Piston ring groove depths ?
Discussion
Any do's or dont's here ?
The current pistons seem to have fairly shallow grooves compared to other pistons Ive used. I've a new/old set of rings I bought a few years ago and didnt use for other pistons. Same bore size, same height of ring etc.
But the ring depths are different. ( Totalseal Gapless top )
Approx...top ring measures about 3.9mm deep, groove is about 4mm deep.
Second ring is about 4.15mm deep, groove is about 4.35mm deep.
Rings that were supplied with the pistons were about 3.65mm and 4mm deep respectively ( again from memory would need to measure and write down exact )
Older pistons I've had, never measured groove depth until now, some are as big as 5mm deep. When buying rings, groove depth is something I've actually never been asked for.
And no, piston supplier is a ballbag and has stolen my money so despite having paid for new rings via him...seems they arent coming.
And the piston maker Diamond....seems they havent a clue what emails are, as they seem incapable of responding.
Obviously the ring should never be fully recessed into the groove...but how much back clearance should there be ?
The current pistons seem to have fairly shallow grooves compared to other pistons Ive used. I've a new/old set of rings I bought a few years ago and didnt use for other pistons. Same bore size, same height of ring etc.
But the ring depths are different. ( Totalseal Gapless top )
Approx...top ring measures about 3.9mm deep, groove is about 4mm deep.
Second ring is about 4.15mm deep, groove is about 4.35mm deep.
Rings that were supplied with the pistons were about 3.65mm and 4mm deep respectively ( again from memory would need to measure and write down exact )
Older pistons I've had, never measured groove depth until now, some are as big as 5mm deep. When buying rings, groove depth is something I've actually never been asked for.
And no, piston supplier is a ballbag and has stolen my money so despite having paid for new rings via him...seems they arent coming.
And the piston maker Diamond....seems they havent a clue what emails are, as they seem incapable of responding.
Obviously the ring should never be fully recessed into the groove...but how much back clearance should there be ?
I was struggling to get some oil ring support rails for some Diamond V8 pistons, in the end I sourced them from
http://www.performanceunlimited.co.uk/ who were most helpful.
I hope this helps as I guess it is best to run the designated ring pack.
Peter
http://www.performanceunlimited.co.uk/ who were most helpful.
I hope this helps as I guess it is best to run the designated ring pack.
Peter
PeterBurgess said:
I was struggling to get some oil ring support rails for some Diamond V8 pistons, in the end I sourced them from
http://www.performanceunlimited.co.uk/ who were most helpful.
I hope this helps as I guess it is best to run the designated ring pack.
Peter
I have plenty of support rails, and any rings I've bought in UK have always been from Dave, including the ones I wish to use now.http://www.performanceunlimited.co.uk/ who were most helpful.
I hope this helps as I guess it is best to run the designated ring pack.
Peter
Just the groove depth seems very shallow. Diamond have finally replied so hopefully they can give me a definitive answer.
Pumaracing said:
This is going to be fun. I'm dying to see how much they know before I give a full analysis of this issue. You have email btw.
no email received as yet.The only issue as such...is the original parts supplier being an asshole and stealing my money
The rings Diamond supplied obviously fitted, I now wish to use some rings I bought a few years ago for different pistons but never used as plans changed.
But they are same 1.5, 1.5, 3mm ( plus oil support ) and for same bore size.
But measuring various pistons I've had and used over the years, ring depths seem to vary massively.
Very interested to know why ! and what is better or what cannot be done.
stevieturbo said:
no email received as yet.
Hmmmm. Nor do I have the copy in my own inbox despite sending it an hour or so ago. Someone here is probably checking the content before forwarding it on 
Fascinating question though. To answer it fully requires consideration of piston ring operation fundamentals, thermal expansion, gas transfer and interstitial crevice pressures, temperature gradients in pistons, bores and rings themselves. Anyone else going to have a proper go at it before I chip in?
Sod it then. I'll have a lash.
The first thing to understand is how piston rings work. It's not just the radial tension of the ring itself that seals it against the bore. Combustion chamber pressure passes through the vertical gap between ring and groove, gets behind the back of the ring and forces it out against the bore. This is taken to its extreme with gas ported pistons whereby small holes are drilled through the crown into the back of the top ring groove although how much benefit this gives is debatable.
On a conventional piston the only flow path is the vertical groove gap and this should be less than 2 thou on a new piston. It should therefore be apparent that the gap behind the ring doesn't need to be much bigger than this to provide an adequate flow path for gas pressure to pass from the chamber, behind the top ring and then on downwards to the second ring in a steady blow-by process.
However what we are really concerned about is dimensions at operating temperature. We've seen in a previous thread how the piston top land diameter is on average 0.6mm or more smaller than the bore size to allow for piston thermal expansion. Let's say we have a 100 mm engine bore with a 99 mm top land on the piston, a top ring with a 4 mm radial depth and a ring groove also exactly 4 mm deep. When the piston is fitted to the bore at ambient temperature there will be a 0.5mm gap all round the top land and also a 0.5mm gap behind the piston ring. As the piston heats up it will expand. The top land will get closer to the cylinder bore and the gap behind the ring will similarly decrease.
How do we factor all this in? We need to know operating temperatures. I covered some of this in a recent thread. Bores tend to stabilise at a bit above coolant temperature, say about 100 C and piston crowns can be 300 - 350 C on a petrol race engine, maybe even a bit more on diesels and extreme duty engines. What of the rings themselves?
The top ring picks up its heat from the piston crown and transmits it both to the underside of the groove and to the bore. It should be apparent that the ring ought to stay at a lower temperature than the crown. We can get a good first approximation of temperature from the ring gaps normally used. The ring temperature can't exceed that which would expand it so much the gap closes up.
4 thou per inch of bore is a decent gap for a road or even competition petrol engine. Let's say a 90mm bore and a 15 thou ring gap at ambient. If we assume a similar coefficient of thermal expansion of 12 x 10^6 per degree C for both ring and bore, 100 C for the bore at operating temp we can calculate how the ring gap changes as the ring heats up.
Ring temp.....Gap
100 C.........15 thou (still the same temp for both ring and bore)
150 C......... 8 thou
200 C......... 2 thou
250 C......... -5 thou
If top ring temperatures even went above 200 C in a 350 C piston crown we can see things are heading for trouble. In actual fact the link I provided above shows temps of only about 100 to 135 C.
A ring with a radial depth of 4 mm and a CTE of 12 will expand that dimension by only a quarter of a thou at 150 C. It's inconsequential. The depth of the ring groove itself in aluminium with a CTE of about twice that of the ring and reaching a temperature of 350 C will expand by 1 thou. Similarly inconsequential but ALWAYS a slightly bigger amount than the expansion of the ring itself.
So if the ring has ANY clearance behind it in the groove at ambient it will never have less at operating temp. In addition there will also be the extra radial clearance behind the ring that the land itself has from the engine bore which will be quite a few thou even at WOT unless the designer has messed up and as I showed previously these land clearances tend to be very much on the safe side.
However, there's a caveat. The tool which machined the ring groove will have some sort of a corner radius however small that may be. The ring itself will probably be almost sharp edged on the inside. The ring will never bottom out quite on the base of the groove but on the corner radii. So the first thing to check is to fit a top ring, push it against the piston in one place and see if it actually sits at least flush or even a bit underneath the top of the groove.
If so you're as safe as houses. You don't need any additional clearance because there'll always be a bit of a gap between land and bore wall and hence also behind the ring, unless the piston is seizing and then rings are the least of your worries.
If the vernier caliper measurements show the groove as being a bit deeper than the ring but the ring still bottoms out on the groove radii and sticks out a tad then a desperate man wanting to avoid the cost of new rings could take a small oilstone and chamfer the inside edges of the rings a bit to compensate.
The first thing to understand is how piston rings work. It's not just the radial tension of the ring itself that seals it against the bore. Combustion chamber pressure passes through the vertical gap between ring and groove, gets behind the back of the ring and forces it out against the bore. This is taken to its extreme with gas ported pistons whereby small holes are drilled through the crown into the back of the top ring groove although how much benefit this gives is debatable.
On a conventional piston the only flow path is the vertical groove gap and this should be less than 2 thou on a new piston. It should therefore be apparent that the gap behind the ring doesn't need to be much bigger than this to provide an adequate flow path for gas pressure to pass from the chamber, behind the top ring and then on downwards to the second ring in a steady blow-by process.
However what we are really concerned about is dimensions at operating temperature. We've seen in a previous thread how the piston top land diameter is on average 0.6mm or more smaller than the bore size to allow for piston thermal expansion. Let's say we have a 100 mm engine bore with a 99 mm top land on the piston, a top ring with a 4 mm radial depth and a ring groove also exactly 4 mm deep. When the piston is fitted to the bore at ambient temperature there will be a 0.5mm gap all round the top land and also a 0.5mm gap behind the piston ring. As the piston heats up it will expand. The top land will get closer to the cylinder bore and the gap behind the ring will similarly decrease.
How do we factor all this in? We need to know operating temperatures. I covered some of this in a recent thread. Bores tend to stabilise at a bit above coolant temperature, say about 100 C and piston crowns can be 300 - 350 C on a petrol race engine, maybe even a bit more on diesels and extreme duty engines. What of the rings themselves?
The top ring picks up its heat from the piston crown and transmits it both to the underside of the groove and to the bore. It should be apparent that the ring ought to stay at a lower temperature than the crown. We can get a good first approximation of temperature from the ring gaps normally used. The ring temperature can't exceed that which would expand it so much the gap closes up.
4 thou per inch of bore is a decent gap for a road or even competition petrol engine. Let's say a 90mm bore and a 15 thou ring gap at ambient. If we assume a similar coefficient of thermal expansion of 12 x 10^6 per degree C for both ring and bore, 100 C for the bore at operating temp we can calculate how the ring gap changes as the ring heats up.
Ring temp.....Gap
100 C.........15 thou (still the same temp for both ring and bore)
150 C......... 8 thou
200 C......... 2 thou
250 C......... -5 thou
If top ring temperatures even went above 200 C in a 350 C piston crown we can see things are heading for trouble. In actual fact the link I provided above shows temps of only about 100 to 135 C.
A ring with a radial depth of 4 mm and a CTE of 12 will expand that dimension by only a quarter of a thou at 150 C. It's inconsequential. The depth of the ring groove itself in aluminium with a CTE of about twice that of the ring and reaching a temperature of 350 C will expand by 1 thou. Similarly inconsequential but ALWAYS a slightly bigger amount than the expansion of the ring itself.
So if the ring has ANY clearance behind it in the groove at ambient it will never have less at operating temp. In addition there will also be the extra radial clearance behind the ring that the land itself has from the engine bore which will be quite a few thou even at WOT unless the designer has messed up and as I showed previously these land clearances tend to be very much on the safe side.
However, there's a caveat. The tool which machined the ring groove will have some sort of a corner radius however small that may be. The ring itself will probably be almost sharp edged on the inside. The ring will never bottom out quite on the base of the groove but on the corner radii. So the first thing to check is to fit a top ring, push it against the piston in one place and see if it actually sits at least flush or even a bit underneath the top of the groove.
If so you're as safe as houses. You don't need any additional clearance because there'll always be a bit of a gap between land and bore wall and hence also behind the ring, unless the piston is seizing and then rings are the least of your worries.

If the vernier caliper measurements show the groove as being a bit deeper than the ring but the ring still bottoms out on the groove radii and sticks out a tad then a desperate man wanting to avoid the cost of new rings could take a small oilstone and chamfer the inside edges of the rings a bit to compensate.
stevieturbo said:
When you refer to a vertical groove gap on a piston....what are you referring to ?
Also I hear you about there needing almost no back clearance...but should there be any allowance for a carbon buildup behind the ring, which is bound to happen over time ?
The vertical clearance of the ring in its groove.Also I hear you about there needing almost no back clearance...but should there be any allowance for a carbon buildup behind the ring, which is bound to happen over time ?
A modern engine on quality oil should get very little carbon buildup and anyway it can only build up where there's excess room to do so.
Pumaracing said:
I'd be interested to know the nominal bore size and the piston top land diameter. Also the aluminium alloy if you know it. 4032, 2618 etc.
Would need to measure piston for ring land diameter, but here are stats supplied.Diamond have also said that the rings I have here would be fine to use.
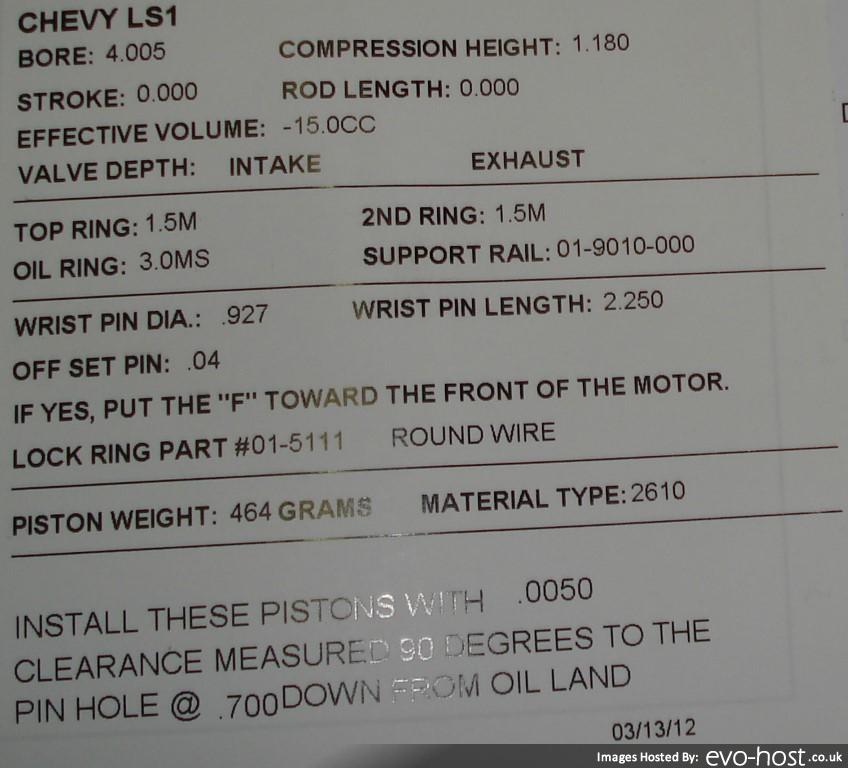
stevieturbo said:
Would need to measure piston for ring land diameter,
If you wouldn't mind.stevieturbo said:
but here are stats supplied.
Diamond have also said that the rings I have here would be fine to use.
I expected them to cop out with "if it isn't our stuff we can't recommend it". Kudos.Diamond have also said that the rings I have here would be fine to use.
Pumaracing said:
I expected them to cop out with "if it isn't our stuff we can't recommend it". Kudos.
Best I can measure is the OD of the piston at the height of the top ring is 100.71mm, 3.965"The new rings finally arrived from the US supplier...the same rings he said they got into stock back in October 2014 for me...the same rings that have a date sticker from Total Seal for the top rings of 19 Feb 2015.
It lists top ring depth as 150thou ( 3.81mm ), so no doubt it's the same as the ones I have here anyway, although I dont have the packaging of the others to compare part numbers
Thank you, so just about 1mm down on bore size. The diametrical clearance at 350C crown temp and 100C bore temp will be 15 thou (0.37mm) so 7.5 thou all round and hence at least this same amount between ring and base of ring groove plus whatever dimension the ring sits below the groove top at ambient.
Piston crown seizure temperature is 520C so the clearance could be smaller in an ideal world but it's all very safe.
Piston crown seizure temperature is 520C so the clearance could be smaller in an ideal world but it's all very safe.
Gassing Station | Engines & Drivetrain | Top of Page | What's New | My Stuff