What Engine for 500BHP
Discussion
Not really sure it matters too much.
Some screw fittings into the oil galleries in the block, some take temp from the sump. I take mine from the remote filter housing, so between sump and engine.
I guess sump is potentially the hottest bit, as the oil ends up there after any heating within the engine...or on the other hand the sump is air cooled and the oil can get cooled after passing through the engine block.
Some screw fittings into the oil galleries in the block, some take temp from the sump. I take mine from the remote filter housing, so between sump and engine.
I guess sump is potentially the hottest bit, as the oil ends up there after any heating within the engine...or on the other hand the sump is air cooled and the oil can get cooled after passing through the engine block.
turbonutter said:
Just been looking at the Oil temperature that was logged & it maxed out at 126C, so there is a difference of 10C between the ECU sensor and my dash gauge - maybe it wasnt as bad as i thought...
Std resistive 2 wire automotive temperature sensors are Negative Temperature Co-efficient (NTC) devices. This means there electrical resistance FALLS as their physical temperature increases. They follow a Log curve, where resitance halves each time temperature doubles, so once over about 100degC they will have a pretty low resistance (compared to their room temperature resistance) As a result various inaccuracies in the measurement systems (voltage offsets, resolution, calibration & reference errors etc) start to become dominant. For the vast majority of OEM sensing, you really only care about absolute accuracy and resolution at low temps (for cold starting/compensation etc) so this trade off is not too bad.if you take a typical sensor:

a 1degC temp change at 20degC changes the sensors resistance by 1.3Kohm, but the same 1degC change at
110degC is just 40 Ohms.
turbonutter said:
Well for a change I can post about a successful day at a track, rather than the usual disaster I seem to have been having recently.
Testing at Blyton on tuesday went really well, We had done some preliminary tweaks to the Boost control & Traction control before going & spent the day fine tuning both..
First off the track was wet, but that was ideal for testing the traction control, we started using Ignition retard & cut & fuel cut to reduce the torque, which worked well, but later added in DBW control for the torque as well, the DBW torque reduction worked really well, so that is now the first operate, with the Fuel and ignition cuts helping out if the slip gets to far off target. It works really well, nice and smooth & the cant feel it operating...
Boost control is also nicely setup now and follows the target wery well, and we set it so that the boost reduces as throttle reduces & also gear by gear.A big reduction in boost in first gear to look after the CV joints, the mid range boost increasing as you change to higher gears.
A question for anyone on traction control; why not just lower the boost by opening the WG in certain gears? It seems yours is a very complex solution so there must be reasons for this.Testing at Blyton on tuesday went really well, We had done some preliminary tweaks to the Boost control & Traction control before going & spent the day fine tuning both..
First off the track was wet, but that was ideal for testing the traction control, we started using Ignition retard & cut & fuel cut to reduce the torque, which worked well, but later added in DBW control for the torque as well, the DBW torque reduction worked really well, so that is now the first operate, with the Fuel and ignition cuts helping out if the slip gets to far off target. It works really well, nice and smooth & the cant feel it operating...
Boost control is also nicely setup now and follows the target wery well, and we set it so that the boost reduces as throttle reduces & also gear by gear.A big reduction in boost in first gear to look after the CV joints, the mid range boost increasing as you change to higher gears.
Edited by 227bhp on Friday 16th October 14:38
227bhp said:
A question for anyone on traction control; why not just lower the boost by opening the WG in certain gears? It seems yours is a very complex solution so there must be reasons for this.
In terms of traction control, altering boost as a reaction to traction loss is a very slow way to try and deal with itEdited by 227bhp on Friday 16th October 14:38
Ignition, fuel or in this case also DBW, are much much faster.
But he is also using gear dependent boost ( among other parameters ) to try and give a power delivery that prevents traction loss in the first place, which ultimately is the best solution...however traction can vary so you could be leaving a lot on the table there by going too low.
stevieturbo said:
227bhp said:
A question for anyone on traction control; why not just lower the boost by opening the WG in certain gears? It seems yours is a very complex solution so there must be reasons for this.
In terms of traction control, altering boost as a reaction to traction loss is a very slow way to try and deal with itEdited by 227bhp on Friday 16th October 14:38
Ignition, fuel or in this case also DBW, are much much faster.
But he is also using gear dependent boost ( among other parameters ) to try and give a power delivery that prevents traction loss in the first place, which ultimately is the best solution...however traction can vary so you could be leaving a lot on the table there by going too low.
As mentioned traction is dependent on many things like the road surface/ water and wit traveling straight or turning, so it is impossible to control just by targeting a certain boost in a particular gear....
Traction control is complex to say the least!
Thanks for the explanations I knew there would be a good reason for it and I can see where you are coming from. My needs are initially more basic - just wheel spin in 1st and second gear in a straight line in the dry when the boost spikes, but I can see as you say that when the conditions vary then the solution becomes more complicated.....
turbonutter said:
You just beat me to the reply and summed it up very well.
As mentioned traction is dependent on many things like the road surface/ water and wit traveling straight or turning, so it is impossible to control just by targeting a certain boost in a particular gear....
Traction control is complex to say the least!
Modern road car traction control systems have a full physics dynamics model of the car, and have "adaptive friction compensation" that uses the engines Torque control strategy to feed forward a limit wheel torque that is estimated to reach peak friction. That value is then modifed by the real time closed loop controllers in order to further optimise the tractive effort curve!As mentioned traction is dependent on many things like the road surface/ water and wit traveling straight or turning, so it is impossible to control just by targeting a certain boost in a particular gear....
Traction control is complex to say the least!
Knocking a bit of spark out, or closing the throttle a bit isn't really "complex" by today's standards.......... ;-)
Max_Torque said:
turbonutter said:
You just beat me to the reply and summed it up very well.
As mentioned traction is dependent on many things like the road surface/ water and wit traveling straight or turning, so it is impossible to control just by targeting a certain boost in a particular gear....
Traction control is complex to say the least!
Modern road car traction control systems have a full physics dynamics model of the car, and have "adaptive friction compensation" that uses the engines Torque control strategy to feed forward a limit wheel torque that is estimated to reach peak friction. That value is then modifed by the real time closed loop controllers in order to further optimise the tractive effort curve!As mentioned traction is dependent on many things like the road surface/ water and wit traveling straight or turning, so it is impossible to control just by targeting a certain boost in a particular gear....
Traction control is complex to say the least!
Knocking a bit of spark out, or closing the throttle a bit isn't really "complex" by today's standards.......... ;-)

Max_Torque said:
turbonutter said:
Just been looking at the Oil temperature that was logged & it maxed out at 126C, so there is a difference of 10C between the ECU sensor and my dash gauge - maybe it wasnt as bad as i thought...
Std resistive 2 wire automotive temperature sensors are Negative Temperature Co-efficient (NTC) devices. This means there electrical resistance FALLS as their physical temperature increases. They follow a Log curve, where resitance halves each time temperature doubles, so once over about 100degC they will have a pretty low resistance (compared to their room temperature resistance) As a result various inaccuracies in the measurement systems (voltage offsets, resolution, calibration & reference errors etc) start to become dominant. For the vast majority of OEM sensing, you really only care about absolute accuracy and resolution at low temps (for cold starting/compensation etc) so this trade off is not too bad.if you take a typical sensor:

a 1degC temp change at 20degC changes the sensors resistance by 1.3Kohm, but the same 1degC change at
110degC is just 40 Ohms.
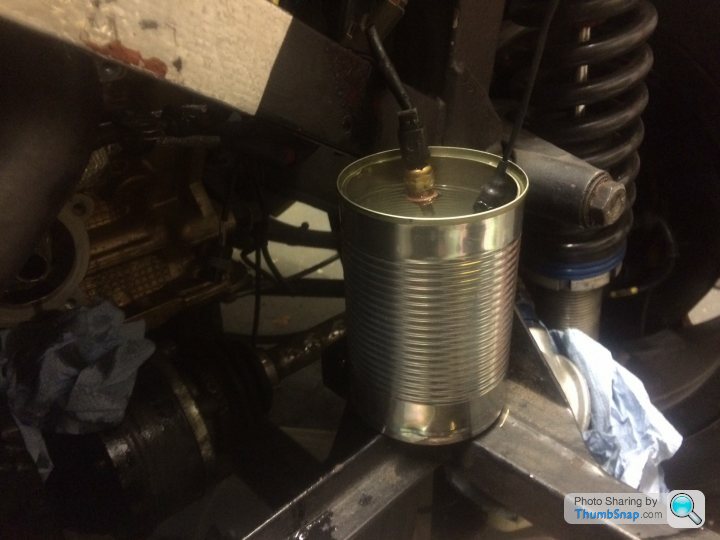
Before the test with the sensors in air - Stack gauge was on minimum (40C) ECU sensor showed 15.5C
With some warm water in the can --------- stack gauge read 62C & ECU 53C
With the water heated to Boiling with a flame, so at 100C, Stack read 107C & ECU 99.2
So at 100C the gauge is over reading by 7% & the ECU is under by 0.8%.
Based on those errors:
When the stack gauge read 138C, temp was 128C
When the ECU read 126C, temp was 127C.
So although high, the temp is in my acceptable range.. There is an option with the Laminova cooler to insert a partial restrictor in the central bypass flow to increase the flow through the cooling channels, so that is something I could try easily...
Checking the oil pressure logs with the oil hot, it was 70psi @2500 rpm & 90psi at 6500rpm even at idle (1200rpm) it only dropped to 38psi. So all good there

stevieturbo said:
But lets face it...a lot of OEM traction control systems are s
te and over aggressive, killing too much power, too often.
Sometimes complex isnt always great.
Mine is set up with dash selectable slip, and with 3mph slip target you can have a controlled slide in the corners..
Sometimes complex isnt always great.
I can choose between "OFF" and 1,2,3,4,5,6,7,8,9mph slip..
Just had a quick visit to the rolling road, to see where I am power wise now the boost control etc is sorted...
I am running 1bar as the max boost at the moment & ended up with 473BHP & 460lb/ft...

http://vid1086.photobucket.com/albums/j446/turbonu...
I am running 1bar as the max boost at the moment & ended up with 473BHP & 460lb/ft...

http://vid1086.photobucket.com/albums/j446/turbonu...
Max_Torque said:
Lovely wide spread of power between 5500 and 6500! Must be easy to drive fast ;-)
Its about 100BHP down on what I had before with 1.3bar boost, but TBH that was maybe too much. Its very nice to drive now, as we have the boost mapped v/s rpm, throttle & gear. In fact its better than before with the extra power.Still thinking of going with a smaller turbo, to get it to spool faster, as on the RR we didnt hit the boost target until 4700rpm & on the road its 500-750 rpm later than that.
Thinking of a GT3076R, with a tial turbine housing, as that will fit to my existing exhaust & boost pipes etc with no modifications. Looking at the turbine flows, the 3076 1.06ar housing flows the same as my current housing, so shouldnt choke the engine any worse than now & so should spool faster and still give me 500BHP... This needs investigating though...
turbonutter said:
Its about 100BHP down on what I had before with 1.3bar boost, but TBH that was maybe too much. Its very nice to drive now, as we have the boost mapped v/s rpm, throttle & gear. In fact its better than before with the extra power.
Still thinking of going with a smaller turbo, to get it to spool faster, as on the RR we didnt hit the boost target until 4700rpm & on the road its 500-750 rpm later than that.
Thinking of a GT3076R, with a tial turbine housing, as that will fit to my existing exhaust & boost pipes etc with no modifications. Looking at the turbine flows, the 3076 1.06ar housing flows the same as my current housing, so shouldnt choke the engine any worse than now & so should spool faster and still give me 500BHP... This needs investigating though...
Are you using stock cams?Still thinking of going with a smaller turbo, to get it to spool faster, as on the RR we didnt hit the boost target until 4700rpm & on the road its 500-750 rpm later than that.
Thinking of a GT3076R, with a tial turbine housing, as that will fit to my existing exhaust & boost pipes etc with no modifications. Looking at the turbine flows, the 3076 1.06ar housing flows the same as my current housing, so shouldnt choke the engine any worse than now & so should spool faster and still give me 500BHP... This needs investigating though...
turbonutter said:
Its about 100BHP down on what I had before with 1.3bar boost, but TBH that was maybe too much. Its very nice to drive now, as we have the boost mapped v/s rpm, throttle & gear. In fact its better than before with the extra power.
Still thinking of going with a smaller turbo, to get it to spool faster, as on the RR we didnt hit the boost target until 4700rpm & on the road its 500-750 rpm later than that.
Thinking of a GT3076R, with a tial turbine housing, as that will fit to my existing exhaust & boost pipes etc with no modifications. Looking at the turbine flows, the 3076 1.06ar housing flows the same as my current housing, so shouldnt choke the engine any worse than now & so should spool faster and still give me 500BHP... This needs investigating though...
IMO weld a fitting onto the manifold pre-turbo and see what pre-turbine pressure is like.Still thinking of going with a smaller turbo, to get it to spool faster, as on the RR we didnt hit the boost target until 4700rpm & on the road its 500-750 rpm later than that.
Thinking of a GT3076R, with a tial turbine housing, as that will fit to my existing exhaust & boost pipes etc with no modifications. Looking at the turbine flows, the 3076 1.06ar housing flows the same as my current housing, so shouldnt choke the engine any worse than now & so should spool faster and still give me 500BHP... This needs investigating though...
IMO there is no way it can be high or choking as you suggest, yet still spool so slowly, and when using relatively low boost.
I'm sure you've said before anyway, but what turbo and turbine housing are on it now ?
The engine is from the Alfa 147 GTA 3.2 V6. I am using the "stock" GTA cams, which i believe are slightly different to the non GTA 3.0l V6. The only other modification to the engine is the Low Compression pistons at about 8.4:1 ( i would have to dig through my files to find the exact C/R.
Gassing Station | Engines & Drivetrain | Top of Page | What's New | My Stuff