EVAP Purge strategy
Discussion
Gernerally speaking it will operate when:
Engine is running
Manifold pressure is below atmospheric (vacuum)
Engine coolant is warm enough (>70degC)
Engine air temperature is not excessively hot or cold
Closed loop fuelling is runing (hot lambda sensors)
Fuel tank leak detection diagnostic has not reported a fuel system leak
The valves pulsewidth will be inversely proportional to intake manifold pressure, as it needs to limit purge vapour fuel contribution to within the closed loop fuel control range
generally speaking, drive a car to warm it up fully, idle engine, purge valve should be operating at that point assuming entry conditions are met.
Engine is running
Manifold pressure is below atmospheric (vacuum)
Engine coolant is warm enough (>70degC)
Engine air temperature is not excessively hot or cold
Closed loop fuelling is runing (hot lambda sensors)
Fuel tank leak detection diagnostic has not reported a fuel system leak
The valves pulsewidth will be inversely proportional to intake manifold pressure, as it needs to limit purge vapour fuel contribution to within the closed loop fuel control range
generally speaking, drive a car to warm it up fully, idle engine, purge valve should be operating at that point assuming entry conditions are met.
Thanks for the response. The reason I asked is not for checking functionality, but to program my ECU (M800) to control it. I know that I could just disconnect it and vent the fumes to air, but I want to keep it if I can.
Edited to add that this is a 1990 BMW M3, not something modern! The valve appears to be a simple solenoid device, but I can fit a valve from a newer model easy enough.
Cheers
Steve
Edited to add that this is a 1990 BMW M3, not something modern! The valve appears to be a simple solenoid device, but I can fit a valve from a newer model easy enough.
Cheers
Steve
Edited by stevesingo on Thursday 20th January 09:09
Oh ok, in that case:
To prevent raw hydrocarbon emissions from a cars fuel tank leaking directly into the atmosphere, (and ruining the carefully mandated emissions limits) the fuel system incorporates a Carbon canister mounted near to the fuel tank. The tank is fully sealed, so any hydrocarbon vapours that are present in the tank (depending upon fuel quantity and vapour pressure /temperature) are forced to travel into the carbon canister, where the activated charcoal catches those hydrocarbon vapours.
The can is then "purged" during engine running by the use of the intake manifold vaccum, which is applied, via the purge solenoid, to the canister. A passive pressure relef valve allows freash air into the carbon can, which carries the hydrocarbon vapours into the intake manifold, where they are burnt by the engine, and effectively then pass through the normal emissions control devices (catalyst etc) i this way raw hydrocarbon emissions are reduced.
The hydocarbon vapour concentration in the purge air varries massively:
after a short soak (engine off) on a cold day with a full fuel tank, hardly any vapour pressure wille exist to drive the HC vapours into the canister, and hence the majority of the purge flow will be air
after a long soak, in a hot climate, with a low fuel level, large quanities of HC's will have been caught by the carbon canister. When the purge valve is opened, a very high concentration of the purgw flow will be HC vapour.
For a production enigne where very close control on engine air/fuel ratio is crictical to catalyst performance and hence exhaust emissions, the purge valve duty is controlled to keep the purge hc vapour massflow low enough to maintain accurate closed loop lambda control. (where the lambda trim feedback allows you to calc the HC vapour concentration.
On a DIY basis you can calibrate a much more crude system, one that simply drives the valve inversely proportional to MAP, to try to limit the total purge flow at high manifold depressions. If you have closed loop lambda enabled, you will be able to see the "rich shift" when you enable the purge valve, and you could use this to get a rough idea of a sensible flow rate.
You will really only want any flow once the engine is warm (to prevent excesively rich warm up's where lambda control is not yet operational), but without proper control strategy your AFR's will vary significantly with actual canister loadings. As soon as the load increases to the point where insufficient manifold vaccuum is generated, you want to turn off all purge flow.
Off the top of my head, a valve pwm % vs rpm and MAP:
To prevent raw hydrocarbon emissions from a cars fuel tank leaking directly into the atmosphere, (and ruining the carefully mandated emissions limits) the fuel system incorporates a Carbon canister mounted near to the fuel tank. The tank is fully sealed, so any hydrocarbon vapours that are present in the tank (depending upon fuel quantity and vapour pressure /temperature) are forced to travel into the carbon canister, where the activated charcoal catches those hydrocarbon vapours.
The can is then "purged" during engine running by the use of the intake manifold vaccum, which is applied, via the purge solenoid, to the canister. A passive pressure relef valve allows freash air into the carbon can, which carries the hydrocarbon vapours into the intake manifold, where they are burnt by the engine, and effectively then pass through the normal emissions control devices (catalyst etc) i this way raw hydrocarbon emissions are reduced.
The hydocarbon vapour concentration in the purge air varries massively:
after a short soak (engine off) on a cold day with a full fuel tank, hardly any vapour pressure wille exist to drive the HC vapours into the canister, and hence the majority of the purge flow will be air
after a long soak, in a hot climate, with a low fuel level, large quanities of HC's will have been caught by the carbon canister. When the purge valve is opened, a very high concentration of the purgw flow will be HC vapour.
For a production enigne where very close control on engine air/fuel ratio is crictical to catalyst performance and hence exhaust emissions, the purge valve duty is controlled to keep the purge hc vapour massflow low enough to maintain accurate closed loop lambda control. (where the lambda trim feedback allows you to calc the HC vapour concentration.
On a DIY basis you can calibrate a much more crude system, one that simply drives the valve inversely proportional to MAP, to try to limit the total purge flow at high manifold depressions. If you have closed loop lambda enabled, you will be able to see the "rich shift" when you enable the purge valve, and you could use this to get a rough idea of a sensible flow rate.
You will really only want any flow once the engine is warm (to prevent excesively rich warm up's where lambda control is not yet operational), but without proper control strategy your AFR's will vary significantly with actual canister loadings. As soon as the load increases to the point where insufficient manifold vaccuum is generated, you want to turn off all purge flow.
Off the top of my head, a valve pwm % vs rpm and MAP:
MAP(kPa abs) |
---|
100 | 0 | 0 | 0 | 0 | 0 |
---|---|---|---|---|---|
80 | 0 | 80 | 80 | 65 | 0 |
60 | 0 | 65 | 65 | 45 | 0 |
40 | 0 | 35 | 35 | 20 | 0 |
20 | 0 | 10 | 10 | 0 | 0 |
0 | 0 | 0 | 0 | 0 | 0 |
500 | 2000 | 3000 | 5000 | 7000 |
Engine speed (rpm) |
---|
Edited by anonymous-user on Thursday 20th January 17:37
Hi chaps,
I've had an intermittent rough idle when warm(more of a flutter really) feels like a vacuum leak. Whenever it occurs a "lambda operating system rich or lean" code is generated.
I can't find anything wrong with the vacuum system, all pipes and connections secure and tight.
I took the purge valve off and with a bit of sucking and blowing I can get air through it. Seems intermittent though, sometimes it holds a vacuum sometimes not. If I connect up 12v DC to it, it snaps open smartly, disconnect power and it stays open for a minute or two, slowly closing. Even when closed I can suck/blow and it won't hold a vacuum.
Anyhoo, I blocked the pipe to the charcoal canister and the vacuum pipe to the inlet manifold. The idle seems to be about perfect, however due to the intermittent nature of the fault I'm not declaring success yet.
Will it do any harm leaving the pipes blocked for a bit to see if it's fixed the problem?
I've had an intermittent rough idle when warm(more of a flutter really) feels like a vacuum leak. Whenever it occurs a "lambda operating system rich or lean" code is generated.
I can't find anything wrong with the vacuum system, all pipes and connections secure and tight.
I took the purge valve off and with a bit of sucking and blowing I can get air through it. Seems intermittent though, sometimes it holds a vacuum sometimes not. If I connect up 12v DC to it, it snaps open smartly, disconnect power and it stays open for a minute or two, slowly closing. Even when closed I can suck/blow and it won't hold a vacuum.
Anyhoo, I blocked the pipe to the charcoal canister and the vacuum pipe to the inlet manifold. The idle seems to be about perfect, however due to the intermittent nature of the fault I'm not declaring success yet.
Will it do any harm leaving the pipes blocked for a bit to see if it's fixed the problem?
I'd just like to thank Max Torque for the detailed posts. You should write a book.
I'm considering setting up EVAP on my standalone. It's not something commonly done, most seem to just vent to atmosphere. I'm all plumbed in and have a spare output on the ECU but not sure which way to go. Is it more hassle than it's worth? Steve, did you end up running the EVAP on your Motec?
I'm considering setting up EVAP on my standalone. It's not something commonly done, most seem to just vent to atmosphere. I'm all plumbed in and have a spare output on the ECU but not sure which way to go. Is it more hassle than it's worth? Steve, did you end up running the EVAP on your Motec?
Because of the long length and small size of the evap lines, generally there is insufficient pre-compressor depression to pull any meaningful flow from the can in that way. It also does bring a small risk of an intercooler explosion in the case of engine backfire (very small, because the purge low is very unlikely to be rich enough to get the entire intake to a rich enough ignition stochiometry)
For a road driven car, which is going to spend the vast majority of it's time off boost, a purge line to the plenum, via the control valve and a passive one way valve to prevent boost pressure feeding back down to the can is sufficient. You want to avoid high valve openings at low loads and engine speeds to prevent excessive lambda excursions, and try to flow the most in the mid range, where you tend to cruise at light load.
In the UK, where it's mostly cold, purge can loadings will be relatively small if the car is used regularly, so the exact valve proportioning is unlikely to be an issue.
For a road driven car, which is going to spend the vast majority of it's time off boost, a purge line to the plenum, via the control valve and a passive one way valve to prevent boost pressure feeding back down to the can is sufficient. You want to avoid high valve openings at low loads and engine speeds to prevent excessive lambda excursions, and try to flow the most in the mid range, where you tend to cruise at light load.
In the UK, where it's mostly cold, purge can loadings will be relatively small if the car is used regularly, so the exact valve proportioning is unlikely to be an issue.
Max_Torque said:
Because of the long length and small size of the evap lines, generally there is insufficient pre-compressor depression to pull any meaningful flow from the can in that way. It also does bring a small risk of an intercooler explosion in the case of engine backfire (very small, because the purge low is very unlikely to be rich enough to get the entire intake to a rich enough ignition stochiometry)
For a road driven car, which is going to spend the vast majority of it's time off boost, a purge line to the plenum, via the control valve and a passive one way valve to prevent boost pressure feeding back down to the can is sufficient. You want to avoid high valve openings at low loads and engine speeds to prevent excessive lambda excursions, and try to flow the most in the mid range, where you tend to cruise at light load.
In the UK, where it's mostly cold, purge can loadings will be relatively small if the car is used regularly, so the exact valve proportioning is unlikely to be an issue.
Thanks for your answers on this topic. Please can you have a look at the photo of my ECU settings to see if I've understood you correctly? How would I find the frequency to set for the PWM output? The car is a 2006 MINI R53For a road driven car, which is going to spend the vast majority of it's time off boost, a purge line to the plenum, via the control valve and a passive one way valve to prevent boost pressure feeding back down to the can is sufficient. You want to avoid high valve openings at low loads and engine speeds to prevent excessive lambda excursions, and try to flow the most in the mid range, where you tend to cruise at light load.
In the UK, where it's mostly cold, purge can loadings will be relatively small if the car is used regularly, so the exact valve proportioning is unlikely to be an issue.
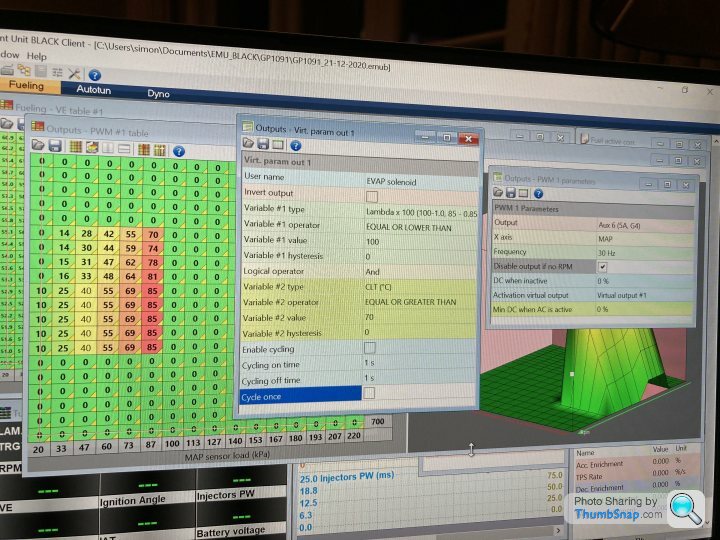
Gassing Station | Engines & Drivetrain | Top of Page | What's New | My Stuff