Tilton Slave, Zircotech Headers and Injector cleaning
Discussion
An RP slave is perfectly fine, but only if it is:
- Fitted correctly within the bellhousing
- Your flywheel isn't worn
- You have a clutch pedal stop fitted and
- Have insulated and heat shielded the the part of clutch line running from master to salve vial the exhaust headers (4.5)
The problem is that the clutch assembly bolts to to the part of the flywheel that doesn't wear.
But the flywheel wears and the step lowers.
The position of diaphragm fingers on a fully fitted AP clutch (in it's engaged, resting position) are governed by the height of the step on the flywheel.
On a new flywheel the diaphragm fingers on a fully fitted new clutch are almost parallel to the friction plates and flywheel - there is not much work required to disengage under these conditions.
As the step wears the engaged resting position of the diaphragm fingers changes and they move away from the flywheel.
The extra effort required from the slave (and master too!), to not only do its normal job of disengaging the clutch, must have to get the diaphragm fingers into their correct position before it actually disengages the clutch.
Consider the extra effort required from the Master and Slave seals in light of substandard or non existent clutch-line heat shielding plus heat soak into the slave seals via the bellhousing from (the poorly cooled) engine that it is mated to.
It is easy to see that we have a situation where the heat and pressure tolerances for the master and slave (OEM or RP) are not able to handle the stress put on them in cars with worn flywheel steps.
Assuming that the slave was fitted correctly and a clutch pedal stop is fitted then as long as the step on the flywheel is correct even an OEM slave is fine,
- Fitted correctly within the bellhousing
- Your flywheel isn't worn
- You have a clutch pedal stop fitted and
- Have insulated and heat shielded the the part of clutch line running from master to salve vial the exhaust headers (4.5)
The problem is that the clutch assembly bolts to to the part of the flywheel that doesn't wear.
But the flywheel wears and the step lowers.
The position of diaphragm fingers on a fully fitted AP clutch (in it's engaged, resting position) are governed by the height of the step on the flywheel.
On a new flywheel the diaphragm fingers on a fully fitted new clutch are almost parallel to the friction plates and flywheel - there is not much work required to disengage under these conditions.
As the step wears the engaged resting position of the diaphragm fingers changes and they move away from the flywheel.
The extra effort required from the slave (and master too!), to not only do its normal job of disengaging the clutch, must have to get the diaphragm fingers into their correct position before it actually disengages the clutch.
Consider the extra effort required from the Master and Slave seals in light of substandard or non existent clutch-line heat shielding plus heat soak into the slave seals via the bellhousing from (the poorly cooled) engine that it is mated to.
It is easy to see that we have a situation where the heat and pressure tolerances for the master and slave (OEM or RP) are not able to handle the stress put on them in cars with worn flywheel steps.
Assuming that the slave was fitted correctly and a clutch pedal stop is fitted then as long as the step on the flywheel is correct even an OEM slave is fine,
Thread resurrection!
My slave has just died on my '99 4.5 and a couple of people have mentioned this thread/ Tilton. Just wondered how durable it's been as my current one has only managed 8k/ 2.5 years.
Thankfully there are still some pics on page 6 (cheers photobucket!) as guide.
Am I right in saying that essentially you cut a 114mm hole in the bell housing to allow the Tilton to fit through, secure it so it can't spin and then extend the hoses. Does the master cylinder need replacing with a smaller bore unit? Does the Tilton need shimming, etc to meet the clutch and can all this be done without removing the engine or manifolds? I will have access to a ramp for the work if that's a factor in not needing to remove the engine/ manifolds.
Are there any recommended suppliers for the parts? Any other advice before jumping in and ordering up the bits?
Thanks,
Ads
My slave has just died on my '99 4.5 and a couple of people have mentioned this thread/ Tilton. Just wondered how durable it's been as my current one has only managed 8k/ 2.5 years.
Thankfully there are still some pics on page 6 (cheers photobucket!) as guide.
Am I right in saying that essentially you cut a 114mm hole in the bell housing to allow the Tilton to fit through, secure it so it can't spin and then extend the hoses. Does the master cylinder need replacing with a smaller bore unit? Does the Tilton need shimming, etc to meet the clutch and can all this be done without removing the engine or manifolds? I will have access to a ramp for the work if that's a factor in not needing to remove the engine/ manifolds.
Are there any recommended suppliers for the parts? Any other advice before jumping in and ordering up the bits?
Thanks,
Ads
It's easy enough removing the manifold, although you do have to undo/loosen the engine mounts to tip the engine.
I tried doing the slave with the manifolds on and gave up in the end and removed the manifolds and made life so much easier.
Keep an eye on eBay for a second bell housing so you can always prepare everything prior to fitting.
I tried doing the slave with the manifolds on and gave up in the end and removed the manifolds and made life so much easier.
Keep an eye on eBay for a second bell housing so you can always prepare everything prior to fitting.
Adturb said:
Thread resurrection!
My slave has just died on my '99 4.5 and a couple of people have mentioned this thread/ Tilton. Just wondered how durable it's been as my current one has only managed 8k/ 2.5 years.
Thankfully there are still some pics on page 6 (cheers photobucket!) as guide.
Am I right in saying that essentially you cut a 114mm hole in the bell housing to allow the Tilton to fit through, secure it so it can't spin and then extend the hoses. Does the master cylinder need replacing with a smaller bore unit? Does the Tilton need shimming, etc to meet the clutch and can all this be done without removing the engine or manifolds? I will have access to a ramp for the work if that's a factor in not needing to remove the engine/ manifolds.
Are there any recommended suppliers for the parts? Any other advice before jumping in and ordering up the bits?
Thanks,
Ads
Youre right wit hthe 114mm hole saw. The Tilton comes with fitting instrictions that explain how to set up the clutch clearances. There's a collar that fits on to the gearbox and the slave cylinder screws onto that. By winding it up and down the thread you set the clarance to the clutch fingers. You may need to cut the collar down to get the clearances right. Then you need to drill and tap an M6 hole in the input bearing retainer to fit the lock bolt to prevent the slave cylinder from spinning around. With standard manifolds I could get the gearbox off and on with them in place but no such luck with the ACT performance ones. Definitely an engine in job though. If you're going to try with the manifolds in place I'd suggest you do the following (after the usual steps for clutch access like exhaust, propshaft, starter motor, gear lever removal):My slave has just died on my '99 4.5 and a couple of people have mentioned this thread/ Tilton. Just wondered how durable it's been as my current one has only managed 8k/ 2.5 years.
Thankfully there are still some pics on page 6 (cheers photobucket!) as guide.
Am I right in saying that essentially you cut a 114mm hole in the bell housing to allow the Tilton to fit through, secure it so it can't spin and then extend the hoses. Does the master cylinder need replacing with a smaller bore unit? Does the Tilton need shimming, etc to meet the clutch and can all this be done without removing the engine or manifolds? I will have access to a ramp for the work if that's a factor in not needing to remove the engine/ manifolds.
Are there any recommended suppliers for the parts? Any other advice before jumping in and ordering up the bits?
Thanks,
Ads
Remove the lambda sensors.
Unbolt the gearbox from the clutch housing.
Unbolt the clutch housing from the engine.
Push/lift the pair of them down the transmission tunnel.
You'll then be able to remove the clutch housing.
Gearbox should then come out forwards and under the engine.
Refitting is the reverse but slightly trickier as you'll need to get the gearbox up on top of the manifolds, then fit the clutch housing to it and get the hoses nicely positioned so they don't drag on the clutch, then finally connect the combined gearbox and clutch housing into place on the engine.
Failing that take the manifolds off and you'll be able to get the gearbox and clutch housing together off the car and fit them as one.
When figuring this out I found the standard 0.7" bore master cylinder moves too much fluid so the clutch engagement becomes very on/off, like a switch. Fitting a .625 makes it lighter than a 0.7" and provides finer clutch control leading to smoother engagement.
I did mine in 2015 so its been good for 5 years so far.
I used Competition Supplies for the slave cylinder (60-6000 and 60-628 for the cylinder and mount). I used Torques ebay store for the AN fittings and hose.
Edited by CerbWill on Tuesday 1st September 10:46
CerbWill said:
Youre right wit hthe 114mm hole saw. The Tilton comes with fitting instrictions that explain how to set up the clutch clearances. There's a collar that fits on to the gearbox and the slave cylinder screws onto that. By winding it up and down the thread you set the clarance to the clutch fingers. You may need to cut the collar down to get the clearances right. Then you need to drill and tap an M6 hole in the input bearing retainer to fit the lock bolt to prevent the slave cylinder from spinning around. With standard manifolds I could get the gearbox off and on with them in place but no such luck with the ACT performance ones. Definitely an engine in job though. If you're going to try with the manifolds in place I'd suggest you do the following (after the usual steps for clutch access like exhaust, propshaft, starter motor, gear lever removal):
Remove the lambda sensors.
Unbolt the gearbox from the clutch housing.
Unbolt the clutch housing from the engine.
Push/lift the pair of them down the transmission tunnel.
You'll then be able to remove the clutch housing.
Gearbox should then come out forwards and under the engine.
Refitting is the reverse but slightly trickier as you'll need to get the gearbox up on top of the manifolds, then fit the clutch housing to it and get the hoses nicely positioned so they don't drag on the clutch, then finally connect the combined gearbox and clutch housing into place on the engine.
Failing that take the manifolds off and you'll be able to get the gearbox and clutch housing together off the car and fit them as one.
When figuring this out I found the standard 0.7" bore master cylinder moves too much fluid so the clutch engagement becomes very on/off, like a switch. Fitting a .625 makes it lighter than a 0.7" and provides finer clutch control leading to smoother engagement.
I did mine in 2015 so its been good for 5 years so far.
I used Competition Supplies for the slave cylinder (60-6000 and 60-628 for the cylinder and mount). I used Torques ebay store for the AN fittings and hose.
Big thank you for the reply and the advice on the gearbox removal, it's a huge help. I'm not sure what manifolds I have but I know the cat-back is ACT. How would I go about setting the bearing clearance to the clutch- is it a case of fitting the gearbox back in fully and looking though a hole somewhere, then remove and adjust and try again, or can that collar be rotated in situ? Remove the lambda sensors.
Unbolt the gearbox from the clutch housing.
Unbolt the clutch housing from the engine.
Push/lift the pair of them down the transmission tunnel.
You'll then be able to remove the clutch housing.
Gearbox should then come out forwards and under the engine.
Refitting is the reverse but slightly trickier as you'll need to get the gearbox up on top of the manifolds, then fit the clutch housing to it and get the hoses nicely positioned so they don't drag on the clutch, then finally connect the combined gearbox and clutch housing into place on the engine.
Failing that take the manifolds off and you'll be able to get the gearbox and clutch housing together off the car and fit them as one.
When figuring this out I found the standard 0.7" bore master cylinder moves too much fluid so the clutch engagement becomes very on/off, like a switch. Fitting a .625 makes it lighter than a 0.7" and provides finer clutch control leading to smoother engagement.
I did mine in 2015 so its been good for 5 years so far.
I used Competition Supplies for the slave cylinder (60-6000 and 60-628 for the cylinder and mount). I used Torques ebay store for the AN fittings and hose.
Edited by CerbWill on Tuesday 1st September 10:46
I can't see 60-628 on their website? Do you recall what length hoses and which adaptors you required? I really want all the gear together before I get the car on the ramp for whichever route I go... Any benefit of Girling or Willwood for the 0.625" slave?
With all the above in mind I'm now sitting on the fence with the solution as I currently have a Powers slave and they're fairly sure it should only need a seal kit and release bearing which is under £50 all in. However if the centre has spun due to the release bearing failing it will want a whole new unit at £200 odd- and I won't know that for sure until it's apart.
Give you've done the mod would you do it again without hesitating or for the sake of £50-£200 renew what's there? I suppose the other factor is that I haven't had the box off before so doing this once will be a learning experience meaning if I go Tilton later I know what I'm looking at?
Adturb said:
Big thank you for the reply and the advice on the gearbox removal, it's a huge help. I'm not sure what manifolds I have but I know the cat-back is ACT. How would I go about setting the bearing clearance to the clutch- is it a case of fitting the gearbox back in fully and looking though a hole somewhere, then remove and adjust and try again, or can that collar be rotated in situ?
Read the fitting instructions here. https://tiltonracing.com/wp-content/uploads/98-111...You need to fit the bellhousing and measure the distance from the bellhousing/gearbox mating face to the clutch fingers then fit the slave cylinder to the gearbox and measure the distance from the gearbox/bellhousing mating face to the end of the throwout bearing the nadjust for the correct clearance. So you can do it off the car.
Adturb said:
I can't see 60-628 on their website? Do you recall what length hoses and which adaptors you required? I really want all the gear together before I get the car on the ramp for whichever route I go... Any benefit of Girling or Willwood for the 0.625" slave?
https://www.competitionsupplies.com/600-6000-series-threaded-hrb-mounting-sleeveI went with Wilwood as it has the most travel. Its also worked for 5 years.
2m of stainless braided PTFE hose should be plenty. The Tilton webpage says what AN adapters you need. Wilwood have drawings of their products so you'll be able to work out what adapters you need buy I think they're AN4.
- EDIT** Wilwood output port is 3/8-24, so AN3.
4 AN4 fittings. 1 to connect to the AN3>4 adapter on the master cylinder, 2 to mate to the female ends on the tilton slave, and 1 to put on the end of the bleed hose from the slave to connect the (supplied) bleed fitting to.
Make sure you get fitting for PTFE hose. AN fittings for rubber hose wont fit/work.
Adturb said:
With all the above in mind I'm now sitting on the fence with the solution as I currently have a Powers slave and they're fairly sure it should only need a seal kit and release bearing which is under £50 all in. However if the centre has spun due to the release bearing failing it will want a whole new unit at £200 odd- and I won't know that for sure until it's apart. Give you've done the mod would you do it again without hesitating or for the sake of £50-£200 renew what's there? I suppose the other factor is that I haven't had the box off before so doing this once will be a learning experience meaning if I go Tilton later I know what I'm looking at?
My car had a history of clutch slave issues. I replaced the original with a Raceproved slave which failed after a few months so I made the Tilton mod. Other cars have been fine for years with the original and/or have had no issues with the Raceproved design. I have a theory its to do with the bellhousings and machining tolerances. I do wonder if some of the housings arent quite square and it puts some interesting sideways/twisting loads on the seals. Have never proved it though. Overall, do you feel lucky?Edited by CerbWill on Wednesday 2nd September 14:24
Thank you for coming back so quickly, all excellent advice and appreciated.
I've bottled it- this time- but if/ when it fails again I'l be 100% onto the Tilton route. I think I'm asking for trouble by going down the modified route this time as I'm not familiar with the original setup so swapping like-for-like should make it easier given I'm going to be time limited on a mates ramp this time around. If it is just the seals as Ive been told it should be then I may plan to do this before it fails again....
WRT to the new hoses and master cylinder, did you replace the hardline from the master and run a flexible the whole way to the box or does the Willwood have the same output thread as OE so it's just new hose from the hardline to the box/ Tilton and a second one for the bleed?
I've bottled it- this time- but if/ when it fails again I'l be 100% onto the Tilton route. I think I'm asking for trouble by going down the modified route this time as I'm not familiar with the original setup so swapping like-for-like should make it easier given I'm going to be time limited on a mates ramp this time around. If it is just the seals as Ive been told it should be then I may plan to do this before it fails again....
WRT to the new hoses and master cylinder, did you replace the hardline from the master and run a flexible the whole way to the box or does the Willwood have the same output thread as OE so it's just new hose from the hardline to the box/ Tilton and a second one for the bleed?
aide said:
A clutch pedal stop is often overlooked.
Good point.Adturb said:
Thank you for coming back so quickly, all excellent advice and appreciated.
I've bottled it- this time- but if/ when it fails again I'l be 100% onto the Tilton route. I think I'm asking for trouble by going down the modified route this time as I'm not familiar with the original setup so swapping like-for-like should make it easier given I'm going to be time limited on a mates ramp this time around. If it is just the seals as Ive been told it should be then I may plan to do this before it fails again....
WRT to the new hoses and master cylinder, did you replace the hardline from the master and run a flexible the whole way to the box or does the Willwood have the same output thread as OE so it's just new hose from the hardline to the box/ Tilton and a second one for the bleed?
You might be able to just change the line from the connector in the driver's wheel arch but then you're still going to run the flexi close to the exhaust, thats pretty unavoidable. I replaced the whole lot and went a for a different route, following the throttle cable, to keep the hose away from the exhaust manifolds.I've bottled it- this time- but if/ when it fails again I'l be 100% onto the Tilton route. I think I'm asking for trouble by going down the modified route this time as I'm not familiar with the original setup so swapping like-for-like should make it easier given I'm going to be time limited on a mates ramp this time around. If it is just the seals as Ive been told it should be then I may plan to do this before it fails again....
WRT to the new hoses and master cylinder, did you replace the hardline from the master and run a flexible the whole way to the box or does the Willwood have the same output thread as OE so it's just new hose from the hardline to the box/ Tilton and a second one for the bleed?
CerbWill said:
keep the hose away from the exhaust manifolds.
The braided clutch hose on my car failed where it had been touching the sumpIronically this happened on the E42 close to where my coolant tank failed yesterday, ruining my plan to test newly fitted Nitrons during DN24 at the Ring
Thread bump. I am looking to do this mod and have a question (probably the first of many):
What purpose does the 61-628 sleeve serve if I buy this: https://www.competitionsupplies.com/search/APS6060... ?
The kit comes with a threaded gearbox mount which presumably the slave screws onto. Or does the 61-628 screw onto the mount and the slave then screw onto the 61-628?
Thanks!
What purpose does the 61-628 sleeve serve if I buy this: https://www.competitionsupplies.com/search/APS6060... ?
The kit comes with a threaded gearbox mount which presumably the slave screws onto. Or does the 61-628 screw onto the mount and the slave then screw onto the 61-628?
Thanks!
pmessling said:
The gearbox mount I'd to stop the slave spinning, the threaded colar is to adjust the amount the slave moves to release the clutch.
I'm in the process of doing mine, all be it very slowly.
I have a brand new hole saw if you want it. I brought two incase I blunted one and I didn't.
Thanks but have already bought the hole saw. I have the starter out so if you still have any shims for that I’m finally ready for one I'm in the process of doing mine, all be it very slowly.
I have a brand new hole saw if you want it. I brought two incase I blunted one and I didn't.

I think the bolt/pin stops the slave spinning. I’ll probably just buy the separate sleeve anyway. I understand the adjustment procedure, it’s the fact that the gearbox mount is threaded confuses me as to why I would need another threaded collar. I expect when the GB is off and I have the parts in hand it will become clear.
FarmyardPants said:
Thread bump. I am looking to do this mod and have a question (probably the first of many):
What purpose does the 61-628 sleeve serve if I buy this: https://www.competitionsupplies.com/search/APS6060... ?
The kit comes with a threaded gearbox mount which presumably the slave screws onto. Or does the 61-628 screw onto the mount and the slave then screw onto the 61-628?
Thanks!
I'm in the process of doing the switch on my Tuscan as well. If I'm looking at the right thing, the kit you've linked includes a threaded sleeve for a different ZF gearbox? If so then the 61-628 sleeve is used instead as it fits the T5. What purpose does the 61-628 sleeve serve if I buy this: https://www.competitionsupplies.com/search/APS6060... ?
The kit comes with a threaded gearbox mount which presumably the slave screws onto. Or does the 61-628 screw onto the mount and the slave then screw onto the 61-628?
Thanks!
Basil Brush said:
I'm in the process of doing the switch on my Tuscan as well. If I'm looking at the right thing, the kit you've linked includes a threaded sleeve for a different ZF gearbox? If so then the 61-628 sleeve is used instead as it fits the T5.
The 61-628 is just a threaded cylinder, it has no bolt holes. It cannot be gearbox specific because it has no mountings.Waiting for CerbWill to advise

Edited by FarmyardPants on Wednesday 17th January 16:07
FarmyardPants said:
Basil Brush said:
I'm in the process of doing the switch on my Tuscan as well. If I'm looking at the right thing, the kit you've linked includes a threaded sleeve for a different ZF gearbox? If so then the 61-628 sleeve is used instead as it fits the T5.
The 61-628 is just a threaded cylinder, it has no bolt holes. It cannot be gearbox specific because it has no mountings.Waiting for CerbWill to advise

Edited by FarmyardPants on Wednesday 17th January 16:07
This is the setup for the T5.
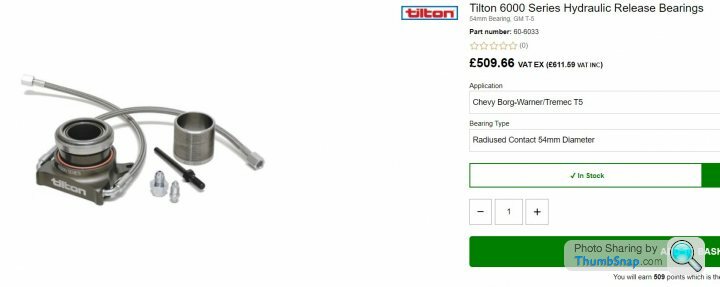
Gassing Station | Cerbera | Top of Page | What's New | My Stuff