Torquing through a spanner
Discussion
I was trying to undo a tricky intake manifold bolt at the weekend so I could change the intake gaskets. However the shape of the intake meant getting a tool onto one of the bolts was almost impossible. Eventually I found a suitable, thin-walled box spanner that could just make contact with the bolt.
The problem comes with trying to find a way to correctly torque up the bolts when I remount the intake - I can't get a socket onto the bolt, so I can't simply torque up the bolt with my torque wrench. I could use the spanner and do it by guesswork, but I'm trying to cure an intake leak as it is, so I'd rather do it properly!
Is it possible to user the torque wrench on the end of the spanner? i.e. put one end of the spanner over the bolt, then use a hex socket in the other end and use my torque wrench to torque the bolt through the spanner? Would this be accurate or would the extra leverage of the spanner make the torque applied to the bolt incorrect?
Cheers for any words of wisdom and apologies for waffling!
The problem comes with trying to find a way to correctly torque up the bolts when I remount the intake - I can't get a socket onto the bolt, so I can't simply torque up the bolt with my torque wrench. I could use the spanner and do it by guesswork, but I'm trying to cure an intake leak as it is, so I'd rather do it properly!
Is it possible to user the torque wrench on the end of the spanner? i.e. put one end of the spanner over the bolt, then use a hex socket in the other end and use my torque wrench to torque the bolt through the spanner? Would this be accurate or would the extra leverage of the spanner make the torque applied to the bolt incorrect?
Cheers for any words of wisdom and apologies for waffling!
http://www.engineersedge.com/manufacturing_spec/to...
I'd just torque the rest up correctly and nip up the last one using your judgement personally! But it is possible to calculate....
I'd just torque the rest up correctly and nip up the last one using your judgement personally! But it is possible to calculate....
DuraAce said:
http://www.engineersedge.com/manufacturing_spec/to...
I'd just torque the rest up correctly and nip up the last one using your judgement personally! But it is possible to calculate....
Top work! That equation'll do the job nicely!I'd just torque the rest up correctly and nip up the last one using your judgement personally! But it is possible to calculate....
Yes, at a push I think I'd probably 'feel' the torque on another bolt with the same spanner and then pull the same amount on the awkward bolt. But it's good to know I've got a method for KNOWING I've got the right torque.
Cheers fellas!
Finally got round to getting those bolts torqued up last weekend. Process went very smoothly:
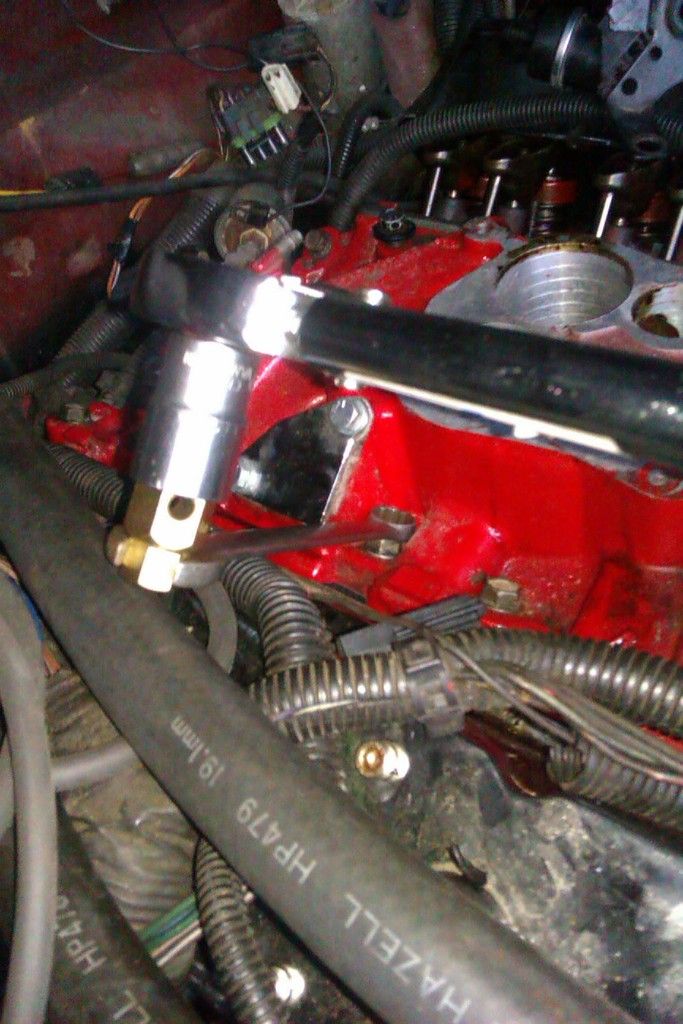
I used a Clarke torque wrench, a snap-on 9/16th box spanner (the only spanner with thin enough walls!), a 14mm drainage plug and a 19mm 1/2" drive socket. Quite a handful!
Calculation: (T x L) / (L + E) = Y
T= specified torque
L= length of wrench
E= length of spanner
Y= required torque
(40Nm x 0.4m) / (0.4m + 0.185mm) = 27.35
Wrench only went down to 28, not ideal as the torque wasn't in the mid-range of the wrench, but it went well. After manhandling the sockets for the four inaccessible bolts with the wrench set to 28Nm, I used the wrench directly at the other four bolts set at 40Nm. After completely torquing all the bolts down, I went back to one of the accessible bolts torqued directly with the wrench and checked the wrench + spanner method with the reduced torque. The bolt took slightly more torque (perhaps a 16th of a turn) before the wrench clicked, which proved the calculation got the torque pretty damn close to what it was supposed to be.
I'd call that success. Thanks for the help everyone - hopefully anyone who's in this position might find this thread and can benefit!
Oh, and this myth is properly dispelled. Always calculate your torque. Holding the wrench at 90 degrees will make no difference to holding it straight and will still result in a higher torque at the bolt.
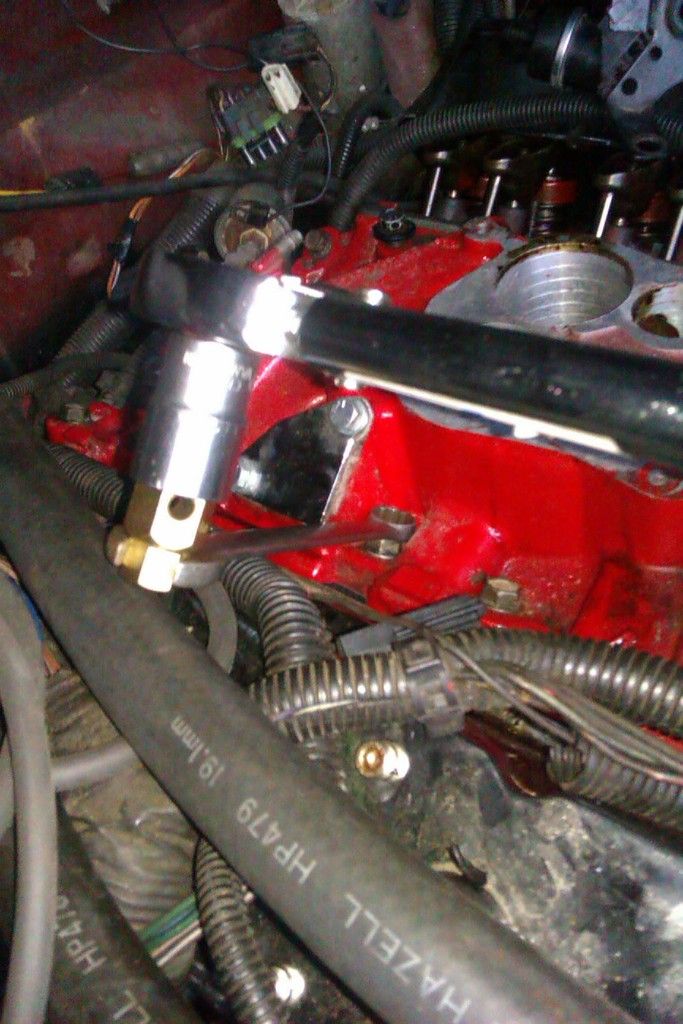
I used a Clarke torque wrench, a snap-on 9/16th box spanner (the only spanner with thin enough walls!), a 14mm drainage plug and a 19mm 1/2" drive socket. Quite a handful!
Calculation: (T x L) / (L + E) = Y
T= specified torque
L= length of wrench
E= length of spanner
Y= required torque
(40Nm x 0.4m) / (0.4m + 0.185mm) = 27.35
Wrench only went down to 28, not ideal as the torque wasn't in the mid-range of the wrench, but it went well. After manhandling the sockets for the four inaccessible bolts with the wrench set to 28Nm, I used the wrench directly at the other four bolts set at 40Nm. After completely torquing all the bolts down, I went back to one of the accessible bolts torqued directly with the wrench and checked the wrench + spanner method with the reduced torque. The bolt took slightly more torque (perhaps a 16th of a turn) before the wrench clicked, which proved the calculation got the torque pretty damn close to what it was supposed to be.
I'd call that success. Thanks for the help everyone - hopefully anyone who's in this position might find this thread and can benefit!
mickrick said:
Blaster72 said:
If the handle of the torque wrench is kept at 90 degrees to the spanner then the reading will be accurate.
This.NDNDNDND said:
Oh, and this myth is properly dispelled. Always calculate your torque. Holding the wrench at 90 degrees will make no difference to holding it straight and will still result in a higher torque at the bolt.
Glad you got what you needed but your last statement isn't correct.You say holding the wrench at 90 degrees will make no difference, that isn't correct.
It's not a myth its a standard practice used for years.
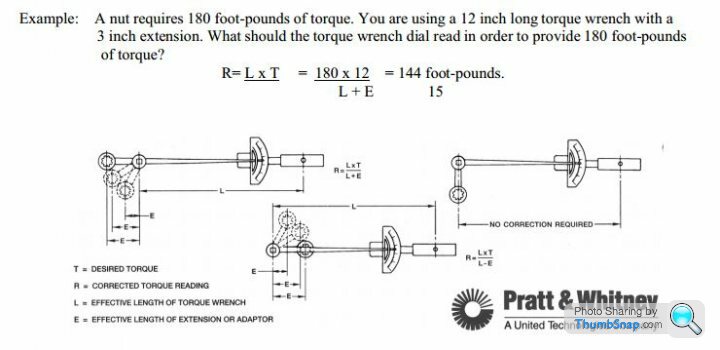
Edited by Blaster72 on Tuesday 3rd November 15:33
Glad you're sorted!
There are other styles of torquing tool, other than the 'adjustable', which may be easier to use in a tight spot.
The beam type has much smaller head, you can get adjustables that come with a set of open-ended spanner tips.
Bike shops sell a style of beam wrench that works more like a torque screwdriver, but only for low, less than 10ft-lbs. Proper torque screwdrivers tend to read only inch-lbs!
John
There are other styles of torquing tool, other than the 'adjustable', which may be easier to use in a tight spot.
The beam type has much smaller head, you can get adjustables that come with a set of open-ended spanner tips.
Bike shops sell a style of beam wrench that works more like a torque screwdriver, but only for low, less than 10ft-lbs. Proper torque screwdrivers tend to read only inch-lbs!
John
Gassing Station | Home Mechanics | Top of Page | What's New | My Stuff