Water pipe - 3.6 SP6
Discussion
glow worm said:
As a DeLorean specialist I guess you must know all about corrosion 
Well I wasn't going to mention it... 
The DeLorean has aluminium pipes which were originally rubber mounted, and I've opened cooling systems and had heads off cars with 20+ year old coolant to find them as clean as a whistle inside.
On chassis corrosion, it's much like TVR with body-off restorations becoming commonplace. Hot-dip-galvanising followed by a powdercoat has become the preferred approach there.
Incognegro said:
My last post didnt show as meant so deleted. but all this agro from changing to stainless I thought they were meant to make life easier?
Im thinking I may learn to love the rust look rather than open a new can of corroding worms lol
Huh.... Look at the coolant you have, it's life expectancy and when it was last changed. The biggest problem with aluminium heads won't be the electrolytic corrosion cell but the scale that builds up when people chuck water in, which reduces the cooling capacity. Im thinking I may learn to love the rust look rather than open a new can of corroding worms lol
Change your coolant annually and this topic dies.
Edited by m4tti on Thursday 4th December 21:16
FFS here we go again with the old water coolant drama. Let's go over how water has the best cooling coefficient but has poor anti corrosion properties due to to all the natural minerals etc etc. Then someone else can chirp up and say how good products like Redline Water Wetter is because it doesn't have the high oxygen content of water so you don't get the hot spots from air bubbles and the over all temperature stays lower.
Failing that we could just use the standard recommended coolant like the rest of the world seems to cope with in their cars then we could get on with using them as intended.
Failing that we could just use the standard recommended coolant like the rest of the world seems to cope with in their cars then we could get on with using them as intended.
Stunned Monkey said:
An electrochemical cell is created through electrical connection of dissimilar conductors in the presence of an electrolyte. If this happens, and without the presence of corrosion inhibitors, the most active metal on the galvanic scale will corrode.
[img] http://www.nstcenter.biz/writeImages/NavyCommunity... [/img]
[img] http://www.nstcenter.biz/writeImages/NavyCommunity... [/img]
Stunned Monkey said:
Replacing them with 304 stainless (which is quite a long way up the scale) WILL promote corrosion of the engine if the coolant is not maintained.
Sorry to correct you here. This list of metallic materials according to their electrochemical potential does not account for passivation of the aluminium, only for the element itself. Aluminium per se is very electronegative, means it corrodes readily in watery conditions (and promotors like chlorides added).But Aluminium (and its alloys) builds up very stable oxide/hydroxide scales which protect ths base material beneath elevating the electropotential of Aluminium. Taking this into account aluminium and stainless steels get very close in this "real life situation" list. Therefore you use stainless bolts in aluminium components because it pairs very well, if aluminium bolts cannot be selected due to strength issues.
I would agree however, that also atmospheric corrosion (ouside wall of the tube) has to be looked at. But also corrosion-erosion and other flow induced phenomena from the inside due to coolant flow.
RobertoBlanco said:
Sorry to correct you here. This list of metallic materials according to their electrochemical potential does not account for passivation of the aluminium, only for the element itself.
I'd be really grateful if you could link me to literature on this as I'd like to put this to bed once and for all? I've now learned a bit about passivating, and based on that tiny bit of research, I'm throwing this back to you because, according to Wikipedia's entry on passivation, while it is true that pure Al will generate its own effective protective layer, "[surface oxidation of] aluminium alloys ... offers little protection against corrosion." and is the reason why we deliberately apply external protection like anodising precisely because it is an electrical insulator.
Most of the rest of the references I'm finding relate to real-world applicaiton. One interesting example is the following:
http://www.bssa.org.uk/topics.php?article=89
It suggests that relative surface areas play a large part in this process. I wouldn't like to guess that ALL the pipes' internal area is insignificant relative to that of the engine. But I rest easy that the copper-slip I applied to my A4 marine grade valve cover bolts probably wasn't necessary

Stunned Monkey said:
RobertoBlanco said:
Sorry to correct you here. This list of metallic materials according to their electrochemical potential does not account for passivation of the aluminium, only for the element itself.
I'd be really grateful if you could link me to literature on this as I'd like to put this to bed once and for all? I've now learned a bit about passivating, and based on that tiny bit of research, I'm throwing this back to you because, according to Wikipedia's entry on passivation, while it is true that pure Al will generate its own effective protective layer, "[surface oxidation of] aluminium alloys ... offers little protection against corrosion." and is the reason why we deliberately apply external protection like anodising precisely because it is an electrical insulator.
Most of the rest of the references I'm finding relate to real-world applicaiton. One interesting example is the following:
http://www.bssa.org.uk/topics.php?article=89
It suggests that relative surface areas play a large part in this process. I wouldn't like to guess that ALL the pipes' internal area is insignificant relative to that of the engine. But I rest easy that the copper-slip I applied to my A4 marine grade valve cover bolts probably wasn't necessary

boats and boat engines have anodes, which are much lower nobility, but this still does not stop 100%
for me is a No
Ok good antifreeze will reduce this massively, but why go there
Walford said:
There are lots of fittings on my (or any) boat that have stainless steel and aluminium, the SS stays perfect and the ali rots away
boats and boat engines have anodes, which are much lower nobility, but this still does not stop 100%
for me is a No
Ok good antifreeze will reduce this massively, but why go there
Ok, when talking about marine applications in salt or fresh water, nothing really helps besides going very high alloyed or plastic. I was talking about atmospheric application, splash water use or in controlled environments like with coolant. Underbolt rot is also an issue, when we are talking about crevice corrosion. Also concentration of anions (halides like chloride)is a factor, also under scales/fouling when not rinsed/flushed for longer periods of time. boats and boat engines have anodes, which are much lower nobility, but this still does not stop 100%
for me is a No
Ok good antifreeze will reduce this massively, but why go there
You also have to take into account area ratios of anode and cathode. You need to get the anode sigbificantly bigger than the cathode. There is no universal sloution you can take off a few charts or diagrams. This really belongs to engineering realm.
Talking about cathodic protection with magnesium anodes in sea water is also a different story.
Trying to stop corrosion of metallic materials is like trying to stop aging of people, really. The question is really how much you can slow things down. So we are talking about mitigation, not immunizing. If you want to stay away from corrosion issues, you really have to either pick a material that is completely unaffected in your environment or change the environment, so that your material is not affected anymore.
Stunned Monkey said:
I'd be really grateful if you could link me to literature on this as I'd like to put this to bed once and for all?
I've now learned a bit about passivating, and based on that tiny bit of research, I'm throwing this back to you because, according to Wikipedia's entry on passivation, while it is true that pure Al will generate its own effective protective layer, "[surface oxidation of] aluminium alloys ... offers little protection against corrosion." and is the reason why we deliberately apply external protection like anodising precisely because it is an electrical insulator.
Most of the rest of the references I'm finding relate to real-world applicaiton. One interesting example is the following:
http://www.bssa.org.uk/topics.php?article=89
It suggests that relative surface areas play a large part in this process. I wouldn't like to guess that ALL the pipes' internal area is insignificant relative to that of the engine. But I rest easy that the copper-slip I applied to my A4 marine grade valve cover bolts probably wasn't necessary
BSSA is a good place to start. For stainless steels you could also tryI've now learned a bit about passivating, and based on that tiny bit of research, I'm throwing this back to you because, according to Wikipedia's entry on passivation, while it is true that pure Al will generate its own effective protective layer, "[surface oxidation of] aluminium alloys ... offers little protection against corrosion." and is the reason why we deliberately apply external protection like anodising precisely because it is an electrical insulator.
Most of the rest of the references I'm finding relate to real-world applicaiton. One interesting example is the following:
http://www.bssa.org.uk/topics.php?article=89
It suggests that relative surface areas play a large part in this process. I wouldn't like to guess that ALL the pipes' internal area is insignificant relative to that of the engine. But I rest easy that the copper-slip I applied to my A4 marine grade valve cover bolts probably wasn't necessary

nickel institute: http://www.nickelinstitute.org/~/link.aspx?_id=1C9...
Outokumpu: http://www.outokumpu.com/en/tools-and-downloads/pr...
Sandvik: http://www.smt.sandvik.com/en/materials-center/
Also other stainless steel manufacturers offer great databases. Also wehn searching for literature you could always try google scholar: http://scholar.google.de/
Yiou might get better results than with regular google
I could look up some references, but not have them handy at the moment.
Aluminium covers itself with its corrosion pruducts - Aluminium oxide and hydroxide, based on the environment the material is in. There layer are to some extend more ceramic than metallic. You can also artificially build up more resistant, thicker and more compact oxide layers with anodizing aluminium (also coloured!). With sealing anodized aluminium you can better corrosion resistance even more. Anodized aluminium is highly resistant to normal wet applications, therefore you will find a broad range of different porducts for cars, bicycles, motorbikes and such.
For publications referring to aluminium I would try the manufacturers first like alcoa or norsk-hydro. Most of the really good publications you'd need access to knovel, sciencedirect, MTI and such knowledgebases.
Side note: Copper slip for A4 bolting would not be necessary to protect the thread from water ingress or so. But if we are talking about stainless steel threading and sstainless bolting you have to make sure to use a lubricant of sorts like machine oil, copper slip or graphite to prevent fretting.
Other than than that, make sure watrey phases do not stagnate on any metallic material, rinse away road salt and try to avoid galvanic couples and small gaps/crevices as much as possible, if you can't awoid watery conditions. This advice sure is not exaustive concerning options, but a good start.
Incognegro said:
My ACT stainless water pipes arrived today for my sp6 Cerbera so I'll be upgrading the rusty originals in a week at 6k service. Collings been great ever since FTing ACT silicone hoses but my advisory due to poor cosmetics was perhaps the stainless pipe upgrade so getting that done!
Nice to read good things about them
Have also recently ordered myself a set of hoses and all the pipes, just waiting for them to arrive !!Nice to read good things about them

dave tvr said:
Incognegro said:
My ACT stainless water pipes arrived today for my sp6 Cerbera so I'll be upgrading the rusty originals in a week at 6k service. Collings been great ever since FTing ACT silicone hoses but my advisory due to poor cosmetics was perhaps the stainless pipe upgrade so getting that done!
Nice to read good things about them
Have also recently ordered myself a set of hoses and all the pipes, just waiting for them to arrive !!Nice to read good things about them

Firstly I would like to reiterate the points made earlier that a) the anti-corrosions properties of good coolant will prevent galvanic corrosion – but this protection degrades over time and b) you can permanently avoid any effects by electrically insulating the stainless pipework from the chassis.
Sorry Roberto, but I have still yet to find anything to back up your assertion that the natural oxide layer will protect the aluminium castings, instead I’ve read multiple resources stating that the protection against galvanic corrosion offered by the natural oxide layer of cast aluminium alloy is poor (but for pure aluminium is good). If you can point me to specific articles which contradict this, I’d be very grateful.
Martin
Sorry Roberto, but I have still yet to find anything to back up your assertion that the natural oxide layer will protect the aluminium castings, instead I’ve read multiple resources stating that the protection against galvanic corrosion offered by the natural oxide layer of cast aluminium alloy is poor (but for pure aluminium is good). If you can point me to specific articles which contradict this, I’d be very grateful.
Martin
Stunned Monkey said:
Sorry Roberto, but I have still yet to find anything to back up your assertion that the natural oxide layer will protect the aluminium castings, instead I’ve read multiple resources stating that the protection against galvanic corrosion offered by the natural oxide layer of cast aluminium alloy is poor (but for pure aluminium is good). If you can point me to specific articles which contradict this, I’d be very grateful.
Martin
Martin, first of all your info is correct. Pure aluminium ~99.5% has the best corrosion resistance, because the oxide layers are purely made of aluminiumoxides. If you add alloying elements like silicone, magnesium, manganese and such to enhance mechnanical properties, the oxide layers are of a mixed type. This causes mismatching of base material atoms and oxide layer atoms causing stresses inside the oxide layer and therefore instability So natural oxide layers of aluminium alloys are less stable than of pure aluminium. Pure aluminium however is quite soft, so not exactly a technical material for the industry.Martin
With anodizing the alloys you get a very rigid, compact oxide layer also of ceramic nature, i.e. less conductive.
Funny enough not all corrosive mechanisms are fully understood to date, so i cannot give you an exhaustive explanation.
Practical electrochemical series for different media and materials are kind of hard to come by. Mostly they are for seawater, so not representative for other watery conditions, but perhaps a first indication.
I found some evidence on a quick search in "Alec Groysman - Corrosion for Everybody (ISBN 978-90-481-3476-2)
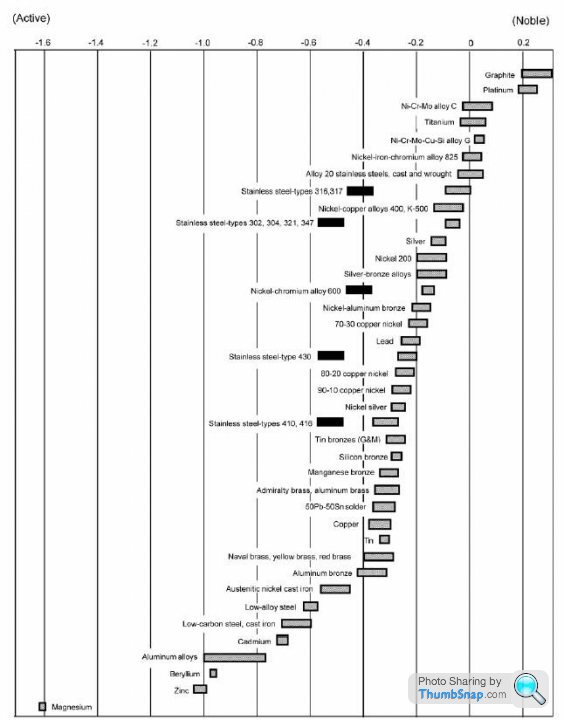
So 300series stainless steels and aluminium alloys do not really overlap, but aren't far apart. Since seawater is very conductive due to high salt concentration ~3.5% chlorides, you can assume that tap water or rainwater is less conductive due to less halides/chlorides. Hence the situation would become less severe. Even more so in inhibited waters like coolants.
And following a passage in "C. Vargel - Corrosion of Aluminium"
"Although there is a great difference in potential between stainless steel and aluminium
alloys, in the order of 650 mV, it is unusual to see galvanic corrosion on aluminium in contact with stainless steel. Aluminium alloy components are often assembled using stainless steel bolts, e.g. in metallic fittings."
If you are unsure you could always use insulation between bolt and plate, for example insulation washers. This is also very common in some applications. BTW anodized aluminium washers are sometimes used for such insulation functions, so this should give you a hint on the conductivity of anodized aluminium alloys.
I couldn't come up with better references in a reasonable amount of time, sorry.
BTW I'm a professional materials and corrosion engineer with a PHD in surface technology & corrosion, so I'm not a beginner in this field. Although I'm currently more focussed on steels due to my work, I previously studied corrosion of magnesium and aluminum alloys in corrosive atmospheres with or without mechanical loading.
If you believe me or not is up to you. ;-)
RobertoBlanco said:
And following a passage in "C. Vargel - Corrosion of Aluminium"
"Although there is a great difference in potential between stainless steel and aluminium
alloys, in the order of 650 mV, it is unusual to see galvanic corrosion on aluminium in contact with stainless steel. Aluminium alloy components are often assembled using stainless steel bolts, e.g. in metallic fittings."
Thanks for that quote, however as noted above in one of my references, surface area is key to combining dissimilar metals - if the surface area of the more active conductor is significantly larger than the less active (eg stainless bolts holding an aluminium panel), there should be no problem, however using aluminium rivets (or indeed zinc plated bolts) to hold a stainless panel is a bad idea - something that hadn't crossed my mind until reading up on this subject. As noted above, I would not like to rely on the internal surface area of the pipework being that much less than the internal surface area of the engine's cooling jacket. Nor should we rely on coolant quality as that's bad engineering."Although there is a great difference in potential between stainless steel and aluminium
alloys, in the order of 650 mV, it is unusual to see galvanic corrosion on aluminium in contact with stainless steel. Aluminium alloy components are often assembled using stainless steel bolts, e.g. in metallic fittings."
Going back to my original post, would you not agree that aluminium is the ideal material for these replacement pipes?
Gassing Station | Speed Six Engine | Top of Page | What's New | My Stuff