GRP monocoque based on steel car?
Discussion
Elite, not Elise. Pistonheads, spelling matters, especially when it means it's a different car smile
http://en.wikipedia.org/wiki/Lotus_Elite
Ha ha ha - sometimes I am such a dick!
http://en.wikipedia.org/wiki/Lotus_Elite
Ha ha ha - sometimes I am such a dick!
Sam_68 said:
singlecoil said:
groomi said:
AFAIK the only all GRP mocoque car produced is the original Lotus Elite, but it's construction is very different to a steel mocoque car.
I think you'd need at least a steel backbone chassis to make it work.
Oh dear, the PH kit car forum is suffused with GTM owners who will want to disagree with you about the Elite being the only one!I think you'd need at least a steel backbone chassis to make it work.
The bottom line is that it can be done, but it's not going to be the most efficient approach in terms of weight/stiffness, because a well-designed steel bodyshell will have been designed to exploit that particular material's strengths (pardon the pun); stuff like the fact that you can make something that's very stiff and light by spot-welding together a number of sharply folded sheets and pressings, whereas with GRP you want to minimise the moulding complexity, manage high point loads differently and avoid both sharp corners and flat panels if at all possible.
If you want an efficient design, it needs to have been developed with the sprecific characteristics of the materials its made from borne in mind from the outset.

skwdenyer said:
In fairness, GRP is absolutely fine with flat panels, so long as it is used primarily as the skin on either side of a sandwich...
For sure, but you then end up with a flat panel that's an inch thick rather than a couple of millimetres, so there's every chance you'll end up with clearance or dimensional problems to address if you're trying to make a straight copy. You also need to be very careful with localised reinforcement if you're putting point loads into it - you can't simply spot weld (or rather bond, obviously) a bracket onto the thin skin of a sandwich panel.Nothing that can't be sorted, perhaps, but I'd still maintain that in the majority of instances you're better off starting with a clean sheet of paper than trying to produce a straight copy of a pressed steel structure in GRP.
Sam_68 said:
skwdenyer said:
In fairness, GRP is absolutely fine with flat panels, so long as it is used primarily as the skin on either side of a sandwich...
For sure, but you then end up with a flat panel that's an inch thick rather than a couple of millimetres, so there's every chance you'll end up with clearance or dimensional problems to address if you're trying to make a straight copy. You also need to be very careful with localised reinforcement if you're putting point loads into it - you can't simply spot weld (or rather bond, obviously) a bracket onto the thin skin of a sandwich panel.
In older steel monocoque designs, don't forget, flat panels are commonly ridged / swaged / ribbed for stiffness or to shift the natural frequency, so the overall impact upon clearances may not be as bad as envisaged. And there's no doubt one can't create an exact copy, but a near copy, due to the obvious differences in joining technology and so on.
Sam_68 said:
Nothing that can't be sorted, perhaps, but I'd still maintain that in the majority of instances you're better off starting with a clean sheet of paper than trying to produce a straight copy of a pressed steel structure in GRP.
Oh I agree entirely - use the best material for the job or, if you must pick a particular material, design accordingly. However the question was whether it could be done, not whether that would be the best way to proceed in any given case. I have a pet project to do a composite monocoque Saab 2-stroke replica, which would have to largely replicate the original steel structure in order to work even a little bit. If I can ever find the time, and partners, to get further with it I'll write up the design process.You (was it you?) were quite right to point out that FEA is perhaps a little further away from the everyday, even now, than one might hope, but it is probably necessary to sort the detail. Otherwise you end up with a structure such as my Alto Duo, where the GFRP is indeed well over an inch thick in places for no obviously good reason!
Didn’t the original Corvette have a GRP chassis as well, Wiki mentions the body, but i thought it was a monocoque. I have a GM book at home about it somewhere and the early cars had issues with the resin setting too quick causing a loss of strength and cracking. The remedy was to keep the resin cool while it was setting to slow the reaction. This allowed the resin to set with less residual stress and improved the strength of the overall product.
http://en.wikipedia.org/wiki/Chevrolet_Corvette_C1
http://en.wikipedia.org/wiki/Chevrolet_Corvette_C1
ezakimak said:
Didn’t the original Corvette have a GRP chassis as well, Wiki mentions the body, but i thought it was a monocoque. I have a GM book at home about it somewhere and the early cars had issues with the resin setting too quick causing a loss of strength and cracking. The remedy was to keep the resin cool while it was setting to slow the reaction. This allowed the resin to set with less residual stress and improved the strength of the overall product.
I'm pretty sure the original Corvette had a ladder frame chassis, but the bodywork was a pretty substantial monocoque shell in its own right, so it would have undoubtedly added to the stiffness. The GRP is massively thicker than equivalent Lotuses etc., which will have caused the resin stress issues you mentioned. End result was certainly much higher quality of finish than the 50's and 60's generation Lotuses, but it weighed a lot more too, of course.
Interesting subject.
The grp floor, sills and bulkhead area would be fine but I'd be interested to know more about the the steel reinforcement areas around the bulkhead areas for the suspension.
Would like to have a go at this sometime on my own project.
Most of the outer body panels are completed and I am tempted to replace the box section chassis.
I know - old post brought back to life.
The grp floor, sills and bulkhead area would be fine but I'd be interested to know more about the the steel reinforcement areas around the bulkhead areas for the suspension.
Would like to have a go at this sometime on my own project.
Most of the outer body panels are completed and I am tempted to replace the box section chassis.
I know - old post brought back to life.
289 said:
...I'd be interested to know more about the the steel reinforcement areas around the bulkhead areas for the suspension.
The pictures on this thread on the Locost forum might interest you.The Costin Nathan (plywood rather than GRP monocoque, but the essential principles are very similar) might make an interesting study, too:
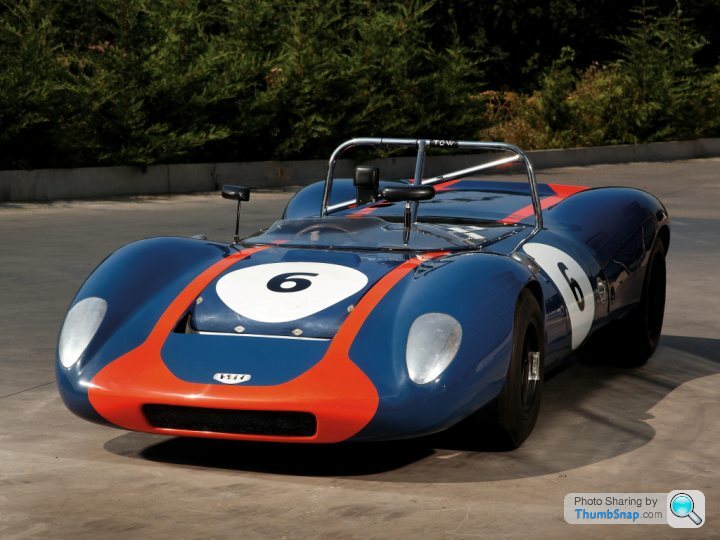
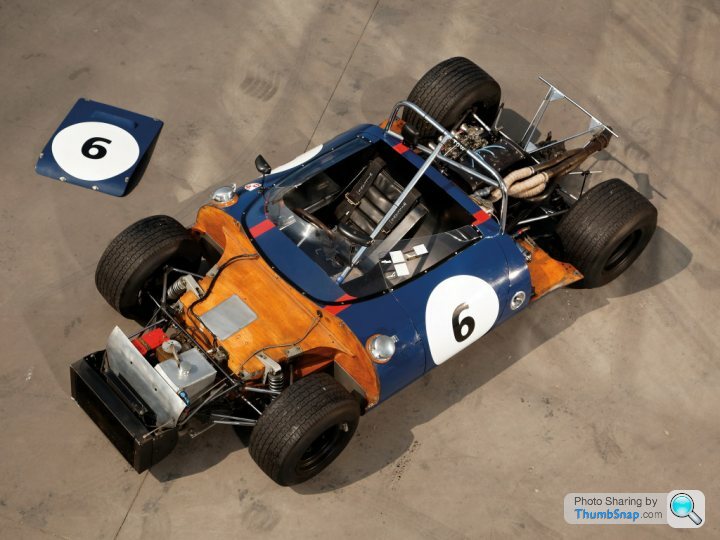
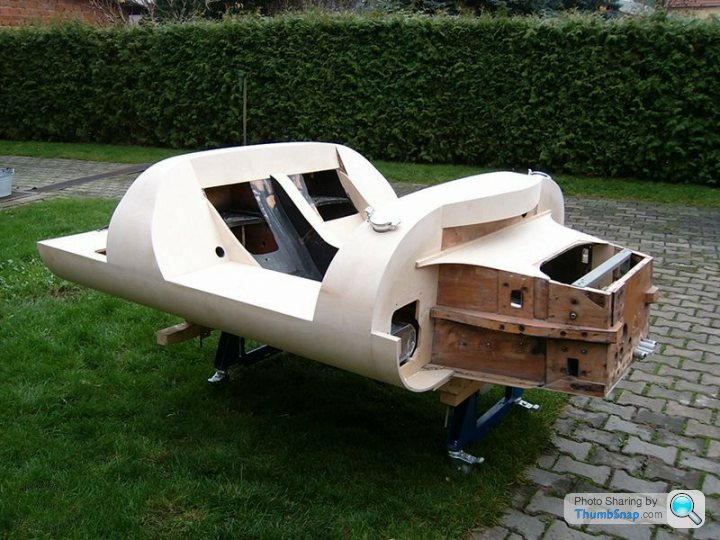
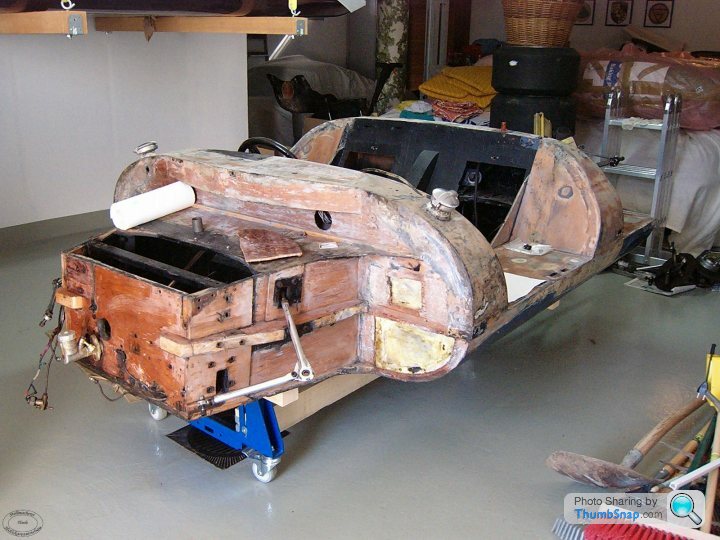
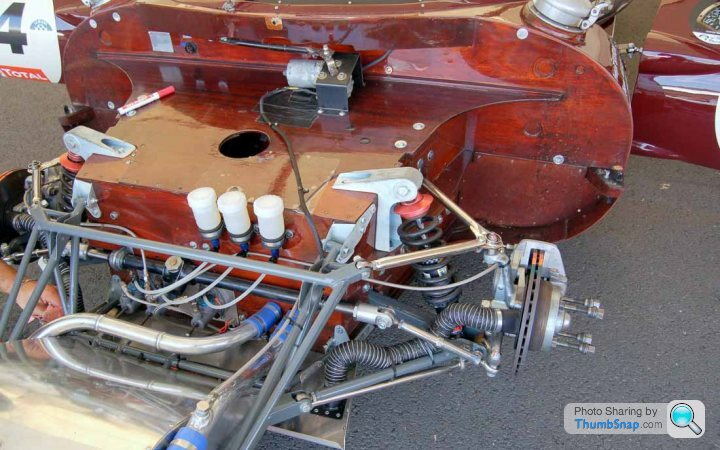
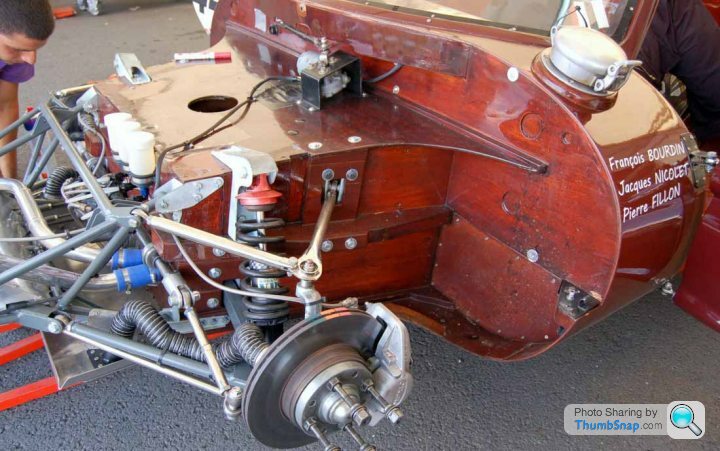
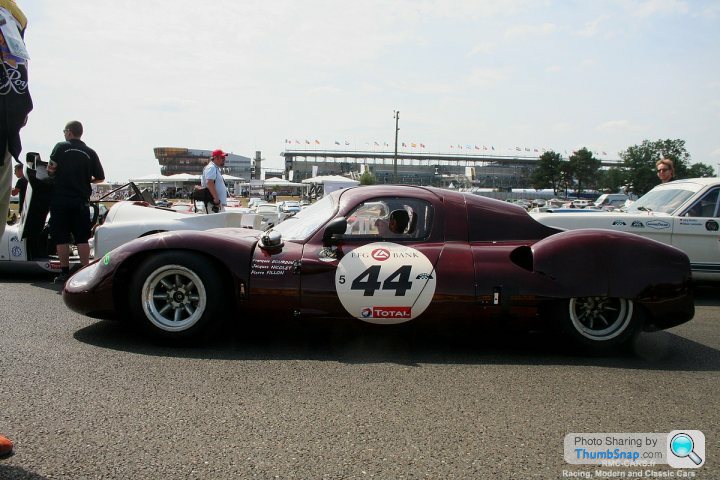
Edited by MintSprint on Thursday 20th November 12:01
niva441 said:
As I recall they had to engineer weakness into the nose section of the Midas Gold, so that it absorbed energy in a controllable manner.
The original Quantum (Fiesta based) was a GRP monocoque, although later versions went to a chassis frame, but that may have been to make a convertible easier to engineer.
The original Quantum with 4 seats (known as mk1) was indeed a GRP monocoque, as indeed was the next model (aqain a 4 seater)known as mk2 - they have a steel box section bonded in the sills, but that's the only 'diversion' from GRP. The 2+2 which could best be described as a 'convertible version of the same car, but with 2 seats + 2 small child seats' was of similar construction, except that the bodywork forward of the doors instead of being part of the GRP monocoque, was a steel tubular subframe bolted to the monocoque. This steel subframe carried the engine/gearbox, and had a flip-up GRP front attached. There were 2 other Quanta (is that the group name?) being the H4, which had a steel chassis and GRP body, and the Extreme which is (still in production) a stainless steel monocoque with GRP rear body parts. The original Quantum (Fiesta based) was a GRP monocoque, although later versions went to a chassis frame, but that may have been to make a convertible easier to engineer.
Nothing wrong with a GRP monocoque, of course it's best tou use woven mat for structure not chopped strand & you need to be careful how you attach point loads, it's been said that GRP is no good in flat sheets - but niether is steel, that's why there are always rebates, flanges, flutes etc pushed into it. In principle taking moulds from a steel car & re-creating in GRP can be done, but it does depend on the car you have in mind & whether you're happy to bond in metal sections to take point loads - or redesign mountings to spread the load over a wider area.
Gassing Station | Kit Cars | Top of Page | What's New | My Stuff