Extra cam lubrication - is this a good idea?
Discussion
Since my car has a worn cam I've been thinking how to get some additional lubrication to the lobes.
My thought is to fabricate an oil spray bar from a bit of brake pipe with oil outlet holes (small) drilled underneath where the black marks are on the tube below.
I have seen this arrangement on a number of ford engines though I guess it must be used elsewhere too.
Where the X is on the left side of the picture is the end of the oil gallery - so I would drill and tap that with an M10 x 1.0 brake pipe fitting then connect the pipe to it.
The right hand end of the bar would be blocked off - either just capped or I thought possibly through the valley wall at the front of the engine and fitted with a small valve to allow the pipe to be flushed through at service time to stop any sludge build up at the end (just open the valve and let the oil come out for a brief period).
(You can get small valves from model steam engine parts suppliers).
The downside that I can see is that it will affect the oil pressure - and I'm running pre serp which I guess won't help. Can anyone with more knowledge than me hazard a guess if this would be a serious drop?
The other maybe slightly wild tangent I had is to fit a solenoid valve so it only runs when the engine is cold and oil pressure is higher, but I think this is added complexity that you just don't need.
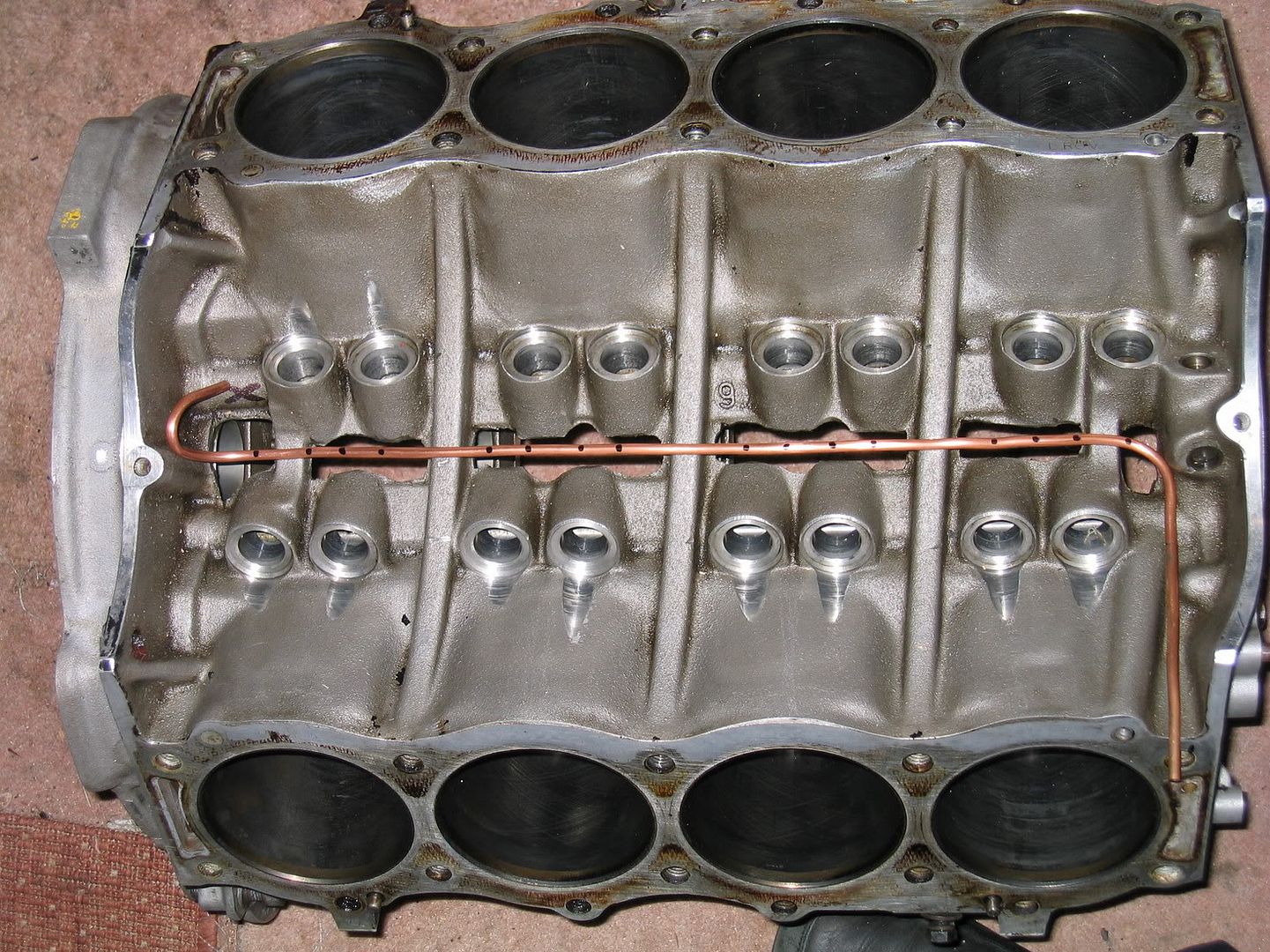
My thought is to fabricate an oil spray bar from a bit of brake pipe with oil outlet holes (small) drilled underneath where the black marks are on the tube below.
I have seen this arrangement on a number of ford engines though I guess it must be used elsewhere too.
Where the X is on the left side of the picture is the end of the oil gallery - so I would drill and tap that with an M10 x 1.0 brake pipe fitting then connect the pipe to it.
The right hand end of the bar would be blocked off - either just capped or I thought possibly through the valley wall at the front of the engine and fitted with a small valve to allow the pipe to be flushed through at service time to stop any sludge build up at the end (just open the valve and let the oil come out for a brief period).
(You can get small valves from model steam engine parts suppliers).
The downside that I can see is that it will affect the oil pressure - and I'm running pre serp which I guess won't help. Can anyone with more knowledge than me hazard a guess if this would be a serious drop?
The other maybe slightly wild tangent I had is to fit a solenoid valve so it only runs when the engine is cold and oil pressure is higher, but I think this is added complexity that you just don't need.
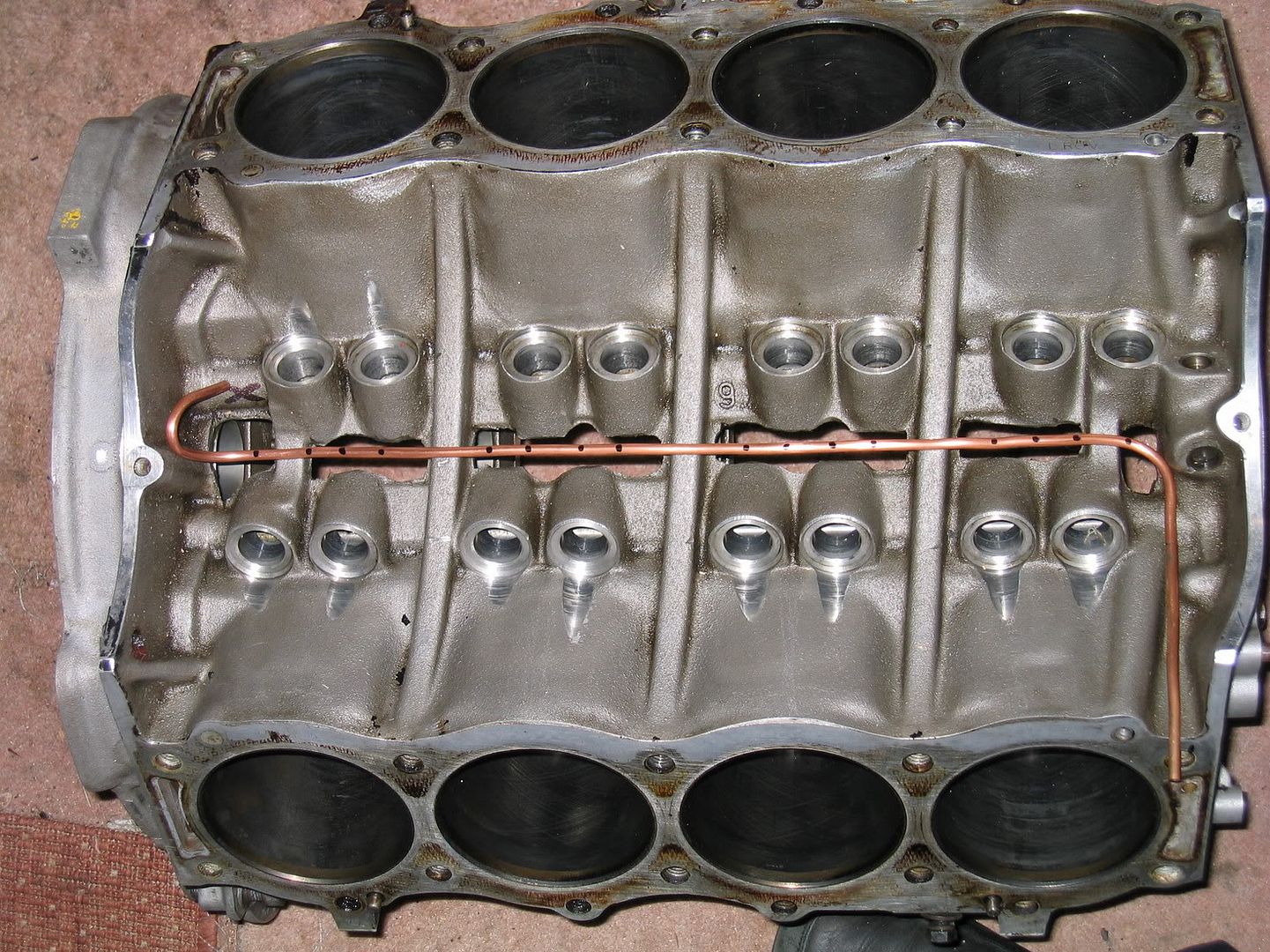
spend said:
Personally, I think its the wrong approach
There is plenty of oil from the rockers draining back down the valley - as well as the stuff coming out of the followers? Why would a pressure feed be necessary, surely just a sheet with holes that made all that oil drip where you wanted it would be better?
I do and don't agree with you Dave.
I think the lubrication for a Range Rover lolloping along at 2500 revs for most of its life is probably marginal at best with the oil eventually coming off the bottom of the followers after startup.
Add to the mix strong double valve springs, a peaky cam and the tendency to rev the nuts off the engine occasionally (technical term) and I don't think its any wonder we see worn cams.
I am seriously thinking of giving this a go - my engine is only a 3.9 litre lump anyway so if I screw it up it won't be the end of the world.
The initial plan is to plumb it in and see what happens when I drive the oil pump with a drill with the inlet manifold & valley gasket off.
Edited by Barkychoc on Thursday 14th May 18:29
OK thinking about this a bit further.
I feel I ought to use copper/nickel pipe rather than copper - whats the view?
It has been suggested above to use 0.3mm holes for the jets - does this sound about right?
It feels like a very small hole to me, left to it I probably would have gone to something like 0.6 but would that be too large? After all there will be 16 of them.
Will 3/16" pipe provide enough flow?
Any further suggestions positive or negative welcome.
I feel I ought to use copper/nickel pipe rather than copper - whats the view?
It has been suggested above to use 0.3mm holes for the jets - does this sound about right?
It feels like a very small hole to me, left to it I probably would have gone to something like 0.6 but would that be too large? After all there will be 16 of them.
Will 3/16" pipe provide enough flow?
Any further suggestions positive or negative welcome.
OK back to the topic - only a little progress but taking a drill to my block was a f
n big step for me today!
Oilway drilled & tapped M10x1.0 (brake pipe fitting thread).
I took the plug out of the rear of the block in order to remove the swarf (pipe cleaners are great for stuff like this
)
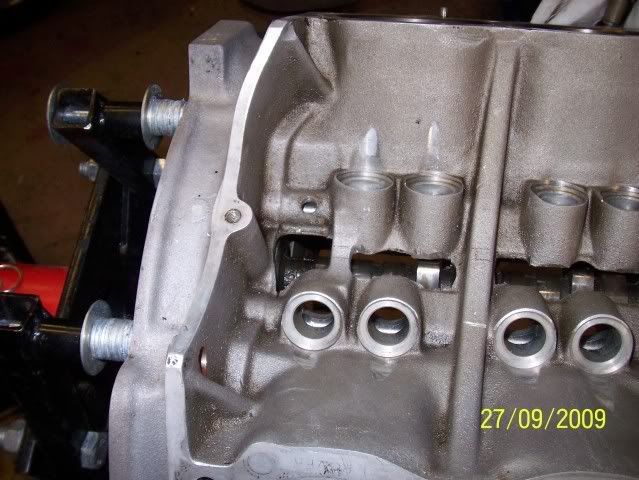
Just to test the fitting this is sawn off the end of an old flexible brake pipe, I'll get a proper (longer thread) bulkhead fitting.
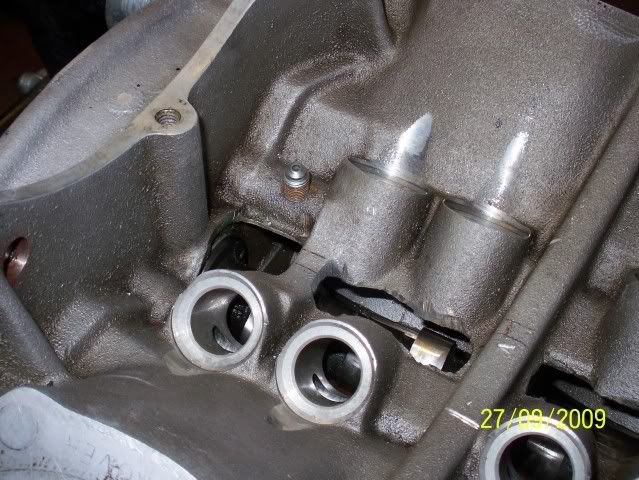
Pipe in place
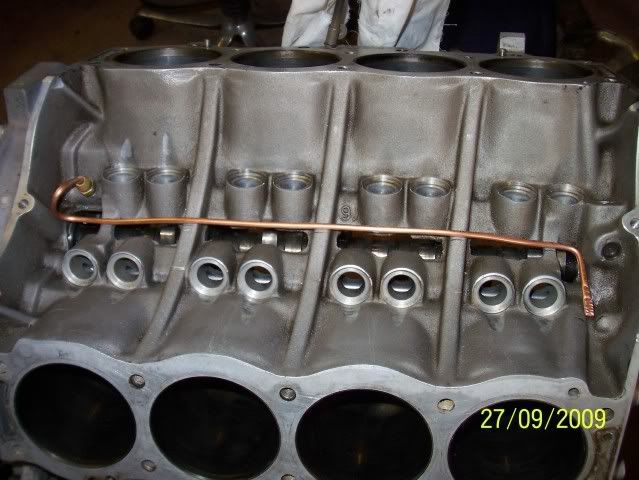

I haven't fully figured out how I'm going to secure it yet - probably just some steel wire around the thin webs at each end unless anyone has a better suggestion.
I'll get the engine back together and drive the oil pump with a drill & see what happens.
I can always blank off the hole if it ends up being a waste of time.

Oilway drilled & tapped M10x1.0 (brake pipe fitting thread).
I took the plug out of the rear of the block in order to remove the swarf (pipe cleaners are great for stuff like this

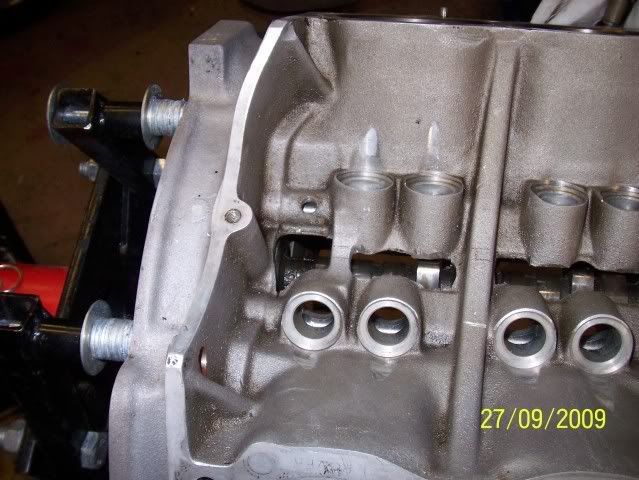
Just to test the fitting this is sawn off the end of an old flexible brake pipe, I'll get a proper (longer thread) bulkhead fitting.
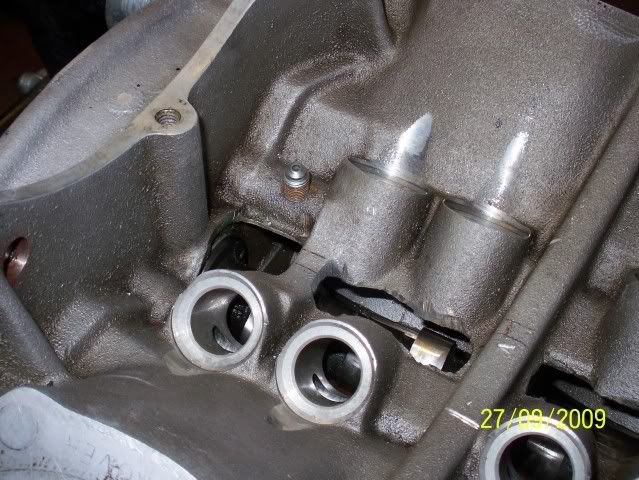
Pipe in place
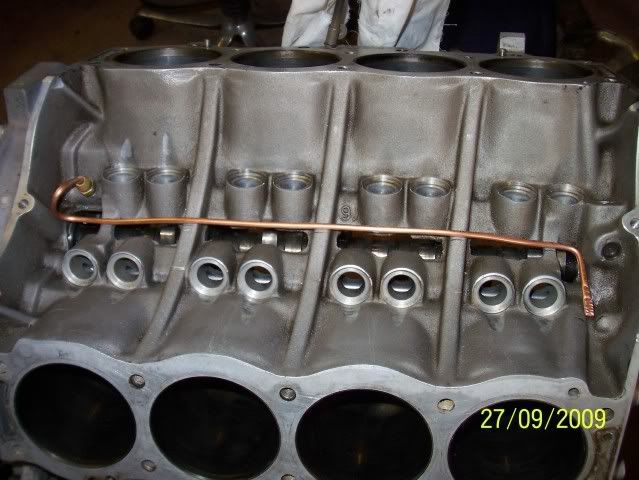

I haven't fully figured out how I'm going to secure it yet - probably just some steel wire around the thin webs at each end unless anyone has a better suggestion.
I'll get the engine back together and drive the oil pump with a drill & see what happens.
I can always blank off the hole if it ends up being a waste of time.
Edited by Barkychoc on Sunday 27th September 21:08
Pupp said:
It would be a major leap of faith to do and I've no idea what it would do to the stiffness of the block but the three thicker webs in the middle would physically take holes to pass the spray bar through... 
I'm not prepared to leap that far - and have you given some thought to how you would actually get a drill in to drill the webs - it can't be done! 
OK you might manage it with one of those right angle jobbies but I'm not going to do it.
I have a couple of thoughts that might work, I'll share them when I've had a tinker.
With regard to the pipe fracturing I'll give that some thought too

Edited by Barkychoc on Sunday 27th September 22:02
OK moving on to securing the pipe, does this work for you?
On the one hand its a crude bodge, on the other maybe Rover & TVR would have been proud!
Wire threaded under web
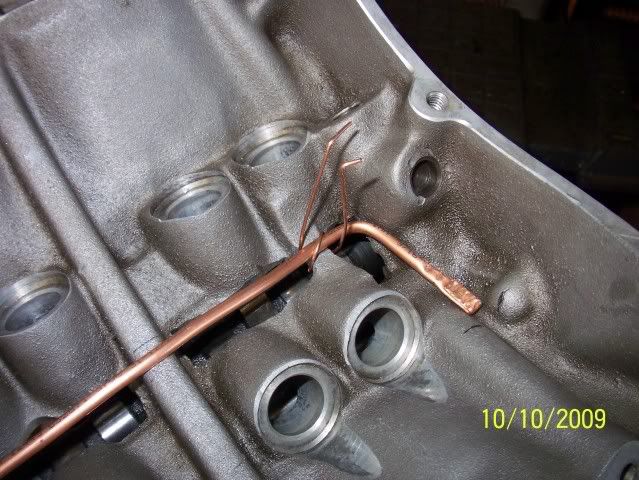
Twisted to secure
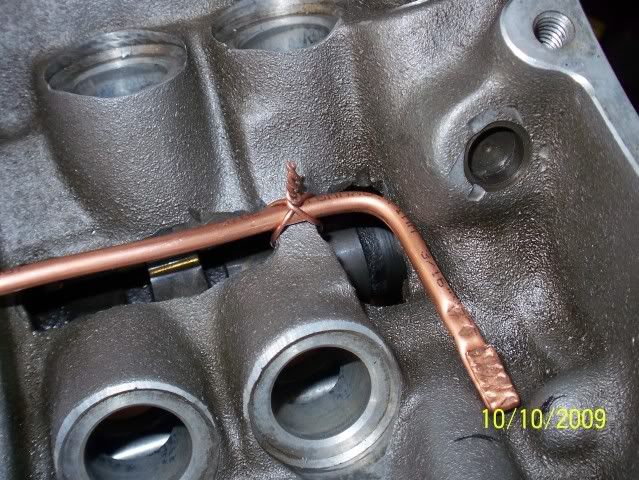
Pipe secured at both ends
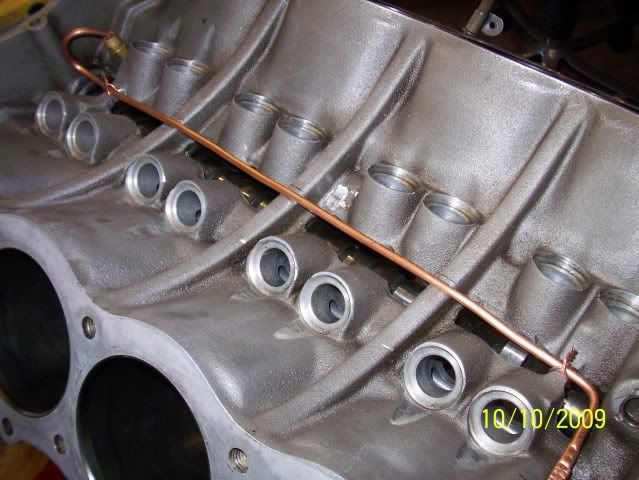
It needs additional support in the centre, my thoughts are to drill and tap the webs and fit a metal strap where the white tape is. There is enough room without hitting the oilway for the tappets to get something like a 4-5mm thread in there. You can see the oilway drilling to avoid in the tappet holes.
You can't see but I also filed a light groove in the top of the webs where the pipe sits just to locate it in position.
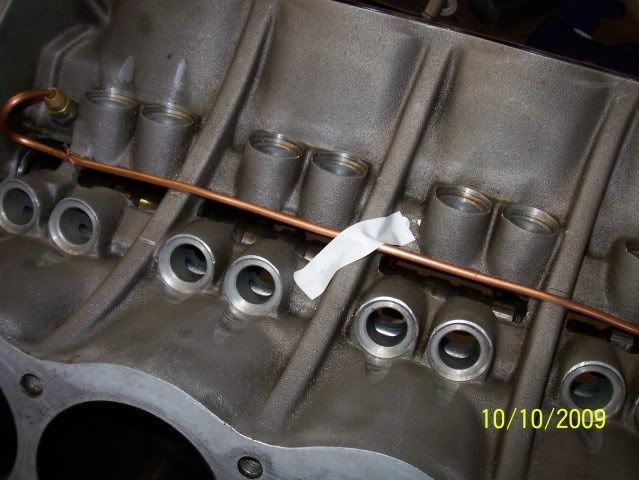
All comments welcomed for and against.
On the one hand its a crude bodge, on the other maybe Rover & TVR would have been proud!

Wire threaded under web
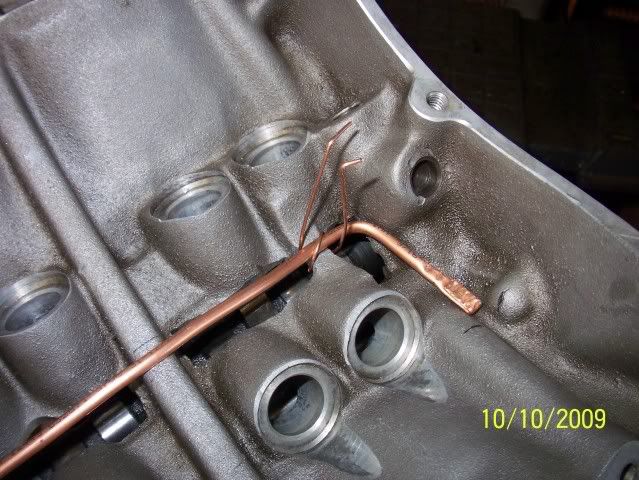
Twisted to secure
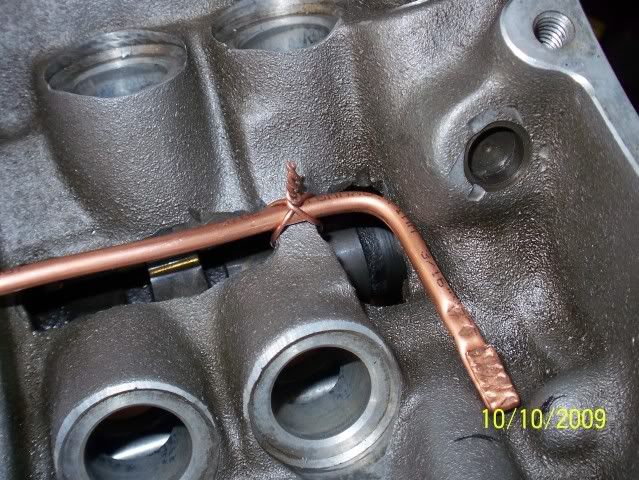
Pipe secured at both ends
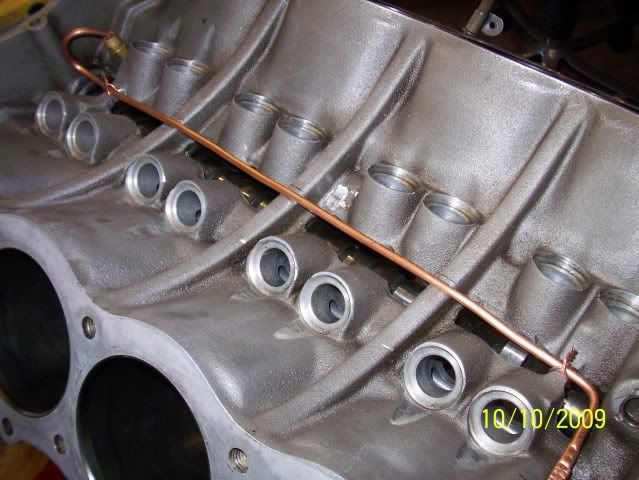
It needs additional support in the centre, my thoughts are to drill and tap the webs and fit a metal strap where the white tape is. There is enough room without hitting the oilway for the tappets to get something like a 4-5mm thread in there. You can see the oilway drilling to avoid in the tappet holes.
You can't see but I also filed a light groove in the top of the webs where the pipe sits just to locate it in position.
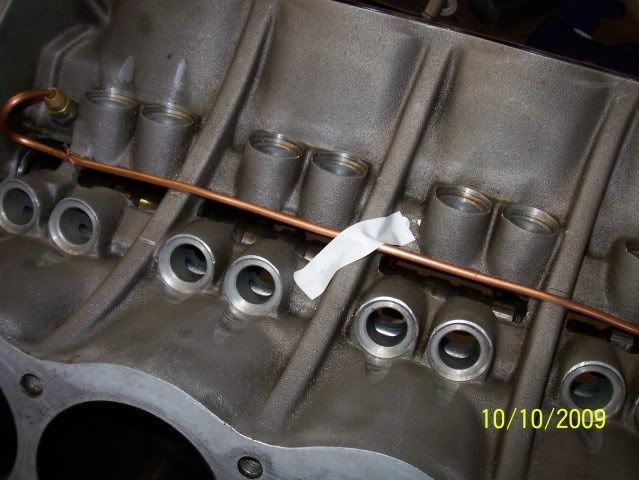
All comments welcomed for and against.
Edited by Barkychoc on Saturday 10th October 15:39
For the middle bracket to make it clearer I was thinking of drilling & tapping as shown roughly here.
I really didn't want to drill the webs across the valley if I could help it.
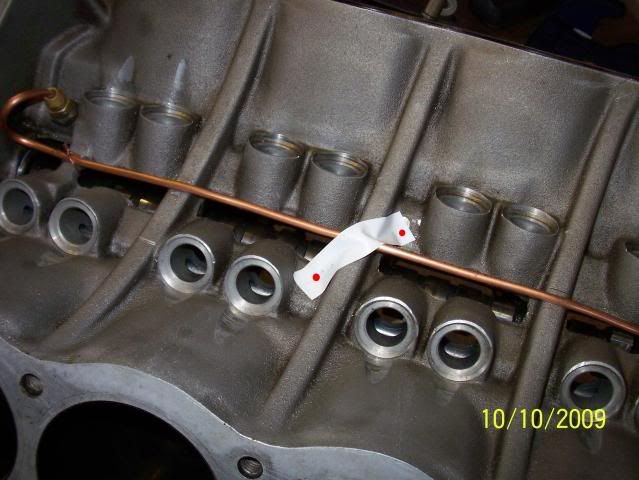
I presume the brackets you are thinking about are P clips like these?

They could be a good idea - a similar arrangement is used on the old ford pinto oil pipe you can see in the top of this pack.

I'm also considering maybe using either kunifer or steel for the pipe, I'm still pondering.
I really didn't want to drill the webs across the valley if I could help it.
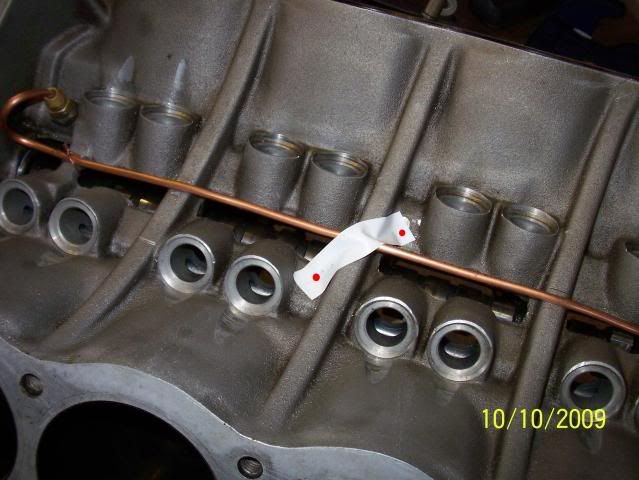
I presume the brackets you are thinking about are P clips like these?

They could be a good idea - a similar arrangement is used on the old ford pinto oil pipe you can see in the top of this pack.

I'm also considering maybe using either kunifer or steel for the pipe, I'm still pondering.
Edited by Barkychoc on Saturday 10th October 17:31
slideways said:
what about taping into the front of the block so you have a fixing at both ends
I have been thinking about that - also if I tapped into the oilway at the front of the block I would have the pipe fed from both ends. As an aside I found these pics of a straight 6 BMW engine rebuild, and there is a spray bar with what seems like no support whatsoever apart from each end, but I guess the pipe is steel. (I think this is the BMW engine Chassis 33 referred to on the first page of the thread).
I've emailed the guys who produced the website to see if there is any support other than either end (and I sent them a link to this thread so sorry guys I borrowed your pics!).



Edited by Barkychoc on Sunday 11th October 22:38
Reply from Patrick the guy with the BMW engine.
Patrick the BMW engine owner said:
Hi Chris,
Interesting project
Yeah the spray bar in the BMW M20 basically looks like a brake pipe with a union either end and holes along the middle. There's no other support other than the two ends.
Thanks, Patrick
Interesting project

Yeah the spray bar in the BMW M20 basically looks like a brake pipe with a union either end and holes along the middle. There's no other support other than the two ends.
Thanks, Patrick
Edited by Barkychoc on Saturday 10th October 22:33
OK I just threw this together to prove the concept - I'm not looking for marks for precision engineering!
The bracket is attached by M4 tapping the block where you can see the 2 screw heads thorough the copper.
I have also now drilled and tapped the pipe into the oilway at the front of the block so it is now attached at both ends.
This is really just a 'first draft' go at making a bracket, I know its a bit rough.
The hole is drilled through the small clamping piece of copper to allow me to solder it all up.
It didn't take long to do really (maybe thats obvious!) so I am considering making 3 brackets, one for each web, it might be a bit OTT but better safe than sorry.
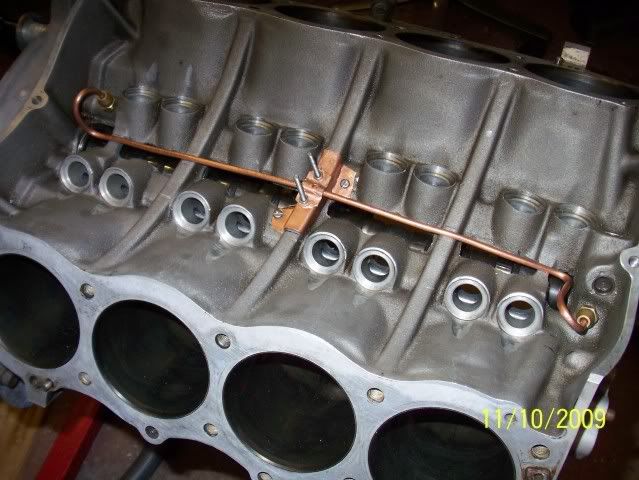
The bracket is attached by M4 tapping the block where you can see the 2 screw heads thorough the copper.
I have also now drilled and tapped the pipe into the oilway at the front of the block so it is now attached at both ends.
This is really just a 'first draft' go at making a bracket, I know its a bit rough.
The hole is drilled through the small clamping piece of copper to allow me to solder it all up.
It didn't take long to do really (maybe thats obvious!) so I am considering making 3 brackets, one for each web, it might be a bit OTT but better safe than sorry.
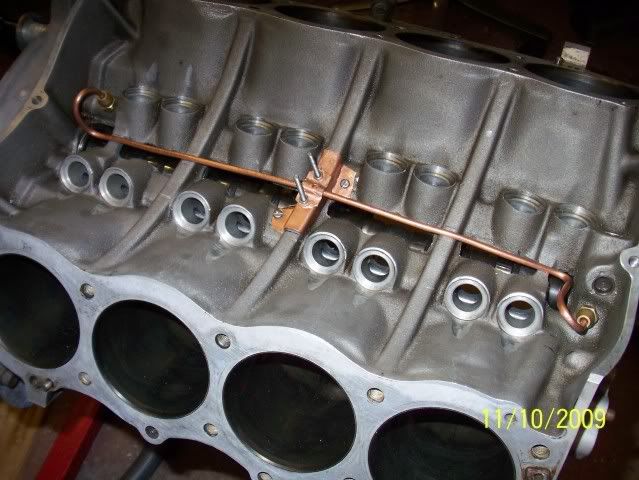
Edited by Barkychoc on Sunday 11th October 20:52
Chassis 33 said:
YUP thats an M20 head, seeing as I'm in the process of replacing my mullered engine I might be able to donate the pipe work to the cause. My only reservation with what you're doing is that you could be robbing too much oil from other areas that need good flow and pressure to feed an issue that only required a small drip, like I said the M20 offers a slow drip maybe once a second, its by no means a pressurised spray.
Regards
Iain
I'm looking for a drip drip really - not an oil pressure washer, but I think there's only one way to see what happens. I'm planning to drill 0.3mm outlet holes in the pipe.Regards
Iain
If it needs slowing down maybe I'll have to do something in TVR tradition like crush the pipe a bit

Iain - I'm not sure the pipe would be of use I guess the holes would be all wrong but it might be useful to see it if its going begging.
With regard to the bolts - I will use threadlock but there's also potential to put a nyloc nut on the other side - its not a flat 90 degree surface as the bolt comes out the other side but I'm sure something could be done, but with decent threadlock I reckon it should be OK anyway.
Edited by Barkychoc on Monday 12th October 13:17
Following on I've done a bit of testing, heres a video.
This is at 50psi, using cold waste oil (Mobil1 15/50) with 0.4mm holes in the pipe.
Note cold oil is thicker than hot, so 0.4mm holes will be too big but I got 10 drill bits cheap just to see if we are anywhere close to this having some potential, I think there's still some mileage in it.
Video Link
This is at 50psi, using cold waste oil (Mobil1 15/50) with 0.4mm holes in the pipe.
Note cold oil is thicker than hot, so 0.4mm holes will be too big but I got 10 drill bits cheap just to see if we are anywhere close to this having some potential, I think there's still some mileage in it.
Video Link
Edited by Barkychoc on Sunday 8th November 12:29
GPT said:
So what happened in the end?
Sorry to drag up an old thread but I found it very interesting when I first read it and was hoping for a bit of resolution.
Sorry but ... nothing!Sorry to drag up an old thread but I found it very interesting when I first read it and was hoping for a bit of resolution.
I think the groove idea is great in the post by Pupp above, but I just haven't had time or cash to progress anything further yet.
I wimped out in the end. Rob Robertson pointed out that only half the lobes would get a good oiling - the ones that hit the follower straight after having oil dripped on them. Where the cam has to rotate 270 degrees before it get to the follower after oil drip most of it would be thrown off.
I have the pipe fitted just no holes in it!
I wish I had bought that chevy tool now and made the grooves in the block where the followers go - its back in this thread somewhere I'm on my phone so not so easy to look. That thinking about it is a better solution.
Chris
I have the pipe fitted just no holes in it!
I wish I had bought that chevy tool now and made the grooves in the block where the followers go - its back in this thread somewhere I'm on my phone so not so easy to look. That thinking about it is a better solution.
Chris
Gassing Station | Chimaera | Top of Page | What's New | My Stuff