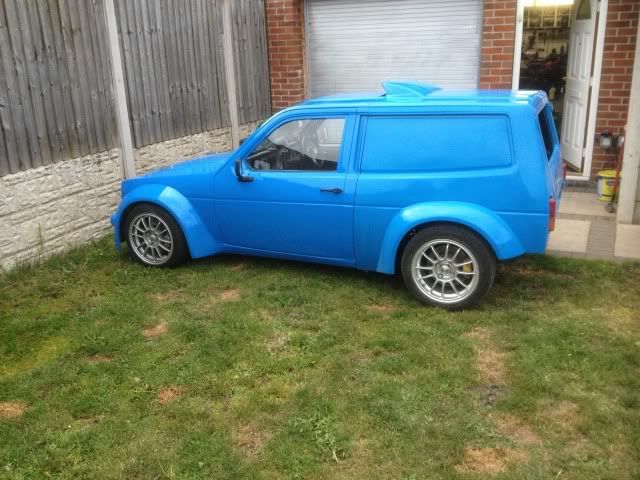
Probably another 50hp in there but at peak boost the cooler temps stay pretty constant and no det issues mainly down to the Saab knock sensing system .
Megaflow said:
Pumaracing said:
Struth. We've answered this specifically and in detail over and over again in the previous 3 pages. If you don't understand any of what's being written maybe you should stick to threads with more basic topics.
Sadly, we can't all be born knowing everything and some of us have to learn it.1) A sensor outputs a signal proportional to a physical parameter. Generally speaking, the signals characteristic that changes should do so linearly with changes in the physical parameter. In the case of a MAP sensor, air pressure acts on a sensing device that converts this pressure to an analogue voltage, that is proportional and linear to that pressure. So, say your MAP sensor is rated for 2bar(abs), you would expect to get zero output voltage at 0bar(abs) and full output voltage at 2bar(abs). In this example, we will assume the MAP sensor is sat at 1barA and outputting a stable and constant voltage of exactly half the supply voltage fed to it
2) For analogue voltages, the embedded microcontroller will use an Analogue to Digital Convertor (ADC) to establish a finite digital value for the current analogue voltage being applied from the sensor. It does this by comparing the input voltage to a reference voltage. Usually the reference voltage is the same as that used to power the sensor, say 5Vdc. Because the ADC is digital, it has a finite number of discrete "steps" or "counts" available. This is referred to as it's resolution. A typical ADC in an engine controller will be a 10bit device (10bits = 2^10 steps = 1024 steps, where 0 = 0v, and 1024 = ref voltage) The result cannot be anything but one of these discrete steps (i.e. it can't be 23 and a half counts say, it must be 23 OR 24 counts) For a 5v reference voltage (typical) that gives us 5v/1024 counts as our best resolution (0.00488V = 4.88mV). In our example, we have a 2.5V signal, that is converted to 512 counts by the ADC
3) A 1D lookup table, or a linear or polynomial expression is then used to convert this ADC count value into "real" units. In this case, with a 2bar(abs) sensor input, we would assign 0barA to 0counts, and 2barA to 1024 counts. Once again, we can calculate the resolution of our system to far (2bar/1024 counts = 0.00195barA or 0.2kPa roughly) Hence, the system as we currently have it, cannot "see" pressure changes of less that 0.2kPa (a relatively decent resolution actually) In this case, we have 512 x 0.00195 = 1barA
4) So, now we have our MAP sensor data, in real units of barA, and with a value of 1
5) Lets say we want to then use this value to "look up" an output value from a calibratable "map" set by the engine tuner. Maps can be 1d, 2d, 3d......Nd (it gets very confusing and difficult to visualise above 3d but mathematically possible!). This refers to how many other parameters the output value varies with. For the sake of simplicity, we'll assume a basic 1d look up table here. A lookup table is really just an area of discrete and finite (you'll see these words a lot when discussing digital electronics!) memory, that is used to attempt to describe a physical characteristic or control property. Generally the way the lookup table data is accessed is as follows:
a) the axis value is compared to the input value to either find a match or to find which two axis values the input value sits between. If we had a "3" cell axis, that has values or 0,1,2 barA, then clearly our input value of 1bar sits exact on the 2nd cell. If the input value does not exactly match one of the axis cell values (much more likely) then the system works out between which two cells it does sit, and by how much. i.e. if our input value was 1.5, it would sit 50% of the way between axis cells 2 & 3. That is called interpolation. Generally speaking, if the input value lies beyond the limits of the axis data, the system will just return the closest cell number (ie. input = 2.5, axis cell = 3)
b) the corresponding output table is then accessed (must be same length as the axis data, ie. 3 cells in this case). If we say our example table had values of 0,10,20 then our output values would be 10, 15, and 20, respectively for the 3 cases above.
As you can see, the complications and subtleties are almost endless, and we haven't even talked about bandwidth in the frequency domain, non linearities in the ADC, errors from ground and reference voltage offset, the capabilities of the sensor itself, Noise and crucially signal to noise ratio, oversampling, ADC type, internal variable type (number of bits) etc etc!
For OEM engine management, a vast amount of time and effort is expended in determining the capability of the system to repeatedly resolve the various input signals into the digital domain accurately with precision and reliability! The exact method and coding of the input scaling and crucially the interpolation routines for the look up tables is critical to delivering a high quality output
mighty kitten said:
Don't take this the wrong way op but why is the power level so important ??
I run a car with a few things in common , similar layout and weight with the same pwr cooler and ran compound charged system with nearly 500hp and it was just hard work to drive and suffered a few failures down to using stretch bolts for the head .
Now running a straight 2.3 turbo set up with decent rods/pistons and arp studs . Mapped for 480hp at 1.7 bar and runs 1 bar on spring pressure with around 300hp which is enough for 90% of the time on public roads .
Probably another 50hp in there but at peak boost the cooler temps stay pretty constant and no det issues mainly down to the Saab knock sensing system .
The goal of this build initially was 500BHP at 1.3-1.4 bar. Which from a 3.2 24V engine is not that huge an amount. Even with the 575 that I had it is only 180bhp/L. Your engine is nearly 210bhp/l.I run a car with a few things in common , similar layout and weight with the same pwr cooler and ran compound charged system with nearly 500hp and it was just hard work to drive and suffered a few failures down to using stretch bolts for the head .
Now running a straight 2.3 turbo set up with decent rods/pistons and arp studs . Mapped for 480hp at 1.7 bar and runs 1 bar on spring pressure with around 300hp which is enough for 90% of the time on public roads .
Probably another 50hp in there but at peak boost the cooler temps stay pretty constant and no det issues mainly down to the Saab knock sensing system .
Yes it has gone over the 500bhp, but I am running less than 1.2 bar - Yes on the road that is too much, but I have low boost for the road if I want. On track though all of the power is useable & if like suggested a different map may widen my power band then it will be improved....and reliable..
Lets face it you dont stick a big turbo on an engine and run it at under 1bar

Max_Torque said:
It's worth a quick recap on how an engine management system (or any 'embedded' microcontroller for that matter) actually works:
1) A sensor outputs a signal proportional to a physical parameter. Generally speaking, the signals characteristic that changes should do so linearly with changes in the physical parameter. In the case of a MAP sensor, air pressure acts on a sensing device that converts this pressure to an analogue voltage, that is proportional and linear to that pressure. So, say your MAP sensor is rated for 2bar(abs), you would expect to get zero output voltage at 0bar(abs) and full output voltage at 2bar(abs). In this example, we will assume the MAP sensor is sat at 1barA and outputting a stable and constant voltage of exactly half the supply voltage fed to it
2) For analogue voltages, the embedded microcontroller will use an Analogue to Digital Convertor (ADC) to establish a finite digital value for the current analogue voltage being applied from the sensor. It does this by comparing the input voltage to a reference voltage. Usually the reference voltage is the same as that used to power the sensor, say 5Vdc. Because the ADC is digital, it has a finite number of discrete "steps" or "counts" available. This is referred to as it's resolution. A typical ADC in an engine controller will be a 10bit device (10bits = 2^10 steps = 1024 steps, where 0 = 0v, and 1024 = ref voltage) The result cannot be anything but one of these discrete steps (i.e. it can't be 23 and a half counts say, it must be 23 OR 24 counts) For a 5v reference voltage (typical) that gives us 5v/1024 counts as our best resolution (0.00488V = 4.88mV). In our example, we have a 2.5V signal, that is converted to 512 counts by the ADC
3) A 1D lookup table, or a linear or polynomial expression is then used to convert this ADC count value into "real" units. In this case, with a 2bar(abs) sensor input, we would assign 0barA to 0counts, and 2barA to 1024 counts. Once again, we can calculate the resolution of our system to far (2bar/1024 counts = 0.00195barA or 0.2kPa roughly) Hence, the system as we currently have it, cannot "see" pressure changes of less that 0.2kPa (a relatively decent resolution actually) In this case, we have 512 x 0.00195 = 1barA
4) So, now we have our MAP sensor data, in real units of barA, and with a value of 1
5) Lets say we want to then use this value to "look up" an output value from a calibratable "map" set by the engine tuner. Maps can be 1d, 2d, 3d......Nd (it gets very confusing and difficult to visualise above 3d but mathematically possible!). This refers to how many other parameters the output value varies with. For the sake of simplicity, we'll assume a basic 1d look up table here. A lookup table is really just an area of discrete and finite (you'll see these words a lot when discussing digital electronics!) memory, that is used to attempt to describe a physical characteristic or control property. Generally the way the lookup table data is accessed is as follows:
a) the axis value is compared to the input value to either find a match or to find which two axis values the input value sits between. If we had a "3" cell axis, that has values or 0,1,2 barA, then clearly our input value of 1bar sits exact on the 2nd cell. If the input value does not exactly match one of the axis cell values (much more likely) then the system works out between which two cells it does sit, and by how much. i.e. if our input value was 1.5, it would sit 50% of the way between axis cells 2 & 3. That is called interpolation. Generally speaking, if the input value lies beyond the limits of the axis data, the system will just return the closest cell number (ie. input = 2.5, axis cell = 3)
b) the corresponding output table is then accessed (must be same length as the axis data, ie. 3 cells in this case). If we say our example table had values of 0,10,20 then our output values would be 10, 15, and 20, respectively for the 3 cases above.
As you can see, the complications and subtleties are almost endless, and we haven't even talked about bandwidth in the frequency domain, non linearities in the ADC, errors from ground and reference voltage offset, the capabilities of the sensor itself, Noise and crucially signal to noise ratio, oversampling, ADC type, internal variable type (number of bits) etc etc!
For OEM engine management, a vast amount of time and effort is expended in determining the capability of the system to repeatedly resolve the various input signals into the digital domain accurately with precision and reliability! The exact method and coding of the input scaling and crucially the interpolation routines for the look up tables is critical to delivering a high quality output
Thanks Max, very interesting. I work for an engine manufacturer, and the mechanical side I get, it understanding what the P&E boys are doing for 000's of hours on end, apart from breaking engines, is always useful and interesting.1) A sensor outputs a signal proportional to a physical parameter. Generally speaking, the signals characteristic that changes should do so linearly with changes in the physical parameter. In the case of a MAP sensor, air pressure acts on a sensing device that converts this pressure to an analogue voltage, that is proportional and linear to that pressure. So, say your MAP sensor is rated for 2bar(abs), you would expect to get zero output voltage at 0bar(abs) and full output voltage at 2bar(abs). In this example, we will assume the MAP sensor is sat at 1barA and outputting a stable and constant voltage of exactly half the supply voltage fed to it
2) For analogue voltages, the embedded microcontroller will use an Analogue to Digital Convertor (ADC) to establish a finite digital value for the current analogue voltage being applied from the sensor. It does this by comparing the input voltage to a reference voltage. Usually the reference voltage is the same as that used to power the sensor, say 5Vdc. Because the ADC is digital, it has a finite number of discrete "steps" or "counts" available. This is referred to as it's resolution. A typical ADC in an engine controller will be a 10bit device (10bits = 2^10 steps = 1024 steps, where 0 = 0v, and 1024 = ref voltage) The result cannot be anything but one of these discrete steps (i.e. it can't be 23 and a half counts say, it must be 23 OR 24 counts) For a 5v reference voltage (typical) that gives us 5v/1024 counts as our best resolution (0.00488V = 4.88mV). In our example, we have a 2.5V signal, that is converted to 512 counts by the ADC
3) A 1D lookup table, or a linear or polynomial expression is then used to convert this ADC count value into "real" units. In this case, with a 2bar(abs) sensor input, we would assign 0barA to 0counts, and 2barA to 1024 counts. Once again, we can calculate the resolution of our system to far (2bar/1024 counts = 0.00195barA or 0.2kPa roughly) Hence, the system as we currently have it, cannot "see" pressure changes of less that 0.2kPa (a relatively decent resolution actually) In this case, we have 512 x 0.00195 = 1barA
4) So, now we have our MAP sensor data, in real units of barA, and with a value of 1
5) Lets say we want to then use this value to "look up" an output value from a calibratable "map" set by the engine tuner. Maps can be 1d, 2d, 3d......Nd (it gets very confusing and difficult to visualise above 3d but mathematically possible!). This refers to how many other parameters the output value varies with. For the sake of simplicity, we'll assume a basic 1d look up table here. A lookup table is really just an area of discrete and finite (you'll see these words a lot when discussing digital electronics!) memory, that is used to attempt to describe a physical characteristic or control property. Generally the way the lookup table data is accessed is as follows:
a) the axis value is compared to the input value to either find a match or to find which two axis values the input value sits between. If we had a "3" cell axis, that has values or 0,1,2 barA, then clearly our input value of 1bar sits exact on the 2nd cell. If the input value does not exactly match one of the axis cell values (much more likely) then the system works out between which two cells it does sit, and by how much. i.e. if our input value was 1.5, it would sit 50% of the way between axis cells 2 & 3. That is called interpolation. Generally speaking, if the input value lies beyond the limits of the axis data, the system will just return the closest cell number (ie. input = 2.5, axis cell = 3)
b) the corresponding output table is then accessed (must be same length as the axis data, ie. 3 cells in this case). If we say our example table had values of 0,10,20 then our output values would be 10, 15, and 20, respectively for the 3 cases above.
As you can see, the complications and subtleties are almost endless, and we haven't even talked about bandwidth in the frequency domain, non linearities in the ADC, errors from ground and reference voltage offset, the capabilities of the sensor itself, Noise and crucially signal to noise ratio, oversampling, ADC type, internal variable type (number of bits) etc etc!
For OEM engine management, a vast amount of time and effort is expended in determining the capability of the system to repeatedly resolve the various input signals into the digital domain accurately with precision and reliability! The exact method and coding of the input scaling and crucially the interpolation routines for the look up tables is critical to delivering a high quality output
Edited by Megaflow on Monday 16th September 21:09
turbonutter said:
And not forgetting - power is addictive

100% agree... also with a turbo car its very easy to restrict power if you end up with too much 


My map is set to restrict boost depending upon throttle possition... so its extremelly easy to drive it on full power and just use the throttle to feed it in as required.... I never drive my car on anything but high boost, even in the rain on Mich cups

Hows the rebuild going?
andygtt said:
100% agree... also with a turbo car its very easy to restrict power if you end up with too much 
My map is set to restrict boost depending upon throttle possition... so its extremelly easy to drive it on full power and just use the throttle to feed it in as required.... I never drive my car on anything but high boost, even in the rain on Mich cups
Hows the rebuild going?
Re build.... I am now away at work until December, so no building until next year..... 
My map is set to restrict boost depending upon throttle possition... so its extremelly easy to drive it on full power and just use the throttle to feed it in as required.... I never drive my car on anything but high boost, even in the rain on Mich cups

Hows the rebuild going?
For now its just some more research & decide which bits I need to order, based on long lead times...
Boost tied to throttle position sounds like a good idea, it should make it much more progressive and the power is just a stab of the right foot away

Gassing Station | Engines & Drivetrain | Top of Page | What's New | My Stuff