Dodge Viper GTS on the rollers
Discussion
Max_Torque said:
Manufacturer certified power figures are the closest to any truely "accurate" figure you are going to get. They will have been recorded from an engine(s) in a known condition, on a certified test system, under controlled conditions (fuel grade, temps, pressures etc, are are "steady state" values (ie, the average power over a 30sec period at that steady state)
All that rototest graph tells us is that this particular setup is about 8% off. Calculating WHY it is 8% off would be an entirely more complex undertaking, involving not just the consideration of cumulative errors but systematic ones too!
In all cases, Power is just the measurement of a torque being generated at a certain velocity, and these days with solid state sensors (load cells using strain gauges etc) and high resolution digital electronics, the basic measurement error for power should be no more than 1% really, (assuming correct and current sensor / system calibration) The really big uncertainties are within the boundary conditions for such testing, and why std correction factors were established to attempt to normalise those anomalous conditions.
For reference i have just helped commission some new state of the art engine test cells, which have cost approx £2M per cell, and can control boundary conditions to 0.5degC / 0.1kPa, run on all known refference fuels, and measure EVERYTHING.
Even then, when we do a cumulative error study, we struggle to get overall accuracy better than 1% In fact, such are the issues with getting accurate and repeatable measurements on modern multi-degree-of-freedom engines, we know use cylinder thermodynamics as our primary arbiter of performance, not flywheel torque!
NewTestCells
Each cell also undergoes a "statistical normalisation study" using an extremely tightly controlled (and instrumented reference engine) so we can estimate both the magnitude and the shape of the data distribution for an individual cell!
Without wishing to sound rude, it makes me laugh when i read tuners on the net shouting about how they "found an extra 5bhp" on a 300bhp engine (1.6%) after a single run on a chassis dyno.
(as an aside, all OEM chassis dynos used single 48" rolls to help avoid tyre effects)
Thanks for that info.All that rototest graph tells us is that this particular setup is about 8% off. Calculating WHY it is 8% off would be an entirely more complex undertaking, involving not just the consideration of cumulative errors but systematic ones too!
In all cases, Power is just the measurement of a torque being generated at a certain velocity, and these days with solid state sensors (load cells using strain gauges etc) and high resolution digital electronics, the basic measurement error for power should be no more than 1% really, (assuming correct and current sensor / system calibration) The really big uncertainties are within the boundary conditions for such testing, and why std correction factors were established to attempt to normalise those anomalous conditions.
For reference i have just helped commission some new state of the art engine test cells, which have cost approx £2M per cell, and can control boundary conditions to 0.5degC / 0.1kPa, run on all known refference fuels, and measure EVERYTHING.
Even then, when we do a cumulative error study, we struggle to get overall accuracy better than 1% In fact, such are the issues with getting accurate and repeatable measurements on modern multi-degree-of-freedom engines, we know use cylinder thermodynamics as our primary arbiter of performance, not flywheel torque!
NewTestCells
Each cell also undergoes a "statistical normalisation study" using an extremely tightly controlled (and instrumented reference engine) so we can estimate both the magnitude and the shape of the data distribution for an individual cell!
Without wishing to sound rude, it makes me laugh when i read tuners on the net shouting about how they "found an extra 5bhp" on a 300bhp engine (1.6%) after a single run on a chassis dyno.
(as an aside, all OEM chassis dynos used single 48" rolls to help avoid tyre effects)
I helped design and commission an OEM engine dyno some years ago, and it is a different world. We spent days and days just sorting the exhaust backpressure control.
I think people also confuse accuracy with repeatability - you can sucessfully tune / map a car on a dyno that read 20% high (or low), providing it is consistant.
The big uncontrolled variable is temperature, especially with turbo engines. Even NA engines suffer from this.
When testing with our NA test mule, it takes a couple of runs to get peak power, then you get two or three back-to-back runs with very similar power, then the power drops off a bit until the car cools down again.
Turbo cars are a nightmare

Again, you can get reasonably consistent figures from a given setup, but if the dyno down the road has a different cooling fan setup, charge temperatures are different, and power as well.
I note you do steady state testing (as I would have expected) - a staggering number of people don't like to dyno their cars at anything less than a fast acceleration. There seems to be an attitude that holding the car at speed will somehow damage the engine, which makes me wonder how they drive up hills or on tracks with long straights*.
- I understand that a drag engine may well not be built for more that 10 seconds at full power, but that's a different story.
Stan Weiss said:
Robert
Thanks for the posts. My data collection was done on a real road logging the OBD II port. I had to use 2nd gear to not go over the speed limit by to much.
Here is a graph from the raw data and then one with the data smoothed. I was thinking that the raw data should have been some what better without any smoothing.
Stan
my pleasure stan , i wonder if you could do a top gear run one night in the dark ,you could get a smoother trace ,trouble with auto's , if it is an auto , is holding it in one gear all the way through a long high gear run is hard .. i quite like the gtech rr stuff ,and have used that for on the rd work sometimes.Thanks for the posts. My data collection was done on a real road logging the OBD II port. I had to use 2nd gear to not go over the speed limit by to much.

Stan
robert.
I have always advocated repeatability as the main importance for my rolling road, I appreciate the £26000 I have invested is a mere pimple on the bottom of what manufacturers would spend but I am 'chuffed' how repeatable the figures are that we achieve.I prefer running inertia tests whenever possible, this keeps temps down and adds to repeatability. Once done we hold the load for as long as necessary to check for detonation (although I must say the inertia tests show power drop rapidly with onset of det) and at times to check fuel supply is sufficient for endurance use such as track racing. Also testing radiator/heating problems.
The SF901 will be commissioned the same as Lister Storm Racing had it (24 Hour Le Mans use) so we can, if required, run flat out without overheating engine or cooling for dyno. This requires massive water tank!
Peter
The SF901 will be commissioned the same as Lister Storm Racing had it (24 Hour Le Mans use) so we can, if required, run flat out without overheating engine or cooling for dyno. This requires massive water tank!
Peter
Stan Weiss said:
If I can ask? At what frequency and how many channels can they log?
It depends on what is being measured, typically, for a fairly std 4 cyl engine, we would be recording maybe 30 thermocouples (at 2Hz), 30 pressure sensors (at 10 Hz) and probably 50 to 100 EMS data parameters (at 10Hz to 100Hz). Fuel flow will be a composite number from both a mass balance and a near real time Coriolis device, Horiba Exhaust emissions are std. Fuel, oil, water, and chargecooling temps, plus intake air, cell pressure, humidity and temperature are all in closed loop control.Add in cylinder pressure measurement (crank synchronous at 0.1degCA), intake and exhaust (esp EGR) dynamic pressure sensors (1000Hz), or a thermal survey engine for example and we can easily add another 100 channels of data!
Diesels get a raft of extra kit, include Smoke analysis (both particle number and size/distribution),injector nozzle lift in near real time. Multi node Structure born vibration and acoustic data is also sampled (at 100Khz) to get a figure for engine "roughness" and NVH
For hybrid systems, or "Powertrain on test" (ie, engine & transmission in cell) the Data aquisition channels all go up again, with synchronous measurement of Emachines, inverters, battery systems and DC:DC convertors. Critical here is full harmonic Electrical Power analysis (sampling at 2Mhz) on the hybrid systems so we can calculate a system power flow and efficiency map etc
Often this is also complicated by the need to replace batteries with battery simulation systems (for both safety and to be able to start testing before a real battery has been developed)
Trust me, a modern passenger car is a VERY complicated machine these days ;-)
ivanhoew said:
my pleasure stan , i wonder if you could do a top gear run one night in the dark ,you could get a smoother trace ,trouble with auto's , if it is an auto , is holding it in one gear all the way through a long high gear run is hard .. i quite like the gtech rr stuff ,and have used that for on the rd work sometimes.
robert.
Robert,robert.
The car was a manual trans. I wish I could do some more data logging on it but I have not had that car for about the last 3 1/2 year.
Stan
Max_Torque said:
It depends on what is being measured, typically, for a fairly std 4 cyl engine, we would be recording maybe 30 thermocouples (at 2Hz), 30 pressure sensors (at 10 Hz) and probably 50 to 100 EMS data parameters (at 10Hz to 100Hz). Fuel flow will be a composite number from both a mass balance and a near real time Coriolis device, Horiba Exhaust emissions are std. Fuel, oil, water, and chargecooling temps, plus intake air, cell pressure, humidity and temperature are all in closed loop control.
Add in cylinder pressure measurement (crank synchronous at 0.1degCA), intake and exhaust (esp EGR) dynamic pressure sensors (1000Hz), or a thermal survey engine for example and we can easily add another 100 channels of data!
Diesels get a raft of extra kit, include Smoke analysis (both particle number and size/distribution),injector nozzle lift in near real time. Multi node Structure born vibration and acoustic data is also sampled (at 100Khz) to get a figure for engine "roughness" and NVH
For hybrid systems, or "Powertrain on test" (ie, engine & transmission in cell) the Data aquisition channels all go up again, with synchronous measurement of Emachines, inverters, battery systems and DC:DC convertors. Critical here is full harmonic Electrical Power analysis (sampling at 2Mhz) on the hybrid systems so we can calculate a system power flow and efficiency map etc
Often this is also complicated by the need to replace batteries with battery simulation systems (for both safety and to be able to start testing before a real battery has been developed)
Trust me, a modern passenger car is a VERY complicated machine these days ;-)
Thanks. That is a lot of data to analyze. Add in cylinder pressure measurement (crank synchronous at 0.1degCA), intake and exhaust (esp EGR) dynamic pressure sensors (1000Hz), or a thermal survey engine for example and we can easily add another 100 channels of data!
Diesels get a raft of extra kit, include Smoke analysis (both particle number and size/distribution),injector nozzle lift in near real time. Multi node Structure born vibration and acoustic data is also sampled (at 100Khz) to get a figure for engine "roughness" and NVH
For hybrid systems, or "Powertrain on test" (ie, engine & transmission in cell) the Data aquisition channels all go up again, with synchronous measurement of Emachines, inverters, battery systems and DC:DC convertors. Critical here is full harmonic Electrical Power analysis (sampling at 2Mhz) on the hybrid systems so we can calculate a system power flow and efficiency map etc
Often this is also complicated by the need to replace batteries with battery simulation systems (for both safety and to be able to start testing before a real battery has been developed)
Trust me, a modern passenger car is a VERY complicated machine these days ;-)

Stan
Ah drat. Max's post about how many engines he's blown up has disappeared before I could quote it, along with those from the nutcase thankfully. I'm sure you were just being modest Max about how many engines you've managed to blow up during the course of your work. No doubt there are quite a few others you've had a hand in with your advice on here 
Ohhh bazinga. Someone call a burn unit specialist.
(nah, no detonation apparent there boy. The waterways just need moving and then stronger head bolts) Tee hee.

Ohhh bazinga. Someone call a burn unit specialist.
(nah, no detonation apparent there boy. The waterways just need moving and then stronger head bolts) Tee hee.
Stan, I'd be interested to analyse your in car acceleration data for that Mustang in my vehicle performance simulation software. I'll generate a horsepower and torque curve accurate within a percent or two. I'll need the times, rpm and speed for each increment, car weight, gearing and tyre size, aero drag should be irrelevant in 2nd gear so I'll input rough numbers for that car unless you have better. Engine mass inertia will be a big factor and I have decent base line numbers for yank V8s.
Pumaracing said:
Stan, I'd be interested to analyse your in car acceleration data for that Mustang in my vehicle performance simulation software. I'll generate a horsepower and torque curve accurate within a percent or two. I'll need the times, rpm and speed for each increment, car weight, gearing and tyre size, aero drag should be irrelevant in 2nd gear so I'll input rough numbers for that car unless you have better. Engine mass inertia will be a big factor and I have decent base line numbers for yank V8s.
Dave,Here is the vehicle information. I hope I got it all.
Stan
Car Weight = 3700.0
Rear Gear Ratio = 3.27
Tire Width = 245.0
Wheel Diameter = 17.0
Aspect Ratio = 45.0
T Gear1 = 3.37
T Gear2 = 1.99
T Gear3 = 1.33
T Gear4 = 1.0
T Gear5 = 0.67
T Gear6 = 0.0
T Gear7 = 0.0
Trans Gear = 2
Coefficient of Drag = 0.36
Frontal Area = 21.46
Tire Diameter = 25.6811
Tire Rolling Radius = 12.84055
=====
RPM Time <<<------- Data logged from OBD II -- Vehicle was in 2nd gear
2207 113.1843
2229.25 113.2778
2256.25 113.364825
2289.25 113.4673
2313.25 113.5576
2340.75 113.650325
2370.25 113.743033
2396 113.84065
2424 113.9382333
2452.5 114.0261
2480 114.121225
2526.75 114.235925
2598.75 114.335133
2721.25 114.428675
2733 114.5336
2804.75 114.6247
2897.75 114.7093
2959.5 114.81175
3046.25 114.928875
3138 115.038675
3238.25 115.16212
3354 115.29294
3481.75 115.41984
3574.75 115.55058
3727.5 115.687725
3822.5 115.83364
3939 115.9781
4076 116.1049667
4175.75 116.246475
4330.25 116.407525
4427.25 116.58124
4573 116.7667
4722.75 116.9703333
4863.75 117.1785667
5047 117.41645
5222.75 117.7470833
5474.25 118.1999176
5795.75 118.7956182
5805.25 118.8133
Here's your power curve Stan. Below 2500 rpm something wasn't panning out so I've just taken it from there up. These are wheel figures. You can work out the torque and graph it against your own calculations.
RPM....BHP
2500...108
3000...154
3500...195
4000...210
4500...227
5000...219
5500...207
6000...195
I did a fair amount of smoothing of the final curve but it all matched the timed figures fairly nicely. Peak flywheel bhp is about 270. Now you can tell me what that motor was supposed to have.
RPM....BHP
2500...108
3000...154
3500...195
4000...210
4500...227
5000...219
5500...207
6000...195
I did a fair amount of smoothing of the final curve but it all matched the timed figures fairly nicely. Peak flywheel bhp is about 270. Now you can tell me what that motor was supposed to have.
PS - Stan, your smoothing algorithms have made some grievous errors in the shape of the smoothed bhp curve. If you look at the unsmoothed curves it's clear the bulk of the peak power numbers occur between 4000 and 4500 rpm. Then there's a downward glitch at 4400 rpm and an upward one at 5085 rpm. Finally the curve kicks upwards again after 5500 rpm which is obviously not really happening as power must be falling by then.
If you ignore all those glitches and try and draw a curve by hand through the rest of it you'll see that power peaks by 4500 rpm and then falls steadily after - as my correct power curve shows. Your smoothing algorithms have put peak power at about 5200 rpm which is way too high.
My own system has looked at the average time increments at different speeds and rpms and then smoothed that into a realistic engine power curve. I know you've done the best you can given the limitations of your birth country. I suppose it's unfair to expect a yank to come up with anything remotely as sophisticated as a European, and especially a Brit, could do. But well done for trying good buddy. It's nice to see people give something their best shot even if it falls short of the mark. I can't really fault you. Hell, most of your lot still believe in invisible sky pixies and that evolution and global warming are lies from the pit of hell.
Anyway I'm always here to correct you and put you straight so take some comfort from that
If you ignore all those glitches and try and draw a curve by hand through the rest of it you'll see that power peaks by 4500 rpm and then falls steadily after - as my correct power curve shows. Your smoothing algorithms have put peak power at about 5200 rpm which is way too high.
My own system has looked at the average time increments at different speeds and rpms and then smoothed that into a realistic engine power curve. I know you've done the best you can given the limitations of your birth country. I suppose it's unfair to expect a yank to come up with anything remotely as sophisticated as a European, and especially a Brit, could do. But well done for trying good buddy. It's nice to see people give something their best shot even if it falls short of the mark. I can't really fault you. Hell, most of your lot still believe in invisible sky pixies and that evolution and global warming are lies from the pit of hell.
Anyway I'm always here to correct you and put you straight so take some comfort from that

Pumaracing said:
Ah drat. Max's post about how many engines he's blown up has disappeared before I could quote it, along with those from the nutcase thankfully. I'm sure you were just being modest Max about how many engines you've managed to blow up during the course of your work. No doubt there are quite a few others you've had a hand in with your advice on here 
Ohhh bazinga. Someone call a burn unit specialist.
(nah, no detonation apparent there boy. The waterways just need moving and then stronger head bolts) Tee hee.
That must have come and gone without me seeing it.
Ohhh bazinga. Someone call a burn unit specialist.
(nah, no detonation apparent there boy. The waterways just need moving and then stronger head bolts) Tee hee.
I haven't blown any engines on the dyno yet, but I'm not a tuner

Dyno shootout comps have seen many a fire and blown engine over the years, as youtube can testify; there was some nice footage from last year of part of a turbo firing out the exhaust and almost taking out a camera, but that's not part of my job.
I did manage to get a white-hot exhaust manifold and about 10' of yellow-red exhaust pipe on a temporary rig trying to work out why our power readings were down 20%.
My excuse is that we were all dog-tired, and we were testing the dyno, not the engine.
Turns out that the dyno ecu on the test mule was missing a sensor, so it gave fully rich mixture and very retarded spark : it revved fine, pulled cleanly, and tried to set the factory on fire at 4am.
Pumaracing said:
I'm sure you were just being modest Max about how many engines you've managed to blow up during the course of your work.
Pumy darling, you do know how to make friends eh! ;-)(for the record, yes, i've "Blown up" a lot of engines during development and racing, but on the flip side engines i've helped develop have won F1 championships, WRC and Touring car series and power several hundred thousand passenger cars around the world today!
(when one of your engines wins the F1 championship, you'll be sure to let me know eh....... ;-)
Dave,
That data logging was done on a 2000 Mustang GT 5 speed with the 4.6l SOHC engine. Rated 260 HP @ 5000 RPM and 302 torque @ 4000 RPM from FORD.
I posted those graphs because they are what I had from 9 years ago.
I have 4 different method with 4 levels for smoothing. This would be another example of my smoothing.
If something is wrong during the run "smoothed that into a realistic engine power curve" that just might hid it.
Stan
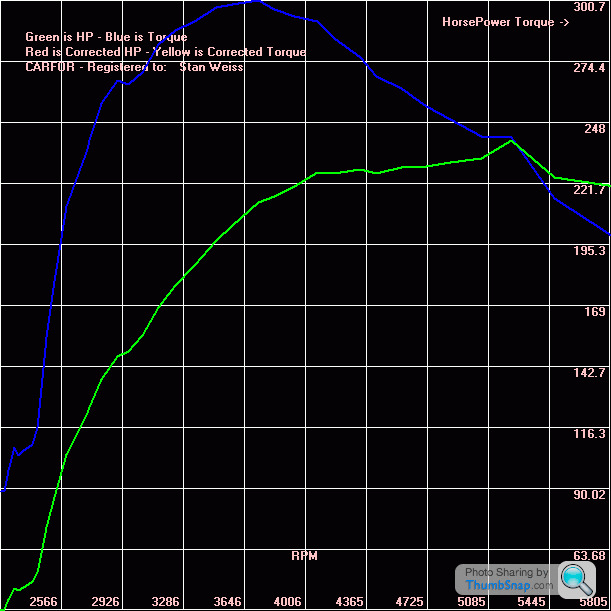
That data logging was done on a 2000 Mustang GT 5 speed with the 4.6l SOHC engine. Rated 260 HP @ 5000 RPM and 302 torque @ 4000 RPM from FORD.
I posted those graphs because they are what I had from 9 years ago.
I have 4 different method with 4 levels for smoothing. This would be another example of my smoothing.
If something is wrong during the run "smoothed that into a realistic engine power curve" that just might hid it.
Stan
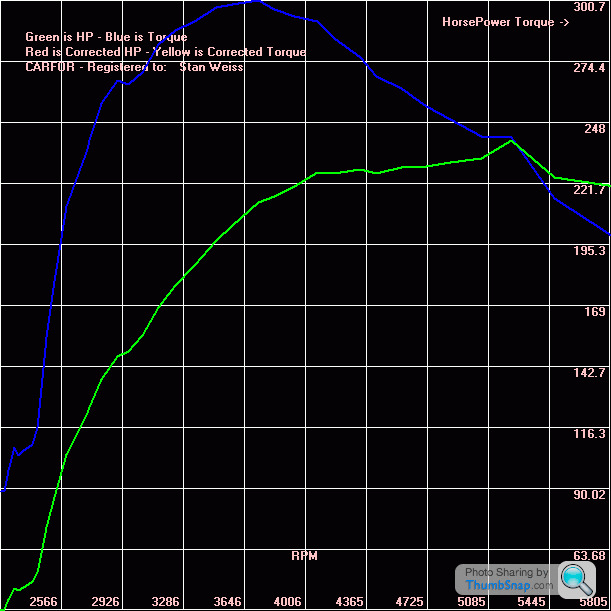
An OEM I worked with had a dyno cell for endurance testing of production engines.
Once an engine had been run through an extended test cycle, it was stripped and inspected to death. The engine was invariably fine, but since it could neither be used or sold, a few were reassembled and run until (forced) failure.
Once an engine had been run through an extended test cycle, it was stripped and inspected to death. The engine was invariably fine, but since it could neither be used or sold, a few were reassembled and run until (forced) failure.
Sounds similar to Lubrizol, we had a visit around 1992 and were impressed with the test facilities. The granite 'room' was cool
They were running and stripping to check for wear, or lack of it! Seemed like a waste of engines, but just part of a big business with big business deep pocket!
My friend did a wear rate test on an old step thru Honda Plag many years ago, held a finger near the carb mouth with knob of grinding paste....engine went aaaaaaaaaaaaaaaaaaaeeeeeeuuuuuuuuUMP and stopped in about twenty seconds
Peter

My friend did a wear rate test on an old step thru Honda Plag many years ago, held a finger near the carb mouth with knob of grinding paste....engine went aaaaaaaaaaaaaaaaaaaeeeeeeuuuuuuuuUMP and stopped in about twenty seconds

Peter
These days we do "radiological" durability analysis of wearing parts!
Special components (bearing shells, liners, rings, crank, lifters etc) are doped with different radioactive isotopes, the engine built and run. At periods during the durab test the oil is sampled for these isotopes and the relative concentrations give us wear values for each part without diss-assembling the engine ;-)
Special components (bearing shells, liners, rings, crank, lifters etc) are doped with different radioactive isotopes, the engine built and run. At periods during the durab test the oil is sampled for these isotopes and the relative concentrations give us wear values for each part without diss-assembling the engine ;-)
That's interesting, with an endurance test must be pretty nasty (powerful) isotopes or the isotope would decay fast as in isotopes used in humans for x-ray purposes. Do the isotopes vary much in half life? Must be very tight safety requirements....to think they used to let us loose with radioactive mono-directional sources in physics 
Peter

Peter
Stan, the first thing I did with your data was interpolate it into 5mph increments as follows. Using accurate data for your tyre size the mph per 1000 rpm in that gear is 11.389.
MPH..RPM...TIME...INCREMENT
30...2634..114.36
35...3073..114.95..0.59
40...3512..115.46..0.51
45...3951..115.99..0.53
50...4390..116.52..0.53
55...4829..117.13..0.61
60...5268..117.83..0.70
65...5707..118.63..0.80
Total time 4.27s
This achieves some pre-smoothing by summing several data points and eliminates most of the glitches. The time increments are actually rather nice - hitting a minimum around peak torque and then increasing again. Finding a power curve match to these increments was not difficult and very little tweaking was required to get the final nice smooth curve I posted.
I did a bit of googling on that engine which I'm not familiar with. The consensus from several web sites and youtube videos is they show about 230 bhp at the wheels at about 4800 rpm. I'll call my calculated 227 bhp just about on the money. You can clearly see from the time increments that power is dropping fast after 5000 rpm and my own power curve shows that too.
Your own power curve looks pretty close up to about 4500 and then just goes a bit too high for a bit too long after that. Not sure why.
Rotational inertia was not actually a big factor on a low revving engine like that. With wheel mass inertia and engine inertia factored in I calculated a total effective vehicle mass of 3942 lbs in that gear.
MPH..RPM...TIME...INCREMENT
30...2634..114.36
35...3073..114.95..0.59
40...3512..115.46..0.51
45...3951..115.99..0.53
50...4390..116.52..0.53
55...4829..117.13..0.61
60...5268..117.83..0.70
65...5707..118.63..0.80
Total time 4.27s
This achieves some pre-smoothing by summing several data points and eliminates most of the glitches. The time increments are actually rather nice - hitting a minimum around peak torque and then increasing again. Finding a power curve match to these increments was not difficult and very little tweaking was required to get the final nice smooth curve I posted.
I did a bit of googling on that engine which I'm not familiar with. The consensus from several web sites and youtube videos is they show about 230 bhp at the wheels at about 4800 rpm. I'll call my calculated 227 bhp just about on the money. You can clearly see from the time increments that power is dropping fast after 5000 rpm and my own power curve shows that too.
Your own power curve looks pretty close up to about 4500 and then just goes a bit too high for a bit too long after that. Not sure why.
Rotational inertia was not actually a big factor on a low revving engine like that. With wheel mass inertia and engine inertia factored in I calculated a total effective vehicle mass of 3942 lbs in that gear.
Gassing Station | Engines & Drivetrain | Top of Page | What's New | My Stuff