Rear wishbones
Discussion
Difficult to tell from the photo but it looks like it's far too big to fit. Squeezing is only possible if the steel inner tube is shorter than the polybush. Are you sure you've got the right bushes as I recently did mine any they all fitted nicely without any real force required, just a smear of grease to help sliding them into the chassis mounts.
Stevo302 said:
Yeh got the right ones apparently. But every mount is slightly different width. I love old cranky cars eh....
Same with my Vixen. I'm not looking forward to fit the new polybushes as I can see that the arms are wider than the tabs on the frame and the old rubber bushes are nowhere near evenly positioned in the frametabs.Let us know how you get on as I might need some guidance when I start to fit mine.
Make a jig the width of a bush, I used wood so not to damage paint, go round all the mounting lugs and set the spaces before fitting the real thing.
Even with all the widths set a few milli here and there can make it an awkward job.
Eta, if the gaps are tight rather than t
t the lugs, use a piece of threaded rod with two nuts and washers, thread the rod through the lugs with the nuts and washers inside the lugs, then use the nuts to jack out to the correct gap.
Even with all the widths set a few milli here and there can make it an awkward job.
Eta, if the gaps are tight rather than t

Edited by GAjon on Tuesday 3rd March 08:19
Right, first thing, nightmare! Second thing, should have planed it better/ if only I had known. 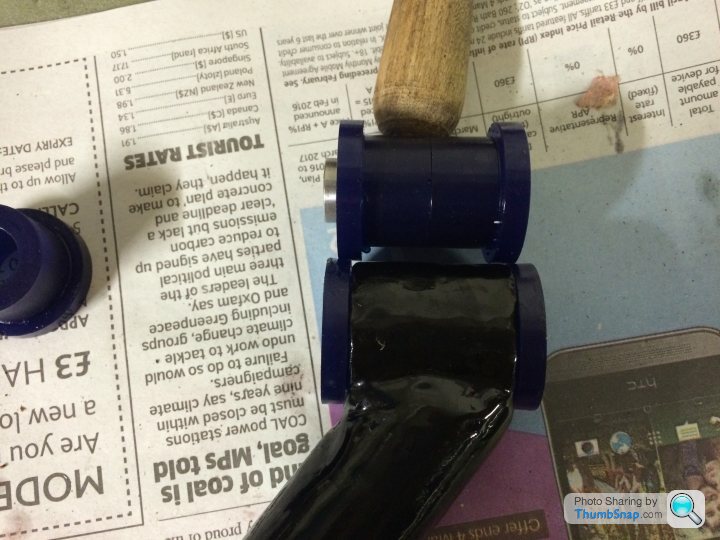
As you can see the steel was a tight fit anyway. I should have ground the steel, fitted the bushes and tried to fit before they went off for plating. Now I think I'm too late. I have wondered about cutting some of the rubber bush off to make things a little better but I've had enough for today.
Any ideas at this stage would be great. Sometimes I could throw in the towel.
Regards.
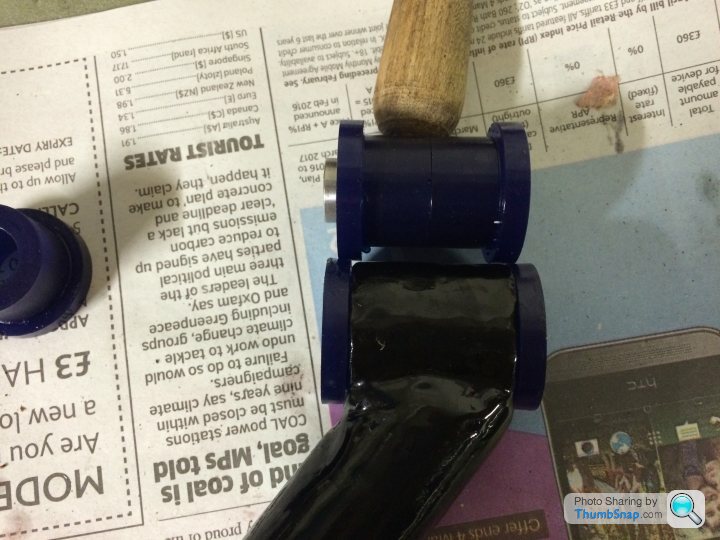
As you can see the steel was a tight fit anyway. I should have ground the steel, fitted the bushes and tried to fit before they went off for plating. Now I think I'm too late. I have wondered about cutting some of the rubber bush off to make things a little better but I've had enough for today.
Any ideas at this stage would be great. Sometimes I could throw in the towel.
Regards.
The powder coating thickness is too negligable to make any difference. Grinding down your wishbones is addressing the wrong issue, if they came out they must fit back in. The problem must be the thickness of the part of the bush which protudes from the end of the wishbone. Taking some thickness out of this sounds like a much less drastic approach than grinding away at wishbones.
Looks no different to the amount of bush sticking out of my wishbones and I've fitted the Metalastic variety. I had to gently spread a couple of my chassis brackets to get them in position. The paint scraper approach is a good idea as if they are tight going in, the bolt hole will sometimes damage the face of the bush as it slides across it.
Does it matter much about the bush protecting the steel? As in the pic you can see the bush 'T'ing round the end of the wishbone?
I might gring a little off the steel and cutt a little off the bush....this might make a bigger difference than grinding/cutting off one piece.
Thanks for all the comments so far.
I might gring a little off the steel and cutt a little off the bush....this might make a bigger difference than grinding/cutting off one piece.
Thanks for all the comments so far.
The steel sleeve is what stops the bush collapsing when the bolt is tightened, squeezing the chassis mounts together.
The flat end of each bush 'top hat' just locates the bushing centrally. The barrel of the bush does all the work of allowing the wishbones to move around without rattling.
IMO, poly bushes are massively overrated and expensive. From the installs I've seem on PH, they mostly fit badly and probably fail faster than they should.
The original-style metalastic bushes locate better and absorb the variances in chassis mount location better.
They flex when moving, unlike poly bushes, which have to twist by design and if not properly lubricated (which is most of the time if the inners aren't cross-hatched to lock in the lube) will wear very quickly.
BTW - if that steel inner in your pic is longer than the bush halves, then it's incorrect for that bush.
The flat end of each bush 'top hat' just locates the bushing centrally. The barrel of the bush does all the work of allowing the wishbones to move around without rattling.
IMO, poly bushes are massively overrated and expensive. From the installs I've seem on PH, they mostly fit badly and probably fail faster than they should.
The original-style metalastic bushes locate better and absorb the variances in chassis mount location better.
They flex when moving, unlike poly bushes, which have to twist by design and if not properly lubricated (which is most of the time if the inners aren't cross-hatched to lock in the lube) will wear very quickly.
BTW - if that steel inner in your pic is longer than the bush halves, then it's incorrect for that bush.
You are trying to avoid any metal on metal contact and allow the wishbone to rotate around the bush. If you have T'ing on the end of the bush tube it will have been touching the chassis mount which isn't good or right, as this will also wear the face of the chassis mount weakening it over time.
Gassing Station | TVR Classics | Top of Page | What's New | My Stuff