Race Car Rebuild
Discussion
Part 1
After many years of racing ZRTmotorsport have decided that after 7 hard years of racing, it is time to look at either re-shelling and rebuilding the Honda DC5 in advance of the 2017 Dubai 24Hrs or to buy another car.
We had considered opting for a new cars such as the Seat Cup racer, BMW 235i or Clio Cup but after running the DC5 for 4-years we came to have more spares than the Honda works teams! The work which went into acquiring the knowledge and stash of parts would be a huge undertaking to start again with a platform we were unfamiliar with. In addition considering the fact the Integra is a great platform to start with and the fact we are very stubborn the decision was taken to stick with what we know.
First step…. Find a shell
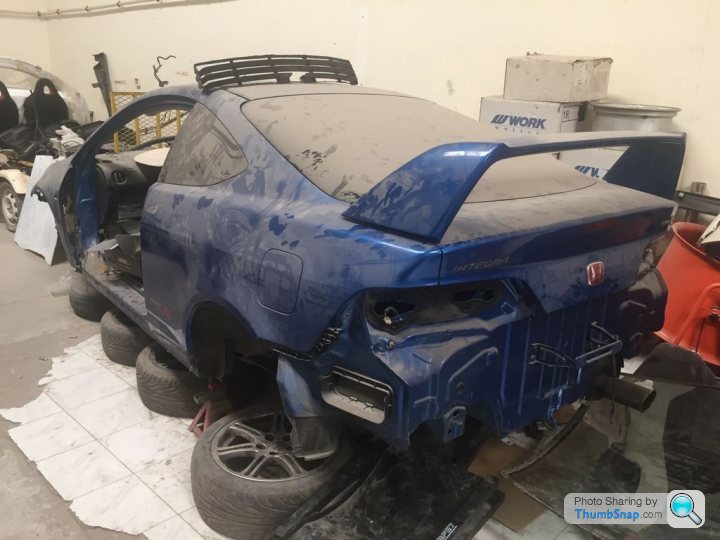
Our competitors and friends Lap 57 were able to assist and supply us with this clean (albeit dusty) 2007 shell.
The next step was to strip the shell and take it to Saluki Motorsport to agree the first stage of the project:
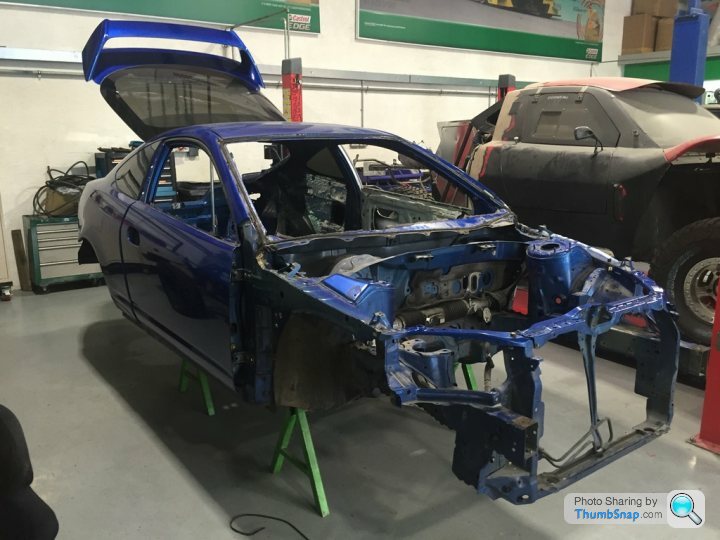
We agreed the following works with the guys at Saluki.
•Full FIA specification roll cage
•BTCC Spec enhancements for the front chassis
•Installation of seat rails
•Installation of air jacks brackets
•Removal of unnecessary brackets
•Provision for fuel cell installation
•Seem weld chassis
Stay tuned for part 2…
After many years of racing ZRTmotorsport have decided that after 7 hard years of racing, it is time to look at either re-shelling and rebuilding the Honda DC5 in advance of the 2017 Dubai 24Hrs or to buy another car.
We had considered opting for a new cars such as the Seat Cup racer, BMW 235i or Clio Cup but after running the DC5 for 4-years we came to have more spares than the Honda works teams! The work which went into acquiring the knowledge and stash of parts would be a huge undertaking to start again with a platform we were unfamiliar with. In addition considering the fact the Integra is a great platform to start with and the fact we are very stubborn the decision was taken to stick with what we know.
First step…. Find a shell
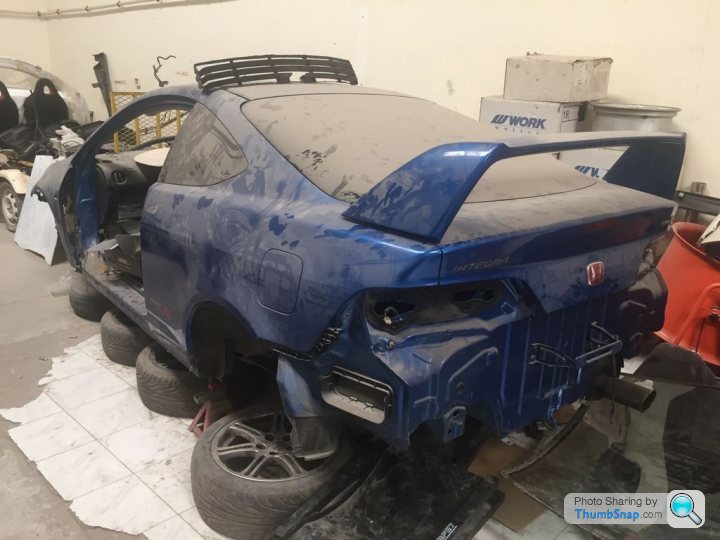
Our competitors and friends Lap 57 were able to assist and supply us with this clean (albeit dusty) 2007 shell.
The next step was to strip the shell and take it to Saluki Motorsport to agree the first stage of the project:
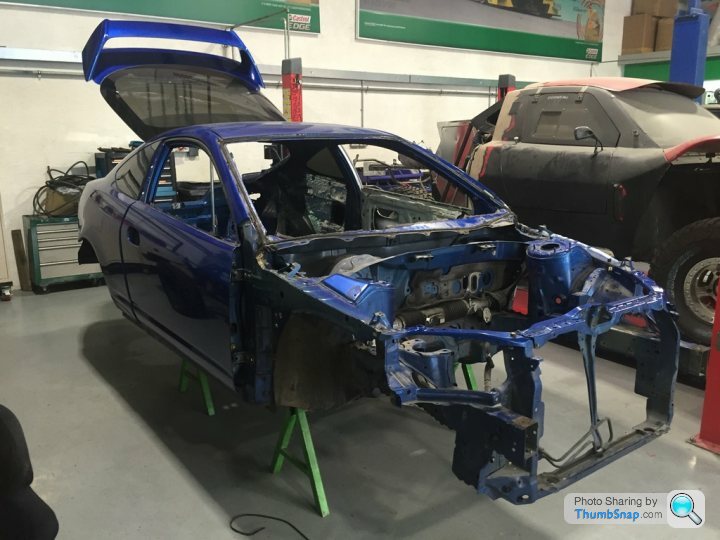
We agreed the following works with the guys at Saluki.
•Full FIA specification roll cage
•BTCC Spec enhancements for the front chassis
•Installation of seat rails
•Installation of air jacks brackets
•Removal of unnecessary brackets
•Provision for fuel cell installation
•Seem weld chassis
Stay tuned for part 2…
Edited by IanUAE on Thursday 26th May 05:20
Part 2
After agreeing the works to be carried out by Saluki, the first step was to shot blast the whole shell so that we uncover any surprises so that any metal work that required to be replaced could be replaced and secondly start with the best possible shell for seem welding.
So after shot blasting the good news was that the shell rust free and solid.
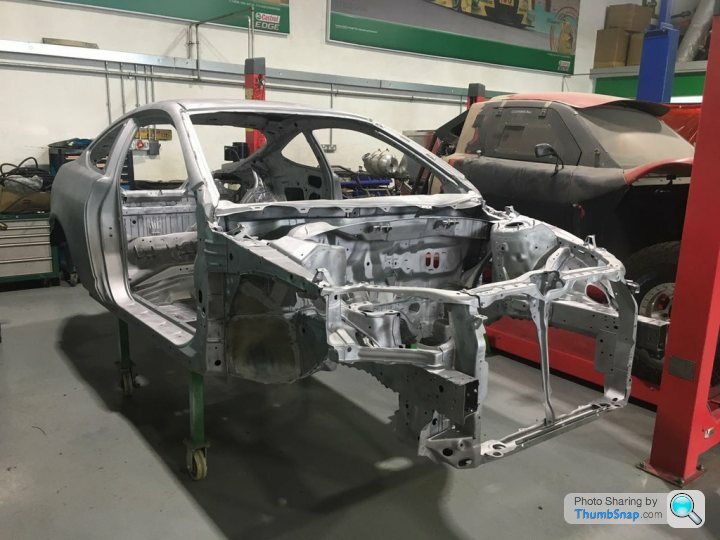
Saluki then got to work with the shell seam welding:
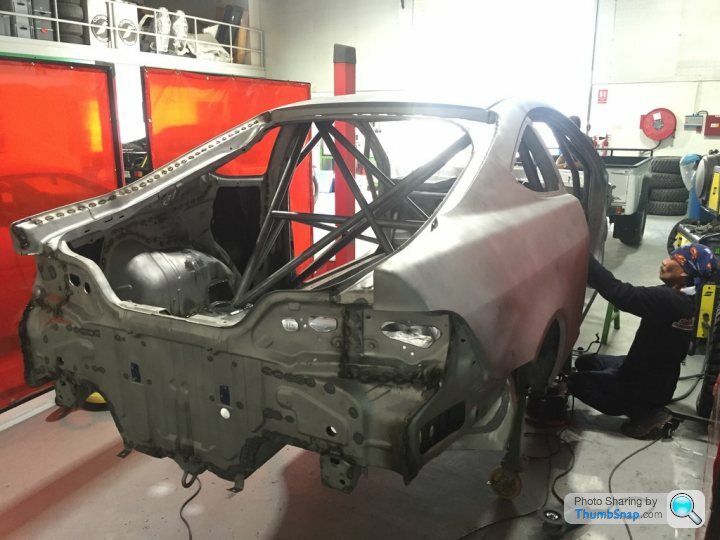
Front chassis is a critical part of the race car so seam welding was given detailed attention.
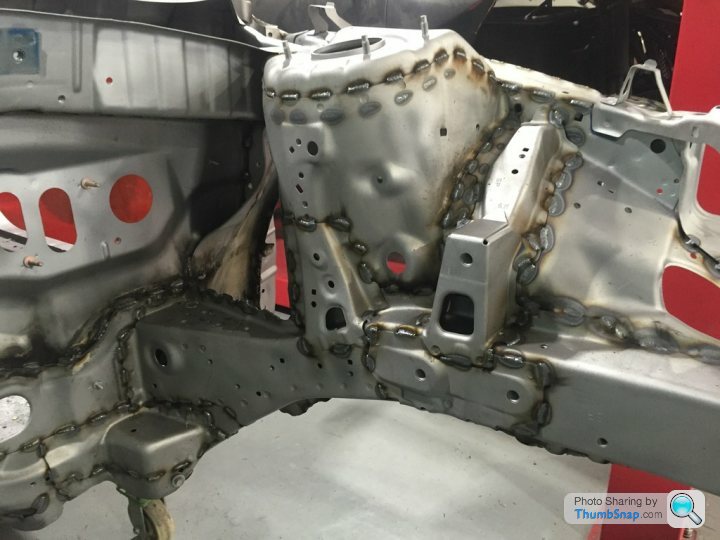
Stay tuned for part 3….
After agreeing the works to be carried out by Saluki, the first step was to shot blast the whole shell so that we uncover any surprises so that any metal work that required to be replaced could be replaced and secondly start with the best possible shell for seem welding.
So after shot blasting the good news was that the shell rust free and solid.
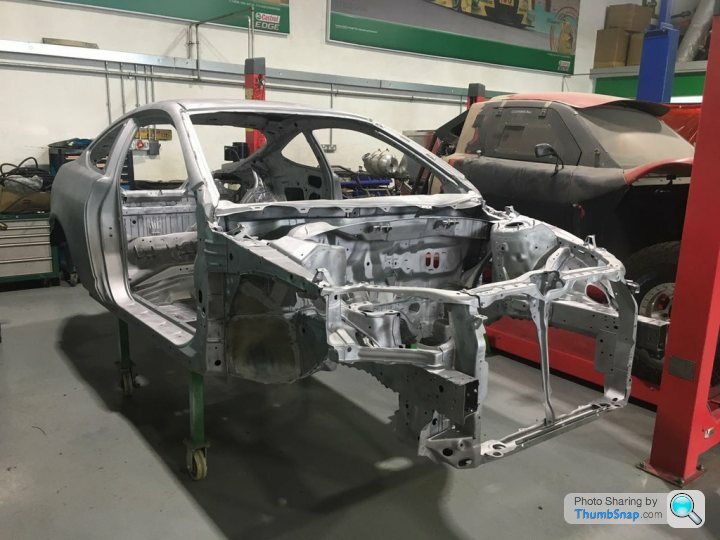
Saluki then got to work with the shell seam welding:
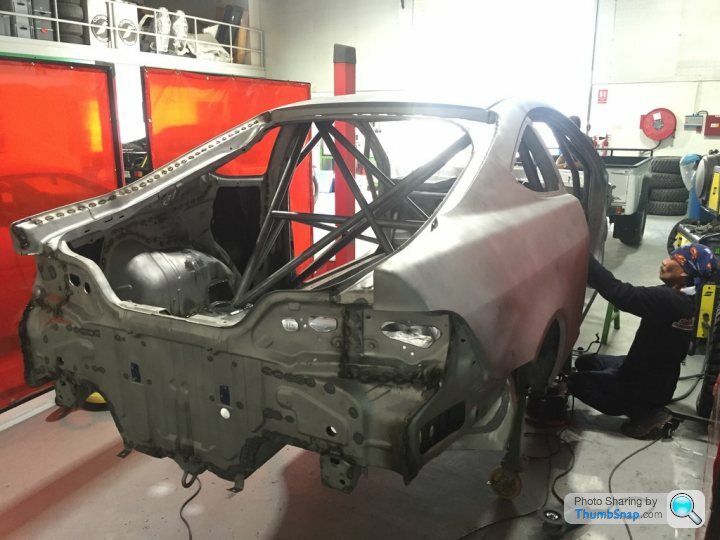
Front chassis is a critical part of the race car so seam welding was given detailed attention.
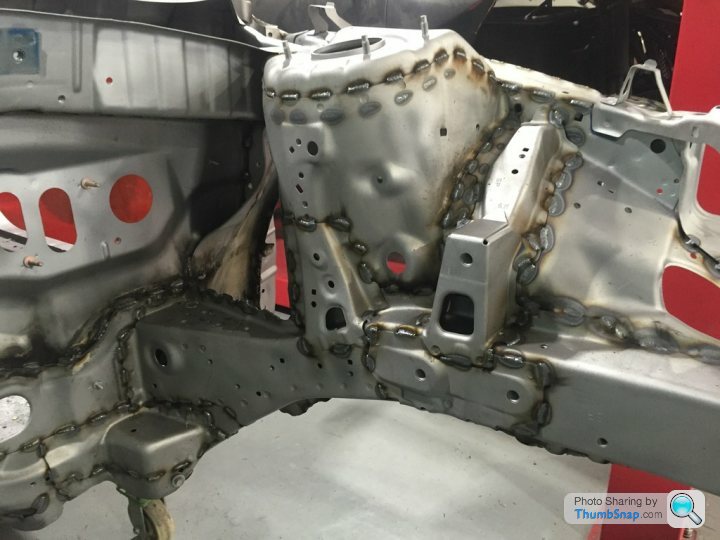
Stay tuned for part 3….
Edited by IanUAE on Thursday 26th May 05:20
Part 3
In our old shell we started facing a problem of windscreens cracking on the lower left of the screen. For anyone who has watched our documentary on Emirates Airline you will remember all too well what a problem this caused in 2015. Again since then a further 2-screens cracked. In the end we were unable to define exactly the cause but we suspect it is due to a weakness in the front chassis.
To combat this in the future and to eliminate the need for a strut brace this time we have replicated the roll cage design of the BTCC Touring cars similar to that of Peter England’s ex-BTCC astra here in Dubai. So in the below image you can see that the turret is strengthened in 4-ways.
1.Seam welding.
2.Triangulated bracing to the roll cage lateral bar at the dash.
3.Connection to the roll cage at the A-post. (Zoom in to see that one)
4.Double plate strengthening of the strut mounting.
We have also allowed for the provision of castor adjustment in the strut plate.
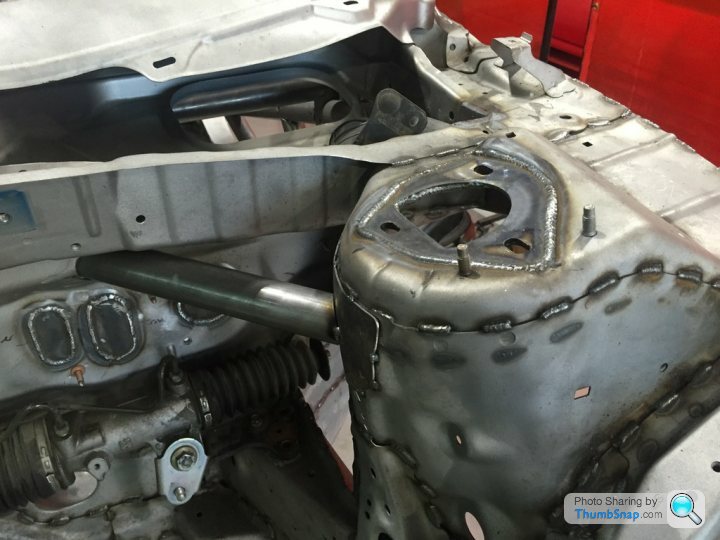
Those with a keen eye will also notice that the holes in the bulkhead (previous pic) have all been closed up as they are not needed on the race car. Most probably they were for water hoses to the heater/a-c but because we already have a car to work from we know they are not required in the build. They are therefore closed for safety and rigidity.
Stay tuned for part 4….
In our old shell we started facing a problem of windscreens cracking on the lower left of the screen. For anyone who has watched our documentary on Emirates Airline you will remember all too well what a problem this caused in 2015. Again since then a further 2-screens cracked. In the end we were unable to define exactly the cause but we suspect it is due to a weakness in the front chassis.
To combat this in the future and to eliminate the need for a strut brace this time we have replicated the roll cage design of the BTCC Touring cars similar to that of Peter England’s ex-BTCC astra here in Dubai. So in the below image you can see that the turret is strengthened in 4-ways.
1.Seam welding.
2.Triangulated bracing to the roll cage lateral bar at the dash.
3.Connection to the roll cage at the A-post. (Zoom in to see that one)
4.Double plate strengthening of the strut mounting.
We have also allowed for the provision of castor adjustment in the strut plate.
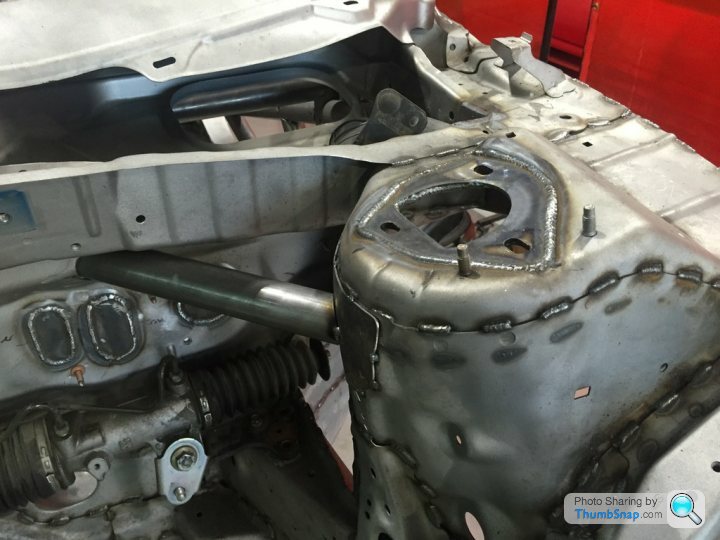
Those with a keen eye will also notice that the holes in the bulkhead (previous pic) have all been closed up as they are not needed on the race car. Most probably they were for water hoses to the heater/a-c but because we already have a car to work from we know they are not required in the build. They are therefore closed for safety and rigidity.
Stay tuned for part 4….
Part 4
Next up is to replace the OEM dash bar with an 38mm CDS section which will become an integral part of the roll cage. In the photo below you can see where the strut bracing sections are located and also its clear that Saluki have removed all unnecessary sections of steel from the floor and bulkhead reducing as much weight as possible.
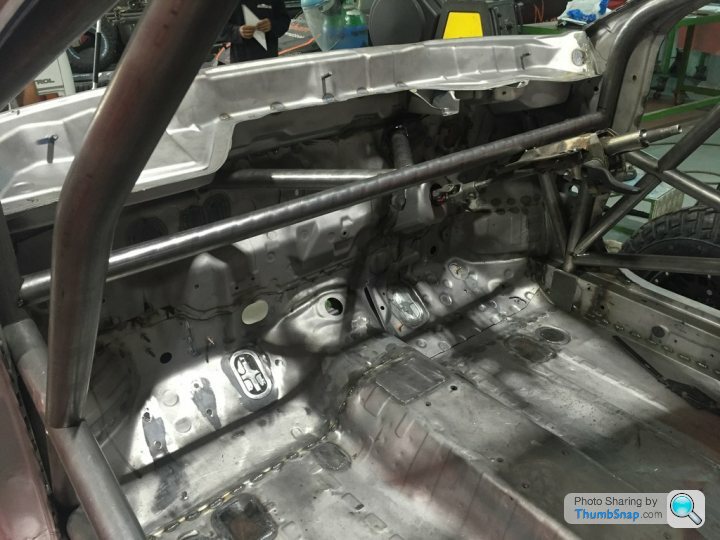
The cage will be built to the highest safety standards in accordance with the FIA regulations. With the cage partly mocked up and tacked into place the guys also start measuring precisely for the gusset reinforcement sections at the doors.

There will be 4 of these per door and the finished product looks like this:
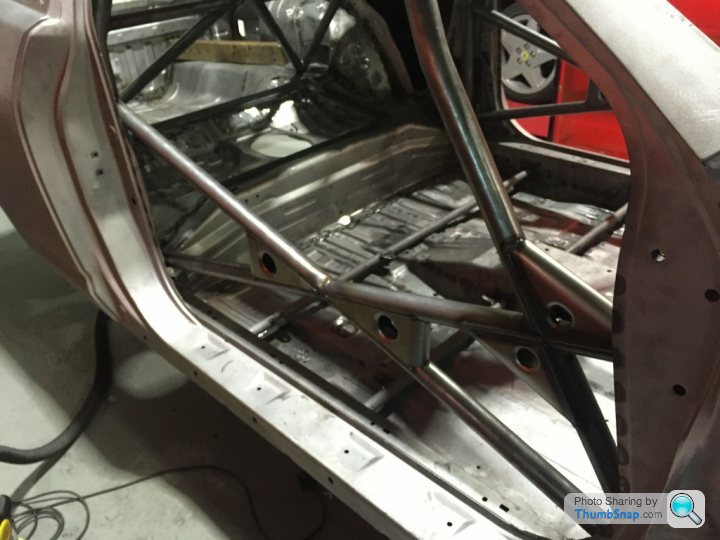
The cage is almost finished and we will post a few pics over the weekend showing the welding quality and explain how the guys weld the tops of the cage (The parts almost touching the roof) which incidentally were not properly welded in our previous car but still passed FIA scrutineering ??
With cars in Dubai 24hr reaching almost 300kph (not ours) we have to put safety as the no. 1 priority and now that we have the chance and expertise to do it we won’t take any shortcuts with the build.
Stay tuned for part 5…
More information about the team etc can be found on www.zrtmotorsport.com
Next up is to replace the OEM dash bar with an 38mm CDS section which will become an integral part of the roll cage. In the photo below you can see where the strut bracing sections are located and also its clear that Saluki have removed all unnecessary sections of steel from the floor and bulkhead reducing as much weight as possible.
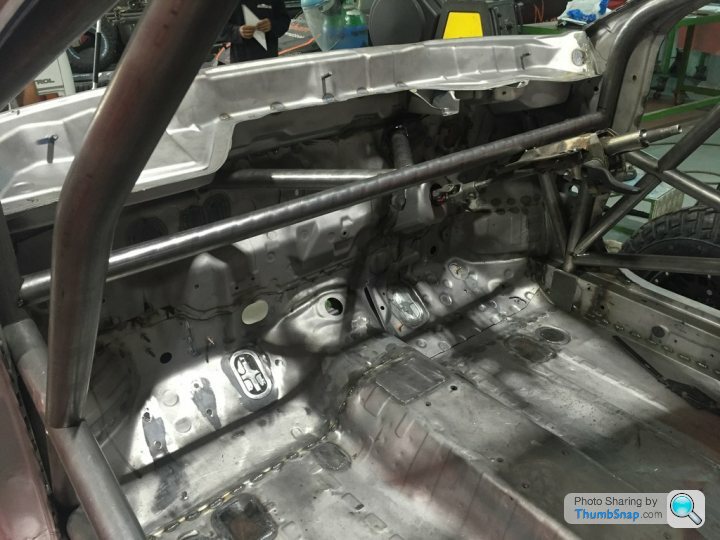
The cage will be built to the highest safety standards in accordance with the FIA regulations. With the cage partly mocked up and tacked into place the guys also start measuring precisely for the gusset reinforcement sections at the doors.

There will be 4 of these per door and the finished product looks like this:
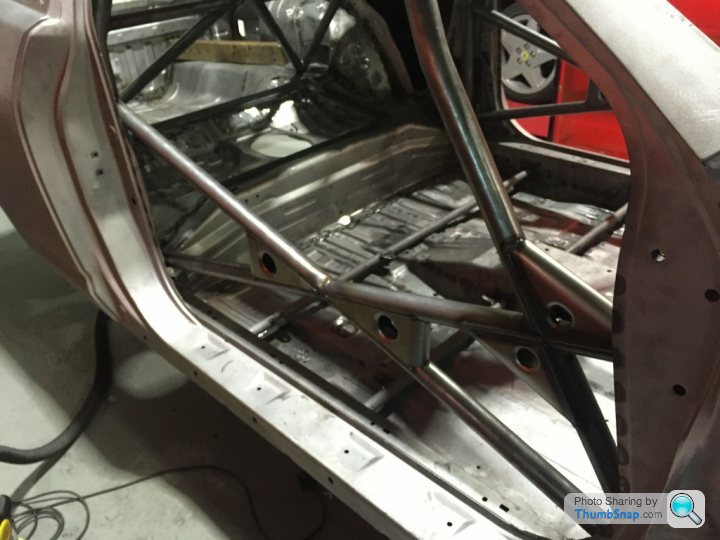
The cage is almost finished and we will post a few pics over the weekend showing the welding quality and explain how the guys weld the tops of the cage (The parts almost touching the roof) which incidentally were not properly welded in our previous car but still passed FIA scrutineering ??
With cars in Dubai 24hr reaching almost 300kph (not ours) we have to put safety as the no. 1 priority and now that we have the chance and expertise to do it we won’t take any shortcuts with the build.
Stay tuned for part 5…
More information about the team etc can be found on www.zrtmotorsport.com
Edited by IanUAE on Thursday 26th May 05:26
TacoExcellence said:
Looks like a Polaris RZR.
Correct. They are very common in the dunes over here and there is a category for them in the various desert rallies.IanUAE said:
This beast is a custom built desert rally car that runs an LS motor and Albans sequential gearbox, has onboard rear tyre deflation / inflation and 300mm of suspension travel (think of PhillipM car but on steroids http://www.pistonheads.com/gassing/topic.asp?h=0&a...Part 5
So, something new to me (having never installed a cage before) is..... How do you weld the bits at the top of the roll cage which are tight to the underside of the roof? Many of you maybe saying... That's easy dummy and so it is.... When you know how. I knew (well I did research for the update on our website on the roll cage) but others might not, so some may it interesting to learn how.
Actually there are two ways:
1.You cut the roof off, weld and refit the roof.
2.You fabricate up the cage in-situ by tack welding together, cut holes in the floor beside the vertical mounting points, remove the lateral supports and drop the cage 50-100mm through the floor, weld 360-degree's around the tops of the cage connection points and then lift the cage back into place and make solid base mounting plates.
If you look at the mounting point in the below image, there is a pre-cut hole and the cage is tack welded in place. That will then be ground off to allow the cage to drop.
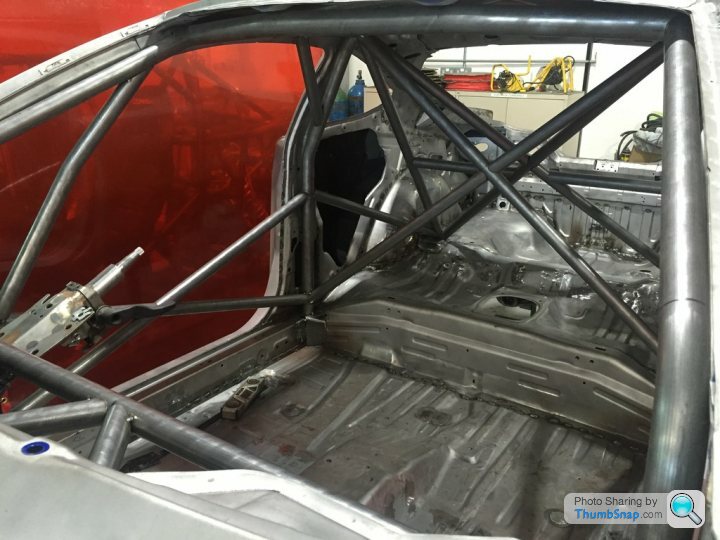
I’m not experienced in welding but when something looks right it probably is 😊
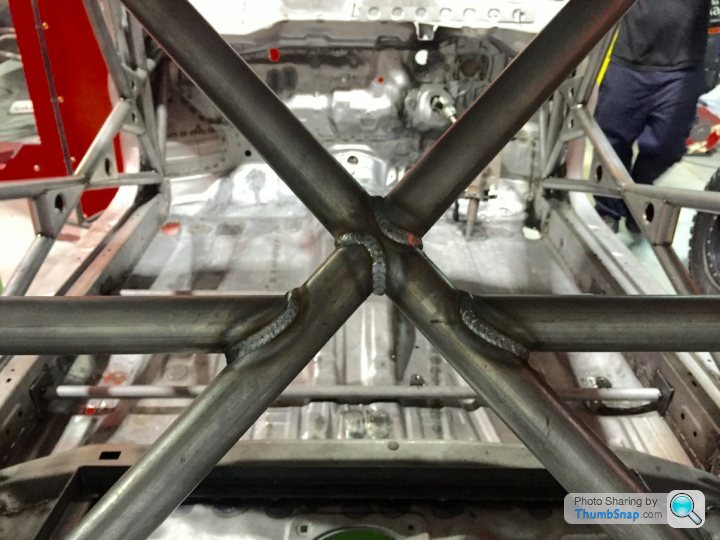
The last thing to talk about today is the seat mounting points. We asked Saluki to make provision for driver and passenger seats because we may wish to take sponsors on taxi rides at the 24-Hrs event.
The seat bars are secured to the sills of the car and fitted as close to the floor as possible. We are using Corbeau Revenge seat supplied by Jon of MotorsportWheels, Dubai so the fixing points are set out to the Corbeau seat frames.
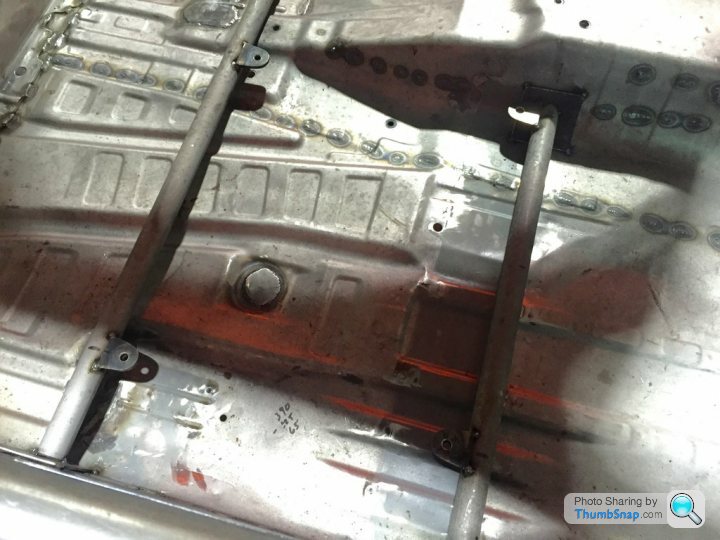
Next up is the 100L fuel cell and just how we are going to squeeze it between the 'X' bars of the cage. Stay tuned for part 6 as this bit is quite cool....
So, something new to me (having never installed a cage before) is..... How do you weld the bits at the top of the roll cage which are tight to the underside of the roof? Many of you maybe saying... That's easy dummy and so it is.... When you know how. I knew (well I did research for the update on our website on the roll cage) but others might not, so some may it interesting to learn how.
Actually there are two ways:
1.You cut the roof off, weld and refit the roof.
2.You fabricate up the cage in-situ by tack welding together, cut holes in the floor beside the vertical mounting points, remove the lateral supports and drop the cage 50-100mm through the floor, weld 360-degree's around the tops of the cage connection points and then lift the cage back into place and make solid base mounting plates.
If you look at the mounting point in the below image, there is a pre-cut hole and the cage is tack welded in place. That will then be ground off to allow the cage to drop.
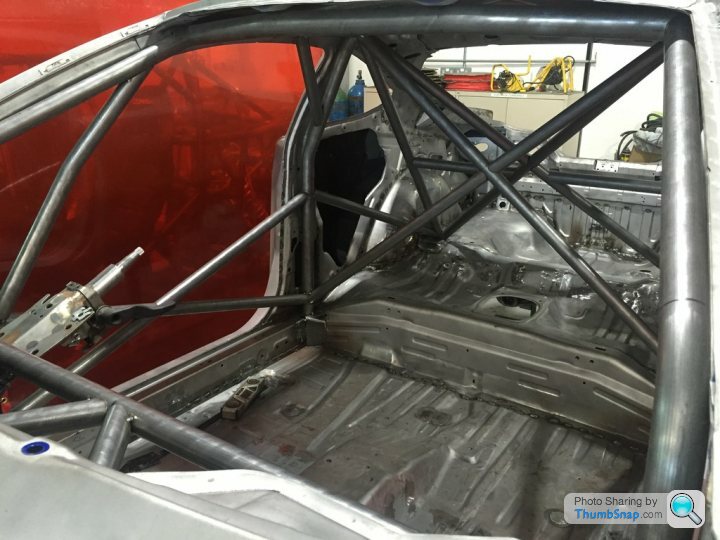
I’m not experienced in welding but when something looks right it probably is 😊
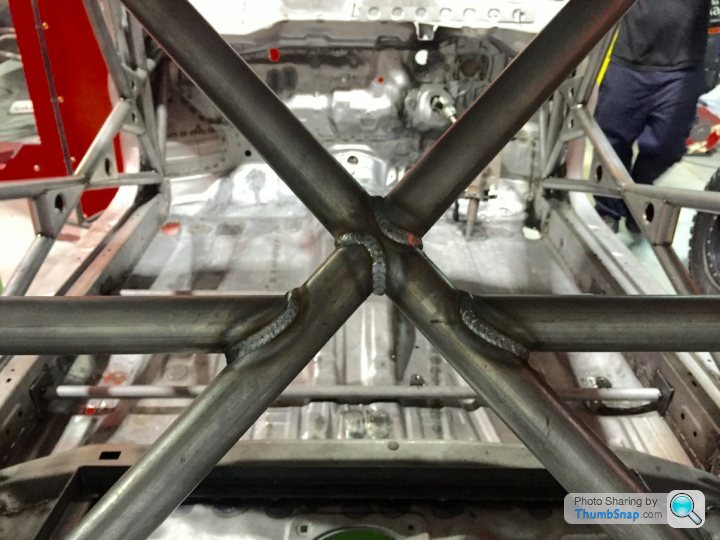
The last thing to talk about today is the seat mounting points. We asked Saluki to make provision for driver and passenger seats because we may wish to take sponsors on taxi rides at the 24-Hrs event.
The seat bars are secured to the sills of the car and fitted as close to the floor as possible. We are using Corbeau Revenge seat supplied by Jon of MotorsportWheels, Dubai so the fixing points are set out to the Corbeau seat frames.
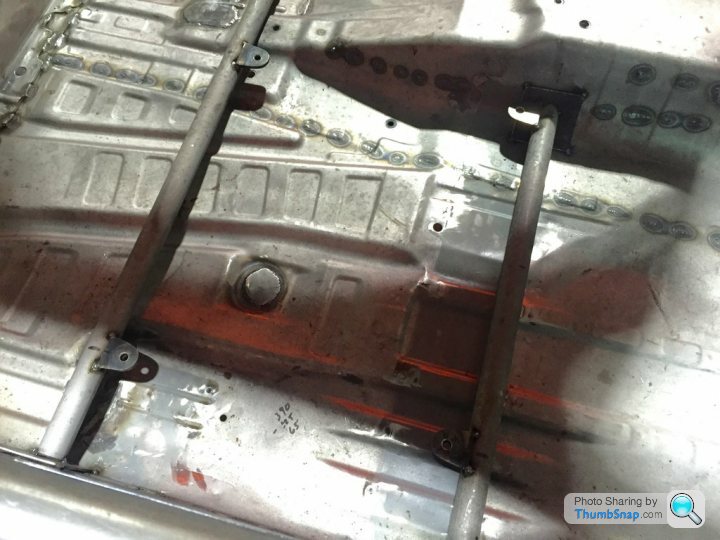
Next up is the 100L fuel cell and just how we are going to squeeze it between the 'X' bars of the cage. Stay tuned for part 6 as this bit is quite cool....
Part 6
Ok before we go on to the tank we'll give an update as to where things are now.
Firstly the cage is pretty much complete with the exception of some final welds in certain places.
Door bars:
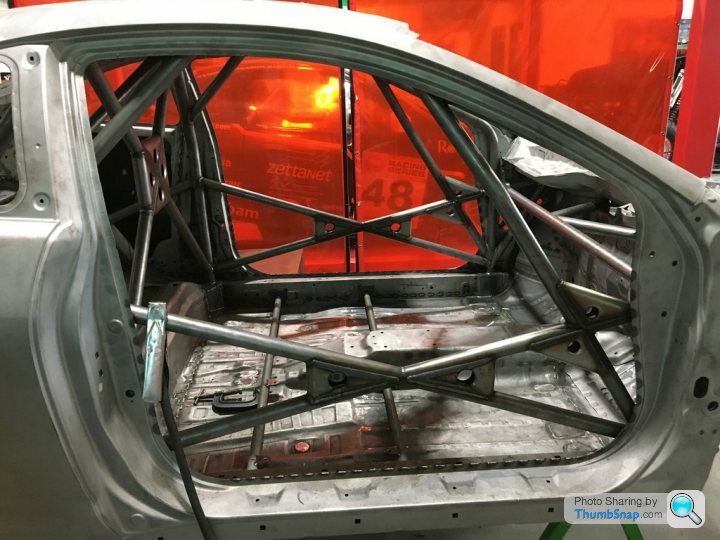
Roof section:
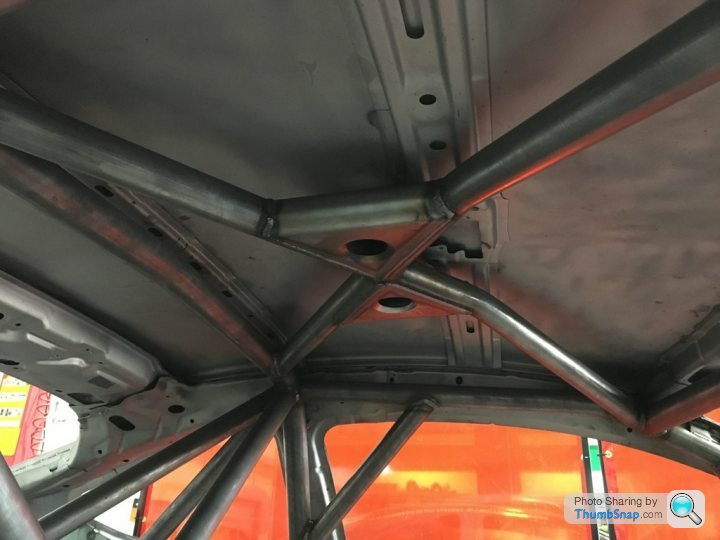
Seat rails in place:
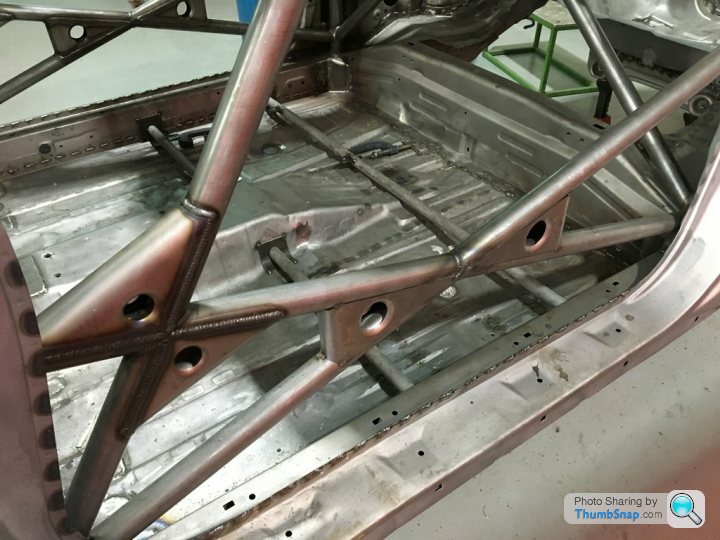
Main cage X section completed.
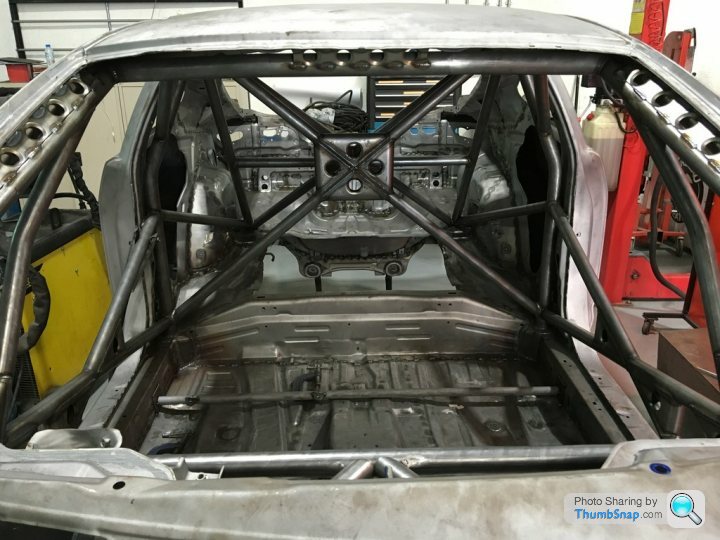
One of the problems we had with the previous Custom cages design was the positioning of the 45-degree support bar at the door. Firstly this restricted the access and secondly it fouled our Corbeau seat to the point whereby we had to hack a section out of the centre tunnel, which in turn led us to moving the pedal box and eventually moving the steering column. (I did mention we were stubborn earlier in the thread!)
So this time no such mods required. Saluki were able to move the support back whilst still being fully compliant with the FIA (Appendix J) regulations. Should also mention that the CC previous cage was 45mm throughout whereas we are now using 38mm with the exception of the main roll bar and the bar above the screen.
Previous:
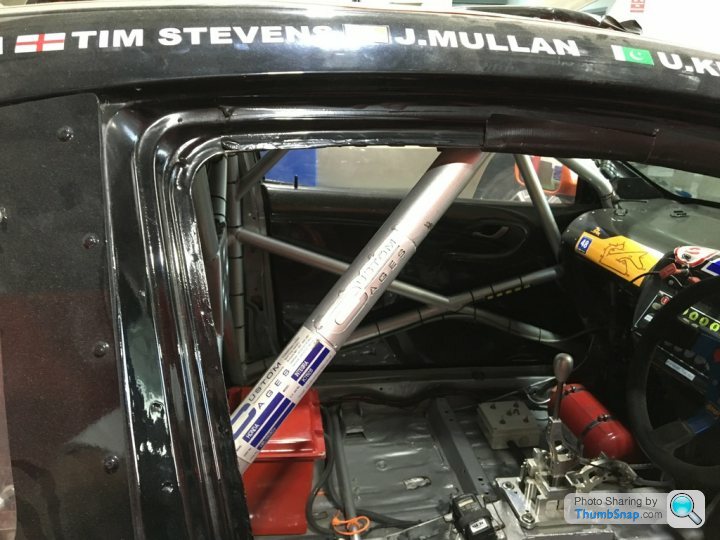
New:
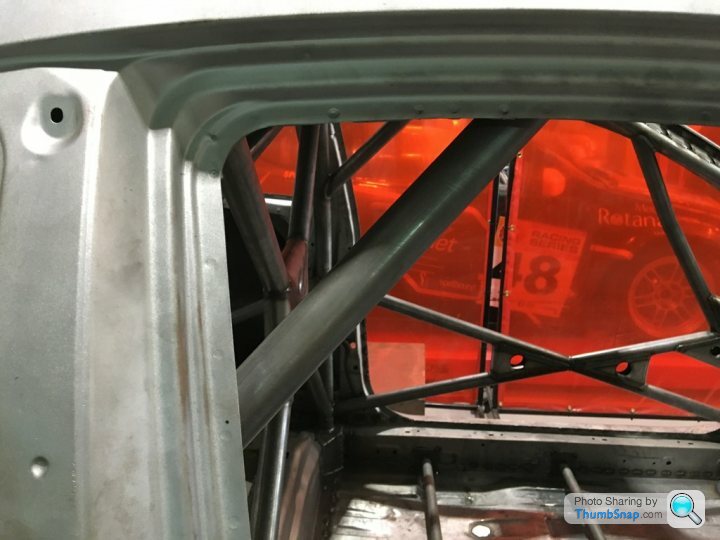
Stay tuned for part 7...
Ok before we go on to the tank we'll give an update as to where things are now.
Firstly the cage is pretty much complete with the exception of some final welds in certain places.
Door bars:
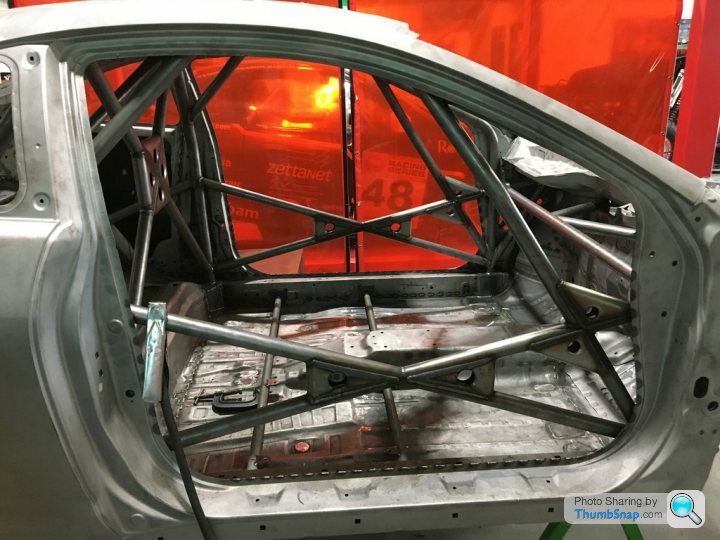
Roof section:
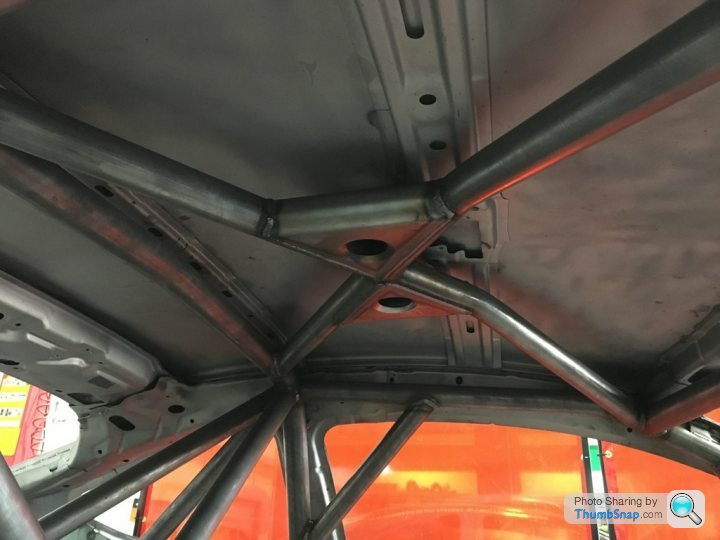
Seat rails in place:
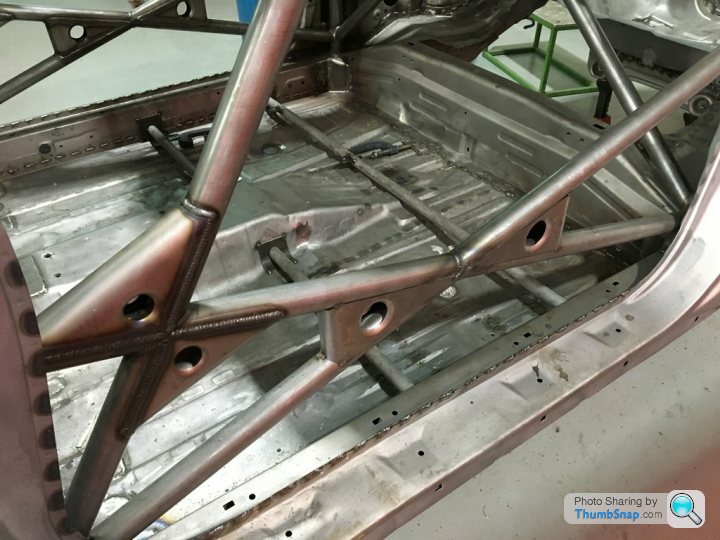
Main cage X section completed.
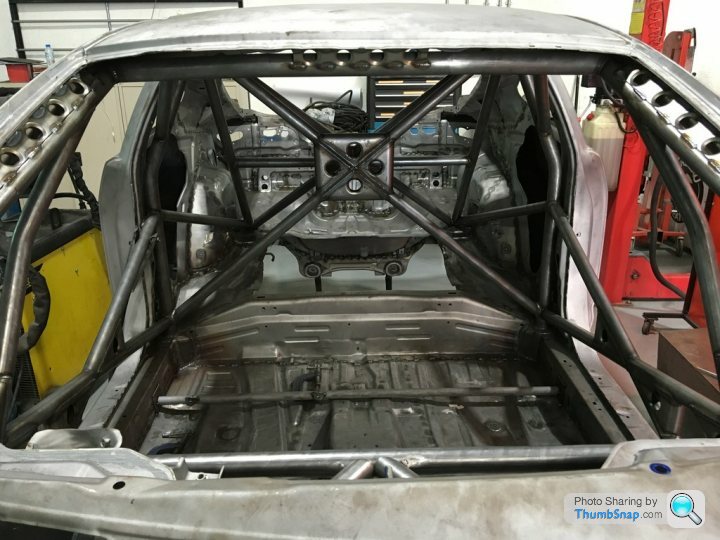
One of the problems we had with the previous Custom cages design was the positioning of the 45-degree support bar at the door. Firstly this restricted the access and secondly it fouled our Corbeau seat to the point whereby we had to hack a section out of the centre tunnel, which in turn led us to moving the pedal box and eventually moving the steering column. (I did mention we were stubborn earlier in the thread!)
So this time no such mods required. Saluki were able to move the support back whilst still being fully compliant with the FIA (Appendix J) regulations. Should also mention that the CC previous cage was 45mm throughout whereas we are now using 38mm with the exception of the main roll bar and the bar above the screen.
Previous:
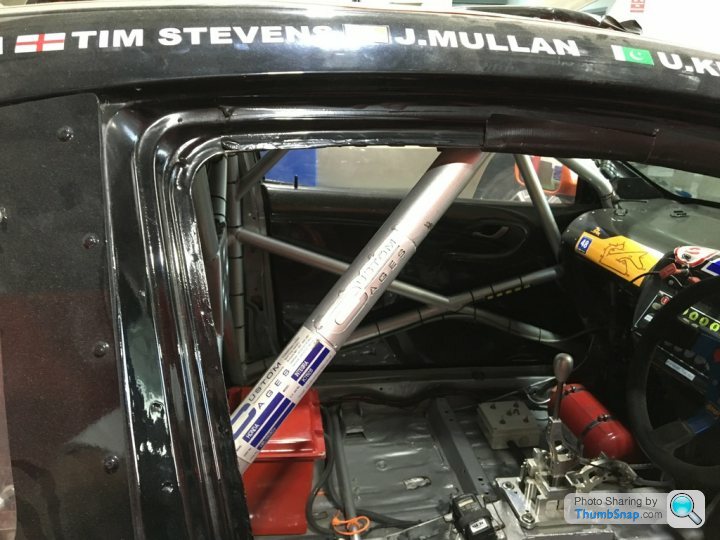
New:
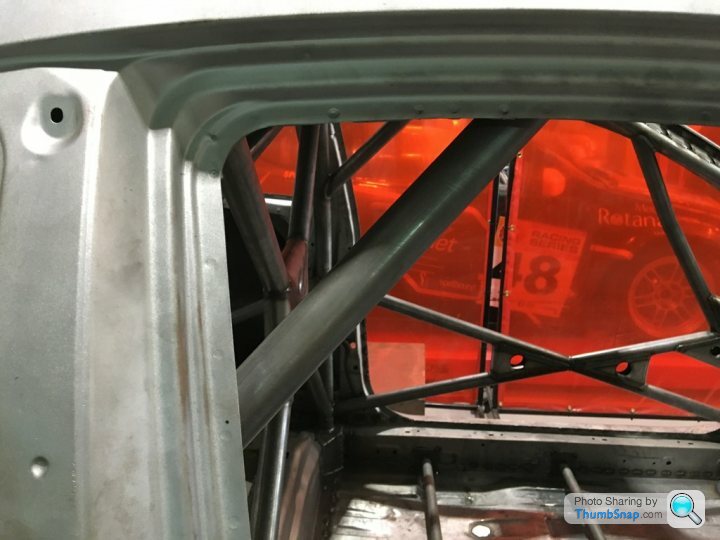
Stay tuned for part 7...
Part 7
As you become 'used' to something you tend not to realise or appreciate when things are wrong. Take the example of the ever widening waistline, few kgs here and there and all of a sudden without any warning you are 10kgs overweight. Well the same happened to our trusty Honda. 4-paint jobs and 3-vinyl wrap schemes later and lots of filler and all of a sudden we were almost 100kgs over our 'sprint' spec weight just 2-years earlier.
So the aim this time is to stay fit and light from the start.
For those that don't know this is the old girl and whilst we moan about her putting on kgs, she did put us on the podium in 14 out of 16 races in 2013-14 so lets not be too hard.
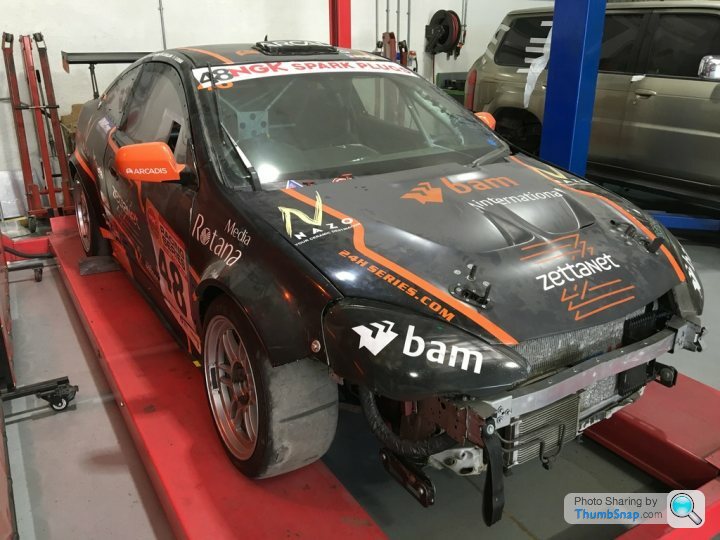
Speaking of wrong (in the same context of the previous point) below are a few examples of our previous cage quality when compared to the new cage.
Previous centre section of the X brace:
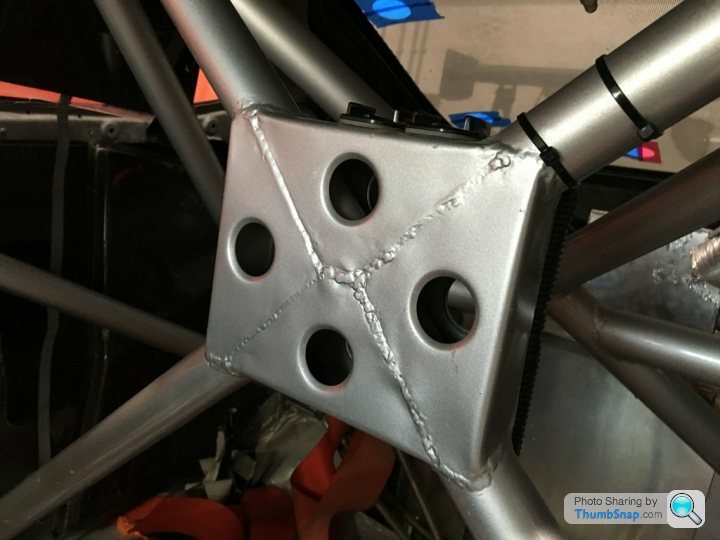
New:
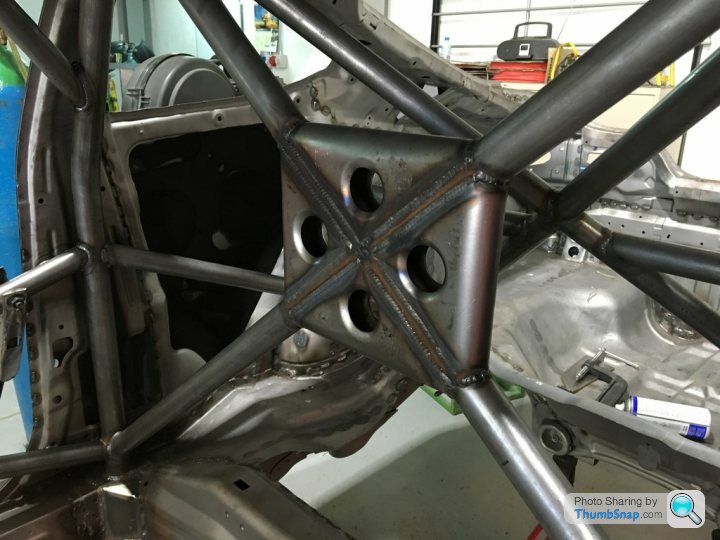
Previous door bars:
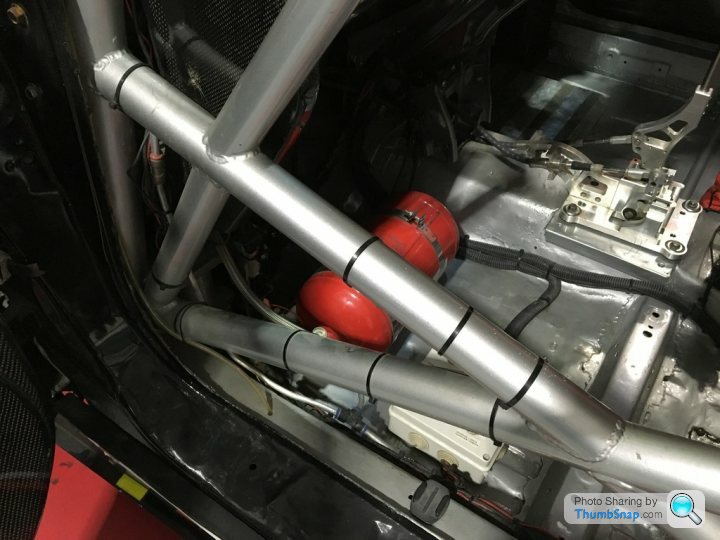
New:
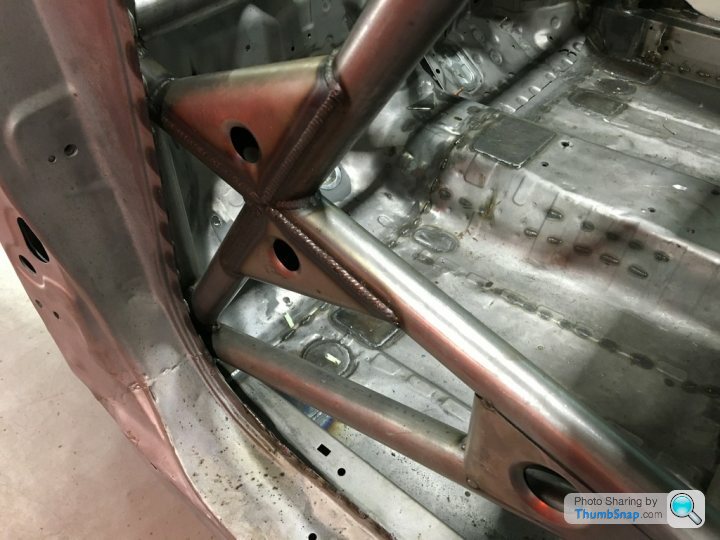
As you can see the quality is vastly improved.
In the below image you can see where the floor was cut to drop the cage through to weld the top sections as mentioned previously:
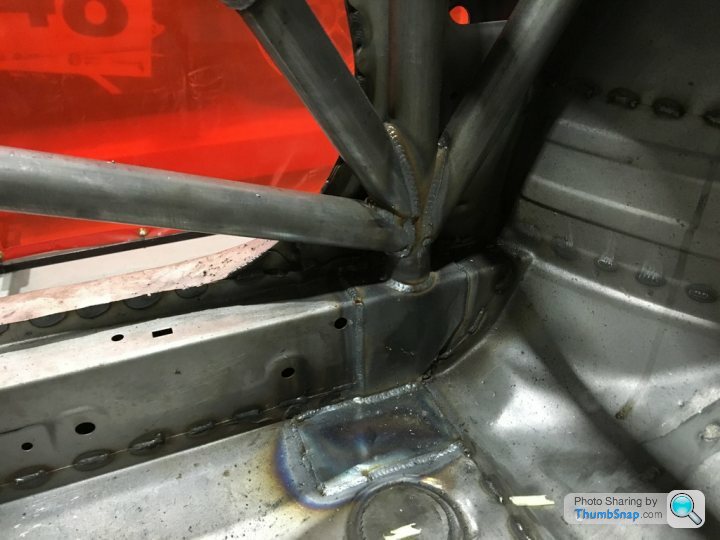
Saluki reinforced the rear shock anchoring sections firstly to support the cage and secondly to give a robust foundation for the rear shocks to be fixed to.
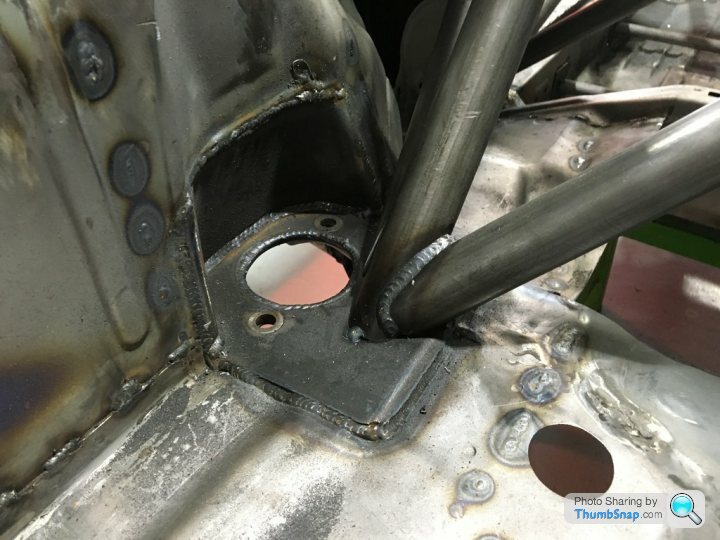
We also went over the car with Saluki looking for areas were we could remove a little weight but not effect the structural integrity of the car. Below is one example of where we are able to remove a little bit of unnecessary metal.
Before:
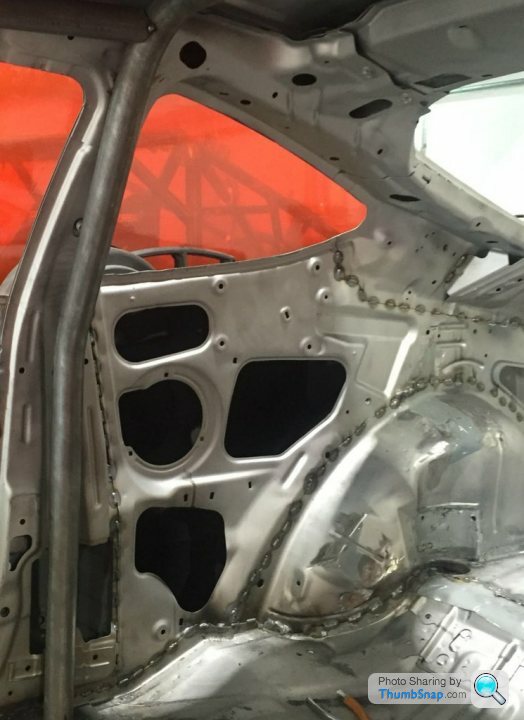
After:
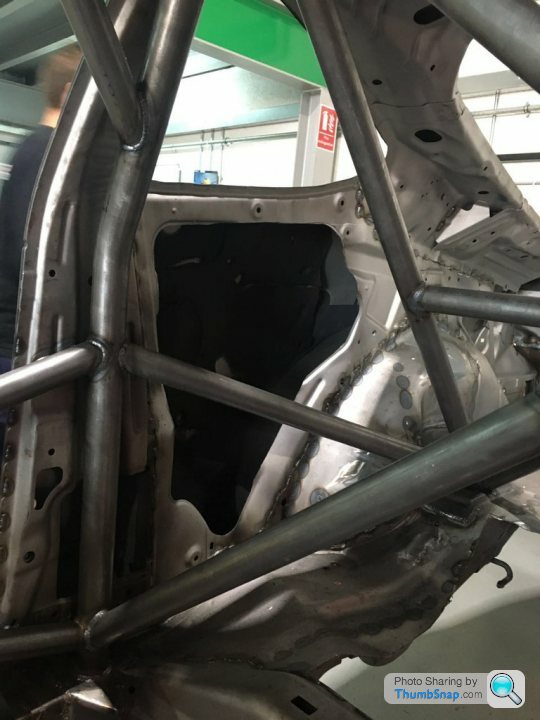
We have a carbon fibre infil panel to cover the new "hole".
At this stage there are only three main jobs left:
1. Air jacks
2. Pedal box
3. Fuel cell
Stay tuned for Part 8....
As you become 'used' to something you tend not to realise or appreciate when things are wrong. Take the example of the ever widening waistline, few kgs here and there and all of a sudden without any warning you are 10kgs overweight. Well the same happened to our trusty Honda. 4-paint jobs and 3-vinyl wrap schemes later and lots of filler and all of a sudden we were almost 100kgs over our 'sprint' spec weight just 2-years earlier.
So the aim this time is to stay fit and light from the start.
For those that don't know this is the old girl and whilst we moan about her putting on kgs, she did put us on the podium in 14 out of 16 races in 2013-14 so lets not be too hard.
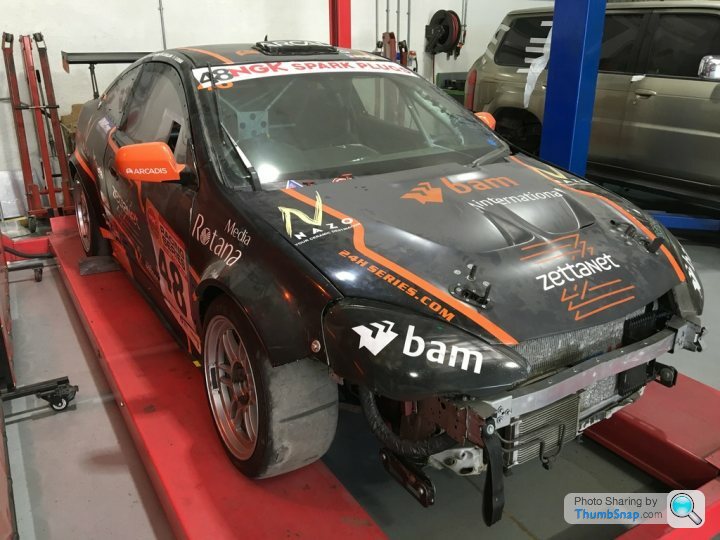
Speaking of wrong (in the same context of the previous point) below are a few examples of our previous cage quality when compared to the new cage.
Previous centre section of the X brace:
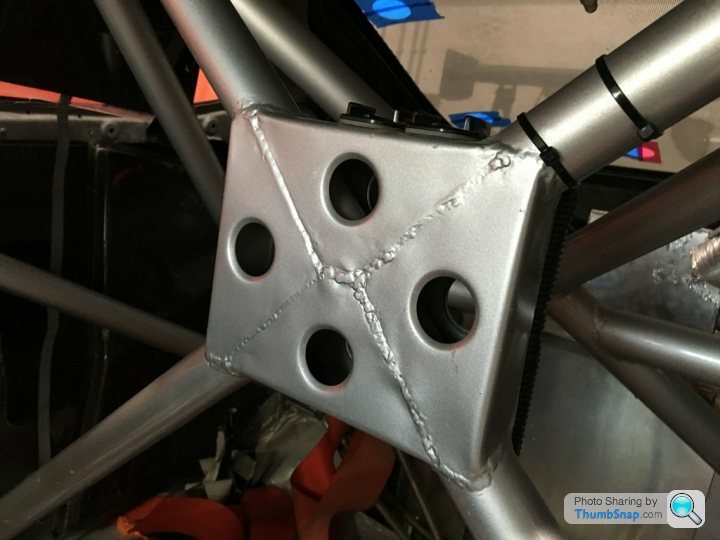
New:
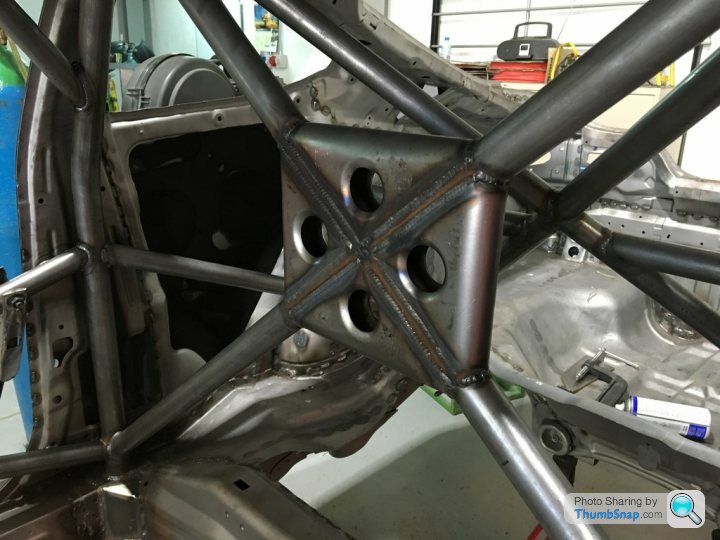
Previous door bars:
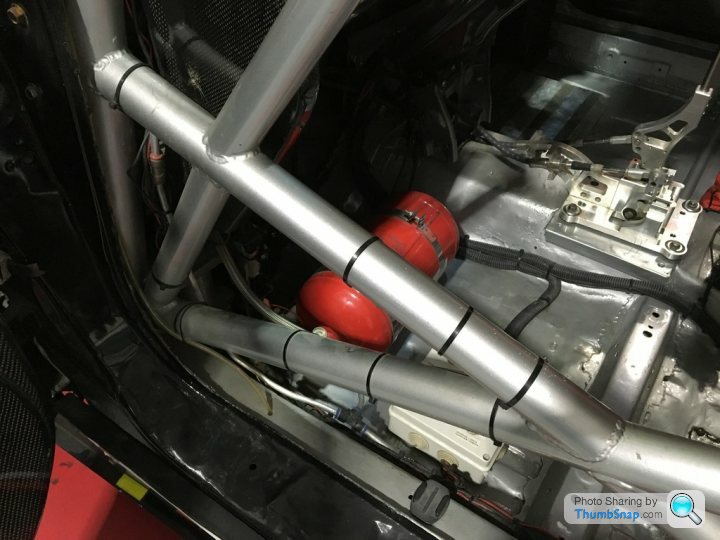
New:
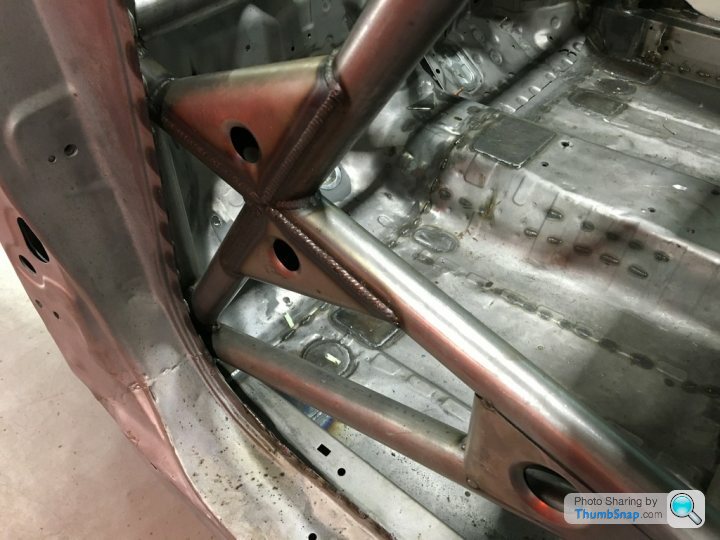
As you can see the quality is vastly improved.
In the below image you can see where the floor was cut to drop the cage through to weld the top sections as mentioned previously:
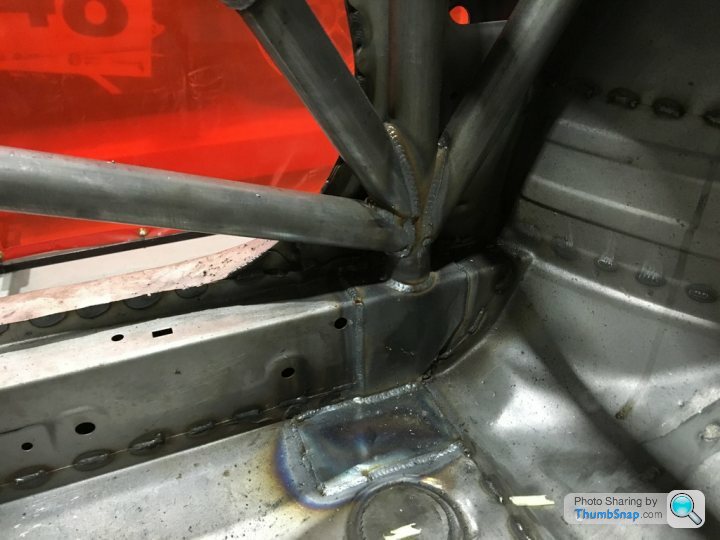
Saluki reinforced the rear shock anchoring sections firstly to support the cage and secondly to give a robust foundation for the rear shocks to be fixed to.
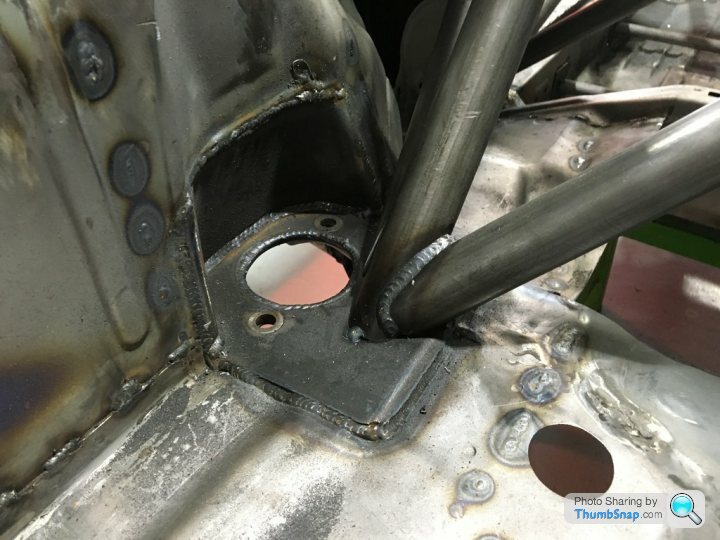
We also went over the car with Saluki looking for areas were we could remove a little weight but not effect the structural integrity of the car. Below is one example of where we are able to remove a little bit of unnecessary metal.
Before:
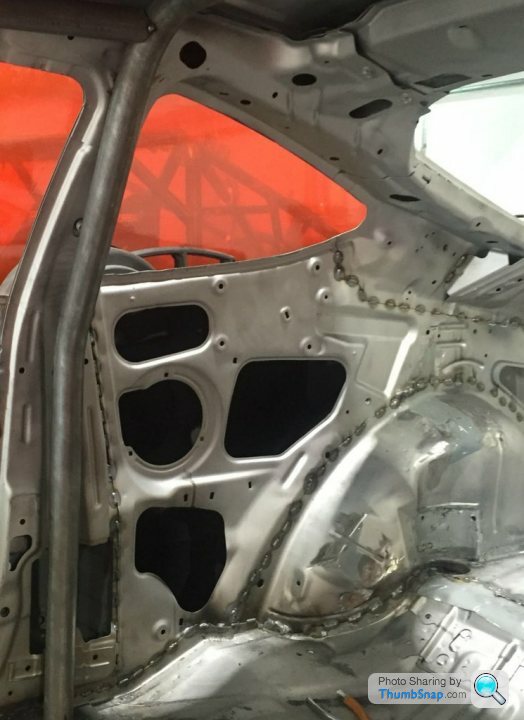
After:
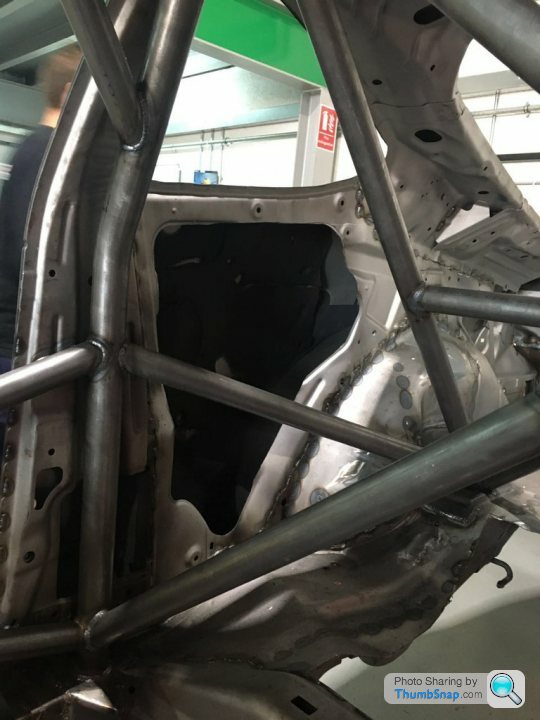
We have a carbon fibre infil panel to cover the new "hole".
At this stage there are only three main jobs left:
1. Air jacks
2. Pedal box
3. Fuel cell
Stay tuned for Part 8....
Part 8
Well it seems we have a problem. Despite our best endeavors the Corbeau Revenge seat doesn't fit.
So we thought about the various options, took some measurements and in the end decided to opt for the Corbeau Pro Series seat.
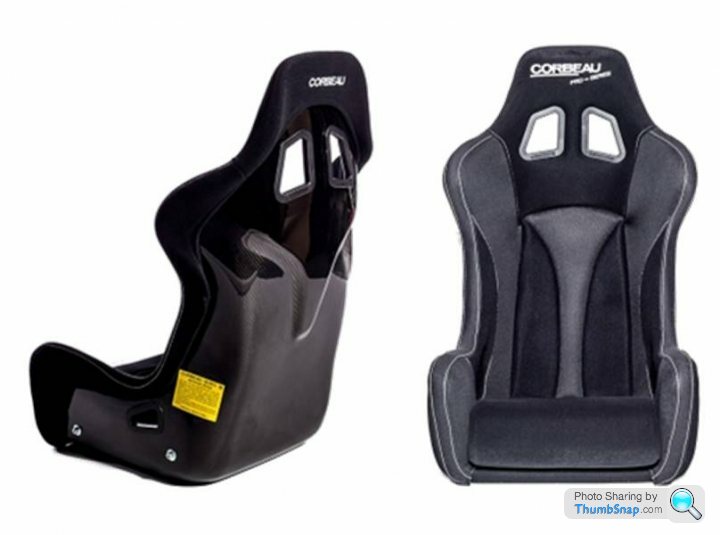
http://www.corbeau-seats.com/motorsports-seats/pro...
As you can see from the description we are clearly not the first people to enounter this problem.
To be honest there are two advantages with this seat type that actually benefit us:
1. Its easier to get in and out of the car during driver changes.
2. The driver has better peripheral vision. (Which is useful with a grid of 100-cars).
So we've placed our order with the MotorsportWheels team and eagerly await delivery.
The old seat will either become an office chair or if I have my way, I will use it to replace one of the hard plastic seats on the pit perch 😊
Next up. Rear air jack and pedal box
Last time we had located the rear jack right at the back of the car boot floor. The reason was because of the location of the fuel cell but because we are able to locate the fuel cell on the back seat this time we are able to locate the air jack more centrally.
This means its positioned closer to the main structure of the roll cage and therefore should not cause any flex in the shell when operated. Below is the rear mounting point.

In the Honda DC5 the firewall is angled where it meets the floor (where the conventional pedals are located) so to fit a race type pedal box. We've ordered the following AP Racing pedal box from our friends at MotorsportWheels.
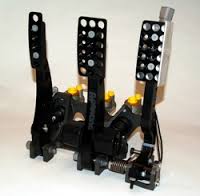
https://www.apracing.com/product_details/race_car/...
In order to fit this pedal box the floor requires modification to be a flat floor. Saluki have ensured that the boxed out section is extremely strong so that there will be no flex in the floor which could impact the effectiveness of the brake pedal.
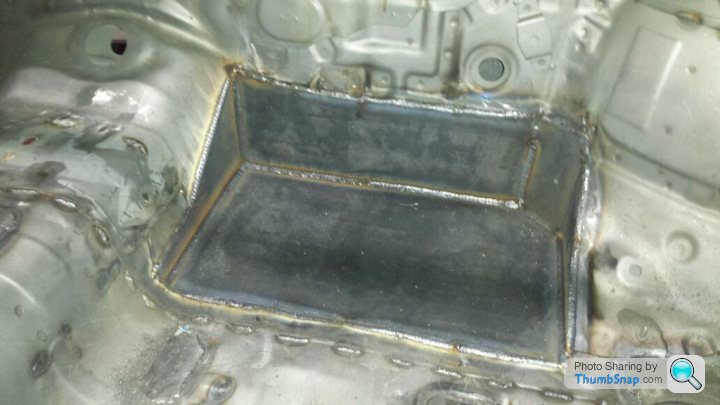
Fuel cell has been located as stated between the roll cage. This hopefully will enhance the cars balance and handling by centralising the weight and making it safer but locating the tank in what should be the safest part of the car.
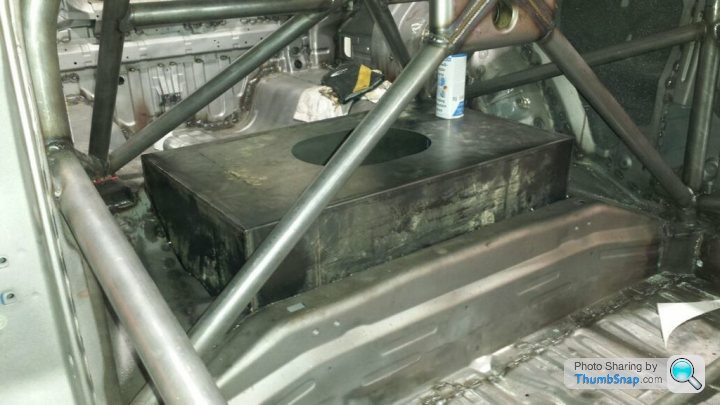
We are very happy with the Engineering work carried out by Saluki Motorsport thus far and by working with some of the best people and businesses in Dubai we are confident the end product will be amazing.
Stay tuned for part 9.
Well it seems we have a problem. Despite our best endeavors the Corbeau Revenge seat doesn't fit.
So we thought about the various options, took some measurements and in the end decided to opt for the Corbeau Pro Series seat.
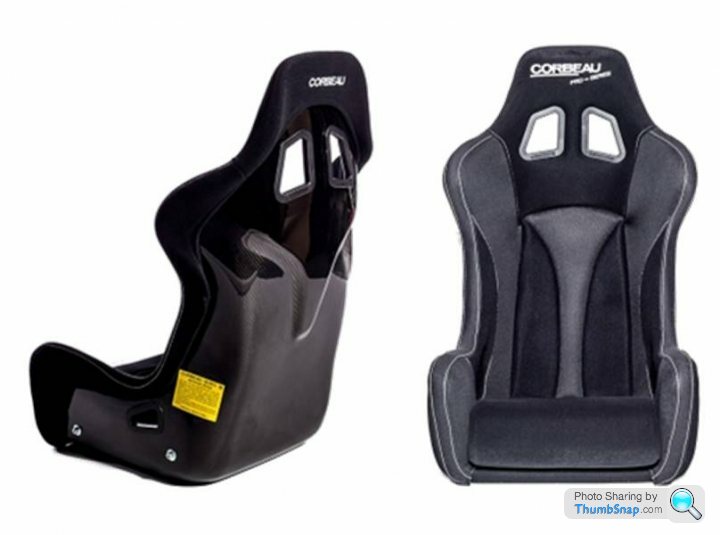
http://www.corbeau-seats.com/motorsports-seats/pro...
As you can see from the description we are clearly not the first people to enounter this problem.
To be honest there are two advantages with this seat type that actually benefit us:
1. Its easier to get in and out of the car during driver changes.
2. The driver has better peripheral vision. (Which is useful with a grid of 100-cars).
So we've placed our order with the MotorsportWheels team and eagerly await delivery.
The old seat will either become an office chair or if I have my way, I will use it to replace one of the hard plastic seats on the pit perch 😊
Next up. Rear air jack and pedal box
Last time we had located the rear jack right at the back of the car boot floor. The reason was because of the location of the fuel cell but because we are able to locate the fuel cell on the back seat this time we are able to locate the air jack more centrally.
This means its positioned closer to the main structure of the roll cage and therefore should not cause any flex in the shell when operated. Below is the rear mounting point.

In the Honda DC5 the firewall is angled where it meets the floor (where the conventional pedals are located) so to fit a race type pedal box. We've ordered the following AP Racing pedal box from our friends at MotorsportWheels.
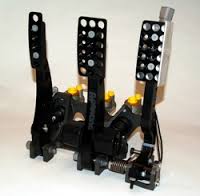
https://www.apracing.com/product_details/race_car/...
In order to fit this pedal box the floor requires modification to be a flat floor. Saluki have ensured that the boxed out section is extremely strong so that there will be no flex in the floor which could impact the effectiveness of the brake pedal.
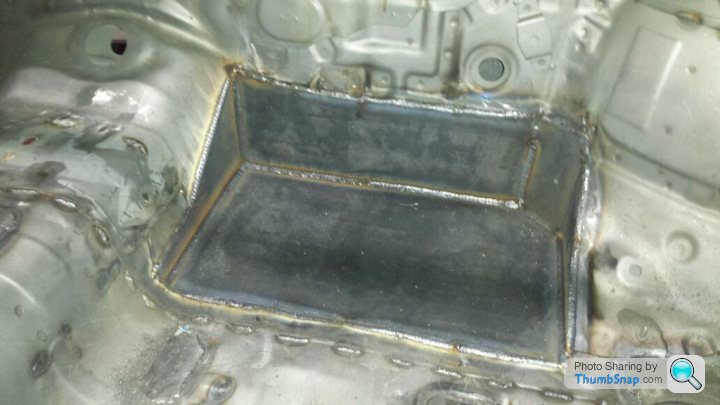
Fuel cell has been located as stated between the roll cage. This hopefully will enhance the cars balance and handling by centralising the weight and making it safer but locating the tank in what should be the safest part of the car.
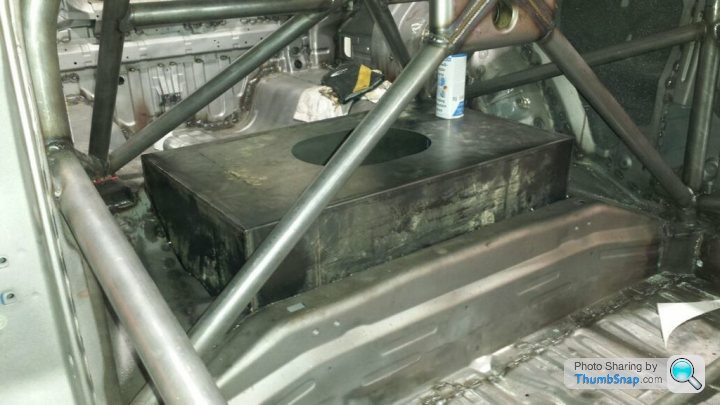
We are very happy with the Engineering work carried out by Saluki Motorsport thus far and by working with some of the best people and businesses in Dubai we are confident the end product will be amazing.
Stay tuned for part 9.
To answer a few of the questions:
Cage Design: Yes it is a custom design that complies with FIA Appendix J. Every piece of the cage has been bent by Saluki who have built multiple roll cages for Dakar style rally cars.
Build Cost: We have purposely chosen to build the car in our off season as we can get the work done quicker and at a lower cost. Our budget is substantially less than 250K AED.
Part 9
Below is a further update on the project. At this stage it looks like Saluki are only 4-days away from finishing which on reflection is a pretty fast build. 1-month from a dusty shell to a fully fabricated race car shell considering the quality and engineering thought process that was required for some components of the build is really impressive.
Although we posted this image of the rear air jack before, below is a much clearer picture showing precisely the welding and engineering quality.
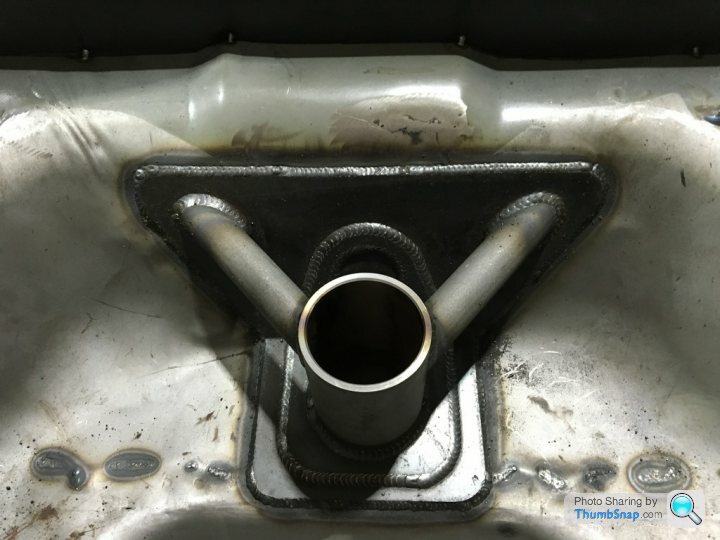
Below is the final door bracing welding
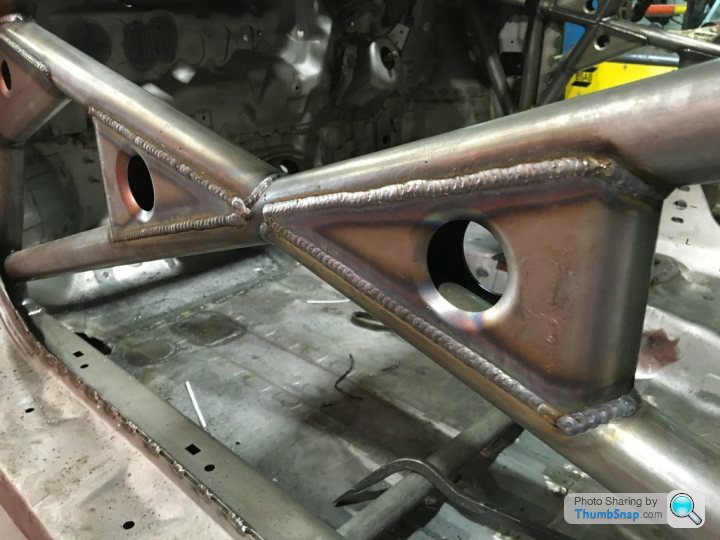
Below is where Saluki have joined the front section of the roll cage to the front strut turret.
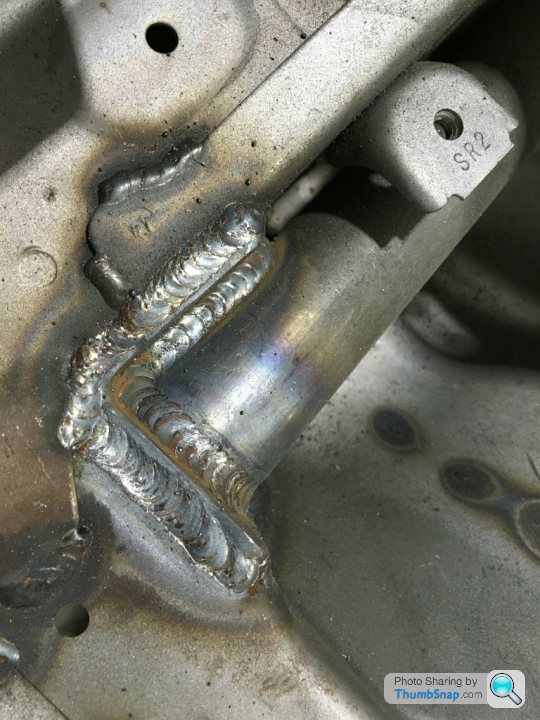
There is a second diagonal support which we posted previously.
Below is a reinforced plate which the K-tuned billet alloy gear shifter is bolted to. Captive nuts have already been welded to the underside of the plate so that the shifter is just bolted down.
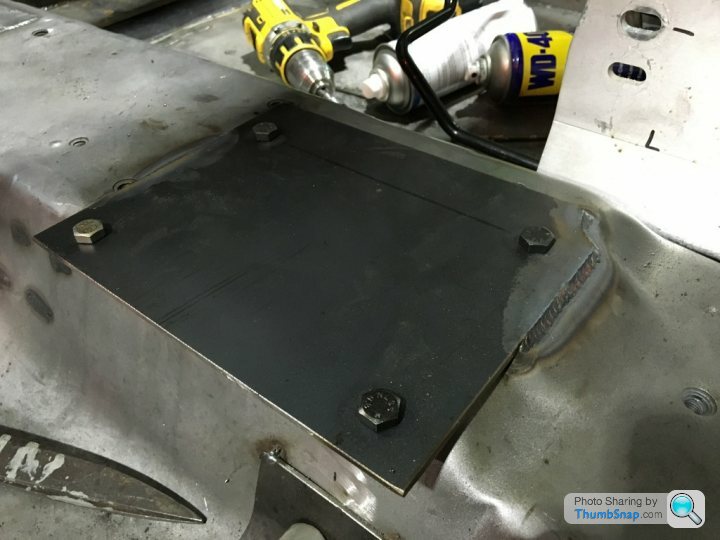
Below is the reinforced plate which the air-jack sleeve will be welded to. The second pic is the sleeve before it is fixed in place. We'll post a pic of the final installation once completed.
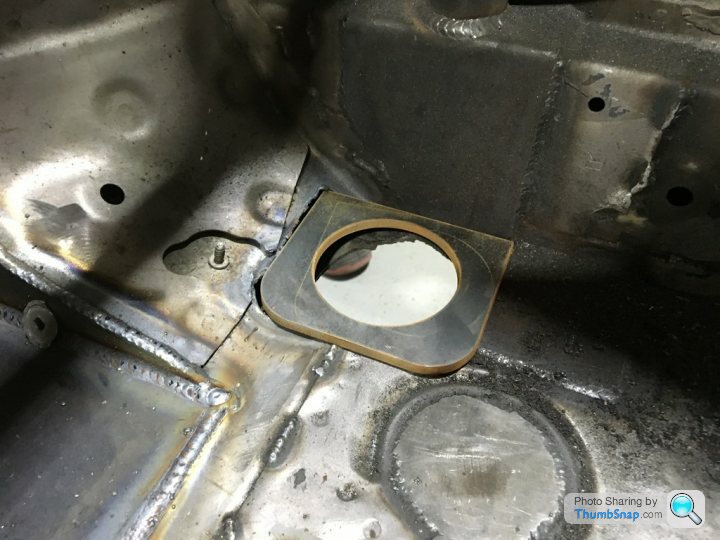
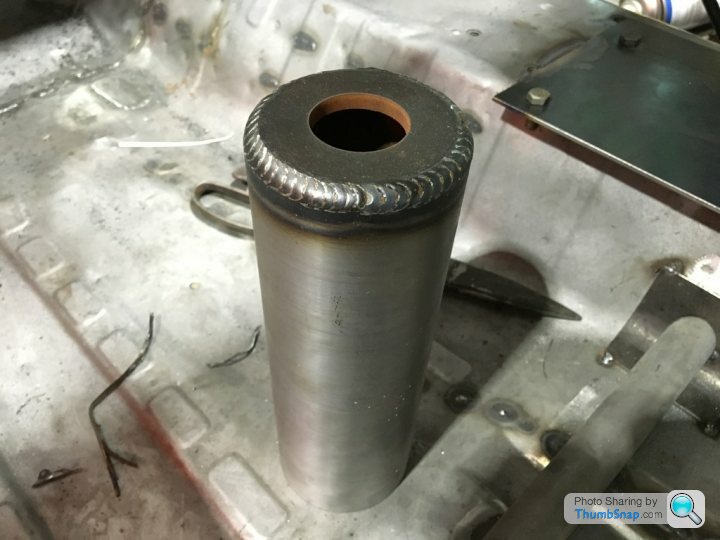
Below is the pedal box mounting plate. This again will have nuts welded to the underside and be recessed into the existing floor plate then welded all around resulting in a strong platform.
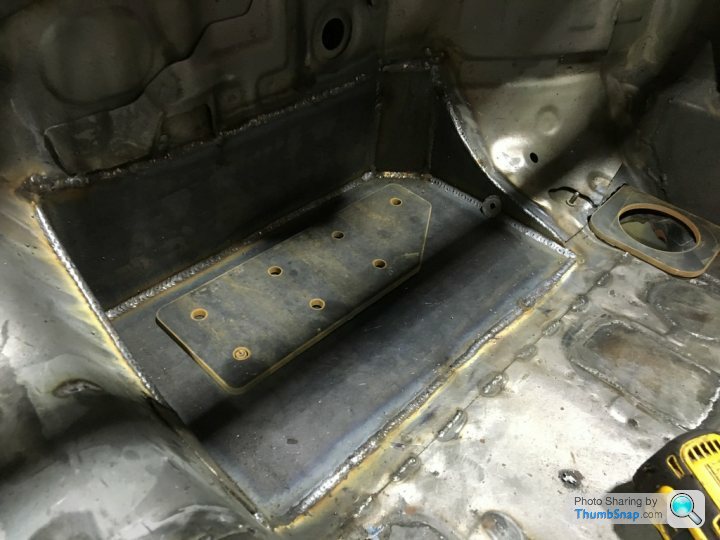
Comparison of the two soon to be one race cars.
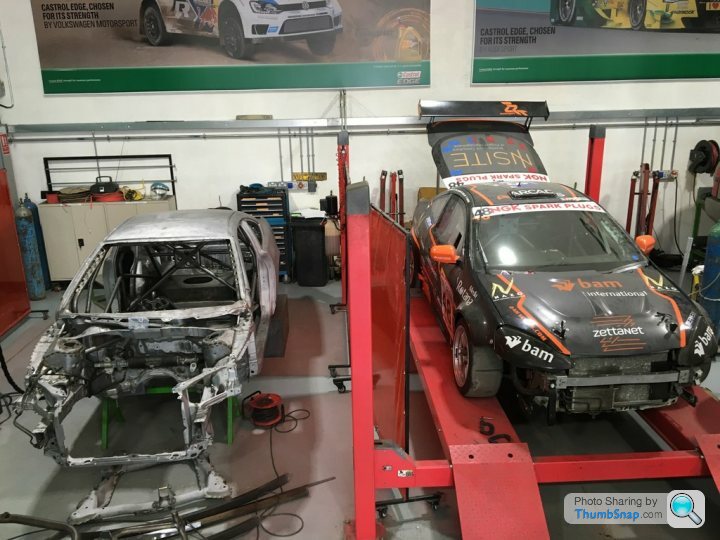
And last up a huge thank you to Robbie of Saluki pictured below who is the head fabricator and has really taken a lot of care and attention for our little project. Thanks Robbie, everyone loves the work and appreciates the efforts.
[
Cage Design: Yes it is a custom design that complies with FIA Appendix J. Every piece of the cage has been bent by Saluki who have built multiple roll cages for Dakar style rally cars.
Build Cost: We have purposely chosen to build the car in our off season as we can get the work done quicker and at a lower cost. Our budget is substantially less than 250K AED.
Part 9
Below is a further update on the project. At this stage it looks like Saluki are only 4-days away from finishing which on reflection is a pretty fast build. 1-month from a dusty shell to a fully fabricated race car shell considering the quality and engineering thought process that was required for some components of the build is really impressive.
Although we posted this image of the rear air jack before, below is a much clearer picture showing precisely the welding and engineering quality.
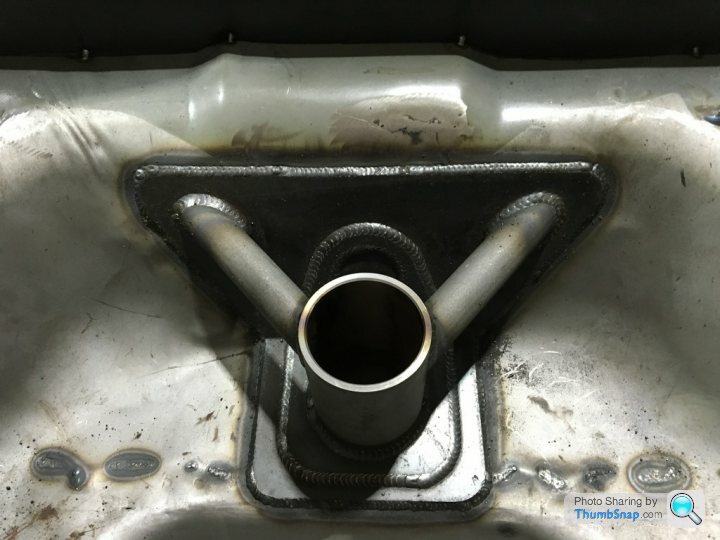
Below is the final door bracing welding
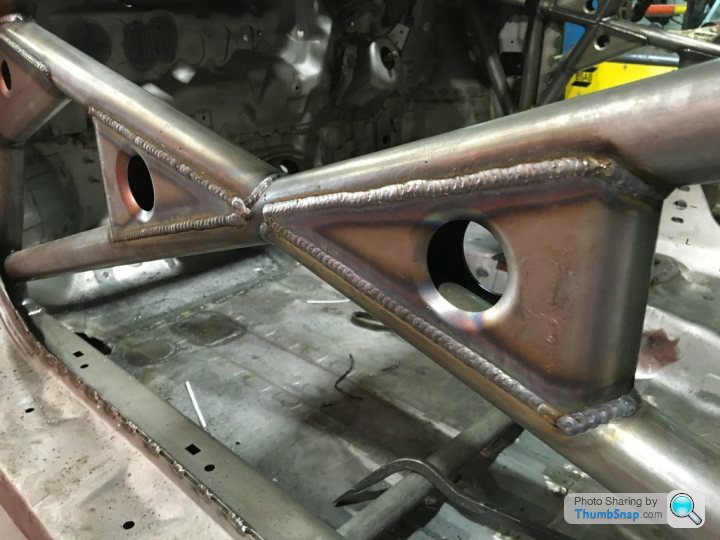
Below is where Saluki have joined the front section of the roll cage to the front strut turret.
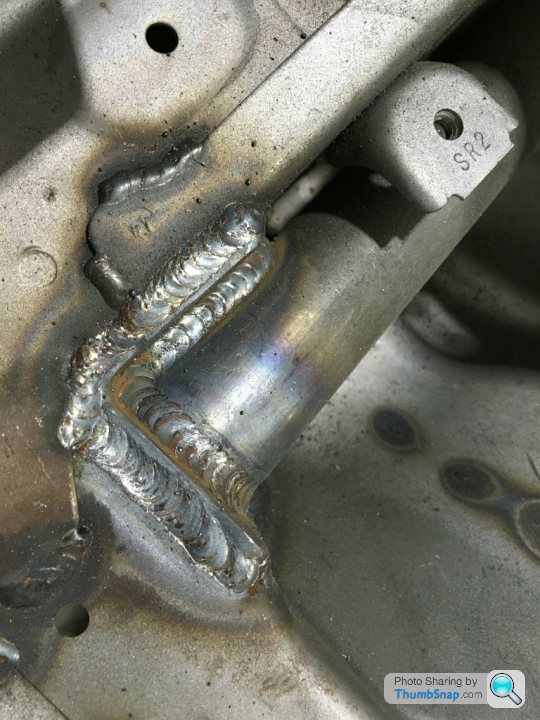
There is a second diagonal support which we posted previously.
Below is a reinforced plate which the K-tuned billet alloy gear shifter is bolted to. Captive nuts have already been welded to the underside of the plate so that the shifter is just bolted down.
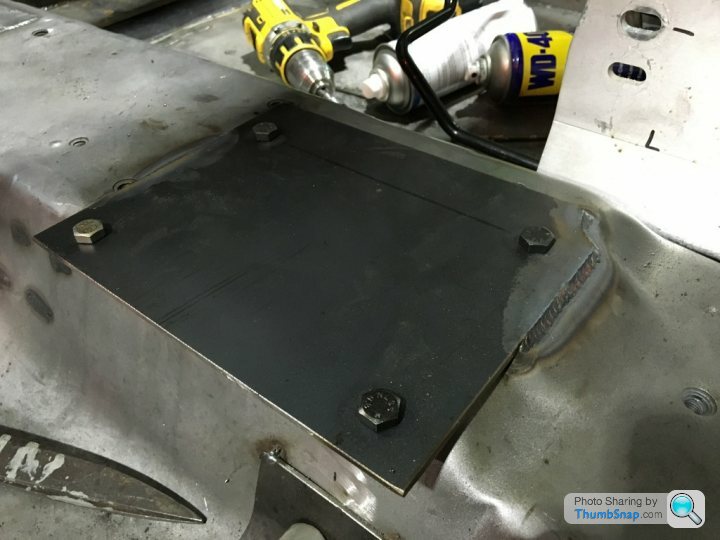
Below is the reinforced plate which the air-jack sleeve will be welded to. The second pic is the sleeve before it is fixed in place. We'll post a pic of the final installation once completed.
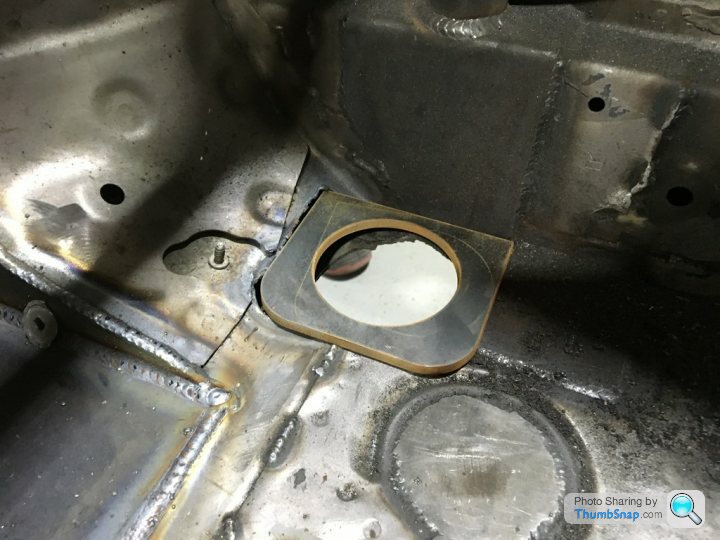
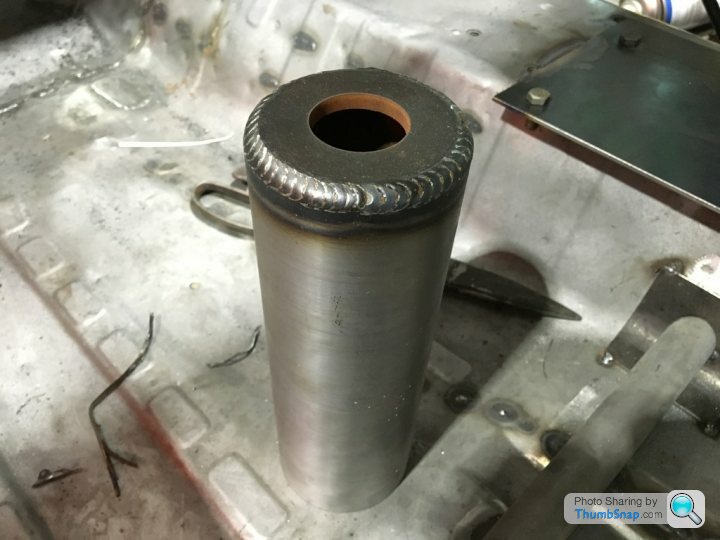
Below is the pedal box mounting plate. This again will have nuts welded to the underside and be recessed into the existing floor plate then welded all around resulting in a strong platform.
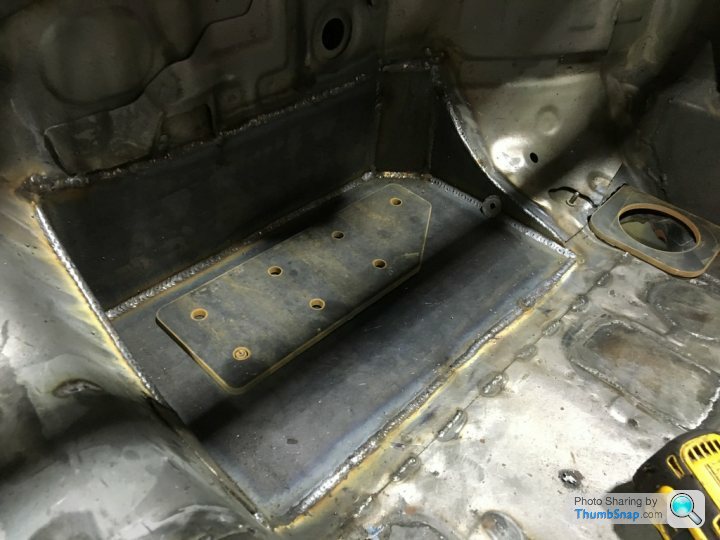
Comparison of the two soon to be one race cars.
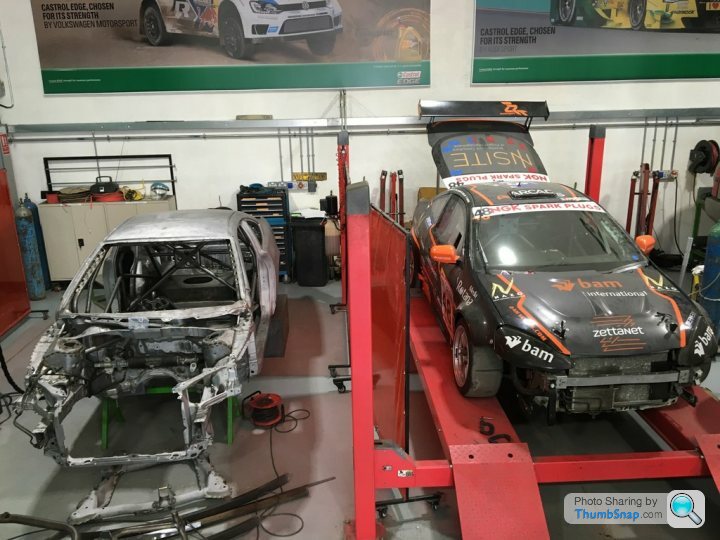
And last up a huge thank you to Robbie of Saluki pictured below who is the head fabricator and has really taken a lot of care and attention for our little project. Thanks Robbie, everyone loves the work and appreciates the efforts.
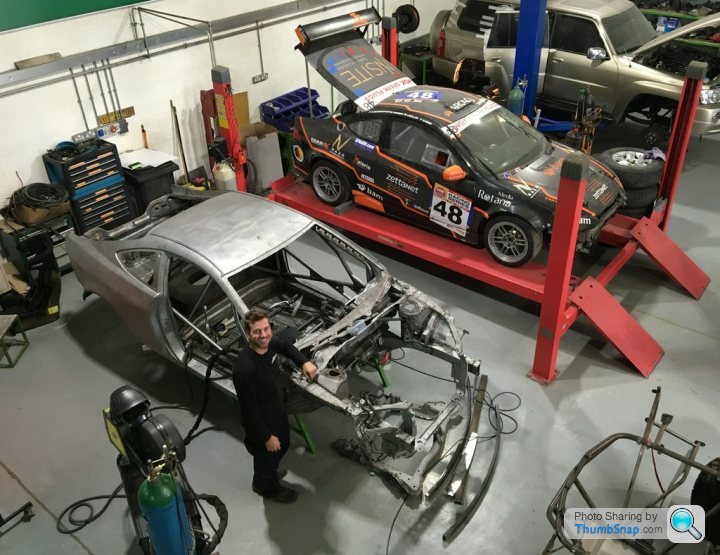
Part 10
It has been a while since the last update (I have been traveling with work, writing updates on braking and car set-up for the team web page, Ramadan, etc), but have no fear work has continued on the rebuild.
So, where were we?
Finalising the build I guess.... Well its finalised, sort of. As mentioned earlier we ordered the Corbeau Seats from Jon at Motorsport Wheels but he very kindly agreed to arrange ZRT Motorsport logo to be embroidered on the seats so the order delivery will take a little longer. Because its a different seat Saluki want to make sure the seat position and steering wheel level is perfect so the dash bar, seat bases and associated triangulated bars are not yet fully welded in case of any minor modifications required.
Below you can see what I mean:
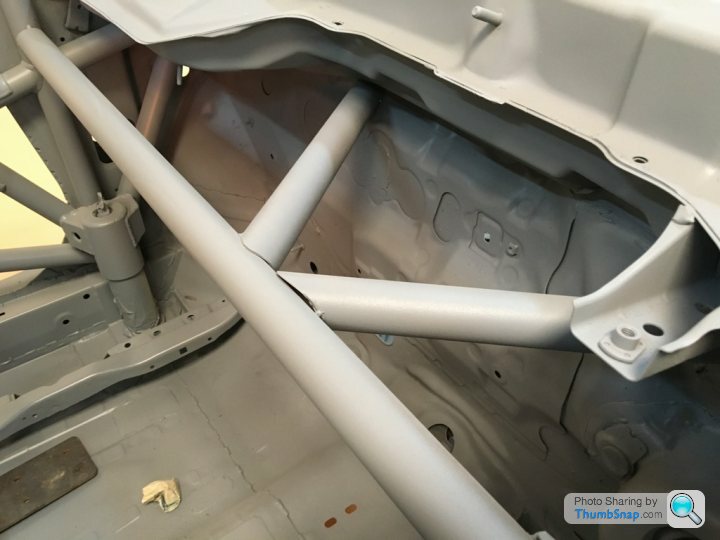
Below is the seat rail bolted in place just for the purpose of fitting but again final positioning may change. We think its unlikely but better safe than sorry:
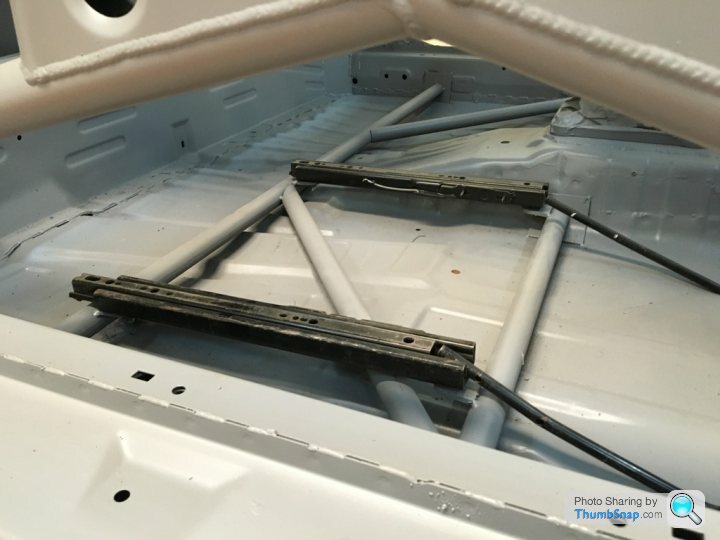
Below is the finished installation of the air jack brackets (2-front and 1-rear). You can see how the bracket is fixed to the cage and also reinforced with a strengthened plate on the floor.
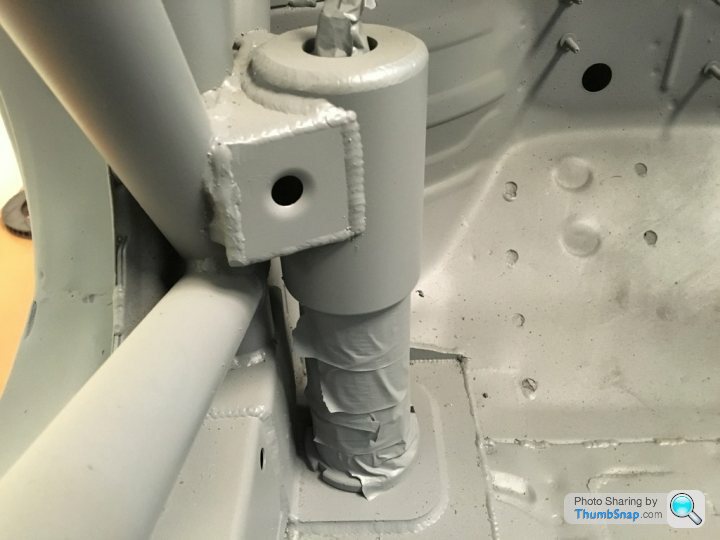
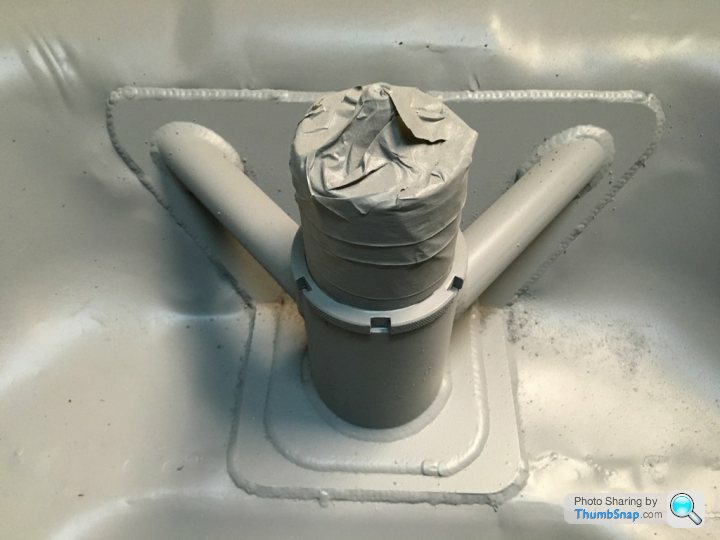
On our previous car we had a straight aluminium bar on the front of the car. This didn't provide much protection so this time Saluki fabricated a steel box section curved to provide more strength in the event of impact.
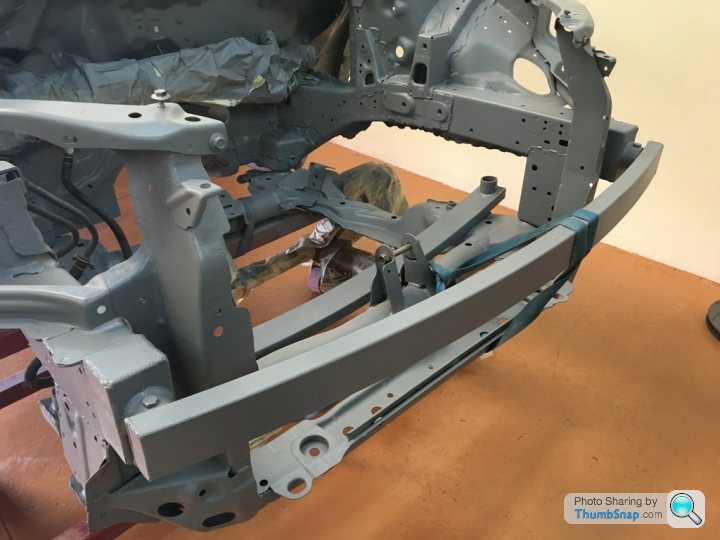
At the moment it is fixed in place with a nut and bolt but this will be replaced with a quick release pin system eventually (We have fabricated a spare in the event of damage).
Below is a close up:
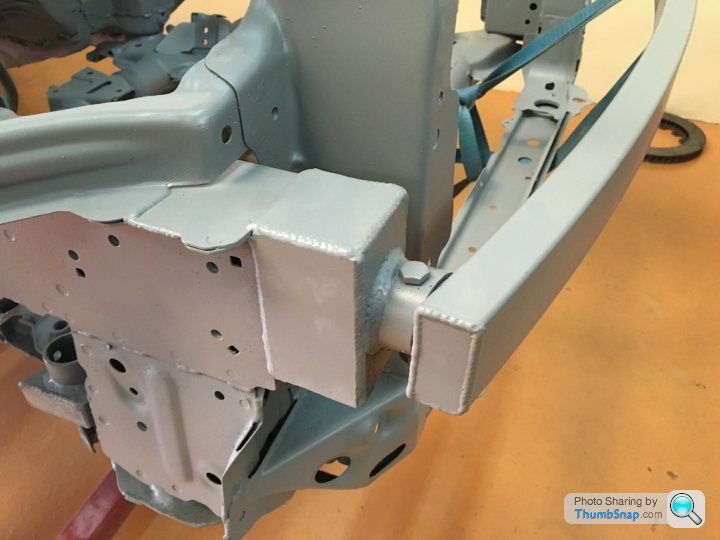
So, with the exception of some final welding we bid farewell to the Saluki Team and wish to thank Mark, Robbie, Rodel, Ben and Jordan for the excellent work. Cheers guys 😊
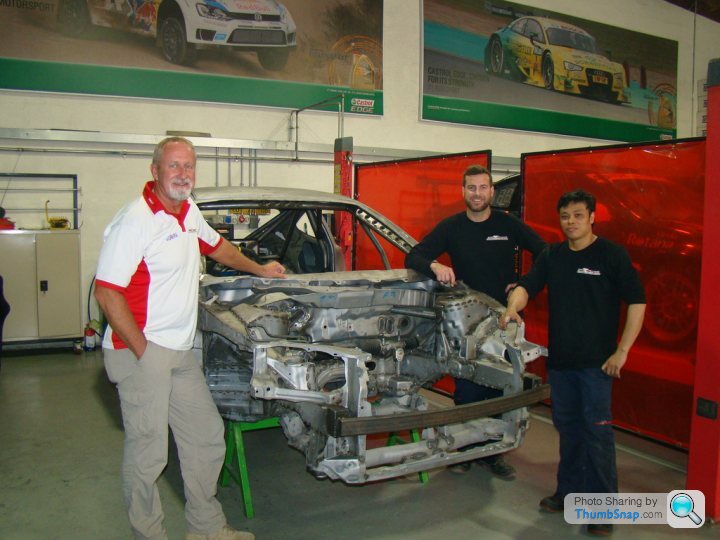
It has been a while since the last update (I have been traveling with work, writing updates on braking and car set-up for the team web page, Ramadan, etc), but have no fear work has continued on the rebuild.
So, where were we?
Finalising the build I guess.... Well its finalised, sort of. As mentioned earlier we ordered the Corbeau Seats from Jon at Motorsport Wheels but he very kindly agreed to arrange ZRT Motorsport logo to be embroidered on the seats so the order delivery will take a little longer. Because its a different seat Saluki want to make sure the seat position and steering wheel level is perfect so the dash bar, seat bases and associated triangulated bars are not yet fully welded in case of any minor modifications required.
Below you can see what I mean:
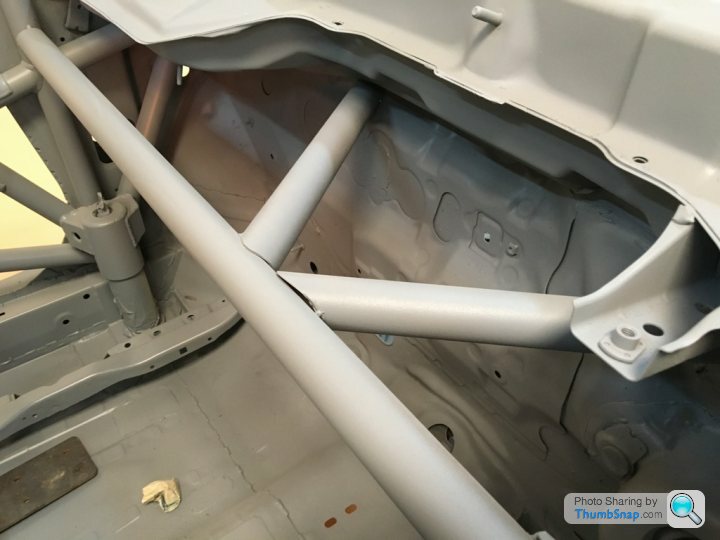
Below is the seat rail bolted in place just for the purpose of fitting but again final positioning may change. We think its unlikely but better safe than sorry:
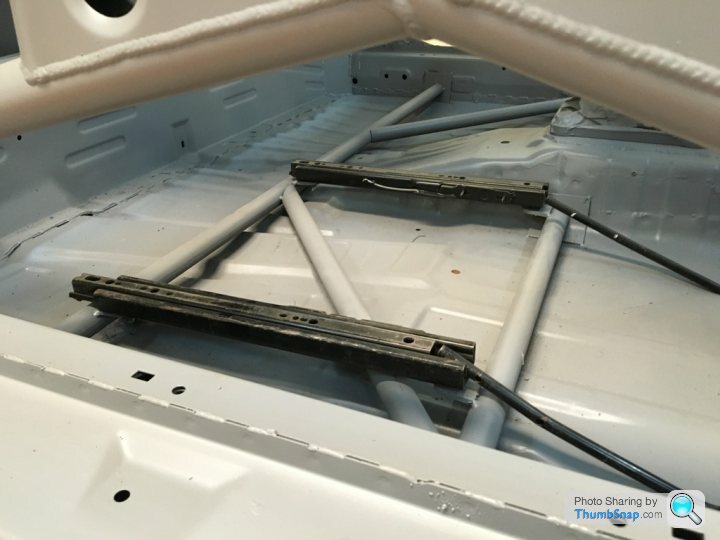
Below is the finished installation of the air jack brackets (2-front and 1-rear). You can see how the bracket is fixed to the cage and also reinforced with a strengthened plate on the floor.
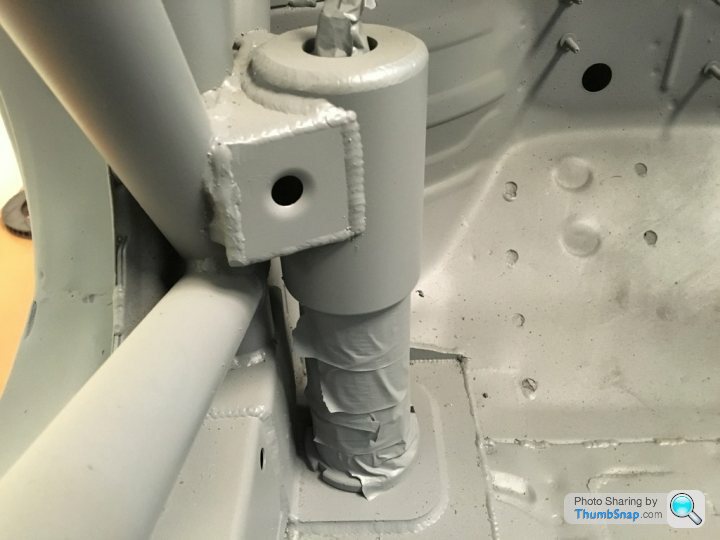
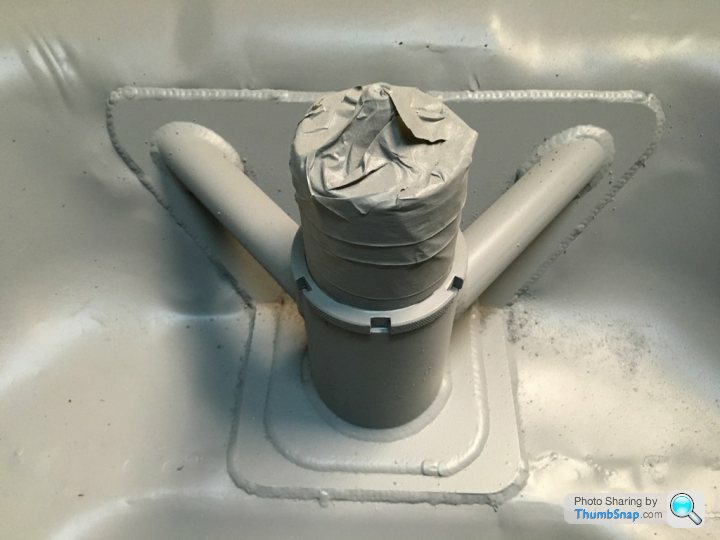
On our previous car we had a straight aluminium bar on the front of the car. This didn't provide much protection so this time Saluki fabricated a steel box section curved to provide more strength in the event of impact.
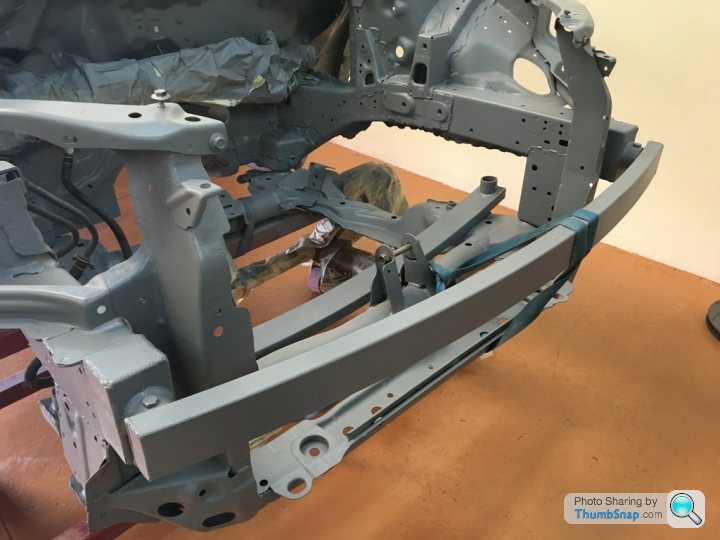
At the moment it is fixed in place with a nut and bolt but this will be replaced with a quick release pin system eventually (We have fabricated a spare in the event of damage).
Below is a close up:
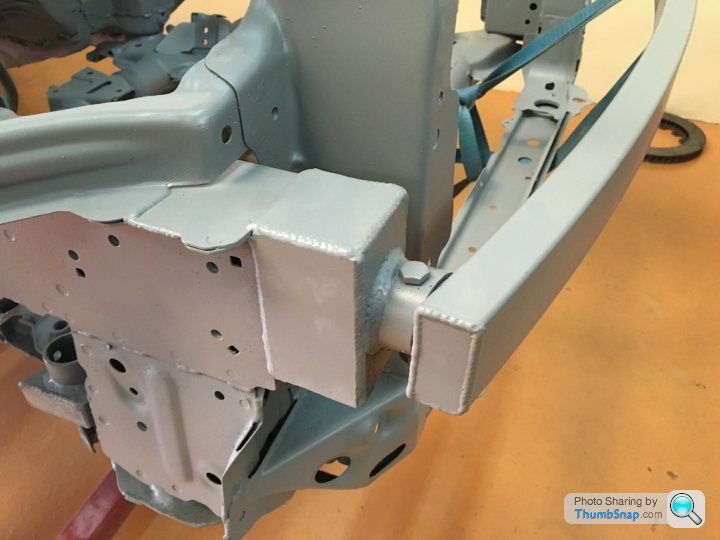
So, with the exception of some final welding we bid farewell to the Saluki Team and wish to thank Mark, Robbie, Rodel, Ben and Jordan for the excellent work. Cheers guys 😊
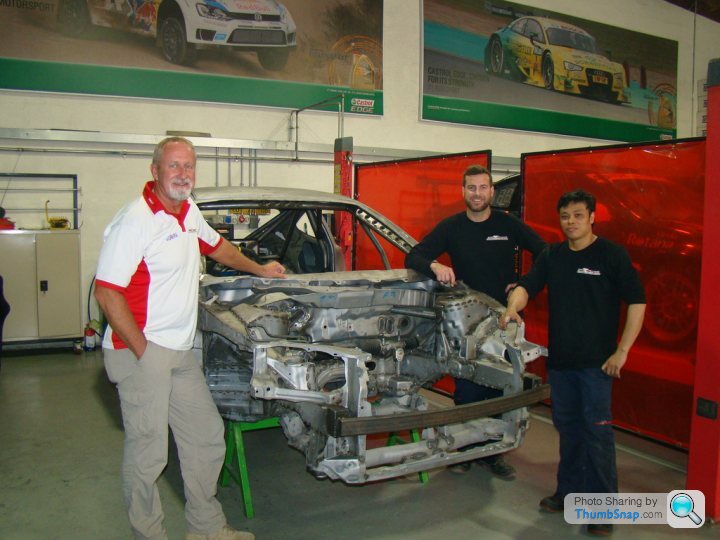
Part 11
When it rains it pours… Nothing for weeks and now two updates at once.
Next stop on our project was to hand the car over to Julian at A-Tech to do the build. The only exception is that our engine will be built by TGMsport in UK.
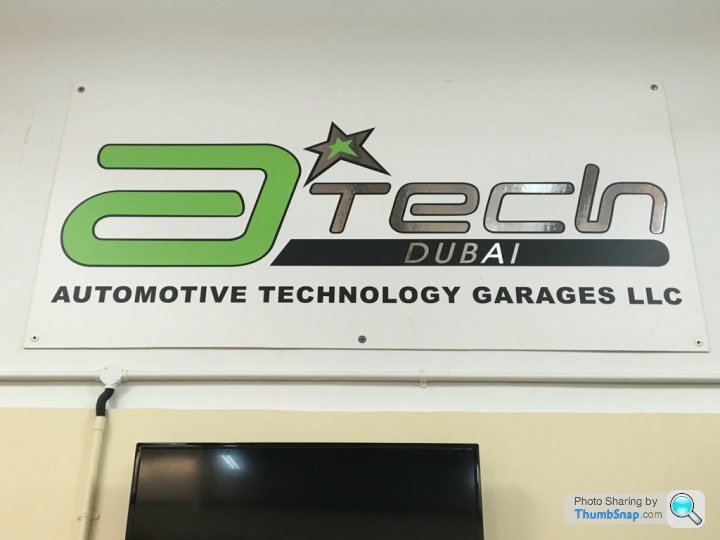
First task was to undertake a primer coat so that the shell is protected. This is only a temporary coat which will eventually be rubbed down before final priming and painting.
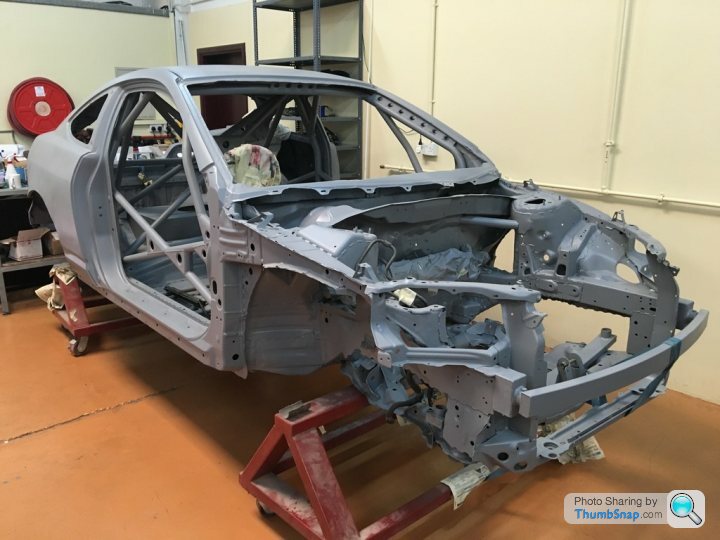
The primer coat was finished pretty quickly and back to A-Tech to plan what is going where.
On the downside the new primer highlighted all the damage caused to the shell by the shot blasting (particularly rear 3/4 panels and roof). On the bright side A-Tech have an excellent panel beater who will spend a day taking the worst out of it and the rest will be smoothed out with a light skim of filler in select places.
Its quite evident in the below photo on the rear panel:
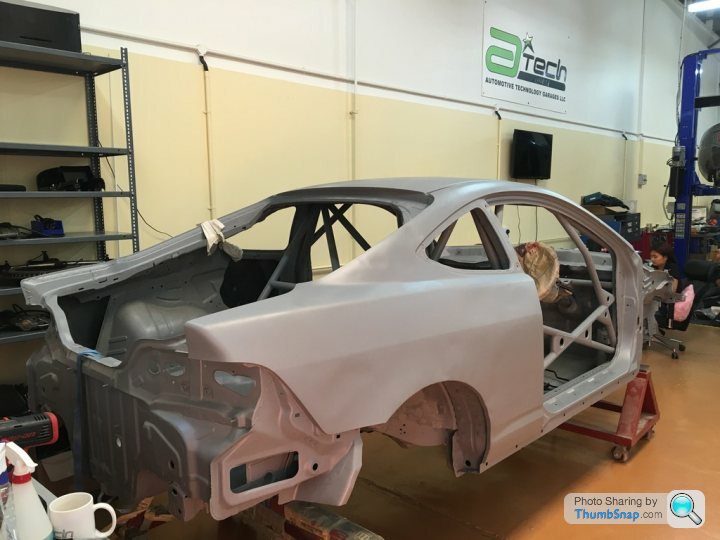
The next update will be the strip down of the old car and some details of what new technology we intend to use in the new car.
Till then… Ciao
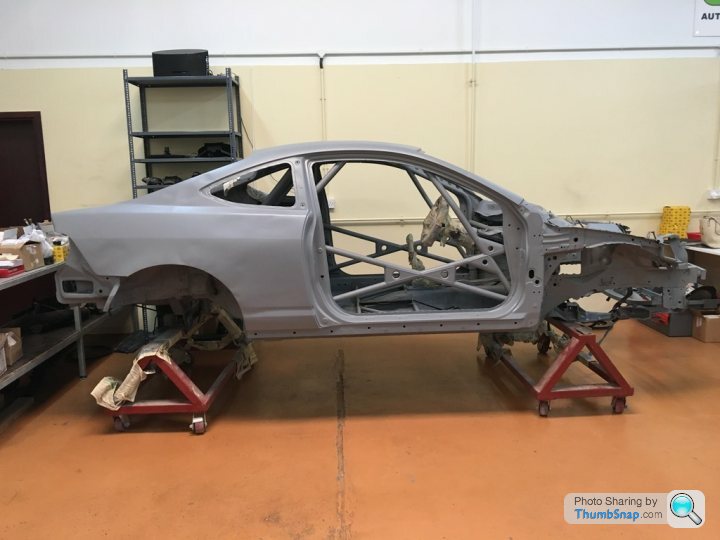
When it rains it pours… Nothing for weeks and now two updates at once.
Next stop on our project was to hand the car over to Julian at A-Tech to do the build. The only exception is that our engine will be built by TGMsport in UK.
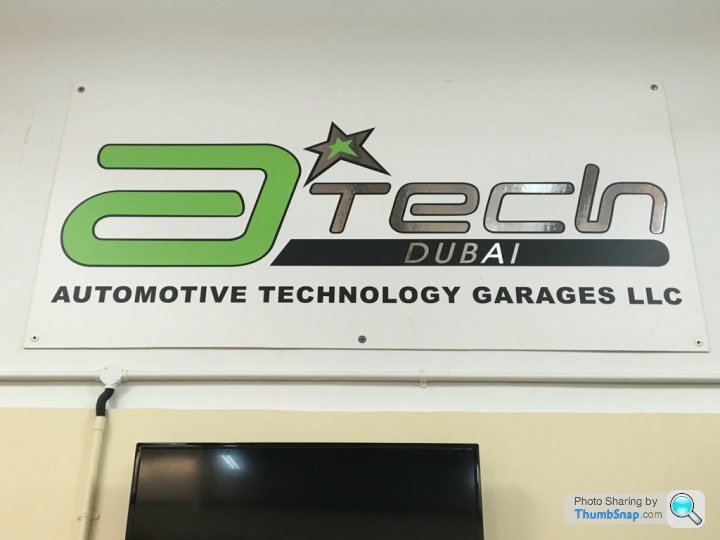
First task was to undertake a primer coat so that the shell is protected. This is only a temporary coat which will eventually be rubbed down before final priming and painting.
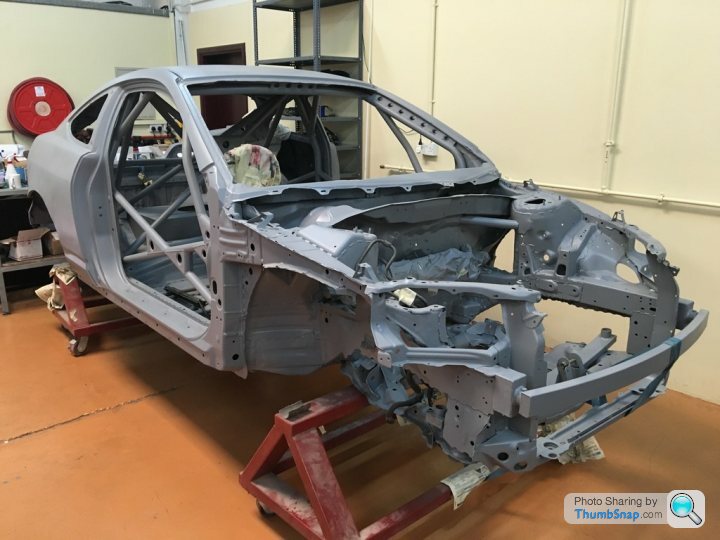
The primer coat was finished pretty quickly and back to A-Tech to plan what is going where.
On the downside the new primer highlighted all the damage caused to the shell by the shot blasting (particularly rear 3/4 panels and roof). On the bright side A-Tech have an excellent panel beater who will spend a day taking the worst out of it and the rest will be smoothed out with a light skim of filler in select places.
Its quite evident in the below photo on the rear panel:
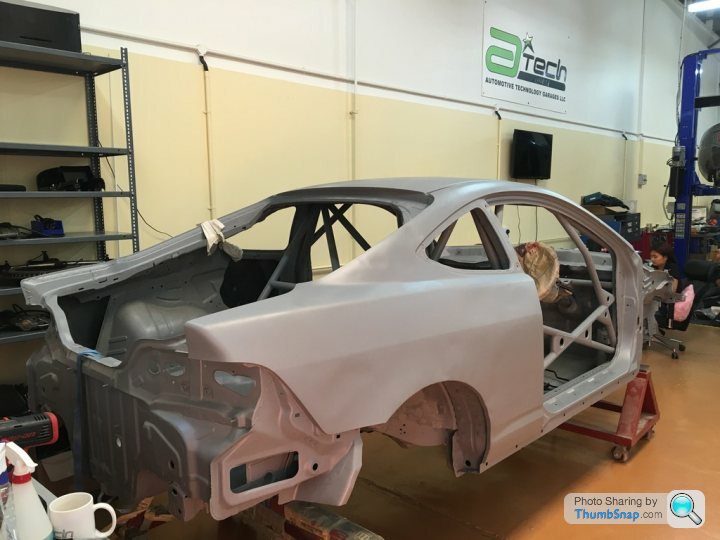
The next update will be the strip down of the old car and some details of what new technology we intend to use in the new car.
Till then… Ciao
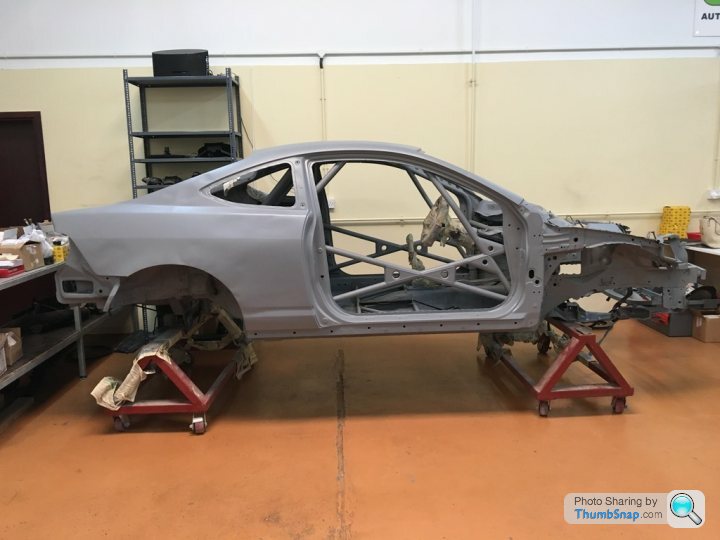
Part 12
Our original race car has been efficiently stripped to a shell. Just the doors, hatch, bonnet, wings, fuel cell and subframe remain to be removed.
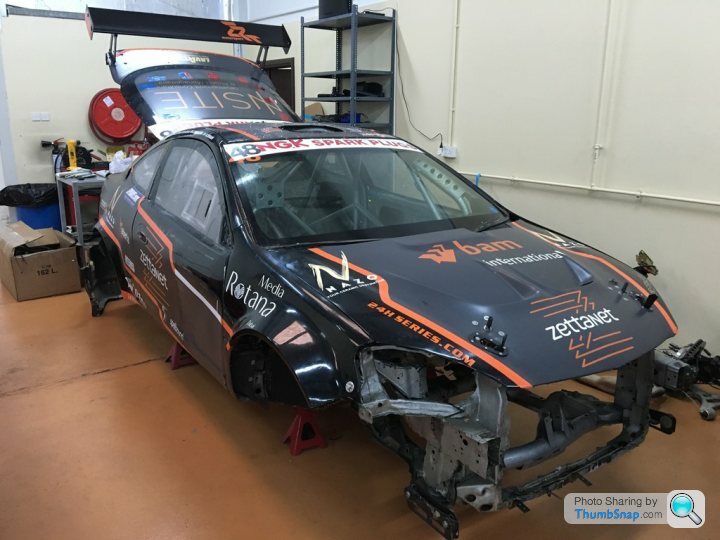
The dash will be reused however re-organised to be a nice neat enduro spec. incorporating all the requirements in a cartek power control panel. Plus we will incorporate all of the Creventic 24Hrs gadgets such as the driver ID switch.
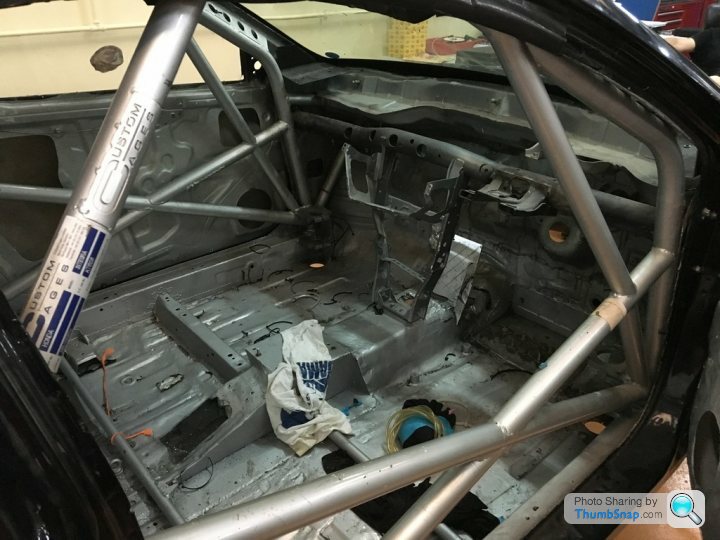
So, this is probably the last photos of the old car before it goes off to the big scrap heaven for race cars.
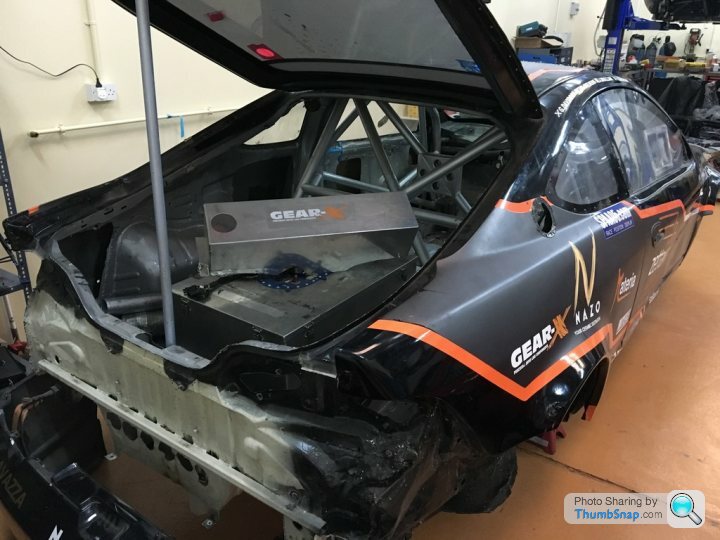
This was our car where it first originated (Sepang) in 2008. The red & white no. 27 car.
https://www.youtube.com/watch?v=sqI3jSiaZ7M
Its had a hard life since to be fair
Ciao for another while
Our original race car has been efficiently stripped to a shell. Just the doors, hatch, bonnet, wings, fuel cell and subframe remain to be removed.
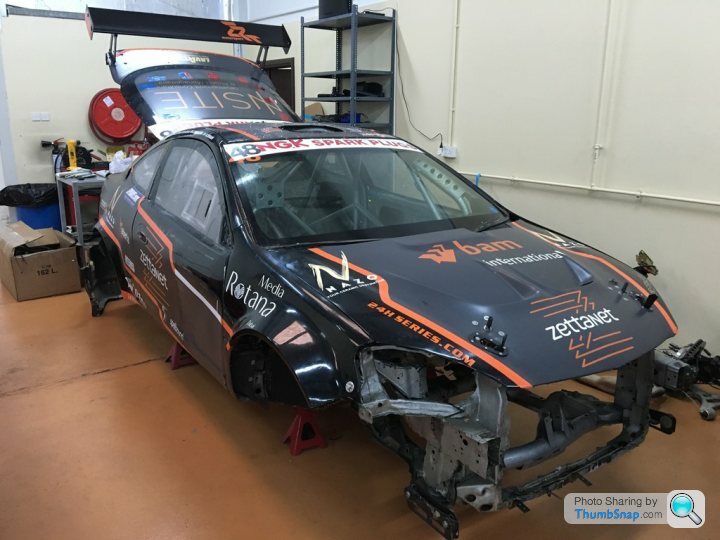
The dash will be reused however re-organised to be a nice neat enduro spec. incorporating all the requirements in a cartek power control panel. Plus we will incorporate all of the Creventic 24Hrs gadgets such as the driver ID switch.
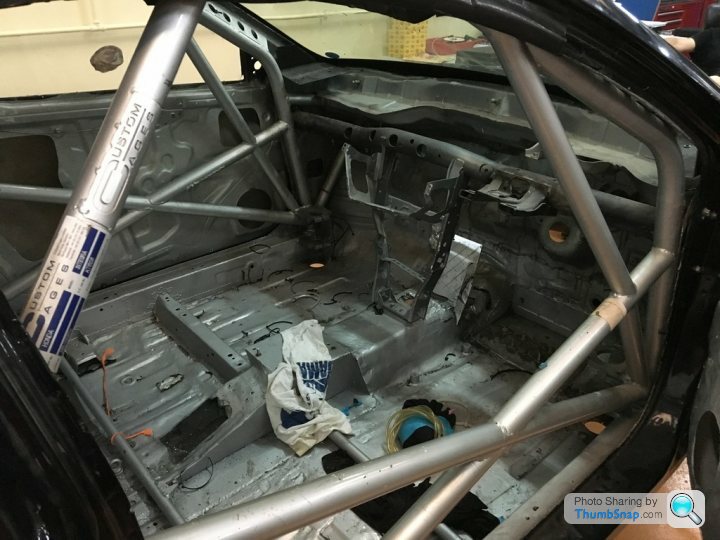
So, this is probably the last photos of the old car before it goes off to the big scrap heaven for race cars.
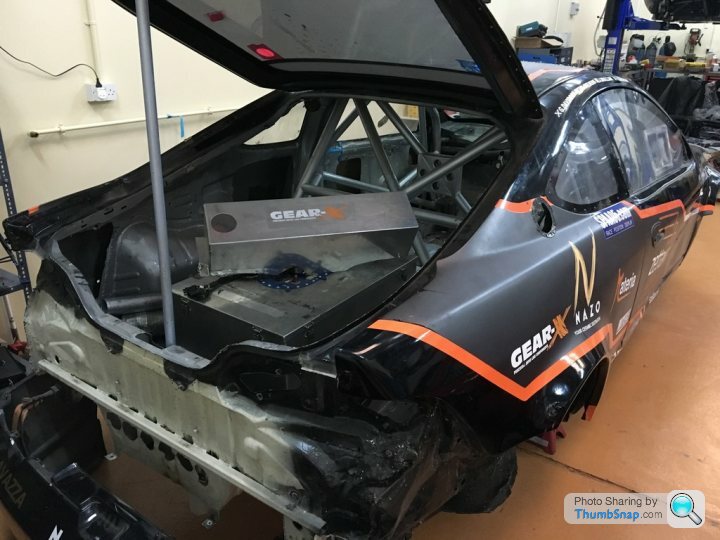
This was our car where it first originated (Sepang) in 2008. The red & white no. 27 car.
https://www.youtube.com/watch?v=sqI3jSiaZ7M
Its had a hard life since to be fair

Ciao for another while
Part 13
As previously mentioned we were waiting on the new seat and pedal box to test-fit with the steering column position before finally welding the remaining roll cage bars. Thanks to Jon Simmonds at MW (MotorsportWheels) the fantastic Corbeau seats arrived fully branded (drivers seat is carbon fibre and the passenger seat is GRP). We opted for the ‘Pro-series’ as we couldn’t fit the ‘Revenge’ seat due to the basic ergonomics of the roll cage design within this shell.
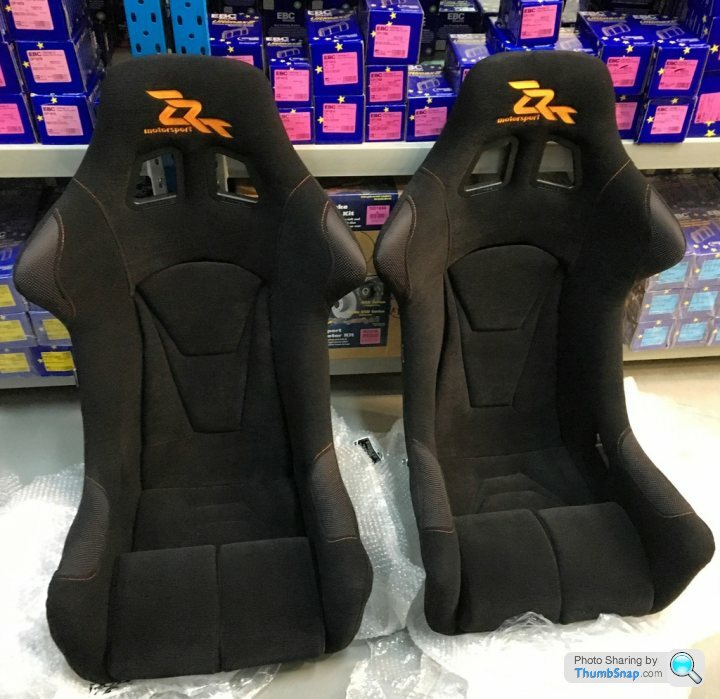
To be honest the Pro-series suits us better. It is easier for the driver to get in and out and gives better peripheral vision, with 90+ cars in the race this is essential. From a marketing perspective the logo will be more visual also.
We did an initial placement along with the steering column, the new AP Racing pedal box (again courtesy of MotorsportWheels) and the gear selector (K-tuned billet shifter). The seat seems a little high. This is partly because we run it on an FIA approved slider rail (10mm), partly because the fact we use the rail we cant put the Corbeau seat on its lowest setting on the side-mount brackets and partly because the actual seat base fixing rails could be lower in the floor. The latter seems to be the easiest fix. It will involve some cutting just behind where the centre console would be but we’ll explain this later with photos.
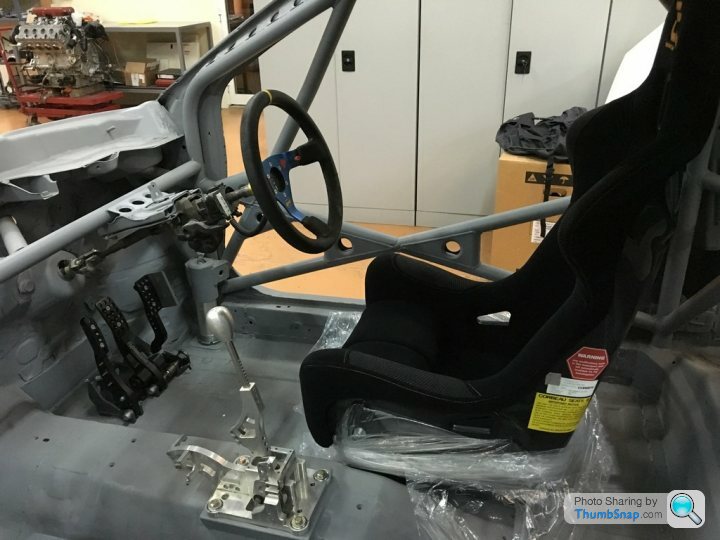
?
You can see in the below image how the seat sits perfectly within the roll cage.
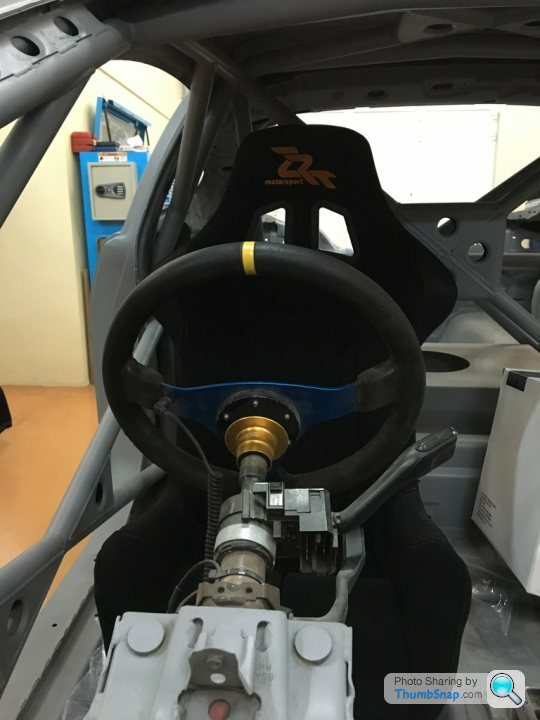
?
Now that all those important components are measured up and positioning is agreed, the car is off to Saluki tomorrow for final welding.
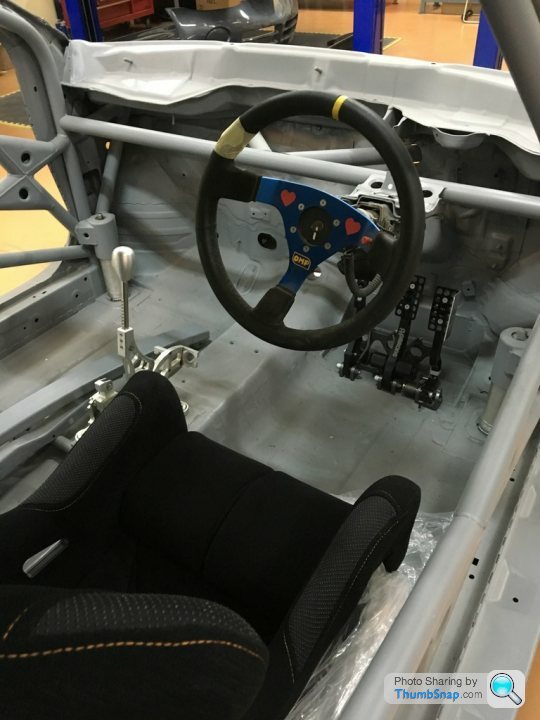
?
Once the welding is complete the interior, underside and inner wings will be painted metallic grey. Stay tuned for that.
Last note for this update is to say goodbye to our old ZRT #48 shell… which incidentally on picking through the cracked paint on the roof we managed to discover that it started out life as a black car, was then painted metallic blue, red, white, lime green and eventually back to black (twice). If you see the layers it was like a time team geological survey.
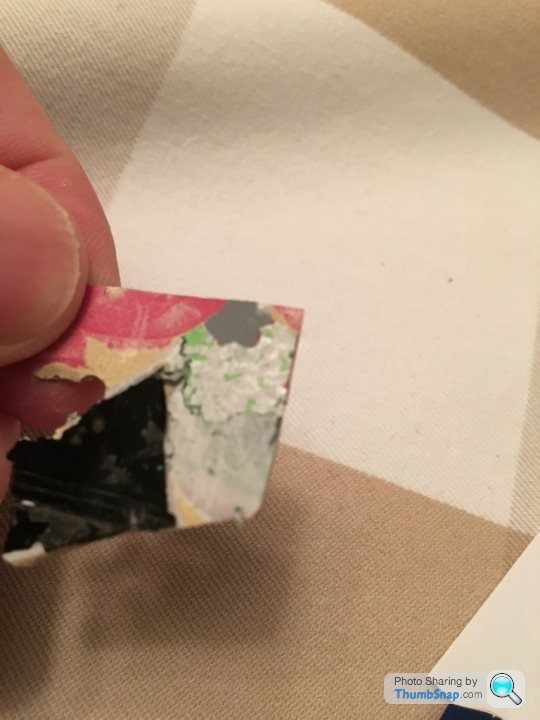
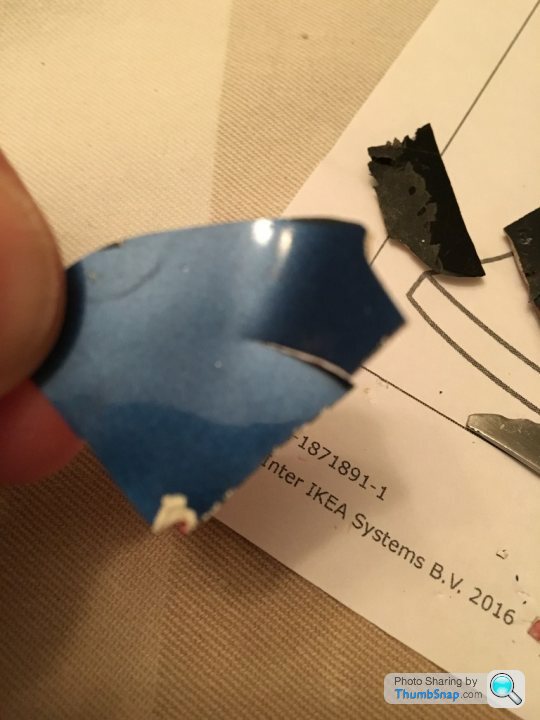
So it's good by old shell...
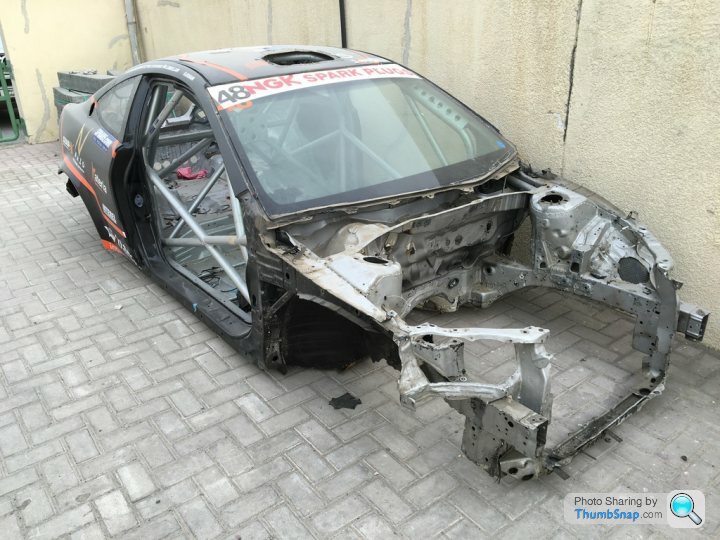
As previously mentioned we were waiting on the new seat and pedal box to test-fit with the steering column position before finally welding the remaining roll cage bars. Thanks to Jon Simmonds at MW (MotorsportWheels) the fantastic Corbeau seats arrived fully branded (drivers seat is carbon fibre and the passenger seat is GRP). We opted for the ‘Pro-series’ as we couldn’t fit the ‘Revenge’ seat due to the basic ergonomics of the roll cage design within this shell.
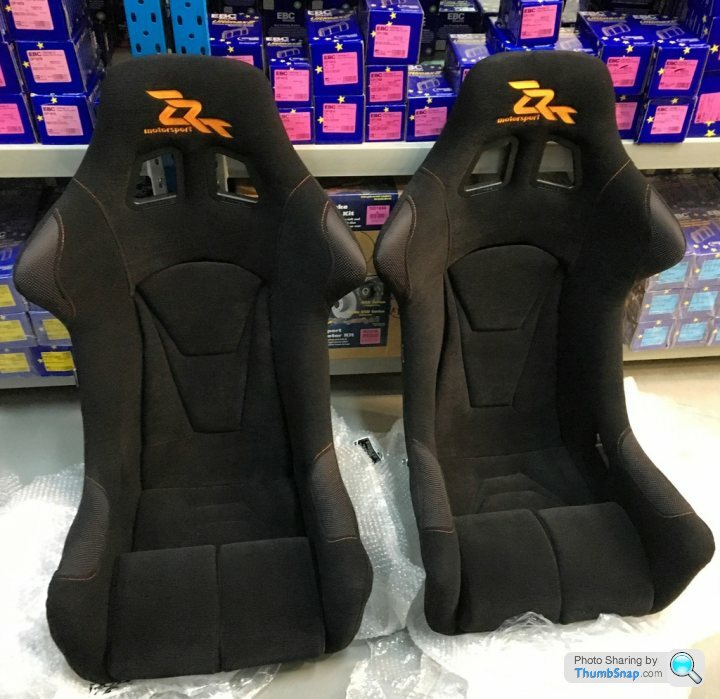
To be honest the Pro-series suits us better. It is easier for the driver to get in and out and gives better peripheral vision, with 90+ cars in the race this is essential. From a marketing perspective the logo will be more visual also.
We did an initial placement along with the steering column, the new AP Racing pedal box (again courtesy of MotorsportWheels) and the gear selector (K-tuned billet shifter). The seat seems a little high. This is partly because we run it on an FIA approved slider rail (10mm), partly because the fact we use the rail we cant put the Corbeau seat on its lowest setting on the side-mount brackets and partly because the actual seat base fixing rails could be lower in the floor. The latter seems to be the easiest fix. It will involve some cutting just behind where the centre console would be but we’ll explain this later with photos.
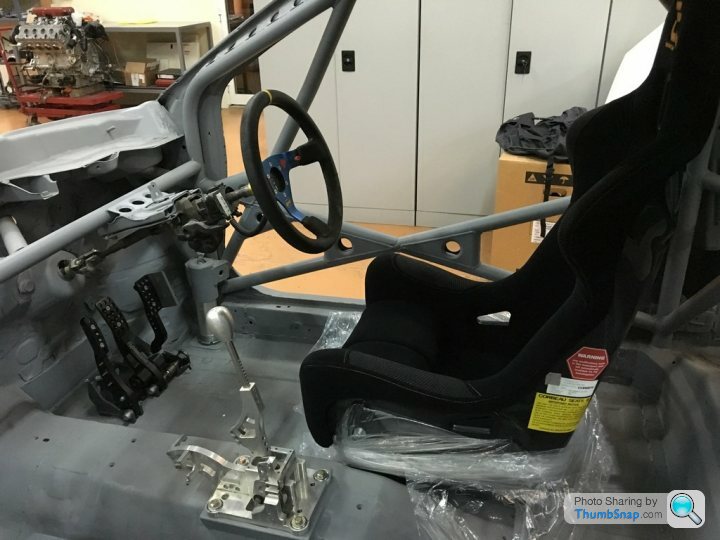
?
You can see in the below image how the seat sits perfectly within the roll cage.
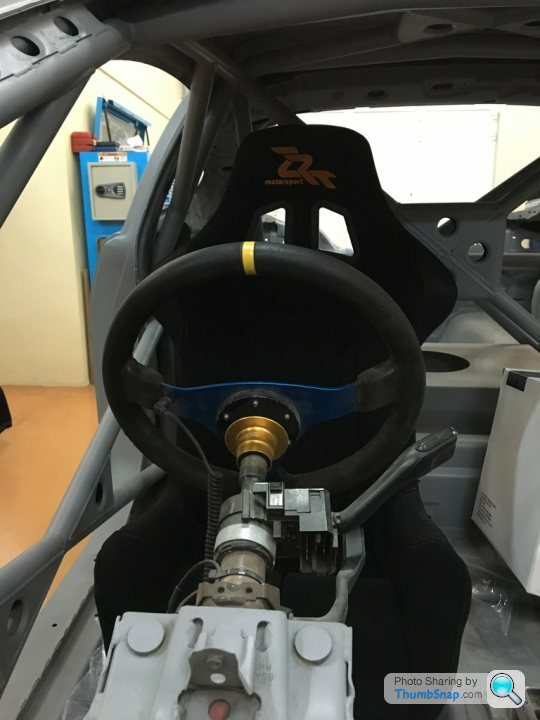
?
Now that all those important components are measured up and positioning is agreed, the car is off to Saluki tomorrow for final welding.
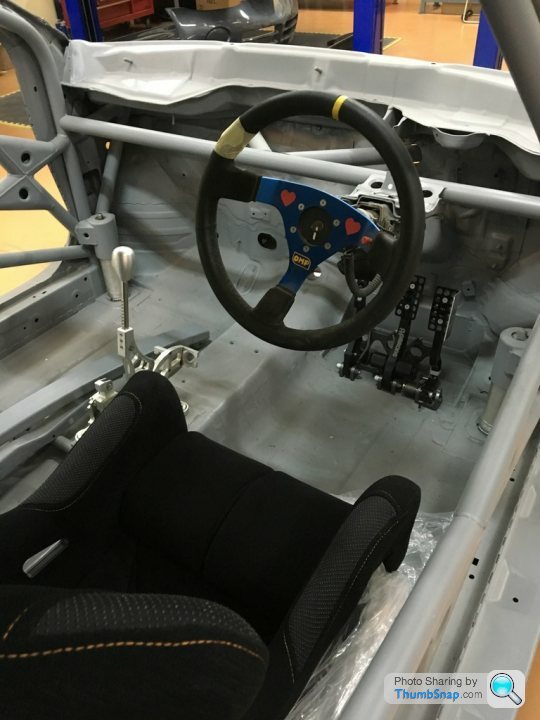
?
Once the welding is complete the interior, underside and inner wings will be painted metallic grey. Stay tuned for that.
Last note for this update is to say goodbye to our old ZRT #48 shell… which incidentally on picking through the cracked paint on the roof we managed to discover that it started out life as a black car, was then painted metallic blue, red, white, lime green and eventually back to black (twice). If you see the layers it was like a time team geological survey.
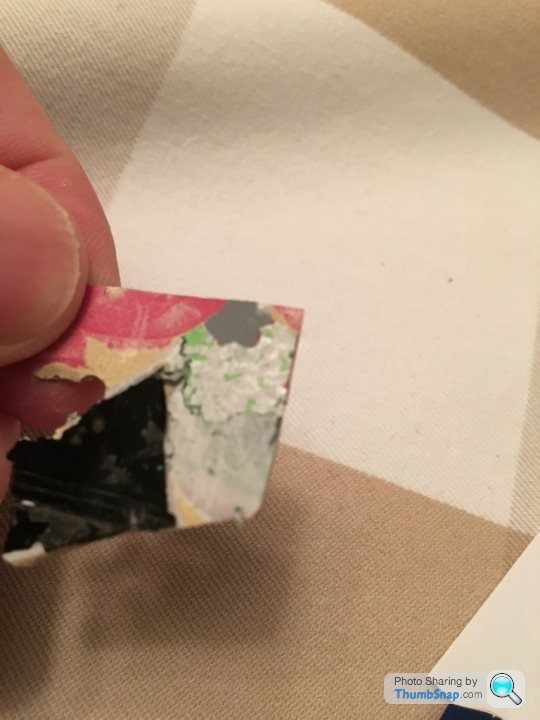
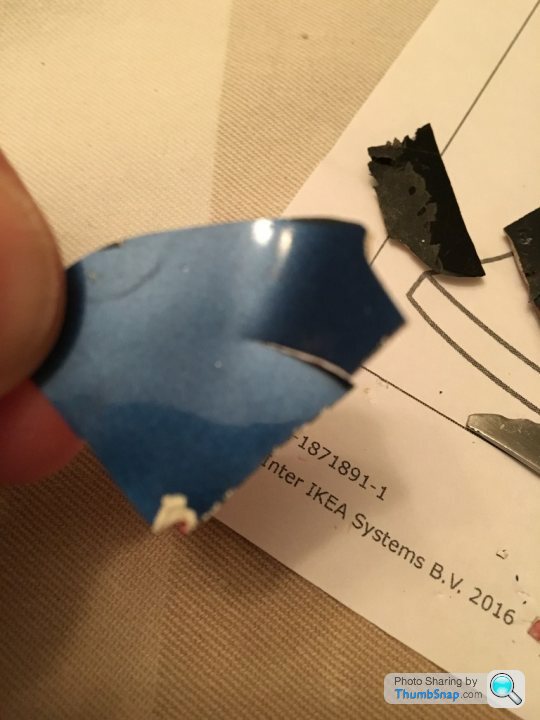
So it's good by old shell...
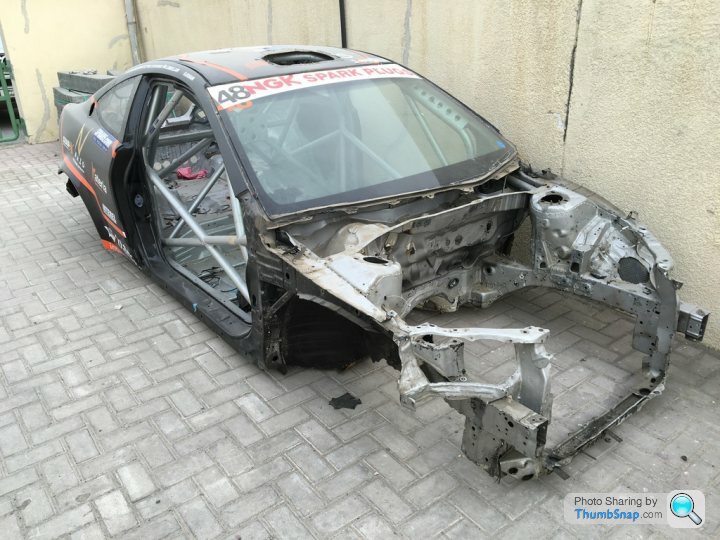
Part 14
I think this will be the last update on the fabrication works as everything seems to be finished. A big thank you to Robbie and Mark at Saluki for the speedy, quality and efficient service. Its worth mentioning that they kept us updated at all times and they took a genuine interest in our project which is reflected in the quality of the Engineering.
So first up the seat rails were fully welded.
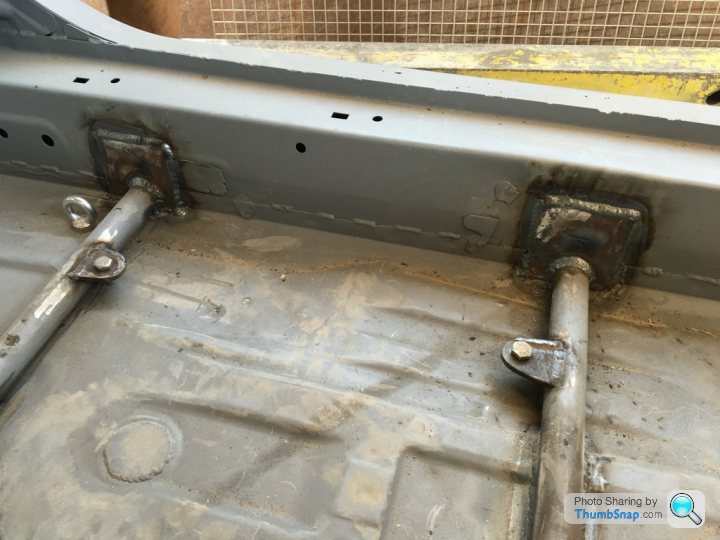
The lugs were also strengthened using fillet gusset pieces.
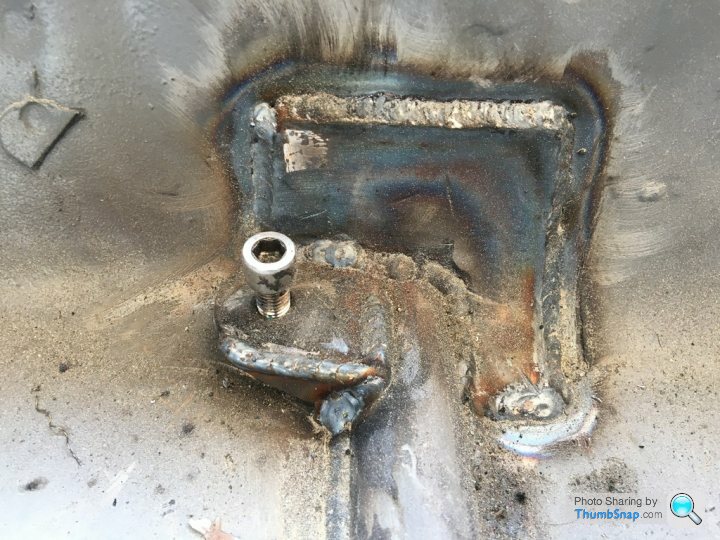
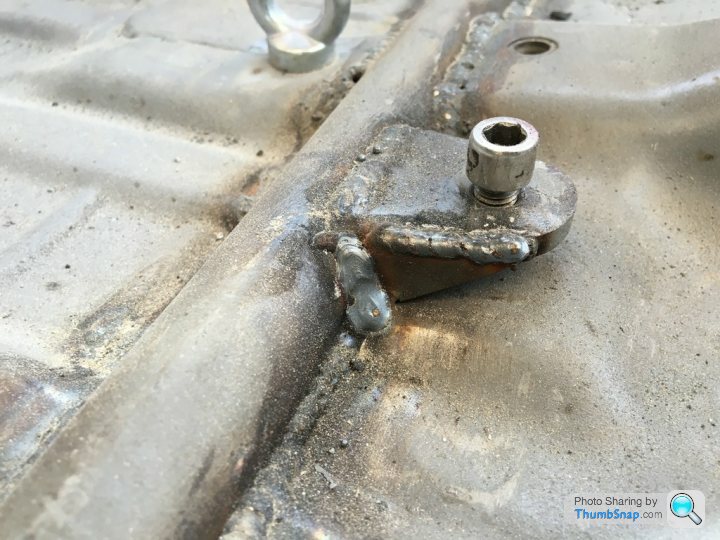
So with the seat positioned and fixed the pedal box reinforced floor plate was installed. Note the multiple holes are for flexibility in terms of the fitment position of the pedal box. They have been fitted with bolts to the underside so it is easy to install/remove/refit the pedal box.
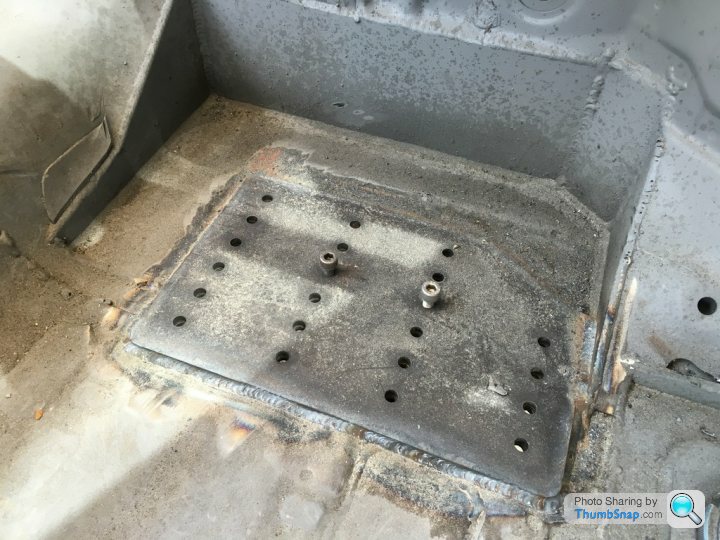
Saluki then firmed up the steering column position and finalised the welding.
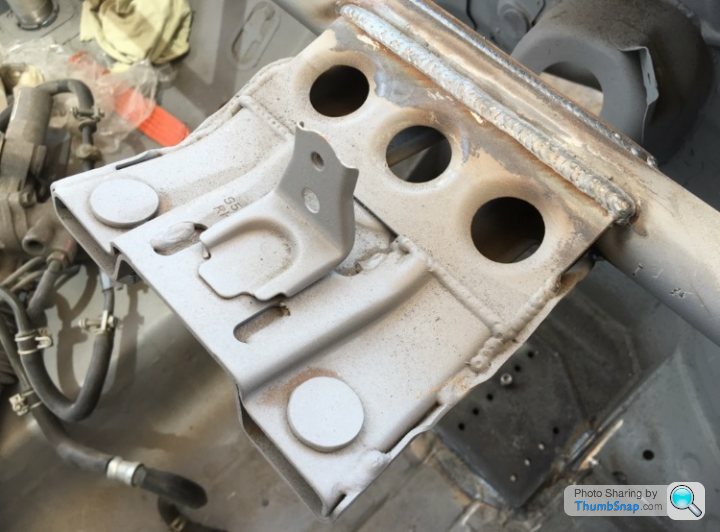
This then enabled the finalisation of the front CDS bar and the triangulated bars to the strut turrets.
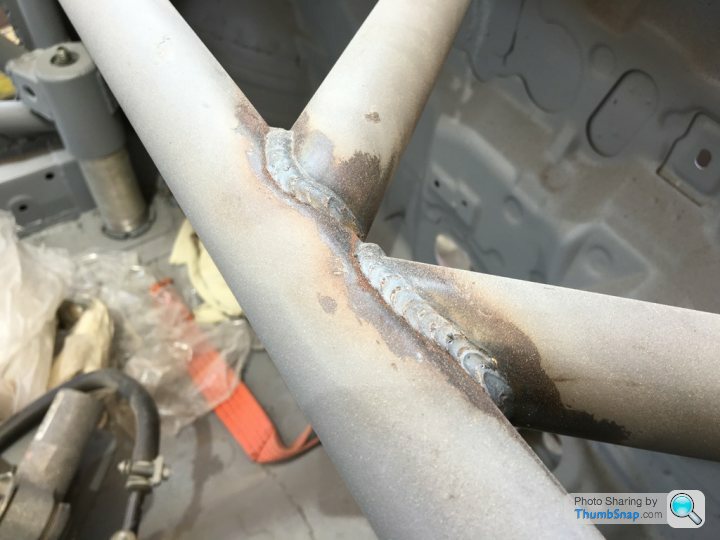
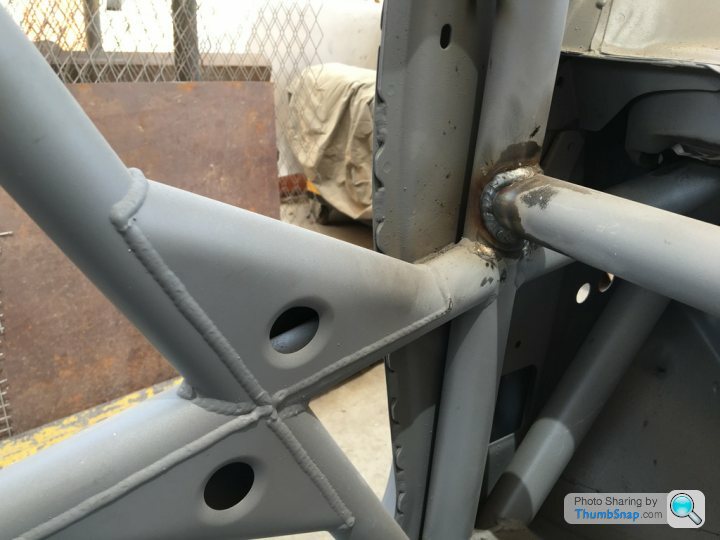
Below is the bar which comes through the bulkhead and provides the lateral strength to the turret. You can see how tidy the hole has been closed.
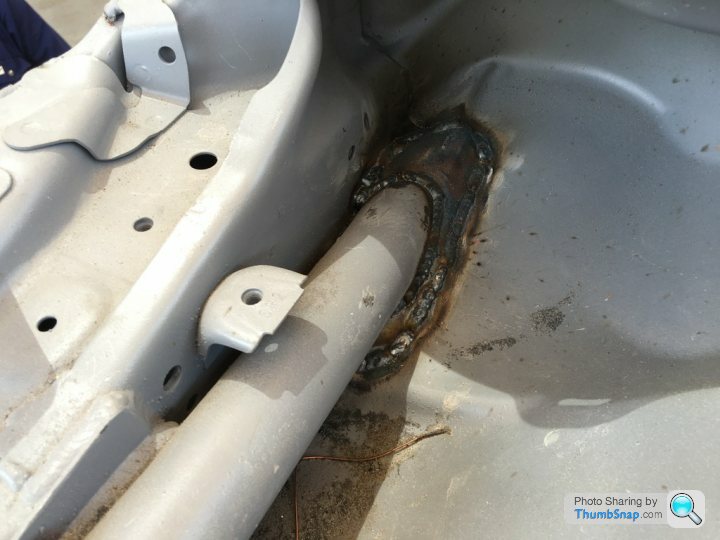
Now the car is in the paint shop for bodywork. Initially it will be protected to prevent rusting of the welding then some bodywork to fix the panels which were damaged by sandblasting then, interior and underside painted then we will definitely start the mechanical works.
On a side note, 2 of the teams drivers will be competing in the Barcelona 24hr race, with myself another team member helping the team the 2 drivers are driving for.
I think this will be the last update on the fabrication works as everything seems to be finished. A big thank you to Robbie and Mark at Saluki for the speedy, quality and efficient service. Its worth mentioning that they kept us updated at all times and they took a genuine interest in our project which is reflected in the quality of the Engineering.
So first up the seat rails were fully welded.
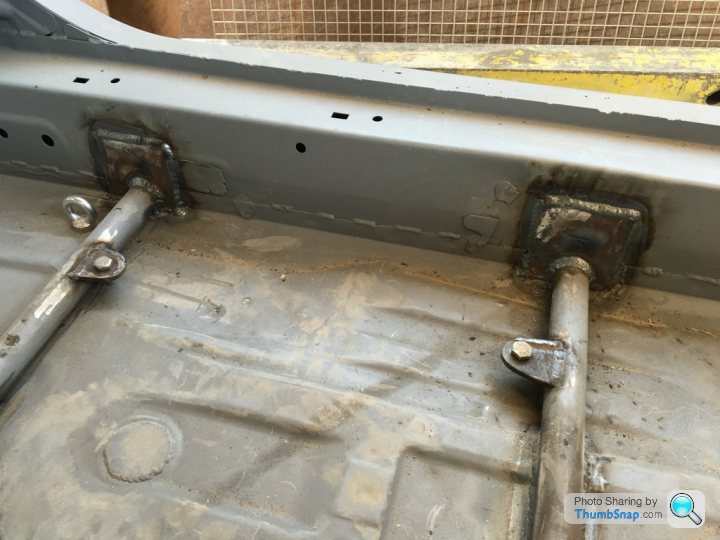
The lugs were also strengthened using fillet gusset pieces.
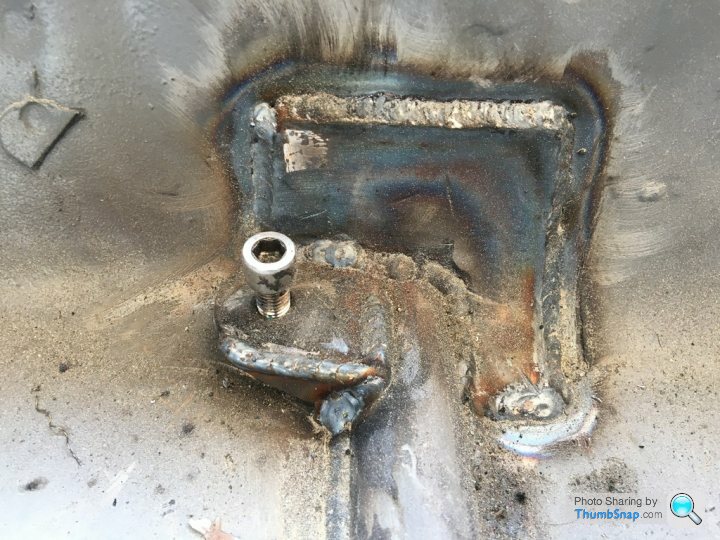
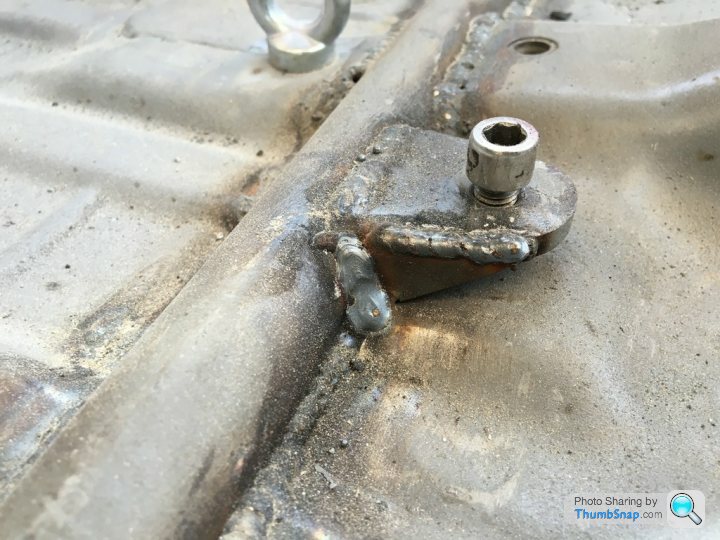
So with the seat positioned and fixed the pedal box reinforced floor plate was installed. Note the multiple holes are for flexibility in terms of the fitment position of the pedal box. They have been fitted with bolts to the underside so it is easy to install/remove/refit the pedal box.
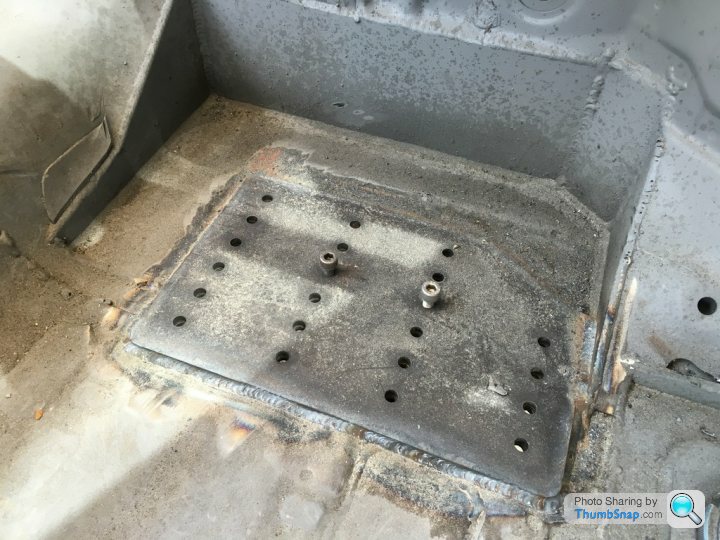
Saluki then firmed up the steering column position and finalised the welding.
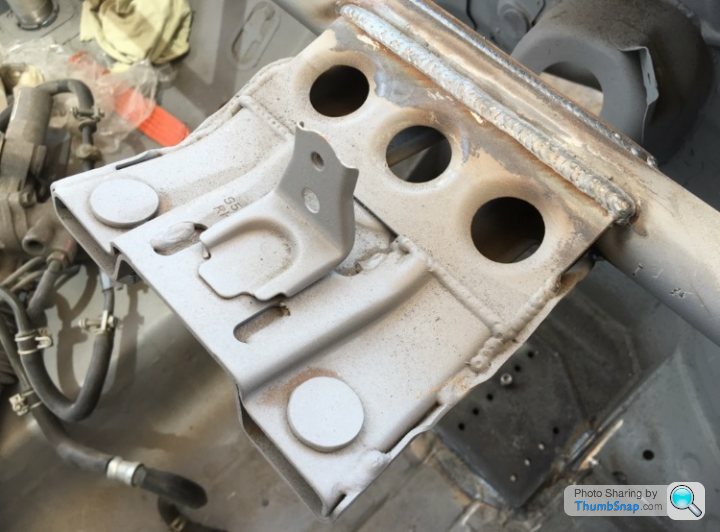
This then enabled the finalisation of the front CDS bar and the triangulated bars to the strut turrets.
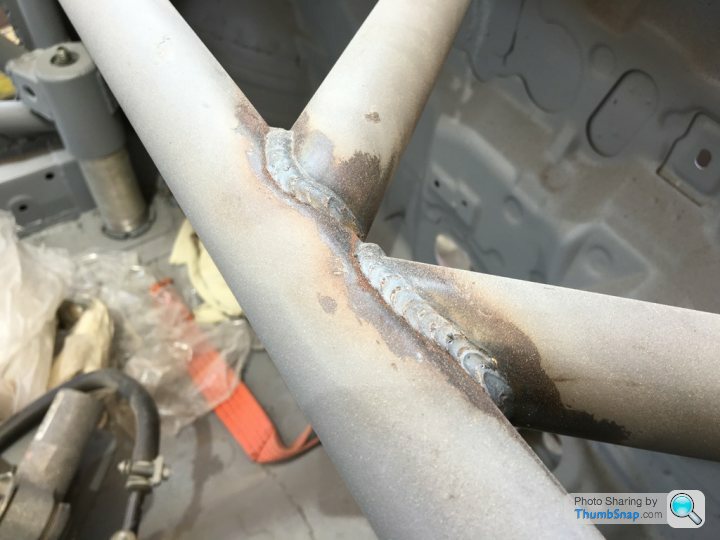
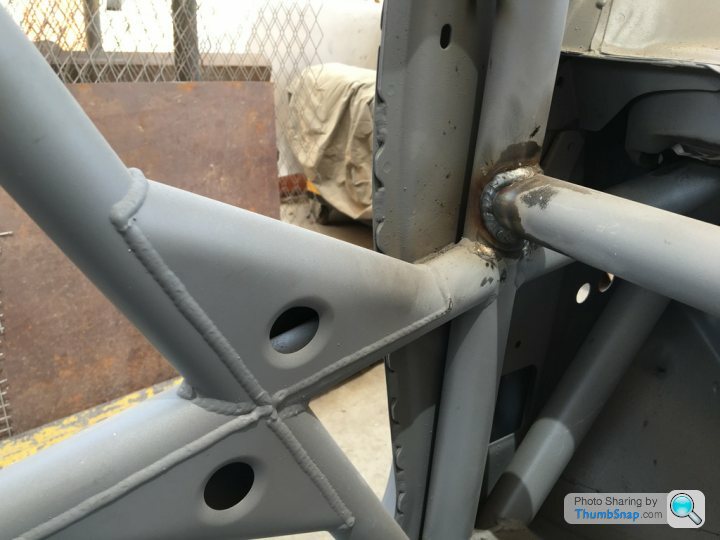
Below is the bar which comes through the bulkhead and provides the lateral strength to the turret. You can see how tidy the hole has been closed.
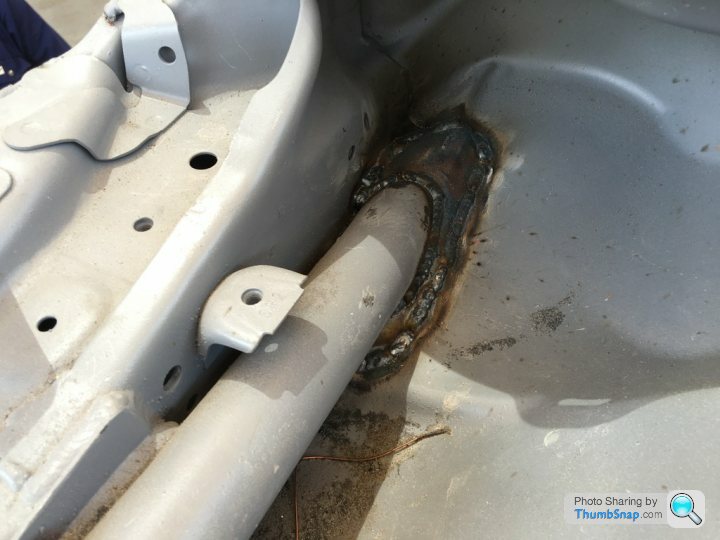
Now the car is in the paint shop for bodywork. Initially it will be protected to prevent rusting of the welding then some bodywork to fix the panels which were damaged by sandblasting then, interior and underside painted then we will definitely start the mechanical works.
On a side note, 2 of the teams drivers will be competing in the Barcelona 24hr race, with myself another team member helping the team the 2 drivers are driving for.
Part 15
After a fairly long gap since the last update (due to holidays / Ramadan / Eid / Racing in Barcelona...) here is the next installment.
Ok so its October instead of September but the good news is that things have moved on and we now have a really smart looking shell (painted under, internally and externally). The bodyshop faced three main issues:
- Front wings needed some modifications at the top where they meet the windscreen posts (actually the windscreen posts were modified as opposed to the wings) with added metal since they both didnt marry up cleanly.
- Doors were modified to fit.
- The shot-blasting caused a lot of damage particulary to the roof and rear 3/4 panels. There was a lot of hammering required to straightening those three sections of the car as opposed to opting for filler.
A-tech insisted in their trademark metallic grey for internals/under/inside the wheel arches/bonnet etc. And a nice clean white for the exterior. Our final livery will be revealed in due course but this year you can expect to see more white as the main part of the scheme.
First up is under the bonnet:
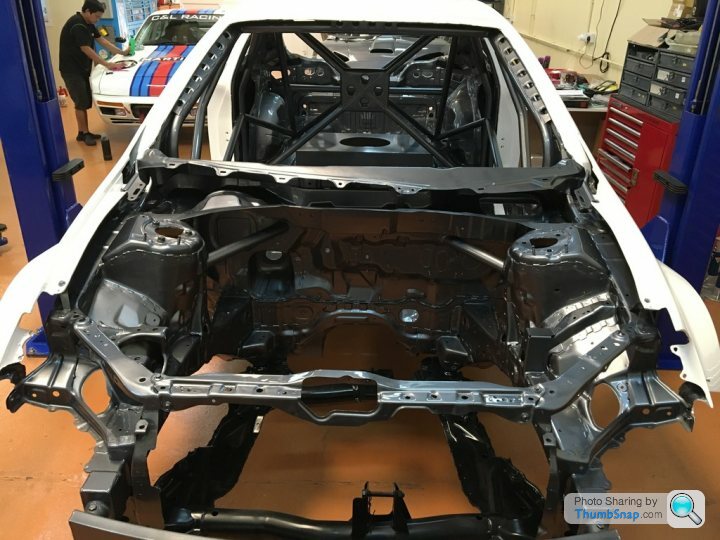
Below is the roll cage which you can see is painted as nicely as the exterior:
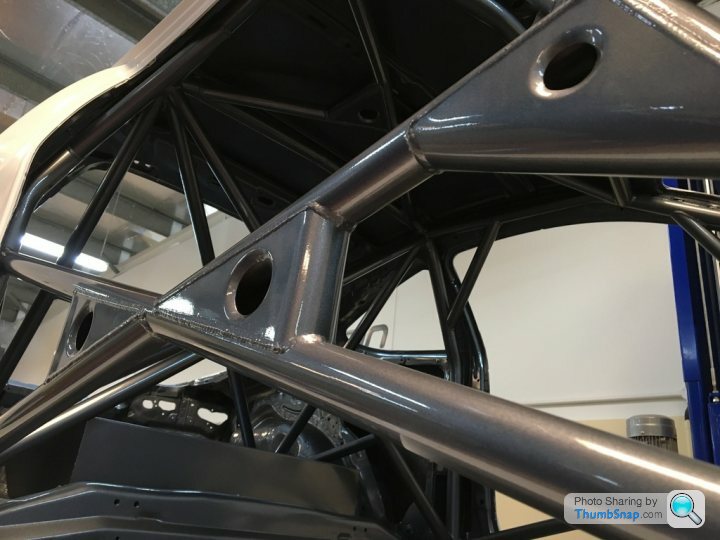
Internally we need to start some fit-out:
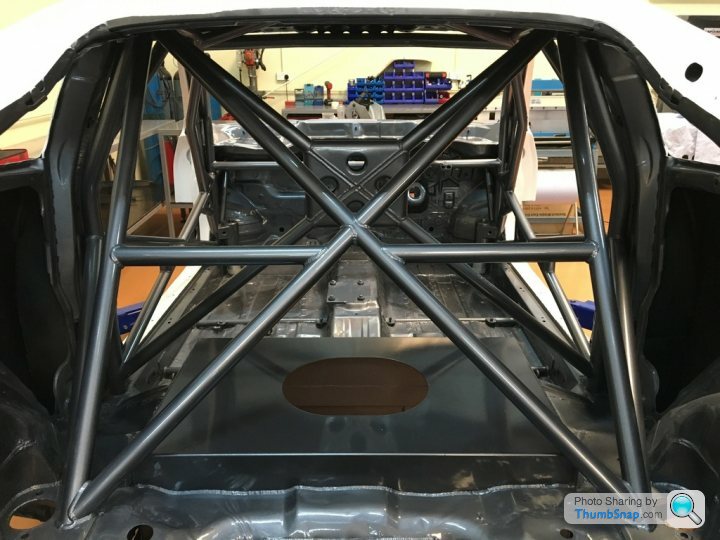
And the last few pics show the exterior of the shell: Doors/bonnet/hatch and bumpers will all be fitted at the end of the build. The other panels will now all be masked off to avoid any damage while the rebuild continues:
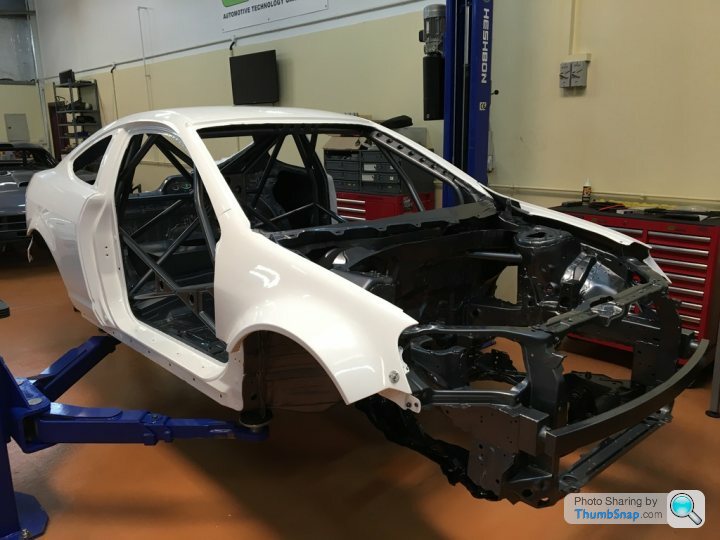
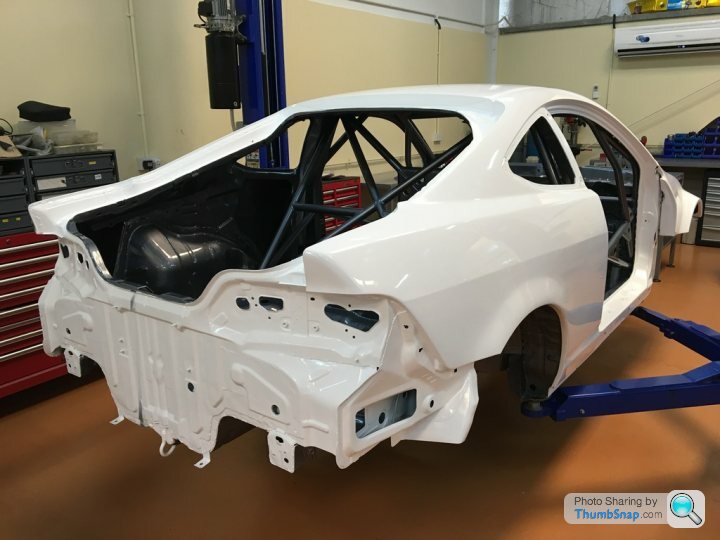
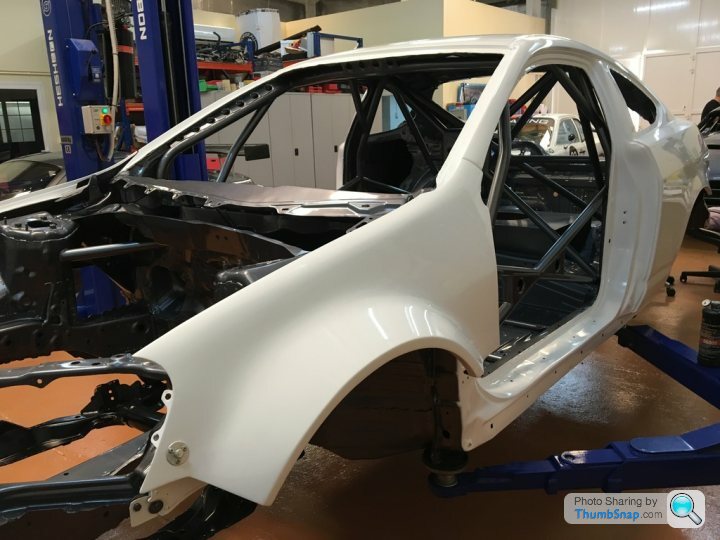
So, with some luck in the coming weeks we shall start to see the shell transforming into a #racecar!
More updates as the build progresses...
After a fairly long gap since the last update (due to holidays / Ramadan / Eid / Racing in Barcelona...) here is the next installment.
Ok so its October instead of September but the good news is that things have moved on and we now have a really smart looking shell (painted under, internally and externally). The bodyshop faced three main issues:
- Front wings needed some modifications at the top where they meet the windscreen posts (actually the windscreen posts were modified as opposed to the wings) with added metal since they both didnt marry up cleanly.
- Doors were modified to fit.
- The shot-blasting caused a lot of damage particulary to the roof and rear 3/4 panels. There was a lot of hammering required to straightening those three sections of the car as opposed to opting for filler.
A-tech insisted in their trademark metallic grey for internals/under/inside the wheel arches/bonnet etc. And a nice clean white for the exterior. Our final livery will be revealed in due course but this year you can expect to see more white as the main part of the scheme.
First up is under the bonnet:
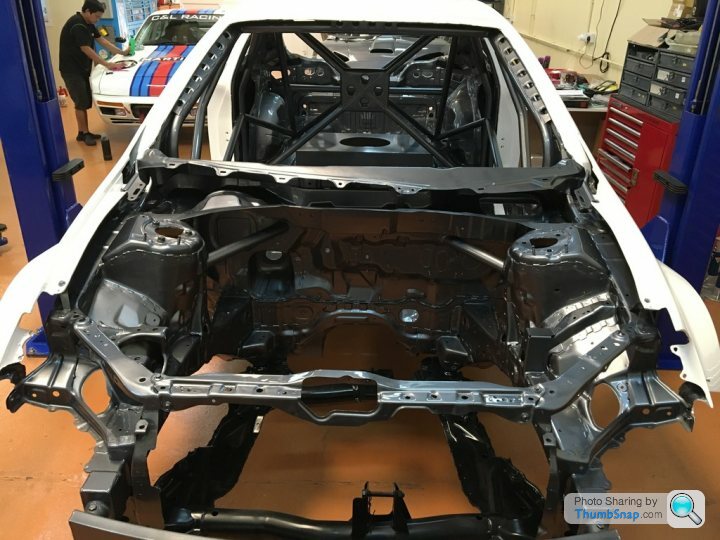
Below is the roll cage which you can see is painted as nicely as the exterior:
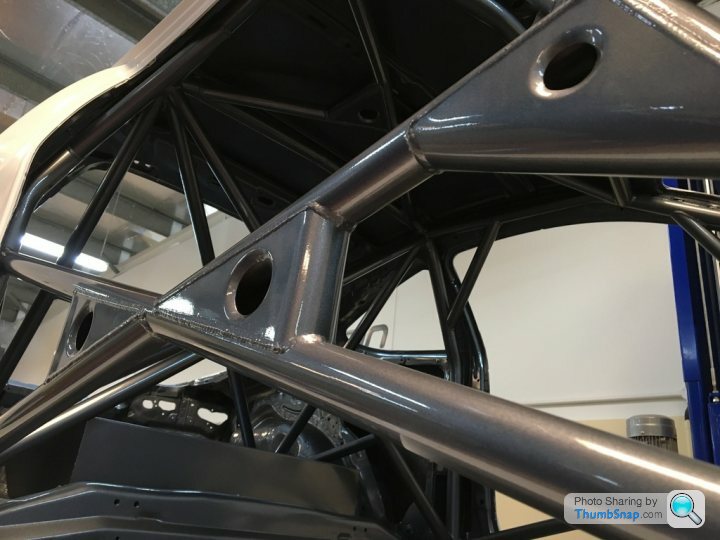
Internally we need to start some fit-out:
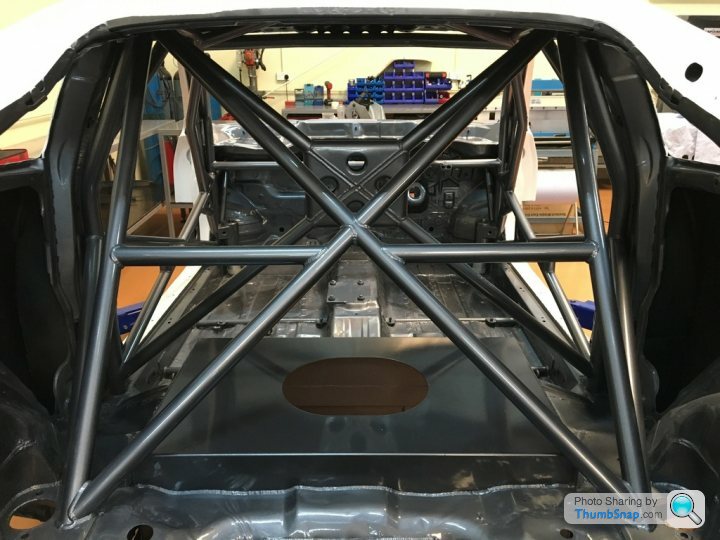
And the last few pics show the exterior of the shell: Doors/bonnet/hatch and bumpers will all be fitted at the end of the build. The other panels will now all be masked off to avoid any damage while the rebuild continues:
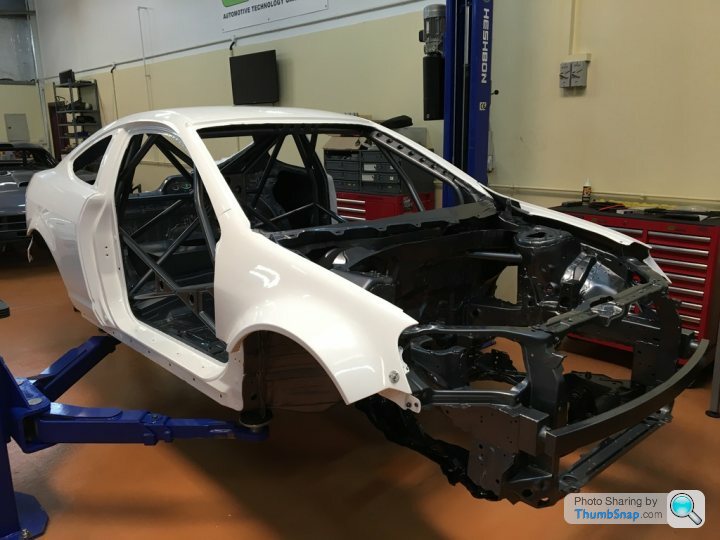
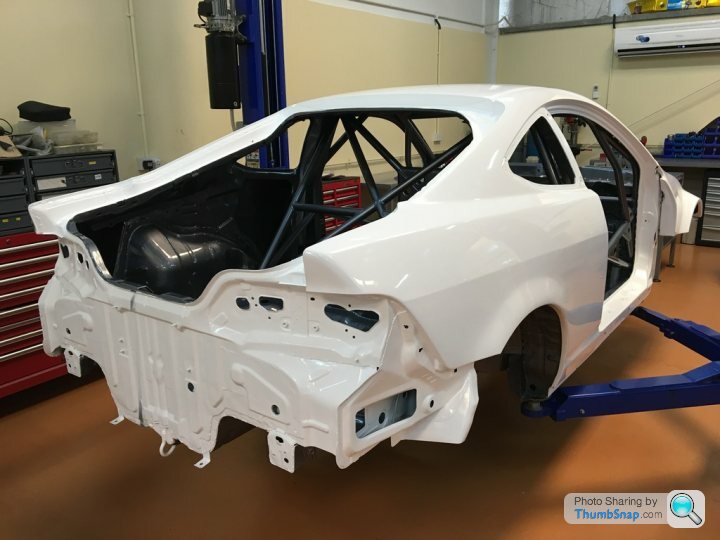
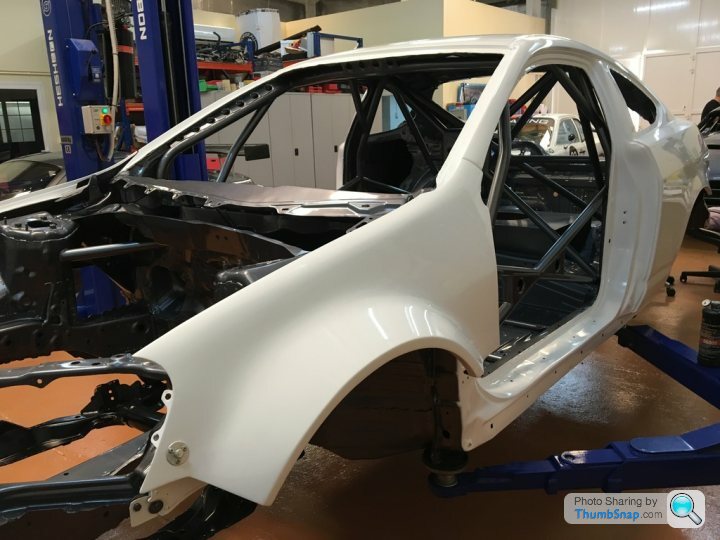
So, with some luck in the coming weeks we shall start to see the shell transforming into a #racecar!
More updates as the build progresses...
Part 16
Another brief update mostly by virtue of images it must be said. Things have progressed and we expect the car to be race ready in little over 1-month from now for its first shake down.
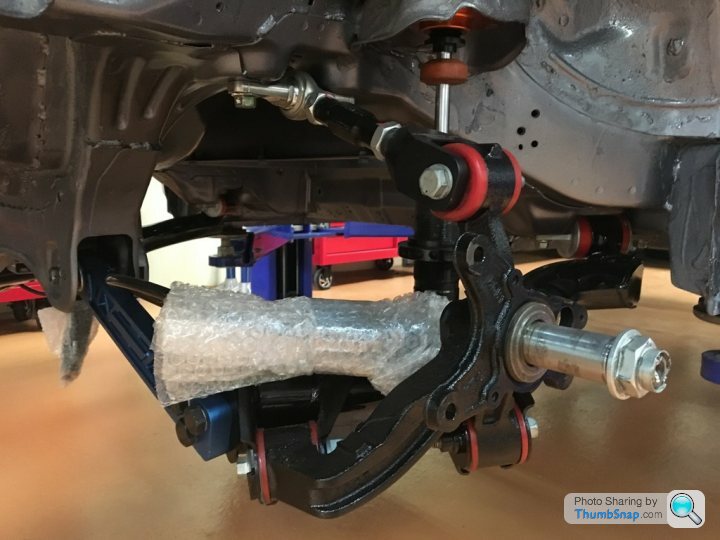
Suspension has been shotblasted, repainted and built up at each corner.
Above is the rear assembly and below front albeit missing springs as they will be fitted later.
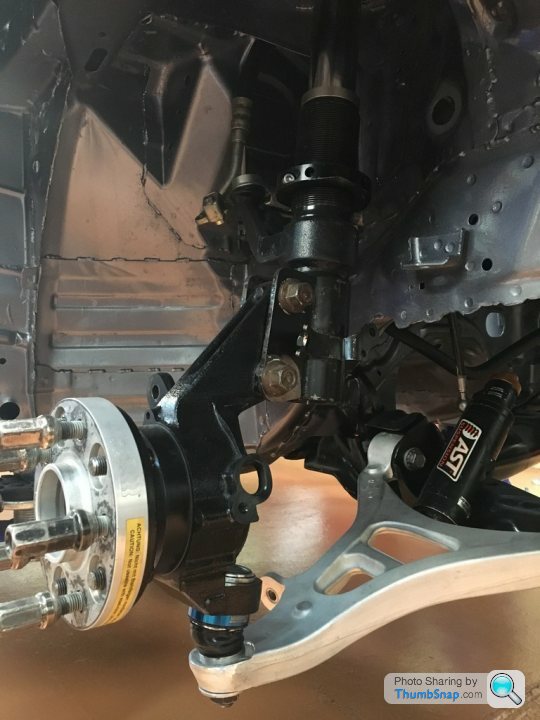
Most of the body panels such as bumpers are all fitted using 4mm allen key bolts c/w Japanese writing on them to give that authentic look! 😂
Below you can see the typical mounting backets and the actual bolts.
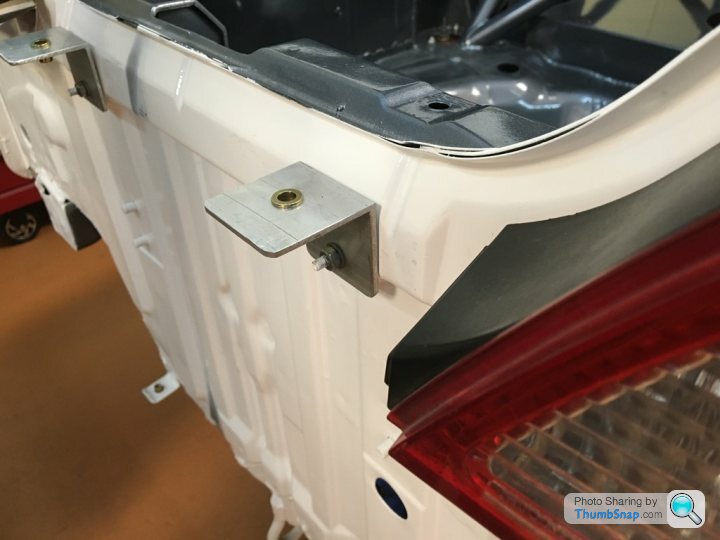
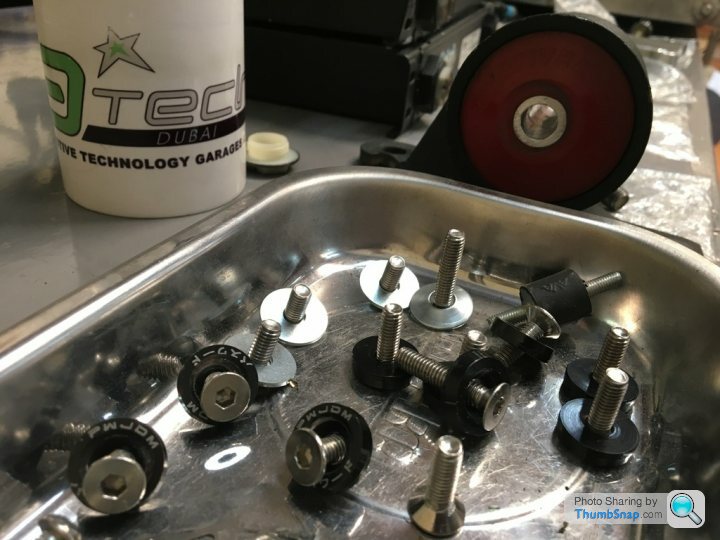
We have started fitting up engine & box using the excellent 'innovative mounts' products. www.innovativemounts.com
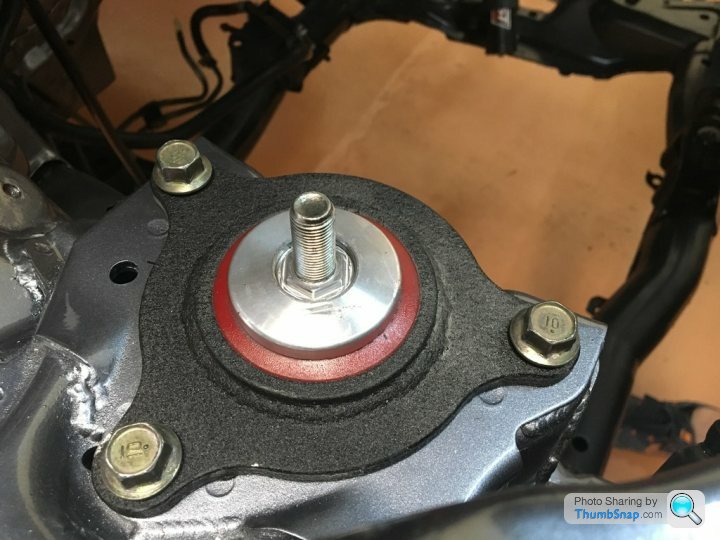
The really special K-tuned billet alloy shifter has been mounted. This time however to preserve the aesthetics of the product we have used stainless steel fixation bolts.
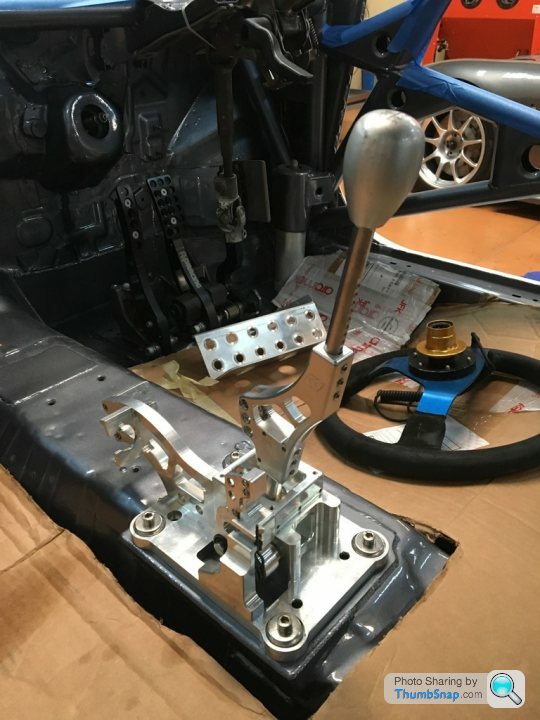
We use a front splitter bracket system provided by specialprojectsmotorsport (KIWI). A-tech made a slight change this time by welding the brackets to the subframe. We will do the same with the spare bracket set and a spare subframe so that in the event of serious damage we can quickly swap both over.
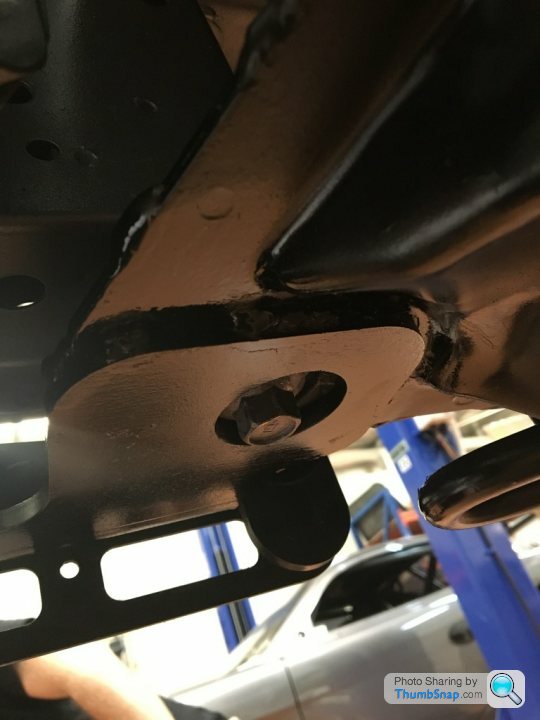
Last up is just a shot of the car itself from front and rear. Bumpers are currently in the paintshop so within a week or so we will be able to post another update. All in all we are really happy with how the build is coming along. It might be the newest Honda Integra in the world at this point in time 😊
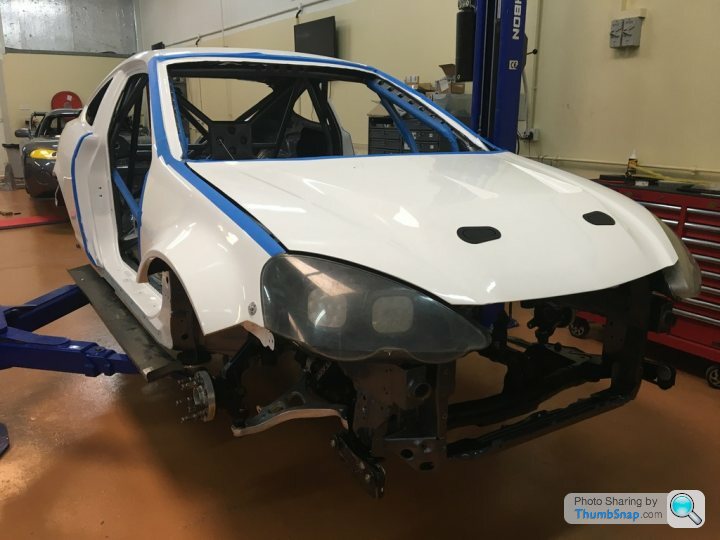
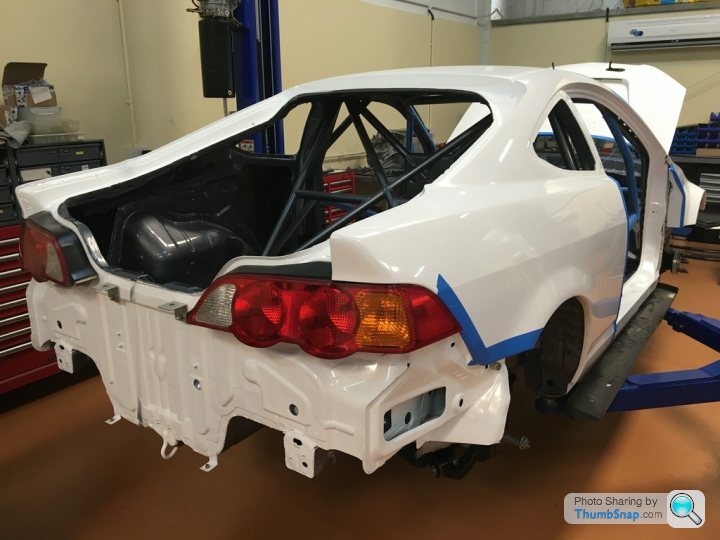
Another brief update mostly by virtue of images it must be said. Things have progressed and we expect the car to be race ready in little over 1-month from now for its first shake down.
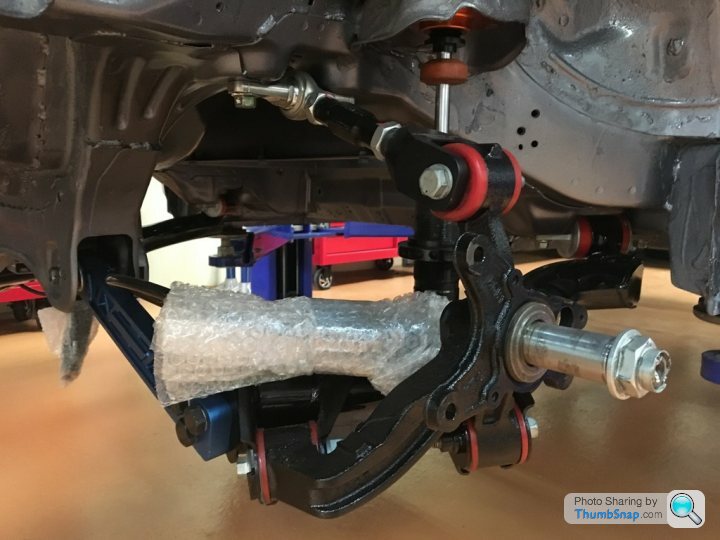
Suspension has been shotblasted, repainted and built up at each corner.
Above is the rear assembly and below front albeit missing springs as they will be fitted later.
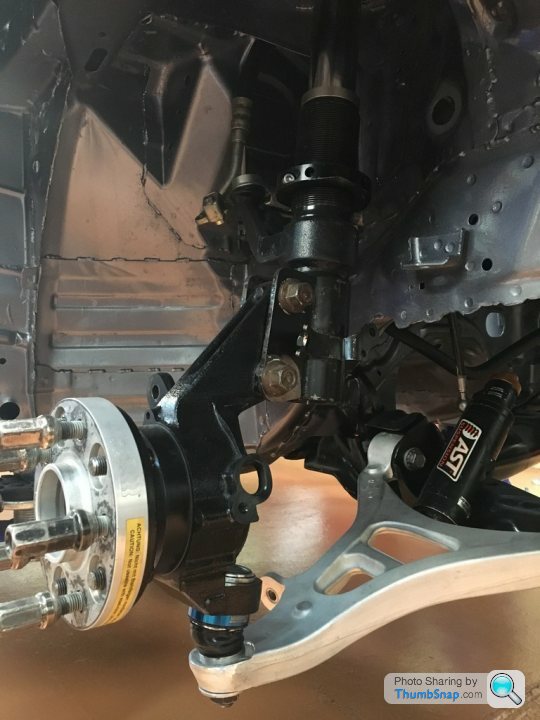
Most of the body panels such as bumpers are all fitted using 4mm allen key bolts c/w Japanese writing on them to give that authentic look! 😂
Below you can see the typical mounting backets and the actual bolts.
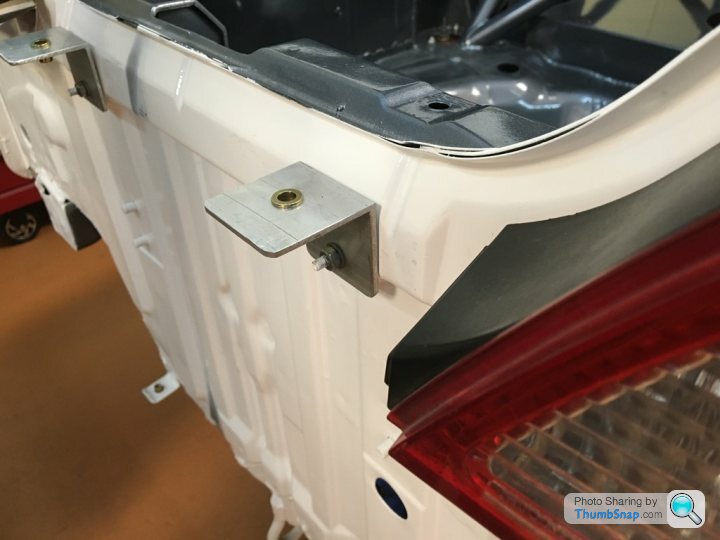
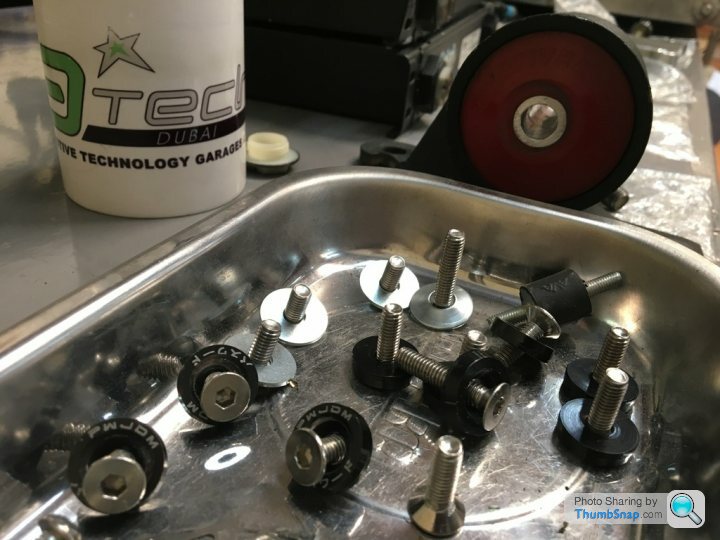
We have started fitting up engine & box using the excellent 'innovative mounts' products. www.innovativemounts.com
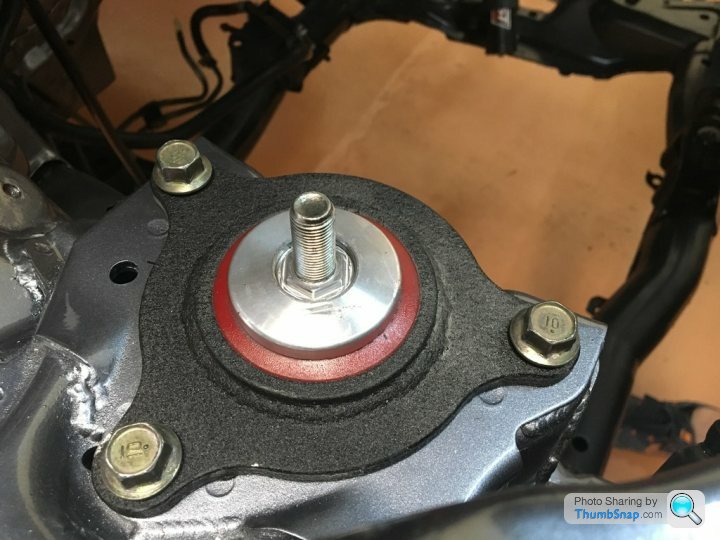
The really special K-tuned billet alloy shifter has been mounted. This time however to preserve the aesthetics of the product we have used stainless steel fixation bolts.
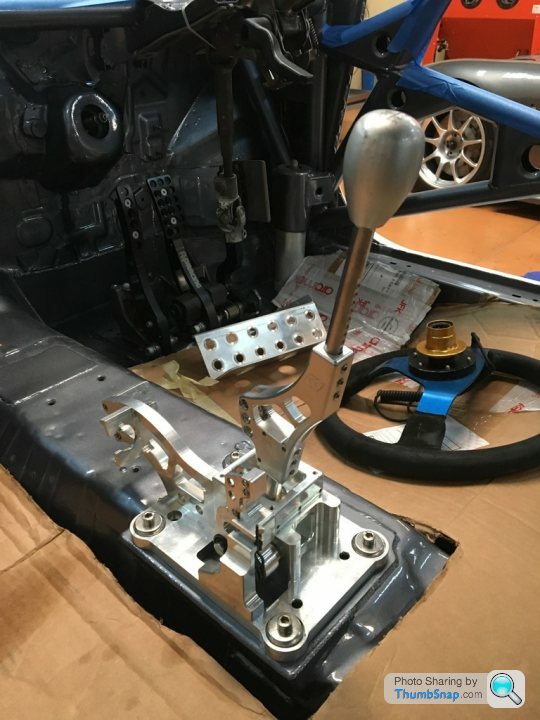
We use a front splitter bracket system provided by specialprojectsmotorsport (KIWI). A-tech made a slight change this time by welding the brackets to the subframe. We will do the same with the spare bracket set and a spare subframe so that in the event of serious damage we can quickly swap both over.
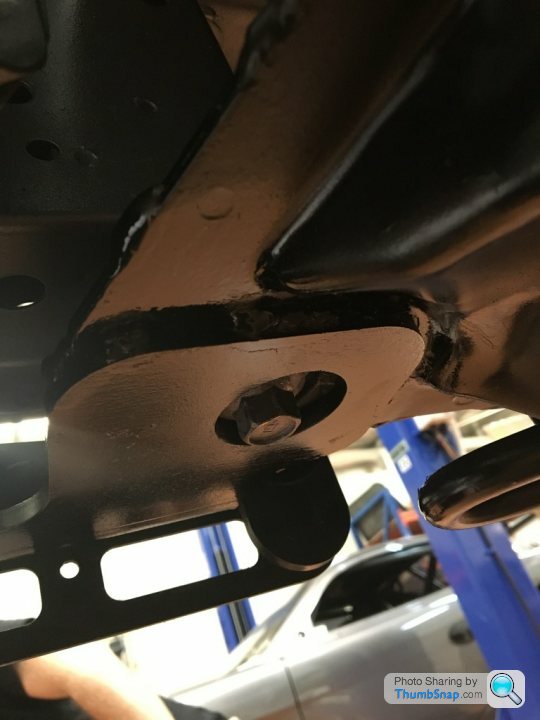
Last up is just a shot of the car itself from front and rear. Bumpers are currently in the paintshop so within a week or so we will be able to post another update. All in all we are really happy with how the build is coming along. It might be the newest Honda Integra in the world at this point in time 😊
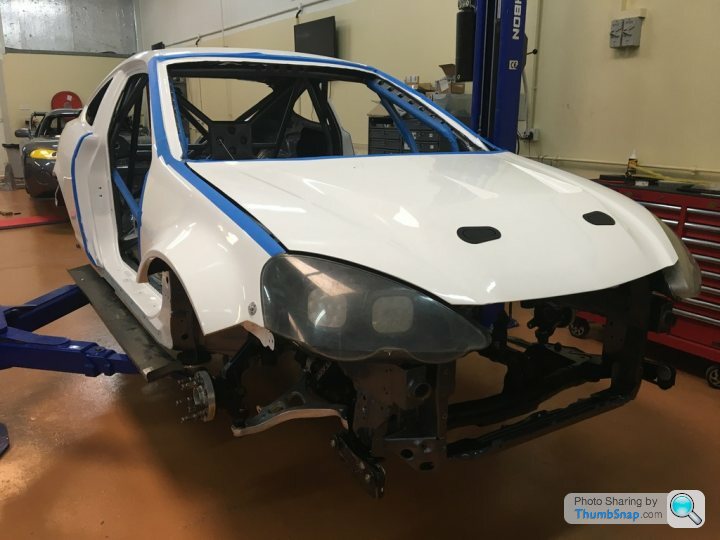
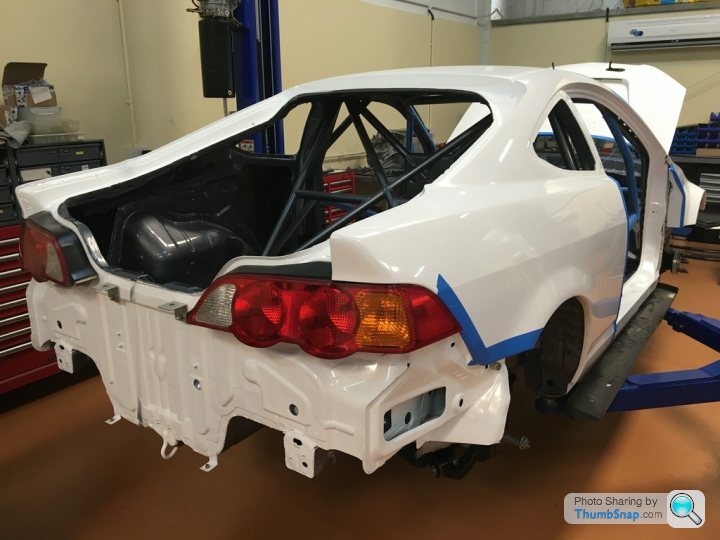
Part 17
Just a snippet of an update from the build..
Firstly and a bit random but the team bus (24Hrs sleeping wagon) has been fitted with a new set of headlights I bought for AED 300 (~£60) in in Al Ain. Actually our friend Kinan Dawood sourced them for us. Probably my favourite new part of the year to be fair. Transformed the look of the old girl (or at least the front of it anyway).
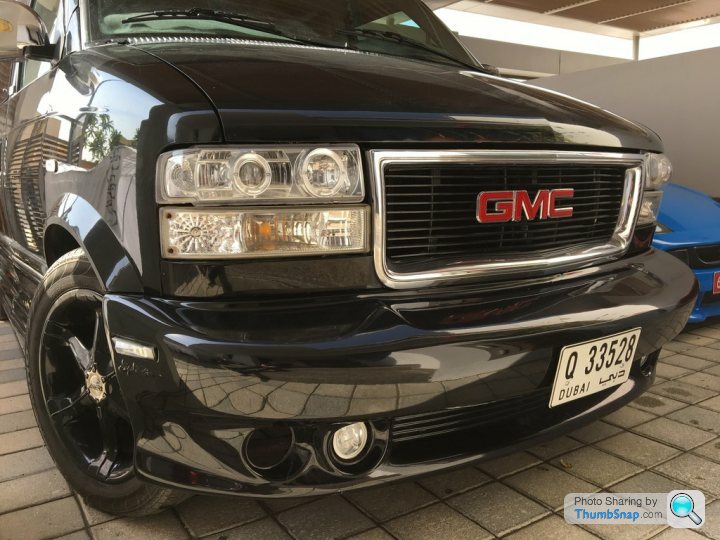
The inside got a spring (winter) clean and its ready to do its annual 100kms driving!
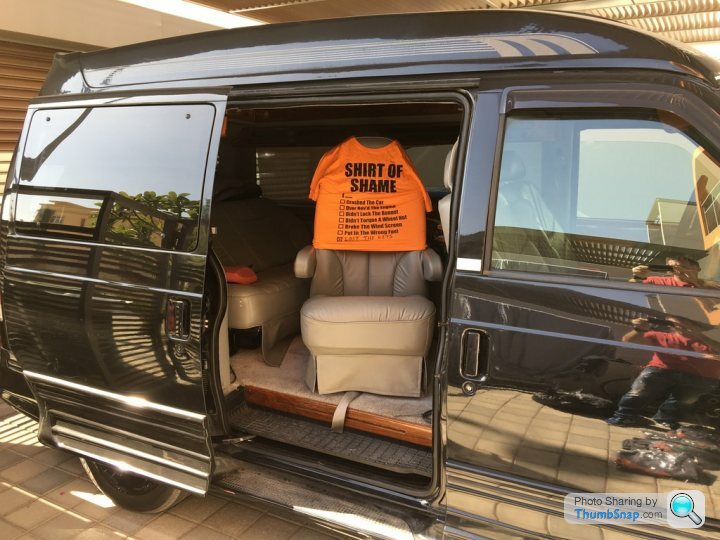
Meanwhile. When I visited the car last weekend there were a few more jobs completed.
New electrical lifeline fire extinguisher kit was fitted (Supplied by our friends MotorsportWheels Dubai):
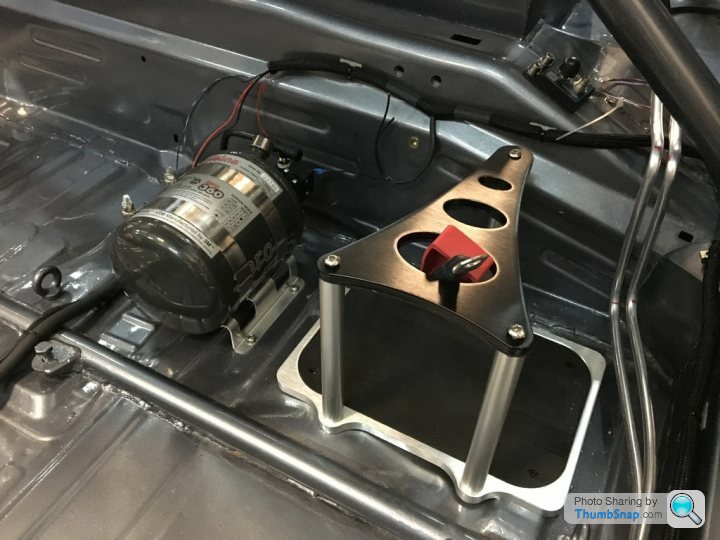
.....along with a spanking new battery holder which can be seen in the above image. Much nicer than the big ugly red box we had previously.
The accusump was positioned and new loom pretty much wired in pending final terminations to things like lights and the control panel.
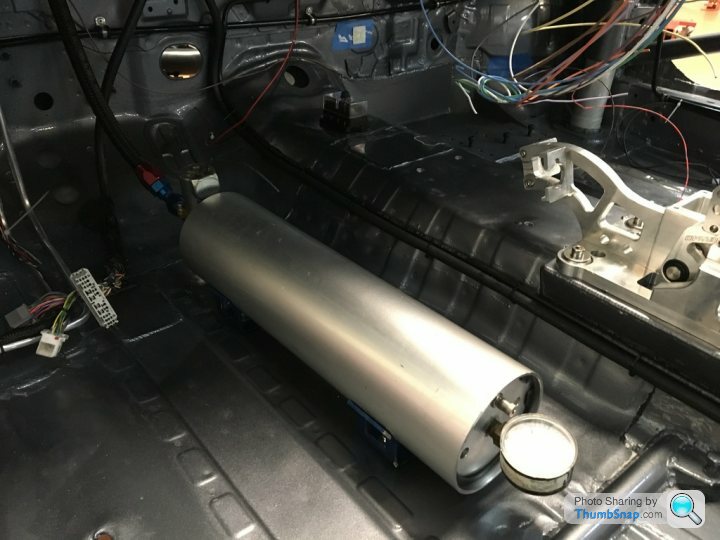
The AST suspension adjustable canisters have been mounted front and rear for easy access. Below is a pic of the rears.
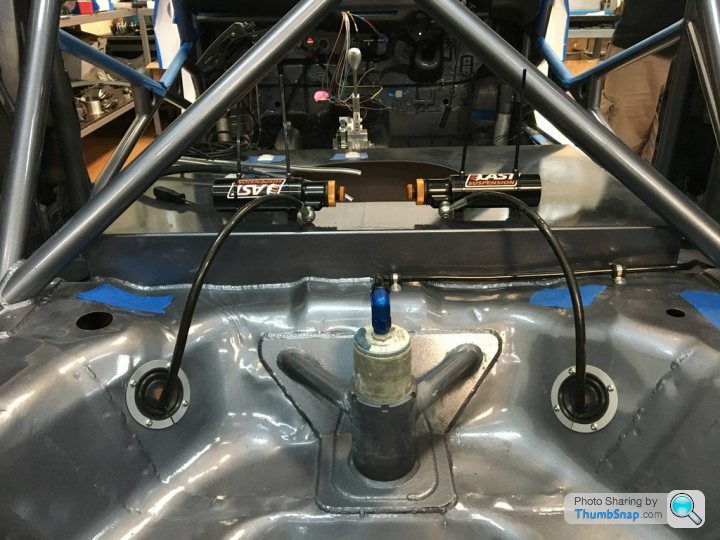
All of the engine connectors are in place on the bulkhead including engine loom plug (from wireworx USA), battery positive and oil lines from the previously photographed accusump.
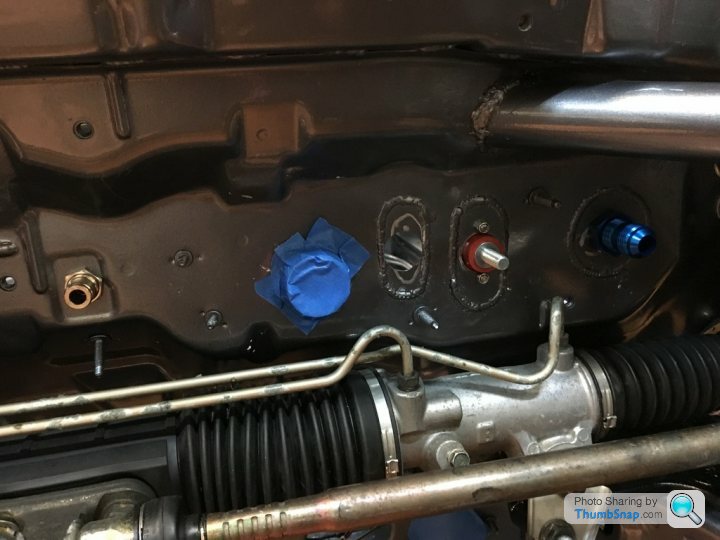
Last up is a pic of the dash mounted in place. Still not sure what the two holes are for but all will be revealed soon.
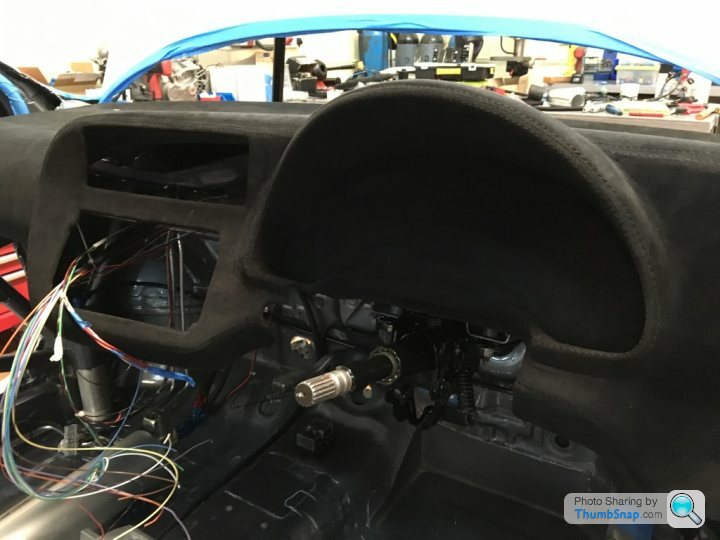
Meanwhile the doors and hatch are all in the paint shop to get tidied up and refreshed in a nice crisp white. I also visited Leadright Dubai earlier today to finalise the shade of orange for the colour scheme. Again something a little different coming your way soon.
Just a snippet of an update from the build..
Firstly and a bit random but the team bus (24Hrs sleeping wagon) has been fitted with a new set of headlights I bought for AED 300 (~£60) in in Al Ain. Actually our friend Kinan Dawood sourced them for us. Probably my favourite new part of the year to be fair. Transformed the look of the old girl (or at least the front of it anyway).
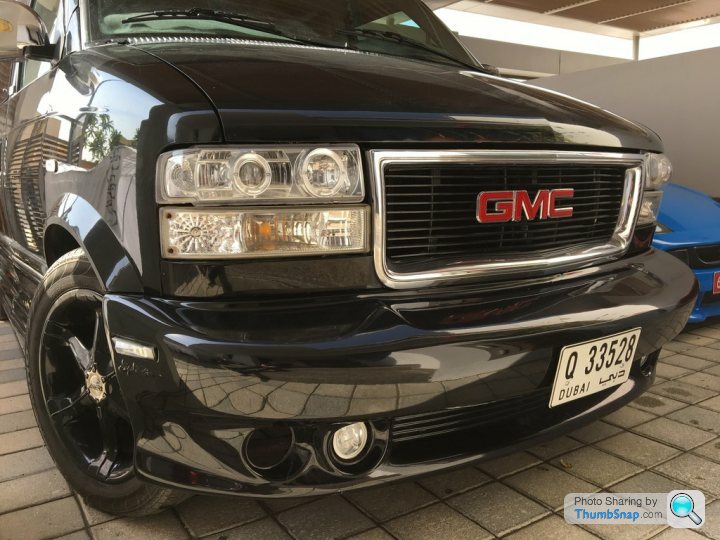
The inside got a spring (winter) clean and its ready to do its annual 100kms driving!
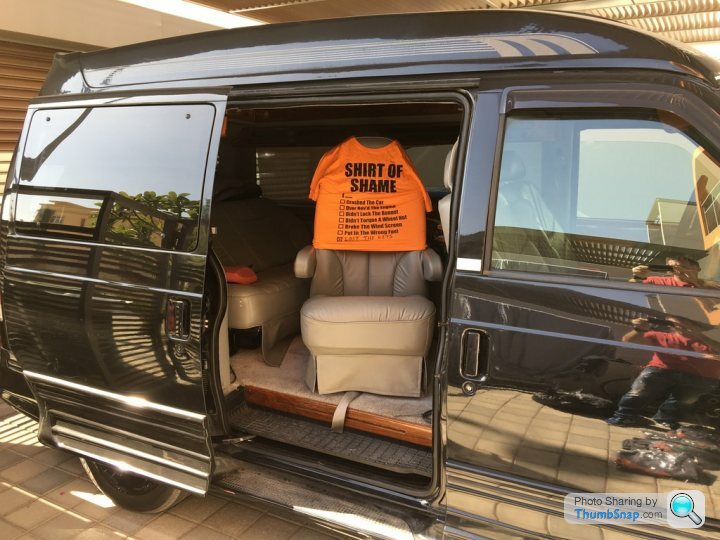
Meanwhile. When I visited the car last weekend there were a few more jobs completed.
New electrical lifeline fire extinguisher kit was fitted (Supplied by our friends MotorsportWheels Dubai):
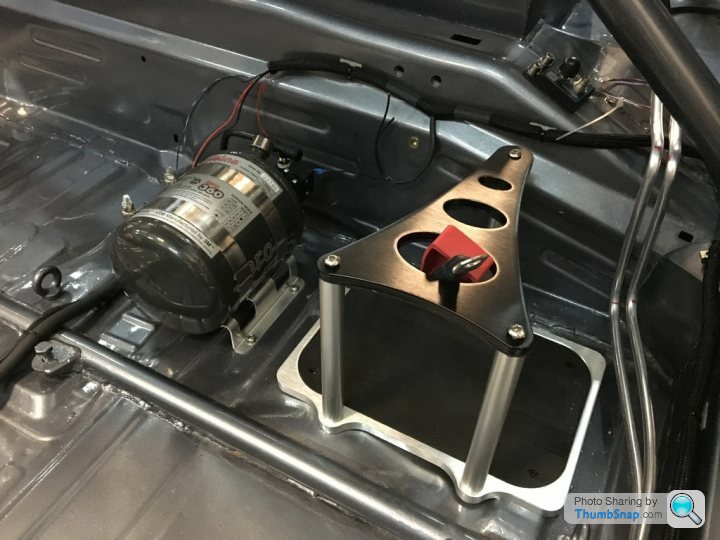
.....along with a spanking new battery holder which can be seen in the above image. Much nicer than the big ugly red box we had previously.
The accusump was positioned and new loom pretty much wired in pending final terminations to things like lights and the control panel.
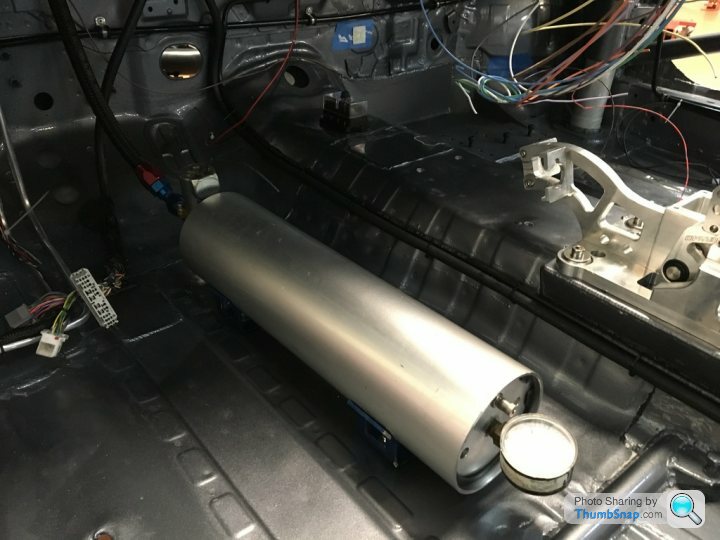
The AST suspension adjustable canisters have been mounted front and rear for easy access. Below is a pic of the rears.
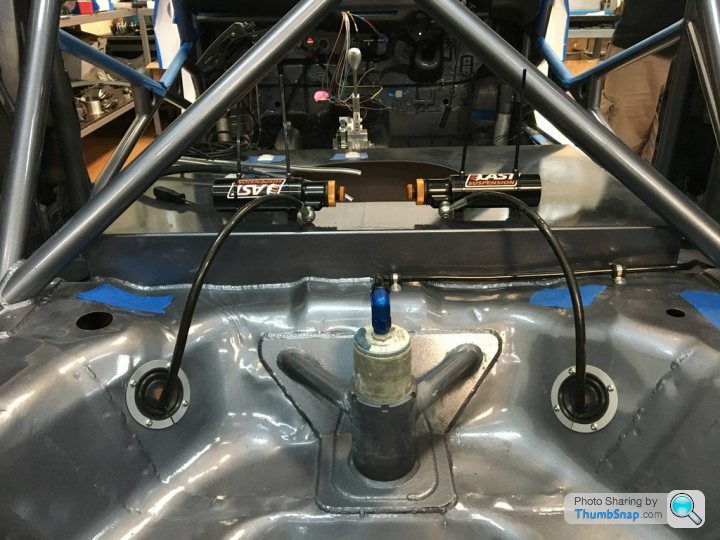
All of the engine connectors are in place on the bulkhead including engine loom plug (from wireworx USA), battery positive and oil lines from the previously photographed accusump.
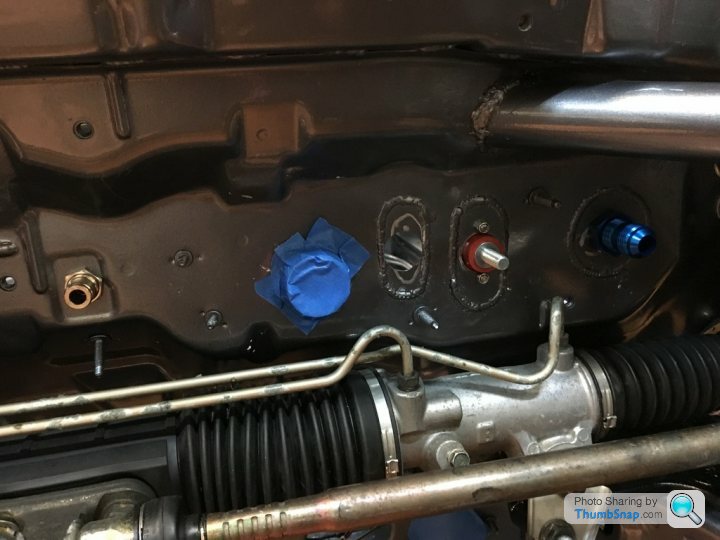
Last up is a pic of the dash mounted in place. Still not sure what the two holes are for but all will be revealed soon.
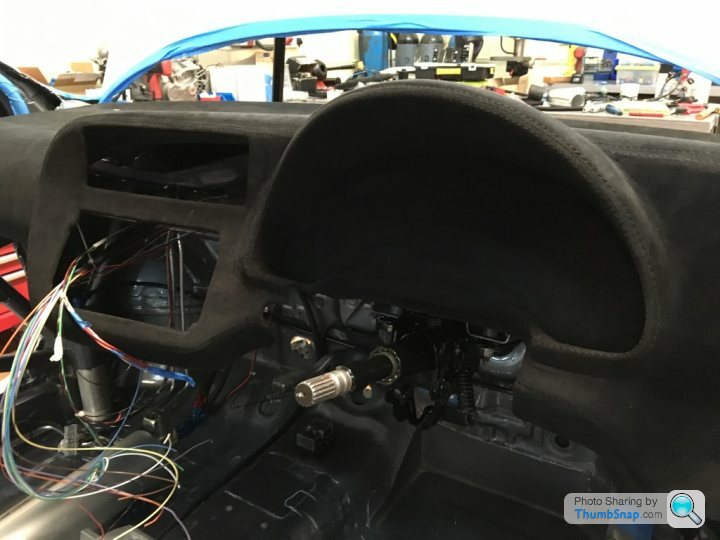
Meanwhile the doors and hatch are all in the paint shop to get tidied up and refreshed in a nice crisp white. I also visited Leadright Dubai earlier today to finalise the shade of orange for the colour scheme. Again something a little different coming your way soon.
Apologies for the late response. From a practical perspective it means everything (body panels) can be removed with 1-tool. Aesthetically it looks great and we just happened to have a load of them. In terms of expense this is pretty low down the overall expense sheet to be honest.
More updates soon.
More updates soon.
Part 18
So where were we!....
A lot has happened since the last update although some days when I visit it looks like we are going backwards rather than forwards. This is because A-tech test fit things then remove them again. The upside to this is perfectionism. The downside to this is that the car is so clean it looks like it should go straight to a museum.
Team roles and responsibilities have been updated this week with each of the drivers having the been allocated the sole task of "DONT CRASH CAR!".
Oh yes... the build..
First up we recently read on www.shgmotorworks.com website about their experience with steering rack failure and what was the cause (track rod slider) and how they developed a solution made from deralin. Evan from Shg (So Honda Garage) took the time to explain to us that the plastic slider wears and allows significant play. This not only causes bump steer by letting the tie rods shift up to 2* but also affects the rack/pinion gear mesh since the rack bar is able to rotate.
Evan designed a Delrin insert to replace the oem part. It increases surface area, depth, hardness and tolerances have also been reduced to just a few thousandths. The cost is $65usd plus shipping and on the face of it seems a must have upgrade for anyone racing or tracking an Integra.
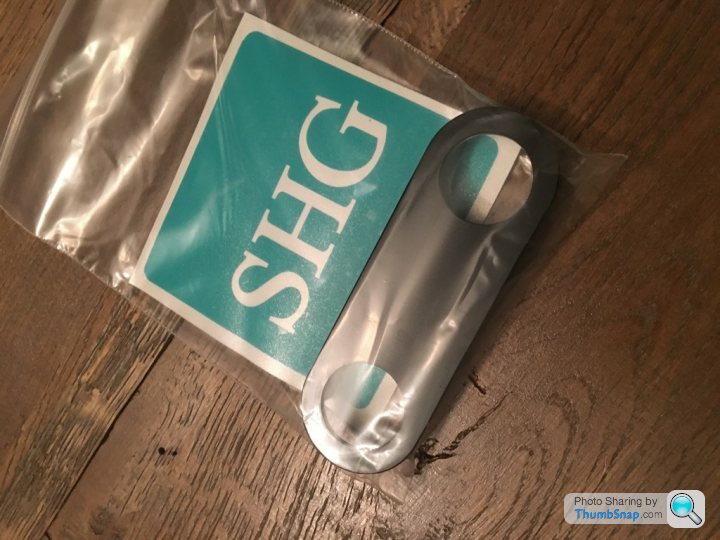
Next then is the infamous footrest. 2-years of moaning from Umair Khan prompted us to finally make something nice and fit for a king khan! I tested it and can confirm it is perfect for his code 60 exploits.
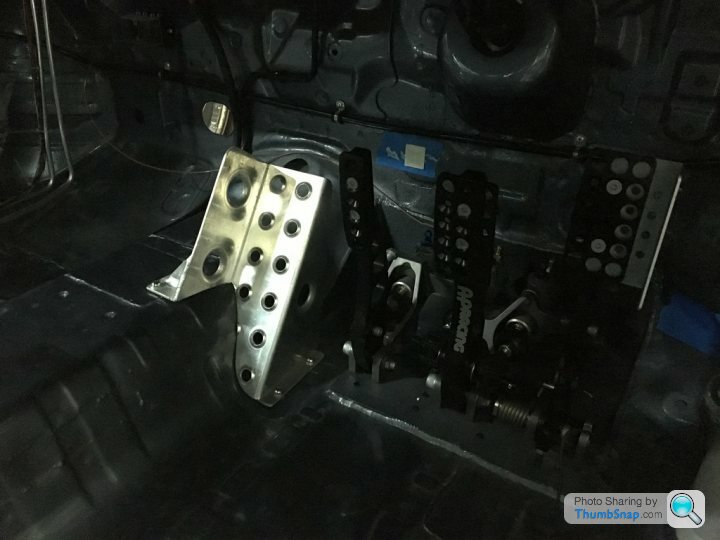
The drivers seat has been fixed in place with three fundamental differences over the old car. (1) It is much easier to get in and out of comparing to the corbeau revenge series, (2) The seat is much lower and (3) The FIA approved slider had to be fitted upside down so in otherwords to slide the seat you have to push the slider down as opposed to pulling it up. Thats a bit un-natural but nothing we can do and besides it still works fine.
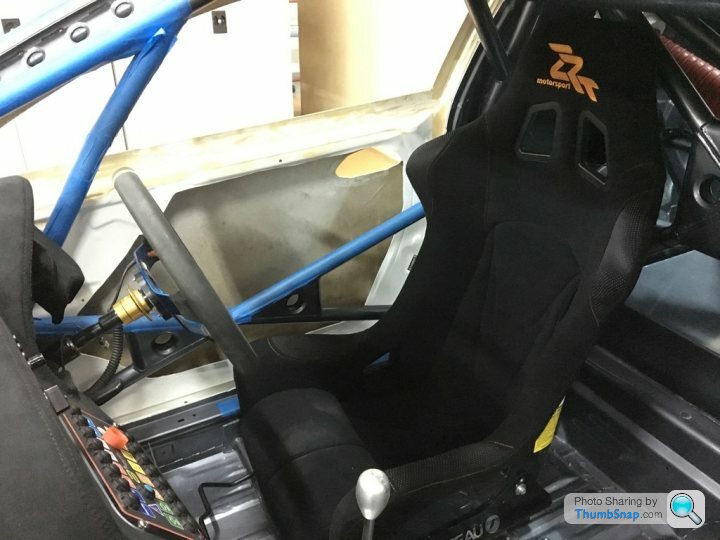
The fuel cell that had some of you wondering about some time back has also now been fitted. We chose to fit dual fillers. The reason being we are not restricted to which side of the pumps we can go to in the refuelling station during the race. (Sometimes there are queues).
Below are two pics showing the installation along with the filler cap (installed within the rear 3/4 windows). It is also worth noting that the rear visibility has been hugely improved along with significantly lower centre of gravity.
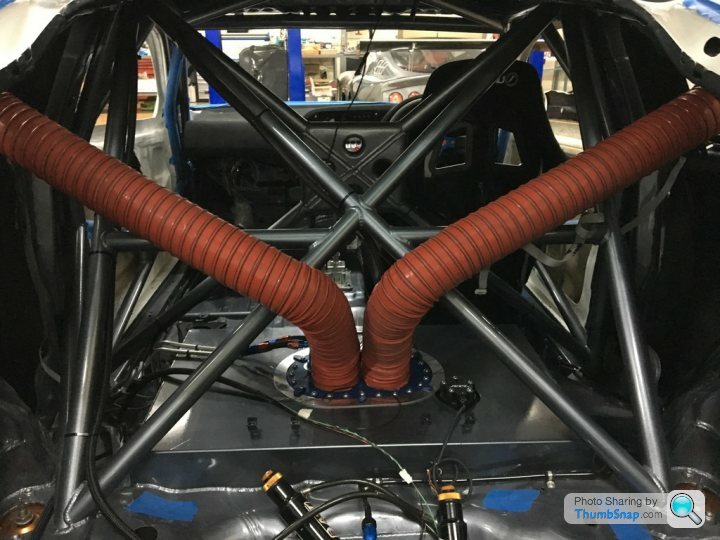
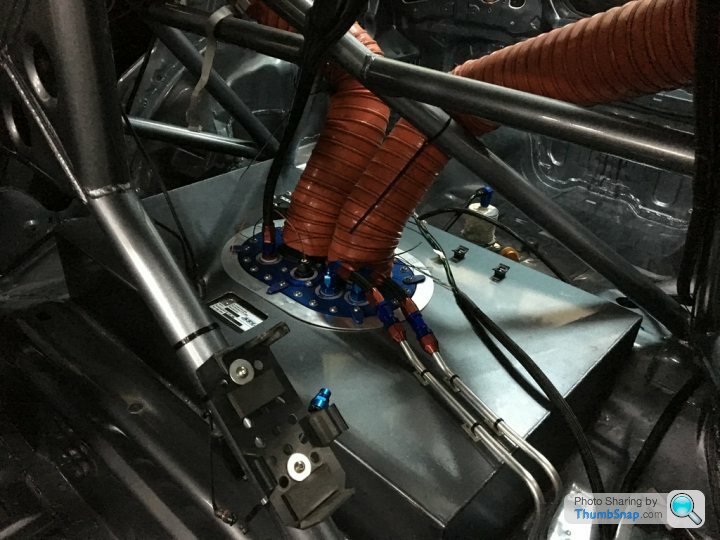
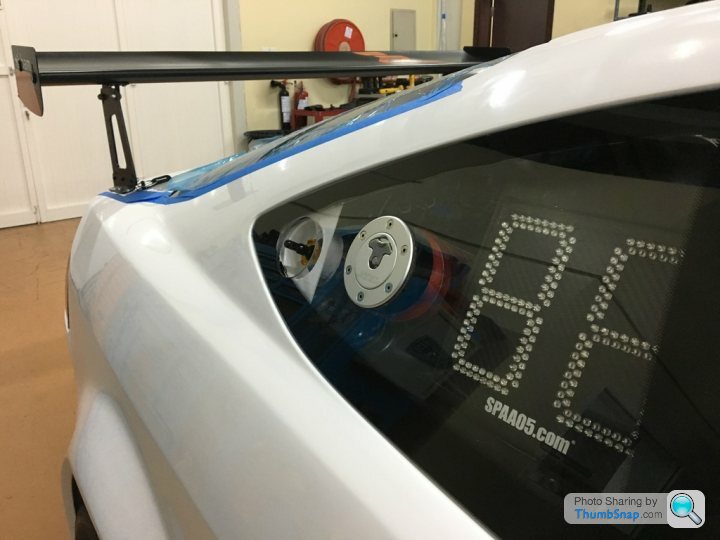
Our doors this year a much lighter. They are not the crazy expensive carbon fibre doors but still pretty good at a fraction of the cost. They do however need some fettling with regard to final fitment which resulted in no end of moaning from Julian but for those of you who know him, he would be lost if he didnt have something to moan about!
You can see the markings in the below image for trimming and painting. We ordered plastic windows (front/rear and sides) from plastics4performance in the UK. Due to the design of our doors the windows will need to be cut down slightly and fitted within the frame as opposed to sitting over the frame in the standard Integra.
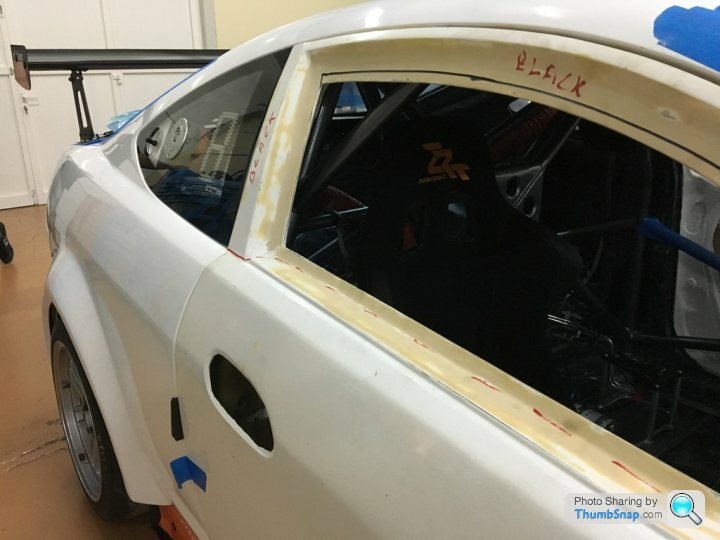
We think it will still look really great and we ordered the pro-slider for the drivers side which is really an impressive quality product. More on this next time.
Last up for this update is the dash. The holes have been filled and sadly no room for the Alpine stereo I ordered.
Go on ask the question.... Whats the fuel button for?
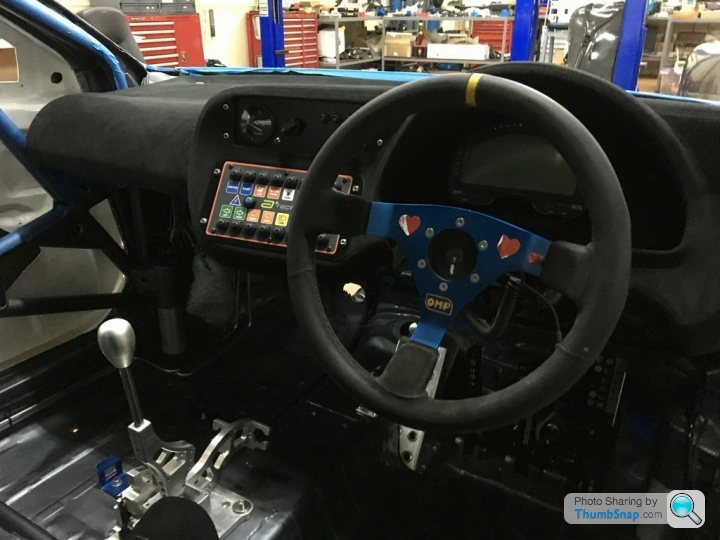
Answer: I have no idea!
Not sure we will manage another update this side of Christmas and New Years so in the meantime Happy holidays from all at ZRT
So where were we!....
A lot has happened since the last update although some days when I visit it looks like we are going backwards rather than forwards. This is because A-tech test fit things then remove them again. The upside to this is perfectionism. The downside to this is that the car is so clean it looks like it should go straight to a museum.
Team roles and responsibilities have been updated this week with each of the drivers having the been allocated the sole task of "DONT CRASH CAR!".
Oh yes... the build..
First up we recently read on www.shgmotorworks.com website about their experience with steering rack failure and what was the cause (track rod slider) and how they developed a solution made from deralin. Evan from Shg (So Honda Garage) took the time to explain to us that the plastic slider wears and allows significant play. This not only causes bump steer by letting the tie rods shift up to 2* but also affects the rack/pinion gear mesh since the rack bar is able to rotate.
Evan designed a Delrin insert to replace the oem part. It increases surface area, depth, hardness and tolerances have also been reduced to just a few thousandths. The cost is $65usd plus shipping and on the face of it seems a must have upgrade for anyone racing or tracking an Integra.
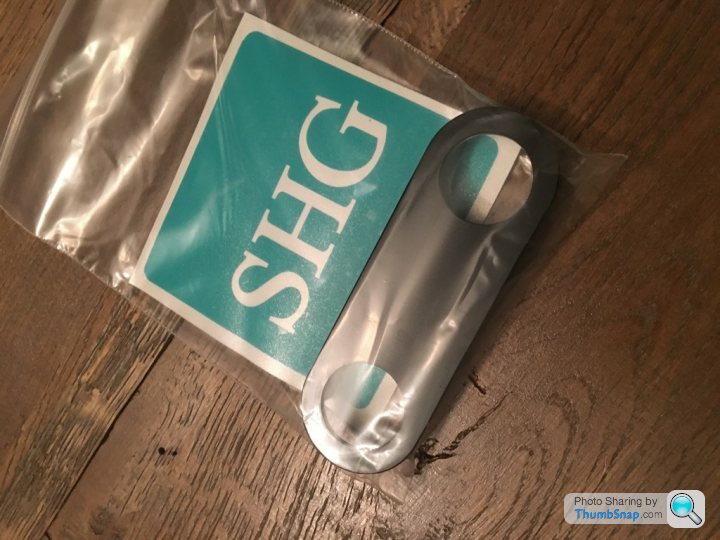
Next then is the infamous footrest. 2-years of moaning from Umair Khan prompted us to finally make something nice and fit for a king khan! I tested it and can confirm it is perfect for his code 60 exploits.
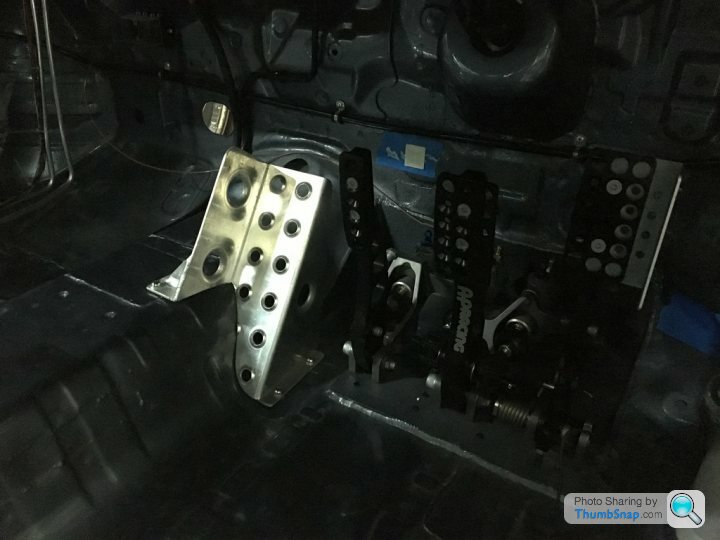
The drivers seat has been fixed in place with three fundamental differences over the old car. (1) It is much easier to get in and out of comparing to the corbeau revenge series, (2) The seat is much lower and (3) The FIA approved slider had to be fitted upside down so in otherwords to slide the seat you have to push the slider down as opposed to pulling it up. Thats a bit un-natural but nothing we can do and besides it still works fine.
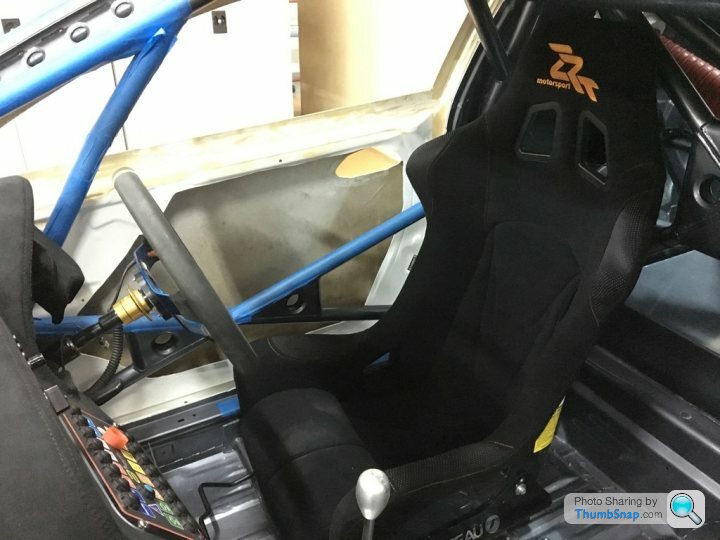
The fuel cell that had some of you wondering about some time back has also now been fitted. We chose to fit dual fillers. The reason being we are not restricted to which side of the pumps we can go to in the refuelling station during the race. (Sometimes there are queues).
Below are two pics showing the installation along with the filler cap (installed within the rear 3/4 windows). It is also worth noting that the rear visibility has been hugely improved along with significantly lower centre of gravity.
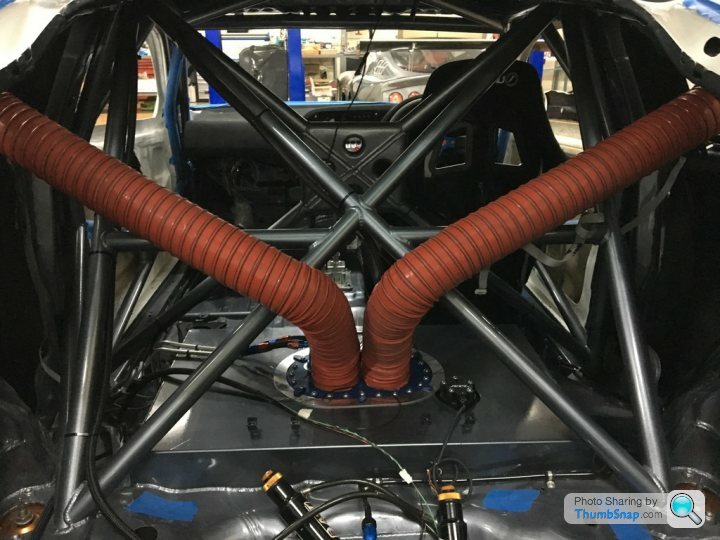
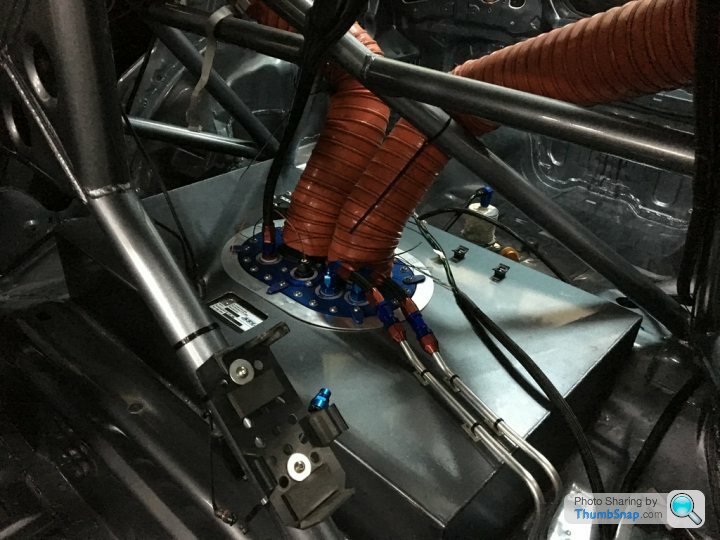
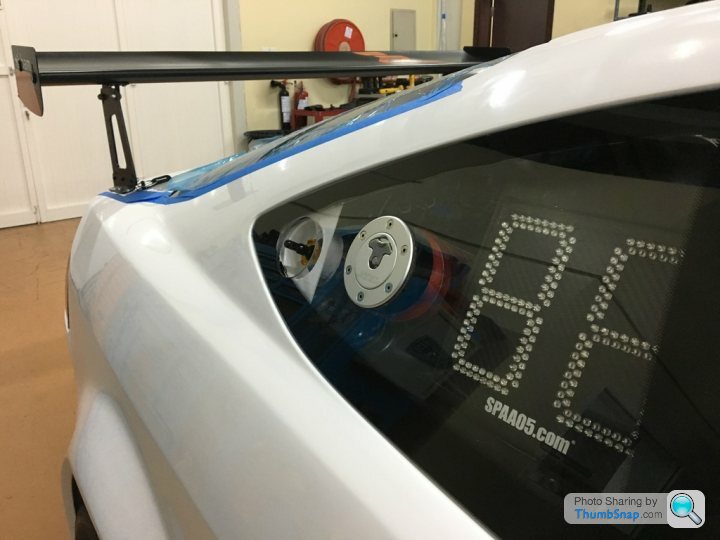
Our doors this year a much lighter. They are not the crazy expensive carbon fibre doors but still pretty good at a fraction of the cost. They do however need some fettling with regard to final fitment which resulted in no end of moaning from Julian but for those of you who know him, he would be lost if he didnt have something to moan about!

You can see the markings in the below image for trimming and painting. We ordered plastic windows (front/rear and sides) from plastics4performance in the UK. Due to the design of our doors the windows will need to be cut down slightly and fitted within the frame as opposed to sitting over the frame in the standard Integra.
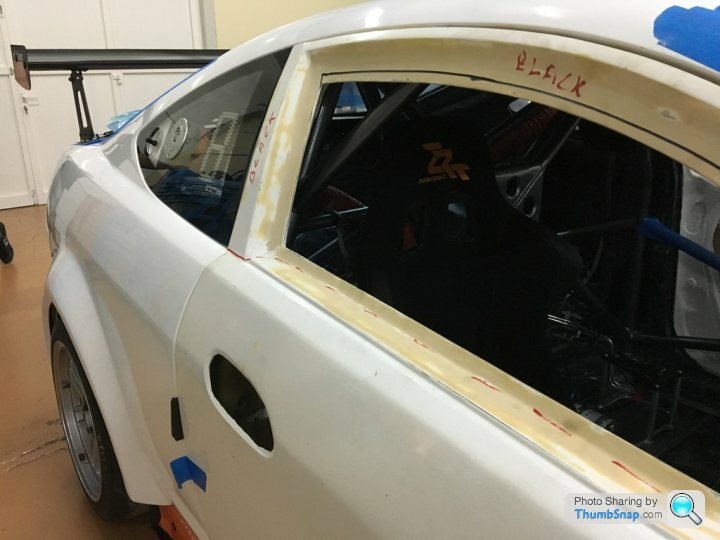
We think it will still look really great and we ordered the pro-slider for the drivers side which is really an impressive quality product. More on this next time.
Last up for this update is the dash. The holes have been filled and sadly no room for the Alpine stereo I ordered.
Go on ask the question.... Whats the fuel button for?
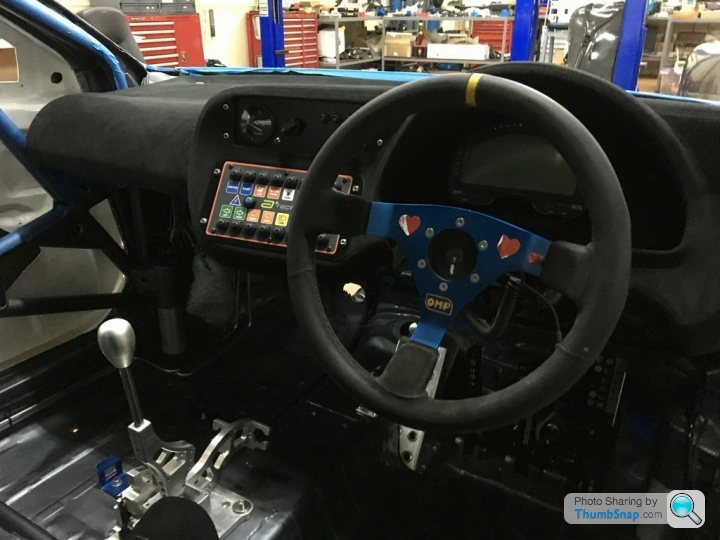
Answer: I have no idea!
Not sure we will manage another update this side of Christmas and New Years so in the meantime Happy holidays from all at ZRT
Gassing Station | Readers' Cars | Top of Page | What's New | My Stuff