Tensile and compression in Ti conrods.
Discussion
Boosted LS1 said:
J17 said "Forged rods aren't as strong (like for like) as billet rods because the FORGING process folds and bends the metal, altering it's internal structure and creating high/low stress areas. If you're going for something reputable I wouldn't expect much difference in the real world though".
I thinke he made a typo, billet is where the metal is bent and folded etc which I would have though made for a denser stronger material.
Boosted.
He was wrong, but you erroneously corrected the bit he got right.I thinke he made a typo, billet is where the metal is bent and folded etc which I would have though made for a denser stronger material.
Boosted.
Forgings are created by working material, usually when hot, by folding and compressing lumps of raw material into roughly the right shape. Where a forging is designed properly it ought to be stronger than a machined fabrication (fabrication).
Typically the design for the forging will include precise details of how the material is worked, such that the grain of the material is caused to be denser in areas of greatest stress. The direction of the grain also can be controlled, and this is another critical part of strength improvements that forgings can offer.
The type of forging process ranges from the use of massive steam or hydraulic "hammers" or presses, where the workpiece is manipulated by a skilled operator, right down to the use of a manual hammer and a blacksmiths hearth. Somewhere in the middle is the modern "drop forging" process, which requires the use of a cooled die and lends itsself to mass production.
Typically a normal component will have been manufactured by machining a lump of material to the required shape using a cutting point, and material removal techniques. In theory the grain of the original material is such that the final component appears as the original, but with lumps removed to achieve the design shape. This is much less strong than a properly designed forging because removing material sets up stress concentrations, and the underlying material is only uniformly strong.
The billet approach uses a machining process on a lump of (refractory iron alloy castings / crucible steel castings) material with uniform grain.
In general it is much better to hot work all metallic materials because the final product ends up stronger, once cool. With materials like titanium, hot working is almost essential, because the material is so tough.
In practice there is much more overlap between hot working, cold forming, and machining processes. This is simply because a typical component made in steel will have been poured from the refractory (like a casting), hot worked into a shape suitable for the steel mill (forging), then cold rolled to an accurate size (cold forming). The final "shape" is achieved by machining off the bits that are not required (fabrication).
A forged component would typically have machined faces (bearing faces), although it is still described as being forged. This is because the majority of the shape of the component has been produced by the forging process, with good control over the grain structure of the material, in relation to it's geometry. The machining processes are minimal to components described as "forged".
Consider a lump of material, maybe a cube, and then imagine a deep slot machined through the middle, to make the cube U-shaped. Even if the machining process, was perfectly square and true, the likelihood is that the slot will not be square. The issue is that the internal grain structure of the block has been broken, and the stresses withing the material must re-aquire equilibrium. When this happens the material is likely to change shape.
This does not happen with the billet approach because the grain structure is uniform, and there are no internal stresses. It also reveals why it is important that the design of a forging is considered in conjunction with the machining operations that will take place on it.
In general a properly designed forging will be better than a machined billet (for a given application), but it doesn't happen unless someone thinks hard about it's design. Obviously a forging will require tooling, and that tooling will have been arrived at as the result of considerable development and modelling (cost).
It's probably also important to remember that terms like "Billet" and "Forging" are somewhat flexible. What's true is that billet is closer to molten metal than forging. In the same way a cold rolled component is further from molten metal than a forging. What may be the case, is that a billet may have been subject to a certain ammount of hot working, but that doesn't make it a "forging".
Typically the constituents of the steel are devised, and lobbed into a big electrically heated crucible. Once molten amd well mixed, metal is poured, and allowed to cool. Once it's solid it's bashed into shape whilst hot, and then bashed some more once it's cold. If have a steel mill, or pay one some money, you can get your own compositions/processes placed into that schema. Equally you can get them to let the metal cool completely at any stage, and then give it to your machining process!


The source
A great picture of some proper "skilled forging".

An excellent video from the past
Please excuse errors and omissions..... I'm a software engineer these days, so I've no idea really.
Edited by dilbert on Saturday 26th January 20:21
GreenV8S said:
I thought the difference was that forged components were forged into (approximately) the right shape so the grain structure followed the shape and tended to concentrate the strength where it was needed. Billet is just a uniform slab of material that is cut down to make the component, so the component is more or less uniform (apart from any machining stresses or subsequent treatment).
Correct.Top postings, very interesting but there seems to be huge overlap with some of these processes. It's hard to know which is best so just buy from a good manufacturer? Apart from the factory forged Ti rods there are also the powdered metal rods. Another process which seems a bit similar to forgings.
Knighty said:
"all billet rods are machined from a rough rod-shaped forging, so they are the best of both worlds, machined and shot peened, with good grain flow.....they are NOT just machined form a square slab".
That seems like a huge short cut. Surely that can't be correct? Wouldn't that make a billet the same as a forging? I've seen the phrase near nett forgings referenced to TRW pistons which sound like what you're describing as opposed to a proper forged piston being made from a lump of solid?
Knighty said:
"all billet rods are machined from a rough rod-shaped forging, so they are the best of both worlds, machined and shot peened, with good grain flow.....they are NOT just machined form a square slab".
That seems like a huge short cut. Surely that can't be correct? Wouldn't that make a billet the same as a forging? I've seen the phrase near nett forgings referenced to TRW pistons which sound like what you're describing as opposed to a proper forged piston being made from a lump of solid?
Boosted LS1 said:
Top postings, very interesting but there seems to be huge overlap with some of these processes. It's hard to know which is best so just buy from a good manufacturer? Apart from the factory forged Ti rods there are also the powdered metal rods. Another process which seems a bit similar to forgings.
Knighty said:
"all billet rods are machined from a rough rod-shaped forging, so they are the best of both worlds, machined and shot peened, with good grain flow.....they are NOT just machined form a square slab".
That seems like a huge short cut. Surely that can't be correct? Wouldn't that make a billet the same as a forging? I've seen the phrase near nett forgings referenced to TRW pistons which sound like what you're describing as opposed to a proper forged piston being made from a lump of solid?
Powdered metal rods are commonly called sinter-forged nowadays, the advantage they have is that they tend to be very consistent in weight and therefore need little balance machining so they are cheap. They are good for road vehicles, but tend to be engineered to just do the job intended, nothing more, nothing less.Knighty said:
"all billet rods are machined from a rough rod-shaped forging, so they are the best of both worlds, machined and shot peened, with good grain flow.....they are NOT just machined form a square slab".
That seems like a huge short cut. Surely that can't be correct? Wouldn't that make a billet the same as a forging? I've seen the phrase near nett forgings referenced to TRW pistons which sound like what you're describing as opposed to a proper forged piston being made from a lump of solid?
While some billet rods are potentially made as Knightly says, I've never seen it, most come from slab.
As regards the pistons, the near-nett type go through a process that removes inclusions, but that's only part of the equation - the rest is down to the type of alloying elements used. The bottom line is that if you are really pushing the boundaries you'd go for forgings, but we are talking 200 bhp/litre upwards, and a good solid skirted piston on a slightly oversquare 2.0 I4 can see 8500 rpm for a race season without falling apart.
I suspect that the ultimate result would depend more on the choice of material than on the method used to shape it. What I means is that casting and forging both impose restrictions on the type of material you can use. It may be that a superior component could be made from a billet of material that wasn't suitable for forging. However, for a given material that can be forged, it may be possible to get a better result by forging than by machining from a billet. But I suspect that in any normal commercial situation the choice of forged / billet would be dictated by the cost of forging moulds versus the cost of machining and not because either produced a superior result.
Here's some interesting reading.
http://en.wikipedia.org/wiki/Forgings#Net-shape_an...
Rods appear to be 'impression die-drop hammer forged' which is why I assumed the metal in the rod was molten?
ETA, here's info about billet stuff. Look halfway down the page at how a billet crank is produced.
http://en.wikipedia.org/wiki/Crankshaft
http://en.wikipedia.org/wiki/Forgings#Net-shape_an...
Rods appear to be 'impression die-drop hammer forged' which is why I assumed the metal in the rod was molten?
ETA, here's info about billet stuff. Look halfway down the page at how a billet crank is produced.
http://en.wikipedia.org/wiki/Crankshaft
Edited by Boosted LS1 on Saturday 26th January 20:19
Boosted LS1 said:
Top postings, very interesting but there seems to be huge overlap with some of these processes. It's hard to know which is best so just buy from a good manufacturer? Apart from the factory forged Ti rods there are also the powdered metal rods. Another process which seems a bit similar to forgings.
Knighty said:
"all billet rods are machined from a rough rod-shaped forging, so they are the best of both worlds, machined and shot peened, with good grain flow.....they are NOT just machined form a square slab".
That seems like a huge short cut. Surely that can't be correct? Wouldn't that make a billet the same as a forging? I've seen the phrase near nett forgings referenced to TRW pistons which sound like what you're describing as opposed to a proper forged piston being made from a lump of solid?
Boosted, believe me, I know what I'm talking about, I have designed and developed many high level race con-rods, and more recently worked on the development of high volume production rods using C70 forged steel, so we could crack the big-end open, and therefore save the cost of machining, its nothing new to be honest.Knighty said:
"all billet rods are machined from a rough rod-shaped forging, so they are the best of both worlds, machined and shot peened, with good grain flow.....they are NOT just machined form a square slab".
That seems like a huge short cut. Surely that can't be correct? Wouldn't that make a billet the same as a forging? I've seen the phrase near nett forgings referenced to TRW pistons which sound like what you're describing as opposed to a proper forged piston being made from a lump of solid?
any decent billet machined rod is machined from a rod shaped forging in order to get the correct grain flow - not a slab, I have used Arrow, Farndon and another manufacturer (forget their name!), and this is how they all do it......but I dare say cheap billet rods are done from slab - you pay peanuts - you get monkeys ......if you catch my drift
production type forged rods need polishing and shot peening to be used in a highly tuned race motor, as the surface finish has low fatigue resistance.
For god sake dont use sinter/powder metal rods in anything remotley high power.......they are just cheap rods intended for the standard production engine......some turbo-diesels use them, but they need to be hit in a forge after cooking in the sintering oven, in order to give them some compressive fatigue resistance, a bit like shot peening, and manufacturers have now realised this is pricey, so they are all now using forged C70 grade steel, with cracked big-ends.
Boosted LS1 said:
There must be a quicker way to make 8 con-rods then that, maybe make them in groups at a time?
For sure.... I think those pictures, are the classic demonstrations. Tehy've been doing it like that for literally hundreds of years. For a modern production car, I think you must be looking at a continuous process. Although I'm no expert on modern enhancements of forging.I know a little bit about electron beam welding, because of the overlap with electronics. The same "electron beam" techniques also map into chemical and physical vapour deposition as used heavily in the semiconductor fabrication processes, and for exotic metal matrix composites.
I should think it's reasonably feasible to adopt progression press tooling techniques for these forging applications. Progression tooling is another whole artform. Like forging we do less and less of it now in this country, but it's another important one for all of the miscellaneous bits that you find in mass produced automotive systems.
Edited to add, I should think that the big problem with the "automated" approach to mass production of forged components, is tool life. I'd not heard of sintered rods before this thread, but I can quite believe they are possible/used. The thing is that if they do use them, it will be to avoid this exact problem of tool life.
The sintering process, overall works at much lower energies, and the tool does not have to be as resilient for a given number of manufactured units. I too am certain that the sintering process is aimed specifically at low cost mass production.
My only beef here is about the exact definition of a billet rod. My take on that is simply that it is a rod that is not as good as it could be if it were forged, but equally it's been subjected to some degree of hot working, and if targetted at a racing application probably going to be better than most commercial forged/sintered rods, which have been designed mainly to be cheap and functional.
The sad fact is that forging has become expensive, dirty and "old fashoined". Practically it is one of the bes metal forming techniques there is, but attitudes move on.
Edited by dilbert on Saturday 26th January 23:06
GreenV8S said:
dilbert said:
Nice picture
Looks expensive, what on earth is it?The basic idea is that the tool will receive a continuous strip of material at one end and parts will fall out of the other. The other half of the tool is not shown, but it goes up and down on the roller posts that you can see in the picture. The whole thing slides into a brake press, and would usually work in conjunction with an air powered strip feeder. The strip feeder is synchronised to the up and down motion of the brake press. When the top of the tool is clear of the strip, the feeder pushes an exact length of strip into the tool.
Typically such a tool will make punched and folded components, perhaps the clip on a metal pen, or the chassis of an electronic assembly, springs, washers, gearwheels, all manner of bits, one would barely think about in most normal engineering activities.
(The butterfly on a carburettor, or perhaps the little bent bit of metal that is on the end of the throttle shaft, that you hook the throttle cable on to)
Such a tool is a continuous process. It would normally run for between 3 days and three weeks between sharpening operations. The tool might make four components simultaneously, at a rate of maybe 2 every second. Perhaps 2 million components every three weeks. Usually the manufacturing process, would run more than one brake press with the other compnents for a product at the same time.
Edited by dilbert on Saturday 26th January 23:40
GreenV8S said:
It's a
off cookie cutter?
That's pretty much the size of it, but the inginuity comes with the folding, because not only will one of these tools cut out the component, it would normally fold it up too. I worked at a factory where they made microswitches once. They use progression tools that did all that, and they would have a second feed of silver wire into the tool for the switch contact.
Two streams of material go in, and one stream of finished components comes out.
I always look at this sort of stuff like mechanical von neumann machines.
I don't know what that particular tool does, but I would think that there are probably five or six stages in what you can see. That is to say there would be five or six bangs from the press, between flat strip, and finished part. With that tool there it could be that two identical parts fall off the end with each bash. The complexity that immediately hits you is somewhat divided, like cells.
Edited by dilbert on Saturday 26th January 23:48
dilbert said:
I'd not heard of sintered rods before this thread, but I can quite believe they are possible/used. The thing is that if they do use them, it will be to avoid this exact problem of tool life.
The sintering process, overall works at much lower energies, and the tool does not have to be as resilient for a given number of manufactured units. I too am certain that the sintering process is aimed specifically at low cost mass production.
I'd say that most road car rods nowadays are sintered and fracture split. Even Jag V6s and V8s use them and they have pretty high specific power for road cars.The sintering process, overall works at much lower energies, and the tool does not have to be as resilient for a given number of manufactured units. I too am certain that the sintering process is aimed specifically at low cost mass production.
But the drivers to go the pwdered metal route are more than just forging tool life - it's EVERYTHING that goes into making the part.
Boosted LS1 said:
Thank you guys.
These are what I'm probably going to buy but I can't make out the writing on the rod. Clearly a forged Ti rod.
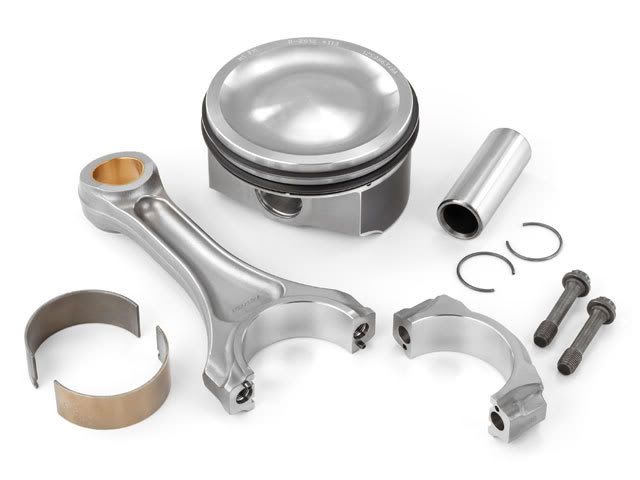
Boosted, those are rods made by a company Called PANKL…..thats the name you cant quite make out..that was the name of the other manufacturer that I forgot……..they are well renowned for their titanium con-rods, they are the main ti con-rod supplier to F1 engine manufacturers, be warned, you will be paying F1 money, they will cost an absolute fortune………also that’s a very interesting picture, where did you get it?..........the truncated small end, and bowl in the piston leads me to think it’s a race rod and piston for a high performance diesel engine…….not gasoline…….where did it come from?These are what I'm probably going to buy but I can't make out the writing on the rod. Clearly a forged Ti rod.
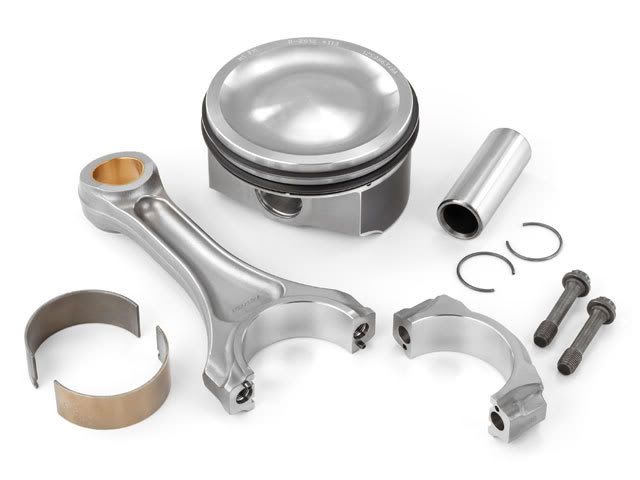
Gassing Station | Engines & Drivetrain | Top of Page | What's New | My Stuff