Air to water intercoolers - educate me
Discussion
leave the crank alone except for a check of its balancing.
with a Rotrex blower, boost never dropped with rpm, whetever pulley I mounted or which of the two Rotrex units I used, a C30-74 and a C30-94.
I believe the TT units start slipping internally past a certain load level due to incorrect engine oil.
with the right oil and oil temp, the TT unit should behalf similar to the Rotrex units.
The next thing that can cause boost to drop is the installation of a very restrictive restrictor in the inlet.
with a Rotrex blower, boost never dropped with rpm, whetever pulley I mounted or which of the two Rotrex units I used, a C30-74 and a C30-94.
I believe the TT units start slipping internally past a certain load level due to incorrect engine oil.
with the right oil and oil temp, the TT unit should behalf similar to the Rotrex units.
The next thing that can cause boost to drop is the installation of a very restrictive restrictor in the inlet.
Ive said:
The next thing that can cause boost to drop is the installation of a very restrictive restrictor in the inlet.
Even quite a small protusion into the air flow can cause a substantial restriction - much greater than just the area reduction. It only needs a slightly misaligned / unmatching joint to leave a step.What I have done to optimise the inlet was to fit a small pipe fitting close to the inlet and in the elbow of the SC outlet.
This allowed me to determine the pressure ratio and the inlet pressure losses.
In the final version I was at 60 mbar inlet pressure loss and this with a pre-compressor throttle body of 55mm plate diameter.
Before the optimisation I had a poorly fitted adapter pipe near the air filter causing a total pressure drop of 200 mbar before the SC.
Boost raised from 0.83 bar to tad over 1 bar by just reducing inlet pressure losses from 200 mbar to 60 mbar. We talk about a unrestricted Rotrex C30-94 at the max rpm limit feeding a 1.8l Rover K.
With these measurements the Rotrex compressor map figures, especially the pressure ratio vs. SC rpm started to make sense and fitted well.
In this map you can see that the pressure ratio stays constant past a certain air flow at 100000 rpm. This is why you get about the same boost with a 1.8l K and a Honda K20 despite the latter digesting a third more air and generating crudely about a third more power accordingly.
This allowed me to determine the pressure ratio and the inlet pressure losses.
In the final version I was at 60 mbar inlet pressure loss and this with a pre-compressor throttle body of 55mm plate diameter.
Before the optimisation I had a poorly fitted adapter pipe near the air filter causing a total pressure drop of 200 mbar before the SC.
Boost raised from 0.83 bar to tad over 1 bar by just reducing inlet pressure losses from 200 mbar to 60 mbar. We talk about a unrestricted Rotrex C30-94 at the max rpm limit feeding a 1.8l Rover K.
With these measurements the Rotrex compressor map figures, especially the pressure ratio vs. SC rpm started to make sense and fitted well.
In this map you can see that the pressure ratio stays constant past a certain air flow at 100000 rpm. This is why you get about the same boost with a 1.8l K and a Honda K20 despite the latter digesting a third more air and generating crudely about a third more power accordingly.
That's very interesting, thank you. I will have 52mm piping running from the air box to the SC and the same size from the SC outlet to the IC, and then on to the inlet manifold. At that point there is a step up to 58mm (from memory) where the throttle body was originally located and the charge moves into the original VVC inlet manifold (albeit modified to to allow the inlet to face in the opposite direction).
I'm using a home made airbox built into the bulkhead which should hopefully utilise a high pressure area at the base of the windscreen (with the help of a bonnet scoop) to get a straight inlet run into the SC.
Listening to your experience, I'll try to ensure that there aren't any protrusions into the airflow.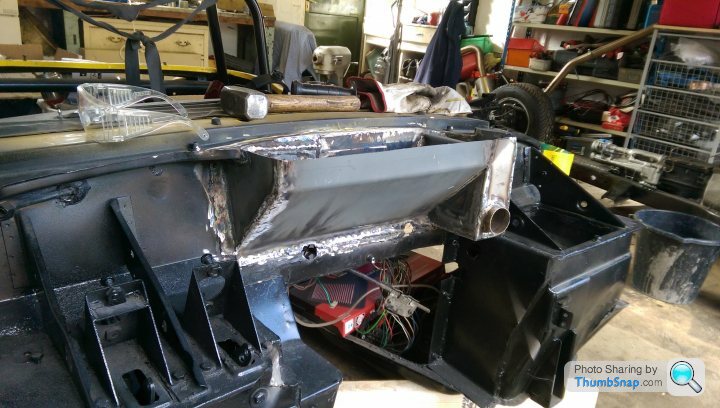
I'm using a home made airbox built into the bulkhead which should hopefully utilise a high pressure area at the base of the windscreen (with the help of a bonnet scoop) to get a straight inlet run into the SC.
Listening to your experience, I'll try to ensure that there aren't any protrusions into the airflow.
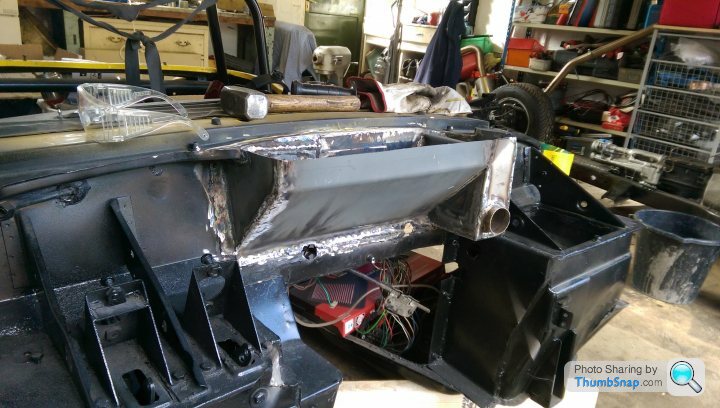
at the inlet, try to maintain a cross section as large as the SC inlet all the way from the air filter inlet to the SC inlet.
So if the SC inlet has a ID of 60mm, try to have at least the equivalent cross section of a 60mm pipe everywhere if possible.
The inlet is very sensitive to restrictions, much less than the outlet.
So if the SC inlet has a ID of 60mm, try to have at least the equivalent cross section of a 60mm pipe everywhere if possible.
The inlet is very sensitive to restrictions, much less than the outlet.
Ive said:
at the inlet, try to maintain a cross section as large as the SC inlet all the way from the air filter inlet to the SC inlet.
At least as large. A small gradual reduction in the direction of flow is OK and actually beneficial as it discourages stagnation. Any increase in area is best avoided or minimised as that encourages boundary layer growth and stagnation. itiejim said:
Thanks for the input, I'll take your advice on the ring gaps. Should I keep the second ring gap as per OE spec?
I'm building it as a VVC with Westwood liners and the Turbo Technics pistons and rods. I'll probably get the crank nitride and the lot balanced.
Are you running 300+ bhp through a totally standard bottom end?
yep, from a rover 75, plenty of clearance on the rings to allow for the boost, im back on the dyno on sunday to see if we can play with the cams and put a little bit more boost in after peak torque to help it at the top end.I'm building it as a VVC with Westwood liners and the Turbo Technics pistons and rods. I'll probably get the crank nitride and the lot balanced.
Are you running 300+ bhp through a totally standard bottom end?
Dont know if your on facebook but if you look for Lee Connor and my main picture is a black lotus I can show you what ive done etc
Gassing Station | Engines & Drivetrain | Top of Page | What's New | My Stuff