Rover 200 BRM - 1.8 K-Series turbo project
Discussion
Jeez you'll be cutting it a bit fine with those figures!
I would've thought the chunky looking rods and light pistons you've got would have allowed you to run considerably tighter squish.
Drilling the rods would be done along it's length, with a drilled bearing to match.
This would allow pressurised oil to run up to the gudgeon pin and cool that area.
I think squirters would be a better option though as they have usually valves built in to shut off flow when oil pressure is low.
On the subject of oil flow is there anything to do to improve it while it's all apart, like porting the oil pump?
I would've thought the chunky looking rods and light pistons you've got would have allowed you to run considerably tighter squish.
Drilling the rods would be done along it's length, with a drilled bearing to match.
This would allow pressurised oil to run up to the gudgeon pin and cool that area.
I think squirters would be a better option though as they have usually valves built in to shut off flow when oil pressure is low.
On the subject of oil flow is there anything to do to improve it while it's all apart, like porting the oil pump?
Luther Blisset said:
Jeez you'll be cutting it a bit fine with those figures!
I would've thought the chunky looking rods and light pistons you've got would have allowed you to run considerably tighter squish.
Drilling the rods would be done along it's length, with a drilled bearing to match.
This would allow pressurised oil to run up to the gudgeon pin and cool that area.
I think squirters would be a better option though as they have usually valves built in to shut off flow when oil pressure is low.
On the subject of oil flow is there anything to do to improve it while it's all apart, like porting the oil pump?
The gasket is the deciding factor with the squish. I've done a bit of measuring. The thinnest gasket I can use (and will use) is the elastomer. A new gasket uncompressed measures 2mm at the fire rings. A used one I have here measures 1.4mm. I'm assuming there's further compression when it's under load from the heat bolts but no way to know without measuring once the head is on. Reckon I'll be lucky if it compresses to 1mm.I would've thought the chunky looking rods and light pistons you've got would have allowed you to run considerably tighter squish.
Drilling the rods would be done along it's length, with a drilled bearing to match.
This would allow pressurised oil to run up to the gudgeon pin and cool that area.
I think squirters would be a better option though as they have usually valves built in to shut off flow when oil pressure is low.
On the subject of oil flow is there anything to do to improve it while it's all apart, like porting the oil pump?
The piston sits 0.2mm below the liners. So best case is 1.2mm which is be happy with.
I can't find anyone who's modified the k-series with oil squirters. I wouldn't know there was a problem though until the bottom end failed. If it was a tried and tested mod I would do it, but I'm not going for mega power so will probably leave as-is. Although I have to admit I didn't know they had valves built in...
Did a bit of porting on the oil pump last time around:
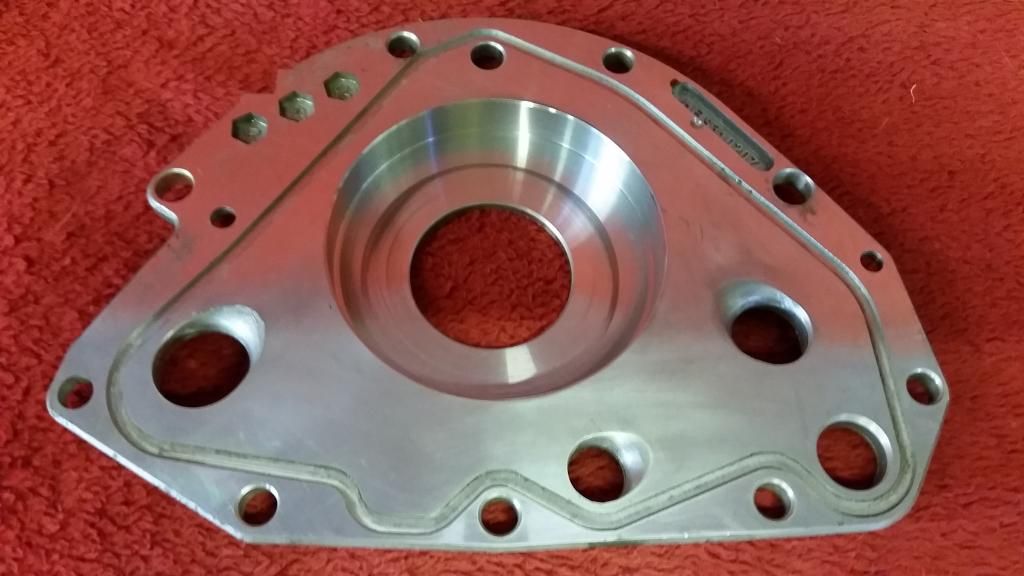
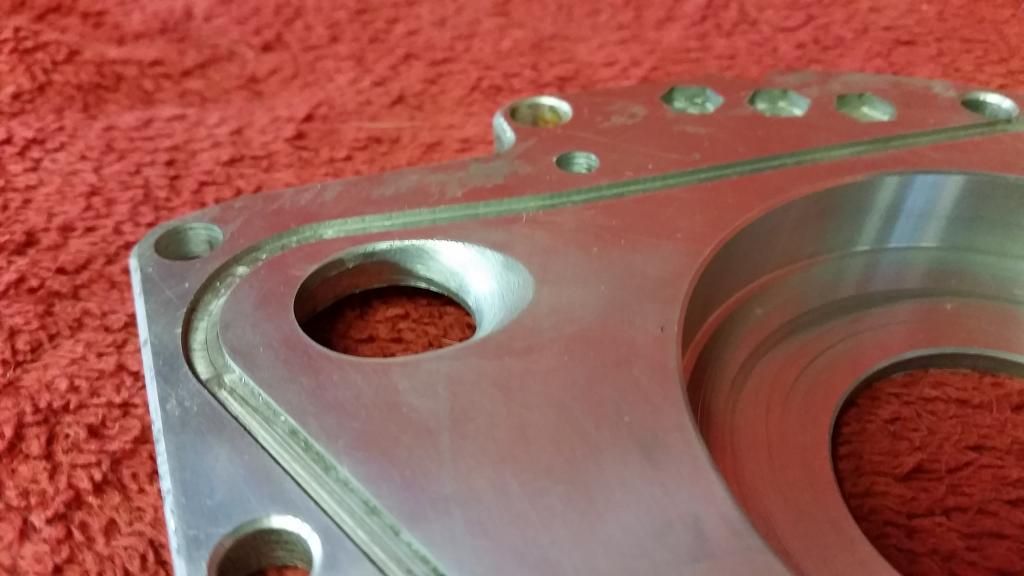
TotalControl said:
Love the work going into this OP. I've wondered if it would ever be worthwhile transplanting a K20A in there instead? Although I admire your perseverance to keep the original K series in there.
Thanks. There are probably a few other options (Honda, Audi, Ford) but anything else would have required fabricating engine mounts, gearbox adapters and possibly driveshafts which I couldn't have done myself. As you say I also wanted to stick with the brand. I must admit though, I've questioned that decision more than once in the last few months! I don't regret anything. I've learned a lot which is the whole point of this project. But what has really tripped me up is what I don't know I don't know. This sums up engine building and tuning for me:

You're a brave man to run that CR. Too late now, but I would have recommended getting someone with a lathe to deepen the bowl in the centre. If you pull it off at least you'll get good MPG!
Definitely keep the squish as tight as you can, as said before it contributes to det' when too big.
Definitely keep the squish as tight as you can, as said before it contributes to det' when too big.
227bhp said:
You're a brave man to run that CR. Too late now, but I would have recommended getting someone with a lathe to deepen the bowl in the centre. If you pull it off at least you'll get good MPG!
Definitely keep the squish as tight as you can, as said before it contributes to det' when too big.
I may be wrong about CR. I need to crunch the numbers again. That said, with a thinner head gasket than before, and a less-dished piston, it'll clearly be a fair amount higher than the 9:1 I had before. Time will tell though. Initial setup will be very low boost with super conservative ignition while I run the engine in. And of course I'll make sure my mapper has an acceptable method for directing detonation! Definitely keep the squish as tight as you can, as said before it contributes to det' when too big.
Nice work on the oil pump, not sure about your specific case but head gaskets are advertised at their compressed thickness which will obviously be less than whatever thickness measured before it's installed.
So do your calcs based on that advertised number.
I'd definitely want under 1mm and I think it's achievable with those pistons and rods assuming they're something like EN24 grade you could probably go as tight as 0.7mm.
Not telling you what to do though OP, it's your build and a very tidy one too.
So do your calcs based on that advertised number.
I'd definitely want under 1mm and I think it's achievable with those pistons and rods assuming they're something like EN24 grade you could probably go as tight as 0.7mm.
Not telling you what to do though OP, it's your build and a very tidy one too.
So I've hit a problem. I just measured everything properly and worked out my static compression ratio and it's 12:1!
Conventional wisdom suggests this is simply too high for a turbo build.
I have a few options:
1. Build it anyway and see how it goes mapping with low boost (~5psi) hoping my slightly-wilder-than-stock Cams (260 degree duration vs 248 - and 1mm more lift) lower my dynamic CR enough for it to work.
2. Remove some material from the pistons (as suggested above) and the combustion chamber. Finding another 2cc from each piston and 4cc from each combustion chamber gets me back down to near 10:1
3. Fit water/meth injection.
4. Fit the shorter (-2mm) turbo-spec rods - adding 2mm to the squish clearance and increasing the rod angle
5. Set fire to it.
I'm still half suspecting I'm calculating something wrong. Although the numbers and calcs have been verified by someone else. I don't know how it's so far of from the 9.5:1 they are advertised as.
Shorter rods feels like a bodge and it's the easy way out. It would increase squish clearance to over 3mm. I might take a die grinder to my spare (scrap) head and see how much material can be safely removed. If the answer is "not much" then I'll look into modifying the pistons.
Conventional wisdom suggests this is simply too high for a turbo build.
I have a few options:
1. Build it anyway and see how it goes mapping with low boost (~5psi) hoping my slightly-wilder-than-stock Cams (260 degree duration vs 248 - and 1mm more lift) lower my dynamic CR enough for it to work.
2. Remove some material from the pistons (as suggested above) and the combustion chamber. Finding another 2cc from each piston and 4cc from each combustion chamber gets me back down to near 10:1
3. Fit water/meth injection.
4. Fit the shorter (-2mm) turbo-spec rods - adding 2mm to the squish clearance and increasing the rod angle
5. Set fire to it.
I'm still half suspecting I'm calculating something wrong. Although the numbers and calcs have been verified by someone else. I don't know how it's so far of from the 9.5:1 they are advertised as.
Shorter rods feels like a bodge and it's the easy way out. It would increase squish clearance to over 3mm. I might take a die grinder to my spare (scrap) head and see how much material can be safely removed. If the answer is "not much" then I'll look into modifying the pistons.
Had a play with a scrap vvc head I have here. Should be able to remove enough material from combustion chamber to bring volume up from 30cc to 37cc. That'll lower compression ratio to 10.5:1.
So the plan is to do that and leave the rod length as it is and run-in on 5psi boost. If I fancy running high boost later, I will run water or water/meth injection.
As part of the rebuild I'm going to do everything i can to lower intake temps such as rerouting the intercooler pipework and relocating the air filter.
Busy day with the die-grinder tomorrow!
So the plan is to do that and leave the rod length as it is and run-in on 5psi boost. If I fancy running high boost later, I will run water or water/meth injection.
As part of the rebuild I'm going to do everything i can to lower intake temps such as rerouting the intercooler pipework and relocating the air filter.
Busy day with the die-grinder tomorrow!
Stuballs said:
So I've hit a problem. I just measured everything properly and worked out my static compression ratio and it's 12:1!
Conventional wisdom suggests this is simply too high for a turbo build.
'Kinell, that's very high for an NA, IIRC Mk1/2 MX5s are circa 9:1.Conventional wisdom suggests this is simply too high for a turbo build.
Show us a pic of a head which has been ground out, you need a thickness tester when taking that much out and be careful you aren't creating pockets for fuel which won't burn properly. That's a sh!tload of metal to lose.
Likewise you need to test thickness when dishing NA pistons to make them turbo, it can only be done when there is enough to remove safely.
Have you got dished valve heads? A small amount can be gained there, also by sinking them in deeper. Not ideal, but at this level worth considering. It's a shame the pistons are coated because the best way is to pinch a bit from everywhere you can.
You need to be confident in your head, block and stud strength before running boost and WI otherwise you'll warp and bend stuff or just lift the head, have the gasket leak etc and from what i've seen the K series isn't particularly strong in any respect.
Edited by 227bhp on Saturday 13th August 23:33
227bhp said:
'Kinell, that's very high for an NA, IIRC Mk1/2 MX5s are circa 9:1.
Show us a pic of a head which has been ground out, you need a thickness tester when taking that much out and be careful you aren't creating pockets for fuel which won't burn properly. That's a sh!tload of metal to lose.
Likewise you need to test thickness when dishing NA pistons to make them turbo, it can only be done when there is enough to remove safely.
Have you got dished valve heads? A small amount can be gained there, also by sinking them in deeper. Not ideal, but at this level worth considering. It's a shame the pistons are coated because the best way is to pinch a bit from everywhere you can.
You need to be confident in your head, block and stud strength before running boost and WI otherwise you'll warp and bend stuff or just lift the head, have the gasket leak etc and from what i've seen the K series isn't particularly strong in any respect.
Thanks for the reply and totally agree with everything you say. The REC inlet valves are slightly dished. But I have standard exhaust valves and replacing those who cost a small fortune. Sinking them could gain a cc but then I'd need custom made shorter valves.Show us a pic of a head which has been ground out, you need a thickness tester when taking that much out and be careful you aren't creating pockets for fuel which won't burn properly. That's a sh!tload of metal to lose.
Likewise you need to test thickness when dishing NA pistons to make them turbo, it can only be done when there is enough to remove safely.
Have you got dished valve heads? A small amount can be gained there, also by sinking them in deeper. Not ideal, but at this level worth considering. It's a shame the pistons are coated because the best way is to pinch a bit from everywhere you can.
You need to be confident in your head, block and stud strength before running boost and WI otherwise you'll warp and bend stuff or just lift the head, have the gasket leak etc and from what i've seen the K series isn't particularly strong in any respect.
Edited by 227bhp on Saturday 13th August 23:33
Picture of the rough cut below. I kept the shape of the chamber as close to original add possible. It's lucky the bore has increased from 80mm to 82mm as that has allowed me to pinch material from the edges.
I haven't thickness tested but after I finished the test on the scrap head I drilled loads of holes to ree how much material there was at various points and to make sure I want close to breaking through to any hollows in the casting. I found there to be loads of meat.
Look how much the plug threads protrude through. I've always thought that odd (I left the central bump around the plug alone save as to smooth it out). I was wondering how important electrode position is and if it's possible to run a plug with shorter thread.
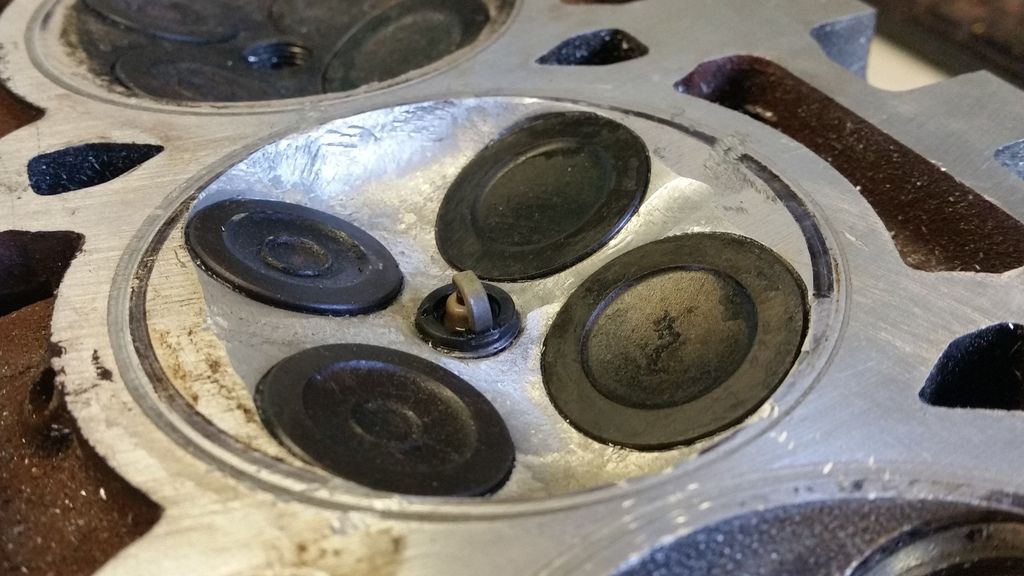
Run with the long plugs, but take the last few threads off the plugs and make sure you remove the last thread in the head! High CR on turbo's is not, in itself an issue, as long as you run sensible boost pressures at low/mid rpm and have it nicely mapped. Full house WRC engines run just under 12:1 on a 34mm restricted (ie high internal EGR) turbo running 3 bar of boost! (but they have had a LOT of combustion development)
as you are just 2wd, there is no point throwing massive boost at the thing at low rpm (say 3krpm) because you just won't be able to put the torque on the ground anyway. And when you get up the gear box and are going fast, then you'll also be up the rev range and at peak power, where the high static CR means you can run low boost and still make good power. Added to which, the ratio of N/A to Boosted torque will be more favourable, reducing lag and making the car drive really nicely (ie you should be able to accurately modulate torque across the full load threshold).
I did exactly the same thing for the engine in my tarmac rally car, optimising the engine for high rpm power rather than low rpm torque (because i'm 2wd too, unlike the 4wd WRC cars that go faster the more torque you give them, whereas my car just goes sideways and wrecks the rear tyres ;-) ) I run water injection in the high boost "stage" mode, but i'm running 2.6bar gauge at 7800rpm on a CR in the high 11s
as you are just 2wd, there is no point throwing massive boost at the thing at low rpm (say 3krpm) because you just won't be able to put the torque on the ground anyway. And when you get up the gear box and are going fast, then you'll also be up the rev range and at peak power, where the high static CR means you can run low boost and still make good power. Added to which, the ratio of N/A to Boosted torque will be more favourable, reducing lag and making the car drive really nicely (ie you should be able to accurately modulate torque across the full load threshold).
I did exactly the same thing for the engine in my tarmac rally car, optimising the engine for high rpm power rather than low rpm torque (because i'm 2wd too, unlike the 4wd WRC cars that go faster the more torque you give them, whereas my car just goes sideways and wrecks the rear tyres ;-) ) I run water injection in the high boost "stage" mode, but i'm running 2.6bar gauge at 7800rpm on a CR in the high 11s
227bhp said:
Stuballs said:
So I've hit a problem. I just measured everything properly and worked out my static compression ratio and it's 12:1!
Conventional wisdom suggests this is simply too high for a turbo build.
'Kinell, that's very high for an NA, IIRC Mk1/2 MX5s are circa 9:1.Conventional wisdom suggests this is simply too high for a turbo build.
Show us a pic of a head which has been ground out, you need a thickness tester when taking that much out and be careful you aren't creating pockets for fuel which won't burn properly. That's a sh!tload of metal to lose.
Likewise you need to test thickness when dishing NA pistons to make them turbo, it can only be done when there is enough to remove safely.
Have you got dished valve heads? A small amount can be gained there, also by sinking them in deeper. Not ideal, but at this level worth considering. It's a shame the pistons are coated because the best way is to pinch a bit from everywhere you can.
You need to be confident in your head, block and stud strength before running boost and WI otherwise you'll warp and bend stuff or just lift the head, have the gasket leak etc and from what i've seen the K series isn't particularly strong in any respect.
Edited by 227bhp on Saturday 13th August 23:33
12.5 is Bloody high for turbo though!!
Would a thicker head gasket be possible or is it beyond that?
Yazza54 said:
227bhp said:
Stuballs said:
So I've hit a problem. I just measured everything properly and worked out my static compression ratio and it's 12:1!
Conventional wisdom suggests this is simply too high for a turbo build.
'Kinell, that's very high for an NA, IIRC Mk1/2 MX5s are circa 9:1.Conventional wisdom suggests this is simply too high for a turbo build.
Show us a pic of a head which has been ground out, you need a thickness tester when taking that much out and be careful you aren't creating pockets for fuel which won't burn properly. That's a sh!tload of metal to lose.
Likewise you need to test thickness when dishing NA pistons to make them turbo, it can only be done when there is enough to remove safely.
Have you got dished valve heads? A small amount can be gained there, also by sinking them in deeper. Not ideal, but at this level worth considering. It's a shame the pistons are coated because the best way is to pinch a bit from everywhere you can.
You need to be confident in your head, block and stud strength before running boost and WI otherwise you'll warp and bend stuff or just lift the head, have the gasket leak etc and from what i've seen the K series isn't particularly strong in any respect.
Edited by 227bhp on Saturday 13th August 23:33
12.5 is Bloody high for turbo though!!
Would a thicker head gasket be possible or is it beyond that?
How about a decompression plate from Ferriday. They do list them
http://www.ferriday.co.uk/head-gasket-drawings-on-...
http://www.ferriday.co.uk/head-gasket-drawings-on-...
OP, sounds like the problem is really with the pistons, with a bit too much meat on them for the job you want them to do. I know they must have cost a bundle (They're so pretty!) but if you want a proper answer I think you need to change them for lower CR items.
On the plus side, if they do add up to that much compression then they'll be handy for someone trying to build a high HP N/A K series engine, so you should be able to offload them for a decent price.
On the plus side, if they do add up to that much compression then they'll be handy for someone trying to build a high HP N/A K series engine, so you should be able to offload them for a decent price.
Gassing Station | Readers' Cars | Top of Page | What's New | My Stuff