Building "Thor"
Discussion
ClockworkCupcake said:
You could stick one of your other Meteors in it. 
I could, but I sold one. 2 are scrap/spare parts engines and one is a WWII veteran which I will get running for posterity. The final one will go up for sale sometime over the next 6 months I think.
However, I have heard about a supply of unused, boxed, refurbished engines in a foreign land far, far away! I can get two boxes on a trailer for a very long road trip!
I also have a friend with a some ARV Centurion refurbished engines.
Most people who have these unused engines sitting in a shed don't need the money they are worth. My friend has a Merlin and various early jet engines, just because he likes having them. This applies to just about everybody that own them.
Paul
Spent a bit of time yesterday reorganising my workshop and then managed to maneuver the chassis into the dirty side.

I don't think I posted any pictures of the gearbox I have had built for the beastie. It is a TH400 3 speed GM that has been built to take 1500ftlbs of torque by a drag racing box expert.
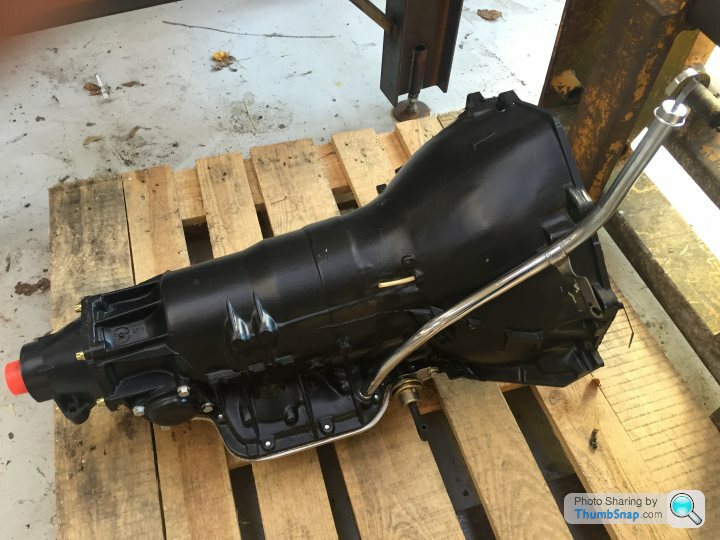

This morning I fired up the gas axe and started removing the parts that I will not need, along with some that may get re-used.
Oxypropane may seem an extreme way of removing bolts, but if done carefully the bulk of the chassis prevents it getting hot enough to melt so you only cut the nut or bolt. With rusted fittings it is way faster than even an air impact nut runner.

The pile of bits I am keeping for now is quite small.
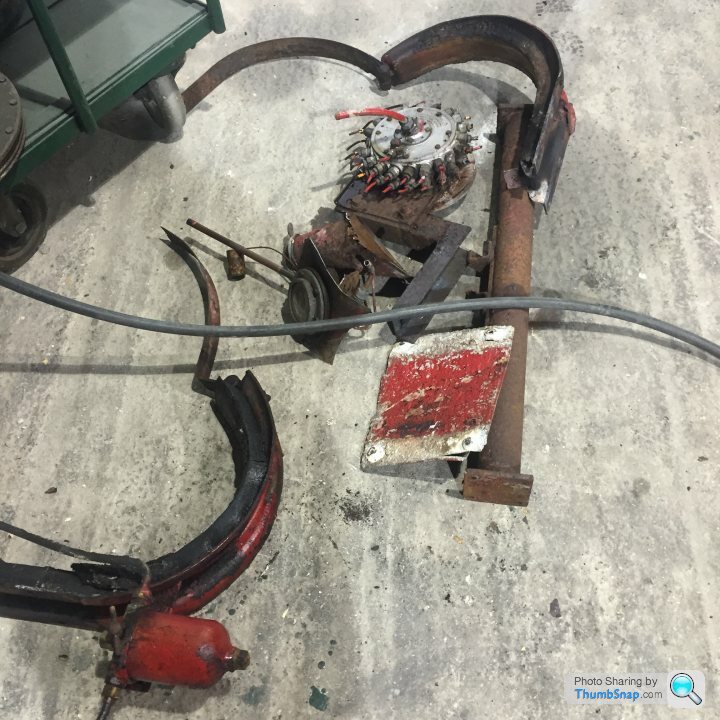
And the pile I am sending to scrap is growing rapidly.

With a bit of luck I will get time to remove the engine and box tomorrow. The chassis has areas of considerable corrosion but it is 8mm thick so there will only be a few small areas that will need attention.
I am keeping the axles in place until the end of the strip down. I think I can take upto 12" out of the front axle height and 8" the rear. More would be good so I will look at what can be done.
Paul

I don't think I posted any pictures of the gearbox I have had built for the beastie. It is a TH400 3 speed GM that has been built to take 1500ftlbs of torque by a drag racing box expert.
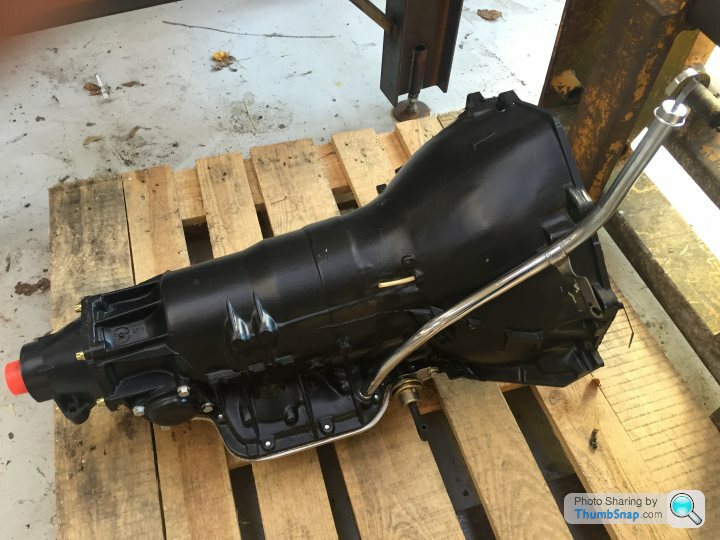

This morning I fired up the gas axe and started removing the parts that I will not need, along with some that may get re-used.
Oxypropane may seem an extreme way of removing bolts, but if done carefully the bulk of the chassis prevents it getting hot enough to melt so you only cut the nut or bolt. With rusted fittings it is way faster than even an air impact nut runner.

The pile of bits I am keeping for now is quite small.
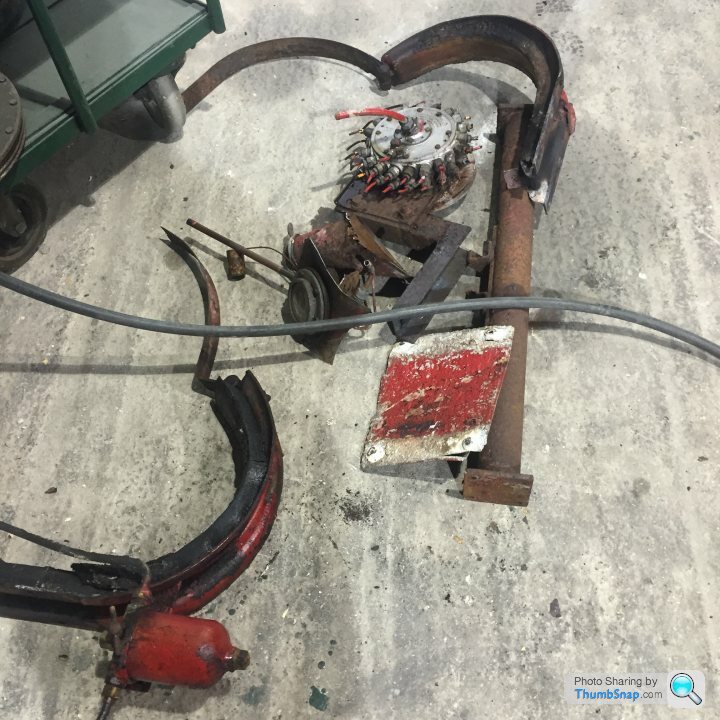
And the pile I am sending to scrap is growing rapidly.

With a bit of luck I will get time to remove the engine and box tomorrow. The chassis has areas of considerable corrosion but it is 8mm thick so there will only be a few small areas that will need attention.
I am keeping the axles in place until the end of the strip down. I think I can take upto 12" out of the front axle height and 8" the rear. More would be good so I will look at what can be done.
Paul
TooMany2cvs said:
It is indeed a pivot pin oiler. There are 40 ports and 38 are used. Every pin and bush is oiled with a lost-oil system. It is driven by belt from the main prop shaft so only works when the vehicle is moving and probably uses a heavy oil rather than grease.It acts on all suspension moving parts, as well as front axle pivots, steering and some brake parts. It is clearly a later modification rather than original and uses micro bore plastic pipes. It turns freely so I hope to re-use it as I don't want that many grease nipple to deal with.
The shed is built with 6"x4" RSJ so the tonne of engine and stand is no big deal.
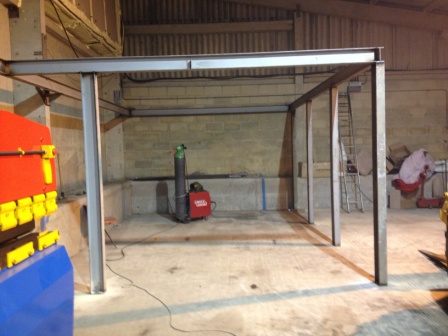
This picture is half way through the steel work (didn't get any more pics) and there is twice as much steel in the roof and all timbers are 6x3". It was built with having a load on the roof and there is probably about 3 tonnes up there at present.
If you are wondering it is my paint booth.

Regarding the chassis, there has been no progress today as other things got in the way. Tomorrow.................maybe.
Paul
A bit more progress today.
The number of bolt holes in the chassis is growing every time I fire up the gas axe!
It is now just a rolling chassis and it still weighs about 2.75 to 3 tonnes, judging by the way my forklift struggled (successfully) to lift it!

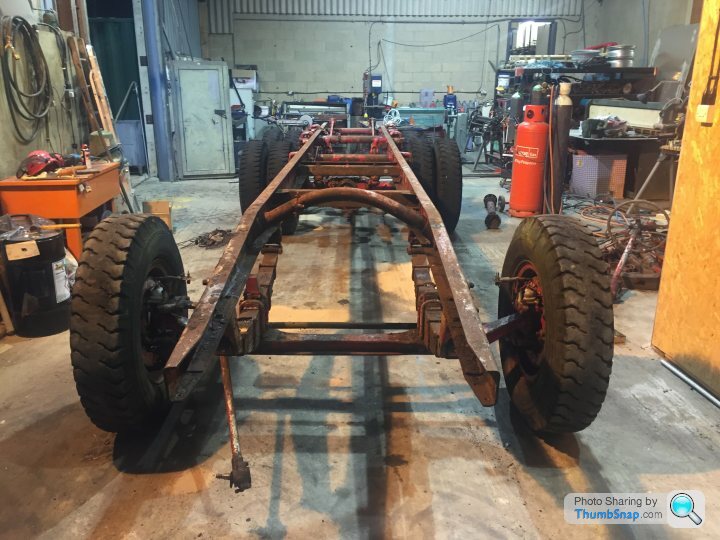
The pile of parts to keep is still small, and everything still on the frame will join that pile eventually.
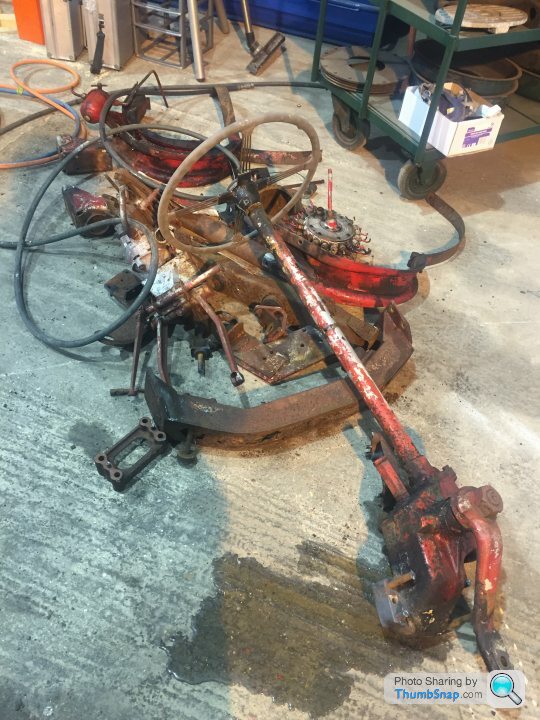
There are one or two areas that will need to be cut out and replaced but they are small parts, mainly the bottom of the channel.

It was built to cope with a vehicle that weighed around 20 tonnes and is 8mm thick, so if there are small areas where is now 5mm thick I don't see it as an issue. The tester may have different ideas, so I will need to check.
Once the chassis is stripped then I will go over the whole thing with a needle gun before sand blasting.
Not exactly fun but ultimately satisfying.
Paul
The number of bolt holes in the chassis is growing every time I fire up the gas axe!
It is now just a rolling chassis and it still weighs about 2.75 to 3 tonnes, judging by the way my forklift struggled (successfully) to lift it!

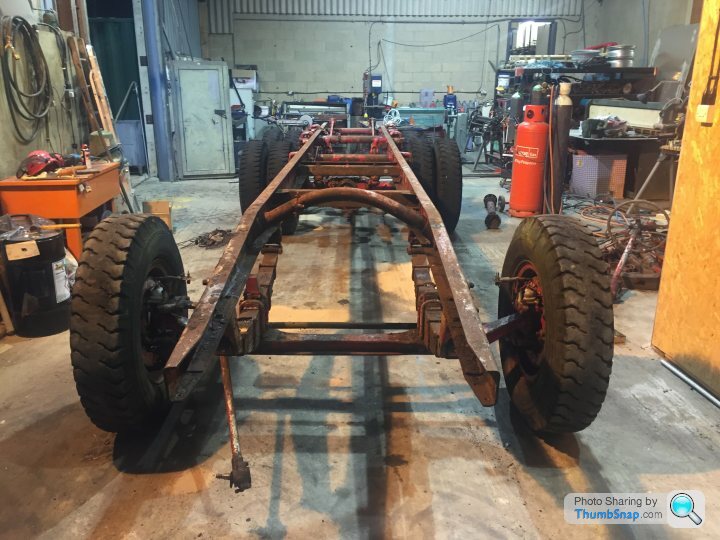
The pile of parts to keep is still small, and everything still on the frame will join that pile eventually.
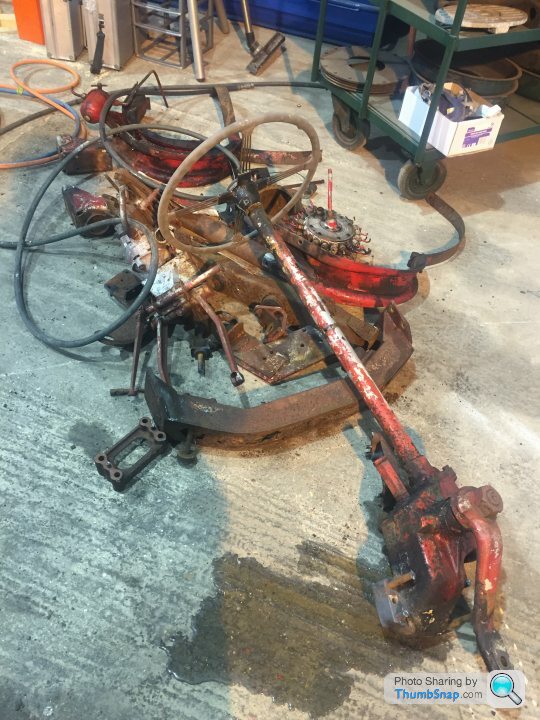
There are one or two areas that will need to be cut out and replaced but they are small parts, mainly the bottom of the channel.

It was built to cope with a vehicle that weighed around 20 tonnes and is 8mm thick, so if there are small areas where is now 5mm thick I don't see it as an issue. The tester may have different ideas, so I will need to check.
Once the chassis is stripped then I will go over the whole thing with a needle gun before sand blasting.
Not exactly fun but ultimately satisfying.
Paul
There will be no way it will be under 3.5t.
The engine and transmission will add at least a tonne. There will probably be 100kgs of oil and water. 200kgs of fuel. Plus the tanks and radiator etc.
That is before we even consider a body.
Alloy wheels will help but I suspect the kit required for airbag suspension will equal the weight drop when the springs are removed.
Items like the steering box are as much as I can lift!!!
I have a sneaking suspicion it will be close to 6 tonnes.
No progress today but some time spent on research.
Paul
The engine and transmission will add at least a tonne. There will probably be 100kgs of oil and water. 200kgs of fuel. Plus the tanks and radiator etc.
That is before we even consider a body.
Alloy wheels will help but I suspect the kit required for airbag suspension will equal the weight drop when the springs are removed.
Items like the steering box are as much as I can lift!!!
I have a sneaking suspicion it will be close to 6 tonnes.
No progress today but some time spent on research.
Paul
Only a bit of investigations on the rear hubs today.
I need to find out what the gearing ratios in the hub and diff are so that Charlie can engineer the engine/gearbox mount/speed 'increaser'.
So first challenge was to remove the wheel nuts. Being a truck they are tight anyway, but rusty threads prevented the 1" drive air wheel gun shifting them!
So out with my favourite tool - gas torch.
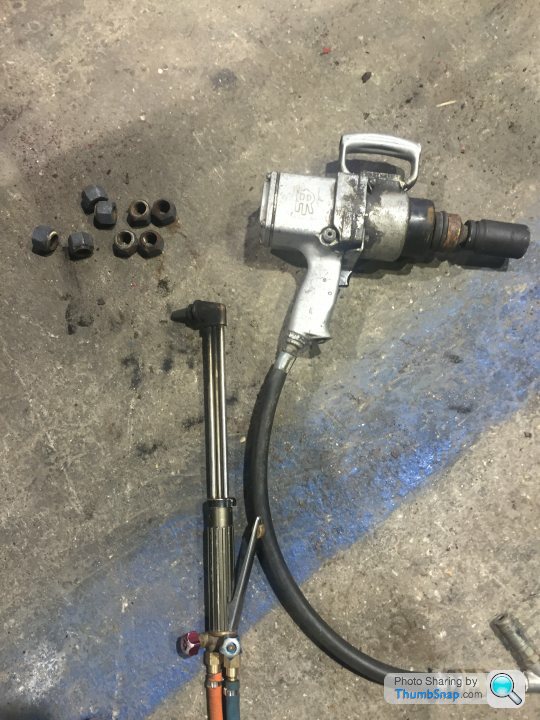
Heat on your nuts makes all the difference! Got them glowing orange and the air gun spun them off fine.
The wheels didn't fight me at all, much to my surprise.
The hubs seem to have a reduction gear inside and appear to be bolted on to the axle. I hope to be able to remove the hub completely along with the brake drum. That will allow me to fabricate new hubs and add disc brakes.
New hubs will also give more choice in wheel size and style.

I will know more when I get it all apart.
Paul
I need to find out what the gearing ratios in the hub and diff are so that Charlie can engineer the engine/gearbox mount/speed 'increaser'.
So first challenge was to remove the wheel nuts. Being a truck they are tight anyway, but rusty threads prevented the 1" drive air wheel gun shifting them!
So out with my favourite tool - gas torch.
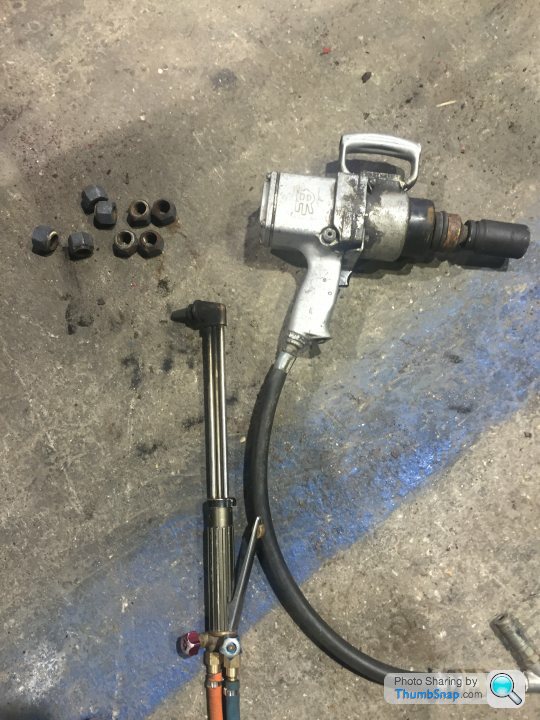
Heat on your nuts makes all the difference! Got them glowing orange and the air gun spun them off fine.
The wheels didn't fight me at all, much to my surprise.
The hubs seem to have a reduction gear inside and appear to be bolted on to the axle. I hope to be able to remove the hub completely along with the brake drum. That will allow me to fabricate new hubs and add disc brakes.
New hubs will also give more choice in wheel size and style.

I will know more when I get it all apart.
Paul
Max_Torque said:
Are you going to ditch the steering box? I'd look at fitting a rack directly to the axle maybe? Pick a nice beefy rack off a large Van or Rangey or similar! Will make the steering a lot nicer than through the original s/box.......
You are not the first to suggest a rack and pinion steering solution.At present I am not sure. I like the 'old world' look of the current system and would just add power assistance. But I also know that a rack would produce better steering control.
It is worth remembering that with a vehicle of this size (and weight) component will need to be 'up to the job'. My background also allows me to look at tractor/agricultural components as solutions. So we could be talking totally hydraulic steering (though probably not!).
Most things are still rather fluid. I will be lowering the chassis but trying to keep the wheel height to try and get the look right.
Hopefully I will get time to do a bit more as the week progresses.
Paul
The more I get into it the more likely it is that it will require an IVA test (bugger). But at least it will be seen as safe on the road.
Today's little bit of work has seen the 1st axle removed.
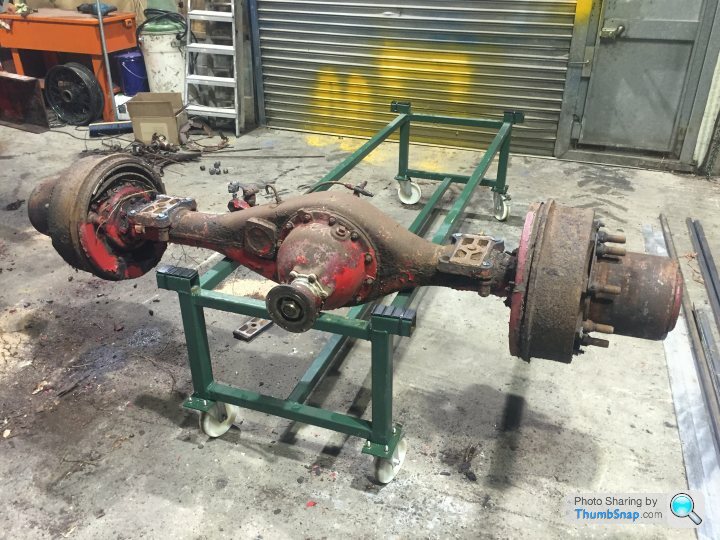

Each wheel weight too much for me to lift so hopefully new alloys will save a bit. The brake drums are rather beefy too.
Paul
Today's little bit of work has seen the 1st axle removed.
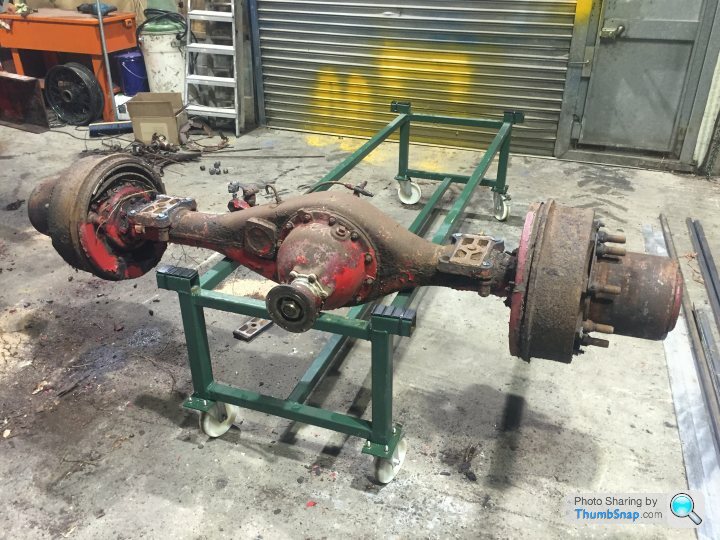

Each wheel weight too much for me to lift so hopefully new alloys will save a bit. The brake drums are rather beefy too.
Paul
Edited by Storer on Thursday 17th November 23:01
Hi Steve
The current drum brakes are rod over hydraulic operation. The pedal acts on a hydraulic servo which then moves rods that work the brakes. Not the most positive of systems!
Also, I suspect discs will be a bit lighter and easier to balance between the axles with adjustable valves. As I am modifying the suspension, a hose connection to route and connect will also be easier.
I have yet to finish stripping off a drum to see exactly what is inside but I hope to remove any reduction gearing in the hub. I have an owners manual on it's way (from Australia!!) to help with the build.
Paul
The current drum brakes are rod over hydraulic operation. The pedal acts on a hydraulic servo which then moves rods that work the brakes. Not the most positive of systems!
Also, I suspect discs will be a bit lighter and easier to balance between the axles with adjustable valves. As I am modifying the suspension, a hose connection to route and connect will also be easier.
I have yet to finish stripping off a drum to see exactly what is inside but I hope to remove any reduction gearing in the hub. I have an owners manual on it's way (from Australia!!) to help with the build.
Paul
A couple of hours this evening investigating...

A sturdy, quite clean diff. There is a tiny amount of surface rust on parts that were not covered in the very thick gear oil.

This is the hub with the 3 planetary reduction gears. It is all in great condition, not that I want to keep it.
All splines on the beefy half shaft look almost new.
Next job is to remove the rest of the hub and brakes to see what is left to work with.

I find I still need my thermal spanner to shift many of the nuts that were exposed to the elements, but anything protected comes off with a spanner/air gun easily.
Until the manual arrives I am working blind as I have no idea how it all comes apart!
Paul

A sturdy, quite clean diff. There is a tiny amount of surface rust on parts that were not covered in the very thick gear oil.

This is the hub with the 3 planetary reduction gears. It is all in great condition, not that I want to keep it.
All splines on the beefy half shaft look almost new.
Next job is to remove the rest of the hub and brakes to see what is left to work with.

I find I still need my thermal spanner to shift many of the nuts that were exposed to the elements, but anything protected comes off with a spanner/air gun easily.
Until the manual arrives I am working blind as I have no idea how it all comes apart!
Paul
Edited by Storer on Sunday 20th November 21:15
Bit of progress today (weather too crap to be outside!) stripping the axle.
An empty axle with diff and half shafts removed.

Brake drum removed.
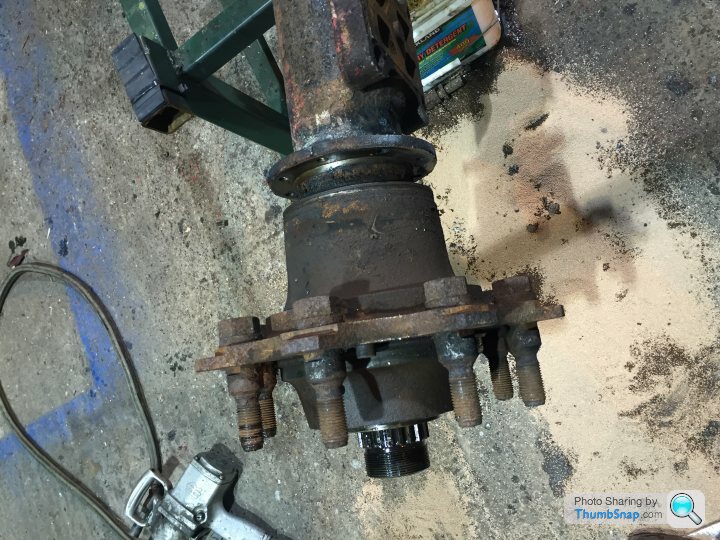
The diff out of the axle.

Splitting the first hub/brake drum was a case of a shot in the dark. The second was easy once I knew how it was assembled.
The thermal spanner is still busy helping shift difficult nuts/bolts and I have just ordered a 2" AF socket. My 2" combination spanner just wouldn't fit.
The socket will release the nut on the input shaft for the diff. The bearing on the input shaft appears to be locked as the diff will not turn. I can't see any issue in the diff so I suspect the input bearing.
The hub bearings are all straight forward taper roller bearings so easy to replace (hopefully).
Now the drum is off it is possible to see how much room is available to fit disc brakes. I think it is totally possible and reasonably easy to do.
Paul
PS. Once diff is mobile I will be able to calculate the ratio and work out what changes we will need for the engine to gearbox connector.
An empty axle with diff and half shafts removed.

Brake drum removed.
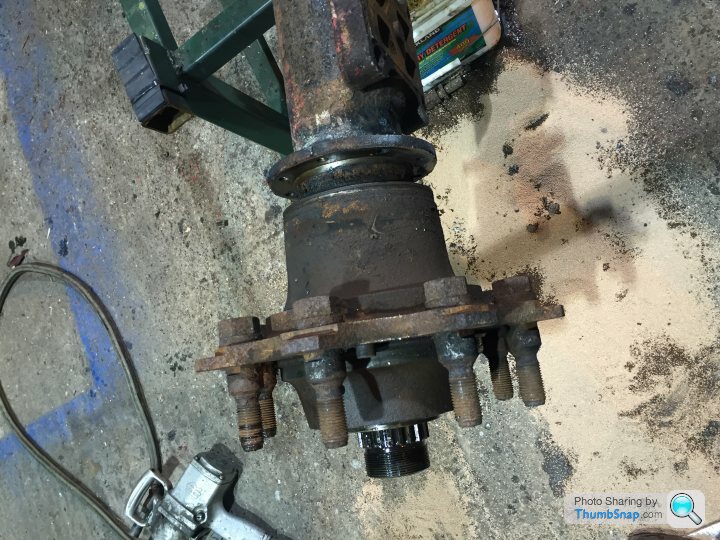
The diff out of the axle.

Splitting the first hub/brake drum was a case of a shot in the dark. The second was easy once I knew how it was assembled.
The thermal spanner is still busy helping shift difficult nuts/bolts and I have just ordered a 2" AF socket. My 2" combination spanner just wouldn't fit.
The socket will release the nut on the input shaft for the diff. The bearing on the input shaft appears to be locked as the diff will not turn. I can't see any issue in the diff so I suspect the input bearing.
The hub bearings are all straight forward taper roller bearings so easy to replace (hopefully).
Now the drum is off it is possible to see how much room is available to fit disc brakes. I think it is totally possible and reasonably easy to do.
Paul
PS. Once diff is mobile I will be able to calculate the ratio and work out what changes we will need for the engine to gearbox connector.
Hi all.
Should have been a little more accurate with my measurement on the shaft nut on the differential. It is not 2" AF (51mm approx.) but 1 1/4" Whitworth (52.77mm) - bugger.
The correct socket is now ordered as none of my mates has that size locally. It is a wince moment at £100.00
but there are 7 nuts that size which will need it over a prolonged period. The vehicle seems to be a mixture of Whitworth and AF which I suppose is par for the course at that age.
My thermal spanner has been coping with both again today with the rear axle hangers removed completely. I had hoped to remove them so they could be sold and re-used by a truck restorer but that orange devil had other ideas and I am getting too old to waste time for a 'possible' few quid. So the scrap pile grows....

I have started degreasing some of the parts that will be reused. Some will get light oiling then storage and others will get sandblasted then primed.
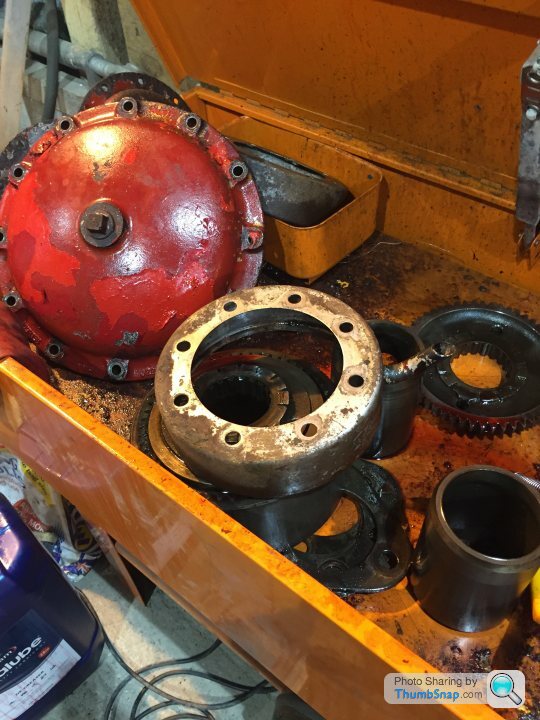
I am looking forward to retiring the thermal spanner soon, as each day I switch off the lights in the workshop there is a 'fog' of smoke from burnt paint, rust and detritus.
Hopefully tomorrow will see another axle removed.
Paul
Should have been a little more accurate with my measurement on the shaft nut on the differential. It is not 2" AF (51mm approx.) but 1 1/4" Whitworth (52.77mm) - bugger.
The correct socket is now ordered as none of my mates has that size locally. It is a wince moment at £100.00

My thermal spanner has been coping with both again today with the rear axle hangers removed completely. I had hoped to remove them so they could be sold and re-used by a truck restorer but that orange devil had other ideas and I am getting too old to waste time for a 'possible' few quid. So the scrap pile grows....

I have started degreasing some of the parts that will be reused. Some will get light oiling then storage and others will get sandblasted then primed.
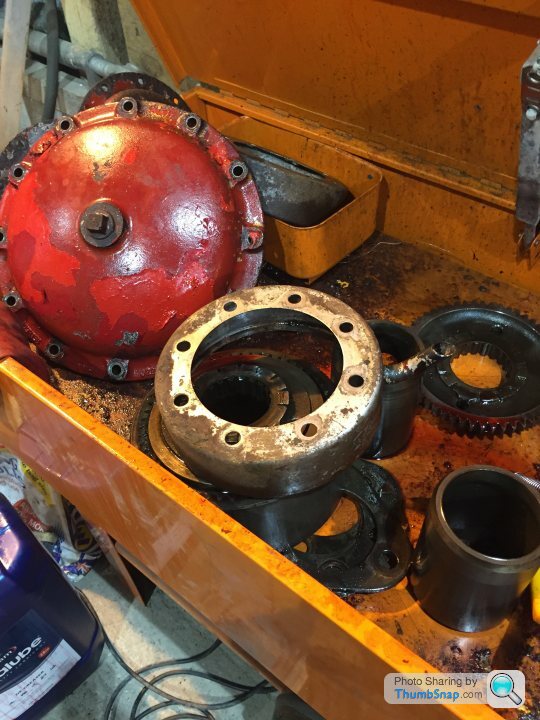
I am looking forward to retiring the thermal spanner soon, as each day I switch off the lights in the workshop there is a 'fog' of smoke from burnt paint, rust and detritus.
Hopefully tomorrow will see another axle removed.
Paul
"Two wheels on my waggon"
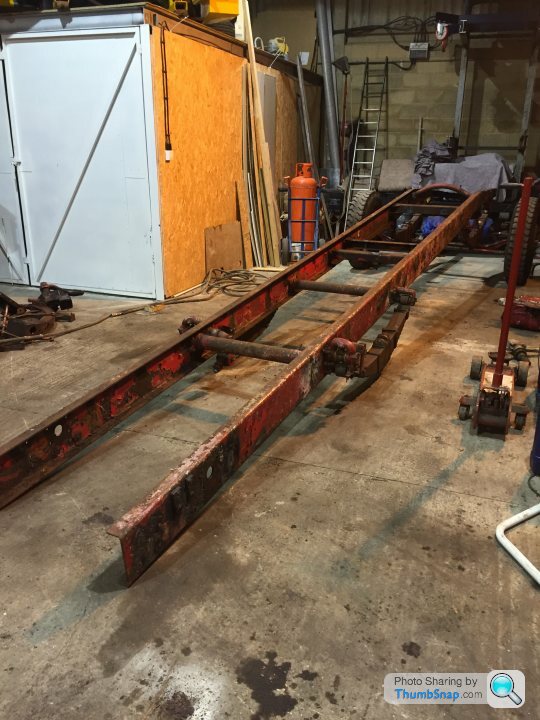

And my new impact socket arrived.....

For that price it should have been gold plated at the very least!
But it worked.

When I get bored using the thermal spanner I can now start the de-greasing and media blasting. The result is quite gratifying despite the task being rather tedious.

Before I send the axle ratios to Charlie to build the engine adaptor I want to open the drive splitter box to check it has no reduction effect.

Robert
I am planning on creating a 4 link suspension system from scratch using air springs and a damper with either a panhrd rod or a triangulated top link. I have no need for the existing setup.
Paul
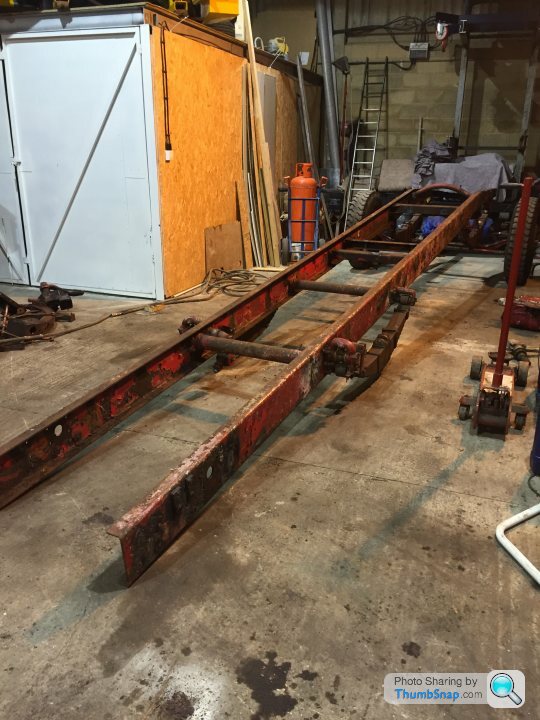

And my new impact socket arrived.....

For that price it should have been gold plated at the very least!
But it worked.

When I get bored using the thermal spanner I can now start the de-greasing and media blasting. The result is quite gratifying despite the task being rather tedious.

Before I send the axle ratios to Charlie to build the engine adaptor I want to open the drive splitter box to check it has no reduction effect.

Robert
I am planning on creating a 4 link suspension system from scratch using air springs and a damper with either a panhrd rod or a triangulated top link. I have no need for the existing setup.
Paul
Bit of deja-vous today.
Another axle strip down.

The oil runs were where I slackened the bolts on the diff and turned it over. Then decided I should tip it back over and drain it....
Everything still looking good inside. Small areas of surface corrosion, as could be expected considering the 20+ years it has been standing with the rear wheels locked. The bearings look surprisingly good but they will get changed. Oil seals have gone hard and must be replaced.
Also had my top off today

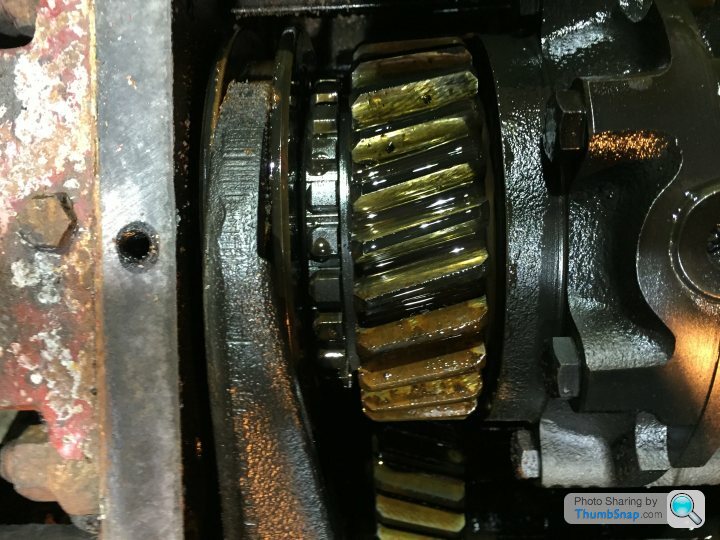
Corrosion is more of an issue inside but a strip down will determine what can be saved. It is interesting that the box rotates the drive shafts to the diffs backwards compared with engine direction.
Also interesting that the box allows selection of either 2wd or 4wd with the rear axle constantly driven with the middle one selectable. Uses air pressure to overcome a spring to maintain 4wd.
Importantly one input rotation equals one output rotation, so no reduction, which is good.
Now need to sit down and calculate the gear ratios.
It may be I will not need to increase engine speed. If so those nice big gears will get the full 1500ftlbs!
Paul
Another axle strip down.

The oil runs were where I slackened the bolts on the diff and turned it over. Then decided I should tip it back over and drain it....
Everything still looking good inside. Small areas of surface corrosion, as could be expected considering the 20+ years it has been standing with the rear wheels locked. The bearings look surprisingly good but they will get changed. Oil seals have gone hard and must be replaced.
Also had my top off today

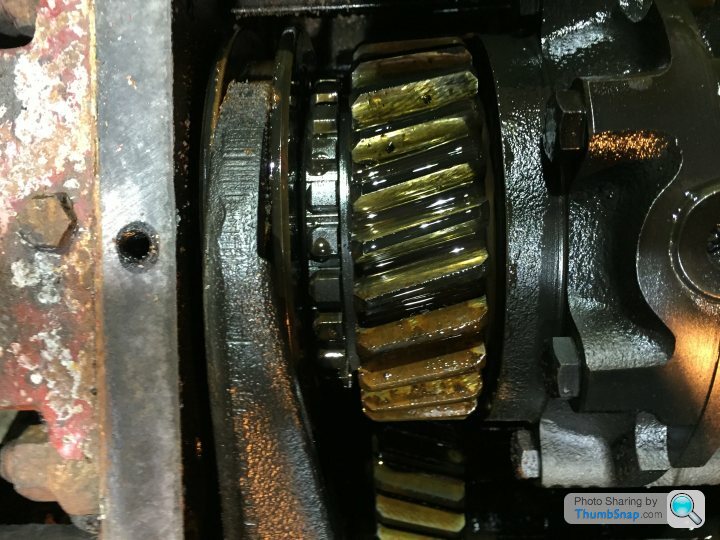
Corrosion is more of an issue inside but a strip down will determine what can be saved. It is interesting that the box rotates the drive shafts to the diffs backwards compared with engine direction.
Also interesting that the box allows selection of either 2wd or 4wd with the rear axle constantly driven with the middle one selectable. Uses air pressure to overcome a spring to maintain 4wd.
Importantly one input rotation equals one output rotation, so no reduction, which is good.
Now need to sit down and calculate the gear ratios.
It may be I will not need to increase engine speed. If so those nice big gears will get the full 1500ftlbs!
Paul
These are the half shafts...
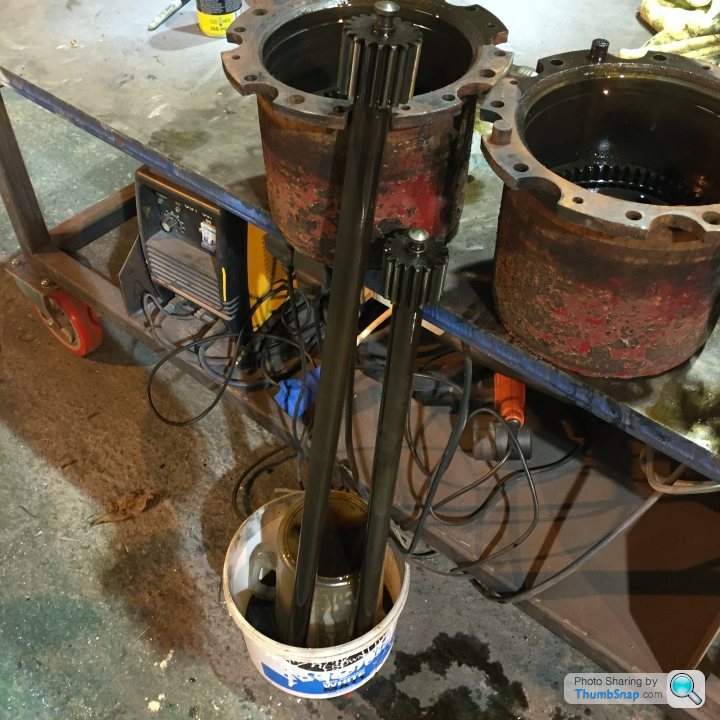
Remember that these parts are from a lorry built to carry 16 tonnes and weigh well over 20 tonnes.
The bearings are around 5" diameter and 2" deep. Even with the 'car' weighing around 6 tonnes it will just spin the rear wheels and smoke the tyres. I suspect I will only lock the second axle if I get stuck. But at least the torque will be split between the two.
It is difficult to get a feel for how substantial everything is from the photos.
Paul
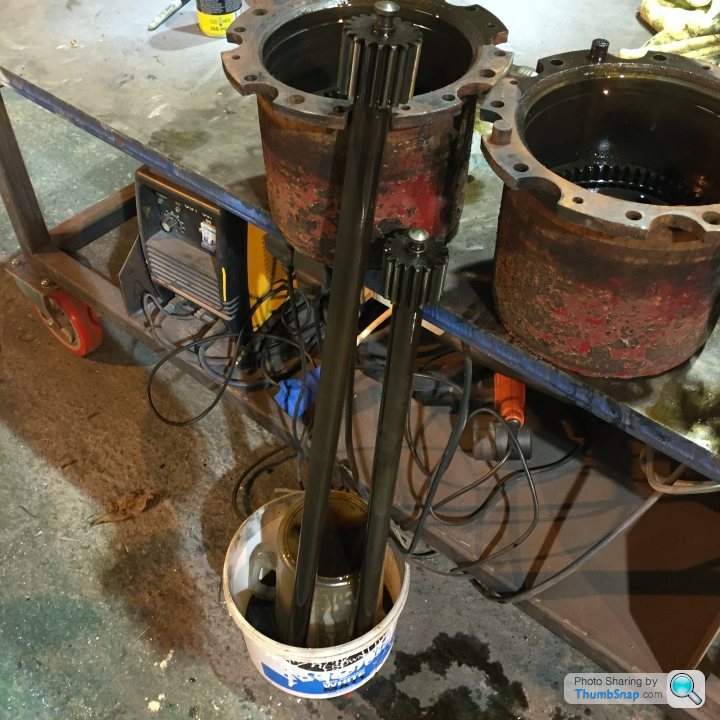
Remember that these parts are from a lorry built to carry 16 tonnes and weigh well over 20 tonnes.
The bearings are around 5" diameter and 2" deep. Even with the 'car' weighing around 6 tonnes it will just spin the rear wheels and smoke the tyres. I suspect I will only lock the second axle if I get stuck. But at least the torque will be split between the two.
It is difficult to get a feel for how substantial everything is from the photos.
Paul
No wheels on my chassis!
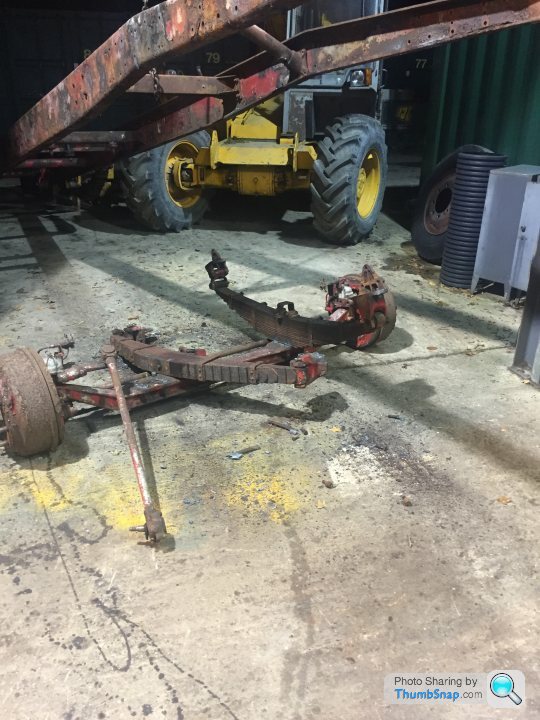
The workshop is a little emptier as I have stashed the bits away. They will come back out for cleaning/blasting and painting or refurbishment.
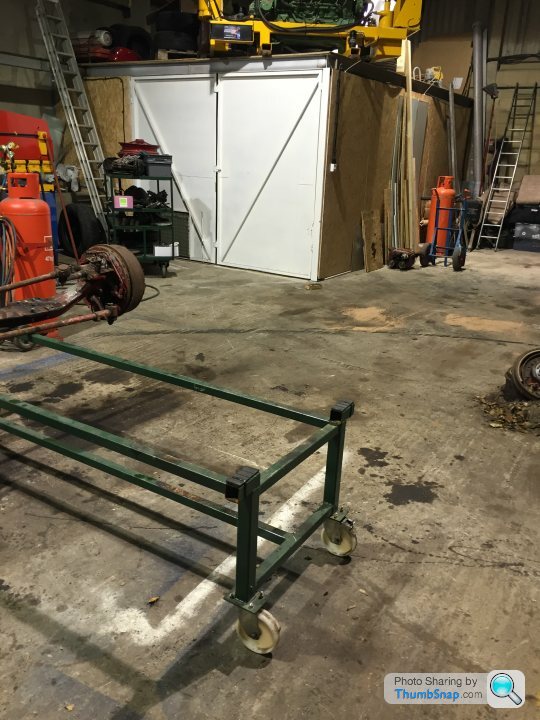
There will be a slow down on progress for a few days due to other commitments.
Some things that have become known now are.
Due to not using the reduction gears in the hubs the axles will need to be turned over to get wheel rotation correct.
This will necessitate the middle axle being the permanent driven one with the rear switchable.
It will not need a gizmo to increase engine speed, just a connection adaptor between engine and transmission.
Some interesting calculated stats are:-
300rpm in 1st = 8.18mph
750rpm in 2nd = 34 mph
500rpm in 3rd(top) = 33mph
1000rpm in 3rd = 67.6mph
1500rpm in 3rd = 101.4mph
2000rpm in 3rd = 135.2mph
2500rpm in 3rd = 169mph
Obviously the 2 fastest of those speeds are likely to be totally academic. But it will do over 100mph in second, which is nice!
I am not building a speed machine, this is about the theatre and challenging myself to build it.
The good thing is that I will not be artificially reducing the power/torque. The mass of gears and thick oil will do that for me!
Tyres are not going to be truck super singles as they are only rated to 75mph so I will be looking to our American cousins for suitable rubber to give the same rolling circumference.
It also maintains the aesthetics in my opinion.
Paul
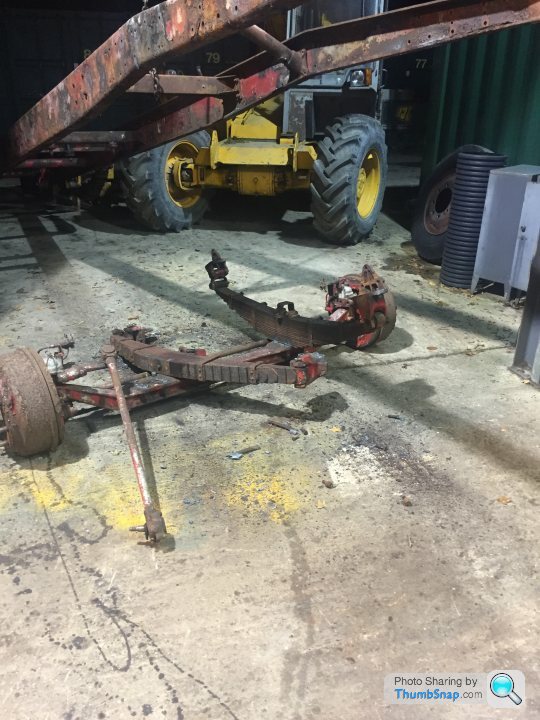
The workshop is a little emptier as I have stashed the bits away. They will come back out for cleaning/blasting and painting or refurbishment.
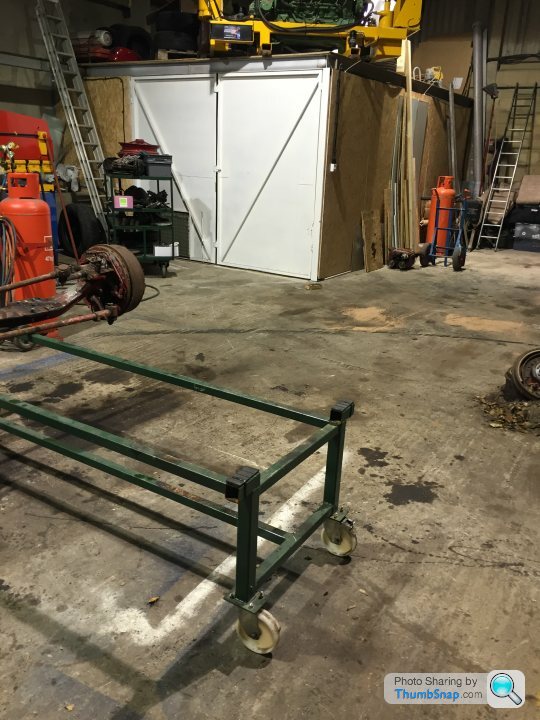
There will be a slow down on progress for a few days due to other commitments.
Some things that have become known now are.
Due to not using the reduction gears in the hubs the axles will need to be turned over to get wheel rotation correct.
This will necessitate the middle axle being the permanent driven one with the rear switchable.
It will not need a gizmo to increase engine speed, just a connection adaptor between engine and transmission.
Some interesting calculated stats are:-
300rpm in 1st = 8.18mph
750rpm in 2nd = 34 mph
500rpm in 3rd(top) = 33mph
1000rpm in 3rd = 67.6mph
1500rpm in 3rd = 101.4mph
2000rpm in 3rd = 135.2mph
2500rpm in 3rd = 169mph
Obviously the 2 fastest of those speeds are likely to be totally academic. But it will do over 100mph in second, which is nice!
I am not building a speed machine, this is about the theatre and challenging myself to build it.
The good thing is that I will not be artificially reducing the power/torque. The mass of gears and thick oil will do that for me!
Tyres are not going to be truck super singles as they are only rated to 75mph so I will be looking to our American cousins for suitable rubber to give the same rolling circumference.
It also maintains the aesthetics in my opinion.
Paul
Gassing Station | Readers' Cars | Top of Page | What's New | My Stuff