ITB question on the vacuum
Discussion
Aiming this question at those who have done ITB setups on cars that used to run a single throttle.
I am doing an ITB setup on my turbo car... Main reason is I want DBW so I can have downshift blips.
Sounds like a lot of work for something so simple, but it means (and has resulted in) some significant changes, for example my M800 ecu is max'd out on the pin count, so instead of throwing further money at it expanding it etc I decided to buy an M150, Im also changing the coils for more powerful items and have bought ID850 injectors (purely for a little extra safety margin as I do run both pretty close to what i consider the limit).
Additionally my very ugly intake plenum is on display under the rear clam due to the perspex engine cover and it would be great to have a decent looking setup.
So with all these other major changes I might as well go whole hog with ITB, tuned runner lengths and a carbon plenum.... I have done the research and made the plenum, trumpets and the ITB (massive amount of work), had the car put on a hub dyno on actuator pressure to get a full 'before' reading and I am now on the final stage making the vacuum take offs, brakes of the DBW actuators etc.
The car is a 3.0l V6, I run a rising rate fuel pressure and vacuum brakes along with a MAP sensor.
My plan has been to run 2 separate vacuum take offs, 1 that will feed the fuel pressure actuator and brakes, the other dedicated top MAP.... but given I am going to be setting the ECU to blip the throttle on down shifts, and on track run full throttle upshifts, will i actually have enough vacuum to provide assistance to the brakes or is it going to be marginal.
I know they have a 1 way valve so in theory you have spare capacity, but cars like my M5 have electric assisted brakes.... is this a hint that in practice its going to be an issue?
I am doing an ITB setup on my turbo car... Main reason is I want DBW so I can have downshift blips.
Sounds like a lot of work for something so simple, but it means (and has resulted in) some significant changes, for example my M800 ecu is max'd out on the pin count, so instead of throwing further money at it expanding it etc I decided to buy an M150, Im also changing the coils for more powerful items and have bought ID850 injectors (purely for a little extra safety margin as I do run both pretty close to what i consider the limit).
Additionally my very ugly intake plenum is on display under the rear clam due to the perspex engine cover and it would be great to have a decent looking setup.
So with all these other major changes I might as well go whole hog with ITB, tuned runner lengths and a carbon plenum.... I have done the research and made the plenum, trumpets and the ITB (massive amount of work), had the car put on a hub dyno on actuator pressure to get a full 'before' reading and I am now on the final stage making the vacuum take offs, brakes of the DBW actuators etc.
The car is a 3.0l V6, I run a rising rate fuel pressure and vacuum brakes along with a MAP sensor.
My plan has been to run 2 separate vacuum take offs, 1 that will feed the fuel pressure actuator and brakes, the other dedicated top MAP.... but given I am going to be setting the ECU to blip the throttle on down shifts, and on track run full throttle upshifts, will i actually have enough vacuum to provide assistance to the brakes or is it going to be marginal.
I know they have a 1 way valve so in theory you have spare capacity, but cars like my M5 have electric assisted brakes.... is this a hint that in practice its going to be an issue?
With the caveat that i have no idea why you needed to go ITB to get DBW, in my experience, you won't have sufficient vacuum source to ensure complete brake booster performance, and even if you do, the bleed air will almost certainly mess up your AFR distribution.
Even without any throttle blipping on downshifts you will have to cross link your ITBs to get a decent vac source, which kinda defeats the point to some degree
Move the brake booster to a mechanical vac pump (usually driven off cam shaft) i'd suggest!
Even without any throttle blipping on downshifts you will have to cross link your ITBs to get a decent vac source, which kinda defeats the point to some degree
Move the brake booster to a mechanical vac pump (usually driven off cam shaft) i'd suggest!
Max_Torque said:
With the caveat that i have no idea why you needed to go ITB to get DBW, in my experience, you won't have sufficient vacuum source to ensure complete brake booster performance, and even if you do, the bleed air will almost certainly mess up your AFR distribution.
Even without any throttle blipping on downshifts you will have to cross link your ITBs to get a decent vac source, which kinda defeats the point to some degree
Move the brake booster to a mechanical vac pump (usually driven off cam shaft) i'd suggest!
Forgive my ignorance, but as I'm looking at ITBs on a turbo engine I have an interest and some ideas on this which I hope will help the debate (and me!).Even without any throttle blipping on downshifts you will have to cross link your ITBs to get a decent vac source, which kinda defeats the point to some degree
Move the brake booster to a mechanical vac pump (usually driven off cam shaft) i'd suggest!
I don't understand why ITB for DBW either.....
If you had vac before, then you will have the same now, so how can anything be any different? Ok, so it's coming from a much smaller area from the butterflies to the cylinder, and no longer has the plenum or settling chamber (call it what you will), but it's still present. You can create another small plenum if the pulses are too strong.
The vac supply to/from the brake is not a constant stream, once it's topped up it stops.
You can use the TPS combined or separate to the MAP to tell the ECU what is going on.
Edit:
I can see how feeding the cylinders to blip the throttle is where the problem is though, I'm not going to have that problem.....
Edited by Evoluzione on Friday 3rd June 14:50
It isn't common to use MAP with multiple TBS but the early VHPD engines in Exiges and Caterham SLRs did just that, they used four separate vacuum takeoff down stream on the throttle plate which were simmered together and routed to the ECU map sensor. In those situations I prefer Alpha-n to MAP.
Dave
Dave
Max_Torque said:
With the caveat that i have no idea why you needed to go ITB to get DBW
I didn't, its just if I am changing so many other things including the plenum etc then I might as well go ITB rather than stick with the single throttle... plus I do like a challenge and developing new thingsMax_Torque said:
in my experience, you won't have sufficient vacuum source to ensure complete brake booster performance, and even if you do, the bleed air will almost certainly mess up your AFR distribution.
Even without any throttle blipping on downshifts you will have to cross link your ITBs to get a decent vac source, which kinda defeats the point to some degree
Move the brake booster to a mechanical vac pump (usually driven off cam shaft) i'd suggest!
I was hoping to get some real world experience from you on this... sounds like i can just have one then which feeds the fuel pressure and MAP, of cause it will need to be linked to give a balanced sourceEven without any throttle blipping on downshifts you will have to cross link your ITBs to get a decent vac source, which kinda defeats the point to some degree
Move the brake booster to a mechanical vac pump (usually driven off cam shaft) i'd suggest!
I believe some cars with ITB's use what could be best described as a vacuum chamber - a small additional chamber/box into which each runner (downstream of the throttle butterfly) is linked via small bore vac hoses.
The various items that then require a vac feed are tee'd off this additional chamber.
For added bling I guess it could be made nice and pretty out of stainless or carbon.
stevieturbo said:
Given it isnt a heavy vehicle etc....maybe just dump the servo ?
That certainly removes that aspect of any problem.
Then for fuel pressure regulator...just take this reading from the plenum which would be more stable, and tune around the fact it will never see vacuum ?
My Ultima with very similar weight and brakes had no servo... brakes felt horrible on the road and I definitely don't want to go that route again. Lots of electric diesel pumps around, will probably fit one at the front of the car.That certainly removes that aspect of any problem.
Then for fuel pressure regulator...just take this reading from the plenum which would be more stable, and tune around the fact it will never see vacuum ?
andygtt said:
My Ultima with very similar weight and brakes had no servo... brakes felt horrible on the road and I definitely don't want to go that route again. Lots of electric diesel pumps around, will probably fit one at the front of the car.
Oddly a friend just changed his Subaru by removing the servo and he finds no problem at all. We were both sceptical about it going to be horrible, but it really wasnt.All done with a very cheap servo delete kit which was a simple bracket and new actuating rod.
Maybe find a diesel alternator that fits ? most of them will have a vacuuum pump on the back of them.
I do like my servo though....although I'm hauling over 1700kgs around !
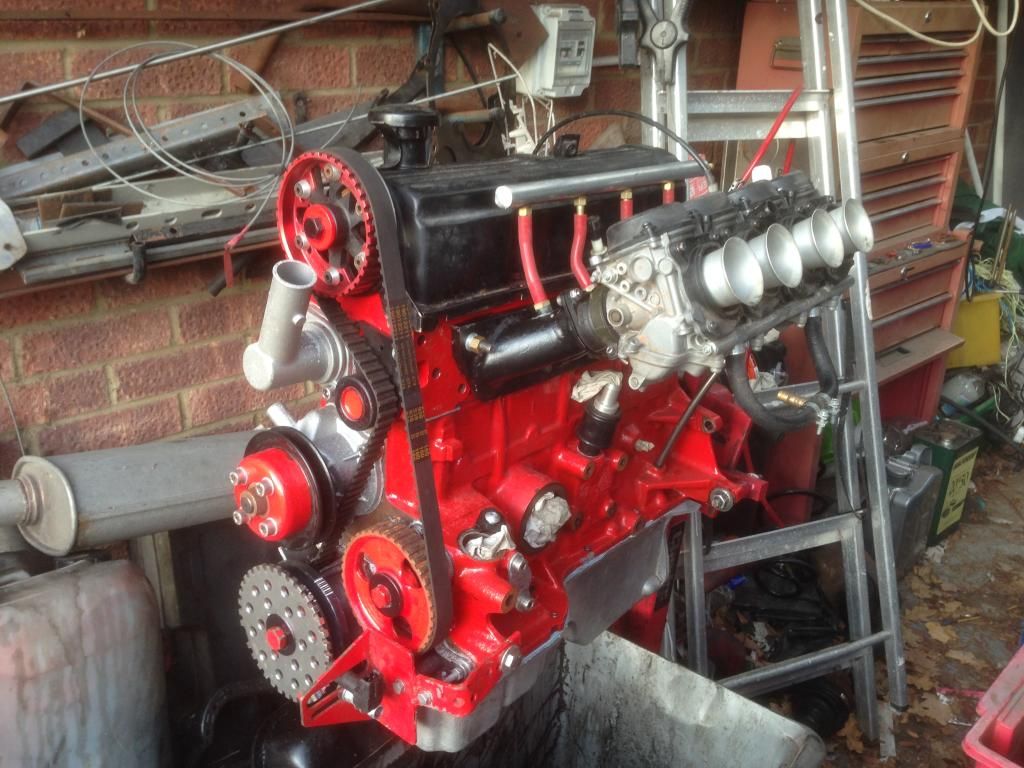
Running MAP and servo and this is one solution
Individual vac take offs after the butterfly's
Recommendation is for 1" X 2" X 3" box but I've found the tube works with one way valve for the servo link
Smooths out vac pulse was the main reason for me
Don't put the one way valve before the ecu feed, ask me how I know?
what makes you think you wont have enough vacuum for brakes? unless youve got cams with quite a bit more overlap than stock it should be fine. if not an electric vacuum pump (Hella UP30 or UP32), vacuum reservoir with vacuum switch works to supplement to whatever level of vacuum you need.
Inline__engine said:
what makes you think you wont have enough vacuum for brakes? unless youve got cams with quite a bit more overlap than stock it should be fine. if not an electric vacuum pump (Hella UP30 or UP32), vacuum reservoir with vacuum switch works to supplement to whatever level of vacuum you need.
PaulKemp said:
Running MAP and servo and this is one solution
Individual vac take offs after the butterfly's
Recommendation is for 1" X 2" X 3" box but I've found the tube works with one way valve for the servo link
Smooths out vac pulse was the main reason for me
Don't put the one way valve before the ecu feed, ask me how I know?
I think you're missing the point (as was I initially). He's worried it won't have enough vac because the engine is still being fed air to keep it revving in between gear changes therefore there won't be much vacuum formed.Individual vac take offs after the butterfly's
Recommendation is for 1" X 2" X 3" box but I've found the tube works with one way valve for the servo link
Smooths out vac pulse was the main reason for me
Don't put the one way valve before the ecu feed, ask me how I know?
Possibly a suck it n see job....
Inline__engine said:
what makes you think you wont have enough vacuum for brakes? unless youve got cams with quite a bit more overlap than stock it should be fine. if not an electric vacuum pump (Hella UP30 or UP32), vacuum reservoir with vacuum switch works to supplement to whatever level of vacuum you need.
My concern over having enough vacuum is because I have 3 significant factors:1. My current setup has Long runners with a plenum at the end so a lot of volume under vacuum, the new setup the runners are shorter plus only half of them can be under vacuum, plus the plenum isn't under vacuum.... So comparatively I will have a fraction of the volume of air available to take vacuum from.
2. On straights I can run full throttle shifts, so Zero vacuum on straights.
3. In the corners I will run a downshift blip to hold the revs while changing down.
All these factors reduce the vacuum available over the stock car... Cams are actually fairly mild.
Can't you just run non-return valves on the vacuum ports for each cylinder? That should generate enough vacuum for a brake servo if you keep them close enough to the ports.
For MAP measurement, you need to sample synchronously with engine speed and at a specific angle - I think it is 40°ATDC from memory - and then you get a superbly linear signal.
edit - the paper is SAE 2003-32-0084 and the sampling angle is 150°BTDC ignition, which is described in the paper as 30°ABDC compression. I think I've got that right.
For MAP measurement, you need to sample synchronously with engine speed and at a specific angle - I think it is 40°ATDC from memory - and then you get a superbly linear signal.
edit - the paper is SAE 2003-32-0084 and the sampling angle is 150°BTDC ignition, which is described in the paper as 30°ABDC compression. I think I've got that right.
Edited by AER on Monday 6th June 02:42
Gassing Station | Engines & Drivetrain | Top of Page | What's New | My Stuff