Unusual job on the bench today
Discussion
ecain63 said:
Came in at £5460 after charges. Happy days! Still waiting for Hoover bags and emery paper burn.
It always shocks me. I still remember at my old work chasing a new apprentice down the stairs because he'd picked up the black bin bags full of old dust filters from the polishing machine and was taking them out with the other rubbish. Noooooo! 
ecain63 said:
That's a brilliant insight into your job - thanks for taking the time to post 
Every so often (ie regularly) we get jobs in where we need to rectify the work of another 'do on the cheap' jeweller. Sometimes the shops that we do work for cut a corner and have another outworker finish a job that would normally be left to us. In this case one of our shops were tasked to design and string a 5-row of pearls and provide a new clasp to make it all work. We do stringing on site but it's not a high priority job for us so often our shops will send to a full time pearl stringing outfit to save time and money. We'd usually be handed the clasp build job on this one after the pearls were strung but it turns out the stringer suggested he could complete the job without the need for Eddie to get involved:
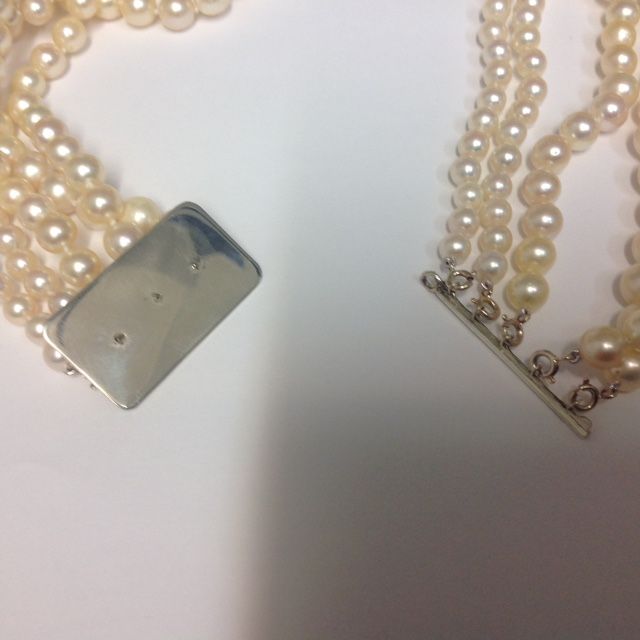
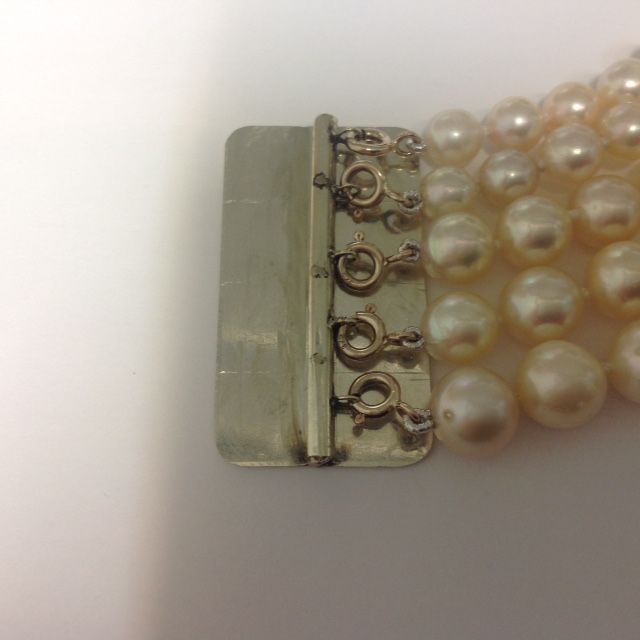
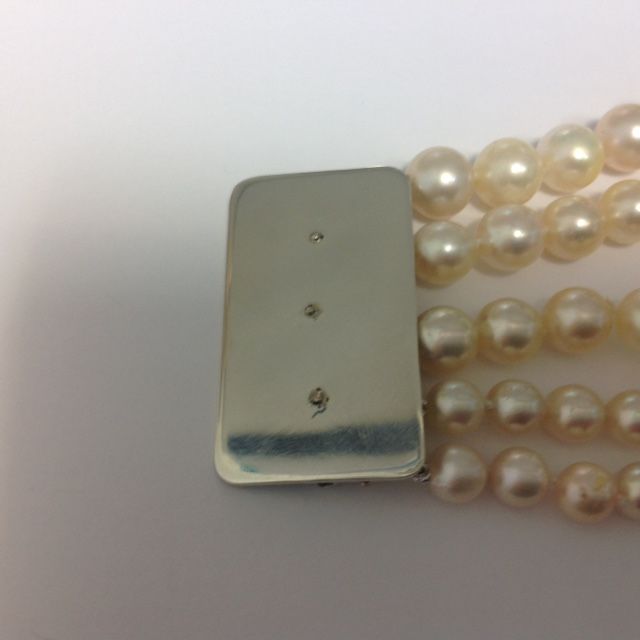
^^^^^^That was the finished product and was supposedly good to go to the customer. I've no idea what the design was based on but the thing had dodgy laser welds, mistakes badly corrected, sharp edges and a poorly cleaned and polished finish with rhodium applied in random places. Luckily the shop in question has worked with us for many, many years so came to me straight away with a request to save the day:
So, I started with some 9ct white gold wire drawn down to a couple of different gauges.
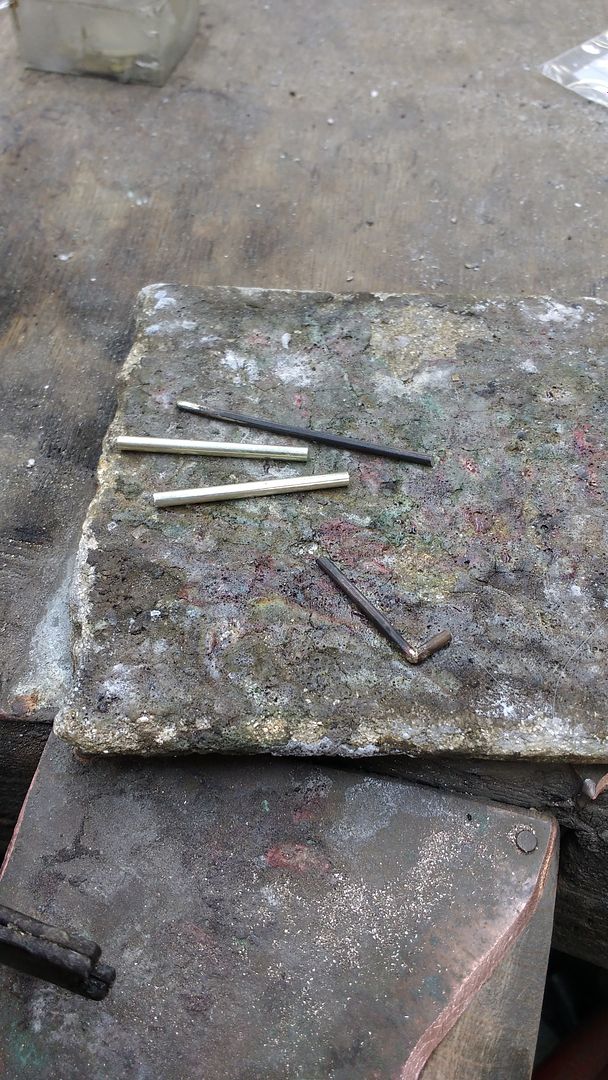
I've missed out a couple stages due to me only deciding to photo log it halfway through the build but here you can see the wires have been cut, soldered and shaped, cleaned and then a tongue fitted to one side:
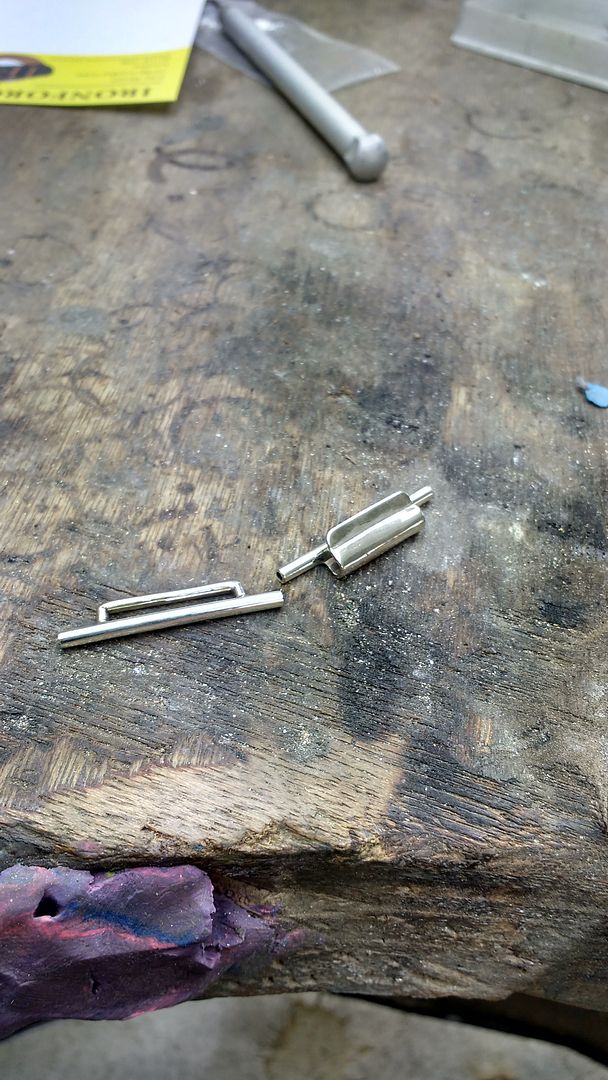
A quick test fit to make sure the clasp works before getting on with the next bit:
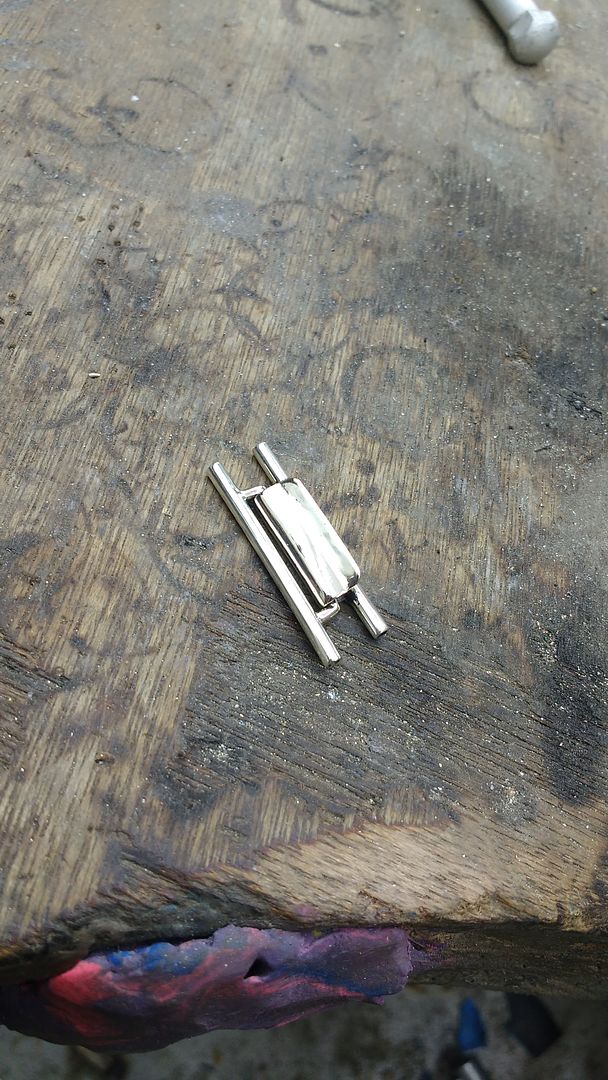
I made up some (10x) 9ct white gold loops for the pearls to clip to and soldered them on at equal intervals on the outside of the bars:
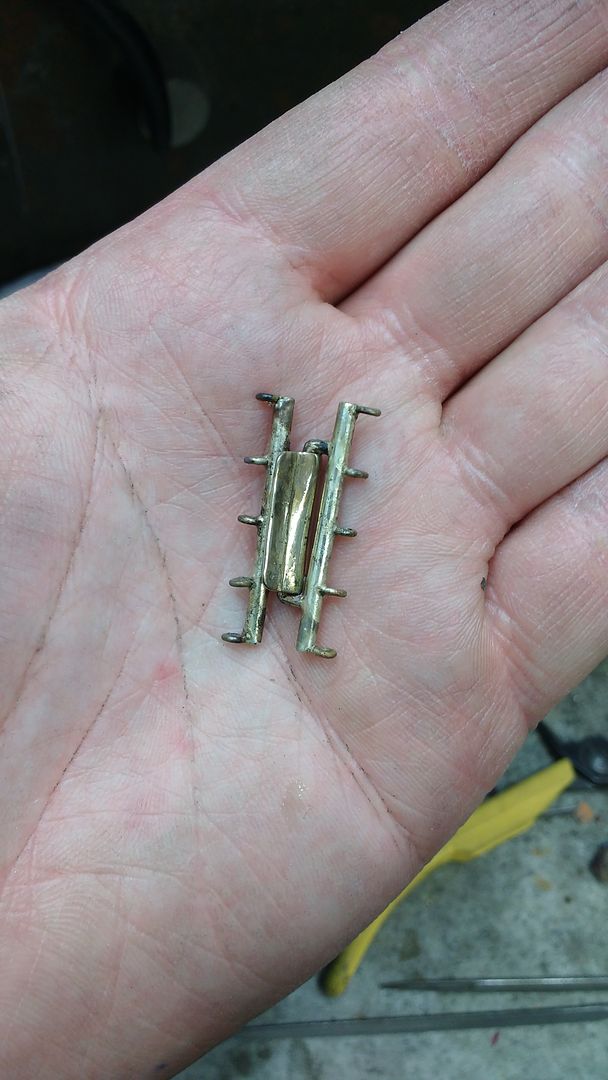
Test fit to make sure the pearls sit in the correct position. I also soldered little balls to the end if the bars to give a little decoration:
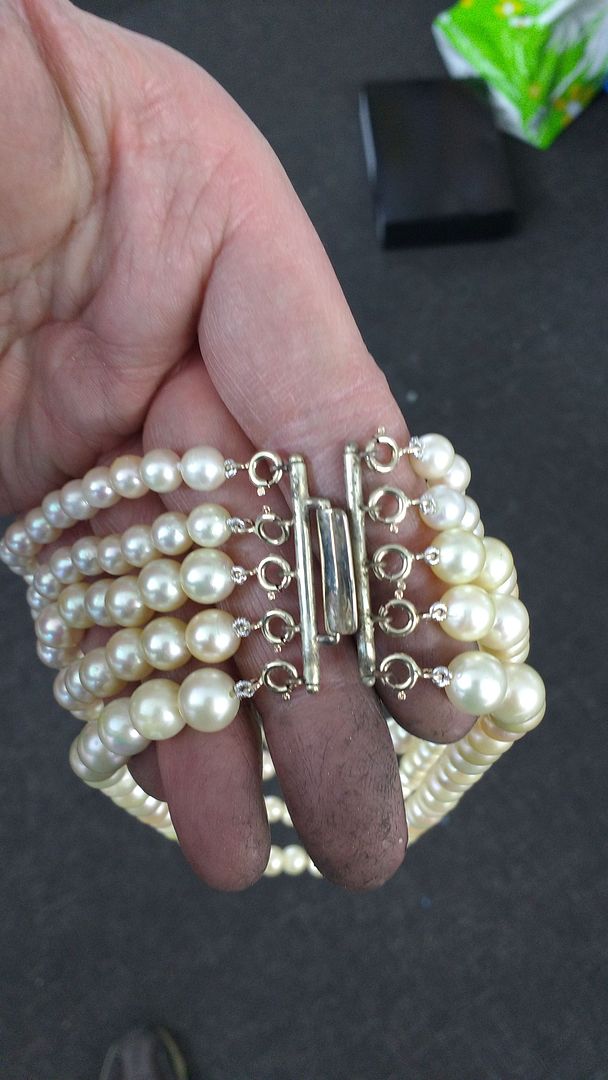
Clean, polish and rhodium and then test fit on the missus:
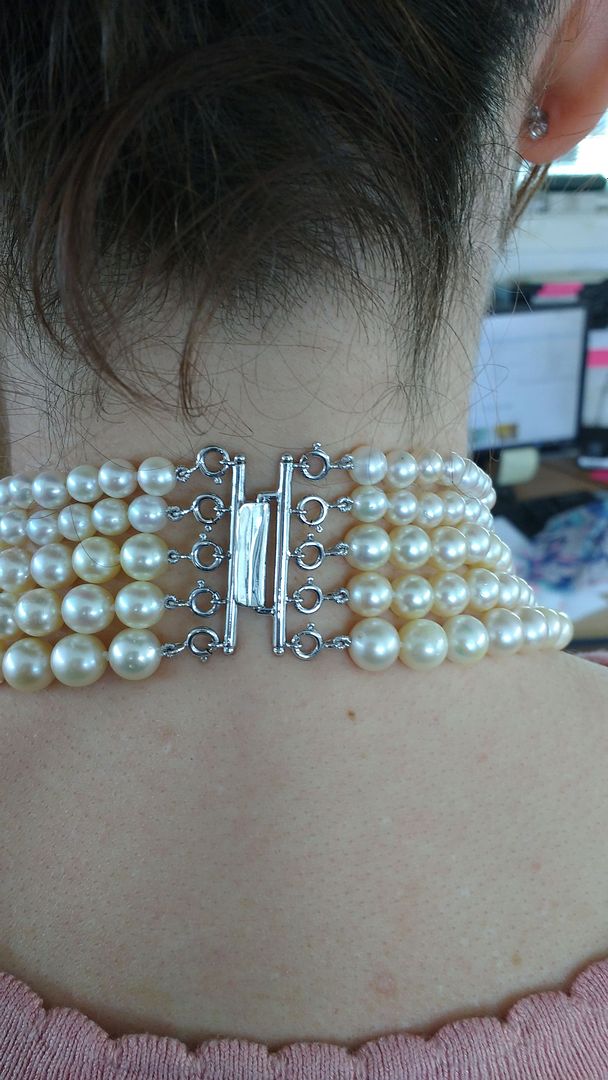
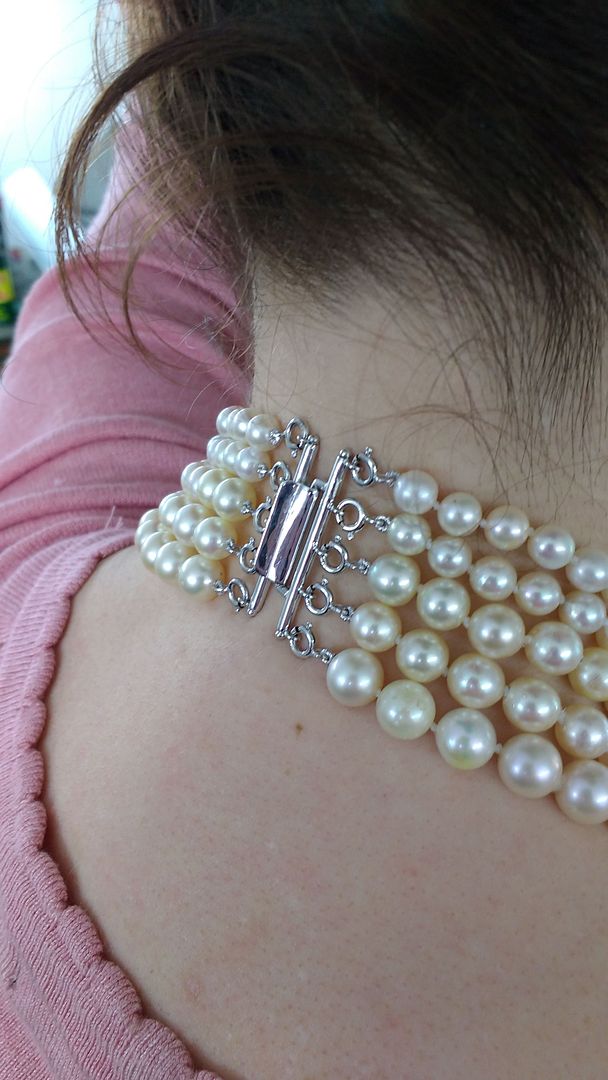
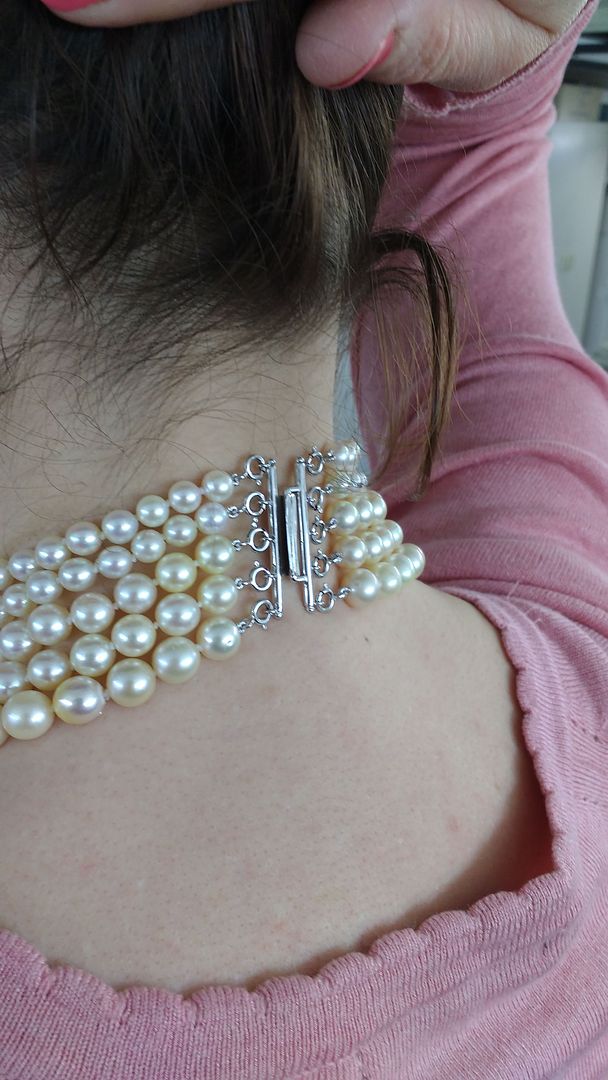
Job done

Eddie
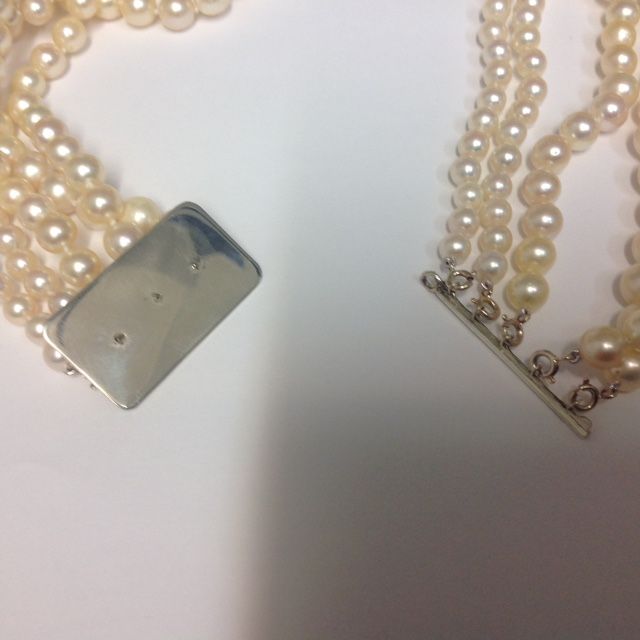
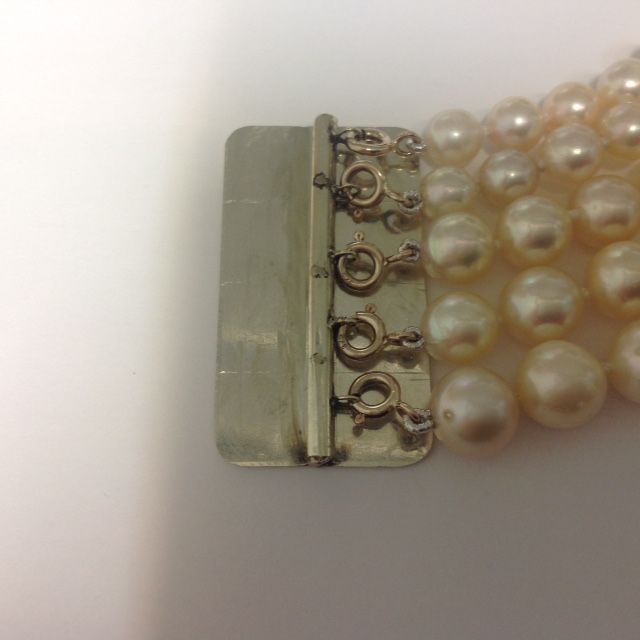
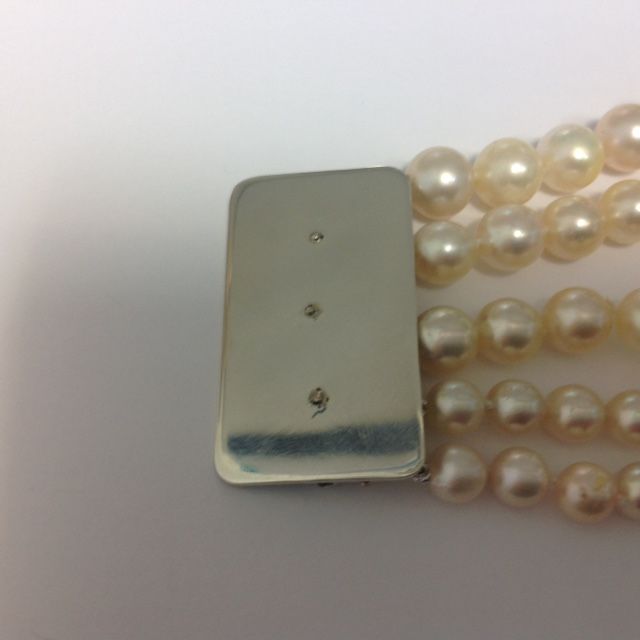
^^^^^^That was the finished product and was supposedly good to go to the customer. I've no idea what the design was based on but the thing had dodgy laser welds, mistakes badly corrected, sharp edges and a poorly cleaned and polished finish with rhodium applied in random places. Luckily the shop in question has worked with us for many, many years so came to me straight away with a request to save the day:
So, I started with some 9ct white gold wire drawn down to a couple of different gauges.
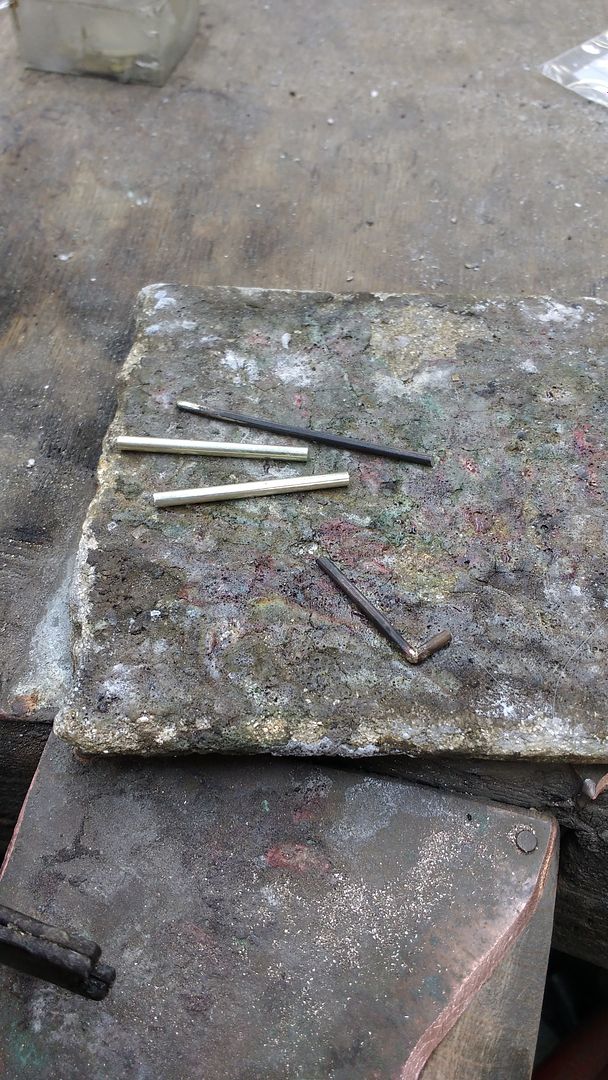
I've missed out a couple stages due to me only deciding to photo log it halfway through the build but here you can see the wires have been cut, soldered and shaped, cleaned and then a tongue fitted to one side:
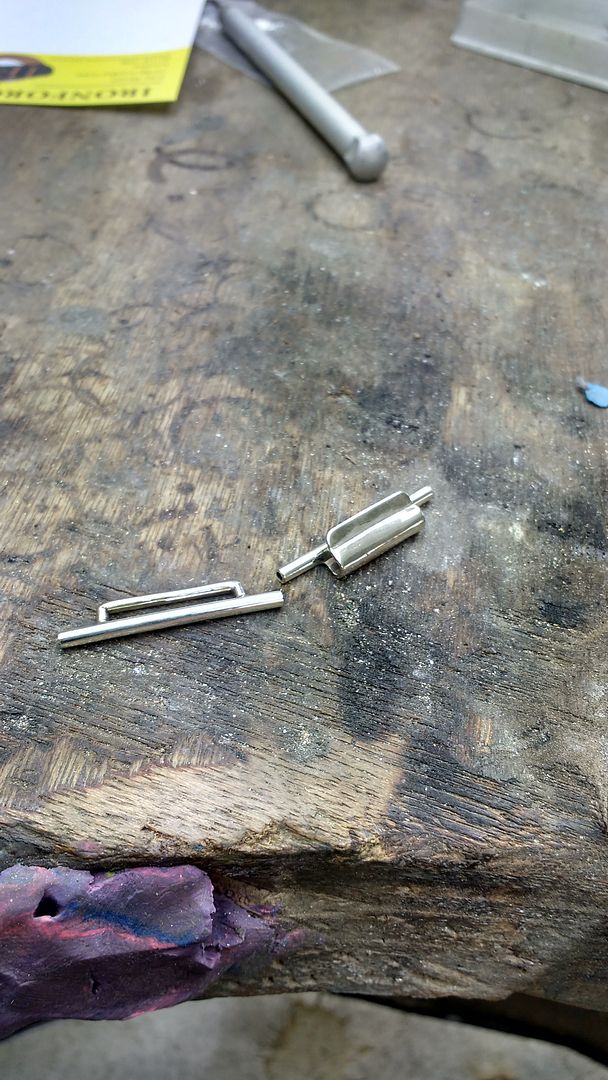
A quick test fit to make sure the clasp works before getting on with the next bit:
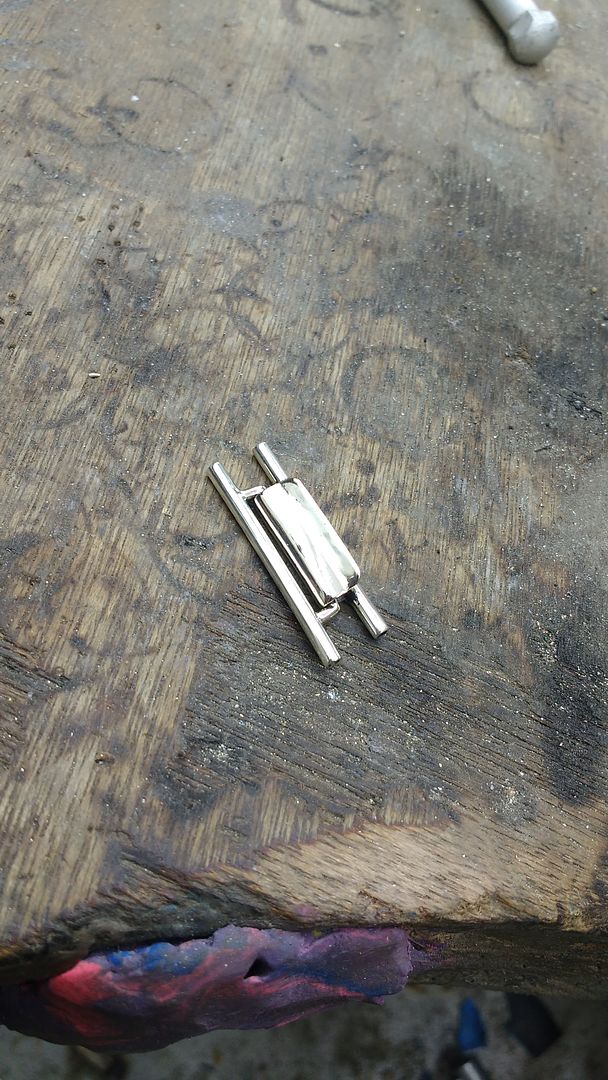
I made up some (10x) 9ct white gold loops for the pearls to clip to and soldered them on at equal intervals on the outside of the bars:
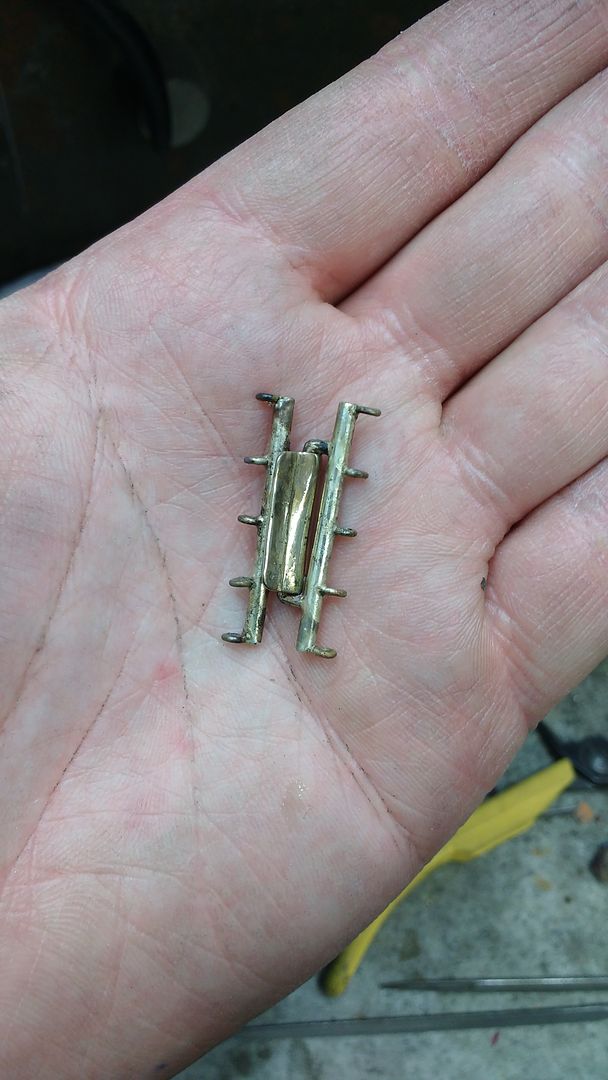
Test fit to make sure the pearls sit in the correct position. I also soldered little balls to the end if the bars to give a little decoration:
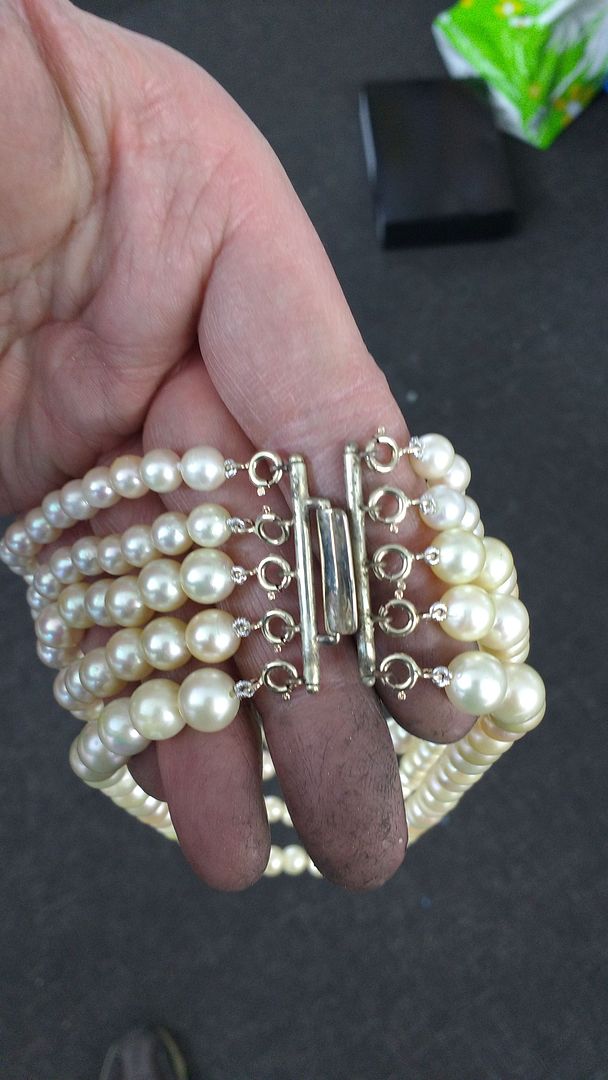
Clean, polish and rhodium and then test fit on the missus:
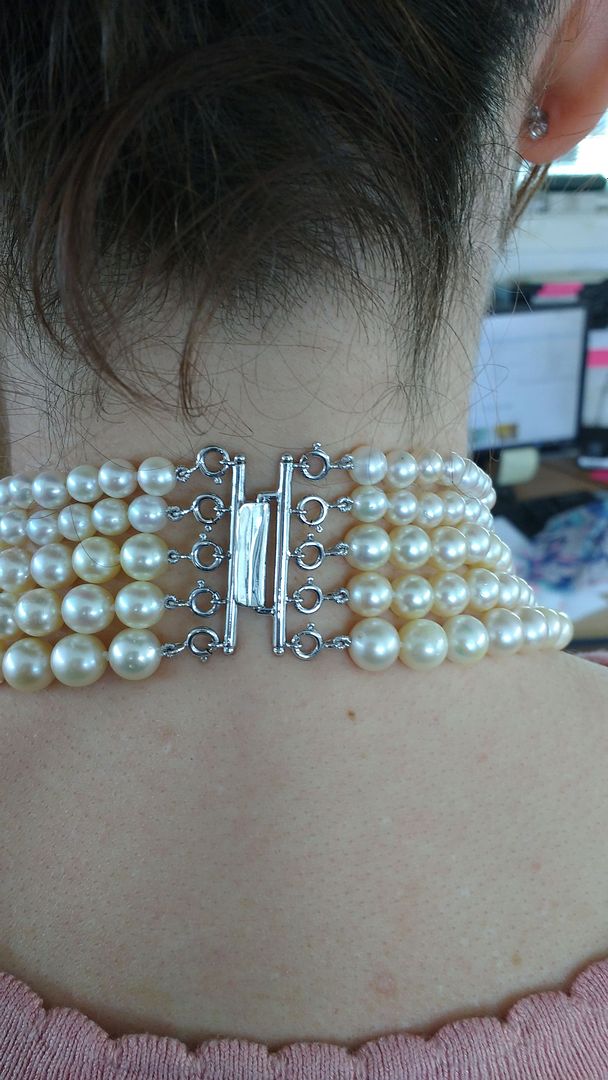
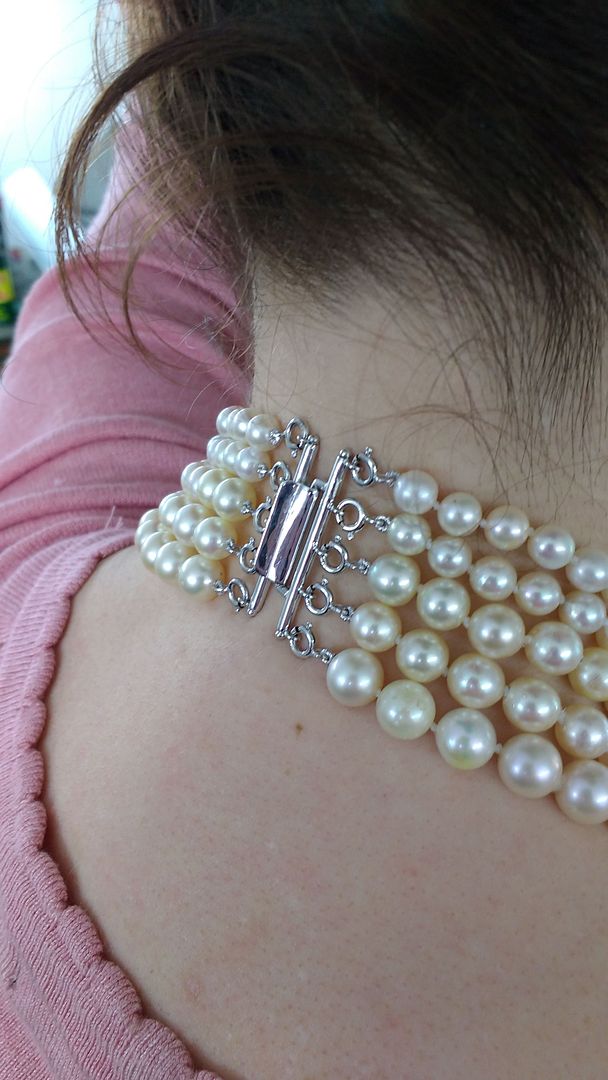
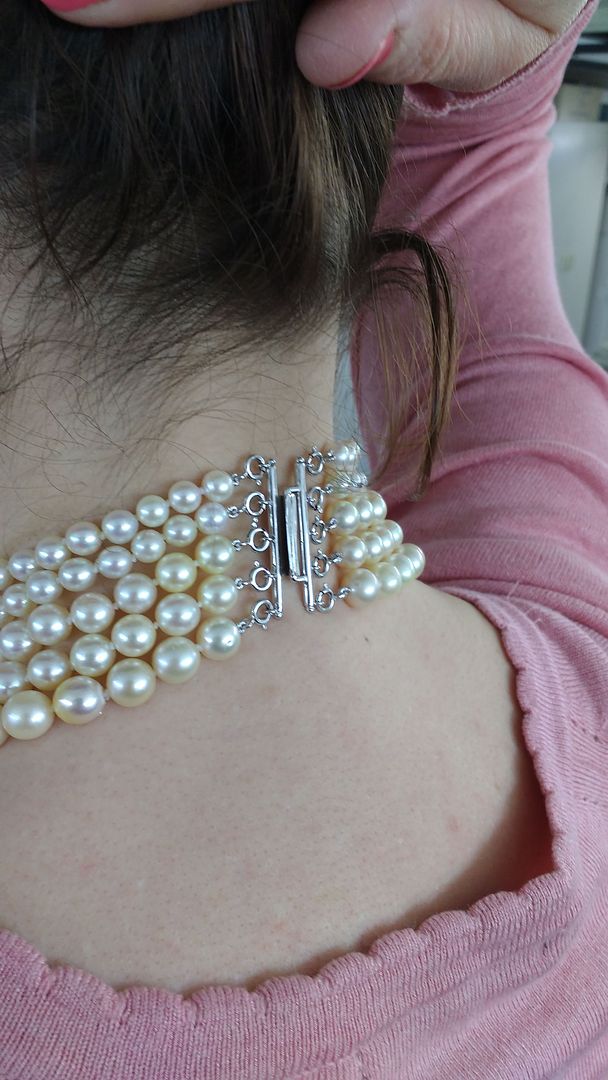
Job done


Eddie
gobuddygo said:
This is one of my favourite threads, amazing work, if i documented my job (IT Technical consultant) it would send you all to sleep.
same here on both points. I get very frustrated that the start of my career i was making things... i mean software things, but it's the same parts of the brain it touches, and rewards it gives when things do what they are meant to do... but now all i do is sit in meetings, arguing with idiots (impossible to win) and writing documents. All v depressing.rat840771 said:
Very interesting vario, but surely the labour involved in repairing that is near the £160 for a new movement? There must be a few hours work there!
Can you do an full Auto strip next, maybe ill send my seadweller across for a service and you can do that?
If it had been a full overhaul the costings would have been close, but this was a minimal strip-down / rinse / assemble and lube to replace obviously missing and damaged parts. Total time was about 2 hours from un-case to re-case.Can you do an full Auto strip next, maybe ill send my seadweller across for a service and you can do that?
The difference with a full overhaul is the inspection, which is what can take time. I'll do an auto strip-down when I have time to take photos during one (been a little busy lately!) but here's an example of the sort of thing that's being looked for in a full overhaul.

This is one of the balance end-stones from a cal. 861 Speedmaster. The single dot of light arrowed is a reflection off a wear pit seen through the left eyepiece of a stereo microscope @ 20x magnification. To give an idea of scale, the blue mark is a single line from a standard Parker medium ballpoint pen.
During the initial work (done with 3x - 10x traditional loupes) I missed this but it was obvious there was a problem from the timing results - dial down and vertical positions were good, but dial up (when the balance pivot is running directly on this jewel) showed a sudden loss of amplitude and between 20 and 25 seconds per day variation in rate.
To give an idea of how easy this sort of thing is to miss, this is the view through the right eyepiece without moving anything. That's a difference in viewpoint of the distance between your eyes and it almost totally disappears - you may just be able to pick it up if you know it's there:
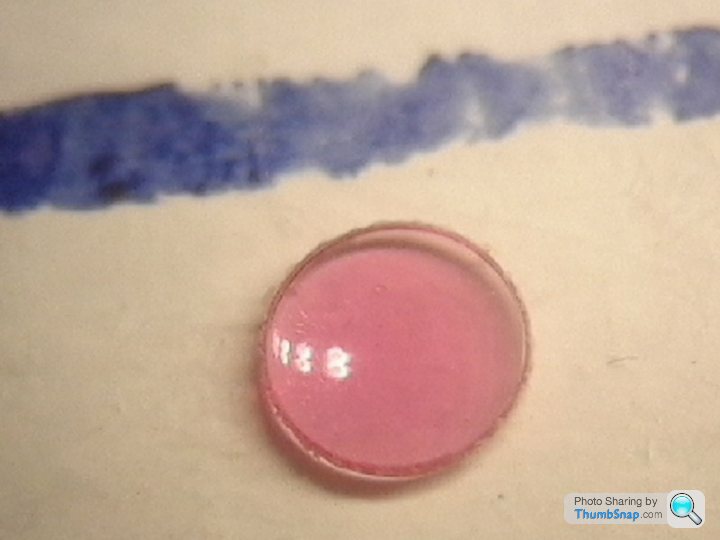
NeMiSiS said:
Excellent as usual.
can't believe the value in that bag of dust.
Your wife suits a pearl necklace, keep updating the best post on PH.
As said, still awaiting the return value of the hoover bags and emery paper. Not sure of the value but i'm hopeful it'll be similar or better than the bag of dust.can't believe the value in that bag of dust.
Your wife suits a pearl necklace, keep updating the best post on PH.
Claire restrings her own pearls as well as the customer jobs. She also does costume and bead work for her own amusement and use. Handy skill to have if you like to vary your wardrobe.
I'll be sure to keep you updated,
Eddie
.
.
.
.
As a sort of funny, sort of not funny story: About 8 weeks ago we had a manhole cover erupt in our storeroom, which emptied a whole lot of sewerage into our polishing room. Obviously we needed to get it cleaned up so employed the services of an industrial carpet and flooring cleaner. I wasn't in that day as I had an appointment with the back doctor so the missus arranged for a chap to come round and clean up. He came along and the job only took an hour with his kit.
Now, it's been 3 years since we changed the carpet in that room and it's had 3 years of dust settle and fall through the pile. What escapes the hoover will be burnt out every 5 to 10 years so we generally get back most of what we waste in the machines eventually. As I said, he came, sucked up and deep cleaned the carpet. Everything that he sucked up not only had s

2 weeks later he came back to make a wedding ring enquiry, which is great for us as a business. The first thing I asked was what he did with the fluids. Before he answered I told him the value of the last carpet burn. With a very gutted and genuinely shocked voice he gave his answer. He'd ditched the waste water down the drain outside the shop as soon as he left! Hahahahahahahahah! Oh how I laughed!
If I'd been there on the day I'd have asked to keep it myself. Perks of the job etc! Being very new to his business (just bought it off another chap) it did not click for him to refine what he'd sucked up. We both missed out at the end of the day but he lost out more by his lack of experience. I reckon a couple of months wages he chucked away that day. Ouch!
Because I know you love them, here is another 2-tone wedding band for a PHer.
Starting with some 18ct yellow gold I made an 8mm wide band, about size X. The customer has big hands so he needs a big old ring!
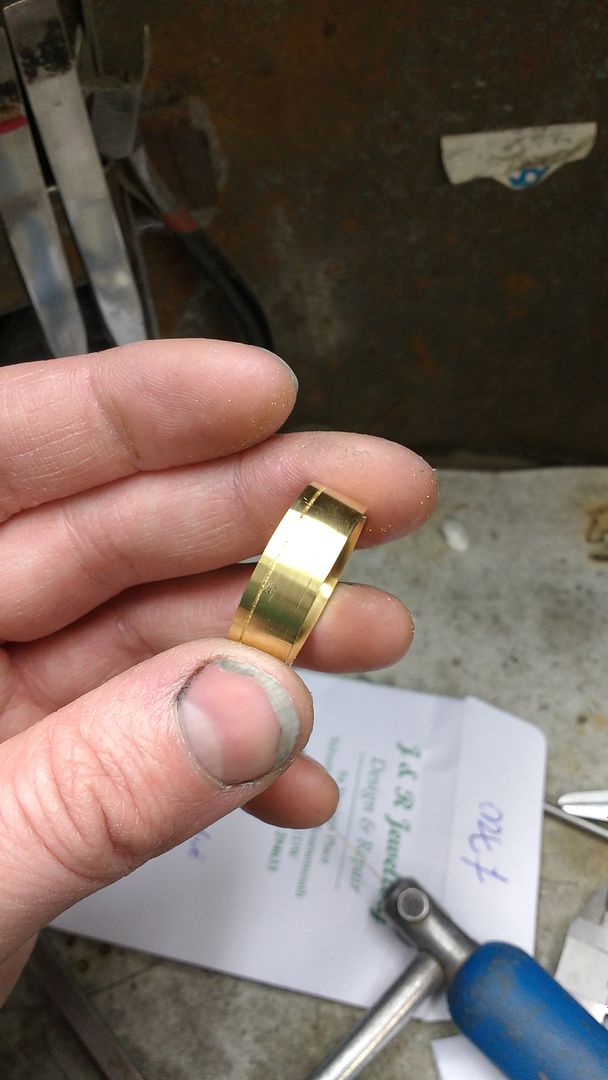
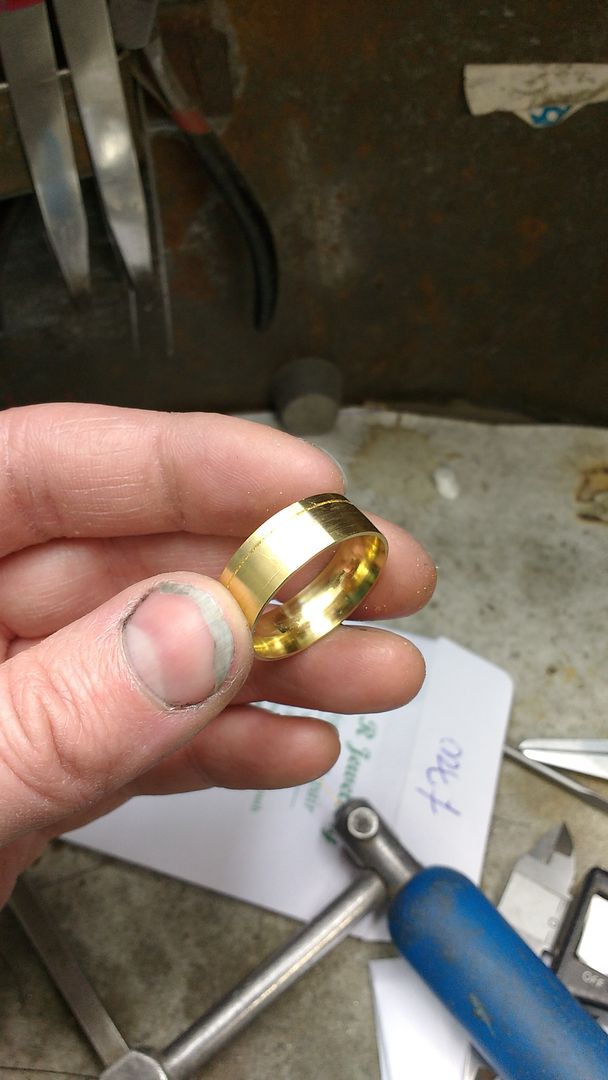
You can see here I've scored it 1.5mm from each edge so that I can add a 5mm centre section later on.
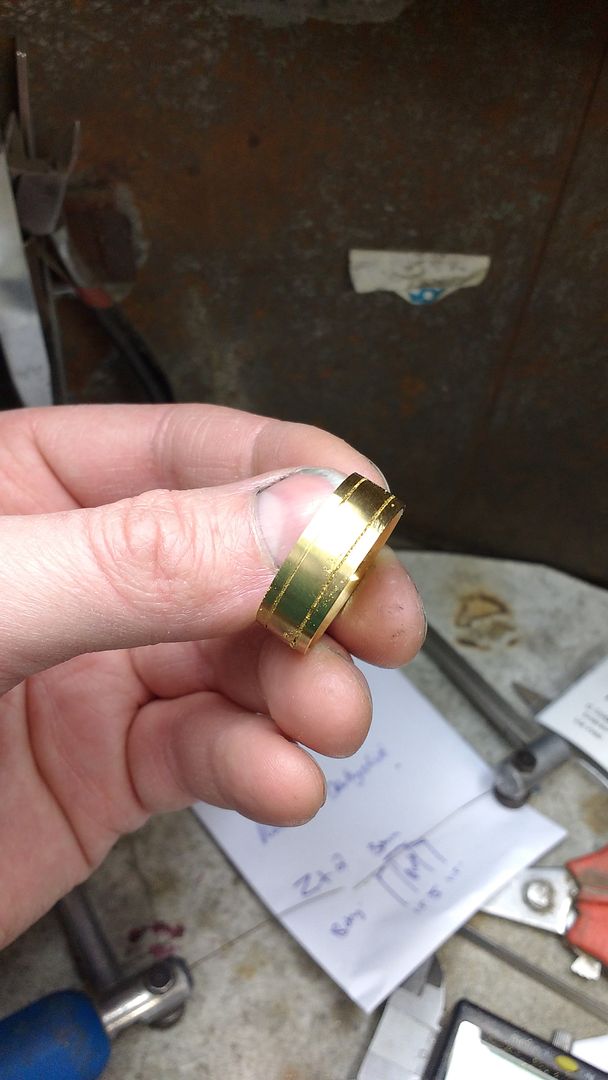
And then the filing and grinding begins!
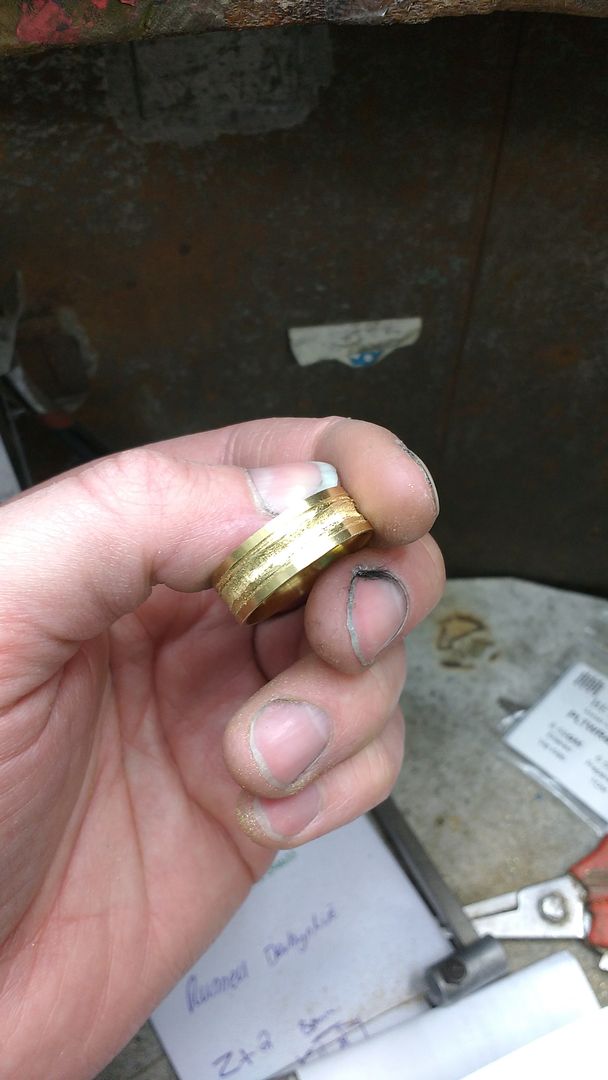
After much sweating and bruising of thumbs the centre is recessed enough to receive the centre section. You can see I've left a little bit of metal at the outer edges. This is to stop me from damaging the visible 1.5mm lip. I remove this safety net before the centre bit goes on.
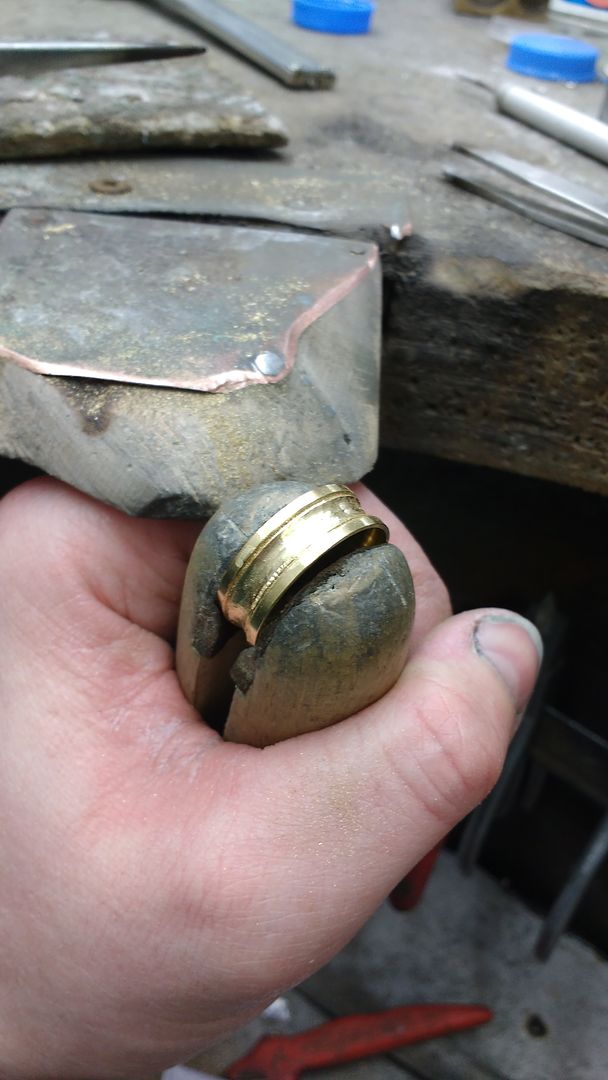
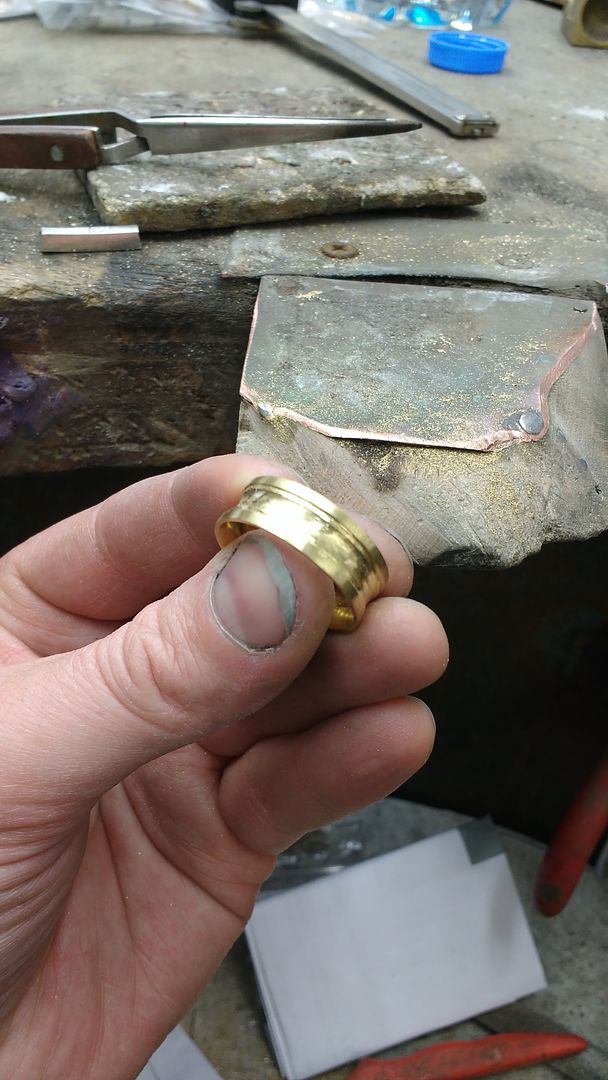
This is a 4mm square wire of platinum. I'll roll this to 5mm wide to make the outer band.
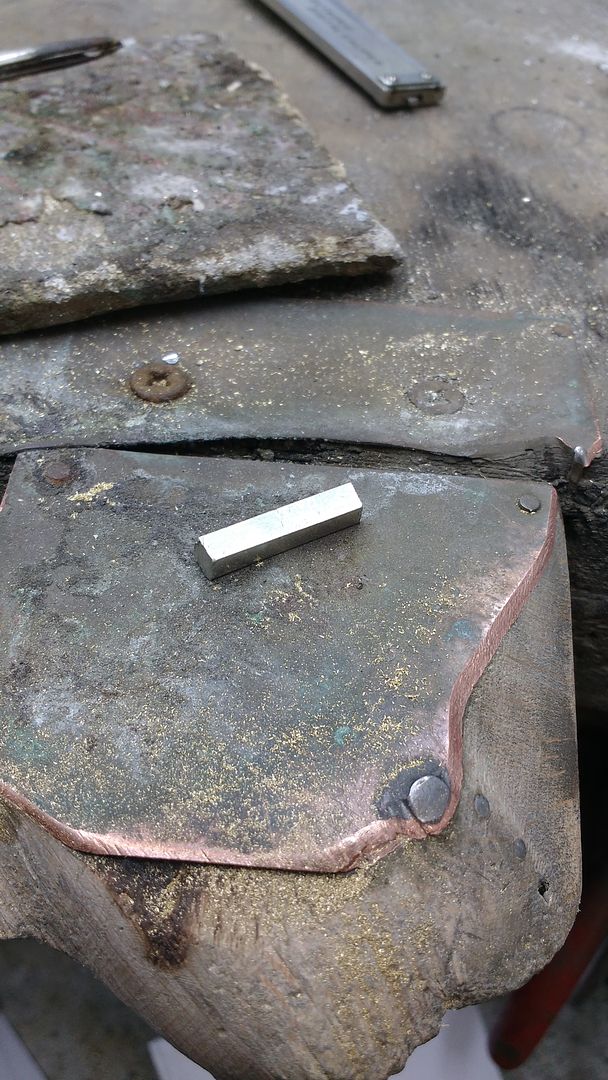
Like so.....
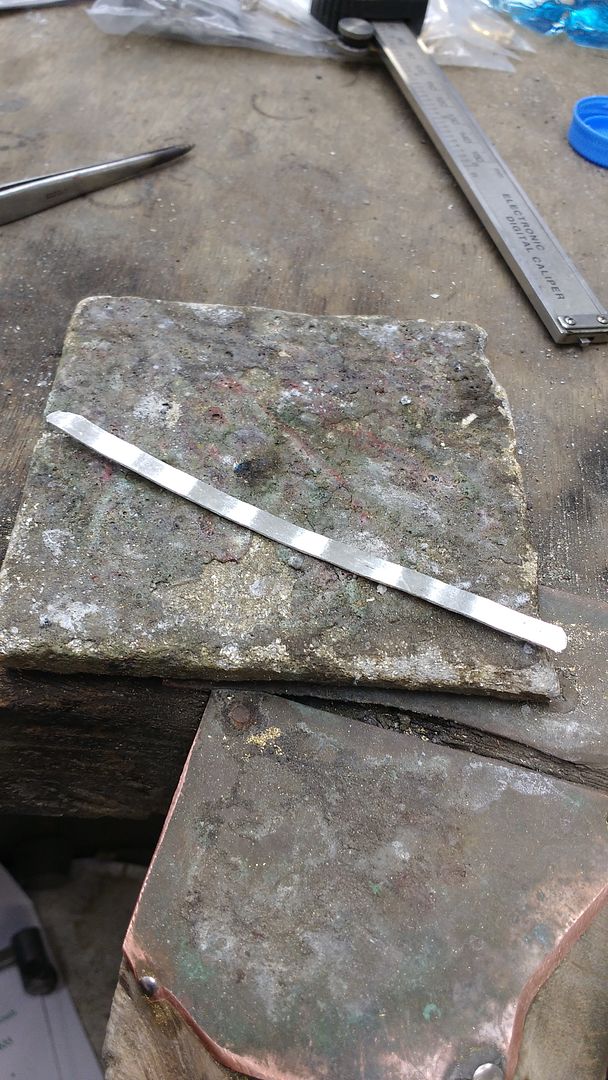
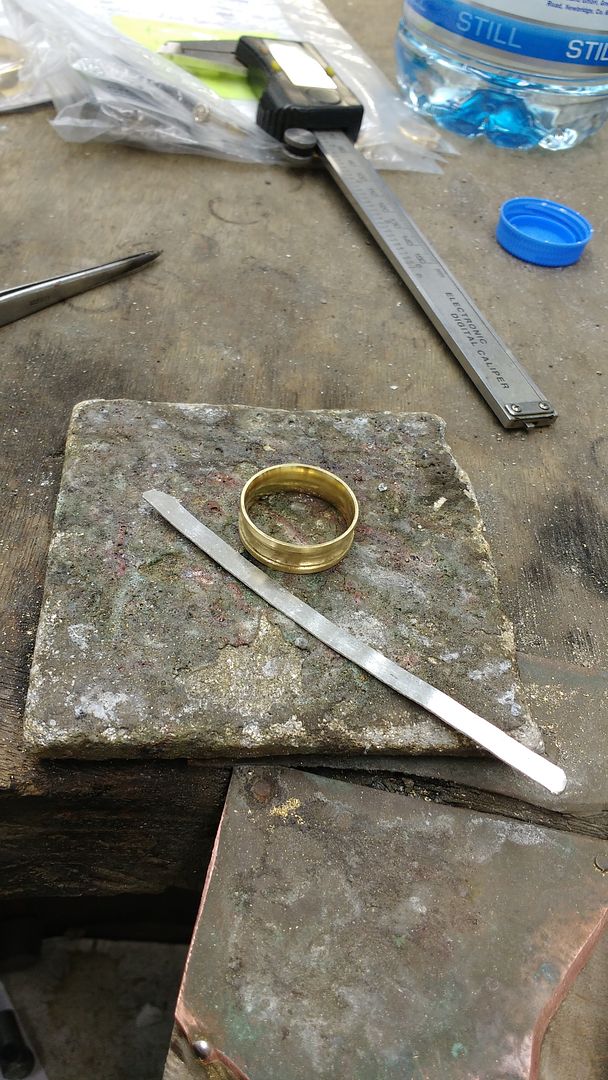
A rough band is made with the platinum. This only just fits over the gold band:
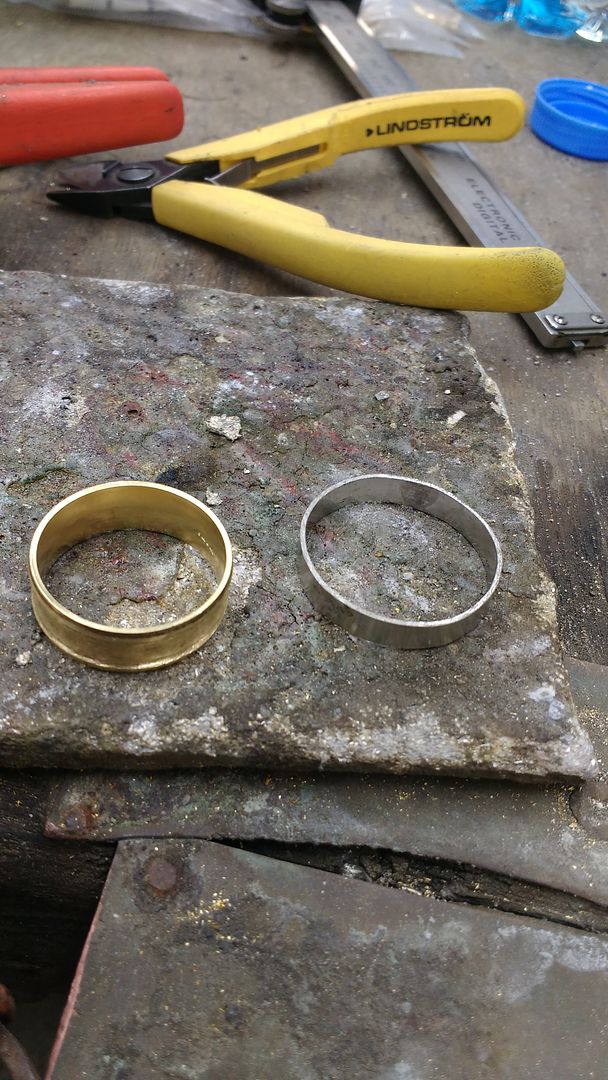
With the safety net removed the platinum band is pushed over the gold band and the gold band stretched up to Z+2. This pulls the platinum band tight over the gold band and should hold it secure. However, in this case the band being so large needed a bit of platinum easy solder to fill the gap underneath and hold the platinum band in place. I run this between the bands by drilling a port hole in the platinum band and running the solder inside. Not an easy or ideal job but one that sometimes needs doing. The result is the same at the end of the day. Here is the band in place:
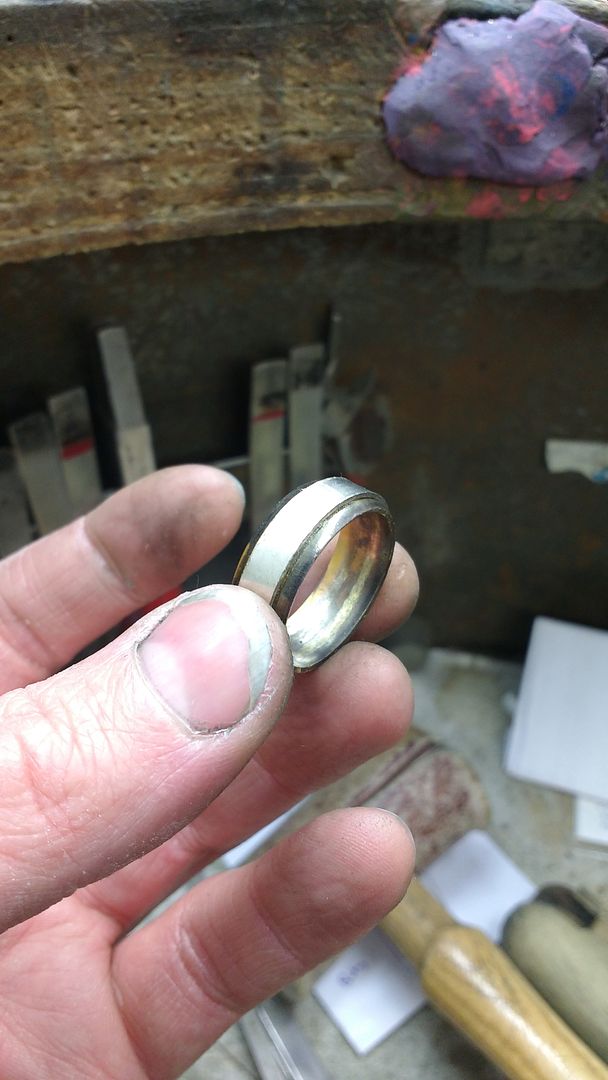
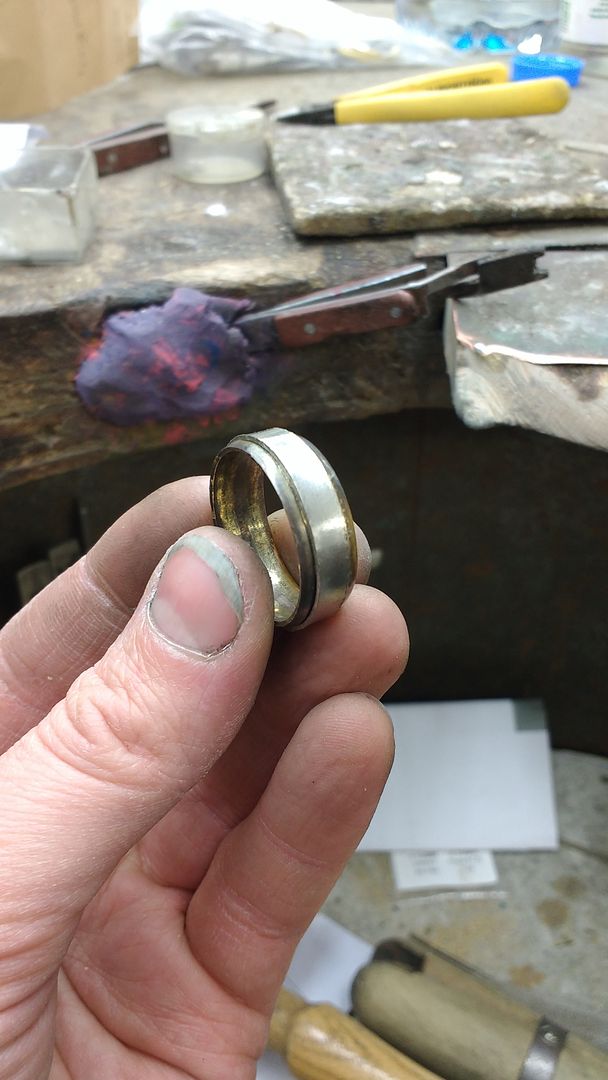
Then one of my oldest and most interesting customers turned up. In a RR Ghost that used to belong to the Sultan of Brunei. He's a nice guy and by all accounts drives this thing every week.
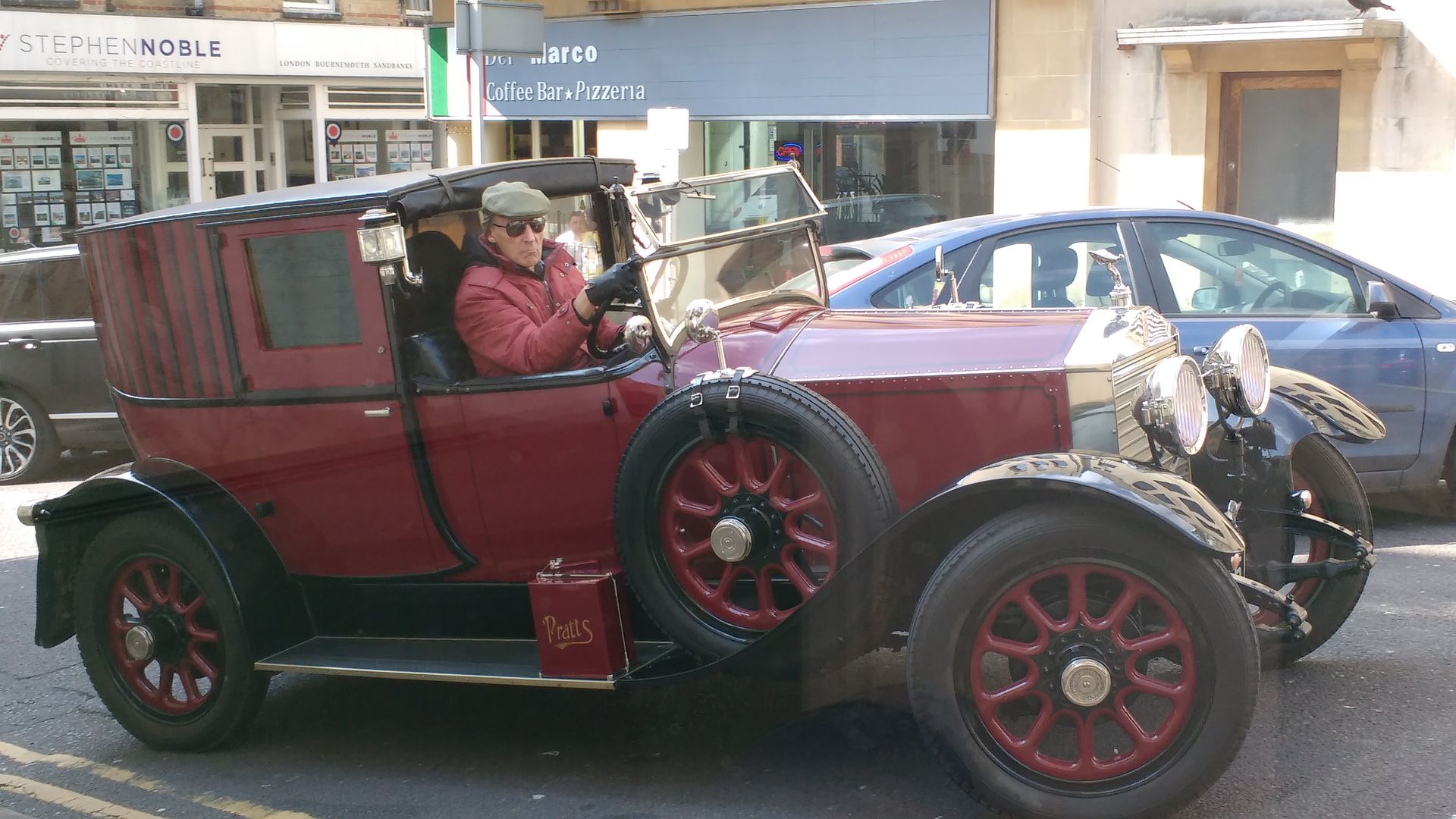
The ring is then filed to the correct profile and polished ready for plating. With the trusty nail polish applied the ring goes in the rhodium and comes out looking great:
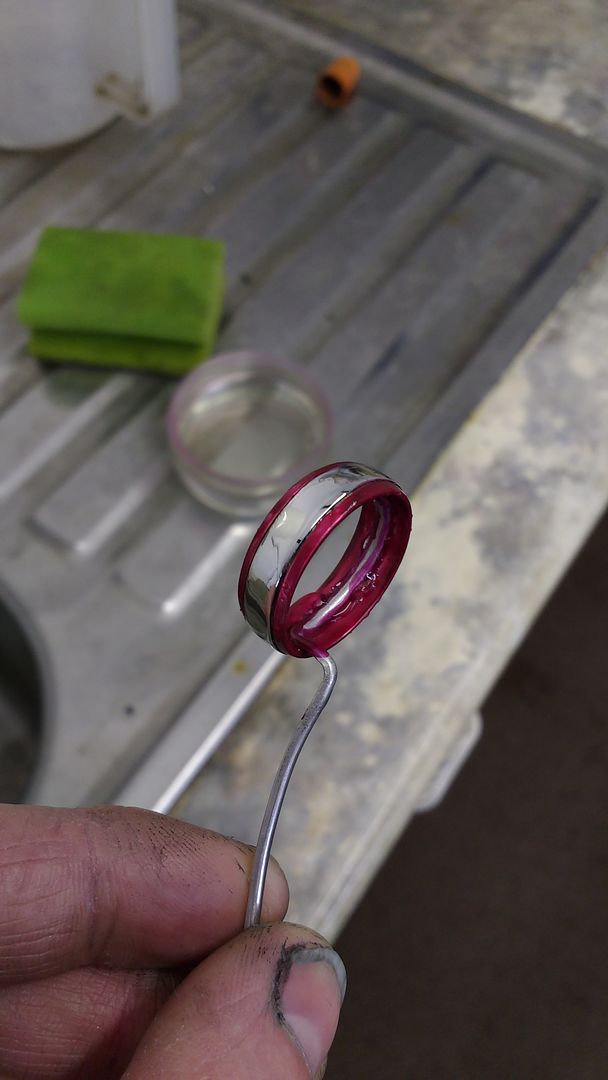
And all done:
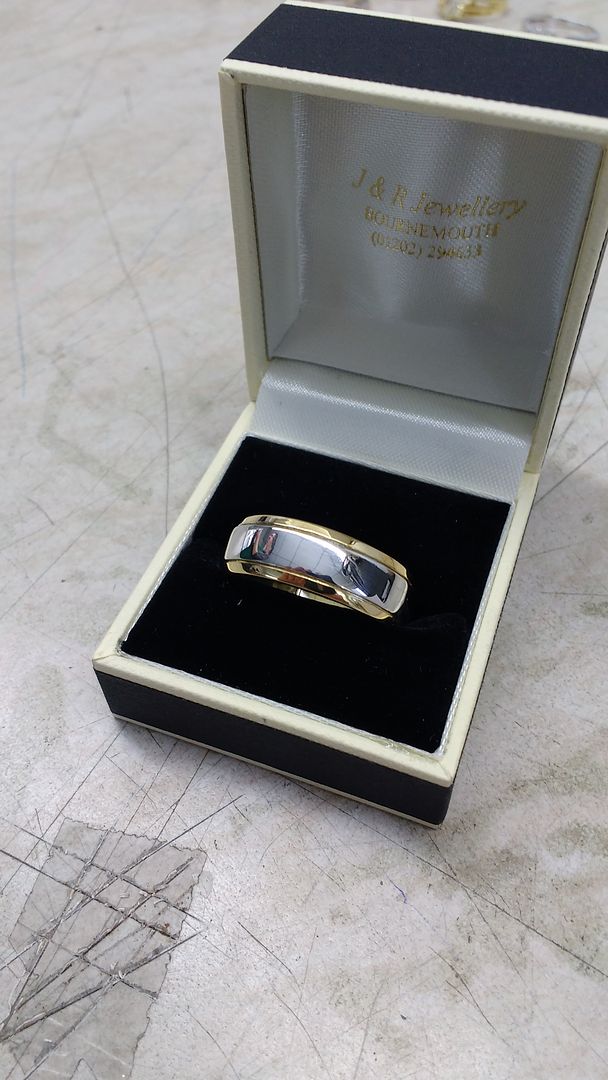
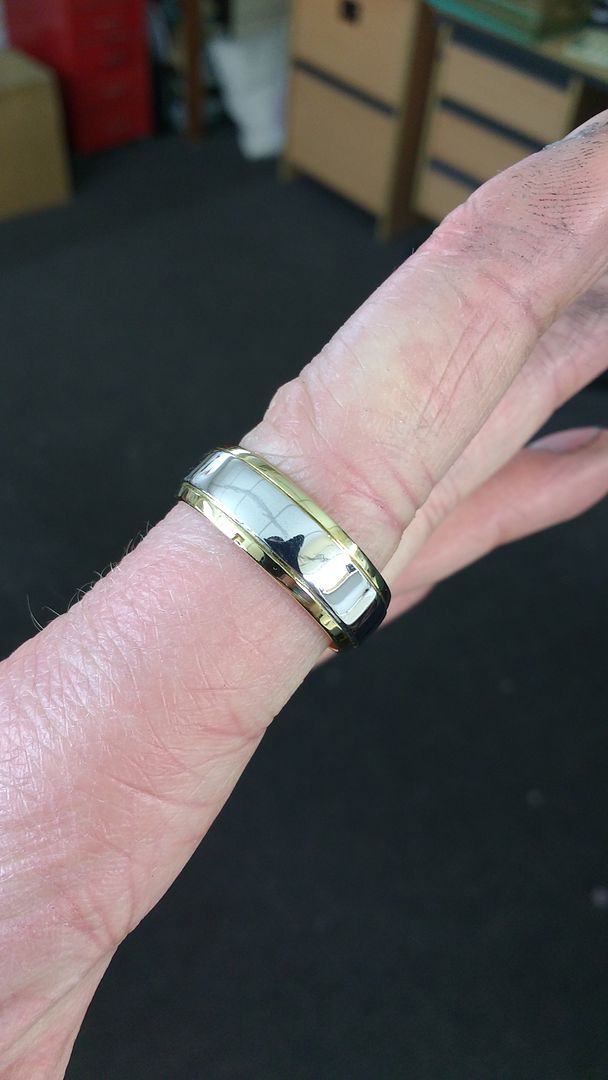
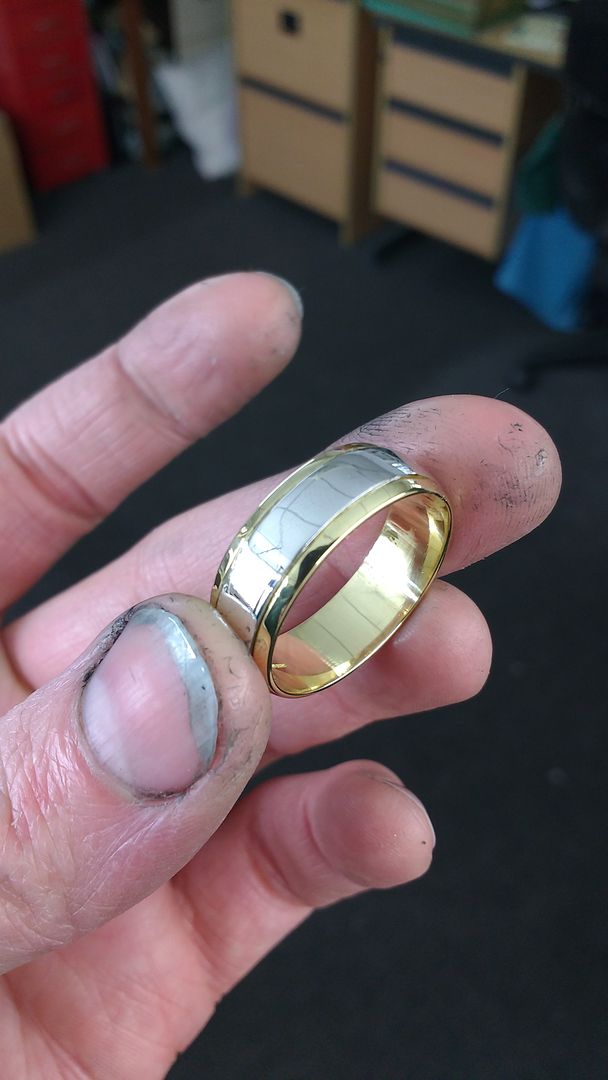
Eddie
Starting with some 18ct yellow gold I made an 8mm wide band, about size X. The customer has big hands so he needs a big old ring!
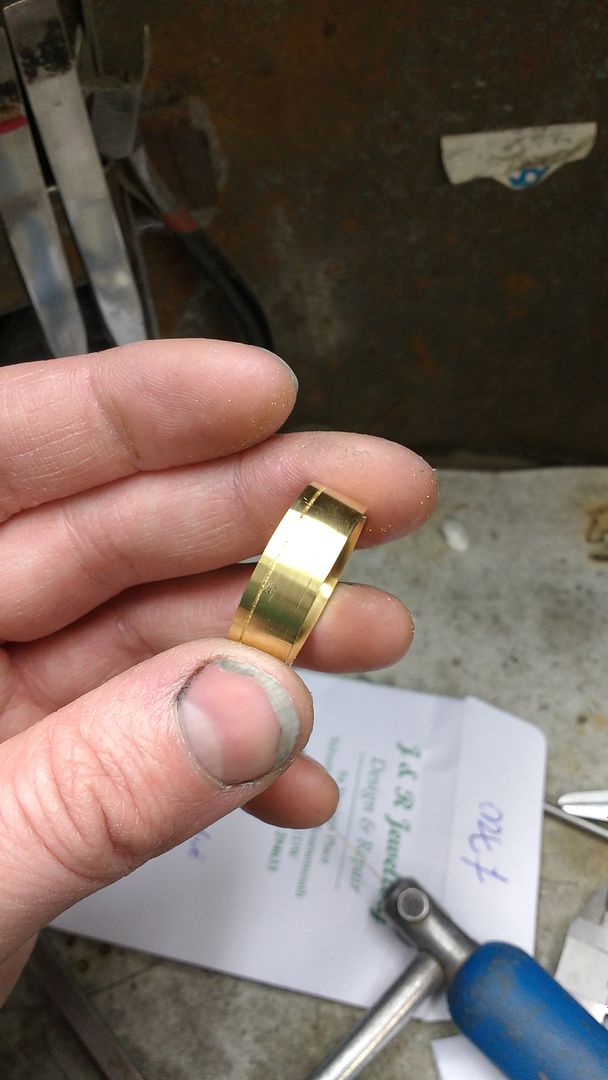
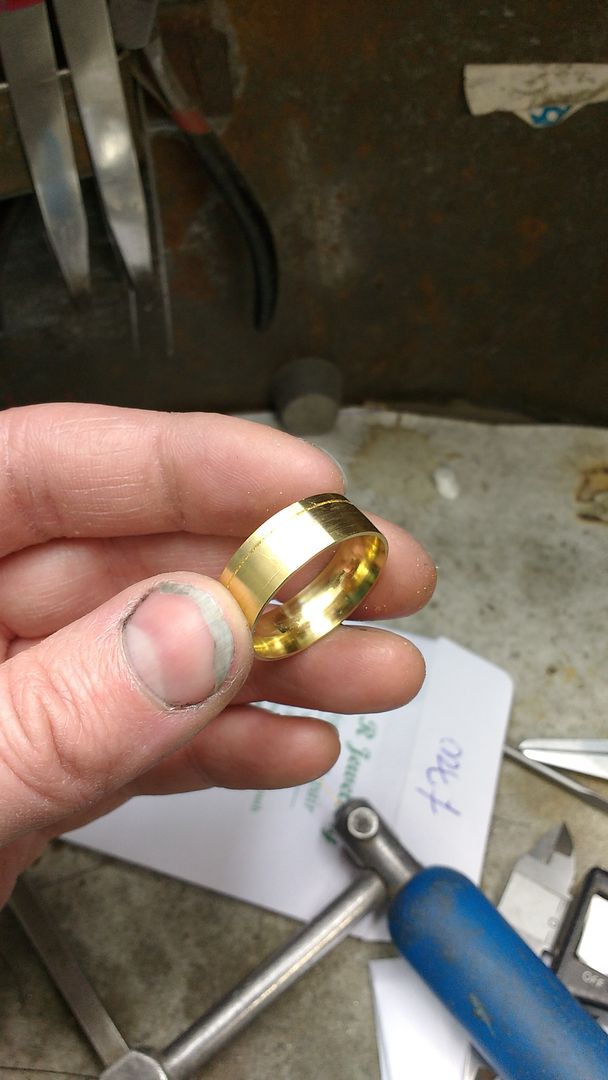
You can see here I've scored it 1.5mm from each edge so that I can add a 5mm centre section later on.
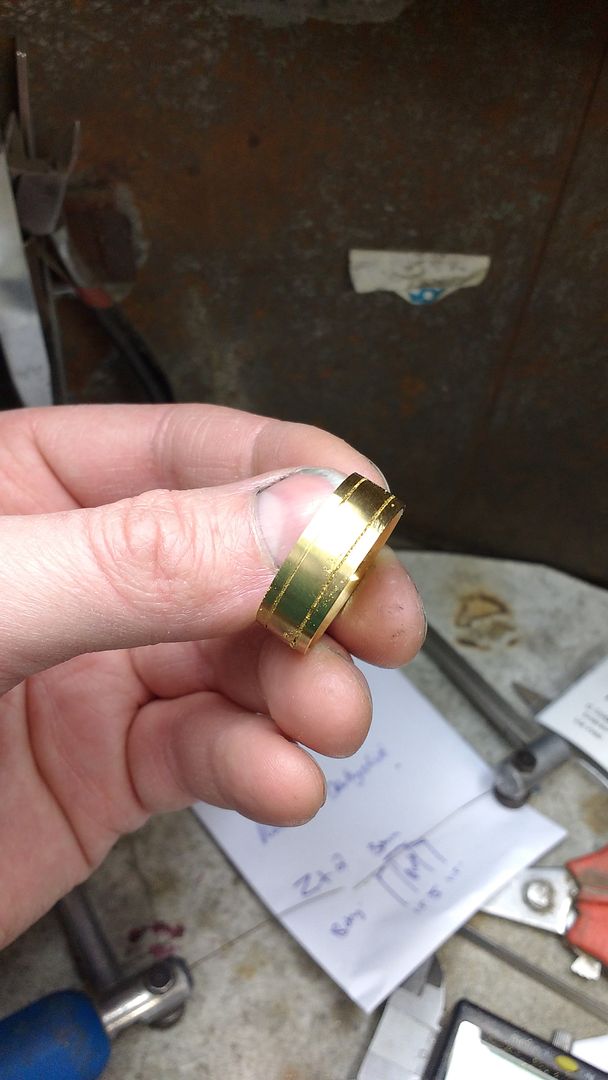
And then the filing and grinding begins!
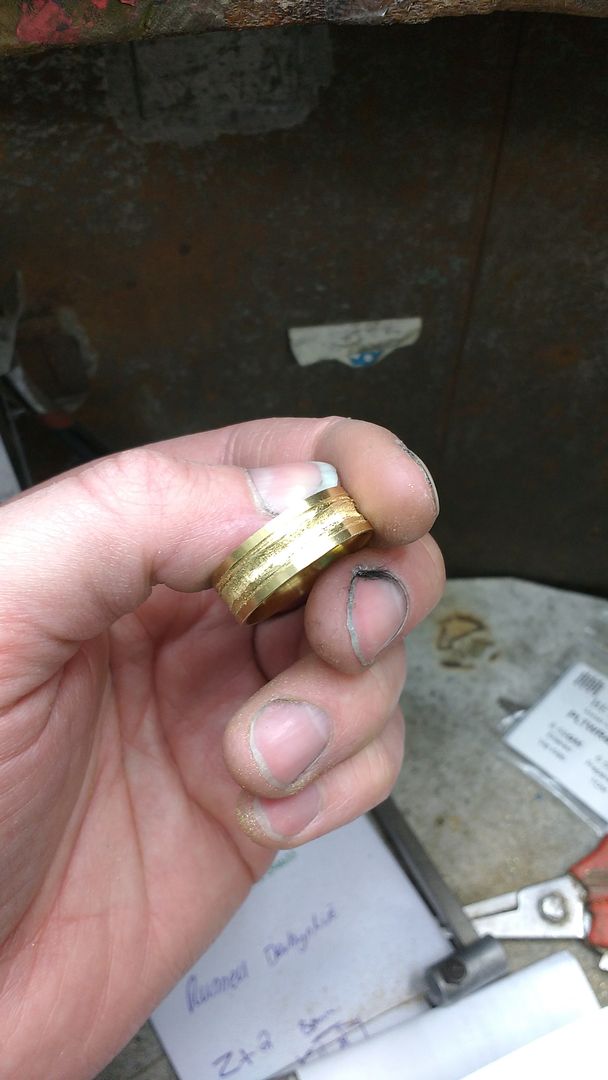
After much sweating and bruising of thumbs the centre is recessed enough to receive the centre section. You can see I've left a little bit of metal at the outer edges. This is to stop me from damaging the visible 1.5mm lip. I remove this safety net before the centre bit goes on.
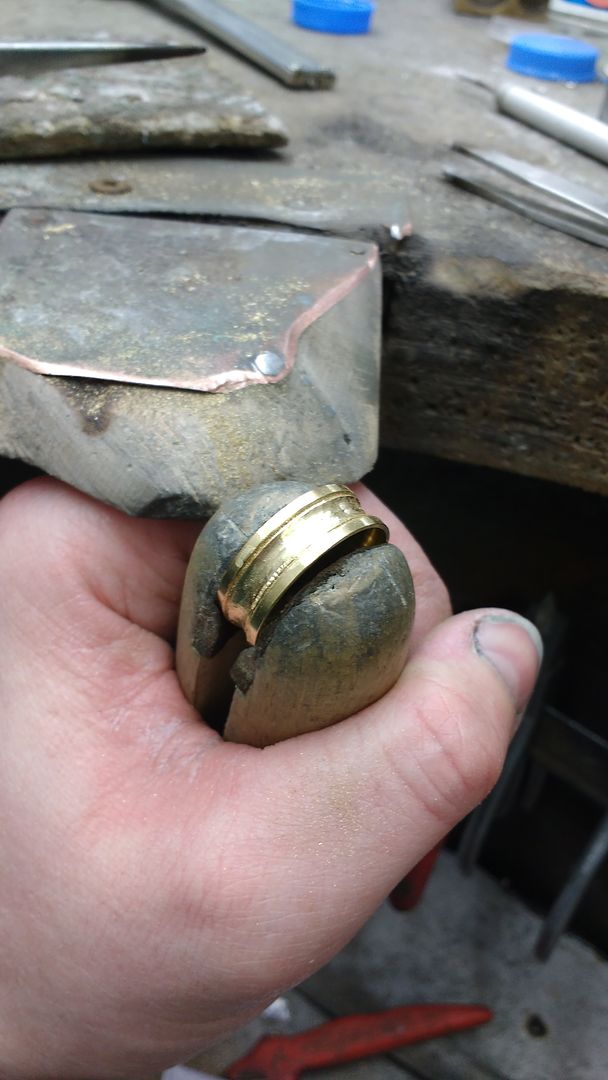
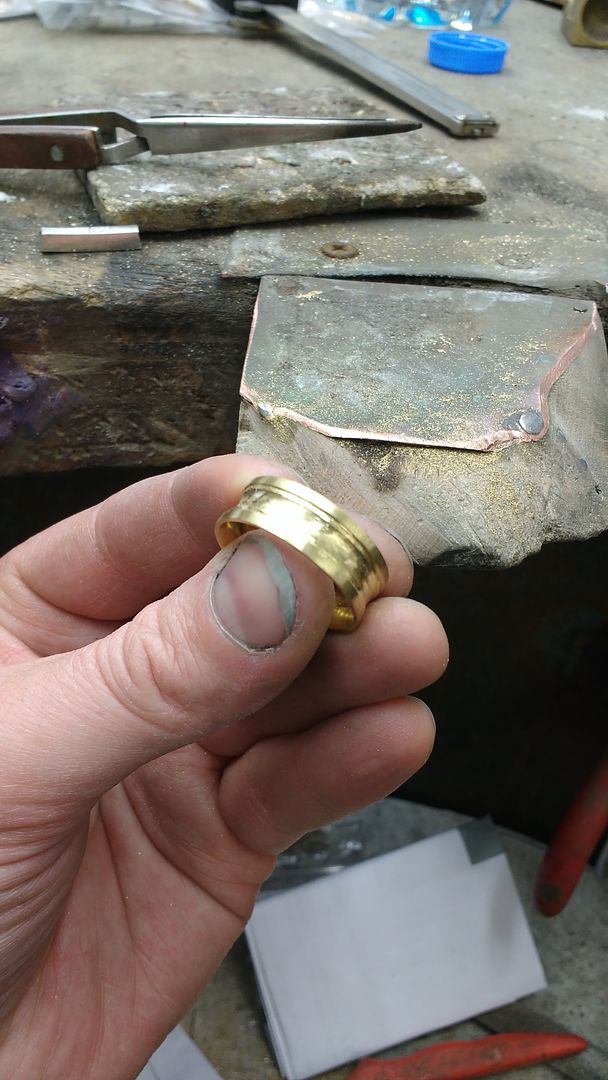
This is a 4mm square wire of platinum. I'll roll this to 5mm wide to make the outer band.
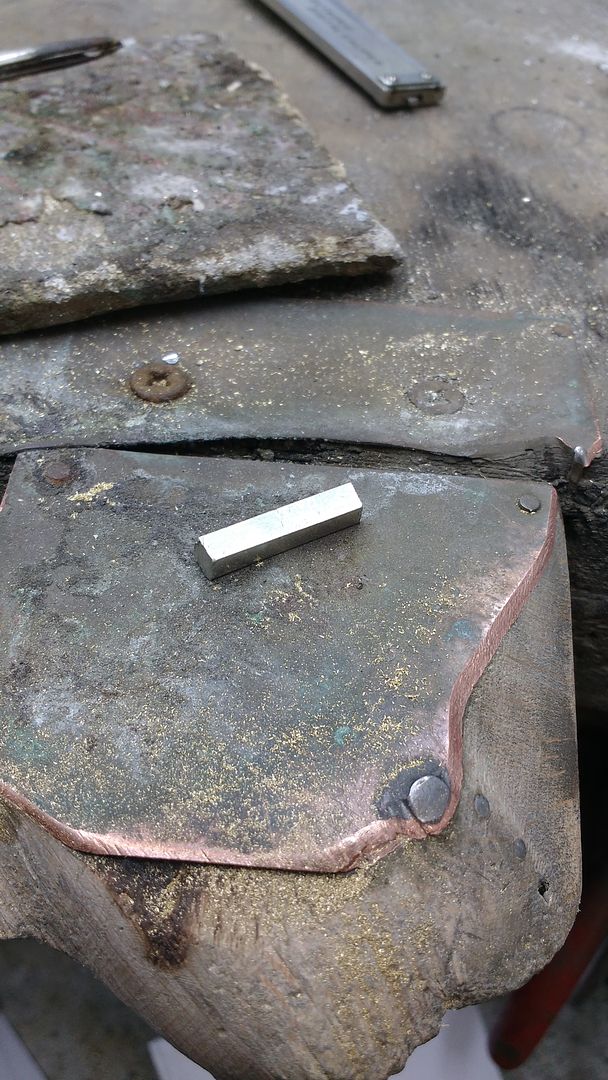
Like so.....
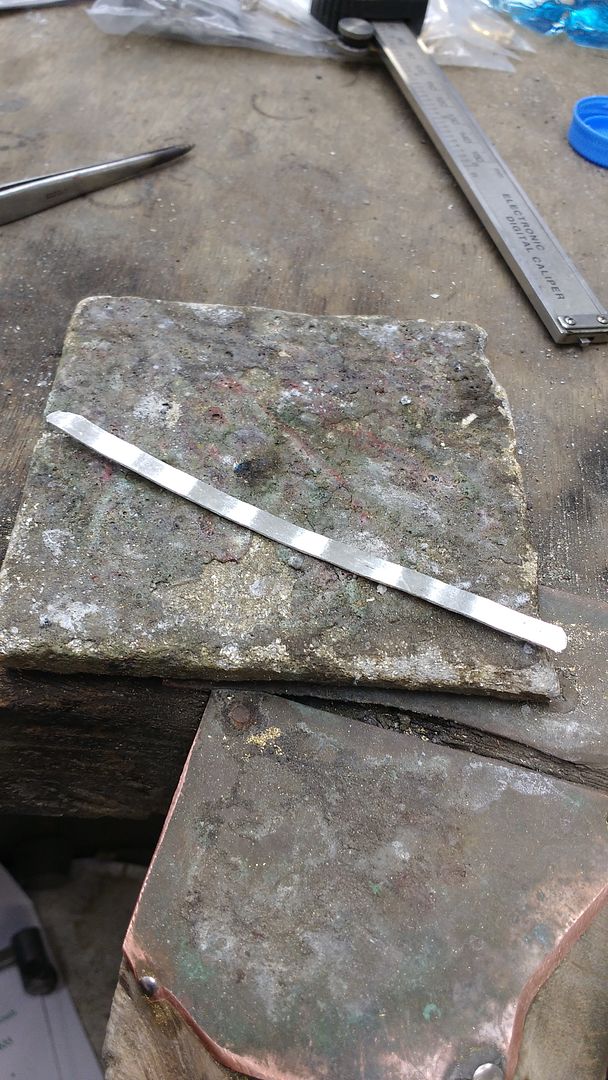
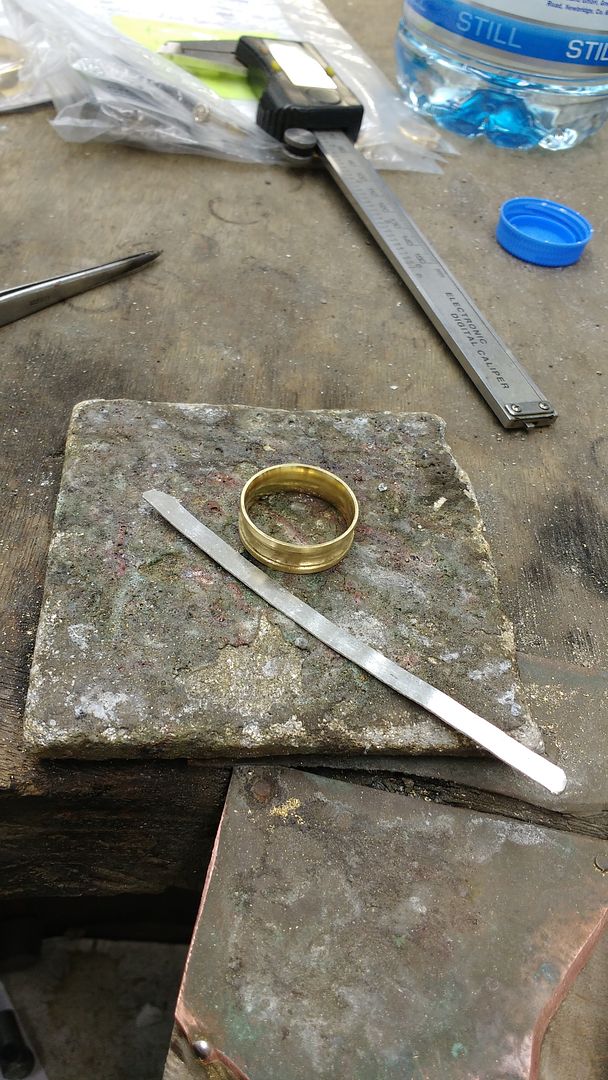
A rough band is made with the platinum. This only just fits over the gold band:
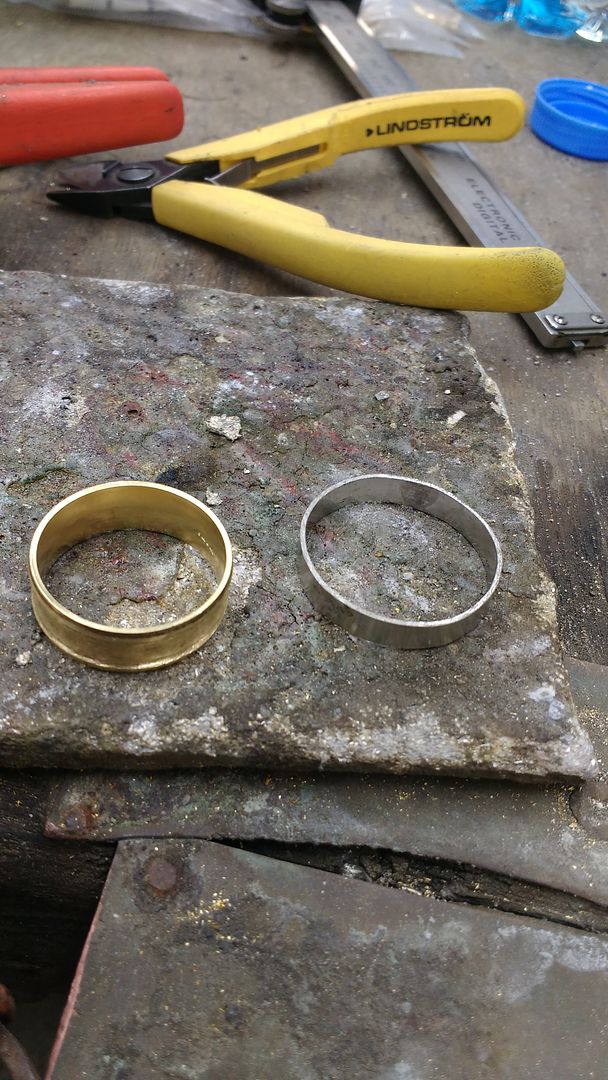
With the safety net removed the platinum band is pushed over the gold band and the gold band stretched up to Z+2. This pulls the platinum band tight over the gold band and should hold it secure. However, in this case the band being so large needed a bit of platinum easy solder to fill the gap underneath and hold the platinum band in place. I run this between the bands by drilling a port hole in the platinum band and running the solder inside. Not an easy or ideal job but one that sometimes needs doing. The result is the same at the end of the day. Here is the band in place:
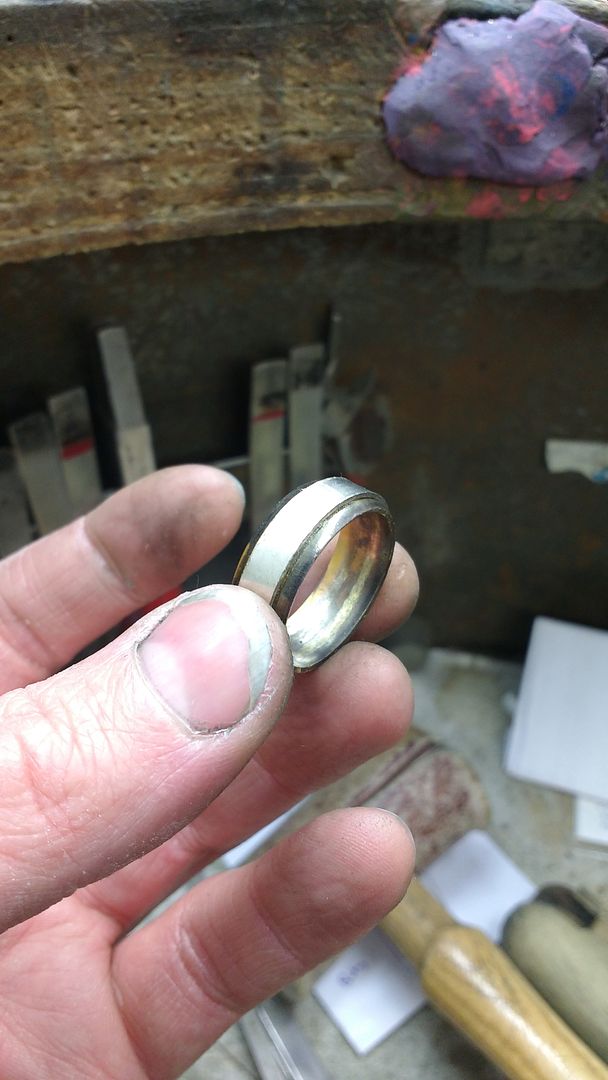
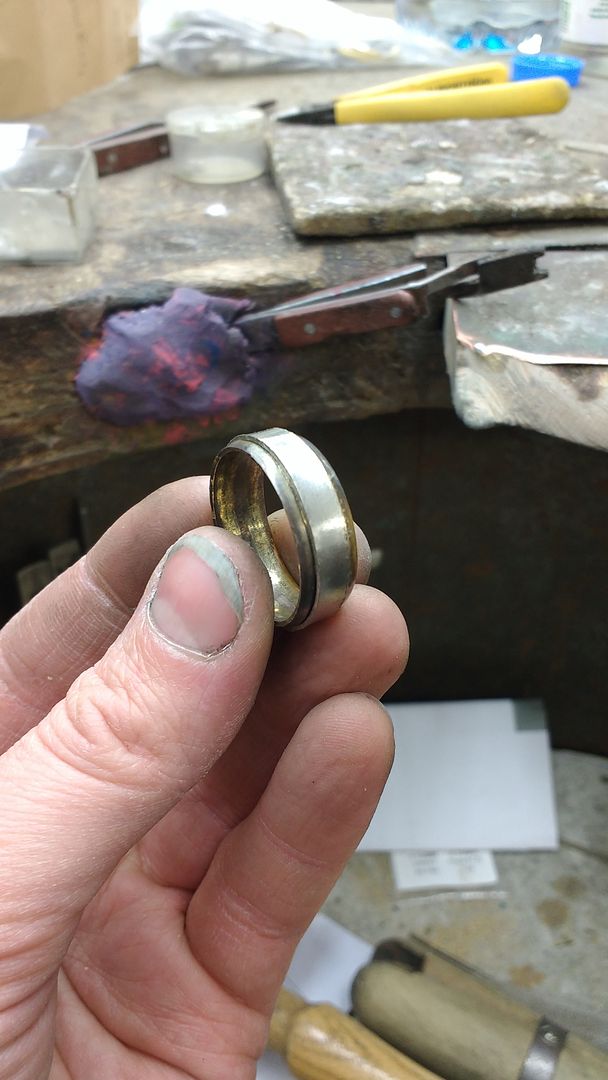
Then one of my oldest and most interesting customers turned up. In a RR Ghost that used to belong to the Sultan of Brunei. He's a nice guy and by all accounts drives this thing every week.
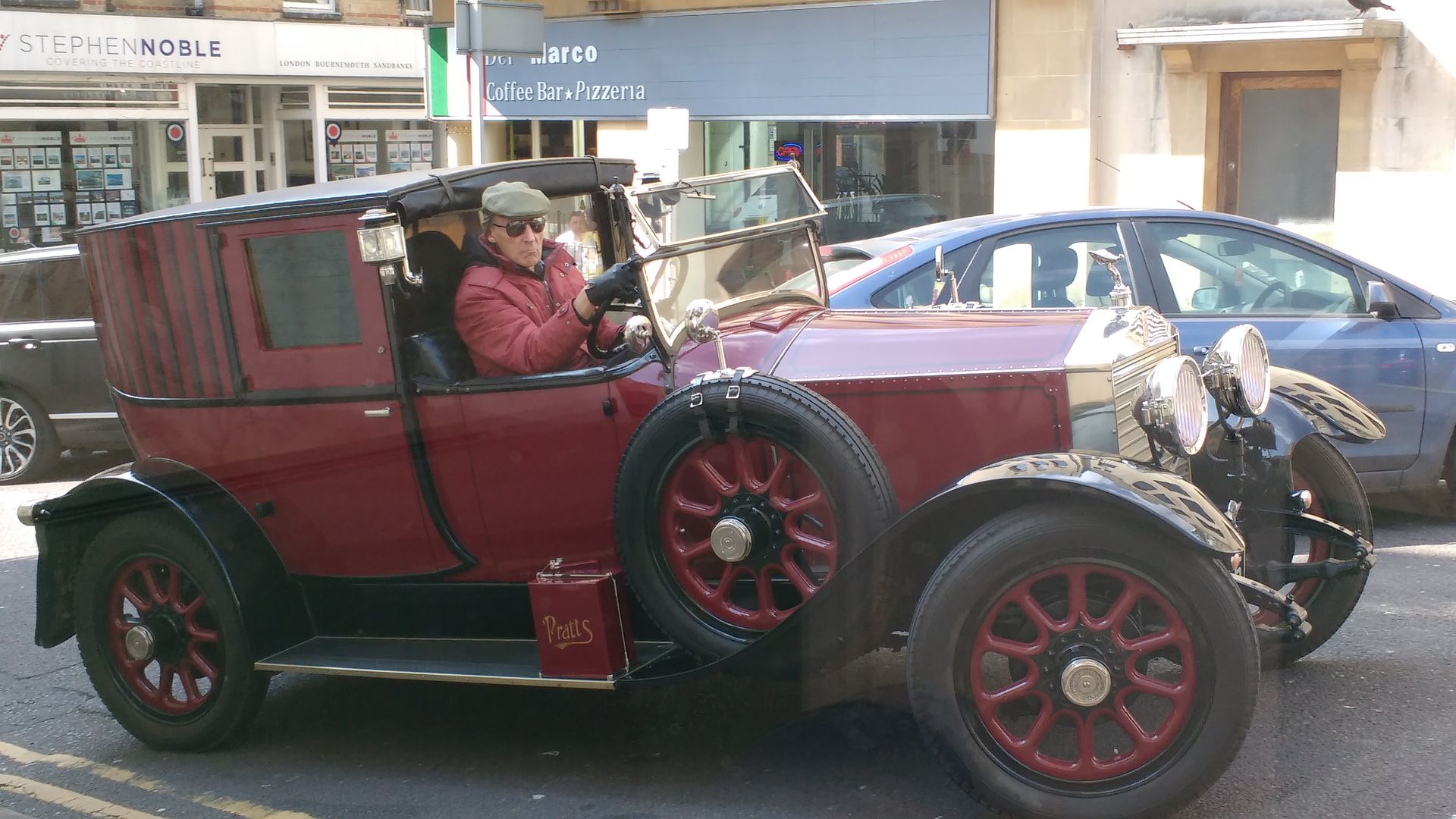
The ring is then filed to the correct profile and polished ready for plating. With the trusty nail polish applied the ring goes in the rhodium and comes out looking great:
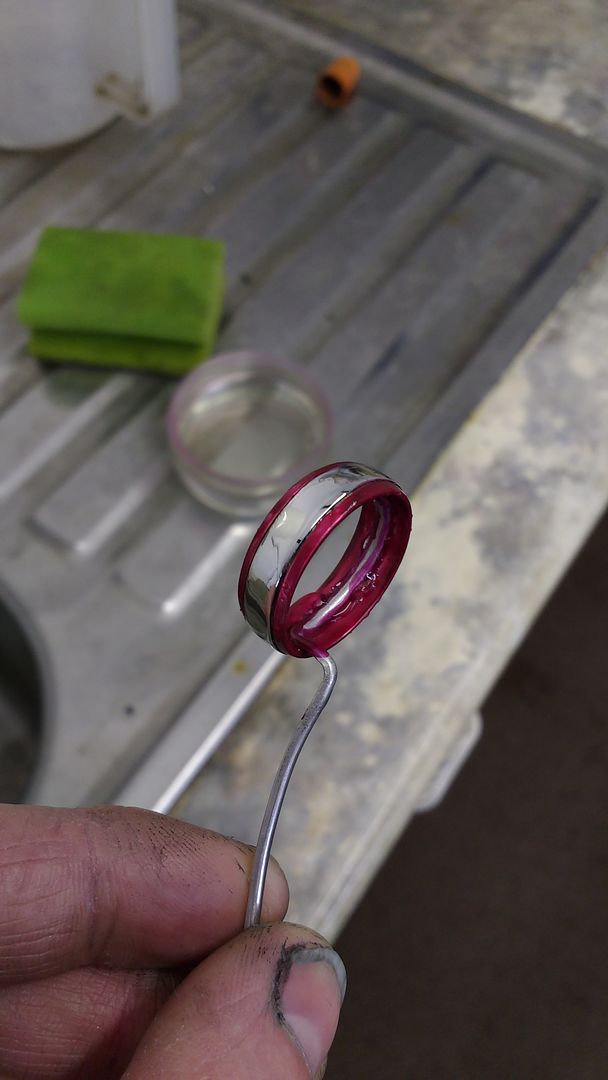
And all done:
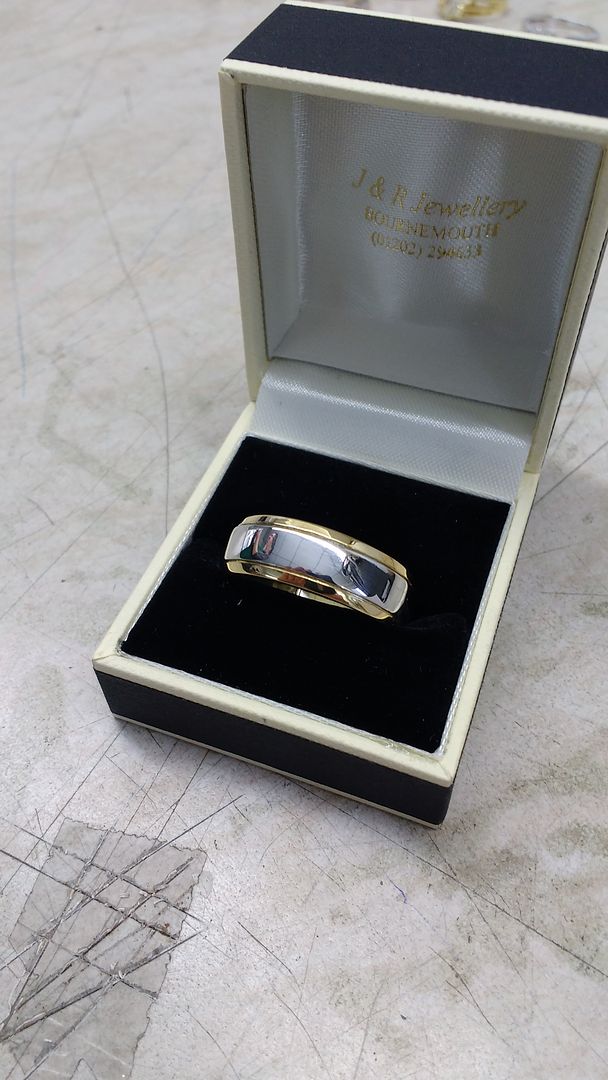
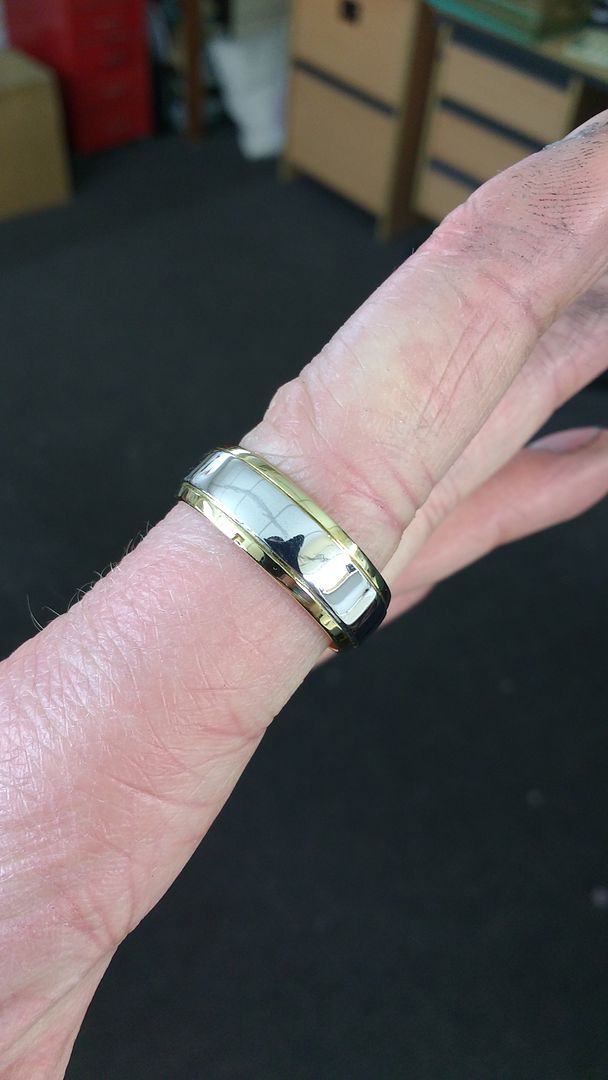
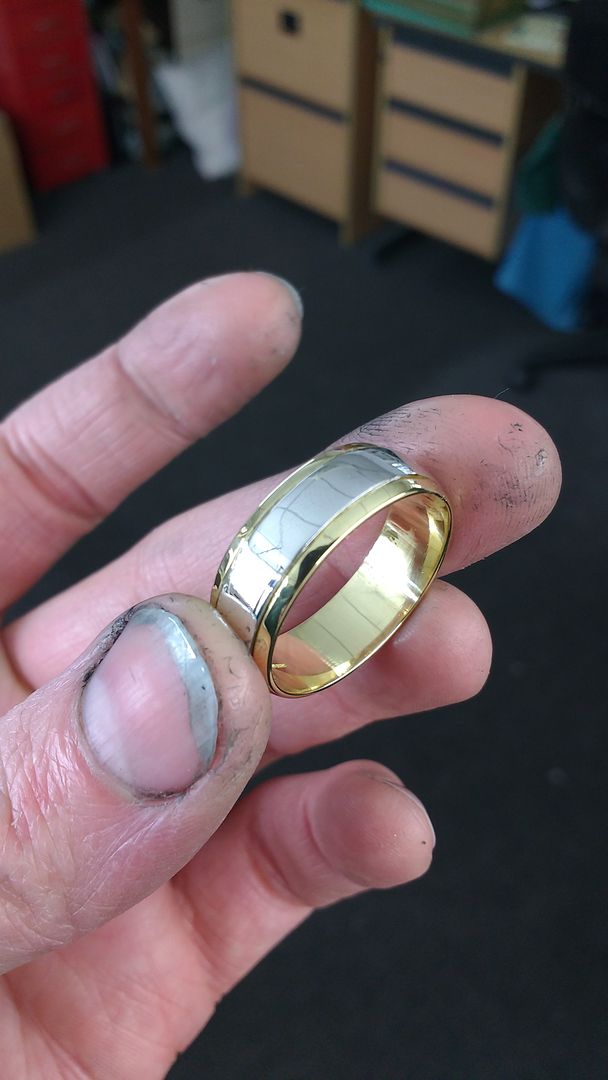
Eddie
Dr G said:
Fascinating - I did wonder how it went together! Was mine a fairly similar process?
If memory serves me correctly, yes it would have been fairly similar. The few thousand jobs between this and yours may have cluttered my memory but the techniques generally don't vary too much. It's only if there are unusual materials, sizes or circumstances that things may differ in the build process. Yesterday I had a guy needing a Z+7 size wedding ring. I don't have ring sticks that big so I'm having to do it all by digital gauge. Everyday a new challenge! Yeah, as above really. Handmade items are where most of my customers focus their attention. Wedding rings and engagement rings are special in their very nature and many people (people who think past the high street) like the idea of putting a little extra thought into what they give their other half. A lathe would definitely make my job easier but the finish would be so perfect that the item may as well be from a catalogue.
Another reason is for me to justify prices. Take this next picture as an example.
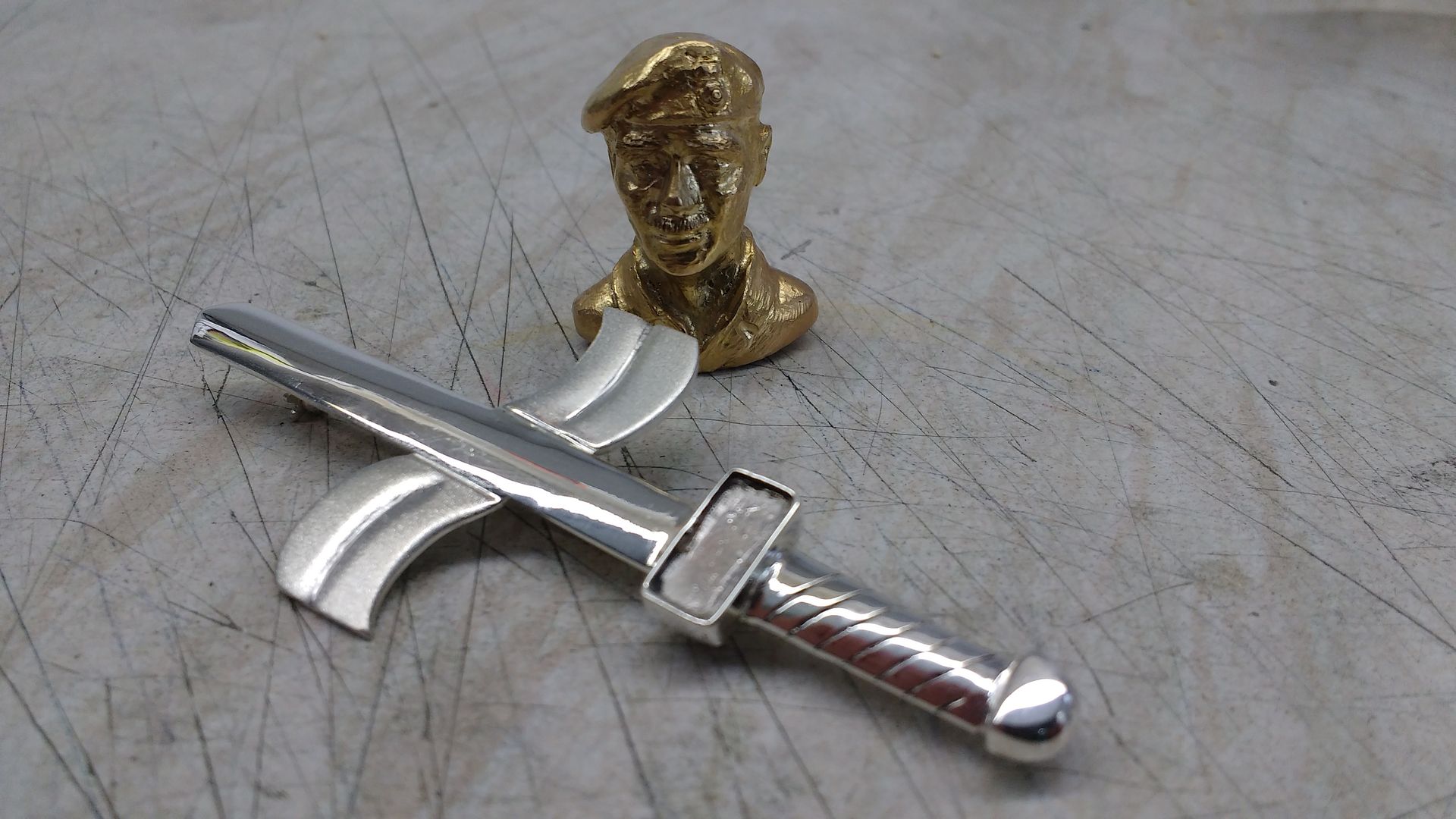
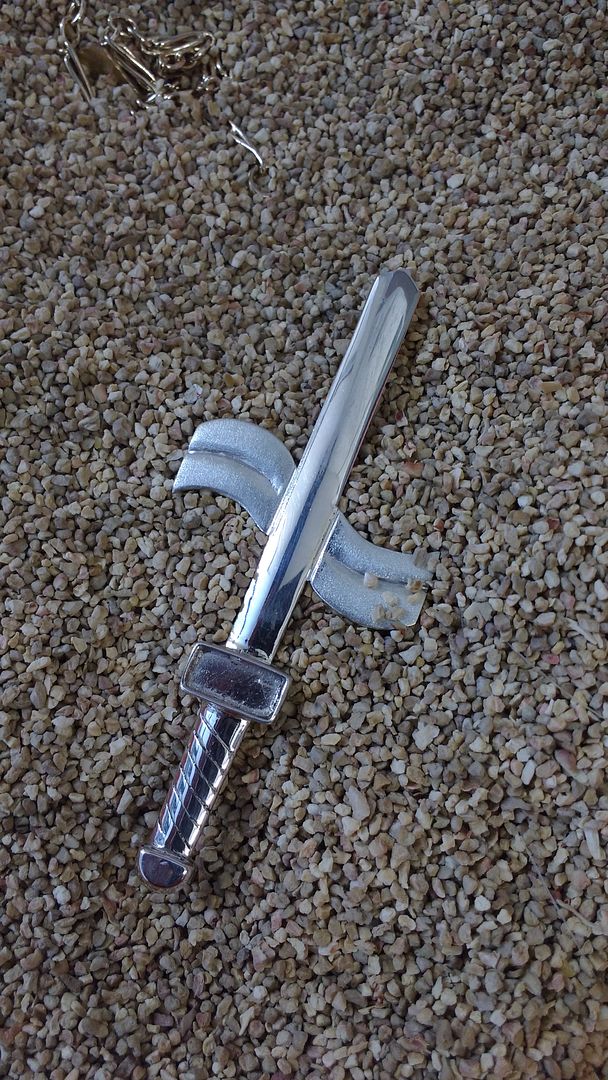
The customer could have gone on eBay or to the PRI shop on camp where he could have bought one for very little money. As it's his wedding kilt pin he wants it to have some sentimental value post event. Queue my input. For the extra cash the customer will have something made specially for him, and in this case by somebody who was also in the marines. I guarantee he'll keep it and use it rather than filing it under 'wedding crap' once the honeymoon is over. Lathes and mills can't make that feeling of being 'handmade'.
Of course, some customers are driven by cost savings and I do have options to cater for them. I just don't show the boring commercial equipment here. Ha!
Happy Easter,
Eddie
Another reason is for me to justify prices. Take this next picture as an example.
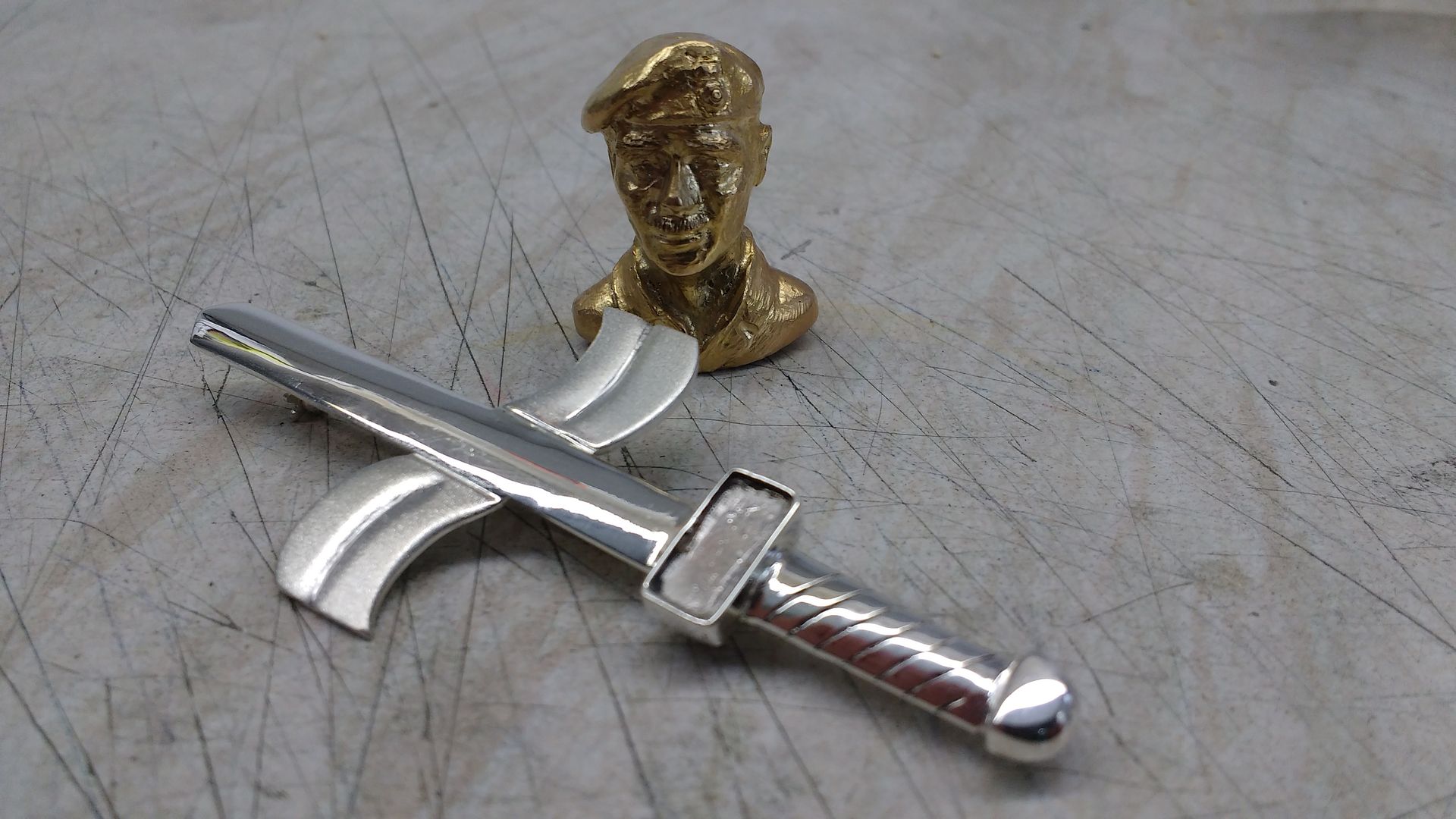
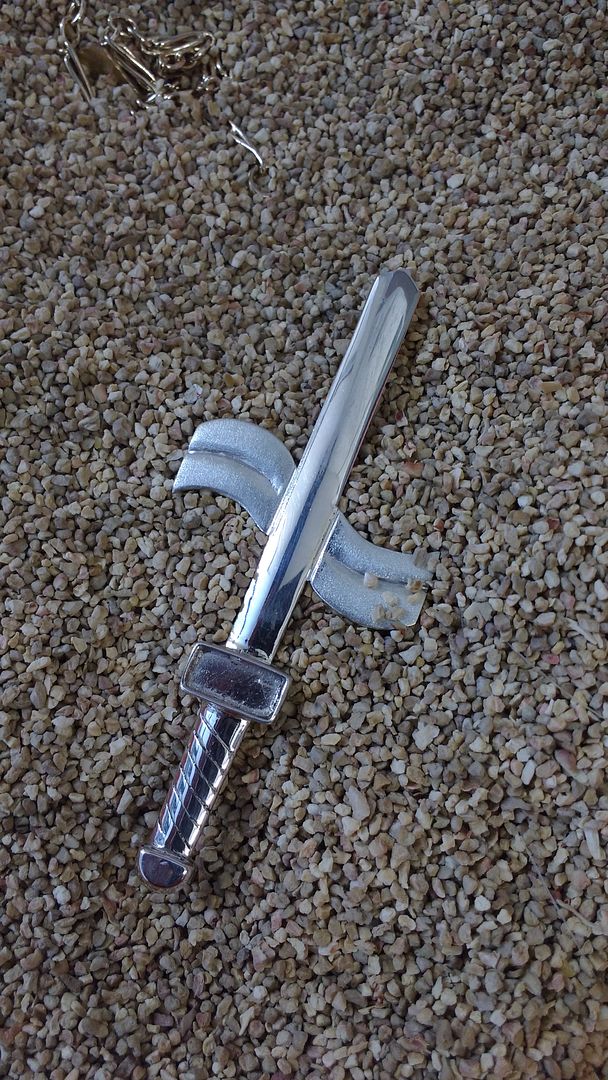
The customer could have gone on eBay or to the PRI shop on camp where he could have bought one for very little money. As it's his wedding kilt pin he wants it to have some sentimental value post event. Queue my input. For the extra cash the customer will have something made specially for him, and in this case by somebody who was also in the marines. I guarantee he'll keep it and use it rather than filing it under 'wedding crap' once the honeymoon is over. Lathes and mills can't make that feeling of being 'handmade'.
Of course, some customers are driven by cost savings and I do have options to cater for them. I just don't show the boring commercial equipment here. Ha!
Happy Easter,
Eddie
Edited by ecain63 on Thursday 24th March 19:14
Another PH job today. Worn out puzzle ring that needs a new solid shank, 2 stones replaced and the settings rebuilt.
I didn't take too many pics of the shank being done as I wasn't planning on documenting the job, but here is the new shank fitted. The original was broken and very worn:
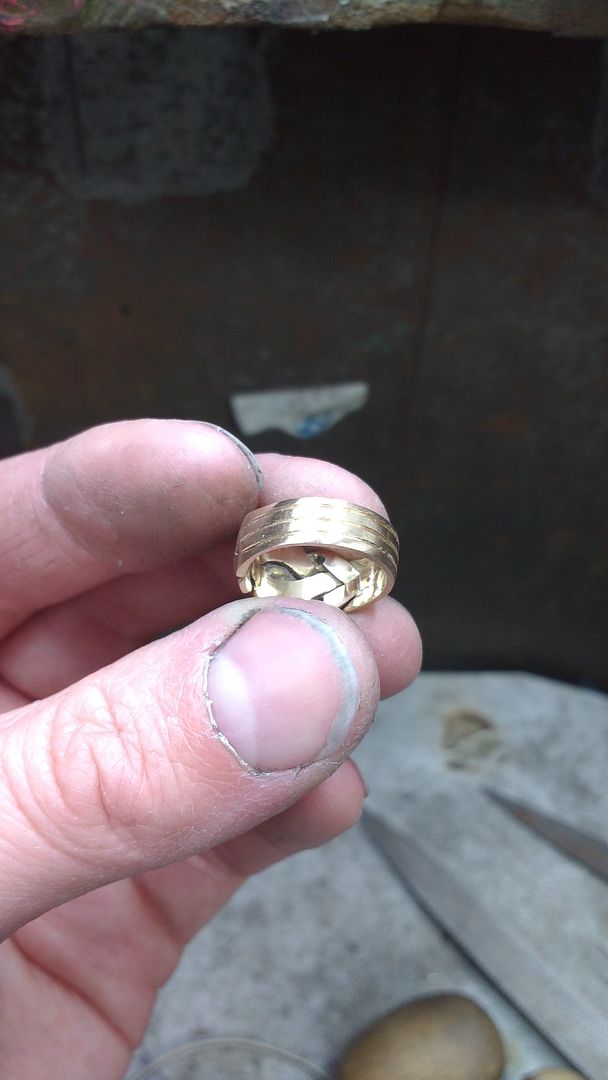
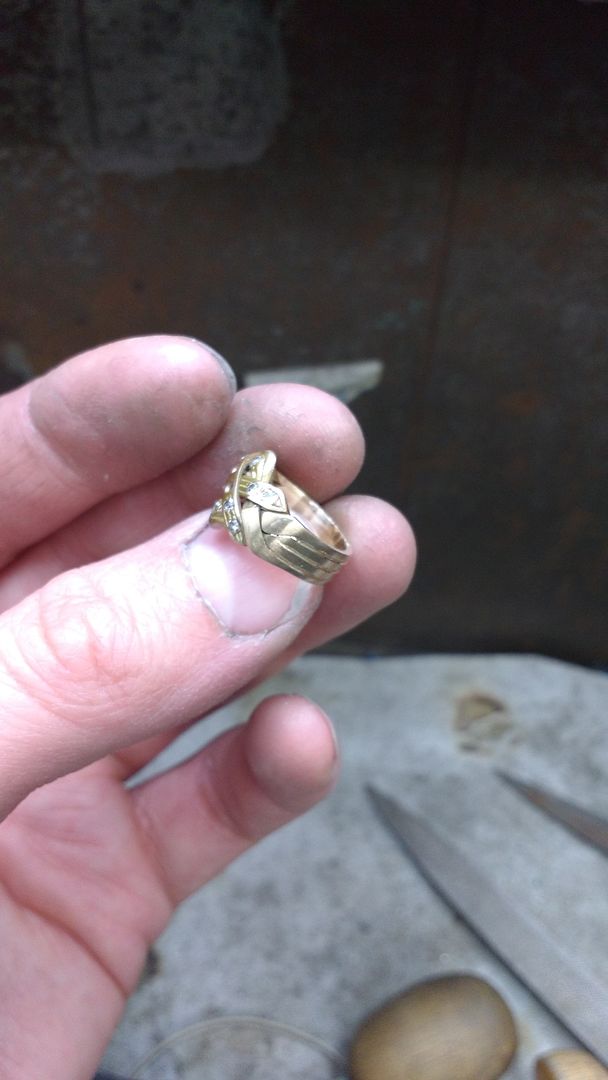
With the new shank in place the next job was to set the 2 missing stones and rebuild the claws that secure them. With the stones laid in place I solder 18ct yellow gold plates either side of each stone. I think 25 in all. I did the outer claws first, trimed them down and then did the centre ones:
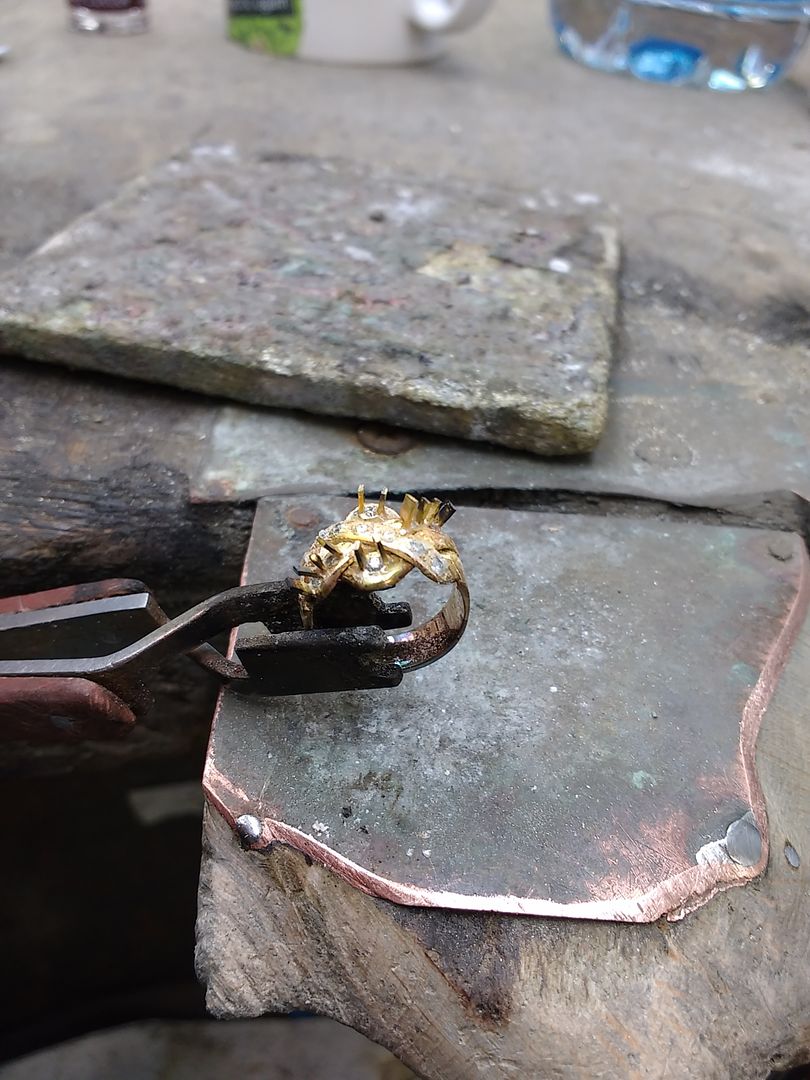
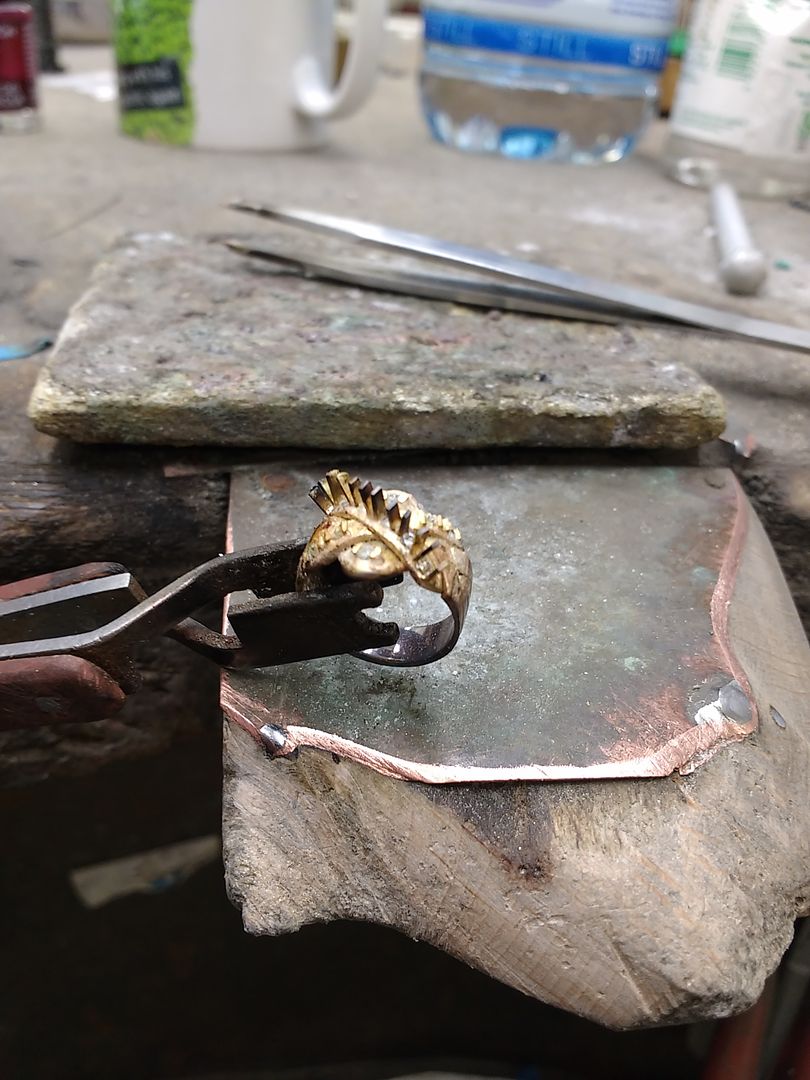
I then trimmed the centre claws down to a suitable level:
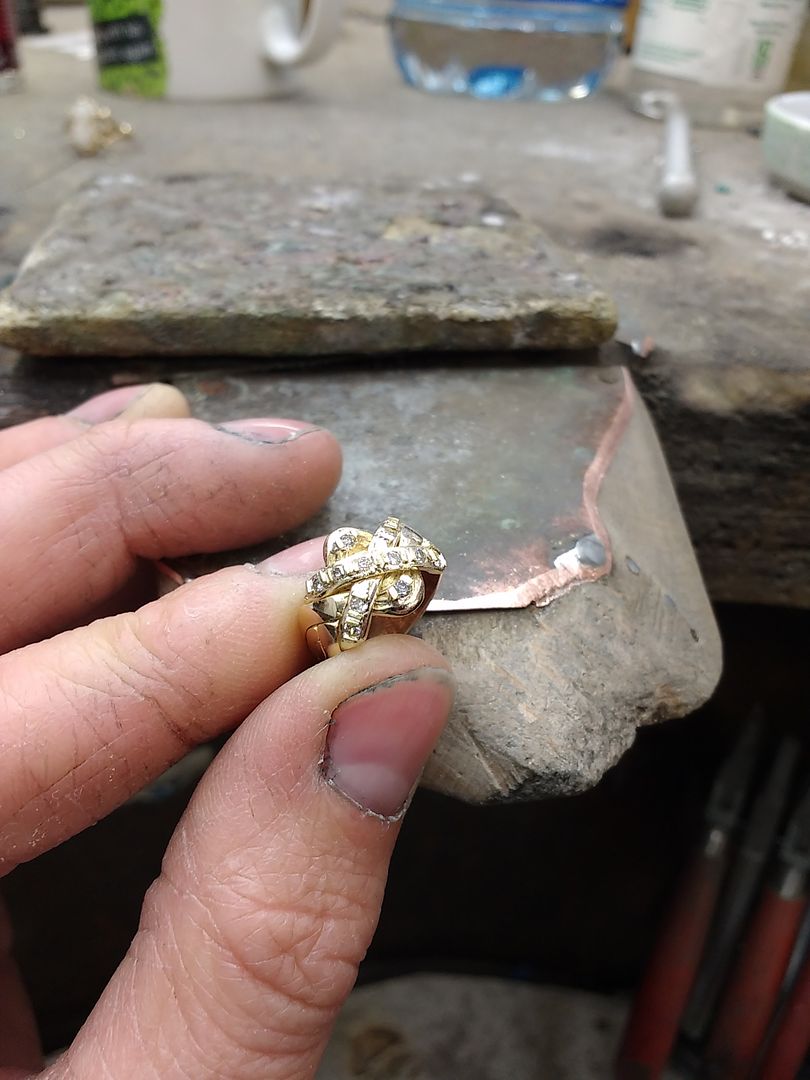
The bars are then split in the middle to create 50 individual claws. The ring is then clamped and the pegs pressed to secure the stones:
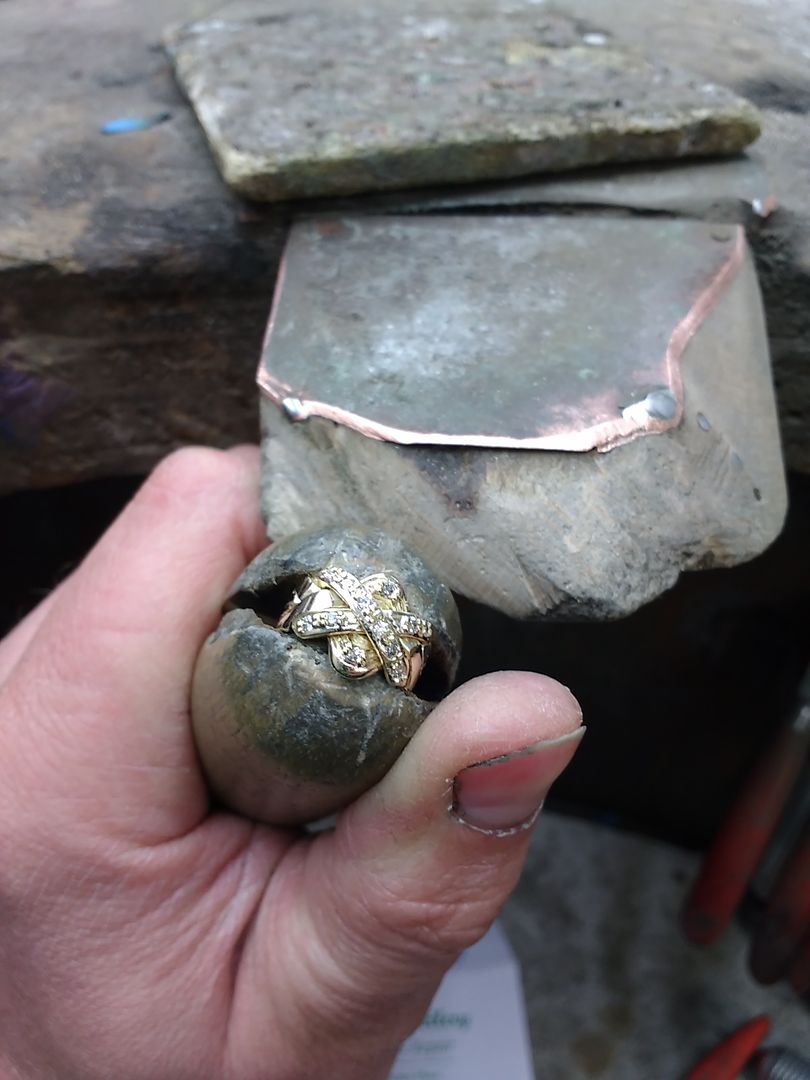
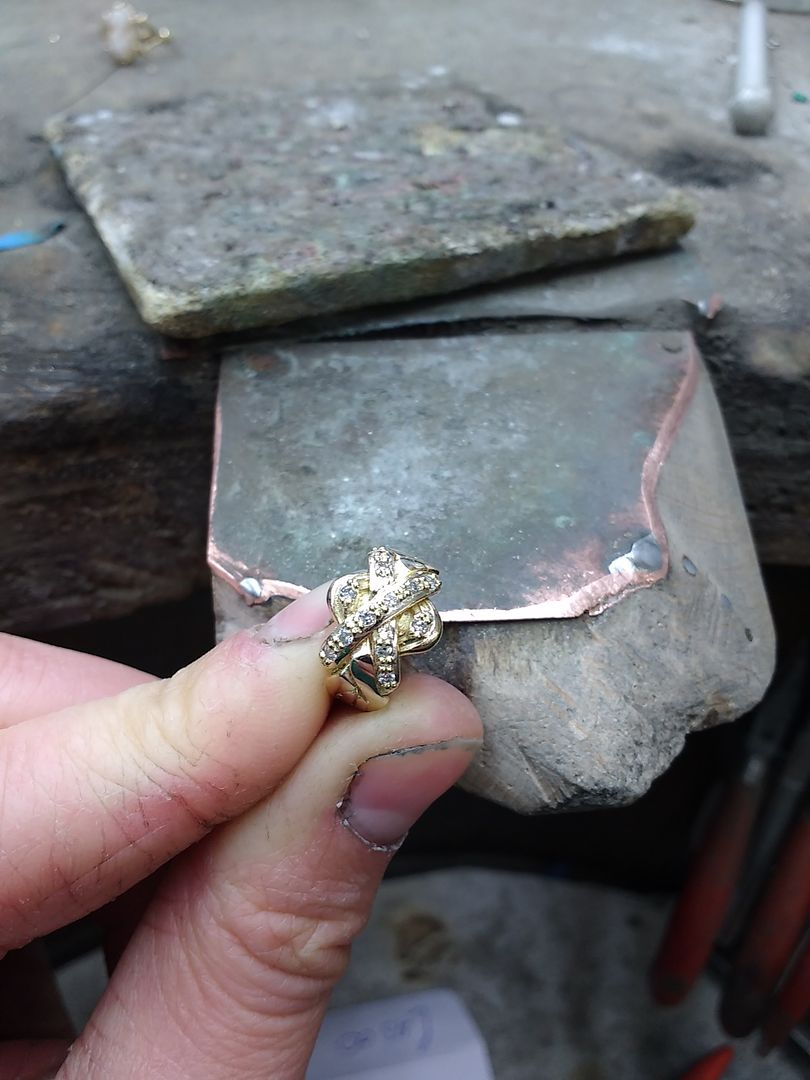
A good polish and a plate and it's all done:
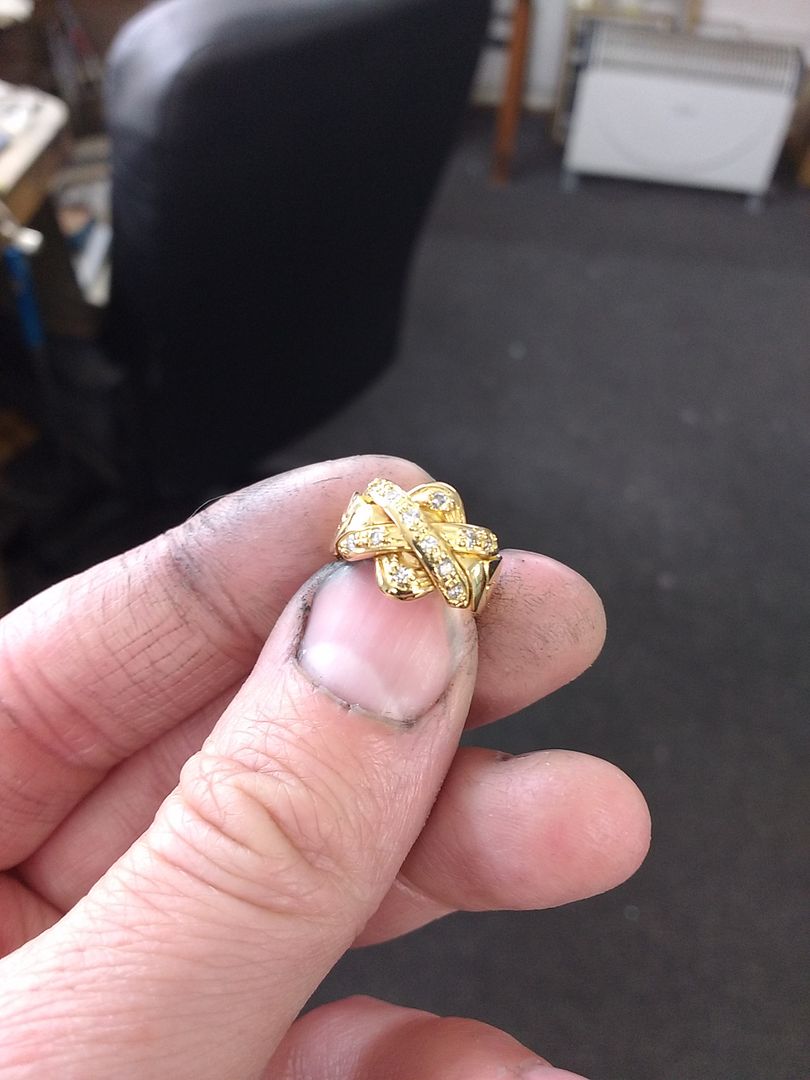
I also made a hinged, 18ct white gold and diamond bangle today. We had an 18ct yellow one already but the customer wanted it in white. So, we cast the components of the yellow bangle in 18 white and transplanted the setting from one to the other:
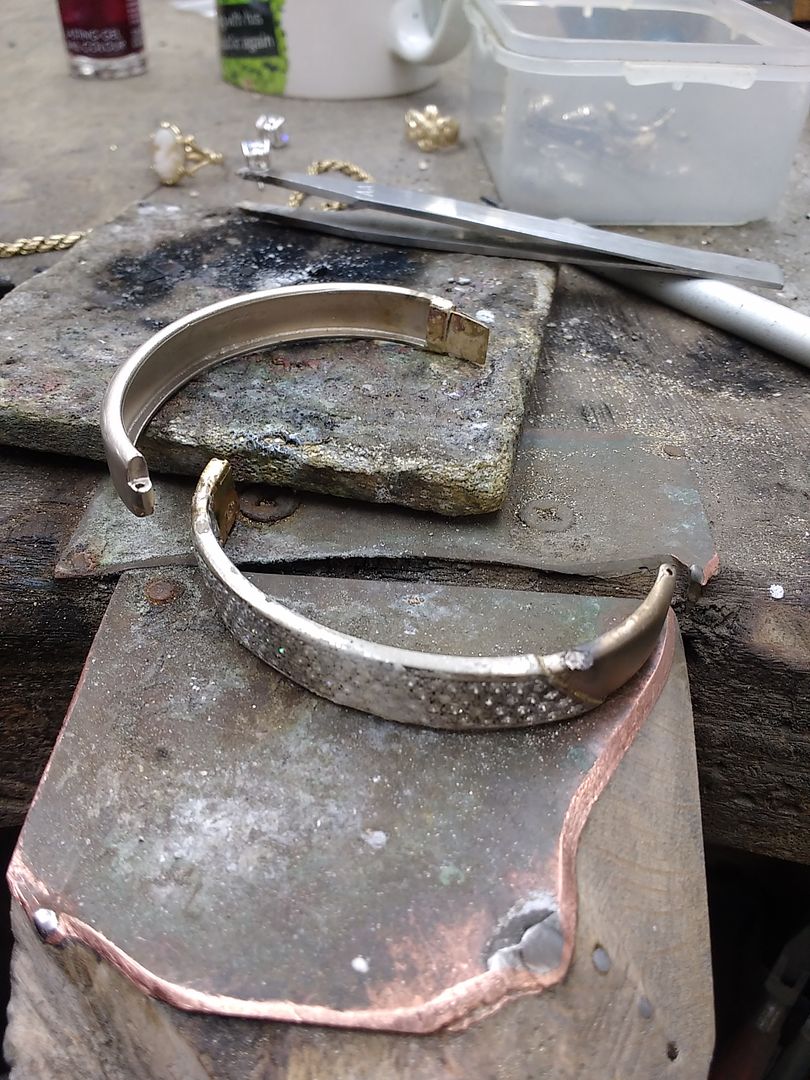
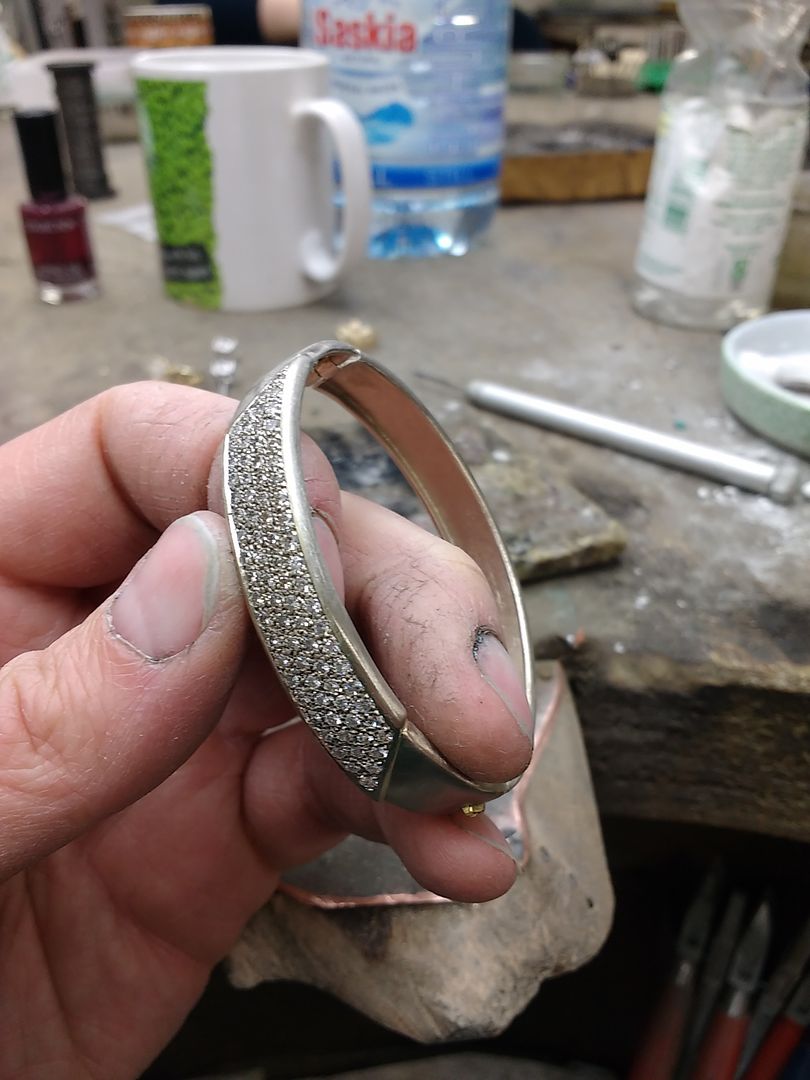
It was then polished and rhodium plated:
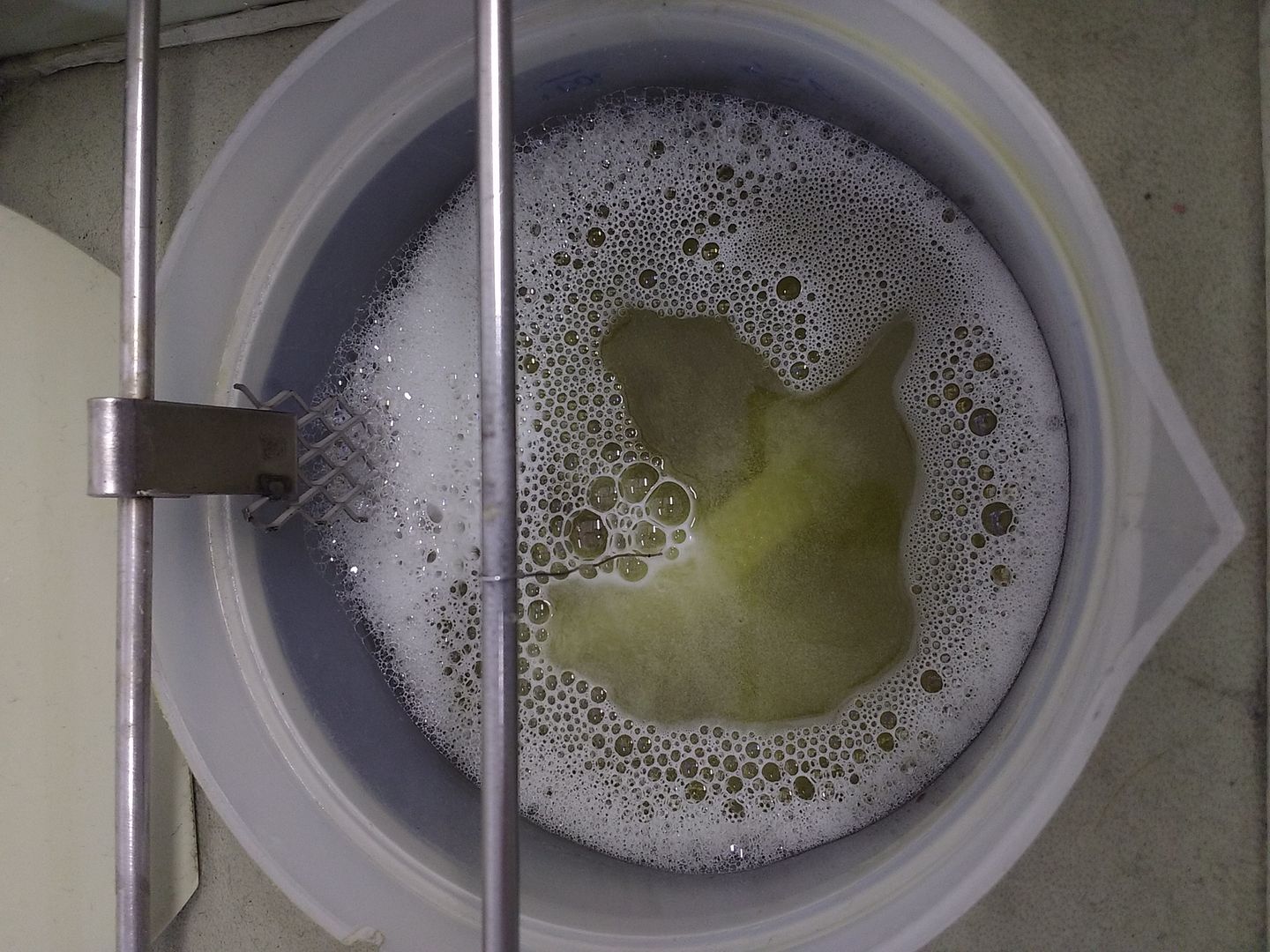
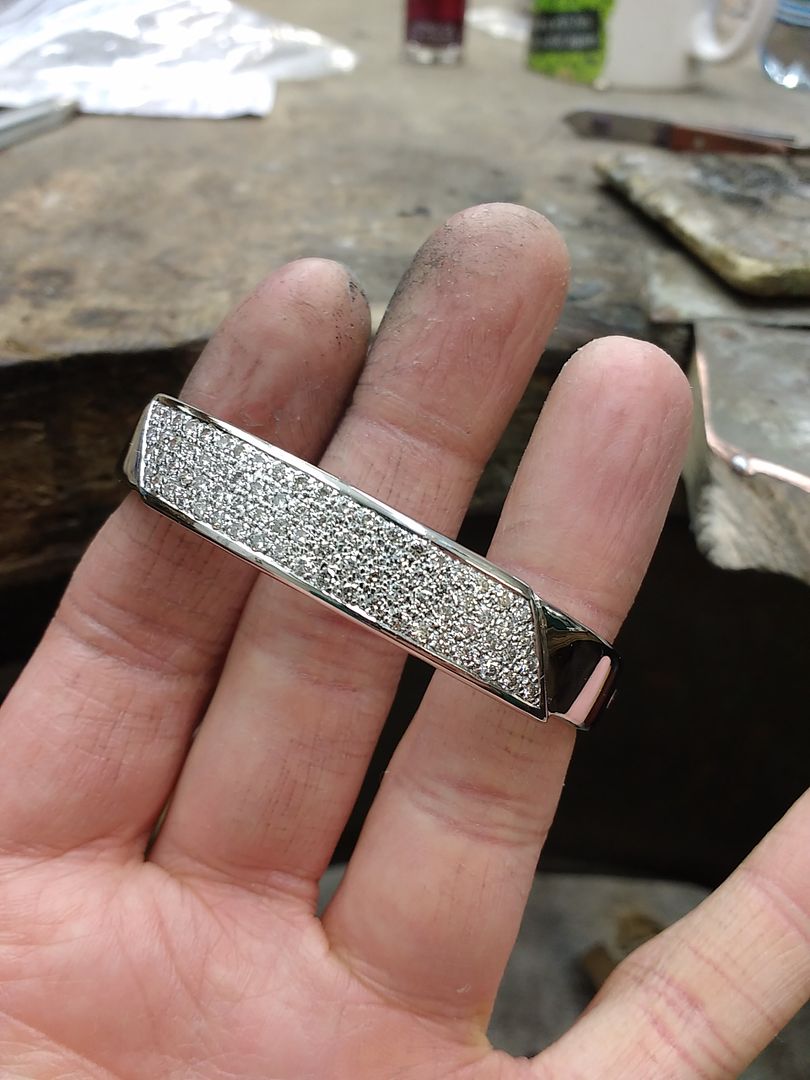
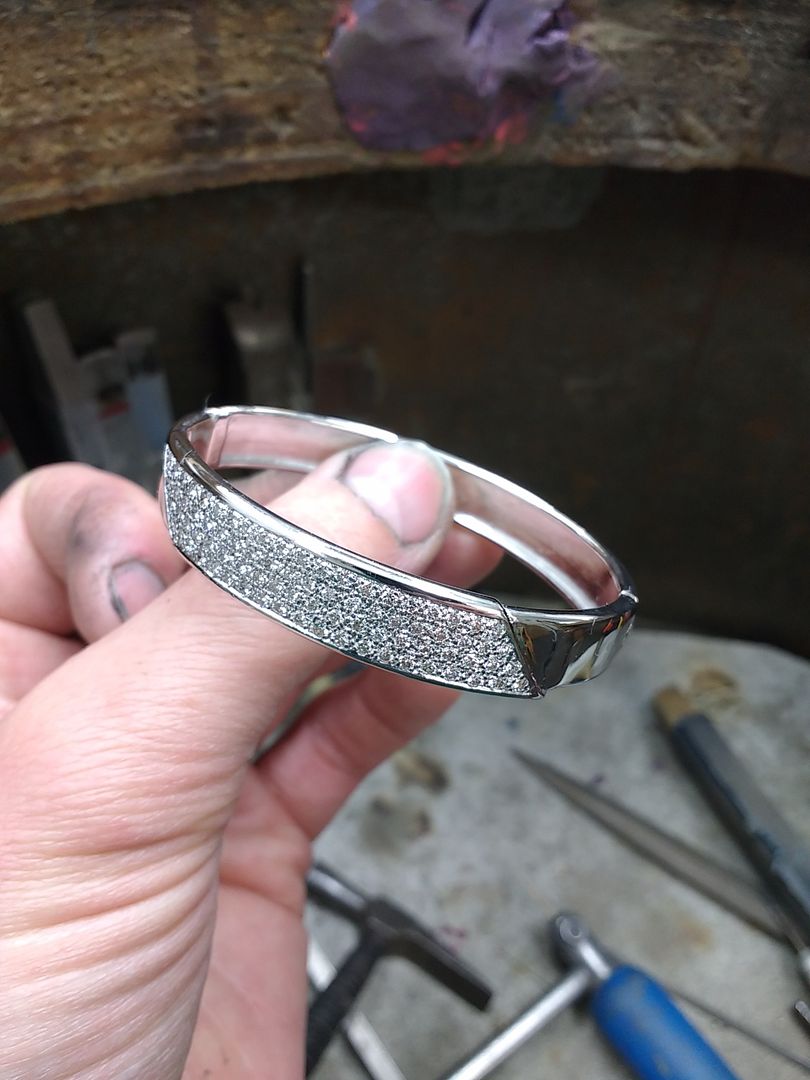
Happy customer!
We did something unusual a little while ago and unfortunately the customer has gone AWOL without payment. We hand made a bracelet in 18ct rose gold. Very few workshops will hand make a bracelet due to the amount of time needed to make the links, the customer was adamant he wanted it made to spec (as per another he owned) rather than off a reel. He was a long term customer and I suspect it may be that his circumstances may have changed, but we are where we are. We'd normally remelt the metal for use in other things but we were quite proud of this item and it stays as is until somebody fancies it.
I fancy it myslef but I think it requires a large frame to carry it off:

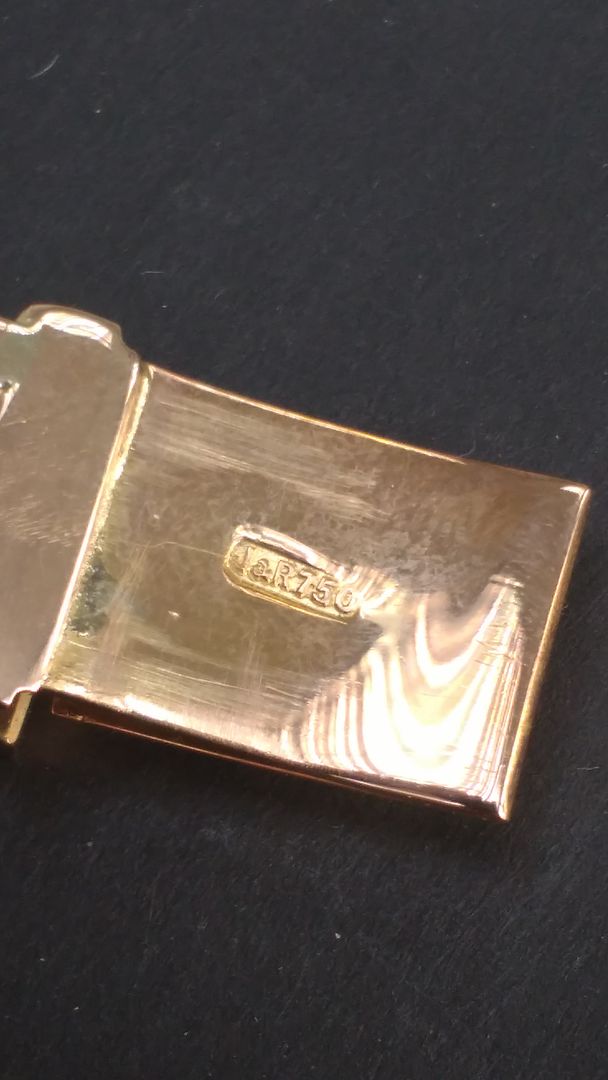
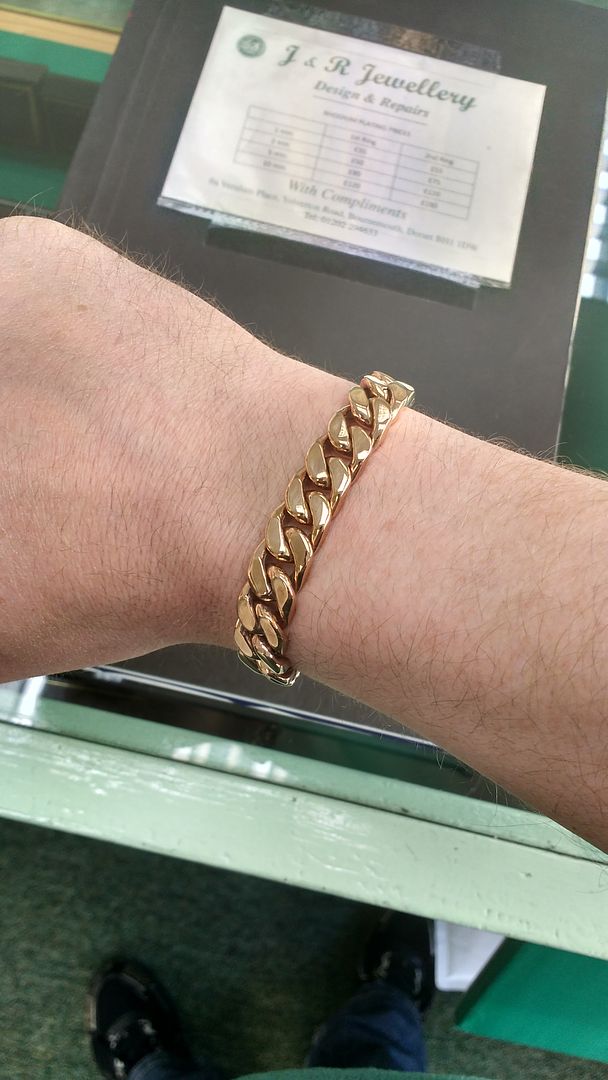
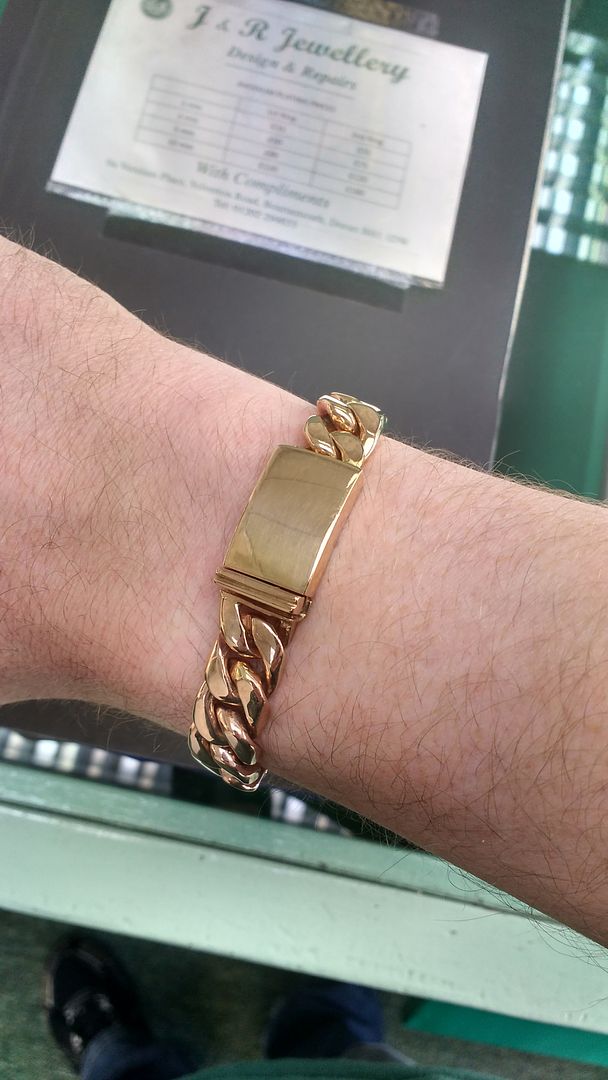
Eddie
I didn't take too many pics of the shank being done as I wasn't planning on documenting the job, but here is the new shank fitted. The original was broken and very worn:
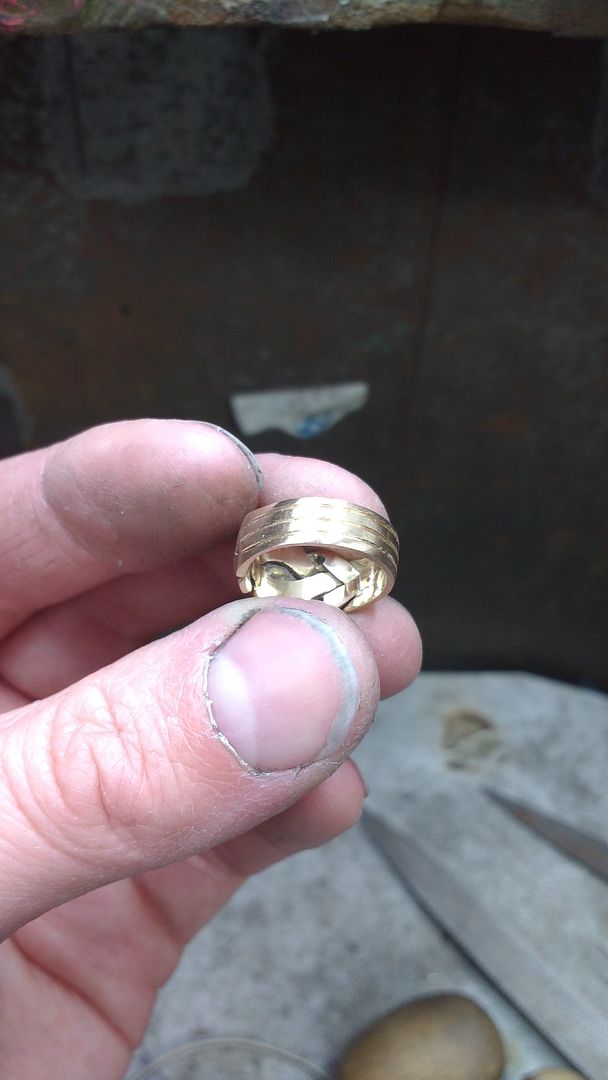
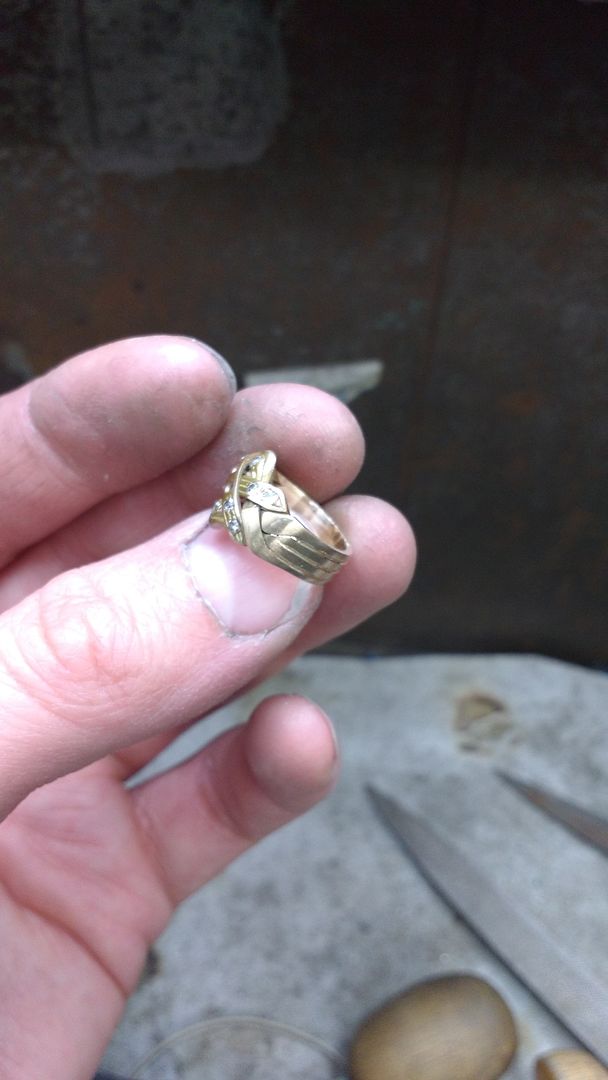
With the new shank in place the next job was to set the 2 missing stones and rebuild the claws that secure them. With the stones laid in place I solder 18ct yellow gold plates either side of each stone. I think 25 in all. I did the outer claws first, trimed them down and then did the centre ones:
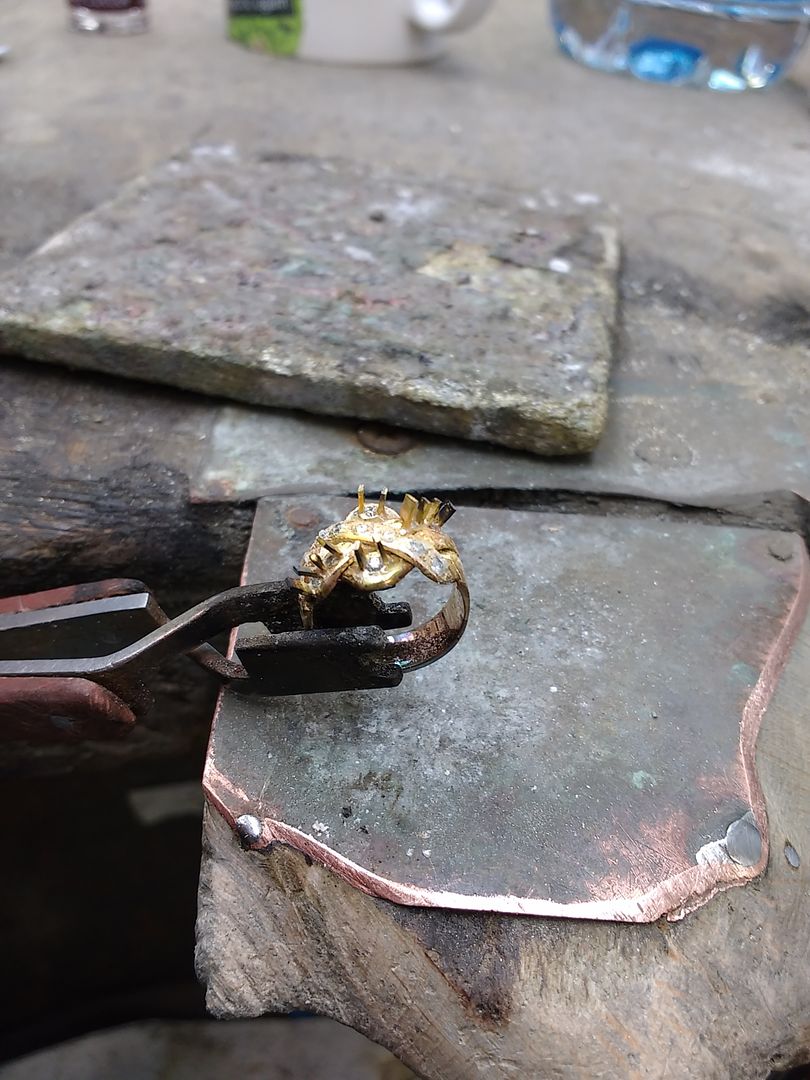
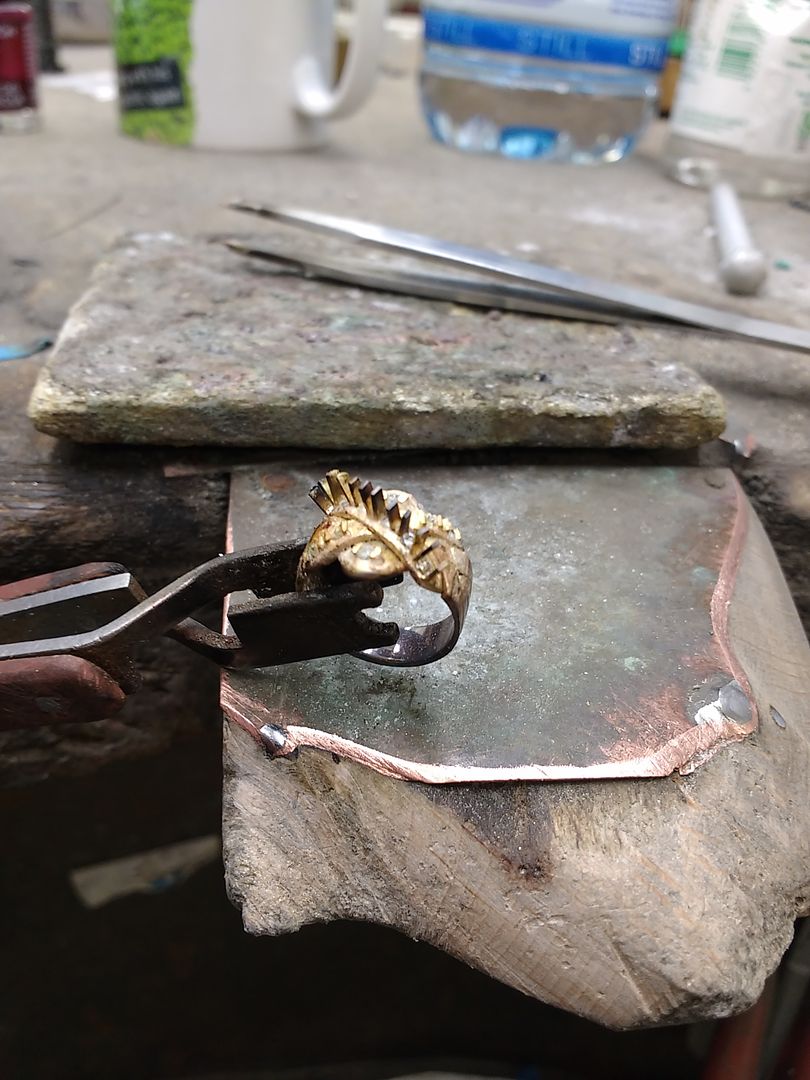
I then trimmed the centre claws down to a suitable level:
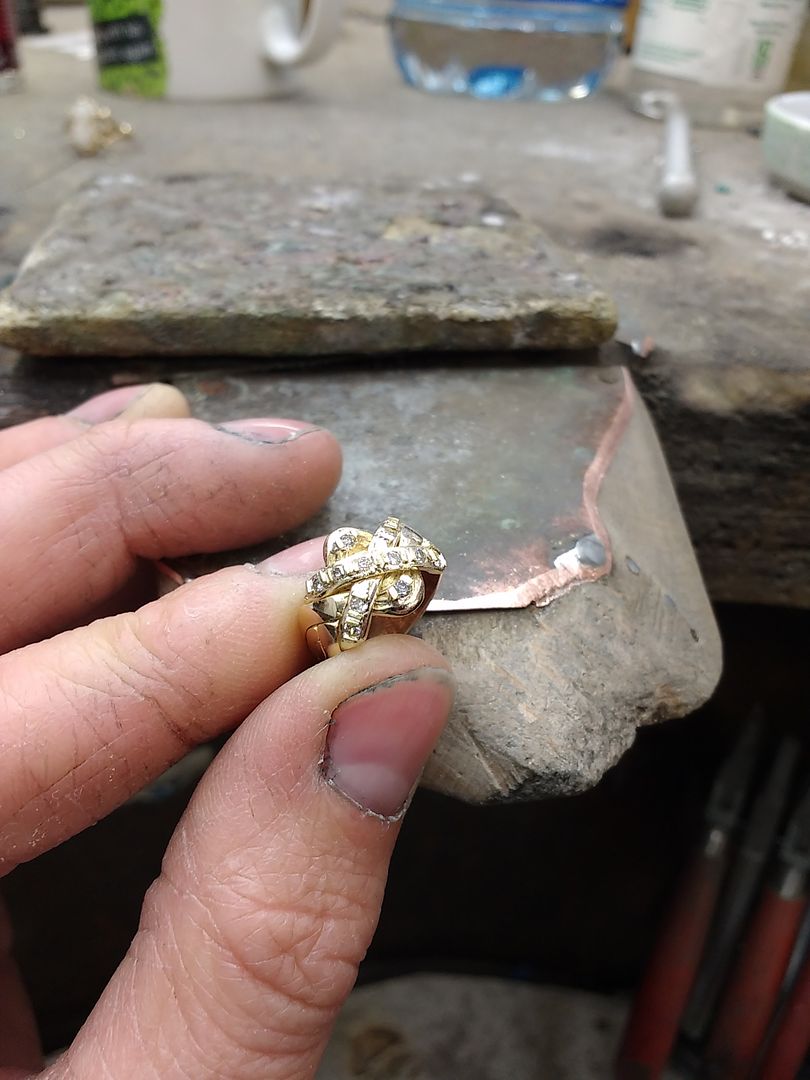
The bars are then split in the middle to create 50 individual claws. The ring is then clamped and the pegs pressed to secure the stones:
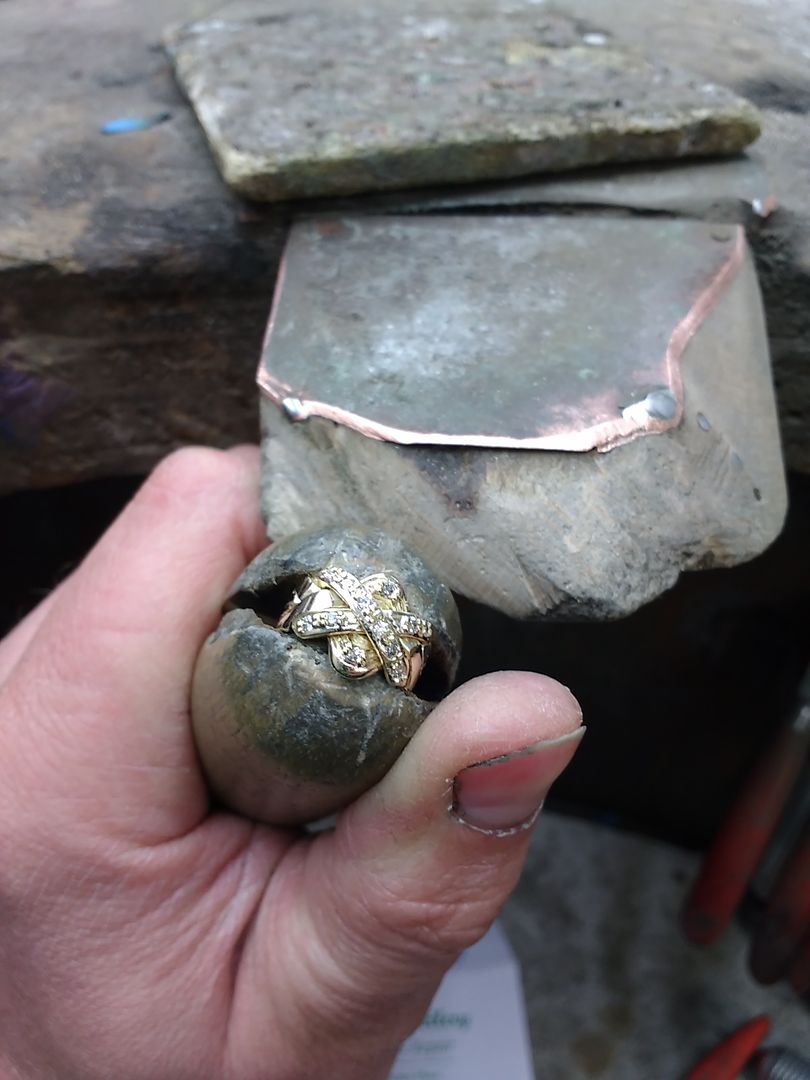
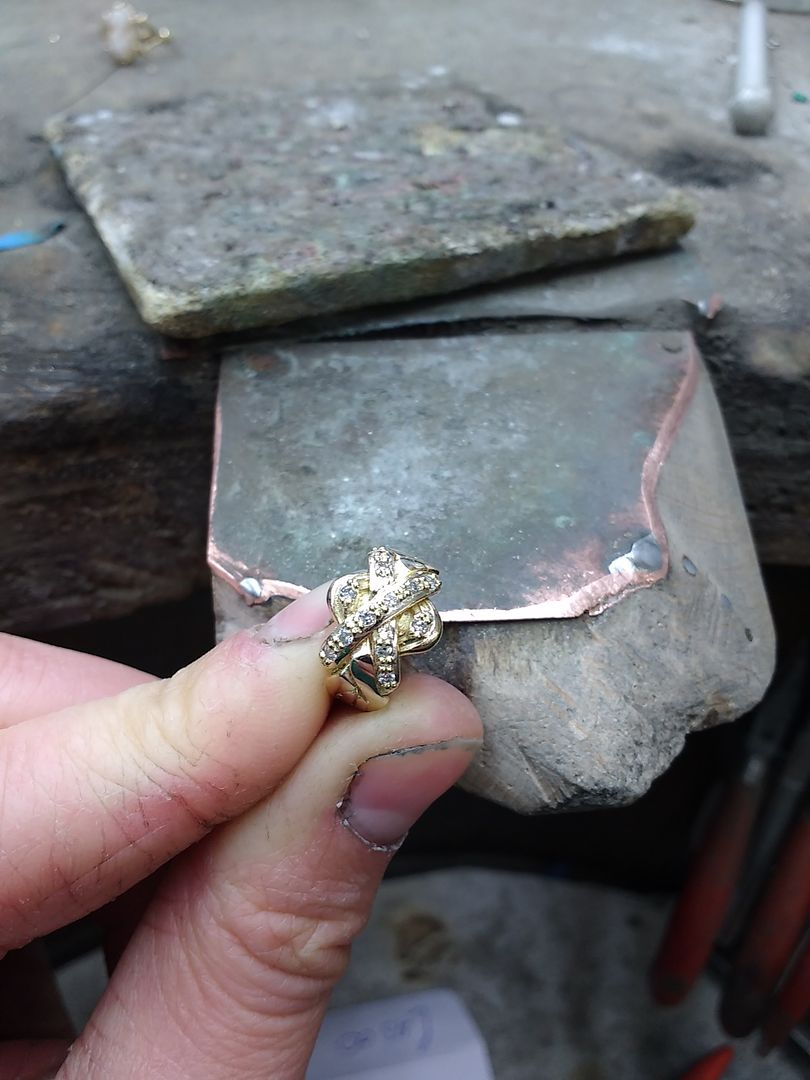
A good polish and a plate and it's all done:
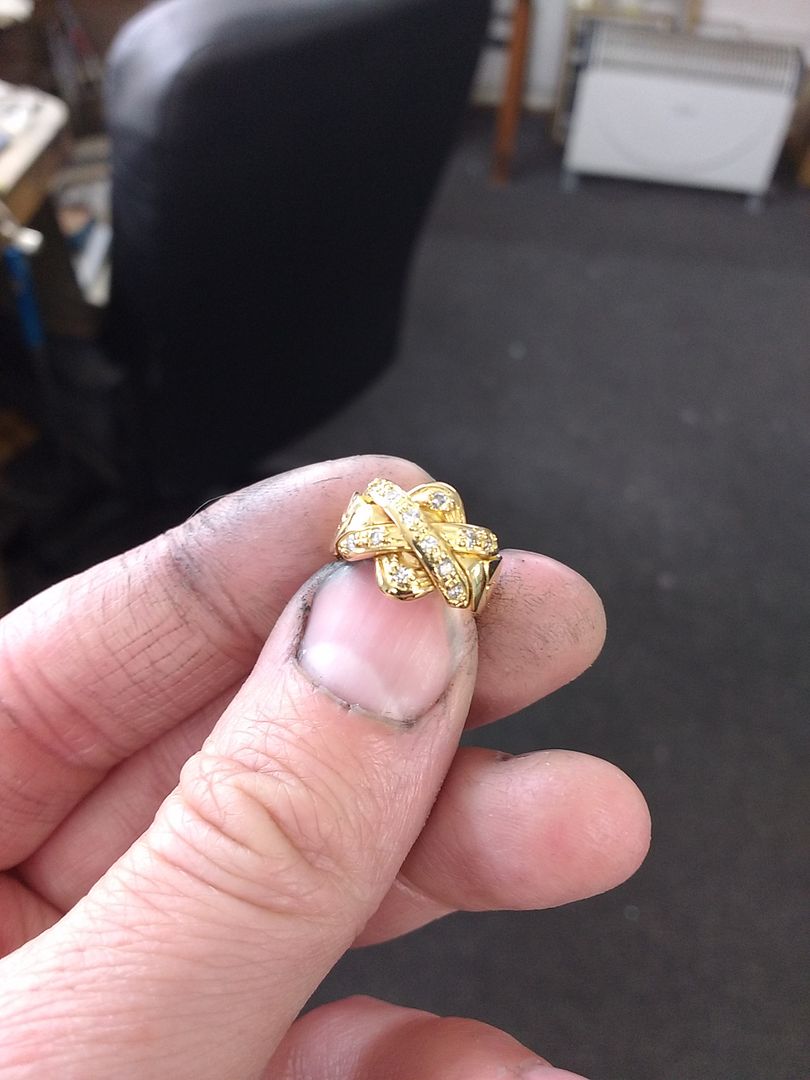
I also made a hinged, 18ct white gold and diamond bangle today. We had an 18ct yellow one already but the customer wanted it in white. So, we cast the components of the yellow bangle in 18 white and transplanted the setting from one to the other:
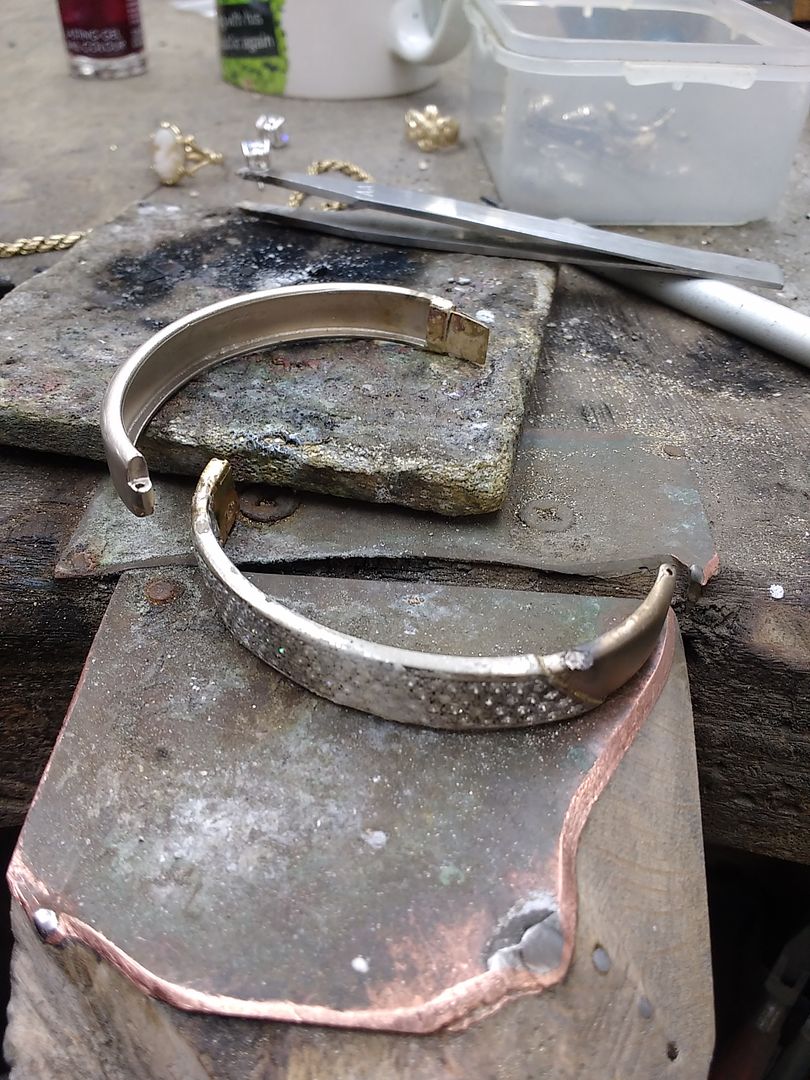
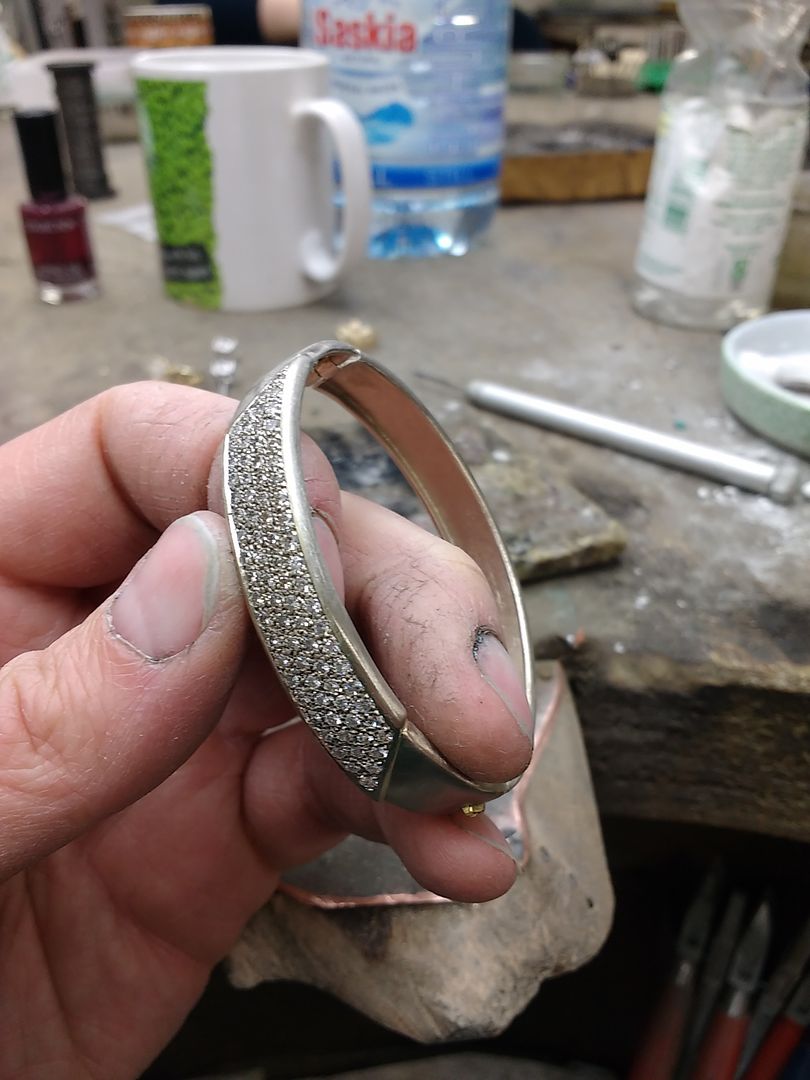
It was then polished and rhodium plated:
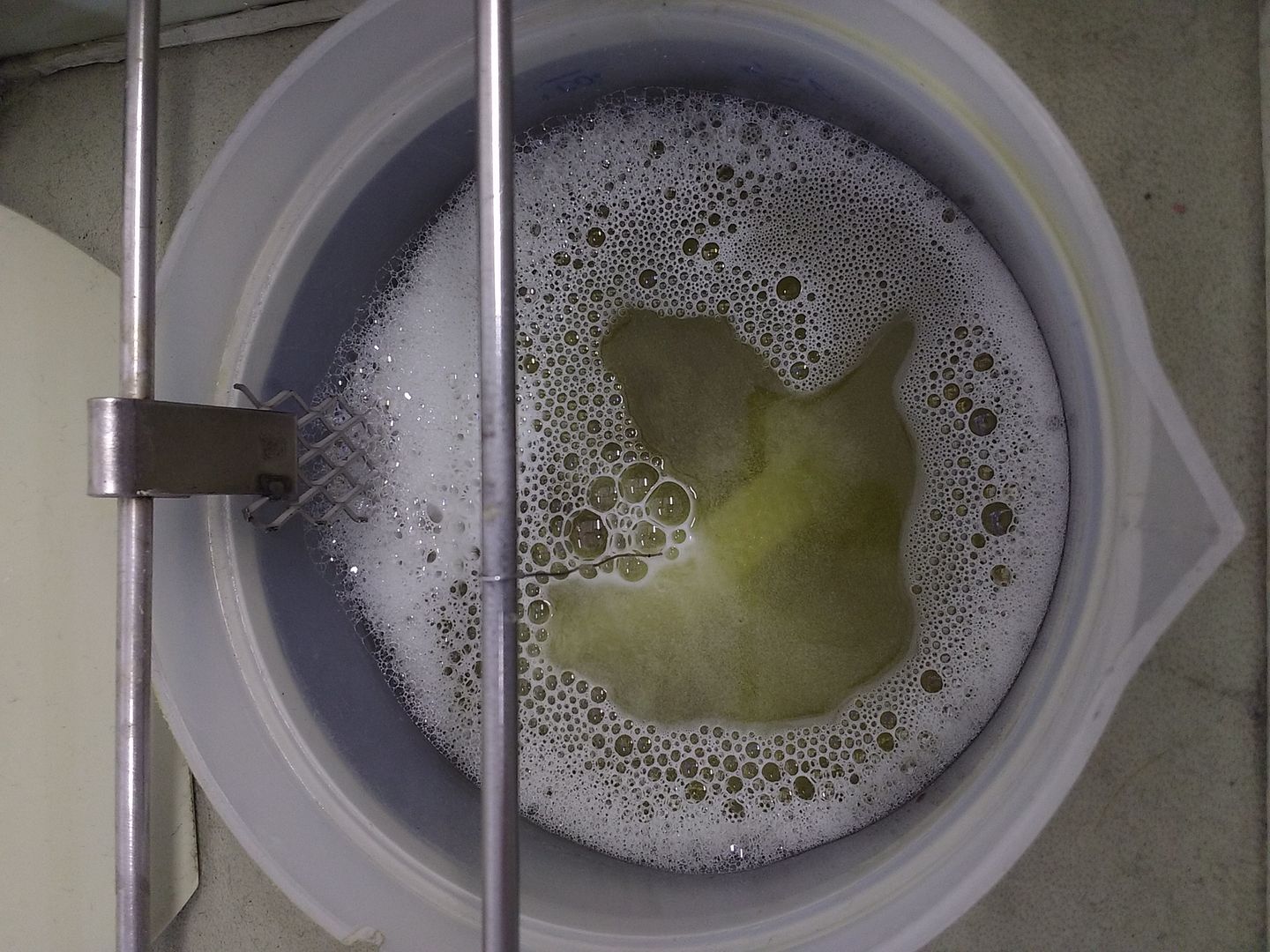
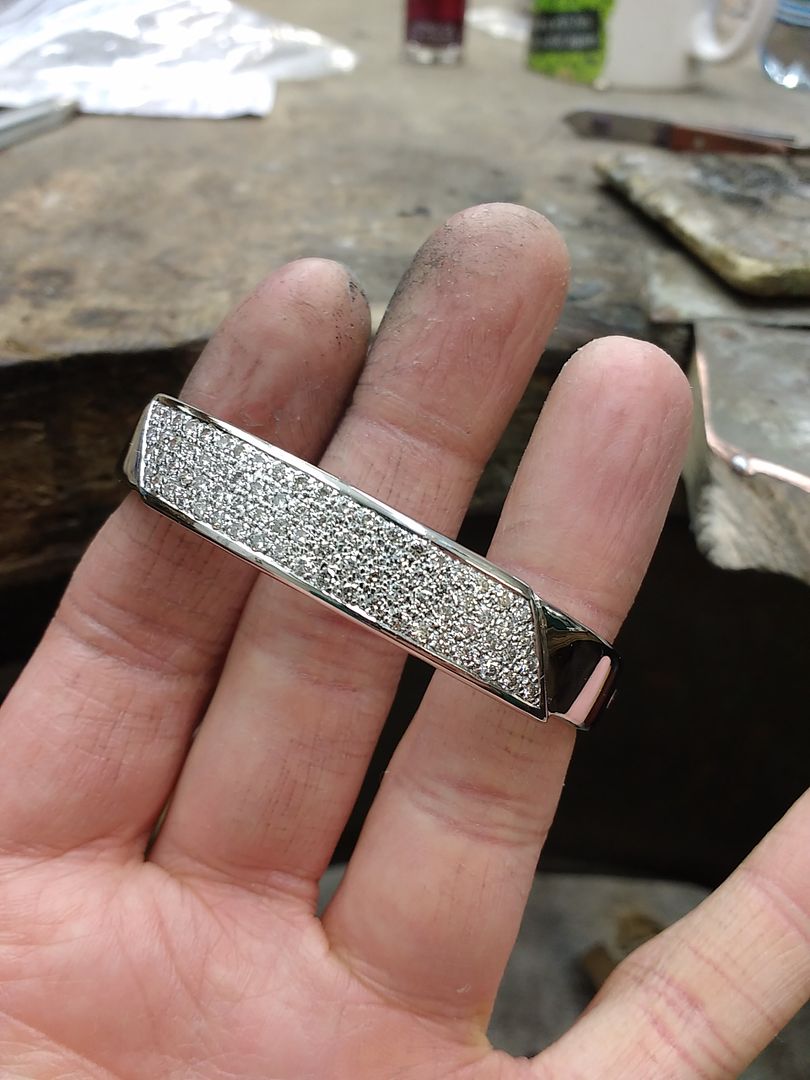
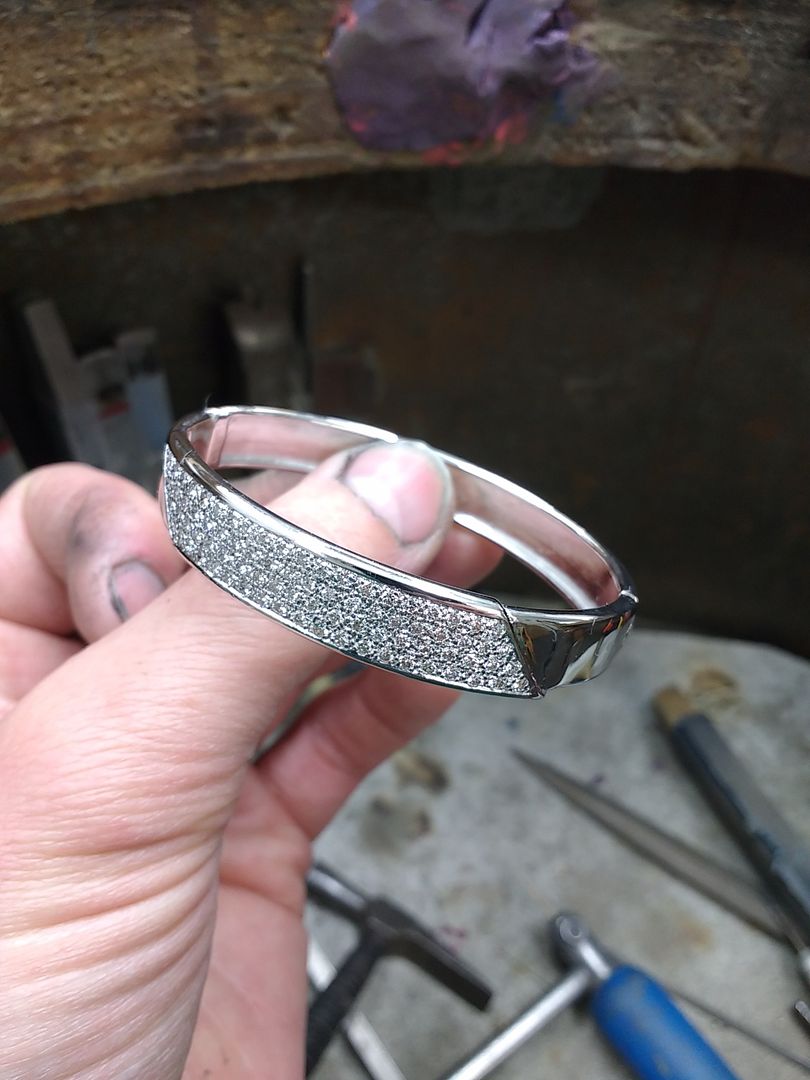
Happy customer!
We did something unusual a little while ago and unfortunately the customer has gone AWOL without payment. We hand made a bracelet in 18ct rose gold. Very few workshops will hand make a bracelet due to the amount of time needed to make the links, the customer was adamant he wanted it made to spec (as per another he owned) rather than off a reel. He was a long term customer and I suspect it may be that his circumstances may have changed, but we are where we are. We'd normally remelt the metal for use in other things but we were quite proud of this item and it stays as is until somebody fancies it.
I fancy it myslef but I think it requires a large frame to carry it off:

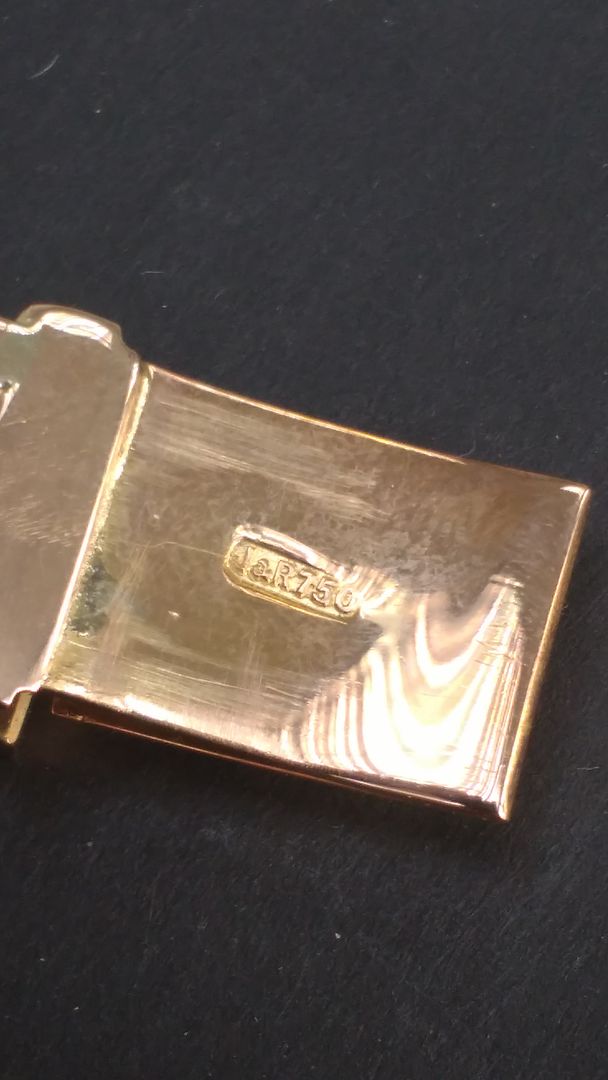
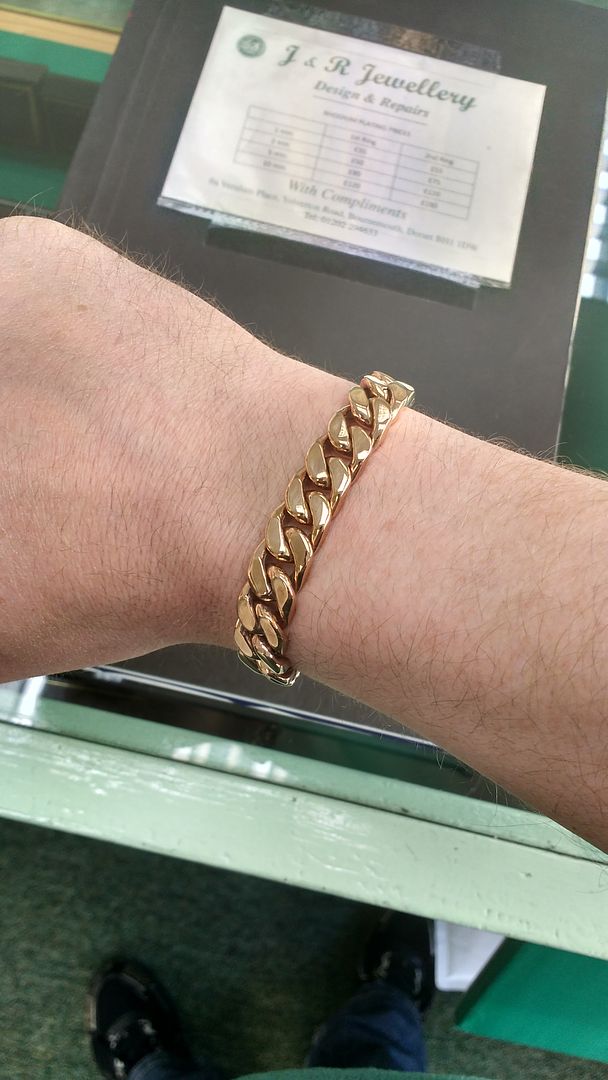
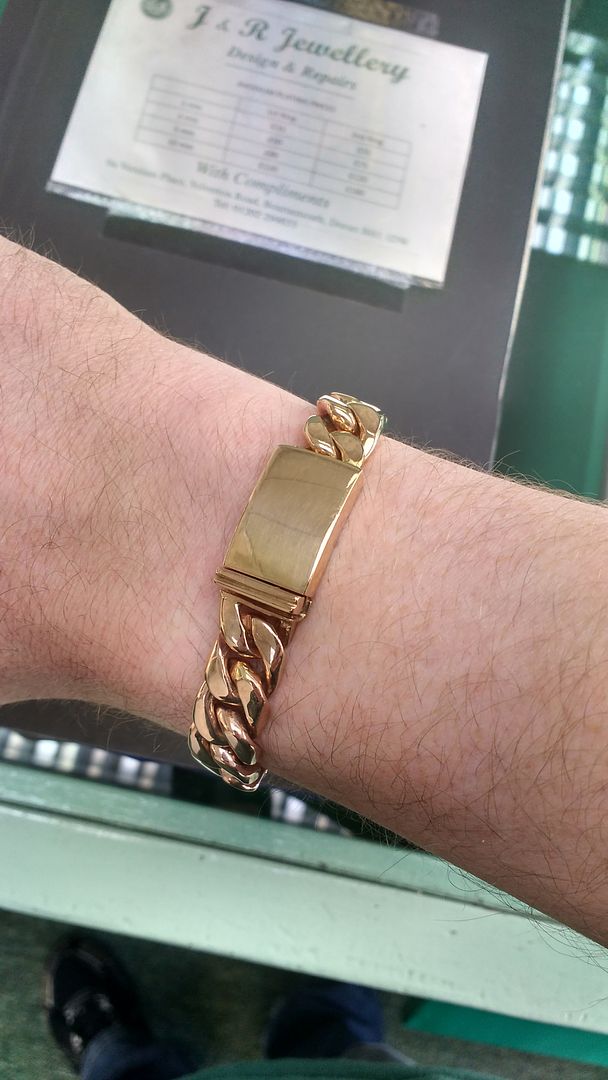
Eddie
Gassing Station | Watches | Top of Page | What's New | My Stuff