The geometry of cam / follower systems
Discussion
After this topic popped up in a recent thread I thought I'd write a brief article to explain the salient points. The majority of engines are either pushrod and rocker (old skool), overhead cam and bucket or cam lobe sliding on a finger follower (Ford Pinto).
The key thing about a round follower is it has to rotate to survive. This evens up wear and allows the cam lobe to bed into the follower and let both items work harden.
Pushrod engines have followers that tend to be in the 3/4" to 7/8" diameter range. Cam lobes are generally half an inch wide or so to generate sufficient stiffness. To rotate the follower the cam lobe has to operate on one side of it. With a follower 3/4" diameter and a lobe 1/2" wide even if you position the lobe right on one side of the follower some of the lobe is acting on the opposite side of the follower and trying to spin it back in the opposite direction.
To counter this pushrod followers are made with a very small convex radius on the top surface. Generally about 1 metre radius of curvature or 2 metres diameter. This gives the follower a dome about 2 thou high which can only be detected against a good straight edge. To run against this the cam lobe is ground with a very small angle from one side to the other, also about 2 thou high from side to side. This angle runs against one side of the dome of the follower so that any part of the cam lobe that extends to the other side of the follower doesn't contact it. This ensures all the forces make the follower spin in one direction.
With overhead cam engines the followers can be much larger in diameter. Normally between 25mm and 40mm diameter. A normal sized cam lobe can sit entirely on one side of the follower. This now means a flat cam lobe can spin the follower one way only if it's positioned entirely on one side of the follower.
So overhead cam engine followers are dead flat and can be resurfaced on a grinder or flat plate with a sheet of wet and dry paper if they have any wear. Pushrod followers are not repairable which is why they have to be replaced with new ones every time you change the cam.
Finger followers have a hard life and unless made of carbide or chill cast iron they tend to wear out steadily over time because the cam lobe wipe area is basically over the whole area of the follower. They also have to be replaced with the cam every time a change is made.
If any points are unclear I'll expand on them.
Edit 15th Feb.
I'll just add a couple of points about grinding cam lobes for domed followers. Firstly it's obviously vital that the small angle ground on the cam lobe runs the correct way in relation to the dome on the lifter and this depends on which side of the lifter the cam follower sits, at least from the perspective of the guy grinding the cam and which way round he's got it held in the grinder. So he has to know the layout of the components in the engine block and for every type of cam he grinds he'll have a spec sheet which says either no lobe angle for OHC engines with flat lifters or it'll say lobe angle runs left to right or right to left and specify how much angle is to be used.
Secondly how does one actually grind an angle across the surface of a cam lobe. That's really easy. You grind the angle into the cam grinder abrasive wheel first. The grinding wheel is dressed with a diamond tipped tool and on a cam grinder the angle at which this traverses the wheel face can be adjusted from parallel for flat tappet cams to sloping L/R or R/L by varying amounts for domed lifters.
The key thing about a round follower is it has to rotate to survive. This evens up wear and allows the cam lobe to bed into the follower and let both items work harden.
Pushrod engines have followers that tend to be in the 3/4" to 7/8" diameter range. Cam lobes are generally half an inch wide or so to generate sufficient stiffness. To rotate the follower the cam lobe has to operate on one side of it. With a follower 3/4" diameter and a lobe 1/2" wide even if you position the lobe right on one side of the follower some of the lobe is acting on the opposite side of the follower and trying to spin it back in the opposite direction.
To counter this pushrod followers are made with a very small convex radius on the top surface. Generally about 1 metre radius of curvature or 2 metres diameter. This gives the follower a dome about 2 thou high which can only be detected against a good straight edge. To run against this the cam lobe is ground with a very small angle from one side to the other, also about 2 thou high from side to side. This angle runs against one side of the dome of the follower so that any part of the cam lobe that extends to the other side of the follower doesn't contact it. This ensures all the forces make the follower spin in one direction.
With overhead cam engines the followers can be much larger in diameter. Normally between 25mm and 40mm diameter. A normal sized cam lobe can sit entirely on one side of the follower. This now means a flat cam lobe can spin the follower one way only if it's positioned entirely on one side of the follower.
So overhead cam engine followers are dead flat and can be resurfaced on a grinder or flat plate with a sheet of wet and dry paper if they have any wear. Pushrod followers are not repairable which is why they have to be replaced with new ones every time you change the cam.
Finger followers have a hard life and unless made of carbide or chill cast iron they tend to wear out steadily over time because the cam lobe wipe area is basically over the whole area of the follower. They also have to be replaced with the cam every time a change is made.
If any points are unclear I'll expand on them.
Edit 15th Feb.
I'll just add a couple of points about grinding cam lobes for domed followers. Firstly it's obviously vital that the small angle ground on the cam lobe runs the correct way in relation to the dome on the lifter and this depends on which side of the lifter the cam follower sits, at least from the perspective of the guy grinding the cam and which way round he's got it held in the grinder. So he has to know the layout of the components in the engine block and for every type of cam he grinds he'll have a spec sheet which says either no lobe angle for OHC engines with flat lifters or it'll say lobe angle runs left to right or right to left and specify how much angle is to be used.
Secondly how does one actually grind an angle across the surface of a cam lobe. That's really easy. You grind the angle into the cam grinder abrasive wheel first. The grinding wheel is dressed with a diamond tipped tool and on a cam grinder the angle at which this traverses the wheel face can be adjusted from parallel for flat tappet cams to sloping L/R or R/L by varying amounts for domed lifters.
Edited by Pumaracing on Sunday 15th February 10:39
Stan Weiss said:
Dave,
I use the lifter radius minus a small amount for safety times PI divided by 180.
? ((.842 / 2) - .01) * pi / 180 = 0.0071733
Stan
Ok, I see what you're doing. I normally work in crank degrees of rotation which would therefore be pi/360 but we also use different safety margins which was why I couldn't quite tie up your numbers.I use the lifter radius minus a small amount for safety times PI divided by 180.
? ((.842 / 2) - .01) * pi / 180 = 0.0071733
Stan
I would suggest that 10 thou is too small a number to safely use. It comes down to contact patch size for the cam lobe and therefore the pressures generated. The further away from the circumference of the lifter the longer the contact patch can be and this is a chord geometry problem.
So let's assume a 20mm diameter lifter and we want to find the chord length at 10 thou (0.254 mm) from the edge. It comes to 4.5 mm long and remember half of that is on the wrong side of the lifter if the lifter is domed. That leaves only 2.25 mm of lifter for the lobe to push against.
The safety margin normally used is 25 thou I believe. On the above example that would produce a chord 7 mm long with 3.5 mm of that on the "right" side of the lifter.
Now obviously as the follower gets bigger the chord length also increases at a given distance from the edge so the safety margin can be reduced a tad but for pushrod engine sized lifters I'd think that 25 thou is a far as one could push things.
For those reading this who are perplexed by what Stan and me are wittering on about I was going to cover this in the second half of the topic. Here's a nice drawing of a cam lobe acting against a flat lifter.
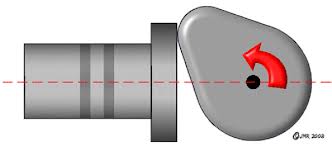
You can see that the contact point is well away from the centreline of the cam lobe, out towards the edge of the lifter. If you imagine the cam continuing to rotate the contact point will move back to the dotted centreline as the cam nose reaches peak lift and also be there whenever the cam is on its base circle.
You can also see that because the lifter is circular, when the contact point is so far out towards the edge then not all of the cam lobe is actually touching the lifter. Most of it is sticking out into fresh air. Only a bit of one edge of the lobe is pushing against the lifter. Here's another nice pic of cam lobe wear patterns.
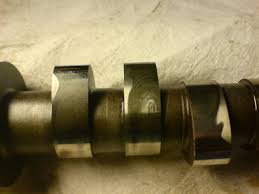
The shiny bits are where the cam lobe is touching the lifter. The base circle is shiny so we can tell this cam operated against a hydraulic lifter which stayed in contact with it all the time unlike a solid lifter cam which will have a tappet clearance. Then you get the distinctive half moon shiny bit up near the nose which matches where the cam lobe was touching in the first drawing. Most of the flank of the lobe never touches the lifter at all.
So what determines how far out this contact point moves? Clearly it can't move out beyond the edge of the lifter because then the lobe would miss the flat face of the lifter, dig into its edge and everything would break. I'll cover that in the next part. In the final part I'll look at the various parts of the cam lobe geometry, how they are specified and what effect each one has on engine performance.
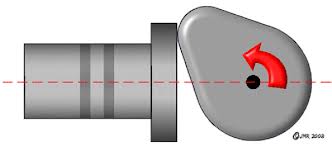
You can see that the contact point is well away from the centreline of the cam lobe, out towards the edge of the lifter. If you imagine the cam continuing to rotate the contact point will move back to the dotted centreline as the cam nose reaches peak lift and also be there whenever the cam is on its base circle.
You can also see that because the lifter is circular, when the contact point is so far out towards the edge then not all of the cam lobe is actually touching the lifter. Most of it is sticking out into fresh air. Only a bit of one edge of the lobe is pushing against the lifter. Here's another nice pic of cam lobe wear patterns.
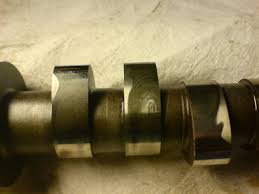
The shiny bits are where the cam lobe is touching the lifter. The base circle is shiny so we can tell this cam operated against a hydraulic lifter which stayed in contact with it all the time unlike a solid lifter cam which will have a tappet clearance. Then you get the distinctive half moon shiny bit up near the nose which matches where the cam lobe was touching in the first drawing. Most of the flank of the lobe never touches the lifter at all.
So what determines how far out this contact point moves? Clearly it can't move out beyond the edge of the lifter because then the lobe would miss the flat face of the lifter, dig into its edge and everything would break. I'll cover that in the next part. In the final part I'll look at the various parts of the cam lobe geometry, how they are specified and what effect each one has on engine performance.
Part 3.
Imagine a seesaw set absolutely horizontal and you're looking at it from the side. Now rotate the seesaw one degree clockwise. How far does any part of the beam move vertically? If the far end of one side moves 4 inches vertically then half way along the beam it will move 2 inches and a quarter of the way from the pivot only 1 inch. Imagine we want to position something contacting the beam so it moves a given distance for every 1 degree of beam rotation. The more we want the thing to move the further out we have to place it. This is how cam lobes work. They move the follower a certain distance per degree of cam rotation and the bigger we want this movement to be the further from the centreline the contact point moves out.
This movement of the follower per degree of cam rotation is called the cam velocity. It's measured in thou of follower lift per degree of cam rotation. The higher the value of this lift the further out the contact point becomes and the bigger the follower needs to be.
The equation that governs this is as follows.
From the cam centreline the Contact Point = lift per degree of cam rotation x 180/pi (57.3).
So if we want the cam to reach a maximum velocity of 10 thou per degree of rotation the cam follower must have a radius of at least 10 x 57.3 = 573 thou = 0.573" = 14.5 mm, or a diameter of 29 mm.
So the follower diameter places a direct limit on how fast the follower can open. This is independent of cam lobe size and purely a function of the opening rate.
If the follower diameter is small then the system needs a rocker to multiply the movement so the valve itself opens at a reasonable rate. This is how pushrod engines are designed. If the follower is large enough then all the valve movement can be created directly from the cam lobe i.e OHC engines.
In the next part I'll look at the four main areas of a cam lobe profile.
Imagine a seesaw set absolutely horizontal and you're looking at it from the side. Now rotate the seesaw one degree clockwise. How far does any part of the beam move vertically? If the far end of one side moves 4 inches vertically then half way along the beam it will move 2 inches and a quarter of the way from the pivot only 1 inch. Imagine we want to position something contacting the beam so it moves a given distance for every 1 degree of beam rotation. The more we want the thing to move the further out we have to place it. This is how cam lobes work. They move the follower a certain distance per degree of cam rotation and the bigger we want this movement to be the further from the centreline the contact point moves out.
This movement of the follower per degree of cam rotation is called the cam velocity. It's measured in thou of follower lift per degree of cam rotation. The higher the value of this lift the further out the contact point becomes and the bigger the follower needs to be.
The equation that governs this is as follows.
From the cam centreline the Contact Point = lift per degree of cam rotation x 180/pi (57.3).
So if we want the cam to reach a maximum velocity of 10 thou per degree of rotation the cam follower must have a radius of at least 10 x 57.3 = 573 thou = 0.573" = 14.5 mm, or a diameter of 29 mm.
So the follower diameter places a direct limit on how fast the follower can open. This is independent of cam lobe size and purely a function of the opening rate.
If the follower diameter is small then the system needs a rocker to multiply the movement so the valve itself opens at a reasonable rate. This is how pushrod engines are designed. If the follower is large enough then all the valve movement can be created directly from the cam lobe i.e OHC engines.
In the next part I'll look at the four main areas of a cam lobe profile.
ShiningWit said:
Why do you want to spoil this thread with a petty argument? I used it as an example of how people can get mixed up with nomenclature, if you want to argue then post up in the relevant thread where it was contested.
I'm afraid this is what trolls do. They try and create arguments and then sit back and take some sort of perverse pleasure in the ensuing mayhem.Stan Weiss said:
Dave
No Cornflakes for me and since I do not drink coffee anymore, I had some tea and it was 9 degrees out and the wind chill was -13. Not fit for man nor beast.
Stan
The oil in your truck will be like grease at that temperature. At least you can walk underneath it and change it to something thinner without ducking your head.No Cornflakes for me and since I do not drink coffee anymore, I had some tea and it was 9 degrees out and the wind chill was -13. Not fit for man nor beast.
Stan
Tea? We'll turn you into a civilised European yet

Stan Weiss said:
PS- have you as a civilized European got indoor running water on the farm?
We even have the option of hot from some taps. 
Mind you, it didn't quite pass the local authority water quality test when I bought the house (too much nitrate) and there were a couple of dead mice floating in the borehole last time I had the cover off, but it tastes ok. Especially if diluted with enough whisky.
ShiningWit said:
Is it possible you could do some basic nomenclature? As was noted on a recent thread we've got people incorrectly calling cam covers rocker covers and cam boxes, I think for the novice, lesser experienced and um, younger people reading this it's difficult to understand which part is which, especially as pushrods are very uncommon now. Finger followers or rockers?
A rocker acts between a pushrod and a valve tip with the pivot in the middle. The cam in that situation acts on the circular follower underneath the pushrod. A finger follower acts between a pivot point at one end, the valve stem at the other and the cam lobe bearing directly on the finger as in the Ford Pinto OHC engine. Some bike engines also use this design.ShiningWit said:
Hope you don't mind me posting these up (if I follow you correctly I don't think you've mentioned them), but they are OHC radiused buckets, Pic is of a BMW engine, although they are by no means new technology:
This is essentially the pad from a Ford Pinto type finger follower designed into a sliding bucket which is pinned so it can't rotate. The advantage is that the cam lobe always has its full width to operate against the follower on. As the posts above have shown, with a circular rotating follower the lobe is only touching the follower on a very small area at maximum velocity when the contact point is out at the edge and this is where the lobe generally starts to fail if contact pressures get too high.Here is an actual measurement plot of a solid lifter flat tappet cam from my database of cams I've measured over the years. I've shown just the opening side of the curve, the closing side is more or less symmetrical, and split the curve into 4 sections, A to D. 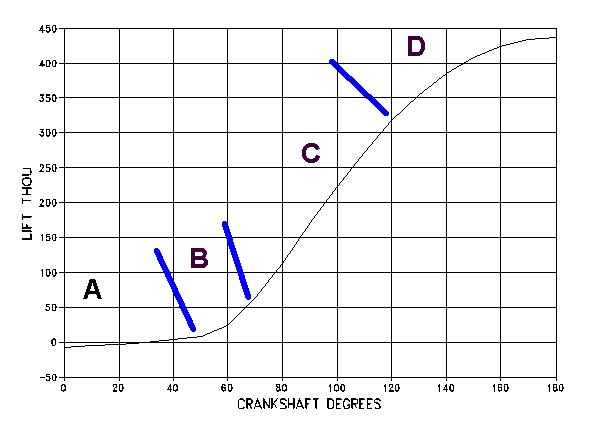
A - Opening (Clearance) Ramp
This is where the valve clearance is taken up. This has to be done very slowly so as not to smash the lobe into the cam follower. Normal opening rates are about 1 thou of lift for every 3 crankshaft degrees. To allow for wear and poor maintenance the ramp has to extend for a few thou above whatever the specified valve clearance is and this poses some problems for engine performance. Because the ramp is so slow any surplus over and above the specified valve clearance can use up a lot of valuable crankshaft degrees of duration which could be better used for opening the valve fast and reaching a higher lift. I've drawn the zero line on the Y axis at the specified 8 thou clearance but you can see the ramp extends beyond this for nearly another 20 degrees of crank rotation.
Hydraulic lifter cams don't need this long slow clearance ramp as the follower is always in contact with the lobe.
B - Acceleration Phase
Once the lobe and follower are in contact the lift can start accelerating fast. The forces produced are very high though and are limited by the materials of the lobe and lifter and the strength of the oil film between them. There's a certain amount of wiggle room for the cam designer in terms of acceleration rate versus wear and cam life but this part of the profile doesn't take up many crankshaft degrees anyway and is best not pushed too far.
C - Constant Velocity Phase
The lift rate has now reached the limit dictated by the follower diameter and nothing can be done to increase this.
D - Deceleration Phase
The rate at which the lobe velocity can slow back to zero is limited by the valve spring force which is all that is now keeping the valve and lifter against the lobe. This phase can be shortened if the valve spring rate is increased but that has adverse effects on wear and parasitic bhp losses.
In the final part I'll look at how these four phases of the cam profile can be varied for race cams versus stock road ones.
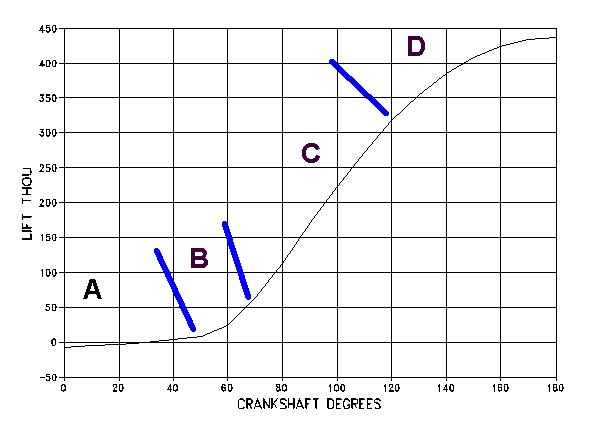
A - Opening (Clearance) Ramp
This is where the valve clearance is taken up. This has to be done very slowly so as not to smash the lobe into the cam follower. Normal opening rates are about 1 thou of lift for every 3 crankshaft degrees. To allow for wear and poor maintenance the ramp has to extend for a few thou above whatever the specified valve clearance is and this poses some problems for engine performance. Because the ramp is so slow any surplus over and above the specified valve clearance can use up a lot of valuable crankshaft degrees of duration which could be better used for opening the valve fast and reaching a higher lift. I've drawn the zero line on the Y axis at the specified 8 thou clearance but you can see the ramp extends beyond this for nearly another 20 degrees of crank rotation.
Hydraulic lifter cams don't need this long slow clearance ramp as the follower is always in contact with the lobe.
B - Acceleration Phase
Once the lobe and follower are in contact the lift can start accelerating fast. The forces produced are very high though and are limited by the materials of the lobe and lifter and the strength of the oil film between them. There's a certain amount of wiggle room for the cam designer in terms of acceleration rate versus wear and cam life but this part of the profile doesn't take up many crankshaft degrees anyway and is best not pushed too far.
C - Constant Velocity Phase
The lift rate has now reached the limit dictated by the follower diameter and nothing can be done to increase this.
D - Deceleration Phase
The rate at which the lobe velocity can slow back to zero is limited by the valve spring force which is all that is now keeping the valve and lifter against the lobe. This phase can be shortened if the valve spring rate is increased but that has adverse effects on wear and parasitic bhp losses.
In the final part I'll look at how these four phases of the cam profile can be varied for race cams versus stock road ones.
Stan Weiss said:
Dave,
Sorry for the confusion. I do not have an cam data from the Suzuki. That data is from a SBF v8.
Do you have an cam data files that you would like to share?
Stan
What sort of stuff are you interested in? I've got std and various performance profiles for Ford CVH, Peugeot 205, most of the Crane Rover V8 profiles (270, 224,234,248,256,266), MGB race cam and a bunch of oddball stuff including 5 valve per cylinder Audi V6 and the Kohler lawnmower engine I helped my apprentice turn into a kart race engine for his degree thesis.Sorry for the confusion. I do not have an cam data from the Suzuki. That data is from a SBF v8.
Do you have an cam data files that you would like to share?
Stan
The Ford Pinto flow figures on your site have some problems. You've got two lines from me marked as "accuracy ???" which I don't recognise. Those need taking out. The other two (stock carb head and stock injection head) look ok and the valve size is 42mm.
The valve size on the CNC ported Pinto heads can't be 1.179" Maybe 1.79".
Here's one of my ported Pinto heads already converted to 28" for you. Inlet valve size 45.6mm
100 - 60
200 - 117
300 - 154
400 - 181
500 - 200
I don't really want any of my cam data on the site. The profiles are someone's intellectual property anyway and probably best not shared.
The valve size on the CNC ported Pinto heads can't be 1.179" Maybe 1.79".
Here's one of my ported Pinto heads already converted to 28" for you. Inlet valve size 45.6mm
100 - 60
200 - 117
300 - 154
400 - 181
500 - 200
I don't really want any of my cam data on the site. The profiles are someone's intellectual property anyway and probably best not shared.
rev-erend said:
Any chance of posting up the Rover V8 crane 256.
I'll give you the headline numbers.INLET
Duration at 50 thou lobe lift - 256
Lobe lift - 0.337" (8.56mm)
Notional duration at 4 thou valve lift - 308 degrees
EXHAUST
Duration at 50 thou lobe lift - 266
Lobe lift - 0.350" (8.89mm)
Notional duration at 4 thou valve lift - 320 degrees
Gassing Station | Engines & Drivetrain | Top of Page | What's New | My Stuff