R400D to R500D Anyone done it?
Discussion
It was like Christmas all over again with lots of goodies arriving from Sb Developments , but most importantly the crank is back. I'm now looking forward to to putting things back together instead of taking them apart.

To go with the keyed crank is the Sb Developments small pulley. The standard pulley is 2 KG heavier. Apart from the obvious advantages of reduced mass, I'm curious about the impact this will have on the inherent vibration of an 'in-line' 4 cylinder engine. No doubt the heavier pulley helps to smooth things out, but does it add to, or reduce, the stresses in the crank?


It was always my intention to 'blue print' the engine so a bit of time was spent positioning the main shells on the webs. The Ford assembly guide gives measurements to center the shells to the oil holes in the crank. The block casting is not perfect, so you can't rely on centering the shell on the web to get this right.

A little care here will maximise oil flow to the big ends.

The ladder is treated the same way, but, as it is also machined and honed in-situ, the final tweak is to align it with the block before torquing down.

I am using the the original graded Ford bearings and there's little I can do to change clearances. But better the devil you know, so I checked them with Plastigauge. Much to my relief all the bearings produced identical measurements and all nicely square. The clearances were bigger than the Ford declared spec of 0.039 mm - probably due to me only using half the specified torque for the check. I am happy, however, that the full 60 ft-lbs on the ARP studs squeezed this up tighter, and it felt 'nice'. I've used Millers Assembly Lubricant this time (I normally use engine oil). Starting it for the first time may be interesting as it is really thick sticky stuff!

And finally all back in place and torqued up


To go with the keyed crank is the Sb Developments small pulley. The standard pulley is 2 KG heavier. Apart from the obvious advantages of reduced mass, I'm curious about the impact this will have on the inherent vibration of an 'in-line' 4 cylinder engine. No doubt the heavier pulley helps to smooth things out, but does it add to, or reduce, the stresses in the crank?


It was always my intention to 'blue print' the engine so a bit of time was spent positioning the main shells on the webs. The Ford assembly guide gives measurements to center the shells to the oil holes in the crank. The block casting is not perfect, so you can't rely on centering the shell on the web to get this right.

A little care here will maximise oil flow to the big ends.

The ladder is treated the same way, but, as it is also machined and honed in-situ, the final tweak is to align it with the block before torquing down.

I am using the the original graded Ford bearings and there's little I can do to change clearances. But better the devil you know, so I checked them with Plastigauge. Much to my relief all the bearings produced identical measurements and all nicely square. The clearances were bigger than the Ford declared spec of 0.039 mm - probably due to me only using half the specified torque for the check. I am happy, however, that the full 60 ft-lbs on the ARP studs squeezed this up tighter, and it felt 'nice'. I've used Millers Assembly Lubricant this time (I normally use engine oil). Starting it for the first time may be interesting as it is really thick sticky stuff!

And finally all back in place and torqued up


Edited by DCL on Saturday 25th January 11:31
The Duratec crank has a flat ground on one of the counter weights. This is to calibrate it for use with the TDC peg which screws into the block.

I made one up while with a 10 mm bolt - carefully grinding it to the correct length. It does make life easier for setting things up and is worth the effort.

Time to move on to the pistons assembly. First thing was to gap the rings - all were bang smack in the middle of tolerance for 250 BHP engine, so it didn't take long.

The second ring has a groove at it's bottom edge - the exact function of this groove is up for debate, but it's likely to help with reducing oil passing upwards and provide a downward pumping action. The flow of oil past piston rings is an interesting subject if you like that sort of thing.

The oil expander ring has a ridge too - this time it is clearly for the retaining rings to hold it in place.

I am Using 12.5 CR Supertech pistons and Carrillo (Cosworth) rods. Ford specify a weight tolerance between their standard pistons that amounts to approximately 3 grams. The Supertech pistons were within 2 grams of each other and the Carrillo rods were within a gram. The gudgeon pins were identical in weight. By grading and matching the components I manage to get each piston assembly to within a gram of each other. The new piston and rods are 66 grams lighter than the standard items.


All four pistons assembled, which was straightforward, except for maybe the cir-clips which are always tricky if you haven't got the right tool. But my confidence took a knock when I was left with two circlips. Self-doubt took over and I had to remove all the pistons to check! But all were present and correct - very funny Supertech
The bearing shells are uprated VP from Cosworth.

I used plasti gauge to check them - all being near the 0.038 mm band which is again in the middle of the Cosworth (and Ford) spec. Not quite as even as the mains, but all well within tolerance.

It is worth noting that the bearings look narrower than the cap, in fact, I think it is 2.5 mm. This coupled with a groove in the crank journal provides a reservoir of oil in the bearing and helps to protect the bearing at times of low pressure by allowing oil to recirculate as the hydrodynamic pressure goes negative on the unloaded side. A feature that, prehaps, makes the Duratec a little more tolerant of low oil pressure.

I did get Simon, at Ultimate Performance, to assemble the head after the CNC work (mainly to stop the hassle or ordering cam followers) but I do intend to 'reassemble' it my self. But with the pistons in, it meant I could check the valve-to-piston clearance.

So with some blue tack on no.1 piston, the head was put on with an old gasket, cams timed, and then the crank rotated.

There was no hard contact (relief!) and so the head was removed to see how close things got.

Nothing was too close and amazingly you could see it all happen through the inlet port!

With clearance check done, time was spent dismantling the head and putting it back together. It is not that I don't trust Ultimate Performance to do it right, it was just that I wanted to go through the full process of the engine build myself. But full marks to Simon at Ultimate Performance - every valve was perfect


I was glad to spot this nasty bit of shaving firmly embedded in the cam bearing. It was very hard so probably debris from the valve seat machining - maybe during manufacture at Ford. I levered it out to leave just an indentation which I'm sure will do no harm.


I made one up while with a 10 mm bolt - carefully grinding it to the correct length. It does make life easier for setting things up and is worth the effort.

Time to move on to the pistons assembly. First thing was to gap the rings - all were bang smack in the middle of tolerance for 250 BHP engine, so it didn't take long.

The second ring has a groove at it's bottom edge - the exact function of this groove is up for debate, but it's likely to help with reducing oil passing upwards and provide a downward pumping action. The flow of oil past piston rings is an interesting subject if you like that sort of thing.

The oil expander ring has a ridge too - this time it is clearly for the retaining rings to hold it in place.

I am Using 12.5 CR Supertech pistons and Carrillo (Cosworth) rods. Ford specify a weight tolerance between their standard pistons that amounts to approximately 3 grams. The Supertech pistons were within 2 grams of each other and the Carrillo rods were within a gram. The gudgeon pins were identical in weight. By grading and matching the components I manage to get each piston assembly to within a gram of each other. The new piston and rods are 66 grams lighter than the standard items.


All four pistons assembled, which was straightforward, except for maybe the cir-clips which are always tricky if you haven't got the right tool. But my confidence took a knock when I was left with two circlips. Self-doubt took over and I had to remove all the pistons to check! But all were present and correct - very funny Supertech
The bearing shells are uprated VP from Cosworth.

I used plasti gauge to check them - all being near the 0.038 mm band which is again in the middle of the Cosworth (and Ford) spec. Not quite as even as the mains, but all well within tolerance.

It is worth noting that the bearings look narrower than the cap, in fact, I think it is 2.5 mm. This coupled with a groove in the crank journal provides a reservoir of oil in the bearing and helps to protect the bearing at times of low pressure by allowing oil to recirculate as the hydrodynamic pressure goes negative on the unloaded side. A feature that, prehaps, makes the Duratec a little more tolerant of low oil pressure.

I did get Simon, at Ultimate Performance, to assemble the head after the CNC work (mainly to stop the hassle or ordering cam followers) but I do intend to 'reassemble' it my self. But with the pistons in, it meant I could check the valve-to-piston clearance.

So with some blue tack on no.1 piston, the head was put on with an old gasket, cams timed, and then the crank rotated.

There was no hard contact (relief!) and so the head was removed to see how close things got.

Nothing was too close and amazingly you could see it all happen through the inlet port!

With clearance check done, time was spent dismantling the head and putting it back together. It is not that I don't trust Ultimate Performance to do it right, it was just that I wanted to go through the full process of the engine build myself. But full marks to Simon at Ultimate Performance - every valve was perfect


I was glad to spot this nasty bit of shaving firmly embedded in the cam bearing. It was very hard so probably debris from the valve seat machining - maybe during manufacture at Ford. I levered it out to leave just an indentation which I'm sure will do no harm.

The Caterham R400 map is locked, but I also wanted to keep the original ECU as, one day, I will return the car to it's original spec. So Sb developments have supplied a new 9A4 with a base map for my spec. In order to reduce the inevitable trouble shooting on the new engine, I decided to fit the new ECU to the existing R400 installation before I remove it. It started on the button and ran like a dream - albeit a bit rich.

Before torquing down the head I did one last check that the timing peg I made was accurate. This time I used a dial gauge to measure an arbitrary figure each side of TDC. By reading off the degrees on the timing disc, and splitting the difference, I was able to locate TDC. This matched the peg with no measurable error. Time to move on
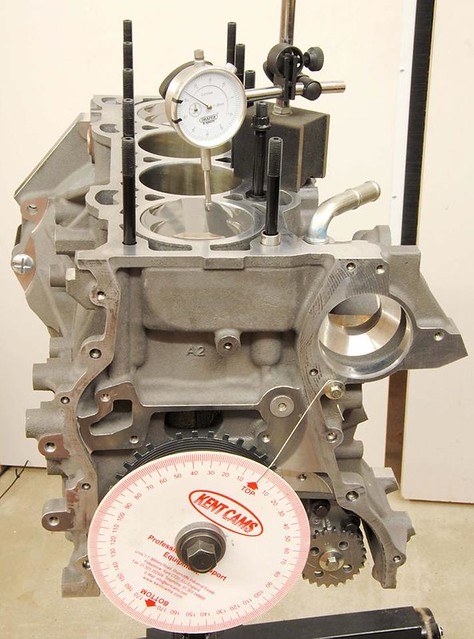
I think most people use an OME type gasket and I decided to purchased the Cosworth item, which appearers to be identical to all the other sources I've seen. It is, however, not identical to the standard FoMoCo item in that the water gallery holes are more restricted - particularly on the exhaust side. But it does have additional holes at the front. I'm guessing that this is a result of some development work to better balance the flow of coolant in the head.
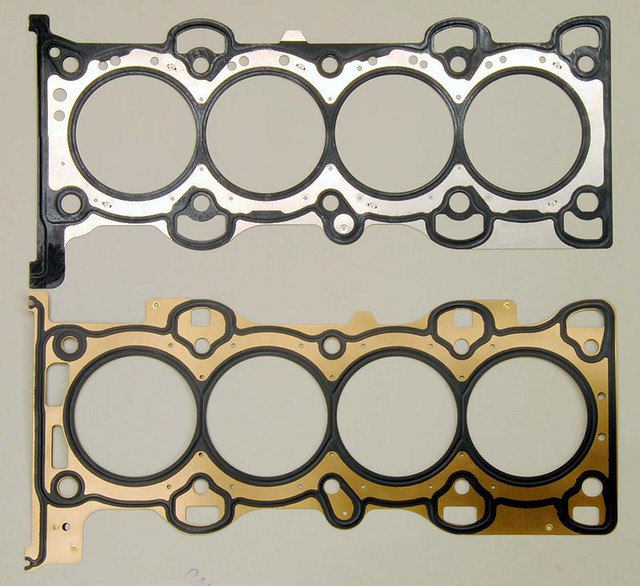
This was a significant day in the project today - the old engine came out. No going back now
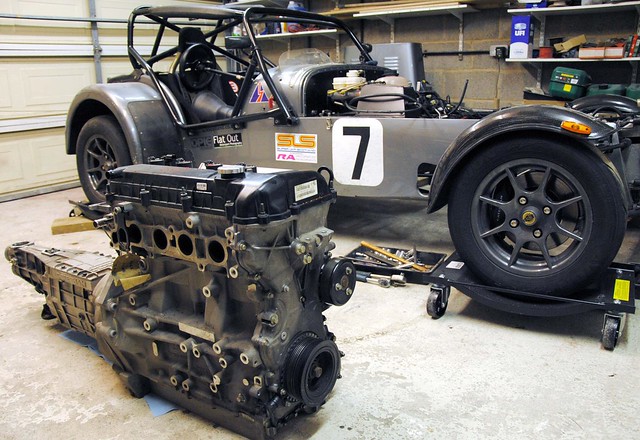
The 'old' engine is now in the process of being stripped of components need for the 'new engine'. A bit I always liked is this breather cover. The dry sump will do away with the breather so this little cover supplied by Caterham does a nice job of covering up the hole. Not a budget item though!
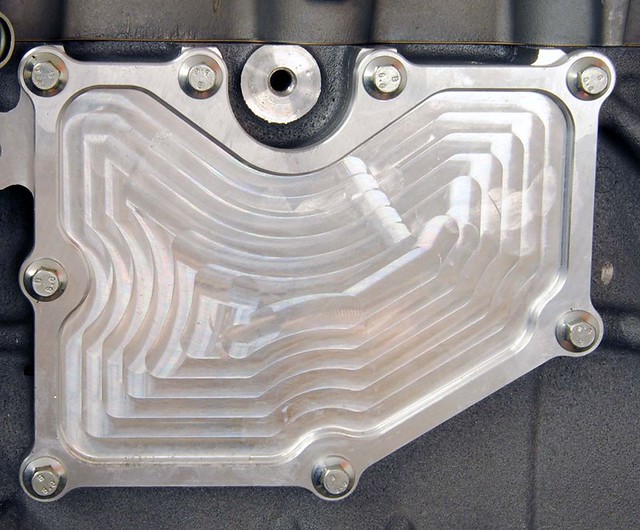
The first major setback looms on the horizon . In fairness, Mic had tipped me off that the sump may not clear the the ARP main studs and, and when stripping the Titan sump off the old engine, it became clear that this sump may have this problem. You can see how close the standard bolts are in the picture. and the ARP studs were about 1 cm longer. The options may be to shorten the studs, or return to the standard bolts. Some careful measurements need to be made . . .
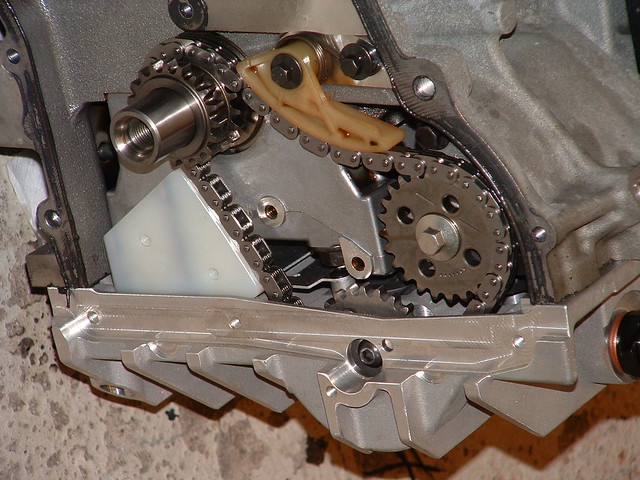
The ARP stud problem: If you look for it, there's quite a lot on the forums about this. Basically the studs appear to be too long and hit the wndage tray. I found it hard to believe that a company like ARP would manufacture a part that would not fit, so first step was to check how deep the threaded hole was in the block. Lo and behold, it was about a 1 mm longer than required.
Next step was to look closely at the stud and look for witness marks where the thread may be binding. Sure enough, the top of the thread looked like it was beginning to get tight. This was good news as, if it had been at the bottom, then the thread would not have been long enough. I needed three more threads and was confident that they could be tightened by this much. It didn't take much torque to tighten them fully home and I probably would have done this if the instruction had not said 'finger tight'. Problem solved

Here’s the sump ‘trial’ fitted to check clearance. In the end there was more than I expected.
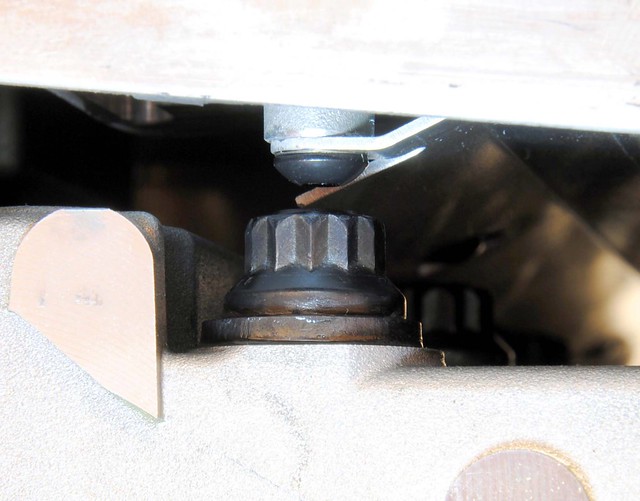
I'm continuing to clean up the components from the old engine and hope to move on assembling them on the new engine soon
Daily post here https://www.facebook.com/Duratec.in.detail

Before torquing down the head I did one last check that the timing peg I made was accurate. This time I used a dial gauge to measure an arbitrary figure each side of TDC. By reading off the degrees on the timing disc, and splitting the difference, I was able to locate TDC. This matched the peg with no measurable error. Time to move on
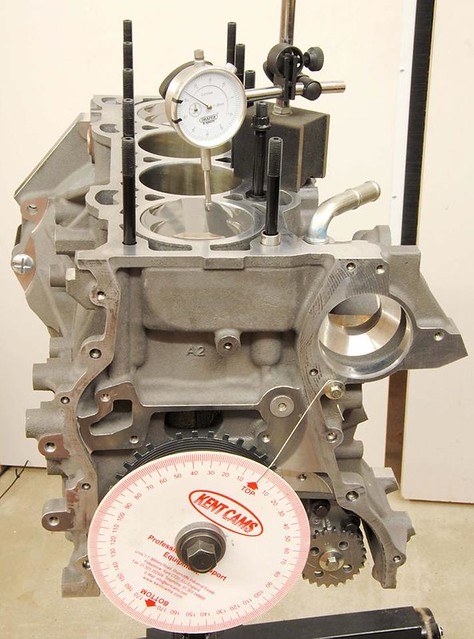
I think most people use an OME type gasket and I decided to purchased the Cosworth item, which appearers to be identical to all the other sources I've seen. It is, however, not identical to the standard FoMoCo item in that the water gallery holes are more restricted - particularly on the exhaust side. But it does have additional holes at the front. I'm guessing that this is a result of some development work to better balance the flow of coolant in the head.
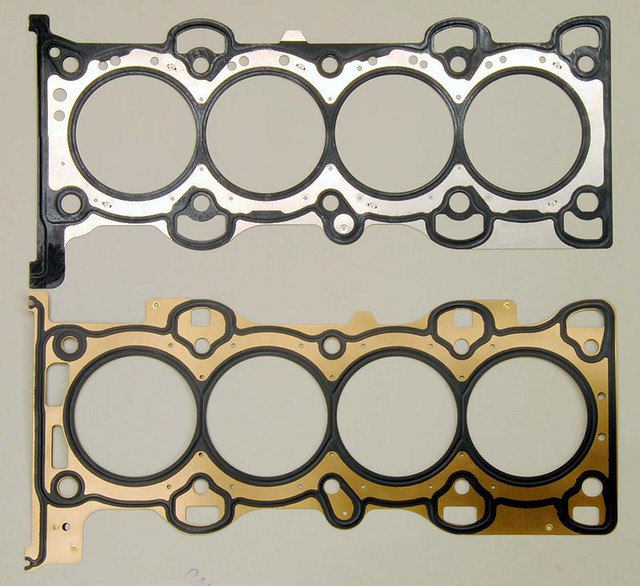
This was a significant day in the project today - the old engine came out. No going back now
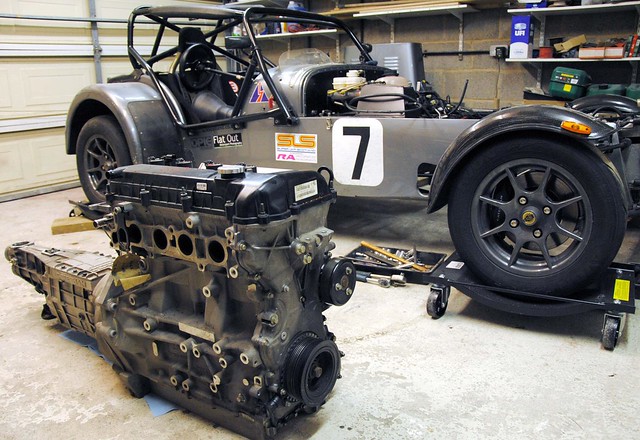
The 'old' engine is now in the process of being stripped of components need for the 'new engine'. A bit I always liked is this breather cover. The dry sump will do away with the breather so this little cover supplied by Caterham does a nice job of covering up the hole. Not a budget item though!
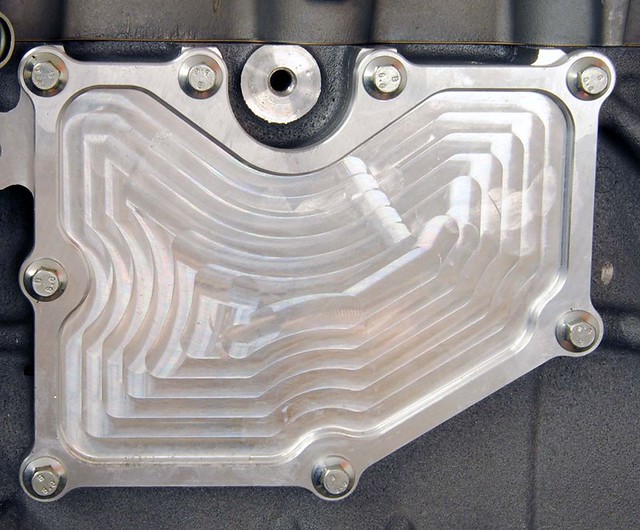
The first major setback looms on the horizon . In fairness, Mic had tipped me off that the sump may not clear the the ARP main studs and, and when stripping the Titan sump off the old engine, it became clear that this sump may have this problem. You can see how close the standard bolts are in the picture. and the ARP studs were about 1 cm longer. The options may be to shorten the studs, or return to the standard bolts. Some careful measurements need to be made . . .
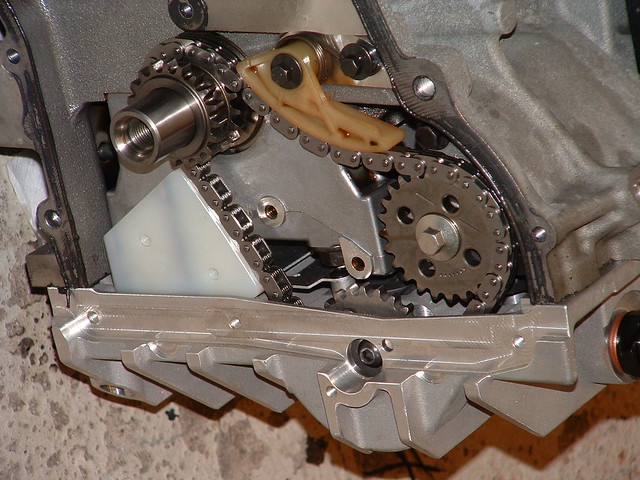
The ARP stud problem: If you look for it, there's quite a lot on the forums about this. Basically the studs appear to be too long and hit the wndage tray. I found it hard to believe that a company like ARP would manufacture a part that would not fit, so first step was to check how deep the threaded hole was in the block. Lo and behold, it was about a 1 mm longer than required.
Next step was to look closely at the stud and look for witness marks where the thread may be binding. Sure enough, the top of the thread looked like it was beginning to get tight. This was good news as, if it had been at the bottom, then the thread would not have been long enough. I needed three more threads and was confident that they could be tightened by this much. It didn't take much torque to tighten them fully home and I probably would have done this if the instruction had not said 'finger tight'. Problem solved

Here’s the sump ‘trial’ fitted to check clearance. In the end there was more than I expected.
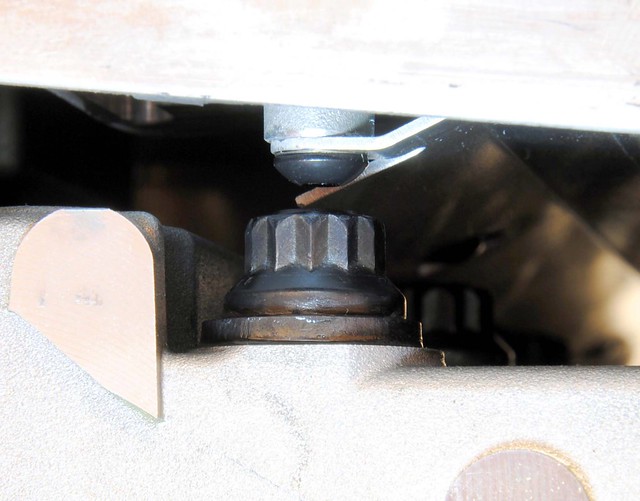
I'm continuing to clean up the components from the old engine and hope to move on assembling them on the new engine soon
Daily post here https://www.facebook.com/Duratec.in.detail
Edited by DCL on Sunday 9th February 23:02
time for an update!
I am using a Caterham branded Titan sump that I purchased in my 2010 upgrade. I covered it on a previous blog so won't go into detail here. It pre-dates the Raceline sump that most people use today and does not provide ground clearance of that unit, but otherwise works well. But there is a weakness in the connection to the pump which needs to be checked: a 'top hat' arrangement provides 2 O-rings that are squashed between the sump but the pump. If the oil pump is ever removed, you need torque it up while it is held up towards the the sump to guarantee a good position and seal.
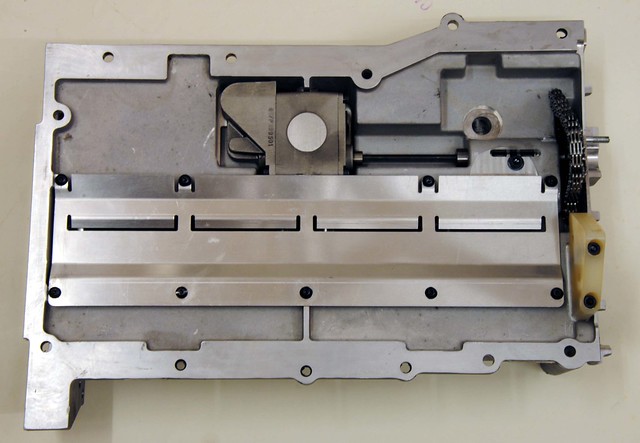
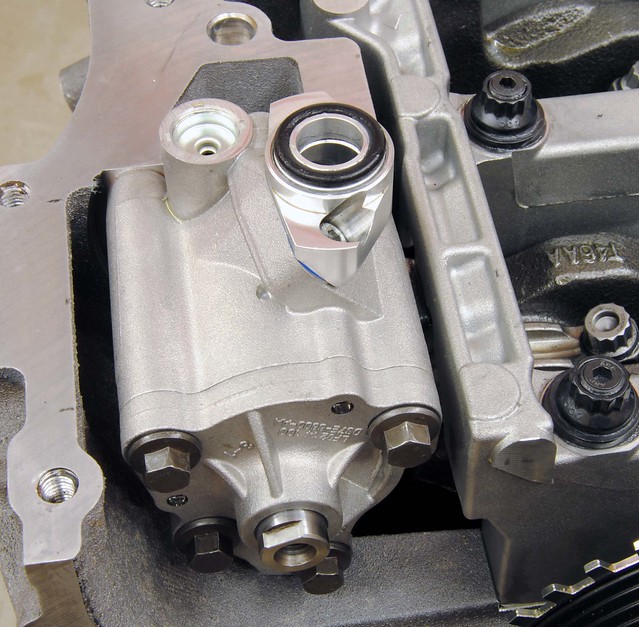
The cams are Ultimate Performance's UL39 & UL40. The choice was made purely on Simon's recommendation for the spec I wanted.
With the initial timing set using the slots on the cams at TDC (Simon felt this was the best way to start), I checked the valve timing with a dial gauge. If you have ever done this you'll understand how difficult it is to get your head round the readings. But after checking a few text books, it began to make sense - they are around 60 80 80 50, with duration of 320 (inlet) and 310 (exhaust). The textbooks suggest this will give a useful RPM range of 3500 - 9000 with peak power somewhere around 8500. Somewhat wilder than I expected but we'll see how it goes .
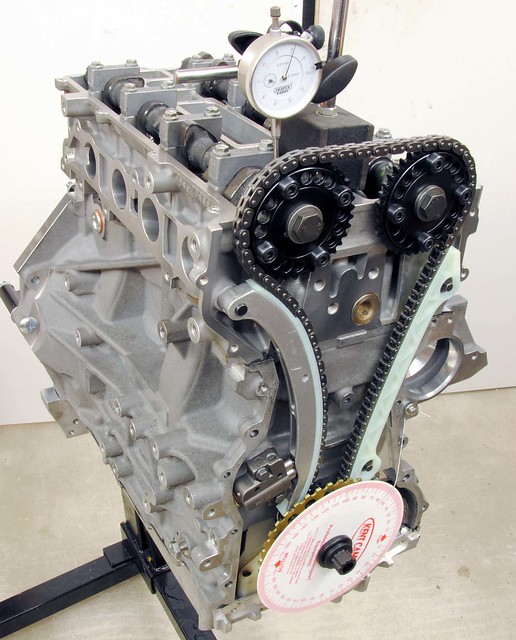
With the engine sealed up I began fitting the auxiliaries. I had thought about fitting the alternator on the exhaust side but, as the smaller pulley worked fine with the original set-up, I decided to keep it that way. Next will be the roller barrels overhaul and fitting.
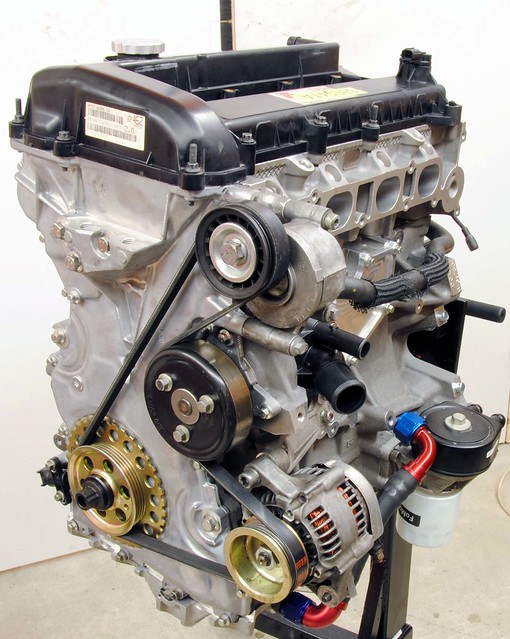
As planned the barrels were overhauled and fitted today. I was surprised at how poor the condition was that they were in, mainly with wear and corrosion. They've done about 5K miles - and they will certainly be past their best by 10K.
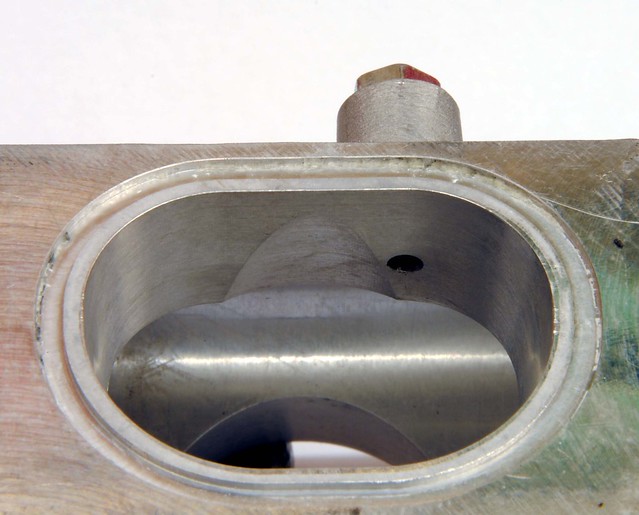
They are, however, a very simple device once the end plates are removed and it was not long before they were done and fitted to the engine. But I did make the classic mistake of not removing the TPS first, so now it's scrap .
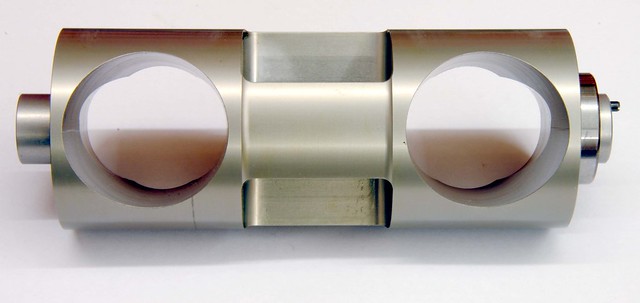
Setting them up is not difficult. Using a 6mm rod to hold them open, the end stops are adjusted in turn to take up the slack. It is worth saying that the 6mm gap at the front is not the 'throttle' opening - that all happens at the back (engine) side. This procedure effectively set the barrel to 'just' closed. There is also a bleed hole which will be adjusted to get idle flow correct when I'm up and running.
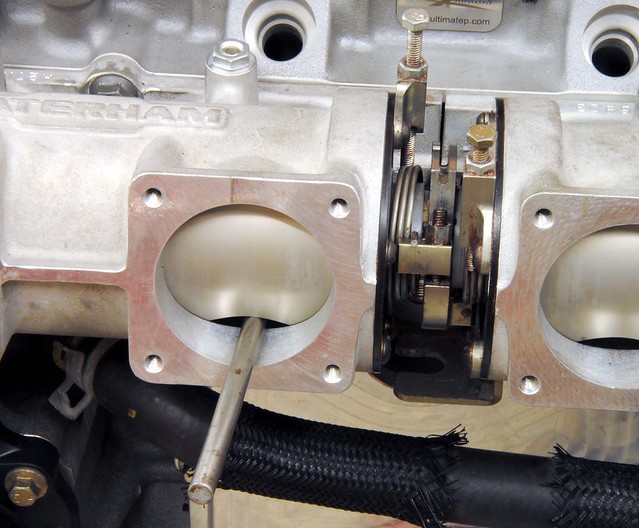
Well, the engine is now finished . the final touch was to fit the rather nice flywheel and twin plate Super Clutch from SB Developments.

The twin plate super clutch is thicker and needs a rounded clutch release bearing. This was supplied with a new release mechanism by SB developments as part of the clutch kit. It also has a spacer to provide the correct position. The hardest part was making up the hoses.
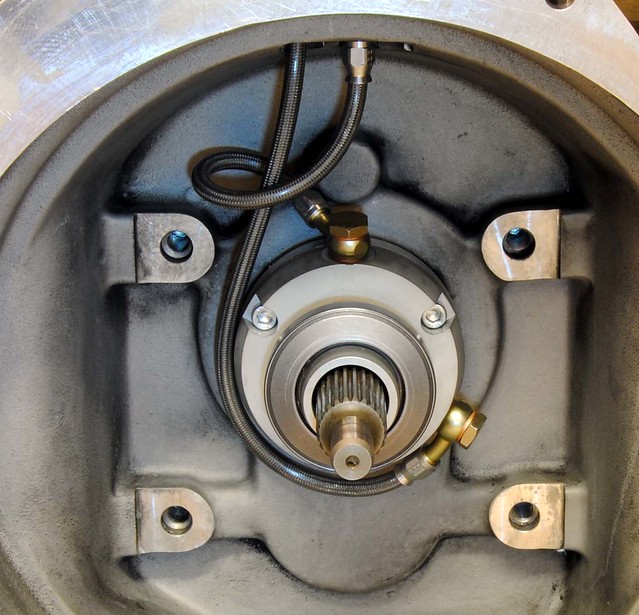
The engine went in today - a fairly standard job with no real issues but the clutch does feel rather 'firm'. I'm sure I'll get used to it. All the fluids are in but the TPS didn't arrive, so couldn't start it up - maybe Monday
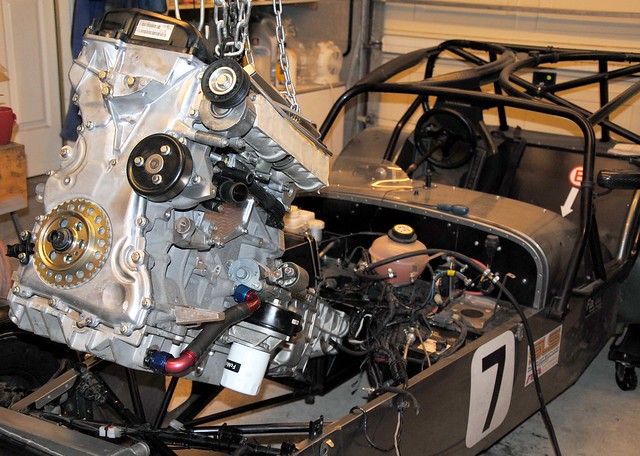
The big moment came! With my son supervising me (and keeping me right) the start button was pushed. I was surprised that it fired instantly. Although I stopped the video by accident, I continued to run it for about 20 minutes. I will not run again until it is on the rolling road next week - so that it's run-in under load.
http://www.youtube.com/watch?v=hrksbKEXfFI
I am using a Caterham branded Titan sump that I purchased in my 2010 upgrade. I covered it on a previous blog so won't go into detail here. It pre-dates the Raceline sump that most people use today and does not provide ground clearance of that unit, but otherwise works well. But there is a weakness in the connection to the pump which needs to be checked: a 'top hat' arrangement provides 2 O-rings that are squashed between the sump but the pump. If the oil pump is ever removed, you need torque it up while it is held up towards the the sump to guarantee a good position and seal.
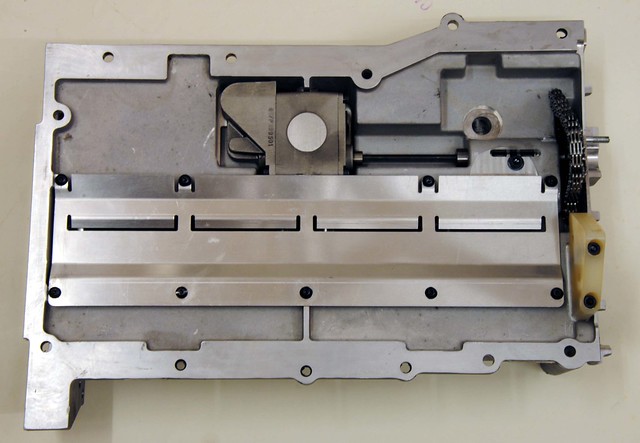
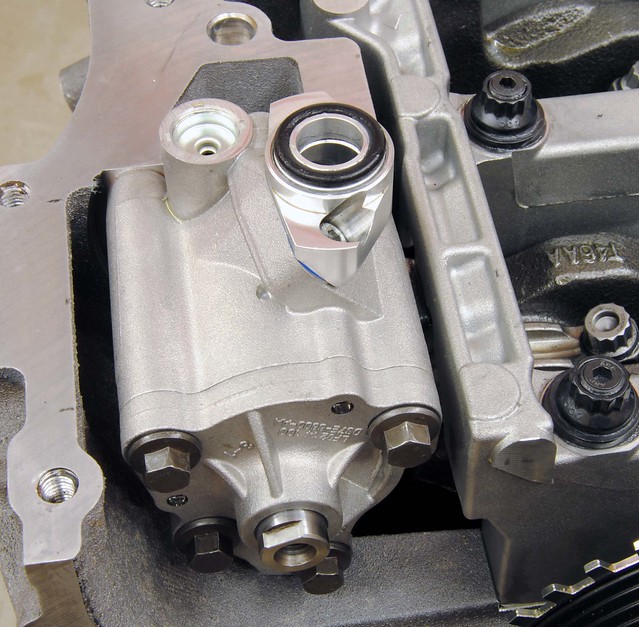
The cams are Ultimate Performance's UL39 & UL40. The choice was made purely on Simon's recommendation for the spec I wanted.
With the initial timing set using the slots on the cams at TDC (Simon felt this was the best way to start), I checked the valve timing with a dial gauge. If you have ever done this you'll understand how difficult it is to get your head round the readings. But after checking a few text books, it began to make sense - they are around 60 80 80 50, with duration of 320 (inlet) and 310 (exhaust). The textbooks suggest this will give a useful RPM range of 3500 - 9000 with peak power somewhere around 8500. Somewhat wilder than I expected but we'll see how it goes .
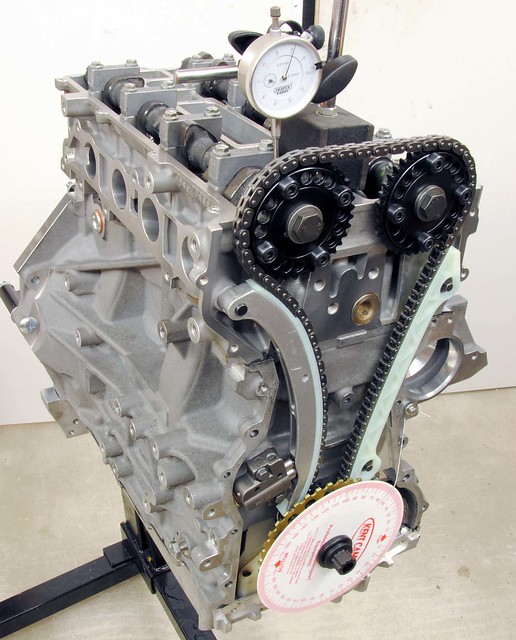
With the engine sealed up I began fitting the auxiliaries. I had thought about fitting the alternator on the exhaust side but, as the smaller pulley worked fine with the original set-up, I decided to keep it that way. Next will be the roller barrels overhaul and fitting.
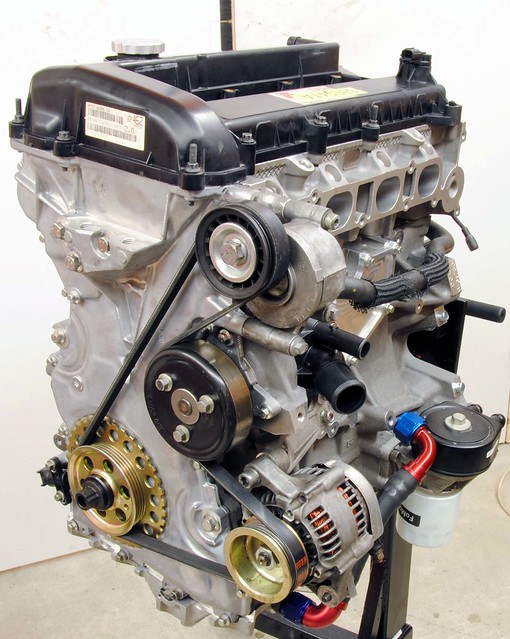
As planned the barrels were overhauled and fitted today. I was surprised at how poor the condition was that they were in, mainly with wear and corrosion. They've done about 5K miles - and they will certainly be past their best by 10K.
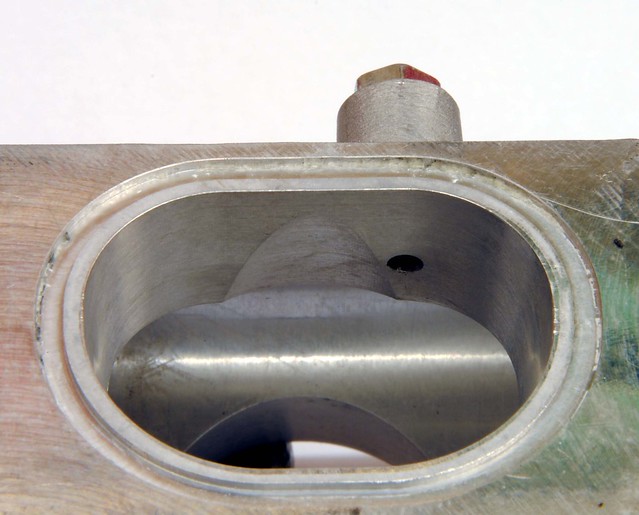
They are, however, a very simple device once the end plates are removed and it was not long before they were done and fitted to the engine. But I did make the classic mistake of not removing the TPS first, so now it's scrap .
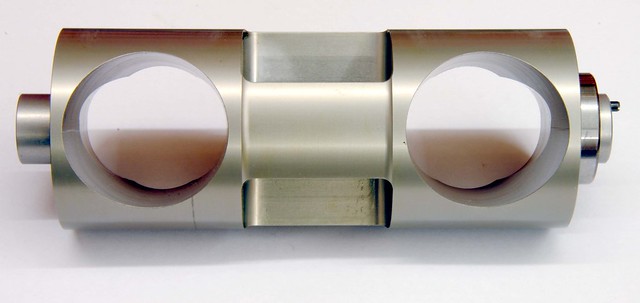
Setting them up is not difficult. Using a 6mm rod to hold them open, the end stops are adjusted in turn to take up the slack. It is worth saying that the 6mm gap at the front is not the 'throttle' opening - that all happens at the back (engine) side. This procedure effectively set the barrel to 'just' closed. There is also a bleed hole which will be adjusted to get idle flow correct when I'm up and running.
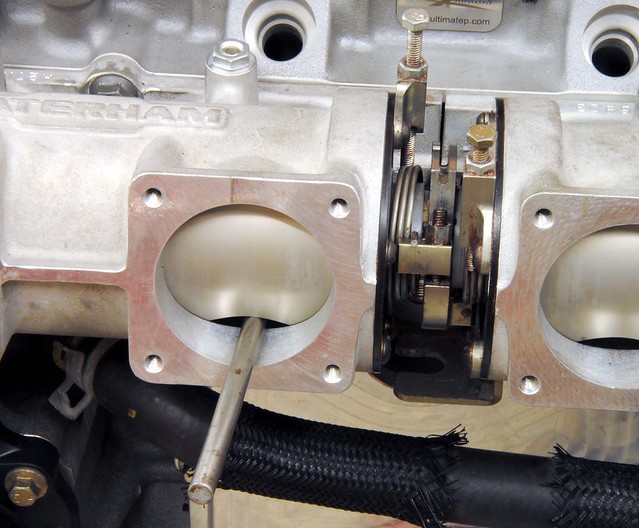
Well, the engine is now finished . the final touch was to fit the rather nice flywheel and twin plate Super Clutch from SB Developments.

The twin plate super clutch is thicker and needs a rounded clutch release bearing. This was supplied with a new release mechanism by SB developments as part of the clutch kit. It also has a spacer to provide the correct position. The hardest part was making up the hoses.
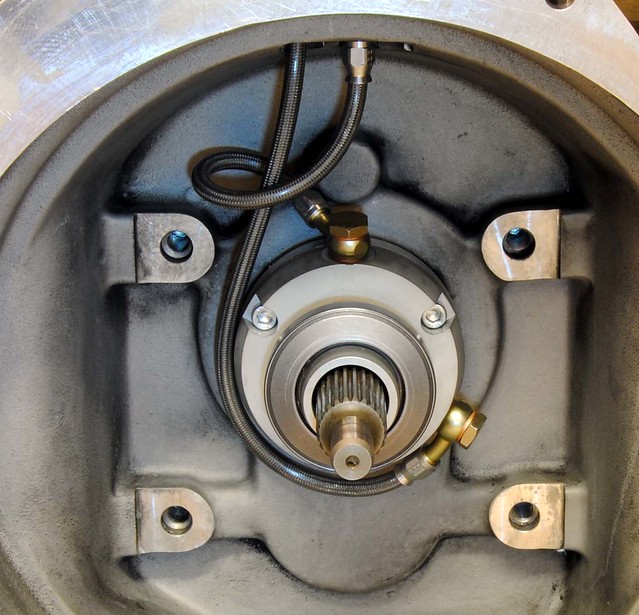
The engine went in today - a fairly standard job with no real issues but the clutch does feel rather 'firm'. I'm sure I'll get used to it. All the fluids are in but the TPS didn't arrive, so couldn't start it up - maybe Monday
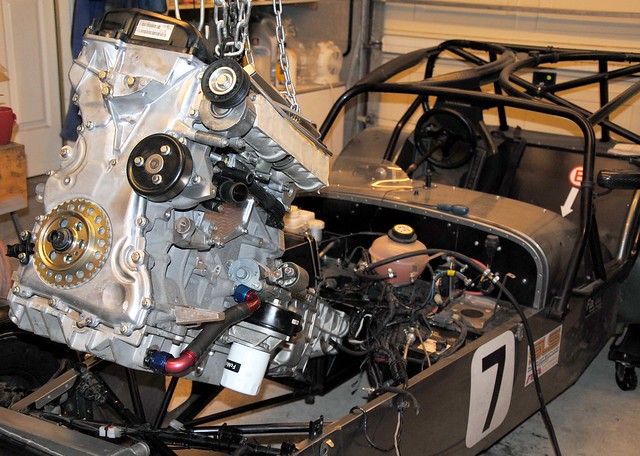
The big moment came! With my son supervising me (and keeping me right) the start button was pushed. I was surprised that it fired instantly. Although I stopped the video by accident, I continued to run it for about 20 minutes. I will not run again until it is on the rolling road next week - so that it's run-in under load.
http://www.youtube.com/watch?v=hrksbKEXfFI
RGambo said:
Great thread. Love the detail. Makes me want to do the upgrade on the sogma myself. The super clutch is the same as I fitted to my VX. They are 'heavy' and very on/off to use. Not good for hill starts :-) In saying that, I did do lemans and back with mine. No issues, other than a really big left calf at the end :-)
That's an interesting comment. Since buying the Superclutch I've had some negative feedback about them, basically saying the solid plate requires an un-achievable tolerance to give any sort of long term durability. Failure of splines and bearings (engine and gearbox) being listed. How many miles has yours done? Any problems? Yesterday was spent on the rolling road running-in and putting together a safe map to allow some track time. The running-in was an alternating pattern between various stages of throttle and full vacuum (closed throttle). The idea (I'm told) is to allow the rings to be pushed out followed by all the debris being sucked out. This went on for about an hours or so as we watched and listened for any thing out of the ordinary. The operator wore a stethoscope bolted to the knock sensor bolt just to give us early warning of any issues. The Supertech pistons, apparently, were heard slapping about a bit - typical of the short skirt design, but it ran smoothly with less vibration than the predecessor.
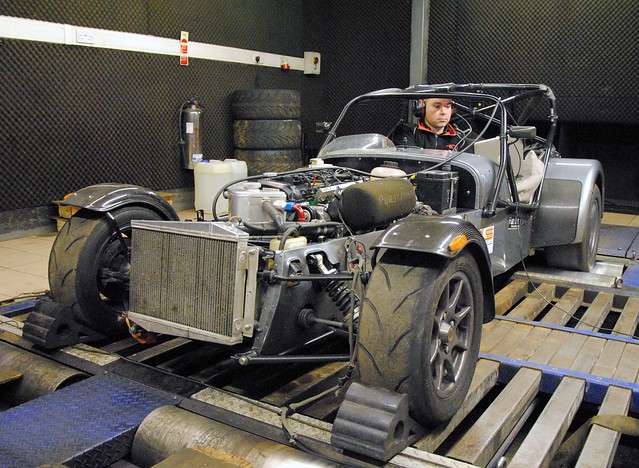
Once this was completed, we moved on to mapping. The objective at this stage was not to get a headline BHP figure, but to get something safe to build a bit of track time. We therefore set a rev limit of 7600 RPM and mapped with an eye on the budget. The detailed tweaking is still to come, but we did a few power runs at the end which gave 226BHP at the wheels - which was better than I expected.
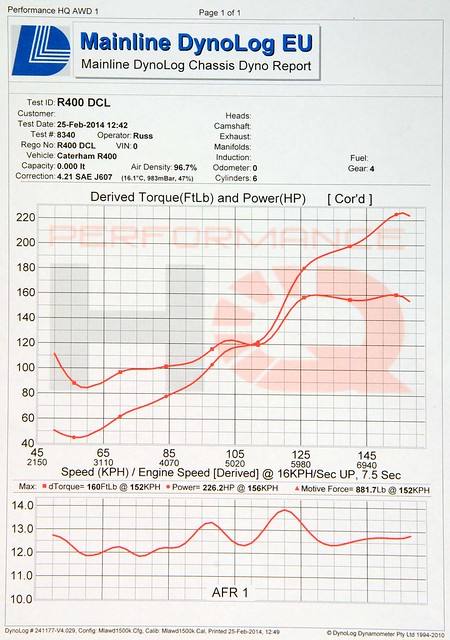
What did become clear is that the cams are really intended for high RPM. It really came alive at 6000 RPM and, in the words of the operator, 'about to go ballistic' when the rev limiter cut in. I know the 4:1 exhaust is not ideal for low torque and also the Cosworth barrels have limitations too, so this was good news and spot on what Simon at Ultimate had predicted.
http://www.youtube.com/watch?v=fU6U_N9_mPc
There was an induction noise at around 3000 rpm that sounds horrible, but is probably the large overlap on the cams. All in all a good day
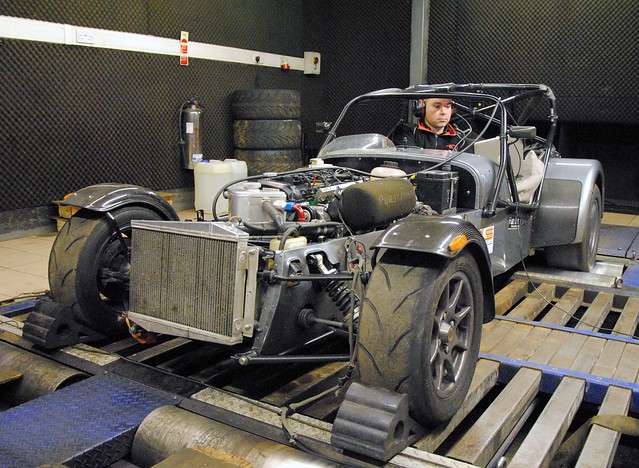
Once this was completed, we moved on to mapping. The objective at this stage was not to get a headline BHP figure, but to get something safe to build a bit of track time. We therefore set a rev limit of 7600 RPM and mapped with an eye on the budget. The detailed tweaking is still to come, but we did a few power runs at the end which gave 226BHP at the wheels - which was better than I expected.
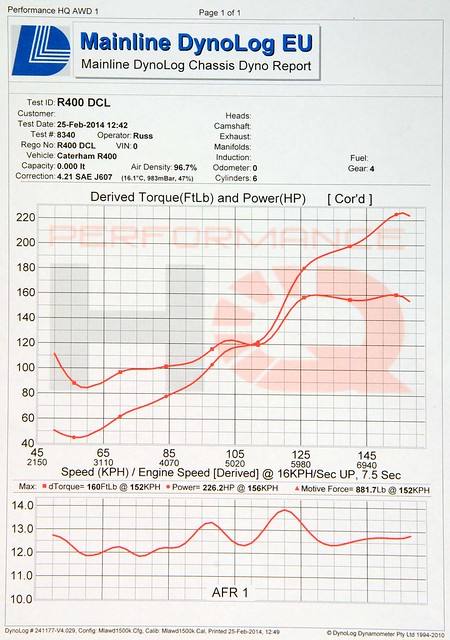
What did become clear is that the cams are really intended for high RPM. It really came alive at 6000 RPM and, in the words of the operator, 'about to go ballistic' when the rev limiter cut in. I know the 4:1 exhaust is not ideal for low torque and also the Cosworth barrels have limitations too, so this was good news and spot on what Simon at Ultimate had predicted.
http://www.youtube.com/watch?v=fU6U_N9_mPc
There was an induction noise at around 3000 rpm that sounds horrible, but is probably the large overlap on the cams. All in all a good day

An update:
226 BHP at the wheels at only 7600 RPM was more impressive than I was expecting, but, I must confess, the torque curve was a little disappointing - particularly when comparing it to the old engine (blue)
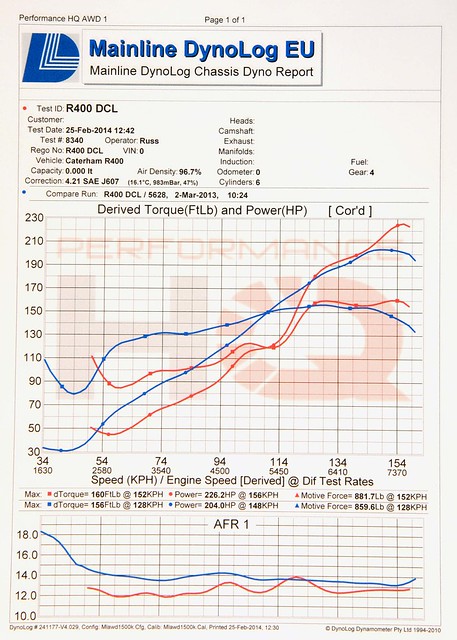
I knew, with the 4-1 exhaust, things would not be great, but feel the skill required to keep it 'on cam' may be beyond both me and the gear ratios. So the decision has been made to bring forward 'phase two' of the project and get a proper 4-2-1 made for this season. So, BTB have been commissioned to make an exhaust to Ultimate performance's spec. It will be a real challenge to package it in the S3 chassis without compromise but thanks to purespeed for prototyping it for me
, I've only got three weeks to my first event, so this will be fun.
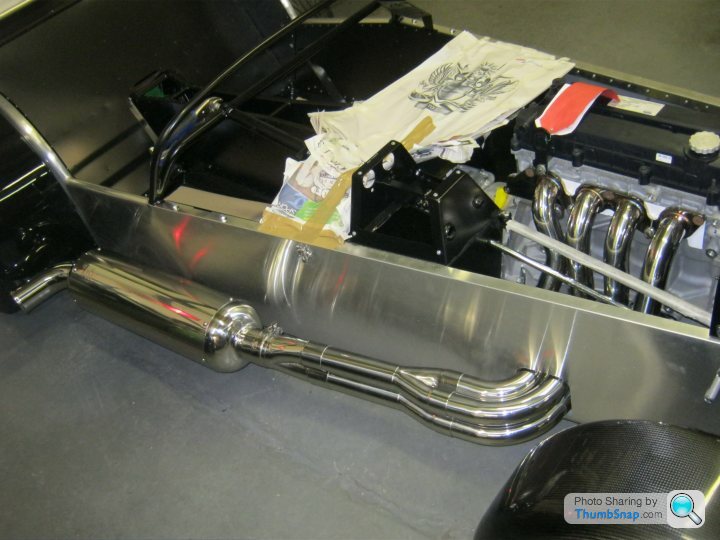
226 BHP at the wheels at only 7600 RPM was more impressive than I was expecting, but, I must confess, the torque curve was a little disappointing - particularly when comparing it to the old engine (blue)
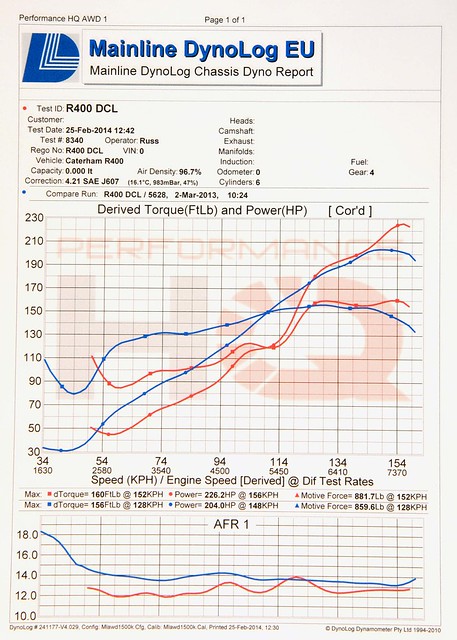
I knew, with the 4-1 exhaust, things would not be great, but feel the skill required to keep it 'on cam' may be beyond both me and the gear ratios. So the decision has been made to bring forward 'phase two' of the project and get a proper 4-2-1 made for this season. So, BTB have been commissioned to make an exhaust to Ultimate performance's spec. It will be a real challenge to package it in the S3 chassis without compromise but thanks to purespeed for prototyping it for me

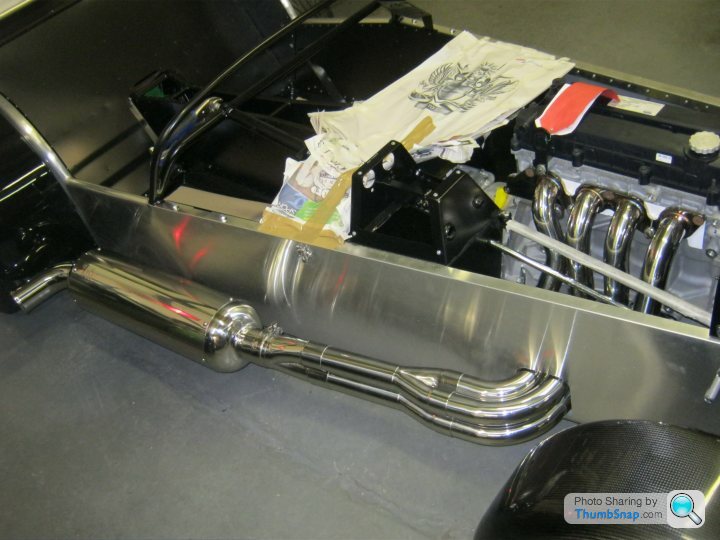
Thanks, that's some good information. The car is purely a track car, so I was intending to go a bit hotter on the cams than I would have done for a road car. But I think I may have overdone done it for the current exhaust and perhaps milder cams may have produced more cost effective results - there's still work to be done!(and I haven't ruled out a cam change).
A couple of things about the graphs - there is a lot of smoothing on the graph and, when you look at the raw dyno data, the power is still going up at the limiter. We think it is going to peak in another 5-600 RPM. Also the derived rpm is a little off due to differing degrees of wheel slip on the runs, so the derived torque is also off as it is defined by the 5252 cross over point - meaning the back to back comparison with the original engine, and figures, shouldn't be taken too literally.
I'm very much in a learning curve at the moment. Most people I have talked to think the exhaust needs to be a bigger diameter, and 4-2-1, so that's the way this project is heading at the moment. I like your comment about induction clearance and will certainly look at that next.
A couple of things about the graphs - there is a lot of smoothing on the graph and, when you look at the raw dyno data, the power is still going up at the limiter. We think it is going to peak in another 5-600 RPM. Also the derived rpm is a little off due to differing degrees of wheel slip on the runs, so the derived torque is also off as it is defined by the 5252 cross over point - meaning the back to back comparison with the original engine, and figures, shouldn't be taken too literally.
I'm very much in a learning curve at the moment. Most people I have talked to think the exhaust needs to be a bigger diameter, and 4-2-1, so that's the way this project is heading at the moment. I like your comment about induction clearance and will certainly look at that next.
Edited by DCL on Saturday 8th March 11:17
I think I said right at the beginning of this project that there was going to be more than one phase - the idea in my head was to build the engine and then upgrade the exhaust and inductions over the following year. But what I have learnt is that the more you push the limits, the less tolerant the engine becomes to minor deficiencies.
So I have decided to accelerate exhaust phase of the project in the hope of a less peaky power delivery.
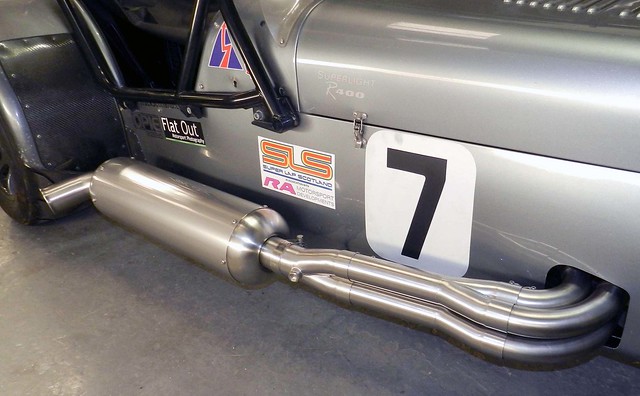
Today the exhaust was finished. It is basically a bigger diameter and a 4-2-1 design. The dimensions are Ultimate's and are specifically for the CNC head and cams I'm using. There are other headers and exhausts on the market that are similar (and may have worked) but I decided the additional cost of one fabricated to the exact dimensions was not that high and would be worth it. So, this is a one is a one-off made by BTB and, I believe, a first for a metric S3 chassis.
Dyno next week! Talk about putting your money where your mouth is - hope it works
So I have decided to accelerate exhaust phase of the project in the hope of a less peaky power delivery.
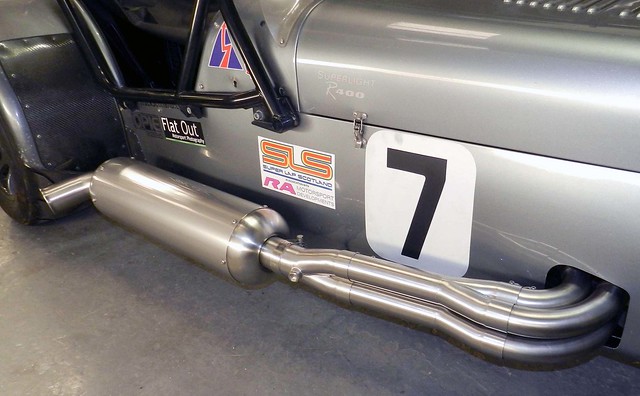
Today the exhaust was finished. It is basically a bigger diameter and a 4-2-1 design. The dimensions are Ultimate's and are specifically for the CNC head and cams I'm using. There are other headers and exhausts on the market that are similar (and may have worked) but I decided the additional cost of one fabricated to the exact dimensions was not that high and would be worth it. So, this is a one is a one-off made by BTB and, I believe, a first for a metric S3 chassis.
Dyno next week! Talk about putting your money where your mouth is - hope it works

k20erham said:
Hi your about 2 years late for the 1st btb in a s3, Joe did a wonderful job on mine, again spot on with how it performs, although had to repack the can twice so far but its not a drama.
Joe said it's the first metric chassis they've done - maybe he's mistaken, but they were measuring templates from it yesterday for future reference. The main difference from an imperial S3 is the cross member on the metric chassis allows no.4 header on the other side of the steering tube and reduce the otherwise tight radius. [edit: as seen on Jason's car photograph in the post above]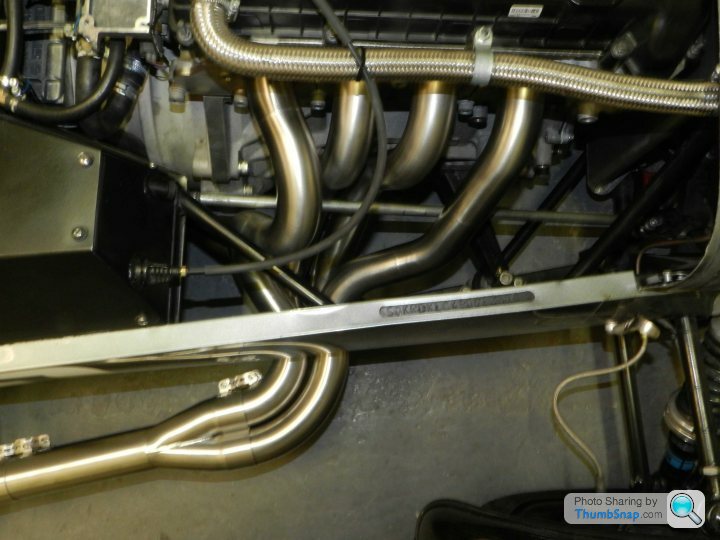
Edited by DCL on Saturday 22 March 22:28
Mostly when I hit a problem I try and think it through, come up with a plan, and start again when my solution doesn't work. But every now and then it all comes together - the last couple of days have been like that. BTB delivered on time, Ulitimate's exhaust spec was spot on, and Northampton Motorsport did their stuff.
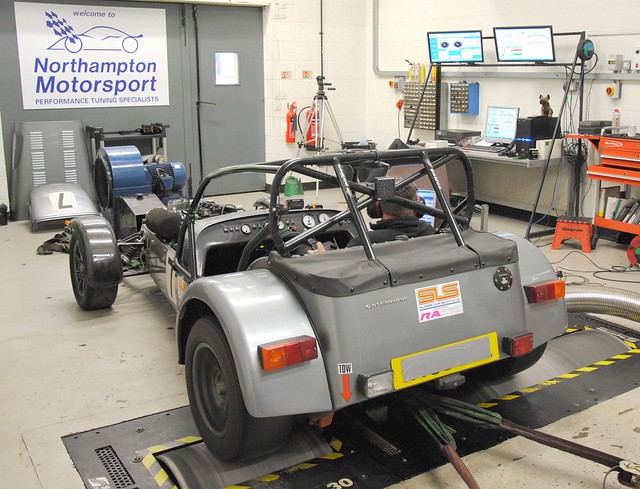

I am still digesting the data and will comment more later, but at last got a torque curve, and BHP figures, that put a smile on my face.
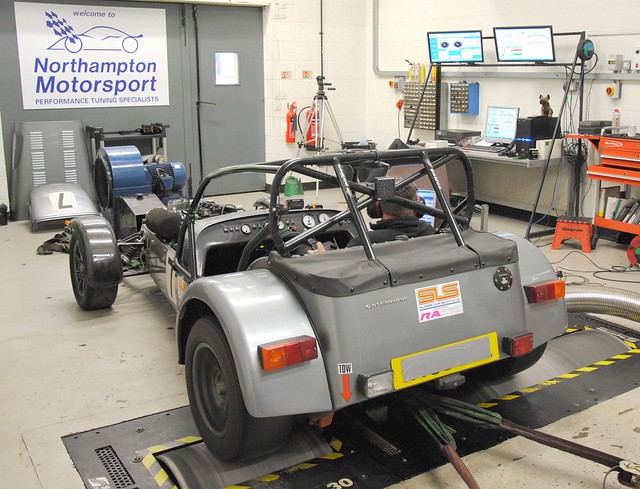

I am still digesting the data and will comment more later, but at last got a torque curve, and BHP figures, that put a smile on my face.

Edited by DCL on Thursday 27th March 12:01
Edited by DCL on Tuesday 15th April 11:15
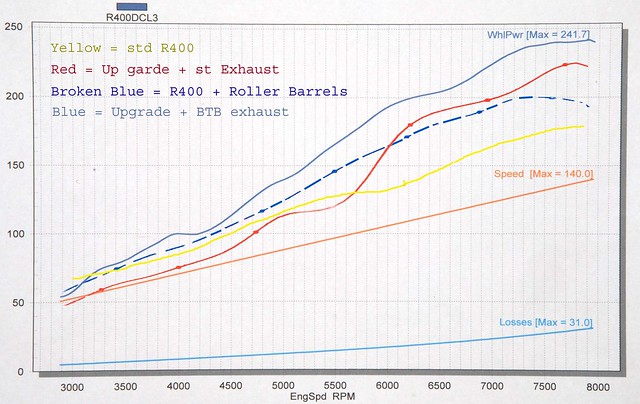
I made this graphic that compares the wheel HP at the various stages of tune the car has been in. Firstly theses are from different dyno so don't take the too literally, but they do give an idea of how things have changed. The new engine has exceeded previous power graphs at all speeds above 3000 rpm. It is a bit bumpy in places but is essentially straight. The BTB exhaust has done to two things - its bigger diameter has released more power, and the 4-2-1 has lifted the the torque and filled the dips below 6000 RPM. Theoretically, the roller barrels are in tune around 7500 to 8500 rpm, and you can see evidence of this with the second bump at peak power. I was thinking of changing the barrels but looking at the graph they do seem to work well with this exhaust (by happy coincidence) and may leave them for the time being.
OK, it time for an update as the project seems to becoming to a natural end by driving the car for the first time.
https://www.youtube.com/watch?v=sVM6hCwQoXc
Although the weather conditions were appalling, it was an excellent test of the car's drive-ability which had been my main worry about the upgrade. In fact, it seemed better behaved than the old engine.
. The Clutch was fine too, maybe a little off or on, but I quickly got used to it.
As the trackday was halted after these laps because of fog, I went to the local rolling road to do a power check for the Super Lap Scotland championship that I'm enetering.
https://www.youtube.com/watch?v=HXVF6Z6ehbc
It gave a wheel HP of 240.2 HP (on a later run not shown in the graph below) which was within a 1 BHP of Northhampton Motorsport figure (in the region of 270-280 BHP at the flywheel). But more importantly, it allowed a direct comparison of pre (red) and post (Blue) exhaust upgrade. I am please with the power, particularly as there's still another 1000 RPM to explore, but it is a little off target for the SLS class B upper limit of 375 WHP/tonne (it came to 386WHP/tonne). I'll either go up and play with the big boys in Class A, or put some ballast in.
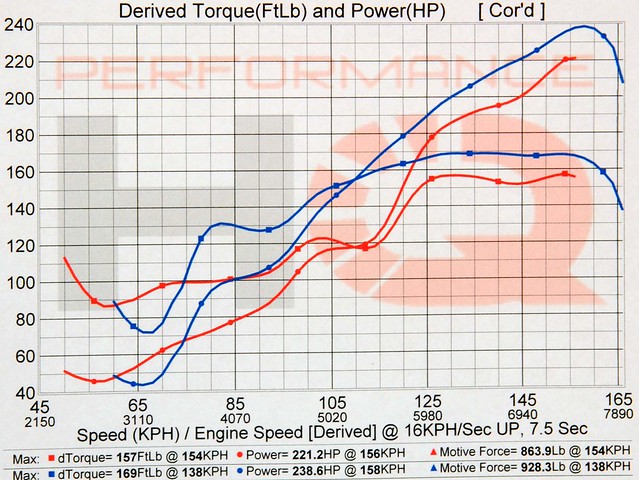
The exhaust works well and effectively solved the torque delivery issues - easily the single most important component in the upgrade. Also, as it was not cheap, it was a great relief that I made the right call in terms of what was wrong after the initial dyno work.
I've learnt a huge amount doing this - maybe not in putting it together, but certainly in the concepts of tuning and what it really works in the real world. The process of manipulating the torque curve hadn't really been fully appreciated by me at the start. The process of using exhaust primaries, secondaries, and induction length all tuned to different RPMs to make a flat torque curve just makes so much more sense now.
Things I would do differently: I wouldn't have bought a new engine, but would have upgraded the old one. Maybe, kept the old flywheel and clutch. Taken more time to research things. But that's about it.
https://www.youtube.com/watch?v=sVM6hCwQoXc
Although the weather conditions were appalling, it was an excellent test of the car's drive-ability which had been my main worry about the upgrade. In fact, it seemed better behaved than the old engine.

As the trackday was halted after these laps because of fog, I went to the local rolling road to do a power check for the Super Lap Scotland championship that I'm enetering.
https://www.youtube.com/watch?v=HXVF6Z6ehbc
It gave a wheel HP of 240.2 HP (on a later run not shown in the graph below) which was within a 1 BHP of Northhampton Motorsport figure (in the region of 270-280 BHP at the flywheel). But more importantly, it allowed a direct comparison of pre (red) and post (Blue) exhaust upgrade. I am please with the power, particularly as there's still another 1000 RPM to explore, but it is a little off target for the SLS class B upper limit of 375 WHP/tonne (it came to 386WHP/tonne). I'll either go up and play with the big boys in Class A, or put some ballast in.
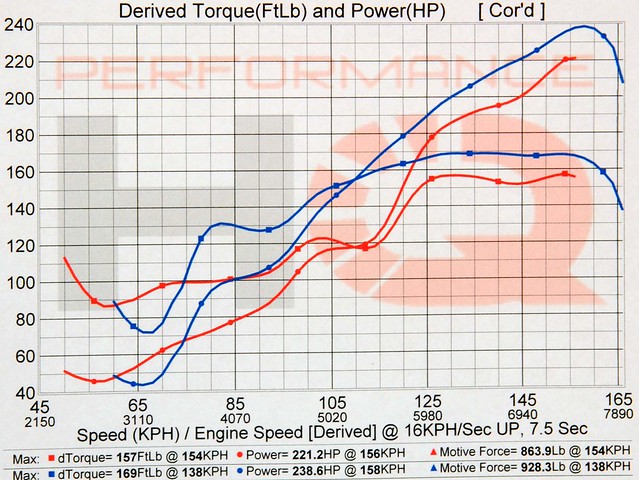
The exhaust works well and effectively solved the torque delivery issues - easily the single most important component in the upgrade. Also, as it was not cheap, it was a great relief that I made the right call in terms of what was wrong after the initial dyno work.
I've learnt a huge amount doing this - maybe not in putting it together, but certainly in the concepts of tuning and what it really works in the real world. The process of manipulating the torque curve hadn't really been fully appreciated by me at the start. The process of using exhaust primaries, secondaries, and induction length all tuned to different RPMs to make a flat torque curve just makes so much more sense now.
Things I would do differently: I wouldn't have bought a new engine, but would have upgraded the old one. Maybe, kept the old flywheel and clutch. Taken more time to research things. But that's about it.
Edited by DCL on Sunday 30th March 14:11
Edited by DCL on Sunday 30th March 14:24
After one aborted track day due to fog, I finally managed to get the car out on track on Saturday evening. Conditions were dry but windy and cold, so it was not going to be a perfect. But first session went without a hitch and two more followed where I was beginning to get my eye in. I felt really rusty after the winter break and the impression was that the car was harder to drive. Perhaps though, things were just happening a bit qicker than before. . .
http://youtu.be/7S4QlDTrJM0
Taking the Knockhill pit lane straight, here's a comparison of pre and post up-garde.
http://youtu.be/nir65SiShy0
The data from last year, and Saturaday night, shows the improvement in acceleration and top speed. Well over 10 MPH and 1.7 second up on the pit straight alone. But this needs to take account of the wind on Saturday which (from my experience) was probably worth .5 second.
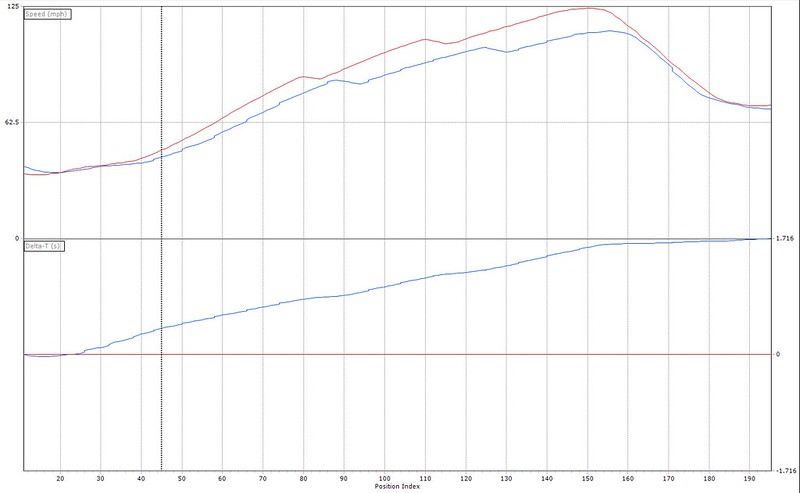
So in conclusion, I think I've achieved what I set out to do. The car is definitely an R500+ now
http://youtu.be/7S4QlDTrJM0
Taking the Knockhill pit lane straight, here's a comparison of pre and post up-garde.
http://youtu.be/nir65SiShy0
The data from last year, and Saturaday night, shows the improvement in acceleration and top speed. Well over 10 MPH and 1.7 second up on the pit straight alone. But this needs to take account of the wind on Saturday which (from my experience) was probably worth .5 second.
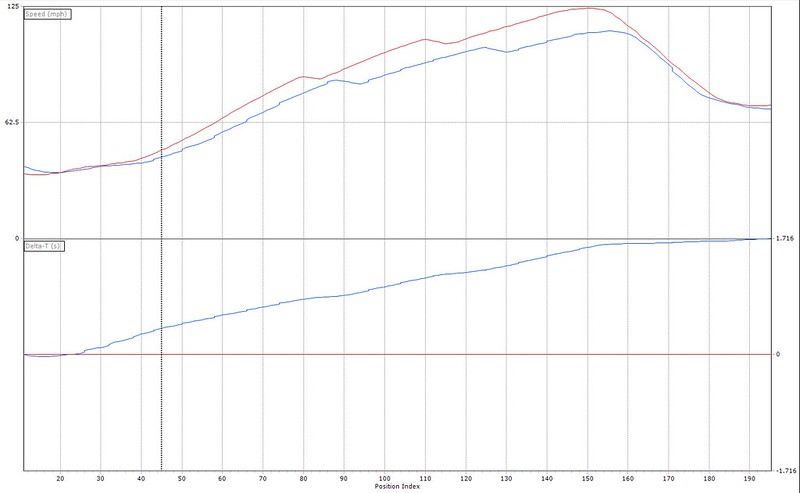
So in conclusion, I think I've achieved what I set out to do. The car is definitely an R500+ now

GreigM said:
Great read and results....look forward to seeing it on sunday. Have you decided to stay in class A or ballast up for class B?
After testing this evening with ballast, I've decided to go with Class A. The ballast took the edge off the braking and general handling which I think was more of a disadvantage that moving up a class. As a close to this thread I though I'd post a report of the first competitive event . . .
(copied from the SE forum)
This year has flown by and before I knew it the SLS round 1 was upon me. This year the power band have been narrowed and I had hoped to be in the top of Class B, unfortunately the power increase on the new engine was a little too much and I found myself at the bottom of Class A. On the positive note, it does leave a bit of head room to develop things further.
This was the first event with the new engine so I was particularly nervous. Also the high workload to get the engine ready meant the rest of the car was under prepared. In particular the suspension and geo needed a check. The engine is still limited to 8000RPM as a precaution, which did compromise gear ratios.
Free Practice:
http://youtu.be/vqvrFx4m4eA

At this point things were looking good with the car being the quickest non pro entry, and a new PB in the bag. But I was surprised that the pace wasn't quicker - maybe my expectation of an extra 50 BHP was too much and, in hindsight, my tyres were beginning to take a dive .
Qualifying
http://youtu.be/RbNNMJvECR8
This didn't go my way, my first two runs were blocked by traffic so last session saw me in an agitated state and not at my best. I got low 58 and 8th place. The surprise was Fee Kindness had found a whole chunk of time and got a 56 - territory beyond me at this stage.
I knew it would be down hill form now on as the Caterham just can't warm the ZZR A60 compound tyres I am using in the 'single lap' format but I was hoping for at least a 58.
The final
http://youtu.be/0KaZ_T6cMOc
I was out on track with Pro Class drivers, Charlie Shaw, and Graham Davidson, so feeling a bit nervous about getting in their way, so the tyre warming probably wasn't as thorough as it should have been. The rear was also looser than usual - I now suspect the rear tyres were past their best having been on the car for over a year of hard tracking. Anyway, the lap started well but I shifted up (old habbit) after MacIntyres, a mistake that cost me all the way through to Clarks, but I was releaved to get a 58.6 which put me in 7th overall and 2nd in Class
Good points for going to round 2. Fourth equal in the championship

Full results here: http://www.mylaps.com/en/events/1005418
(copied from the SE forum)
This year has flown by and before I knew it the SLS round 1 was upon me. This year the power band have been narrowed and I had hoped to be in the top of Class B, unfortunately the power increase on the new engine was a little too much and I found myself at the bottom of Class A. On the positive note, it does leave a bit of head room to develop things further.
This was the first event with the new engine so I was particularly nervous. Also the high workload to get the engine ready meant the rest of the car was under prepared. In particular the suspension and geo needed a check. The engine is still limited to 8000RPM as a precaution, which did compromise gear ratios.
Free Practice:
http://youtu.be/vqvrFx4m4eA

At this point things were looking good with the car being the quickest non pro entry, and a new PB in the bag. But I was surprised that the pace wasn't quicker - maybe my expectation of an extra 50 BHP was too much and, in hindsight, my tyres were beginning to take a dive .
Qualifying
http://youtu.be/RbNNMJvECR8
This didn't go my way, my first two runs were blocked by traffic so last session saw me in an agitated state and not at my best. I got low 58 and 8th place. The surprise was Fee Kindness had found a whole chunk of time and got a 56 - territory beyond me at this stage.
I knew it would be down hill form now on as the Caterham just can't warm the ZZR A60 compound tyres I am using in the 'single lap' format but I was hoping for at least a 58.
The final
http://youtu.be/0KaZ_T6cMOc
I was out on track with Pro Class drivers, Charlie Shaw, and Graham Davidson, so feeling a bit nervous about getting in their way, so the tyre warming probably wasn't as thorough as it should have been. The rear was also looser than usual - I now suspect the rear tyres were past their best having been on the car for over a year of hard tracking. Anyway, the lap started well but I shifted up (old habbit) after MacIntyres, a mistake that cost me all the way through to Clarks, but I was releaved to get a 58.6 which put me in 7th overall and 2nd in Class

Good points for going to round 2. Fourth equal in the championship


Full results here: http://www.mylaps.com/en/events/1005418
Edited by DCL on Monday 21st April 12:34
Edited by DCL on Monday 21st April 15:12
Well, now my season has ended, it's time to report how the engine did.
Following the mapping at Northamptom Motorsport, the engine hasn't been touched and it has ran faultlessly the whole season. It delivered 4 SLS class wins, SLS Class Championship, 2nd overall in the 'King of the Hill' championship, class lap records in both directions at KH. A few trackdays thrown in too. I'm happy with that
.
The main issues I had was with tyres - I ended up using the the soft compound Kumho V70 as the harder compound tyres just didn't give me the traction I needed to compete with the big power 4WD cars.
But things don't stop, so I going to fit the SBD taper boddies to see if I can improve the lower end a bit. I will update when it's done. Also there's the Sadev which I'll cover in my other thread

Following the mapping at Northamptom Motorsport, the engine hasn't been touched and it has ran faultlessly the whole season. It delivered 4 SLS class wins, SLS Class Championship, 2nd overall in the 'King of the Hill' championship, class lap records in both directions at KH. A few trackdays thrown in too. I'm happy with that

The main issues I had was with tyres - I ended up using the the soft compound Kumho V70 as the harder compound tyres just didn't give me the traction I needed to compete with the big power 4WD cars.
But things don't stop, so I going to fit the SBD taper boddies to see if I can improve the lower end a bit. I will update when it's done. Also there's the Sadev which I'll cover in my other thread

Edited by DCL on Monday 22 September 18:44
With the season over I'm enjoying a caffeine overdose in the workshop and have started planning the next upgrade campaign.
I removed the roller barrels and started to look at what will be required for the switch the taper bodies. I've chosen to make significant changes to the fuel supply by adding a return and fuel rail regulator. Maybe that's normal in turbo charged cars but Caterham use a single line.
Here's them side by side - the taper bodies slightly longer but the main difference is the injectors being further out and underneath.
l
This means that I need to block the old injector hole in the head. Rather than just fit a blanking plug, I decided to make some dummy injector blanks to fill the injector cavity. I'm not sure if the cavity would have any detrimental effect but it was a good excuse to play with the lathe
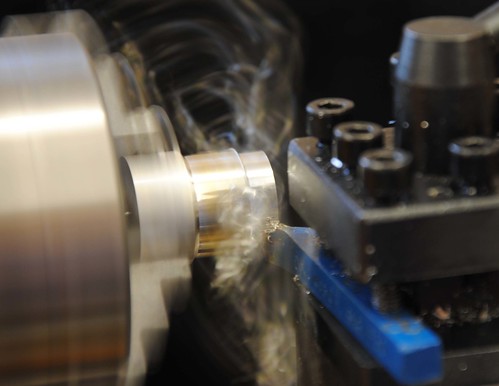
To make these:
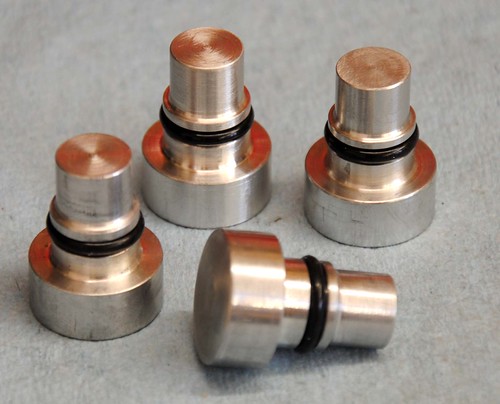
That fit here:
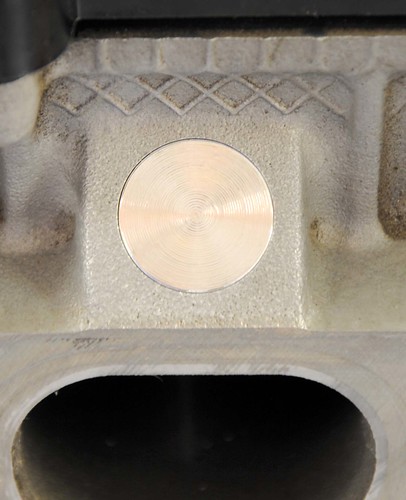
They are a tight fit and will be locked in with loctite and a punch.
I removed the roller barrels and started to look at what will be required for the switch the taper bodies. I've chosen to make significant changes to the fuel supply by adding a return and fuel rail regulator. Maybe that's normal in turbo charged cars but Caterham use a single line.
Here's them side by side - the taper bodies slightly longer but the main difference is the injectors being further out and underneath.
l

This means that I need to block the old injector hole in the head. Rather than just fit a blanking plug, I decided to make some dummy injector blanks to fill the injector cavity. I'm not sure if the cavity would have any detrimental effect but it was a good excuse to play with the lathe

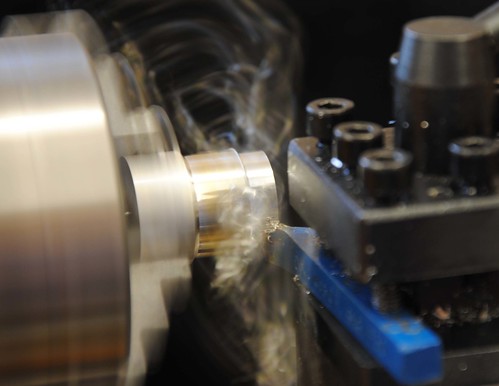
To make these:
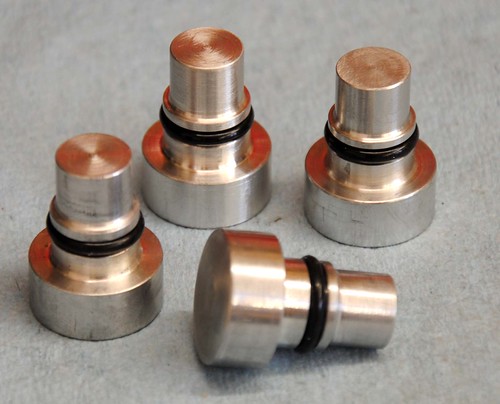
That fit here:
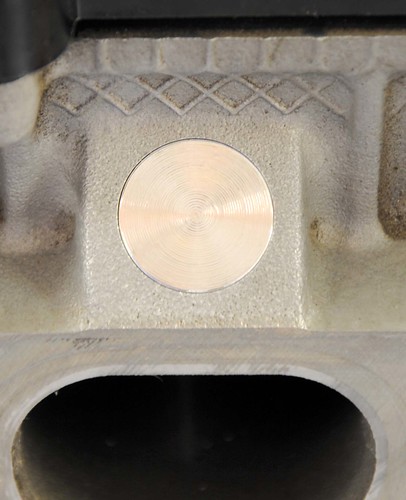
They are a tight fit and will be locked in with loctite and a punch.
I honestly don't know. The data suggest it would be around 2 seconds, but I think other factors will come into play that will peg that back a bit - so maybe a second. The main problem I have is that the car is harder to drive consistently with more power. You just need more throttle input to optimise traction. And little mistakes just have a bigger impact on the lap times as you get quicker.
Gassing Station | Caterham | Top of Page | What's New | My Stuff