New TVR still under wraps!
Discussion
My 2p worth...
Corrosion - if the chassis is only well enough protected for a decade then it is no better than a T car. How difficult would it be to galvanize it in production? Will we have to refurb our chassis every 10-20 years and how difficult will it be. I don't suppose this has been thought about.
Recycled cardboard inners in the composite panels - won't give much resistance to water ingress if the panel is compromised in a small 'accident'. I was under the impression that the cardboard replaced the usual alu honeycomb to keep cost down. How much of a weight advantage do the carbon panels have over the less expensive glass/alu honeycomb ones? Can't be more that a few kgs in total as the glass/alu ones are extremely light and strong and in common use in aircraft. Smacks of a marketing gimmick to me.
T cars were usually about half the price of a similar 911, the current 911 turbo is 145k so the TVR had better be close to half that.
IHMO
Corrosion - if the chassis is only well enough protected for a decade then it is no better than a T car. How difficult would it be to galvanize it in production? Will we have to refurb our chassis every 10-20 years and how difficult will it be. I don't suppose this has been thought about.
Recycled cardboard inners in the composite panels - won't give much resistance to water ingress if the panel is compromised in a small 'accident'. I was under the impression that the cardboard replaced the usual alu honeycomb to keep cost down. How much of a weight advantage do the carbon panels have over the less expensive glass/alu honeycomb ones? Can't be more that a few kgs in total as the glass/alu ones are extremely light and strong and in common use in aircraft. Smacks of a marketing gimmick to me.
T cars were usually about half the price of a similar 911, the current 911 turbo is 145k so the TVR had better be close to half that.
IHMO
Willfin said:
I struggle to see how a jig formed tubular steel chassis can be churned out quickly and by unskilled labour? Welding itself is a certified profession, and it's certainly quite a time consuming process.
Unless it's automated, or labour and materials are managed in the it in time Japanese manufacturing concept then it will be a reletaviley slow but precise process.
I would say that the tubing will be bonded into place, as I have never seen the I-stream technology it is only an educated guess, from my passed experiences making A/C parts from FRP techniques I have acquired over the years in my line of work.Unless it's automated, or labour and materials are managed in the it in time Japanese manufacturing concept then it will be a reletaviley slow but precise process.
http://www.raf.mod.uk/rafwittering/newsweather/ind...
m4tti said:
The carbon fibre with closed cell foam core is incredibly strong.... the panels I've handled before, I hazard a guess that you could even walk across them.
Did they indicate whether these were autoclaved panels or mass vacuum formed pieces.
Auto claves are very expensive, I have only used VAC bags and heat Pads and lamps on A/C part manufacture and repair, these methods are cheaper but still run into the £1000's, but and very effective in pressuring the layers of carbon into the resin and getting the component shape you require.Did they indicate whether these were autoclaved panels or mass vacuum formed pieces.
The carbon and the resin will bond naturally without heat application it will just take longer to achieve this. Heat pads and lamps are used instead of Auto claves to keep costs low. I presume this is what is being adopted for GMD to keep tooling costs down.
The pre- pregnated Carbon will go hard if the role is left out of the re-refrigerator, or you have a power cut as we found out once.

Edited by portzi on Sunday 29th January 12:03
Edited by portzi on Sunday 29th January 12:37
leerdam23 said:
My 2p worth...
Recycled cardboard inners in the composite panels - won't give much resistance to water ingress if the panel is compromised in a small 'accident'. I was under the impression that the cardboard replaced the usual alu honeycomb to keep cost down. How much of a weight advantage do the carbon panels have over the less expensive glass/alu honeycomb ones? Can't be more that a few kgs in total as the glass/alu ones are extremely light and strong and in common use in aircraft. Smacks of a marketing gimmick to me.
This page: http://istreamtechnology.co.uk/1/ipanels.htmlRecycled cardboard inners in the composite panels - won't give much resistance to water ingress if the panel is compromised in a small 'accident'. I was under the impression that the cardboard replaced the usual alu honeycomb to keep cost down. How much of a weight advantage do the carbon panels have over the less expensive glass/alu honeycomb ones? Can't be more that a few kgs in total as the glass/alu ones are extremely light and strong and in common use in aircraft. Smacks of a marketing gimmick to me.
is claiming structural integrity (but with a 3mm glue around the edges???) as the advantage. Weight doesn't seem to be part of their argument. So there doesn't appear to be a rationale for their "paper or paper based" core - so presumably it's cost. But it might be speed: what if the core was formed in the same as the paper core for skeleton doors (strips of paper glued in alternative positions, then pulled apart after the glue sets to form the honeycomb) - this would greatly speed manufacture of the panels themselves. But for speed to be a material driving force, you need volume of production...
Another claimed advantage:
"The process centres on a separate body chassis assembly process, in which pre-painted body panels are delivered to the line after the powertrain, wiring harnesses, brakes and suspension have been fitted directly to the chassis. The body panels are married to the completed chassis near the end of the assembly process, cutting down on paint damage"
Source: Professional Engineering, 6 October 2010.
"The process centres on a separate body chassis assembly process, in which pre-painted body panels are delivered to the line after the powertrain, wiring harnesses, brakes and suspension have been fitted directly to the chassis. The body panels are married to the completed chassis near the end of the assembly process, cutting down on paint damage"
Source: Professional Engineering, 6 October 2010.
dxg said:
leerdam23 said:
My 2p worth...
Recycled cardboard inners in the composite panels - won't give much resistance to water ingress if the panel is compromised in a small 'accident'. I was under the impression that the cardboard replaced the usual alu honeycomb to keep cost down. How much of a weight advantage do the carbon panels have over the less expensive glass/alu honeycomb ones? Can't be more that a few kgs in total as the glass/alu ones are extremely light and strong and in common use in aircraft. Smacks of a marketing gimmick to me.
This page: http://istreamtechnology.co.uk/1/ipanels.htmlRecycled cardboard inners in the composite panels - won't give much resistance to water ingress if the panel is compromised in a small 'accident'. I was under the impression that the cardboard replaced the usual alu honeycomb to keep cost down. How much of a weight advantage do the carbon panels have over the less expensive glass/alu honeycomb ones? Can't be more that a few kgs in total as the glass/alu ones are extremely light and strong and in common use in aircraft. Smacks of a marketing gimmick to me.
is claiming structural integrity (but with a 3mm glue around the edges???) as the advantage. Weight doesn't seem to be part of their argument. So there doesn't appear to be a rationale for their "paper or paper based" core - so presumably it's cost. But it might be speed: what if the core was formed in the same as the paper core for skeleton doors (strips of paper glued in alternative positions, then pulled apart after the glue sets to form the honeycomb) - this would greatly speed manufacture of the panels themselves. But for speed to be a material driving force, you need volume of production...
dxg said:
Another claimed advantage:
"The process centres on a separate body chassis assembly process, in which pre-painted body panels are delivered to the line after the powertrain, wiring harnesses, brakes and suspension have been fitted directly to the chassis. The body panels are married to the completed chassis near the end of the assembly process, cutting down on paint damage"
Source: Professional Engineering, 6 October 2010.
The interesting aspect of that is that it suggests the concept of 'chassis for life'. When you get bored of how your car looks you can return it to have a different set of panels fitted. "The process centres on a separate body chassis assembly process, in which pre-painted body panels are delivered to the line after the powertrain, wiring harnesses, brakes and suspension have been fitted directly to the chassis. The body panels are married to the completed chassis near the end of the assembly process, cutting down on paint damage"
Source: Professional Engineering, 6 October 2010.
DonkeyApple said:
dxg said:
Another claimed advantage:
"The process centres on a separate body chassis assembly process, in which pre-painted body panels are delivered to the line after the powertrain, wiring harnesses, brakes and suspension have been fitted directly to the chassis. The body panels are married to the completed chassis near the end of the assembly process, cutting down on paint damage"
Source: Professional Engineering, 6 October 2010.
The interesting aspect of that is that it suggests the concept of 'chassis for life'. When you get bored of how your car looks you can return it to have a different set of panels fitted. "The process centres on a separate body chassis assembly process, in which pre-painted body panels are delivered to the line after the powertrain, wiring harnesses, brakes and suspension have been fitted directly to the chassis. The body panels are married to the completed chassis near the end of the assembly process, cutting down on paint damage"
Source: Professional Engineering, 6 October 2010.
HarryW said:
DonkeyApple said:
dxg said:
Another claimed advantage:
"The process centres on a separate body chassis assembly process, in which pre-painted body panels are delivered to the line after the powertrain, wiring harnesses, brakes and suspension have been fitted directly to the chassis. The body panels are married to the completed chassis near the end of the assembly process, cutting down on paint damage"
Source: Professional Engineering, 6 October 2010.
The interesting aspect of that is that it suggests the concept of 'chassis for life'. When you get bored of how your car looks you can return it to have a different set of panels fitted. "The process centres on a separate body chassis assembly process, in which pre-painted body panels are delivered to the line after the powertrain, wiring harnesses, brakes and suspension have been fitted directly to the chassis. The body panels are married to the completed chassis near the end of the assembly process, cutting down on paint damage"
Source: Professional Engineering, 6 October 2010.
HarryW said:
Here's an interesting ppt including details on the GMD iStream CF composite panels, not sure about the graph on page 17 that shows the strength exceeds the others but appears to show total collapse occurs sooner on the compressibility scale... https://www.lbcg.com/media/downloads/events/545/fr...
Really interesting. As is the tub on the last slide. Do we know what that's from? Looks like it's for something mid or rear engined, though...DonkeyApple said:
Something I've just remembered about the GM design, which I had forgotten but found interesting at the time, was I asked why the tubing was so large and had it explained that it was to allow the tubes to be made of any material type by making them thicker or thinner but always retaining the external diameter so that you never had to change the design of the chassis. I don't think it is relevant to TVR but I just found it such an obvious and clever little solution.
Does anyone have any more on this, or even a source? Would be very helpful for something I'm working on at the moment...dxg said:
HarryW said:
Here's an interesting ppt including details on the GMD iStream CF composite panels, not sure about the graph on page 17 that shows the strength exceeds the others but appears to show total collapse occurs sooner on the compressibility scale... https://www.lbcg.com/media/downloads/events/545/fr...
Really interesting. As is the tub on the last slide. Do we know what that's from? Looks like it's for something mid or rear engined, though...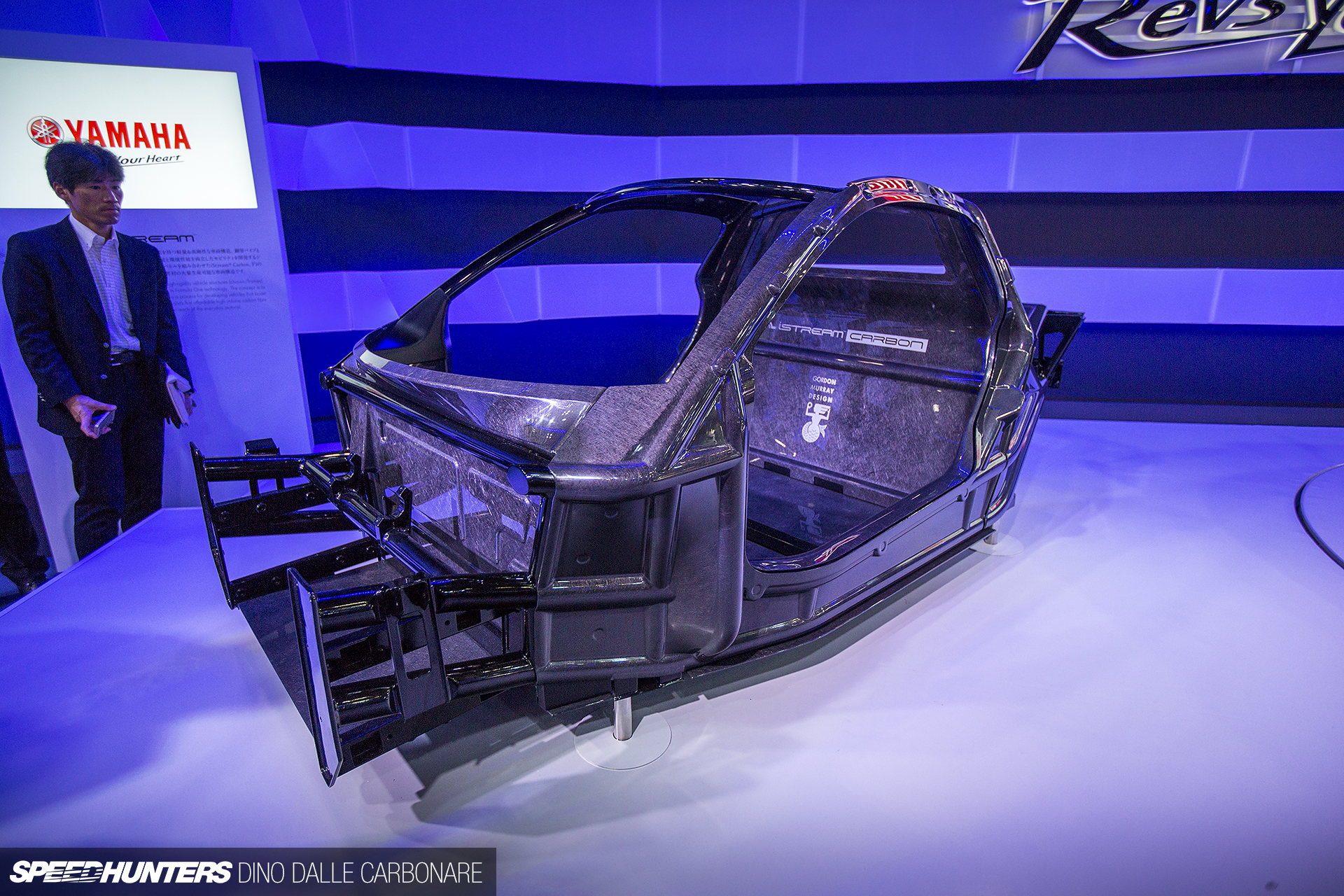
It's from that Yamaha prototype they did.
What's also interesting about that photo is that I think it shows two types of panel. The structural ones visible above and what must be the painted cladding ones offered up at the end of the production line...
bennno said:
RichB said:
urely an observation but typically someone considering a Mustang would not even look at a TVR and vice versa. They are poles apart. All MO of course.
Not sure I agree with that, have bought several new TVR's previously and loved the individuality, grunty performance, noise and value for money. I didn't like the ownership 'niggles', which occurred on multiple variants of Griff, Cerb and T350 owned. I now have a Mustang GT with a Roush exhaust. Its an absolute blast, very close in spirit to my Griff, but mix in everyday reliable. To add it cost £3K less than the Griffith 500 I bought new 17 years ago.
Personally a TVR would need to be an ultra quick, lightweight, spaceframe chassis, coyote engined, no frills, roadster at sub £50k to really appeal.
Bennno
HarryW said:
Here's an interesting ppt including details on the GMD iStream CF composite panels, not sure about the graph on page 17 that shows the strength exceeds the others but appears to show total collapse occurs sooner on the compressibility scale... https://www.lbcg.com/media/downloads/events/545/fr...
The interesting slide that explains everything is the 'development matrix' slide - this says it's made out of plutonium. 
I was thinking about this earlier, and there's nothing on the market today like the TVR of old
and I mean this in the good way when everything on the car was working properly
what can you buy thats light ( sub 1200kg)
powerful (400bhp +)
rear wheel drive
tight responsive handling
minimum of frills
good looking inside and out
small enough for a UK b road blat
Ok there's lotus as a possible but its not a TVR
closest I can think of as a modern equivalent is a BMW Z3 or a tuned up Gt86?
so if they make a modern Sagaris / T350 then I'd say they've cracked it
and I mean this in the good way when everything on the car was working properly
what can you buy thats light ( sub 1200kg)
powerful (400bhp +)
rear wheel drive
tight responsive handling
minimum of frills
good looking inside and out
small enough for a UK b road blat
Ok there's lotus as a possible but its not a TVR
closest I can think of as a modern equivalent is a BMW Z3 or a tuned up Gt86?
so if they make a modern Sagaris / T350 then I'd say they've cracked it
350Matt said:
I was thinking about this earlier, and there's nothing on the market today like the TVR of old
and I mean this in the good way when everything on the car was working properly
what can you buy thats light ( sub 1200kg)
powerful (400bhp +)
rear wheel drive
tight responsive handling
minimum of frills
good looking inside and out
small enough for a UK b road blat
Ok there's lotus as a possible but its not a TVR
closest I can think of as a modern equivalent is a BMW Z3 or a tuned up Gt86?
so if they make a modern Sagaris / T350 then I'd say they've cracked it
although you've missed out the value for money aspect and I mean this in the good way when everything on the car was working properly
what can you buy thats light ( sub 1200kg)
powerful (400bhp +)
rear wheel drive
tight responsive handling
minimum of frills
good looking inside and out
small enough for a UK b road blat
Ok there's lotus as a possible but its not a TVR
closest I can think of as a modern equivalent is a BMW Z3 or a tuned up Gt86?
so if they make a modern Sagaris / T350 then I'd say they've cracked it

Gassing Station | General TVR Stuff & Gossip | Top of Page | What's New | My Stuff