Charge cooler or intercooler? Which would suit?
Discussion
I'm building a Boxster that's turbo charged. I'm going charge cooled, I don't have any previous experience with it but I'm trying to get everything as big as possible as that seems to be the key. Massive charge cooler, 1.25 gallon water tank, long water pipes. It falls down on the pre-radiators, I can't easily get a decent surface area in the front, going to try using the air conditioning condensers (one each side on a Boxster) for water, the diameter of the pipes are narrow so I want to split them with a T-piece and have each radiator cooling half each.
I can't say I'm confident, it seems everyone that goes for a charge cooler set-up is ultimately disappointed. Hope I won't be.
I can't say I'm confident, it seems everyone that goes for a charge cooler set-up is ultimately disappointed. Hope I won't be.
Escy said:
I'm building a Boxster that's turbo charged. I'm going charge cooled, I don't have any previous experience with it but I'm trying to get everything as big as possible as that seems to be the key. Massive charge cooler, 1.25 gallon water tank, long water pipes. It falls down on the pre-radiators, I can't easily get a decent surface area in the front, going to try using the air conditioning condensers (one each side on a Boxster) for water, the diameter of the pipes are narrow so I want to split them with a T-piece and have each radiator cooling half each.
I can't say I'm confident, it seems everyone that goes for a charge cooler set-up is ultimately disappointed. Hope I won't be.
For any chargecooler system the MOST important bit to size correctly is the LTR, the bit that you say you (and frankly most people who are "disappointed" by CC systems) are most the compromised! (because this is where the lowest differential temperature occurs, and as heat transfer is of course = Mdot.DeltaT.CP)I can't say I'm confident, it seems everyone that goes for a charge cooler set-up is ultimately disappointed. Hope I won't be.
Escy said:
I'm building a Boxster that's turbo charged. I'm going charge cooled, I don't have any previous experience with it but I'm trying to get everything as big as possible as that seems to be the key. Massive charge cooler, 1.25 gallon water tank, long water pipes. It falls down on the pre-radiators, I can't easily get a decent surface area in the front, going to try using the air conditioning condensers (one each side on a Boxster) for water, the diameter of the pipes are narrow so I want to split them with a T-piece and have each radiator cooling half each.
I can't say I'm confident, it seems everyone that goes for a charge cooler set-up is ultimately disappointed. Hope I won't be.
Using an intercheller would definitely help you. Check out the HSV & Monaro forum on here for the Forced Induction Interchiller thread. Single degree inlet temps in Australia!I can't say I'm confident, it seems everyone that goes for a charge cooler set-up is ultimately disappointed. Hope I won't be.
HappyMidget said:
Using an intercheller would definitely help you. Check out the HSV & Monaro forum on here for the Forced Induction Interchiller thread. Single degree inlet temps in Australia!
He didnt say he as doing that, he wants to ditch the aircon and actually use their heat exchangers to cool the water in his systembut he could look into using the aircon to try and cool some of the water in the system
stevieturbo said:
HappyMidget said:
Using an intercheller would definitely help you. Check out the HSV & Monaro forum on here for the Forced Induction Interchiller thread. Single degree inlet temps in Australia!
He didnt say he as doing that, he wants to ditch the aircon and actually use their heat exchangers to cool the water in his systembut he could look into using the aircon to try and cool some of the water in the system

Max_Torque said:
For any chargecooler system the MOST important bit to size correctly is the LTR, the bit that you say you (and frankly most people who are "disappointed" by CC systems) are most the compromised! (because this is where the lowest differential temperature occurs, and as heat transfer is of course = Mdot.DeltaT.CP)
The 2 air-con condensers have a reasonably large surface area, it's the diameter of the pipes that concern me which is why I plan to split the flow so each one does half of the cooling rather than run them in series. The interchiller idea is intresting but I no longer have the air-con compressor. 
Really you'd be better off making up new water rads and replace the aircon parts rather than trying to use those cores.
Or you could weld/braze/solder on larger pipework better suited to flowing a lot of water.
but making new rads, as big as possible, to hold as much water as possible would be the better choice.
Or you could weld/braze/solder on larger pipework better suited to flowing a lot of water.
but making new rads, as big as possible, to hold as much water as possible would be the better choice.
for the street, I'd also get new cores made. For track work, I'd even add a third one in front of the engine radiator.
min 32mm pipes, better even 38mm and some big pumps, e.g. CD EWP150 or a Pierburg CWA400 plus controller.
you don't want a 400W CC pump to run 100% all the tie on the road.
min 32mm pipes, better even 38mm and some big pumps, e.g. CD EWP150 or a Pierburg CWA400 plus controller.
you don't want a 400W CC pump to run 100% all the tie on the road.
I have not heard of any DC pump failures lately. All reports I have seen were from many years ago.
The Pierburg pumps are definitely better and build to OEM standards. BMW uses them as main engine colant pumps on the 1 and 3-series.
The smaller CWA50 and 100 are used as CC pumps on the BMW M-models and by AMG. They are rated for 6000h. They employ brushless motors, a integrated controller accepting a external PWM signal and a magnetic coupling, so no shaft seals to leak.
Bet is you get them cheaply 2nd hand from the wreckers.
I personally run a CWA50 as a CC pump and a DC EWP80 to support the cooling system with zero issues so far.
The Pierburg pumps are definitely better and build to OEM standards. BMW uses them as main engine colant pumps on the 1 and 3-series.
The smaller CWA50 and 100 are used as CC pumps on the BMW M-models and by AMG. They are rated for 6000h. They employ brushless motors, a integrated controller accepting a external PWM signal and a magnetic coupling, so no shaft seals to leak.
Bet is you get them cheaply 2nd hand from the wreckers.
I personally run a CWA50 as a CC pump and a DC EWP80 to support the cooling system with zero issues so far.
Escy said:
227bhp said:
I can't say I'm surprised, you're ignoring everything mentioned in this thread and just following the well trodden path to failure instead, well done. 
What are you basing this on? I haven't seen anyone do what i'm planning. 

The basics are:
Shift a lot of water, very quickly through water cooling rads fed by appropriately sized piping.
So you've picked a w@nky pump (mentioned in this thread) and are going to try to make it push water through two rads which are for cooling gas fed by pipes with the diameters of drinking straws?
Spend some time reading the thread properly, people who have actually done it (right and wrong) have spent time contributing their knowledge and experience.
Escy said:
I'll get some custom radiators made if the a/c condensers don't perform. I bought a Bosch pump 0392022002, it seems to be the common choice.
Just for reference, I measured flow of this BOSCH PCA pump in my CC setup. Mid engined Elise.19mm pipes, pro alloy engine radiator sized pre rad, PWR barrel charge cooler.
Flow of the pump alone in a bucket: 24l/min at zero pressure. In my CC setup, I got 7l/min!! This is good enough the cool the charge of a smart diesel, but not what most try to cool with it. You need to study pump maps in the same way as compressor maps of turbo chargers. What flow do I get at what pressure.
This is a good read to start with containing flow vs. pressure charts of various pumps.
http://mbworld.org/forums/w211-amg/411058-intercoo...
A pre rad for 19mm lines has connectors with a ID below 17mm! This is no good. I have a second CWA50. This should increase flow to 25l/min. Marginally OK. I will have 1 bar of back pressure in the CC system at this flow! The Bosch PCA has zero flow at 1 bar of back pressure. It never gets there :-)
A small CWA50, the 500HP BMW X6M contains two of them, flowed 12l/min. Both the BOSCH and the Pierburg CWA50 in series did 17l/min. Still not enough to cool 240g or air per second to near ambient temps. In Spa or the Autobahn I hit 45C above ambient with ease. Would I do it again? No, it is not cost efficient and not simple A simple air to air cooler even with s

You might also go hybrid. Fit a small air to air cooler behind one of the rear intakes and connect it in series with your charge cooler. This takes a lot of the load out of the system.
[
Edited by Ive on Monday 13th June 14:03
Max_Torque said:
er, nope.
Do the maths, and get back to me!
(hint: compare Cp for water and air, then consider the effect of residency time in both the PHE and LTR)
The lots buy you heat capacity. 4 J/(g*k). Air has about 1 J/(g*K).Do the maths, and get back to me!
(hint: compare Cp for water and air, then consider the effect of residency time in both the PHE and LTR)
This heat capacity helps you to slow down the heating of the water in the system and with it of the air.
If you only do a few seconds of WOT on the road, this will help you to keep the IATs low.
If the cooling power, so heat per time unit dissipated to the atmosphere, is low, your system will take a long time to recover, I.e. Cool down.
Next comes the fast part.
In order to cool down the air you need to remove a lot of thermal energy that needs to be stored in the water.
How much depends on how hot the air temperature comes out of your compressor, what mass flow it has and how much above ambient your target air temperature sits. How long the water resides in the heat exchanger is not important. Only mass flow counts. This is valid for turbulent flows.
A 300HP engine flows some 240g of air per second. Say that the turbo compressor exit temperature sits at 100C and you want it at 40C with 20C being ambient temperature. Crunch the numbers any you get that you need to shed 14.4kW of thermal energy.
Now let's assume your water enters the heat exchanger with 20C and exits it with 40C, equal to your target temp.
Again do the numbers any you find you need a tad under 11l/min of water to do that. This assumes both heat exchangers are 100% efficient. They are not. This drives demand up.
If that water now stays in the CC for 10ms flowing at near sonic speed or for 10 seconds is largely irrelevant. As long as the flow is highly turbulent, it won't matter. At these flow rates you are limited by the flow rate itself and the temperature of the incoming water.
Once your water exits the CC cooler than the air exiting it, your CC's heat transfer rate is insufficient. You need a bigger or better one. The other way to describe it is, if your air exits (significantly) hotter than the water.
If the water enters the CC warmer than ambient, than the pre rad is too inefficient.
If the water exits the CC cooler than the air exiting it, the CC is inefficient, either itself or due to flow rates.
If the water enters at ambient temperature, but air and water exit hotter than the target temperature, the flow rate is insufficient for that target.
As it is not uncommon to see CC system efficiencies of 30-50%, you need two to three times those 11l/min to cool that air for 300HP to 20C above ambient. If your target is 10C above ambient under sustained WOT, things get much harder. As the temperature difference across the pre radiator has dropped in half, it needs twice the air flow or needs to be twice the area or whatever means to double its cooling power per K of temperature difference.
On SELOC Chris Randall's Lotus Europa race car running 400HP uses 32mm lines, a DC EWP115 pump and flows 60l/min.
He stays below 20C above ambient on track. That is the best I have seen so far.
His advice: big pipes, monster pre radiator, lots of air flow and big pumps.
Any step reduction of barbs, inlets etc. create a huge pressure drop. Minimize those, chamfer edges.
Have the ID of a radiator barb match the ID of the pipe.
It is always important to separate the dynamic and the static behaviour of a CC system. For the road, you can cover up a lot of the isses by installing a large water reservoir or a charge cooler with tons of internal water volume. It will only warm up slowly and provide cool charge for a few seconds e.g. On a drag strip or a quick squirt on speed restricted roads.
On the Autobahn or a high speed track work, this component is of less importance. Here the static heat dissipation capabilities count. For this you need sufficiently fast flow, enough that the exit temperature of the water from the CC does not get hotter than your air temperature target, and you need enough pre rad too cool that flow back to ambient temp within a single pass of the pre rad.
In my CC system it takes about one minute of WOT before intake air temperatures stabilize some 45C above ambient.
This is not good. I have yet to measure the air temperature before the CC and the water temperatures before and after.
Only then can I really tell what is happening.
To cut things short. A 7l/min flow rate of a BOSCH PCA is no good on a turbocharged Porsche Boxter. At least it is not worth the trouble for the result he'll get. A simple Audi TT air to air cooler would have done the same job for a 1/10th of the cost and a 1/20th of the effort to install it.
Edited by Ive on Monday 13th June 21:34
Max_Torque said:
227bhp said:
The basics are:
Shift a lot of water, very quickly
er, nope.Shift a lot of water, very quickly
Do the maths, and get back to me!
(hint: compare Cp for water and air, then consider the effect of residency time in both the PHE and LTR)
It's pretty pointless babbling on in a language very few understand, you might aswell have written in Welsh.
Maybe that is why you do it.....
I've spent literally blooming ages looking at all options and to my mind you can't beat a simple air to air intercooler. This is my recent addition 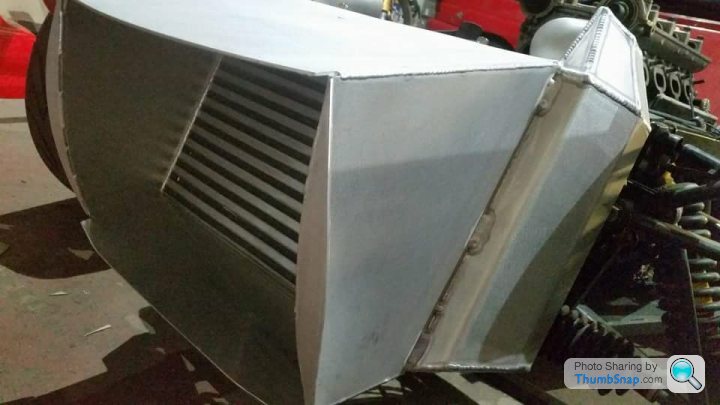
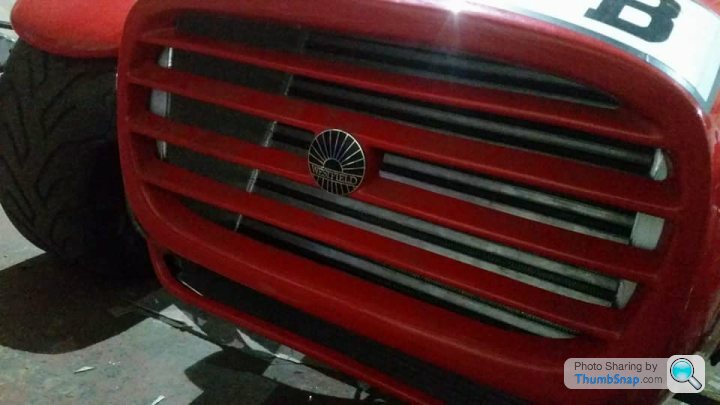
To be fair though this has meant relocation the rad.
If I were in your position I would run two intercoolers, like the old Renault 21 turbo, where the air con rads were.
Or you may just get away with one. Get a Garrett bar and plate core.
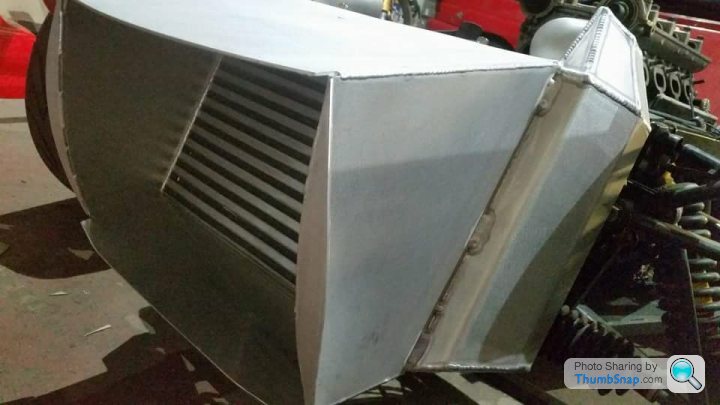
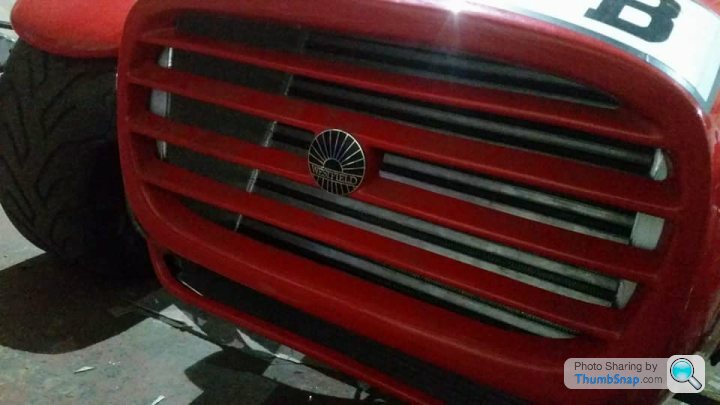
To be fair though this has meant relocation the rad.
If I were in your position I would run two intercoolers, like the old Renault 21 turbo, where the air con rads were.
Or you may just get away with one. Get a Garrett bar and plate core.
Gassing Station | Engines & Drivetrain | Top of Page | What's New | My Stuff