R400D to R500D Anyone done it?
Discussion
The 2.5L is relatively new variation to the Duratec range and it has a slightly larger big-end journal. This meant that the bearings shells were not available in the up-rated materials when the rods were designed. So this engine, will use the Subaru VP2 shells which happen to be identical in journal diameter. These bearings have a notch, or tang, so the rods have been machined to accommodate them.

The bespoke nature of the rods also gave the opportunity to rethink the factory spec and they have been made slightly longer and the gudgeon pin size has been reduced. This will reduce weight and improve geometry.

The ARP2000 bolts, although no longer my first choice in bolts, where the logical option and are well proven solution.
Pistons next . . .

The bespoke nature of the rods also gave the opportunity to rethink the factory spec and they have been made slightly longer and the gudgeon pin size has been reduced. This will reduce weight and improve geometry.

The ARP2000 bolts, although no longer my first choice in bolts, where the logical option and are well proven solution.
Pistons next . . .
A quick update . . .
The 2.5L project took a little bit of a break during May but I'm back on task now. All the major parts have now all been sourced, or at least on order, and the latest bit to arrive was a new crate engine which I've spent the last few day stripping it down. I don't plan to use that much of it beyond the block, but it's always nice to have a complete set of compatible parts, and they represent good value IMHO. Quite a lot to talk about in terms of the differences between the 2.0L and 2.5L, some of them are quite subtle, but significant. Quality control issues on this engine too that surprised me - more later.
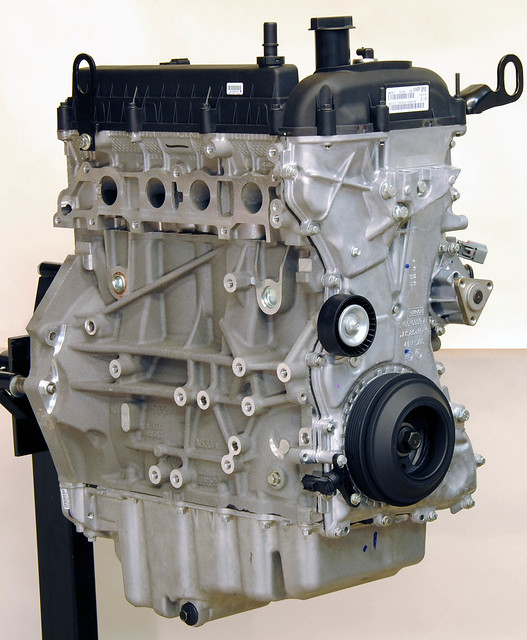
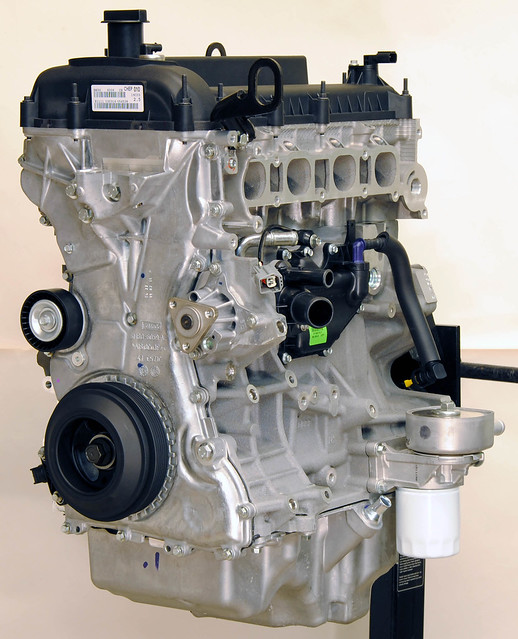
The 2.5L project took a little bit of a break during May but I'm back on task now. All the major parts have now all been sourced, or at least on order, and the latest bit to arrive was a new crate engine which I've spent the last few day stripping it down. I don't plan to use that much of it beyond the block, but it's always nice to have a complete set of compatible parts, and they represent good value IMHO. Quite a lot to talk about in terms of the differences between the 2.0L and 2.5L, some of them are quite subtle, but significant. Quality control issues on this engine too that surprised me - more later.
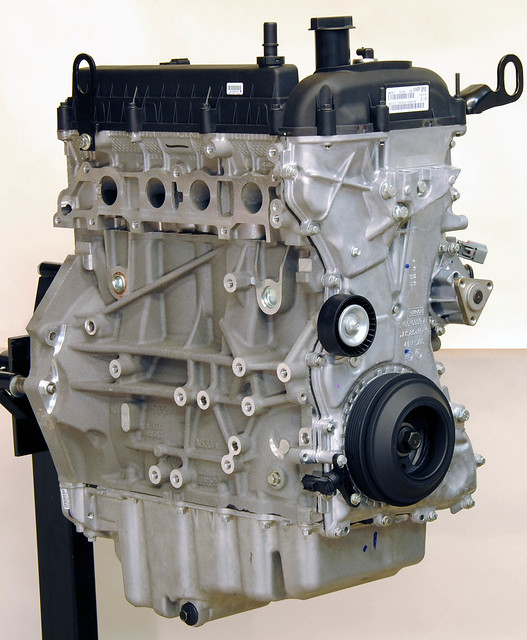
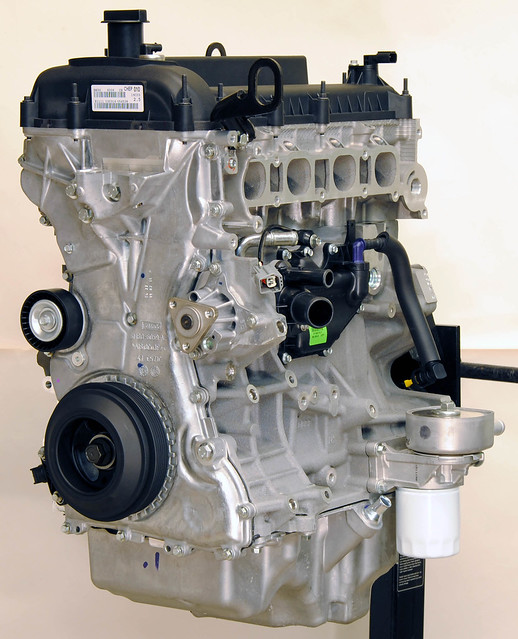
Edited by DCL on Thursday 8th June 21:54
After the crate engine arrived, I had a fun day stripping it down. A few quality issues on this Mexican built engine, but nothing I can't deal with.
Video here . . .
https://youtu.be/8hxuqvI7ESg
It gave me my first opportunity to compare the cranks - the standard one being 4 Kg heavier.
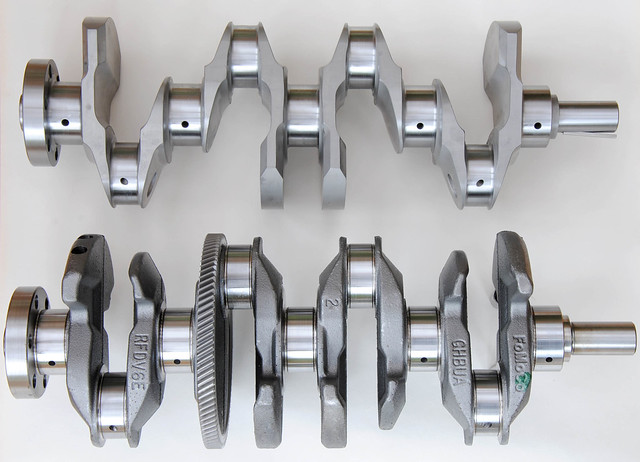
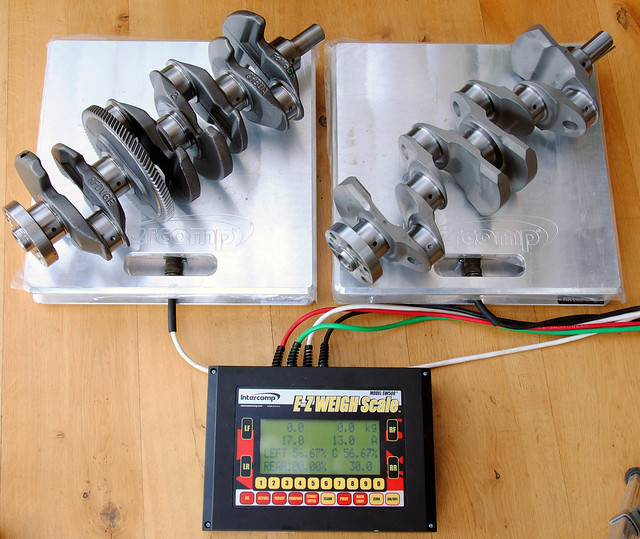
The quality problems were relatively minor in nature but these things are always annoying. The engine seems to have been assembled in a poorly washed condition and corrosion had taken place on many of the bolts and casting. Some alloy debris was evident on the head gasket and there were some scratch marks on the deck of the block - but not deep enough to require reworking. Ford are usually spot on, so a little surprises by this. The main bearings, the part I was most interested in, was all in good order.
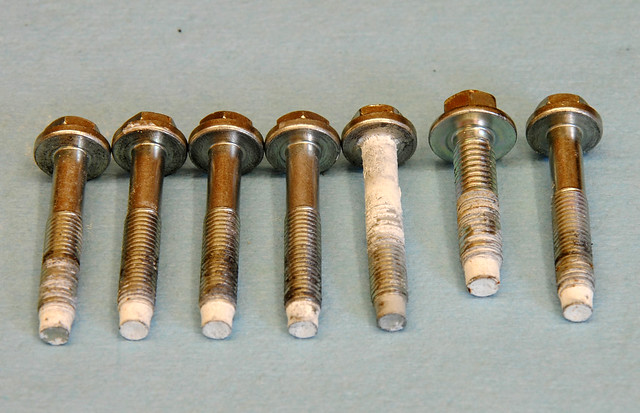
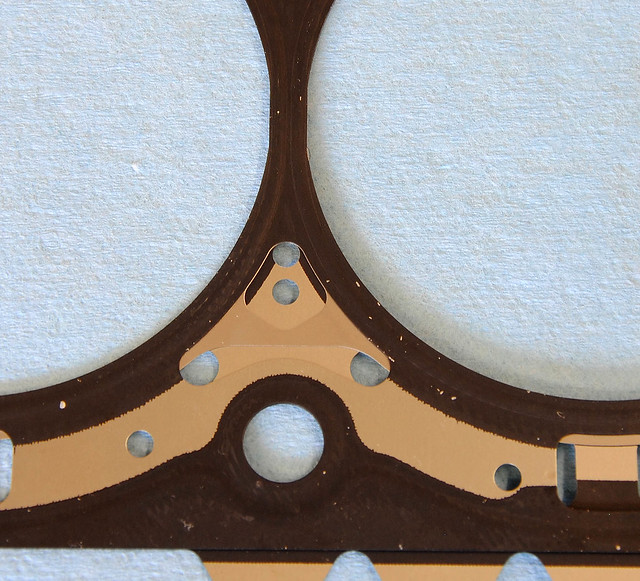
Video here . . .
https://youtu.be/8hxuqvI7ESg
It gave me my first opportunity to compare the cranks - the standard one being 4 Kg heavier.
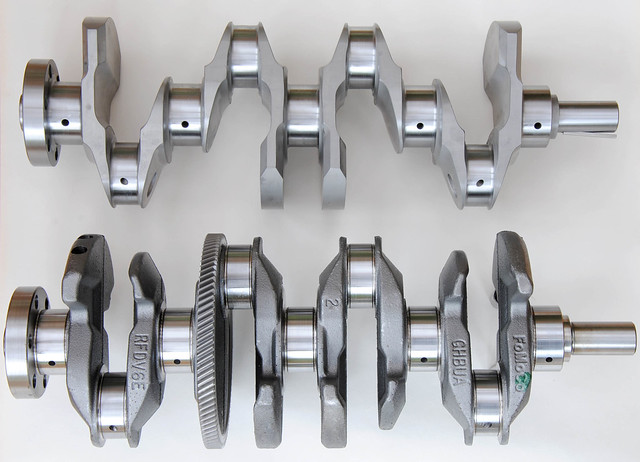
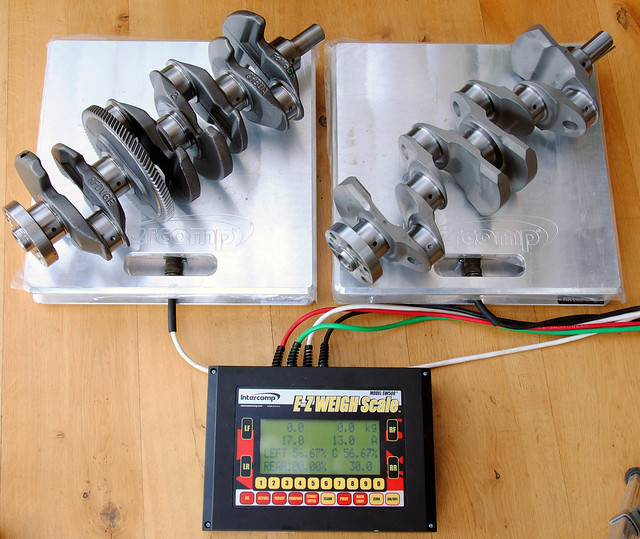
The quality problems were relatively minor in nature but these things are always annoying. The engine seems to have been assembled in a poorly washed condition and corrosion had taken place on many of the bolts and casting. Some alloy debris was evident on the head gasket and there were some scratch marks on the deck of the block - but not deep enough to require reworking. Ford are usually spot on, so a little surprises by this. The main bearings, the part I was most interested in, was all in good order.
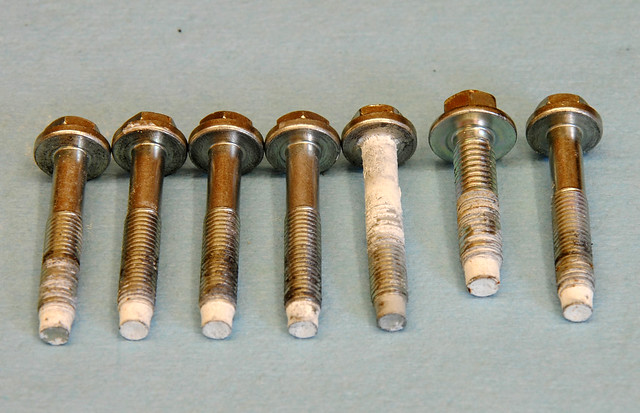
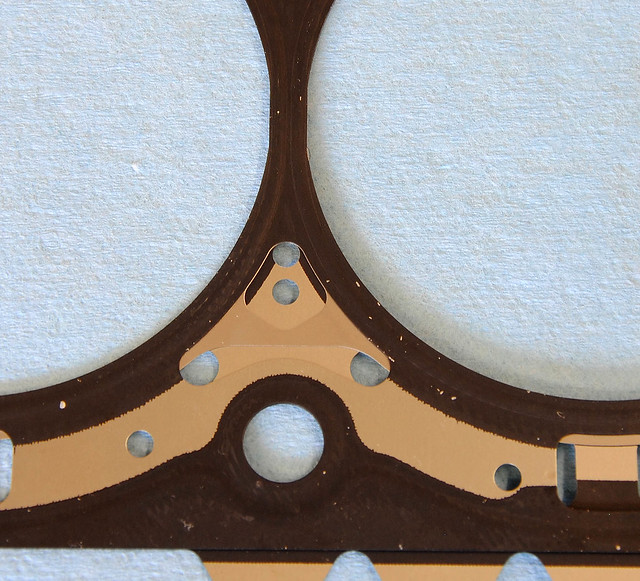
Edited by DCL on Sunday 11th June 22:31
DCL said:
The 2.5L is relatively new variation to the Duratec range and it has a slightly larger big-end journal. This meant that the bearings shells were not available in the up-rated materials when the rods were designed. So this engine, will use the Subaru VP2 shells which happen to be identical in journal diameter. These bearings have a notch, or tang, so the rods have been machined to accommodate them.

The bespoke nature of the rods also gave the opportunity to rethink the factory spec and they have been made slightly longer and the gudgeon pin size has been reduced. This will reduce weight and improve geometry.

The ARP2000 bolts, although no longer my first choice in bolts, where the logical option and are well proven solution.
Pistons next . . .
Any reason for choosing the X beam design over the I?
The bespoke nature of the rods also gave the opportunity to rethink the factory spec and they have been made slightly longer and the gudgeon pin size has been reduced. This will reduce weight and improve geometry.

The ARP2000 bolts, although no longer my first choice in bolts, where the logical option and are well proven solution.
Pistons next . . .
The general thought is that H rods are stiffer (in compression) for a given weight, but tend to weaker in tensile strength (stretching). So most high torque low revving engines would choose an H section - typically turbo applications. In this engine the limiting factor will be mean piston speed, so the tensile strength is more important. In other words the the best tensile strength design has been used.
A four cylinder inline engine is always going to be a compromise when it comes to balance. But it is worth getting the static balance correct as an error from one end of the crank to the other will 'rock', or bend, the crank and that's bad for the main bearings and longevity of the engine.
With this engine (and it's extremely long stroke) I decided it was worth going to the extra effort of balancing it professionally.
So it was off to Midland Balancing Ltd to spend an interesting few hours in their workshop.

Spinning up my crank on their balance rig was straightforward with no bob weights required on an inline 4 cylinder. It proved to be good out the box at 5 grams at 1 cm (less than 0.5 grams at the web), that was good figure! Even more satisfying was that it appeared to be the key-way that was causing the unbalance, and when we fitted the sprocket and pulley it got better. After some light grinding we got it down to 2-3 grams at 1 cm (about as low as we could measure reliably). Then the flywheel was fitted and a small adjustment made to bring it back to same balance.
Following that, the pistons rods, and pins where weighed and mixed and matched to find the best balance. In the end we achieved 0.1 gram between the set without removing material - a truly remarkable figure and praise should go to Omega and Robson for there ability to provide such good matching sets.

Finally we used a rig with precision bearings to measure each end of the rods. All were within 0.5 grams and we felt that it was better to maintain the peened finish than adjust.
This is probably the best balanced set of parts I have ever achieved. Whether that is luck, or just everyone upping their game for this 'early' spec engine, I don't know.
With this engine (and it's extremely long stroke) I decided it was worth going to the extra effort of balancing it professionally.
So it was off to Midland Balancing Ltd to spend an interesting few hours in their workshop.

Spinning up my crank on their balance rig was straightforward with no bob weights required on an inline 4 cylinder. It proved to be good out the box at 5 grams at 1 cm (less than 0.5 grams at the web), that was good figure! Even more satisfying was that it appeared to be the key-way that was causing the unbalance, and when we fitted the sprocket and pulley it got better. After some light grinding we got it down to 2-3 grams at 1 cm (about as low as we could measure reliably). Then the flywheel was fitted and a small adjustment made to bring it back to same balance.
Following that, the pistons rods, and pins where weighed and mixed and matched to find the best balance. In the end we achieved 0.1 gram between the set without removing material - a truly remarkable figure and praise should go to Omega and Robson for there ability to provide such good matching sets.

Finally we used a rig with precision bearings to measure each end of the rods. All were within 0.5 grams and we felt that it was better to maintain the peened finish than adjust.
This is probably the best balanced set of parts I have ever achieved. Whether that is luck, or just everyone upping their game for this 'early' spec engine, I don't know.
With all the parts available, and balancing done, the assembly went ahead without problems. It's all covered in earlier posts, so I won't do it again. The engine started first time.
https://youtu.be/A_jNq4MD9eU
So it was off to Northampton Motorsport for Troy to do his magic. Running it was totally uneventful and the mapping straight forward - basically more fuel needed everywhere.
https://youtu.be/2kph7idDizg
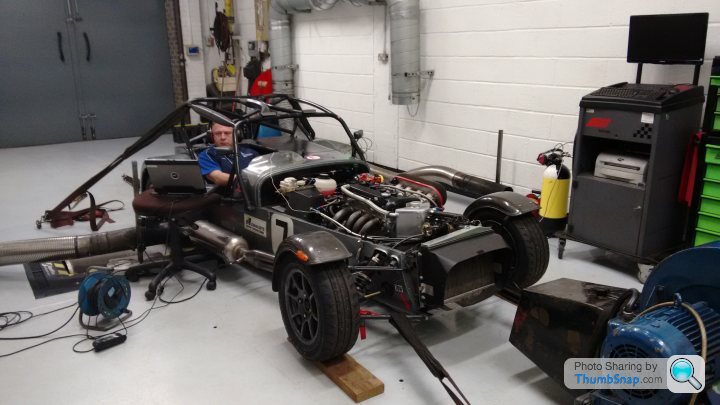
The power runs were keep to conservative RPM levels and raised in stages to 7,500 RPM where we will leave it for the time being. We will go higher, but I want to get some track experience with it before risking the engine for the sake of a few more RPM. Despite the runs seeming a bit subdued (compared to the frantic 2L engine), it gave a healthy 294 BHP which was a shade above what I expected for this RPM. Torque was very good too, reaching over 90% of the theoretical maximum. So good potential and all working well.
The graphs are comparisons to the 2L engine.
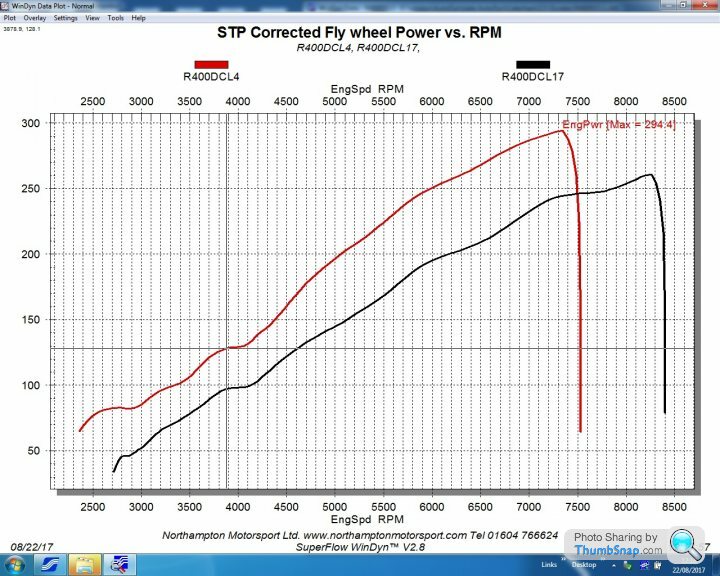

So pleased with the result but still work in progress.
https://youtu.be/A_jNq4MD9eU
So it was off to Northampton Motorsport for Troy to do his magic. Running it was totally uneventful and the mapping straight forward - basically more fuel needed everywhere.
https://youtu.be/2kph7idDizg
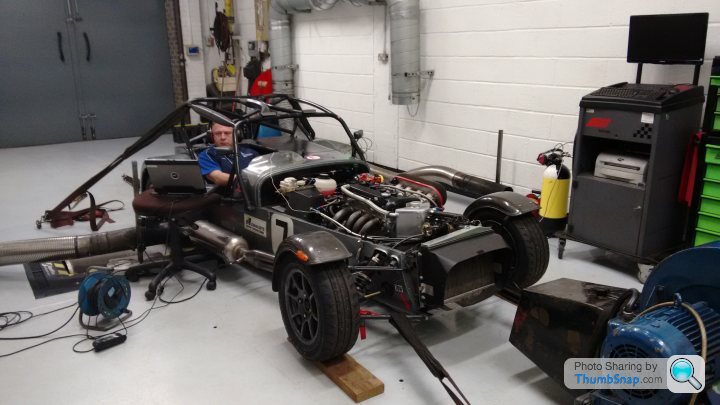
The power runs were keep to conservative RPM levels and raised in stages to 7,500 RPM where we will leave it for the time being. We will go higher, but I want to get some track experience with it before risking the engine for the sake of a few more RPM. Despite the runs seeming a bit subdued (compared to the frantic 2L engine), it gave a healthy 294 BHP which was a shade above what I expected for this RPM. Torque was very good too, reaching over 90% of the theoretical maximum. So good potential and all working well.
The graphs are comparisons to the 2L engine.
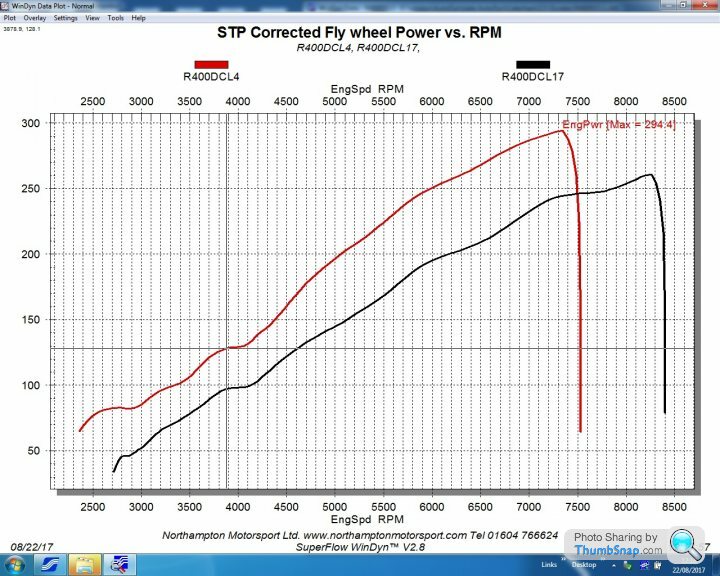

So pleased with the result but still work in progress.
Edited by DCL on Wednesday 23 August 09:42
Well the engine held together for the first couple of events at the weekend.
Knockhil anti-clockwise.
https://youtu.be/zgyMVm7GdJo
Knockhill clockwise.
https://youtu.be/q8qm3ZtZcAw
The car is much easier to drive with a more progressive power delivery and, on road tyres, it delivered PBs almost every time I went out. It finished Second overall out of a field of 40+ cars.
So that concludes this story . . . who mentioned superchargers . . .
Knockhil anti-clockwise.
https://youtu.be/zgyMVm7GdJo
Knockhill clockwise.
https://youtu.be/q8qm3ZtZcAw
The car is much easier to drive with a more progressive power delivery and, on road tyres, it delivered PBs almost every time I went out. It finished Second overall out of a field of 40+ cars.
So that concludes this story . . . who mentioned superchargers . . .
Edited by DCL on Monday 28th August 13:27
With a couple of days to look at the VBox data, it is clear that the car was working exceptionaly well. I thought the extra power would make a difference, but I wasn't prepared for how much easier the wider torque curve made it to drive. And that translated directly into more confidence and better apex speeds. In fact, the combination of both, made it about 1.5 seconds quicker on the 1.3 mile Knockhill circuit. And it is clear there's more there too. The straight delta line showing an improvement everywhere.
The car also weighed 3KG lighter. Now I had to scratch my head about that one as, at most, I could only account for half that (the crank was lighter). I suspect although the engine is 13 mm taller, it is bored out more, and the balance shaft has more of the block casting machined (not in the 2L)
Red 2.5L Blue 2L

The car also weighed 3KG lighter. Now I had to scratch my head about that one as, at most, I could only account for half that (the crank was lighter). I suspect although the engine is 13 mm taller, it is bored out more, and the balance shaft has more of the block casting machined (not in the 2L)
Red 2.5L Blue 2L

Edited by DCL on Tuesday 29th August 14:57
I've taken some time to put together a website to support the Duratec in Detail's Facebook page. For those of you not familiar with the page, it blogs my Duratec engine builds. The site is not intended to replace the Facebook page, but I hope it will provide an index-able resource for those interested in the Duratec.
http://duratecindetail.com/
http://duratecindetail.com/
Gassing Station | Caterham | Top of Page | What's New | My Stuff