What Engine for 500BHP
Discussion
eliot said:
Max_Torque said:
Just measure the delta pressure across the rad............
Not sure why we are focussing on flow when what we are interested ultimately is cooling. So Why not measure the outlet and inlet temperatures on the engine block to get the delta - if the pump works, the delta would
Except you don't really care about any of that. What "matters" is the actual engine metal temps, everything else is just a result of circumstance! It would be better to drill and instrument (thermocouple/PRT) a cylinder head and build a thermal survey engine. Determine things like the max metal temp of the exhaust valve bridge (usually the hotest point) etc.
However all that is really pretty pointless for the average kit car driver. What they want to know is "Does my car boil over or not". And the std mech pump is quite capable of providing enough coolant flow in any application. The limiting factor is the heat rejection at the radiator end of things! The coolant just moves heat energy from A to B, and the mean temperature at which it does that depends upon the coolant flow rate (HEAT FLUX = Mdot.CP.DeltaT).
In effect if the radiator rejects heat at the same rate the engine creates it, the system temperature stays the same. More engine heat, or less radiator rejection and temps climb. A typical coolant loop system only needs around 6degC DeltaT to transport the heat flux, and yet the radiator is generally operating at >60degC deltaT to it's environment! That should tell you where the principal limiting factor lies!
I'm always amazed that people seem to be more interested in spending hundreds of ££ on elecy pumps and stuff like that, rather than just doing the radiator and it's air ducting properly! (The thing is a properly ducted and designed radiator doesn't look very "trick" it has no "pub boasting" potential. Whereas some sort of "High Tech" electric booster pump looks all wizzbang and fast and stuff) ;-)
turbonutter said:
TheRealFingers99 said:
Just a thought: why not consider going waterless/pressureless? Hell, with a car that gorgeous you might even get some free in a sponsorship deal!
This is somthing that I have looked into and now the system is drained would be a perfect time to do it. The question is does this waterless coolant work - I assume you mean the Evans Brand.Yes according to the website its fantastic stuff, but I havent found any independent tests that confirm this, so if anyone is using the stuff is it any good????

Not used Evans or any other waterless yet but will be doing soon [not Evans ] basically it too expensive £65 ish a litre and unless the system is dry a similar price for prep/flush -- £1200 for a 10 litre system ??? . Top ups must not be water or it degrades love the idea but not the price!!!
one eyed mick]Not used Evans or any other waterless yet but will be doing soon [not Evans said:
basically it too expensive £65 ish a litre and unless the system is dry a similar price for prep/flush -- £1200 for a 10 litre system ??? . Top ups must not be water or it degrades love the idea but not the price!!!
Got your facts wrong a bit there.Circa £65 per gallon.
I literally have no idea why you would want to use "waterless" coolant? Water is perfect! It has a high specific heat capacity, and at a really quite convenient temp you get an extra heat absorption boost from the latent heat during the phase change. Added to which it's effectively free, can be got from anywhere, is basically non toxic and easy to handle. Add a couple of quid of long life antifreeze and you're good to go.
If you want to get a similar performance from using a waterless coolant, just send me £100 and i'll post you a small bit of cardboard you can use to block up your radiator with a bit.............. ;-)
If you want to get a similar performance from using a waterless coolant, just send me £100 and i'll post you a small bit of cardboard you can use to block up your radiator with a bit.............. ;-)
I wonder if I've gone too big with my rad with a 70mm core . Originally I had a line from the head to the header tank to help bleed any air out but that made matters worse , looking at logs from my road car with the same engine in after a long pull the Cyl head temps would reach 110c and drop to 100c after a few seconds with rad temp at 95c . I never see head water temp over 105 even in summer .
The road car carried 9 litres of coolant where I'm now carrying 15 litres
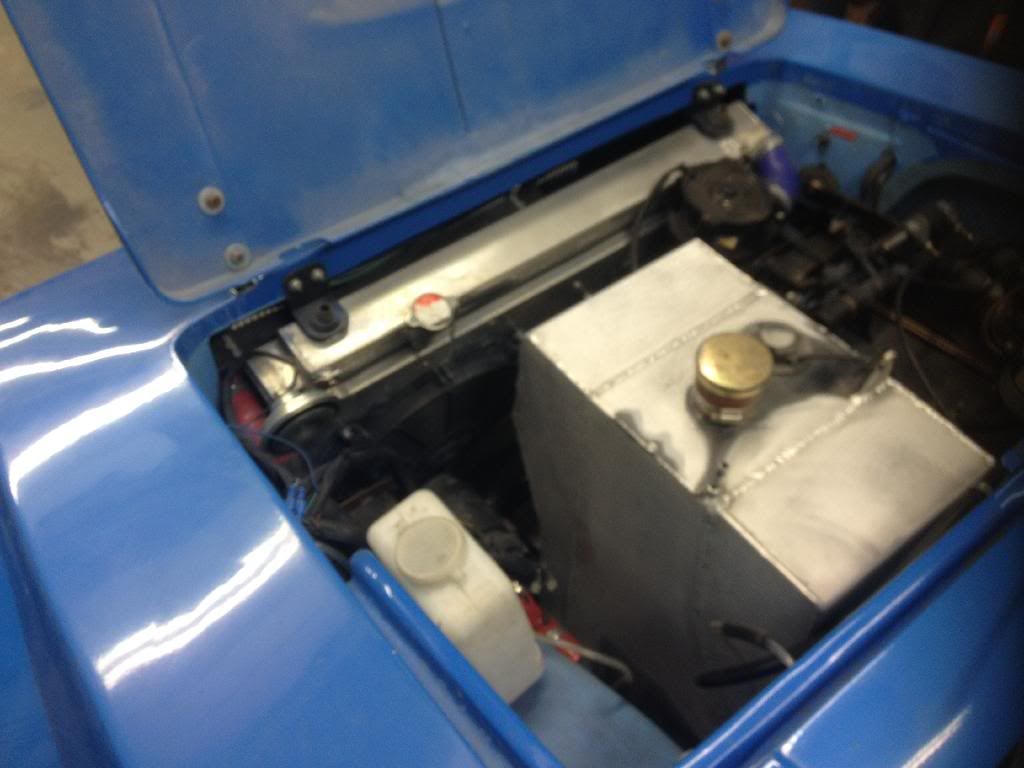
The road car carried 9 litres of coolant where I'm now carrying 15 litres
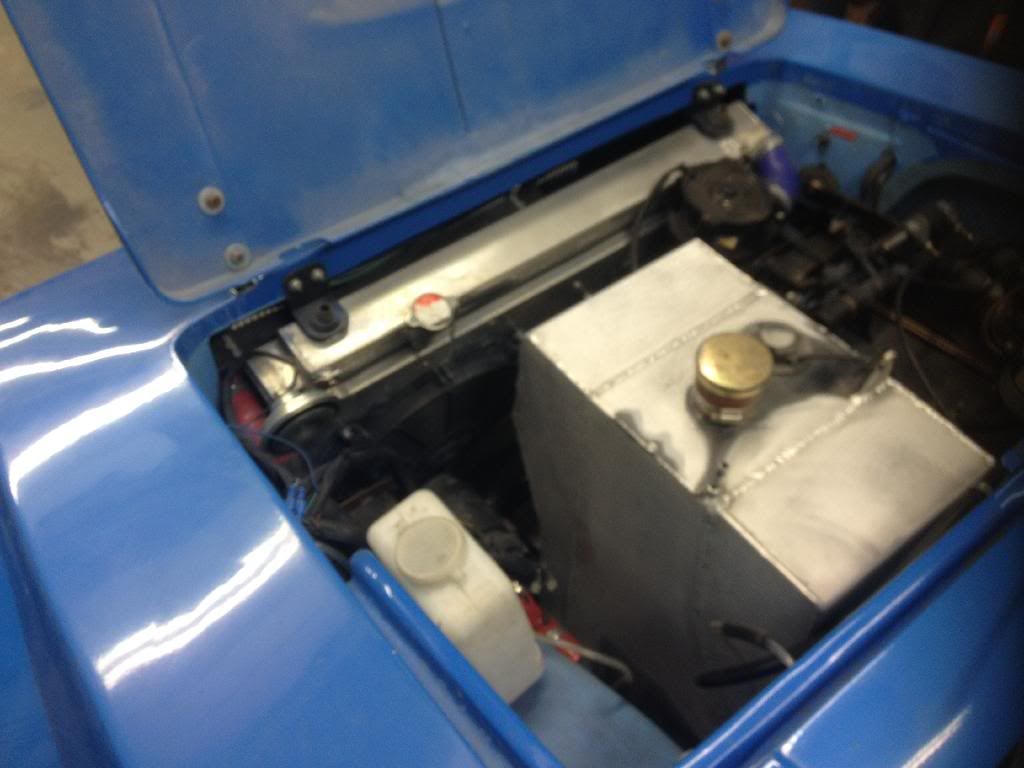
Max_Torque said:
eliot said:
Max_Torque said:
Just measure the delta pressure across the rad............
Not sure why we are focussing on flow when what we are interested ultimately is cooling. So Why not measure the outlet and inlet temperatures on the engine block to get the delta - if the pump works, the delta would
Aux pump off:
Water temp out of the engine: 90'c
Water temp returning to engine:70'c (i'm guessing the actual figures)
Delta of 20'c
Aux pump on:
Water temp out of the engine: 90'c
Water temp returning to engine:60'c (i'm guessing the actual figures)
Delta of 30'c
My assumption is that cooler water gets returned if the pump helps the flow through the rad in some way?
eliot said:
Not sure why we are focussing on flow when what we are interested ultimately is cooling.
So Why not measure the outlet and inlet temperatures on the engine block to get the delta - if the pump works, the delta would increase and if it makes no difference the delta would remain the same.
The question arose a few posts back, as to werther the electric pump actually helps the flow or not - hence the focus on flow is to determin if there is a benefit or not!So Why not measure the outlet and inlet temperatures on the engine block to get the delta - if the pump works, the delta would increase and if it makes no difference the delta would remain the same.
From experience at idle RPM I have found that an electric booster pump helps, but this has been disputed.
The other Question is if it helps at higher RPM's or if indeed it will become restriction.
As stevie said, I now know that you doo need a certain amount of flow, which it looks like i screwed up on first time round.....
My setup with the DC pumps could have been a contributing factor to the head gasket failiure, as it controlled the pump based on temperature only, so if the temperature was ok, it would run the pump at minimum speed & flow - then if you use all the power, the pump would stay at minimum speed & flow, until the water temperature increased.... So you have a situation where you have max heat going into the heads & a very low cooling flow, possibly allowing localized boiling of the water, creating steam pockets, which reduces the cooling of the head even more - A higher flow rate helps to avoid this as amount of heat transfered per litre of water flowing through the head is reduced...
At least that is how i understand it.
Max_Torque said:
I literally have no idea why you would want to use "waterless" coolant? Water is perfect! It has a high specific heat capacity, and at a really quite convenient temp you get an extra heat absorption boost from the latent heat during the phase change. Added to which it's effectively free, can be got from anywhere, is basically non toxic and easy to handle. Add a couple of quid of long life antifreeze and you're good to go.
If you want to get a similar performance from using a waterless coolant, just send me £100 and i'll post you a small bit of cardboard you can use to block up your radiator with a bit.............. ;-)
As I think I said, I did look at it, one of the reasons was that when I pressure tested my cooling system, to check for leaks (15psi), it leaked from the o ring seal on the DC pump! And waterless coolant runs with zero pressure.If you want to get a similar performance from using a waterless coolant, just send me £100 and i'll post you a small bit of cardboard you can use to block up your radiator with a bit.............. ;-)
Having searched around the net, apart from the makers, I dont find anyone other than the makers singing its praises. But you do find disadvantages - its expensive & as you are hinting above, your system will run slightly hotter...
In the end I just sealed the DC pump o-ring with gasket Sealant, but I see even that failed when the blown gasket over pressurized the system... I guess the DC pumps do have one use and that is as a safety valve

It's clear that people are failing to understand the basic physics behind cooling systems!
1) The engine generate heat energy, from burning fuel mixture. The amount of heat generated is pretty much equivalent to the power output of the engine (so more rpm and /or more load, both equal more heat)
2) That heat energy is transferred from the combustion chamber to the metal of the engine by radiation and conduction primarily.
3) This warms up the metal of the engine components, and it must be cooled by a flow of coolant, which must have a mean temperature below that of the metal (for heat to flow the right way!). For heat to flow, a temperature gradient must exist, so at every transfer stage, the input is hotter than the output. Heat is therefor "absorbed" at condition 1, and "rejected" at condition 2, where 1 must be hotter than 2.
4) To reject heat to the environment (with a radiator) the mean temp of the coolant must be higher than the environment it is trying to reject heat into. The environment in our case is atmospheric air, generally around about 10-20degC (in the UK).
5) Heat carried around by a fluid (air or water etc) is dependent on the mass flow of the fluid, the "delta" (in-out) temperature of that fluid and the specific heat of the fluid. For any fixed heat flow, if you increase the mass flow, the deltaT falls (as Cp doesn't change)
6) heat transfer between a moving fluid and a stationary wall, such as in an engine cylinder head or radiator, depends upon the difference in temperature between the fluid and the wall of the component, but also on the velocity existing between them. Higher velocities mean more turbulent, less laminar flow, and help to "pull" heat away from the stationary hot wall. This is why coolant flow rate is important for engine cooling.
7) Generally, the heat created by the engine is effectively fixed, the external environmental temp is effectively fixed (for any given day) and the flow rate of the coolant is "fixed" (it varies with engine speed, but so does engine power)
8) Air unfortunately has a poor Cp (a low specific heat) which means each molecule of air cannot carry a lot of heat energy (unlike water, which is 4x better by mass, and a lot lot better by volume due to its higher density than air). As a result, even with a lot of airflow, you need quite a high delta T to carry the engine heat away. With the mean temp of a car radiator being say 90degC, on a 20degC day, there is 70degC of deltaT trying to push heat away and into the environment. As such, the mean coolant temp is primarily set by this requirement, and a radiator must be sized to allow enough air through it to keep the mean temps under the boiling point of the coolant (say 125degC typically) Obviously, at zero road speed, the only thing driving the air flow will be convection, and a radiator would have to be impractically massive! So, we fit electric fans to help, pushing air through the rad at the equivalent usually of about 20mph. Generally, a typical system will NOT be able to reject the maximum engine out heat (engine kept at peak power), but luckily for us, passenger cars have a road load proportional to their speed, so this is not usually an option (unless you're towing a massive caravan up a 1:3 mountain pass in a 45degC ambient etc!)
9) We now know what the mean coolant temp must be for the radiator to reject the same amount of heat the engine is generating (and for that mean temp to stay constant). For the closed circuit coolant loop, the same amount of heat must be transported from the engine to the radiator, but with the excellent specific heat of water, and its high density, this only requires a much lower deltaT, typically between 6 and 10degC. What this means is that the difference in temperature between the top and bottom hoses will be that value. For the coolant mean temp to remain at 90, that clearly means the top hose must be say 95degC and the bottom how 85degC etc. What you find is this delta T is load dependent. At engine idle and with low heat fluxes, not only will the mean coolant temp fall (because the radiator has less heat to reject to the environment) but also the coolant deltaT reduces (because the coolant loop is carrying less heat)
10) From the engine component point of view, the metal parts of the engine must be higher in temperature than the mean coolant temp in order to be able to reject heat to it. A higher coolant flow rate will pull more heat from the metal but also reduce the coolant loop delta T, but an increase in the mean temp will occur because the radiator must now reject this extra heat to the environment (which has not changed temp!)
11) The resulting interdependencies are complex, with coolant mean temp and deltaT depending on all the parameters discussed above. However, as long as you have a high enough engine coolant flow rate to remove the heat, the penalty for a poor water pump is actually quite limited (eventually, the water will boil in the heat, because mean coolant temp + deltaT > boil point. But even then all is not lost because the latent heat of boiling acts to remove heat, which is what makes water such a good coolant!!).
12) it should be quite clear from that, that the principal limiting factor for coolant mean coolant temp (which is what we care about) is the ability of the radiator to reject the heat to the environment. Spending money to increase flow rate, once it is above a basic minimum value could reduce the system deltaT by a couple of degrees (doubling flow rate halves deltaT) with the resultant effect of reducing engine metal temps by a similar amount. However, doubling the size of the radiator, or doubling the airflow rate though it (from better ducting, lower pressure drop etc) could drop mean coolant temp by 20degC!
13) finally, the idea that an electric water pump somehow "saves" power is ridiculous unless you use a clever smart alternator and large battery storage system. A typical alternator is only 65% efficient, the pump elec motor probably 80% efficient, and without a large battery, you will be therefore pulling more power from the crank at high engine speeds than a belt driven pump! Of course, there used to be some fuel economy benefits from an electric pump, but even these have been much reduced by downspeeding (i.e. driving at light load but at 6000rpm, the drag of the water pump is the least of your worries!)
1) The engine generate heat energy, from burning fuel mixture. The amount of heat generated is pretty much equivalent to the power output of the engine (so more rpm and /or more load, both equal more heat)
2) That heat energy is transferred from the combustion chamber to the metal of the engine by radiation and conduction primarily.
3) This warms up the metal of the engine components, and it must be cooled by a flow of coolant, which must have a mean temperature below that of the metal (for heat to flow the right way!). For heat to flow, a temperature gradient must exist, so at every transfer stage, the input is hotter than the output. Heat is therefor "absorbed" at condition 1, and "rejected" at condition 2, where 1 must be hotter than 2.
4) To reject heat to the environment (with a radiator) the mean temp of the coolant must be higher than the environment it is trying to reject heat into. The environment in our case is atmospheric air, generally around about 10-20degC (in the UK).
5) Heat carried around by a fluid (air or water etc) is dependent on the mass flow of the fluid, the "delta" (in-out) temperature of that fluid and the specific heat of the fluid. For any fixed heat flow, if you increase the mass flow, the deltaT falls (as Cp doesn't change)
6) heat transfer between a moving fluid and a stationary wall, such as in an engine cylinder head or radiator, depends upon the difference in temperature between the fluid and the wall of the component, but also on the velocity existing between them. Higher velocities mean more turbulent, less laminar flow, and help to "pull" heat away from the stationary hot wall. This is why coolant flow rate is important for engine cooling.
7) Generally, the heat created by the engine is effectively fixed, the external environmental temp is effectively fixed (for any given day) and the flow rate of the coolant is "fixed" (it varies with engine speed, but so does engine power)
8) Air unfortunately has a poor Cp (a low specific heat) which means each molecule of air cannot carry a lot of heat energy (unlike water, which is 4x better by mass, and a lot lot better by volume due to its higher density than air). As a result, even with a lot of airflow, you need quite a high delta T to carry the engine heat away. With the mean temp of a car radiator being say 90degC, on a 20degC day, there is 70degC of deltaT trying to push heat away and into the environment. As such, the mean coolant temp is primarily set by this requirement, and a radiator must be sized to allow enough air through it to keep the mean temps under the boiling point of the coolant (say 125degC typically) Obviously, at zero road speed, the only thing driving the air flow will be convection, and a radiator would have to be impractically massive! So, we fit electric fans to help, pushing air through the rad at the equivalent usually of about 20mph. Generally, a typical system will NOT be able to reject the maximum engine out heat (engine kept at peak power), but luckily for us, passenger cars have a road load proportional to their speed, so this is not usually an option (unless you're towing a massive caravan up a 1:3 mountain pass in a 45degC ambient etc!)
9) We now know what the mean coolant temp must be for the radiator to reject the same amount of heat the engine is generating (and for that mean temp to stay constant). For the closed circuit coolant loop, the same amount of heat must be transported from the engine to the radiator, but with the excellent specific heat of water, and its high density, this only requires a much lower deltaT, typically between 6 and 10degC. What this means is that the difference in temperature between the top and bottom hoses will be that value. For the coolant mean temp to remain at 90, that clearly means the top hose must be say 95degC and the bottom how 85degC etc. What you find is this delta T is load dependent. At engine idle and with low heat fluxes, not only will the mean coolant temp fall (because the radiator has less heat to reject to the environment) but also the coolant deltaT reduces (because the coolant loop is carrying less heat)
10) From the engine component point of view, the metal parts of the engine must be higher in temperature than the mean coolant temp in order to be able to reject heat to it. A higher coolant flow rate will pull more heat from the metal but also reduce the coolant loop delta T, but an increase in the mean temp will occur because the radiator must now reject this extra heat to the environment (which has not changed temp!)
11) The resulting interdependencies are complex, with coolant mean temp and deltaT depending on all the parameters discussed above. However, as long as you have a high enough engine coolant flow rate to remove the heat, the penalty for a poor water pump is actually quite limited (eventually, the water will boil in the heat, because mean coolant temp + deltaT > boil point. But even then all is not lost because the latent heat of boiling acts to remove heat, which is what makes water such a good coolant!!).
12) it should be quite clear from that, that the principal limiting factor for coolant mean coolant temp (which is what we care about) is the ability of the radiator to reject the heat to the environment. Spending money to increase flow rate, once it is above a basic minimum value could reduce the system deltaT by a couple of degrees (doubling flow rate halves deltaT) with the resultant effect of reducing engine metal temps by a similar amount. However, doubling the size of the radiator, or doubling the airflow rate though it (from better ducting, lower pressure drop etc) could drop mean coolant temp by 20degC!
13) finally, the idea that an electric water pump somehow "saves" power is ridiculous unless you use a clever smart alternator and large battery storage system. A typical alternator is only 65% efficient, the pump elec motor probably 80% efficient, and without a large battery, you will be therefore pulling more power from the crank at high engine speeds than a belt driven pump! Of course, there used to be some fuel economy benefits from an electric pump, but even these have been much reduced by downspeeding (i.e. driving at light load but at 6000rpm, the drag of the water pump is the least of your worries!)
eliot said:
I dont understand why you are saying that the delta would decrease instead of increase? We were discussing whether an aux pump helps or not - so my thinking was this:
Aux pump off:
Water temp out of the engine: 90'c
Water temp returning to engine:70'c (i'm guessing the actual figures)
Delta of 20'c
Aux pump on:
Water temp out of the engine: 90'c
Water temp returning to engine:60'c (i'm guessing the actual figures)
Delta of 30'c
My assumption is that cooler water gets returned if the pump helps the flow through the rad in some way?
For say a 20 degC ambient temp:Aux pump off:
Water temp out of the engine: 90'c
Water temp returning to engine:70'c (i'm guessing the actual figures)
Delta of 20'c
Aux pump on:
Water temp out of the engine: 90'c
Water temp returning to engine:60'c (i'm guessing the actual figures)
Delta of 30'c
My assumption is that cooler water gets returned if the pump helps the flow through the rad in some way?
If the extra flow rate doesn't "Pull" more heat from the engine:
Pump Off:
Water temp out of the engine: 90'c
Water temp returning to engine:70'c
(Delta of 20'c, mean temp 80degC)
Pump On: (+10% flow lets say)
Mean temp stays at 80 degC (because that's what rad still needs to reject the same about of heat)
DeltaT falls by 10% to 18 degC(because flow rates gone up 10% but no extra heat is being carried)
Top Hose = 89 degC
Bottom Hose = 71 degC
If the extra flow rate does "Pull" 10% more heat from the engine:
Pump Off (same as above^^^ case)
Pump On: (+10% Flow +10% Heat, lets say)
Mean temp increases to 86 degC (80 + ((80-20)*10%) to reject extra 10% of heat
DeltaT stays at 20 degC (flow rates gone up 10% but extra 10%heat is being carried)
Top Hose = 96 degC
Bottom Hose = 76 degC
In reality that^^^ would be highly unlikely to occur, as the limiting performance of the radiator means the engine is now on average 6degC hotter! So, the engine metal temps would also climb by 6DegC in response, which we don't want.
As i've said, the limiting factor is always the radiator, not the water pump.........
Edited by anonymous-user on Saturday 23 November 19:59
Mikey G said:
What has system pressure got to do with cavitation? What happens for those minutes before the system gets up to temperature which then generates the pressure? Do our pumps cavitate until then?
The onset of cavitation is controlled by the vapour pressure (the pressure below which the coolant "boils") of the fluid being pumped. At low temps, although the absolute pressure is low, so is the coolant temp, which helps reduce vapour pressure!If you look at a cooling system, the header tank feed pipe will be connected directly infront of the water pump inlet. This has the effect of setting the system pressure at this (critical) point to the header cap pressure, and increasing the minimum vapour pressure to avoid cavitation.
But yes, quite often, coolant pumps can cavitate badly if the engine is rev'd hard when cold!
I'm no expert, but I would have thought cavitation was a combination of impellor speed and design. If a pump is designed to flow x amount at a maximum y rpm, then if you try to exceed these then cavitation occurs. I thought as long as the pump is properly flooded then if you stay within these parameters then pressure before the pump has no effect, and vapour pressure at the top of the header tank is different to water pressure on the inlet side of any pump is it not?
Most header tanks are not refilled directly from the circuit under water pressure, more of an expansion circuit in the system to keep it all up to level. Now if it was a header tank in the way you seem to be describing then all circuits would return to this tank and then supply water direct to the pump in a gravity type of feed supplying positive pressure to the inlet of the pump.
Most header tanks are not refilled directly from the circuit under water pressure, more of an expansion circuit in the system to keep it all up to level. Now if it was a header tank in the way you seem to be describing then all circuits would return to this tank and then supply water direct to the pump in a gravity type of feed supplying positive pressure to the inlet of the pump.
Mikey G said:
I'm no expert, but I would have thought cavitation was a combination of impellor speed and design. If a pump is designed to flow x amount at a maximum y rpm, then if you try to exceed these then cavitation occurs. I thought as long as the pump is properly flooded then if you stay within these parameters then pressure before the pump has no effect, and vapour pressure at the top of the header tank is different to water pressure on the inlet side of any pump is it not?
Most header tanks are not refilled directly from the circuit under water pressure, more of an expansion circuit in the system to keep it all up to level. Now if it was a header tank in the way you seem to be describing then all circuits would return to this tank and then supply water direct to the pump in a gravity type of feed supplying positive pressure to the inlet of the pump.
As soon as the pump inlet pressure (or more accurately the impeller blade backside pressure) falls below the vapour pressure of the fluid, it will "boil" and the vapour created is the "cavitation".Most header tanks are not refilled directly from the circuit under water pressure, more of an expansion circuit in the system to keep it all up to level. Now if it was a header tank in the way you seem to be describing then all circuits would return to this tank and then supply water direct to the pump in a gravity type of feed supplying positive pressure to the inlet of the pump.
Typical header tanks are connected to the pump inlet via the same pipe used to fill the system. As there is (virtually) no flow in this pipe, and hence no pressure loss, the pump inlet pressure will be the same as the header tank pressure. Also, there tends to be a small degas vent pipe from either the top of the radiator or just pre-thermostat, the "short circuits" the main cooling loop. The aim of this small amount of flow is to allow any gas/vapour/steam to escape to the top of the header tank to ensure system performance is gain and maintained properly. This does create a small amount of flow in the header tank -> bottom hose pipe, but that flow is limited by a small orifice, usually in the entry stub to the header tank.
eliot said:
how do you know if your coolant is flowing round at the optimum speed?
The best method as i hinted at above to is instrument various parts of your engine with direct measurement sensors, such as thermocouples or PRTs. Measuring, and minimising, the metal temps under various running conditions is how production cooling systems are verified (they are developed/designed these days on extremely complex thermal simulations running in custom software environments) These "thermal survey" test engines will carry something like 200 separate temperature sensors, often drilled deep into the engines core structure.For the rest of us, you can't beat simply fitting the biggest radiator you can (within sensible aerodrag limits of course!) and installing the best ducting possible to guide the incoming airstream to and from that rad. Chances are, using the std OEM water pump is good enough, especially with modern engines that utilise "proper" impeller designs that have been CFD optimised (old water pumps used basic "flat" style impellers and had a relatively low efficiency)
Gassing Station | Engines & Drivetrain | Top of Page | What's New | My Stuff