Supercharger 6 month in
Discussion
First off I'd like to say thanks to John & Nick. I've learnt a lot from their threads and picked up many ideas I used on my car, hopefully I can do the same for someone else.
My story started last year when I wanted to use a Jag M112 Eaton PD supercharger, I'd seen pictures of a Land Rover 90 using one on a 4.6 and I started out trying to replicate his setup. He was using a box shaped plenum above the inlet manifold and I quickly found height was going to be an issue. So I ditched the idea of the box and wondered if I could mill out the internals of an inlet manifold to form the plenum. I also needed the inlet manifold to be biased towards the front as even with the long neck on the supercharger the outlet was over the front 4 cylinders.
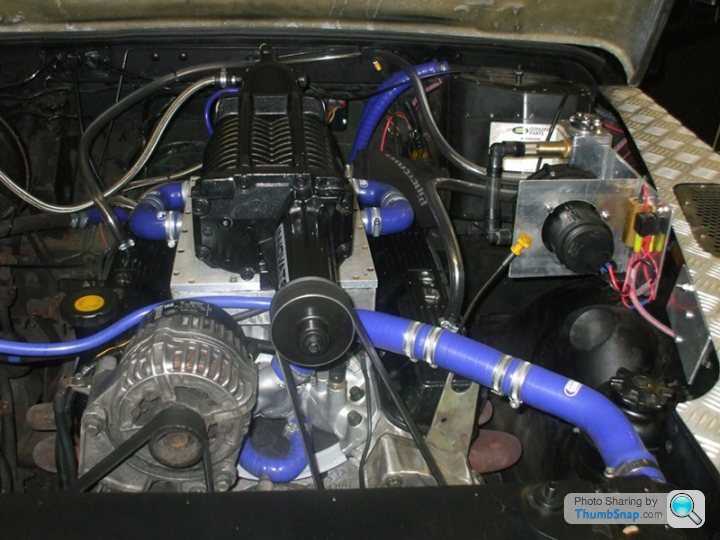
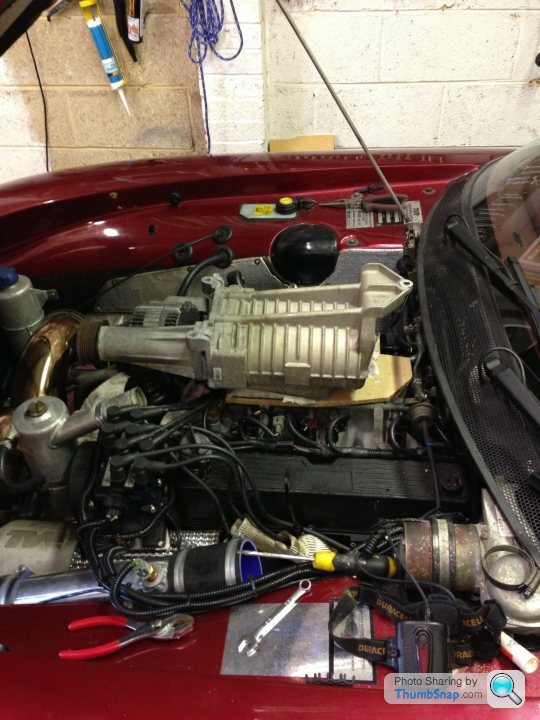
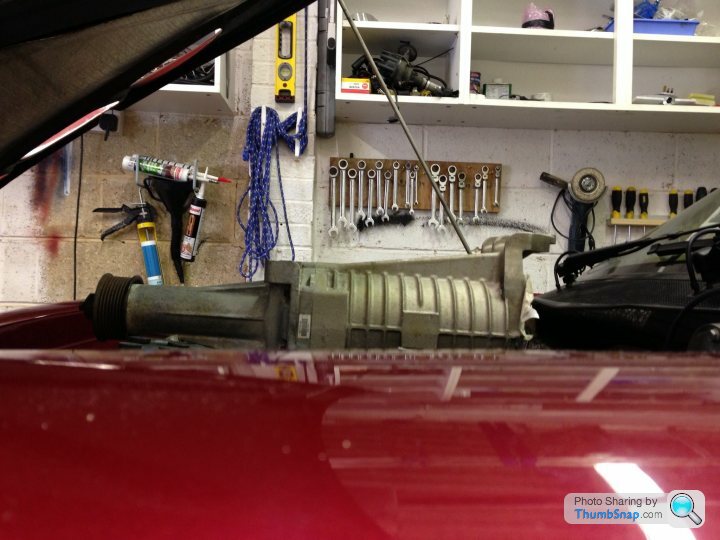
So I bought a Thor inlet manifold and started converting it to work backwards by removing the water chamber and milling out the middle. I was planning on using Clio 197 injectors as they are very short so I could mill the top off inlet manifold so the charger would sit lower. After more measuring and mocking it became clear I was going to need to cut the bonnet.
The main problem was I wanted the charger to sit as low as possible but by doing that there less common volume so there rear most 4 cylinder would start to get affected by flow issues and run rich.


So the PD supercharger idea was abandoned and after reading John and Nicks thread I got in contact with SC Power. We decided on the C30 due to mine being a 4.0 and to use a smaller pulley as I could make the most of it using an MS ECU. After a bit of a wait for TTS to get more units imported my kit arrived. The brackets were very impressive and fitting the kit was straight forward. I had several other jobs to do as well such as moving coil packs, new HT leads, SC Power engine mounts, uprated fuel pump and bigger Astra VXR 470cc injectors.


Whilst waiting for the kit to arrive I had the wheels refurbished in smoked chrome and went with 16" fronts.
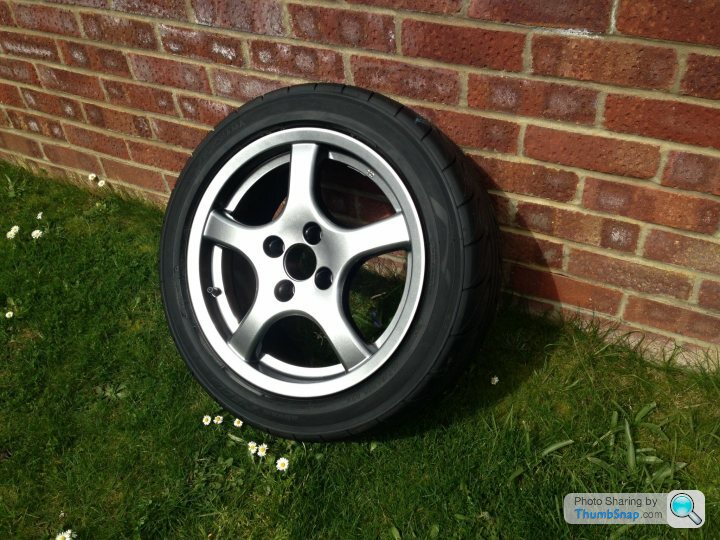

The 16" front allowed me to fit something I wanted to for a while, a bigger front disc. I was using sierra 283mm discs so I ordered a pair of MK1 Focus RS discs at 324mm. I was hoping to use them as is but the crossover pipe was a bit too close. I wanted 5mm clearance just in case the wheel changes shape via a pot hole.


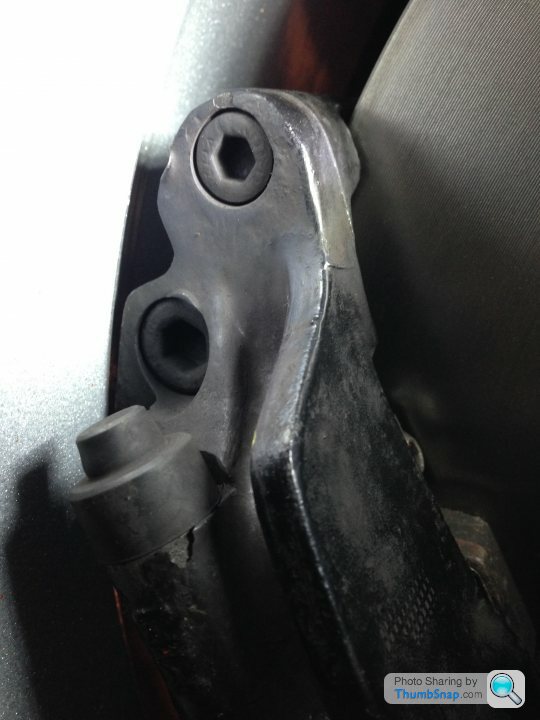

Towards the end of fitting the kit I was not happy with the throttle cable routing, I didn't like the 180deg bend it had to take so I started looking for alternatives. I found some P38 range rovers use a forward entry bracket and after a quick email to TVR Power they supplied a LHD throttle cable. Which greatly shortens the cable and removes the bend. The bracket works great and even uses the original bolts into the plenum. I definitely recommend this to any supercharger owners, the throttle pedal was so much lighter and quicker to return. It does need modifying to clear the bonnet. I cut the top off, re-drilled the hole for the cable and then made a small bracket to fit on the throttle spindle as the new lower position was causing the cable to touch the throttle spindle with the throttle closed. The picture below is before I modified the bracket. If anyone needs a LHD cable, I have one spare.


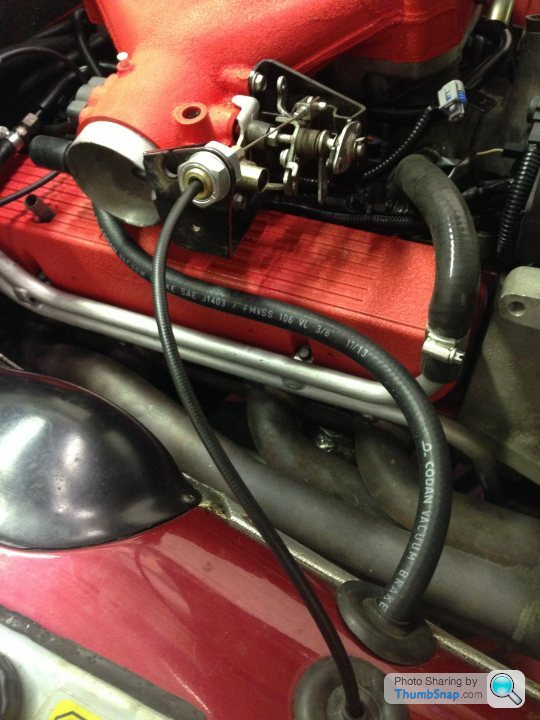
The first test drive went well, John was kind enough to share his ignition map with me so I had a good starting point I just needed to shape the VE table using the wideband.
Johns map uses Alpha N, so I changed my ECU to use Alpha N as I was previously using speed density. Whilst running in the supercharger I set the rev limit to 3K, once run I raised the rev limit 1K at a time to reduce the area of the map I was tuning. The first issue I had was belt slip, the supplied belt must have been for the larger pulley as at full load the belt stretched enough that the tensioner could sit on its stop providing no tension. A new belt worked great, I fitted the smallest I could as being a clock spring in the tensioner the shorter the belt the more tension.

The next problem to solve was no matter how much I back off the full boost cells at 5Krpm+ of the VE table the wideband would always show 10.0 AFR. I took loads of fuel out but no change. I suspected the fuel reg. I kept the standard one as I could control the fuelling I didn't need the Begi Rising Rate. Around 5K revs with 12psi+ the diaphragm was completely closing off the return and raising the rail pressure to pump pressure. I guess the standard item was never designed to deal with boost so it did pretty well considering. I didn't want a remote reg so I started hunting for a standard item to fit the rail that was fitted to a boosted engine as standard. I found Bosch 0280 160 258 which are fitted to Porsche 944 turbo. 3 bar reg
This bolted straight on to the rail and raise the static pressure to 3bar. I had to take a bit of fuel out of the whole map to account for the rise in static pressure but at full boost the fuelling was now spot on.
On with more tuning and I was now using a 6K rev limit, the next issue I found was the inlet temps were reaching 55deg regularly and it would knock intermittently. Max boost was 13psi at 6K. Heading out for a tuning session the inlet temp would start at 20deg, after some tuning and pulling into a layby to check the logs the inlet temp would be 45deg idling. Driving away cruising the inlet temp would not come back down, only rise to 55deg on boost and back to 40/45 deg. I suspected the aluminium pipework was picking up heat from the exhaust and not being able to get rid of it. The cold pipe passes the Y-piece with a 10mm gap and then runs parallel to the exhaust manifold. I cut the cold pipe and rotated the top piece, using a silicone joiner I could route the pipe around the Y-piece instead of over it. According to the logs this did help but rather than a drop in temp it now took longer for the heat soak to set in.

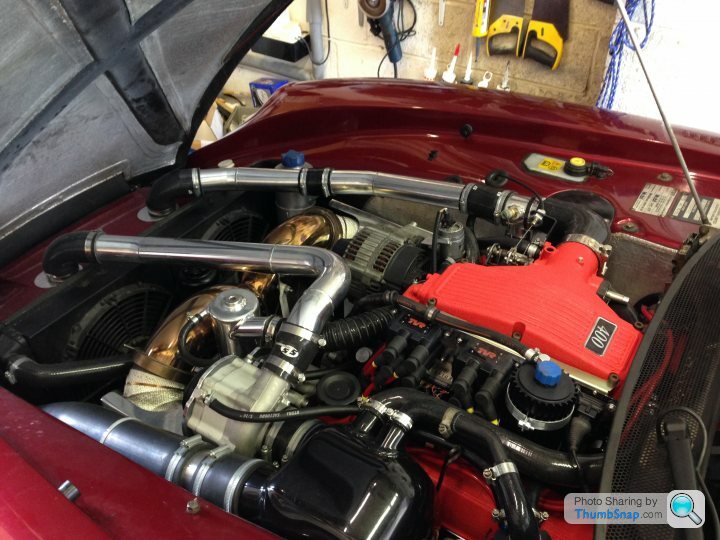
I also double checked the calculations for the speed of the supercharger. The crank pulley is 7" (177.8m) and the charger pulley is 85mm, 2.09 ratio. 2.09 X 6K rpm = 12,550rpm input speed! The C30-94 max input speed is 10,500rpm so over spinning the charger was most likely contributing to the excess heat. I reduced the rev limit down and only rev it to 5.5K now to keep the input speed within the +10% speed TTS recommend.
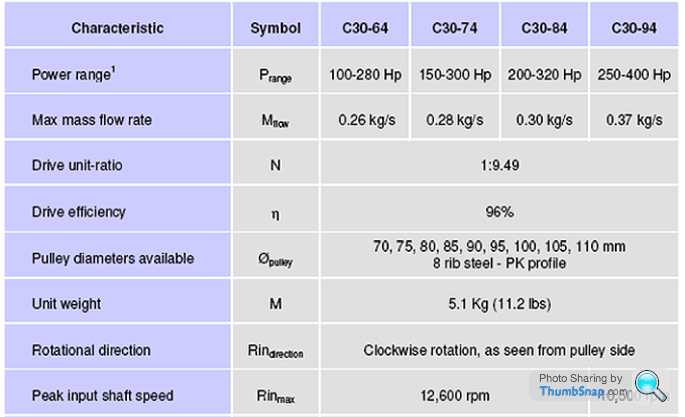
With Santa Pod coming up, this was not going to work well as the queue can be quite long so by the time I stage the inlet temp will be 45+ easily. I started looking into alternative pipework to stop the cold pipe running parallel to the exhaust manifold.

The plan was to move the alternator to the air con compressor position and move the throttle to the front like the Westfield’s use. Luckily I have mate who is handy with a Tig welder and is happy to be paid in beer. It took a couple of attempts and lots of measuring, eventually we ended up with near straight pipework from the intercooler to the throttle and a bigger gap to the Y piece. I was advised it wouldn't work well with the throttle at the front and the rear cylinders wouldn't get enough air. I thought this was rubbish as I used a GEMS plenum to get more volume and left the side chamber fairly big so there should be no shortage of air. I cut the trumpets right down, with the supercharger I wasn't fussed on losing any torque the trumpets provide. I cut them equally as per Jools blended base which I hope to use eventually.



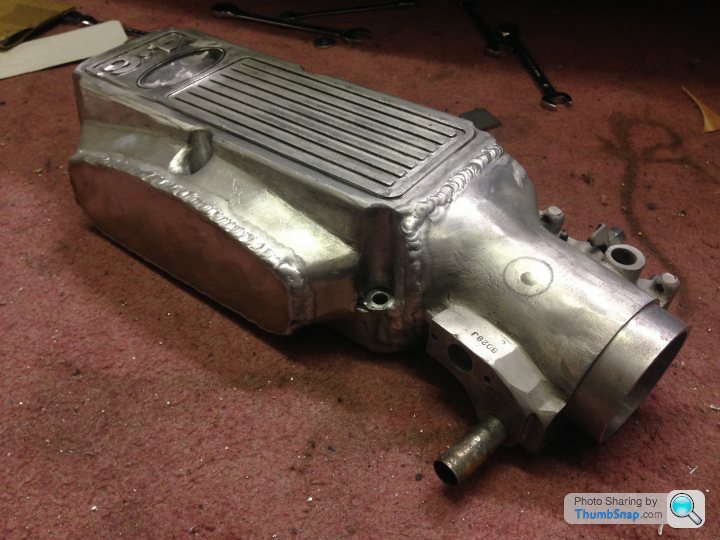
A new longer 2315mm belt, reverted back to the old throttle cable, add an inlet for the idle valve and amended the dump valve pipework and we're ready for another test.

The following tuning sessions showed much more promising results, the inlet temp were down about 5deg and took much longer to heat soak. Not a great as I had hoped for but happy for an improvement. Next was a small tweak to the hot pipe, it was really close to inlet temp sensor and cold pipe. I cut the curved end off the hot pipe and removed more material from the throttle bracket.



Next was some testing for Santa Pod, after a run through 1st to 4th the inlet temp peaked at 60deg. The ECU is set to start pulling timing at 54deg so most of 4th gear was done with 10deg ignition timing. It feels really flat when this happens and is definitely not good for power.
After a bit of research water injection seemed like a good option and with a supplier just down the road a progressive kit was ordered. It was easy to fit and worked really well the max temp was 40deg not matter how hard I tried! The pump lives in the boot with the gallon tank and there’s a progressive controller in the cabin. The controller needs a vacuum hose and brings the pump in at 15% duty cycle at the first pot setting then 100% at the second. I was using 3psi for 15% and 8psi for 100%. I ran the water line along the chassis and into driver’s foot well, behind the brake servo and out the throttle grommet. This saved me running the water line over the inlet manifold and picking up heat when not in use.

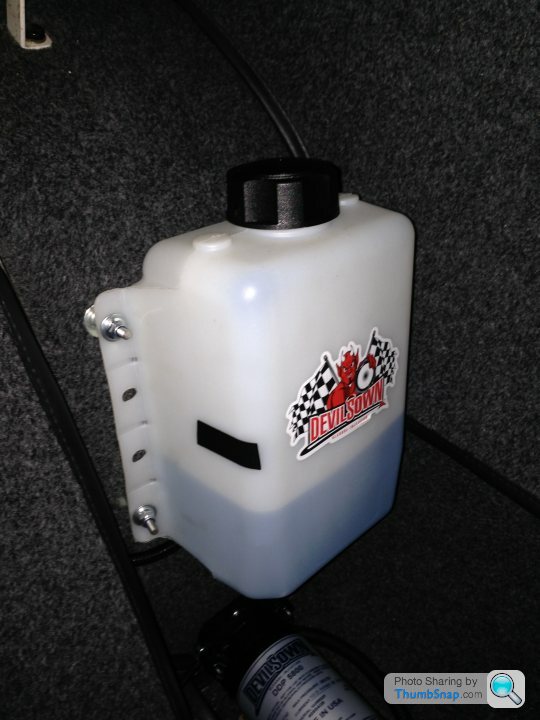
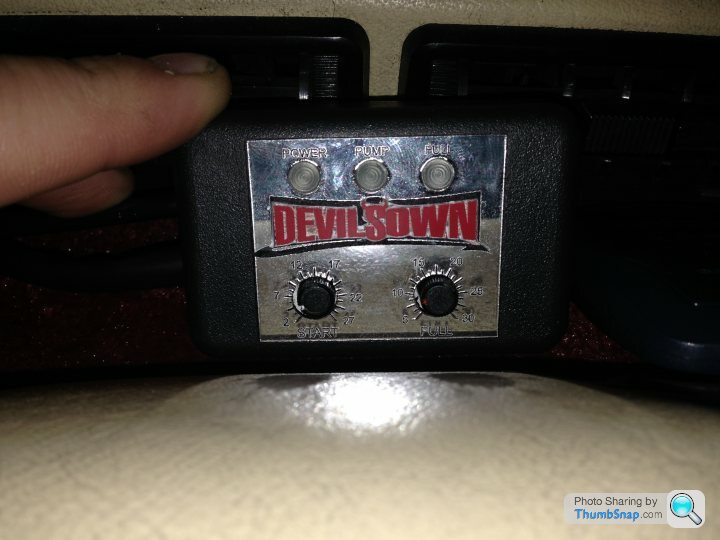
I was really happy with it now the intermittent knock stopped and the inlet temp are predictable. Just to help matters I wrapped the cold pipe in reflective tape and fibreglass cloth.
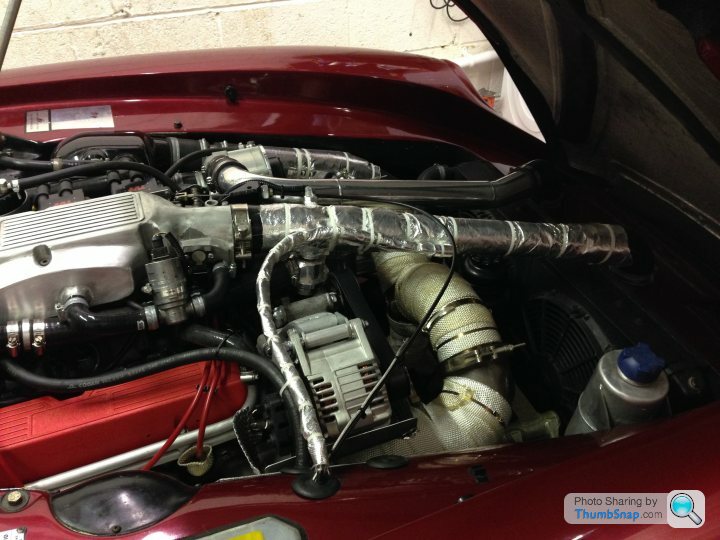
That night was pub club so a nice run out to West Meon and back. It went really well but when I had a quick glance over the engine in the garage there was a small puddle on the radiator dripping from the fibreglass cloth. My first thought was the water line was leaking but with the pump pressure at 200psi I thought it would be more noticeable. I peeled back the fibreglass wrap and found whole pipe covered in condensation so it must of been cold!

Before Santa Pod I checked the plugs to see if there is any truth in the cylinders getting different volumes of air. Below is the offside bank in order the rightmost being number 2 and I couldn't see any differences between them. They looked the same as the last time I checked them, nice and clean. I use 8s as recommend by SC Power. I also went up a water jet size from 252cc/min to 315cc/min. The meant the max air temp is 35deg and only rises into the 30s when ¾ boost.


After checking the logs from Santa Pod I found the temps were a bit chaotic and the GoPro video confirmed the pump was only running in some gears. My fastest run was done with the pump only working in 1st and 4th so a bit more to come hopefully. I’ve now removed the progressive controller, the ECU is going to control the pump. This means I’m going to lose the progressive start but hopefully a more reliable trigger for the pump. I can set what boost and inlet temp the pump should come in so I’m going to start with boost > 4psi and inlet temp > 28deg with a 10deg hysteresis on the inlet temp.
That'll do for now, next on the list is to get it on a rolling road and then start on the winter upgrades!
My story started last year when I wanted to use a Jag M112 Eaton PD supercharger, I'd seen pictures of a Land Rover 90 using one on a 4.6 and I started out trying to replicate his setup. He was using a box shaped plenum above the inlet manifold and I quickly found height was going to be an issue. So I ditched the idea of the box and wondered if I could mill out the internals of an inlet manifold to form the plenum. I also needed the inlet manifold to be biased towards the front as even with the long neck on the supercharger the outlet was over the front 4 cylinders.
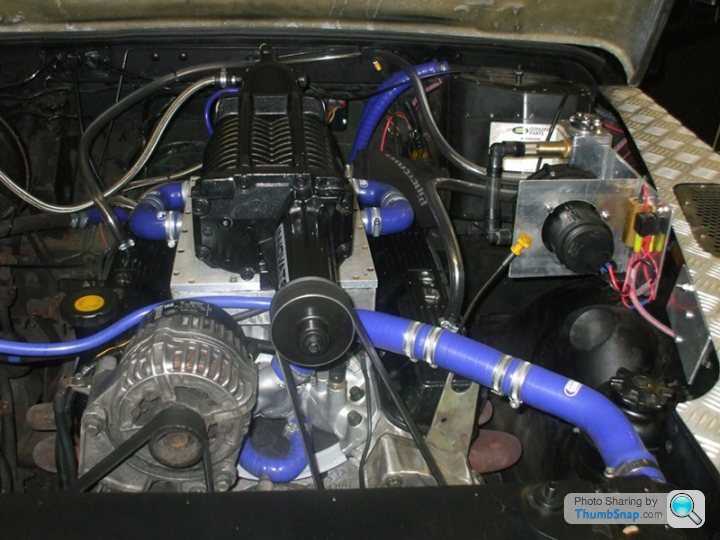
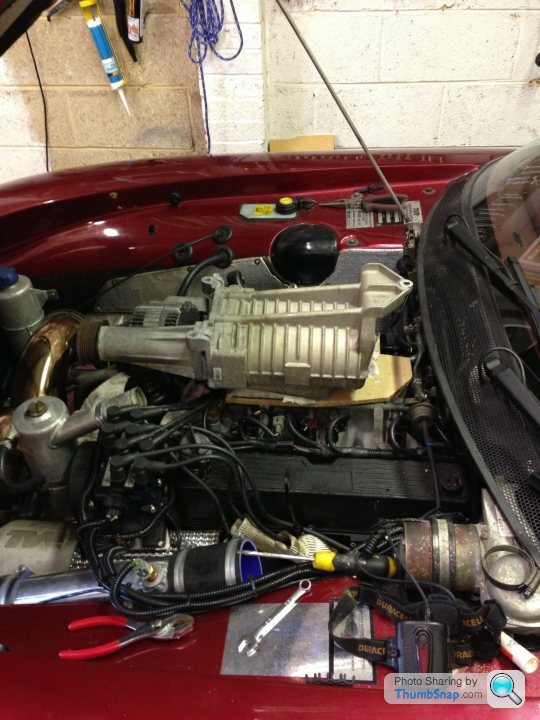
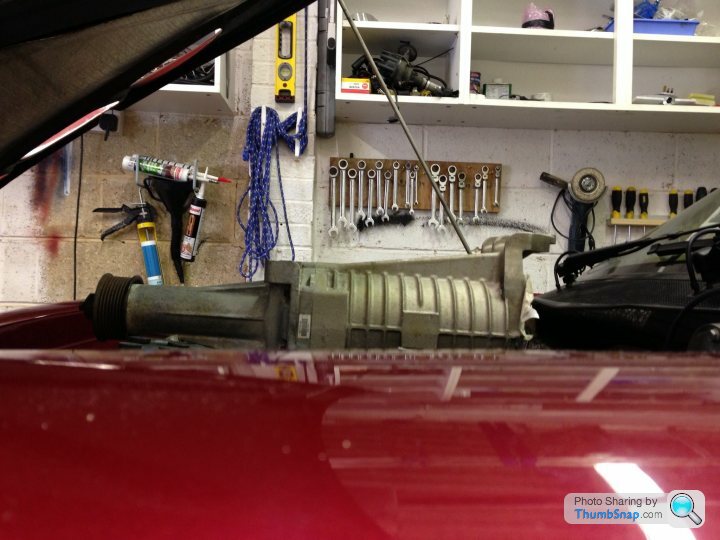
So I bought a Thor inlet manifold and started converting it to work backwards by removing the water chamber and milling out the middle. I was planning on using Clio 197 injectors as they are very short so I could mill the top off inlet manifold so the charger would sit lower. After more measuring and mocking it became clear I was going to need to cut the bonnet.
The main problem was I wanted the charger to sit as low as possible but by doing that there less common volume so there rear most 4 cylinder would start to get affected by flow issues and run rich.


So the PD supercharger idea was abandoned and after reading John and Nicks thread I got in contact with SC Power. We decided on the C30 due to mine being a 4.0 and to use a smaller pulley as I could make the most of it using an MS ECU. After a bit of a wait for TTS to get more units imported my kit arrived. The brackets were very impressive and fitting the kit was straight forward. I had several other jobs to do as well such as moving coil packs, new HT leads, SC Power engine mounts, uprated fuel pump and bigger Astra VXR 470cc injectors.


Whilst waiting for the kit to arrive I had the wheels refurbished in smoked chrome and went with 16" fronts.
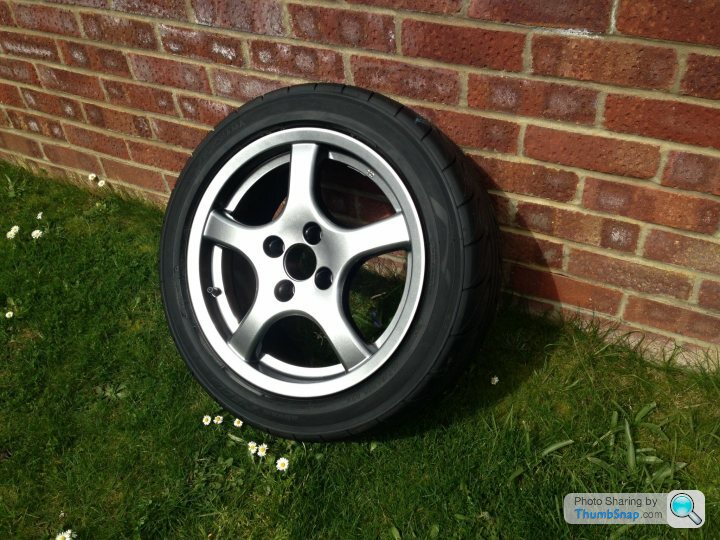

The 16" front allowed me to fit something I wanted to for a while, a bigger front disc. I was using sierra 283mm discs so I ordered a pair of MK1 Focus RS discs at 324mm. I was hoping to use them as is but the crossover pipe was a bit too close. I wanted 5mm clearance just in case the wheel changes shape via a pot hole.


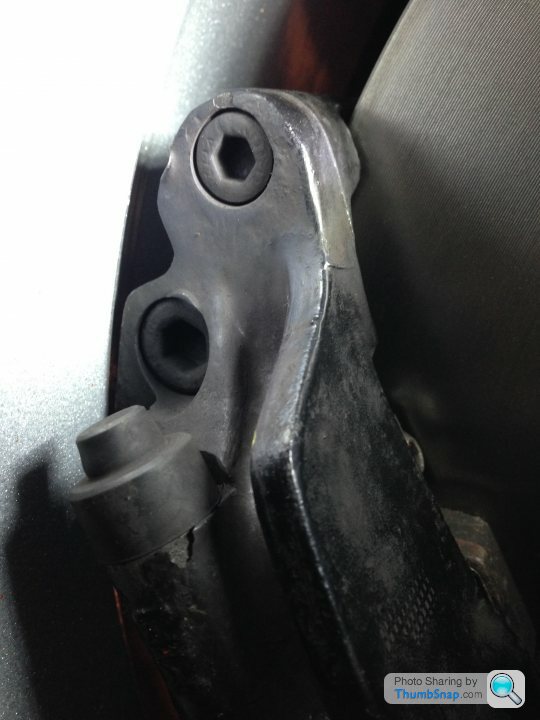

Towards the end of fitting the kit I was not happy with the throttle cable routing, I didn't like the 180deg bend it had to take so I started looking for alternatives. I found some P38 range rovers use a forward entry bracket and after a quick email to TVR Power they supplied a LHD throttle cable. Which greatly shortens the cable and removes the bend. The bracket works great and even uses the original bolts into the plenum. I definitely recommend this to any supercharger owners, the throttle pedal was so much lighter and quicker to return. It does need modifying to clear the bonnet. I cut the top off, re-drilled the hole for the cable and then made a small bracket to fit on the throttle spindle as the new lower position was causing the cable to touch the throttle spindle with the throttle closed. The picture below is before I modified the bracket. If anyone needs a LHD cable, I have one spare.


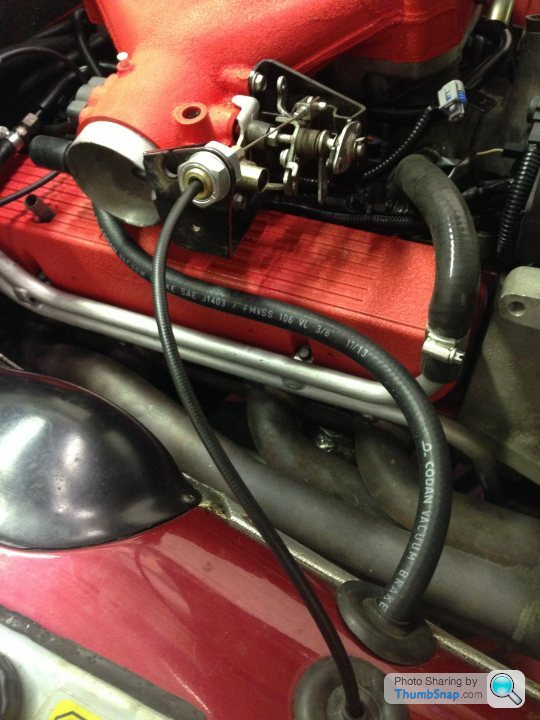
The first test drive went well, John was kind enough to share his ignition map with me so I had a good starting point I just needed to shape the VE table using the wideband.
Johns map uses Alpha N, so I changed my ECU to use Alpha N as I was previously using speed density. Whilst running in the supercharger I set the rev limit to 3K, once run I raised the rev limit 1K at a time to reduce the area of the map I was tuning. The first issue I had was belt slip, the supplied belt must have been for the larger pulley as at full load the belt stretched enough that the tensioner could sit on its stop providing no tension. A new belt worked great, I fitted the smallest I could as being a clock spring in the tensioner the shorter the belt the more tension.

The next problem to solve was no matter how much I back off the full boost cells at 5Krpm+ of the VE table the wideband would always show 10.0 AFR. I took loads of fuel out but no change. I suspected the fuel reg. I kept the standard one as I could control the fuelling I didn't need the Begi Rising Rate. Around 5K revs with 12psi+ the diaphragm was completely closing off the return and raising the rail pressure to pump pressure. I guess the standard item was never designed to deal with boost so it did pretty well considering. I didn't want a remote reg so I started hunting for a standard item to fit the rail that was fitted to a boosted engine as standard. I found Bosch 0280 160 258 which are fitted to Porsche 944 turbo. 3 bar reg
This bolted straight on to the rail and raise the static pressure to 3bar. I had to take a bit of fuel out of the whole map to account for the rise in static pressure but at full boost the fuelling was now spot on.
On with more tuning and I was now using a 6K rev limit, the next issue I found was the inlet temps were reaching 55deg regularly and it would knock intermittently. Max boost was 13psi at 6K. Heading out for a tuning session the inlet temp would start at 20deg, after some tuning and pulling into a layby to check the logs the inlet temp would be 45deg idling. Driving away cruising the inlet temp would not come back down, only rise to 55deg on boost and back to 40/45 deg. I suspected the aluminium pipework was picking up heat from the exhaust and not being able to get rid of it. The cold pipe passes the Y-piece with a 10mm gap and then runs parallel to the exhaust manifold. I cut the cold pipe and rotated the top piece, using a silicone joiner I could route the pipe around the Y-piece instead of over it. According to the logs this did help but rather than a drop in temp it now took longer for the heat soak to set in.

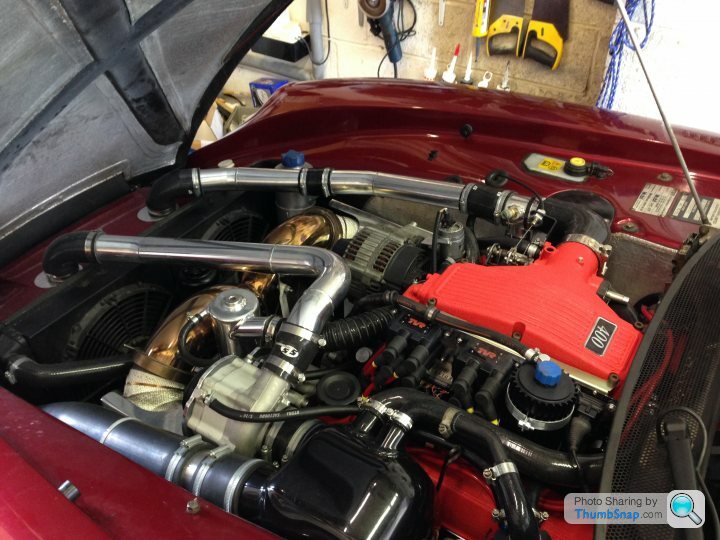
I also double checked the calculations for the speed of the supercharger. The crank pulley is 7" (177.8m) and the charger pulley is 85mm, 2.09 ratio. 2.09 X 6K rpm = 12,550rpm input speed! The C30-94 max input speed is 10,500rpm so over spinning the charger was most likely contributing to the excess heat. I reduced the rev limit down and only rev it to 5.5K now to keep the input speed within the +10% speed TTS recommend.
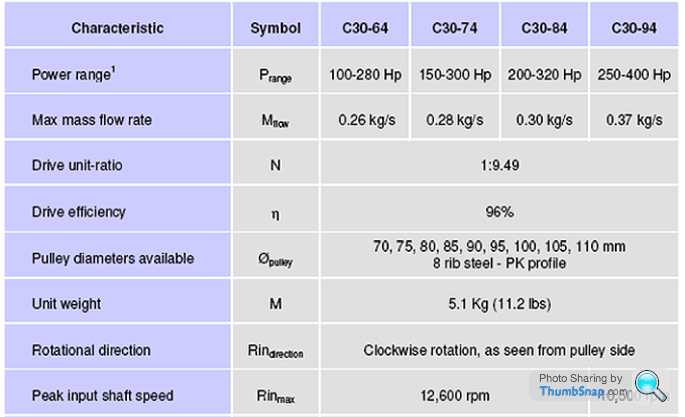
With Santa Pod coming up, this was not going to work well as the queue can be quite long so by the time I stage the inlet temp will be 45+ easily. I started looking into alternative pipework to stop the cold pipe running parallel to the exhaust manifold.

The plan was to move the alternator to the air con compressor position and move the throttle to the front like the Westfield’s use. Luckily I have mate who is handy with a Tig welder and is happy to be paid in beer. It took a couple of attempts and lots of measuring, eventually we ended up with near straight pipework from the intercooler to the throttle and a bigger gap to the Y piece. I was advised it wouldn't work well with the throttle at the front and the rear cylinders wouldn't get enough air. I thought this was rubbish as I used a GEMS plenum to get more volume and left the side chamber fairly big so there should be no shortage of air. I cut the trumpets right down, with the supercharger I wasn't fussed on losing any torque the trumpets provide. I cut them equally as per Jools blended base which I hope to use eventually.



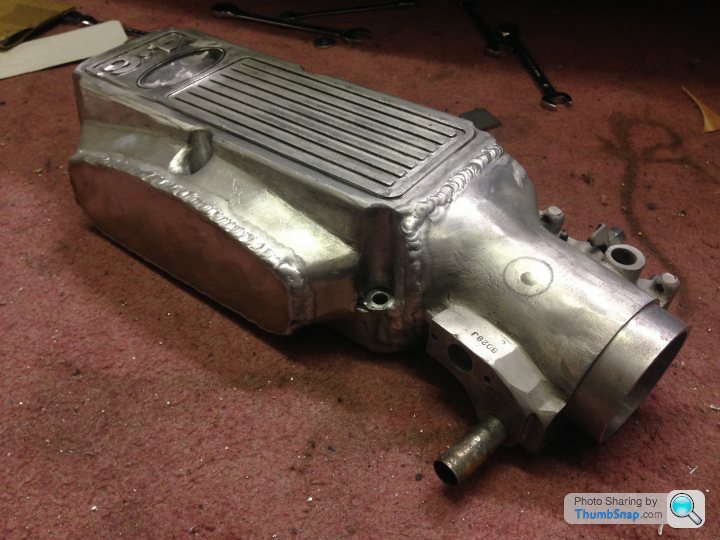
A new longer 2315mm belt, reverted back to the old throttle cable, add an inlet for the idle valve and amended the dump valve pipework and we're ready for another test.

The following tuning sessions showed much more promising results, the inlet temp were down about 5deg and took much longer to heat soak. Not a great as I had hoped for but happy for an improvement. Next was a small tweak to the hot pipe, it was really close to inlet temp sensor and cold pipe. I cut the curved end off the hot pipe and removed more material from the throttle bracket.



Next was some testing for Santa Pod, after a run through 1st to 4th the inlet temp peaked at 60deg. The ECU is set to start pulling timing at 54deg so most of 4th gear was done with 10deg ignition timing. It feels really flat when this happens and is definitely not good for power.
After a bit of research water injection seemed like a good option and with a supplier just down the road a progressive kit was ordered. It was easy to fit and worked really well the max temp was 40deg not matter how hard I tried! The pump lives in the boot with the gallon tank and there’s a progressive controller in the cabin. The controller needs a vacuum hose and brings the pump in at 15% duty cycle at the first pot setting then 100% at the second. I was using 3psi for 15% and 8psi for 100%. I ran the water line along the chassis and into driver’s foot well, behind the brake servo and out the throttle grommet. This saved me running the water line over the inlet manifold and picking up heat when not in use.

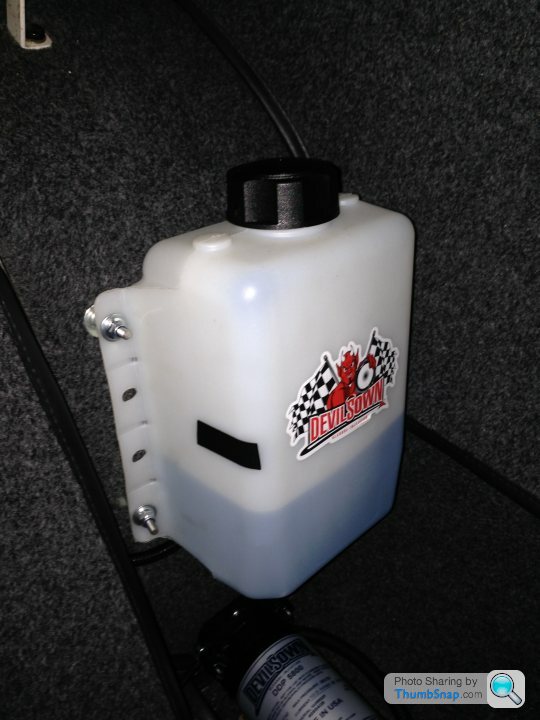
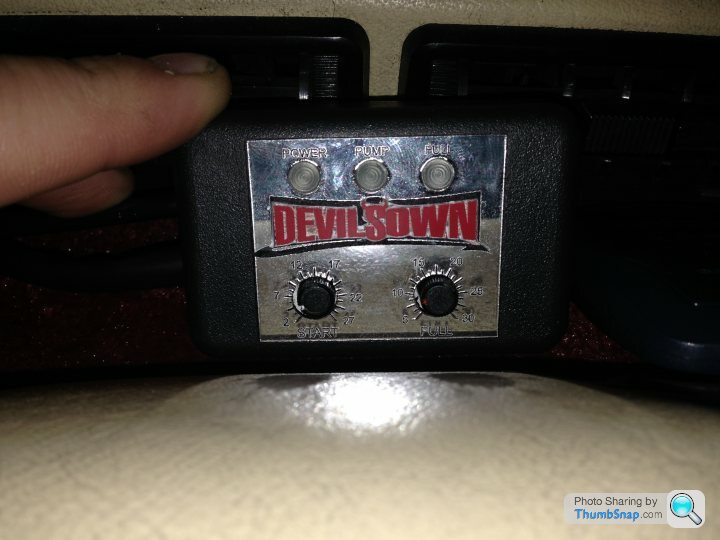
I was really happy with it now the intermittent knock stopped and the inlet temp are predictable. Just to help matters I wrapped the cold pipe in reflective tape and fibreglass cloth.
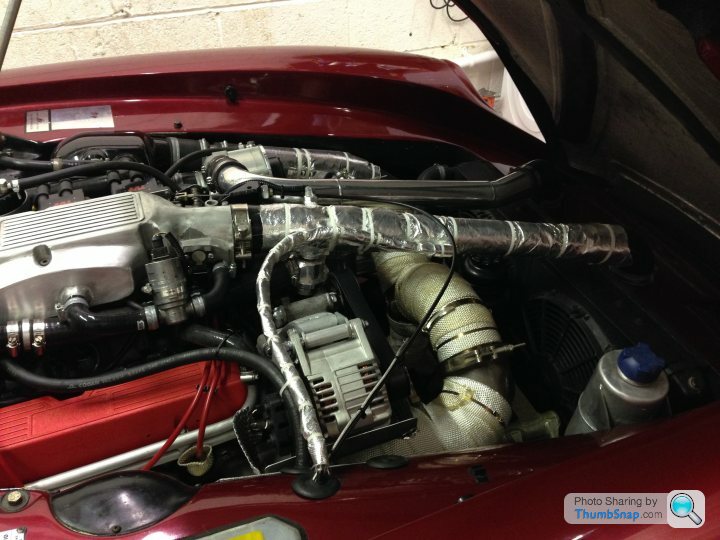
That night was pub club so a nice run out to West Meon and back. It went really well but when I had a quick glance over the engine in the garage there was a small puddle on the radiator dripping from the fibreglass cloth. My first thought was the water line was leaking but with the pump pressure at 200psi I thought it would be more noticeable. I peeled back the fibreglass wrap and found whole pipe covered in condensation so it must of been cold!

Before Santa Pod I checked the plugs to see if there is any truth in the cylinders getting different volumes of air. Below is the offside bank in order the rightmost being number 2 and I couldn't see any differences between them. They looked the same as the last time I checked them, nice and clean. I use 8s as recommend by SC Power. I also went up a water jet size from 252cc/min to 315cc/min. The meant the max air temp is 35deg and only rises into the 30s when ¾ boost.


After checking the logs from Santa Pod I found the temps were a bit chaotic and the GoPro video confirmed the pump was only running in some gears. My fastest run was done with the pump only working in 1st and 4th so a bit more to come hopefully. I’ve now removed the progressive controller, the ECU is going to control the pump. This means I’m going to lose the progressive start but hopefully a more reliable trigger for the pump. I can set what boost and inlet temp the pump should come in so I’m going to start with boost > 4psi and inlet temp > 28deg with a 10deg hysteresis on the inlet temp.
That'll do for now, next on the list is to get it on a rolling road and then start on the winter upgrades!
Edited by BoostedChim on Wednesday 24th September 21:15
BoostedChim said:
Cheers! I thought 7 was standard so 8 is only one grade colder to deal with the extra heat. What do you use in your turbo?
I was advised to use 6's by my mapper [I was using 8's] with my lower CR and told it would clean up the tickover. Mines a 4.6 and contrary to what is stamped on the block the CR is lower than the stamped 9.35:1 I tried it and amazed to find it works for me, and it seems many others on here. Not a problem since. Though the 4.0 may well be higher CR and I thought before reading that yours was a 4.6.Had a couple

Someone????
Edited by macdeb on Wednesday 24th September 21:46
Sardonicus said:
Why use Alpha N when running forced induction? far more aggressive way of managing spark & fuel IMO always confuses me this one, your missing out, take my hat off to all your work and your install though, just an observation not a critism.
It does work well and keeps things simple. It's really responsive as well. The downside is if you get a small amount of belt slip it suddenly runs rich, whereas speed density would adjust itself. I swapped back to speed density around the time of changing the plenum.macdeb said:
I was advised to use 6's by my mapper [I was using 8's] with my lower CR and told it would clean up the tickover. Mines a 4.6 and contrary to what is stamped on the block the CR is lower than the stamped 9.35:1 I tried it and amazed to find it works for me, and it seems many others on here. Not a problem since. Though the 4.0 may well be higher CR and I thought before reading that yours was a 4.6.
Had a couple
Someone????
Ah ok, that's interesting. I probably could get away with 7 or 6 as it's only on max boost for less than a second most of the time.Had a couple

Someone????
Edited by macdeb on Wednesday 24th September 21:46
FWIW, I've used BR8ECS on a NA basis for years (mainly because I needed a resistor plug and wanted to keep the stronger ECS ground electrode; there is no 'R' variant on a 7) - assuming you can keep the fuelling clean enough to avoid cold-fouling, I doubt you'll have any problems and the extra heat dissipation of the colder grade is an obvious bonus with FI. I have just installed a fresh set of the same 8s to commence duty with the new turbo... I will be starting with minimal boost and an existing (adapted) set-up however, so will hopefully avoid the worst of the fouling issues that can bedevil entirely new hardware across the board.
Just scored a new genuine 044 pump for beer money so that will be the first step in avoiding fuel headroom issues; be interesting to see when the Lucas injectors top out on their duty cycle (well within currently despite popular wisdom)
Just scored a new genuine 044 pump for beer money so that will be the first step in avoiding fuel headroom issues; be interesting to see when the Lucas injectors top out on their duty cycle (well within currently despite popular wisdom)
How did they get this one to fit ? It sits very low .
http://www.britishv8.org/articles/mgb-v8-superchar...
http://www.britishv8.org/mg/billjacobson.htm
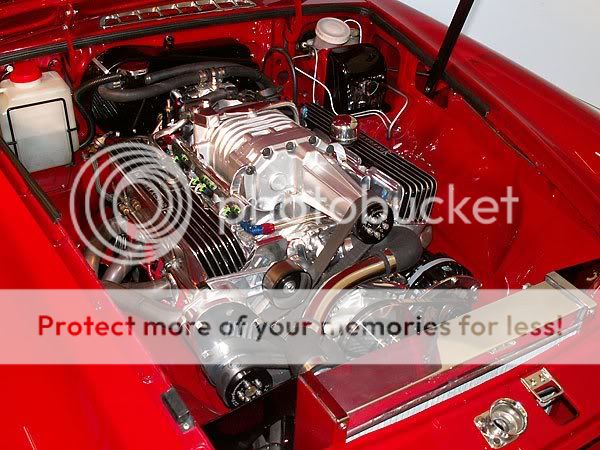
http://www.britishv8.org/articles/mgb-v8-superchar...
http://www.britishv8.org/mg/billjacobson.htm
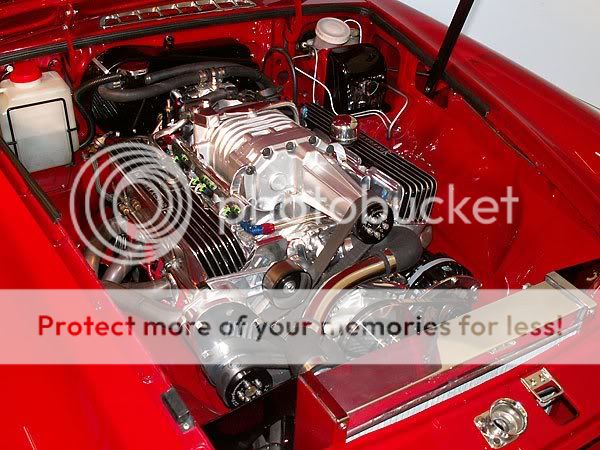
Edited by SILICONEKID345HP on Wednesday 24th September 22:39
Edited by SILICONEKID345HP on Wednesday 24th September 22:41
SILICONEKID345HP said:
I have seen that one before and wondered about asking my mate to weld me a manifold but I have a feeling that MG is not running a lot of boost so that design works ok.Engineer1949 said:
Brilliant post i am particularly impressed with the water injection great to see the car at santa pod defiantly more to come there
John
Its definitely worth looking in to if you get time between all your projects! I would pay a bit more next time and go with Aquamist, their controllers take a feed from one injector to correctly supply 10-15% water / fuel. I just over a quarter of my tank with a 280 mile round trip and runs up the strip. You would easily empty the tank on a track day!John
Gassing Station | Chimaera | Top of Page | What's New | My Stuff