Finishing turned wood
Discussion
I amused myself yesterday making a couple of tealight holders. So far I've sanded them with medium and fine paper (whilst spinning) and burnished with wood shavings, but they need a nice durable finish. The wood is staved cherry from some leftover kitchen worktop. What would give the best finish from Ronseal/varnish or furniture wax? (I presume the best results would be achieved using a rag back on the lathe)
OSMO will give a good finish and good protection to any bare wood.
I've used this stuff with great success.
http://www.osmouk.com/sitechapter.cfm?chapter=82&a...
I've used this stuff with great success.
http://www.osmouk.com/sitechapter.cfm?chapter=82&a...
Simpo Two said:
minivanman said:
I give it a couple of coats of sanding sealer on the lathe then micro crystalline wax. Gives a durable gloss finish.
Do you find sanding necessary before the wax?A few pics of the stuff my Dad used to make:
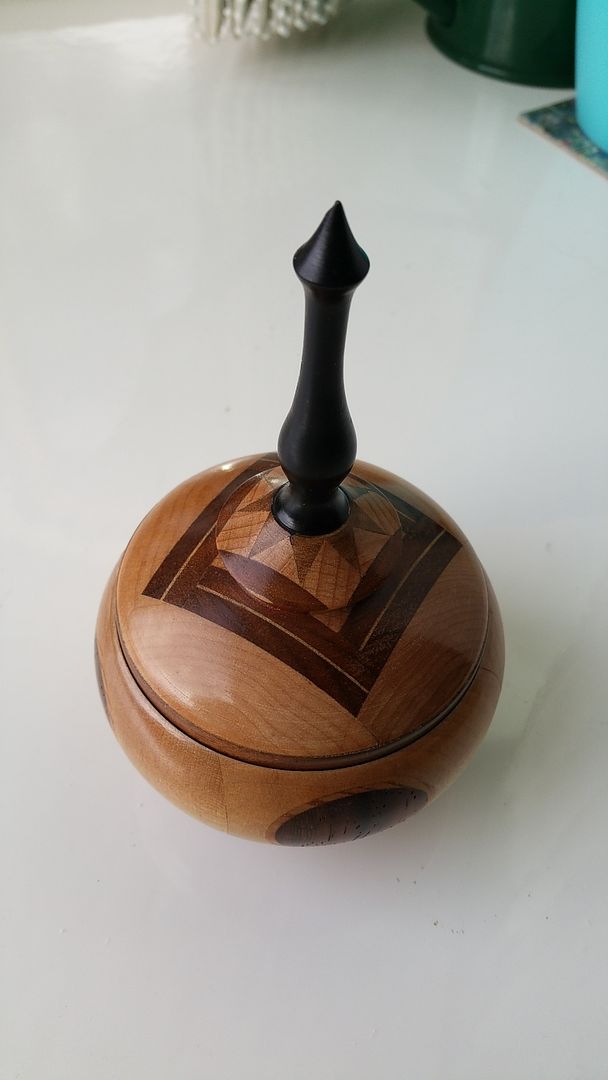
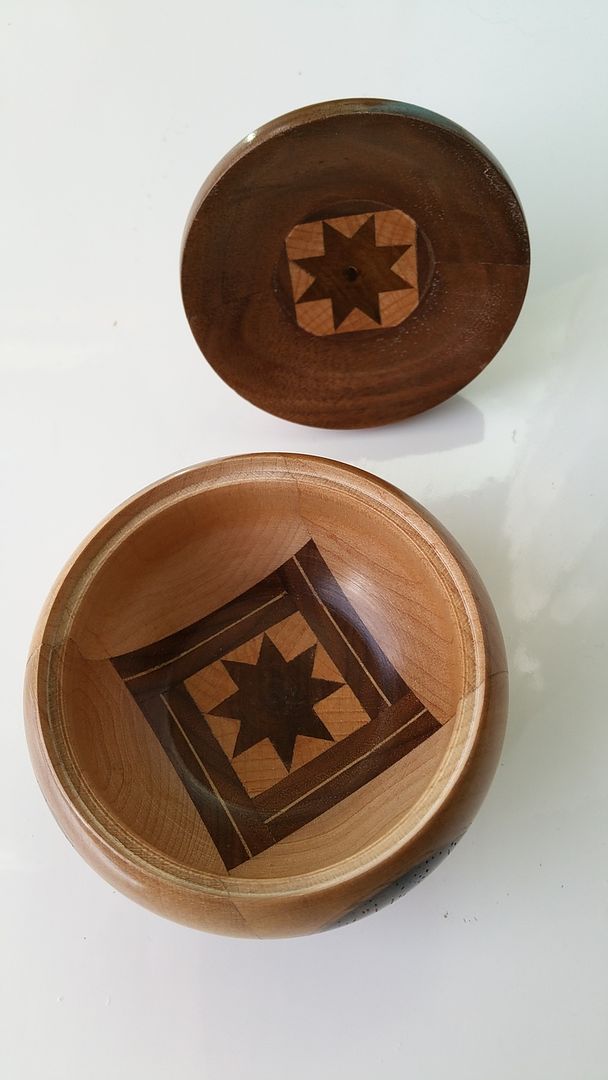

Edited by Evoluzione on Monday 26th September 23:12
That's wonderful!
A problem I'm having is that I need to get to both top and bottom of the tealight holder to turn/finish it, and rechucking is not only time consuming but inaccurate. The stock is only 40mm thick to start with, and the product maybe 36mm, so I can't turn a sacrificial peg (or whatever the official name is). I use a faceplate to turn the top (leaving four holes) then reverse it onto a 3-jaw chuck which engages in the 40mm tealight hole.
Looking at the commercial example more closely I see the 40mm hole was actually made with a Forstner bit, so I've ordered one and that will save time and improve accuracy. It also doesn't have any holes underneath, and I can't work out how they did it.
As for the finish, I tried wax, Osmo and yacht varnish on three different holders yesterday. The wax gives the easiest, smoothest result. Both varnishes have left a slightly rough finish which means they'll need more finisihng work, and of course there's the drying time too. Of the two Osmo is easier to apply as it's thinner and less sticky.
A problem I'm having is that I need to get to both top and bottom of the tealight holder to turn/finish it, and rechucking is not only time consuming but inaccurate. The stock is only 40mm thick to start with, and the product maybe 36mm, so I can't turn a sacrificial peg (or whatever the official name is). I use a faceplate to turn the top (leaving four holes) then reverse it onto a 3-jaw chuck which engages in the 40mm tealight hole.
Looking at the commercial example more closely I see the 40mm hole was actually made with a Forstner bit, so I've ordered one and that will save time and improve accuracy. It also doesn't have any holes underneath, and I can't work out how they did it.
As for the finish, I tried wax, Osmo and yacht varnish on three different holders yesterday. The wax gives the easiest, smoothest result. Both varnishes have left a slightly rough finish which means they'll need more finisihng work, and of course there's the drying time too. Of the two Osmo is easier to apply as it's thinner and less sticky.
If it's a really good piece to do it justice it needs shellac sanding sealer and white polish, (or cellulose equivalent which is cheaper and easier to get hold of) varnish is a bit gash. It's too thick and takes an age to dry so picks up all the bits floating round.
Using SS and polish (button polish for colour if you like) means you can work with it (like car bodywork), you can't do that with varnish, although don't get anything damp near it, it'll turn white.
Using SS and polish (button polish for colour if you like) means you can work with it (like car bodywork), you can't do that with varnish, although don't get anything damp near it, it'll turn white.
Just a quick point about varnish, water based varnishes such as are made by Ronseal dry very quickly. They do of course raise the grain a bit, so smoothing between coats is necessary. In a warm dry place three coats in one day is doable.
Much easier to use and better results than polyurethane varnishes.
Much easier to use and better results than polyurethane varnishes.
Yes, I give it a very fine sand after the sealer. A proper woodworking chuck has been a revelation to me - they can grab so many different shapes just by swapping the jaws. I recommend the supernova 2 chuck, you can get inserts to fit inboard and outboard threads on an ml8 and a lot of other jaws seem to fit it.
minivanman said:
A proper woodworking chuck has been a revelation to me - they can grab so many different shapes just by swapping the jaws. I recommend the supernova 2 chuck
This seems like a whole world of complexity: http://www.woodturningz.com/Nova_Chucks_and_Jaws.h...Presume the 4-jaw chucks are self-centering? How do I know which one I want?
So far I have a Myford faceplate, a 3" 3-jaw chuck and am looking for a screw chuck.
I remember using something called friction polish, it had a nice, very distinctive smell... I wonder what was in it.
Whatevers, it gave a nice, high gloss very quickly, applied with a cloth, you had to be careful not to let the cloth get caught by the workpiece or you'd end up with a broken finger.
Them wert days.
Whatevers, it gave a nice, high gloss very quickly, applied with a cloth, you had to be careful not to let the cloth get caught by the workpiece or you'd end up with a broken finger.
Them wert days.

Most likely, though it didn't smell of meths. I remember it was creamy like a sanding sealer and the smell got stronger the hotter it got.
I can almost smell it but not quite. A bit like having something on the tip of your tongue...but with your nose.
I might have to find some so I can have a sniff.
A quick google for friction polish recipes suggests de natured alcohol for the solvent, so methanol, wood naptha, there are quite a few variations. That must have been it.
I can almost smell it but not quite. A bit like having something on the tip of your tongue...but with your nose.
I might have to find some so I can have a sniff.

A quick google for friction polish recipes suggests de natured alcohol for the solvent, so methanol, wood naptha, there are quite a few variations. That must have been it.
Simpo Two said:
This seems like a whole world of complexity: http://www.woodturningz.com/Nova_Chucks_and_Jaws.h...
Presume the 4-jaw chucks are self-centering? How do I know which one I want?
So far I have a Myford faceplate, a 3" 3-jaw chuck and am looking for a screw chuck.
I got lucky with my ML8 and it came with pretty much all the useful attachments. I have a supernova2 chuck. It has to be the "insert" type - some are direct threaded to fit more common sizes of spindle thread. The beauty of that is that you can take the chuck if you move onto another lathe. All the 4 jaw chucks are self centering, and a lot of the good makes are interchangeable with the jaws - I know sorby and record power both fit the nova. They also come with a woodworm screw which does away with the screwchuck - you just drill it, wind the screw in and grab it with the lathe.Presume the 4-jaw chucks are self-centering? How do I know which one I want?
So far I have a Myford faceplate, a 3" 3-jaw chuck and am looking for a screw chuck.
minivanman said:
I have a supernova2 chuck. It has to be the "insert" type - some are direct threaded to fit more common sizes of spindle thread.
By 'insert' do you mean it would go in the 3-jaw metalworking chuck I have? I'd prefer a direct thread - 1" 12tpi.minivanman said:
All the 4 jaw chucks are self centering, and a lot of the good makes are interchangeable with the jaws - I know sorby and record power both fit the nova.
What I don't understand is that the four jaws are each a quadrant, together making a circle. So if the work you want to hold is smaller than that it won't grip at all, and if it's bigger, it will only touch in four places...minivanman said:
They also come with a woodworm screw which does away with the screwchuck - you just drill it, wind the screw in and grab it with the lathe.
Drill what?Simpo Two said:
minivanman said:
I have a supernova2 chuck. It has to be the "insert" type - some are direct threaded to fit more common sizes of spindle thread.
By 'insert' do you mean it would go in the 3-jaw metalworking chuck I have? I'd prefer a direct thread - 1" 12tpi.minivanman said:
All the 4 jaw chucks are self centering, and a lot of the good makes are interchangeable with the jaws - I know sorby and record power both fit the nova.
What I don't understand is that the four jaws are each a quadrant, together making a circle. So if the work you want to hold is smaller than that it won't grip at all, and if it's bigger, it will only touch in four places...minivanman said:
They also come with a woodworm screw which does away with the screwchuck - you just drill it, wind the screw in and grab it with the lathe.
Drill what?The woodworm screw - you drill your blank in the centre and wind the screw into it. The base of it is large and square, so it goes in behind the jaws and the carriers grip it. The advantage is that the piece is resting up against the front face of the jaws, giving it a lot more support.
loughran said:
Most likely, though it didn't smell of meths. I remember it was creamy like a sanding sealer and the smell got stronger the hotter it got.
I can almost smell it but not quite. A bit like having something on the tip of your tongue...but with your nose.
A quick google for friction polish recipes suggests de natured alcohol for the solvent, so methanol, wood naptha, there are quite a few variations. That must have been it.
While I try to get my head around chucks (how do they make bowls with thin sides and bases?) - was it Briwax?I can almost smell it but not quite. A bit like having something on the tip of your tongue...but with your nose.
A quick google for friction polish recipes suggests de natured alcohol for the solvent, so methanol, wood naptha, there are quite a few variations. That must have been it.
Gassing Station | Homes, Gardens and DIY | Top of Page | What's New | My Stuff