Setting rocker preload
Discussion
Another solution and the one I'd recommend (at a cost) is use normal pushrods but mated with Yella Terra roller rockers - they have the adjustment in the rocker so don't need shims, avoid the risk of pads being shed and resulting valve damage, and if mated with decent shafts and outriggers will make a fairly bullet proof valve train well up to anything likely to confront a road car. Not cheap but the thing will be sorted.
Pupp said:
Another solution and the one I'd recommend (at a cost) is use normal pushrods but mated with Yella Terra roller rockers - they have the adjustment in the rocker so don't need shims, avoid the risk of pads being shed and resulting valve damage, and if mated with decent shafts and outriggers will make a fairly bullet proof valve train well up to anything likely to confront a road car. Not cheap but the thing will be sorted.

Sardonicus said:
macdeb said:
Sorry bloke but didn't receive. Steve's got it pretty covered though and depends on how exact you want it to be, I wanted all mine exactly the same as I'd gone to the measure of cc'ing my heads and deck heights of all pistons. Anorak I know. 
Not anorak at all mate 

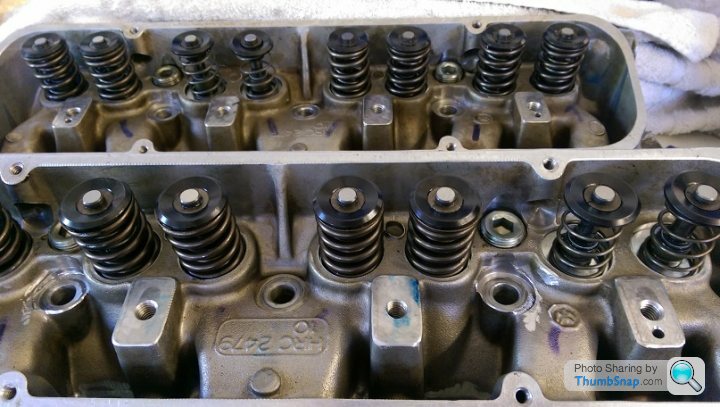
Edited by Sardonicus on Tuesday 18th October 11:05


[long time bloke, hope you ok]
Edited by macdeb on Tuesday 18th October 20:06
Sardonicus said:
ot anorak at all mate
when I had my seats cut for the bigger valves stems are at correct fitted height all machine shops should work to this standard IMO hence my rocker arm adjusters all sit equal and roller angle & tips sweep valve stems equal, you could run a straight edge over these in total confidence
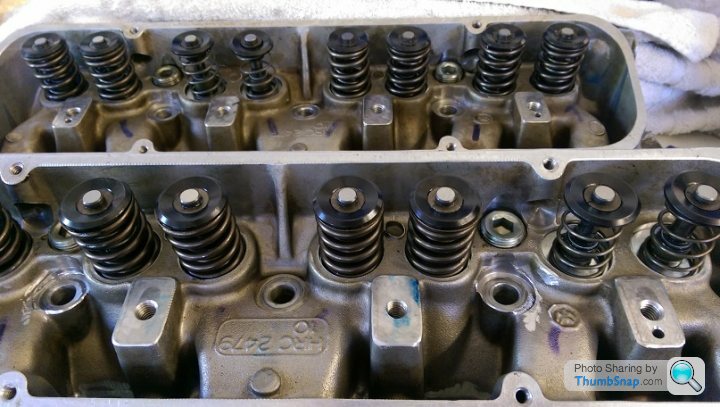
Nice valve springs on the far right pot at the bottom... you got a biro that no longer goes 'click'? 
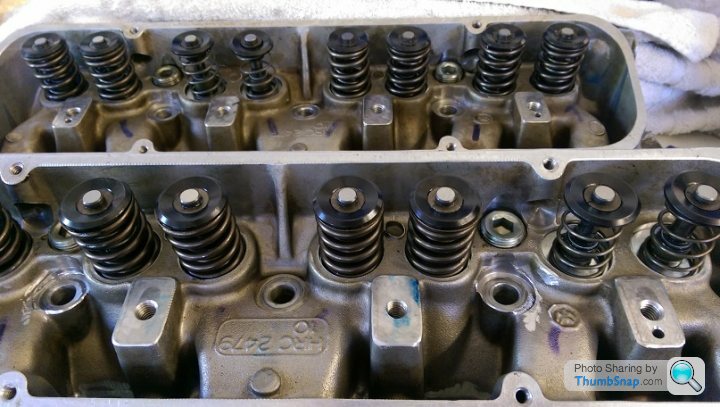
Edited by Sardonicus on Tuesday 18th October 11:05

carsy said:
With no1 in firing position,
Set Intakes, 2 & 7, and Exhausts, 4 & 8.
turn the engine 1/2 rotation,
Set Intakes, 1 & 8, and Exhausts, 3 & 6,
turn the engine 1/2 rotation,
Set Intakes, 3 & 4, and Exhausts, 5 & 7,
Turn the engine 1/2 rotation,
Set Intakes, 5 & 6, and Exhausts 1 & 2,
Carsy Set Intakes, 2 & 7, and Exhausts, 4 & 8.
turn the engine 1/2 rotation,
Set Intakes, 1 & 8, and Exhausts, 3 & 6,
turn the engine 1/2 rotation,
Set Intakes, 3 & 4, and Exhausts, 5 & 7,
Turn the engine 1/2 rotation,
Set Intakes, 5 & 6, and Exhausts 1 & 2,
Brilliant!!! Thank you.
Saves a lots of time and unnecessary turning the crank when you want to turn it the least, reminds me of the old rule of 9 used on the old Mini engines.
Steve_D said:
Thanks for the setting sequence Carsy that will speed thing up. There are some who say settings even up in the 100 thou range are still acceptable but I can't force myself past 60. Below 20 is a definite no-no. Steve
Steve_DSorry to fire up an old thread but as you can’t force yourself past 60 thou I’m interested in your thoughts, I totally agree with you regarding less than 20 thou.
In the past I’ve used Realsteels preload setting from their old diagram below that came with a set of pedestal shims more than a few years ago. Now I’ve more recently seen “V8 Developments” instructions suggesting up 100 thou is ok I’m starting to think maybe they have a valid point because you can push the inner piston down about 200 thou and the preload is a random point within the piston's travel.
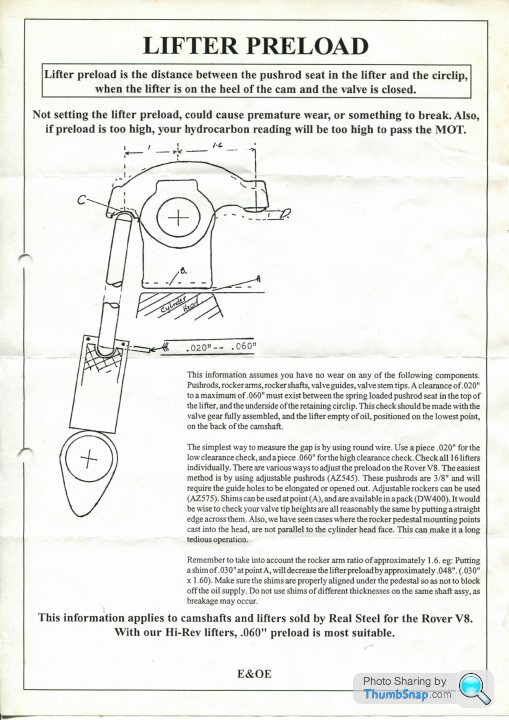
Should preloads be kept to a minimum so when lifters bleed down at high RPMs the inner piston doesn’t bottom out or do they bottom out anyway because they leak oil and isn’t enough time for them to refill at high RPMs? They also bleed down and may bottom out when left standing during the winter layup.
If bottoming out isn’t an issue the preload could be set to 100 thou so at high rpm they don’t bleed down so far?
Any thoughts welcome.
Steve
Why would they bleed down at high rpm? At higher rpm the oil pressure should be right up to the relief valve pressure so they should stay up. I'm also not sure how you would know if they were bleeding down.
Ref the preload I'm not convinced any lifters I have used will travel .2" though I have not measured it. I do know that some I've used would bottom out at .1".
Steve
Ref the preload I'm not convinced any lifters I have used will travel .2" though I have not measured it. I do know that some I've used would bottom out at .1".
Steve
Oh, and don't do as I did - choose a set of pedestal shims out of three supplied, based on your findings; put all the rockers together and tighten the bolts only to realise that the result won't be (measured preload - shim thickness) but rather (measured preload - (shim thickness x 1.6)) due to the rocker ratio.... 



Edited by 900T-R on Thursday 22 March 08:52
Regarding bleeding down.
I used to do track days with my old 4.6 engine chim. When I was pushing on, the engine became very hot and especially through chicanes with left and rights at high-speed, the lifters would bleed down and this was obvious through the tremendous rattling that occurred.
Oil pressure was still up so I would just back off the throttle for about four or five seconds, they would pressurise up and I would continue flat out.
Given the above circumstances it seems that it is a mixture of very hot oil and high G force.
This would happen a lot using Triple 8s on airfield days where the tarmac was very grlppy.
I understand what you're saying Steve but the fact is this has happened to me dozens of times.
Disappointingly, this happened once or twice with my old 5.5 engine but I believe that was at a time when it had a small oil cooler fitted and has never happened since I fitted a massive one and a larger baffled sump.
I used to do track days with my old 4.6 engine chim. When I was pushing on, the engine became very hot and especially through chicanes with left and rights at high-speed, the lifters would bleed down and this was obvious through the tremendous rattling that occurred.
Oil pressure was still up so I would just back off the throttle for about four or five seconds, they would pressurise up and I would continue flat out.
Given the above circumstances it seems that it is a mixture of very hot oil and high G force.
This would happen a lot using Triple 8s on airfield days where the tarmac was very grlppy.
I understand what you're saying Steve but the fact is this has happened to me dozens of times.
Disappointingly, this happened once or twice with my old 5.5 engine but I believe that was at a time when it had a small oil cooler fitted and has never happened since I fitted a massive one and a larger baffled sump.
^ I'd say that they 'didn't' bleed down during normal use but rather there was a fault and they were starved of oil.
As an aside I had a GpA big wing sump on my engine with a spring loaded oil pick up. It was a very fancy sump with spring loaded trap doors inside :-) All the oil was directed to a small square box around the pick up and the 4 trap doors opened or closed depending on which direction there was g force in action.
As an aside I had a GpA big wing sump on my engine with a spring loaded oil pick up. It was a very fancy sump with spring loaded trap doors inside :-) All the oil was directed to a small square box around the pick up and the 4 trap doors opened or closed depending on which direction there was g force in action.
Sardonicus said:
If anything lifters pump/jack up under high RPM use
bleed down at high RPM is usually oil surge not always recorded on the gauge (slow response) or excess oil temp
signs are diminishing oil pressure anyway
I agree with all of that. I always kept an eye on the gauge and it seemed to be okay but in my mind it was because the oil pick up was momentarily starved and with high grip tyres and high G forces I guess occasionally the pick up was very occasionally sucking air!

phazed said:
Sardonicus said:
If anything lifters pump/jack up under high RPM use
bleed down at high RPM is usually oil surge not always recorded on the gauge (slow response) or excess oil temp
signs are diminishing oil pressure anyway
I agree with all of that. I always kept an eye on the gauge and it seemed to be okay but in my mind it was because the oil pick up was momentarily starved and with high grip tyres and high G forces I guess occasionally the pick up was very occasionally sucking air!



Belle427 said:
Not ideal to shim I know it I’m going to run with it.
Nothing wrong with using pedestal shims and they are often used to make up the difference with skimmed heads. I ran an old 3.5 with Realsteel’s shims and 40 thou ish preloads that produced 190 bhp at the wheels for many years.Steve_D said:
Why would they bleed down at high rpm? At higher rpm the oil pressure should be right up to the relief valve pressure so they should stay up. I'm also not sure how you would know if they were bleeding down.
Ref the preload I'm not convinced any lifters I have used will travel .2" though I have not measured it. I do know that some I've used would bottom out at .1".
Steve
Kent Cam’s techies confirmed their lifters bleed down at higher revs than the spec of the cam and the exact bleed down point depends on the acceleration of the lifter which depends on the profile of the cam. Increased RPM increases the force on the lifter and therefore increases the oil leakage plus their is less time for the lifters to refill and eventually bleed down. In the good old days I use to consider lifters as a rpm limiter as they were known to bleed down and limit revs like Kent Cams confirmed. Ref the preload I'm not convinced any lifters I have used will travel .2" though I have not measured it. I do know that some I've used would bottom out at .1".
Steve
Kent Cam’s techie also said preloads should be kept to a minimum but no less than 20, and 40 thou allows for wear and changing clearance as an engine gets hot. Any larger will over pressurise the lifter as their is less oil to compress resulting in less cushioning effect which sounds good to me not bad, but they’re the experts.
My Kent lifter's pistons definitely push down more than 160 thou which I measured with two of your clever little wire gauges before reducing them down to 20 & 40 thou with a hammer and file.
When the lifter is on the cams base circle oil ways align and the upper chamber fills up taking up the slack in the valvetrain. As the cam rotates the lifter rises and the oil ways become out of alignment leaving the oil in the lifter trapped inside. We know that oil can't compress unless it's aerated.
So, how can a properly primed lifter bleed down? Even when it returns to the lower position gallery oil will want to enter it.
It will bleed down over time when the engines stationary hence a rattle on startup sometimes.
As for revs being limited by the lifters I think that's more about them pumping up and maybe leaving the valves slightly open. There's a discussion to be had here :-)
So, how can a properly primed lifter bleed down? Even when it returns to the lower position gallery oil will want to enter it.
It will bleed down over time when the engines stationary hence a rattle on startup sometimes.
As for revs being limited by the lifters I think that's more about them pumping up and maybe leaving the valves slightly open. There's a discussion to be had here :-)
^ Valve float can cause all sorts of nasty things to happen. Argh.
Here we go, this a good read:
http://www.enginebuildermag.com/2012/01/hydraulic-...
Here we go, this a good read:
http://www.enginebuildermag.com/2012/01/hydraulic-...
Edited by Boosted LS1 on Thursday 22 March 22:44
Boosted LS1 said:
^ Valve float can cause all sorts of nasty things to happen. Argh.
Here we go, this a good read:
http://www.enginebuildermag.com/2012/01/hydraulic-...
Perfect bedtime reading, thanksHere we go, this a good read:
http://www.enginebuildermag.com/2012/01/hydraulic-...
Steve
Gassing Station | Chimaera | Top of Page | What's New | My Stuff