opinions sought re small 12cyl twin turbo
Discussion
This is all theoretical ATM with the view of doing it for real in the near future.
Specs:
Bore 60mm
Stroke 60mm
Valve lift 10mm and using 1.5 ratio roller rockers
Inlet valves 2 - 24mm with 28mm diameter ports running approx 70mm in length - 1 port for EACH valve
Exhaust valves as above but 21mm valves and 25mm diameter ports
Im looking at running 1 turbo for each bank of 6 cylinders. Looking at data a gt25r would be nice for each bank.
Rpm redline is 13k and max power from those 2 gt25s is approx 640bhp @ 12000rpm.
The thing I'm considering is using slightly smaller turbos so they spool up quicker without sacrificing much on power.
Any recommendations? I much prefer garret turbos but willing to look at others if they fit the bill.
Also for the more knowledgeable, is there a way of calculating theoretical airflow through an open port? Given the diameter, length and atmospheric pressure? Just curious
Just looking for more input from a fresh brain looking at it. Maybe we can "debate" whether its worth running turbos aside from the fact everyone loves a turbo
Specs:
Bore 60mm
Stroke 60mm
Valve lift 10mm and using 1.5 ratio roller rockers
Inlet valves 2 - 24mm with 28mm diameter ports running approx 70mm in length - 1 port for EACH valve
Exhaust valves as above but 21mm valves and 25mm diameter ports
Im looking at running 1 turbo for each bank of 6 cylinders. Looking at data a gt25r would be nice for each bank.
Rpm redline is 13k and max power from those 2 gt25s is approx 640bhp @ 12000rpm.
The thing I'm considering is using slightly smaller turbos so they spool up quicker without sacrificing much on power.
Any recommendations? I much prefer garret turbos but willing to look at others if they fit the bill.
Also for the more knowledgeable, is there a way of calculating theoretical airflow through an open port? Given the diameter, length and atmospheric pressure? Just curious

Just looking for more input from a fresh brain looking at it. Maybe we can "debate" whether its worth running turbos aside from the fact everyone loves a turbo

Max_Torque said:
Let me get this clear:
You want to engineer a completely bespoke high performance race engine from scratch, and yet you need to ask how to calculate port flow??
Er, don't take this as negative, but are you sure you have the skills and money to make that work?
Yes I do, You want to engineer a completely bespoke high performance race engine from scratch, and yet you need to ask how to calculate port flow??
Er, don't take this as negative, but are you sure you have the skills and money to make that work?

If you don't ask you will never know

I don't often takes things negative unless it's a complete slant. I quite agree with your point and whilst lacking the funds at present I do believe I have the skills.
I can't double quote here for some reason so I'll have to double post - sorry

davepoth said:
Crankshaft is going to the critical thing IMO - I guess it's the only fully custom part (I assume cylinder heads and crankcases are coming from elsewhere and being welded together?) and it's going to be a pricey job to make it do everything you want since it'll be so long.
Did you consider making an H16 instead? The noise is even more epic than a flat 12...
crankshaft below (roughly drawn up and needs more work/modifying and the lighting in the pic is awful - i'm still getting to grips with the program). Everything is going to be machined, crankcase, block, heads, cam carriers, sump pan will be made from sheet ally with a kickout and probably gated.Did you consider making an H16 instead? The noise is even more epic than a flat 12...
length is approx 590mm so not that long really

I did think about making a H24 like a napier sabre but it would cost 3 times as much and whilst the noise would more than likely justify it the mechanics of it wouldn't, plus it would be heavier and higher which I didn't want.

^^ hopefully I got the code right

Evoluzione said:
You need:
An engine simulation package
An engine (or specifications of) with your 60mm bore and stroke - possibly a motorbike engine? so you can study the head.
A lot of money
performance trends engine analyzer An engine simulation package
An engine (or specifications of) with your 60mm bore and stroke - possibly a motorbike engine? so you can study the head.
A lot of money

a lot of money agreed, about 40k covers it, which if you consider all the machining and materials involved isn't THAT expensive for a 1 off.
I suppose a V engine would be simpler but that's the norm IMO, I was looking to do something a bit more...i suppose crazy lol

I appreciate the comments/critics, all taken on board so far.
anyone have any input on the original question re turbos?

Max_Torque said:
I suspect the engine would never run, or only for a few seconds before failure however.
Would you care to elaborate this theory please? 
as for the costing, £400k seems a little on the crazy side of what I have costed so far.
I agree there are ALOT of parts to this engine...
12 pistons and rods
12 cylinder liners
48 valves, springs, caps, rockers, guides, seats.
4 rocker shafts
4 camshafts
1 billet crank
24 Big end shells
14 Main bearing shells
2 identical crankcases (probably cast this so just needs final machining)
2 identical split heads
2 identical blocks (probably cast this so just needs final machining)
2 identical cam covers
2 exhaust manifolds (make these myself)
2 inlet manifolds (make these myself)
1 sump pan (make this myself)
1 or 2 water pumps - depending on how I decide to do it - might go for electric though (saves a little on machining)
1 billet flywheel
1 clutch (twin plate)
1 release bearing and associated cylinders
2 turbos
12 piston cooling jets
2 timing chains
slippers and tensioners
oil pump (purchase a good generic aftermarket one - whichever fits the bill best)
12 injectors
fuel tank and pump (make fuel tank myself)
not forgetting:
2 headgaskets
14 Main bolts
28 head bolts
2 thermostats & housings - or 1 common thermostat but i think 2 is better (1 per side)
12 spark plugs
HT leads/coil packs depending on which I decide on being best
oil and a filter
other associated gaskets
front and rear main seals and housings
front timing chain covers
more miscellaneous bolts/nuts
and balancing the engine
not a bad little shopping list really. I can go and pick it all up, who's gonna pay for it?

In answer to some of the questions,
@AER - I appreciate all constructive input and criticism and in answer to some of the points you raised,
I don't think the surface to volume ratio needs to be considered with too much vigor due to me only running a CR of 8.5/9:1. not like i'm going F1 spec with 13:1 and N/A for that kind of power.
reason I want 12 cylinders and low cc is: 12 cylinders at 2 litre means less stress per cylinder as opposed to a 4cyl @ the same rpm and power output, crank is 7 main bearing so no different to a conventional V12 but the HOP will be more balanced between these mains.
Re the firing order, yes I agree. I was considering going along the lines of the jaguar v12 firing order at first but oweing to the fact mine is completely different, I don't think it would pan out.
The idea is to use the engine in a circuit racing car similar to an atom/caterham - no road use, just track.
With regard to "schwerpunkt", If I package it well it "should" have a lower COG than a V8 or a V12, unles they're 180 degree V's ofcourse

Bladerider: thanks for the input, I think the GT28 is too big - the exhaust gas flow won't spool it up quick enough unless i go VGT or get a specific housing made up (hybrid), accoding to PFEA it won spool until about 9000rpm whereas the gt25r is the best match I can find so far spooling at 6000rpm and holding it right through to 12000rpm @14psi. I'll definately look at contacting the guys at Turbo Dynamics, Thanks.
@dblack1: I suppose coolness is a factor yes, but who doesn't like the sound of 12 cylinders going over 9000rpm?


@Evoluzione: i am speccing the turbos to the engine BEFORE building it because it's the best way. If I build the engine then spec the turbos for it I will likely have to change something which would cost more. better to do it right first time than have to stepback and redo something.
Edited by jimbob82 on Tuesday 12th February 21:05
Max_Torque said:
If you had said:
"I have spent 30 years designing and developing race engines from scratch, and i have a £200k budget" then yes, there is a chance that a completely bespoke one off engine might run properly the first time and not pick up a ring, scuff a bore, spin a bearing, suffer from oil starvation, experience valve float, have a thermal failure of parts of the cylinder head, have a TV failure of the crank, or about a thousand other things that can, and do, go wrong with bespoke engines.
I should know, i've broken enough of them............. Anyway, i wish you the best of luck with this project!
regarding CofG, there is no point whatsoever in having the engines CofG very low if you can't package the engine low in the chassis because for example you have to fit an exhaust system underneath. As you can see, there are exactly no F1 engines using flat layouts for this very reason (and the only production car that does has a high CofG due to such package limitations.
I assume you have a plan to accomodate the necessary bank stagger and deal with stuff like timing drive to identical head castings/machinings etc?
OK thanks for the input. I appreciate what your saying but everyone has to start somewhere no? "I have spent 30 years designing and developing race engines from scratch, and i have a £200k budget" then yes, there is a chance that a completely bespoke one off engine might run properly the first time and not pick up a ring, scuff a bore, spin a bearing, suffer from oil starvation, experience valve float, have a thermal failure of parts of the cylinder head, have a TV failure of the crank, or about a thousand other things that can, and do, go wrong with bespoke engines.
I should know, i've broken enough of them............. Anyway, i wish you the best of luck with this project!
regarding CofG, there is no point whatsoever in having the engines CofG very low if you can't package the engine low in the chassis because for example you have to fit an exhaust system underneath. As you can see, there are exactly no F1 engines using flat layouts for this very reason (and the only production car that does has a high CofG due to such package limitations.
I assume you have a plan to accomodate the necessary bank stagger and deal with stuff like timing drive to identical head castings/machinings etc?

Thanks for the best wishes

re bank stagger:
I have that sorted yes.
SuperchargedVR6 said:
I pondered on this last night in bed (sad I know) and wondered why 12 cylinders would be required to get 640hp from 2 litres? Is it a hp per cylinder thing or just a mega revs thing?
12 cylinders aren't strictly "required" for that HP. 12 vs 4 at the same output means less stress per piston.12 cylinders @ 640hp = approx 50HP per piston
vs
4 cylinders @640hp = approx 160HP per piston
with more pistons and shorter stroke it will rev quicker aswell and lighter flywheel can be used

Nick1point9 said:
R&D obviously isn't your thing... Do you really think the first engine you make will work well? With highly skilled engineering you might have something that works well after attempt 4 or 5, so absolutely no way under the sun you'll get what you want for £40k. Oh and wait until you break one.

-Bladerider- said:
I dont think sensibleness is what is wanted !! lol
I think "extreme" "unique" and "because its a challenge" are the prime buzzwords !!
lol, nail on the head I think "extreme" "unique" and "because its a challenge" are the prime buzzwords !!

SuperchargedVR6 said:
The last time I flicked through the net about Duratecs, I'm sure I saw a 320hp n'asp one. Standalone, ITBs, cams, the lot. One of those with a turbo would be impressive I reckon.
yeh the ecotecs can do 300bhp N/A too, seen one recently being fitted into a mk2 escort.if you turbocharged one of those without modifying them you'd highly likely blow the thing to bits.
from that 320bhp you quoted, you'll probably find it's developing that power somewhere around or between 7k-9krpm depending on how they've set it up. that's why F1 engines run at 19krpm, if you want more power without turbocharging or increasing displacement you have to rev higher. higher revs = higher piston speeds and piston acceleration which in turn puts more pull on the inlet ports thus increasing VE% and developing more power. This isn't as much a factor when turbocharging because the turbo is always FORCING the air in, (when it's operating at boost level, before boosting it's lagging because it can't supply the amount of air required). but you more than likely know this

Nick1point9 said:
If you don't mind me asking, what is your professional background?
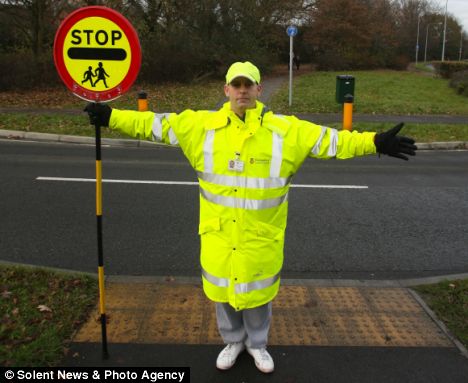
^^ THIS
is something I could never do

I've been a mechanic for about 15 years, engine rebuilds mainly but also general mechanics. also do body repair and light fabrication. my business partner has been a mechanic for over 50 years (used to work for rolls royce, jaguar, aston martin), he was tuning jags in the 60's & 70's and he's taught me most of what i know. the rest I have gleened from books and other people.
Edited by jimbob82 on Thursday 14th February 11:09
andygtt said:
Im always doing things professionals think I am mad attempting in my garage... however even I think designing and building an engine from scratch is an epic task to do right.
Worth mentioning that some of the people I have seen replying on here actually do this kind of thing for a living... so take heed of their advice.
The areas I would be concerned about in the design would be hot spots and oiling... not simple to avoid I expect... also how are you going to design out the chance of the engine producing a harmonic at any rev that destroys itself?
Id be basing the design around something existing which is what most of the bespoke engines I have seen have done... ie take a bike engine and use the heads on a new block and crank.
Good luck and keep us informed of progress.
I accept, appreciate and welcome all advice AND criticism and will heed warnings. Epic task yes. But I wanted a challenge Worth mentioning that some of the people I have seen replying on here actually do this kind of thing for a living... so take heed of their advice.
The areas I would be concerned about in the design would be hot spots and oiling... not simple to avoid I expect... also how are you going to design out the chance of the engine producing a harmonic at any rev that destroys itself?
Id be basing the design around something existing which is what most of the bespoke engines I have seen have done... ie take a bike engine and use the heads on a new block and crank.
Good luck and keep us informed of progress.

Oiling and hotspots is a concern but I think I can design a way to reduced/limit the possibility. All this is theoretical at the moment as stated in my OP but I do hope to be able to build it for real. Subject to more experienced approval/appraisal.
The harmonics are going to be my biggest concern and probably the most likely culprit for failure. I'd have to get a custom harmonic damper of course but they're only good to a point. If the firing order is panned out to eliminate the chances I think I'd be in with a chance of it being reliable, to an extent anyway.
Maybe someone could give advice on my current firing order and let me know what they think.
With regard to other bespoke engines, I don't want anyone to take this the wrong way or think I'm trying to be clever, but the way I thought about it was that if your going to make a bespoke engine yourself do it from scratch. Using another engine or multiples of is sort of cheating in my mind. I'm not saying its wrong and shouldn't be done quite the contrary. I would emplore anyone to do it if they so wish. I just wanted to do it differently. This brings more problems and likelyhood of failure but at least if/when I do get it done and its working sweet and reliable I can stand back and say the good old words "I made that"

Probably stupid thinking to some people but a sense of accomplishment like that would rival no other IMO.

now then,
the block and crankcase is as follows:


note the offset for the bores, this means that I could use the same identical units each side, allowing for a cheaper production cost, 2 identical patterns = cheaper to machine.
The heads were going to be billet, only the crankcase and block were going to be casted (rough) then final machined. in answer to a previous question I was considering casting these parts myself. The application of casting in itself is not difficult but getting the right scale to allow for shrinkage when the ally cools is where it can get tricky.

Cost for the crank as a 1 piece billet with the appropriate treatments is approx 4k from Arrow Precision, but that was subject to them getting a drawing and whether I wanted 1 or more. Not that bad for a custom crank. It doesn't HAVE to be a 1 piece however. Hirth couplings would save alot of aggro yes, I'll consider this and investigate it further. Wasn't the aston martin V12 using a flat plane crank aswell? IIRC that on it's own was enough of a problem, without the oil troubles.the block and crankcase is as follows:


note the offset for the bores, this means that I could use the same identical units each side, allowing for a cheaper production cost, 2 identical patterns = cheaper to machine.
Tango13 said:
I've been thinking this over after a couple of boring night shifts...
Firstly get a copy of Karl Ludvigsens' book on the V12 engine, it will give you a few ideas as to the problems and pit falls involved and as I posted the other day there is a good section on firing orders which should help.
I will do this asap and have a good red through.Firstly get a copy of Karl Ludvigsens' book on the V12 engine, it will give you a few ideas as to the problems and pit falls involved and as I posted the other day there is a good section on firing orders which should help.
Tango13 said:
A couple of questions for the Op...
How bespoke were you planning on going and does it have to be 2litres? If you want to save a lot of time, money, R&D etc you could buy over the counter pistons & rings from a CRF150 dirtbike, it would mean either a shorter stoke or a slightly bigger engine though.
I was going FULL custom/bespoke pretty much EVERYTHING would be custom, pistons, nimonic exhaust valves with stellite seats, 214 inlet valves, custom rods, crank, pistons, cams, rockers - all to my specs/design. It doesn't HAVE to be 2 litre it was just what I settled on being the most viable stroke/bore/cost wise - in relative terms.How bespoke were you planning on going and does it have to be 2litres? If you want to save a lot of time, money, R&D etc you could buy over the counter pistons & rings from a CRF150 dirtbike, it would mean either a shorter stoke or a slightly bigger engine though.
Tango13 said:
With regards the cylinder heads have you given any thought to how you were going to make them? Casting is far too involved and expensive for a 2off, plus spares. It would be much easier to machine them from a solid billet and then weld the water jacket around the ports etc. Again a dirt bike head would give you some ideas as to port shape etc which could be laser scanned to provide the machine code for manufacture. Valves, guides and seats could possibly come from a dirtbike too.
as I put above, I was going to get the heads machined in 2 piece, machine everything around the ports for the water flow and then have the other section of the head that takes the cams, rockers and valve springs, etc bolted on top - as I understand it this is how some or maybe most of the NHRA monster engines are built.The heads were going to be billet, only the crankcase and block were going to be casted (rough) then final machined. in answer to a previous question I was considering casting these parts myself. The application of casting in itself is not difficult but getting the right scale to allow for shrinkage when the ally cools is where it can get tricky.
Tango13 said:
Cam shaft drive and where abouts on the crank also gears, chain or belt? I think it was BMW who built a prototype race V12 that had one bank driven from the front of the crank and the other from the rear, this allowed them to 'cheat' and use the same head for each bank. I'd go with gears for two reasons, first you can build up the gears in their own carrier so you can test them with out risking the engine and secondly they will sound >insert cliche here< at high revs!
If you take the cam drive from the center of the crank then you could bolt the cams onto a central gear allowing a shorter cam which would be easier/cheaper to make.
I was considering helical geared for the cams but the cost would be insane, I decided on a chain drive (duplex) and 1 going to each cam bank (2 x duplex chains) but run them from the crank via a helical drive to an idler with 2:1 ratio for the chains to run off. central chain is a good idea but it would increas machining and crankshaft costs significantly I think, plus the centre main is in the way lol If you take the cam drive from the center of the crank then you could bolt the cams onto a central gear allowing a shorter cam which would be easier/cheaper to make.

Tango13 said:
Crankshaft, Is there any reason it has to be one piece? A V12 crank is a big expensive lump of metal but if you were to build it up using Hirth couplings it would save an awful lot of aggravation. It would also allow the use of ball races for the crank bearings so you wouldn't have the same oil pressure problems Aston Martin had with their V12
For the crankcases again I'd take the top half from a solid billet but with the horizontal split below the centerline of the crank to help with keeping things rigid. I'd keep the barrels seperate from the head and cases for ease of manufacture and costs though and again I'd try to design it to allow for a welded water jacket.
For the crankcases again I'd take the top half from a solid billet but with the horizontal split below the centerline of the crank to help with keeping things rigid. I'd keep the barrels seperate from the head and cases for ease of manufacture and costs though and again I'd try to design it to allow for a welded water jacket.
The crankcase pictured above is not finished - obviously - there's no sump


The images if nothing else will more than likely give people something to laugh at lol.

Anyway, further to my post of last night. I have decided to take a different approach to my first build. I'll start another thread to discuss it as I'd like to keep this unmolested for when I return to it. I'm not giving up on this, just re-evaluating my current position. I'll keep posting here regarding any questions, comments or advice and look forward to hearing all of them.

Gassing Station | Engines & Drivetrain | Top of Page | What's New | My Stuff