www's new build thread
Discussion
MagicalTrevor said:
Can I ask what your thought process was for using timber frame as I assume SIPS was also considered? I'm not, of course, suggesting you're wrong. I'm just interested to hear your views.
A lot of it was down to reducing risk on site. The more wet trades you have, the more decisions you're going to be making at the last minute and the more you're affected by weather, resource etc. I'm managing the project and am a busy guy - the last thing I needed was more problems! So, going down the timber frame route meant that most of the big decisions could/would be made before we hit the site which meant I could do all my thinking up front and I knew exactly what I'd be getting. And it's way more accurate 
Choice of supplier largely came down to recommendation. The fact that they produced a very efficient structure was largely secondary tbh.
SIPS were a bit more expensive and not as flexible
Ok, groundworks finished for now! Yay!!!
I've updated the blog https://selfbuildnoviceblog.wordpress.com but here is a bit of an excerpt from the latest instalment
So after 4 days we’ve stripped the site where needed, prepared an area of hardstanding at the front, dug down for the slab and back-filled with MOT Type 1. Oh, and we’ve had a storage/office container and site toilet delivered. Nice.
The plot has a slope from front to back and we always knew that there would be a bit of ‘landscaping’ to get the levels right. The topological survey we had done is good but there’s no substitute for actually looking at what you have in front of you with your own eyes (now recently tested and aided by a lovely pair of Lindberg glasses from my local optician – too nice for the site methinks though). Yet again, I digress…
So why do I mention this? Well it’s obvious that the top of the slab, let’s call it the FFL (Finished Floor Level) even though technically it isn’t, will not be the required 150mm above the surrounding ground. Actually, I suppose if you consider that the house sits about 1m inside the dug slab area then it is, but we still need to Do Something. What that means is that we’re going to have to re-level part of the sides and the front of the plot. I’m not sure at the moment how I want it to look as it could be a fully graded slope but I want a flat driveway area so it could be that we build a small retaining wall about 400mm high. In some respects I wish we had done more levelling before the dig but in reality I think it’s really only obvious now what may be needed. I think no-matter what we’d done there would have been some re-jigging so I’m not too fussed really. I’ll have a word with the architect and see what he thinks.
Water
In addition to the heavy work, I’ve had a stand-pipe for a temporary water supply fitted by the plumber. This is all a real palaver and may mean that we don’t have site water initially, although I have a back-up plan.
Basically, I needed the trench dug but couldn’t get this done until the ground workers were on site. Then I needed the pipe fitting. Then it needs to be approved – in writing. Then I need to make an application for connection. Then it takes about 21 days to get connected.
The ground workers were waiting for the spec of the dig and in-fill from the structural engineer before they’d turn up (obviously) and this only came 3 and a half weeks before the timber frame guys are due to start. Not the fault of the timber frame guys but really piss-poor planning from the SE. So, timber frame guys, if you have no water on site you know who to ‘pay a visit’! At least the ground workers were brilliant at getting on site as quick as possible

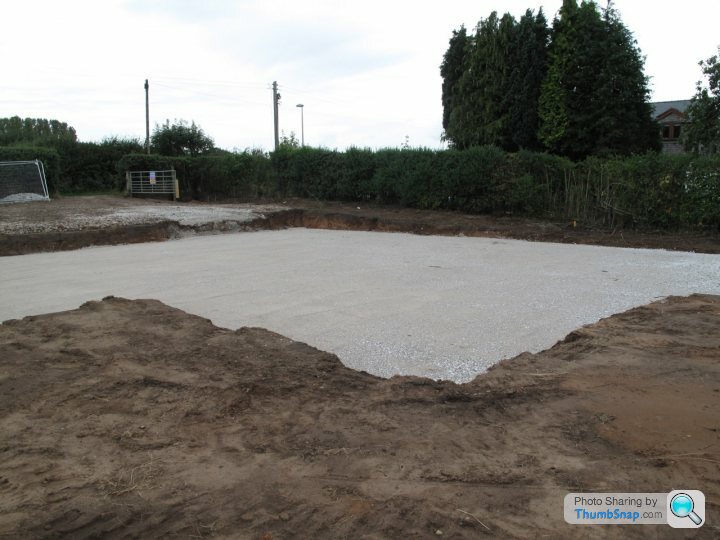
Someone hasn't bothered to wait for completion before moving in
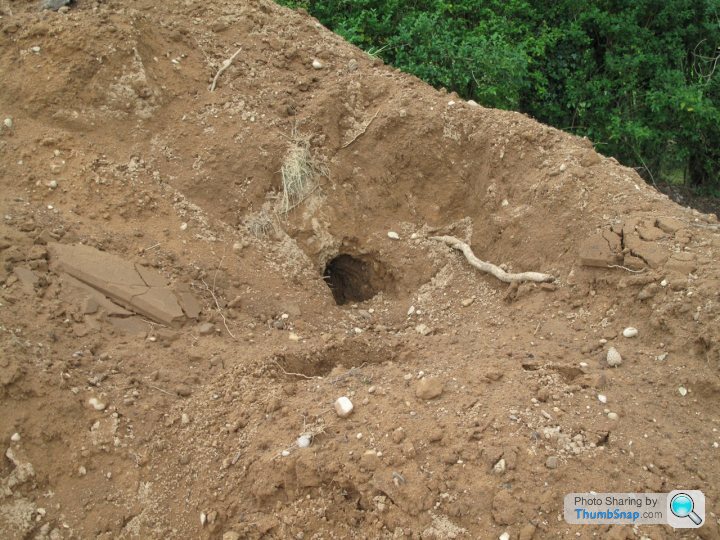
I've updated the blog https://selfbuildnoviceblog.wordpress.com but here is a bit of an excerpt from the latest instalment
So after 4 days we’ve stripped the site where needed, prepared an area of hardstanding at the front, dug down for the slab and back-filled with MOT Type 1. Oh, and we’ve had a storage/office container and site toilet delivered. Nice.
The plot has a slope from front to back and we always knew that there would be a bit of ‘landscaping’ to get the levels right. The topological survey we had done is good but there’s no substitute for actually looking at what you have in front of you with your own eyes (now recently tested and aided by a lovely pair of Lindberg glasses from my local optician – too nice for the site methinks though). Yet again, I digress…
So why do I mention this? Well it’s obvious that the top of the slab, let’s call it the FFL (Finished Floor Level) even though technically it isn’t, will not be the required 150mm above the surrounding ground. Actually, I suppose if you consider that the house sits about 1m inside the dug slab area then it is, but we still need to Do Something. What that means is that we’re going to have to re-level part of the sides and the front of the plot. I’m not sure at the moment how I want it to look as it could be a fully graded slope but I want a flat driveway area so it could be that we build a small retaining wall about 400mm high. In some respects I wish we had done more levelling before the dig but in reality I think it’s really only obvious now what may be needed. I think no-matter what we’d done there would have been some re-jigging so I’m not too fussed really. I’ll have a word with the architect and see what he thinks.
Water
In addition to the heavy work, I’ve had a stand-pipe for a temporary water supply fitted by the plumber. This is all a real palaver and may mean that we don’t have site water initially, although I have a back-up plan.
Basically, I needed the trench dug but couldn’t get this done until the ground workers were on site. Then I needed the pipe fitting. Then it needs to be approved – in writing. Then I need to make an application for connection. Then it takes about 21 days to get connected.
The ground workers were waiting for the spec of the dig and in-fill from the structural engineer before they’d turn up (obviously) and this only came 3 and a half weeks before the timber frame guys are due to start. Not the fault of the timber frame guys but really piss-poor planning from the SE. So, timber frame guys, if you have no water on site you know who to ‘pay a visit’! At least the ground workers were brilliant at getting on site as quick as possible

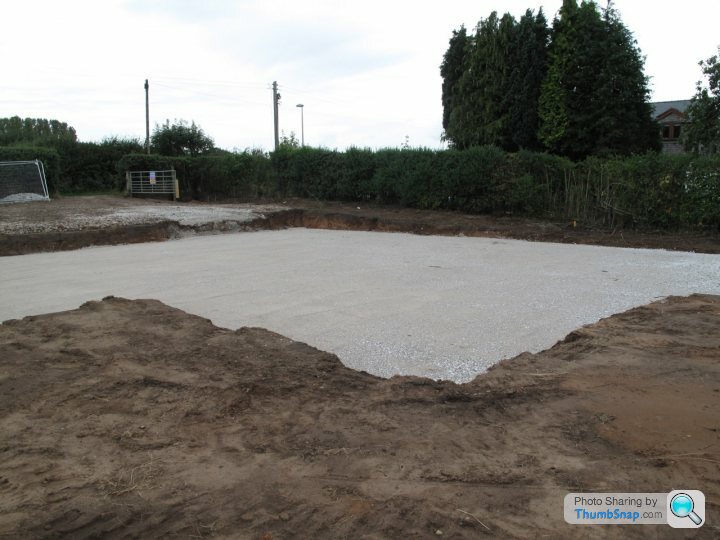
Someone hasn't bothered to wait for completion before moving in
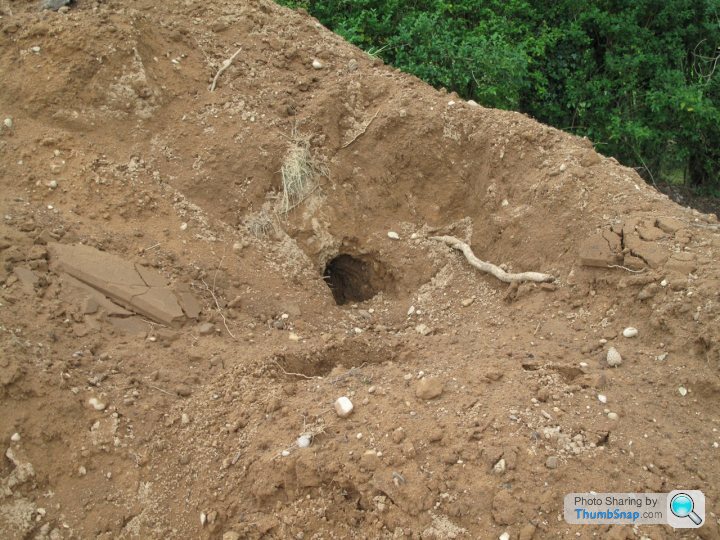
alfie2244 said:
Not read the whole blog yet....just a quick one for you:
What are the falls like for the drive? I.e. always best to fall away from the house.
Yeah, no chance of that. The road is about 1m higher than the house. Wish it was the other way around, but it is what it is I suppose What are the falls like for the drive? I.e. always best to fall away from the house.

magooagain said:
So with the sandwich of the insulation and concrete slab it will raise up by what? 40 or 50cms to ffl ?
Yes, 500mmmagooagain said:
So with the sandwich of the insulation and concrete slab it will raise up by what? 40 or 50cms to ffl ?
Hopefully that will get you above the drive level,but still looks like you may need some surface drains around the house perimeter.
Yes, drains are in the plansHopefully that will get you above the drive level,but still looks like you may need some surface drains around the house perimeter.
magooagain said:
So with the sandwich of the insulation and concrete slab it will raise up by what? 40 or 50cms to ffl ?
What would be the consequences of putting in more mot to get the house up out of any rainfall danger?
House too high for planningWhat would be the consequences of putting in more mot to get the house up out of any rainfall danger?
Peanut Gallery said:
Regarding your internet issue at 7 grand.
Decent cell connection, mobile phone on an unlimited contract, set up as a wifi router? - Tech people will be able to come up with a far better solution, but I have seen results from 4G faster than from my normal internet.
Please disregard if this will not work for you!
And thread bookmarked!
There is 4G but it's not the best - inside the house i think it will be non-existent. Decent cell connection, mobile phone on an unlimited contract, set up as a wifi router? - Tech people will be able to come up with a far better solution, but I have seen results from 4G faster than from my normal internet.
Please disregard if this will not work for you!
And thread bookmarked!
Thanks for the suggestion though

So, a quick update. It looks like the slab may be being laid earlier than expected so suddenly I've got a bit of a panic on to decide what ducting I need to install in the slab for routing of the services. Aside from gas, nothing will go through the wall - it will all come up through the insulated slab.
So, here's my thinking so far. Ducting to/from the house is through the slab
electric (meter cabinet is by the plot boundary)
Anyone care to fill in the blanks and suggest areas I've overlooked?
So, here's my thinking so far. Ducting to/from the house is through the slab
electric (meter cabinet is by the plot boundary)
- 2 x 110mm duct from cabinet to plant room (feed and return)
- 63mm duct from cabinet to garage
- 63mm duct from cabinet (spare)
- ???mm from house to garden for lighting and power
- ???mm to the kitchen island (25mm rigid polyduct?)
- 63mm duct from main to house
- ???mm from ??? to garden - not sure where to route this from. Should it come from the house or can it be teed off before the feed enters the house?
- ???mm from ??? to garage - not sure where to route this from. Should it come from the house or can it be teed off before the feed enters the house?
- duct 54 to plant room
- want to also route ethernet from house to garage, but not sure how best to do this without another duct. Are there tee pieces for duct 54?
- duct ??? for coax cable from aerial at bottom of garden
Anyone care to fill in the blanks and suggest areas I've overlooked?
Just a quick update on the blog this evening. Nothing has really happened lately but...
WE START TOMORROW!!!!!!!!
https://selfbuildnoviceblog.wordpress.com
But as we all like a picture
here's a couple to whet the appetite!


WE START TOMORROW!!!!!!!!
https://selfbuildnoviceblog.wordpress.com
But as we all like a picture



WE'VE STARTED!!!
https://selfbuildnoviceblog.wordpress.com
Due to traffic issues on the way over to site on the first day the guys that are doing the slab were delayed by an hour or so, so we had our own little Operation Stack. First one in was a delivery of ‘dust’ – blinding material on top of which the insulation will sit. The driver (a really nice guy) was pretty patient waiting for them to turn up but in the end I just told him to dump it – just not in the hole!
The second lorry was waiting to deliver the insulation itself. I think this driver was quite happy to wait though and jumped straight back in his cab to brew up!
So, the first day was spent getting this ‘dust’ levelled on the slab to a thickness of 50mm. It was pretty slow going (2 guys) but they were very thorough. You can just about see a couple of the battens laid on the slab that they used to help set the levels (with the help of a theodolite). Due to the late start they were off site about 6:30-7:00pm and I think they would have stayed later if it hadn’t started to go dark.

Two of the key features of the build are it’s high levels of insulation and its air-tightness. To put the level of air-tightness into perspective let’s compare it to standard UK Building Regulations.
Part L1A of the ‘regs’ state that any new dwellings are tested for air tightness by using a method known as a ‘blower door test’ in accordance with BS EN 13829. The measurement is taken by blowing air into the house via a particular door that is mounted in the main entrance. Part L1A requires an air tightness of maximum 10 m3/hr/m2 air loss at a pressure of 50 Pa. Standard good practice for air tightness testing in the UK is a maximum of 7 m3/hr/m2.
We are building to Passiv standards and the measure they use is in air changes per hour (ACH). A house built to Passiv standards requires no more than 0.6ACH and that’s what we are aiming for.
There isn’t really a direct way to convert from m3/hr/m2 to ACH as it depends on volume and floor area, but a reasonable finger-in-the-air would be to say that Part L1A is looking for around 7-10ACH. That’s like leaving a door wide open!
So next time your builder says he’s building to the regs, go and find another builder. Or more fairly, another build method.
Every time you put a hole in the structure you compromise its air-tightness. Water, electricity, gas, phone etc. all need to get into the house so how best to do this? Aside from the gas which must go straight in (though the wall) everything else can and will come up through the slab in ducts. The ducts still need sealing and insulating, but that’s a relatively trivial job.
What isn’t trivial though is working out where you want everything to come through the slab and then actually doing it. Accurately. Hence the chat to confirm everything. We’ve changed a few things from my original ideas (“I spent bloody ages working all that out, I’m not changing it now!”) but I’m going with advice based on past experience. Obviously I’m assuming that experience is Good Experience and not repeated carnage, but I’ll be honest and say I daren’t ask! Sometimes it’s good (not) to talk.
Day 2 saw the start of the insulation going down and the first cock-up.
The surveyor had previously set-out the slab perimeter with steel pins but it seems these had been interpreted as something the groundworkers had left in (for a laugh?). I’m not quite sure how you could possibly jump to that conclusion but anyway, they were largely ignored, moved or squashed. Fortunately, 3 were still in-tact so rather than just playing dot-to-dot with a bit of Extruded Polystyrene (EPS) it looks like they’ve got a lot more work to do to ensure it’s all in the right position. I know it’ll be right in the end, but it is more than a bit annoying.
Anyway, end of my day 2 (they were still there way after 6pm) and a couple of photos of some of the EPS waiting to be positioned.
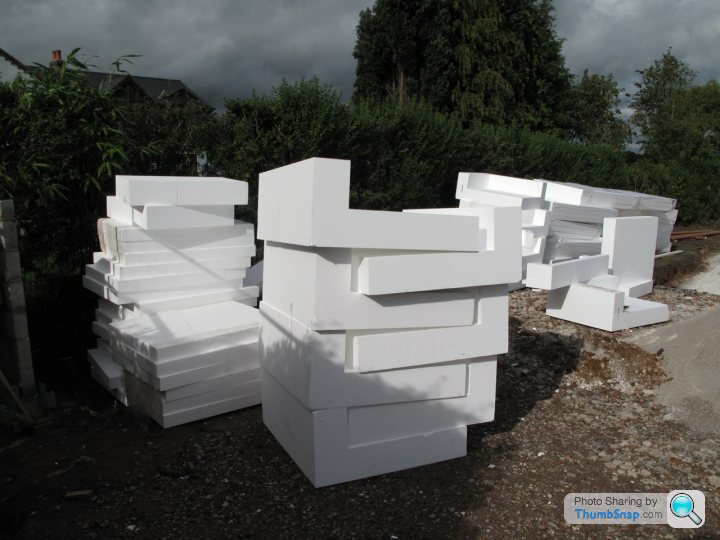
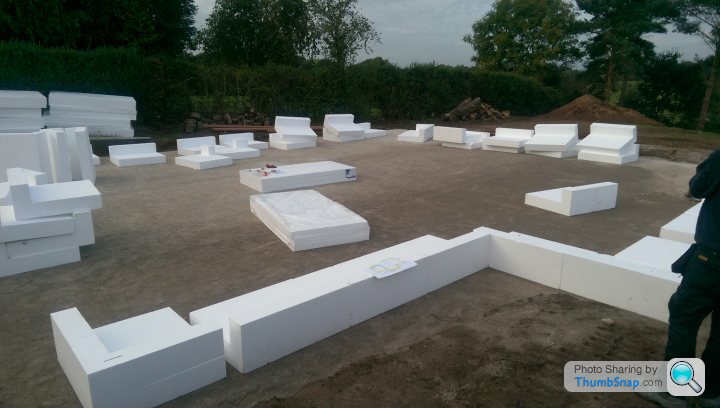
https://selfbuildnoviceblog.wordpress.com
Due to traffic issues on the way over to site on the first day the guys that are doing the slab were delayed by an hour or so, so we had our own little Operation Stack. First one in was a delivery of ‘dust’ – blinding material on top of which the insulation will sit. The driver (a really nice guy) was pretty patient waiting for them to turn up but in the end I just told him to dump it – just not in the hole!
The second lorry was waiting to deliver the insulation itself. I think this driver was quite happy to wait though and jumped straight back in his cab to brew up!
So, the first day was spent getting this ‘dust’ levelled on the slab to a thickness of 50mm. It was pretty slow going (2 guys) but they were very thorough. You can just about see a couple of the battens laid on the slab that they used to help set the levels (with the help of a theodolite). Due to the late start they were off site about 6:30-7:00pm and I think they would have stayed later if it hadn’t started to go dark.

Two of the key features of the build are it’s high levels of insulation and its air-tightness. To put the level of air-tightness into perspective let’s compare it to standard UK Building Regulations.
Part L1A of the ‘regs’ state that any new dwellings are tested for air tightness by using a method known as a ‘blower door test’ in accordance with BS EN 13829. The measurement is taken by blowing air into the house via a particular door that is mounted in the main entrance. Part L1A requires an air tightness of maximum 10 m3/hr/m2 air loss at a pressure of 50 Pa. Standard good practice for air tightness testing in the UK is a maximum of 7 m3/hr/m2.
We are building to Passiv standards and the measure they use is in air changes per hour (ACH). A house built to Passiv standards requires no more than 0.6ACH and that’s what we are aiming for.
There isn’t really a direct way to convert from m3/hr/m2 to ACH as it depends on volume and floor area, but a reasonable finger-in-the-air would be to say that Part L1A is looking for around 7-10ACH. That’s like leaving a door wide open!
So next time your builder says he’s building to the regs, go and find another builder. Or more fairly, another build method.
Every time you put a hole in the structure you compromise its air-tightness. Water, electricity, gas, phone etc. all need to get into the house so how best to do this? Aside from the gas which must go straight in (though the wall) everything else can and will come up through the slab in ducts. The ducts still need sealing and insulating, but that’s a relatively trivial job.
What isn’t trivial though is working out where you want everything to come through the slab and then actually doing it. Accurately. Hence the chat to confirm everything. We’ve changed a few things from my original ideas (“I spent bloody ages working all that out, I’m not changing it now!”) but I’m going with advice based on past experience. Obviously I’m assuming that experience is Good Experience and not repeated carnage, but I’ll be honest and say I daren’t ask! Sometimes it’s good (not) to talk.
Day 2 saw the start of the insulation going down and the first cock-up.
The surveyor had previously set-out the slab perimeter with steel pins but it seems these had been interpreted as something the groundworkers had left in (for a laugh?). I’m not quite sure how you could possibly jump to that conclusion but anyway, they were largely ignored, moved or squashed. Fortunately, 3 were still in-tact so rather than just playing dot-to-dot with a bit of Extruded Polystyrene (EPS) it looks like they’ve got a lot more work to do to ensure it’s all in the right position. I know it’ll be right in the end, but it is more than a bit annoying.
Anyway, end of my day 2 (they were still there way after 6pm) and a couple of photos of some of the EPS waiting to be positioned.
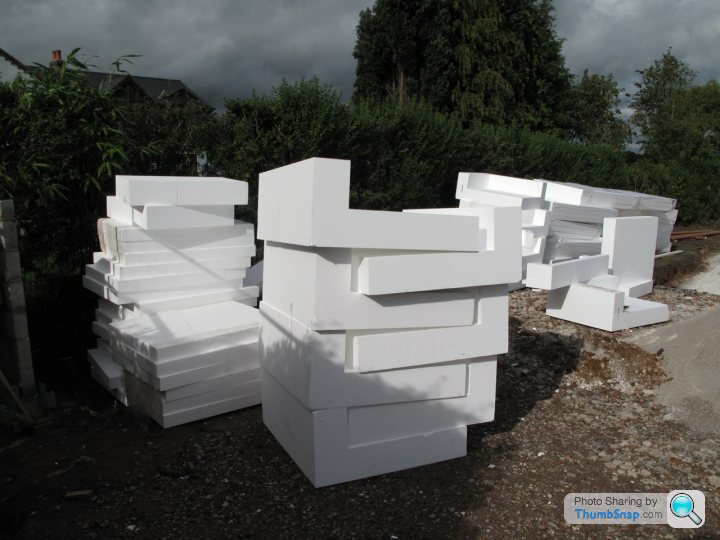
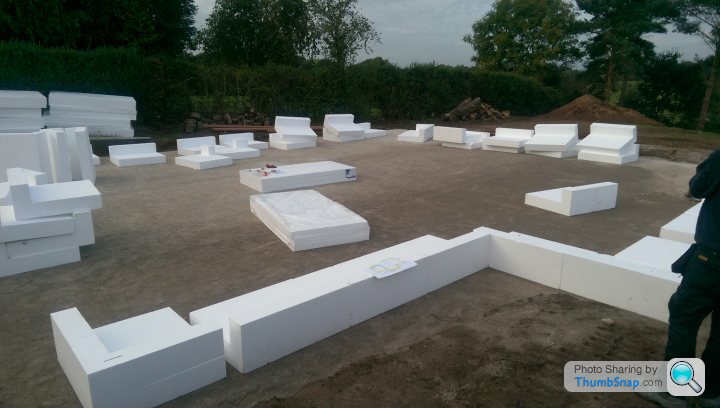
Edited by worldwidewebs on Tuesday 27th September 21:17
Another update to https://selfbuildnoviceblog.wordpress.com
Well, by now I was expecting to be able to say the slab was finished and the timber frame was just starting to go up. No prizes for guessing that’s not what’s happened.
I don't want to copy/paste the entire blog but here are a few photos to whet the appetite...
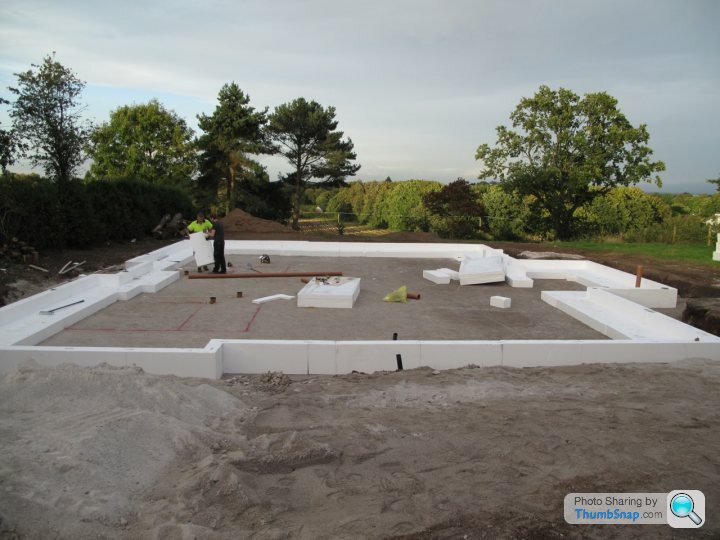
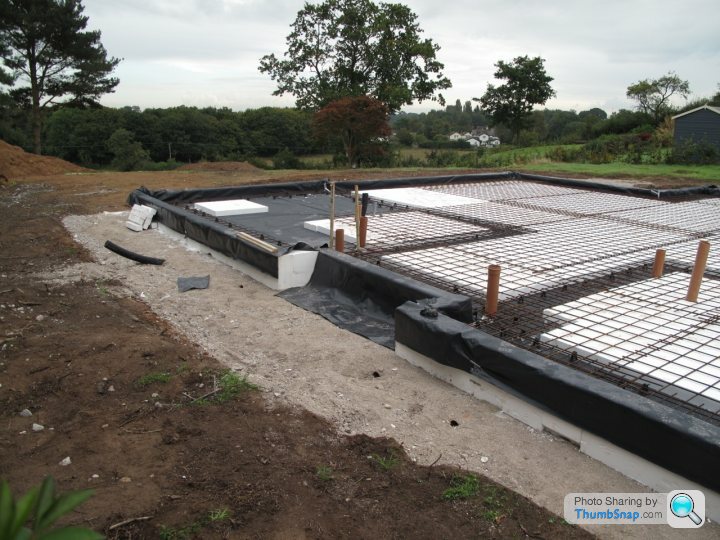


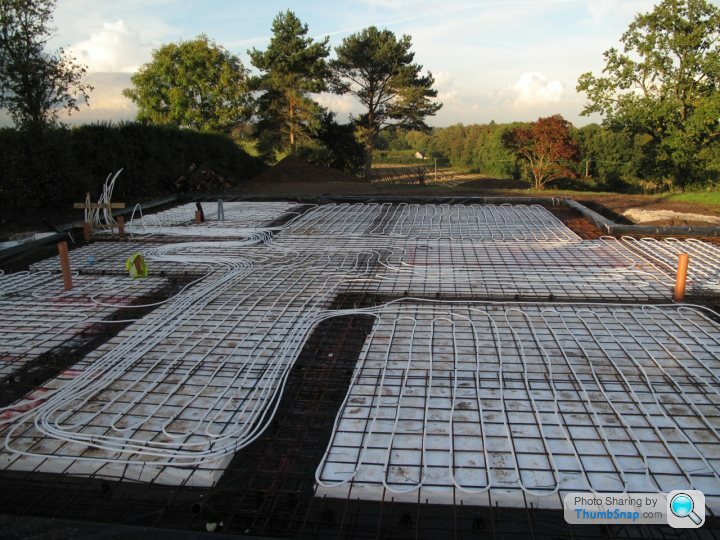
Well, by now I was expecting to be able to say the slab was finished and the timber frame was just starting to go up. No prizes for guessing that’s not what’s happened.
I don't want to copy/paste the entire blog but here are a few photos to whet the appetite...
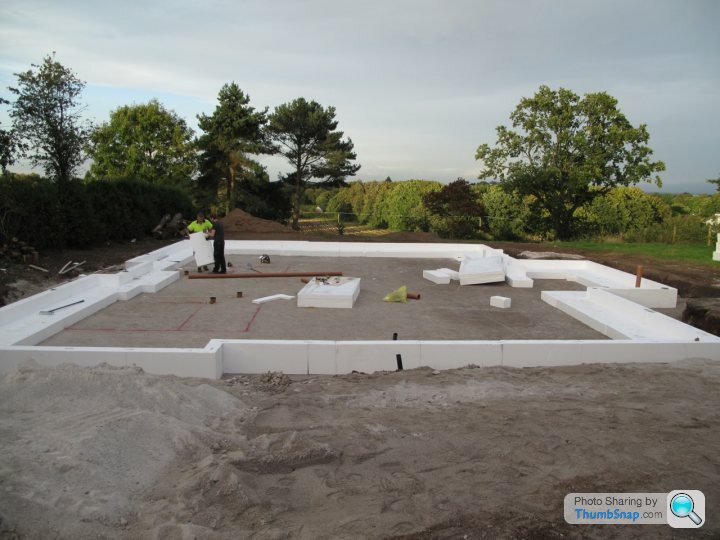
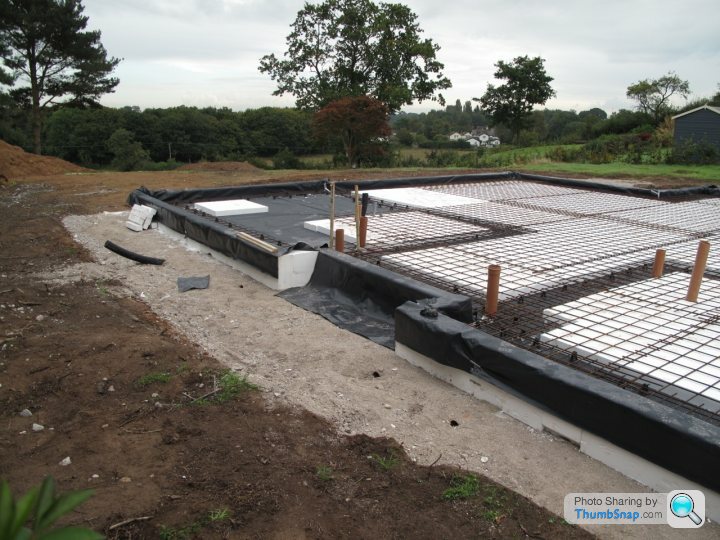


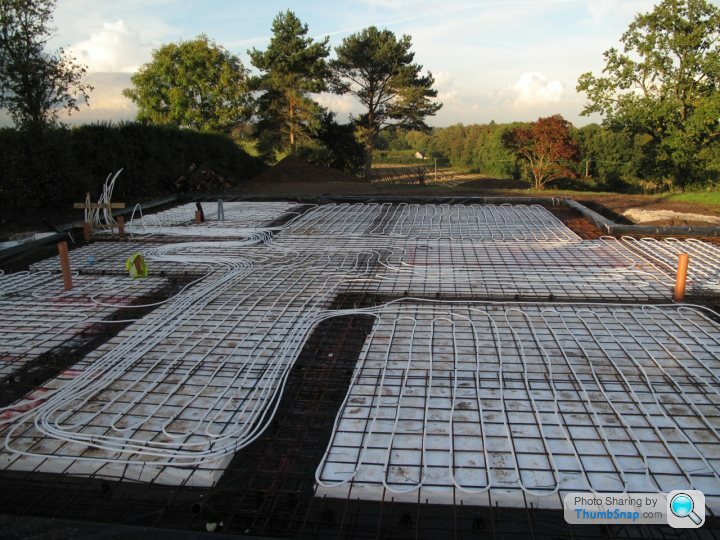
dxg said:
Has your builder done air-tightness before?
Yes, many and just one of the reasons I went with them. Actually, the timber frame company are responsible for all this, including the air tightness test itself and one of the last payments to them is actually dependent on the test passing an agreed level of air-tightness. dxg said:
Has your builder done air-tightness before?
I make these points from watching the performance of an unnamed development of "airtight" houses go badly wrong because none of the subbies cared enough to look at any drawings, let alone change the way they'd done the work on all the past jobs...
Yes, they're fair and valid points. I've tried to be as careful as I can be in choosing my trades (some I've used previously, some recommended) but I know there is going to be a level of law-laying that will be going onI make these points from watching the performance of an unnamed development of "airtight" houses go badly wrong because none of the subbies cared enough to look at any drawings, let alone change the way they'd done the work on all the past jobs...
souper said:
Great build.
Will the underfloor pipes be held under pressure when the concretes poured, I'm halfway through laying a 4 manifold system and have the pipes fully pressurized with water to approx 6bar and it stays like that for at least 21 days while the screed cures and any heat can be introduced to the system.
No, I don't think so - none are connected to anything at the momentWill the underfloor pipes be held under pressure when the concretes poured, I'm halfway through laying a 4 manifold system and have the pipes fully pressurized with water to approx 6bar and it stays like that for at least 21 days while the screed cures and any heat can be introduced to the system.
The slab is done. Finally.
The day started overcast but not too bad and when I turned up on site at about 6pm the concrete had been poured and the panning to level the slab had commenced. Then the first few drops of rain came down and it started to go dark. Then it REALLY started to rain. The weather apps showed clear skies. My mind drifted back to Michael Fish and 1987 and we went to the pub.
Brendan was back on site at 3am (yes, really!) to do what he could with it. As a client we were fortunate on 3 levels: he was prepared to come out then to ensure it was all ok; one set of neighbours were on holiday; the other set of neighbours were beyond understanding and didn’t complain (they were asked prior to it though).
The rain significantly slowed the concrete going ‘off’ and it was almost 3pm on Friday before Brendan had finished. The slab perhaps doesn’t have as good a finish as it might, but it is flat and level (or as good as needs to be)
There are a couple of issues that need to be resolved, 1 more significant than the other, but both will be resolved in the next few weeks.
In two weeks time the timber frame erection will start
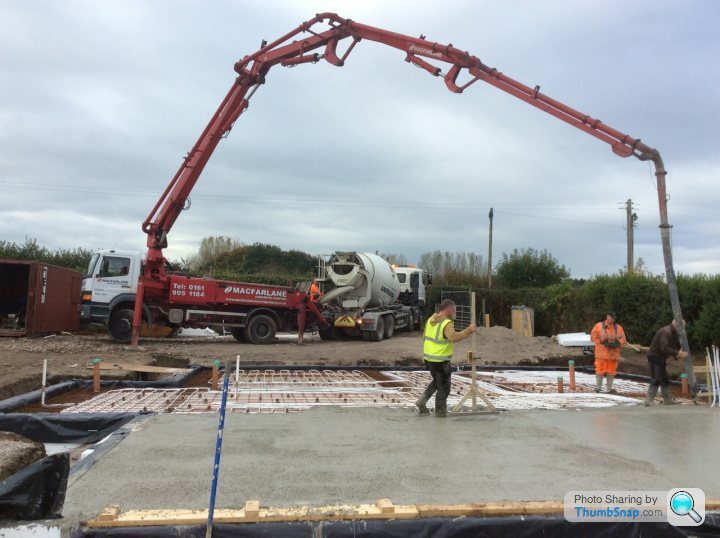
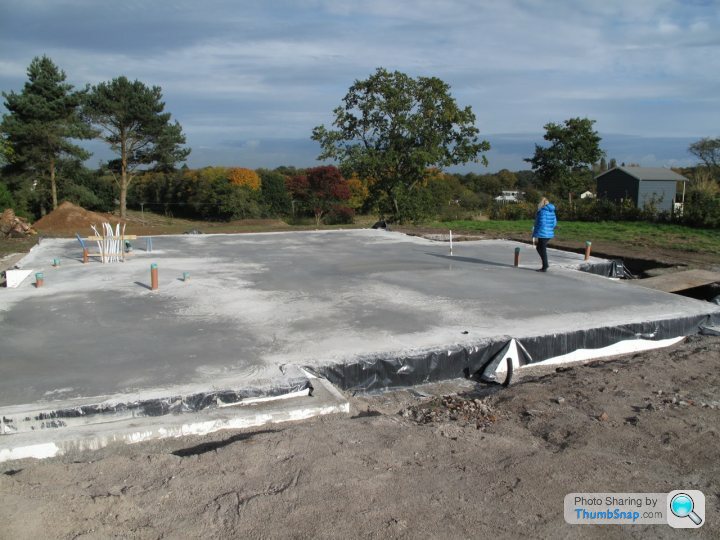
There's a bit more detail and photos on the blog: https://selfbuildnoviceblog.wordpress.com
The day started overcast but not too bad and when I turned up on site at about 6pm the concrete had been poured and the panning to level the slab had commenced. Then the first few drops of rain came down and it started to go dark. Then it REALLY started to rain. The weather apps showed clear skies. My mind drifted back to Michael Fish and 1987 and we went to the pub.
Brendan was back on site at 3am (yes, really!) to do what he could with it. As a client we were fortunate on 3 levels: he was prepared to come out then to ensure it was all ok; one set of neighbours were on holiday; the other set of neighbours were beyond understanding and didn’t complain (they were asked prior to it though).
The rain significantly slowed the concrete going ‘off’ and it was almost 3pm on Friday before Brendan had finished. The slab perhaps doesn’t have as good a finish as it might, but it is flat and level (or as good as needs to be)
There are a couple of issues that need to be resolved, 1 more significant than the other, but both will be resolved in the next few weeks.
In two weeks time the timber frame erection will start

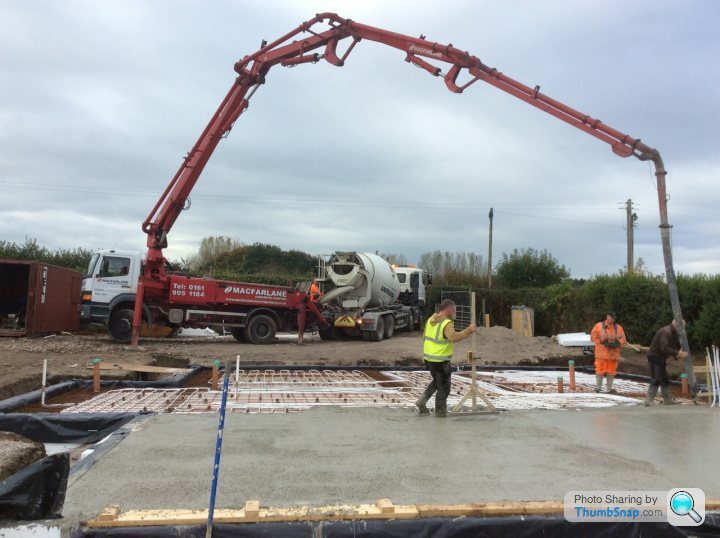
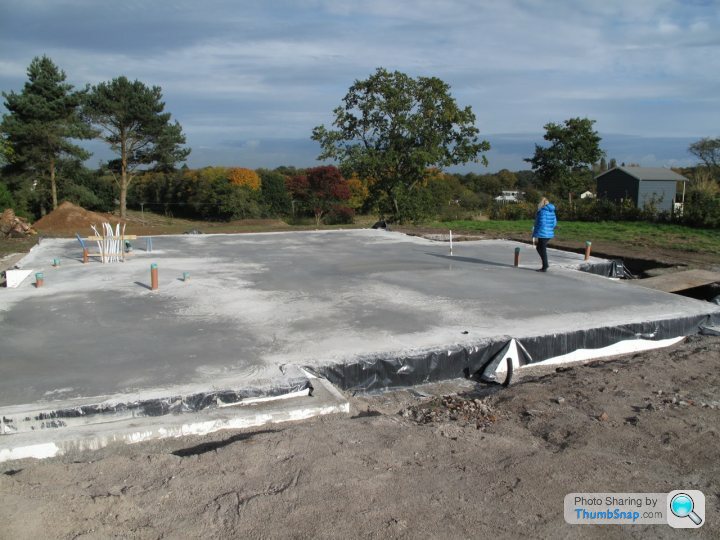
There's a bit more detail and photos on the blog: https://selfbuildnoviceblog.wordpress.com
It's been a while but the timber frame is starting to go up
https://selfbuildnoviceblog.wordpress.com
It's starting to feel quite exciting now, despite me only really seeing progress when it's dark due to the short days.
|http://thumbsnap.com/7vB4PrWS[/url]
|http://thumbsnap.com/XcuLTAZ5[/url]
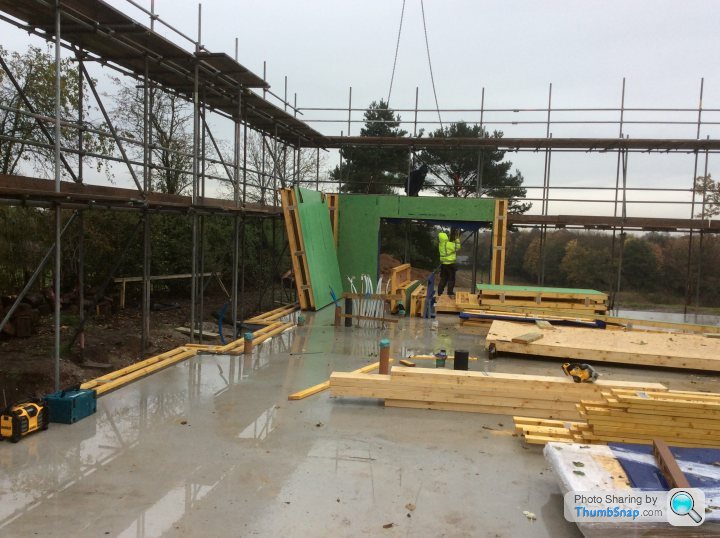
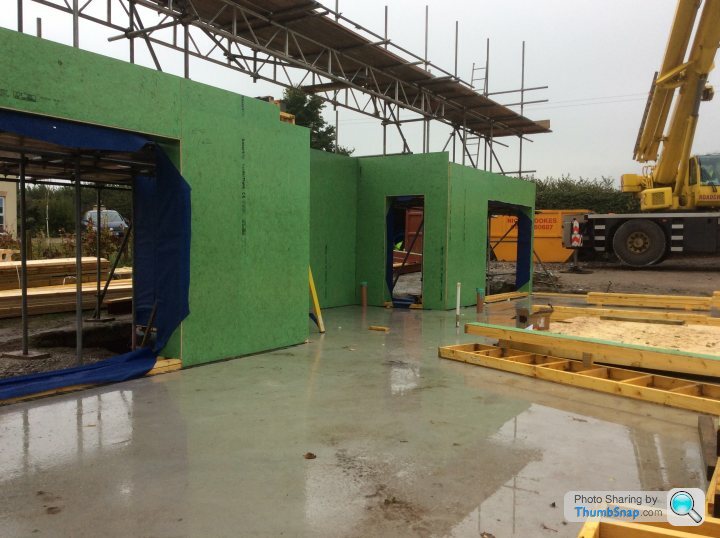
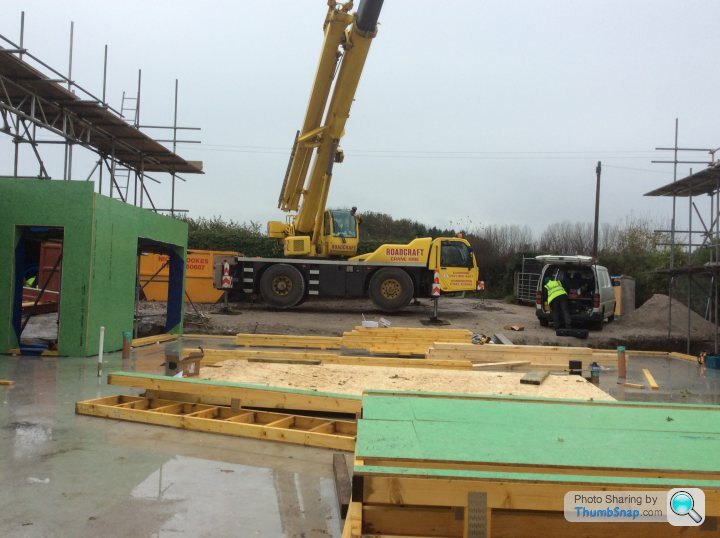
[url][url]
https://selfbuildnoviceblog.wordpress.com
It's starting to feel quite exciting now, despite me only really seeing progress when it's dark due to the short days.
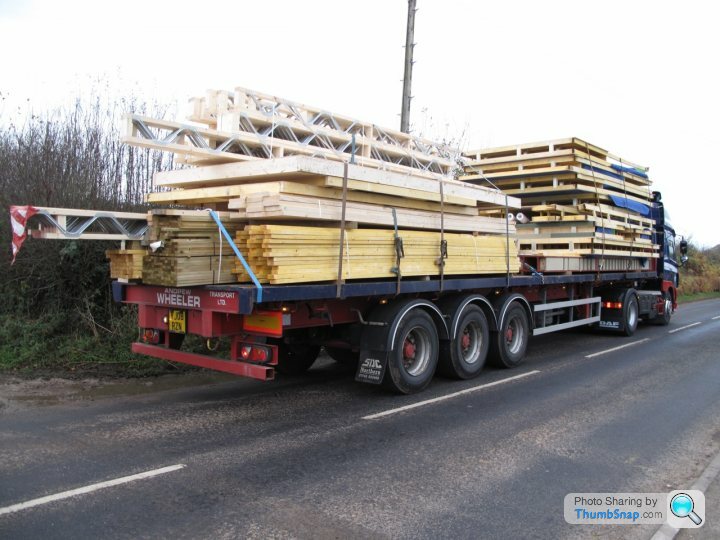

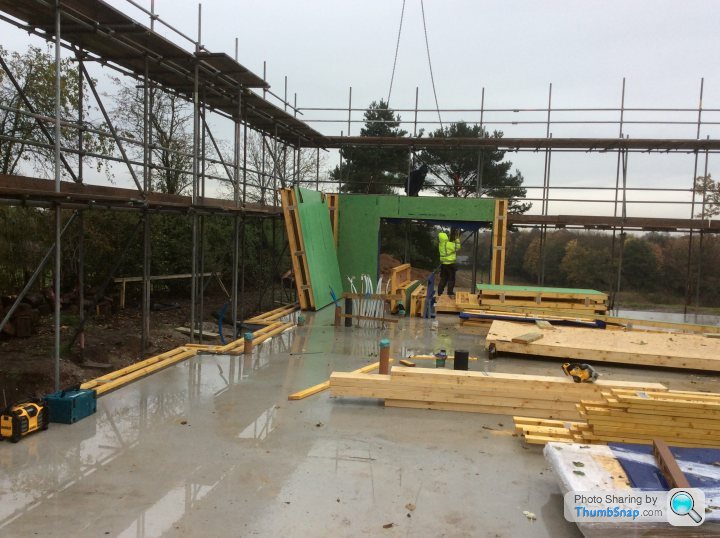
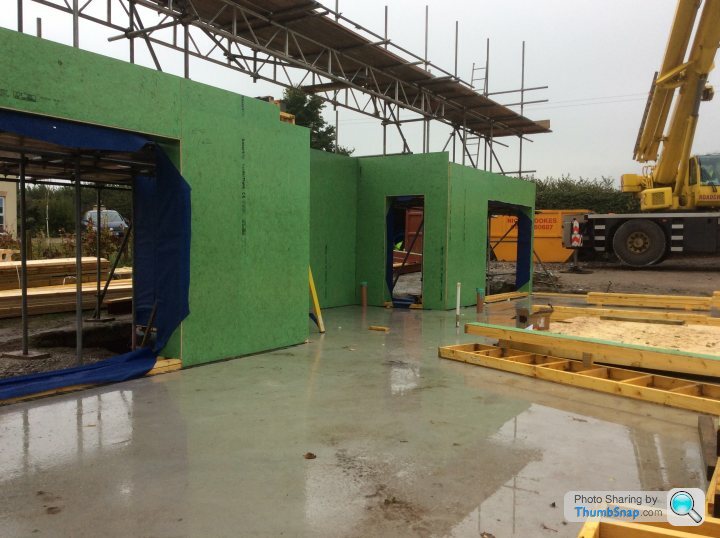
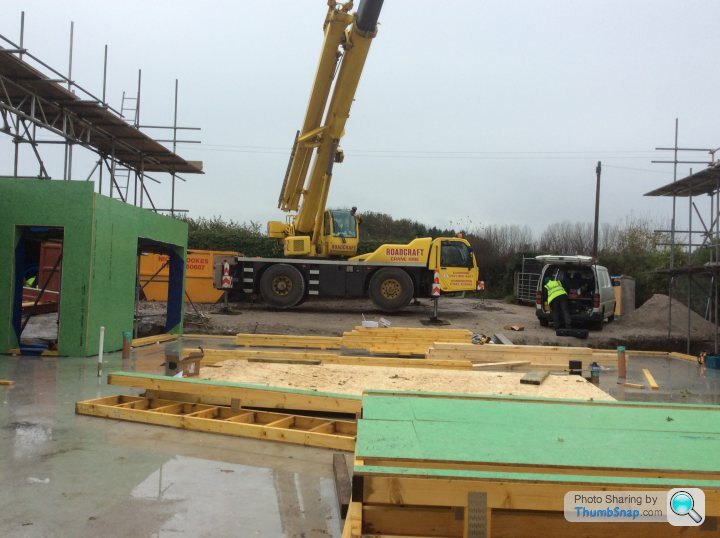
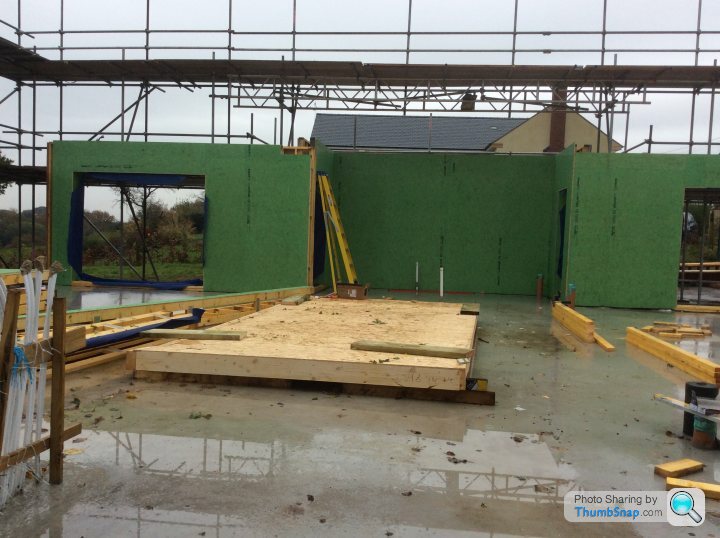
Gassing Station | Homes, Gardens and DIY | Top of Page | What's New | My Stuff