Suzuki 500 2 stroke Cafe Racer
Discussion
Update to progress. The tank cover is now on the bike, I am making the actual tank now to go under it now... I did the design, and mocked it up in cardboard, but I was concerned it would not be big enough... So I covered the inside with tape and filled it with water, I was surprised it held 16Ltr! That will do for me!
To make the tank I had to learn to TIG weld. I had a session today with a mate who is a welder, he showed me what to do and left me to it for a while. It was easier than I thought, and here is the result after about an hour of practice, I now feel confident enough to weld the tank together after I finish cutting the templates out tomorrow. The plate on the fuel tap will be welded to the bottom of the tank, I have made a spare which I will also weld on the other side, just in case I need another tap fitting at some stage. I won’t drill the spare one through into the tank though…
Glad I decided to do a dry build… the tubes I had put on the frame were too close to the carbs so as I had only tacked them on, it was an easy fix to move them. I have also rebuilt the front calliper with a new seal kit. As part of the dry build I am using any old bolts, I will then replace them with stainless when it all comes apart.
I am still undecided about the seat design, but have shelved that for a few days while I think about it, and anyway I need the new shockers to see how far the wheel comes up on max travel, which may influence the seat design.
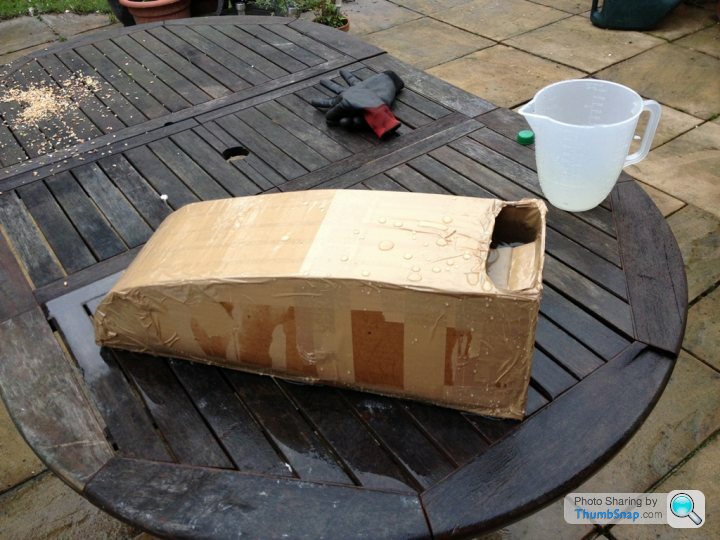
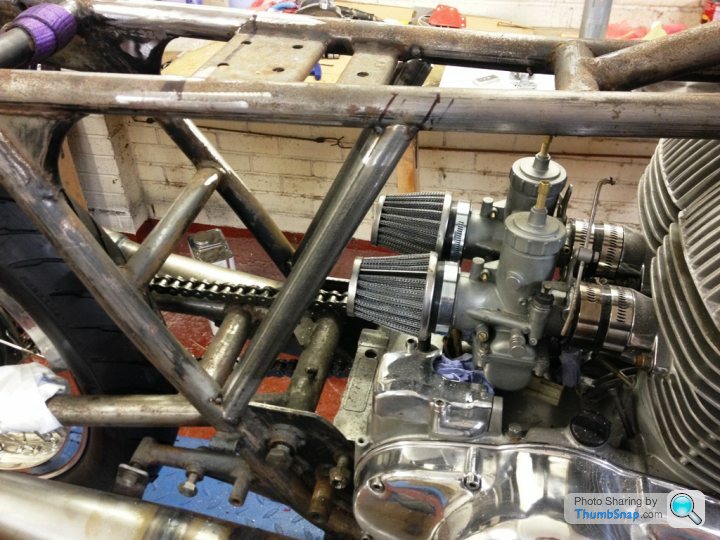
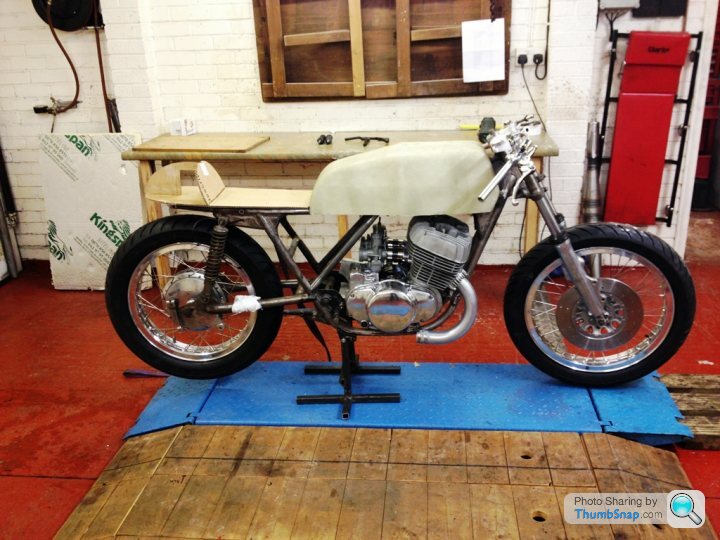

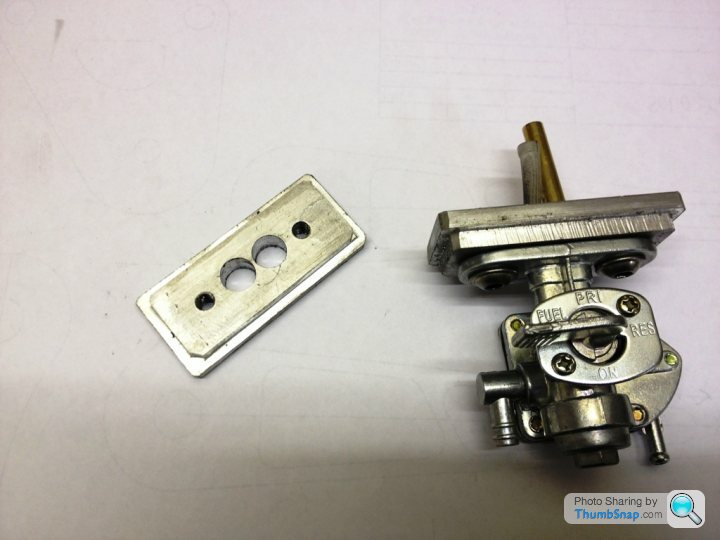
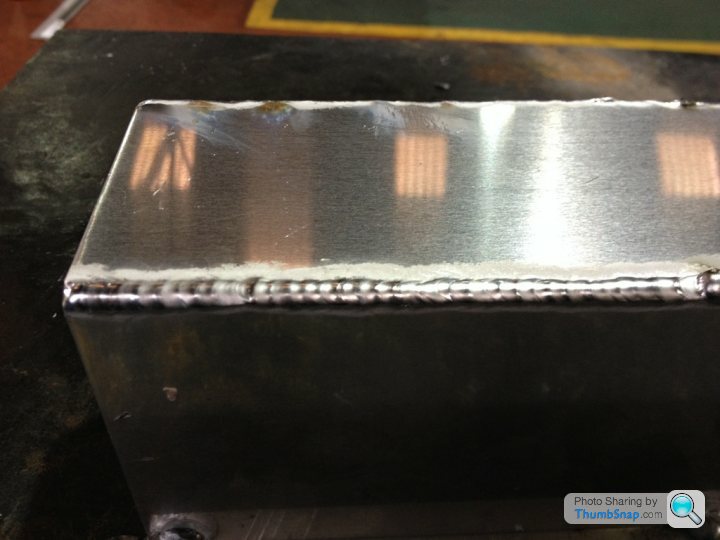
To make the tank I had to learn to TIG weld. I had a session today with a mate who is a welder, he showed me what to do and left me to it for a while. It was easier than I thought, and here is the result after about an hour of practice, I now feel confident enough to weld the tank together after I finish cutting the templates out tomorrow. The plate on the fuel tap will be welded to the bottom of the tank, I have made a spare which I will also weld on the other side, just in case I need another tap fitting at some stage. I won’t drill the spare one through into the tank though…
Glad I decided to do a dry build… the tubes I had put on the frame were too close to the carbs so as I had only tacked them on, it was an easy fix to move them. I have also rebuilt the front calliper with a new seal kit. As part of the dry build I am using any old bolts, I will then replace them with stainless when it all comes apart.
I am still undecided about the seat design, but have shelved that for a few days while I think about it, and anyway I need the new shockers to see how far the wheel comes up on max travel, which may influence the seat design.
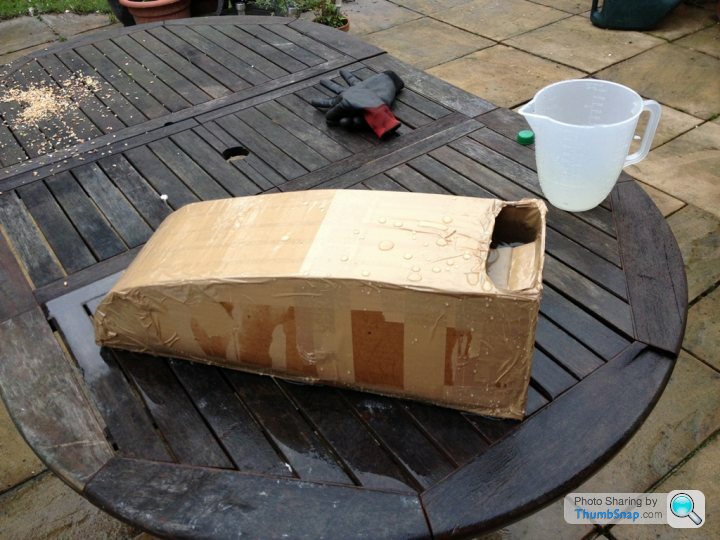
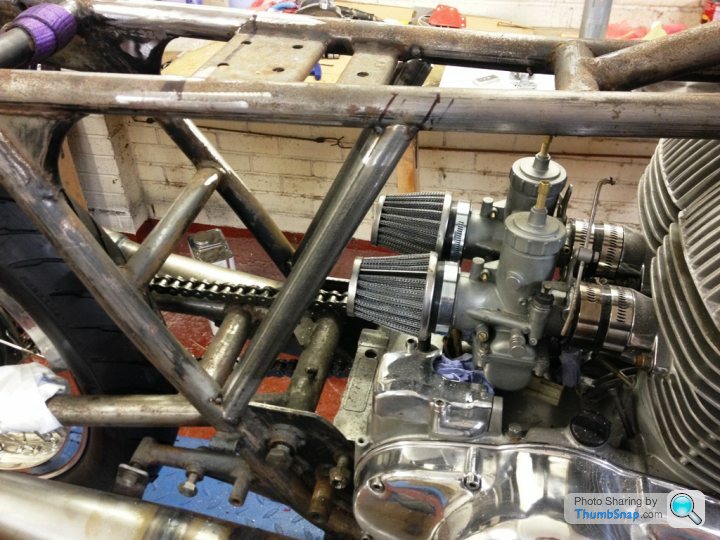
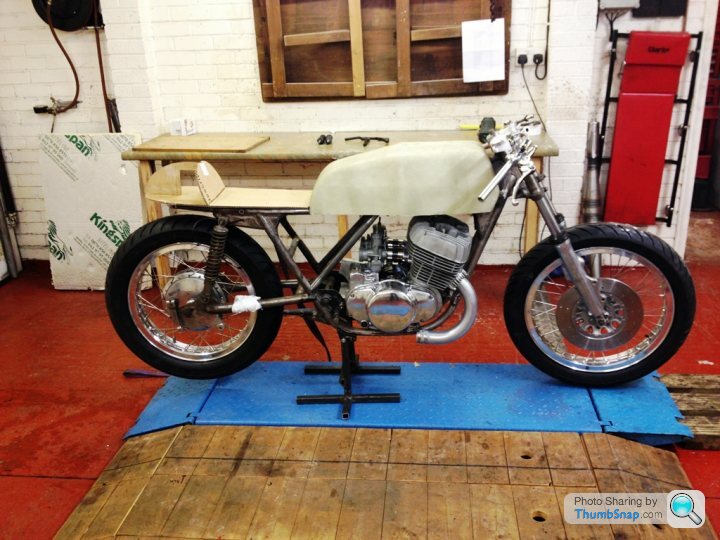

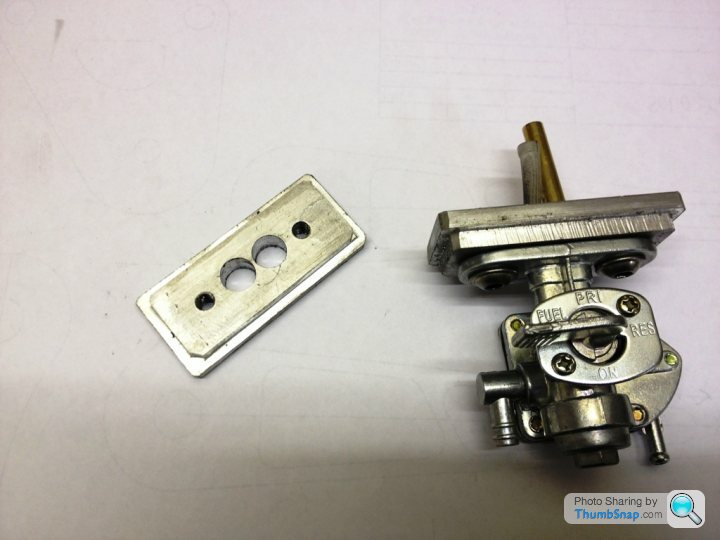
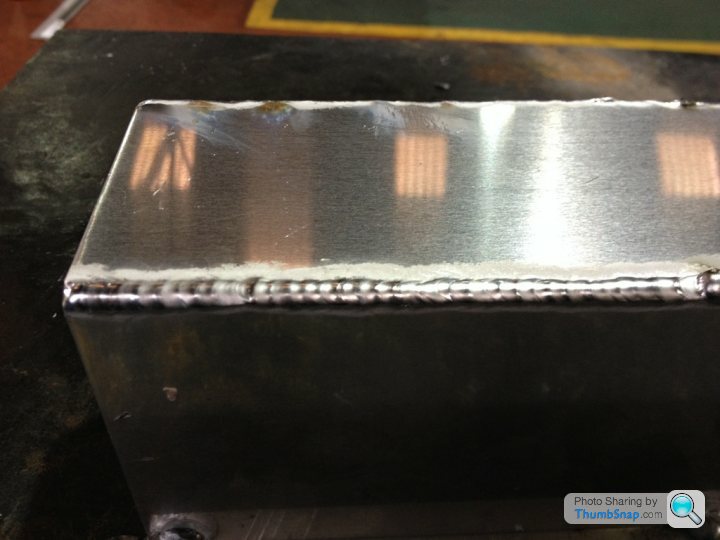
Edited by buzzer on Wednesday 6th January 23:48
My first few attempts at TIG alloy welding just resulted in blown holes and what can best be described as pigeon poo. 
The thicker the easier though, I can now manage quite nicely on ~2mm but any less than that and without a decent heat sink I'm still failing.
Definitely good work as a beginner there though, just make sure no holes!

The thicker the easier though, I can now manage quite nicely on ~2mm but any less than that and without a decent heat sink I'm still failing.
Definitely good work as a beginner there though, just make sure no holes!

Fastdruid said:
... I can now manage quite nicely on ~2mm but any less than that and without a decent heat sink I'm still failing.
Check some of these out 
https://www.youtube.com/results?search_query=weldi...
The Newark bike looks nice!
Been busy in the garage today making the seat, and another mudguard as I didn't like the shape of the first one. the mudguard was easy to get to shape, but the seat took quite a bit longer due to the complex shape. Its there now though and has had the first layup of glass mat. In fact, I have been using glass cloth as it is better for compound curves and falls to the shape as you can see on the mudguard.

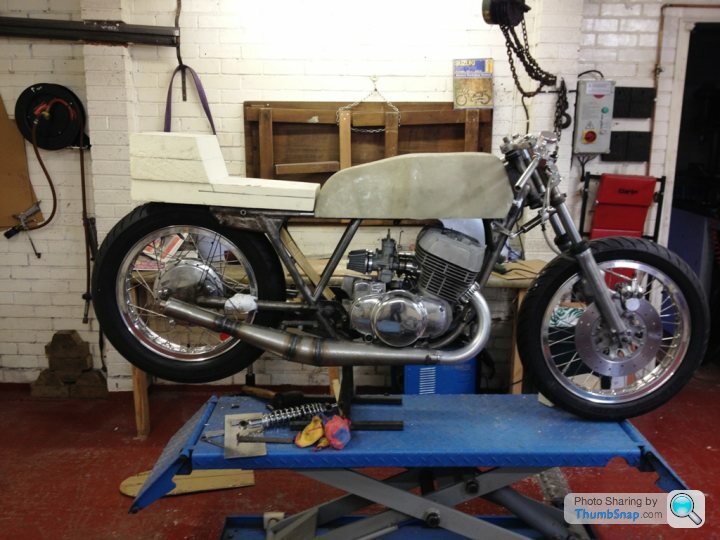
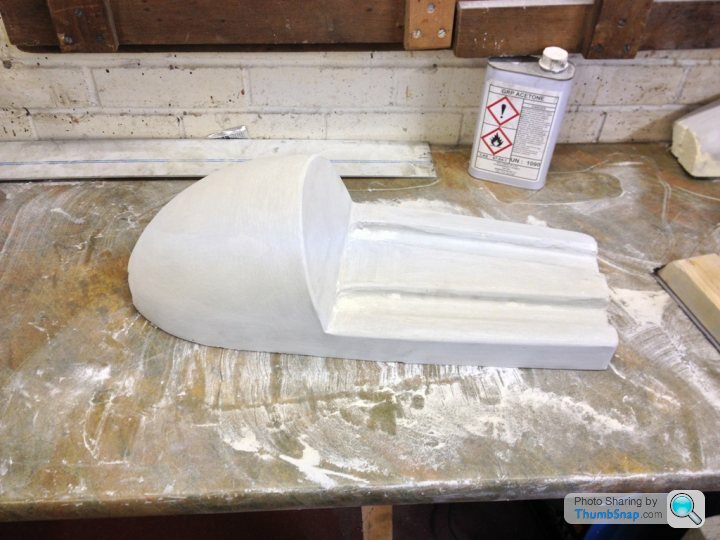
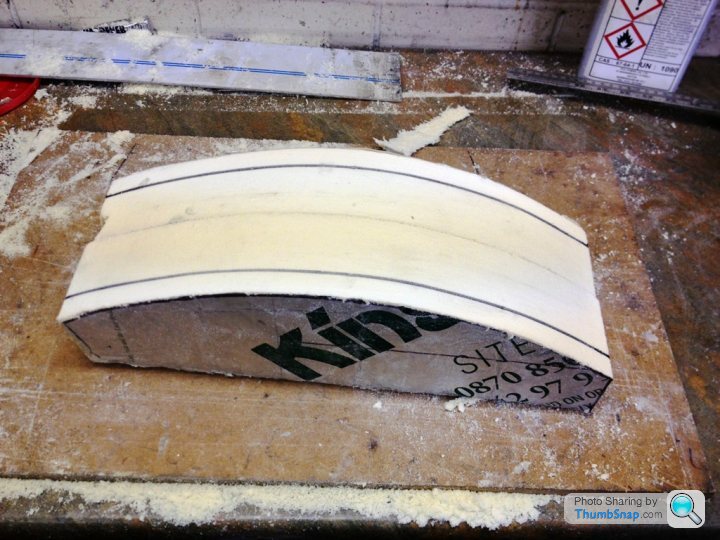
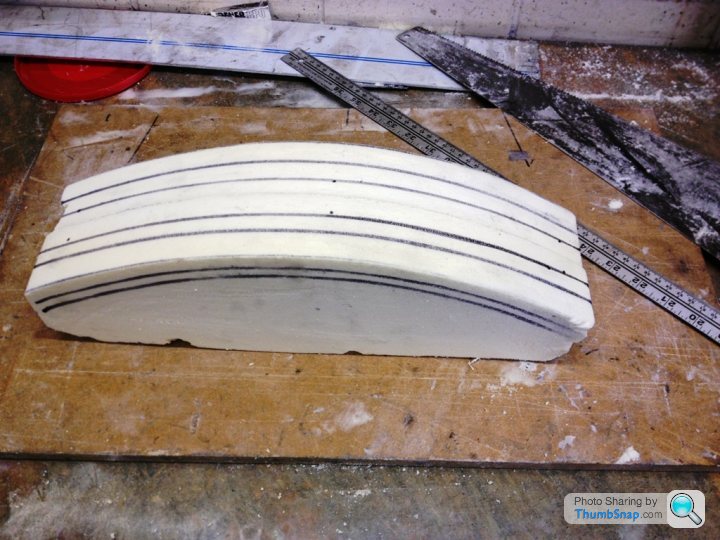

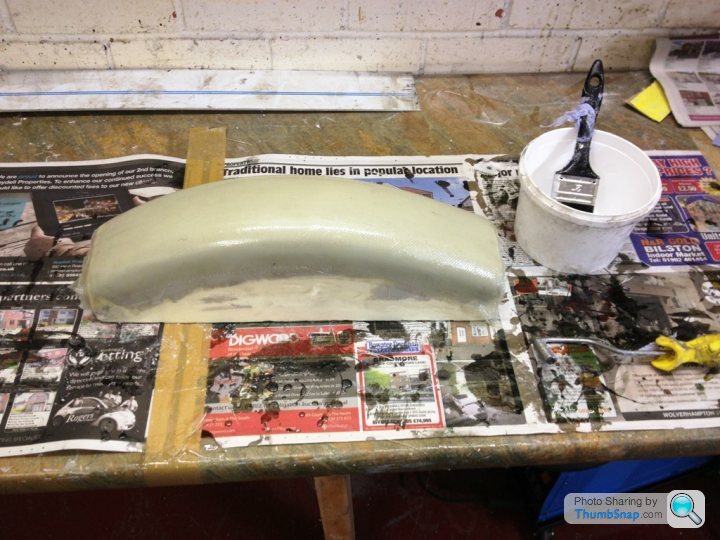
Been busy in the garage today making the seat, and another mudguard as I didn't like the shape of the first one. the mudguard was easy to get to shape, but the seat took quite a bit longer due to the complex shape. Its there now though and has had the first layup of glass mat. In fact, I have been using glass cloth as it is better for compound curves and falls to the shape as you can see on the mudguard.

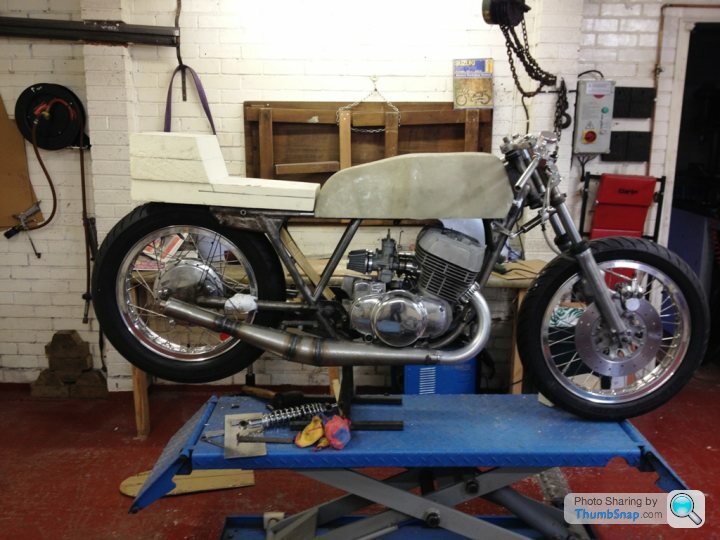
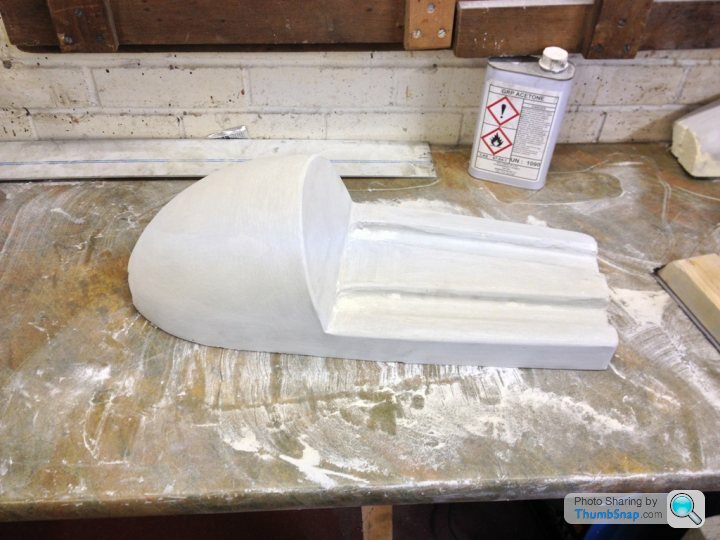
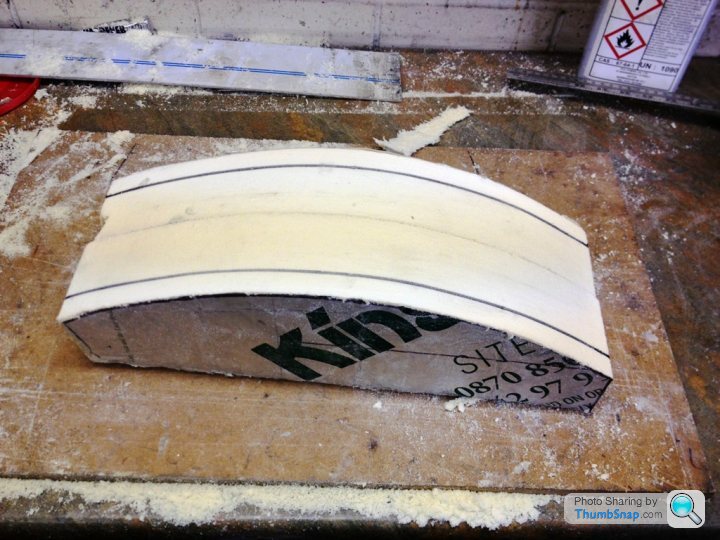
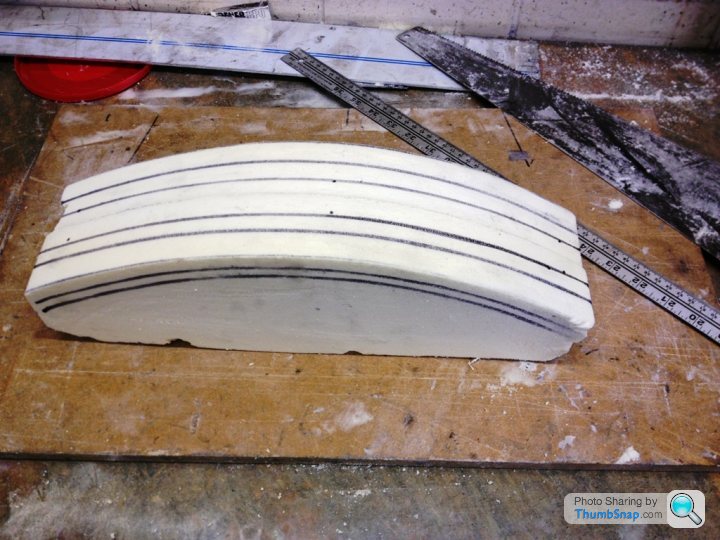

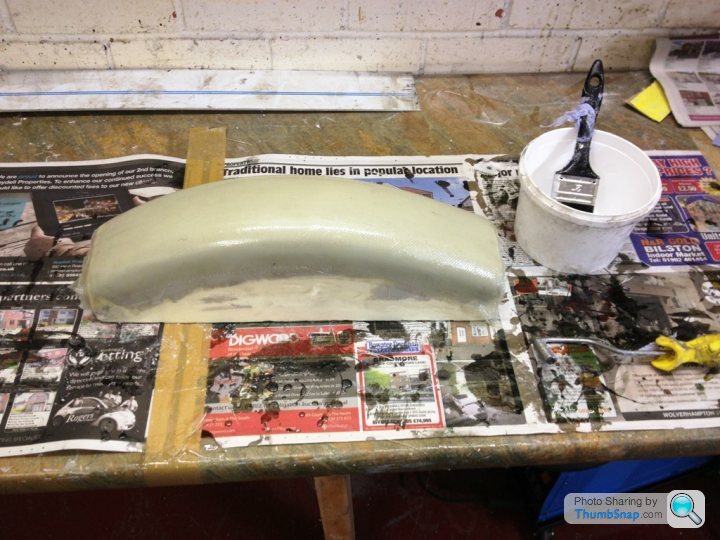
The oil tank and petrol tank are now finished. I welded both up today and used some dye to test for leaks. I didn't want the oil tank ends to be flat so I spun them in the lathe to give an angled dish. an old method of metal forming The filler cap took a bit of thinking about, I have used the original and made an adapter which will fit on with a couple of grub screws and seal with an "O" ring.
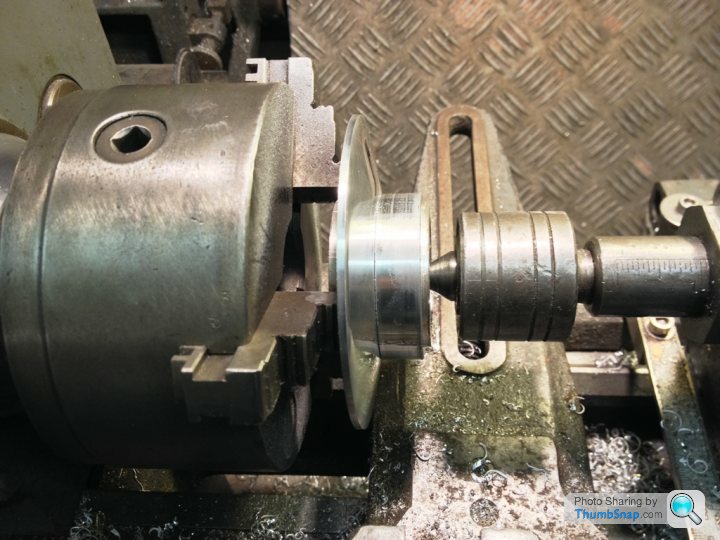
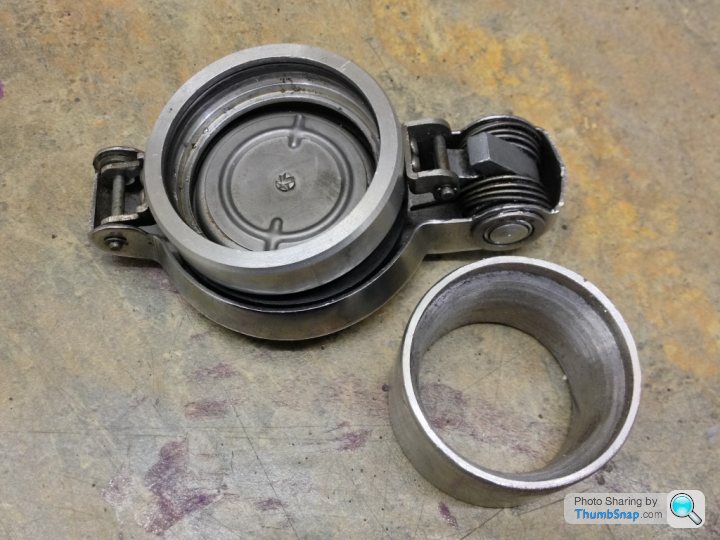
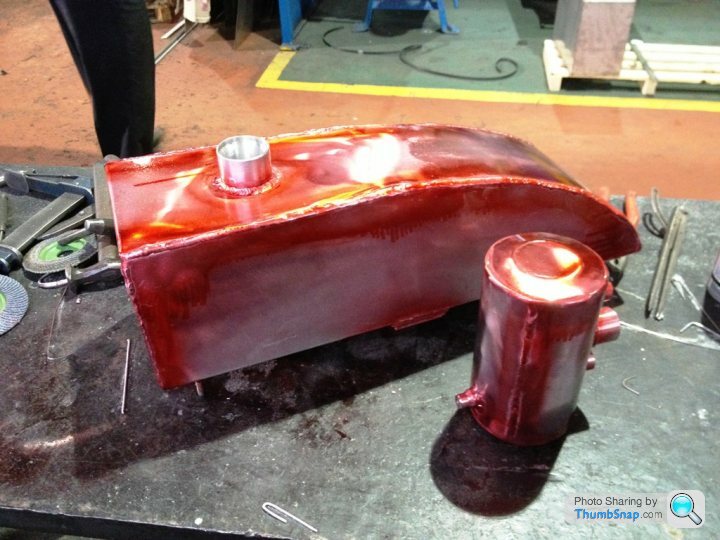
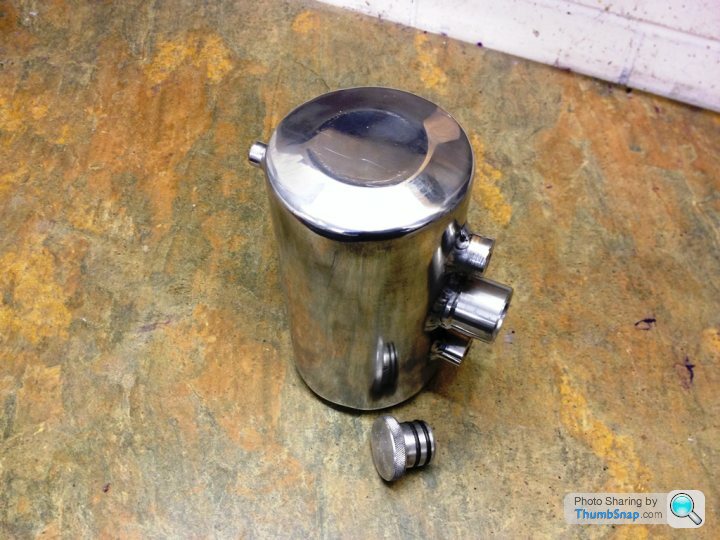

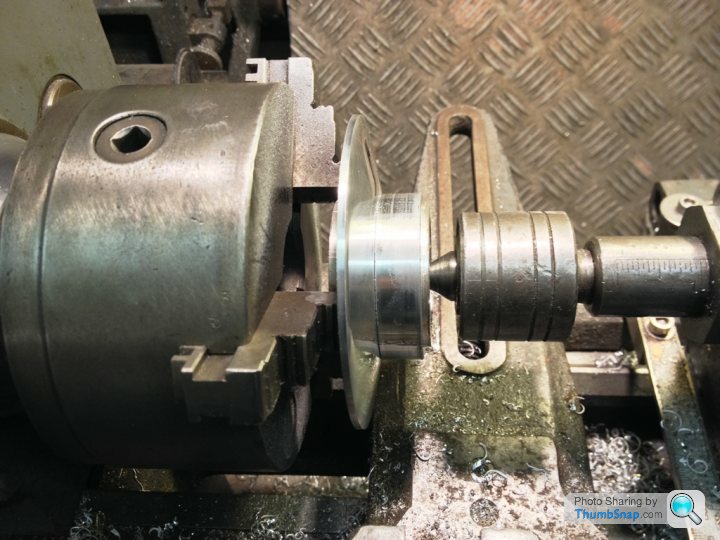
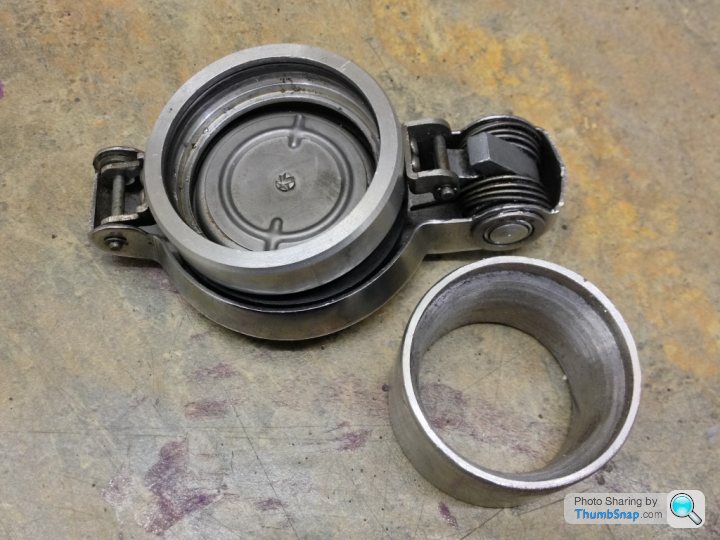
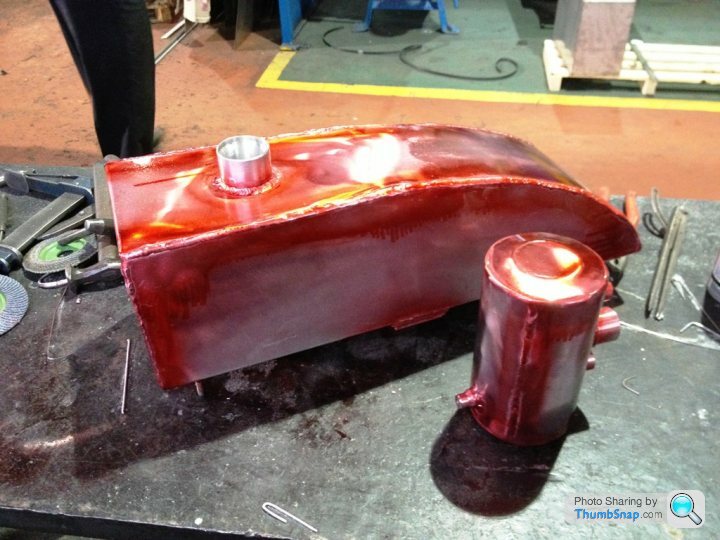
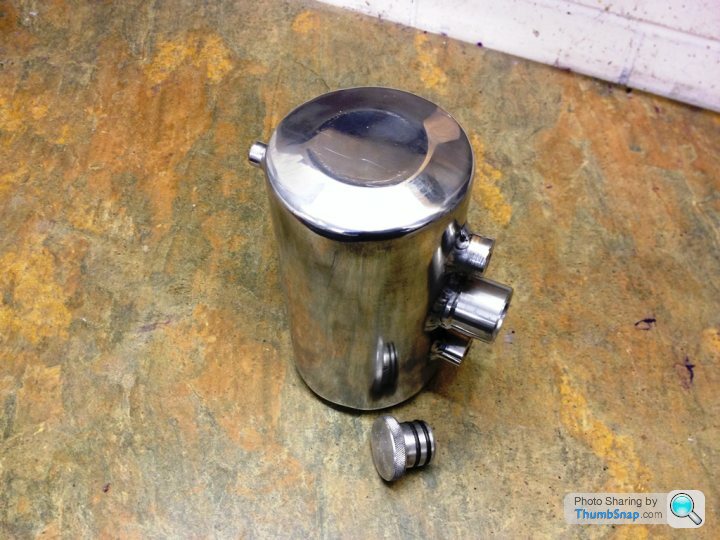

Yazza54 said:
Nice work
Are you doing any work on the engine? Or standard everything, carbs pipes etc?
The engine will be standard, although I did tidy up the ports. some pictures on my blog at Are you doing any work on the engine? Or standard everything, carbs pipes etc?
https://jtccc.wordpress.com/our-motorbikes/suzuki-...
Great thread as I had a GT500 in my University days. If I remember correctly the tacho is driven off the oil pump. When you pull the clutch in the tacho will drop to zero which means the oil pump has stopped working. So don't sit at traffic lights with the clutch pulled in for a long time.
Great bike though as I like in Devon and went to Uni in Hull and it was a great commute.
Great bike though as I like in Devon and went to Uni in Hull and it was a great commute.
Bit more progress.... the bike is now back in bits and the frame is off to the powder coaters tomorrow...
I have been busy making the rear sets, which will be polished once they are trial fitted and all is OK. they took a while to make, but since I converted my milling machine and lathe to digital read outs using some cheap digital calipers, its transformed the ease of use and accuracy!
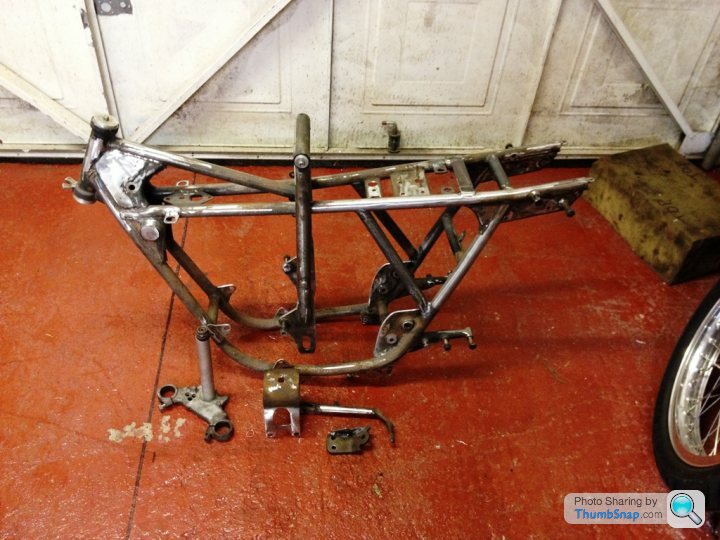
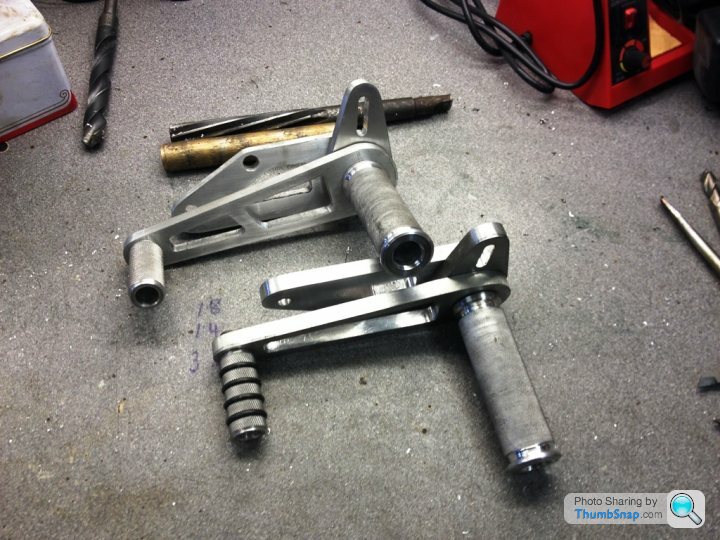
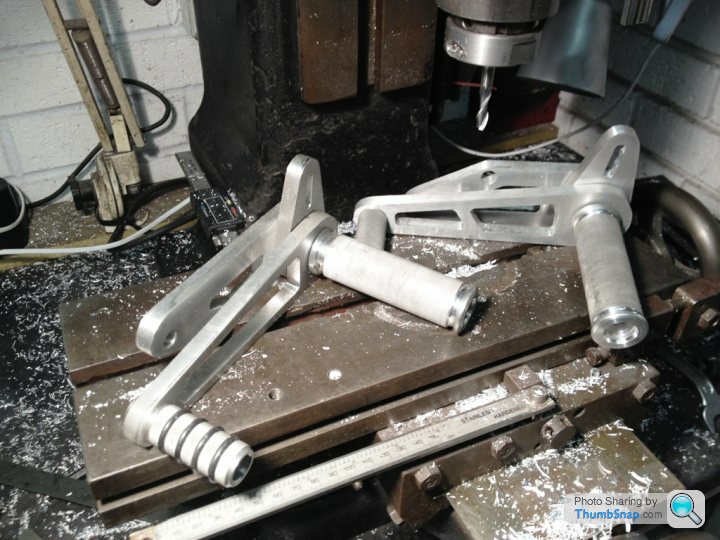
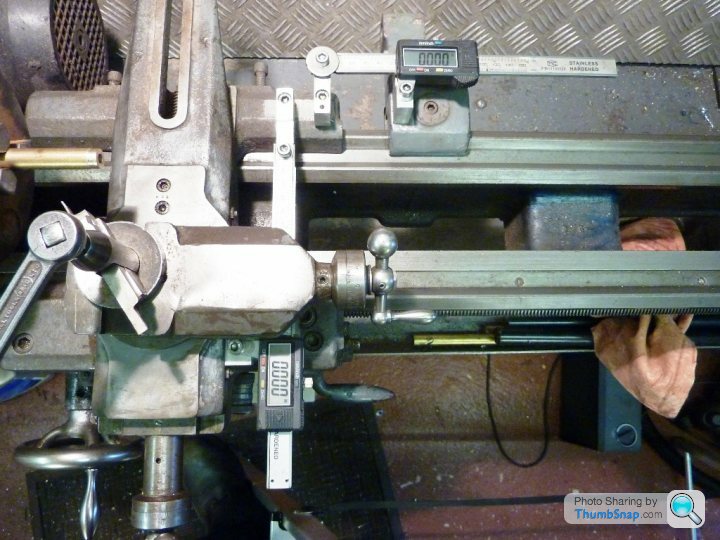
I have been busy making the rear sets, which will be polished once they are trial fitted and all is OK. they took a while to make, but since I converted my milling machine and lathe to digital read outs using some cheap digital calipers, its transformed the ease of use and accuracy!
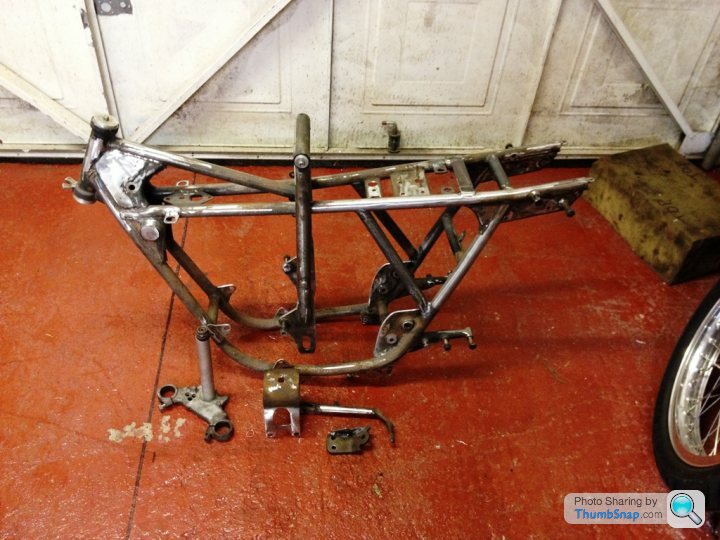
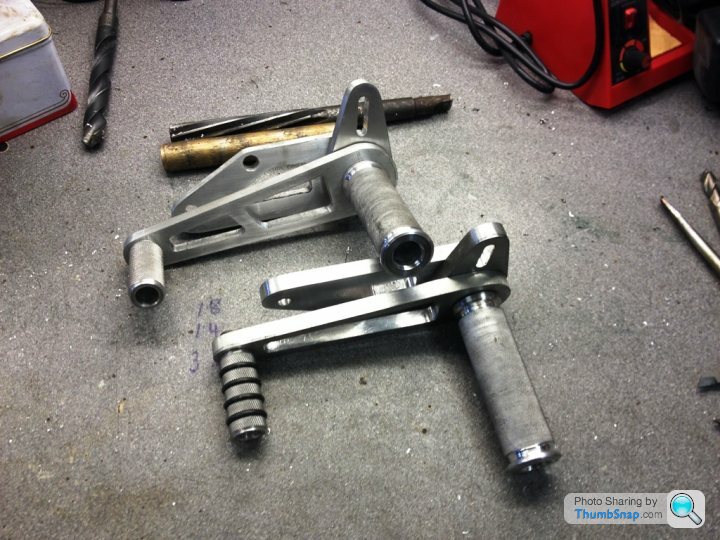
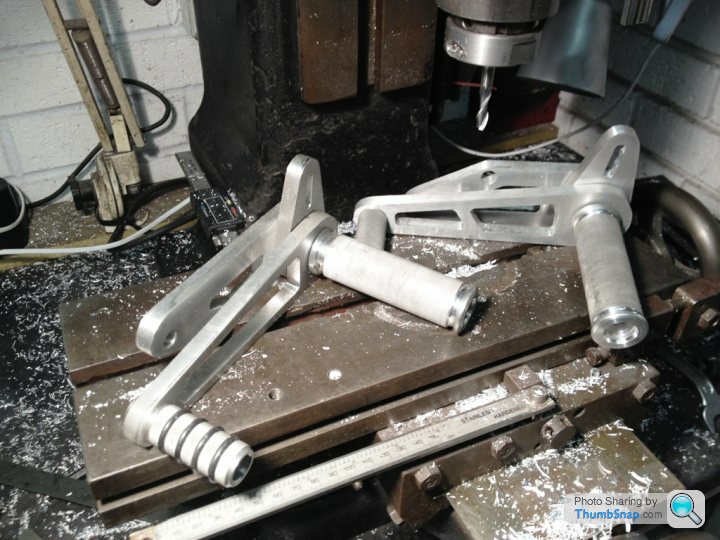
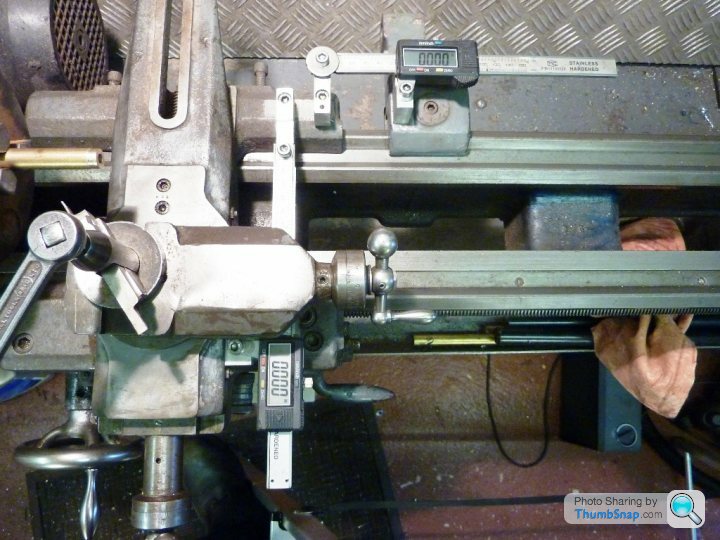
While the frame is away I have been looking at the wiring. The intention was always to replace it, but as I will be modifying most of the electrics I decided to make a loom from scratch as this will need to incorporate key-less ignition, a modern rectifier and voltage regulator and LED indicators, along with a brake light switch on the front, as opposed to rear brake.
I cur the old loom apart and laid it out on the bench and noted the colours, so where possible I can stick to the original colour scheme. I then measured each wire and made a list. There were around 20 colours, and when the parts guy saw the list he thought he had a big order… until he realised that many of the lengths were just one meter!
Here is the horn, and light switch being rebuilt, my eyes and fingers are not what they used to be, hence the neat little helper! The horn switch was broken, the small mica insulator was split in half, which is a common fault, so I had to make a new one… I looked around for some material that was resistant to heat (so I could solder the terminal) but importantly was an insulator. I found the perfect material in the splatter shield off an arc welding mask! Perfect for the job.
I have also rebuilt the front forks with new seals...
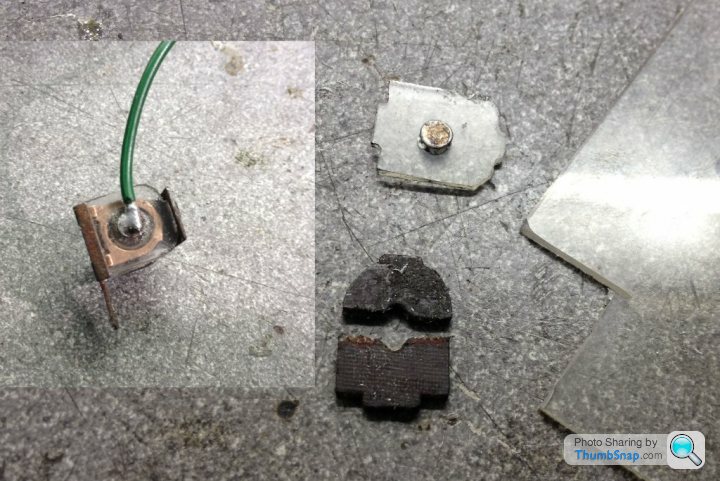
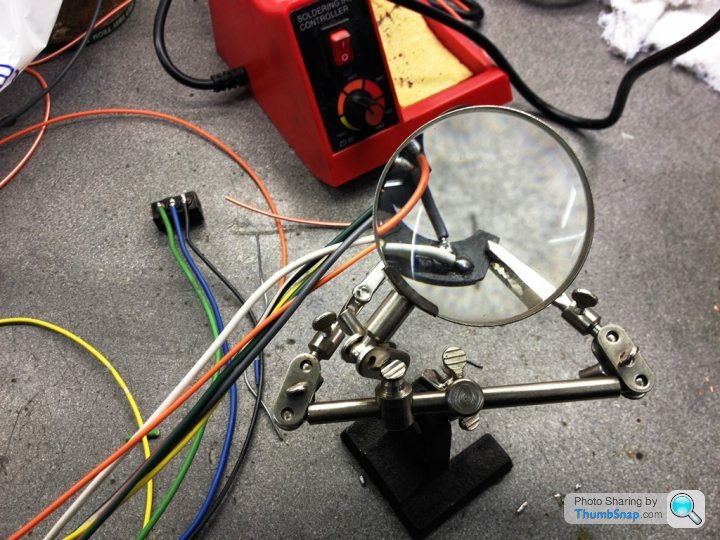
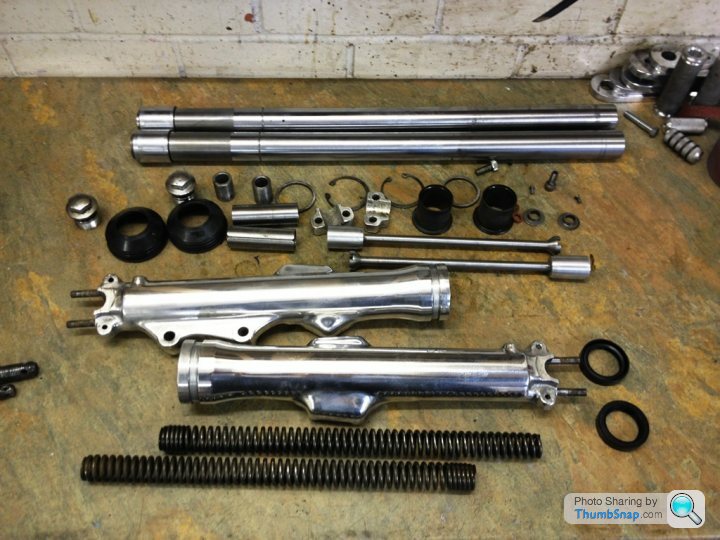
I cur the old loom apart and laid it out on the bench and noted the colours, so where possible I can stick to the original colour scheme. I then measured each wire and made a list. There were around 20 colours, and when the parts guy saw the list he thought he had a big order… until he realised that many of the lengths were just one meter!
Here is the horn, and light switch being rebuilt, my eyes and fingers are not what they used to be, hence the neat little helper! The horn switch was broken, the small mica insulator was split in half, which is a common fault, so I had to make a new one… I looked around for some material that was resistant to heat (so I could solder the terminal) but importantly was an insulator. I found the perfect material in the splatter shield off an arc welding mask! Perfect for the job.
I have also rebuilt the front forks with new seals...
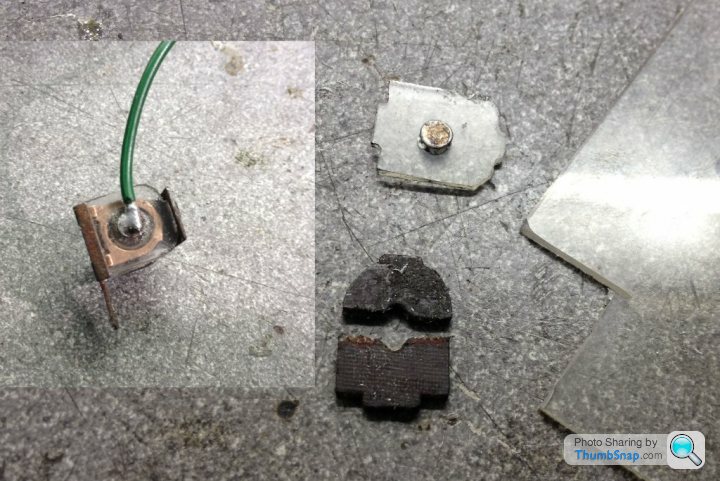
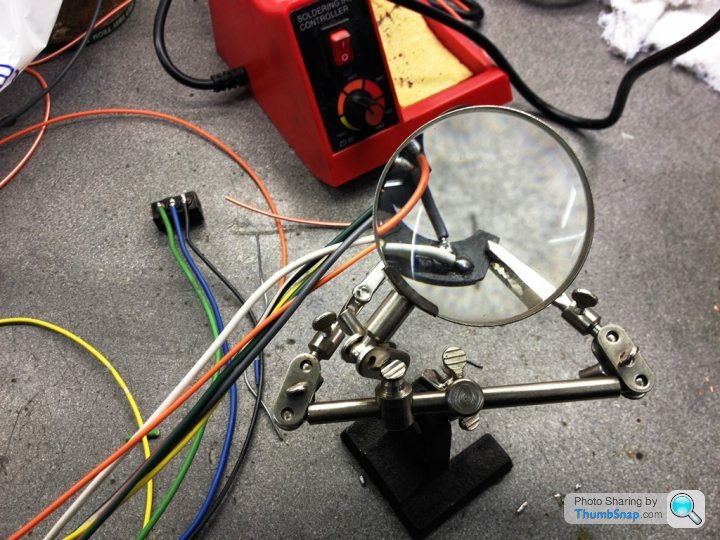
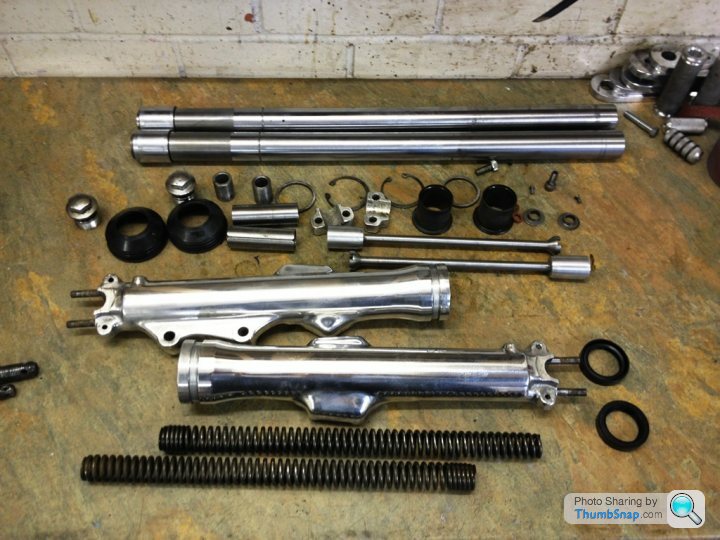
Gassing Station | Biker Banter | Top of Page | What's New | My Stuff