Ultima New boy finding my feet
Discussion
xrtim said:
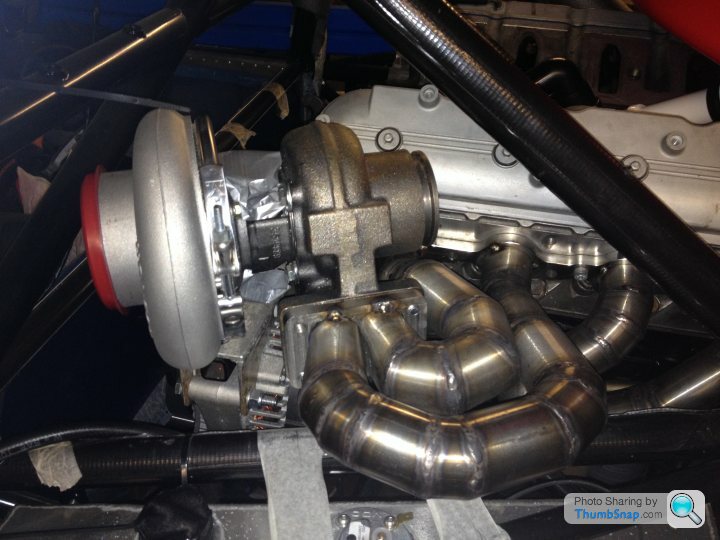
This is my first attempt at tig welding the exhaust (passenger's side) I have got to finish it off with waste gate and fully welding the flanges. Engine is LM7 5.3L and I may destroke it to 4.8l yet. Position of turbos has meant that all of the ancilary and dry sump drives have had to be custom made as will have to be the fuel surge and dry sump tanks. I'm going to use a charge cooler to lower intake air temps and laminova coolers/preheaters for the gearbox and engine oil. This will free up side pod intakes for cold air intake for each turbo once air con rad is relocated megasquirt MS3 pro will control the engine,boost and 16 injectors. Once I have everything in its final place the engine will go to the machine shop and will be re-installed and run up before body goes on.
xrtim said:
Tim, there is a web site / face book feed that i have subscribed too, its called "weldporn" (i think it should be safe for work) which has some great examples on it. they have talked about back purging in the past and seem to plug the tubes and fill with an inert gas to produce better welds.hope that helps
regards Ryan
ezakimak said:
Tim, there is a web site / face book feed that i have subscribed too, its called "weldporn" (i think it should be safe for work) which has some great examples on it. they have talked about back purging in the past and seem to plug the tubes and fill with an inert gas to produce better welds.
hope that helps
regards Ryan
Sure is acceptable porn...hope that helps
regards Ryan
https://www.facebook.com/pages/Welding-Porn/144440...
ezakimak said:
xrtim said:
they have talked about back purging in the past and seem to plug the tubes and fill with an inert gas to produce better welds.hope that helps
regards Ryan
Paul
T junction and second regulator of gas bottle, a length of hose and some way off plunging the end of the tube. i would think you would want a very low pressure in the part you are welding otherwise it is going to push the weld out, like when welding galvanised with regular rods or welding over a slag inclusion - stuff that I'm sure we have all done by mistake when learning to weld.
ive got a second regulator here just need to get a T junction and some more hose. presume a couple of blocks of wood cut to size with a hole saw such that they are reasonably close in size might be ok to form a make shift bung. if the end of the tube is far enough away you could probably just use a rag stuffed in the end as it wont get hot enough.
if I end up getting another welder (TIG) that will probably come with a 3rd reg.
ive got a second regulator here just need to get a T junction and some more hose. presume a couple of blocks of wood cut to size with a hole saw such that they are reasonably close in size might be ok to form a make shift bung. if the end of the tube is far enough away you could probably just use a rag stuffed in the end as it wont get hot enough.
if I end up getting another welder (TIG) that will probably come with a 3rd reg.
Gassing Station | Ultima | Top of Page | What's New | My Stuff