Extra cam lubrication - is this a good idea?
Discussion
slideways said:
what about taping into the front of the block so you have a fixing at both ends
I have been thinking about that - also if I tapped into the oilway at the front of the block I would have the pipe fed from both ends. As an aside I found these pics of a straight 6 BMW engine rebuild, and there is a spray bar with what seems like no support whatsoever apart from each end, but I guess the pipe is steel. (I think this is the BMW engine Chassis 33 referred to on the first page of the thread).
I've emailed the guys who produced the website to see if there is any support other than either end (and I sent them a link to this thread so sorry guys I borrowed your pics!).



Edited by Barkychoc on Sunday 11th October 22:38
Reply from Patrick the guy with the BMW engine.
Patrick the BMW engine owner said:
Hi Chris,
Interesting project
Yeah the spray bar in the BMW M20 basically looks like a brake pipe with a union either end and holes along the middle. There's no other support other than the two ends.
Thanks, Patrick
Interesting project

Yeah the spray bar in the BMW M20 basically looks like a brake pipe with a union either end and holes along the middle. There's no other support other than the two ends.
Thanks, Patrick
Edited by Barkychoc on Saturday 10th October 22:33
Barkychoc said:
For the middle bracket to make it clearer I was thinking of drilling & tapping as shown roughly here.
Thinking round in circles I came to the same conclusion. It just doesn't seem right to leave that length flapping around and I think the strap you have will do the job nicely. All I'd add is to solder the strap to the pipe before you fit it, so the pipe is firmly supported and not just held down.OK I just threw this together to prove the concept - I'm not looking for marks for precision engineering!
The bracket is attached by M4 tapping the block where you can see the 2 screw heads thorough the copper.
I have also now drilled and tapped the pipe into the oilway at the front of the block so it is now attached at both ends.
This is really just a 'first draft' go at making a bracket, I know its a bit rough.
The hole is drilled through the small clamping piece of copper to allow me to solder it all up.
It didn't take long to do really (maybe thats obvious!) so I am considering making 3 brackets, one for each web, it might be a bit OTT but better safe than sorry.
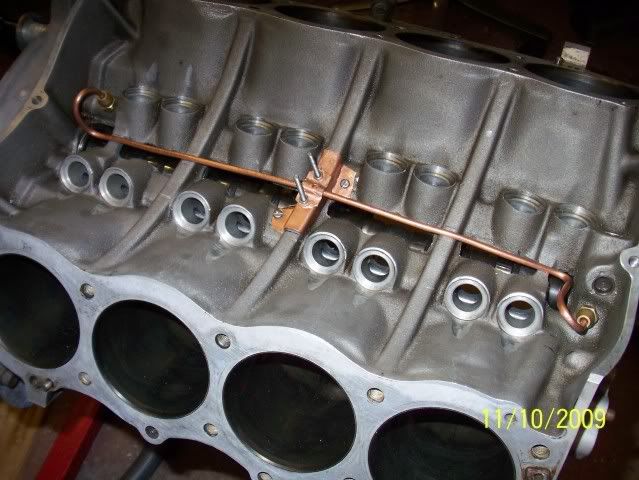
The bracket is attached by M4 tapping the block where you can see the 2 screw heads thorough the copper.
I have also now drilled and tapped the pipe into the oilway at the front of the block so it is now attached at both ends.
This is really just a 'first draft' go at making a bracket, I know its a bit rough.
The hole is drilled through the small clamping piece of copper to allow me to solder it all up.
It didn't take long to do really (maybe thats obvious!) so I am considering making 3 brackets, one for each web, it might be a bit OTT but better safe than sorry.
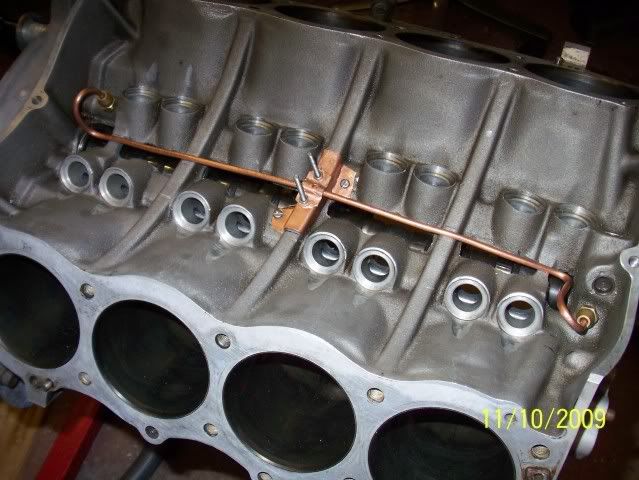
Edited by Barkychoc on Sunday 11th October 20:52
I think the damage those supporting screws could do if they came out would be far worse that the tube moving about a bit. If it has some bends in it them it will be stiffer anyway.
When are you going to fire the engine up and prove the concept ?
Nice video of all the oil being flung around your garage
When are you going to fire the engine up and prove the concept ?
Nice video of all the oil being flung around your garage

Barkychoc said:
slideways said:
what about taping into the front of the block so you have a fixing at both ends
I have been thinking about that - also if I tapped into the oilway at the front of the block I would have the pipe fed from both ends. As an aside I found these pics of a straight 6 BMW engine rebuild, and there is a spray bar with what seems like no support whatsoever apart from each end, but I guess the pipe is steel. (I think this is the BMW engine Chassis 33 referred to on the first page of the thread).
I've emailed the guys who produced the website to see if there is any support other than either end (and I sent them a link to this thread so sorry guys I borrowed your pics!).
Regards
Iain
Chassis 33 said:
YUP thats an M20 head, seeing as I'm in the process of replacing my mullered engine I might be able to donate the pipe work to the cause. My only reservation with what you're doing is that you could be robbing too much oil from other areas that need good flow and pressure to feed an issue that only required a small drip, like I said the M20 offers a slow drip maybe once a second, its by no means a pressurised spray.
Regards
Iain
I'm looking for a drip drip really - not an oil pressure washer, but I think there's only one way to see what happens. I'm planning to drill 0.3mm outlet holes in the pipe.Regards
Iain
If it needs slowing down maybe I'll have to do something in TVR tradition like crush the pipe a bit

Iain - I'm not sure the pipe would be of use I guess the holes would be all wrong but it might be useful to see it if its going begging.
With regard to the bolts - I will use threadlock but there's also potential to put a nyloc nut on the other side - its not a flat 90 degree surface as the bolt comes out the other side but I'm sure something could be done, but with decent threadlock I reckon it should be OK anyway.
Edited by Barkychoc on Monday 12th October 13:17
Barkychoc said:
I'm planning to drill 0.3mm outlet holes in the pipe.
Hot oil flows like water and I think 0.3mm at 50 psi might produce rather more than you want. Perhaps worth testing the flow rate to see what you get. Ideally you want to testing using something which when cold has similar viscosity to hot engine oil. I suppose there is probably a light oil that is about right.Following on I've done a bit of testing, heres a video.
This is at 50psi, using cold waste oil (Mobil1 15/50) with 0.4mm holes in the pipe.
Note cold oil is thicker than hot, so 0.4mm holes will be too big but I got 10 drill bits cheap just to see if we are anywhere close to this having some potential, I think there's still some mileage in it.
Video Link
This is at 50psi, using cold waste oil (Mobil1 15/50) with 0.4mm holes in the pipe.
Note cold oil is thicker than hot, so 0.4mm holes will be too big but I got 10 drill bits cheap just to see if we are anywhere close to this having some potential, I think there's still some mileage in it.
Video Link
Edited by Barkychoc on Sunday 8th November 12:29
Barkychoc said:
Note cold oil is thicker than hot
What sort of flow rate are you aiming for? Unless you've seen the difference in viscosity between oil at 20C and 100C I don't think you will appreciate how thin it gets. Try your test again with water instead of oil and I think you'll get something more realistic. Or get the oil and everything else good and hot and try again.Much as I like the idea of this, there is another perhaps more elegant way of getting oil to the cam/lifter interface by 'just' grooving the correct side of the lifter bore from the cross-gallery down to the bottom lip on the side the cam 'approaches' from in rotation. As well as directing an oilstream to the cam surface, this also assists lifter rotation.
Suspect a version of the tool shown on p334 here would do the job. Next one I build will have this done for sure
Suspect a version of the tool shown on p334 here would do the job. Next one I build will have this done for sure

GPT said:
So what happened in the end?
Sorry to drag up an old thread but I found it very interesting when I first read it and was hoping for a bit of resolution.
Sorry but ... nothing!Sorry to drag up an old thread but I found it very interesting when I first read it and was hoping for a bit of resolution.
I think the groove idea is great in the post by Pupp above, but I just haven't had time or cash to progress anything further yet.
Gassing Station | Chimaera | Top of Page | What's New | My Stuff