Bloodhound LSR Thread As Requested...
Discussion
mcdjl said:
AER said:
mcdjl said:
It's a material specification grade for aluminium. It looks like a rather large lump of metal, approximately a cuboid just a bit bigger than the finished thing. And yes I'm guessing that 90% will have been machined away...thats aircraft levels of loss!
to be honest, it doesn't take very long neither does it cost very much especially relative to the cost of the programming and machining time, the vast majority of which is in the finishing operations.In my opinion, the only realistic additive manufacturing method for volume production is already here in the form of fibre reinforced composites. 3D printing is for prototyping and for those with no skills and machinery to make things in a better way.
Storer said:
I know you plan to do 1000mph in a straight line but some form of steering must be required to keep it straight.
What, where and how?
I assume it is a one-off design but is it power assisted, British built and is it connected mechanically to the steering wheel or "fly by wire(or hydraulic hose)"?
Paul
Std rack & pinion, steel steering colum, couple of UJ's. About 5deg of wheel movement is all that's required.What, where and how?
I assume it is a one-off design but is it power assisted, British built and is it connected mechanically to the steering wheel or "fly by wire(or hydraulic hose)"?
Paul
Has an EPAS system installed should we require it, but we doubt we will, so if proven true it'll be ditched in the second year.
Excuse the crappy CAD image, but the system hasn't been assembled yet.
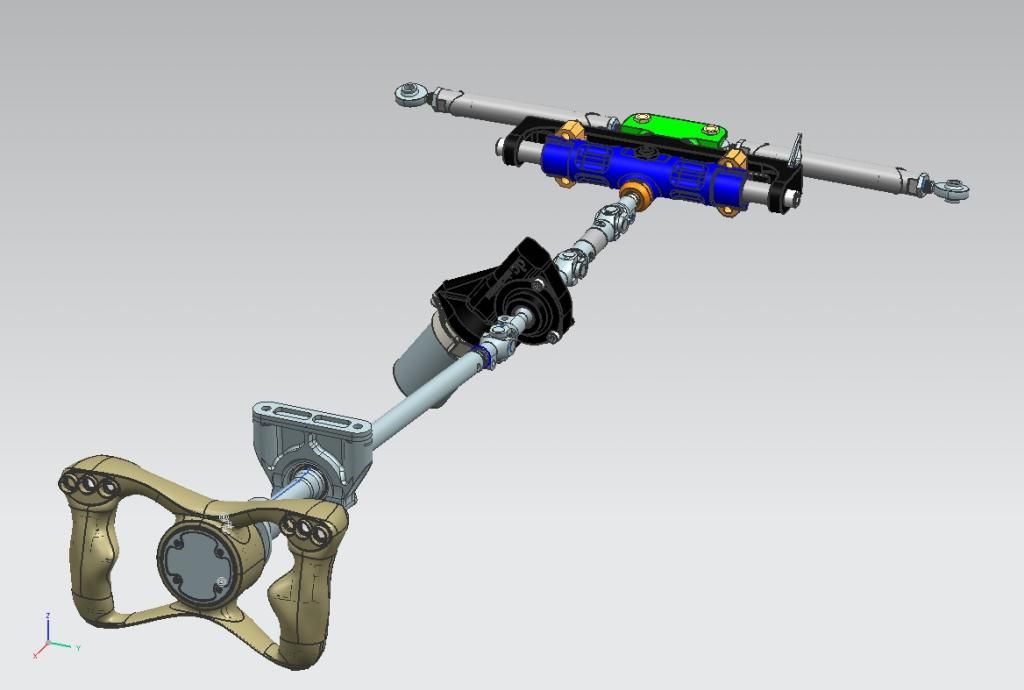
Storer said:
There was me expecting a high tech approach but instead it is a tried and tested one! One less thing to give trouble though.
One question.
What is the reasoning behind the steering rods not being directly connected to the ends of the rack?
Paul
Only way to get geometry that would give zero bump steer.One question.
What is the reasoning behind the steering rods not being directly connected to the ends of the rack?
Paul
IN51GHT said:
About 5deg of wheel movement is all that's required.
Lets hope so:dab_of_oppo_at_700mph
;-)
ETA. Not clear if you meant handwheel angle or roadwheel angle btw
Edited by anonymous-user on Tuesday 25th November 12:39
IN51GHT said:
Really rather please with how this part came out.
It's the front bulkhead, the nose cone attaches to it on one side, the wheel arches & under belly panel on the other.
Machined from 7075 T6 billet, then vapor blasting to give a matte finish to enable the inspection scanner to it's stuff.
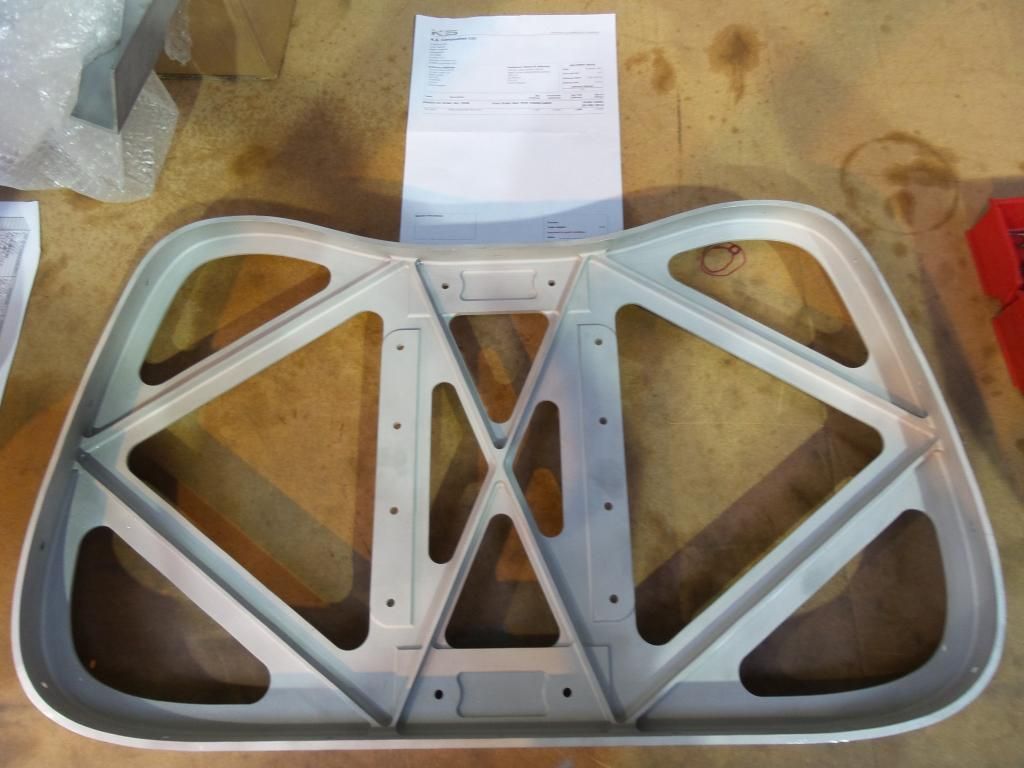
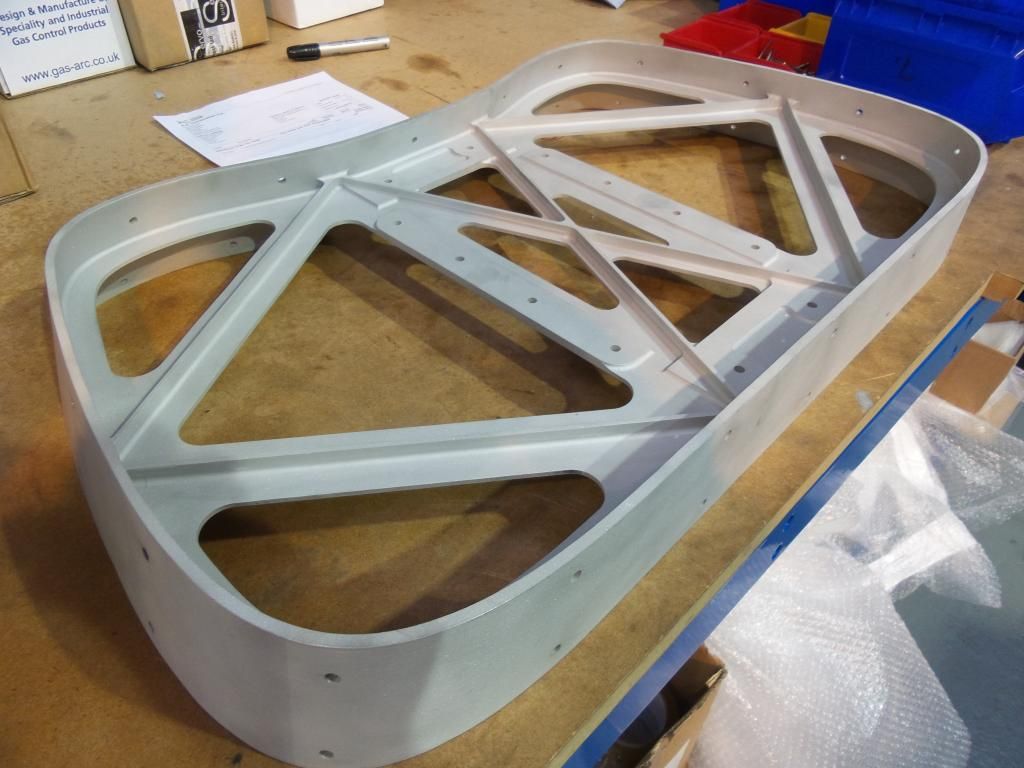
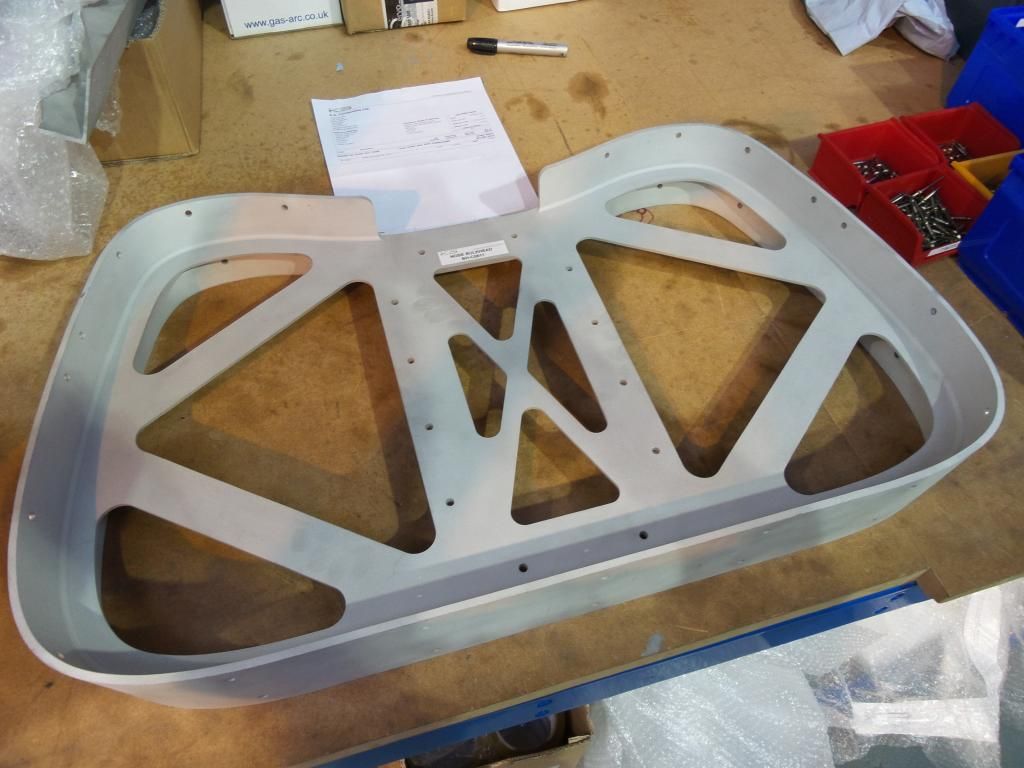
Lovely bits of course.It's the front bulkhead, the nose cone attaches to it on one side, the wheel arches & under belly panel on the other.
Machined from 7075 T6 billet, then vapor blasting to give a matte finish to enable the inspection scanner to it's stuff.
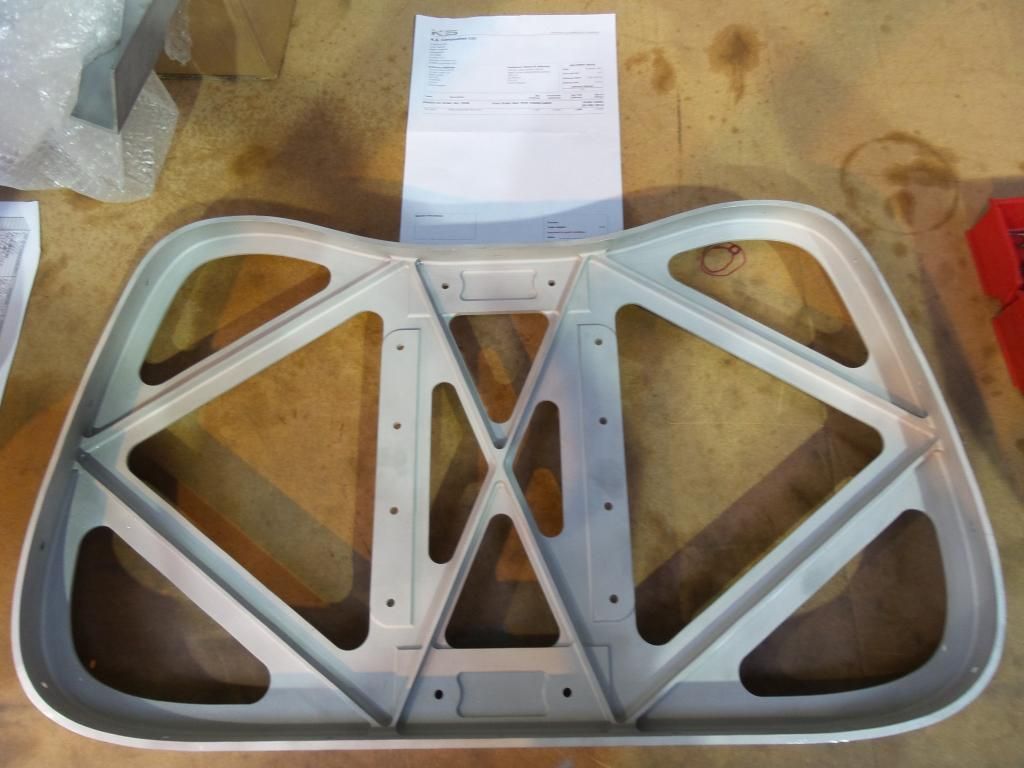
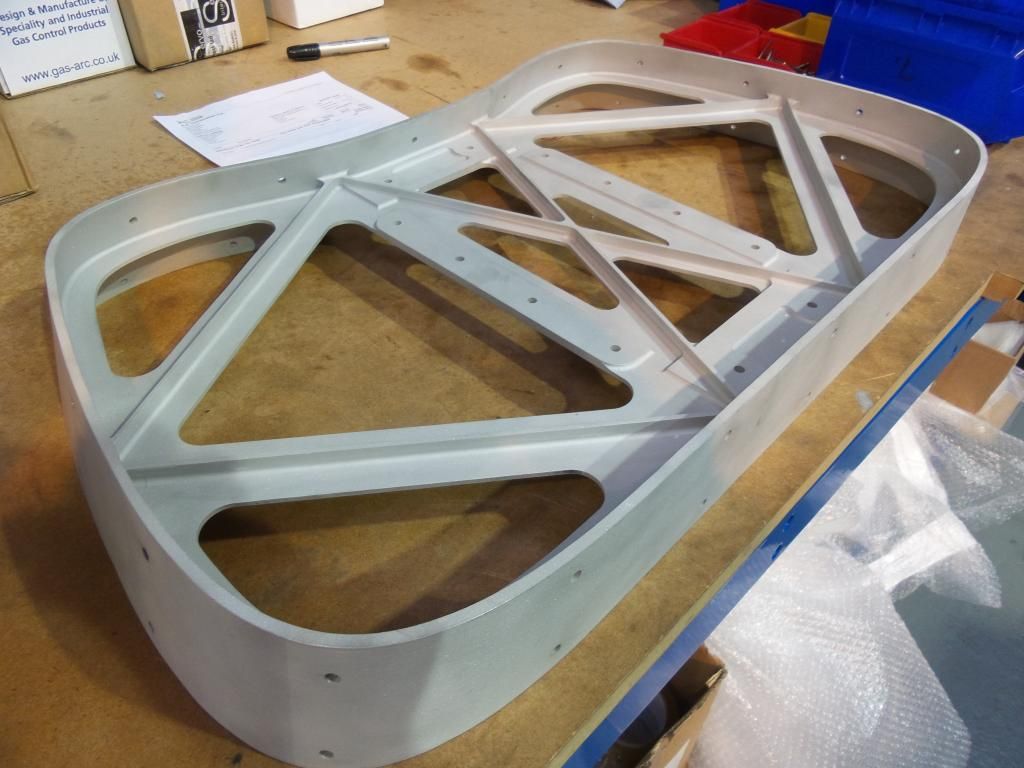
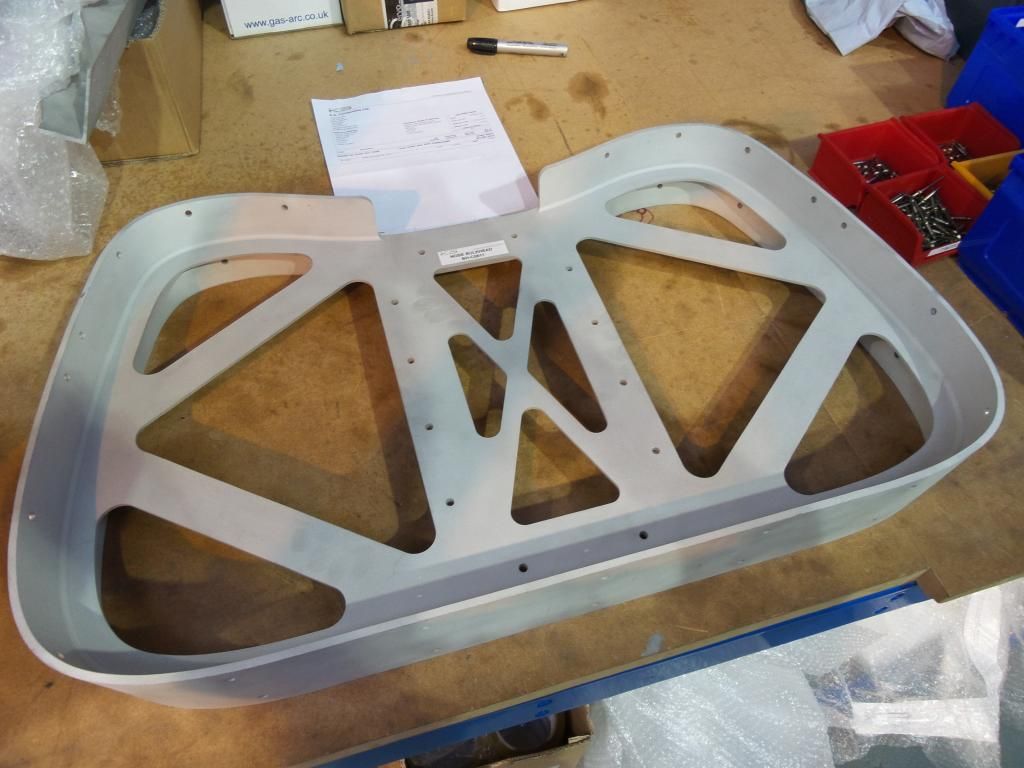
Edited by IN51GHT on Friday 21st November 16:01
But have you explored alternative production methods? How about lost wax castings, and then HIP (Hot Isostatic Pressurisation). Bumps the material properties upto near forging values. Used it on a dunking sonar body many years ago. Also, CNC bits, electron beam or laser welded. A great way to make hollow (light but strong components). Used this to salavge the forged bodies on MK44 torpedoes. Cut of the joint section. Electron beam welded on a new ring. Machined back to original dimensions. Success.
JordanTurbo said:
This update is for IN51GHT as he left before we did it. (excuse the poor mobile phone picture)
Completed upper chassis got lifted and weighed this evening, before going to the oven next Monday.

The exact weight is a secret for now
I'm going to hazard an educated guess at around 265-270kgCompleted upper chassis got lifted and weighed this evening, before going to the oven next Monday.

The exact weight is a secret for now

Edited by JordanTurbo on Tuesday 25th November 21:20
IN51GHT said:
JordanTurbo said:
This update is for IN51GHT as he left before we did it. (excuse the poor mobile phone picture)
Completed upper chassis got lifted and weighed this evening, before going to the oven next Monday.

The exact weight is a secret for now
I'm going to hazard an educated guess at around 265-270kgCompleted upper chassis got lifted and weighed this evening, before going to the oven next Monday.

The exact weight is a secret for now

Edited by JordanTurbo on Tuesday 25th November 21:20
Can I have a job please?

IN51GHT said:
JordanTurbo said:
This update is for IN51GHT as he left before we did it. (excuse the poor mobile phone picture)
Completed upper chassis got lifted and weighed this evening, before going to the oven next Monday.

The exact weight is a secret for now
I'm going to hazard an educated guess at around 265-270kgCompleted upper chassis got lifted and weighed this evening, before going to the oven next Monday.

The exact weight is a secret for now

Edited by JordanTurbo on Tuesday 25th November 21:20
IN51GHT said:
IN51GHT said:
JordanTurbo said:
This update is for IN51GHT as he left before we did it. (excuse the poor mobile phone picture)
Completed upper chassis got lifted and weighed this evening, before going to the oven next Monday.

The exact weight is a secret for now
I'm going to hazard an educated guess at around 265-270kgCompleted upper chassis got lifted and weighed this evening, before going to the oven next Monday.

The exact weight is a secret for now

Edited by JordanTurbo on Tuesday 25th November 21:20
JordanTurbo said:
We've put Mark (IN51GHT) out of his misery now. 
Upper chassis weighs 288kg. Awesome considering the design target was <400kg!

Since its so much under target will you have to ballast up to get the balance right? Reason for thinking this is that most of the power is being used to push air out of the way, not the mass of the car.
Upper chassis weighs 288kg. Awesome considering the design target was <400kg!

Gassing Station | General Gassing | Top of Page | What's New | My Stuff