short intake restriction calcs?
Discussion
Max_Torque said:
The 2.0 engine was just an example that you can' use exhaust diameter as an indicator to inlet diameter, other than the exhaust needs to be, roughly, twice the cross sectional area of the intake!
This is getting somewhat surreal now. What you're telling the OP is that if his engine has twin 2.5" exhausts then it should manage at the other end on a single 2.5" inlet. I suspect he isn't going to believe that either.Anyway, back to you Mr OP as I'm a bit bemused by what Max is trying to say but I'll leave that between the two of you. Firstly I've just worked out what you meant by fwhp which I'd originally taken to mean at the wheels although I wasn't sure what the f was supposed to be. "front" maybe although that made no sense for a V8. You mean flywheel horsepower I think. I've only ever used that when spelled out in full for clarity although whp is quite common for "wheel horse power". So I've erroneously been working on 500 wheel bhp and hence maybe 580 flywheel. So if it's really only 500 flywheel bhp then that's a whole new ball of wax.
Forgetting that for now let's get back into relative sizing of exhausts and intakes. This isn't a new topic obviously. Vizard has been looking at these in CFM flow terms for decades as have many others. Going right back to his Mini books I think he used to reckon to get no restrictions you needed 1.5 CFM per flywheel bhp for intakes and 2.2 CFM per bhp for exhausts. I forget at what pressure drop but that's not relevant for now as we are only interested in the ratio. I think back in those days he worked at 25" of water as I always have but since moving to the States he's got sucked into the 28" thing that the yanks use. There was also another standard for flowing carbs which I think was 1.5 inches of mercury and maybe that's what he used above but I'm not sure. I'll ask him sometime.
Anyway obviously many other factors affect this ratio such as the number of cylinders drawing on a given intake and the same numbers won't apply exactly to a 4 pot as to a V8 or V12 for example. But in rough terms it means a single intake pipe only needs to be about 17% smaller in diameter than the correctly sized exhaust. Given that there's never any point in skimping on air feed at the intake side that's why I said above that your exhaust size puts you in the ballpark and will at least be well safe on the intake side. However you're trying to find out if you can "get away" with the Y piece you bought and so if it's really 500 bhp not 580 we have to rethink.
On that basis you might just about be ok on a single 3" o/d intake if the bends and welds don't cause much restriction but clearly it's a really tight judgement call. At 580 bhp it would certainly be too small.
Forgetting that for now let's get back into relative sizing of exhausts and intakes. This isn't a new topic obviously. Vizard has been looking at these in CFM flow terms for decades as have many others. Going right back to his Mini books I think he used to reckon to get no restrictions you needed 1.5 CFM per flywheel bhp for intakes and 2.2 CFM per bhp for exhausts. I forget at what pressure drop but that's not relevant for now as we are only interested in the ratio. I think back in those days he worked at 25" of water as I always have but since moving to the States he's got sucked into the 28" thing that the yanks use. There was also another standard for flowing carbs which I think was 1.5 inches of mercury and maybe that's what he used above but I'm not sure. I'll ask him sometime.
Anyway obviously many other factors affect this ratio such as the number of cylinders drawing on a given intake and the same numbers won't apply exactly to a 4 pot as to a V8 or V12 for example. But in rough terms it means a single intake pipe only needs to be about 17% smaller in diameter than the correctly sized exhaust. Given that there's never any point in skimping on air feed at the intake side that's why I said above that your exhaust size puts you in the ballpark and will at least be well safe on the intake side. However you're trying to find out if you can "get away" with the Y piece you bought and so if it's really 500 bhp not 580 we have to rethink.
On that basis you might just about be ok on a single 3" o/d intake if the bends and welds don't cause much restriction but clearly it's a really tight judgement call. At 580 bhp it would certainly be too small.
227, I think we had a spear point , the merge collectors are different so I suppose a real super douper design is a spear point merge collector, I am not trying to split hairs you can call them pointy bits or whatever, the reality is the engines make more power with the spear point design so we use it when we can as we are into making as much bhp per buck as we can for our customers.
Link to spear point/merge explanation. http://www.perfweldheaders.com/compmerg.html
Mud, I do not have generic flow capability charts. As you are doing a one off you are experimenting and will or will not get it running right, part of research and learning curve. You will have specific knowledge and not generic knowledge as lots of experts have. Max-Torque is right, suck it and see. It is like the V8 we look after. Most rolling road testing is done hood/bonnnet up, customer says, what happens with it down as it would be in race? Answer, massive increase in temp around carb bellmouth and loss of power, hence plenum chamber messing to try and duct cooler air in on the track. Worked nicely in practice (well in the race!)
Maybe Mike Johnson would chip in and share some of his knowledge of the LS1?
Peter
Link to spear point/merge explanation. http://www.perfweldheaders.com/compmerg.html
Mud, I do not have generic flow capability charts. As you are doing a one off you are experimenting and will or will not get it running right, part of research and learning curve. You will have specific knowledge and not generic knowledge as lots of experts have. Max-Torque is right, suck it and see. It is like the V8 we look after. Most rolling road testing is done hood/bonnnet up, customer says, what happens with it down as it would be in race? Answer, massive increase in temp around carb bellmouth and loss of power, hence plenum chamber messing to try and duct cooler air in on the track. Worked nicely in practice (well in the race!)

Maybe Mike Johnson would chip in and share some of his knowledge of the LS1?
Peter
A straight 3" pipe at 1.5" Hg (generally used for rating) should flow about 880 cfm.
A straight 3" pipe at 1.0" Hg (more of what I would want to see at peak HP / WOT) should flow about 720 cfm.
Pipe wall thickness, bends and merging will reduce the flow numbers from a 3" straight pipe
Stan
A straight 3" pipe at 1.0" Hg (more of what I would want to see at peak HP / WOT) should flow about 720 cfm.
Pipe wall thickness, bends and merging will reduce the flow numbers from a 3" straight pipe
Stan
Stan Weiss said:
A straight 3" pipe at 1.5" Hg (generally used for rating) should flow about 880 cfm.
A straight 3" pipe at 1.0" Hg (more of what I would want to see at peak HP / WOT) should flow about 720 cfm.
Pipe wall thickness, bends and merging will reduce the flow numbers from a 3" straight pipe
Stan
I agree your numbers for a pipe that's 3" I/D rather than O/D if that's what you meant?A straight 3" pipe at 1.0" Hg (more of what I would want to see at peak HP / WOT) should flow about 720 cfm.
Pipe wall thickness, bends and merging will reduce the flow numbers from a 3" straight pipe
Stan
Layman's viewpoint here.
I know there are several people who have answered in incredible detail and with lots of VERY good info above, but here is my thought.
Surely if you have found/calculated/been advised that 3" is enough for the individual inlet and based on the likelihood that each opposing cylinder across the "V" won't be sucking at the same time, then as only one tract needs air, the Y you show won't actually cause a significant restriction.
I would guess (again, layman's view) that, that is why the above example of dropping to one inlet resulted in no significant drop in power, as only one cylinder wants air at a time.
I know there are several people who have answered in incredible detail and with lots of VERY good info above, but here is my thought.
Surely if you have found/calculated/been advised that 3" is enough for the individual inlet and based on the likelihood that each opposing cylinder across the "V" won't be sucking at the same time, then as only one tract needs air, the Y you show won't actually cause a significant restriction.
I would guess (again, layman's view) that, that is why the above example of dropping to one inlet resulted in no significant drop in power, as only one cylinder wants air at a time.
Edited by E-bmw on Monday 10th October 09:36
E-bmw said:
Layman's viewpoint here.
I know there are several people who have answered in incredible detail and with lots of VERY good info above, but here is my thought.
Surely if you have found/calculated/been advised that 3" is enough for the individual inlet and based on the likelihood that each opposing cylinder across the "V" won't be sucking at the same time, then as only one tract needs air, the Y you show won't actually cause a significant restriction.
I would guess (again, layman's view) that, that is why the above example of dropping to one inlet resulted in no significant drop in power, as only one cylinder wants air at a time.
Not even remotely so. There's always considerable overlap between cylinders drawing air at the same time - or expelling exhaust gases at the same time. Camshaft events can last from 250 ish to well over 300 degrees of crankshaft rotation. Each piston stroke is only 180 degrees so by definition at least two cylinders must always be doing the same thing at the same time to some extent. It depends on the number of cylinders in the engine and the firing order which is why I said above that a 4 pot won't follow the exact same mathematical rules as a V8 or V12 and it also clearly depends on the camshaft duration. Stock motors don't have so much cylinder overlap as race ones.I know there are several people who have answered in incredible detail and with lots of VERY good info above, but here is my thought.
Surely if you have found/calculated/been advised that 3" is enough for the individual inlet and based on the likelihood that each opposing cylinder across the "V" won't be sucking at the same time, then as only one tract needs air, the Y you show won't actually cause a significant restriction.
I would guess (again, layman's view) that, that is why the above example of dropping to one inlet resulted in no significant drop in power, as only one cylinder wants air at a time.
Edited by E-bmw on Monday 10th October 09:36
There's actually a really interesting point that comes up from E-BMW's assumption above. Gut feel might tell most people that if you have two separate inlets for each bank, each with their own plenum, then those inlets can surely be much smaller than if you just had one inlet feeding one big plenum for all 8 cylinders. Stands to reason right because the two small inlets are only each feeding half of the engine maybe they can be half the size of a single inlet on one plenum?
Well not so. Each inlet needs to be big enough to feed the maximum air demand it ever sees and that will be when two or more cylinders are overlapping and drawing air at the same time. Here's the deal though. On a cross plane V8 sometimes the adjacent firing cylinders are on opposite banks but sometimes they are on the same bank! In fact even with short duration camshafts you get some overlap from three cylinders on a V8.
So actually the peak air demand on each of two separate plenums is not much smaller than the peak air demand on a single inlet feeding one big plenum. Nowt's ever as simple with engines as you think until you delve below the surface.
Well not so. Each inlet needs to be big enough to feed the maximum air demand it ever sees and that will be when two or more cylinders are overlapping and drawing air at the same time. Here's the deal though. On a cross plane V8 sometimes the adjacent firing cylinders are on opposite banks but sometimes they are on the same bank! In fact even with short duration camshafts you get some overlap from three cylinders on a V8.
So actually the peak air demand on each of two separate plenums is not much smaller than the peak air demand on a single inlet feeding one big plenum. Nowt's ever as simple with engines as you think until you delve below the surface.
I'll reread all the comments later, but to ask a naive question: neglecting any tuning effects, is moving to oversized pipe just equivalent to running without airboxes? NA ITBs remember.
E: edit to add, I appreciate the responses, and yes, fwhp = flywheel horse power... I assume that is the more relevant metric.
E: edit to add, I appreciate the responses, and yes, fwhp = flywheel horse power... I assume that is the more relevant metric.
Edited by Mud_ on Monday 10th October 12:28
Mud_ said:
I'll reread all the comments later, but to ask a naive question: neglecting any tuning effects, is moving to oversized pipe just equivalent to running without airboxes? NA ITBs remember.
E: edit to add, I appreciate the responses, and yes, fwhp = flywheel horse power... I assume that is the more relevant metric.
The idea is to find the area in the intake system that is the restriction. Increasing air box size or piping size will do very little if the throttle body does not have the needed flow.E: edit to add, I appreciate the responses, and yes, fwhp = flywheel horse power... I assume that is the more relevant metric.
Edited by Mud_ on Monday 10th October 12:28
Stan
KiaDiseasel said:
What you're telling the OP is that if his engine has twin 2.5" exhausts then it should manage at the other end on a single 2.5" inlet. I suspect he isn't going to believe that either.
Precisely. And go and look, and you'll find an awful lot of proddy engines running throttles or around about 60 to 70mm diameter.And of course they work fine, with very little inlet restriction, because as i highlighted previously, the dynamic pressure of a flow at around 25m/s is still rather small, as air really isn't very dense.
Unfortunately, the aftermarket "bigger is always better" approach tends to be applied to lots of after market tuning, resulting in oversized slow flowing, and poorly optimised intake systems......
Reread all the posts and nothing to add, just appreciate the comments 

Given I'm running a relatively mild cam for my supporting mods I will probably put in a bigger cam later...so I will see how big the airboxes end up, but I could probably go 2x4" with no major issues. Sounds like overkill given the numbers in this thread, but I'm struggling to see a downside - there's no MAF, and of course the throttle bodies are close to the intake valve so lots of lazy air outside the trumpets doesn't seem like a terrible thing...?

Stan Weiss said:
The idea is to find the area in the intake system that is the restriction. Increasing air box size or piping size will do very little if the throttle body does not have the needed flow.
Stan
That's full circle on my fears from the opening post Stan

Given I'm running a relatively mild cam for my supporting mods I will probably put in a bigger cam later...so I will see how big the airboxes end up, but I could probably go 2x4" with no major issues. Sounds like overkill given the numbers in this thread, but I'm struggling to see a downside - there's no MAF, and of course the throttle bodies are close to the intake valve so lots of lazy air outside the trumpets doesn't seem like a terrible thing...?
Max_Torque said:
Precisely. And go and look, and you'll find an awful lot of proddy engines running throttles or around about 60 to 70mm diameter.
And of course they work fine, with very little inlet restriction, because as i highlighted previously, the dynamic pressure of a flow at around 25m/s is still rather small, as air really isn't very dense.
Unfortunately, the aftermarket "bigger is always better" approach tends to be applied to lots of after market tuning, resulting in oversized slow flowing, and poorly optimised intake systems......
As above, are you talking generically, or do you think it's true of my particular system? 5.7 litre cross-plane V8 spinning to say 7k rpm with individual throttle bodies, making around 500hp at the crank. And of course they work fine, with very little inlet restriction, because as i highlighted previously, the dynamic pressure of a flow at around 25m/s is still rather small, as air really isn't very dense.
Unfortunately, the aftermarket "bigger is always better" approach tends to be applied to lots of after market tuning, resulting in oversized slow flowing, and poorly optimised intake systems......
Max_Torque said:
KiaDiseasel said:
What you're telling the OP is that if his engine has twin 2.5" exhausts then it should manage at the other end on a single 2.5" inlet. I suspect he isn't going to believe that either.
Precisely. And go and look, and you'll find an awful lot of proddy engines running throttles or around about 60 to 70mm diameter.
Not a production engine link and not as simple as pipe size but here is a link to Jenveys take on bhp and single throttle body.
http://www.jenvey.co.uk/faq/big-single
Peter
http://www.jenvey.co.uk/faq/big-single
Peter
KiaDiseasel said:
It depends on the number of cylinders in the engine and the firing order which is why I said above that a 4 pot won't follow the exact same mathematical rules as a V8 or V12 and it also clearly depends on the camshaft duration. Stock motors don't have so much cylinder overlap as race ones.
I understand all of that, hence why I worded the middle paragraph using the words."3" is enough for the individual inlet and based on the likelihood that each opposing cylinder across the "V" won't be sucking at the same time"
Yes, I also know that valve open cycles can be 250 degrees or more, but as this is around 1/3 of the 720 degrees of the full 4-stroke cycle and the cylinders using the same inlet are opposed across the V-angle, what are the chances of inlet overlap in the one inlet tract?
This will answer the question surely, when referred to the firing order & cam angles etc.
PeterBurgess said:
Not a production engine link and not as simple as pipe size but here is a link to Jenveys take on bhp and single throttle body.
http://www.jenvey.co.uk/faq/big-single
Peter
I wouldn't disagree with their comments and I was thinking about mentioning restricted intake F3 engines earlier as an example of what can be done when enough money and technology is thrown at a problem. The F3 engine generates an amazing amount of power through a single 26mm inlet but it has a plenum the size of a dustbin behind that so the inlet venturi never sees the peak air demand. Technically interesting but not of much use to the OP.http://www.jenvey.co.uk/faq/big-single
Peter
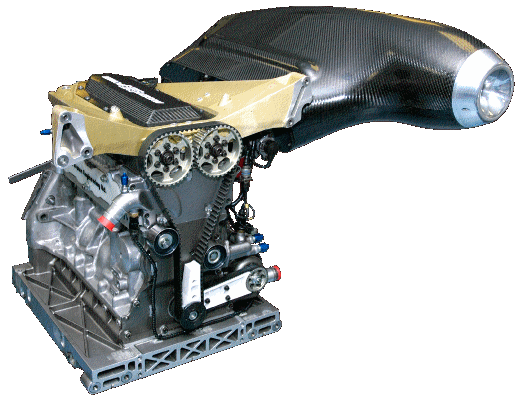
E-bmw said:
Yes, I also know that valve open cycles can be 250 degrees or more, but as this is around 1/3 of the 720 degrees of the full 4-stroke cycle and the cylinders using the same inlet are opposed across the V-angle, what are the chances of inlet overlap in the one inlet tract?
Exactly 100%.On a V8, regardless of crank configuration, there's a new cylinder starting its induction stroke every 90 degrees. Even with a short duration cam that means three cylinders must be somewhere on their induction stroke at the same time and with a long duration cam it's four cylinders. When adjacent firing cylinders can be on the same bank, as with a cross plane crank configuration like the OP's, then with a short duration cam you get two cylinders breathing through one bank and the third on the other and with long duration cams you actually get three of the four breathing through one bank at the same time and only the fourth on the other side.
So as I said above, if you have two plenums and a separate inlet pipe for each, the peak air demand on each of those inlets is not much less than if you just had a single big plenum and a single big inlet.
With a flat plane crank V8 as used in race engines, Ferraris etc the situation is different because the firing order is different. Even with a long duration cam you can only get two cylinders breathing at the same time on each bank.
This topic appears to be causing some confusion, but maybe a simple thought experiment can throw more light on it.
Imagine we just have a single cylinder 4 stroke engine of say 500c producing 50 bhp on a 270 degree inlet cam. The engine breathes through a single butterfly situated just upstream of the inlet port. As the inlet valve starts to open air starts flowing through the inlet port. As the valve lifts further that flow rate increases until by the time the valve is at about 3/4 of its full lift the flow rate is close to peak and it stays at that, or close to that, until the valve is back down to 3/4 of its full lift on the closing side and then gradually drops further until the valve shuts. Let's assume to keep the numbers nice and round that the peak flow rate is 100 CFM.
Now obviously the average flow rate over the whole 270 degree induction cycle is less than the peak flow rate. The ratio of average flow rate to peak flow rate will depend on cam profile and duration but let's call it 40%, so in this example that's 40 CFM.
The inlet port and butterfly need to be sized so they don't restrict the peak flow rate of 100 CFM and the sizes for those are well established. A single 40mm ITB butterfly will just about flow enough to feed a single 50 bhp cylinder and pro rata for other butterfly sizes.
Of course the engine also needs an air filter and therefore a filter box or plenum but imagine as in Formula 3 that the rules limit the inlet hole size into that plenum to limit horsepower. How large does that hole need to be?
First thought might be it needs to be as large as the butterfly but not so. Imagine the engine is stationary and the plenum it breathes through is enormous, the size of a house, full of millions of litres of air at atmospheric pressure. Each induction cycle will only draw about 500cc of air out of that plenum and barely affect the air pressure inside it a jot even if the plenum was sealed. To replenish the air in that plenum before the next induction cycle starts, 720 degrees after the previous one, the inlet hole can keep flowing for the whole 720 degrees.
If the average inlet flow over just the 270 degrees of the induction stroke is 40 CFM then over the whole 720 degrees of the 4 stroke cycle it is 40 x 270/720 = 15 CFM
So the plenum inlet hole only needs to flow 15 CFM to supply an inlet valve with a peak flow rate of 100CFM - as long as the plenum is big enough!
So that's essentially why there's a dustbin hanging off the side of an F3 engine because the rules only allow a 26mm inlet hole for the whole engine to breathe through.
In the real world plenums can't be the size of a house but the larger they are the smaller the inlet pipe tends to need to be to supply a given bhp.
Now consider what happens as you connect more and more cylinders to a single plenum.
Imagine we just have a single cylinder 4 stroke engine of say 500c producing 50 bhp on a 270 degree inlet cam. The engine breathes through a single butterfly situated just upstream of the inlet port. As the inlet valve starts to open air starts flowing through the inlet port. As the valve lifts further that flow rate increases until by the time the valve is at about 3/4 of its full lift the flow rate is close to peak and it stays at that, or close to that, until the valve is back down to 3/4 of its full lift on the closing side and then gradually drops further until the valve shuts. Let's assume to keep the numbers nice and round that the peak flow rate is 100 CFM.
Now obviously the average flow rate over the whole 270 degree induction cycle is less than the peak flow rate. The ratio of average flow rate to peak flow rate will depend on cam profile and duration but let's call it 40%, so in this example that's 40 CFM.
The inlet port and butterfly need to be sized so they don't restrict the peak flow rate of 100 CFM and the sizes for those are well established. A single 40mm ITB butterfly will just about flow enough to feed a single 50 bhp cylinder and pro rata for other butterfly sizes.
Of course the engine also needs an air filter and therefore a filter box or plenum but imagine as in Formula 3 that the rules limit the inlet hole size into that plenum to limit horsepower. How large does that hole need to be?
First thought might be it needs to be as large as the butterfly but not so. Imagine the engine is stationary and the plenum it breathes through is enormous, the size of a house, full of millions of litres of air at atmospheric pressure. Each induction cycle will only draw about 500cc of air out of that plenum and barely affect the air pressure inside it a jot even if the plenum was sealed. To replenish the air in that plenum before the next induction cycle starts, 720 degrees after the previous one, the inlet hole can keep flowing for the whole 720 degrees.
If the average inlet flow over just the 270 degrees of the induction stroke is 40 CFM then over the whole 720 degrees of the 4 stroke cycle it is 40 x 270/720 = 15 CFM
So the plenum inlet hole only needs to flow 15 CFM to supply an inlet valve with a peak flow rate of 100CFM - as long as the plenum is big enough!
So that's essentially why there's a dustbin hanging off the side of an F3 engine because the rules only allow a 26mm inlet hole for the whole engine to breathe through.
In the real world plenums can't be the size of a house but the larger they are the smaller the inlet pipe tends to need to be to supply a given bhp.
Now consider what happens as you connect more and more cylinders to a single plenum.
Edited by KiaDiseasel on Tuesday 11th October 14:38
Gassing Station | Engines & Drivetrain | Top of Page | What's New | My Stuff