Instructions to change fuel maps on 14CUX Griffith, Chimaera
Discussion
Colin has released a new version of RoverGauge version 0.9.3 to fix the disappearing column headings and also includes the recent additions, like displaying the battery saved data and a new scalar to recalibrate the RoverGauge Speedo that does not effect the ECU's internal road speed.
I would like to take this opportunity to thank Colin & Dan on behalf of the hundreds of RoverGauge users for implementing all our requests quickly and effectively. RoverGauge looks and feels like a very professional, mature and complete diagnostic tools and we are all very very lucky and grateful its free. I've always believed the best software is free and RoverGauge certainly proves it.
Three Cheers for Colin and his father Dan for cracking the 14CUX, Mark Blitz for making the cables and Mark Blitz & DaveP for their continued support.
Heres the latest RoverGauge Version 0.9.3
https://github.com/colinbourassa/rovergauge/releas...
Battery saved data
I would like to take this opportunity to thank Colin & Dan on behalf of the hundreds of RoverGauge users for implementing all our requests quickly and effectively. RoverGauge looks and feels like a very professional, mature and complete diagnostic tools and we are all very very lucky and grateful its free. I've always believed the best software is free and RoverGauge certainly proves it.
Three Cheers for Colin and his father Dan for cracking the 14CUX, Mark Blitz for making the cables and Mark Blitz & DaveP for their continued support.
Heres the latest RoverGauge Version 0.9.3
https://github.com/colinbourassa/rovergauge/releas...
Battery saved data
$40 | Temporary use during right lambda calculations (2 bytes) |
$42 | Lambda Long Trim Right (2 bytes) |
$44 | Temporary use during left lambda calculations (2 bytes) |
$46 | Lambda Long Trim Left (2 bytes) |
$48 | High Fuel Temperature (2 bytes) |
$40 -> $4E | Fault Codes (6 bytes) |
$4F | Stepper Motor Saved Value |
$50 | Fuel Map Number |
$51 | Throttle Pot Minimum (2 bytes) |
$53 | Throttle Pot Min Copy & ram Checksum (2 bytes) |
cosecon said:
Good day to all!!!
Lately I have been testing different roms with minor adjustments to my Land Rover Defender 14cux.
Just a quick info for my setup.: Rover V8 4.0 crossbolted block. ported heads from 3.5. mild road cam with anti pump lifters. Increased compression and megajolt for spark.
Yesterday I started with the original R3652 rom and did the following changes:
1. base idle 700
2. neutral idle 100
3. overrun fueling 04 (this corresponds to 4500 i suppose)
4. coasting idle hold up (offset 0242) 21 (hex) ;experimenting.
I installed and start the engine (warm day). On the first 3 or 4 traffic lights the idle rpm was fluctuating and the engine died.
For a couple of traffic lights i kept the idle with my foot on accelerator.
After that "magically" idle was perfect.
I continue driving with no any problem.
Finally I decided to test full throttle. The moment I reached 5000+ rpm (I have a rev limiter with megajolt @ about 5000rpm by fully dropping the advance to 0). The engine died completely and would not start . Switch off and on ... no start...Remove refit ecu start normally.
Retried full throttle engine dies...
What do you think?
NOT POSSIBLE TO RESTART UNLESS ECU IS UNPLUGGED and PLUGGED.
Checked with other roms, no problem.
Hi again KonstantinosLately I have been testing different roms with minor adjustments to my Land Rover Defender 14cux.
Just a quick info for my setup.: Rover V8 4.0 crossbolted block. ported heads from 3.5. mild road cam with anti pump lifters. Increased compression and megajolt for spark.
Yesterday I started with the original R3652 rom and did the following changes:
1. base idle 700
2. neutral idle 100
3. overrun fueling 04 (this corresponds to 4500 i suppose)
4. coasting idle hold up (offset 0242) 21 (hex) ;experimenting.
I installed and start the engine (warm day). On the first 3 or 4 traffic lights the idle rpm was fluctuating and the engine died.
For a couple of traffic lights i kept the idle with my foot on accelerator.
After that "magically" idle was perfect.
I continue driving with no any problem.
Finally I decided to test full throttle. The moment I reached 5000+ rpm (I have a rev limiter with megajolt @ about 5000rpm by fully dropping the advance to 0). The engine died completely and would not start . Switch off and on ... no start...Remove refit ecu start normally.
Retried full throttle engine dies...
What do you think?
NOT POSSIBLE TO RESTART UNLESS ECU IS UNPLUGGED and PLUGGED.
Checked with other roms, no problem.
I'm sorry to hear your Megajolt rpm limter is crashing the 14CUX and unfortunately sorry I have no idea why it won’t restart after hitting your Megajolt rpm limiter with Land Rover’s original R3652 rom. I’ll be very surprised if it doesn’t restart after turning off the ignition for more than 5 seconds until you hear the main relay click off as that clears down all the internal temporary ram data and resets the processor, but obviously not the battery saved data.
Your choice of Land Rovers original R3652 makes a lot of sense as that’s Land Rover’s last revision for high compression 3.9s, however here’s Land Rover original high compression rom from the previous year 1994 and certainly worth trying first unmodified.
www.stevesprint.com/remap-14cux/bins/LR_R3360_94_3...
You may have the warming up idle issues as your coasting idle hold up (rom offset 242) of hex 21 seems far too low, it should be 6C hex, increasing the ‘coasting idle hold up’ actually lowers the ‘hold up idle’ and decreasing it raises the’ hold up idle’ and only requires small adjustments for example hex 8 at a time. The ECU will require unpluging after change the coasting idle hold up as it value is held in the battery saved data.
The overrun fuelling of 04 hex raises the upper starting point of the overrun fuel cut to 4,500 rpm meaning fuel is not cut off when lifting off below 4,500 rpm.
We know when revving passed 5,000 rpm the 14CUX processor starts running out of processing time between the sparks and maybe your Megajolt suddenly altering the spark advance at 5,000 rpm changes the spark periods enough to crash the processor but I don't know. This is more of a question for Dan as he has commented in the past how some roms have been optimised to save processing time and maybe the reason why some roms don't crash but again I don’t know.
Sorry & Good Luck
cosecon said:
stevesprint said:
You may have the warming up idle issues as your coasting idle hold up (rom offset 242) of hex 21 seems far too low, it should be 6C hex, increasing the ‘coasting idle hold up’ actually lowers the ‘hold up idle’ and decreasing it raises the’ hold up idle’ and only requires small adjustments for example hex 8 at a time.
I tried 21 because one ROM from Tornado is like this. Just to experiment. cosecon said:
I do not believe it is the Megajolt. The Megajolt is the best thing that happened to my engine.
Today I did the following, I prepared a simple R3652 with no mod and it works perfect at Rev limit. I am not sure. Maybe I made some change accidentally.
Thanks for putting my mind at ease.Today I did the following, I prepared a simple R3652 with no mod and it works perfect at Rev limit. I am not sure. Maybe I made some change accidentally.
jjohnson23 said:
Hello all,its been a while since I have been on here.
Unfortunately both the car and myself suffered illness at the beginning of the year.
The car has a new heart(well 2nd hand) as the original engine had a bad misfire which turned out to be a wiped inlet cam lobe.
I had already built a new bottom end (3.9),so I put a new std cam in and got the rear axle changed to a 3.08:1.
Anyway,I would like to use a normal Range Rover image such as R3652 but eliminate the speed limiter just to get me on my way again.
Would this be possible and if so where would the location I need to alter be?
Sorry to impose but I have not had the opportunity to play for a while and would like to get back on the road now that I can get about now.
Sorry to hear you’ve both suffered illness, but at least you’re both now on the road to recovery, 3.08:1 brings back memories of my old TR7 V8 14CUX. Unfortunately both the car and myself suffered illness at the beginning of the year.
The car has a new heart(well 2nd hand) as the original engine had a bad misfire which turned out to be a wiped inlet cam lobe.
I had already built a new bottom end (3.9),so I put a new std cam in and got the rear axle changed to a 3.08:1.
Anyway,I would like to use a normal Range Rover image such as R3652 but eliminate the speed limiter just to get me on my way again.
Would this be possible and if so where would the location I need to alter be?
Sorry to impose but I have not had the opportunity to play for a while and would like to get back on the road now that I can get about now.
Sorry, I currently I don’t have the standard Land Rover R3652 with just the Road Speed limiter removed however I’ll happily build one for you.
To get you on the road you could try any of the following and then let me know what configuration your prefer, like idle speed, rpm limiter, overrun cracks & pops etc.
Land Rover OEM
http://home.btconnect.com/stevesprint/remap-14cux/...
http://www.stevesprint.com/remap-14cux/bins/LR_R33...
Land Rover with Raised idle, road speed limiter removed and lower idle immediate after cranking,
http://home.btconnect.com/stevesprint/remap-14cux/...
TVR 400 Precat and CAT merged into one tune.
http://home.btconnect.com/stevesprint/remap-14cux/...
Good Luck
Steve
Mark,
Its brilliant you’re keen to perfect the idle control as its a common cause of complaint and you’re making impressive progress with the assembler code. Dan always said the idle control code is the most complicated part of the code as you’ve discovered.
Normally the stepper is held fully open before cranking up to the temperature stored at prom offset 17E (87 deg C) which is inside the cranking stepper control table at offset 17B to 195 and the stepper is then controllable before cranking above 87 deg c.
A few years ago I changing “cmpb $C17E” to “cmpb $C182” in the code below which appears in the RoverGauge screen shot to allow stepper control before cranking down to –14 degrees C as required and even starts ok, BUT sadly before cranking you can hear the stepper motor buzzing which must mean the stepper is repeatedly pulled fully open again elsewhere in the code. We really need to flow diagram idleControl.asm, stepperMtr2.asm and coolant.asm to understand the bigger picture, I've tried several times and end up lost in the maze of code.
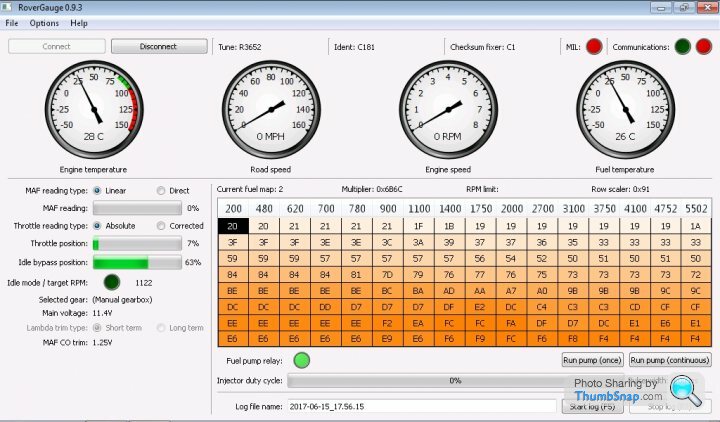
It make sense what you are trying to do but unfortunately raising the base idle without stepper control before cranking is exacerbating your cranking issue and also creates other issues like raising the coasting idle which can all be re-adjusted for. This is because all the stepper control code and data tables are written for a larger difference between the base idle and target idle. Mark Blitz normally recommends setting the base idle as low as possible i.e. just before the engine stalls without any extra air via the stepper and the stepper should normally be between 20% to 30% when idling hot.
As a result I’ve been lowering the base idle as much as possible as it also reduces your initial cranking idle issue and coasting idle. Eventually lowering the base idle too much then creates a hot cranking idle issue which I’ve successfully over come with my hot start fix.
Two heads are better than one (I don’t mean cylinder heads) and investigating both avenues is a good way to learn and help find the best solution to improve our cars.
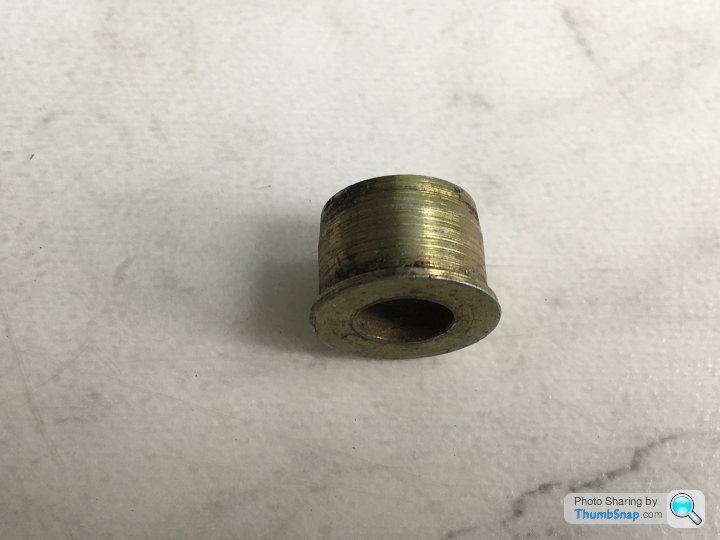
Its brilliant you’re keen to perfect the idle control as its a common cause of complaint and you’re making impressive progress with the assembler code. Dan always said the idle control code is the most complicated part of the code as you’ve discovered.
Normally the stepper is held fully open before cranking up to the temperature stored at prom offset 17E (87 deg C) which is inside the cranking stepper control table at offset 17B to 195 and the stepper is then controllable before cranking above 87 deg c.
A few years ago I changing “cmpb $C17E” to “cmpb $C182” in the code below which appears in the RoverGauge screen shot to allow stepper control before cranking down to –14 degrees C as required and even starts ok, BUT sadly before cranking you can hear the stepper motor buzzing which must mean the stepper is repeatedly pulled fully open again elsewhere in the code. We really need to flow diagram idleControl.asm, stepperMtr2.asm and coolant.asm to understand the bigger picture, I've tried several times and end up lost in the maze of code.
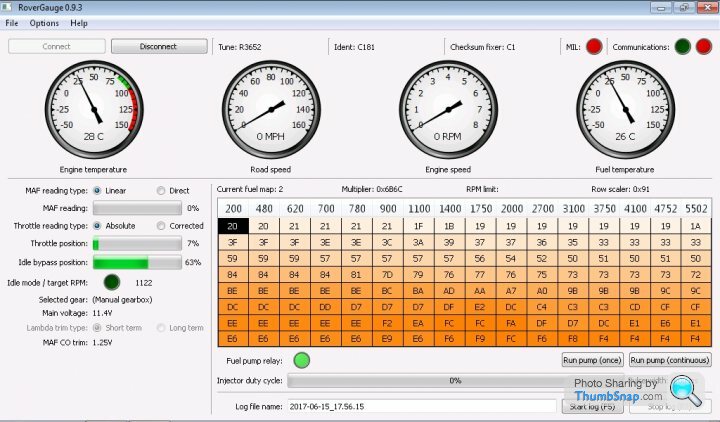
;Land Rover 3.9: R3652, R3383 & all TVR 2967 4L - 5L except 430BVCat
;Degrees C 130 114 94 87 55 50 25 -14 -21
C17B DB $00, $0B, $1C, $23, $48, $51, $88, $E4, $F2 ; Coolant temperature (Compared one ahead)
C184 DB $78, $78, $A0, $A0, $88, $85, $72, $50, $1E ; Column starting Y Axis
C18D DB $00, $97, $00, $2A, $15, $16, $18, $E5, $08 ; Rate of increase/decrease to right (00=flat)
idleControl.asm
ldaa $0085 ; bits value
bita #$04 ; test 0085.2 (set and tested in IS routine)
bne .LD690 ; rtn if 0085.2 is set
bita #$80 ; test 0085.7 (may indicate low eng RPM)
beq .LD691 ; branch ahead if 0085.7 is clr (engine running)
ldab ignPeriod
cmpb $C16F ; for 3360 code, value is $53 (353 RPM)
bcs .LD691 ; branch ahead & continue if engine PW is LT $5300 (RPM > 353)
ldab coolantTempCount
cmpb $C17E ; inside coolant temp table (value is $23)
bcs .LD691 ; branch ahead & continue if cool temp is LT $23 (hotter than)
.LD690 rts
eisdielenbiker said:
The effect at 64% so far counts up to 200 rpm only, I will lower this little mor maybe 45% for the summer. You could possibly use the standard coolant idle tab values to get a simple temperatur dependency...if required. In the end you only had to preselect the coolant tab stepper count a little ahead to its appliaction in idlecontrol.asm I will proof the necessity of this further step in November.
Base idle screw is set 700 rpm to keep stepper valve influence at minimum on idle , ECU base software idle is 750 when engine is warm. The first might be causing a higher effect of a 100% open valve immediately after cranking...
Mark,Base idle screw is set 700 rpm to keep stepper valve influence at minimum on idle , ECU base software idle is 750 when engine is warm. The first might be causing a higher effect of a 100% open valve immediately after cranking...
It make sense what you are trying to do but unfortunately raising the base idle without stepper control before cranking is exacerbating your cranking issue and also creates other issues like raising the coasting idle which can all be re-adjusted for. This is because all the stepper control code and data tables are written for a larger difference between the base idle and target idle. Mark Blitz normally recommends setting the base idle as low as possible i.e. just before the engine stalls without any extra air via the stepper and the stepper should normally be between 20% to 30% when idling hot.
As a result I’ve been lowering the base idle as much as possible as it also reduces your initial cranking idle issue and coasting idle. Eventually lowering the base idle too much then creates a hot cranking idle issue which I’ve successfully over come with my hot start fix.
Two heads are better than one (I don’t mean cylinder heads) and investigating both avenues is a good way to learn and help find the best solution to improve our cars.
OR
you could cheat with one of these in the stepper hose or add some washers to the stepper motor plunger to limit the fully open position, but where's the fun in that !!!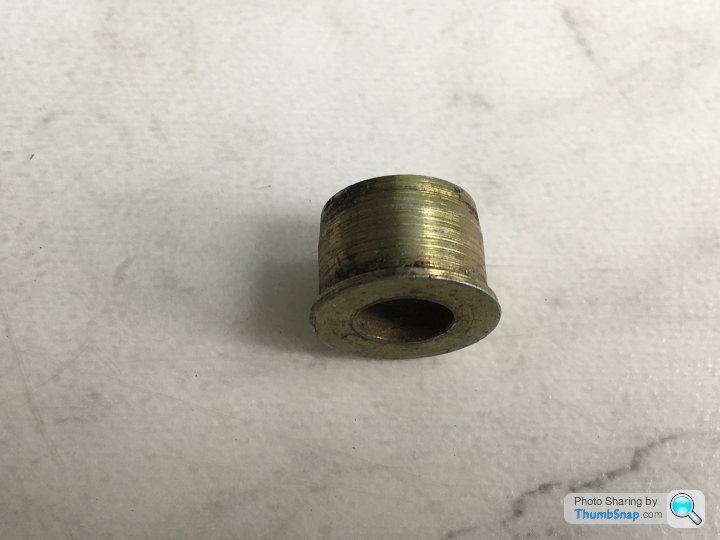
Michael (Tahiti)
Its good to hear from you and to know the GEMS stepper motor code mod worked, thanks. Are you still running the standard GEMs throttle pot with the 14CUX?
There are two temperature thresholds at the very end of each fuel map and one of them might be what you are looking for as they allow different temperature thresholds for each map. Try copying both temperature threshold from map 5 to your map 2 plus you could also try copying the very last byte in map 5 as I think it also has something to do with overrun. I haven’t had cause to experiment with these last four parameters in each map except the ‘full load fuel gain’ which MPO and myself have both proved works. It would be great to tick off these last few parameters in each map.
As you know the overrun fuel cut kicks in when the overrun starts above the RPM set at prom offset 137 & offset 137 definitely works for map 2 and 5. I think prom offset 138 & 139 are the low RPM points when the injectors are reinstated & offset 13B contains the length of delay before closed loop is reinstated after overrun fuel is cut. Also, there is a timer delay from cranking before the overrun fuel cut is active.
I hope this helps disable your overrun fuel and makes towing your boat down hill safer, interesting how TVR owners prefer overrun fuel to increase the sound track.
Its good to hear from you and to know the GEMS stepper motor code mod worked, thanks. Are you still running the standard GEMs throttle pot with the 14CUX?
There are two temperature thresholds at the very end of each fuel map and one of them might be what you are looking for as they allow different temperature thresholds for each map. Try copying both temperature threshold from map 5 to your map 2 plus you could also try copying the very last byte in map 5 as I think it also has something to do with overrun. I haven’t had cause to experiment with these last four parameters in each map except the ‘full load fuel gain’ which MPO and myself have both proved works. It would be great to tick off these last few parameters in each map.
Last four bytes in each map
$2C 78 Deg C Warm up threshold (copied to X200E, Default from offset 13C)
$2D 77 Deg C Warm up threshold (copied to X200F, Default from offset 13A)
$68 Full load fuel Gain Glyn and I have proved this work (copied to X2010)
$3C Deceleration Gain Maybe something to do with overrun (Copied to X2011)
; Coolant Temperature Conversion table from Hex to Deg C.
; First hex byte down, second byte across, therefore 2C is 2 down and C across, 78 Deg C
; 0 1 2 3 4 5 6 7 8 9 A B C D E F
; 0 130,129,127,126,124,123,121,120,118,117,115,114,112,111,109,108, 0
; 1 106,105,104,103,102,101,100, 99, 98, 97, 96, 95, 94, 93, 92, 91, 1
; 2 90, 89, 88, 87, 86, 85, 84, 83, 82, 81, 80, 79, 78, 77, 76, 75, 2
; 3 74, 73, 72, 71, 70, 70, 69, 68, 67, 66, 65, 64, 63, 63, 62, 61, 3
; 4 60, 59, 59, 58, 58, 57, 56, 56, 55, 55, 54, 54, 53, 52, 52, 51, 4
; 5 51, 50, 50, 49, 49, 48, 48, 47, 47, 46, 46, 45, 45, 44, 44, 43, 5
; 6 43, 42, 42, 41, 41, 40, 40, 39, 39, 38, 38, 37, 37, 36, 36, 35, 6
; 7 35, 35, 34, 34, 33, 33, 32, 32, 31, 31, 30, 30, 29, 29, 28, 28, 7
; 8 28, 28, 27, 27, 26, 26, 26, 25, 25, 24, 24, 23, 23, 23, 22, 22, 8
; 9 22, 21, 21, 20, 20, 19, 19, 18, 18, 17, 17, 16, 16, 15, 15, 14, 9
; A 14, 14, 13, 13, 12, 12, 11, 11, 10, 10, 9, 9, 8, 8, 7, 7, A
; B 7, 7, 6, 6, 6, 5, 5, 5, 4, 4, 3, 3, 3, 2, 2, 2, B
; C 2, 1, 1, 0, 0, -1, -1, -2, -2, -3, -3, -4, -4, -5, -5, -6, C
; D -6, -6, -7, -7, -8, -8, -8, -9, -9,-10,-10,-11,-11,-11,-12,-12, D
; E -12,-13,-13,-14,-14,-15,-15,-16,-16,-17,-17,-18,-18,-19,-19,-20, E
; F -20,-20,-21,-21,-22,-22,-22,-23,-23,-23,-24,-24,-24,-25,-25,-25 F
; 0 1 2 3 4 5 6 7 8 9 A B C D E F
As you know the overrun fuel cut kicks in when the overrun starts above the RPM set at prom offset 137 & offset 137 definitely works for map 2 and 5. I think prom offset 138 & 139 are the low RPM points when the injectors are reinstated & offset 13B contains the length of delay before closed loop is reinstated after overrun fuel is cut. Also, there is a timer delay from cranking before the overrun fuel cut is active.
Hex | Rough RPM |
$10 | 1,600 |
$09 | 2,700 |
$08 | 3,000 |
$07 | 3,400 |
$06 | 4,000 |
$05 | 4,800 |
I hope this helps disable your overrun fuel and makes towing your boat down hill safer, interesting how TVR owners prefer overrun fuel to increase the sound track.
Edited by stevesprint on Monday 7th August 19:49
MPO said:
I want to extend my cranking time before the injectors start pulsing any idea where this variable is in the code anyone?
Cheers
MPO
Maybe try "startupDelayCount" in the data asm file, you probably missed it becuase its not in the normal data section (0->800) but rather a constant in the code.Cheers
MPO
Please let me know if it works.
Steve
RR90 said:
Hi, to all first time poster. This is not strictly a tvr issue, but relating to tunerpro and the 14cux adx file.
My hard drive died recently ,and after a new hard drive and new install of win7 (64bit), I am having a problem getting tunerpro to work properly.
After I load the xdf file there are maps and scalars listed on the tree, but only about half of them. Flags are missing altogether.
I have tried various versions of tunerpro, and I have uploaded all the microsoft c++ visual studio things I can find. ,but still no good.
Has anyone here had cause to reload tunerpro recently. Any advice appreciated. Steve ( range rover classic 4.6 Thor manifold)
Yes and I reinstalled an old version.My hard drive died recently ,and after a new hard drive and new install of win7 (64bit), I am having a problem getting tunerpro to work properly.
After I load the xdf file there are maps and scalars listed on the tree, but only about half of them. Flags are missing altogether.
I have tried various versions of tunerpro, and I have uploaded all the microsoft c++ visual studio things I can find. ,but still no good.
Has anyone here had cause to reload tunerpro recently. Any advice appreciated. Steve ( range rover classic 4.6 Thor manifold)
As you are running Windows 7 I suggest you also stick to the older version, below, which also contains the required Visual C++ runtime.
http://www.remap-14cux.uk/TunerPro/TunerProWin7(VC...
Here are my latest 14CUX Definition files and checksum.dll that needs to be copied to the TunerPro directory.
http://www.remap-14cux.uk/TunerPro/TunerPro14CUXCo...
However, if you’ve updated your Visual C++ runtime and can’t down grade VC to the earlier 2013 you could try this later TunerPro 5.
Free Version
http://www.remap-14cux.uk/TunerPro/vc2015/SetupTun...
Emulator Version
http://www.remap-14cux.uk/TunerPro/vc2015/SetupTun...
Visual C++ 2015 Runtime
http://www.remap-14cux.uk/TunerPro/vc2015/vc_redis...
http://www.remap-14cux.uk/TunerPro/vc2015/vc_redis...
Please let me know how you get on.
Steve
Dave (Kiwi RRC)
Sorry for the delayed reply, my son keeps distracting me in the garage with his Rover V8 MX5 project.
I’m impressed you successfully socketed your ECU, its not an easy task especially as its a multi-layer PCB, I’m pleased to learn from yourself R3833 was also used in Discos and not exclusive to RRC.
Mark is right the PROM chip contains both, the 5 fuel maps and the program code, which I’m sure you now know, that’s why I’ve merged TVR’s fuel maps with Land Rover’s later code.
There are a few other proms with later PROGRAM CODE than R3383/R3604 but they are for CAT vehicles with special requirements for example
R3365 NAS 94 Defender (contains code optimisation to improve road speed limiter accuracy)
R3452 Japan MGR V8 (Hot climate with extra ECU monitoring CATs temperatures
R3526 NAS 95 Range Rover Classic
R3652 NAS Cold weather upgrade
If you do give the Aussie and Saudi fuel maps a spin let us know how they run.
Best of luck and please let me know if I can be of further assistance.
Steve
Sorry for the delayed reply, my son keeps distracting me in the garage with his Rover V8 MX5 project.
I’m impressed you successfully socketed your ECU, its not an easy task especially as its a multi-layer PCB, I’m pleased to learn from yourself R3833 was also used in Discos and not exclusive to RRC.
Mark is right the PROM chip contains both, the 5 fuel maps and the program code, which I’m sure you now know, that’s why I’ve merged TVR’s fuel maps with Land Rover’s later code.
KiwiRRC said:
..... is the 3383 about as good as gets for a stock tune for a 1992 RRC 3.9l V8 with no cat and a 14CUX?
YES, even though R3604 is from a 1997 UK 3.9 Disco and must be the very last PROM developed for a UK Vehicle albeit for CATs. This last UK R3604 prom has exactly the same program code and same 5 maps as R3833 but with a few minor tweaks for very cold cranking & cold idle & the minimum temperature to disable closed loop, I’ll add R3604 to my site in case you live in a very cold climate.There are a few other proms with later PROGRAM CODE than R3383/R3604 but they are for CAT vehicles with special requirements for example
R3365 NAS 94 Defender (contains code optimisation to improve road speed limiter accuracy)
R3452 Japan MGR V8 (Hot climate with extra ECU monitoring CATs temperatures
R3526 NAS 95 Range Rover Classic
R3652 NAS Cold weather upgrade
If you do give the Aussie and Saudi fuel maps a spin let us know how they run.
Best of luck and please let me know if I can be of further assistance.
Steve
Gecko
Thanks for your positive feedback, it encourages me to keep my 14CUX efforts going. Please let me know if you need a hand tweaking your map, like increasing the idle or the RPM limiter.
Update (May 2019)
Although this 14CUX effort may appear quiet I’ve been quietly hacking away at the program code this winter and successfully reprogrammed the AC condenser and AC clutch outputs to control my cooling fans in 2 stages at configurable temperature threshold. I’ve put the temperature on/off thresholds in the data section so they can be changed by anyone with a chip programmer and running my cooling fans code enhancement.
I’m also successfully running the bigger 4.6 Bosch MAF sensor by changing the AFM scalar and offset in the fuel map to keep the idle on the second row and full throttle on the bottom row. The 4.6 Bosch MAF also required a full remap and an extra 5 volt reference feed which I took from the throttle POT. I much prefer the Bosch MAF as its electronics are encapsulated inside the cool intake airflow and are more compact which makes room for a heat shield.
I’m now so pleased with the results I’ll tidy up the installation.

The 4.6 Bosch MAF (Part No: 0280 218 010) are available new from your local goodies store including Eurocar Parts and should be available new for a while as the internal hot film sensor (F 00C 2G2 029) is commonly used on BMWs of the same period.
Should you have any questions please do hot hesitate to contact me.
Thanks for your positive feedback, it encourages me to keep my 14CUX efforts going. Please let me know if you need a hand tweaking your map, like increasing the idle or the RPM limiter.
Update (May 2019)
Although this 14CUX effort may appear quiet I’ve been quietly hacking away at the program code this winter and successfully reprogrammed the AC condenser and AC clutch outputs to control my cooling fans in 2 stages at configurable temperature threshold. I’ve put the temperature on/off thresholds in the data section so they can be changed by anyone with a chip programmer and running my cooling fans code enhancement.
I’m also successfully running the bigger 4.6 Bosch MAF sensor by changing the AFM scalar and offset in the fuel map to keep the idle on the second row and full throttle on the bottom row. The 4.6 Bosch MAF also required a full remap and an extra 5 volt reference feed which I took from the throttle POT. I much prefer the Bosch MAF as its electronics are encapsulated inside the cool intake airflow and are more compact which makes room for a heat shield.
I’m now so pleased with the results I’ll tidy up the installation.

The 4.6 Bosch MAF (Part No: 0280 218 010) are available new from your local goodies store including Eurocar Parts and should be available new for a while as the internal hot film sensor (F 00C 2G2 029) is commonly used on BMWs of the same period.
Should you have any questions please do hot hesitate to contact me.
Joolz
No secret, maybe because my 5AM was running at +96% airflow where as the Bosch 4.6 runs at 75% airflow.
Here’s my new 4.6 Bosch MAF from Euro Car Parts, do you know if the part number is correct and the same as the cars you tested.


Here’s a comparison of the AFMs with the inner diameters measured at the narrowest point
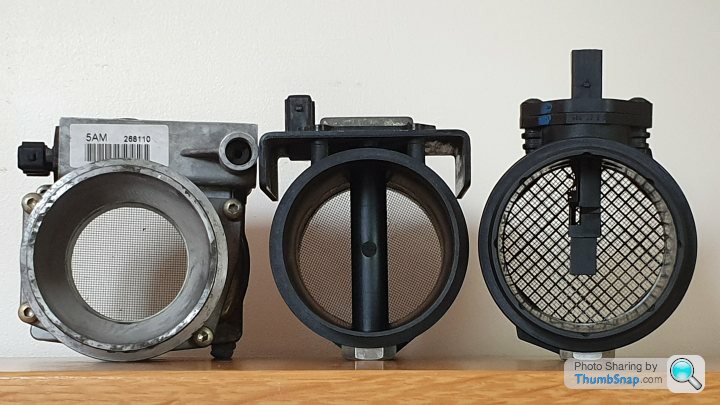
3/5AM (54mm) ..................................................... 20AM (70mm) .............................4.6 Bosch MAF (76.5mm)
You can see below my ‘Row Scalar’ is EA, in addition you’ll also notice I’m now running your all new RPM set points without any issues and hope you don’t mind. To pull the idle back up to the second row I had to increase the ‘Row Offset’ at prom offset 1C8 from 1E to 34. The Row Scalar, as you know, is a multiplier and there are 6 per chip, one per fuel map, whereas there is only one ‘Row Offset’ per chip and it shifts the usable range of the fuel table uniformly up and down. For my information, I also change the Ident at the top of the RoverGauge screen to 34B5 so I can quickly see my current ‘Row Offset’ & my fuel table version B5 for Bosch 5, but please don’t analyse this fuel table too closely as it was an old work in progress and now tidied up in B6.
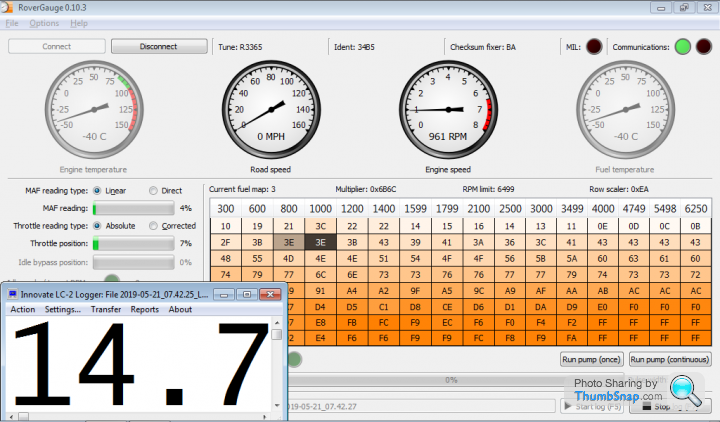
No secret, maybe because my 5AM was running at +96% airflow where as the Bosch 4.6 runs at 75% airflow.
Here’s my new 4.6 Bosch MAF from Euro Car Parts, do you know if the part number is correct and the same as the cars you tested.


Here’s a comparison of the AFMs with the inner diameters measured at the narrowest point
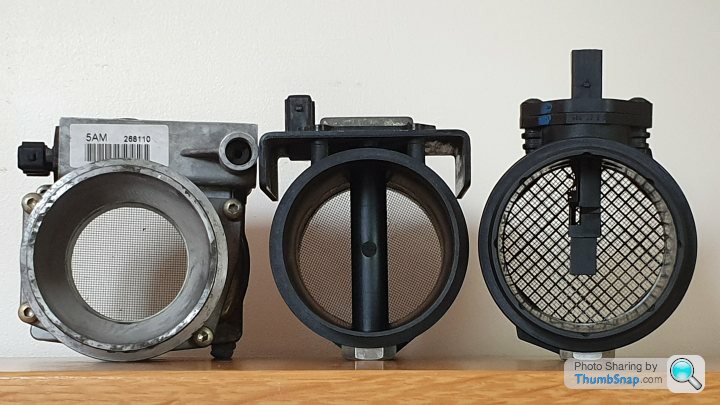
3/5AM (54mm) ..................................................... 20AM (70mm) .............................4.6 Bosch MAF (76.5mm)
You can see below my ‘Row Scalar’ is EA, in addition you’ll also notice I’m now running your all new RPM set points without any issues and hope you don’t mind. To pull the idle back up to the second row I had to increase the ‘Row Offset’ at prom offset 1C8 from 1E to 34. The Row Scalar, as you know, is a multiplier and there are 6 per chip, one per fuel map, whereas there is only one ‘Row Offset’ per chip and it shifts the usable range of the fuel table uniformly up and down. For my information, I also change the Ident at the top of the RoverGauge screen to 34B5 so I can quickly see my current ‘Row Offset’ & my fuel table version B5 for Bosch 5, but please don’t analyse this fuel table too closely as it was an old work in progress and now tidied up in B6.
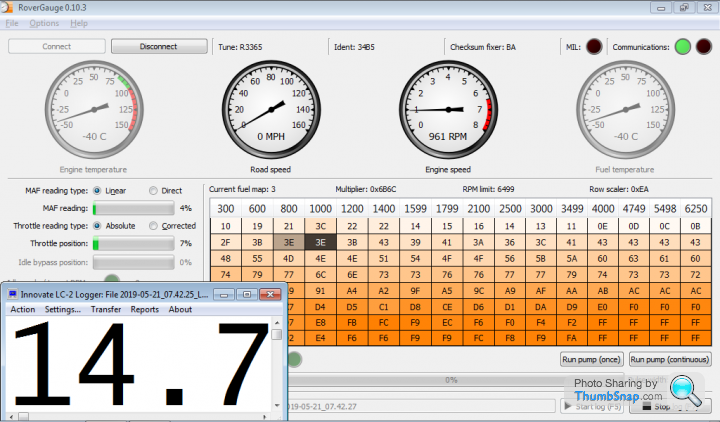
Edited by stevesprint on Sunday 2nd June 15:49
MPO said:
Hi
What is the default value for the fuel temperature in the 14CUX code if the sensor is disconnected?
Also,
Is it possible to set the this default temperature to something else if wanted and where in the code?
Many thanks
Dan & DaveWhat is the default value for the fuel temperature in the 14CUX code if the sensor is disconnected?
Also,
Is it possible to set the this default temperature to something else if wanted and where in the code?
Many thanks
Great to hear from you both and thanks for your help as usual.
Glyn
If you’re looking for a free input to repurpose Dan has confirmed both the ‘heated screen’ and ‘A/C’ inputs can be re-used for other purposes and both input routines do an 8-bit conversion which is ideal but wasteful for off/on switches like A/C and heat screen, if the result is less than 128, the signal is low, otherwise it's high.
However, my cooling fans have always been connected to the heated screen input which lifts the idle for 2 sec when the fans first kick in and works extremely well and therefore recommended.
I was considering using the A/C input to monitor the intake air temperature via the Bosch AFM temperature sensor to lean off the fuel if required due to heat soak. However I’m now less concerned as I’m finding the AFR is less effected by heat soak with the Bosch AFM which could be due to its internal & cool electronics or maybe my new heat shield. I drove into London last week on a really hot and sunny day and was cooked for over an hour in stationary/slow moving traffic due to an accident and my AFR was barely effected by the heat soak.
I’m so impressed with the Bosch AFM I would definitely recommend one but obviously they require a full re-map and it makes room for a heat shield as its smaller on the outside (& bigger on the inside).
RV8 - I'm doing my bit for Global warming
Edited by stevesprint on Wednesday 10th July 23:41
As you have the earlier MVA5033 PAL chip your best option is to remap R2422 with TunerPro, see below. Please let me know if you need a hand or require any additional R2422 tuning parameters added to TunerPro.
However, as Mark explains you’ll first have to remove your current chip and solder in a socket.
Apparently you can run later chips in 14CUXs with the earlier MVA5033 but only the non cat map 2.
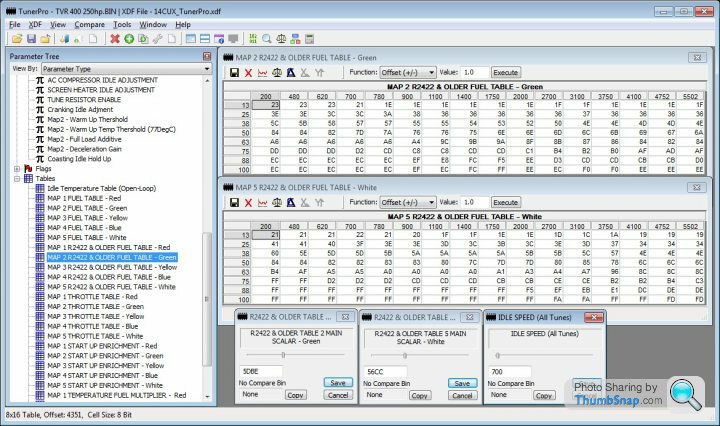
However, as Mark explains you’ll first have to remove your current chip and solder in a socket.
Apparently you can run later chips in 14CUXs with the earlier MVA5033 but only the non cat map 2.
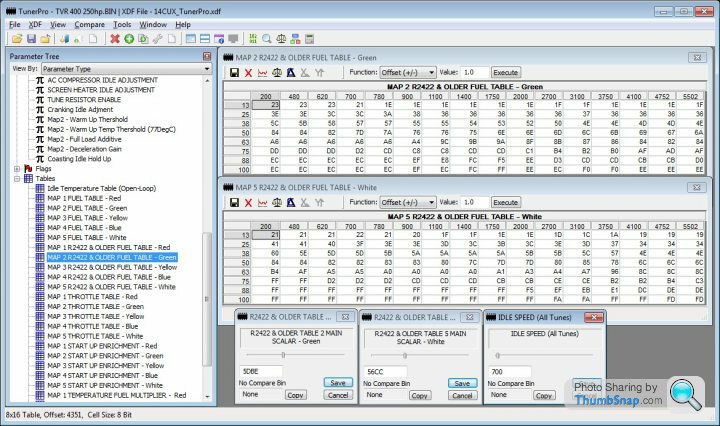
TRIUMPHBULLET said:
Hi all, as I have been tied to home for the last few weeks I decided to play with the TR7 again.
Thanks to Steve Sprint for help a few years ago I modified my ecu to take an eeprom and have run it with success but also had a supercharger project on the back burner which is now installed,feel free to laugh I know its not textbook.
Its a little 'crude' in its execution but runs well, just a little flat spot if the throttle is pressed fast although the injection system will need tuning by an expert when I can travel the distances needed.I am running a 4L Chimera pre cat map at the moment.I will order a wide band lambda system when I can sort out what to buy,The AEM 30-0300 looks like it is affordable,if its any good.
I have included a few photos for your amusement as I know some have you have produced some works of art.
Details are a std distributor with advance limited to 28 degrees and a 1.8 to 1 drive ratio for the Eaton M112 making 5lbs boost through a cheapo aluminium intercooler.
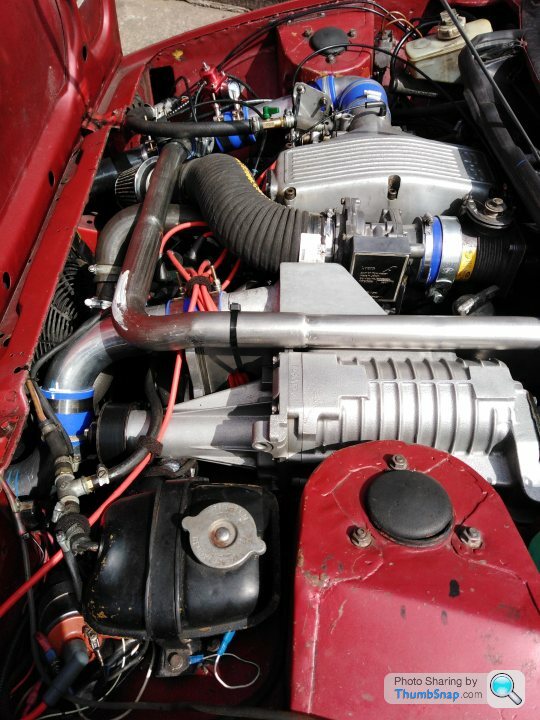
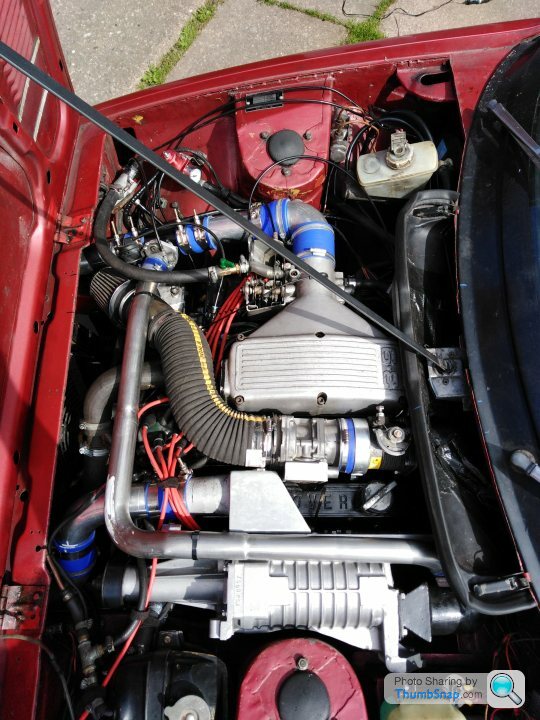

Very impressive, do you know what sort of power it will produces?Thanks to Steve Sprint for help a few years ago I modified my ecu to take an eeprom and have run it with success but also had a supercharger project on the back burner which is now installed,feel free to laugh I know its not textbook.
Its a little 'crude' in its execution but runs well, just a little flat spot if the throttle is pressed fast although the injection system will need tuning by an expert when I can travel the distances needed.I am running a 4L Chimera pre cat map at the moment.I will order a wide band lambda system when I can sort out what to buy,The AEM 30-0300 looks like it is affordable,if its any good.
I have included a few photos for your amusement as I know some have you have produced some works of art.
Details are a std distributor with advance limited to 28 degrees and a 1.8 to 1 drive ratio for the Eaton M112 making 5lbs boost through a cheapo aluminium intercooler.
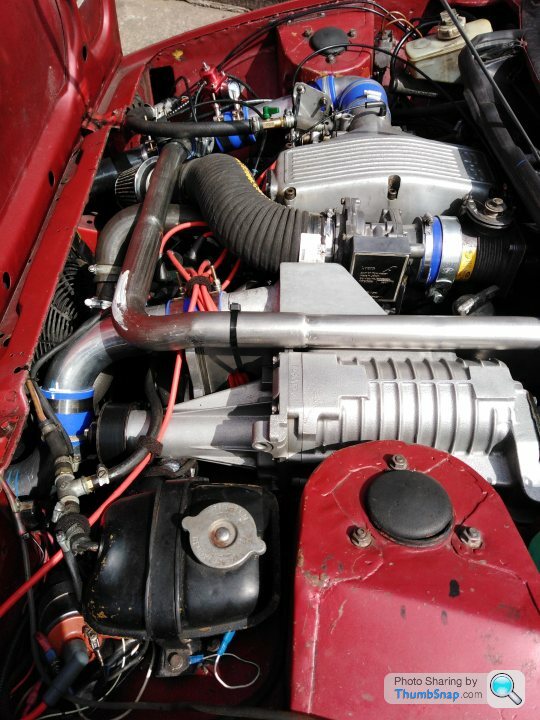
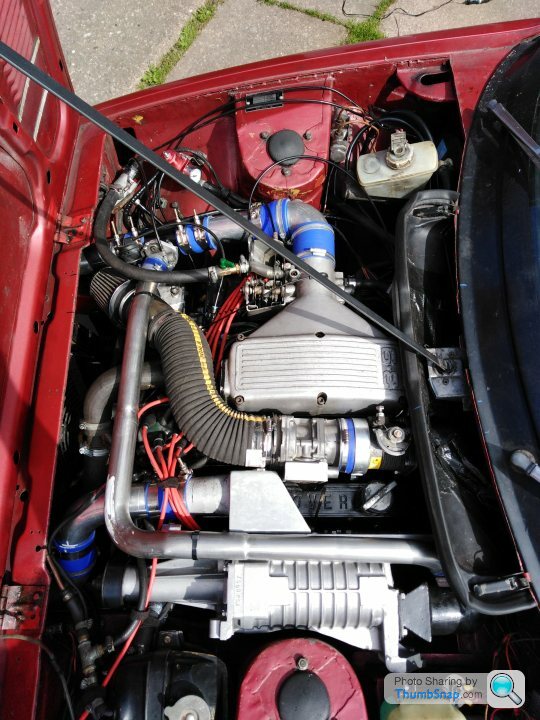

Seeing a Rover V8 EFi in a Red TR7 brings back happy memories even though my old TR7’s engine bay wasn’t so busy as yours.
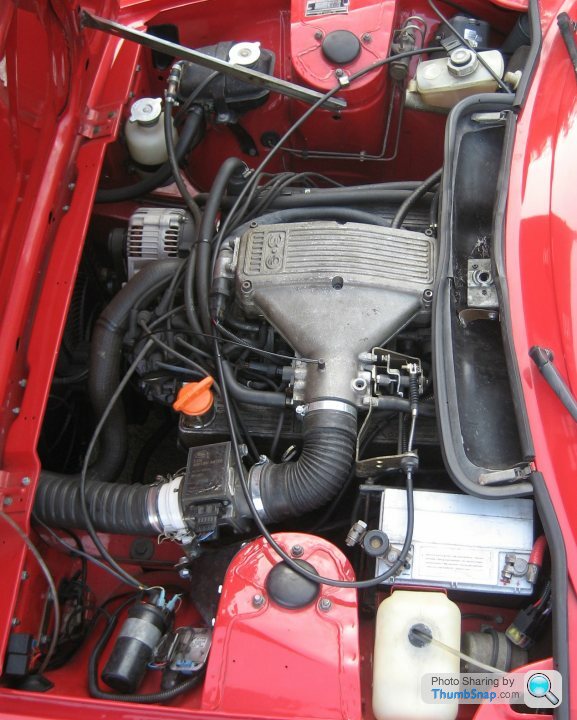
If you are planning to keep the 14CUX you might benefit from using a 123 Ignition distributor as they are fully programmable for vacuum and boost.
Is that your idle stepper behind the right headlamp & does it work there? I guess you don't have room to mount it on the front of the plenum like mine.
Please let me know if you need a hand re-mapping the old 14CUX ECU or you need to run bigger injectors or a bigger airflow meter, if you buy an Innovate LC-2 lambda controller I could help you re-map it yourself from the RoverGauge & LC2 logs after driving safely on the roads.
Thanks for posting your pictures, very interesting.
Steve Sprint
Edited by stevesprint on Sunday 10th May 11:20
RangerRovering
Welcome back, you original post is at the bottom of page 32
https://www.pistonheads.com/gassing/topic.asp?h=0&...
I would first try copying your standard ECU fuel map to your tuned ECU to help identify the issue and let me know how it goes.
I tend to buy chips new or second hand from ebay and always buy ST M27C256 PROMs or Atmel AT28C256 EPROMs and never had a problem with them, for long term use I would always suggest PROMs.
A 20AM won’t work very well on a 3.5 as you won’t flow enough air and not reach the bottom row of the fuel table even if you max out the AFM scalar, sorry.
To use a 20AM the wiring is straight forward and I always refer to Mark Blitz well illustrated wiring diagram.
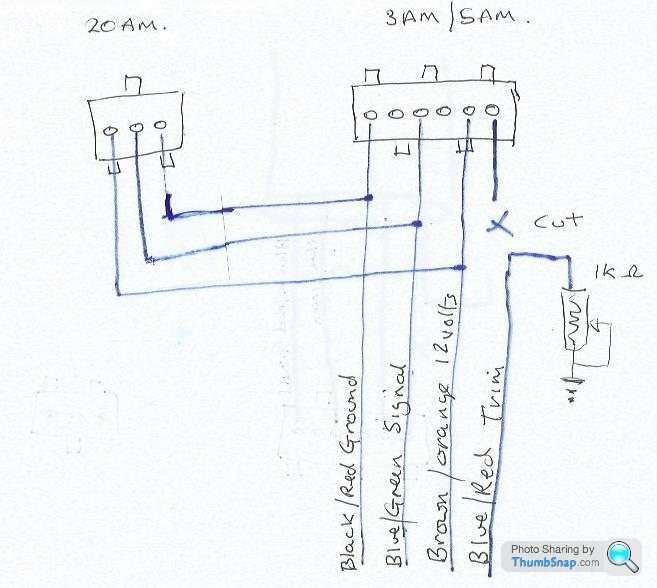
As the 5v output curve are the same in theory you can just change the row scalar and will drive reasonably well provided you adjust the scalar to give the same rows at the same loads as the 5AM, I suggest working from the RoverGauge log files before and after as they are more accurate than the on screen active cell trace, you should then really get the map checked & fine tuned on a rolling road.
Thanks for your kind words and play safe.
Welcome back, you original post is at the bottom of page 32
https://www.pistonheads.com/gassing/topic.asp?h=0&...
I would first try copying your standard ECU fuel map to your tuned ECU to help identify the issue and let me know how it goes.
I tend to buy chips new or second hand from ebay and always buy ST M27C256 PROMs or Atmel AT28C256 EPROMs and never had a problem with them, for long term use I would always suggest PROMs.
A 20AM won’t work very well on a 3.5 as you won’t flow enough air and not reach the bottom row of the fuel table even if you max out the AFM scalar, sorry.
To use a 20AM the wiring is straight forward and I always refer to Mark Blitz well illustrated wiring diagram.
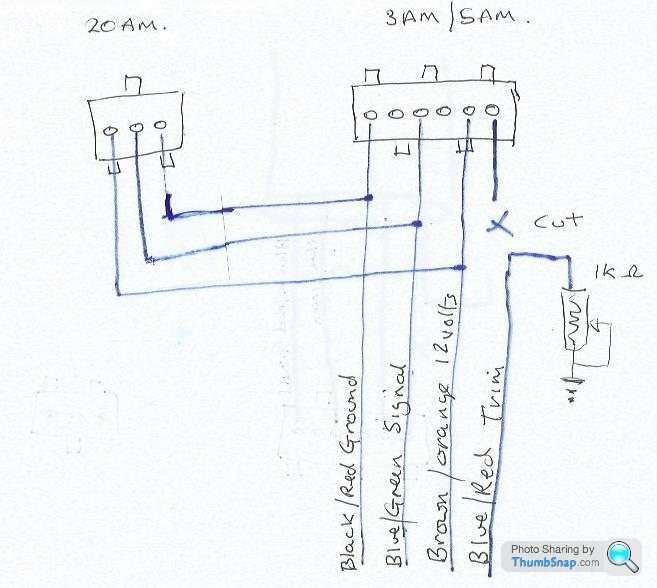
As the 5v output curve are the same in theory you can just change the row scalar and will drive reasonably well provided you adjust the scalar to give the same rows at the same loads as the 5AM, I suggest working from the RoverGauge log files before and after as they are more accurate than the on screen active cell trace, you should then really get the map checked & fine tuned on a rolling road.
Thanks for your kind words and play safe.
TRIUMPHBULLET
From my limited experience the standard injectors max out at about 340 bhp @ 6,000rpm so you should be ok.
Arrr yes I see your idle valve is plumbed in after your intercooler, interesting.
Are LC2 reliable?
Very good question, depends on the installation and how your engine runs. I’m on my second wideband probe in 7 years but probably because I run my Precat Griff richer than 14.7 for smoothness as I have a lairy cam, plus I had some running issues in 2018 with a dodgy 20AM that may have cause it to die before its time. Innovate have updated the LC2 firmware since mine and now they come with the later LSU4.9 Bosch wideband probe where as mine is the old LSU 4.2 probe, maybe worth checking before buying.
Your main priority is to decide on the outputs and/or gauge required. I chose the Innovate LC2 as it has an analogue output for a dash gauge plus its serial port outputs 10 AFR readings per second so there’s always a AFR reading to synchronize with the RoverGauge log records, this allows me to easily create an Excel pivot table showing the AFR for each fuel table cell.
Good luck with your back & gearbox/clutch and let me know if you buy a LC2 and need a hand re-mapping from the comfort of your arm chair.
From my limited experience the standard injectors max out at about 340 bhp @ 6,000rpm so you should be ok.
Arrr yes I see your idle valve is plumbed in after your intercooler, interesting.
Are LC2 reliable?
Very good question, depends on the installation and how your engine runs. I’m on my second wideband probe in 7 years but probably because I run my Precat Griff richer than 14.7 for smoothness as I have a lairy cam, plus I had some running issues in 2018 with a dodgy 20AM that may have cause it to die before its time. Innovate have updated the LC2 firmware since mine and now they come with the later LSU4.9 Bosch wideband probe where as mine is the old LSU 4.2 probe, maybe worth checking before buying.
Your main priority is to decide on the outputs and/or gauge required. I chose the Innovate LC2 as it has an analogue output for a dash gauge plus its serial port outputs 10 AFR readings per second so there’s always a AFR reading to synchronize with the RoverGauge log records, this allows me to easily create an Excel pivot table showing the AFR for each fuel table cell.
Good luck with your back & gearbox/clutch and let me know if you buy a LC2 and need a hand re-mapping from the comfort of your arm chair.
Edited by stevesprint on Sunday 17th May 23:51
Talking of injectors above, I’ve recently switched to Vectra injectors because Joolz & COG both say they have a better spray pattern that helps smoothness which I can now confirm they do slightly help smoothness.

Surprisingly my Precat Griff started & ran with the Vectra injectors and my original fuel map but obviously ran very rich until I reduced the main fuel table multiplier by about 8% and the cranking fuel. This confirms what Chimpandtonic (COG) said back in 2012
“The car ran perfectly on the Vectra injectors without any adjustments to the fuelling”
However, I suspect his lambda trims went minus % to compensate which isn’t ideal but proved the flow increase isn’t massive and you could fit them yourself before driving to Joolz for a remap.
GM90501588(Siemens5WK90761) .. Bosch 0280 155 931(Corvette 5.7) .. Land Rover No: ERR722 (Lucas: D1830GA)


You can see the Vectra injectors are a straight swap where as the Bosch ones fit but you have to cut the top grooves for the fuel rail clips.
You can see the Lucas & Vectra spay patterns and flow rates here
https://www.pistonheads.com/gassing/topic.asp?h=0&...
https://www.pistonheads.com/gassing/topic.asp?t=11...
Would be interesting to experiment with the Bosch injectors next year to compare how much extra fuel they flow.

Surprisingly my Precat Griff started & ran with the Vectra injectors and my original fuel map but obviously ran very rich until I reduced the main fuel table multiplier by about 8% and the cranking fuel. This confirms what Chimpandtonic (COG) said back in 2012
“The car ran perfectly on the Vectra injectors without any adjustments to the fuelling”
However, I suspect his lambda trims went minus % to compensate which isn’t ideal but proved the flow increase isn’t massive and you could fit them yourself before driving to Joolz for a remap.
GM90501588(Siemens5WK90761) .. Bosch 0280 155 931(Corvette 5.7) .. Land Rover No: ERR722 (Lucas: D1830GA)


You can see the Vectra injectors are a straight swap where as the Bosch ones fit but you have to cut the top grooves for the fuel rail clips.
You can see the Lucas & Vectra spay patterns and flow rates here
https://www.pistonheads.com/gassing/topic.asp?h=0&...
https://www.pistonheads.com/gassing/topic.asp?t=11...
Would be interesting to experiment with the Bosch injectors next year to compare how much extra fuel they flow.
Dave,
I never noticed the Vectra injectors are more audible until you mentioned it and you have to put your ear right up to them to hear them.
As the injectors are fired twice for one valve opening you live in hope half a squirt goes straight into the cylinders without first collecting on the side walls and the back of the valves, maybe that’s why they are marginally smoother while bimbling along as I do, unlike you at Millbrook
I agree standard disc atomisation and flow rates are fine, however you can see from my RoveGauge and AFR merged log my standard injectors are running at 94.6% duty cycle on RoverGauge’s last log record at 5,119rpm and therefore reaches 100% at approximately 5,500rpm. I know for sure my injectors are maxing out because increasing the main scalar further & inserting FF’s in the last cell of the fuel table made no difference to AFR.

Although my injectors maxing out doesn’t seem to cause me any issues I thought it would interesting to see if you can install bigger injectors and/or a higher fuel pressure regulator and then only change the main fuel table scalar. I’m pleased to say I did and it drives and goes the same as before although the AFR is now not always spot so I will fine tune a few cells in the main fuel table.
The Vectra injectors run at 89.2% duty cycle at RoverGauge last log record at 5,200rpm which is about 5% less and max out at approximately 6,000rpm instead of 5,500rpm, therefore they only made a surprisingly small difference to duty cycle especially as I also upgraded to a 3 bar fuel pressure regulator at the same time.
So why do some people suggest you shouldn’t run injectors above 80% duty cycle?
I never noticed the Vectra injectors are more audible until you mentioned it and you have to put your ear right up to them to hear them.
As the injectors are fired twice for one valve opening you live in hope half a squirt goes straight into the cylinders without first collecting on the side walls and the back of the valves, maybe that’s why they are marginally smoother while bimbling along as I do, unlike you at Millbrook

I agree standard disc atomisation and flow rates are fine, however you can see from my RoveGauge and AFR merged log my standard injectors are running at 94.6% duty cycle on RoverGauge’s last log record at 5,119rpm and therefore reaches 100% at approximately 5,500rpm. I know for sure my injectors are maxing out because increasing the main scalar further & inserting FF’s in the last cell of the fuel table made no difference to AFR.

Although my injectors maxing out doesn’t seem to cause me any issues I thought it would interesting to see if you can install bigger injectors and/or a higher fuel pressure regulator and then only change the main fuel table scalar. I’m pleased to say I did and it drives and goes the same as before although the AFR is now not always spot so I will fine tune a few cells in the main fuel table.
The Vectra injectors run at 89.2% duty cycle at RoverGauge last log record at 5,200rpm which is about 5% less and max out at approximately 6,000rpm instead of 5,500rpm, therefore they only made a surprisingly small difference to duty cycle especially as I also upgraded to a 3 bar fuel pressure regulator at the same time.
So why do some people suggest you shouldn’t run injectors above 80% duty cycle?
On my bins page you should already be running “TVR Griffith 500 (1995on) (R2967)” which is under “TVR OEM Tune Files”, send us a RoverGauge screen shot and we'll confirm what you're running.
How bad is your jerking? Full on changarooing or mild shacking?
Mark’s (Blitz) non cat 500 map sounds like a good idea as it effectively gives you manual control of the lambda long trims so you maybe able to adjust out the jerking and I’m sure he’d send you a chip for a small fee.
How bad is your jerking? Full on changarooing or mild shacking?
Mark’s (Blitz) non cat 500 map sounds like a good idea as it effectively gives you manual control of the lambda long trims so you maybe able to adjust out the jerking and I’m sure he’d send you a chip for a small fee.
Gassing Station | Griffith | Top of Page | What's New | My Stuff