Unusual job on the bench today
Discussion
Thanks all.
Ive got a big retipping job to do over the next couple of weeks so i'll take some pics and you can see how thats done. A lot of people think that jewellers / goldsmiths just 'stick' bits of gold where needed and hey presto. When you see the retipping process you'll see where your money goes. Took me the best part of 5 years to get a grip of tipping.
Ive got a big retipping job to do over the next couple of weeks so i'll take some pics and you can see how thats done. A lot of people think that jewellers / goldsmiths just 'stick' bits of gold where needed and hey presto. When you see the retipping process you'll see where your money goes. Took me the best part of 5 years to get a grip of tipping.
Revs_Addiction said:
Great thread, great skills. How much would that bracelet be worth?!
Thats a tough question to answer, really depends on the quality of the stones and where you are buying it. In this case the stones were roughly 0.12ct each (centre stones slightly larger, maybe 0.15ct) and VVS G/H quality. The item was being rebuilt for one the souths most prestigious jewellers and it was bought there as new a couple of years back. If i wanted to make one today I worked it out that it'd cost me £10k to £12k in materials alone (trade prices). So once my labour and consumables are factored in, the item moved to a retailer, probably a high class of jewellers so big mark up, I'd say the customer could be looking at anything over £20k.
I don't have the footfall / diary of well suited customers to sell these to myself (wish i did) but every so often you do get asked to make something like this for the trade.
ALawson said:
I appreciate the workmanship but don't like the orange and green number.
Your wife's ring on the other hand looks great!
Get some moisturiser on those hands!
The Fire Opal and Emerald ring is definitely an item that very few people could appreciate / have the foresight for. The good thing is that she is exactly the sort of person to carry it off and i doff my hat to her for being so excellent and different. Your wife's ring on the other hand looks great!
Get some moisturiser on those hands!
Its jobs like that which give me enjoyment in my work. The day to day stuff is really really boring and i hate 85% of what i do. The buzz is in seeing the faces of those 15% when they turn up to collect their items. Whether it be a simple maintenance job or a full custom piece its those few private customers that give the satisfaction in my work.
Glad you like the theory behind it all.
Ref the wifes ring. She loves it. Its not an everyday ring with Tanzanite being quite soft, but she does enjoy showing it off at work when new customers come in to see what we do.
My hands are way beyond moisturising point! lol
NeMiSiS said:
Excellent Saturday morning read.
The ring you made for your wife should put you in the good books for a while.
The rescued bracelet looked like scrap, how you re-place/re-weld tiny hooks and pins to make a new hinge is an art form.
I've noticed one downside to your profession, you seem to be wearing your fingers out.
Thanks mate. The ring you made for your wife should put you in the good books for a while.
The rescued bracelet looked like scrap, how you re-place/re-weld tiny hooks and pins to make a new hinge is an art form.
I've noticed one downside to your profession, you seem to be wearing your fingers out.

The loops and pins are quite easy to do actually, the difficulty is in making sure they are all level. If they are out at all, or the pins / loops too heavy a gauge the bracelet won't lie flat. Its just something that takes time to get right.
Once you see the claw work on the upcoming retipping job you'll see the stress of working on a tiny scale. I do retipping on a daily basis but this one will take me a couple of weeks to find time for.
Ref the fingers. I often wear them through the top layer and the best cure is superglue. Just dab it over the spots where its bleeding or nearly worn through and hey presto, you've got another 5 - 10 mins of use of out of them before a reglue is needed. Its a result of buffing rings with fine emery paper. The paper we used to get (dry stuff) was pretty gentle on the fingers and i had very few issues but since 2010 the main stockists are only supplying wet and dry paper of the same grade which is much stiffer. As a result it rubs your fingers more when on the spindle. You dont even know its worn through your flesh until the paper goes red. Perks of the job!
I did promise a 'claw job' post this month.
Its not the one I'd originally planned on, owing to it being a very busy month and not having time to photograph and do the work (cannot complain at being busy) and me suffering from a fairly draining / all-encompassing stomach issue that is currently under investigation (can complain), but it does demonstrate the processes involved.
Take one pretty worn out and old sapphire and diamond ring. Its a very old fashioned item and has a hand carved construction that we have to maintain.
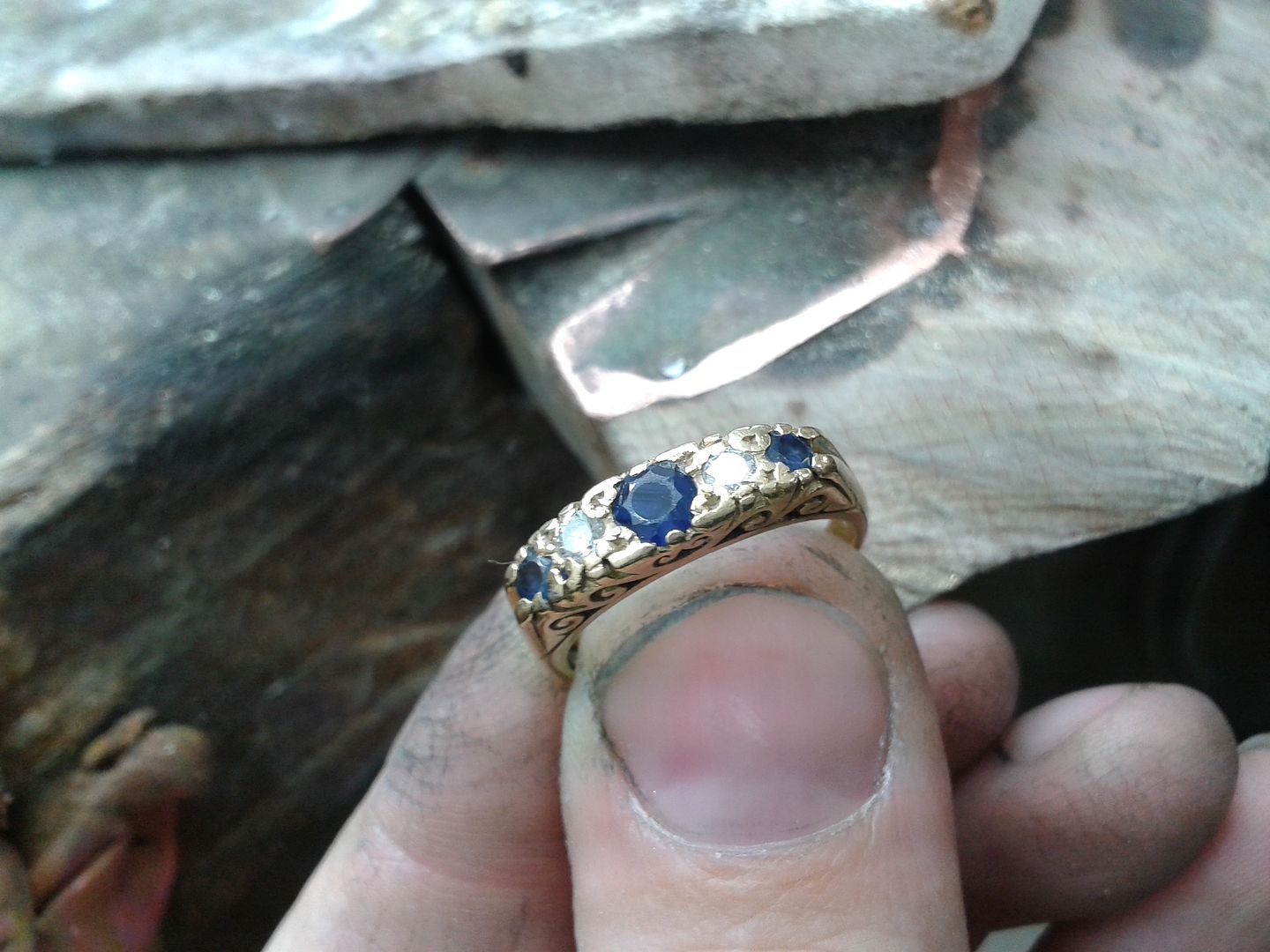
Note the 8 x missing small diamonds from between the main stones. We will replace these as part of the process:
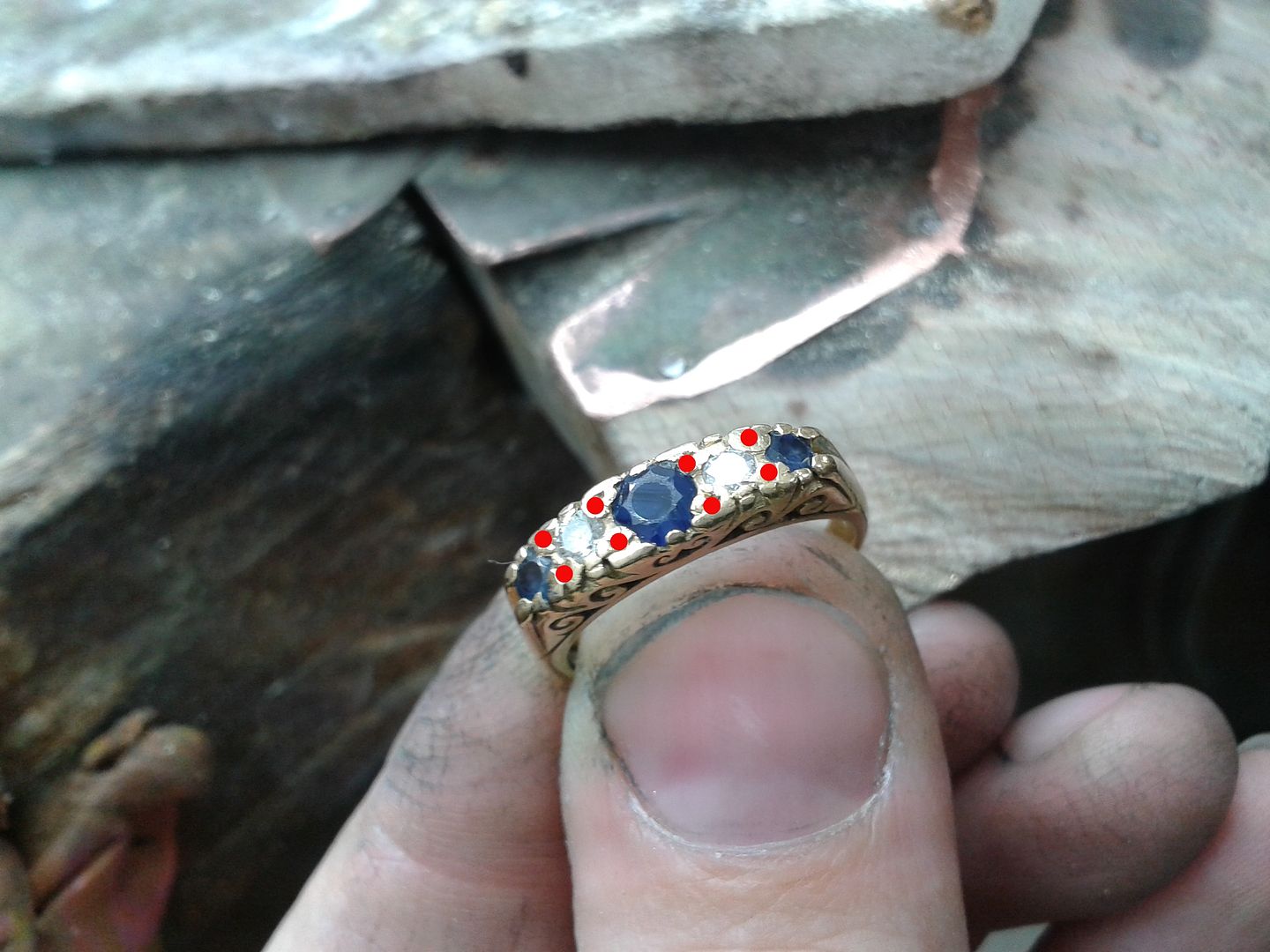
You can see from the picture here the condition of the sapphires. They are pretty worn and abraded. In some circumstances we'd have these removed and replaced or re-polished by a lapidary but the customer wants to maintain the 'used' look.... so they stay.
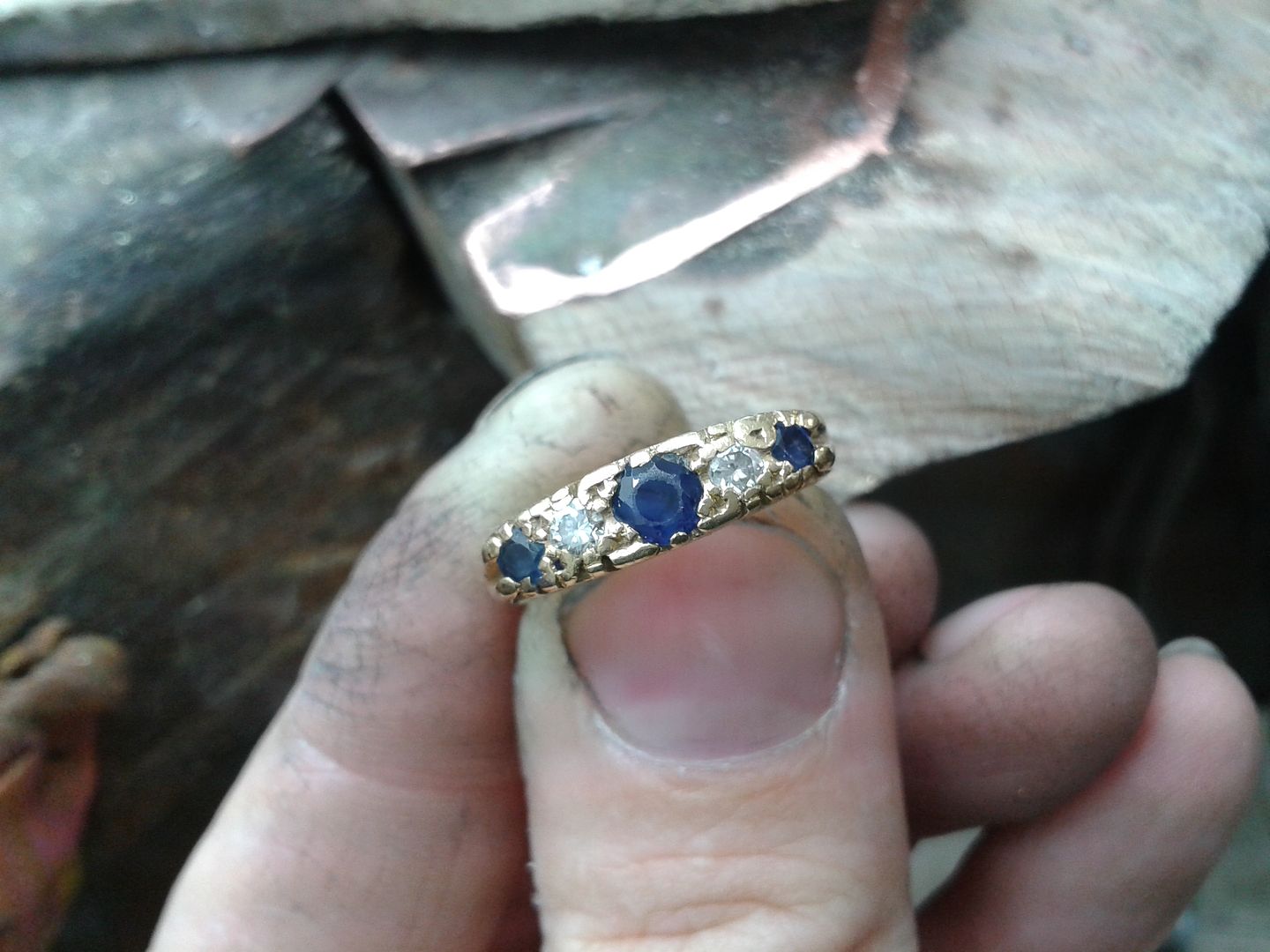
So, first job is to get the missing diamonds back in place. Here i have drilled the 8 x settings ready to take the new stones. They are only very small but do accent the other stones pretty well.
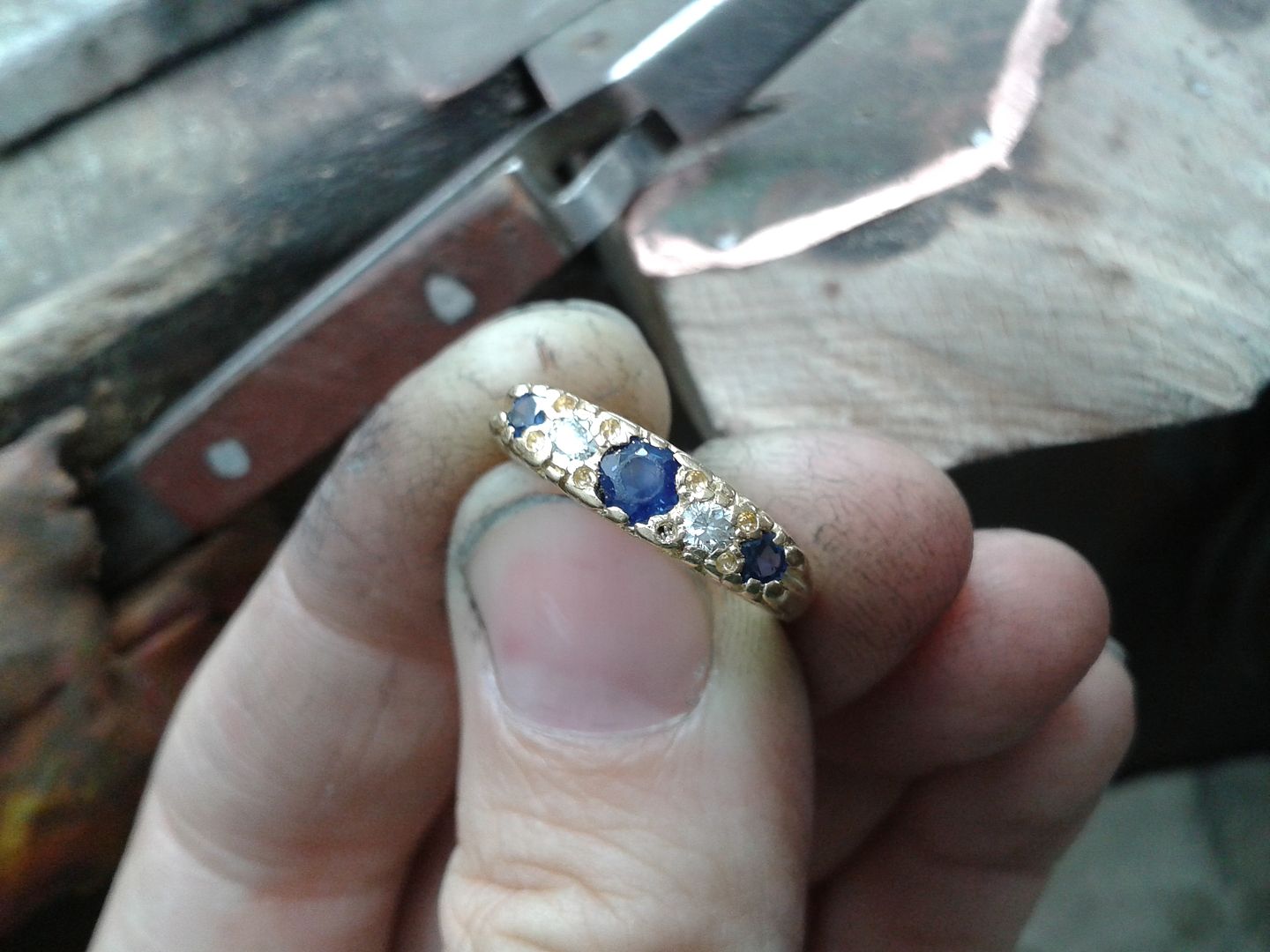
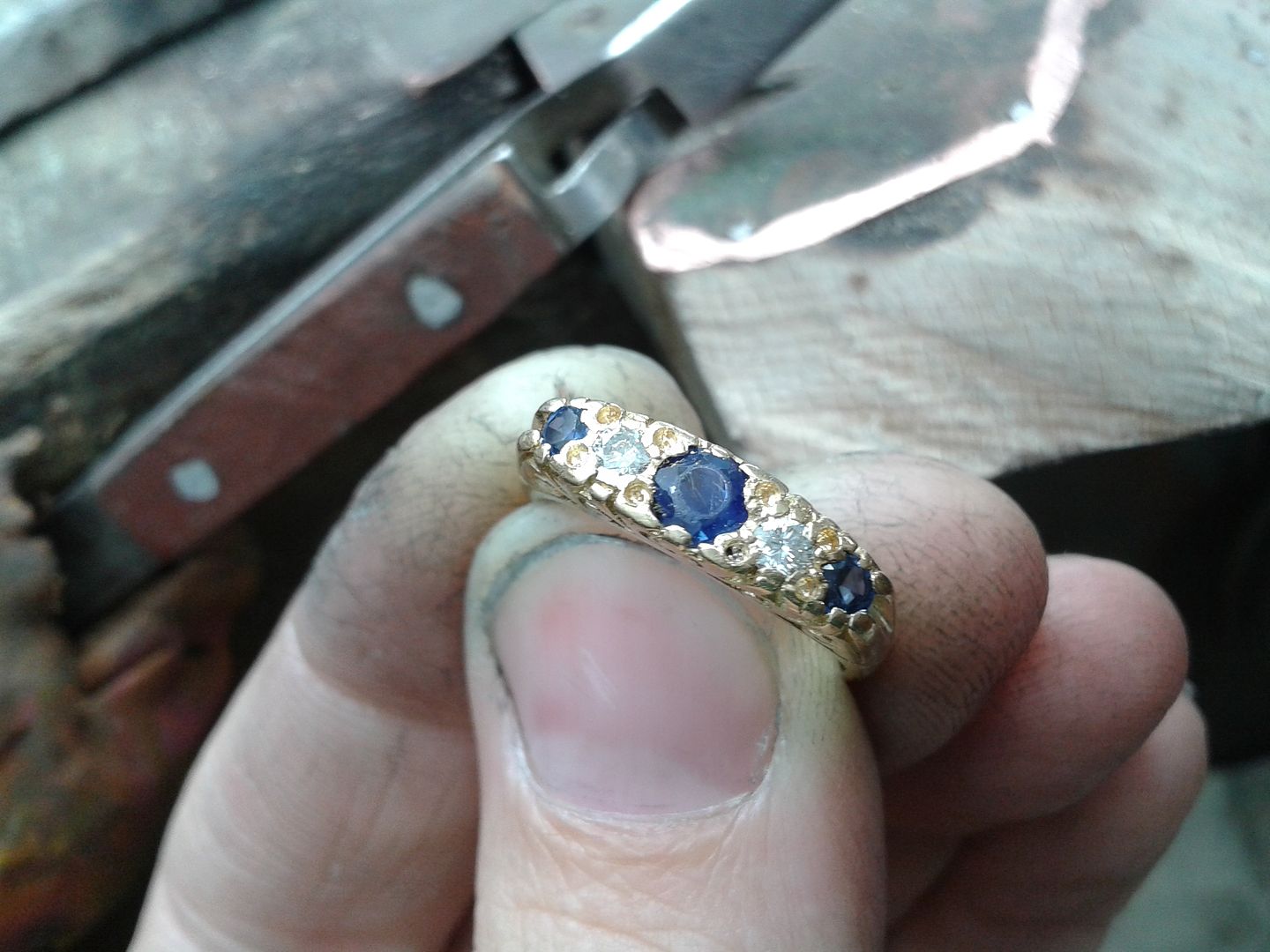
Apologies for no 'setting' pic but this is the 8 diamonds now set and ready for other work to start.
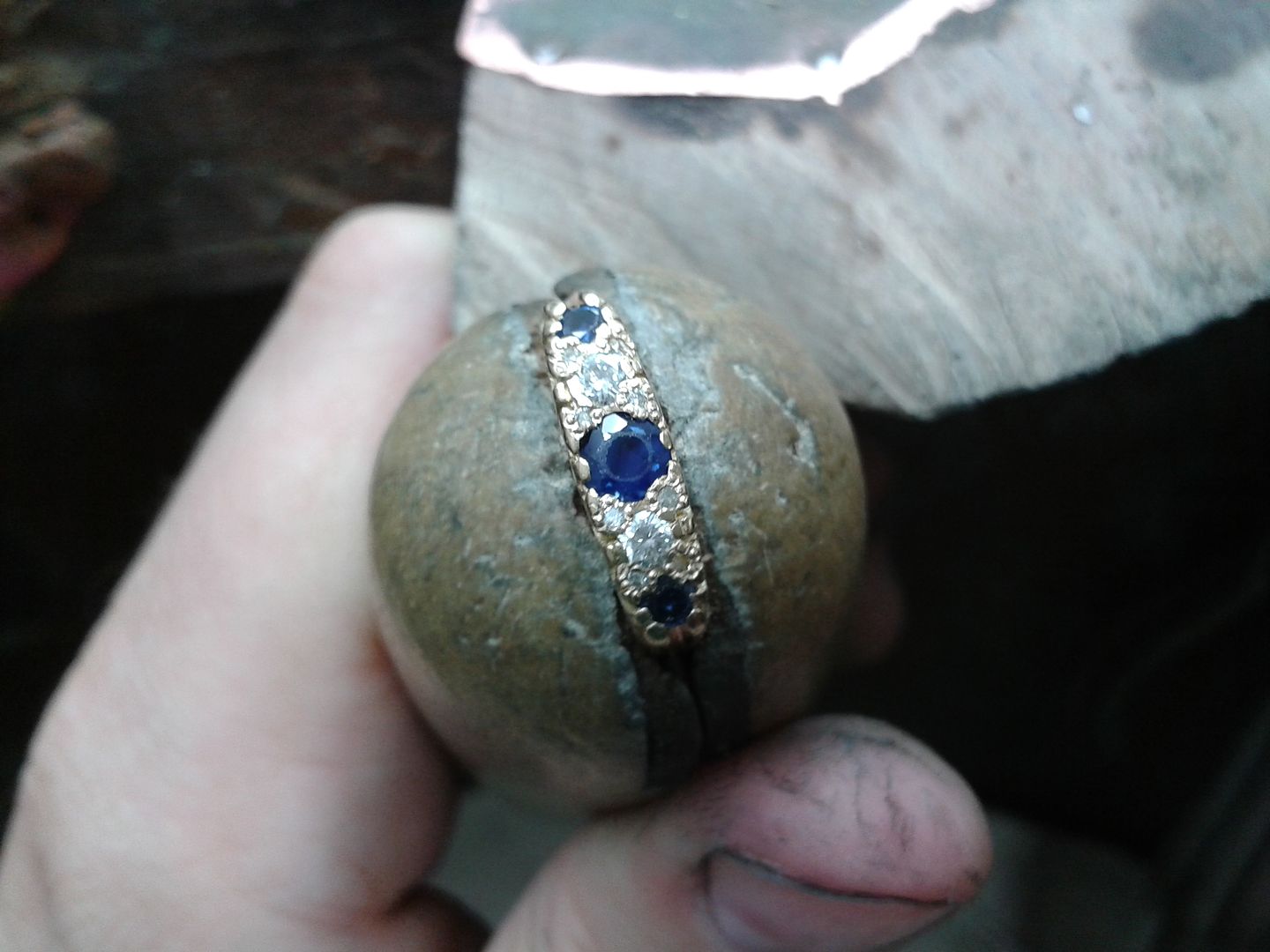
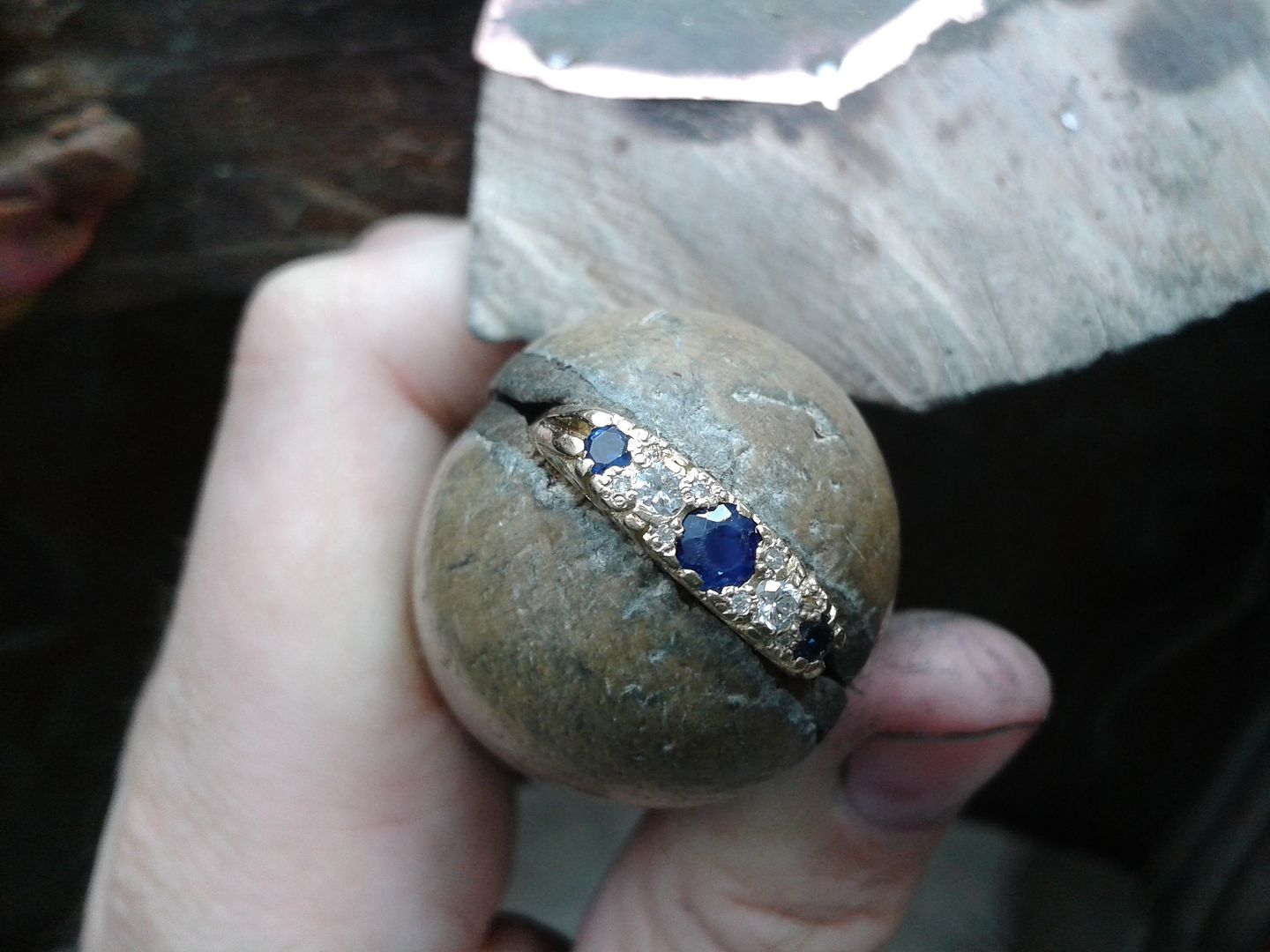
The next thing to do is to remove the old claws that hold the sapphires and larger diamonds. Look closely and you can see where ive filed the old ones down to the base:
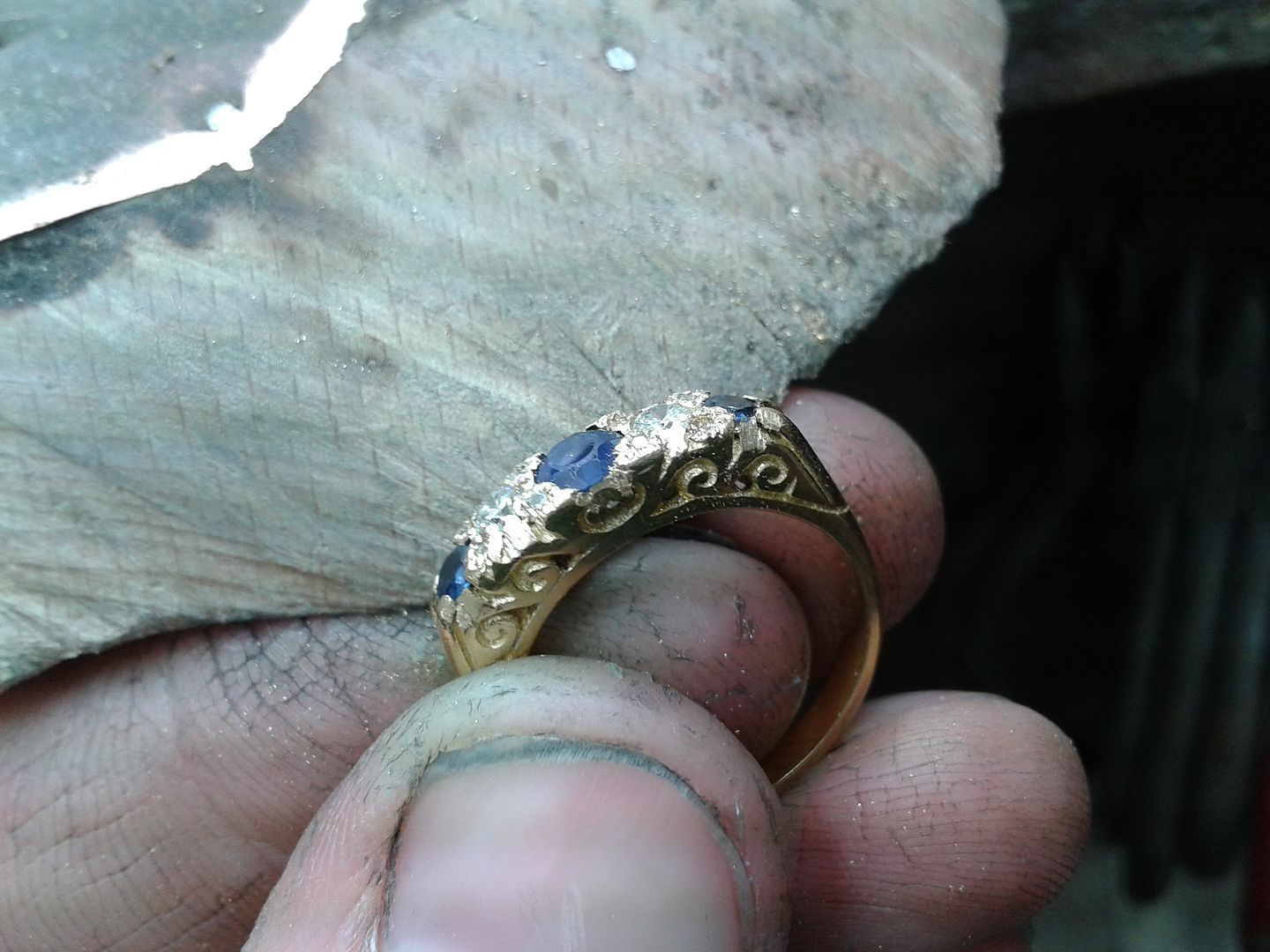
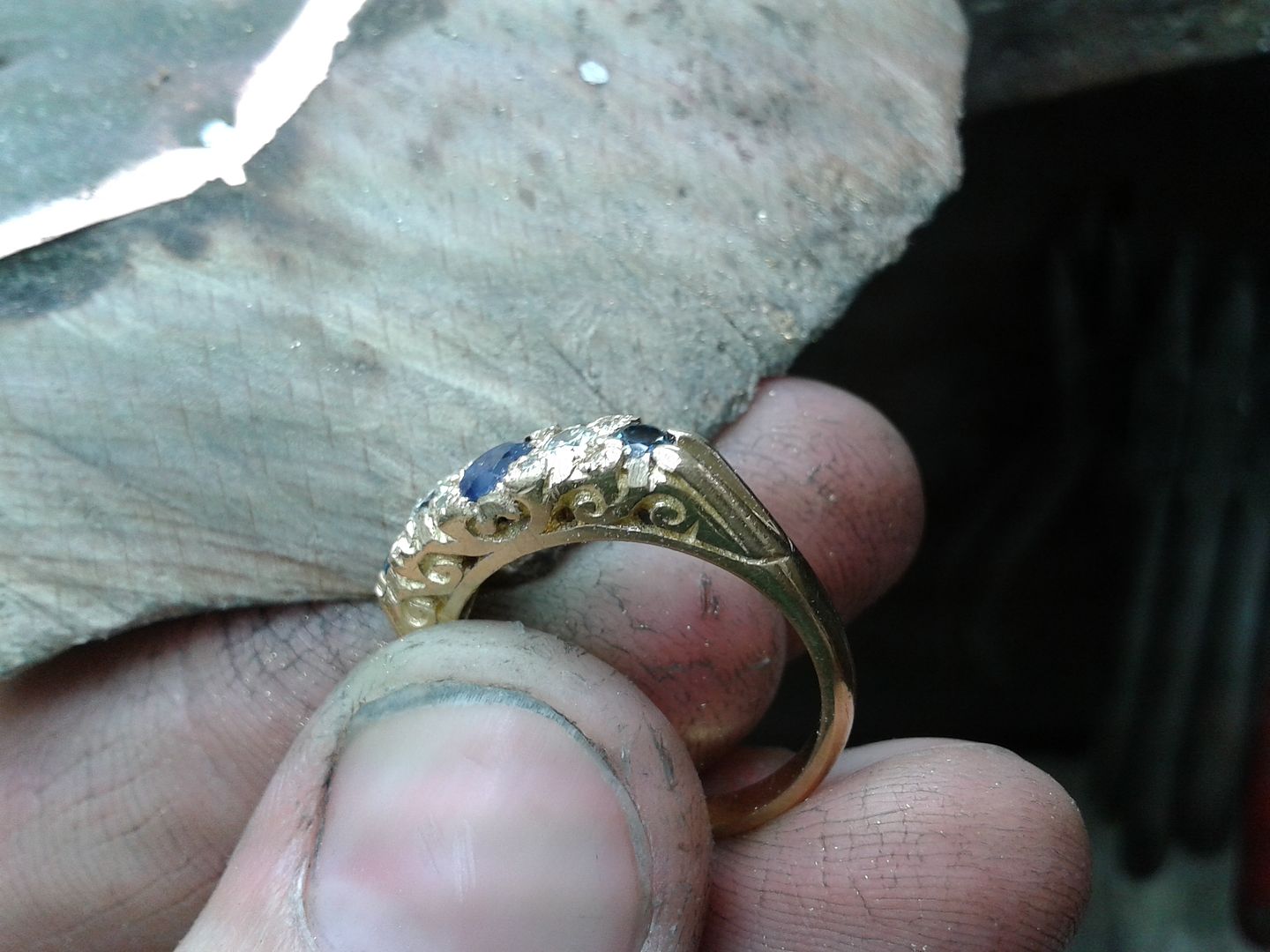
These are claws. They are cut in varying sizes (job dependant) from solid 18ct yellow gold bar that we roll down (without annealing) to the required thickness. We dont anneal the claw material before cutting as it makes it easier to cut. It'll soften up nicely when i solder it on. Same process for white claws, except we use rolled down 18ct white bar.
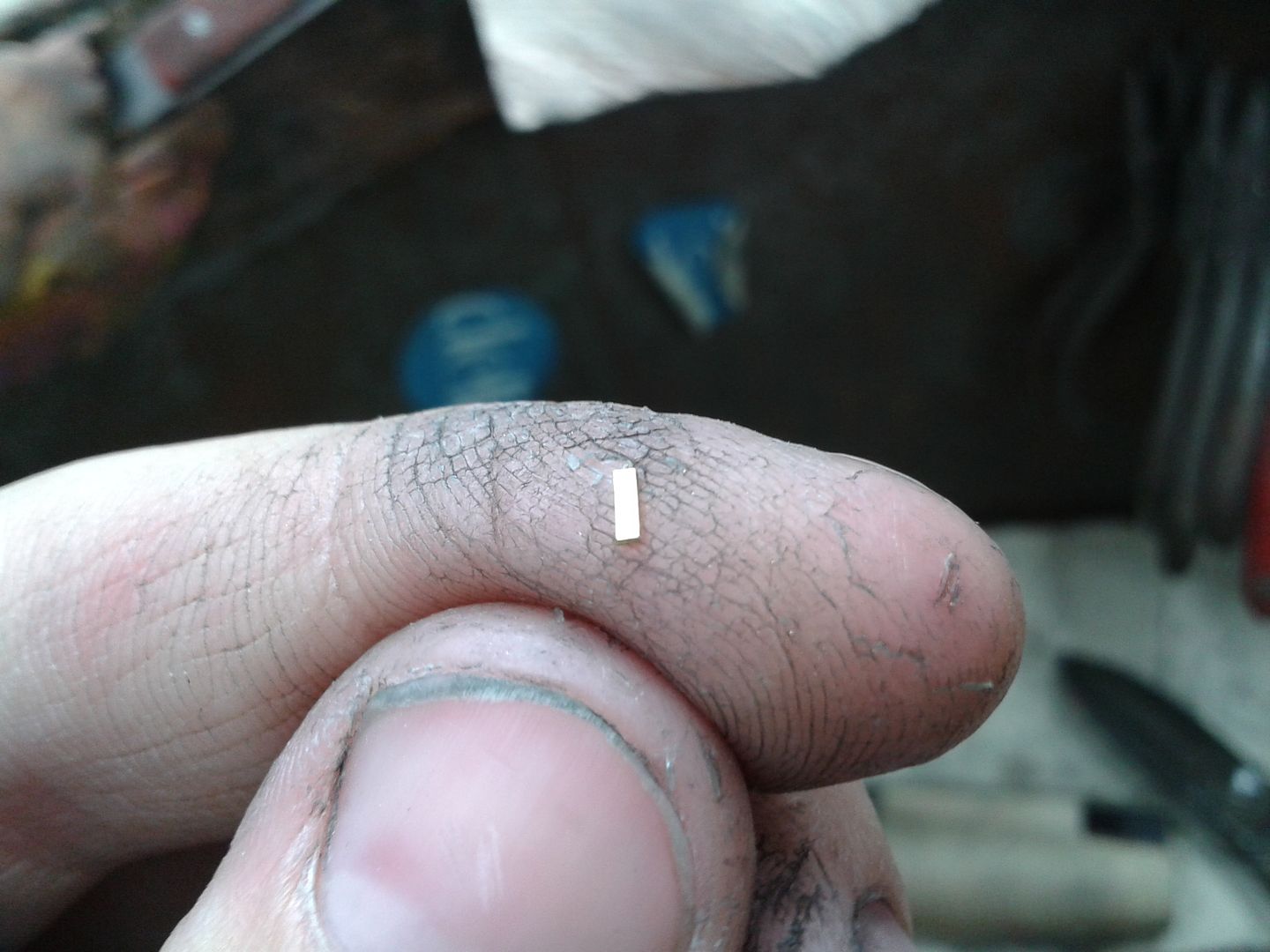
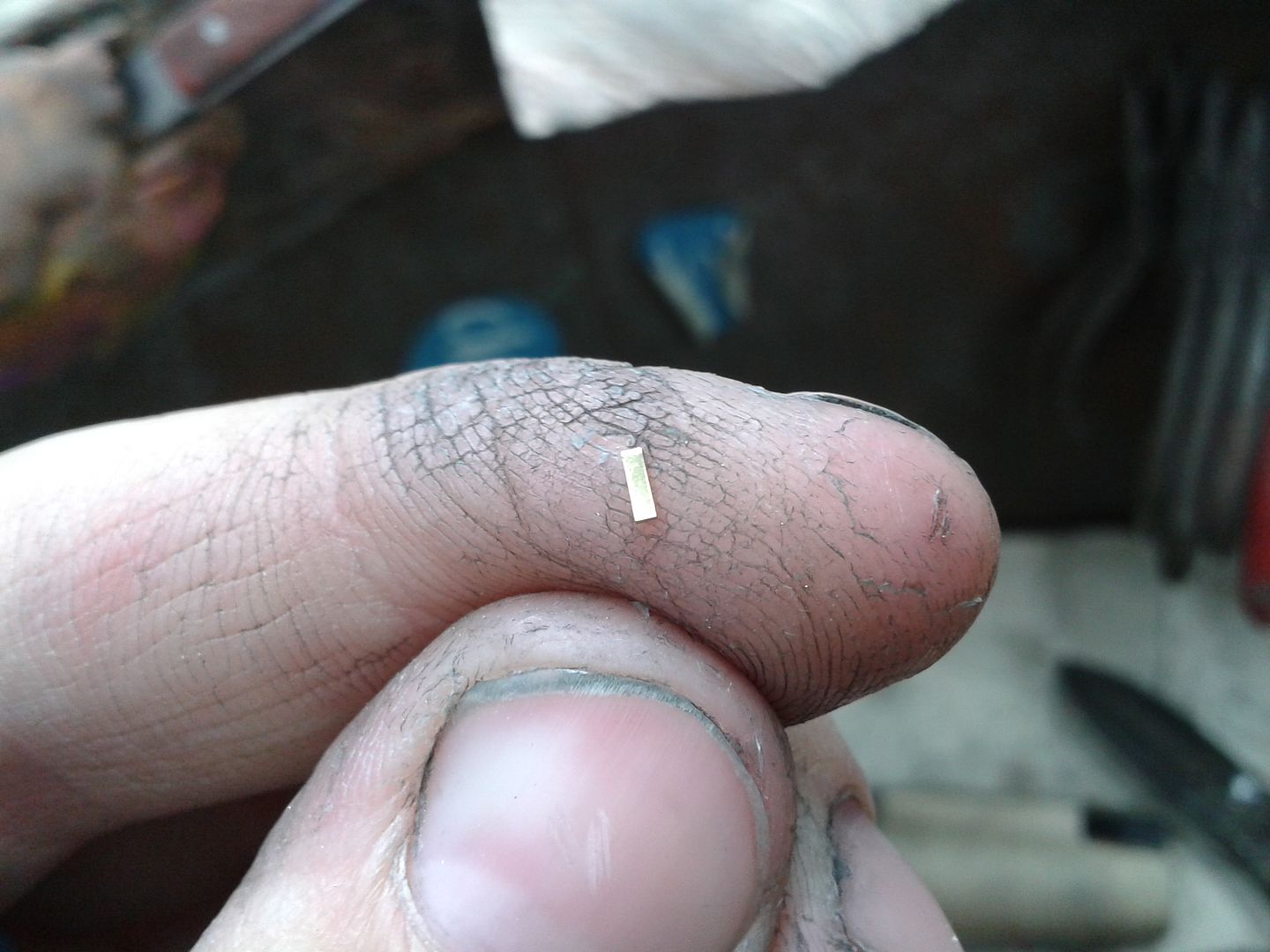
Starting on one side i solder the 5 main structural claws that hold in the sapphires and diamonds. There are 2 more on each end that i'll do once all the stones are secure enough. Note that we are maintaining the original claw pattern as per the sides.
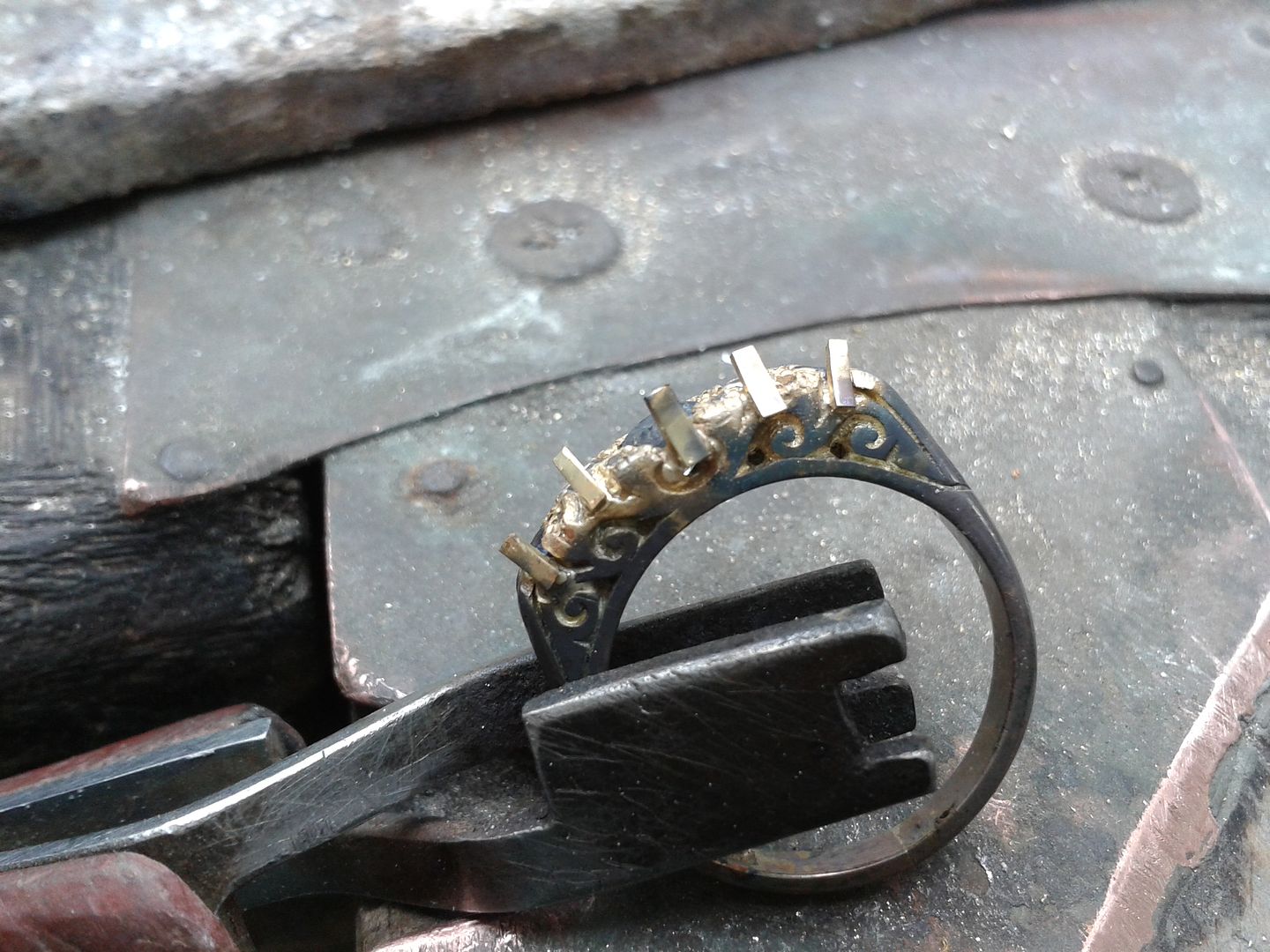
Other side filed down to the bases. Point to note: The diamonds are protected from the heat by applying borax. The sapphires dont respond well to borax and are easily damaged by the borax corrosive properties, leaving the surface cloudy and damaged. So long as the sapphires don't take direct heat they cope well with high temperatures. This is why claw work can be so tricky. Knowing your stones and getting the heat right.
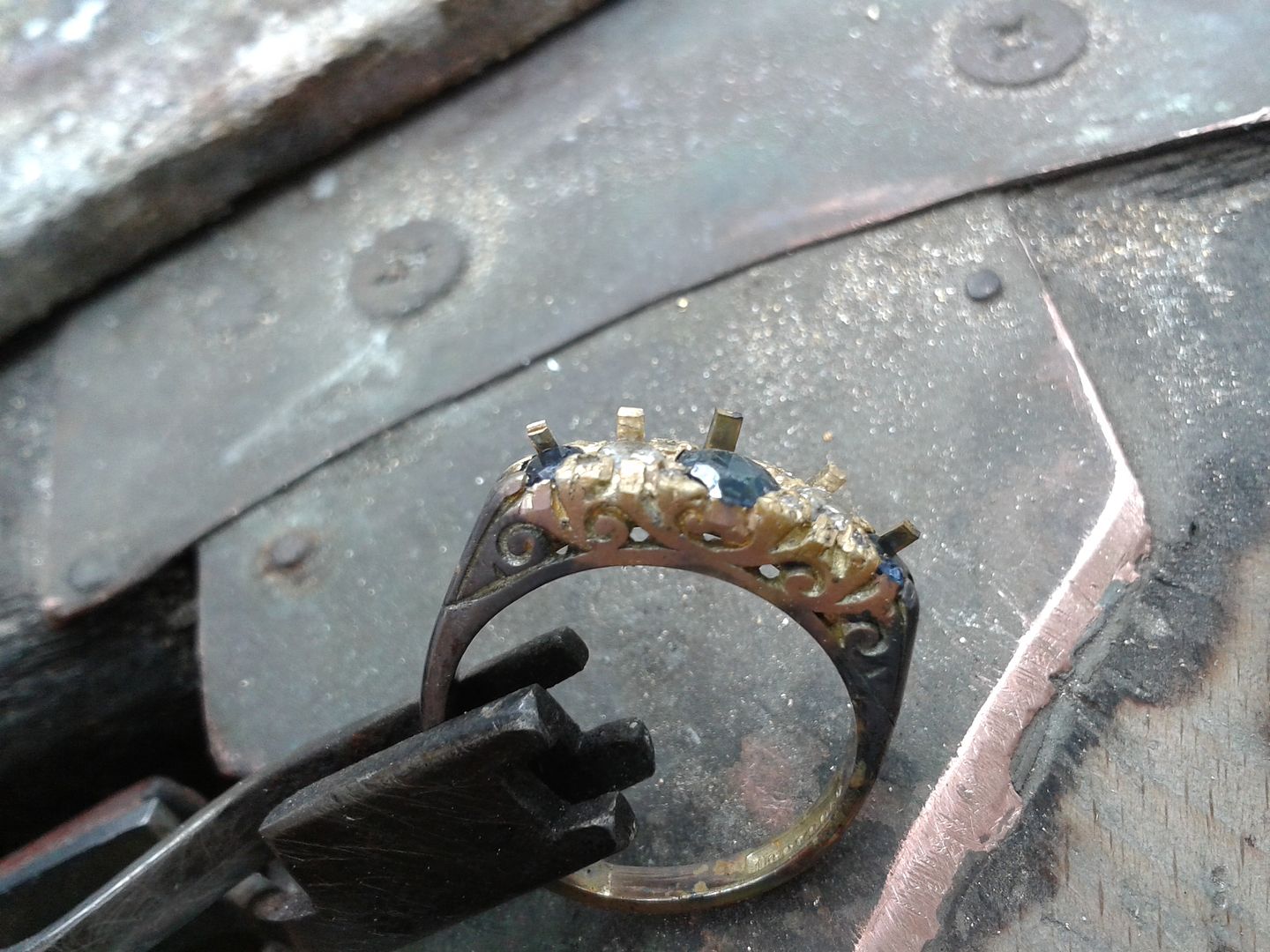
5 more claws applied and in place:
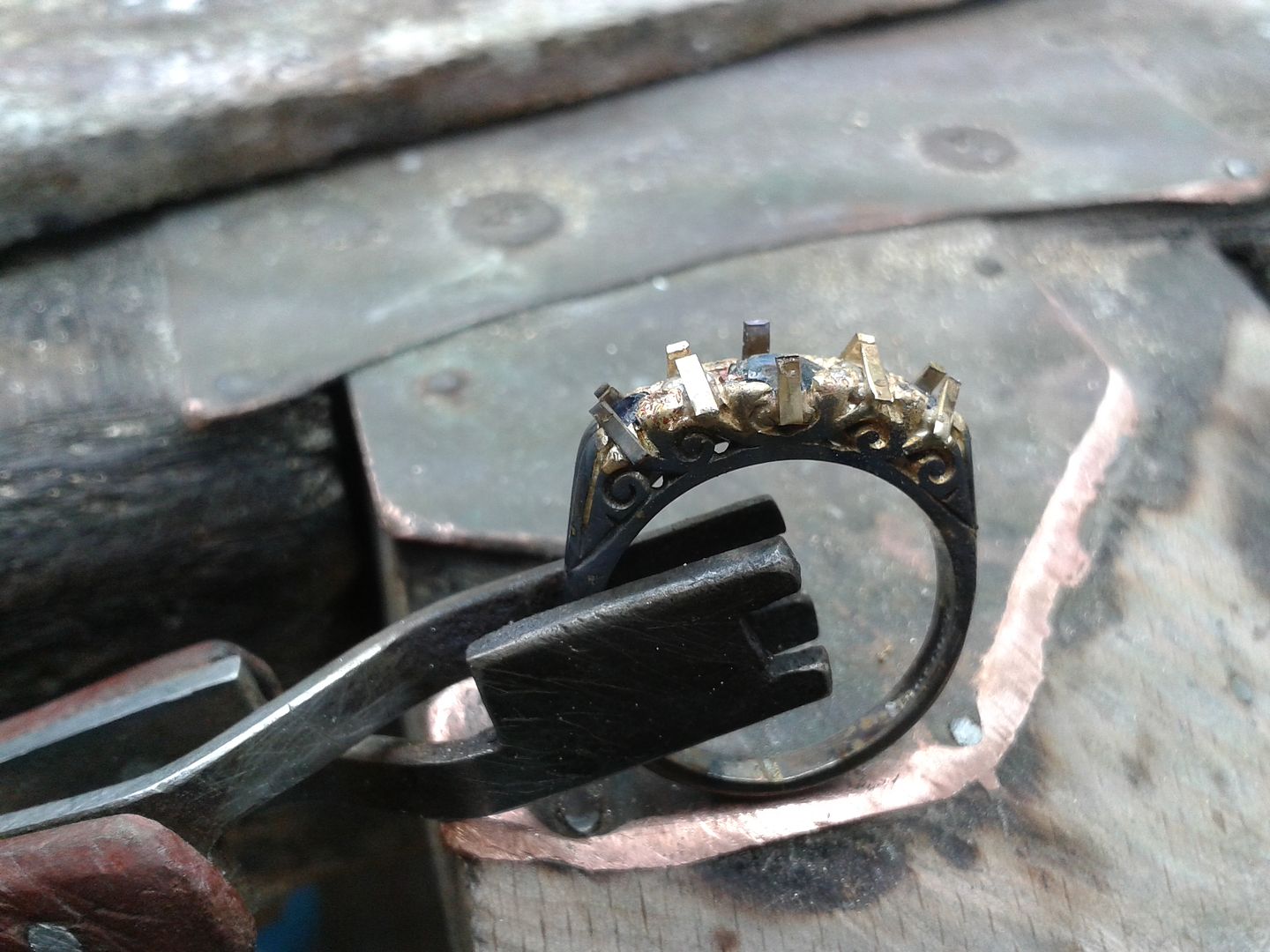
The 10 claws are then pressed over the sapphires and diamonds and then cut down in length to keep them out of the way of further work. Note the 2 other claws on each end that still need to be replaced.
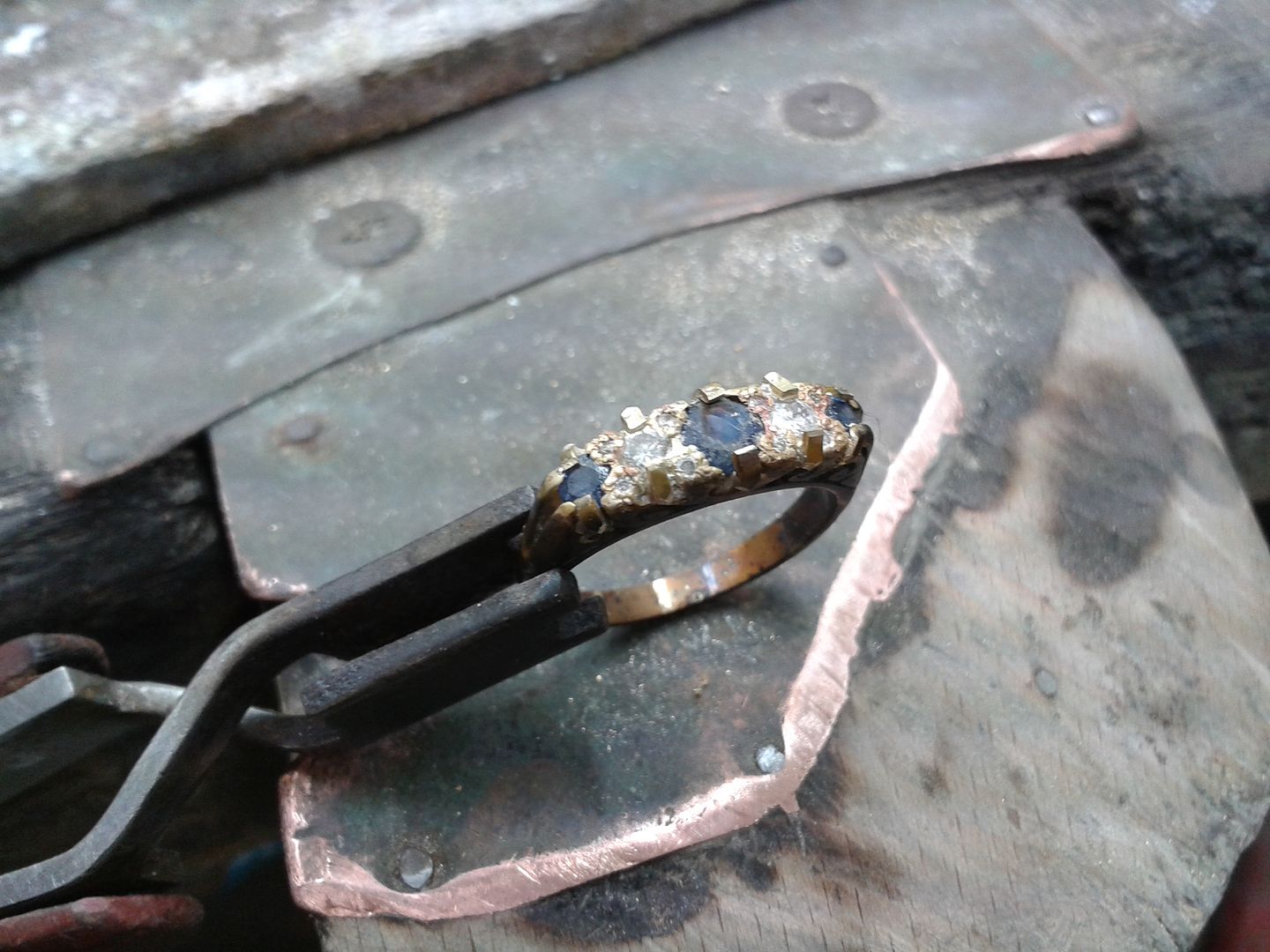
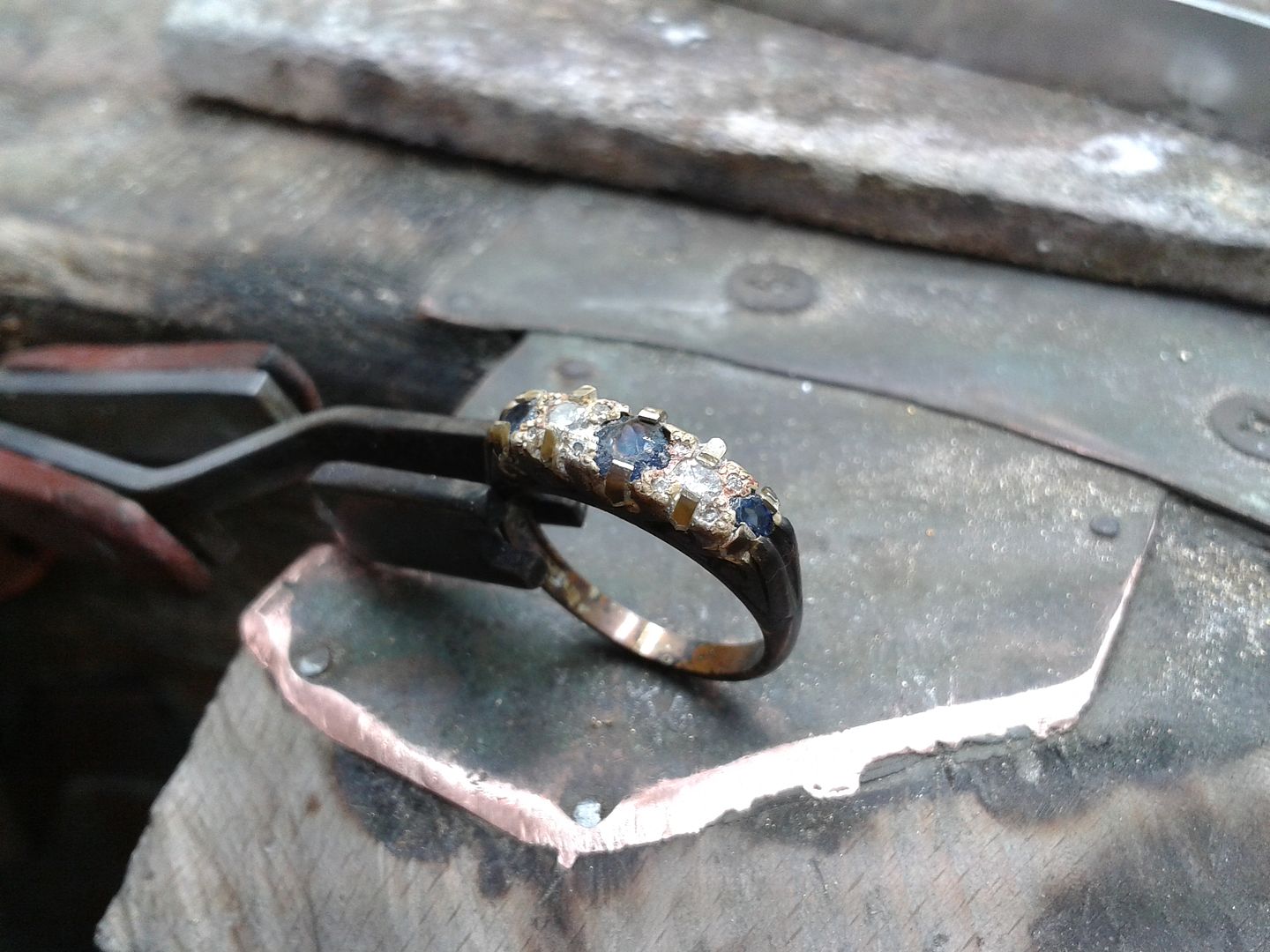
2 x end claws filed down:
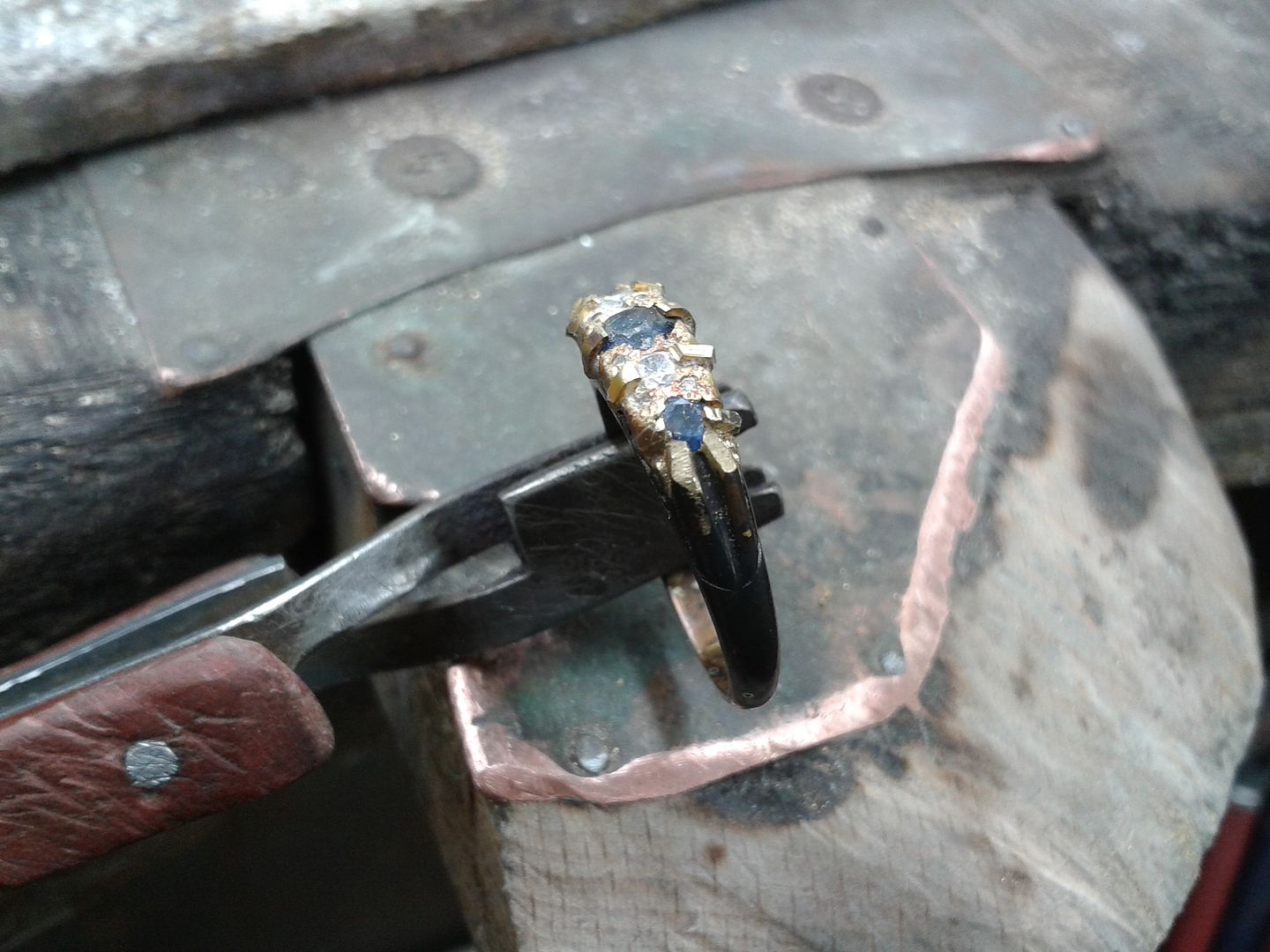
2 x new claws applied: These end ones are actually quite tricky to keep in place. You get one down ok and then because of the proximity to the next one it can move because of the heat. Practice practice.
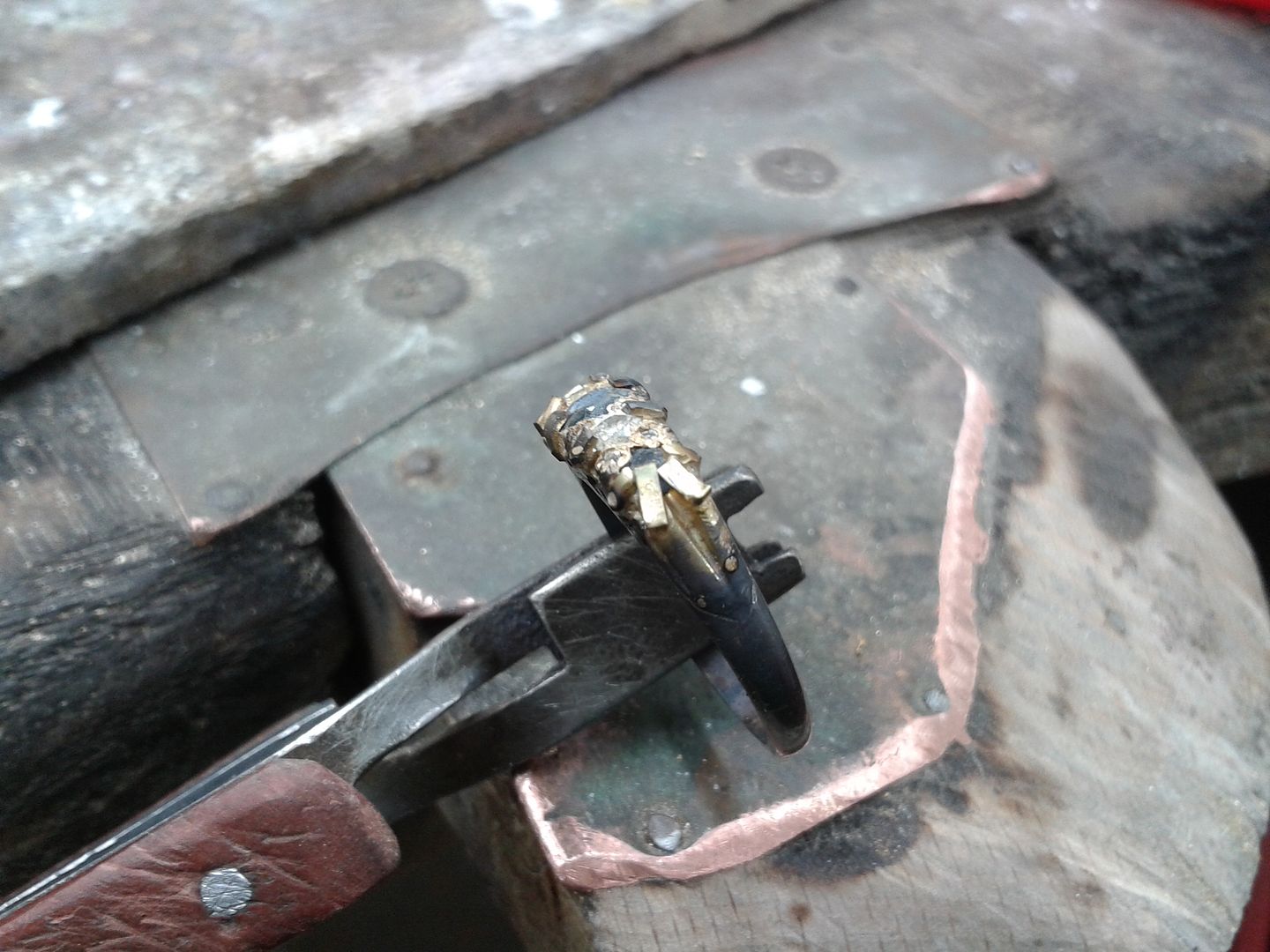
And the other end done too:
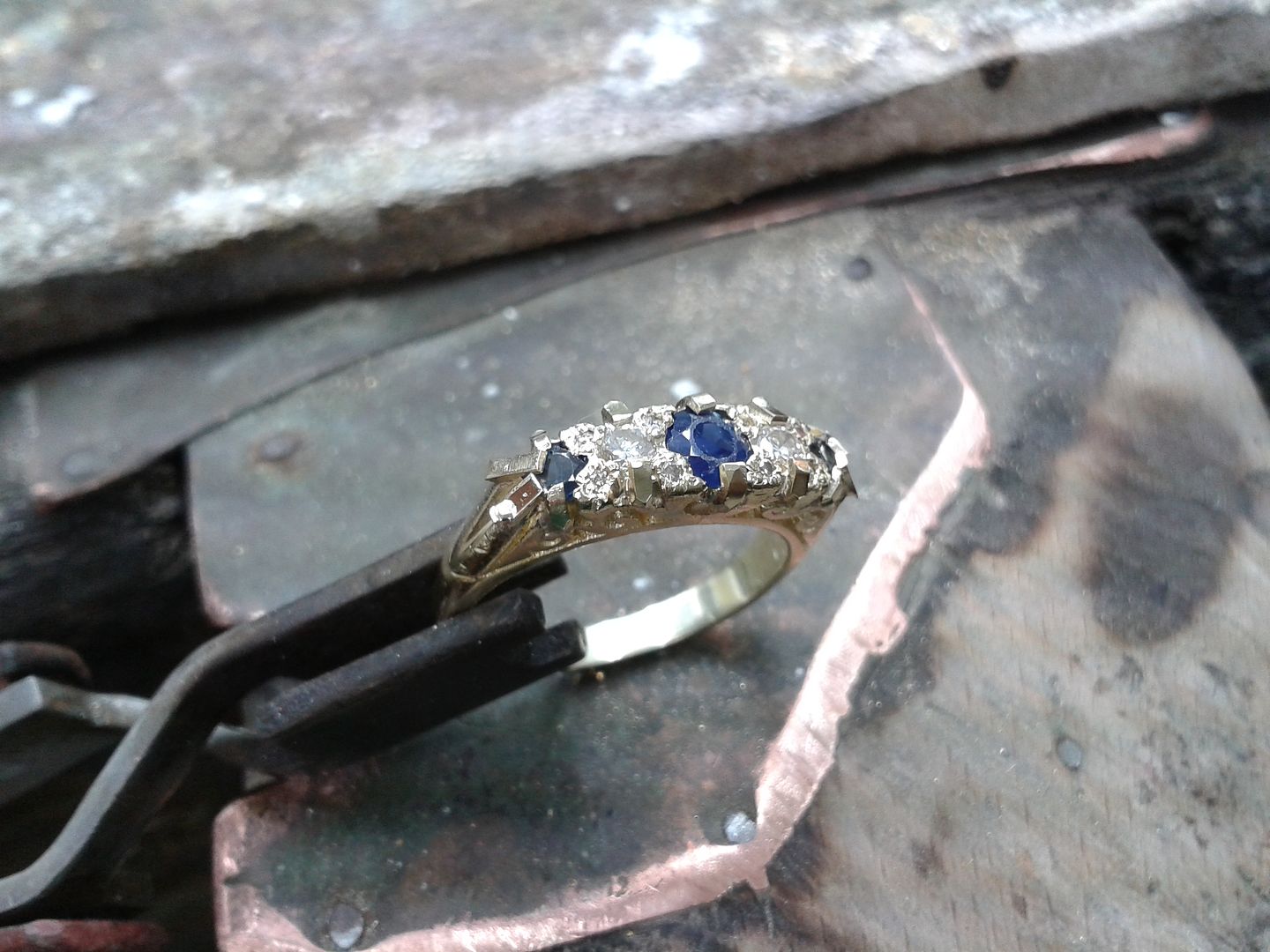
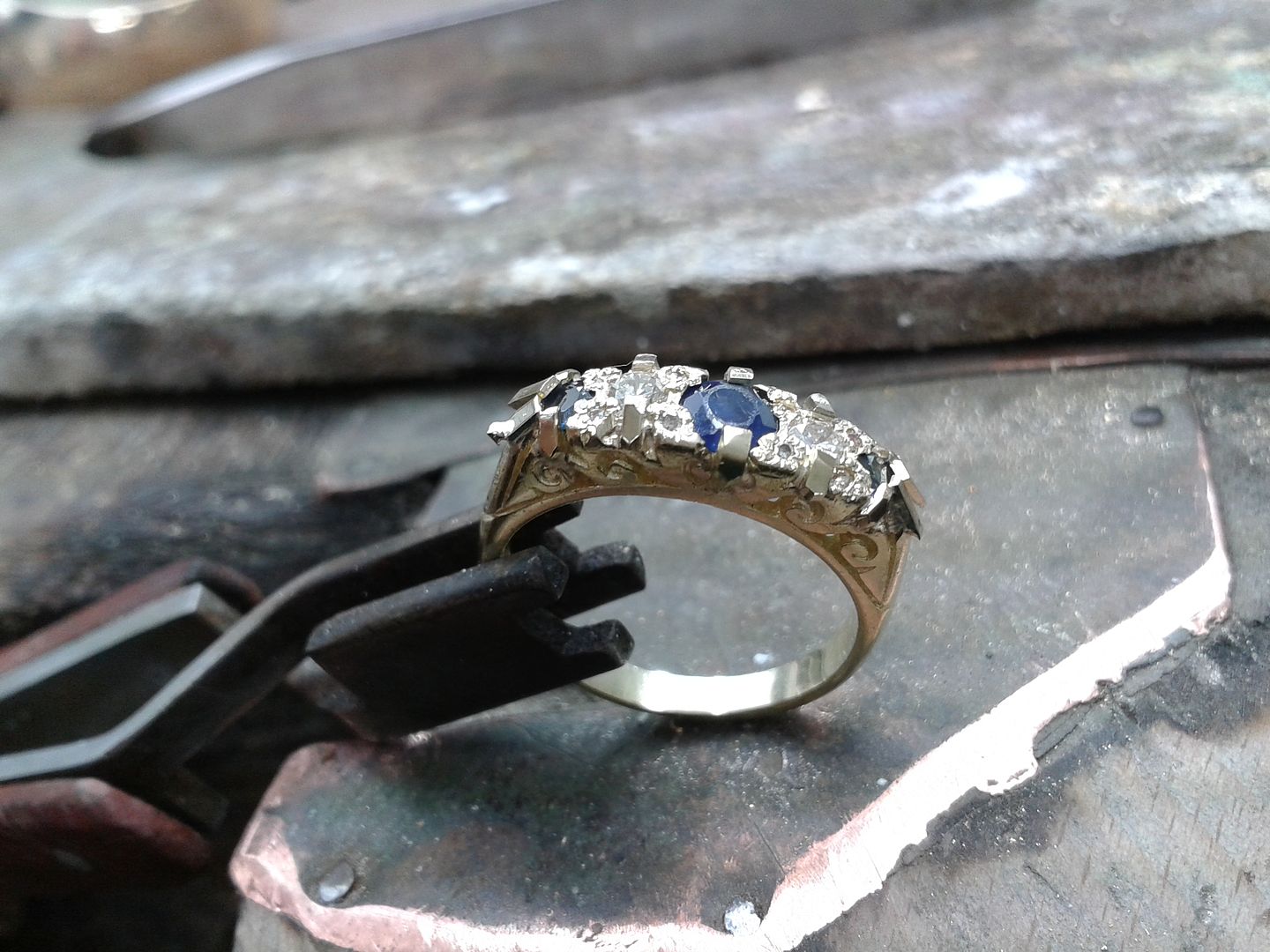
The next phase is to shape the main claws. Here you can see the sides roughly filed and profiled to shape:
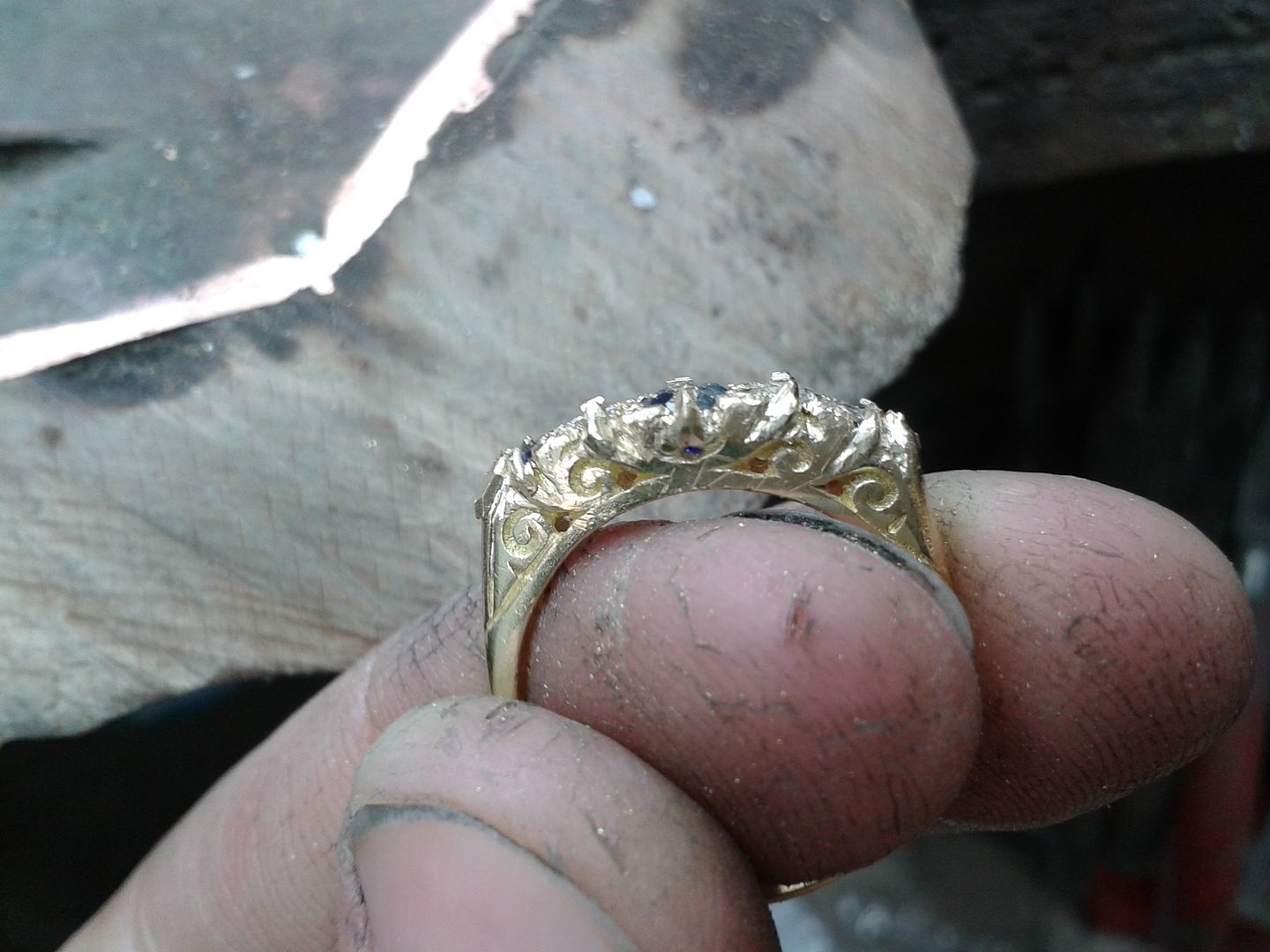
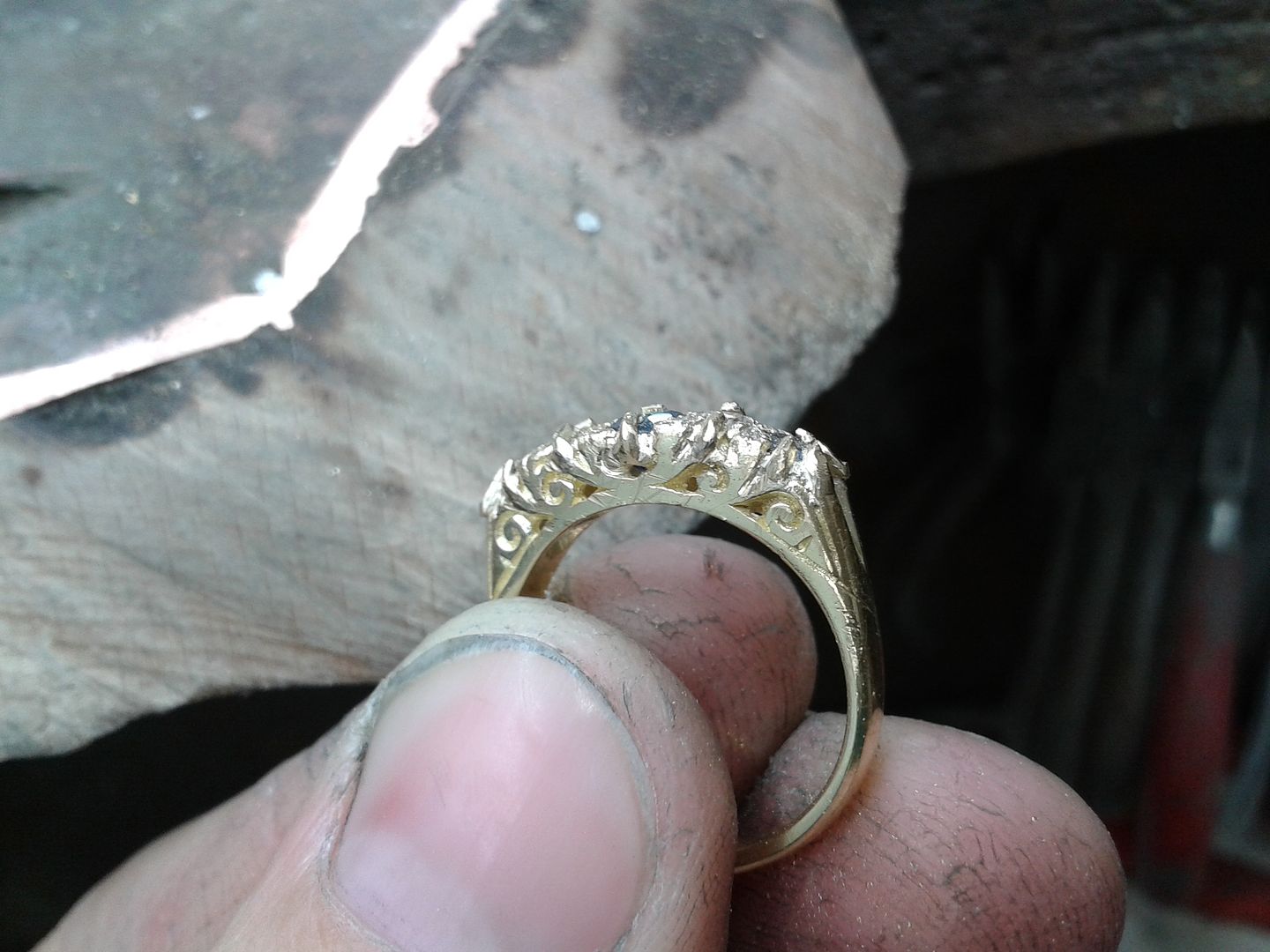
And the tops in a rough shape:
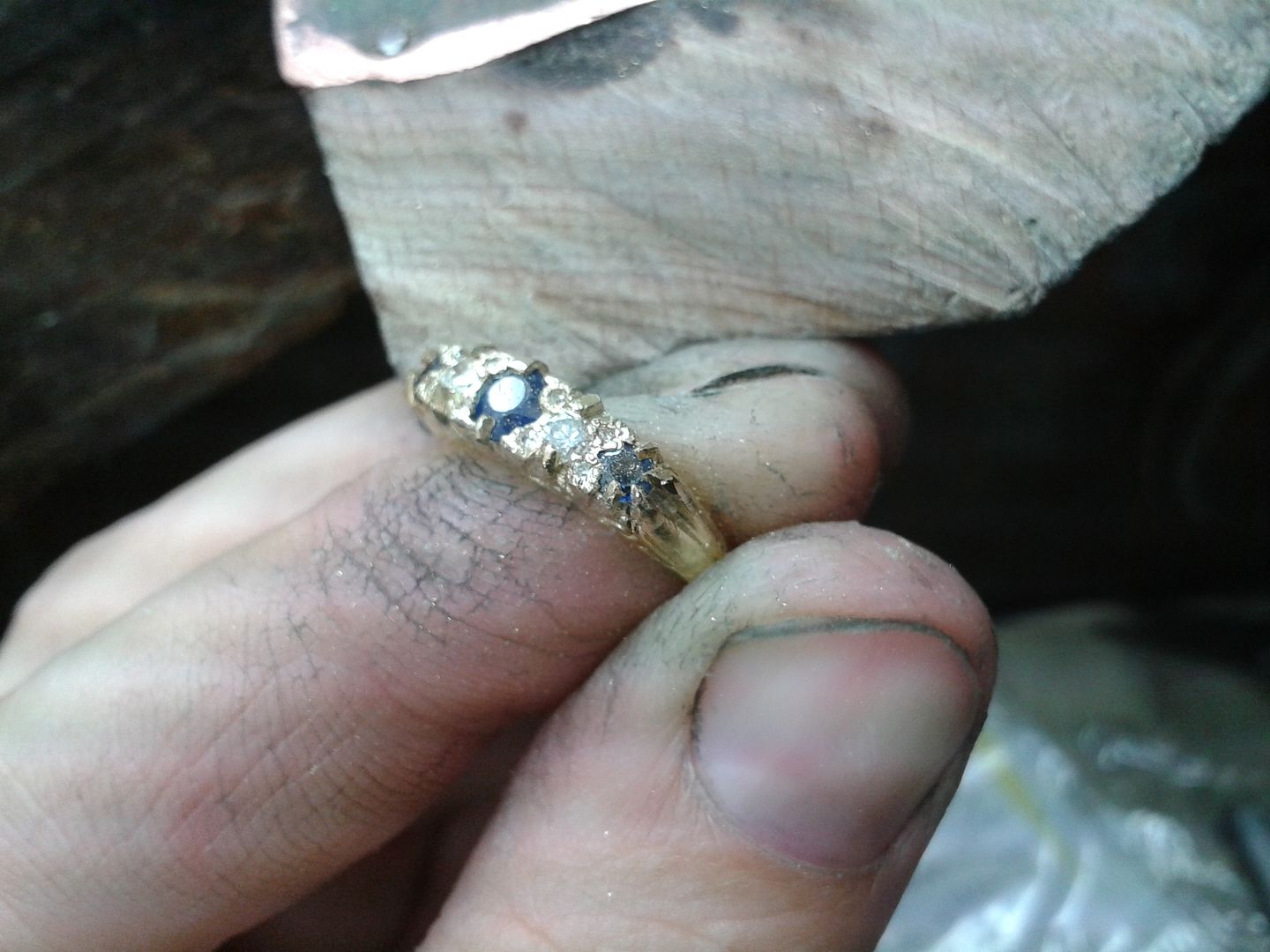
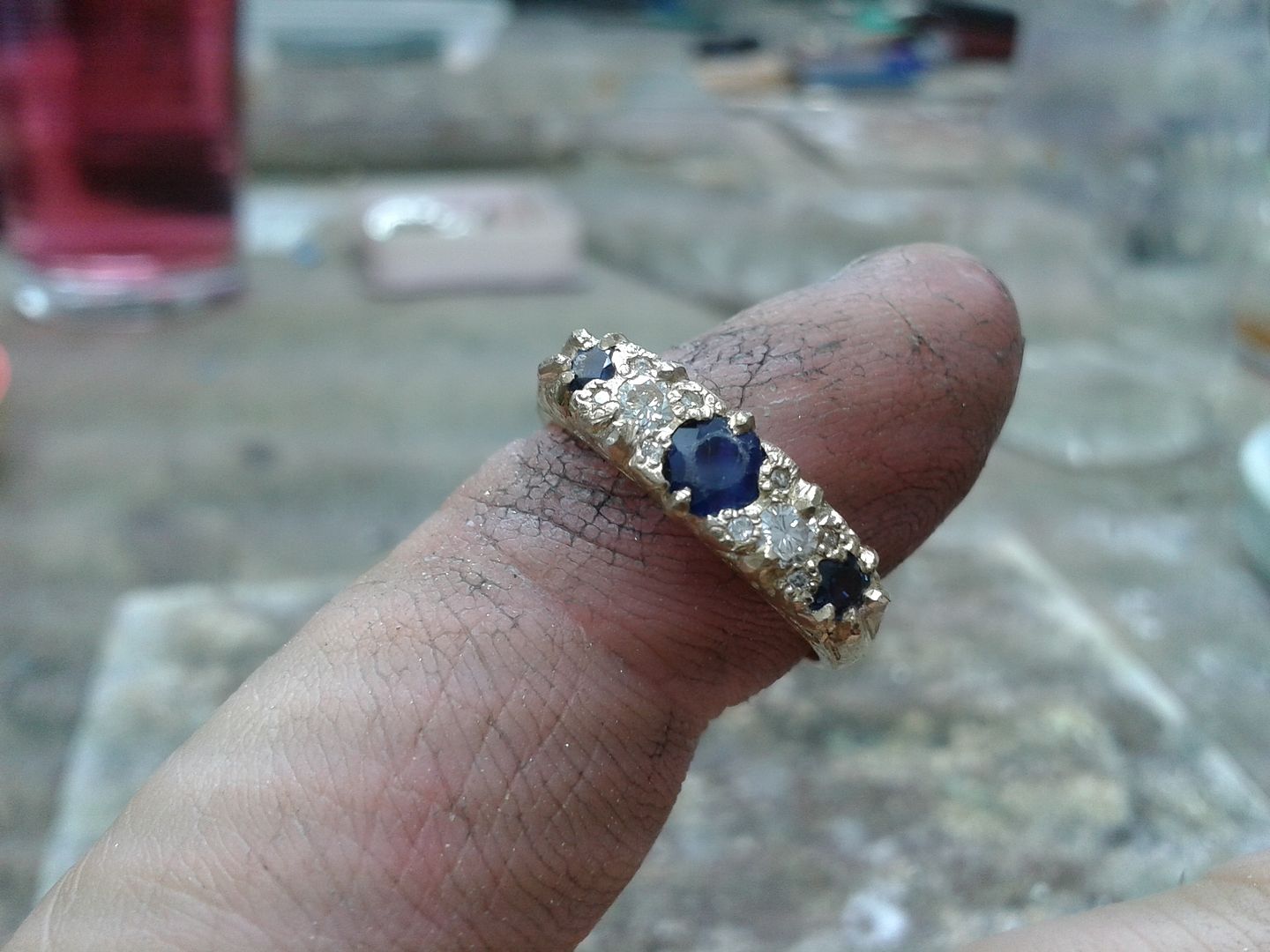
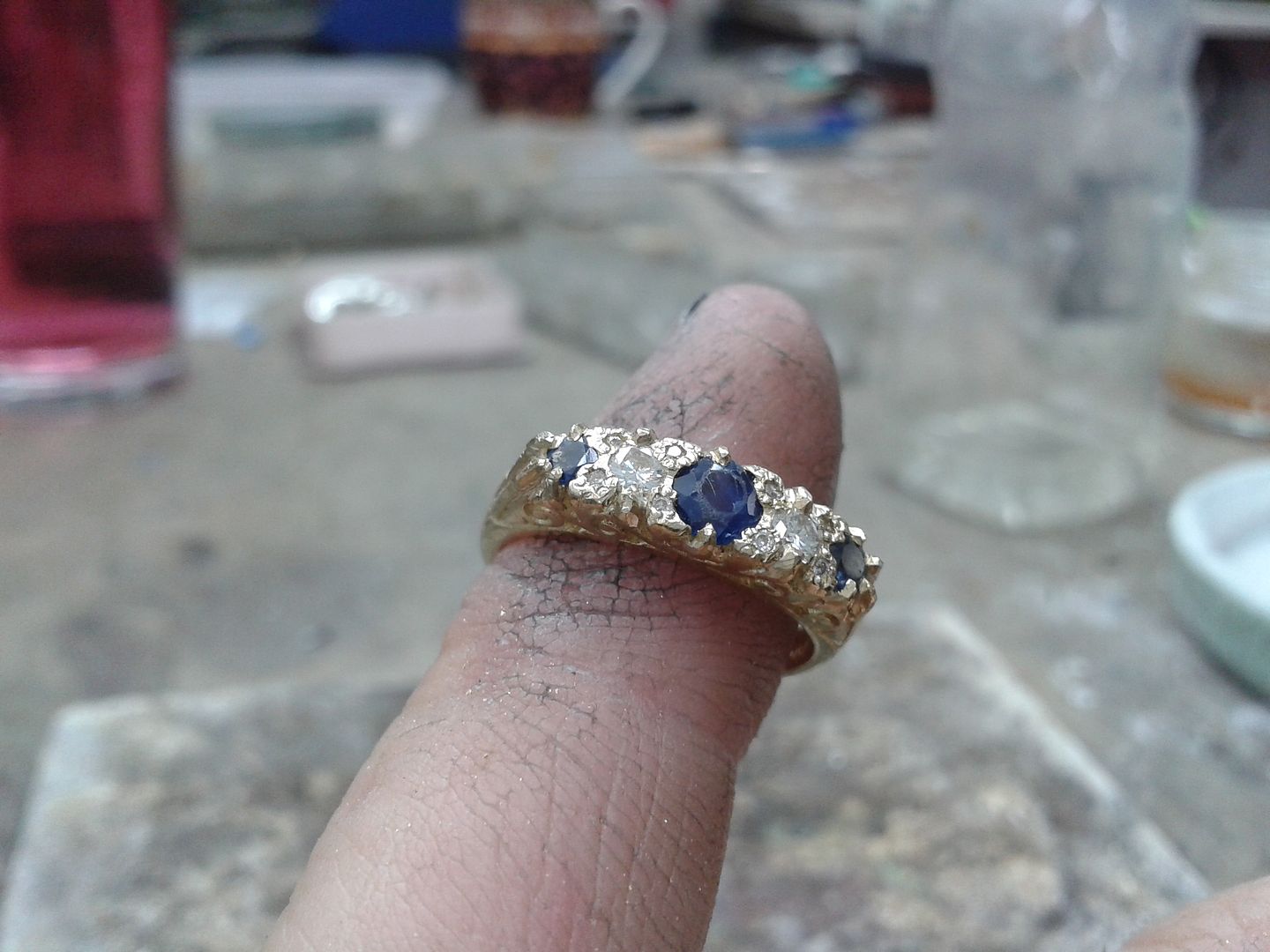
Its difficult to see in the following pics but the most tricky bit of the process is still to come. We have to solder tiny claws known as 'grains' around the ring to secure the stones in places where standard claws are not an option. The red dots mark where they will go. The solder we use is a shop recipe.
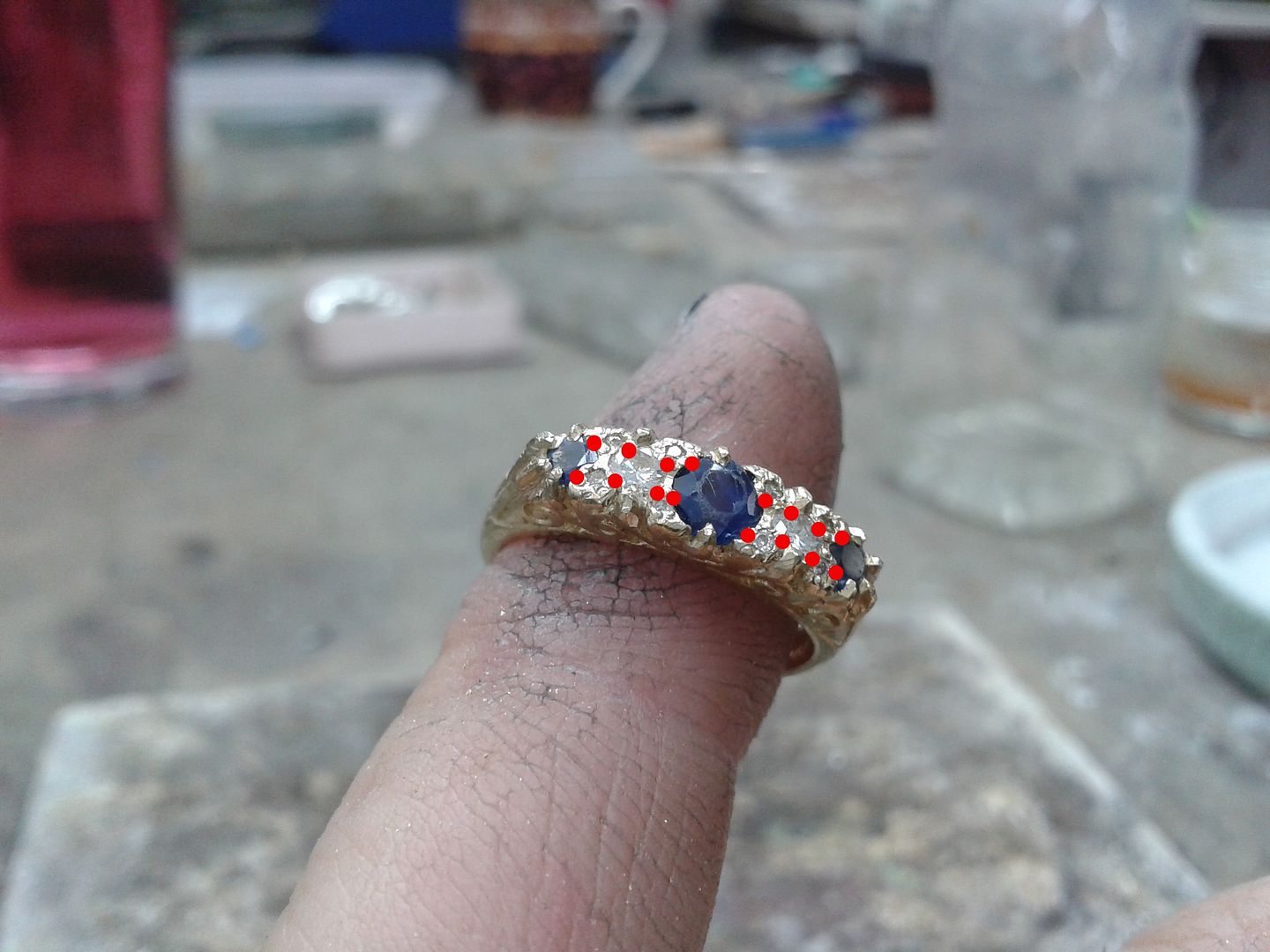
Here you can see them applied: The phone pics dont help but the grains are all there.
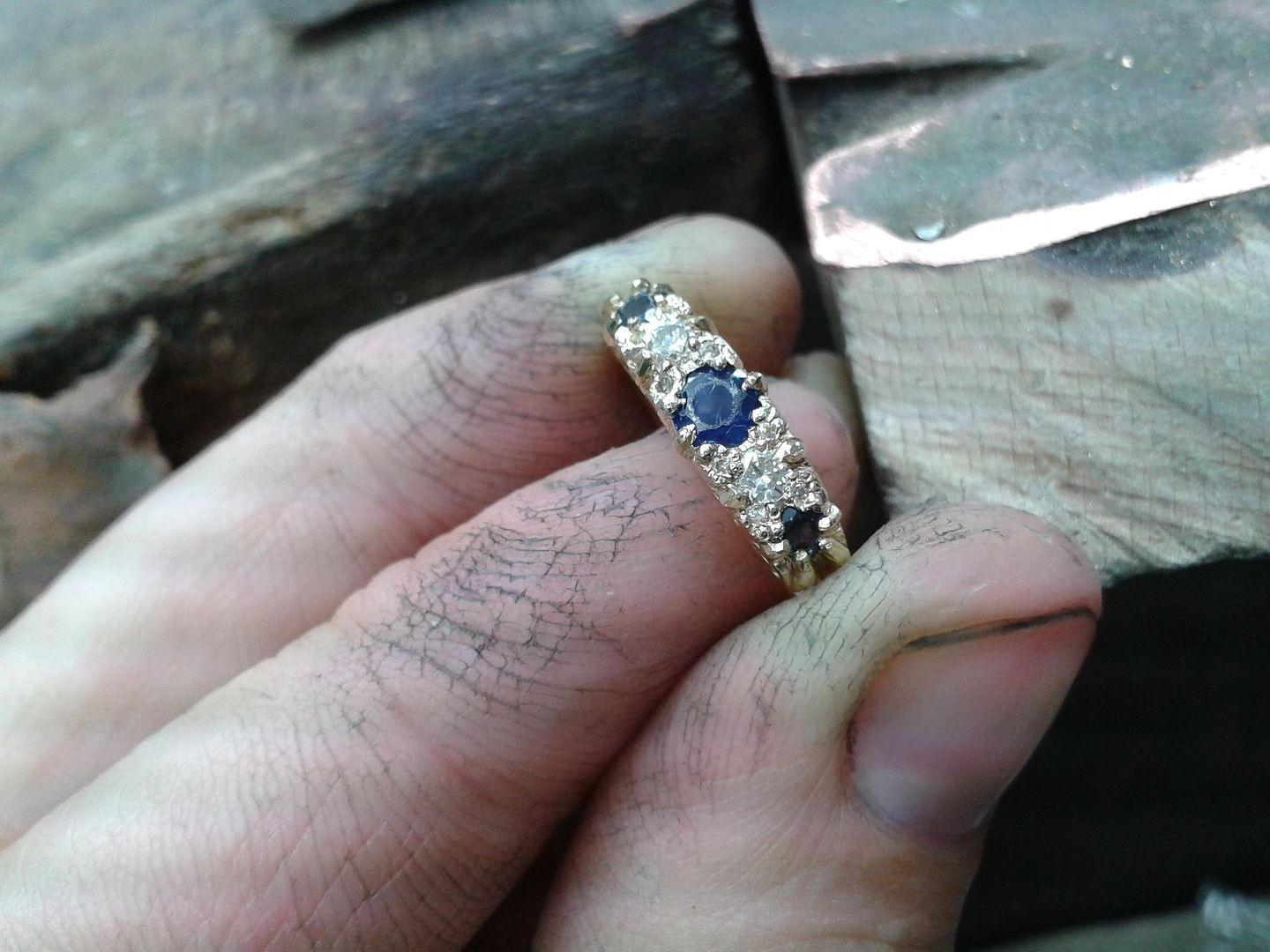
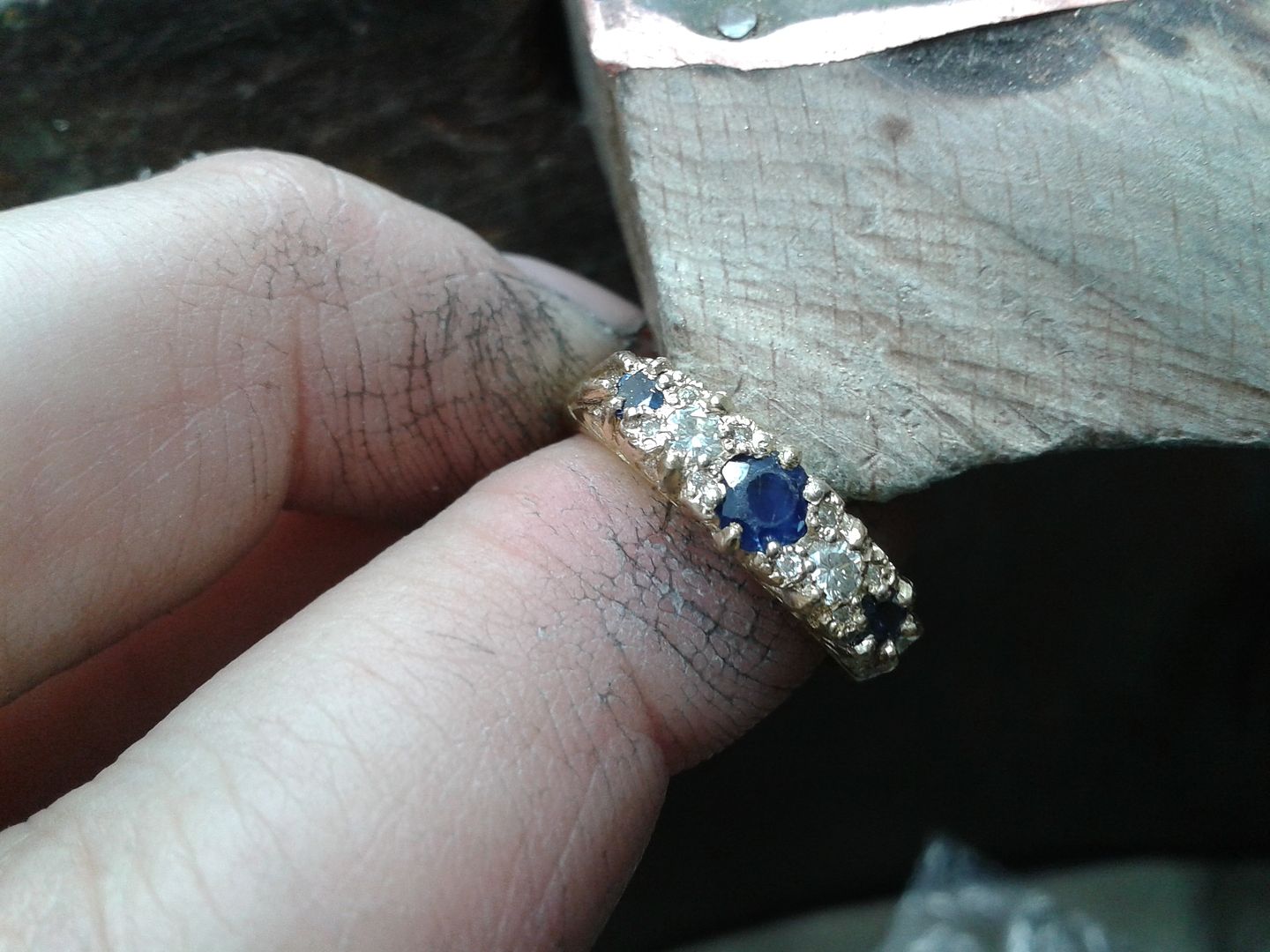
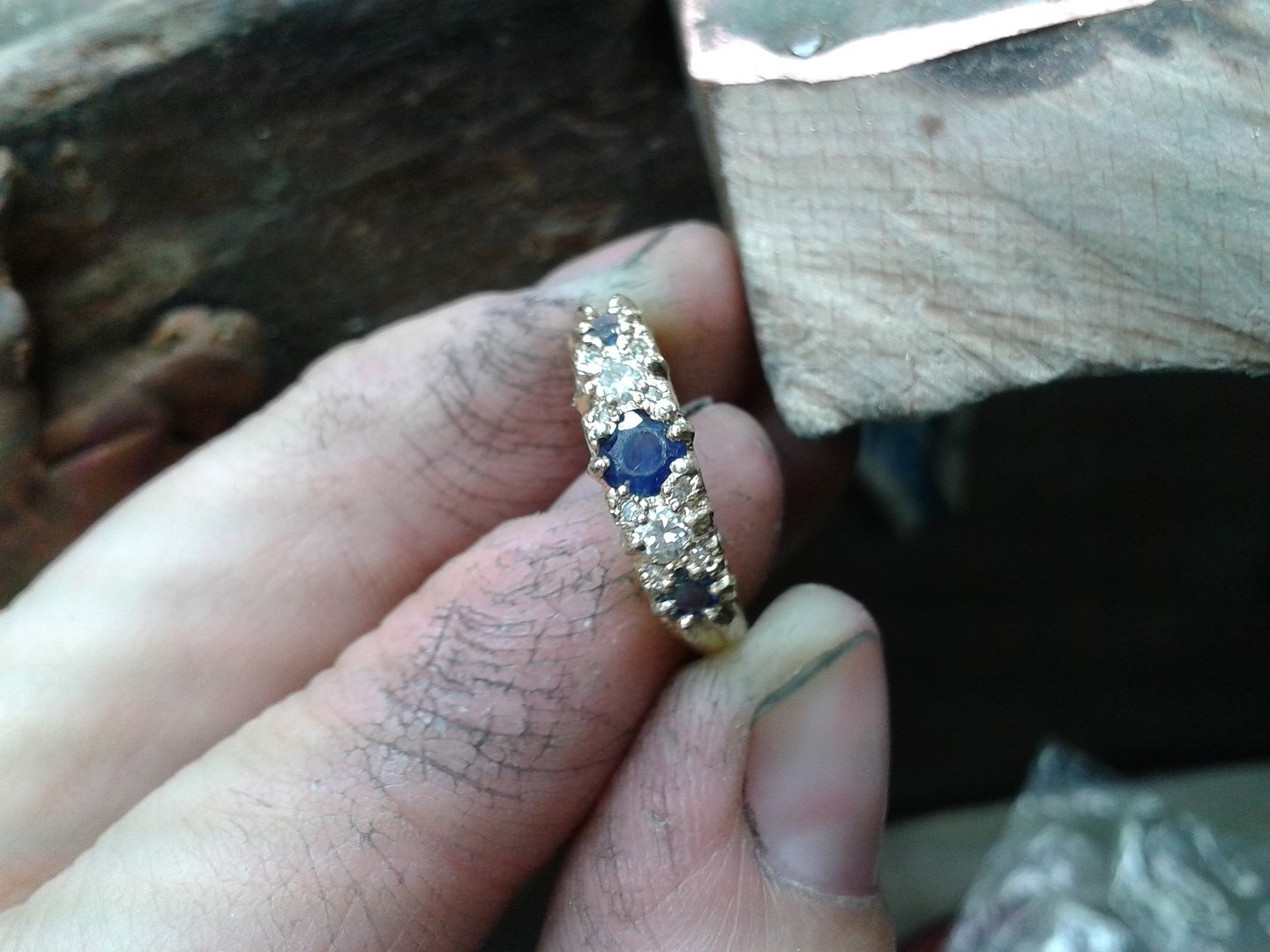
We then give the ring a good polish to give light to all the hard work. It also highlights any areas where we need to do more. In this case we are fine.
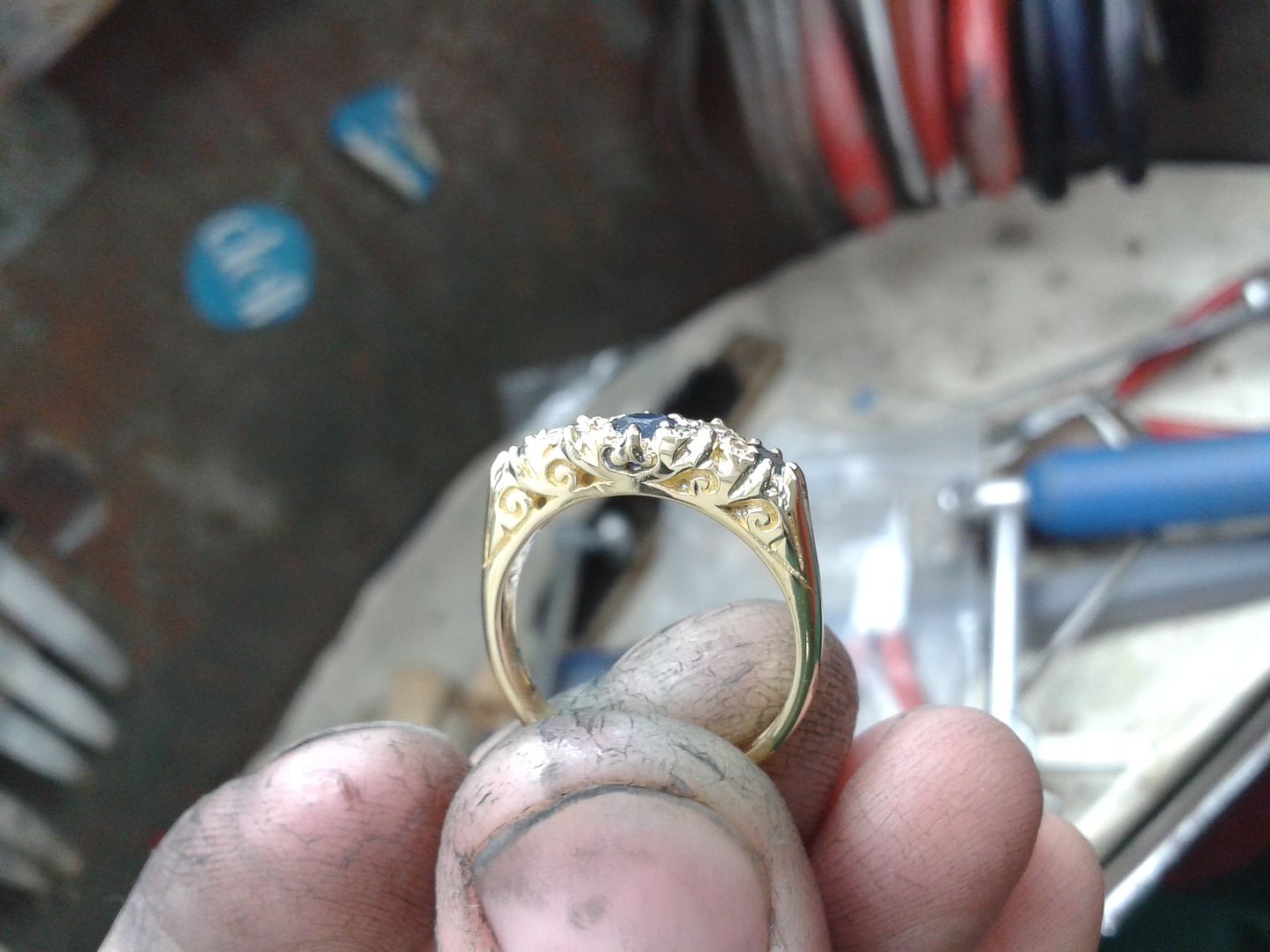
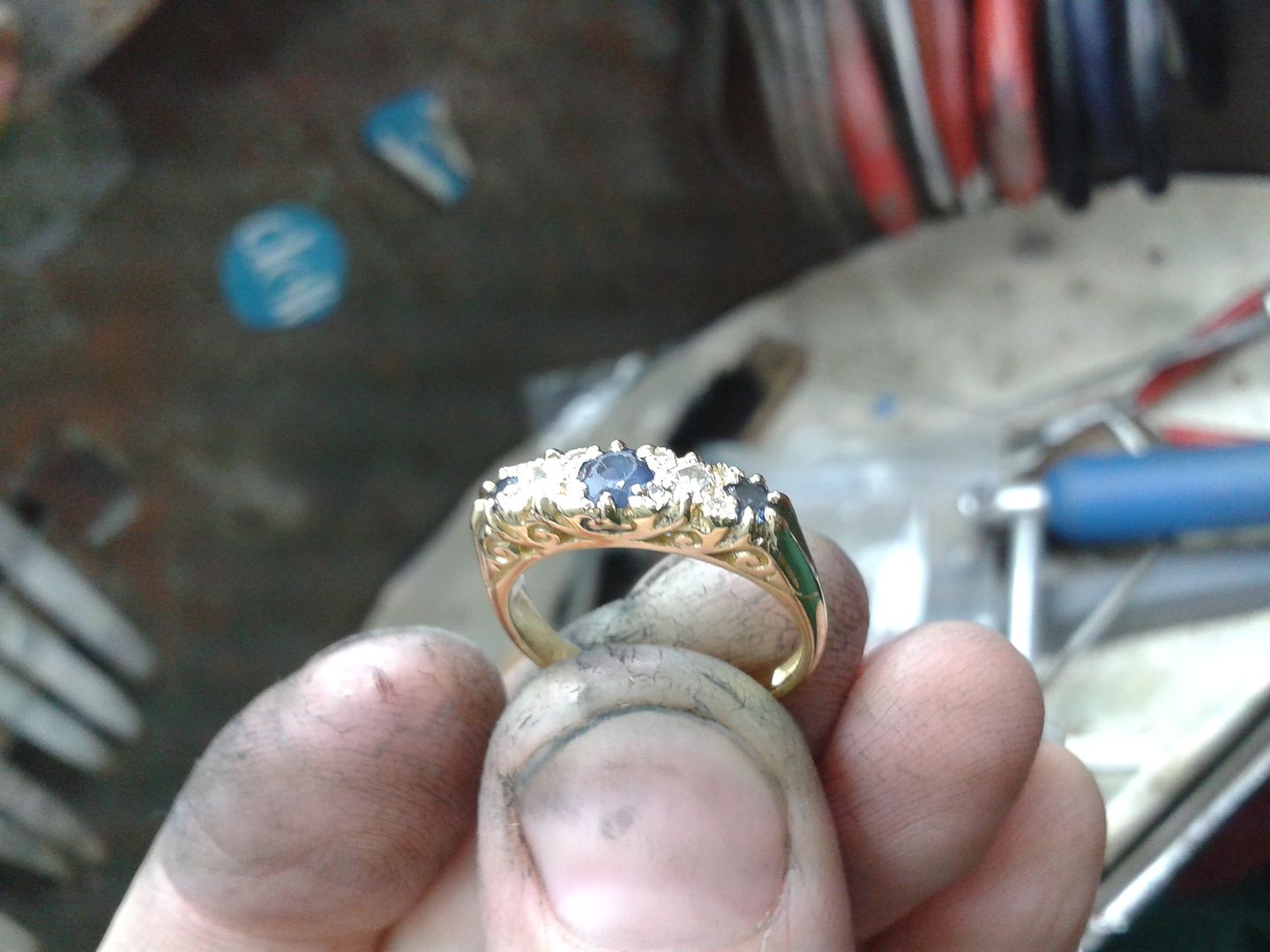
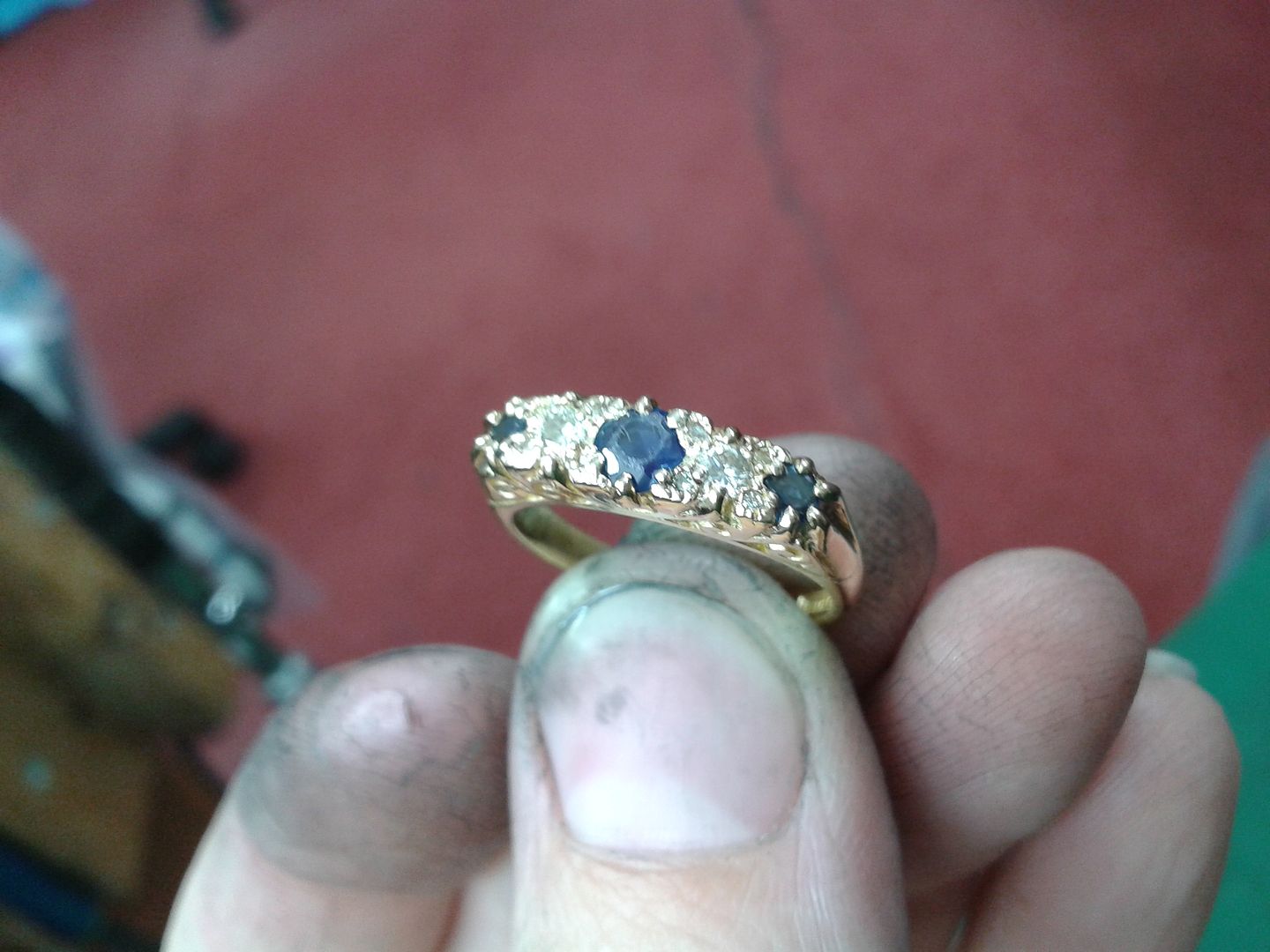
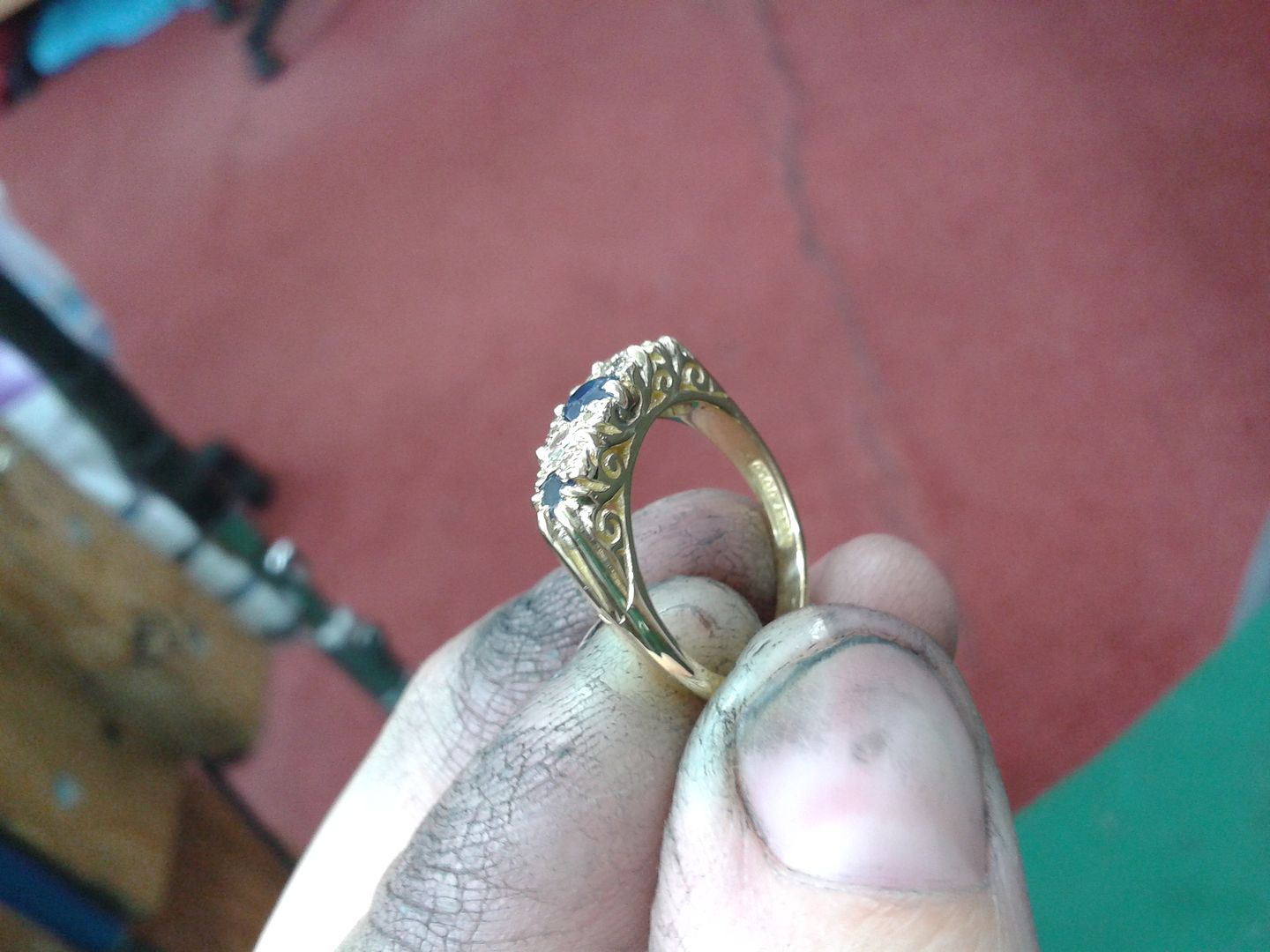
For an added sparkle the customer has opted to have the top of the setting rhodium plated. This gives a platinum white finish to the setting and allows the stones to show their best colours. Masking out the ring for plating:
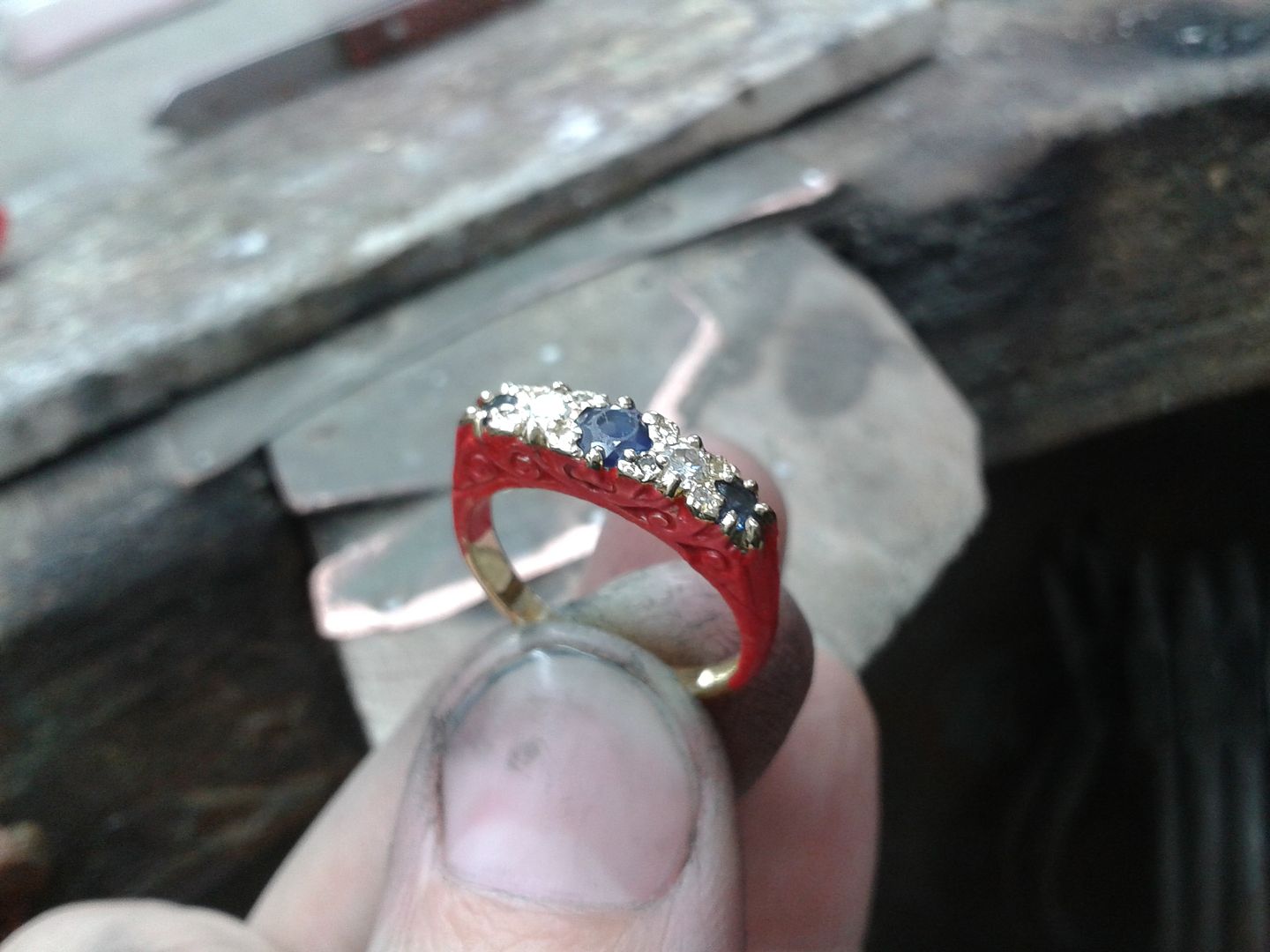
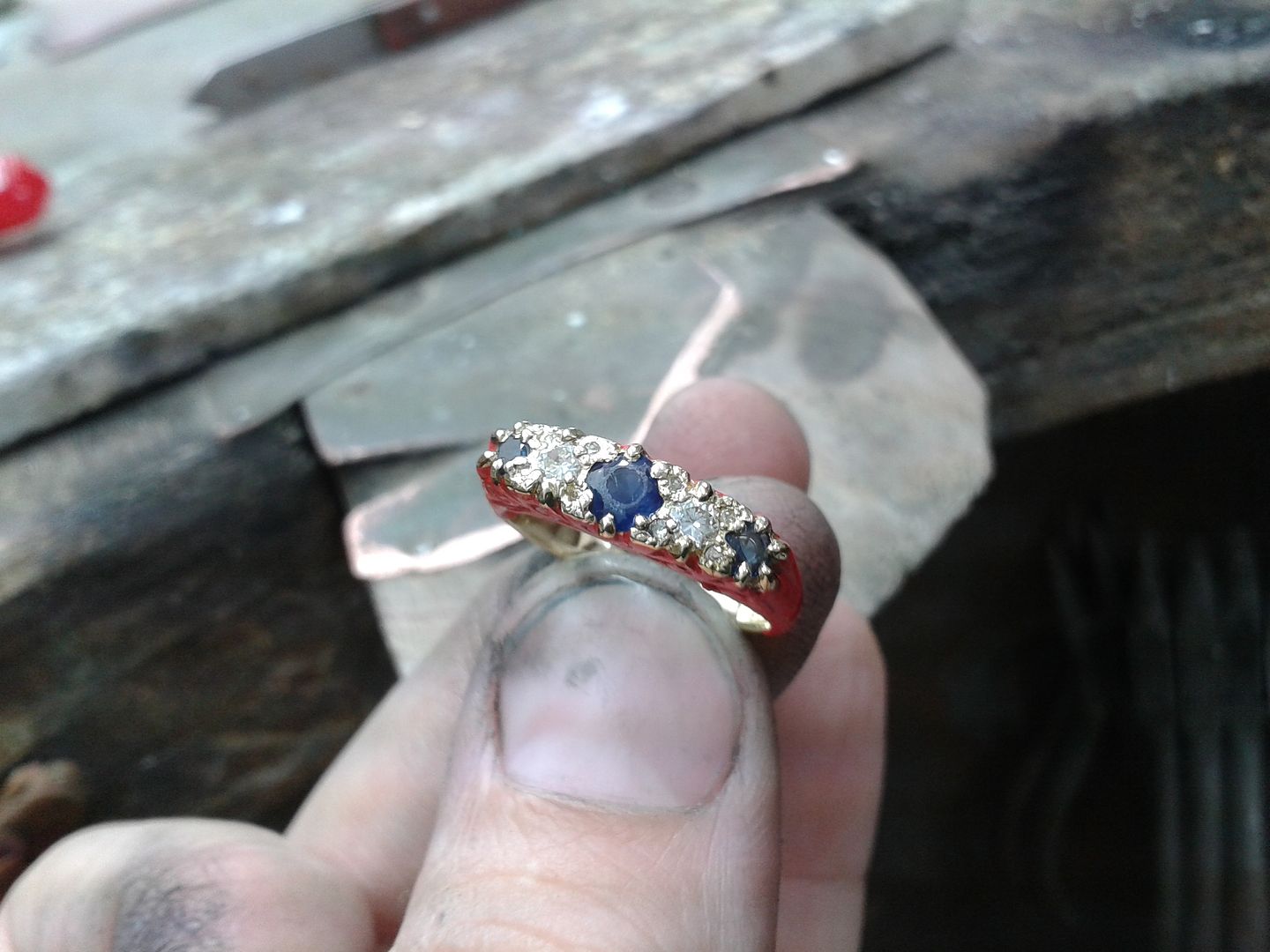
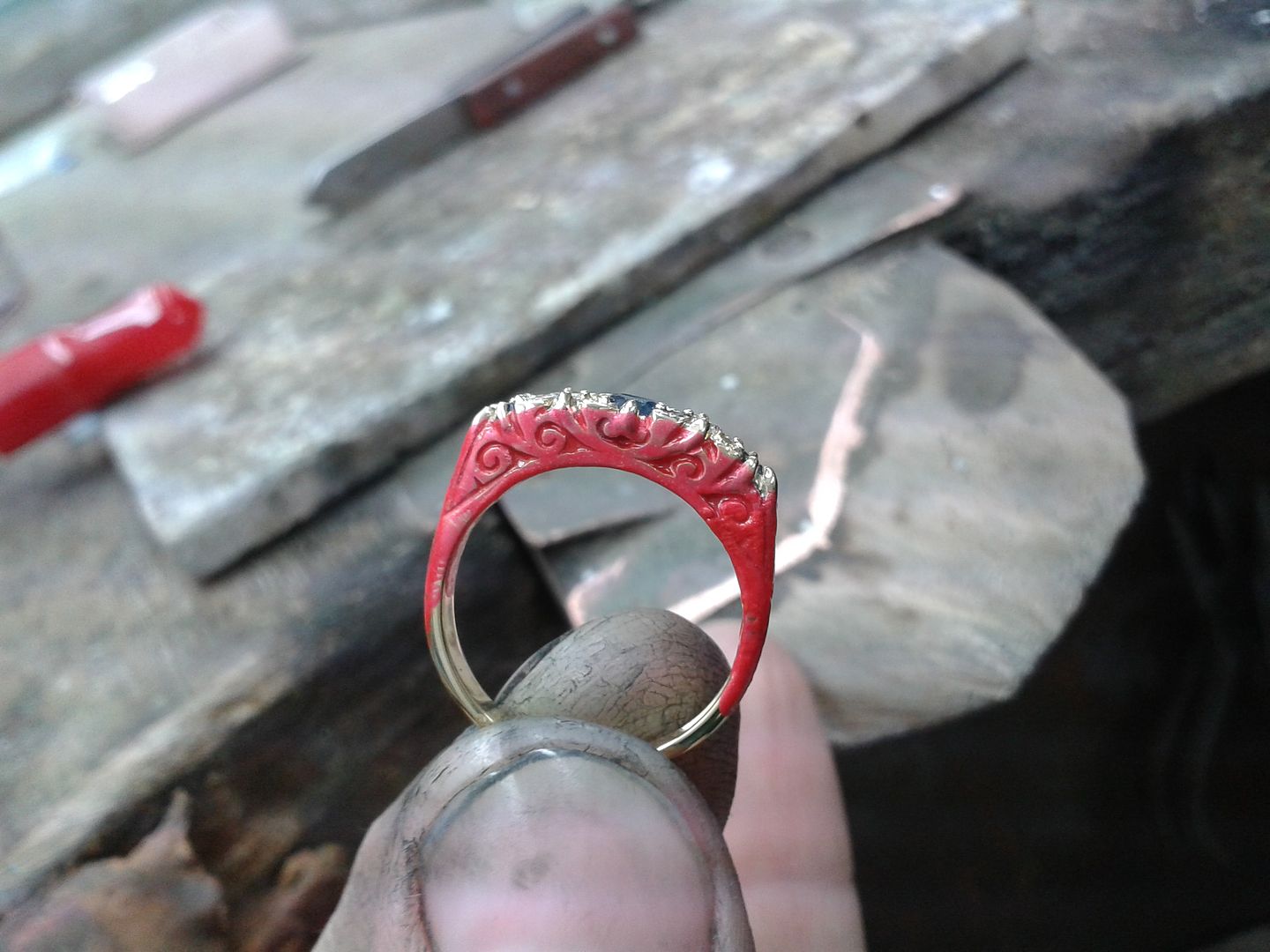
And plated. Sorry about the hair sticking out of the top of the ring. Its from the polishing mop and was removed afterward:
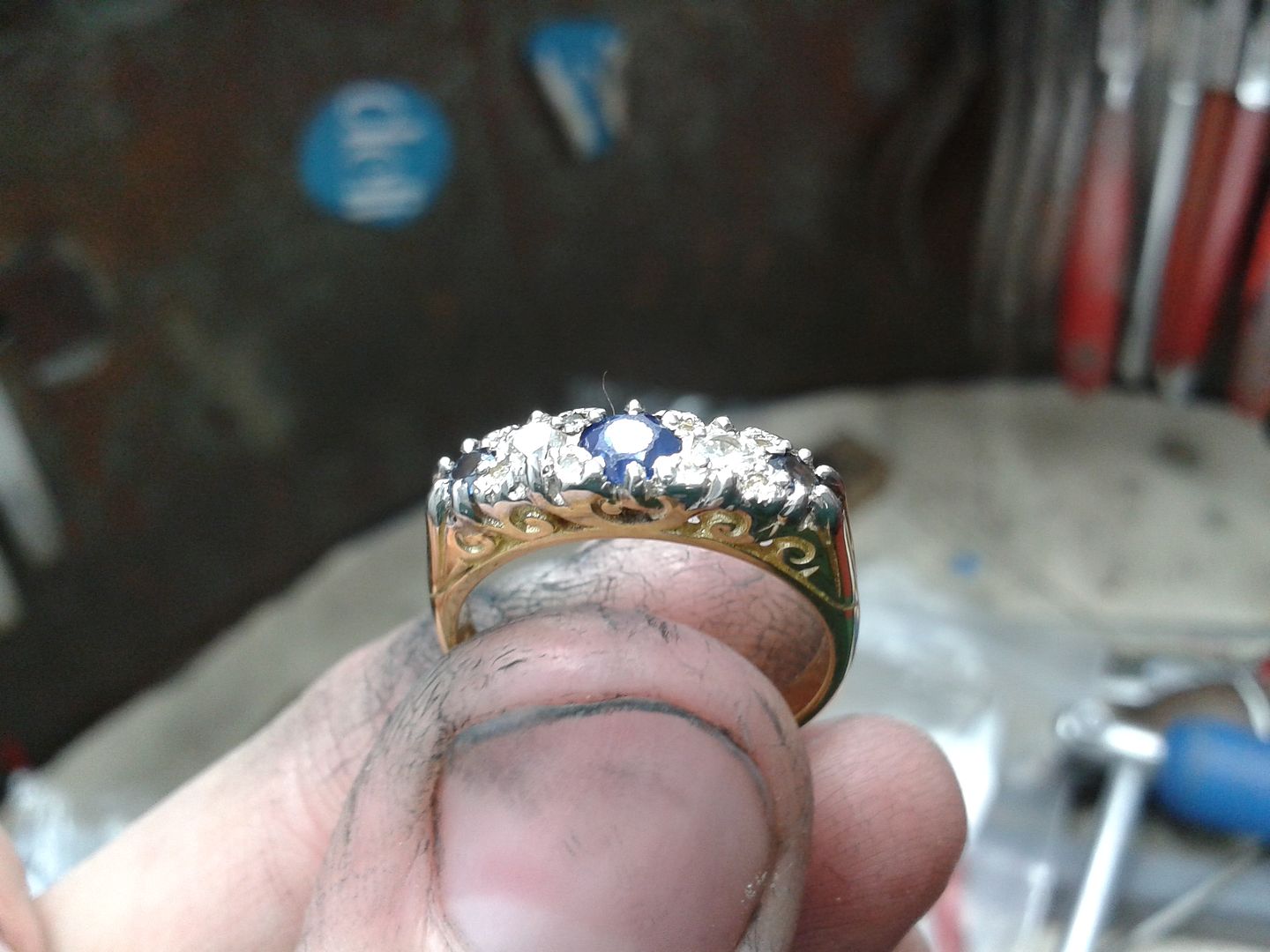
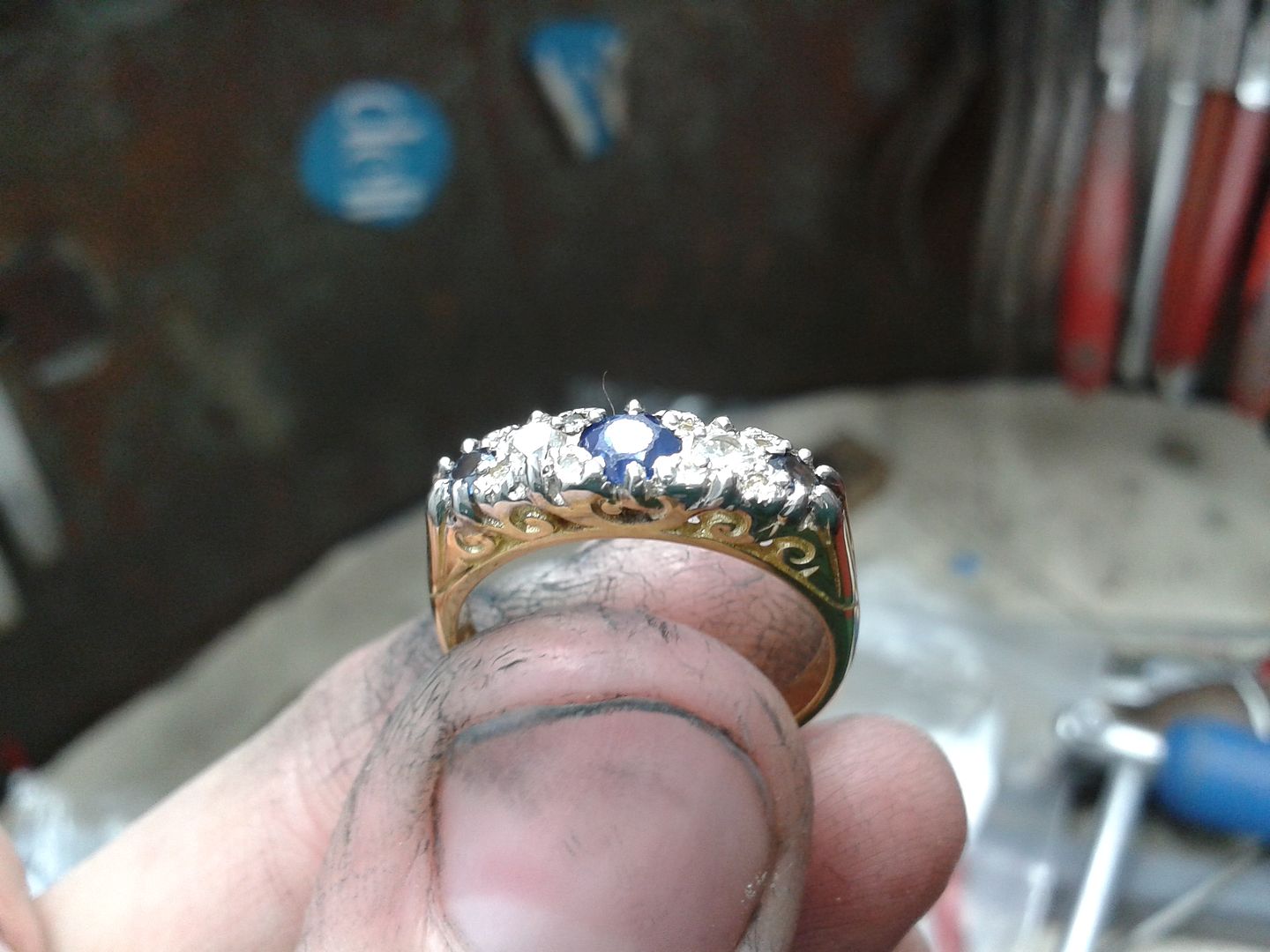
The phone pics don't do it justice but it was a really successful job.
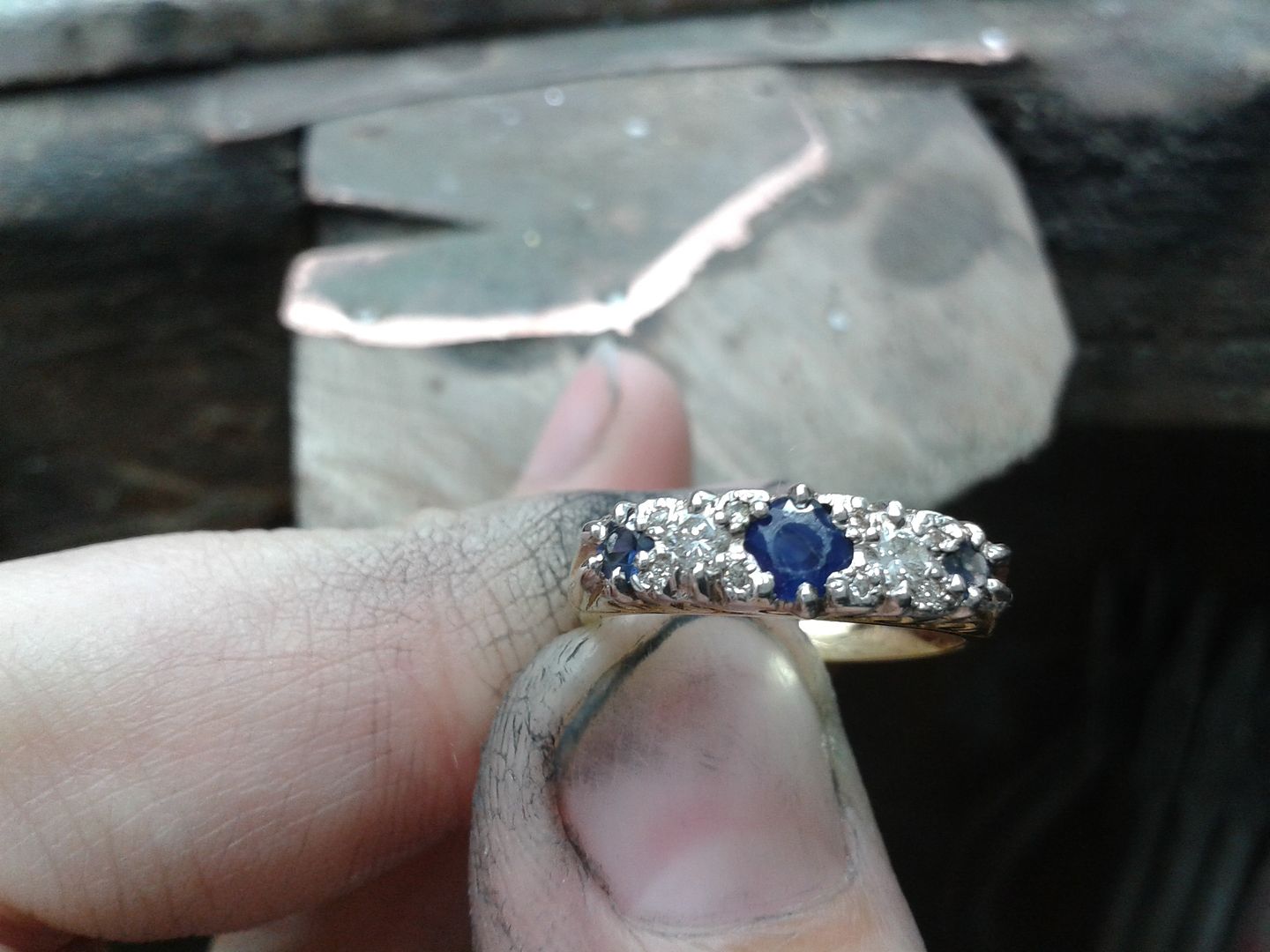
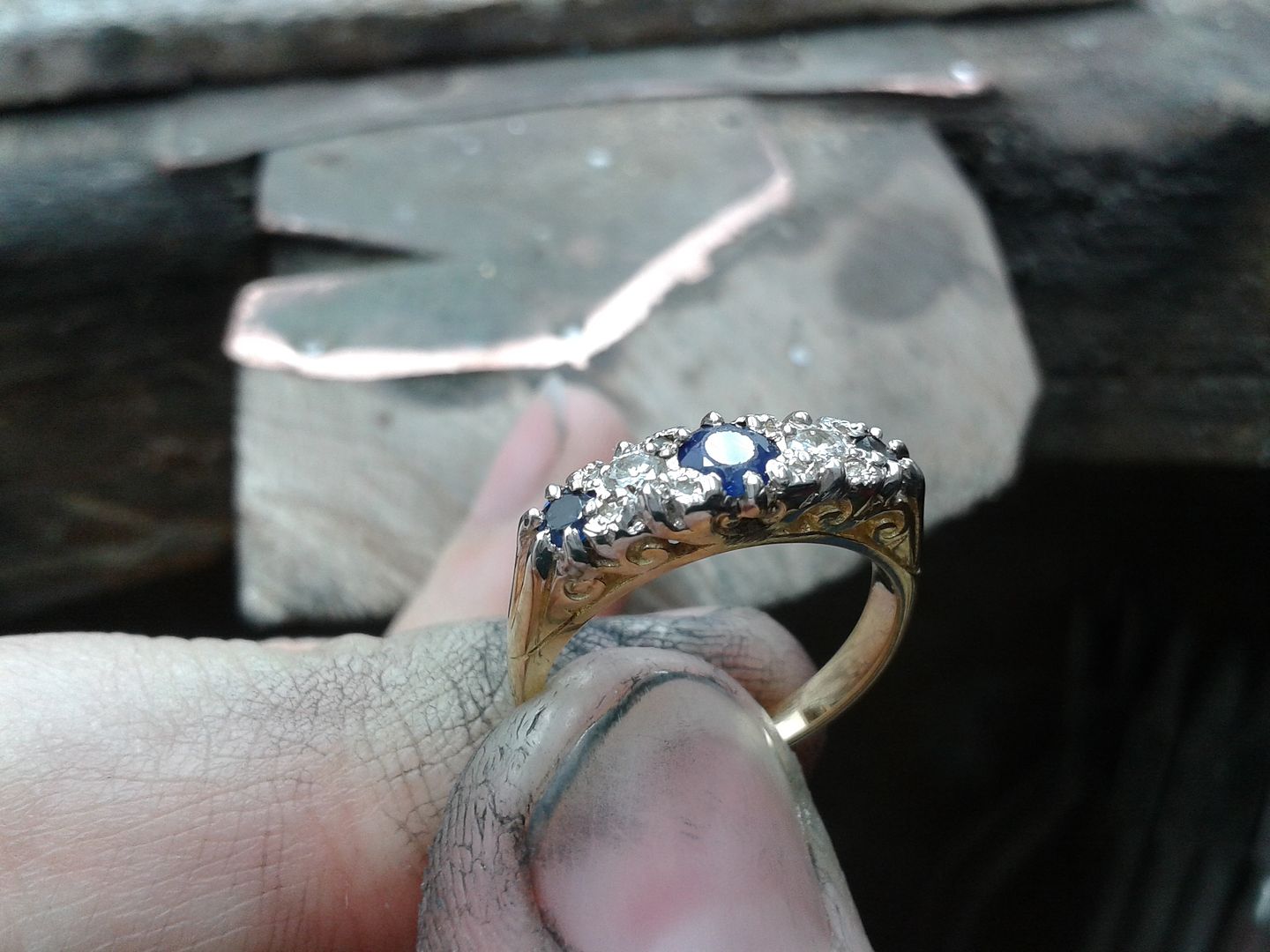
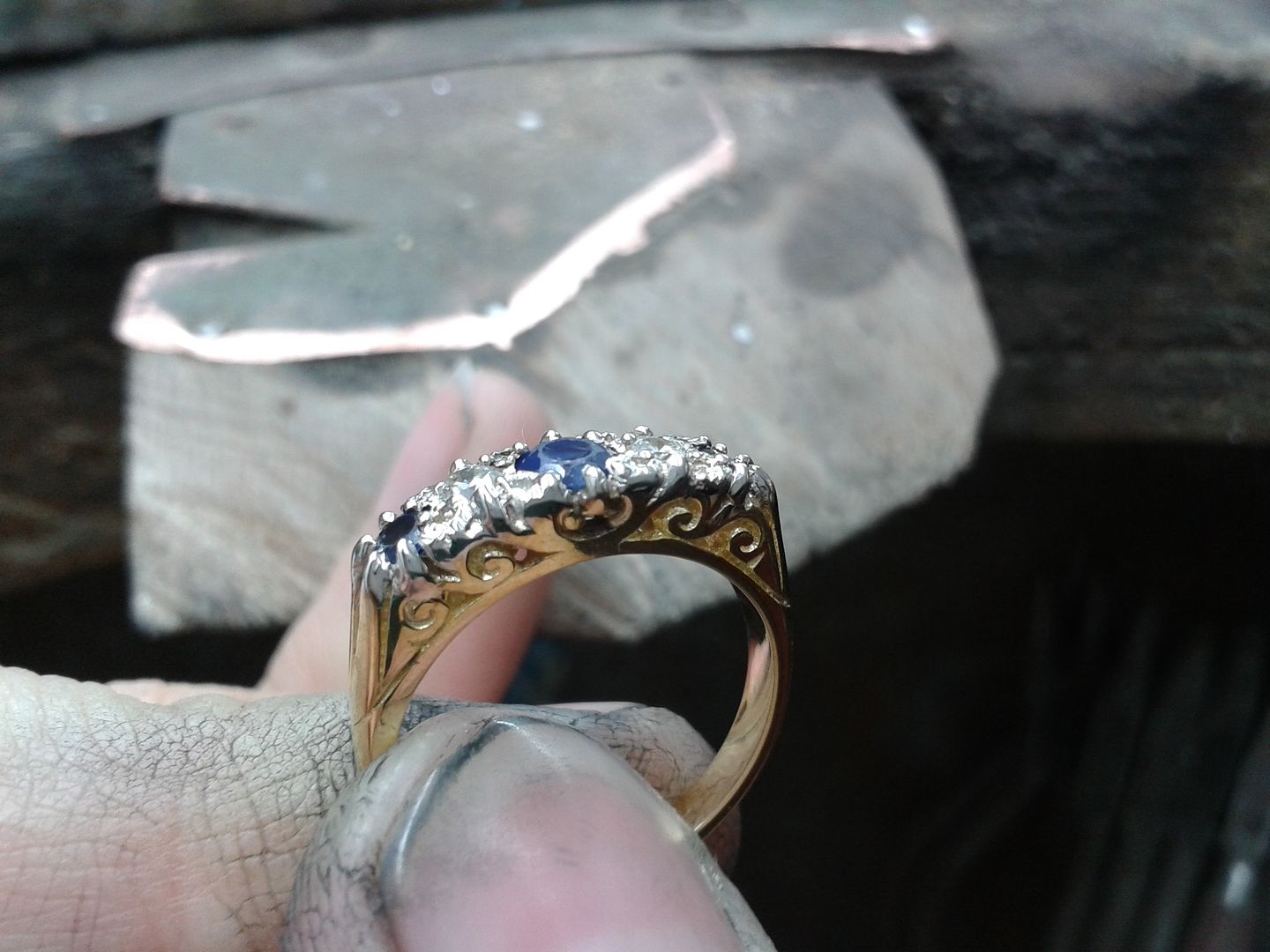
Before and after:
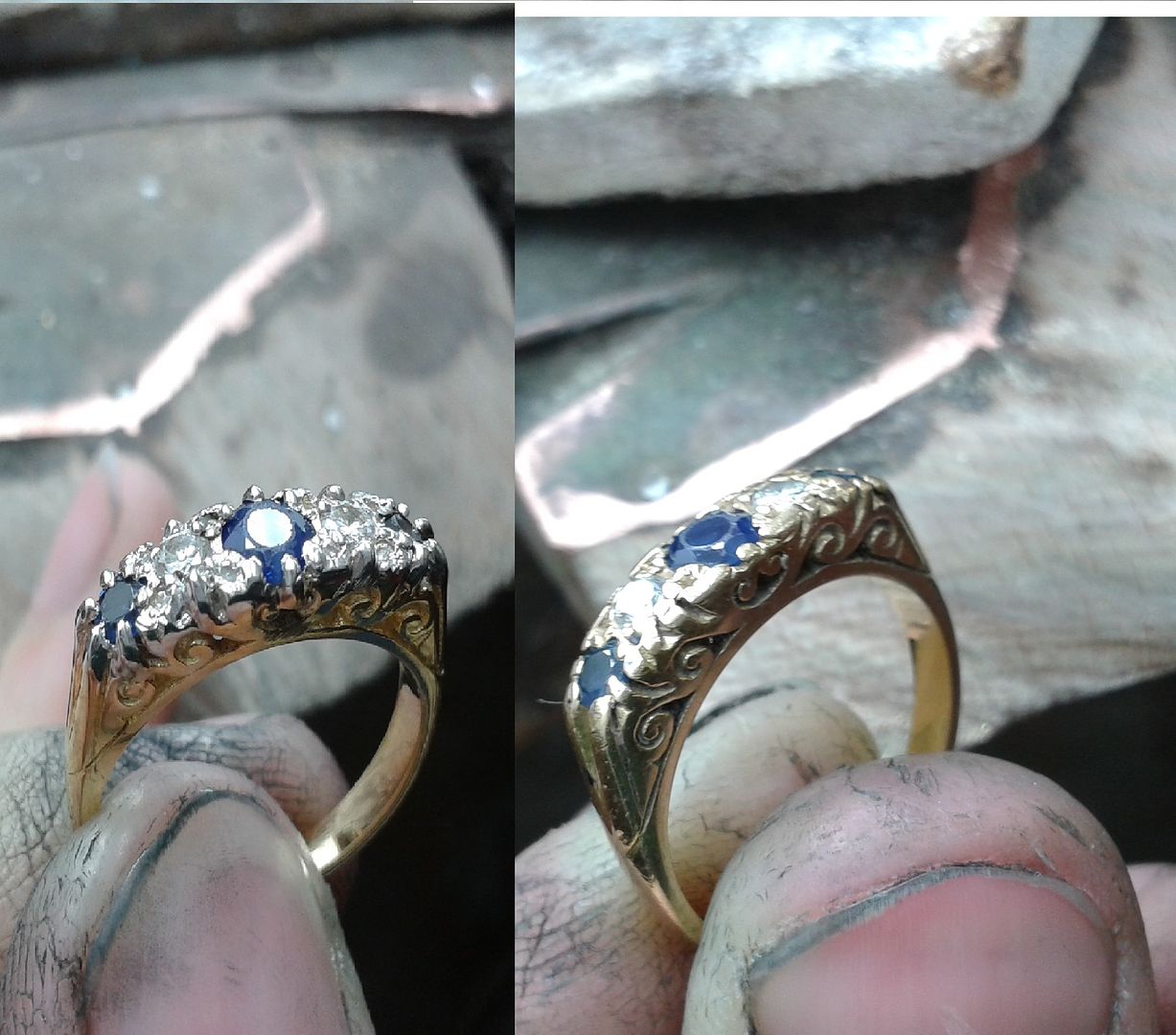
Eddie
Its not the one I'd originally planned on, owing to it being a very busy month and not having time to photograph and do the work (cannot complain at being busy) and me suffering from a fairly draining / all-encompassing stomach issue that is currently under investigation (can complain), but it does demonstrate the processes involved.
Take one pretty worn out and old sapphire and diamond ring. Its a very old fashioned item and has a hand carved construction that we have to maintain.
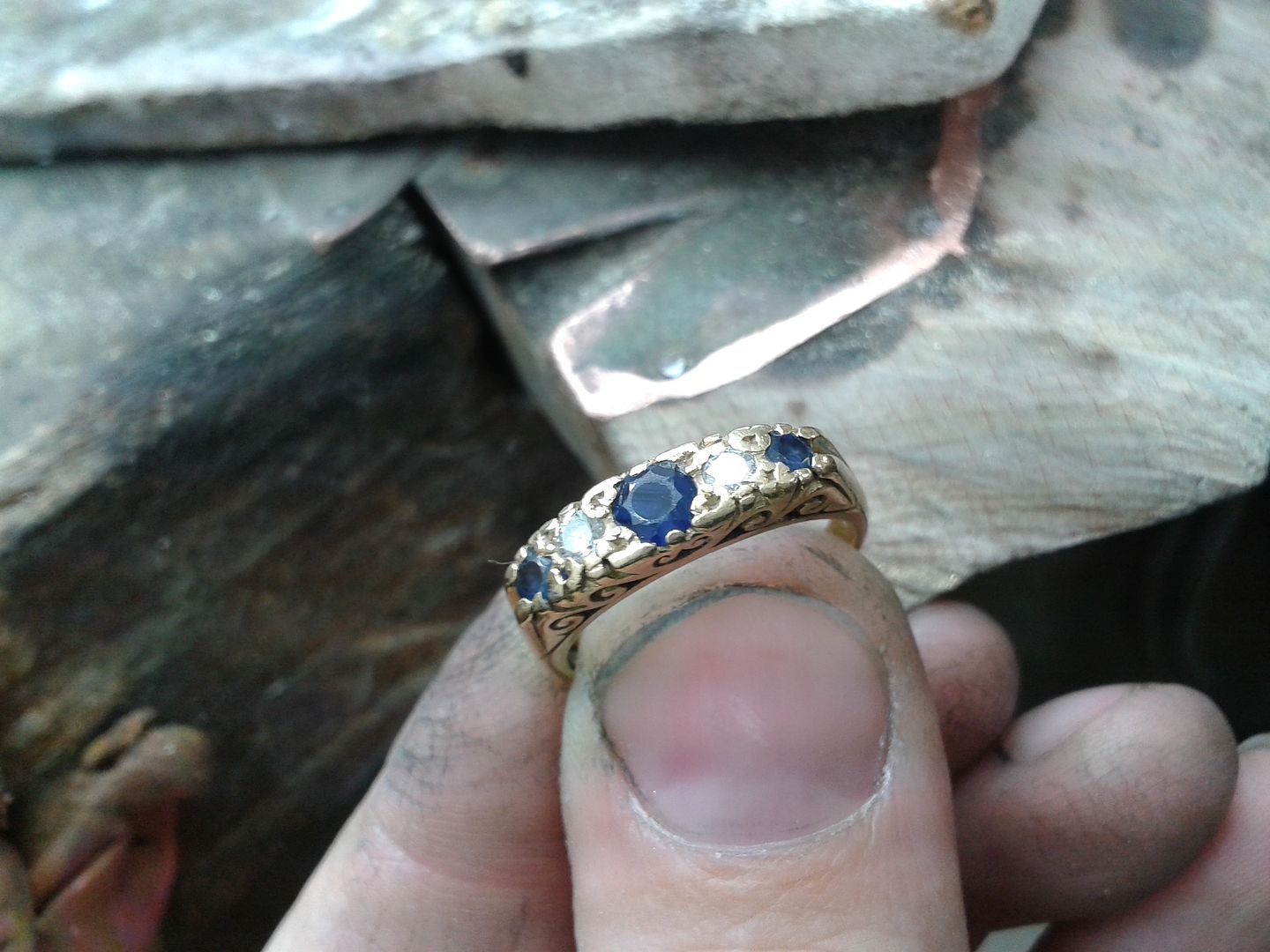
Note the 8 x missing small diamonds from between the main stones. We will replace these as part of the process:
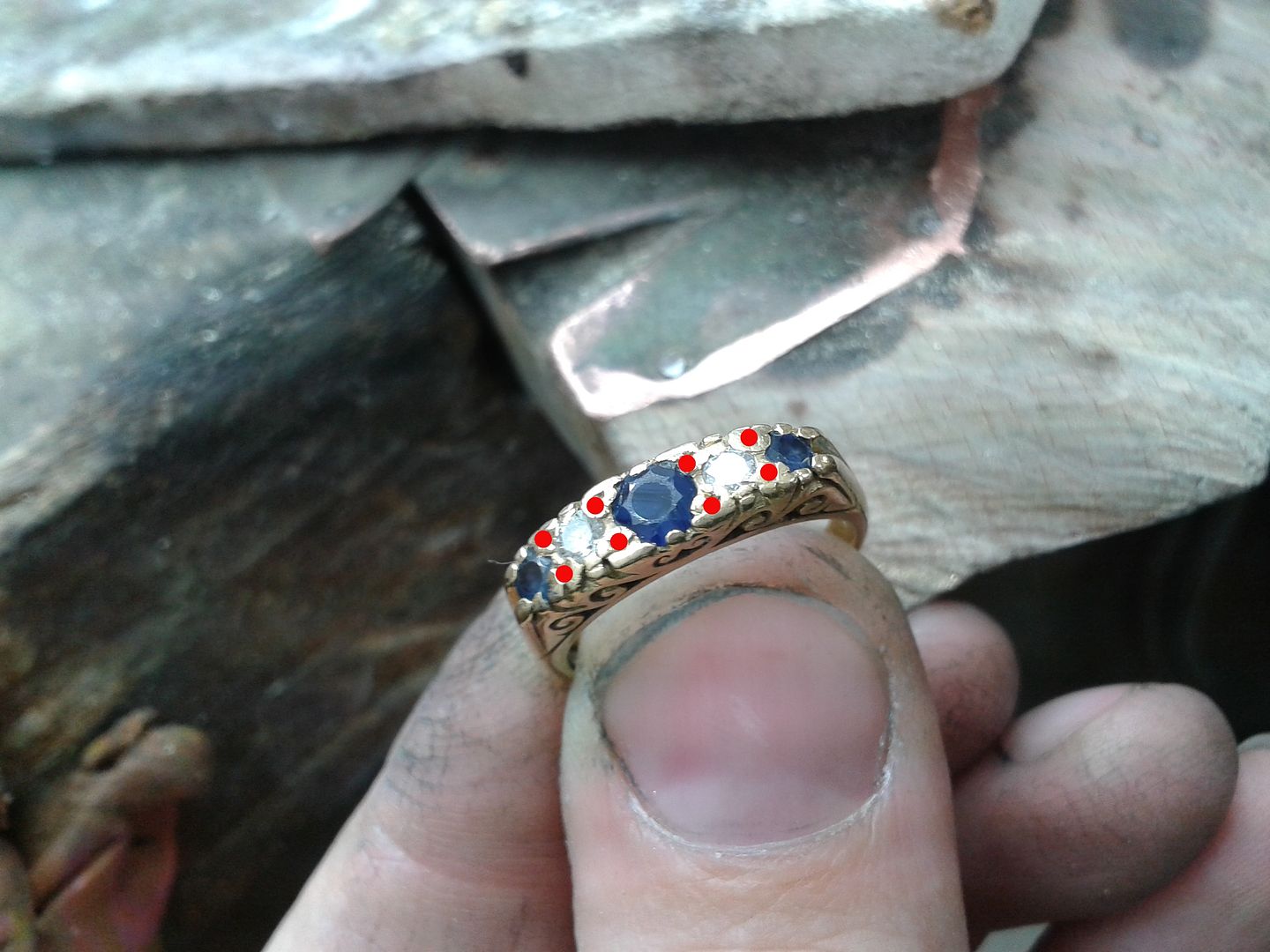
You can see from the picture here the condition of the sapphires. They are pretty worn and abraded. In some circumstances we'd have these removed and replaced or re-polished by a lapidary but the customer wants to maintain the 'used' look.... so they stay.
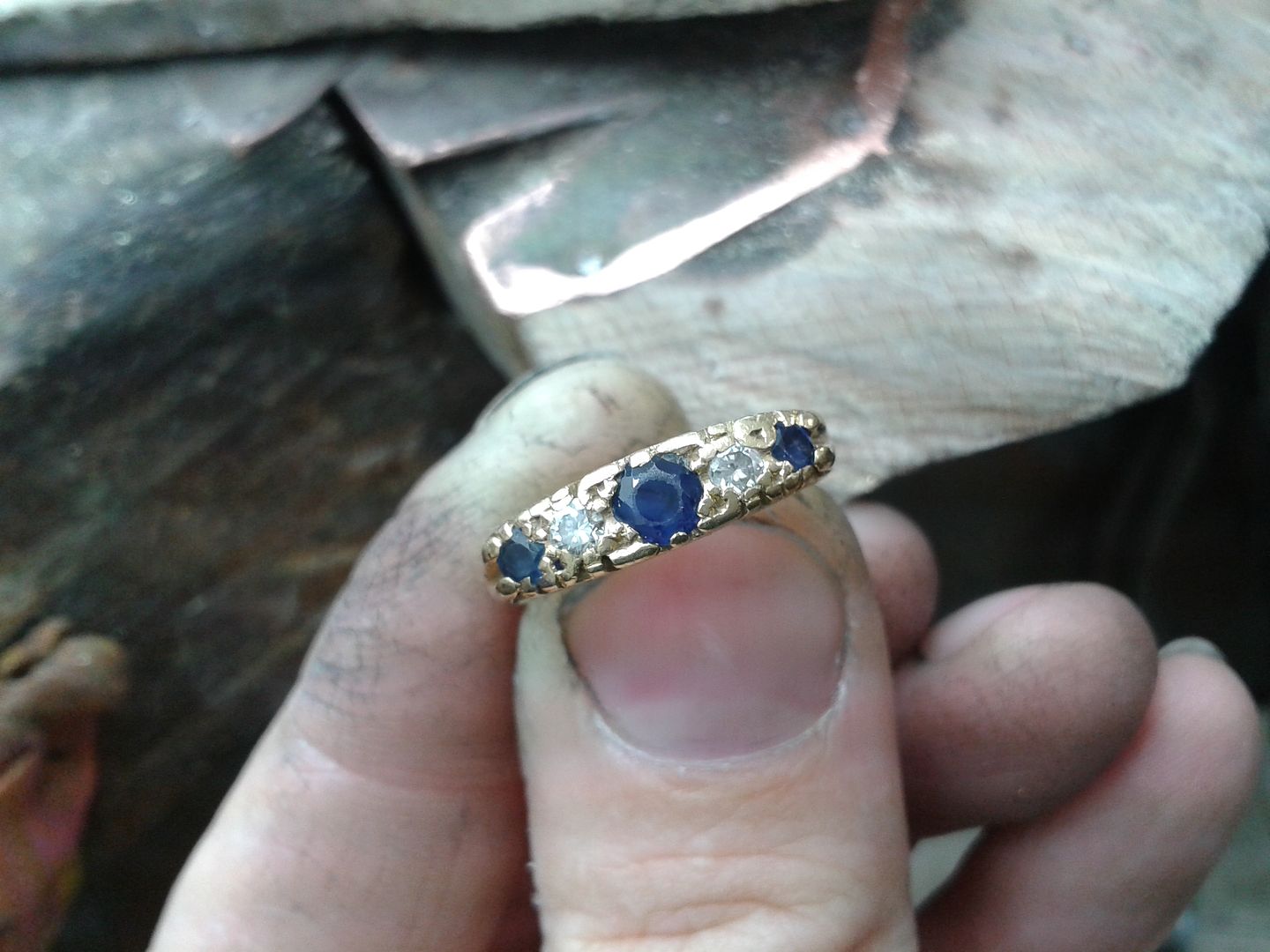
So, first job is to get the missing diamonds back in place. Here i have drilled the 8 x settings ready to take the new stones. They are only very small but do accent the other stones pretty well.
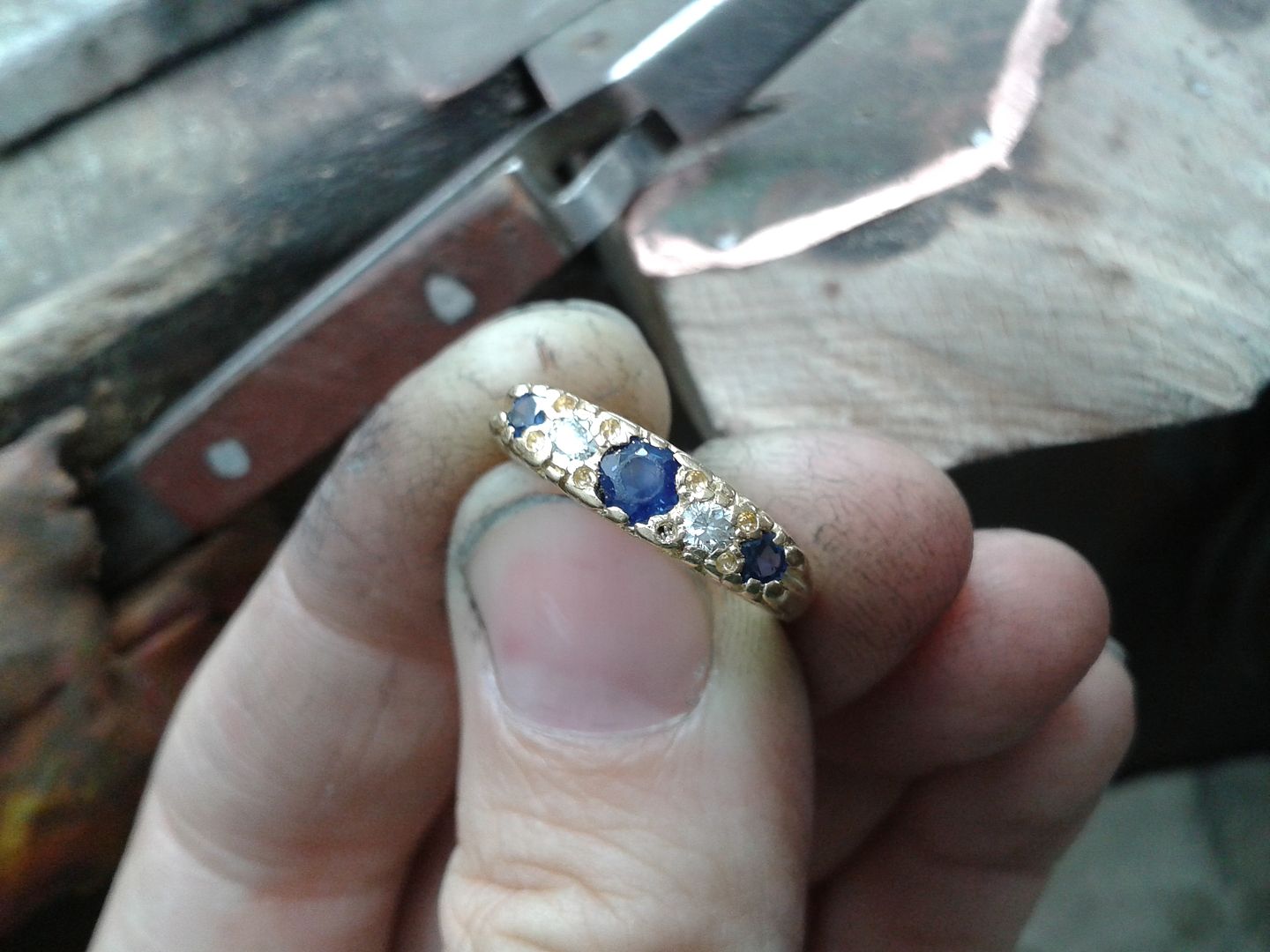
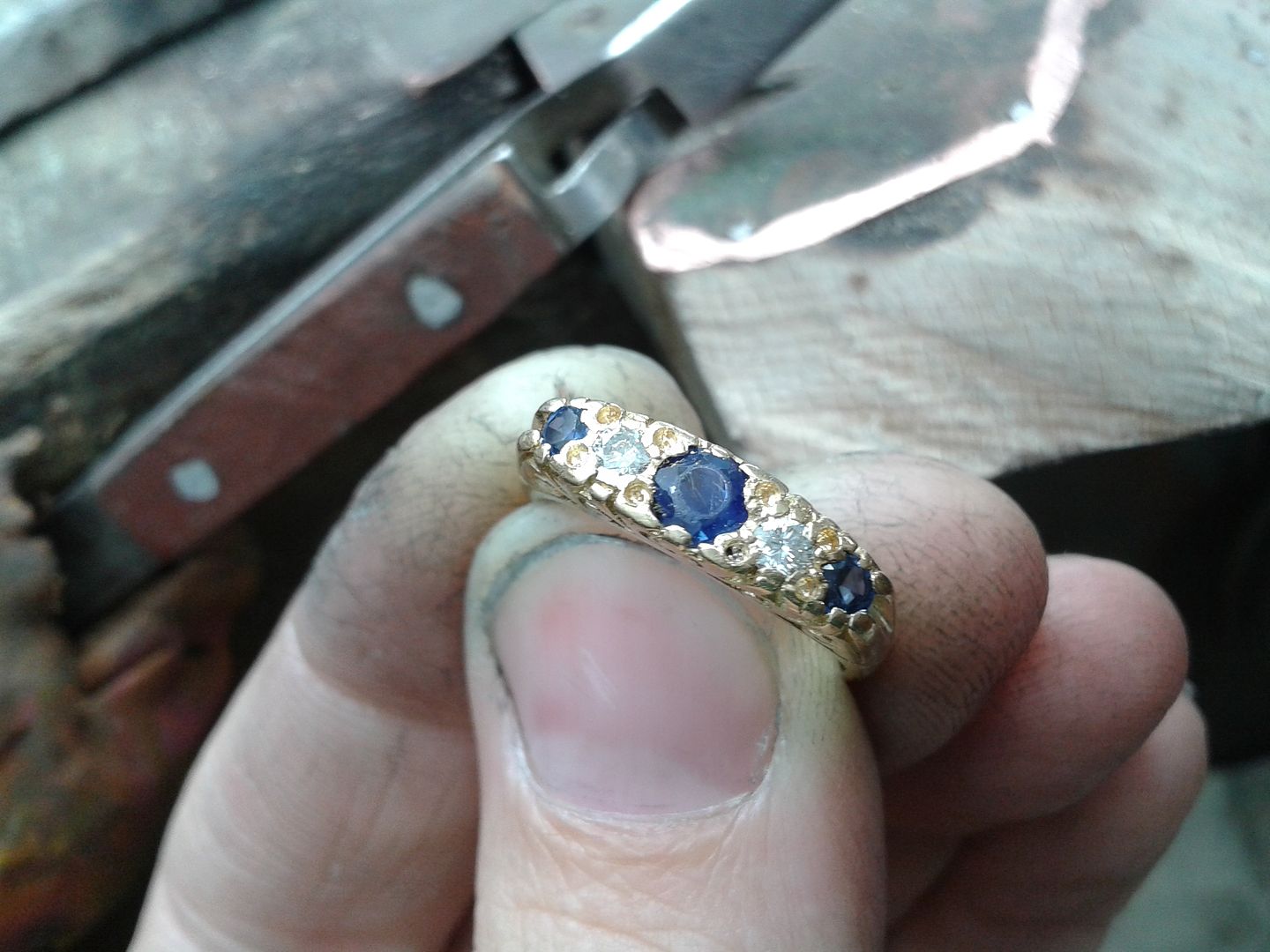
Apologies for no 'setting' pic but this is the 8 diamonds now set and ready for other work to start.
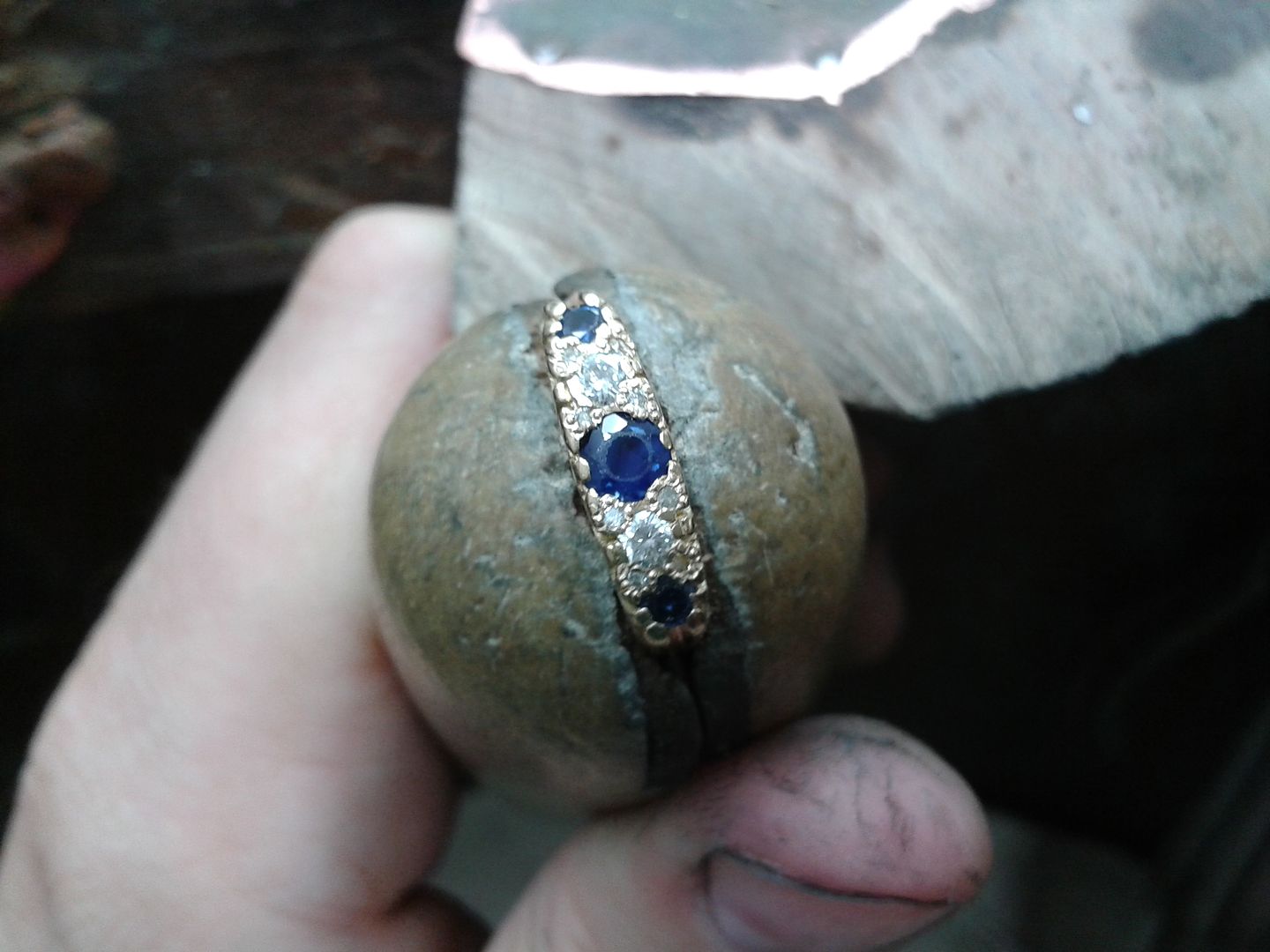
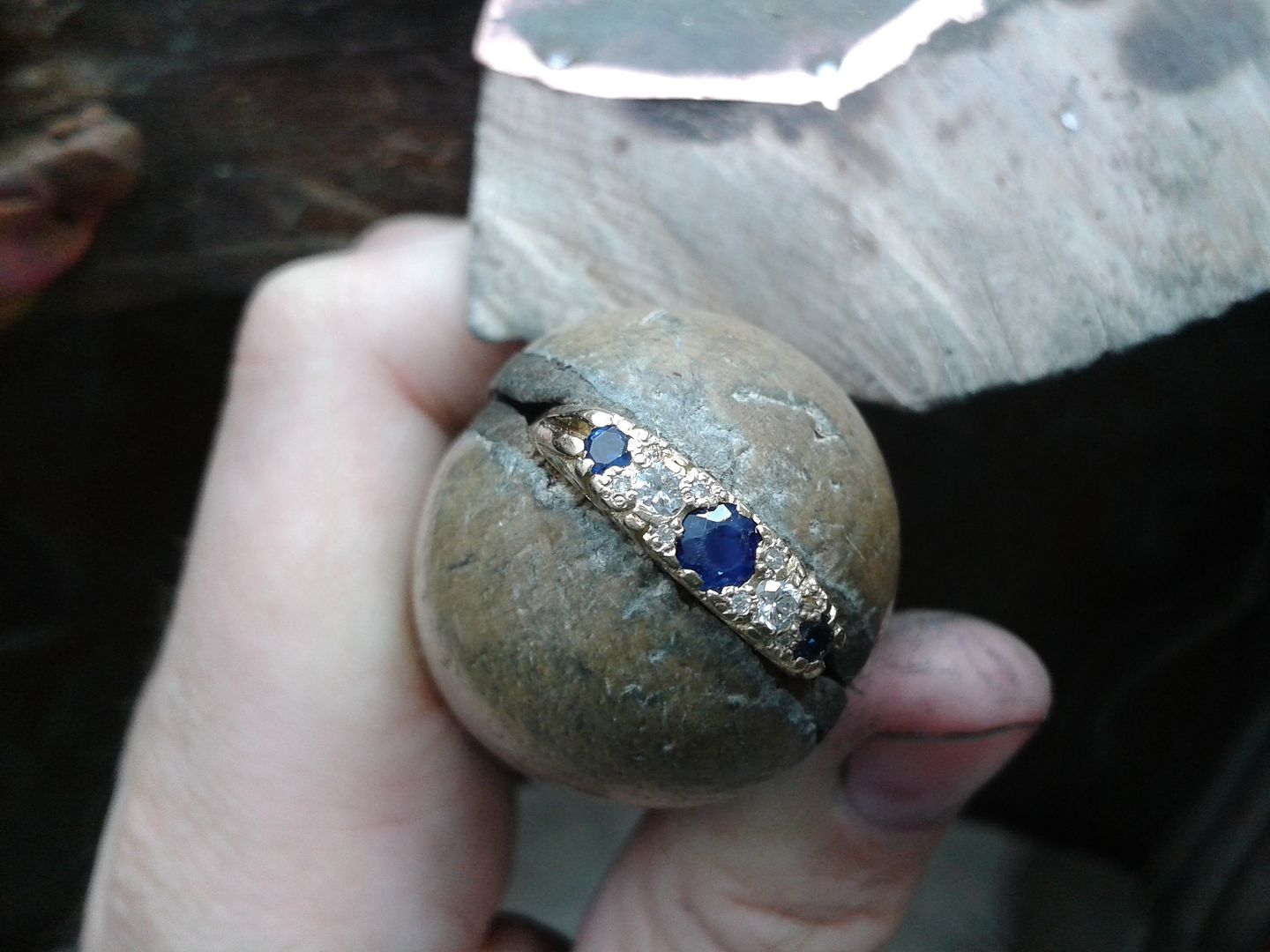
The next thing to do is to remove the old claws that hold the sapphires and larger diamonds. Look closely and you can see where ive filed the old ones down to the base:
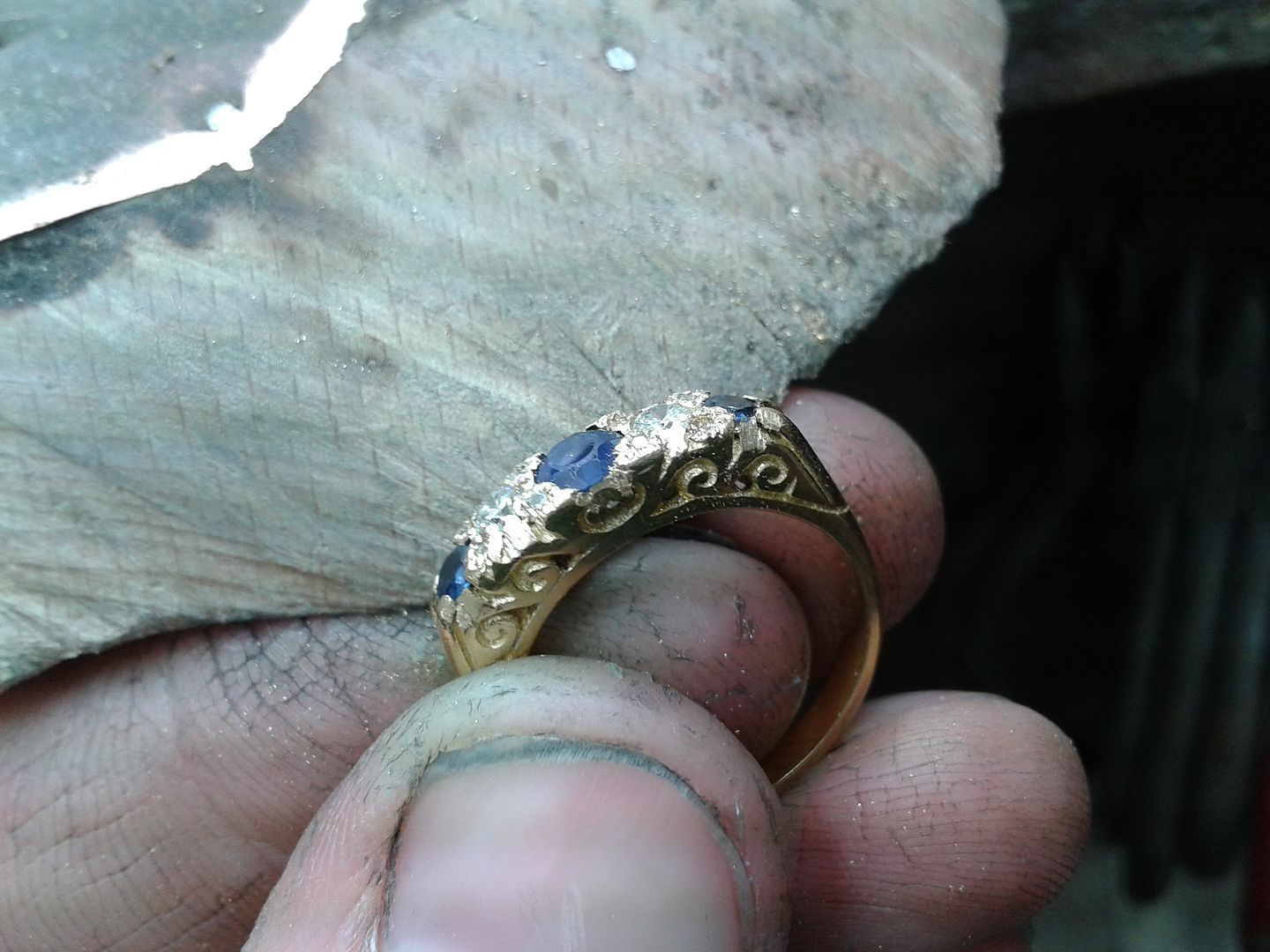
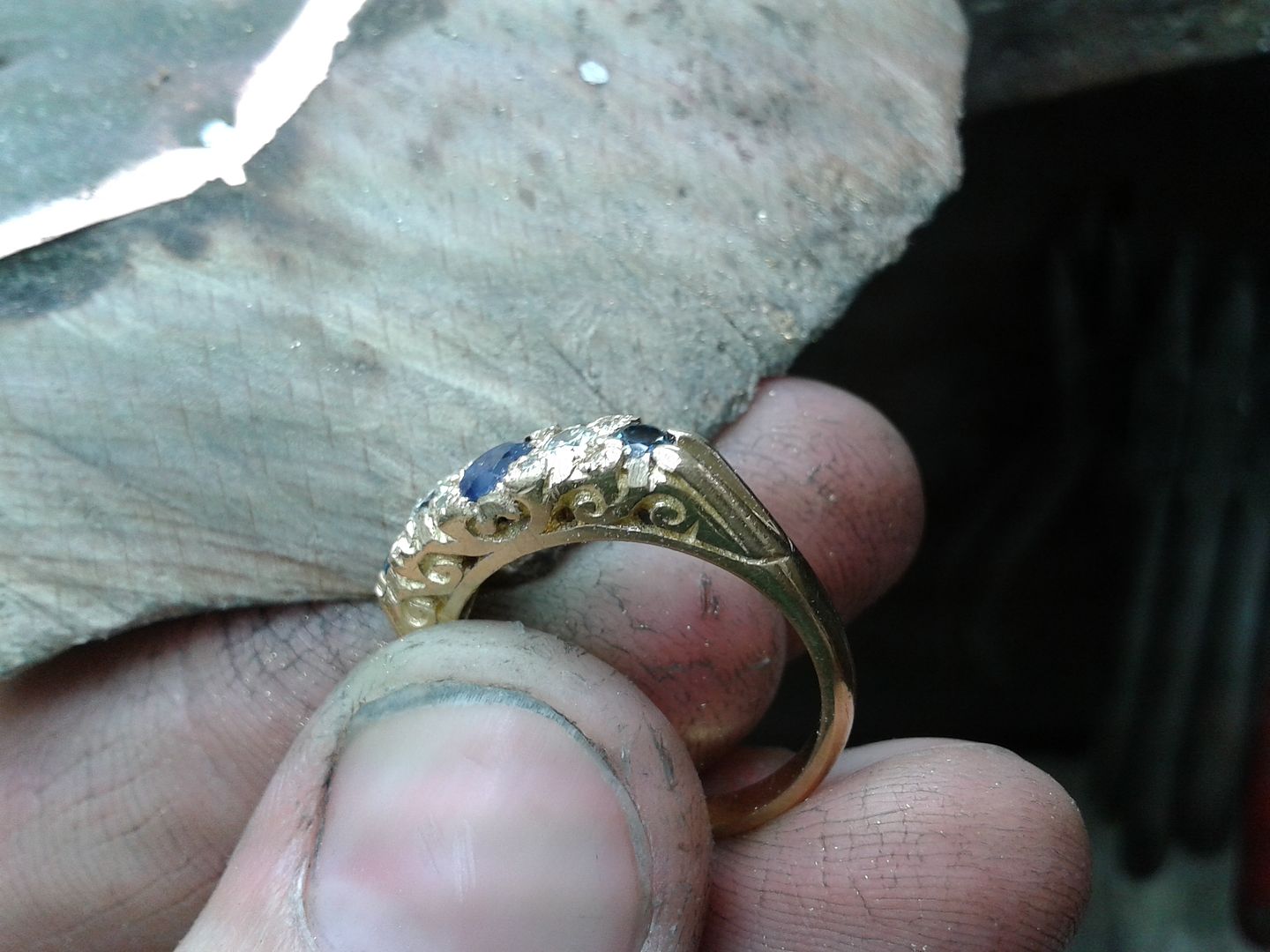
These are claws. They are cut in varying sizes (job dependant) from solid 18ct yellow gold bar that we roll down (without annealing) to the required thickness. We dont anneal the claw material before cutting as it makes it easier to cut. It'll soften up nicely when i solder it on. Same process for white claws, except we use rolled down 18ct white bar.
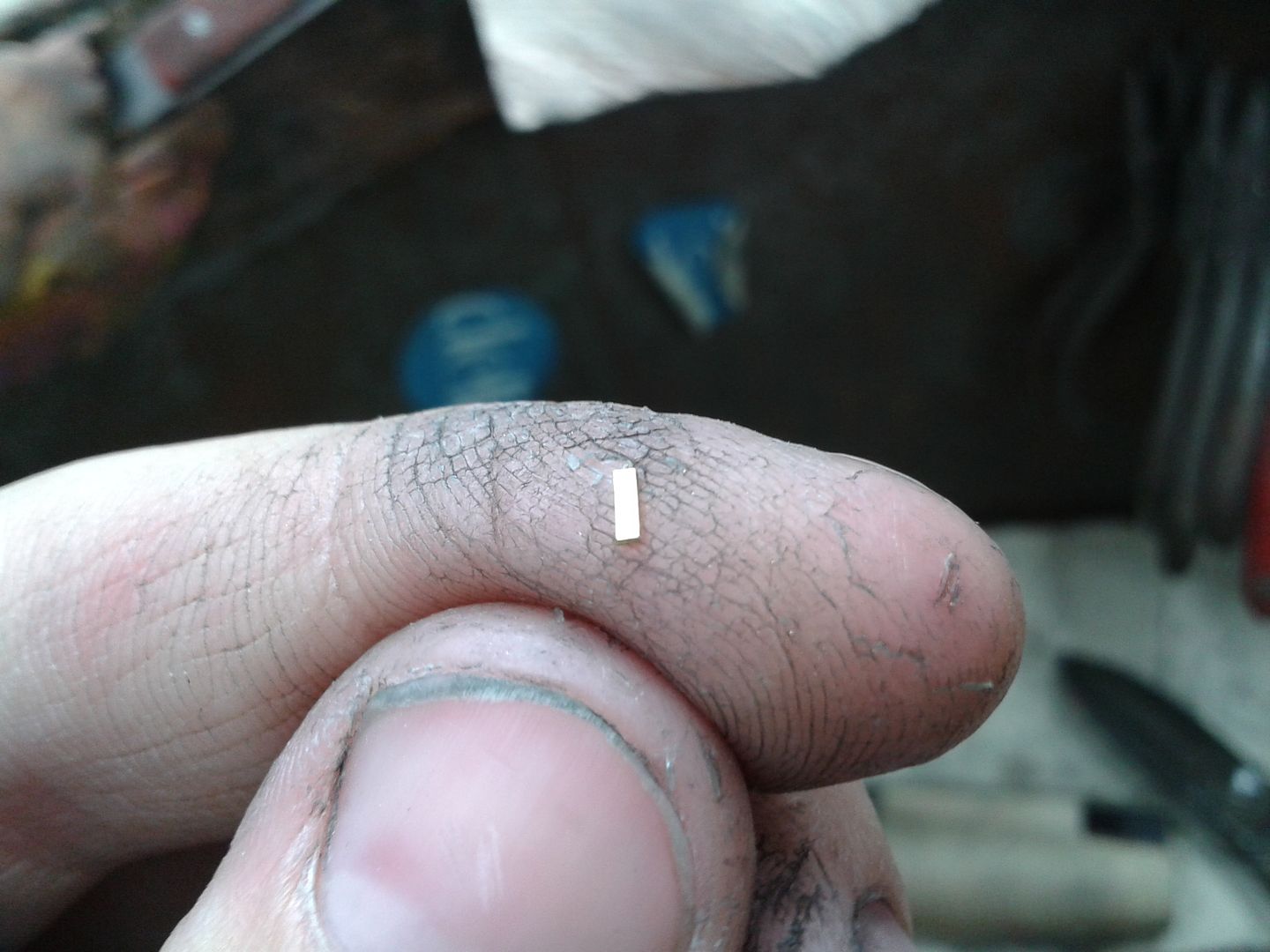
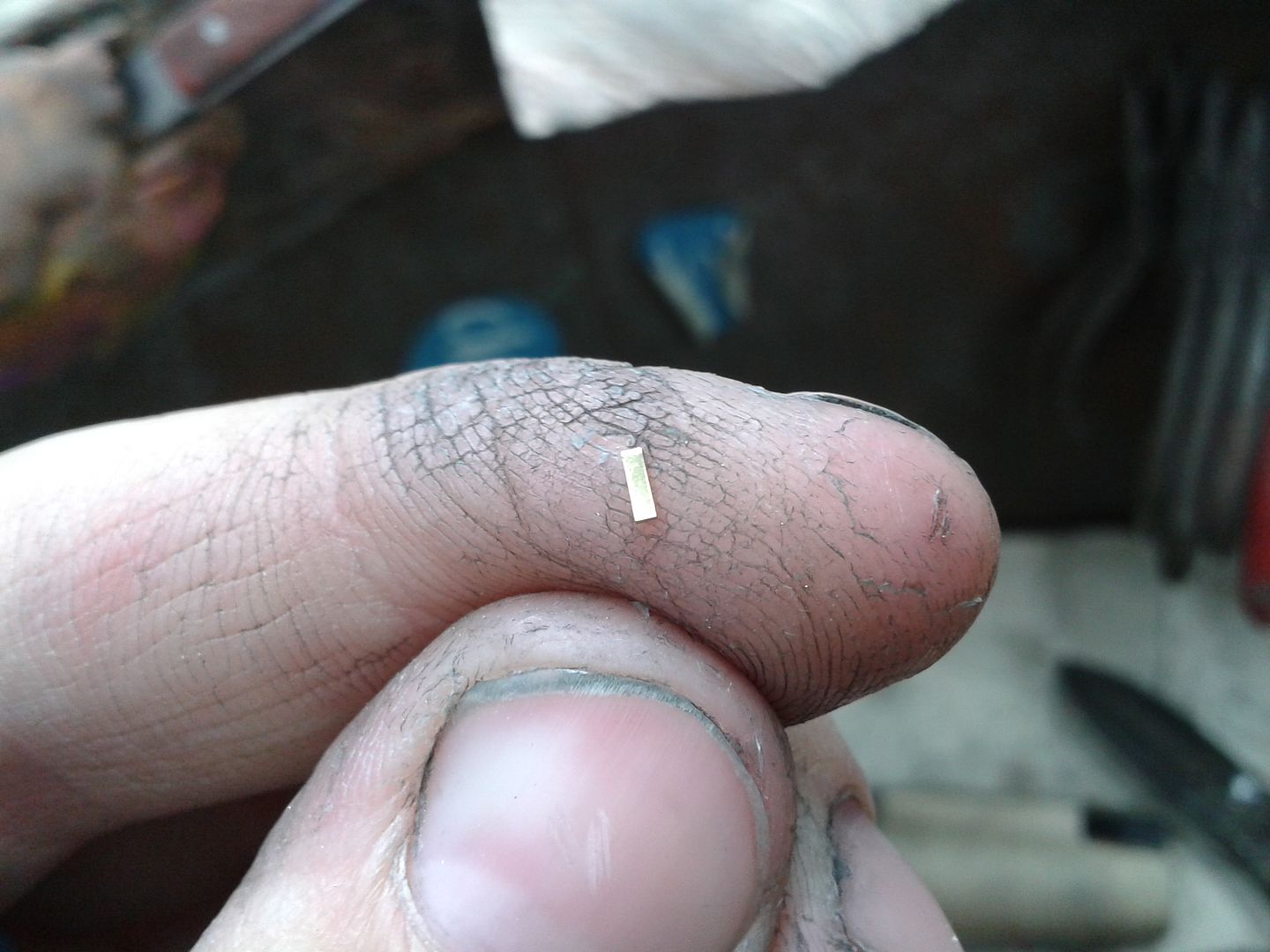
Starting on one side i solder the 5 main structural claws that hold in the sapphires and diamonds. There are 2 more on each end that i'll do once all the stones are secure enough. Note that we are maintaining the original claw pattern as per the sides.
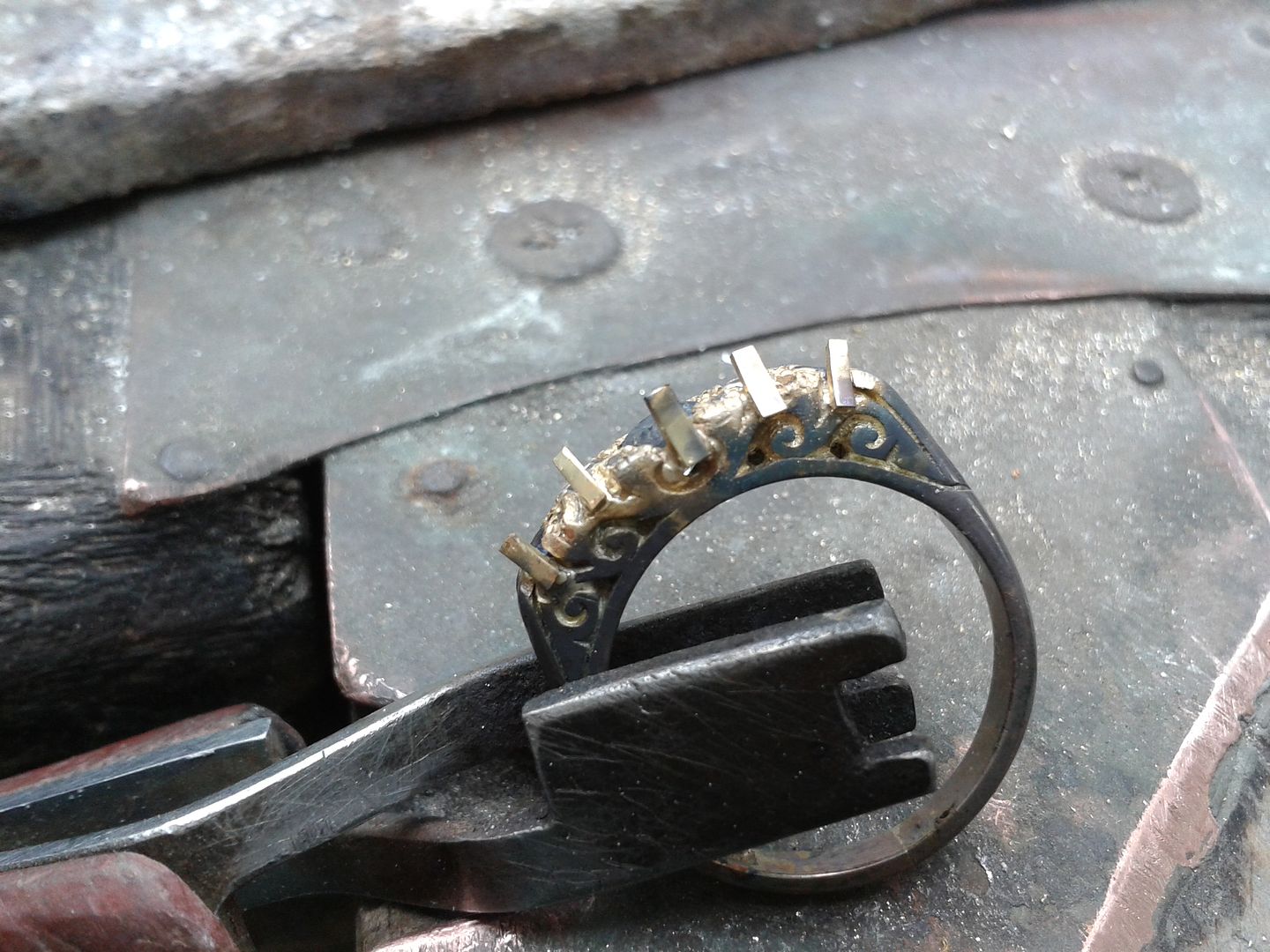
Other side filed down to the bases. Point to note: The diamonds are protected from the heat by applying borax. The sapphires dont respond well to borax and are easily damaged by the borax corrosive properties, leaving the surface cloudy and damaged. So long as the sapphires don't take direct heat they cope well with high temperatures. This is why claw work can be so tricky. Knowing your stones and getting the heat right.
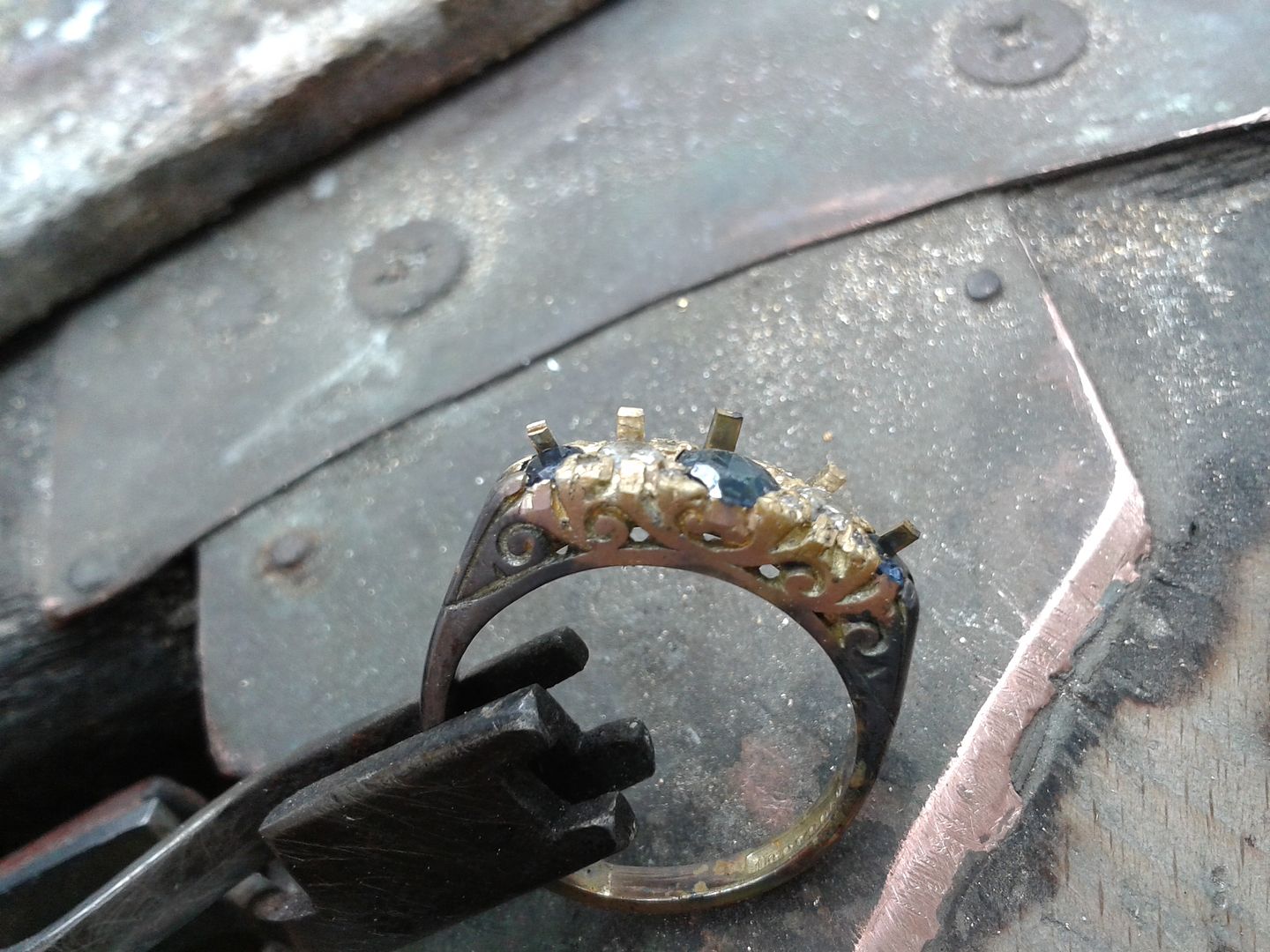
5 more claws applied and in place:
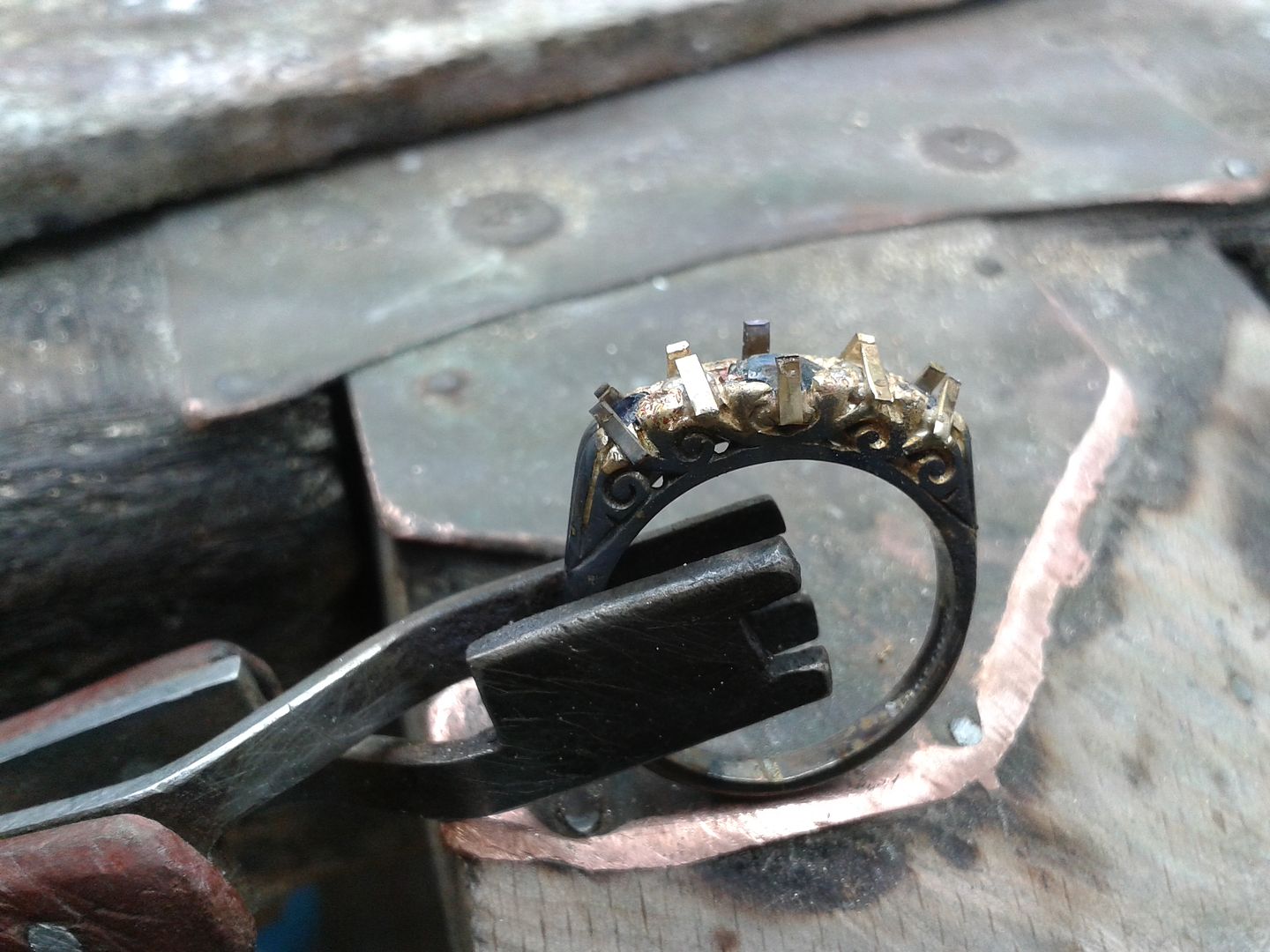
The 10 claws are then pressed over the sapphires and diamonds and then cut down in length to keep them out of the way of further work. Note the 2 other claws on each end that still need to be replaced.
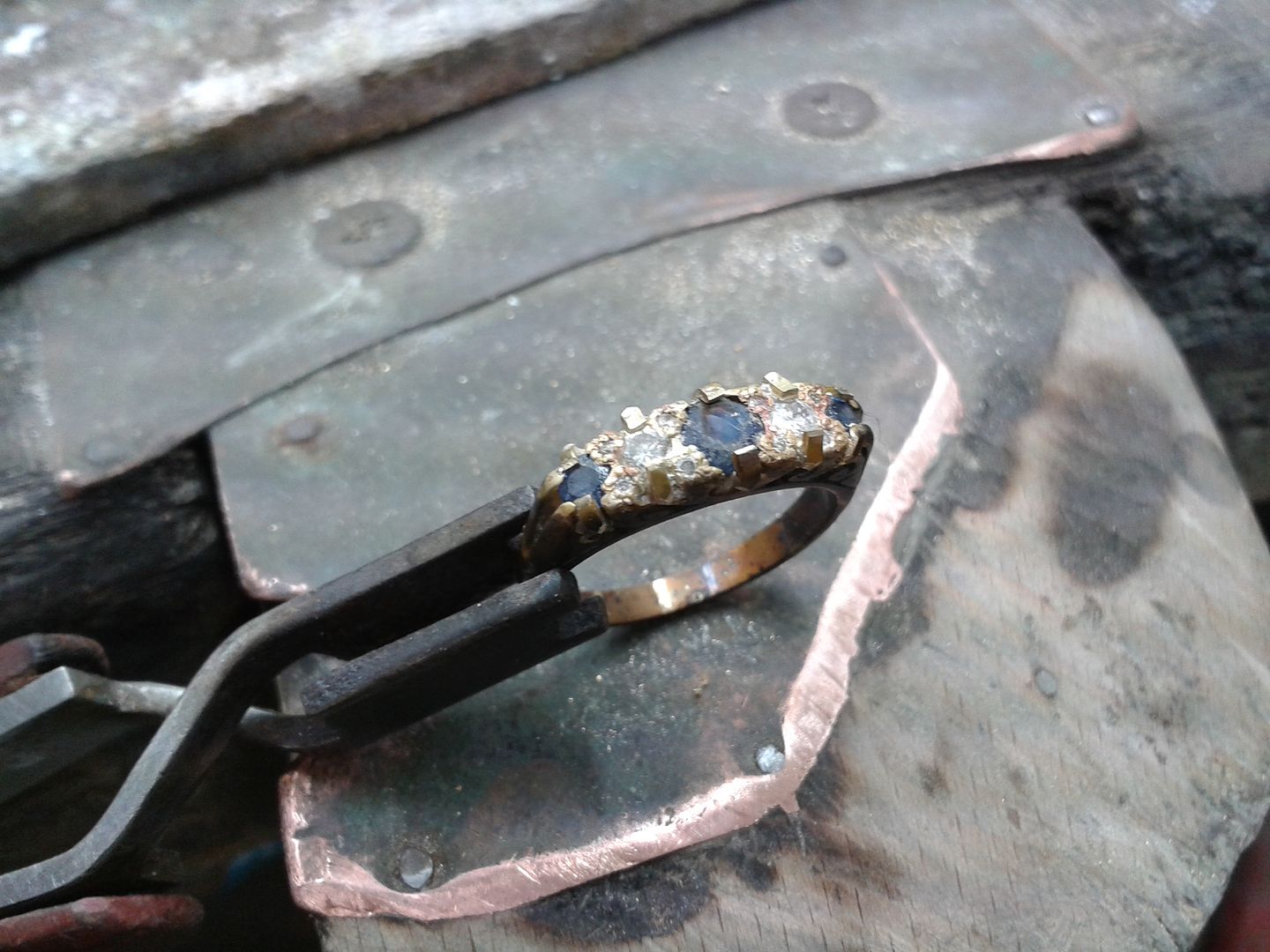
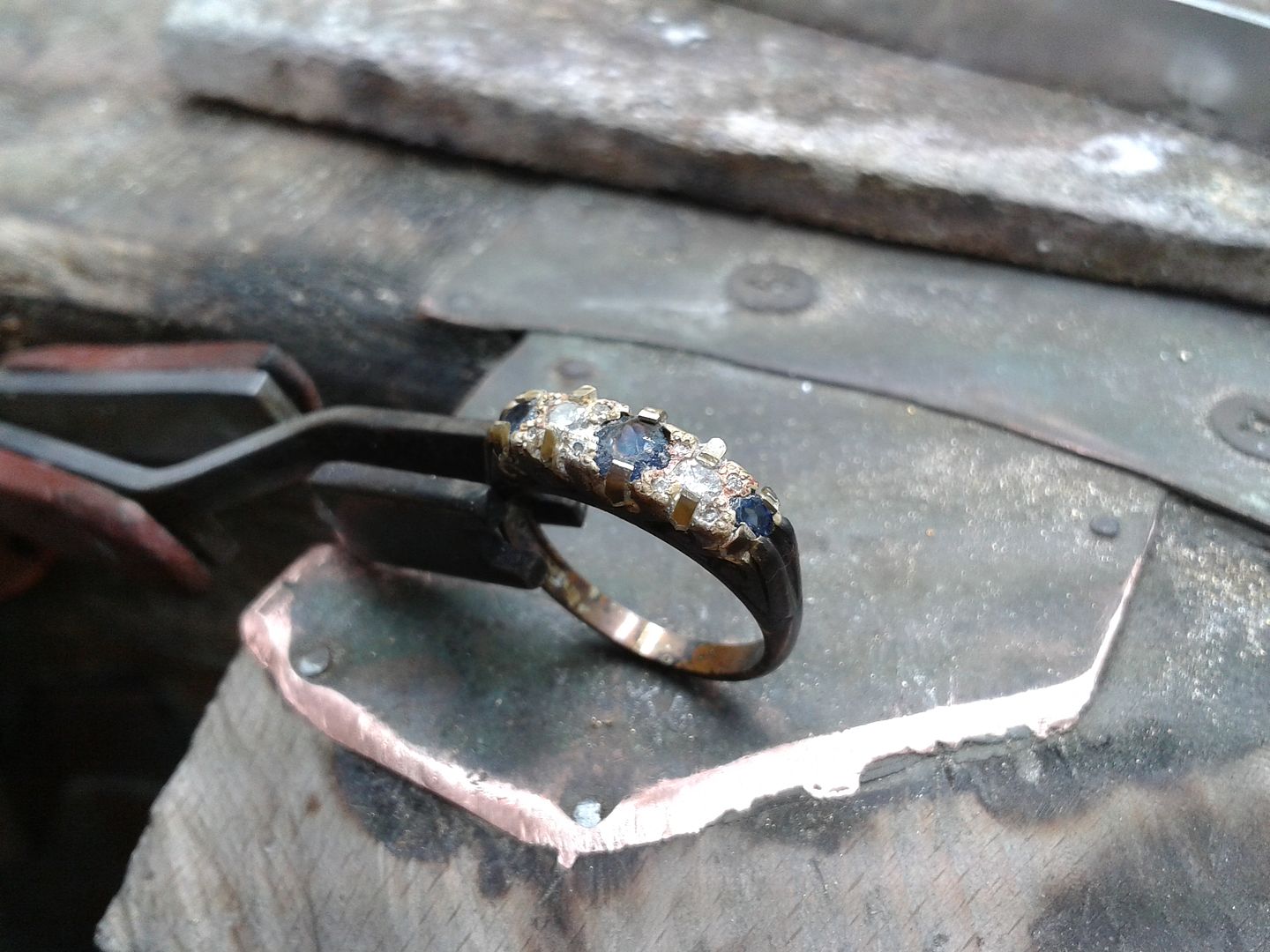
2 x end claws filed down:
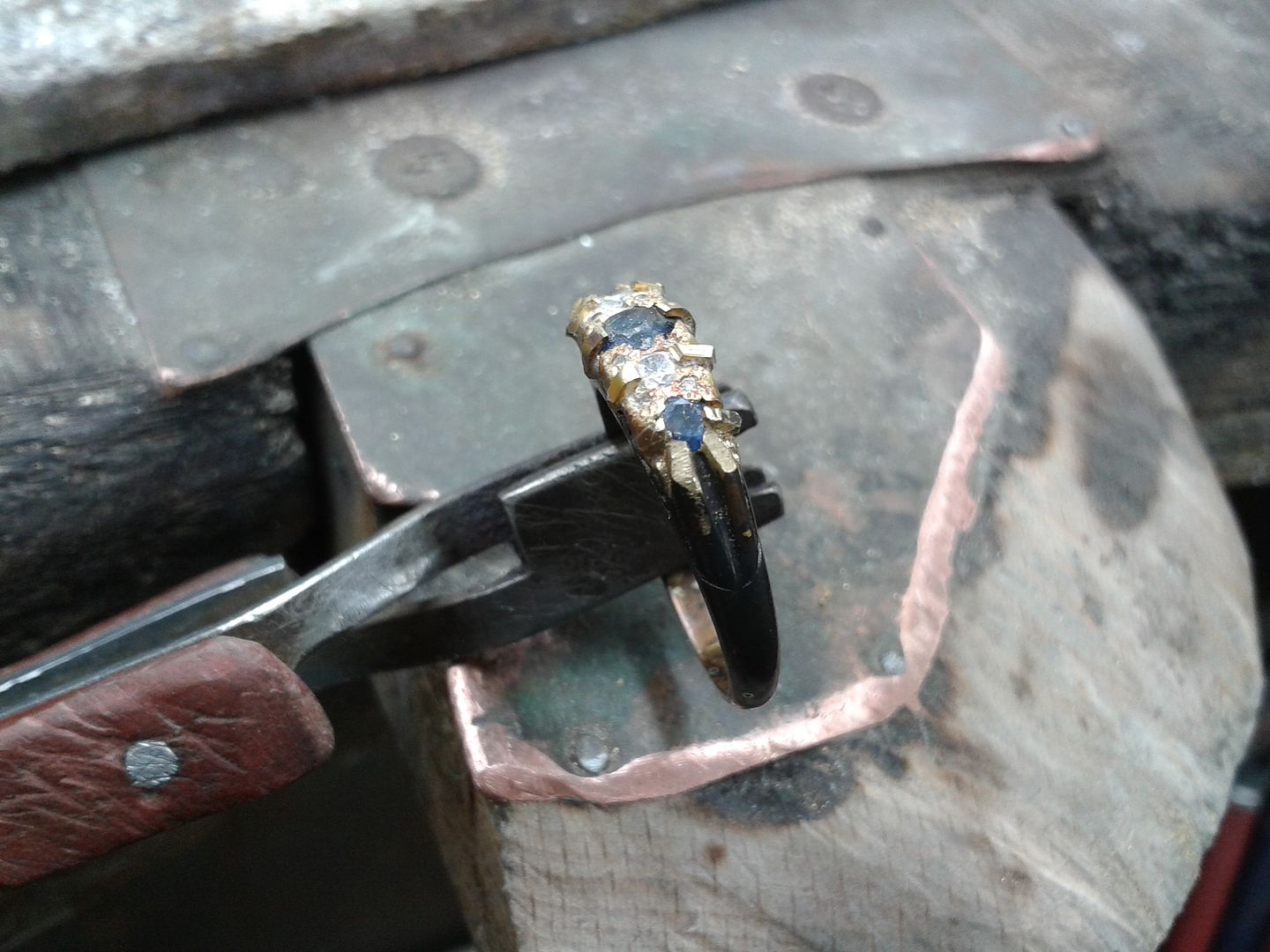
2 x new claws applied: These end ones are actually quite tricky to keep in place. You get one down ok and then because of the proximity to the next one it can move because of the heat. Practice practice.
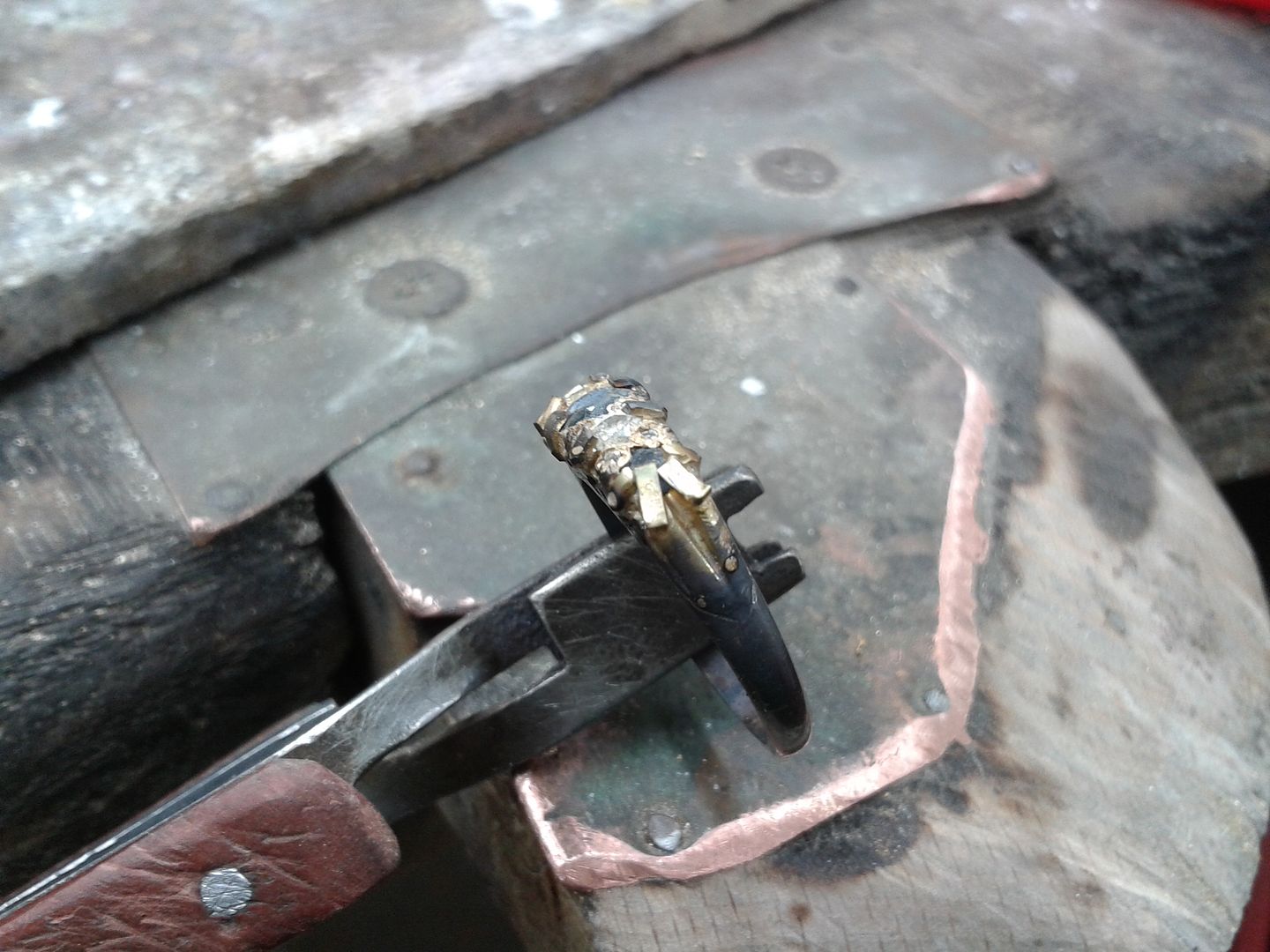
And the other end done too:
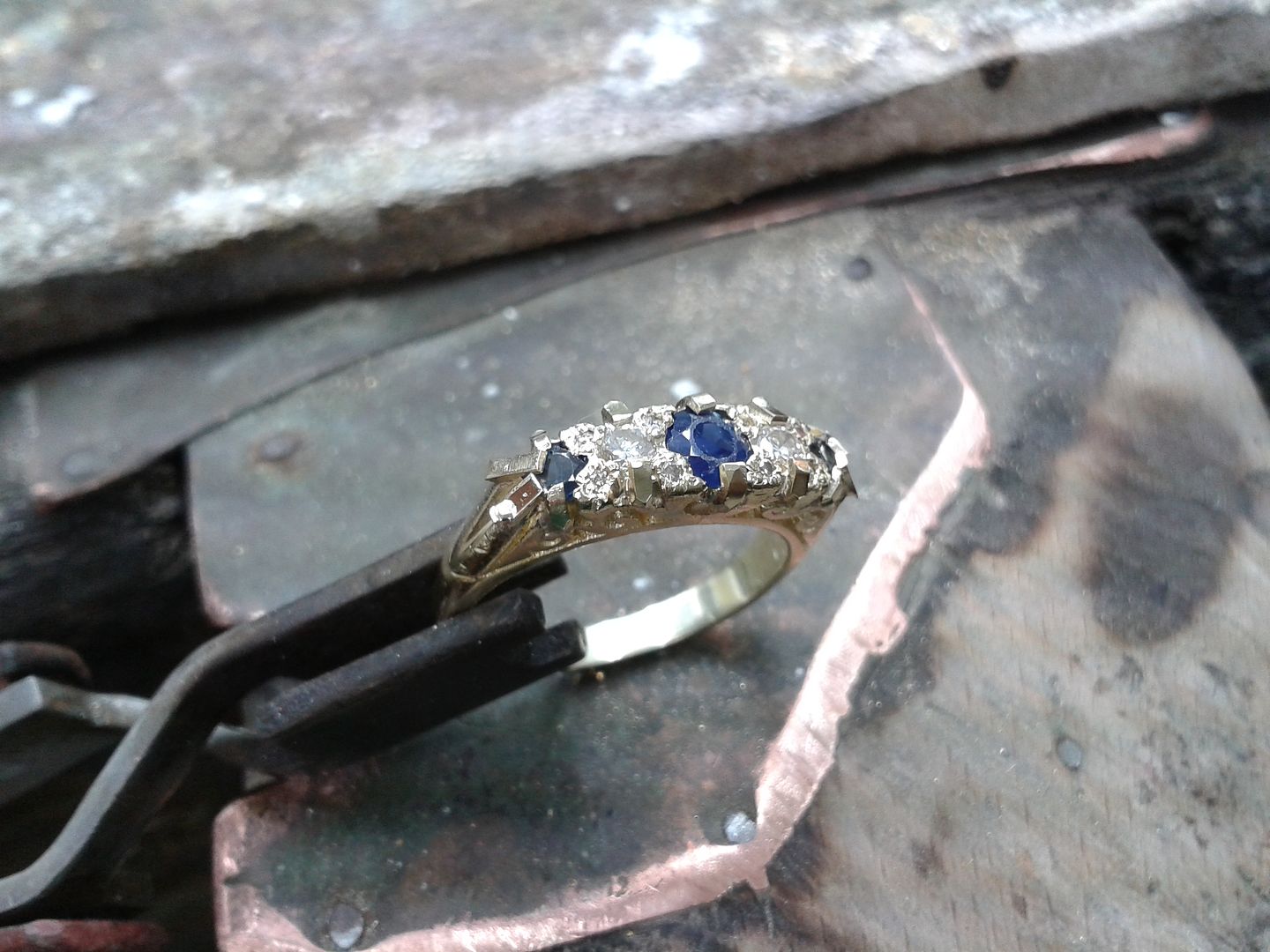
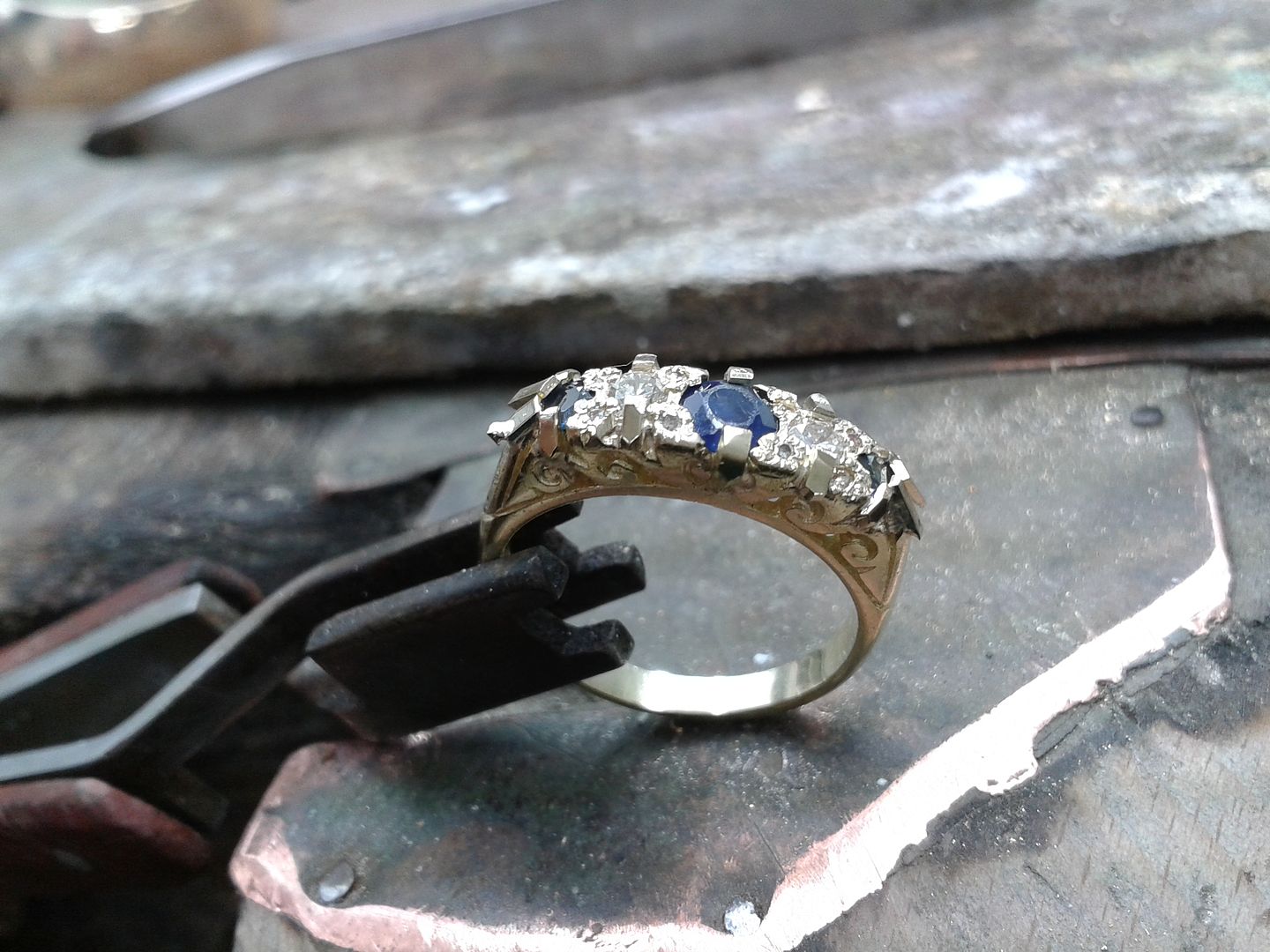
The next phase is to shape the main claws. Here you can see the sides roughly filed and profiled to shape:
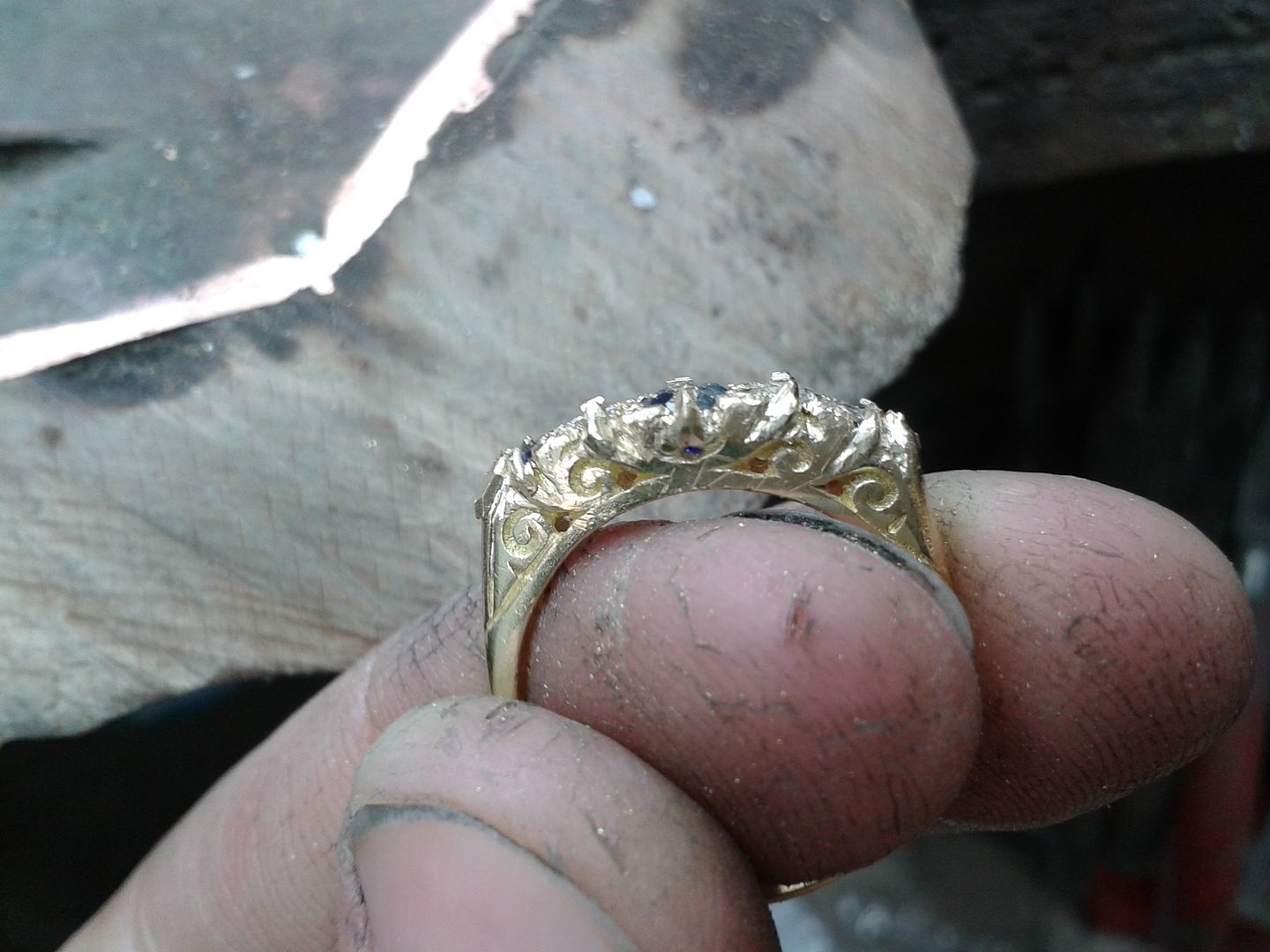
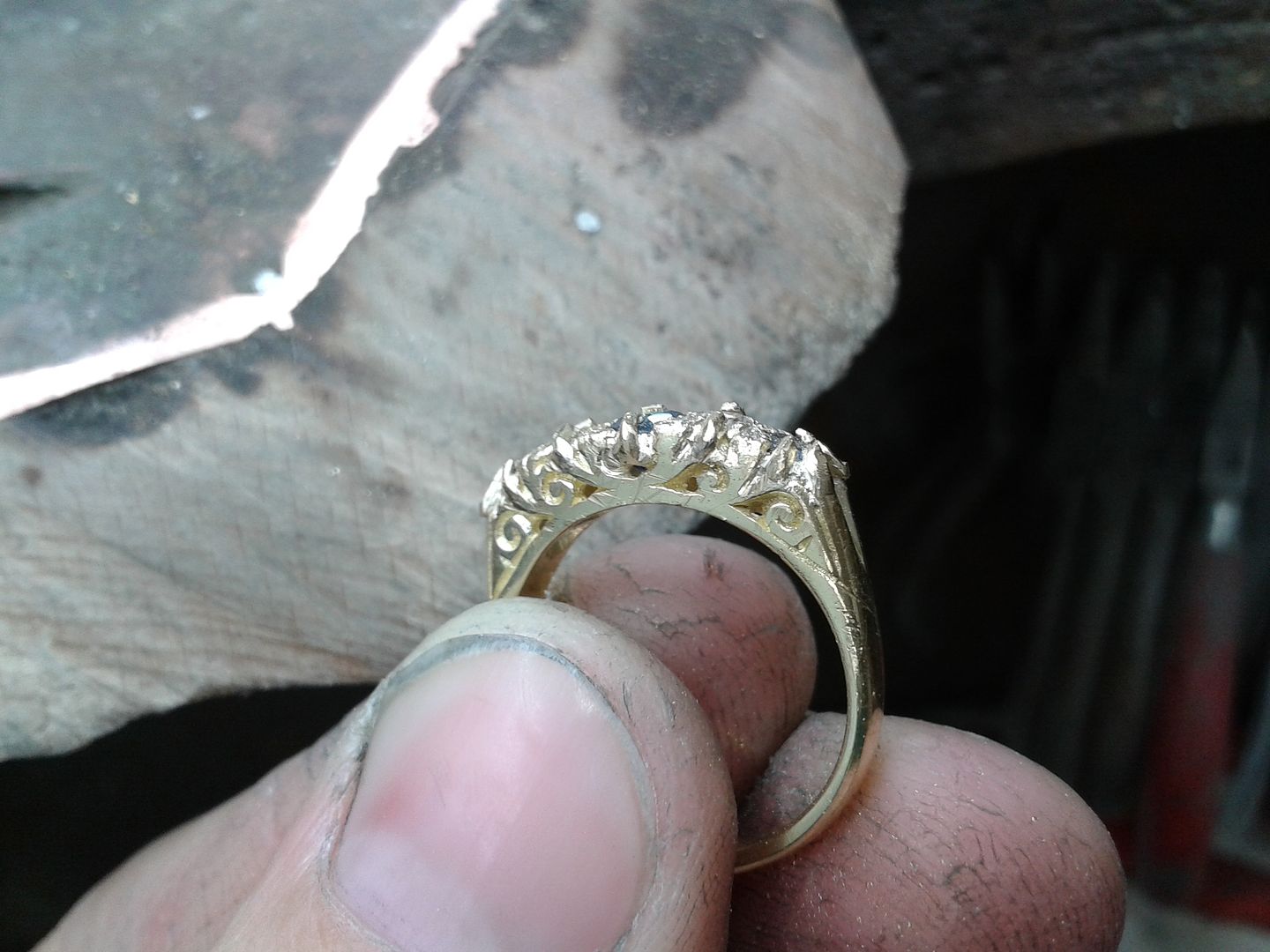
And the tops in a rough shape:
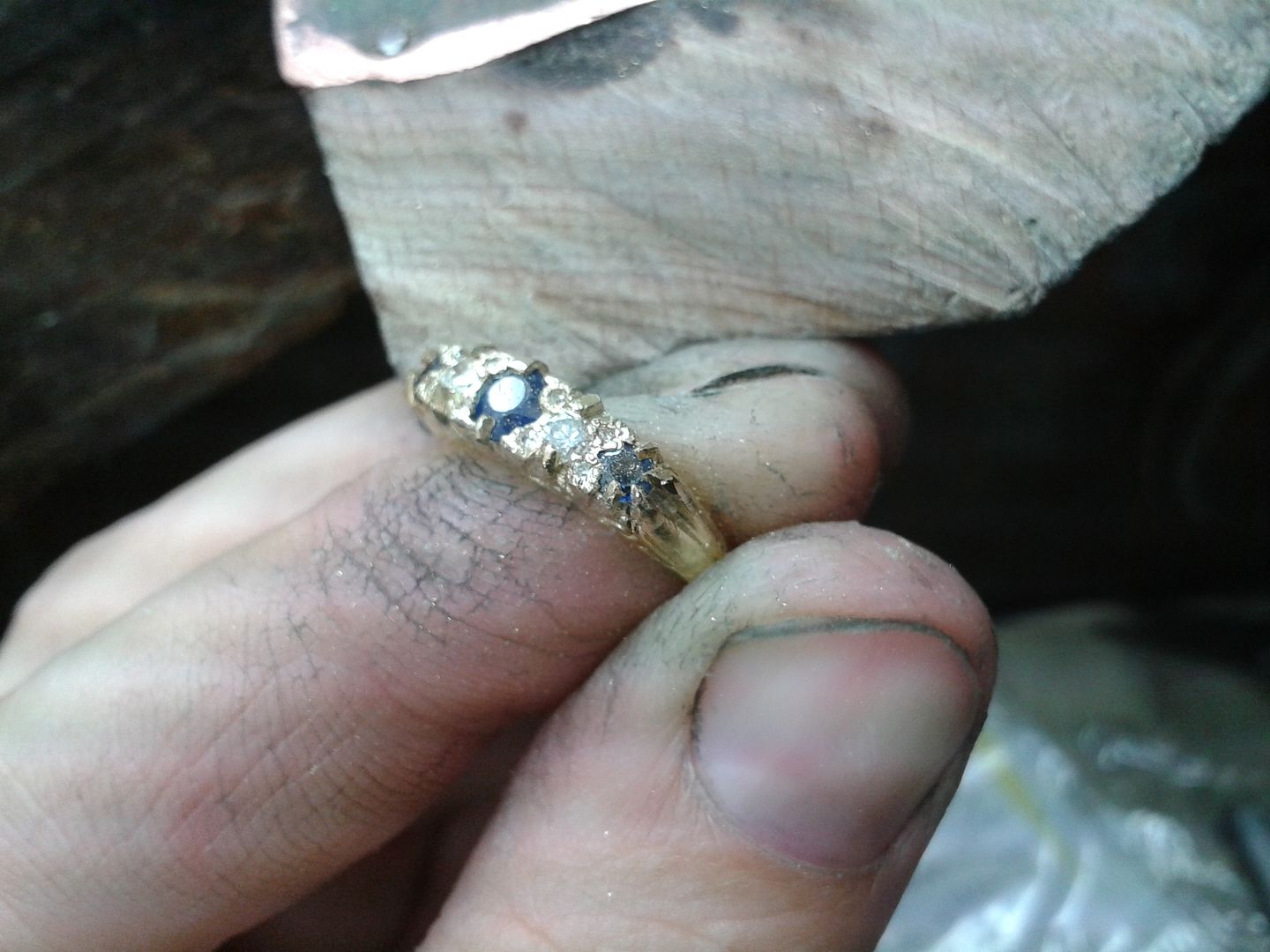
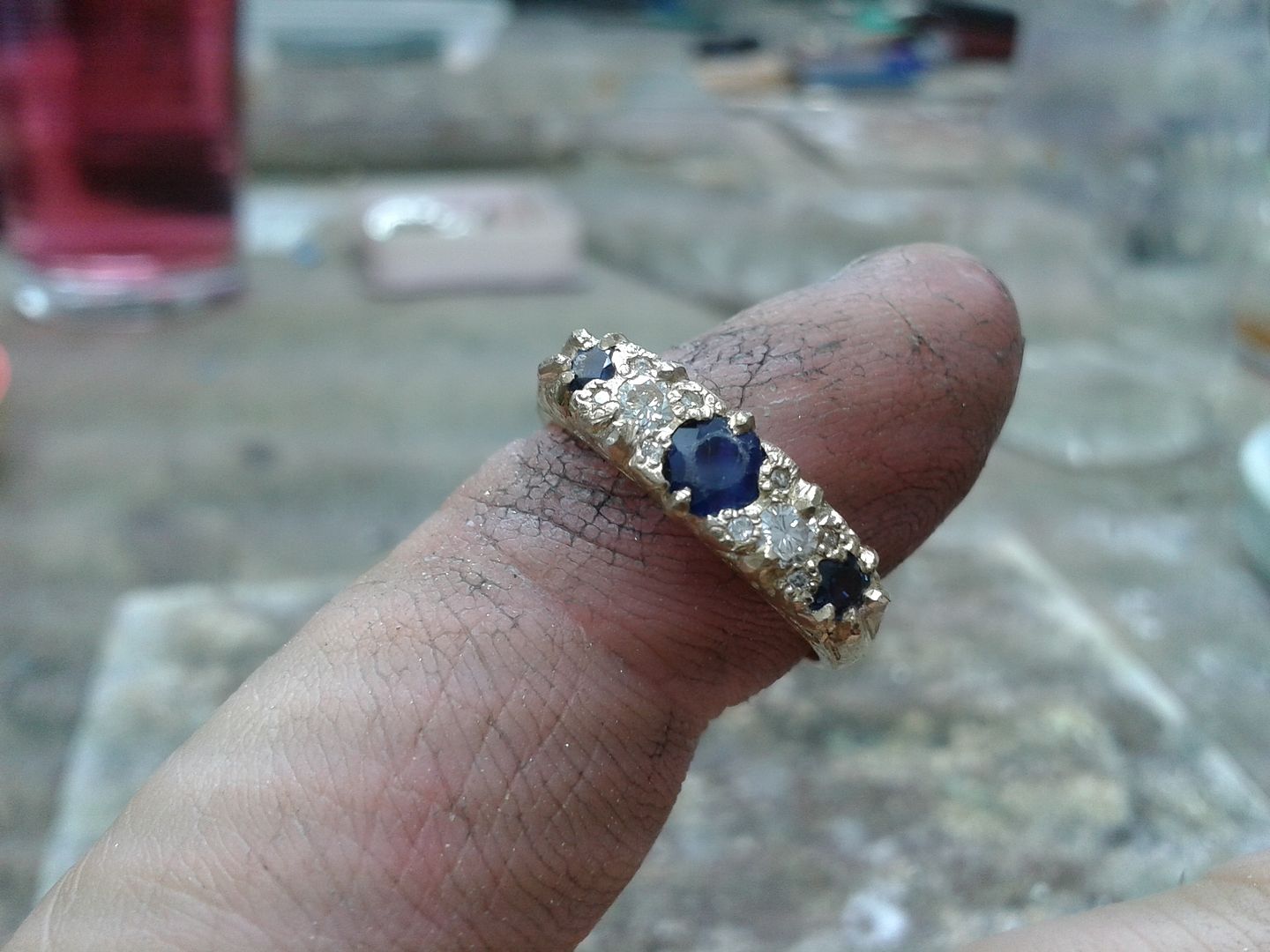
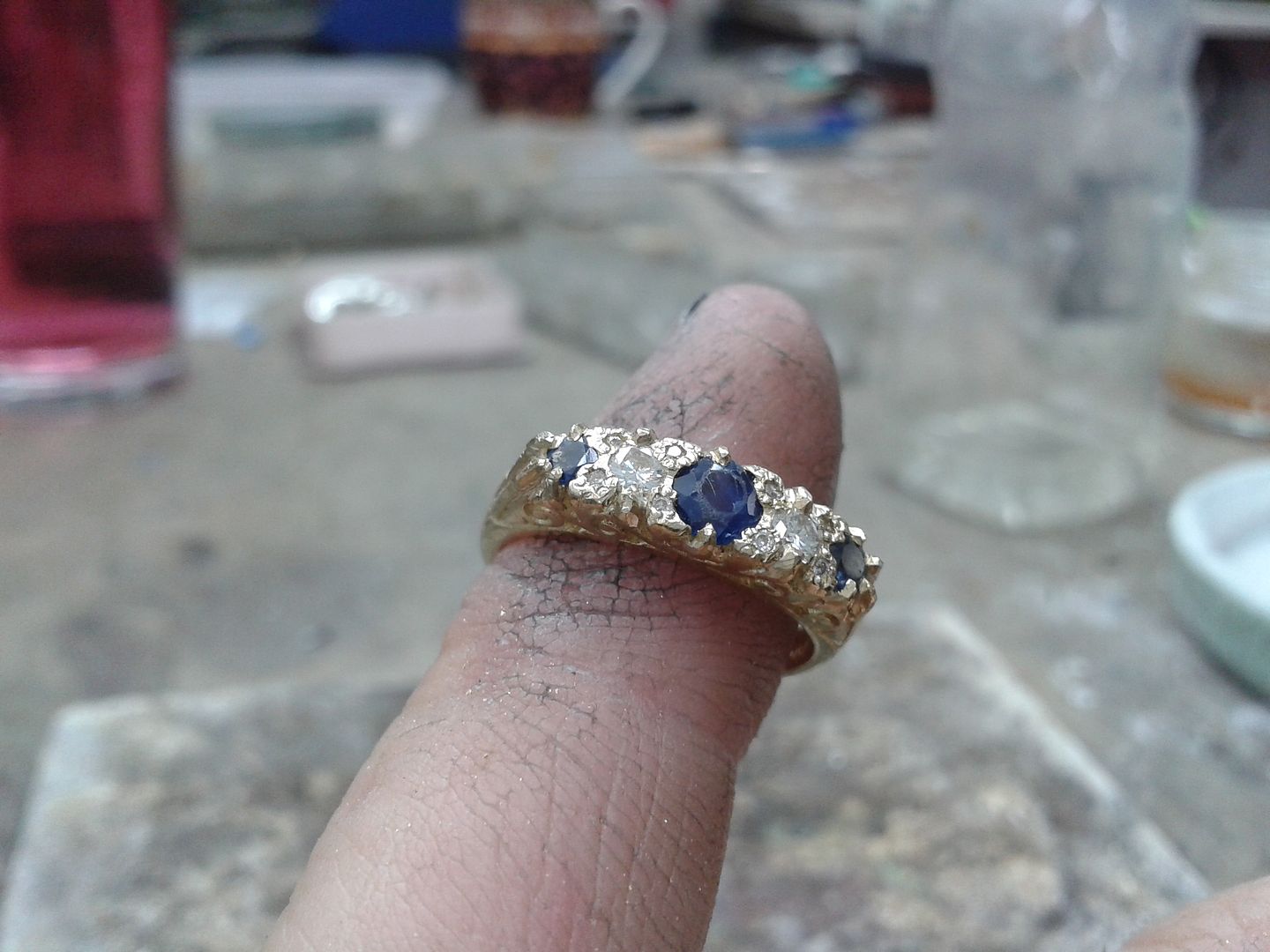
Its difficult to see in the following pics but the most tricky bit of the process is still to come. We have to solder tiny claws known as 'grains' around the ring to secure the stones in places where standard claws are not an option. The red dots mark where they will go. The solder we use is a shop recipe.
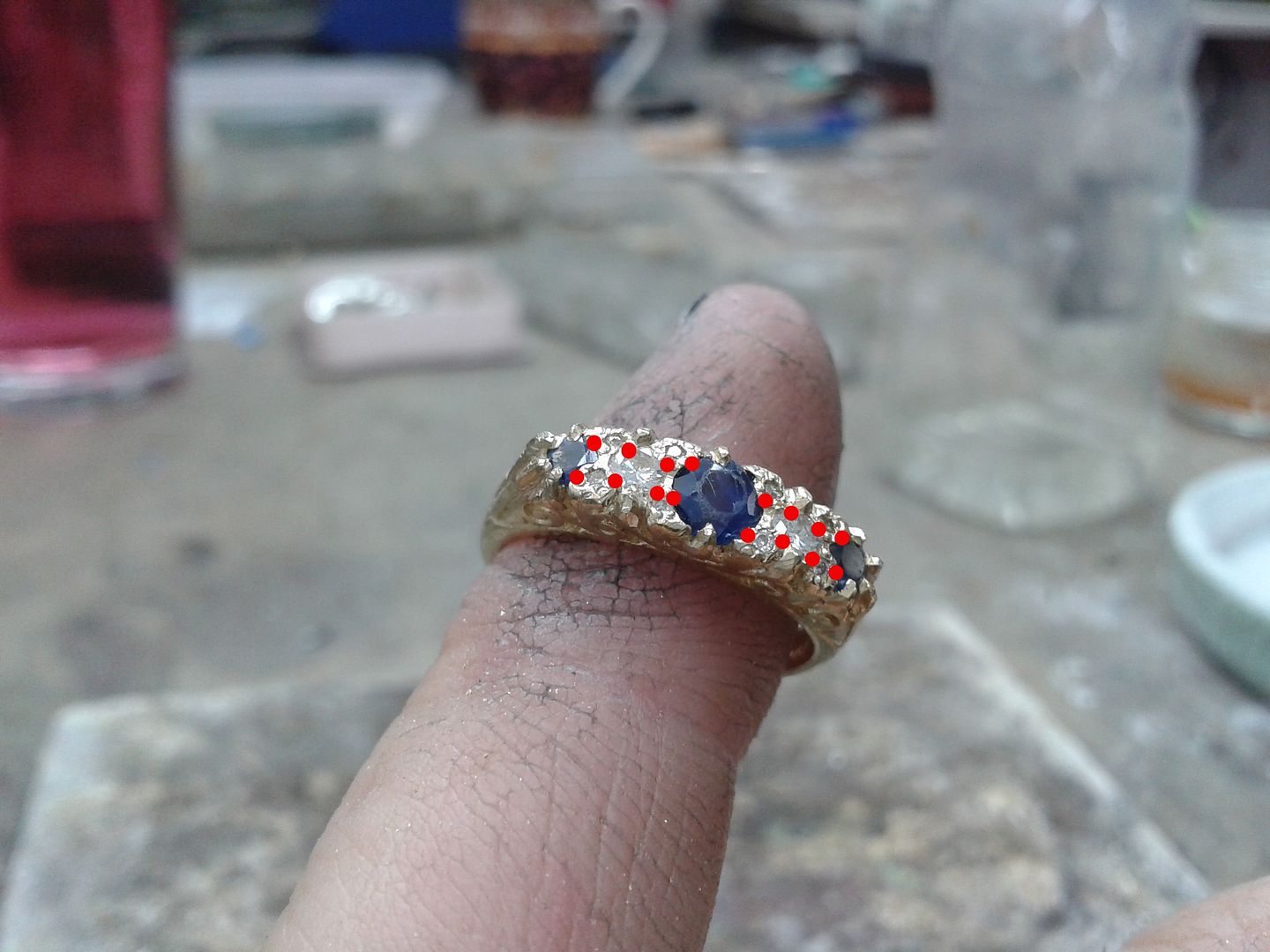
Here you can see them applied: The phone pics dont help but the grains are all there.
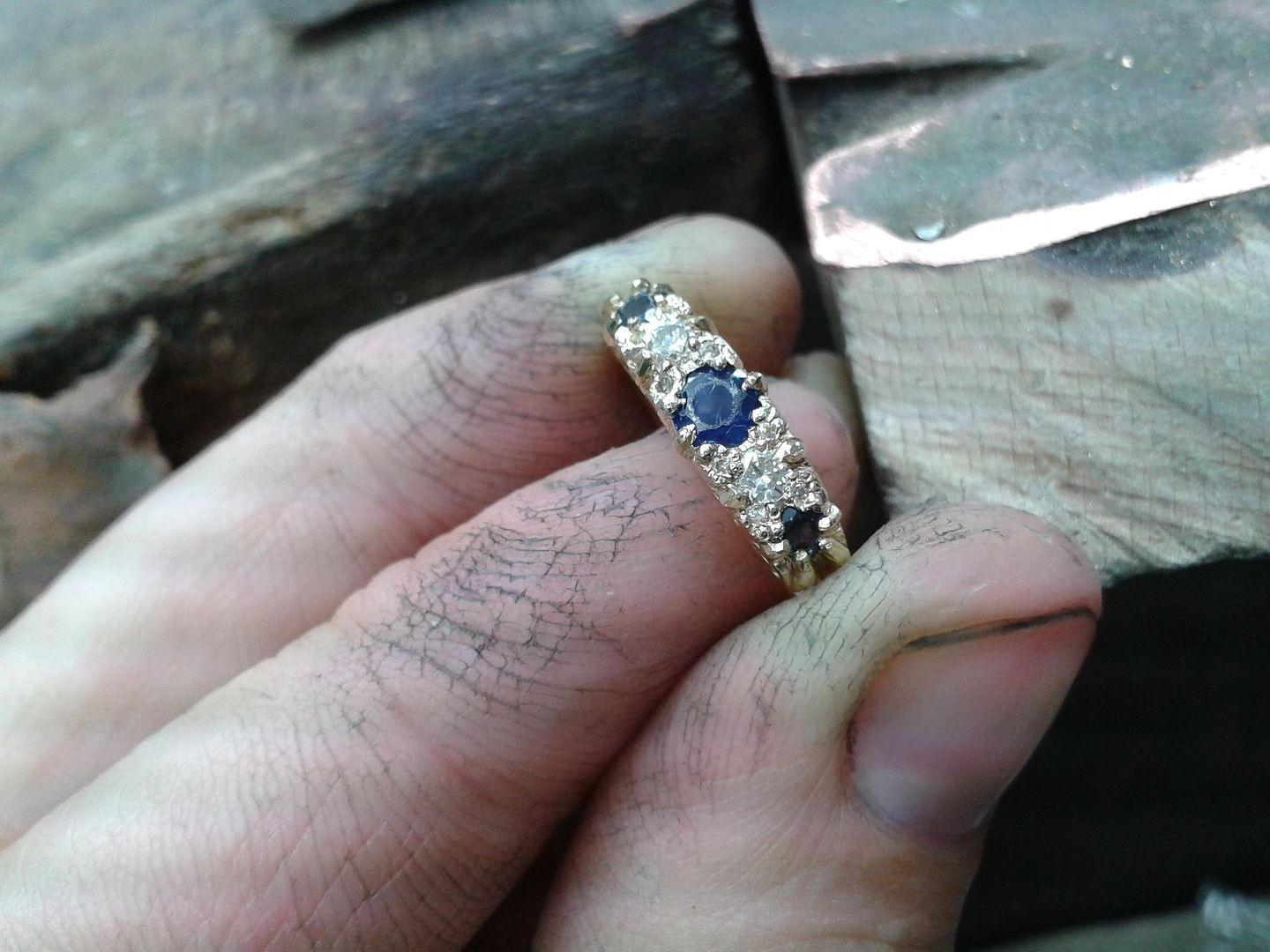
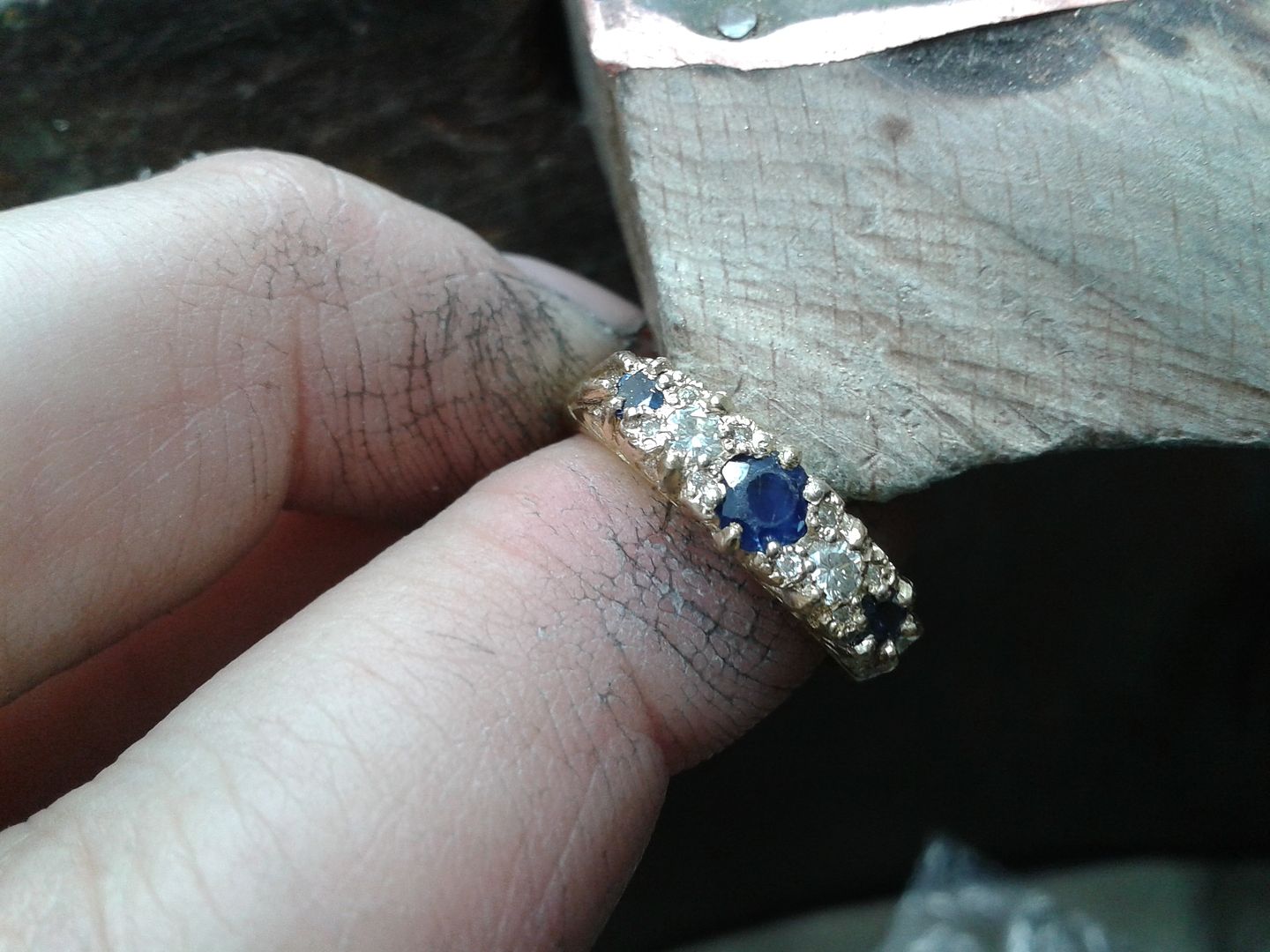
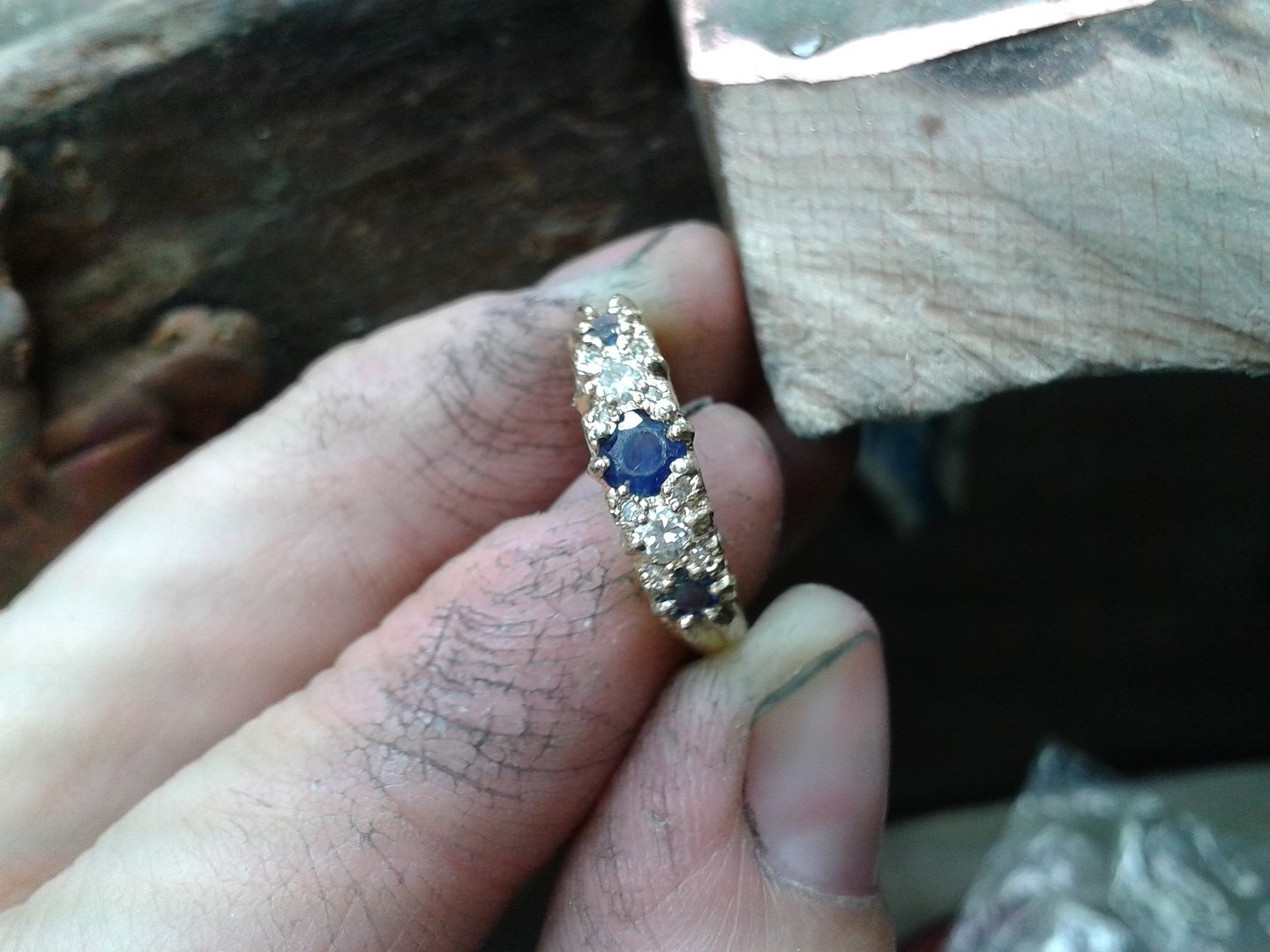
We then give the ring a good polish to give light to all the hard work. It also highlights any areas where we need to do more. In this case we are fine.
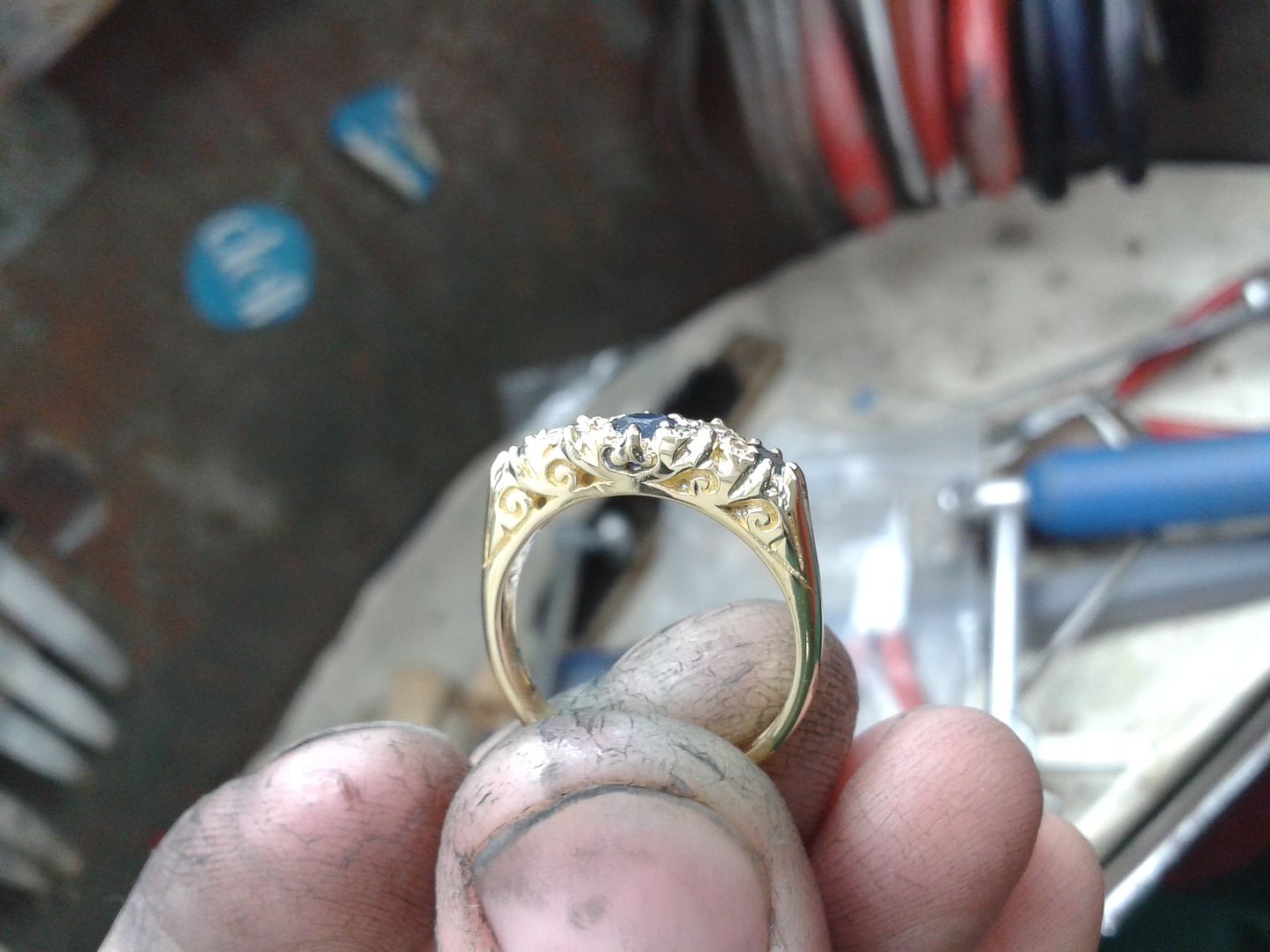
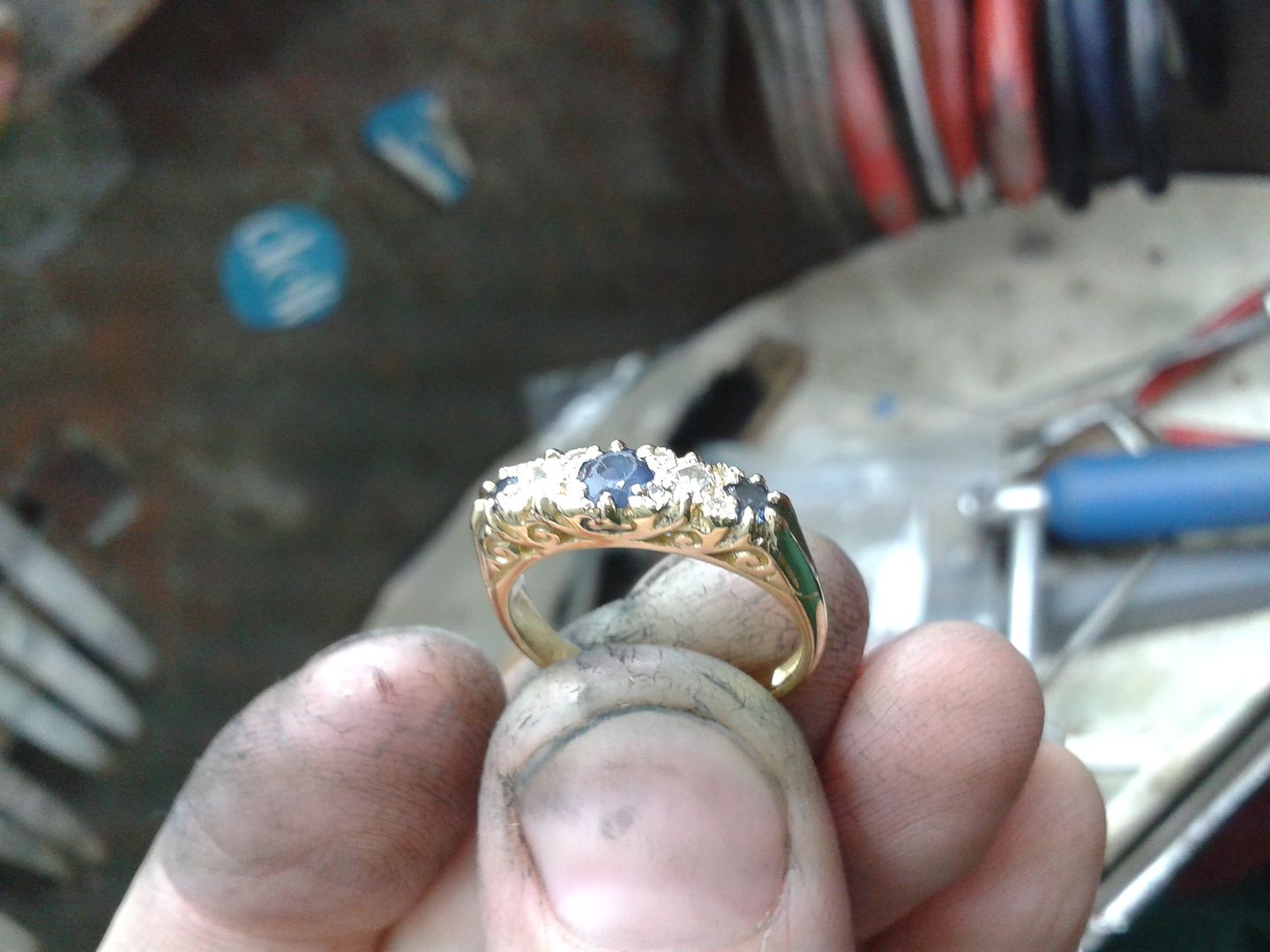
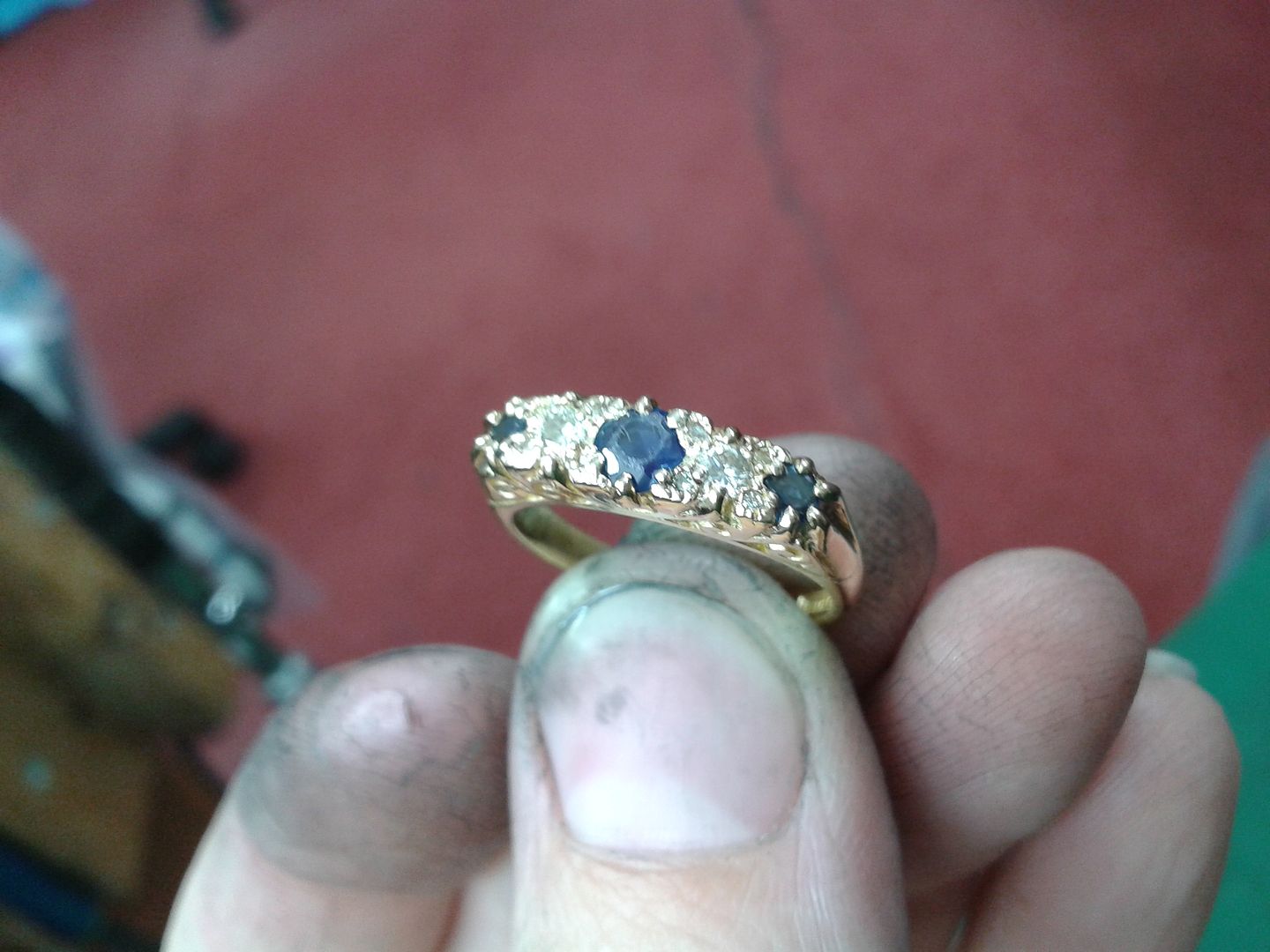
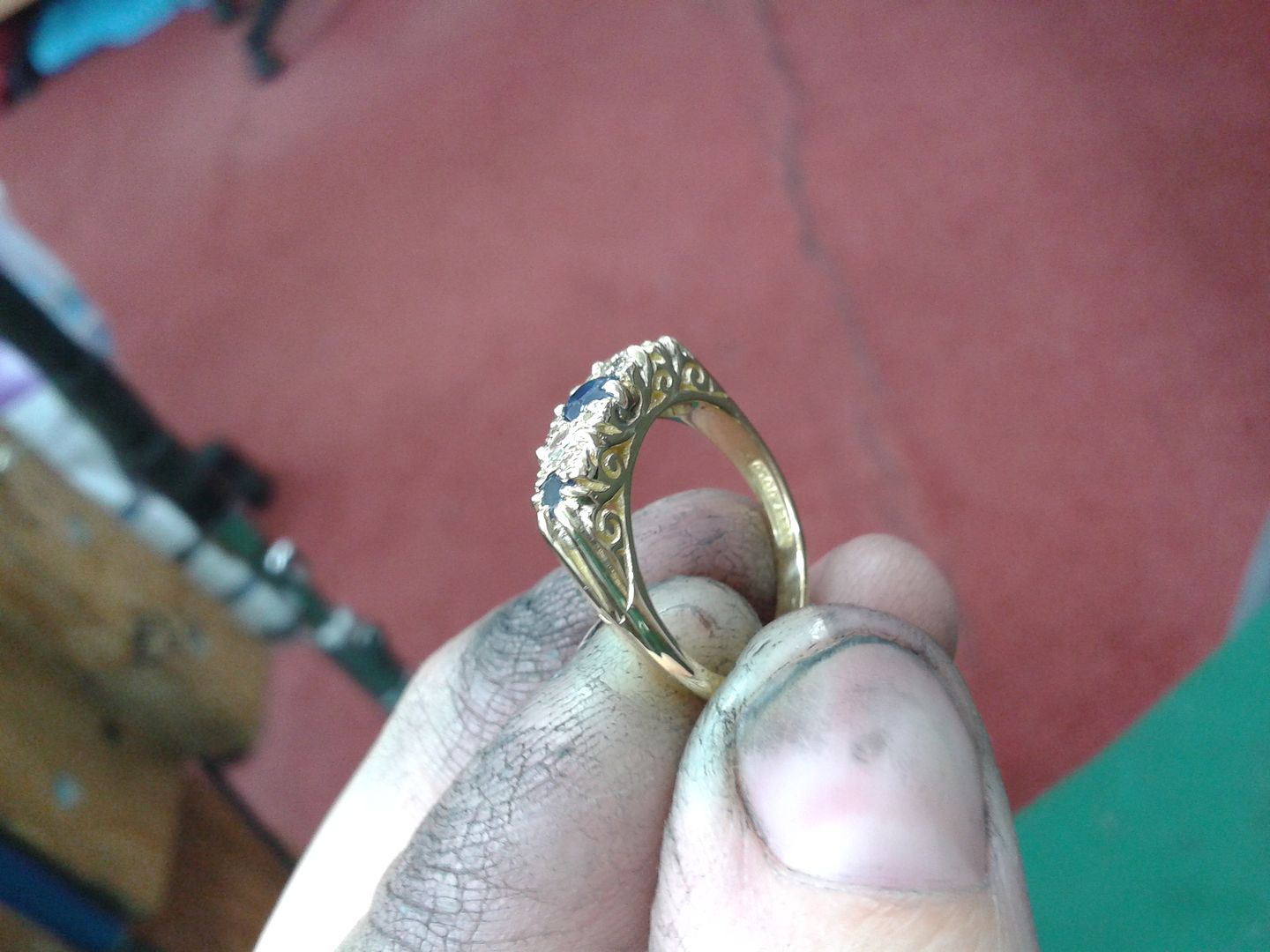
For an added sparkle the customer has opted to have the top of the setting rhodium plated. This gives a platinum white finish to the setting and allows the stones to show their best colours. Masking out the ring for plating:
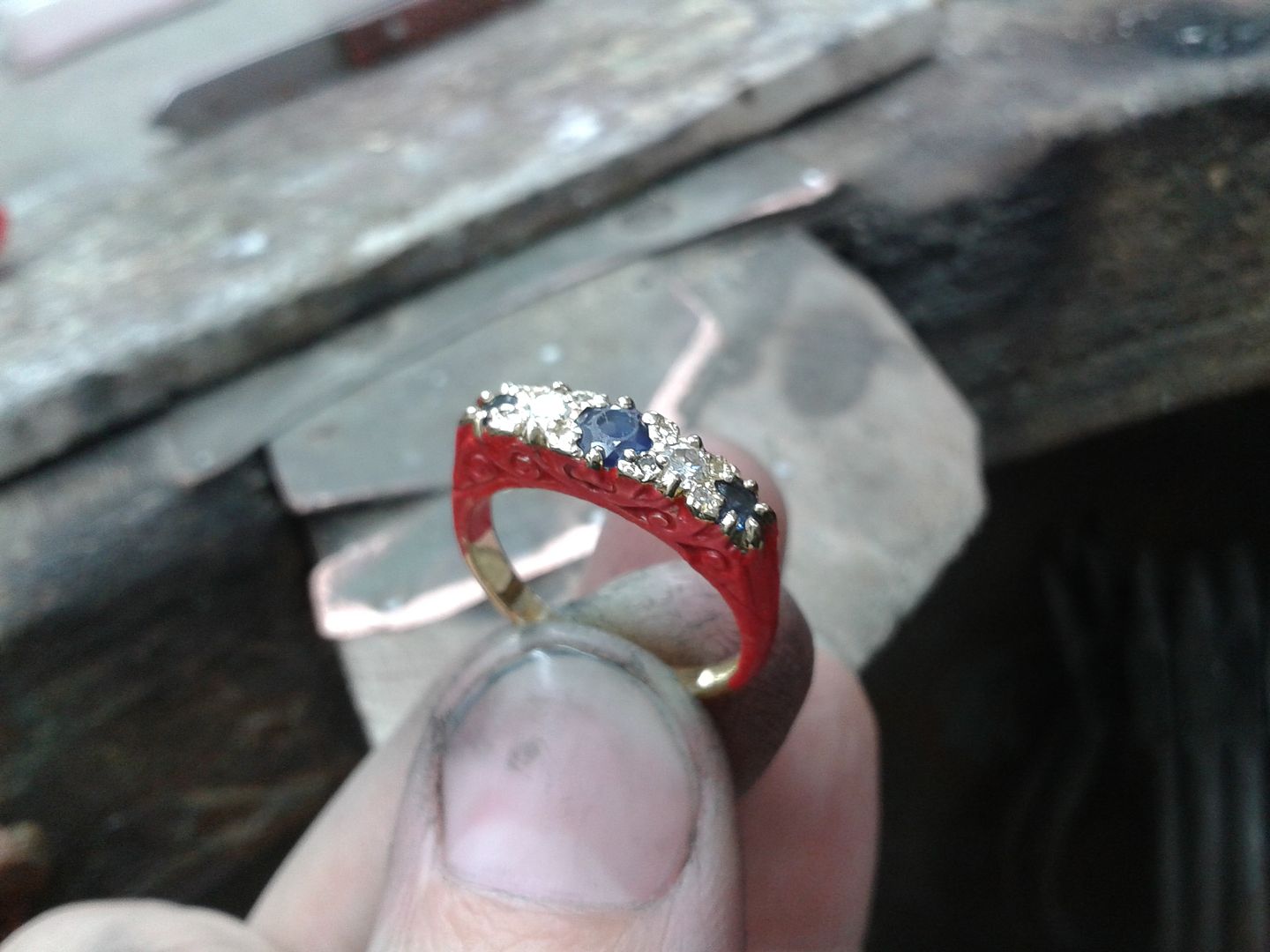
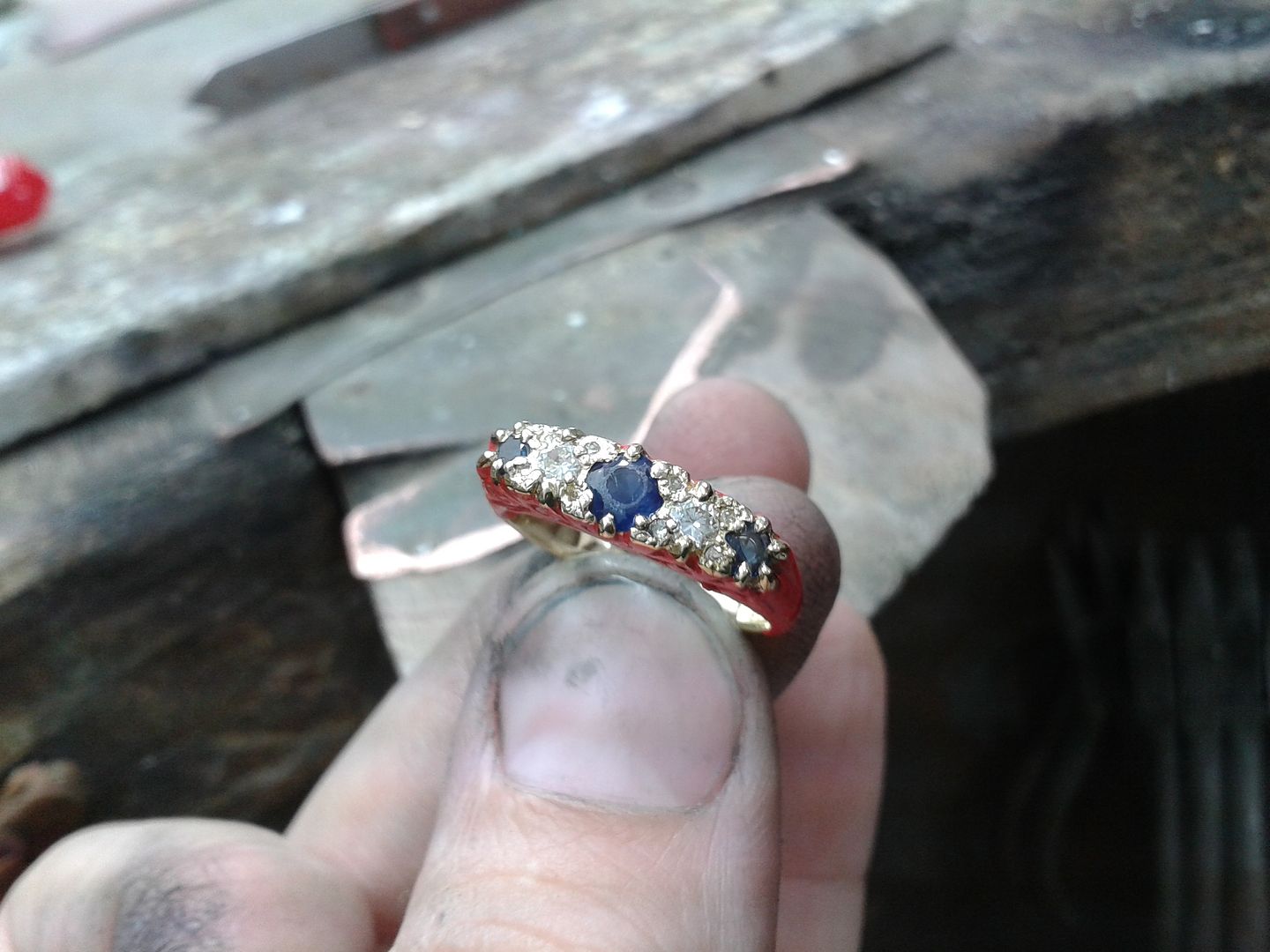
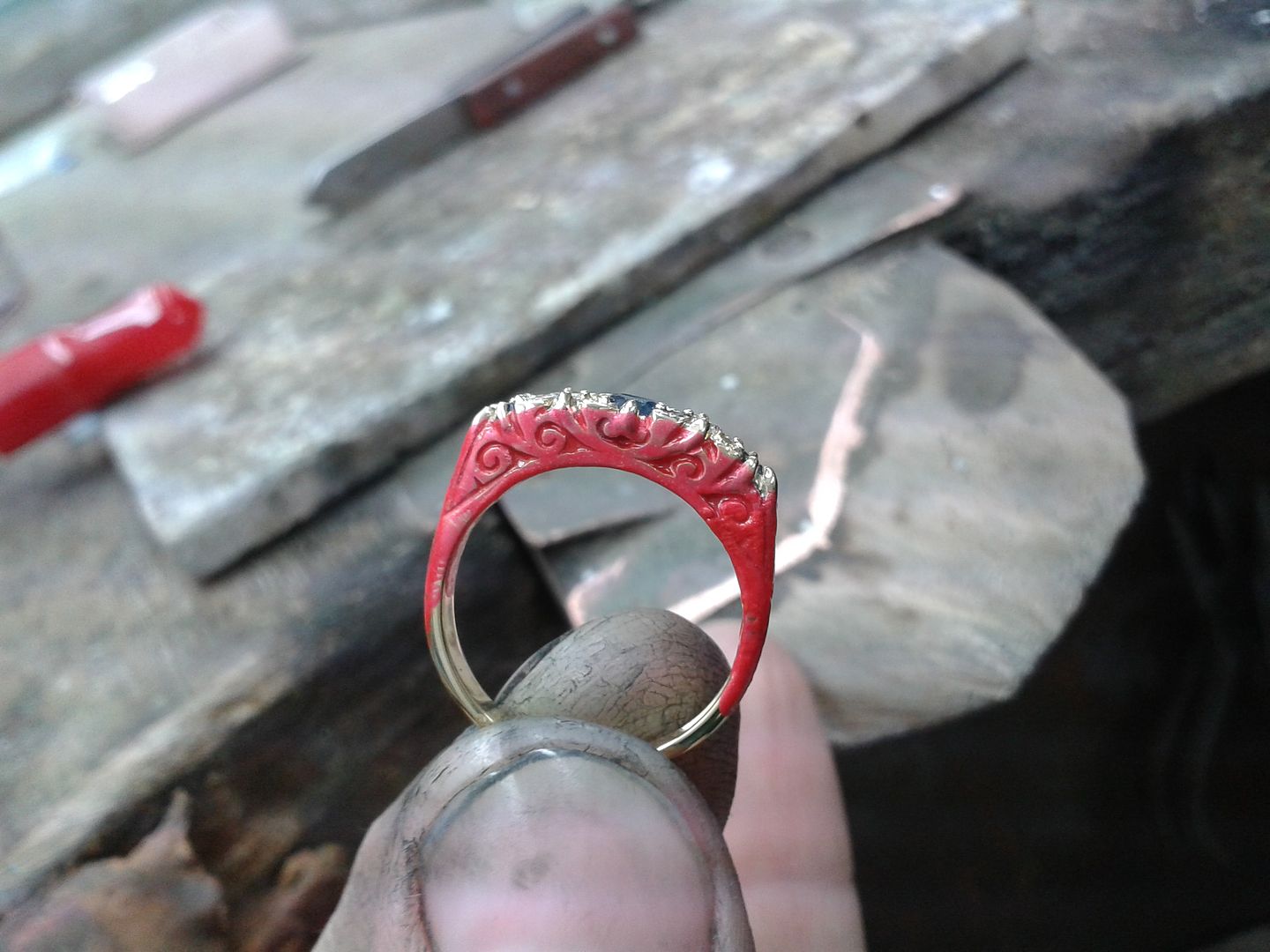
And plated. Sorry about the hair sticking out of the top of the ring. Its from the polishing mop and was removed afterward:
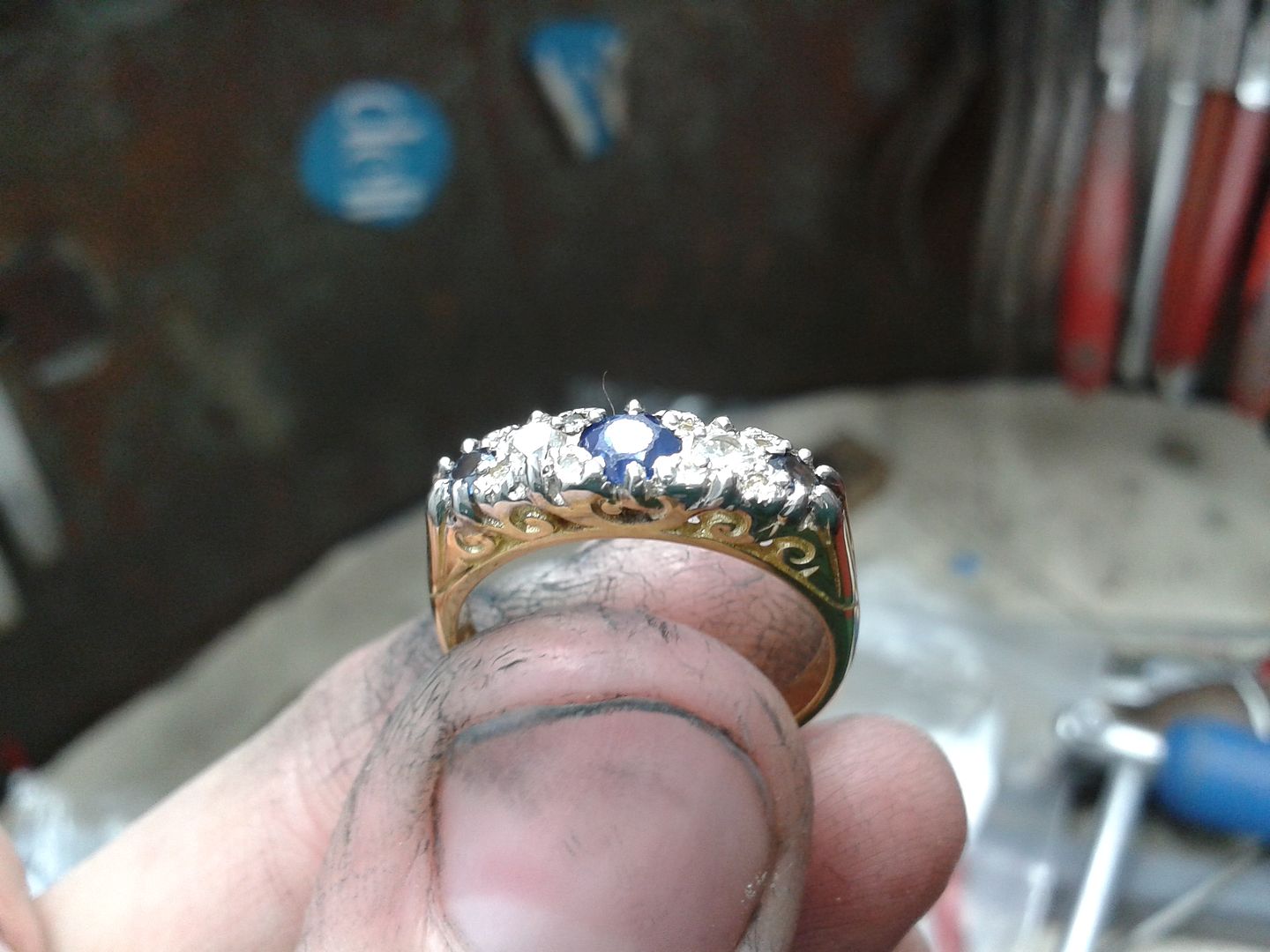
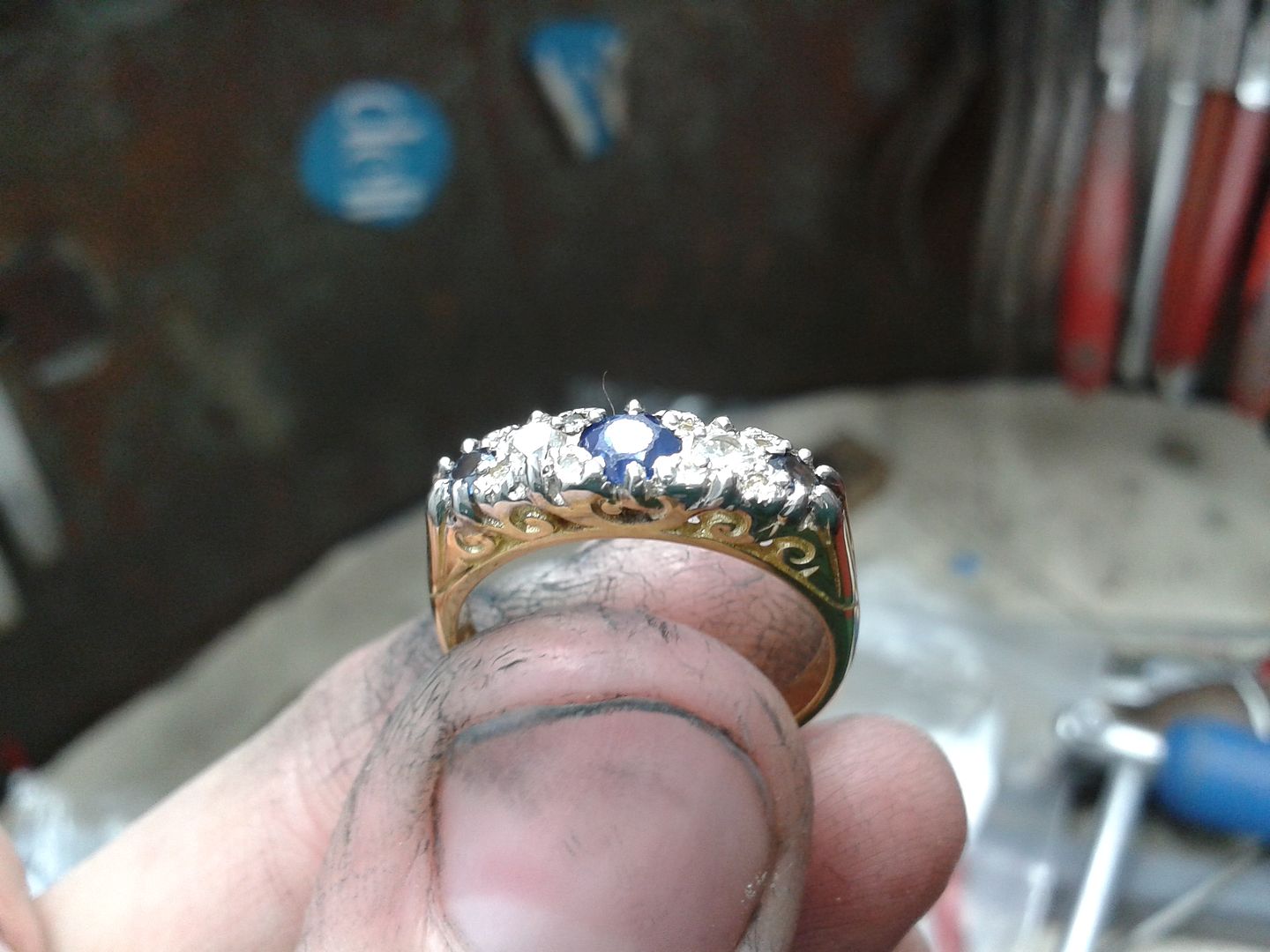
The phone pics don't do it justice but it was a really successful job.
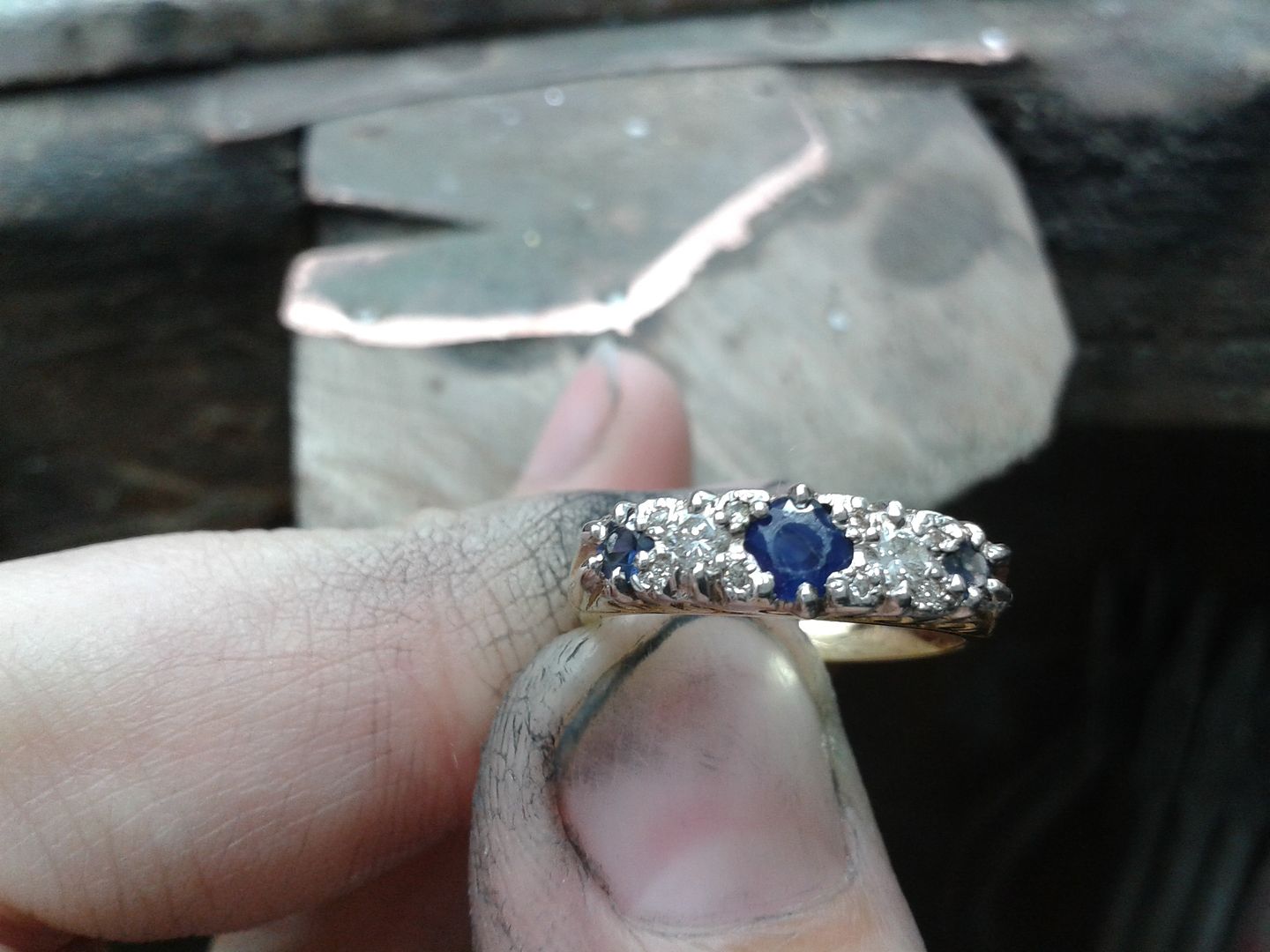
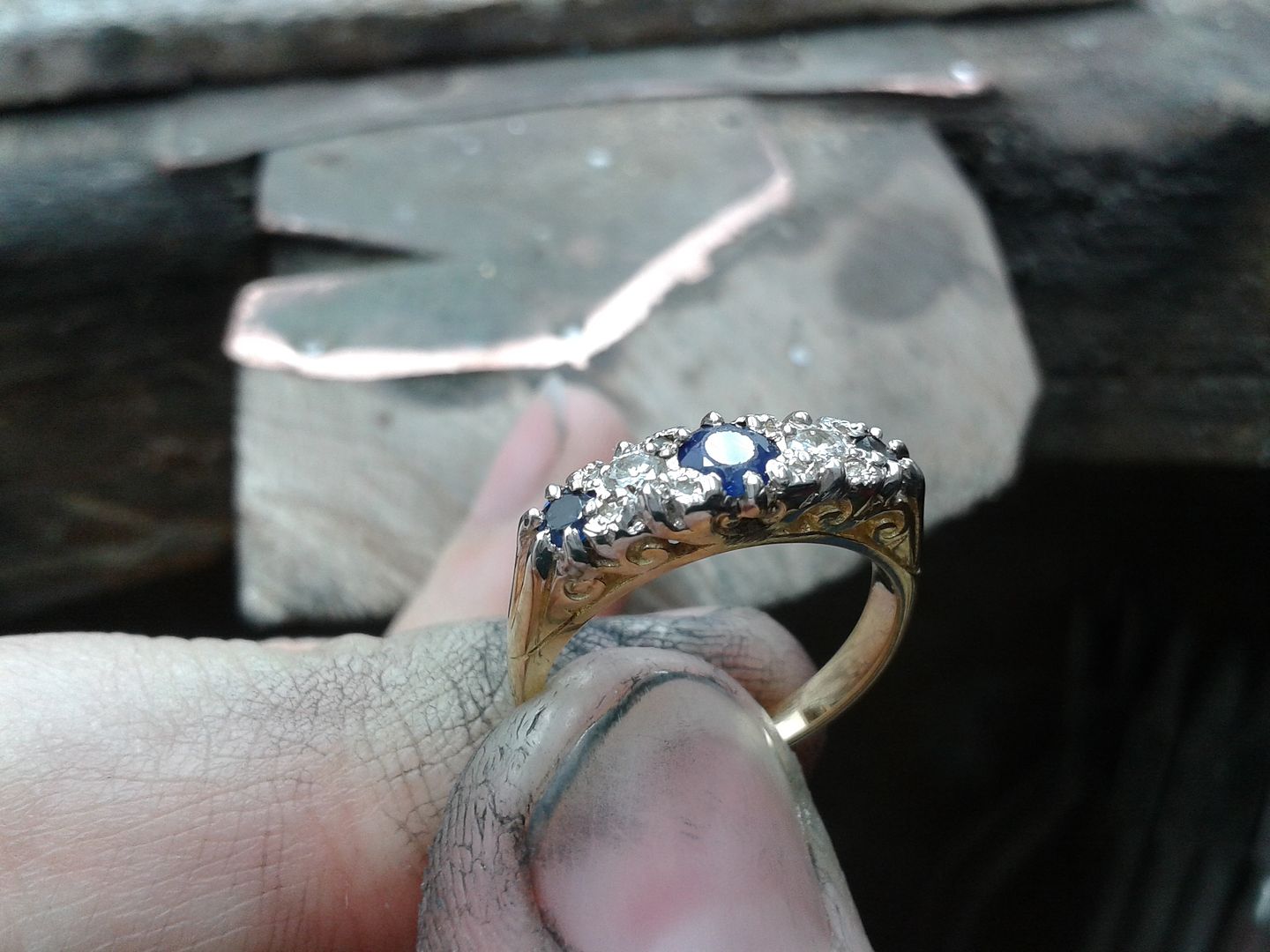
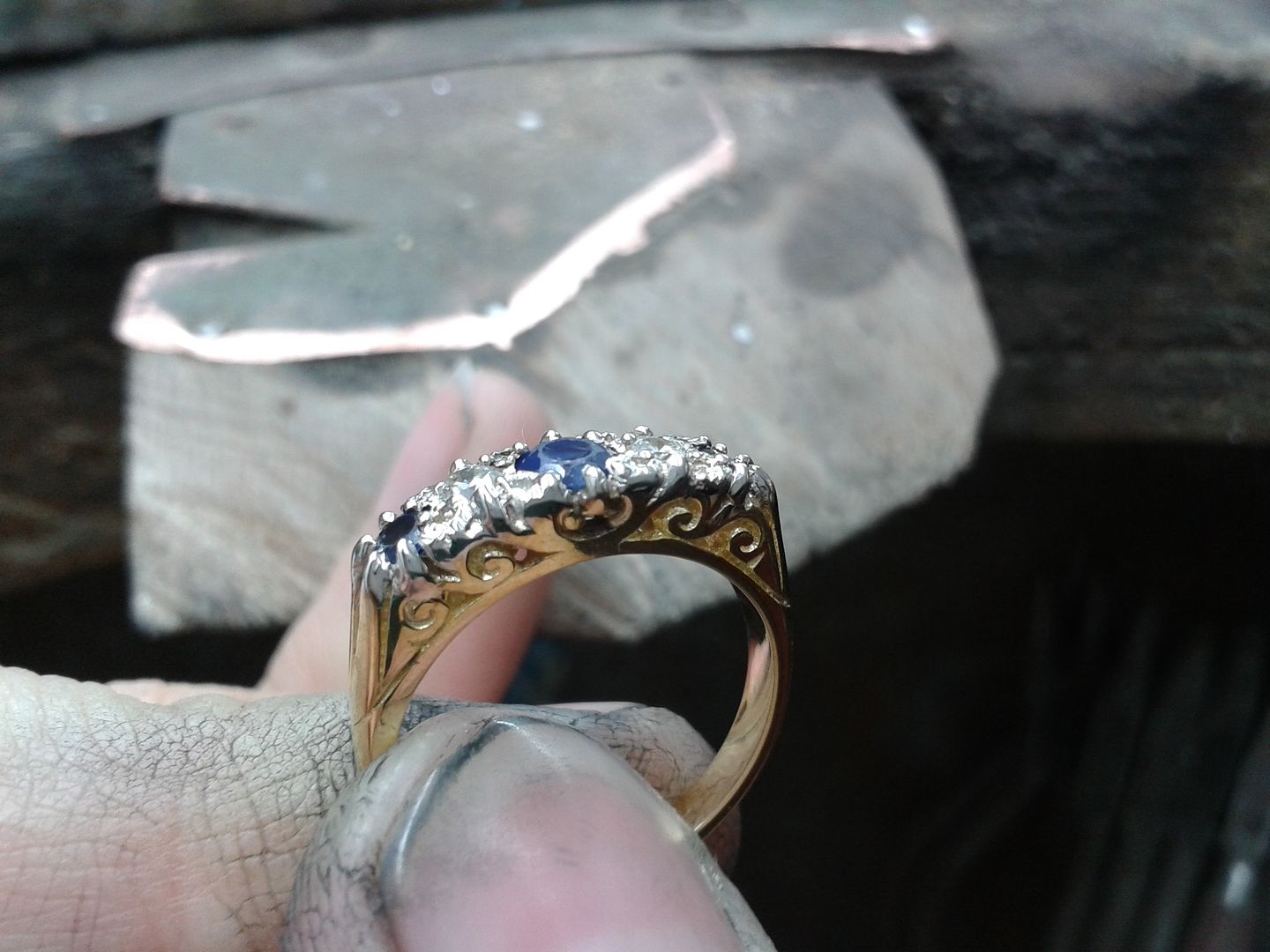
Before and after:
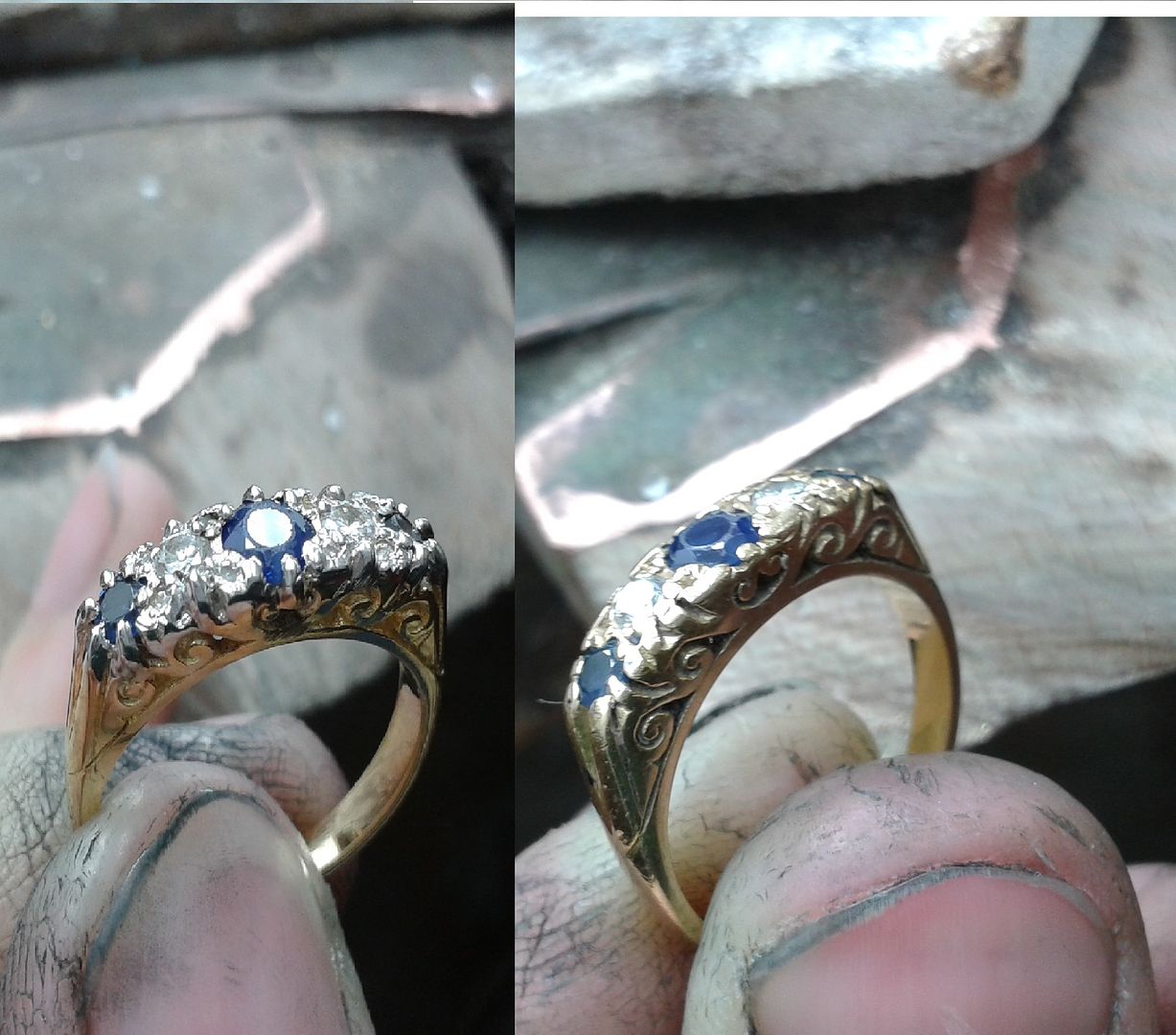
Eddie
Edited by ecain63 on Sunday 29th September 20:45
Apologies again for the delay in getting you an update. Reason is that i was diagnosed with colon cancer last month and its been a bit of a run around with treatments, testing and meetings etc. On the upside I should be ok so im no overly fussed by the diagnosis until somebody tells me otherwise. On the work front ive had to take the odd day off here and there and even when i am in the side effects of the chemo mean what i can do is a bit limited.
That said, here is a little something my very sore hands made on monday:
Start with 1 x tanzanite and some of the customers own gold, which we melted down from a couple of inherited wedding bands she had.
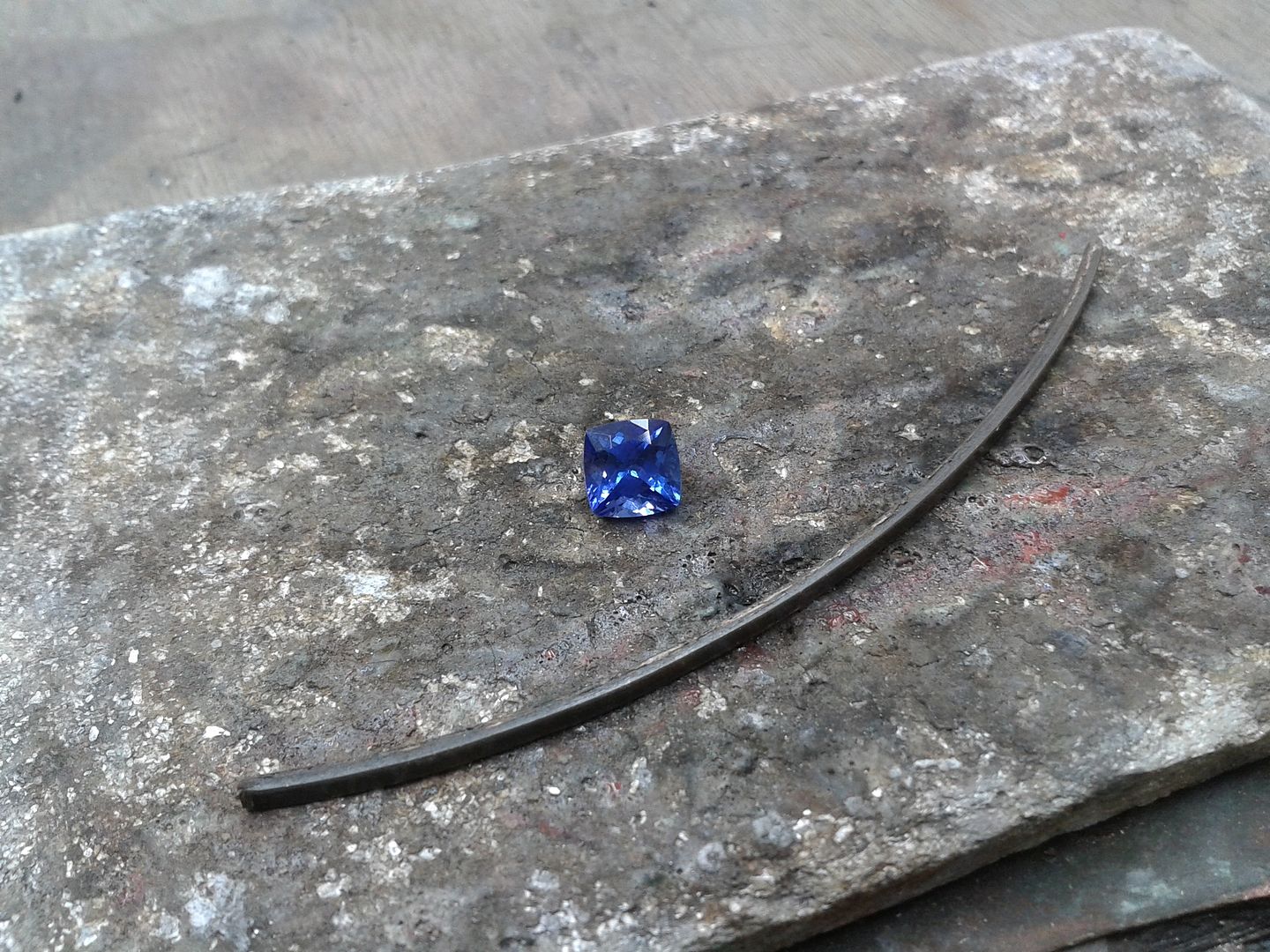
Take the gold bar (2.25mm wide x 1.75mm thick) and make a shank. Note the split shoulders (and finger).
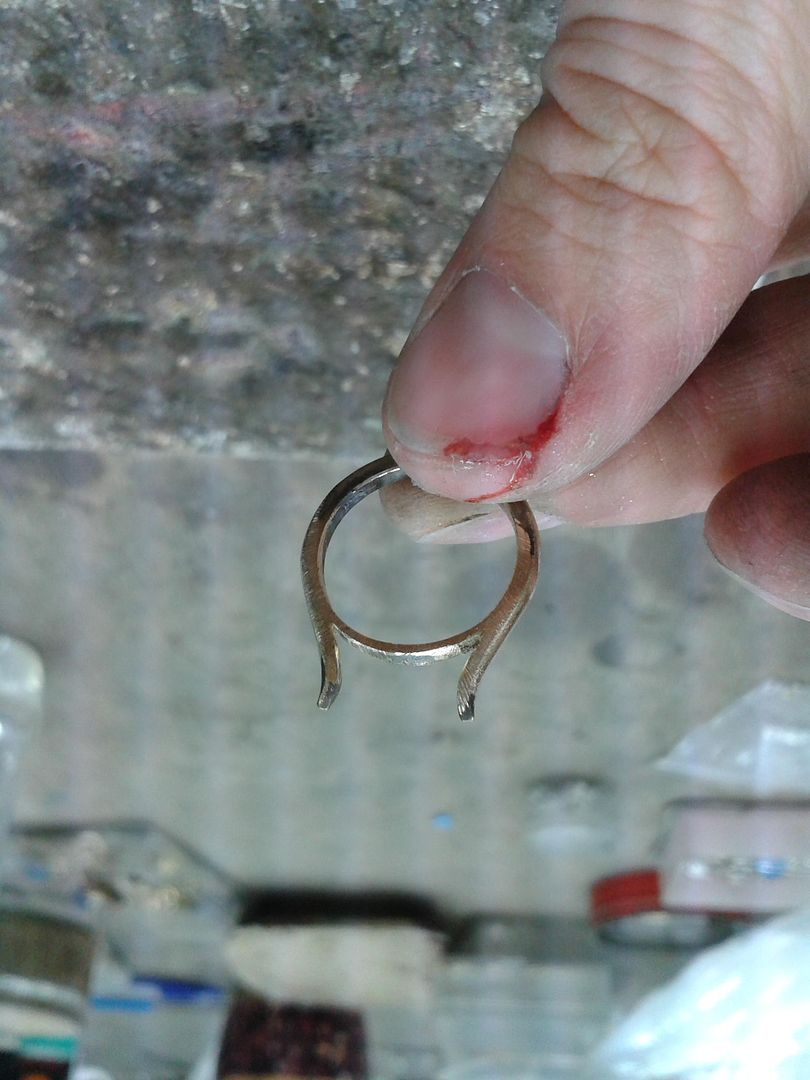
Now the shank is all cleaned up its time to make the setting. I made the setting using platinum wire to give it a lovely white finish. Its nice and soft too which makes it easier when setting such a fragile stone.
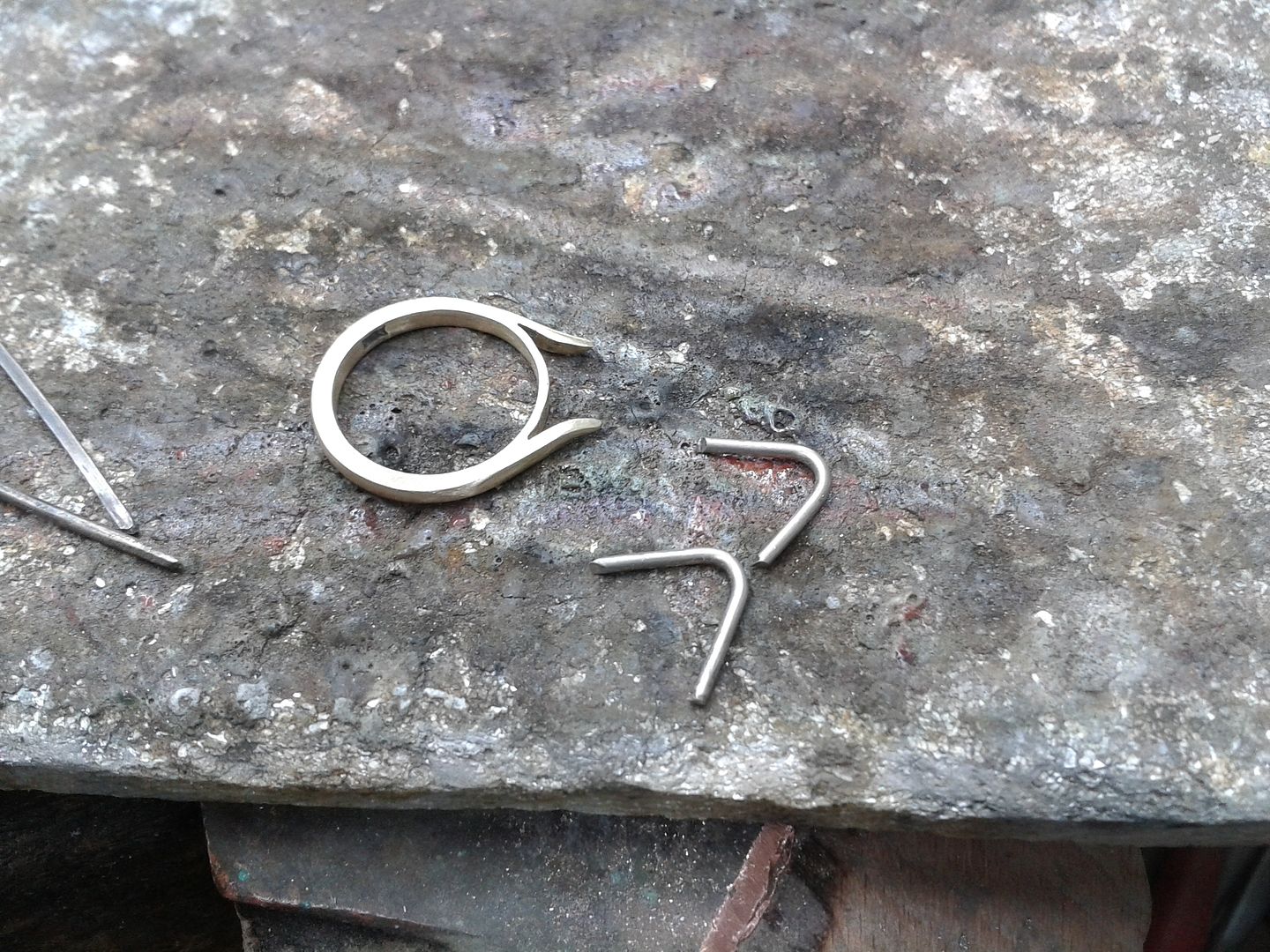
Simple setting part done
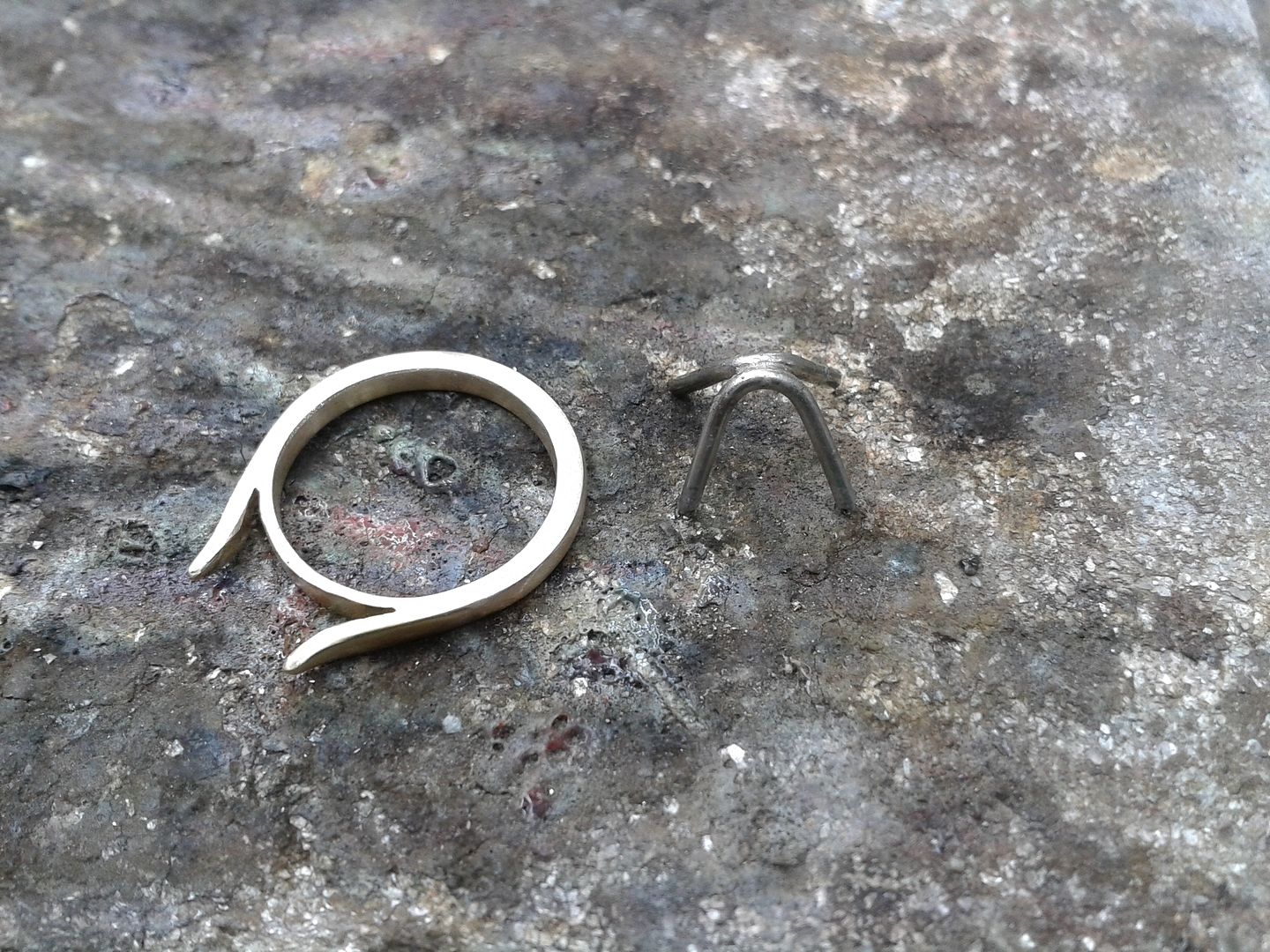
Setting complete, just needs fitting to the shank and finishing off. Note the strengthening brace around the setting.
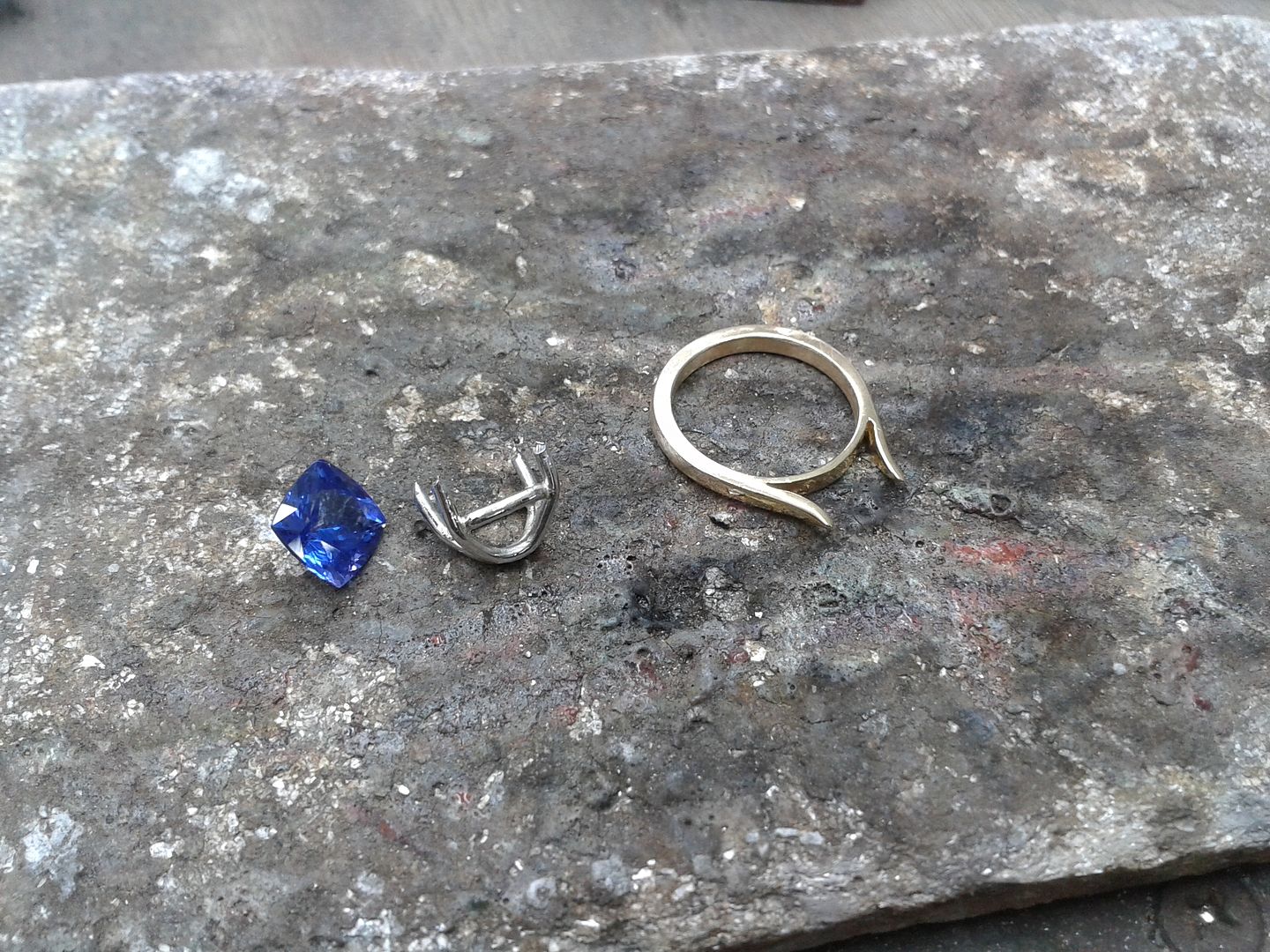
Fully assembled. Just need to set the stone.
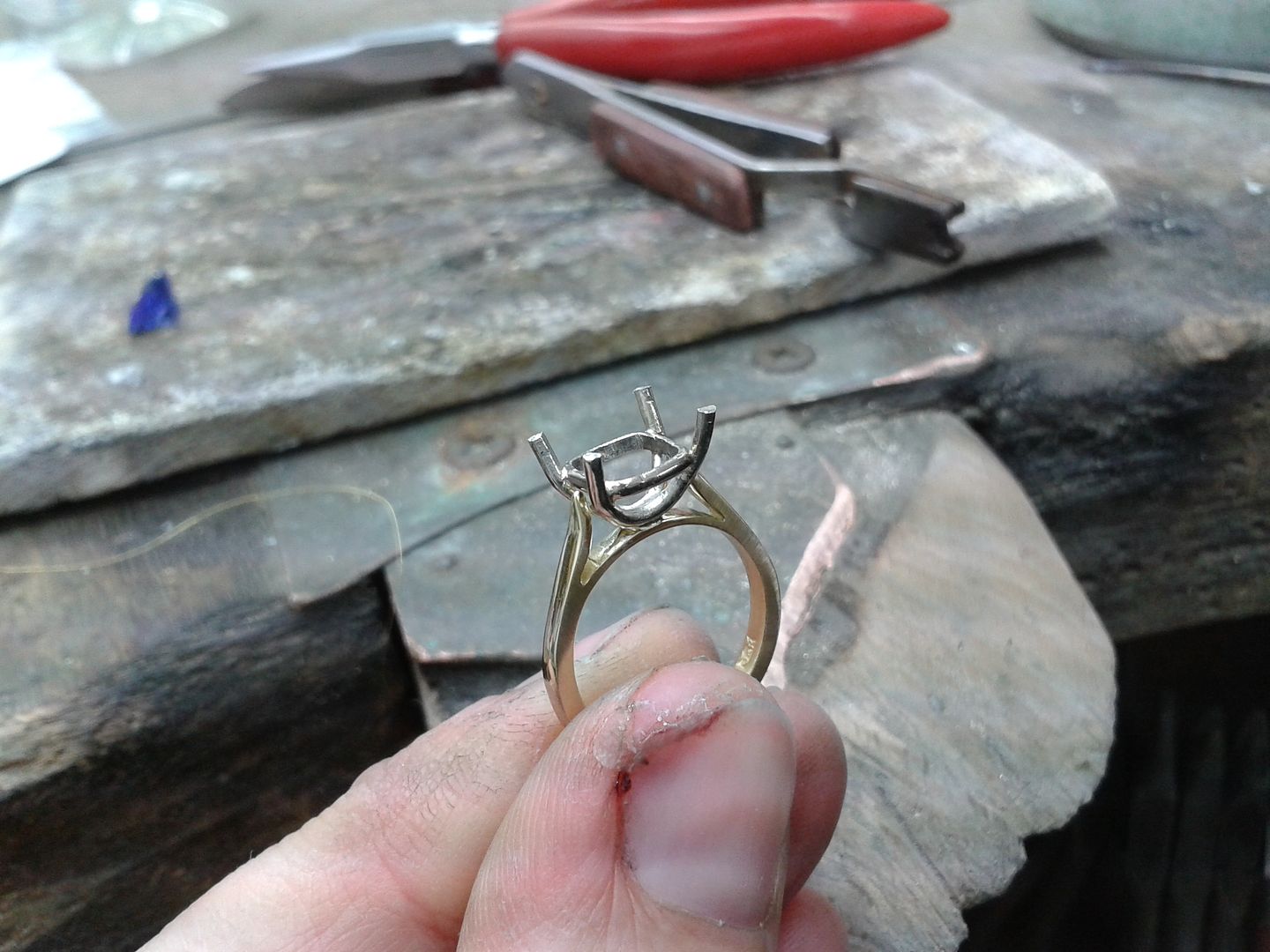
And all done:
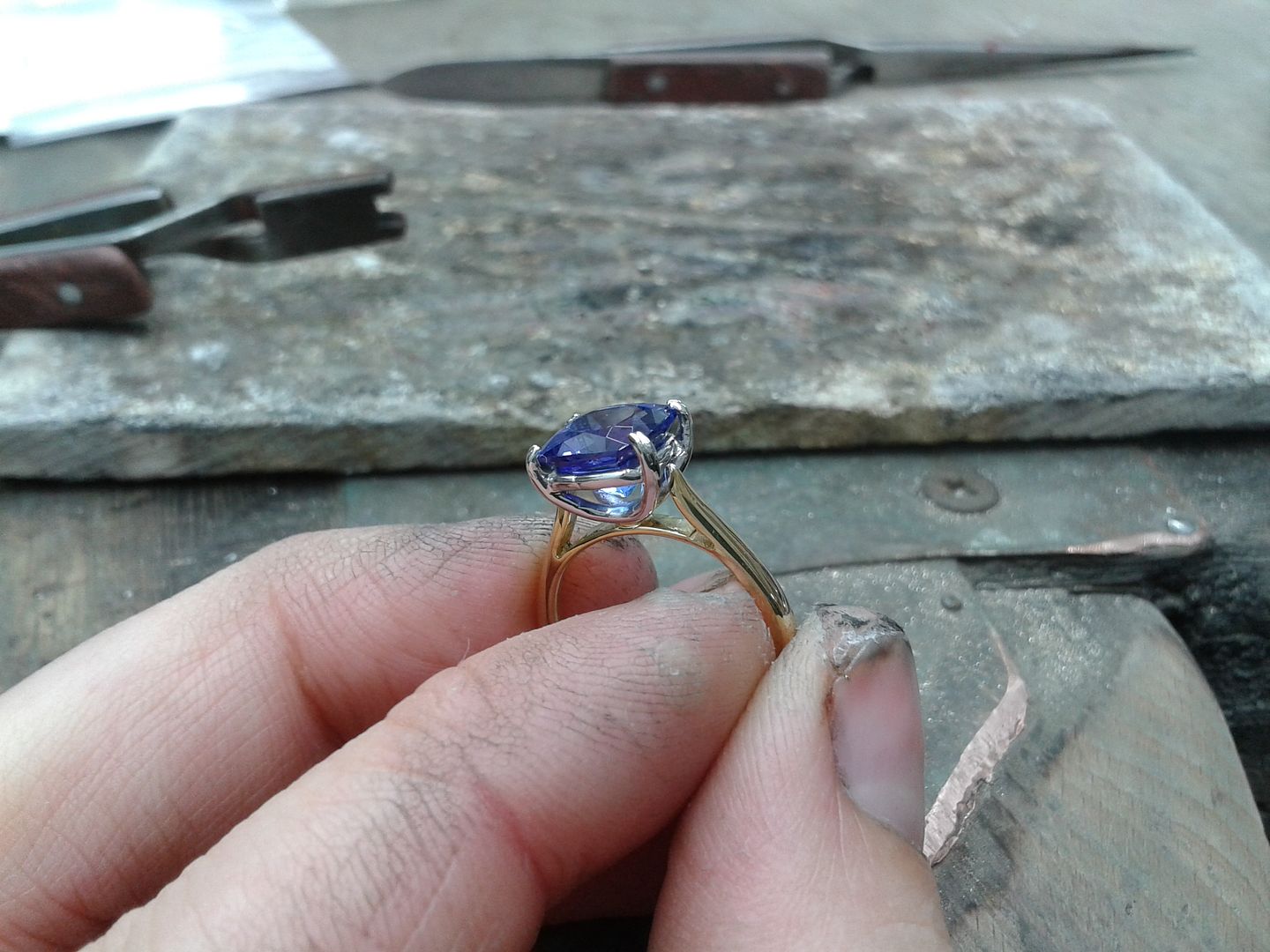
Another happy customer.........
More next month i hope.
Oh, here's a couple of other things i made between chemo treatments:
Made this cross to replace an item stolen from a customer.
Photo from customers insurance docs: 9ct and emerald
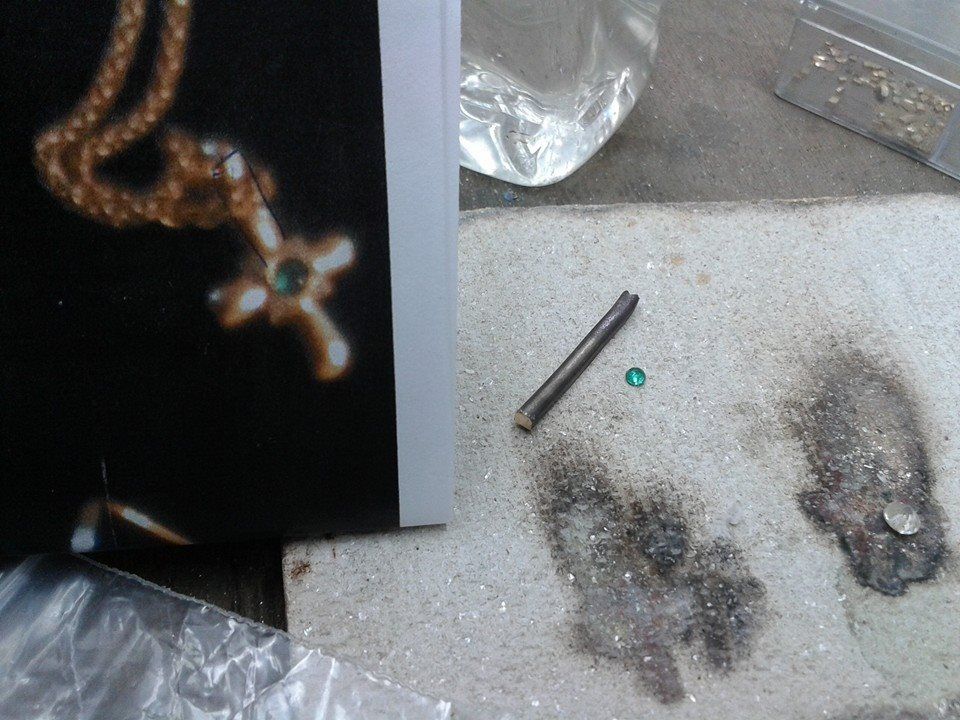
Cross built, just needs the emerald setting
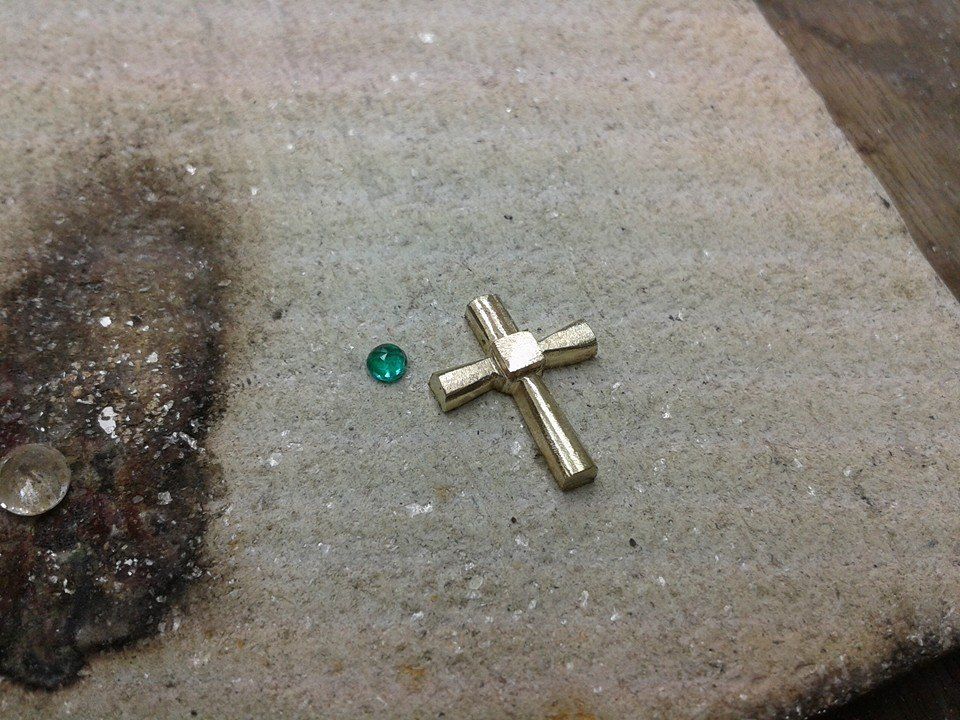
Drilling the setting
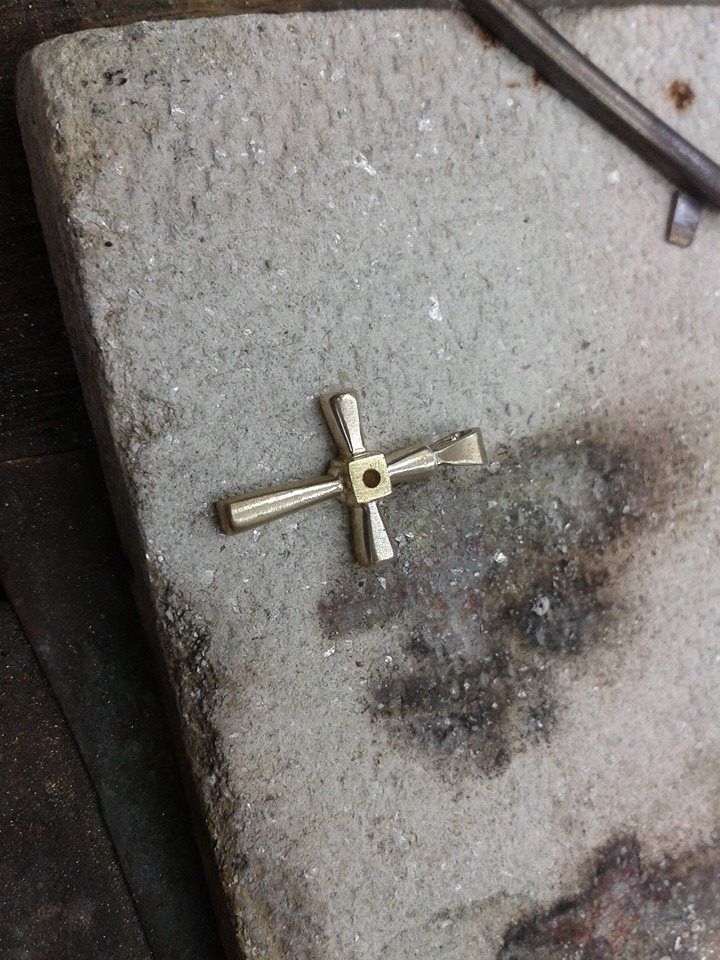
Setting all cut and ready for the stone
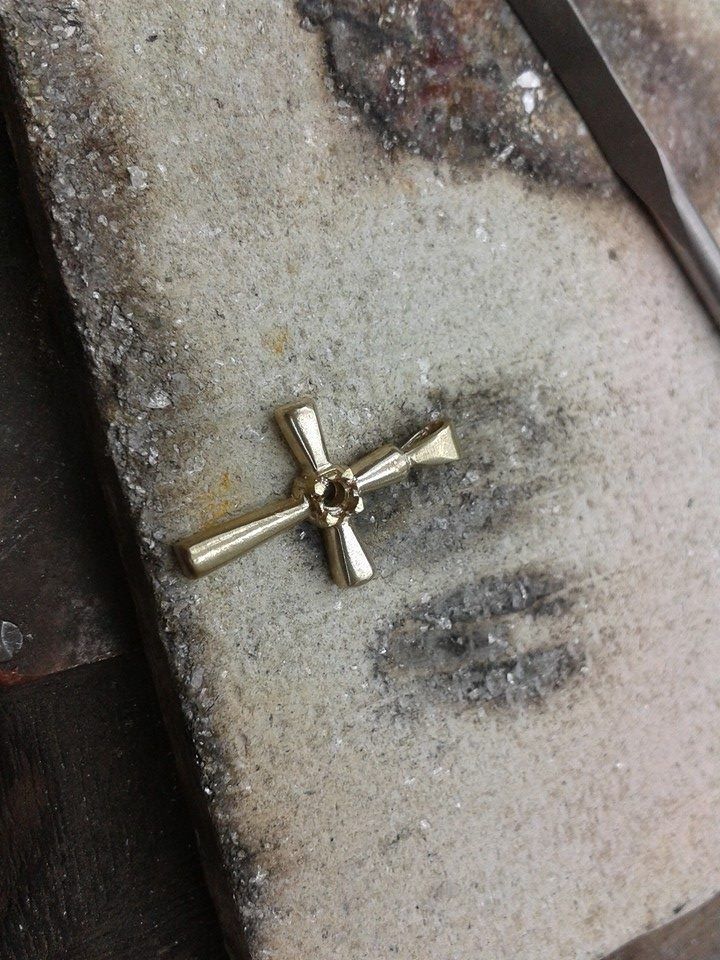
And all set
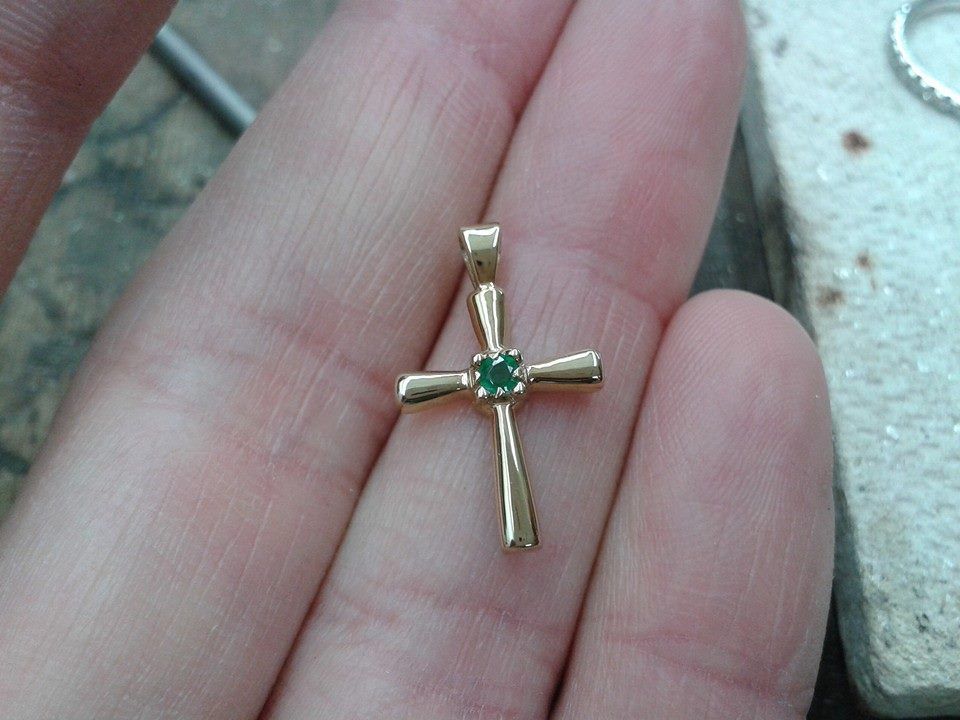
Because i liked it so much i made another chunkier one for stock
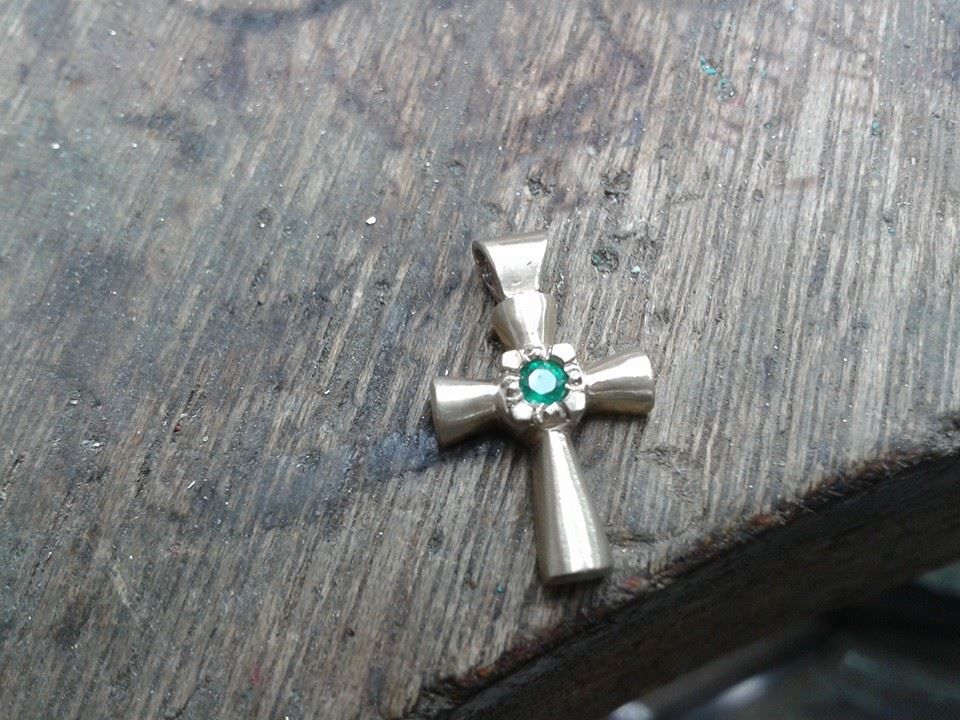
And finally a couple of watches in for service and refurb
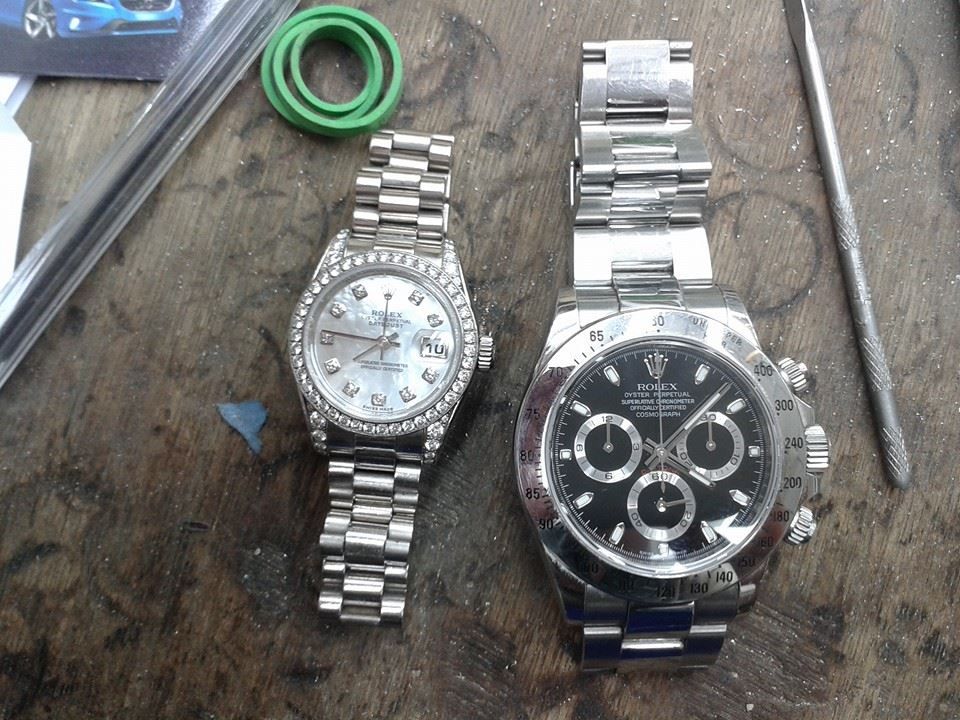
That said, here is a little something my very sore hands made on monday:
Start with 1 x tanzanite and some of the customers own gold, which we melted down from a couple of inherited wedding bands she had.
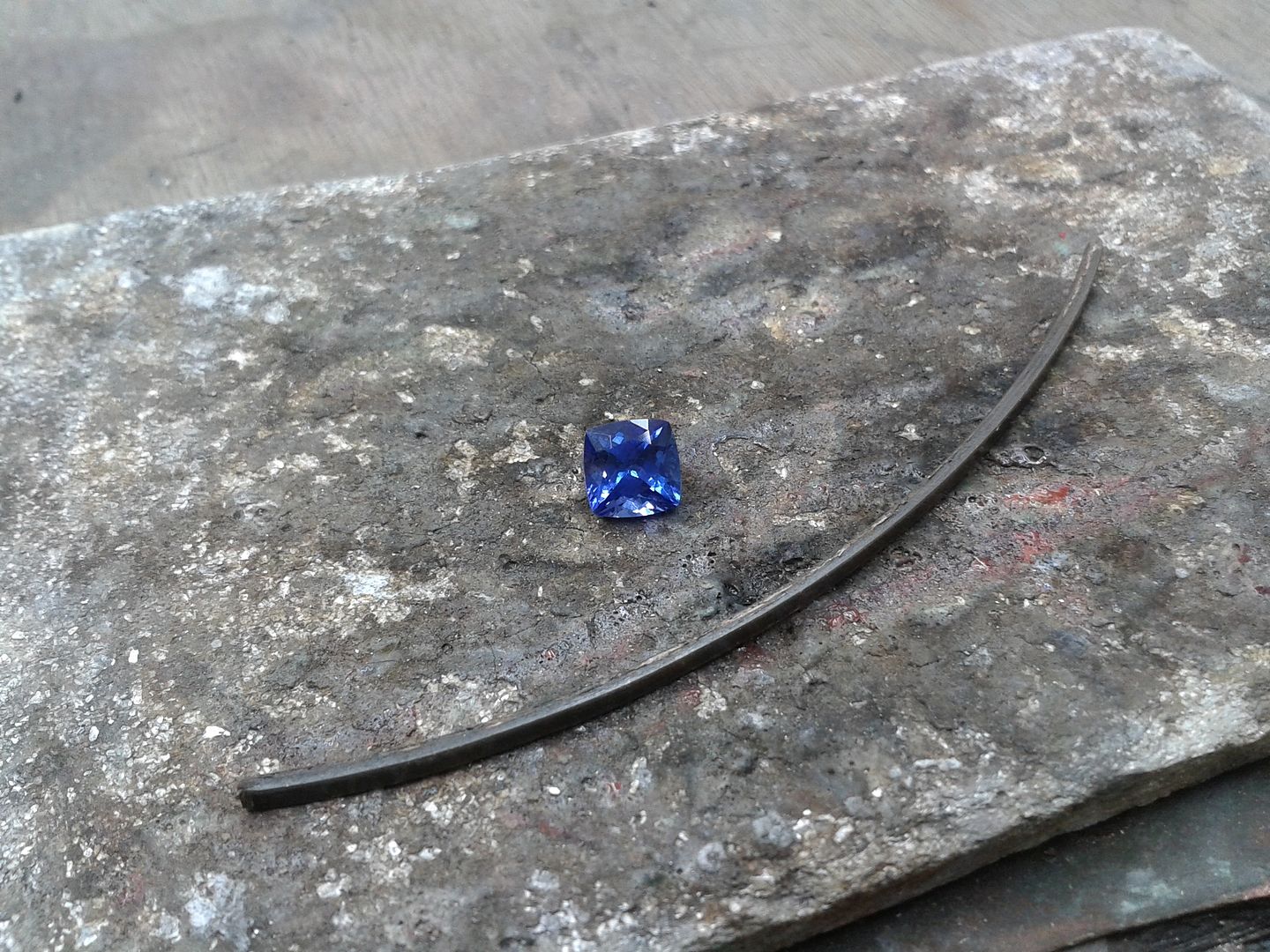
Take the gold bar (2.25mm wide x 1.75mm thick) and make a shank. Note the split shoulders (and finger).
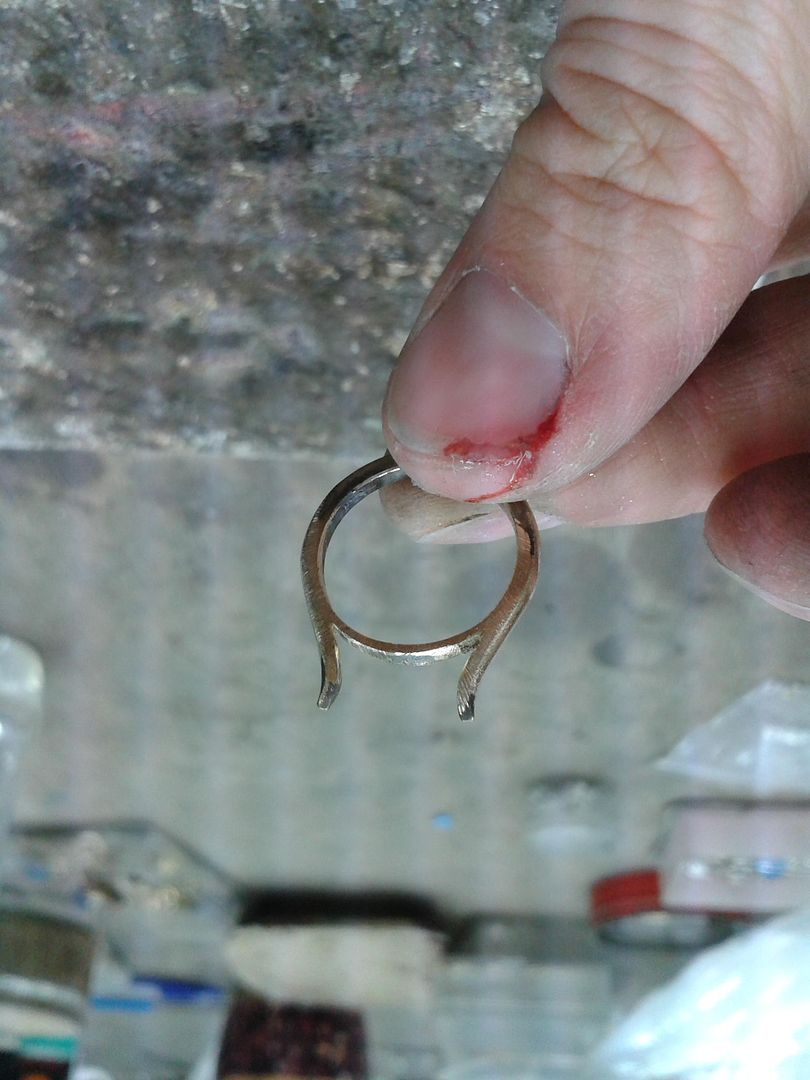
Now the shank is all cleaned up its time to make the setting. I made the setting using platinum wire to give it a lovely white finish. Its nice and soft too which makes it easier when setting such a fragile stone.
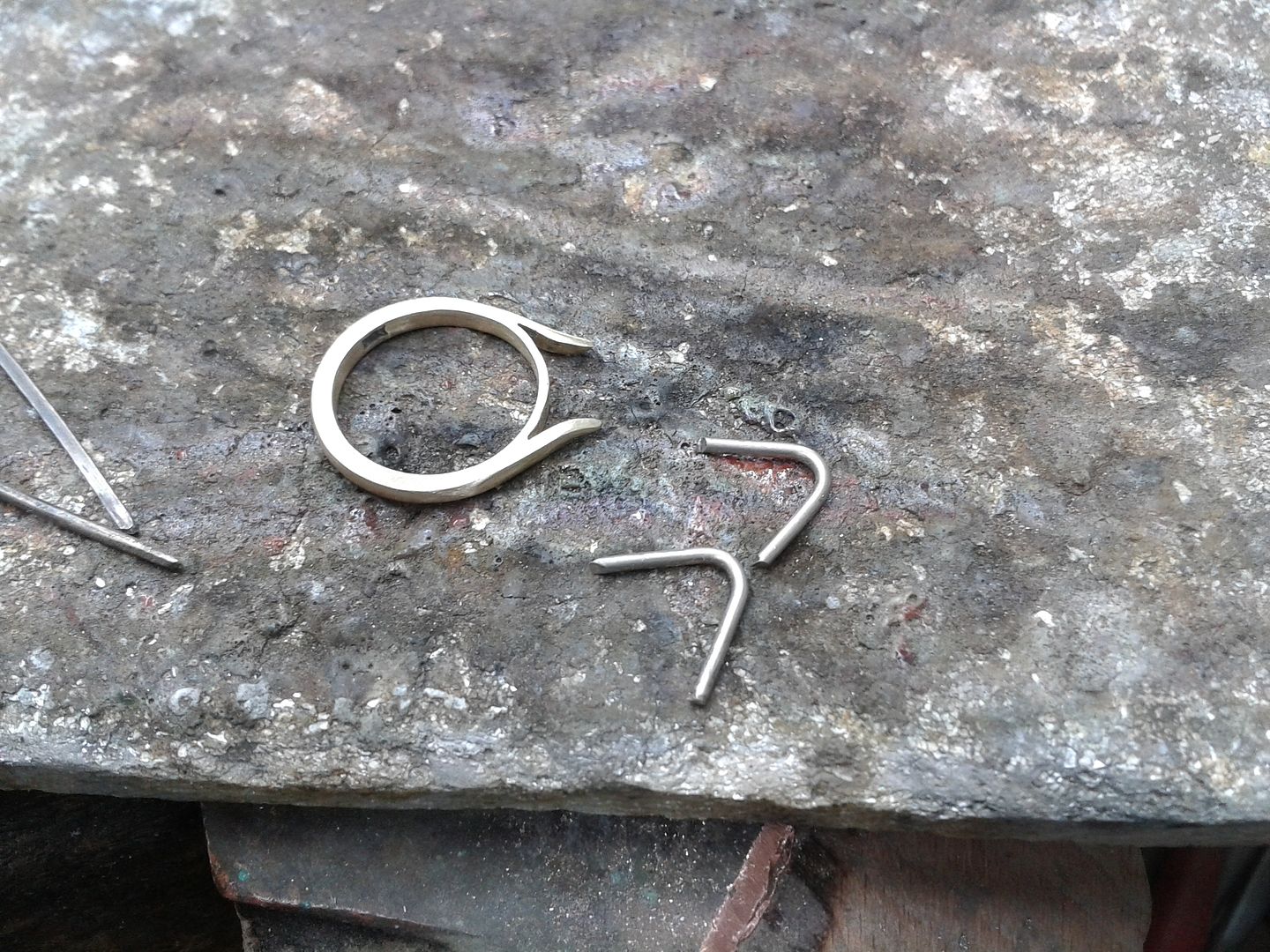
Simple setting part done
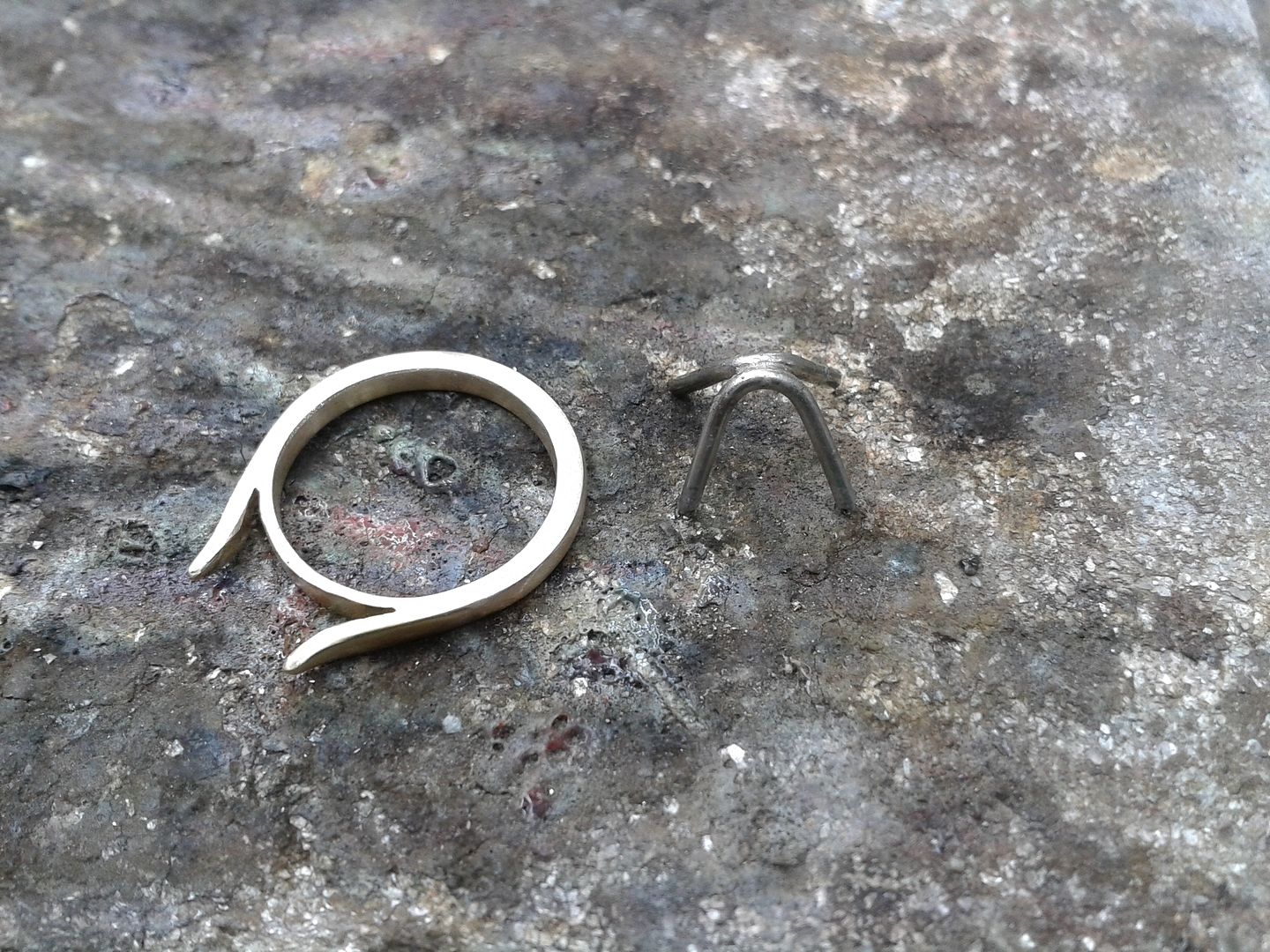
Setting complete, just needs fitting to the shank and finishing off. Note the strengthening brace around the setting.
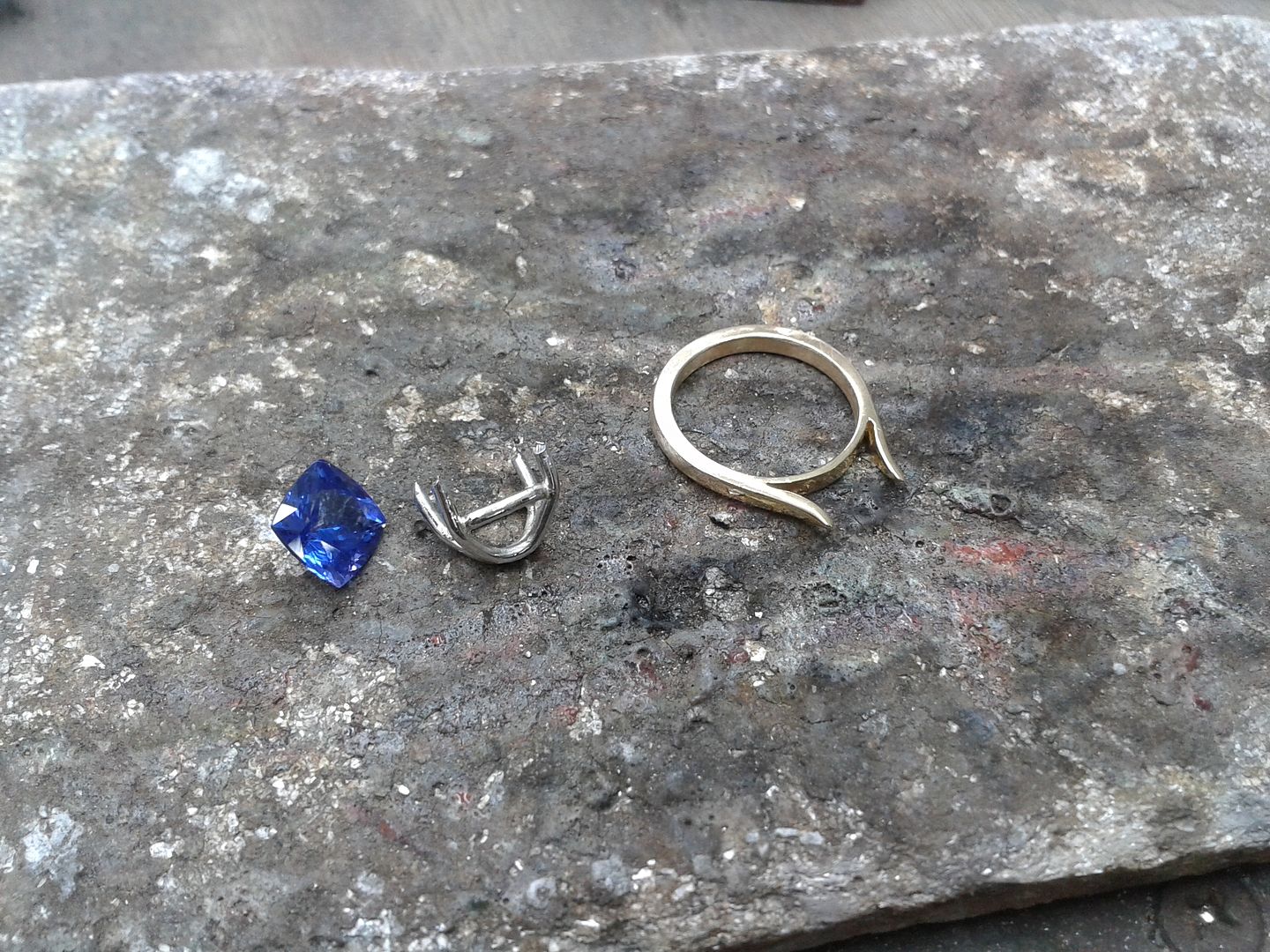
Fully assembled. Just need to set the stone.
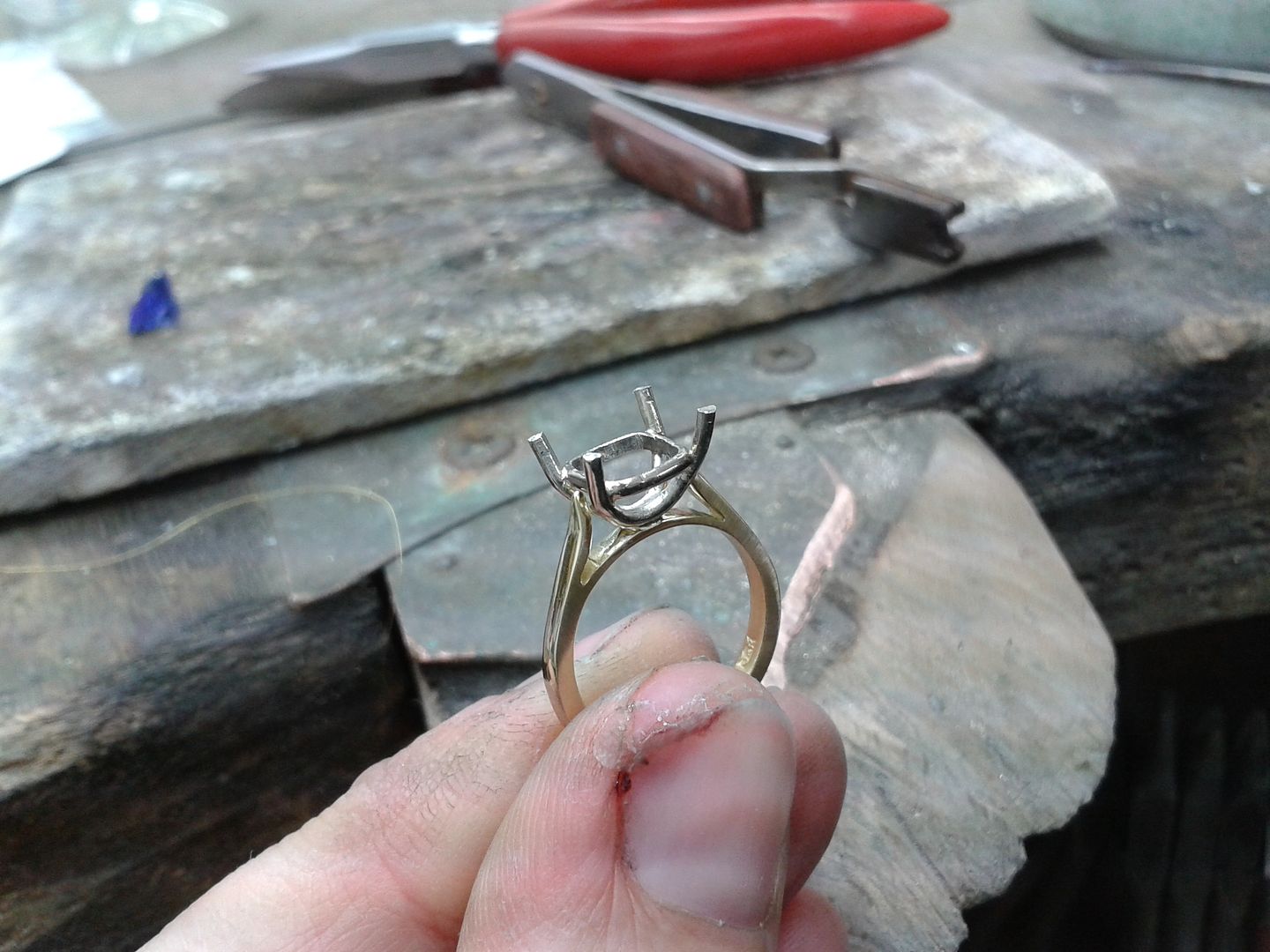
And all done:
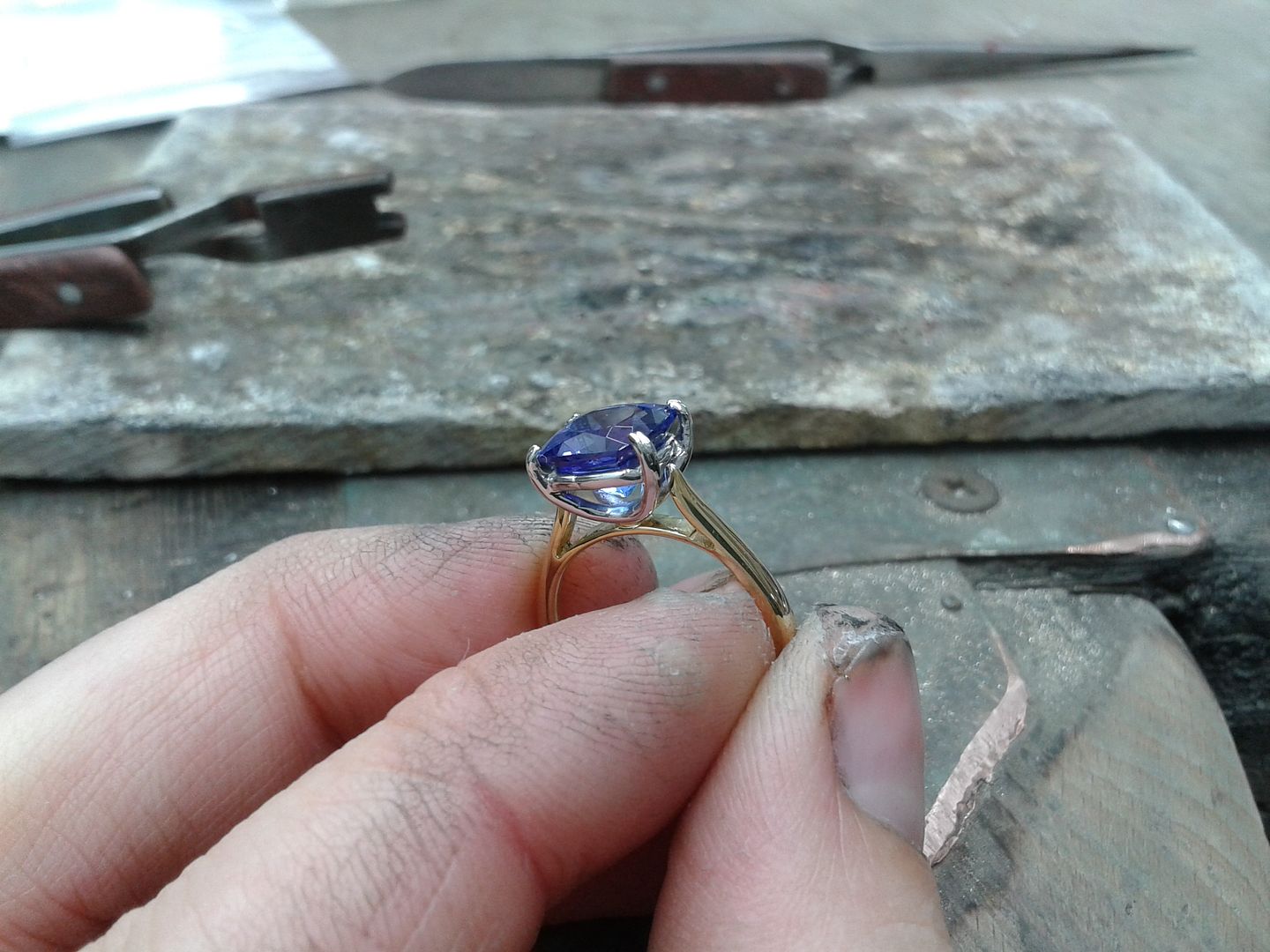
Another happy customer.........
More next month i hope.
Oh, here's a couple of other things i made between chemo treatments:
Made this cross to replace an item stolen from a customer.
Photo from customers insurance docs: 9ct and emerald
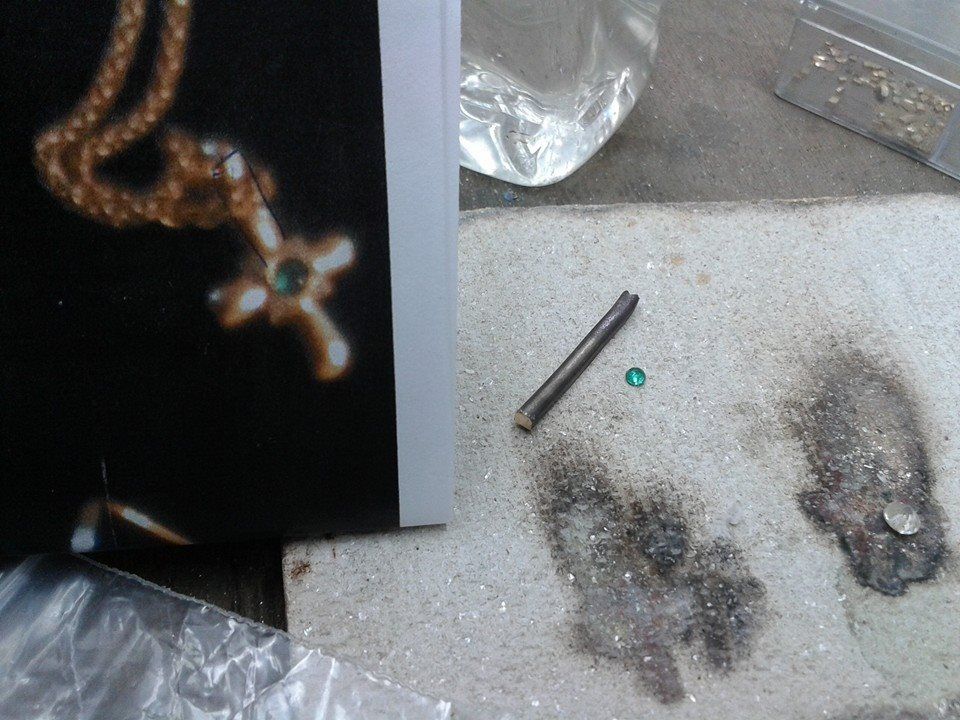
Cross built, just needs the emerald setting
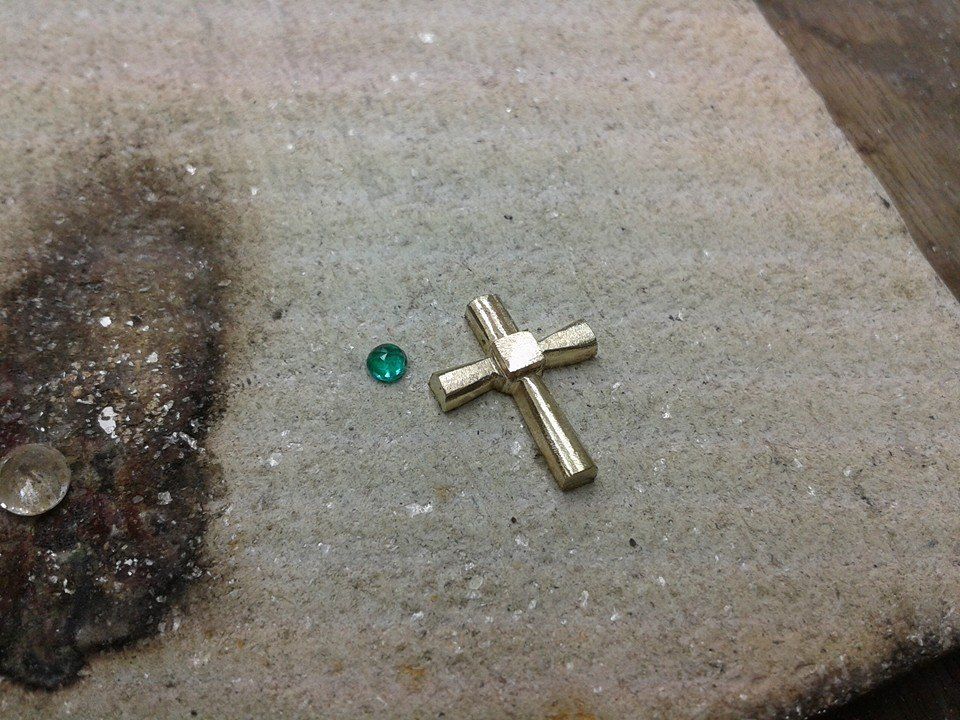
Drilling the setting
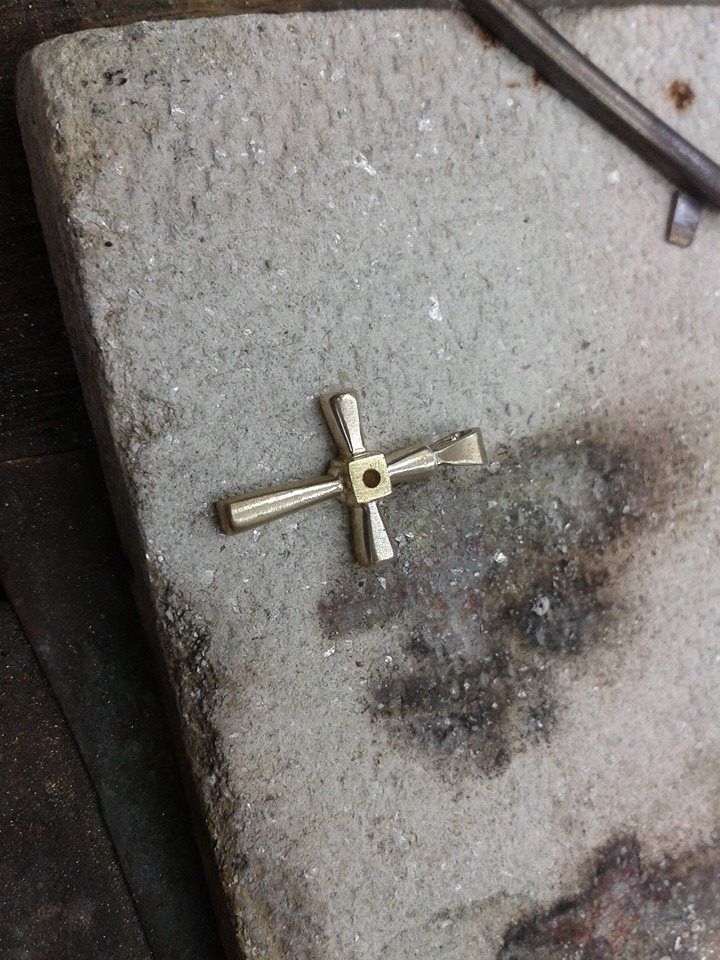
Setting all cut and ready for the stone
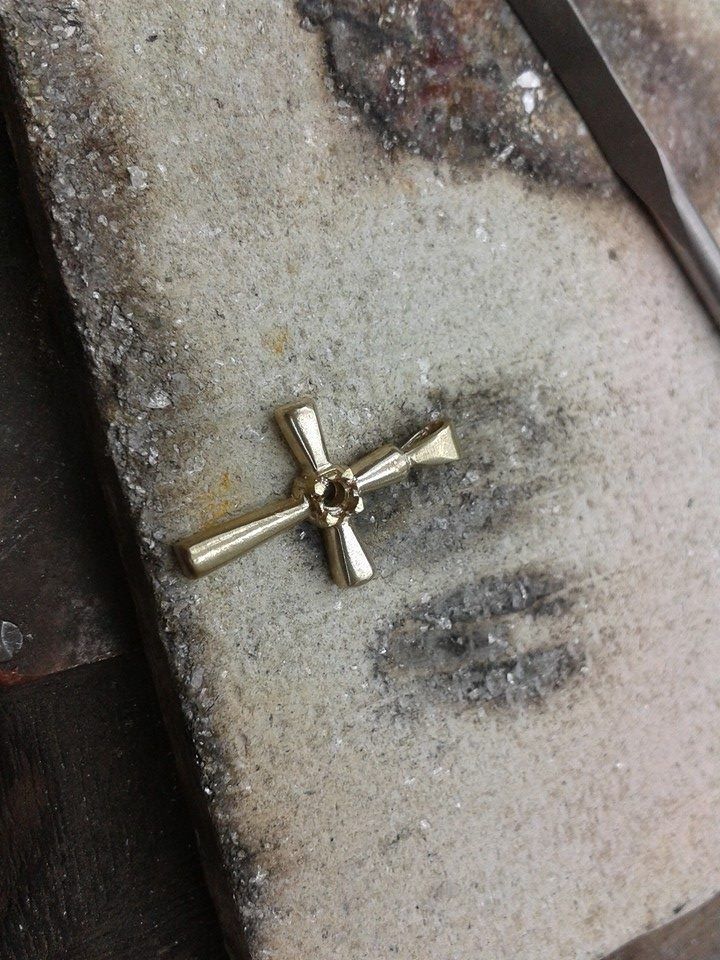
And all set
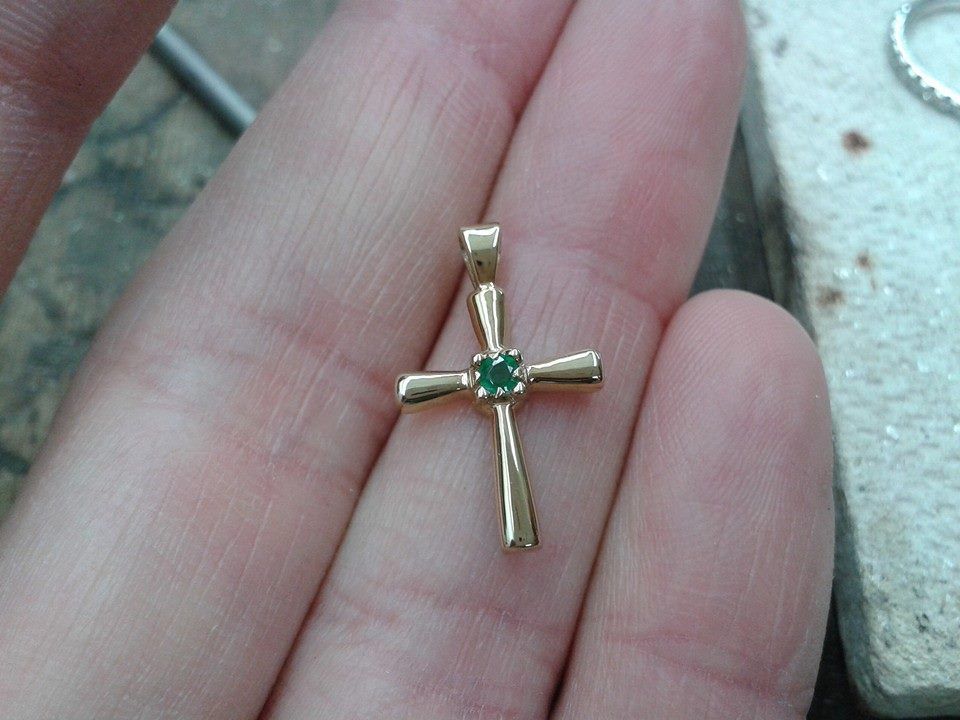
Because i liked it so much i made another chunkier one for stock
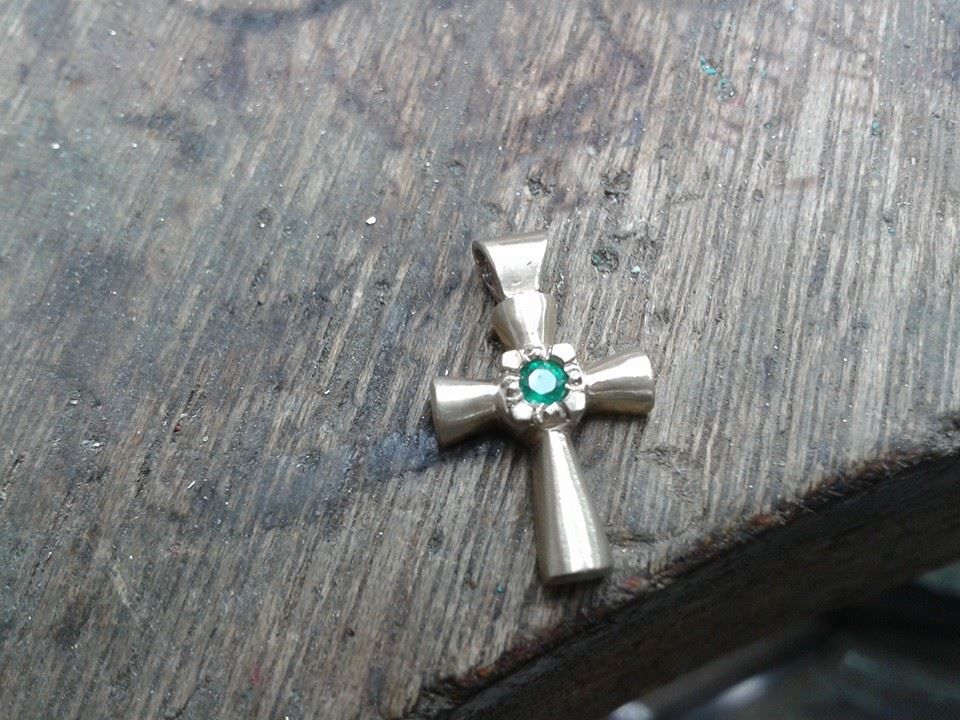
And finally a couple of watches in for service and refurb
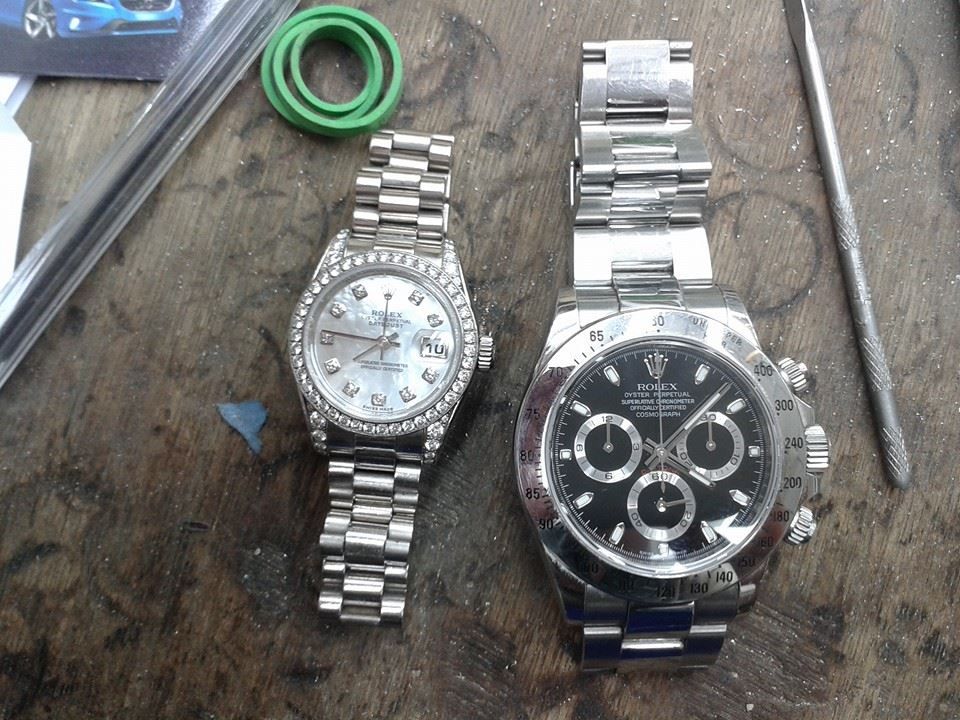
Thanks chap. As i said earlier, im not that fussed by it. It was a massive shock when i found out but medical science i so good now and the care im getting is so spot on i have every hope im going to come through it stronger than ever. I had my second chemo session yesterday and all looks to be going well.
Top tip for all out there. If you have any dodgy symptom, big or small. Be sure to get it checked out asap. My tumour was 10cm by the time it was discovered which is pretty big. Im just lucky it hasnt spread anywhere else!
Top tip for all out there. If you have any dodgy symptom, big or small. Be sure to get it checked out asap. My tumour was 10cm by the time it was discovered which is pretty big. Im just lucky it hasnt spread anywhere else!
Gassing Station | Watches | Top of Page | What's New | My Stuff