Charge cooler or intercooler? Which would suit?
Discussion
Basically, heat moves across a "Boundary" from hot to cold, and it is driven by the temperature difference and the transfer co-efficient.
The deltaT bit is easy to understand, the greater the differential, the more heat energy can pass in any given time period.
The transfer co-efficient is MUCH more complex when we are talking about fluids / gases, because velocity makes a huge difference (both local "macro" turbulence and the larger scale "average" velocity of the fluids.
Consider a hot stream of water, moving past an cooler alluminium "wall". If we assume the water molecules all at the same temp, the molecules closest to the wall loose their heat to the wall, but if the flow of the stream is laminar, and parallel to the wall, the molecules further away must transfer their heat to the molecules closer to the wall first. Local turbulence, the swirling and non laminar flow helps this mixing, increasing the heat transfer co-efficient.
Hence, as flow rate increases, assuming the flow becomes more turbulent, the heat transfer co-efficient increases (good) but any given molecule of water spends less time passing through the heat exchanger, so the first effect gets negated by the second one. The exact magnitudes of those effects, an hence the optimum flow velocity is non-trivial to calculate, and very much depends upon the macro design of the heat exchangers etc.
If you consider the PHE (Primary Heat Exchnanger) where heat is lost from the charge air and pushed into the intermediate coolant, this wants the fastest possible flow of the coldest possible coolant. Here, every time one molecule of coolant gets heated even slightly by the heat energy from the charge air, it gets pushed out the way and replaced by a nice new cold one.
So, viewed in isolation, the PHE performance increases with flow rate.
But at the other end of the system, where heat is rejected to ambient, the situation is different. Here, we want the slowest possible flow (that is commensurate with a creating enough turbulence for a decent transfer co-efficient) and the fastest, coldest possible flow of cooling air.
As result, when you test a complete system, you generally find that as flow rate is increased the performance of the PHE improves, but that of the LTR reduces, and so overall system effectiveness stays surprisingly constant! At very low flows (typically <7l/min) the lack of turbulence starts to dominate and system performance falls. And at very high flows, system loses result in poor pump efficiency (which incidentally heats up the coolant all on it's own!) and become im-practical.
Hence, you'll find OEM systems that flow, typically, between about 12 and 25l/min.
It's also worth noting the inherent corollary of intercooling systems that use an intermediate medium (ie the water) between charge air and ambient air: You want the lowest possible mean water temp for the PHE, but the highest possible average temp for the LTR. So again as the flow rate is increased, mean water temp falls (because the same amount of heat, carried by a higher mass flow, means a lower temperature) and this directly impacts on LTR performance, and the system rebalances!
The best option, is to understand (via measurement, calculation or simulation, (or even better, all three!!)), which part of your particular system is limiting, and to tailor the system flow to optimise that components performance, which will bring the best overall system effectiveness.
The deltaT bit is easy to understand, the greater the differential, the more heat energy can pass in any given time period.
The transfer co-efficient is MUCH more complex when we are talking about fluids / gases, because velocity makes a huge difference (both local "macro" turbulence and the larger scale "average" velocity of the fluids.
Consider a hot stream of water, moving past an cooler alluminium "wall". If we assume the water molecules all at the same temp, the molecules closest to the wall loose their heat to the wall, but if the flow of the stream is laminar, and parallel to the wall, the molecules further away must transfer their heat to the molecules closer to the wall first. Local turbulence, the swirling and non laminar flow helps this mixing, increasing the heat transfer co-efficient.
Hence, as flow rate increases, assuming the flow becomes more turbulent, the heat transfer co-efficient increases (good) but any given molecule of water spends less time passing through the heat exchanger, so the first effect gets negated by the second one. The exact magnitudes of those effects, an hence the optimum flow velocity is non-trivial to calculate, and very much depends upon the macro design of the heat exchangers etc.
If you consider the PHE (Primary Heat Exchnanger) where heat is lost from the charge air and pushed into the intermediate coolant, this wants the fastest possible flow of the coldest possible coolant. Here, every time one molecule of coolant gets heated even slightly by the heat energy from the charge air, it gets pushed out the way and replaced by a nice new cold one.
So, viewed in isolation, the PHE performance increases with flow rate.
But at the other end of the system, where heat is rejected to ambient, the situation is different. Here, we want the slowest possible flow (that is commensurate with a creating enough turbulence for a decent transfer co-efficient) and the fastest, coldest possible flow of cooling air.
As result, when you test a complete system, you generally find that as flow rate is increased the performance of the PHE improves, but that of the LTR reduces, and so overall system effectiveness stays surprisingly constant! At very low flows (typically <7l/min) the lack of turbulence starts to dominate and system performance falls. And at very high flows, system loses result in poor pump efficiency (which incidentally heats up the coolant all on it's own!) and become im-practical.
Hence, you'll find OEM systems that flow, typically, between about 12 and 25l/min.
It's also worth noting the inherent corollary of intercooling systems that use an intermediate medium (ie the water) between charge air and ambient air: You want the lowest possible mean water temp for the PHE, but the highest possible average temp for the LTR. So again as the flow rate is increased, mean water temp falls (because the same amount of heat, carried by a higher mass flow, means a lower temperature) and this directly impacts on LTR performance, and the system rebalances!
The best option, is to understand (via measurement, calculation or simulation, (or even better, all three!!)), which part of your particular system is limiting, and to tailor the system flow to optimise that components performance, which will bring the best overall system effectiveness.
Thanks for taking the time to explain things. If I add larger barbs onto my a/c condensers (19mm is as big as I can go) and run them in series so the water has a longer LTR residency time, providing they aren't too restrictive and the system is capable of over 7 litres per minute they should be up to the job.
They measure 330x275mm and are 19mm thick.
They measure 330x275mm and are 19mm thick.
Max_Torque said:
I've probably designed and developed something like 20 OEM and motorsport systems, so far, the LTR has always been the limiting factor (because ultimately you have to reject the heat to ambient, and the LTR has the lowest DeltaT across it)
Take a typical 550bhp engine chargecooling system i designed, at a heatflux of 60kW, effectiveness was dam nearly constant for between 7 and 25 l/min, when tested in the MIRA CWT, and only really fell right off below ~5l/min as flow turbulence fell in the system.
So i'll reiterate - Do the maths, work out the flow and sizing you need. It's all simple maths.
Or you, know, just guess like 99% of internet experts are doing........ ;-)
Max whilst I have the greatest respect for knowledge in the automotive arena, as noted a few posts earlier you are not sharing that knowledge. Posting "do the math" along with a load of acronyms doesn't add anything and comes across elitist. My day job is IT infrastructure, cars are my pastime. I can’t do the maths until I know the formula and ideally an example.Take a typical 550bhp engine chargecooling system i designed, at a heatflux of 60kW, effectiveness was dam nearly constant for between 7 and 25 l/min, when tested in the MIRA CWT, and only really fell right off below ~5l/min as flow turbulence fell in the system.
So i'll reiterate - Do the maths, work out the flow and sizing you need. It's all simple maths.
Or you, know, just guess like 99% of internet experts are doing........ ;-)
On my Dakar website I shared my trial and error over 10 pages. Nobody could tell me the principles of chargecooing (including PACE) - so it's all trial and error - but I did take the time to instrument the whole setup in order to prove if something made a difference or not.
I did spend quite a bit of time thinking about the speed of the coolant, but I couldn’t find any information and nobody contributed, so I left it with the Bosch PCA12.
As we know, part of that trial and error was to try a £60 Chinese ebay intercooler which worked and the CC remains on the shelf.
My 10 pages of research were done 10 years ago now (Gulp..) - things I never found the answer to were:
>What are the principles? Do we want the water flowing fast through the chargecooler and slow through the pre-radiator ?
>What flow rate of coolant is required?
>Should the chargecooler be long and thin or tall and narrow. In my case it was three cores in front of each other with the water going round in series – should I have flowed the water in parallel across those cores
>The pre-radiators – again, long tubes or short tubes, short or tall, thin or thick. What principle are we trying to achieve with the design of the radiator.
So why not post up the principles of chargcooling, the maths and a worked example taken from a decent OEM setup that could be applied to a DIY setup. That way you get to prove your knowledge of those 20 OEM systems and share some knowledge with likeminded enthusiasts who don’t have limitless supply of cash and time to spend on research.
Edited by eliot on Wednesday 15th June 09:23
Escy said:
Thanks for taking the time to explain things. If I add larger barbs onto my a/c condensers (19mm is as big as I can go) and run them in series so the water has a longer LTR residency time, providing they aren't too restrictive and the system is capable of over 7 litres per minute they should be up to the job.
They measure 330x275mm and are 19mm thick.
Series / parallel isn't actually that easy a question to answer! Residency time is actually the same for any given water molecule, because the flow rate is halved.They measure 330x275mm and are 19mm thick.
In series, the flow path is twice as long, and the average velocity is the same in each series rad, and twice that of the parallel setup, but the second rad has a much lower average DeltaT because it receives water already significantly cooled by the first rad!
In parallel, each rad has the same deltaT but the velocity in each is halved (assuming they share the total system flow equally) so heat transfer co-efficient will be reduced.
Which is the more important factor? Good question. Gut feeling says run in parallel as deltaT is a powerful factor, but ideally test both setups!
Edited by anonymous-user on Wednesday 15th June 19:01
People Who Know Things seem to live here, so...
I'm building the cheapest turbo conversion I can (seriously, the parts budget is under £400) for an LPG-powered trackday car. It's an E30 325i running a 1st generation LPG system, just a vaporiser and mixer. I've got most of the bits, just need to get hold of an intercooler.
Can I use one from a turbodiesel van such as an Expert, Transit etc? They're very cheap and presumably well developed, I just don't know how much boost they'll hold.
I'm building the cheapest turbo conversion I can (seriously, the parts budget is under £400) for an LPG-powered trackday car. It's an E30 325i running a 1st generation LPG system, just a vaporiser and mixer. I've got most of the bits, just need to get hold of an intercooler.
Can I use one from a turbodiesel van such as an Expert, Transit etc? They're very cheap and presumably well developed, I just don't know how much boost they'll hold.
handpaper said:
People Who Know Things seem to live here, so...
I'm building the cheapest turbo conversion I can (seriously, the parts budget is under £400) for an LPG-powered trackday car. It's an E30 325i running a 1st generation LPG system, just a vaporiser and mixer. I've got most of the bits, just need to get hold of an intercooler.
Can I use one from a turbodiesel van such as an Expert, Transit etc? They're very cheap and presumably well developed, I just don't know how much boost they'll hold.
Buy as big as you can in all capacities. Airflow paths, cooling paths etc.I'm building the cheapest turbo conversion I can (seriously, the parts budget is under £400) for an LPG-powered trackday car. It's an E30 325i running a 1st generation LPG system, just a vaporiser and mixer. I've got most of the bits, just need to get hold of an intercooler.
Can I use one from a turbodiesel van such as an Expert, Transit etc? They're very cheap and presumably well developed, I just don't know how much boost they'll hold.
And how much boost they'll hold depends on size ( force, area and other such nonsense ), and their construction ( and quality of construction )
Clearly a IC with crimped plastic end tanks will blow apart far sooner than an all metal constructed unit, or all welded.
handpaper said:
People Who Know Things seem to live here, so...
I'm building the cheapest turbo conversion I can (seriously, the parts budget is under £400) for an LPG-powered trackday car. It's an E30 325i running a 1st generation LPG system, just a vaporiser and mixer. I've got most of the bits, just need to get hold of an intercooler.
Can I use one from a turbodiesel van such as an Expert, Transit etc? They're very cheap and presumably well developed, I just don't know how much boost they'll hold.
This is a thread for chargecoolers (water cooled), there was a thread just recently in the Home mechanics section which would help you more if I remember right.I'm building the cheapest turbo conversion I can (seriously, the parts budget is under £400) for an LPG-powered trackday car. It's an E30 325i running a 1st generation LPG system, just a vaporiser and mixer. I've got most of the bits, just need to get hold of an intercooler.
Can I use one from a turbodiesel van such as an Expert, Transit etc? They're very cheap and presumably well developed, I just don't know how much boost they'll hold.
Max_Torque said:
Basically...
Thanks for taking time to post that up, I can understand the explanation, but one thing isn't clear. In other threads about engine cooling and EWP (http://www.pistonheads.com/gassing/topic.asp?h=0&f=66&t=1158978 there are probably others) it has been noted that efficency drops right off if you aren't shifting enough water. The only difference I can see is the temperatures dealt with - obviously the engine temps are much higher than the CC and being so much further away from ambient will (i'm guessing) cool a bit quicker.So why are you now saying the opposite?
227bhp said:
Max_Torque said:
Basically...
Thanks for taking time to post that up, I can understand the explanation, but one thing isn't clear. In other threads about engine cooling and EWP (http://www.pistonheads.com/gassing/topic.asp?h=0&f=66&t=1158978 there are probably others) it has been noted that efficency drops right off if you aren't shifting enough water. The only difference I can see is the temperatures dealt with - obviously the engine temps are much higher than the CC and being so much further away from ambient will (i'm guessing) cool a bit quicker.So why are you now saying the opposite?
Engine cooling works at a mean temperature that is way above ambient. Typical mean coolant temp for a modern car would be just over 90degC, and even in a 50degC ambient, that's a 40degC deltaT. As such, the performance of the heat rejection elements (radiator) is much less compromised than for a charge cooling loop (which has a big deltaT in the PHE and a very small one in the LTR)
(The aim with chargecooling is to get the charge air back down to ambient temp, so the system is necessarily operating with a much smaller deltaT.)
Metal temps in your engine, although you can't see or feel them, are also significantly higher than the bulk coolant temp, reaching well over 150degC in the hottest locations under full load. Here, nucleate boiling occurs, and although that initially rapidly removes heat from the metal engine structure, unless that vapour is quickly "washed away" and replaced with fluid, the heat transfer co-efficient collapses. As such, a coolant system will need to be run at a high flow rate to maintain a high transfer co-efficient.
Engine coolant loops are also not linear, they have large areas of low intensity heat (say around the bores) and small areas of high intensity (like between the exhaust valve bridge etc). In old system we just sloshed around lot of water in large volume coolant passages, but these days "precision" cooling designs use a much smaller volume of water, moving much faster in much smaller passages to remove heat effectively from various different parts of the engine.
Also, not a lot of people understand that for anything but drag car, around 30 to 60% of the intercooler heat flux is removed by the charge air itself!! IE, because boost is transient (unless drag racing / or at vmax) when you come off boost and compressor outlet temps fall, the air itself removes the heat "soaked" into the chargecooler system during the on-boost period
I'm just chatting to a guy who is running some parts I supplied for an engine years ago, he's just had it on the dyno at over 500bhp with a CC fitted, 20 ltrs, 38mm hoses, 90lph pump, 600 x 400 x 45 rad, PWR barrel, 14'c ambient and 26' inlet mani temp at the end of a run.
That's quite cool, I was suspicious, but he swears it's correct.
That's quite cool, I was suspicious, but he swears it's correct.
Evoluzione said:
I'm just chatting to a guy who is running some parts I supplied for an engine years ago, he's just had it on the dyno at over 500bhp with a CC fitted, 20 ltrs, 38mm hoses, 90lph pump, 600 x 400 x 45 rad, PWR barrel, 14'c ambient and 26' inlet mani temp at the end of a run.
That's quite cool, I was suspicious, but he swears it's correct.
That's great but how long was the run? Assuming it's not long and the system has only cycled the 20ltr through the system once you would expect the intake temps to be cold, even with no low temp rad! This is the principle with drag race setups that use ice water (sure you are fully aware of this).That's quite cool, I was suspicious, but he swears it's correct.
Would be interesting to see how long the run was. And maybe how much time in boost as well?
Also is there a ratio for low temp rad to chargecooler in terms of size that should be aimed for? Or is it a case of just fit as much low temp rad in there as you can?
chuntington101 said:
Evoluzione said:
I'm just chatting to a guy who is running some parts I supplied for an engine years ago, he's just had it on the dyno at over 500bhp with a CC fitted, 20 ltrs, 38mm hoses, 90lph pump, 600 x 400 x 45 rad, PWR barrel, 14'c ambient and 26' inlet mani temp at the end of a run.
That's quite cool, I was suspicious, but he swears it's correct.
That's great but how long was the run? Assuming it's not long and the system has only cycled the 20ltr through the system once you would expect the intake temps to be cold, even with no low temp rad! This is the principle with drag race setups that use ice water (sure you are fully aware of this).That's quite cool, I was suspicious, but he swears it's correct.
Would be interesting to see how long the run was. And maybe how much time in boost as well?
Also is there a ratio for low temp rad to chargecooler in terms of size that should be aimed for? Or is it a case of just fit as much low temp rad in there as you can?
Although to answer your question, I didn't cross examine him, so don't really know. It wasn't a cheap system I know that.
I use water/meth injection on a progressive controller on a 2ltr TFSi golf .... we gained nearly 40hp and
our intake temps are very good now and instant. Running around 470 hp @ 1.5bar
There are plenty on the market i use Devils own from the US ...
https://www.snowperformance.net/
http://www.alcohol-injection.com/en/
Water Methanol works great. Got it, too.
For CC, try to fit as large of a low temp radiator as possible. The worst than can happen is that half the rad carries cold water. But that won't happen.
The closer you try to get tot ambient temperatures the harder it gets.
If you are happy with cooling from 120C to 60C, CC is relatively easy. Going from 120C to say 30C at 20C ambient is much harder.
In the Lotus Elise running a Honda K20A2 and a Eaton MP62 blower, CC gets them from 300 to about 350HP. They still have IATs on the order of 90C after CC. This is still way cooler than without CC and the very high temperatures in the CC circuit allow to get away with a rather small low temp heat exchanger while still getting a significant IAT reduction. 350Hp in a 850kg car is plenty fast.
Non-CC or intercooled MP62 Roots blowers are not the most efficient thing on earth at those flow and pressure ration levels.
For CC, try to fit as large of a low temp radiator as possible. The worst than can happen is that half the rad carries cold water. But that won't happen.
The closer you try to get tot ambient temperatures the harder it gets.
If you are happy with cooling from 120C to 60C, CC is relatively easy. Going from 120C to say 30C at 20C ambient is much harder.
In the Lotus Elise running a Honda K20A2 and a Eaton MP62 blower, CC gets them from 300 to about 350HP. They still have IATs on the order of 90C after CC. This is still way cooler than without CC and the very high temperatures in the CC circuit allow to get away with a rather small low temp heat exchanger while still getting a significant IAT reduction. 350Hp in a 850kg car is plenty fast.
Non-CC or intercooled MP62 Roots blowers are not the most efficient thing on earth at those flow and pressure ration levels.
227bhp said:
On reflection (many years on) with a different car If I was to do it again I would:
Put a large modern car rad on the front.
Consider putting an LPG tank in the spare wheel well and use it as a reservoir. It is increased weight, but at the rear less of a problem. It doesn't have to be full.
Use a much more powerful pump (more LPH) than the usual weedy Bosch item.
That's what I did some years ago in my Corrado project. There was zero room for an air-air cooler without chopping the front of the car, which is something I just don't do on road cars. So air-water it was and it worked extremely well.Put a large modern car rad on the front.
Consider putting an LPG tank in the spare wheel well and use it as a reservoir. It is increased weight, but at the rear less of a problem. It doesn't have to be full.
Use a much more powerful pump (more LPH) than the usual weedy Bosch item.
I used a full frontal custom sized Setrab radiator, Meziere 20gpm water pump (with bleed port) and a 4 gallon alloy tank in the boot.
I remember on one tuning session, it spent all day on the dyno and the water in the tank got lukewarm at best. IATs never exceeded 50 in the dyno cell on the day. Compared to other VW projects I've done over the years, it massively out performed front and side mount air-air setups.
I did also drive another Corrado with the same setup, but with air-air instead and it was noticeably laggier.
As much as I enjoy delving into the science behind these things, real world experimenting is sometimes the only way to find out for sure. Some you win, some you lose.
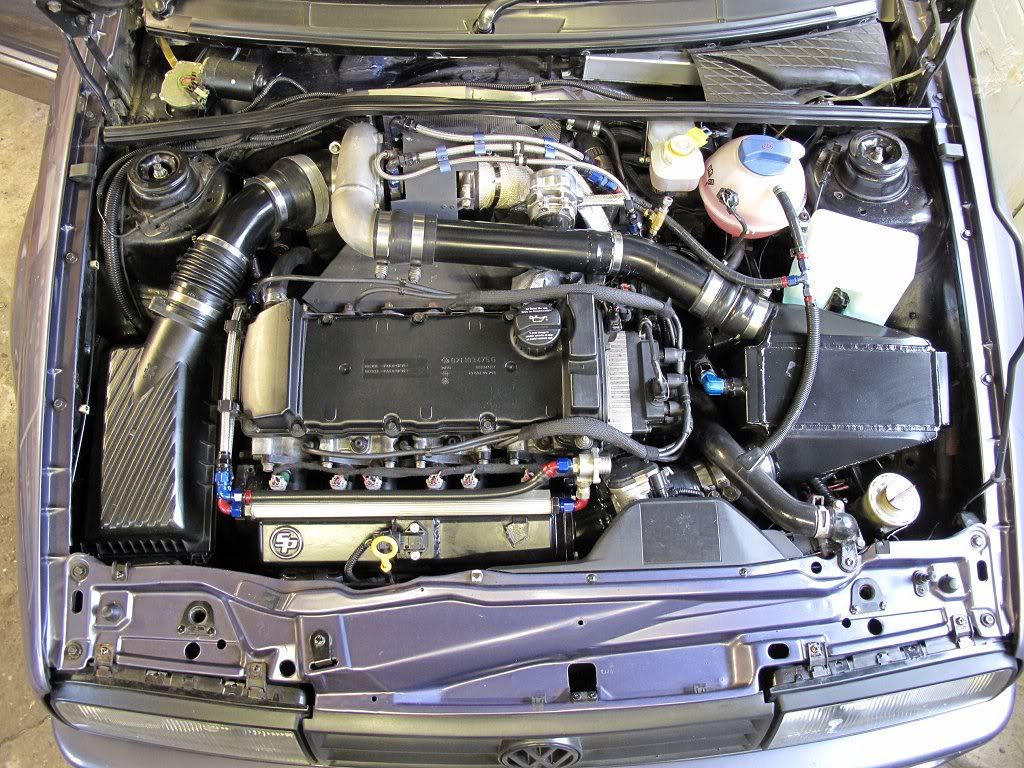
What chargecooler core did you use? Also how long were he pulls? As Max Torque said a lot of the heat is pulled out the system when not in boost. So if you are only doing shorts runs you should be able to keep temls down with a decent size low temp rad and a decent sized charge cooler.
IIRC it was a Spearco core with end tanks welded on by my supplier.
Yeah a lot of the day was idle and part load mapping and at least a dozen full load pulls. Air-air is simpler and cheaper but I was happy with my CC setup and it did the job well in that application. What amazed me was temperature drop across that tiny core. I didn't take any actual measurements but under boost, I could feel the inlet end was warm and the outlet was cold. It was a road car so full throttle pulls weren't frequent, so plenty of time to soak the heat away during cruising.
As already discussed, using the right components and sizing is the key to it. I suppose it comes down to a comparison of quenching hot metal in a bucket of water, or pissing on it? Spraying water onto air-air can be quite effective too.
Yeah a lot of the day was idle and part load mapping and at least a dozen full load pulls. Air-air is simpler and cheaper but I was happy with my CC setup and it did the job well in that application. What amazed me was temperature drop across that tiny core. I didn't take any actual measurements but under boost, I could feel the inlet end was warm and the outlet was cold. It was a road car so full throttle pulls weren't frequent, so plenty of time to soak the heat away during cruising.
As already discussed, using the right components and sizing is the key to it. I suppose it comes down to a comparison of quenching hot metal in a bucket of water, or pissing on it? Spraying water onto air-air can be quite effective too.
I thought i'd post up my chargecooler since I got some good advice from this thread (copied from my build thread)
There isn't much space at the front of a Boxster, it's impressive how Porsche have mounted the radiators, they've made the most out of the available airflow with some nice ducting. I don't want to mess with the shrouds as it's not like i'm going to be able to design anything better. Being a Boxster S, it has the extra radiator in the middle. Most Boxsters that are turbocharged use this centre radiator as the charge cooler radiator, I spoke to someone who tried it, the verdict was "fine on the street, won't cope on track". With that in mind I decided to go a different route and fit a pair of radiators either side in front of the engine radiators. I bought a pair of Polo radiators but they were too big, I then bought a pair of classic Mini radiators but they were also too big. I looked into large oil cooler radiators, quad bike and motorbike radiators but couldn't find anything the size I wanted so I thought I may as well see if I could use the air conditioning condensers (modified to take larger pipes).




I ran the pipework where the old a/c pipes used to be, up over the front arch liner, under the floor and into the boot through the air vent. I've put 6 bleed points in the various high points of the pipework.


I initially bought a Bosch pump (the one used on the Mk1 Focus RS) but took some advice that it wasn't going to be up to the job. I started looking at other options and it looked like the Pierburg pumps are the best performers, I'm using a CWA-50 which is controlled by a tiny-CWA from Tecomotive. It will allow me to have the pump speed controlled by the coolant temperature, no point in blasting coolant around at full speed if i'm sat in traffic. I have to say, Tobias at Tecomotive was extremely helpful.

The chargecooler core was mounted in the boot, I went for a pretty large one. I bought a header tank from the US, there aren't many options I found in the UK. The tank is 5.5 litres, the more water capacity, the longer it will take to warm up. I don't know what the total capacity is, would probably say around 15 litres. I wish I could weld alloy so I could design my own bits as using off the shelf parts has made for a compromise. The tank should be the highest point of the system but I can't mount it any higher as sit's under the rear light and that's pretty much the only place it was going to fit. As the highest point is the chargecooler, i've drilled a hole and added a bleed screw that i'll use to top the system up, the cap on the tank will stay closed. You can see the Tecomotive pump controller in the picture, it's the red square that's by the expansion tank, it'll be mounted into the boot carpet.

It's taken me a while putting it all together, i'm please with how the install looks, hopefully i'm pleased with the results.
There isn't much space at the front of a Boxster, it's impressive how Porsche have mounted the radiators, they've made the most out of the available airflow with some nice ducting. I don't want to mess with the shrouds as it's not like i'm going to be able to design anything better. Being a Boxster S, it has the extra radiator in the middle. Most Boxsters that are turbocharged use this centre radiator as the charge cooler radiator, I spoke to someone who tried it, the verdict was "fine on the street, won't cope on track". With that in mind I decided to go a different route and fit a pair of radiators either side in front of the engine radiators. I bought a pair of Polo radiators but they were too big, I then bought a pair of classic Mini radiators but they were also too big. I looked into large oil cooler radiators, quad bike and motorbike radiators but couldn't find anything the size I wanted so I thought I may as well see if I could use the air conditioning condensers (modified to take larger pipes).




I ran the pipework where the old a/c pipes used to be, up over the front arch liner, under the floor and into the boot through the air vent. I've put 6 bleed points in the various high points of the pipework.


I initially bought a Bosch pump (the one used on the Mk1 Focus RS) but took some advice that it wasn't going to be up to the job. I started looking at other options and it looked like the Pierburg pumps are the best performers, I'm using a CWA-50 which is controlled by a tiny-CWA from Tecomotive. It will allow me to have the pump speed controlled by the coolant temperature, no point in blasting coolant around at full speed if i'm sat in traffic. I have to say, Tobias at Tecomotive was extremely helpful.

The chargecooler core was mounted in the boot, I went for a pretty large one. I bought a header tank from the US, there aren't many options I found in the UK. The tank is 5.5 litres, the more water capacity, the longer it will take to warm up. I don't know what the total capacity is, would probably say around 15 litres. I wish I could weld alloy so I could design my own bits as using off the shelf parts has made for a compromise. The tank should be the highest point of the system but I can't mount it any higher as sit's under the rear light and that's pretty much the only place it was going to fit. As the highest point is the chargecooler, i've drilled a hole and added a bleed screw that i'll use to top the system up, the cap on the tank will stay closed. You can see the Tecomotive pump controller in the picture, it's the red square that's by the expansion tank, it'll be mounted into the boot carpet.

It's taken me a while putting it all together, i'm please with how the install looks, hopefully i'm pleased with the results.
Gassing Station | Engines & Drivetrain | Top of Page | What's New | My Stuff