McLaren F1 (Virtual) Build
Discussion
Hi all
Not quite sure where to put this on PH, but with my TVR almost finished I'm beginning to embark on a whole different sort of project.
A (Virtual) build of a Mclaren F1.
"What the hell does that mean?" I hear you ask, In essence its a very good excuse/driver to research and reverse engineer as much about my absolute dream car as possible. At the same time enhancing the basic CAD skills I'm starting out with (As an active automotive engineer, these are valuable skills).
It'll be a long process, and the chances are fairly incomplete - but the important thing here is that I'm not too fussed about replicating 100% of the parts on CAD, but those I do tackle must be thoroughly researched and replicated.
Quality NOT Quantity.
So far I've visited the car on display at the peterson auto museum in L.A. and collected a fairly good catalogue of photos showing various areas of the car.
I have SolidWorks 2007 (old but it'll do the trick) and an old version of ANSYS (for structural analysis. I meant it when I said thorough. Every part must be near enough functional should I ever wish to get them made.)
I also have "imageJ" for measuring images once a scale can be deduced.
Basically a study into the finest ever car to be created.
I've also found out the following carry-over parts:
Rear Lights - Bova Coach(/Truck?)
Front Indicators - Lotus Elan/Esprit
Headlight Projectors - BMW E34
Key - BMW E36 (or similar Era BMW)
Boot Lock - BMW E36/E34
Mirror Switch - Corsa B
Electric Window Switches - BMW E36
Indicator/Headlight Stalks - BMW E34 based
Mirrors - VW Corrado
CD Changer - Kenwood KDC C-600 (may be useful for scaling)
I thought I would tackle the pedal box first and found these:
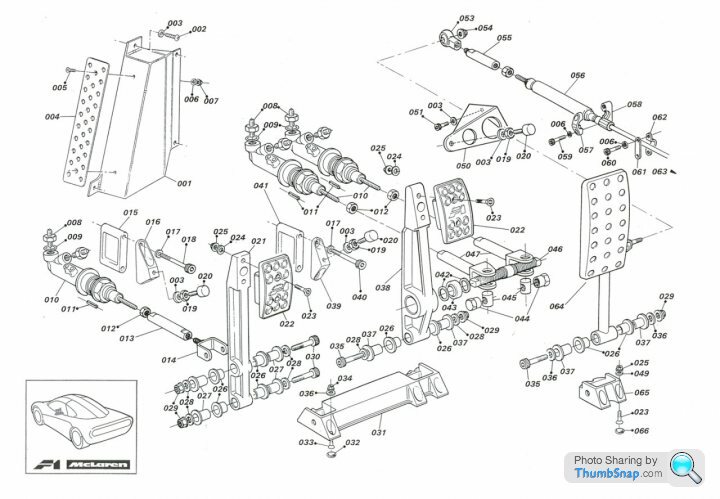
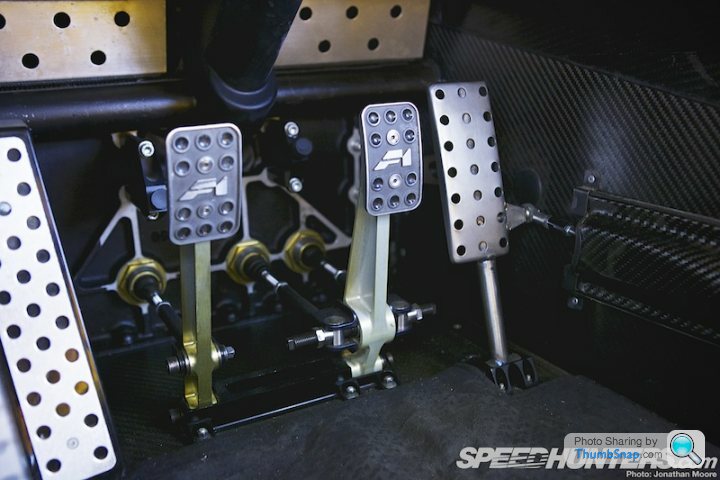
Using the below below chart (the ISO specifications for Allen Head Bolts) assuming some of them are M8 it got me started to work out the scale.
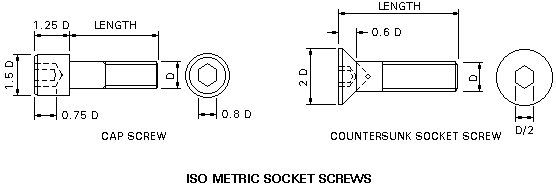
I rotated the image, and counted the number of pixels to see how many pixels/mm - A bit rough and ready, but it gets me started.
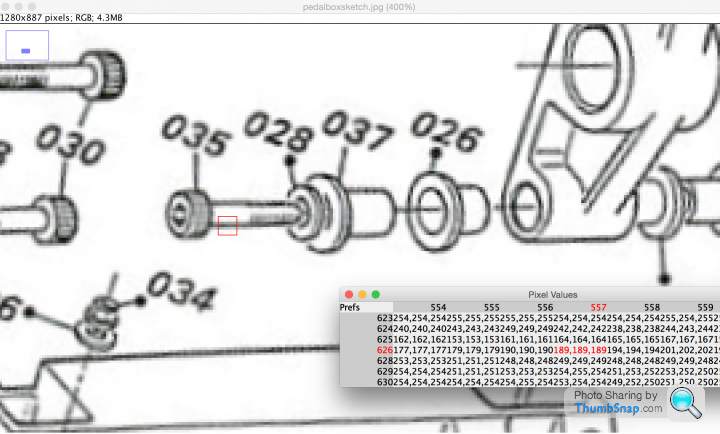
From that, I've started to tackle the clutch pedal, bare in mind that I know I have lots to learn! (which is one of the main reasons for doing this)
So from this drawing found in the F1 GTR user guide, I now have this in solidworks... (about 3 hours work....)
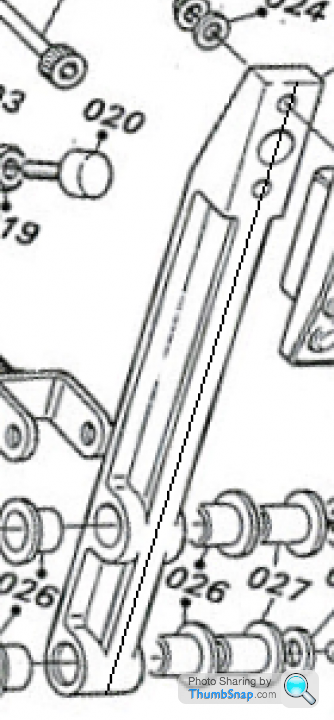
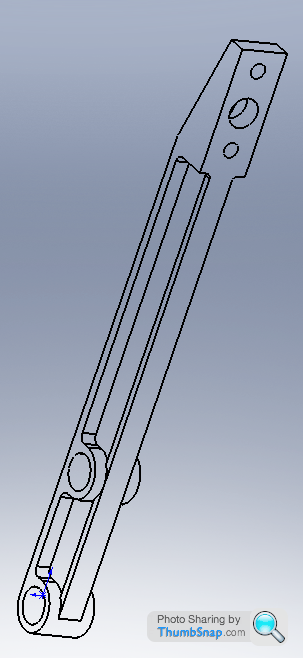
Not quite sure where to put this on PH, but with my TVR almost finished I'm beginning to embark on a whole different sort of project.
A (Virtual) build of a Mclaren F1.
"What the hell does that mean?" I hear you ask, In essence its a very good excuse/driver to research and reverse engineer as much about my absolute dream car as possible. At the same time enhancing the basic CAD skills I'm starting out with (As an active automotive engineer, these are valuable skills).
It'll be a long process, and the chances are fairly incomplete - but the important thing here is that I'm not too fussed about replicating 100% of the parts on CAD, but those I do tackle must be thoroughly researched and replicated.
Quality NOT Quantity.
So far I've visited the car on display at the peterson auto museum in L.A. and collected a fairly good catalogue of photos showing various areas of the car.
I have SolidWorks 2007 (old but it'll do the trick) and an old version of ANSYS (for structural analysis. I meant it when I said thorough. Every part must be near enough functional should I ever wish to get them made.)
I also have "imageJ" for measuring images once a scale can be deduced.
Basically a study into the finest ever car to be created.
I've also found out the following carry-over parts:
Rear Lights - Bova Coach(/Truck?)
Front Indicators - Lotus Elan/Esprit
Headlight Projectors - BMW E34
Key - BMW E36 (or similar Era BMW)
Boot Lock - BMW E36/E34
Mirror Switch - Corsa B
Electric Window Switches - BMW E36
Indicator/Headlight Stalks - BMW E34 based
Mirrors - VW Corrado
CD Changer - Kenwood KDC C-600 (may be useful for scaling)
I thought I would tackle the pedal box first and found these:
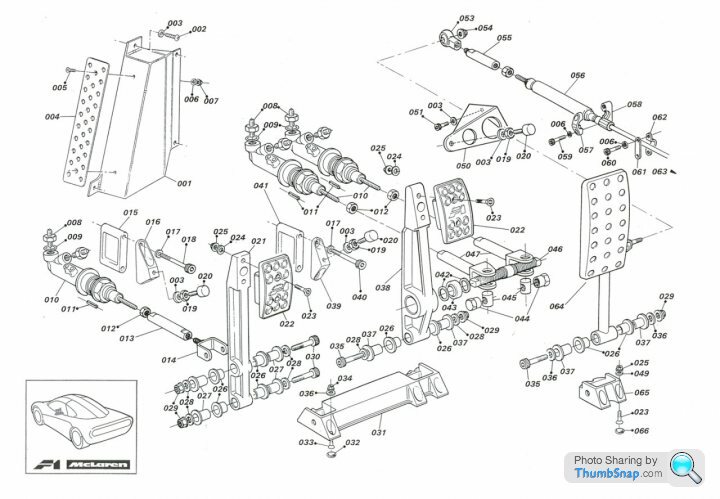
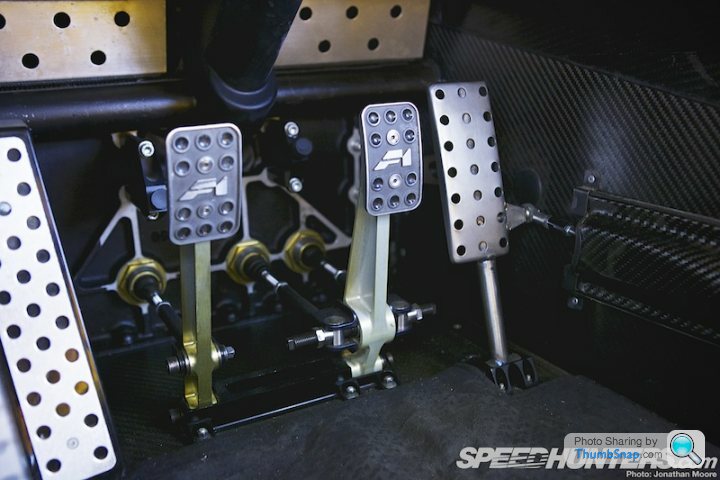
Using the below below chart (the ISO specifications for Allen Head Bolts) assuming some of them are M8 it got me started to work out the scale.
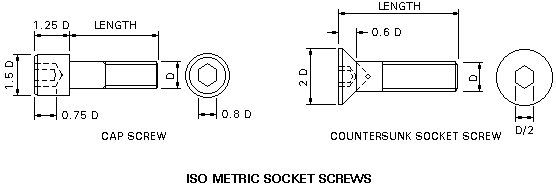
I rotated the image, and counted the number of pixels to see how many pixels/mm - A bit rough and ready, but it gets me started.
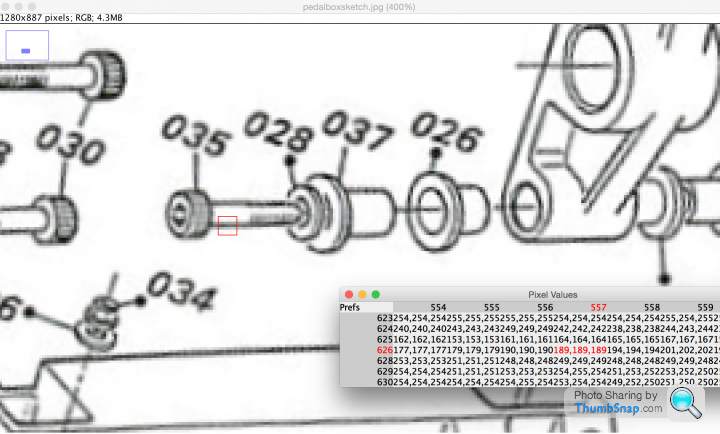
From that, I've started to tackle the clutch pedal, bare in mind that I know I have lots to learn! (which is one of the main reasons for doing this)
So from this drawing found in the F1 GTR user guide, I now have this in solidworks... (about 3 hours work....)
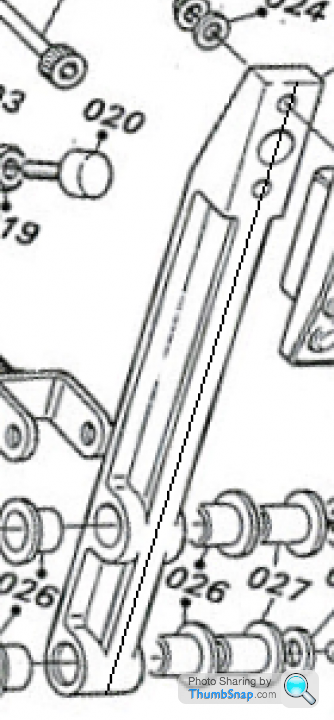
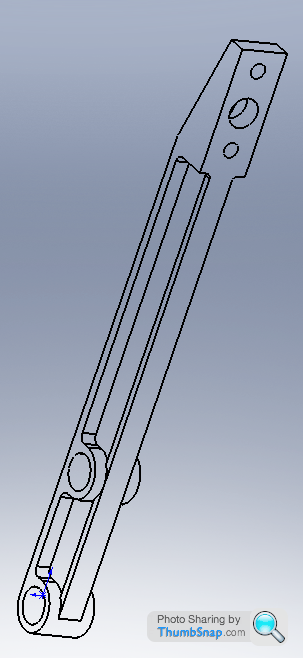
Hitch said:
Lot of time on your hands chap?
Actually yes! Just moved so saving myself 3 hours a day commuting and living away from the other half during the week- I'm not a fan of most TV and need something to get stuck into that doesn't cost me much. I don't have a driveway or garage most of the time, so this is to keep me sane.
Gav147 said:
Good luck OP, you sure got a big task ahead of you, not sure if you are aware of it but I used to browse a forum that was exactly on this topic (site is http://www.smcars.net/), might be worth a look if you are after any help, believe they have a collection of blueprints of most cars on there too for reference.
Brilliant! Ill join up.Tonights progress so far:
It seemed a little long, so I measured from my heel to the ball of my foot and realised it could do with being 15mm shorter. So I took 15mm off it.
I've also run a basic bit of stress analysis, finding that if 6061 Aluminium is used theres a factor of safety of 1.12 if 300N (30.59kg) is applied at the pedal (meaning up to 300N before any yield, comfortably), I got a gain of 51N of strength by increasing the front rib by 1mm in depth - and it weighs 207.69grams. Quite acceptable for a clutch pedal.
I've also filleted all the bits a tool wouldn't physically be able to get into to make. So (in theory) I should be able to send this off to get CNC'd up should I please.
These bring up an important consideration in this process- I'm going to make sure they are all viable, useful parts. Even if that means small deviation from visual of the original parts.
I used this article here for some ballpark figures:
http://www.ekko.mk/modules/blog/datafiles/FILE_DF3...
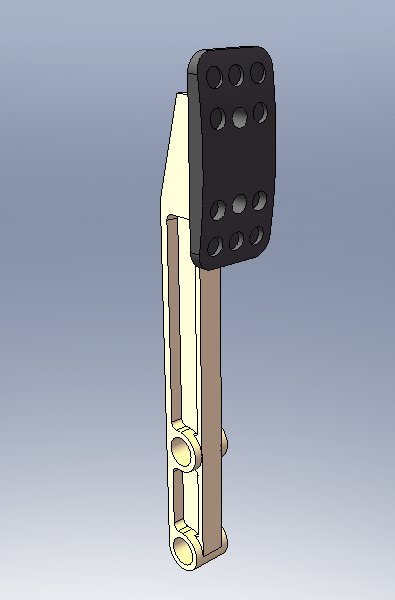

And onto the brake pedal!
It seemed a little long, so I measured from my heel to the ball of my foot and realised it could do with being 15mm shorter. So I took 15mm off it.
I've also run a basic bit of stress analysis, finding that if 6061 Aluminium is used theres a factor of safety of 1.12 if 300N (30.59kg) is applied at the pedal (meaning up to 300N before any yield, comfortably), I got a gain of 51N of strength by increasing the front rib by 1mm in depth - and it weighs 207.69grams. Quite acceptable for a clutch pedal.
I've also filleted all the bits a tool wouldn't physically be able to get into to make. So (in theory) I should be able to send this off to get CNC'd up should I please.
These bring up an important consideration in this process- I'm going to make sure they are all viable, useful parts. Even if that means small deviation from visual of the original parts.
I used this article here for some ballpark figures:
http://www.ekko.mk/modules/blog/datafiles/FILE_DF3...
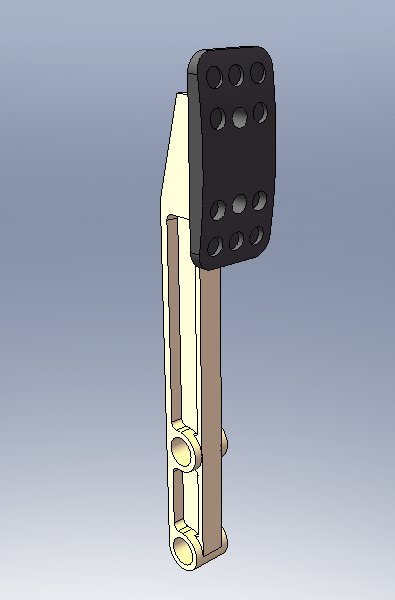

And onto the brake pedal!
I found an old study into brake pedal force, showing the 95th percentile maximum in an emergency situation to be 185lbs, which translates to 822N! Considerably more than the clutch pedal, as expected.
185lbs, is basically my bodyweight, 83kg. From sitting down, slowly lift yourself up using only 1 leg, this is the force going to the pedal...feels about right!
https://deepblue.lib.umich.edu/bitstream/handle/20...
I've Cadded up the pedal and it shows, with a load of 822N, a factor of safety of 1.2. Which is absolutely fine.
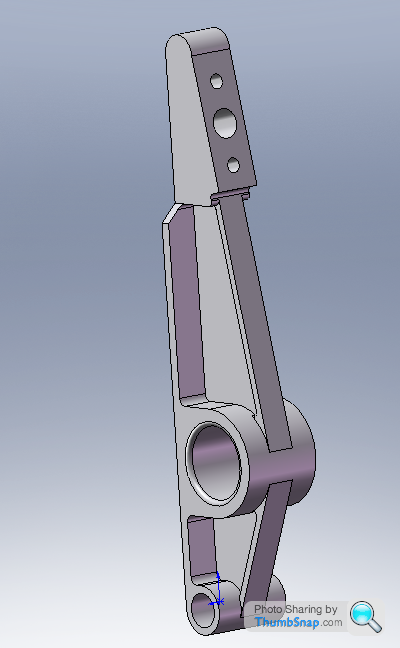
And these are the areas with a factor of safety less than 2.
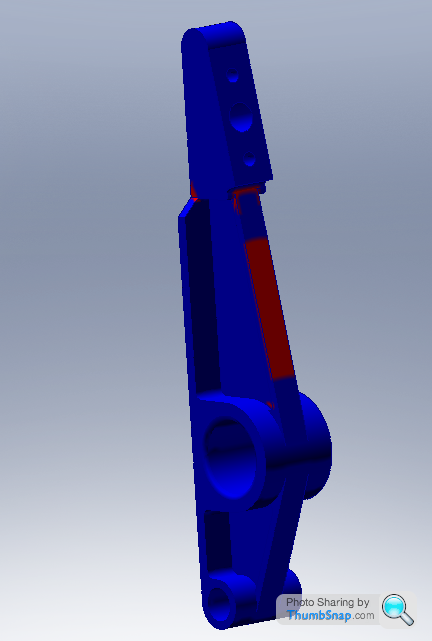
With a pedal...
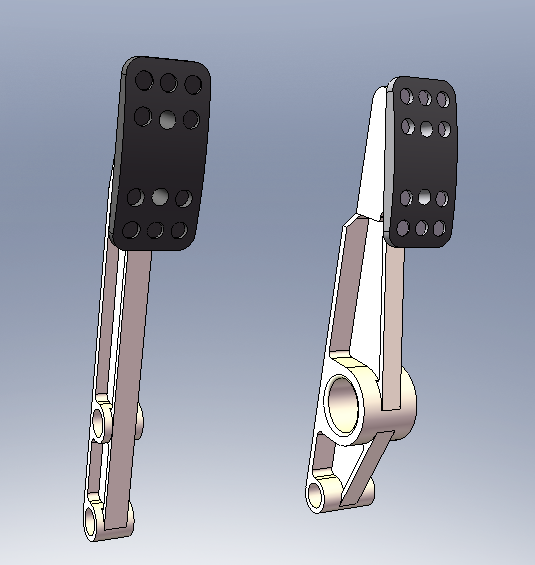
Interestingly, its around 3 times stronger than the clutch pedal, but only 363grams! An immensely strong design.
185lbs, is basically my bodyweight, 83kg. From sitting down, slowly lift yourself up using only 1 leg, this is the force going to the pedal...feels about right!
https://deepblue.lib.umich.edu/bitstream/handle/20...
I've Cadded up the pedal and it shows, with a load of 822N, a factor of safety of 1.2. Which is absolutely fine.
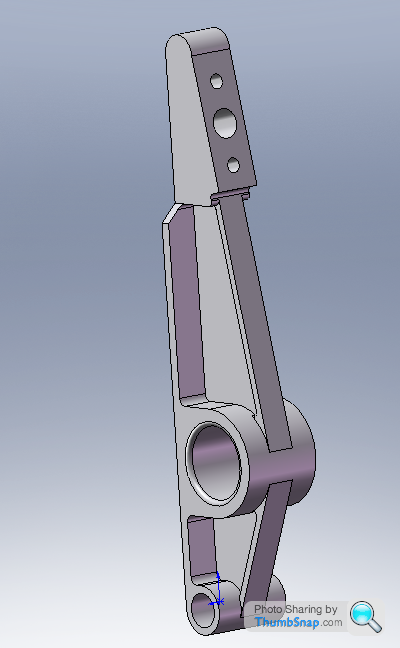
And these are the areas with a factor of safety less than 2.
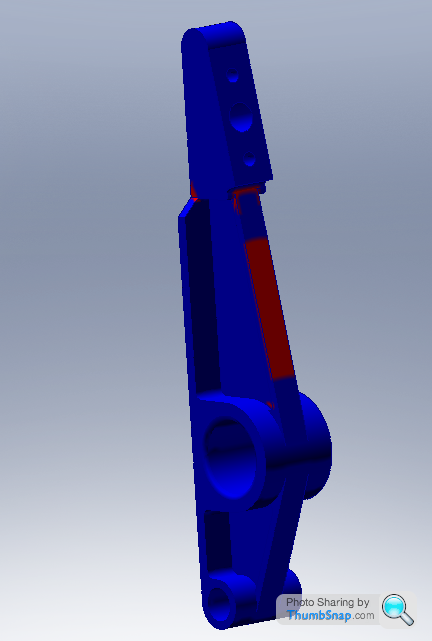
With a pedal...
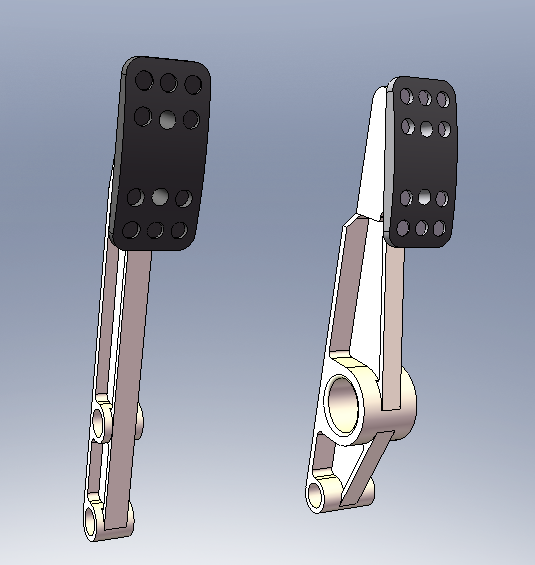
Interestingly, its around 3 times stronger than the clutch pedal, but only 363grams! An immensely strong design.
Edited by crosseyedlion on Monday 16th January 19:57
More of the same tonight. I've altered the dimensions for a perfect 5:1 pedal ratio, used an AP racing pedal box drawing for dimensions.
I've also beefed up some sections of the brake pedal and tweaked it to take the total load before any yield to 1697N or 173kg (this does not mean the point at which the pedal will fail, just the point where elements MAY be damaged)
At least this means I'd know it'd work and could be used in anger should I ever decide to get them made.
Total weight for the brake pedal and arm is now 460grams.
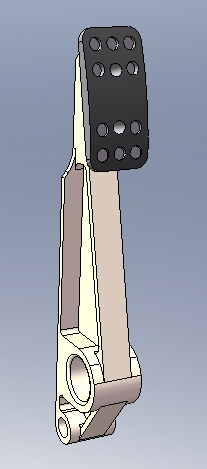
I've also modified the clutch pedal arm in a similar manner, it can now take 56kg and weights 277grams
I've also beefed up some sections of the brake pedal and tweaked it to take the total load before any yield to 1697N or 173kg (this does not mean the point at which the pedal will fail, just the point where elements MAY be damaged)
At least this means I'd know it'd work and could be used in anger should I ever decide to get them made.
Total weight for the brake pedal and arm is now 460grams.
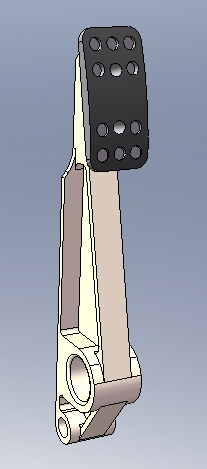
I've also modified the clutch pedal arm in a similar manner, it can now take 56kg and weights 277grams
Edited by crosseyedlion on Tuesday 17th January 19:58
xjay1337 said:
awesome awesome awesome.
The idea of having your own F1 made from bits you made would be amazing.
I genuinely hope someone at McLaren sees this project in 2 years when you've got every thing working and help make it all as a sort of throwback. Probably won't happen but here's hoping lol.
Thanks!The idea of having your own F1 made from bits you made would be amazing.
I genuinely hope someone at McLaren sees this project in 2 years when you've got every thing working and help make it all as a sort of throwback. Probably won't happen but here's hoping lol.
It's evolving already, I'm not designing replica parts as I see them. But parts near the same aesthetically which I would be confident getting made and using (big difference) - I'm not going to use guesswork for the engineering. Getting into the mindset of the designers seems to be more important.
Hence the pedal design changing from that original image.
The worst case is I get them made and put them into a kit/project car
Snubs said:
crosseyedlion said:
It seemed a little long, so I measured from my heel to the ball of my foot and realised it could do with being 15mm shorter. So I took 15mm off it.
Just a thought, but if you measured your bare foot, perhaps the pedal was originally longer to take account of the heel of your shoe, lifting the ball of your foot up by roughly that amount?Great project BTW

It's a learning process, but In the end I should end up with viable parts...
DuncB7 said:
ETA: did you use the FEA package in Solidworks for the renders earlier in the thread?
Thanks! You'll have to be patient though, I'm learning and trying to get things right at the same time. I've got a busy couple of weeks but the pedal box and the face of the front bulkhead should be modelled in couple of weeks. Edited by DuncB7 on Thursday 19th January 15:44
Regarding FEA, I'm using the very basic package that came with Solidworks 2007 (Cosmo!?). I do have ANSYS, which is much more powerful, but I'm using a 5 year old laptop and fear progress will be demotivatingly slow. So I'm going to move onto that once the bulk of the car is done.
I imagine that the FEA in Solidworks 2007 is similar or slightly better than the tools available in 1990-1992.
It's very tempting to just draw the parts (I'm fairly good at engineering drawing) - but that won't improve my skills, won't be as epic and I wouldn't be able to run it through FEA.
LankyLegoHead said:
Also a Design Engineer here, so I'll be following this.
Having said that, how do you spend all day on CAD and come home to do more? I'm struggling myself to get the motivation to scheme up some small parts for my motorbike!
Well the thing is, apart from having a quick look at parts I don't really use cad at work. I'm not a professional cad user at all. Hence the learning Having said that, how do you spend all day on CAD and come home to do more? I'm struggling myself to get the motivation to scheme up some small parts for my motorbike!

That said, I'll quite happily spend all day thinking about and talking about cars, then come home and carry on. Its an affliction I'm sure many can relate to.
TomScrut said:
The force applied in a reg 13 emergency braking test is 750N IIRC which correlates quite well with your findings.
I will be following this with interest. You may benefit from a newer version of SW where the analysis might be a bit better integrated into the program.
Yea, baring in mind that the f1 had no power assistance (so would be on the higher end of that frequently), and feel was all important (no flex in normal use allowed!) - I doubled its capacity, crudely evaluated on basic caeI will be following this with interest. You may benefit from a newer version of SW where the analysis might be a bit better integrated into the program.
Lurking said:
Have you got a copy of 'driving ambition'? McLaren's book about the F1? It has a few design images, not many, and mainly pictures of bits of paper with design spec on. But maybe one or two nuggets in there.
Its on my purchase list, along with the 1/12th model by minichamps (sanctioned by McLaren themselves) but both will run me about £500 between the 2. GetCarter said:
I'm a friend of Gordon Murray, I'll show him this thread if it's ok with you. Knowing how bonkers he is, I think he'll be interested.
He's not back in my neck of the woods until March, but I'll bookmark this.
The idea of that made me fall off my chair, I'd happily buy him lunch for an hour of his time. He's not back in my neck of the woods until March, but I'll bookmark this.
RoverP6B said:
This sounds intriguing.
If ever this project gets to the stage where a real car can be built, a suitable engine might be the BMW N73, as found in the E65 760i and Rolls-Royce Phantom. Even the long-stroke Rolls engine should be good for 9000rpm if pushed to just under 5000 feet per minute mean piston speed, and the 760i could go to 9600rpm... assuming power scales linearly to rpm, the 6.0 could make 700bhp at redline. The 6.75 could make about 760bhp at 9000rpm. Or you could build a Franken-N73 6.4 using the Rolls big-bore block and 760i crank to make 750bhp at 9600rpm. Might take a bit more compression and more aggressive cams to make such power though - and I know that, in practice, engines rarely make power all the way to redline. Even so, a pretty conservative 700bhp should be attainable. It's also a bit lighter than the S70/2 - that's 274kg, the N73 is 240kg.
I've been thinking along the same lines for the past year! Although in the hypothetical build I would use the 6.0 to start, dry sumped with itbs and a similar , it would be good for over 500hp and produces the same torque as the f1 near enough stock.If ever this project gets to the stage where a real car can be built, a suitable engine might be the BMW N73, as found in the E65 760i and Rolls-Royce Phantom. Even the long-stroke Rolls engine should be good for 9000rpm if pushed to just under 5000 feet per minute mean piston speed, and the 760i could go to 9600rpm... assuming power scales linearly to rpm, the 6.0 could make 700bhp at redline. The 6.75 could make about 760bhp at 9000rpm. Or you could build a Franken-N73 6.4 using the Rolls big-bore block and 760i crank to make 750bhp at 9600rpm. Might take a bit more compression and more aggressive cams to make such power though - and I know that, in practice, engines rarely make power all the way to redline. Even so, a pretty conservative 700bhp should be attainable. It's also a bit lighter than the S70/2 - that's 274kg, the N73 is 240kg.
In the f1 it is a stressed member though, to that would be an important consideration to engineer around.
RoverP6B said:
This sounds intriguing.
If ever this project gets to the stage where a real car can be built, a suitable engine might be the BMW N73, as found in the E65 760i and Rolls-Royce Phantom. Even the long-stroke Rolls engine should be good for 9000rpm if pushed to just under 5000 feet per minute mean piston speed, and the 760i could go to 9600rpm... assuming power scales linearly to rpm, the 6.0 could make 700bhp at redline. The 6.75 could make about 760bhp at 9000rpm. Or you could build a Franken-N73 6.4 using the Rolls big-bore block and 760i crank to make 750bhp at 9600rpm. Might take a bit more compression and more aggressive cams to make such power though - and I know that, in practice, engines rarely make power all the way to redline. Even so, a pretty conservative 700bhp should be attainable. It's also a bit lighter than the S70/2 - that's 274kg, the N73 is 240kg.
I've been thinking along the same lines for the past year! Although in the hypothetical build I would use the 6.0 to start, dry sumped with itbs and a similar , it would be good for over 500hp and produces the same torque as the f1 near enough stock.If ever this project gets to the stage where a real car can be built, a suitable engine might be the BMW N73, as found in the E65 760i and Rolls-Royce Phantom. Even the long-stroke Rolls engine should be good for 9000rpm if pushed to just under 5000 feet per minute mean piston speed, and the 760i could go to 9600rpm... assuming power scales linearly to rpm, the 6.0 could make 700bhp at redline. The 6.75 could make about 760bhp at 9000rpm. Or you could build a Franken-N73 6.4 using the Rolls big-bore block and 760i crank to make 750bhp at 9600rpm. Might take a bit more compression and more aggressive cams to make such power though - and I know that, in practice, engines rarely make power all the way to redline. Even so, a pretty conservative 700bhp should be attainable. It's also a bit lighter than the S70/2 - that's 274kg, the N73 is 240kg.
In the f1 it is a stressed member though, to that would be an important consideration to engineer around.
thegreenhell said:
crosseyedlion said:
if 6061 Aluminium is used
I'm sure I read many years ago that the pedals were machined from titanium.That would explain having to add a little bulk though. Thanks.
Gassing Station | Readers' Cars | Top of Page | What's New | My Stuff