here we go again
Discussion
Engineer1949 said:
daz cant realy give you a price as not done it yet problem with using this box on the rover is no bellhousings available so i am having to heavily modify the existing lt77 one will be starting that next week so watch this space but as to the job box is out flywheel and clutch off and have had the tko600 mocked up in place looks tight but doable i have ordered the centre shift kit and the new clutch and have machined the flywheel just the fixings to do today on the rotary table.
john
DSCN2397 by Brundall Motorsport, on Flickr
DSCN2398 by Brundall Motorsport, on Flickr
Great Machining there.john
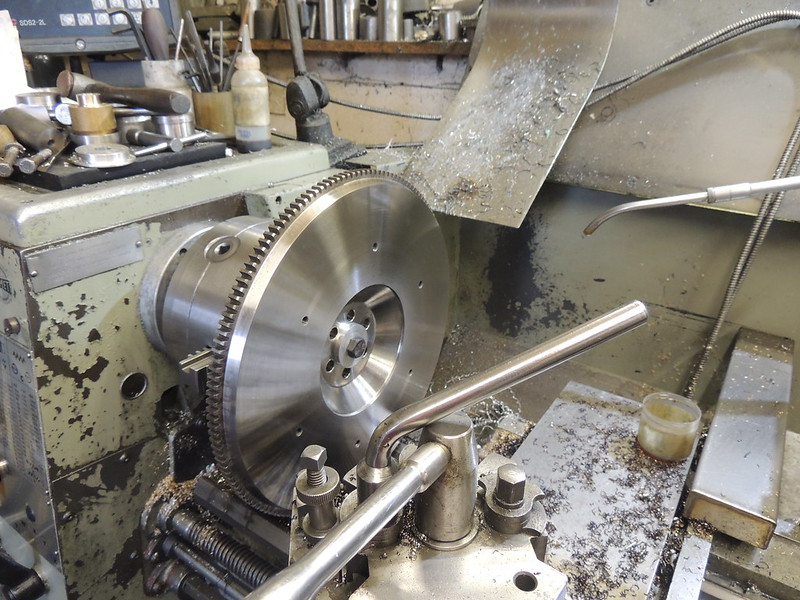
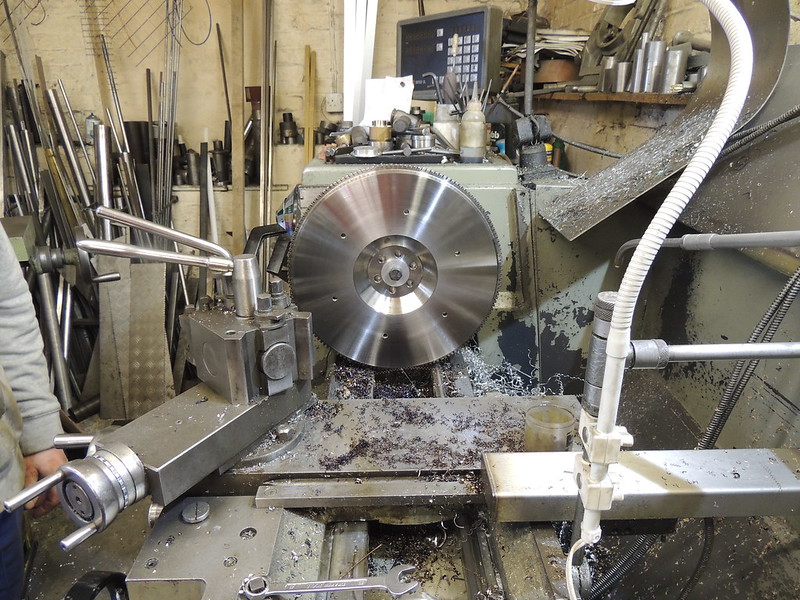
I know your a highly experienced Engineer John, but your house husbandry needs a fresh pair of eyes, especially on your head stock, as you have probably witnessed accidents from falling tools hitting a spinning chuck also.
started putting things together flywheel on and clutch but not before turning up a clutch centring tool for the mcloed clutch all looks good, then stripped off the shocks and started cleaning them and then removed the heavy weight springs from the nitrons and removed the standard springs from the original bilstiens and built the rears up with the standard springs and refitted them, the teflon liner also arrived for the mig so much welding today then skim the faces to make sure they are square.
john
DSCN2436 by Brundall Motorsport, on Flickr
DSCN2438 by Brundall Motorsport, on Flickr
DSCN2445 by Brundall Motorsport, on Flickr
DSCN2447 by Brundall Motorsport, on Flickr
DSCN2439 by Brundall Motorsport, on Flickr
DSCN2441 by Brundall Motorsport, on Flickr
DSCN2442 by Brundall Motorsport, on Flickr
DSCN2443 by Brundall Motorsport, on Flickr
DSCN2444 by Brundall Motorsport, on Flickr
john









well all went well today got the bellhousing all lined up and tacked it to the mounting plate then fully welded the two together, after it was properly cooled i mounted it on the mill table to skim the plate where it meets the gearbox to assure a level mating surface it had warped about 15thou after welding so with that done i mounted it all on the gearbox and refitted the register plate to be sure everything was spot on, then fitted the bellhousing to the engine to get the measurements for the fitting of the centre push release bearing.
john
DSCN2448 by Brundall Motorsport, on Flickr
DSCN2449 by Brundall Motorsport, on Flickr
DSCN2450 by Brundall Motorsport, on Flickr
DSCN2451 by Brundall Motorsport, on Flickr
DSCN2452 by Brundall Motorsport, on Flickr
DSCN2453 by Brundall Motorsport, on Flickr
DSCN2454 by Brundall Motorsport, on Flickr
DSCN2456 by Brundall Motorsport, on Flickr
DSCN2457 by Brundall Motorsport, on Flickr
DSCN2458 by Brundall Motorsport, on Flickr
DSCN2459 by Brundall Motorsport, on Flickr
john











back in the workshop had a great break but glad to be back, got the remaining shocks sorted with the standard springs and refitted then stripped the tko 600 and fitted the centre stick conversion all went well apart from having to turn up a drift for the roll pins securing the selectors.
john
DSCN2471 by Brundall Motorsport, on Flickr
DSCN2472 by Brundall Motorsport, on Flickr
DSCN2473 by Brundall Motorsport, on Flickr
DSCN2474 by Brundall Motorsport, on Flickr
DSCN2475 by Brundall Motorsport, on Flickr
DSCN2476 by Brundall Motorsport, on Flickr
DSCN2477 by Brundall Motorsport, on Flickr
DSCN2478 by Brundall Motorsport, on Flickr
john








Damn we just nearly gave away a nice gizmo that would have been perfect for doing those PCD's. Call a Tbow (spelleing?) head and it has two columns that hold a arm with vernier scale in imperail 0.005" graduations if I recall correct and a drill bush holder at each end. Has degree scale around the 8" chuck base plus a ratchet that can index up to 48 holes on the ratchet lever. Could mount on it's back to do the PCD's of horizontal for milling etc. Heafty old bit of kit.
We just had to clear out Dads old workshop due to the upcoming move. No one wanted the old manual machines. In 1982 the Tbow head in metric was £1200 +VAT. I booked the new one in as was doing holiday cover in tools stores.
We just had to clear out Dads old workshop due to the upcoming move. No one wanted the old manual machines. In 1982 the Tbow head in metric was £1200 +VAT. I booked the new one in as was doing holiday cover in tools stores.
Engineer1949 said:
you say you nearly gave it away does this mean it is still available
john
The workshop has been cleared however the brother who did it may be willing to let his tool go as they certainly do not kow how to use it so will ask them. We tried advertising stuff but it became a real pain. Some one wnated the old 18" shaper but wanted to pay £60 and expected us to pallet it up and send it to Scotland for that. The boys had:-john
Holbrook lathe with taper turnign slide
Victoria U2 but no vertical head
pallas universal mill (small)
Pacra bench drill
Small vertical surface grinder with two mag chuck plates
Cylindrical grinder
Ward 2 capstan
Tool and cutter grinder
Westinhouse 3 phase converter
Dividing head
10" manual rotary table
Marlco head (collet chuck)
all the taper shank drill numerous chucks for the machines
metal stock
Milling cutters etc
As we are moving and have to leave vacant possesion it had to all go. We did manage over the last year to sell the Student gap bed lathe, Raglan 5" lathe and 2 Myford 7's and the old Rapido saw.
Gassing Station | Chimaera | Top of Page | What's New | My Stuff