Aluminium monocoupes and kit cars
Discussion
Ferg said:
740-something at S.V.A.
Sorry, I'm unfamiliar with the Libra. Does it have a steel chassis, or is it a fiberglass monocoque?ETA, just did a quick Google, and I see it's a monocoque. Nice looking thing actualy.

My comment about metal, wood, and leather, is purely personal preference of course.

Getting back on topic, those Boys back in 1967 didn't do too badly with the ally tub of the type 49 and 400hp! Obviously that was a time when Men where Men, and Sheep where nervous!

Edited by mickrick on Sunday 14th November 08:38
Sam_68 said:
Dr Derek Doctors said:
We're aiming for 400kg.
To be fair, you're hardly comparing apples with apples.Indeed it is a road car with all sorts of stuff most lightweights could only dream of! The 'donor' car route means it's a steel fuel tank, too, and some quite hefty cast uprights all 'round. Add in a heater, sound proofing, internal trim panels, door cards, 17" x 7" spare wheel and tyre and about 5" of glass that never emerge from the door due to their true Fiesta identity and it's not doing too badly to get down below 800kg, I reckon.
Sam_68 said:
cymtriks said:
...surely a lingering doubt regarding years of exposure at outdoor temperatures must still exist.

Exposure to UV can be a problem (albeit easily solved), but going soft in the sun hasn't been a consideration since the early days of Elites going saggy in California.
Sam_68 said:
cymtriks said:
...If the advantages are so obvious why so few?
I thought we covered that: cost.Aston Martin?
Ferrari?
Lamborghini?
The main production models are not Carbon chassis but cost a huge ammount and sell in market where race car engineering would surely be a selling point.
If cost is the reason then how much are we talking about? Enough to rule it out for a car that sells on performance, is related to motorsport in the public view and costs well over 100K ?
Sam_68 said:
cymtriks said:
...With a composite chassis how would you tell if internal delamination had occured?
Quite easily. You have never worked with a CF tub, obviously? You can tell very easily by tapping against the composite with your knuckle.cymtriks said:
...How many garages could fix it?
It rarely happens, so the question is academic, but the repair procedure is actually quite simple: if the skins delaminate from the honeycomb core, you can drill holes and inject epoxy as a repair
Anyway what about a flat pack chassis of composites or honeycombe? I know its not a new idea and that its been discussed before but has anyone actually built a small run of chassis like this? Combined with ally extrusions it might be a very interesting way forwards.
cymtriks said:
Anyway what about a flat pack chassis of composites or honeycomb? I know its not a new idea and that its been discussed before but has anyone actually built a small run of chassis like this? Combined with ally extrusions it might be a very interesting way forwards.
I find this idea very interesting. It sounds to me like the kind of job best done with a router and templates (which could be CNC cut). Do we have any details of how point loads such as suspension connections are best fed into this material? I'm sure there is plenty of information to be had from books, but a few brief details here would seem to fit this thread very well.It's certainly the sort of thing I would be prepeared to have a go at, not the design maybe, but certainly cutting the panels and assembling them.
Singlecoil
Not kit cars, but a few years ago there was a microlight called the shadow that had a fuselage made of flat pack nomex honeycomb. The original company has folded but they are still being made by a comapny at Old Sarum. The loads aren't exactly the same but they maust have a way of hanging the engine from the monocoque.
DrDD
I haven't looked at the regs for RGB for a while but isn't there a rule that if you use a composite chassis that you have to have made them for series production?
Not kit cars, but a few years ago there was a microlight called the shadow that had a fuselage made of flat pack nomex honeycomb. The original company has folded but they are still being made by a comapny at Old Sarum. The loads aren't exactly the same but they maust have a way of hanging the engine from the monocoque.
DrDD
I haven't looked at the regs for RGB for a while but isn't there a rule that if you use a composite chassis that you have to have made them for series production?
I know that one of the ideas is to get the loads fed in near the edges of the panels, so with a plane fuselage I suppost that would mean a subframe mounted near the edge of the front bulkhead (if a single engine plane).
But how is the actual mounting itself done, what's the actual physical process?
But how is the actual mounting itself done, what's the actual physical process?
Smart roadster said:
Singlecoil
Not kit cars, but a few years ago there was a microlight called the shadow that had a fuselage made of flat pack nomex honeycomb. The original company has folded but they are still being made by a comapny at Old Sarum.
?
Was this the Microlight ?Not kit cars, but a few years ago there was a microlight called the shadow that had a fuselage made of flat pack nomex honeycomb. The original company has folded but they are still being made by a comapny at Old Sarum.
?
http://www.davidcookaviator.com/david-cook/shadows...
cymtriks said:
It is still true that liquids getting into the matrix can cause problems.
Not significantly. Certainly nothing like as true as if you'd made the same statement about steel construction.I've owned 35 year old Elans; now, if you know anything about Elans, you'll know that there are a number of places where water will collect in the bodyshell (in the nose, for instance, where it will doubtless be mixed with hydrocarbons). It has not the slightest structural effect on the fibreglass; Nada. Zip.
And that's with polyester resin, not epoxy.
Further evidence? A major cosmetic problem with '60's Lotuses (again, now pretty much solved on modern cars) is 'osmosis'. This is where water that has soaked into the fibreglass is 'wicked' up under the paint and forms blisters. You can stick a pin in the blisters and they will pop and let the water out. Now, osmosis is a serious pain in the arse and requires that you strip the shell back to gelcoat and dry it out in a low-bake oven before you respray, if you want to be certain of curing it. But it has no structural effect whatsoever; it's purely a cosmetic problem.
I have never encountered structural damage to automotive fibre composites that could be attributed to damage by water or other liquids. Impact damage; fire damage; stress cracking of gelcoats, sure, but never water damage.
Forget about it. It simply isn't a problem in practice. You're jumping at shadows.
cymtriks said:
Sam_68 said:
I thought we covered that: cost.
Not convincingly covered.Aston Martin?
Ferrari?
Lamborghini?
'Aha!' Says Cymtriks, 'you said cost, you didn't say anything about large scale production difficulties!'
But, my dear chap, they amount to the same thing: if you want to build 50 cars a week (and it may surprise you to discover that even Ferrari builds twice that number), in theory there's nothing stopping you setting up a vast factory with rows of autoclaves and dozens of Italian tailors cutting patterns out of pre-preg for you, but the costs to be amortised would be absolutely astronomical.
There are a good few extremely limited production supercars that have used carbon fibre (Bugatti EB110, McLaren F1, KTM Crossbow, Bugatti Veyron, Ferrari F50 etc.), but at present the technologies have an economic 'glass ceiling' on production numbers.
cymtriks said:
If cost is the reason then how much are we talking about? Enough to rule it out for a car that sells on performance, is related to motorsport in the public view and costs well over 100K?
Yes, compared to the much cheaper technologies of extruded aluminium, which are sexy enough, cheap enough, light enough, stiff enough and vastly cheaper and more production-friendly.It's anecdotal, I know, but I've been told by a very reliable source that the reason Westfield didn't produce more than 6 FW400's is that when they went back to place an order for the next batch of tubs after the initial prototype run, they were told that the cost would be such that it would put the price of the car into Porsche 911 territory. That's for a 'Seven', with an MGF engine... If CF makes a 'Seven' cost as much as a Porsche 911 (and if you have difficulty believing that, look at the price of the KTM Crossbow, and what happened to that, commercially), then how much is a carbon fibre 911, going to cost. And how much for a carbon fibre Ferrari 458?
cymtriks said:
You know that, does Joe Average kit car builder or a local MOT centre?
If I was an F1 engineer, that would be a valid argument. I'm an Architect; there's no reason why your Joe Average shouldn't become as clued up on the properties of CF as I am... it really isn't particularly unsual or difficult to get a grasp of: it's pretty much like glass fibre, only better in every way (except cost, where it's still spectacularly worse at the moment). The kit car industry isn't scared of glassfibre, neither is Joe Average, neither is any decent MOT inspector.Honestly... you're imagining problems that either simply aren't there, or at least aren't the slightest bit significant.
There is one massive and overbearing reason why CF doesn't make sense if you want to build more than a handful of cars: cost.
That's all.
However good it is in other respects, if it doesn't make economic sense, it ain't gonna happen.
Edited by Sam_68 on Sunday 14th November 19:11
singlecoil said:
cymtriks said:
Anyway what about a flat pack chassis of composites or honeycomb? I know its not a new idea and that its been discussed before but has anyone actually built a small run of chassis like this?
...Do we have any details of how point loads such as suspension connections are best fed into this material? 
In terms of point loads, it's basically identical in principle to the details given in Tony Pashley's book for aluminium honeycomb panel construction. You use pairs of 'top hat' section bobbins designed to mate with each other from either side of the panel. Groups of these can be used bolt angle brackets onto for suspension/engine mounts etc.
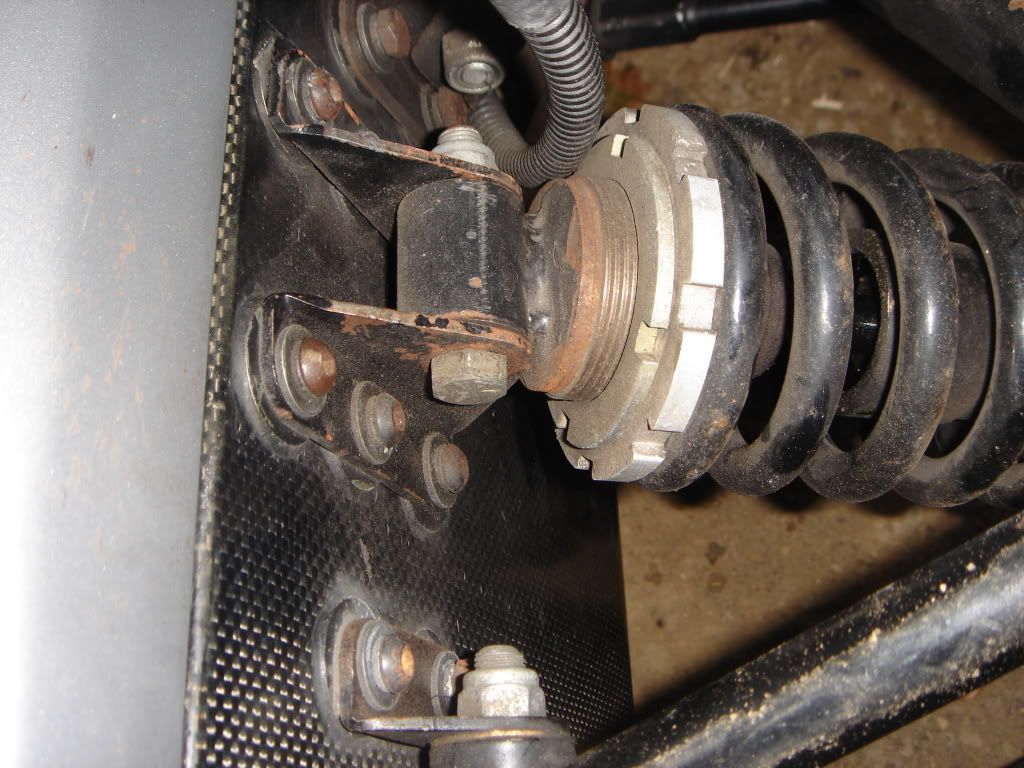
Best photo I can find to illustrate this without going down to the garage in the cold and wet is this one ^^^ (unfortunately before I cleaned up and painted the brackets, which as you can see, aren't quite as impervious to Cymtrik's water as the carbon fibre is

You do need to be very careful about design and location of the brackets, though... the brackets for anything that could feed a big moment into the chassis (like engine mounts, rollover bars etc.) are designed to be 'wrapped around' the corners, so that the forces can always be taken out in shear.
Sam_68 said:
singlecoil said:
cymtriks said:
Anyway what about a flat pack chassis of composites or honeycomb? I know its not a new idea and that its been discussed before but has anyone actually built a small run of chassis like this?
...Do we have any details of how point loads such as suspension connections are best fed into this material? 
In terms of point loads, it's basically identical in principle to the details given in Tony Pashley's book for aluminium honeycomb panel construction. You use pairs of 'top hat' section bobbins designed to mate with each other from either side of the panel. Groups of these can be used bolt angle brackets onto for suspension/engine mounts etc.
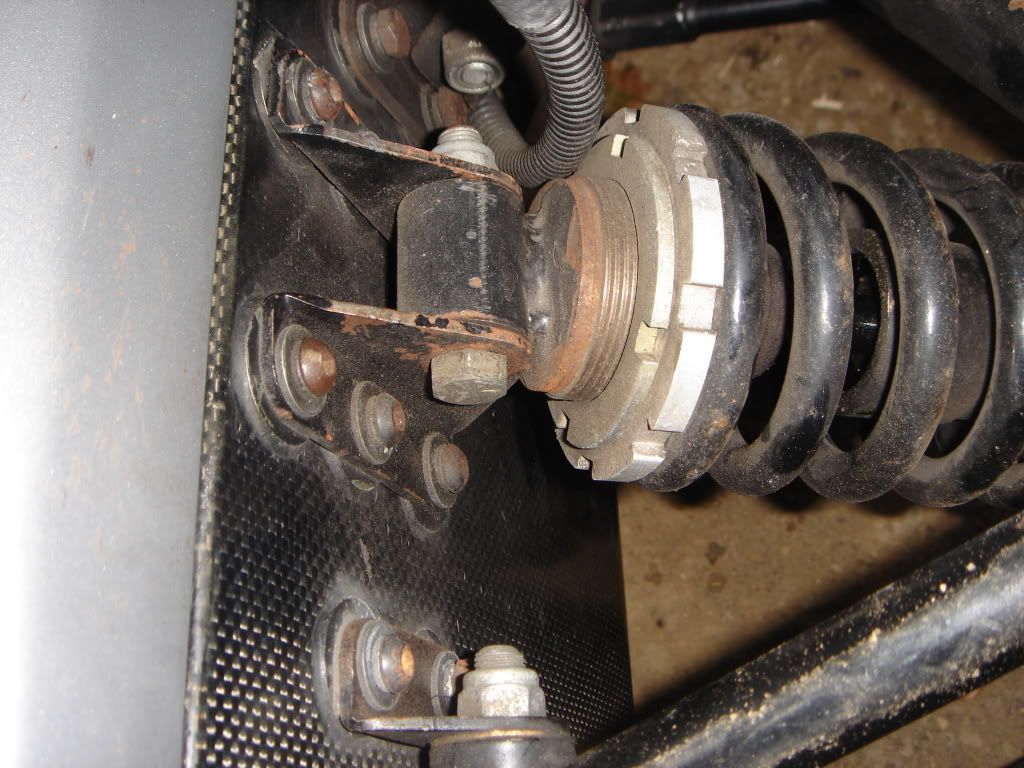
Best photo I can find to illustrate this without going down to the garage in the cold and wet is this one ^^^ (unfortunately before I cleaned up and painted the brackets, which as you can see, aren't quite as impervious to Cymtrik's water as the carbon fibre is

You do need to be very careful about design and location of the brackets, though... the brackets for anything that could feed a big moment into the chassis (like engine mounts, rollover bars etc.) are designed to be 'wrapped around' the corners, so that the forces can always be taken out in shear.
I know there are books on this stuff, but the problem with books is that you can't ask the author specific questions. At this stage I'm also trying to assess whether this whole subject is worth my getting involved with.
singlecoil said:
Presumably the bobbins are specific to the material in use, and are bonded to the panels.
The design is, yes. Tony Pashley's book suggests that they are designed so that the distance between the opposing flanges of the 'top hats' is the thickness of the panel plus 0.05mm per adhesive layer, but Martin Ogilvie suggested an alternate design where they are threaded into one another (and therefore effectively adjustable to accommodate minor variations in the panel thickness). Obviously the bigger the diameter of the flange, the more they will spread the the load into the skin of the panel. But obviously you would standardise on just a few designs of bobbins per car, using them in multiple if you need to spread the loads over a greater area.
And yes, they're bonded to the panels using epoxy.
singlecoil said:
I'd love to see some other pictures as and when it's convenient. If possible it would be great to get some details of how the perpendicular joins are achieved, and how open edges are sealed.
I'll see what I can do, if I remember, but it's all really quite straightforward. Open edges are usually sealed by overlapping the face of the abutting panel (which has had one face and the honeycomb routed away along the edge, to the depth of the panel it abuts), or by strips/angles of carbon fibre bonded over the exposed edge. Internal angles just have a strip of CF tape laid up over them.Ferg said:
Sam_68 said:
Dr Derek Doctors said:
We're aiming for 400kg.
To be fair, you're hardly comparing apples with apples.Indeed it is a road car with all sorts of stuff most lightweights could only dream of! The 'donor' car route means it's a steel fuel tank, too, and some quite hefty cast uprights all 'round. Add in a heater, sound proofing, internal trim panels, door cards, 17" x 7" spare wheel and tyre and about 5" of glass that never emerge from the door due to their true Fiesta identity and it's not doing too badly to get down below 800kg, I reckon.
Our car will be road legal and IVA'd and will be a two seater.
its pretty obvious from the CAD pics that it has two seats.
Dr Derek Doctors said:
Ferg said:
Sam_68 said:
Dr Derek Doctors said:
We're aiming for 400kg.
To be fair, you're hardly comparing apples with apples.Indeed it is a road car with all sorts of stuff most lightweights could only dream of! The 'donor' car route means it's a steel fuel tank, too, and some quite hefty cast uprights all 'round. Add in a heater, sound proofing, internal trim panels, door cards, 17" x 7" spare wheel and tyre and about 5" of glass that never emerge from the door due to their true Fiesta identity and it's not doing too badly to get down below 800kg, I reckon.
Our car will be road legal and IVA'd and will be a two seater.
its pretty obvious from the CAD pics that it has two seats.
Compare with the Libra by all means, but make sure it is like for like won't you?
Doors.
Wind-up windows.
5 wheels and tyres.
Carpets and soundproofing.
Proper hard roof, not rag topped.
Opening boot.
Windscreen with wipers.
Heater.
If you have these, well done for weight saving, if not then any comparison is pretty pointless isn't it?
Dr Derek Doctors said:
Well I'd love to know were you two got your info from?
Erm... from you?Dr Derek Doctors said:
Myself and two collegaues freinds are designing a car for Road/RGB championship and Aluminium monocoque is the way were going. Considering that we have all worked in fairly high level motorsport this is not a decision based on hopes and dreams.
Of course I did make the rather rash assumption that you have some sort of clue about what you're doing; though in my defence, you did claim that your decision was based on more than hopes and dreams?Unless, perhaps, you're going to tell us that you think you can build a competitive RGB car with all mod cons and production car comforts as per Ferg's list above?
In which case, I'm afraid I may have some bad news for you...
And if you think you're fitting full doors to the tub design you posted above, I may have some more bad news for you...

Edited by Sam_68 on Sunday 14th November 22:02
Sam_68 said:
I'll see what I can do, if I remember, but it's all really quite straightforward. Open edges are usually sealed by overlapping the face of the abutting panel (which has had one face and the honeycomb routed away along the edge, to the depth of the panel it abuts), or by strips/angles of carbon fibre bonded over the exposed edge. Internal angles just have a strip of CF tape laid up over them.
Like this? With the brown representing the tape?
Correct for the internal corner.
For the external corner, you'd either use a moulded corner or simply rout and fold the panel.
For the exposed ends, you'd generally use a simple strip or an L-section rather than a U-section (it's mainly cosmetic, anyway - if you look at the pictures of Martin Ogilvie's routed-and-folded 'Wisper' electric 'Westfield' monocoque, you'll see that he actually left the edge of the honeycomb exposed).
It's not as neat and classy as a 'proper' autoclaved moulding, but it works.
For the external corner, you'd either use a moulded corner or simply rout and fold the panel.
For the exposed ends, you'd generally use a simple strip or an L-section rather than a U-section (it's mainly cosmetic, anyway - if you look at the pictures of Martin Ogilvie's routed-and-folded 'Wisper' electric 'Westfield' monocoque, you'll see that he actually left the edge of the honeycomb exposed).
It's not as neat and classy as a 'proper' autoclaved moulding, but it works.

Did anyone see the aluminium composite Beetle floorpan/suspension that Chesil were showing at Exeter? Looked impressive, but I wasn't convinced the section that mounts the front wishbones looked strong enough, especially given the lengths of the wishbones. I may be grossly underestimating the strength of this material, but seems like a fairly modest force through a single wishbone (e.g. hitting a pot hole) would be putting the chassis section in the middle under a lot of stress.
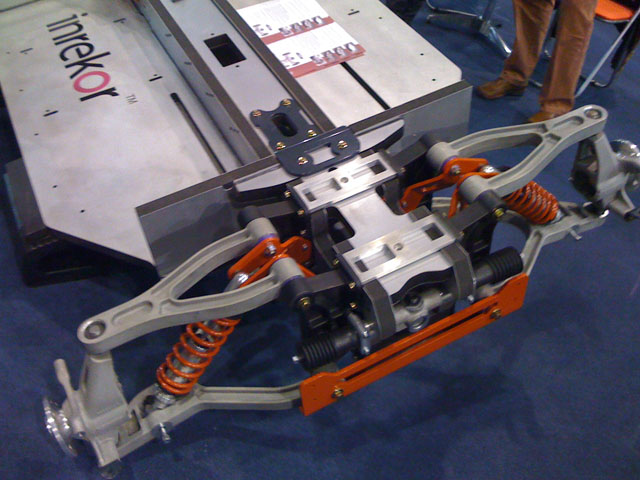
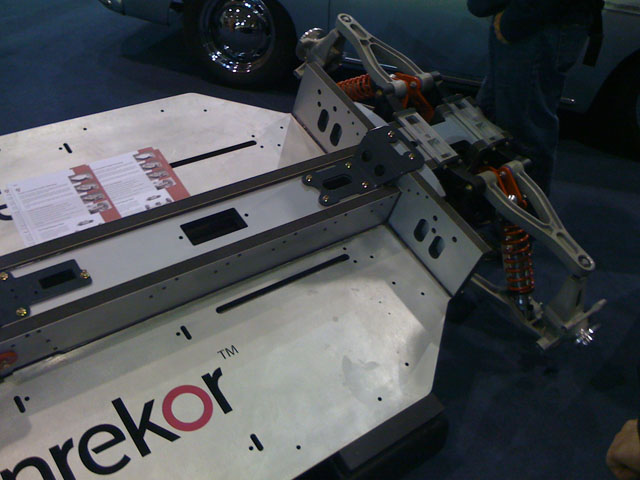
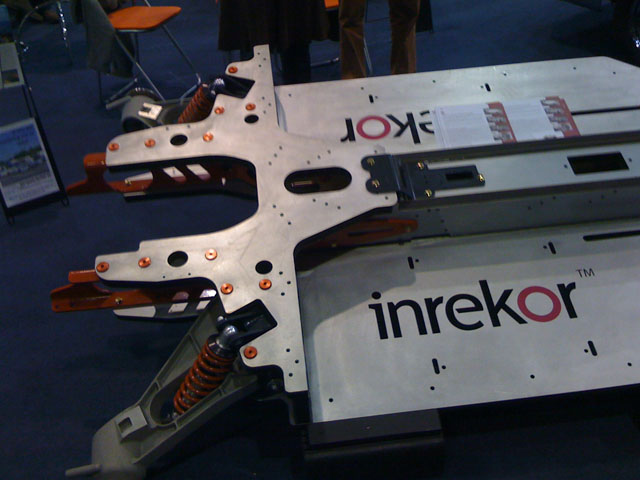
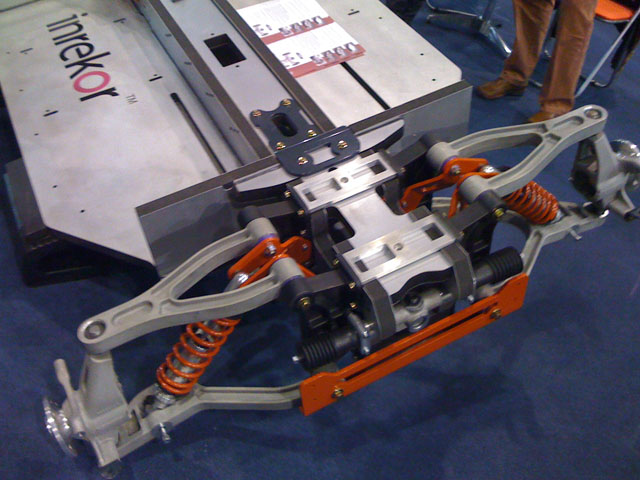
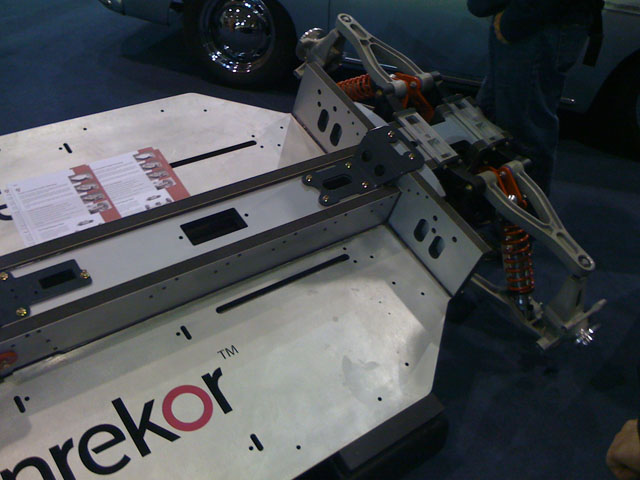
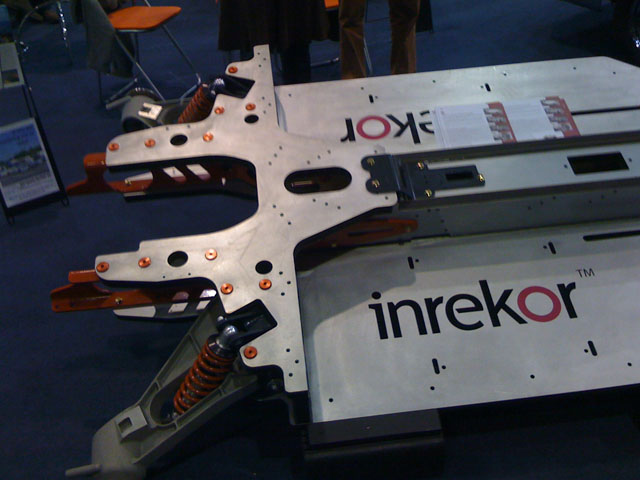
Edited by Mr2Mike on Sunday 14th November 22:07
Gassing Station | Kit Cars | Top of Page | What's New | My Stuff