Nova Race Transmissions: PH2 Meets
All the gears and lots of ideas....
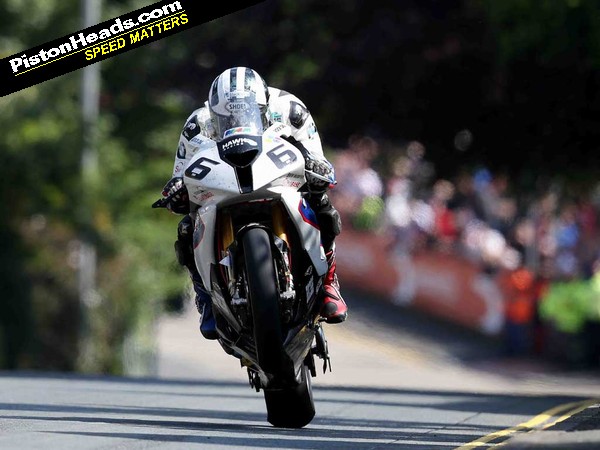
All geared up
When you walk into Nova's workshops the first thing that strikes you is the fact it sounds and feels like a proper engineering company. On the wall is a huge sign saying 'racing is life, anything before or after is just engineering' and you are surrounded by a weird mix of old machines that manually force metal into submission via big cogs and cutting edge CNC lathes that rely on computers to tell them what to do.
The whole workshop smells pleasingly of oil and heat while every free surface is covered in gears in various stages of construction. There are racks of metal bars that will soon be cut into shape and printouts that show the precise dimensions of the gears being built. Speaking to some of the workers I discover the gear cutting machines Nova still use every day were built in the 1960s, but apparently they have yet to be bettered and it's the precision of the cutting head that determines the gear's performance. But aren't all gears the same? Apparently not and I'm given a run down on exactly what it takes to built a gearbox that can withstand the harshest of race abuse.
It's what's inside that counts
Before Nova cut any metal the gears are designed on a CAD program that can run computer simulations to ensure the dimensions are correct. Once happy, Nova then builds a prototype gear that they slot into a mock-up gearbox to test it works in reality and not just on a computer screen. Then, if all is good, it's time to start building the gearbox.
According to Nova, the key to ensuring a gearbox can withstand a load of abuse is the metal the gears are constructed from. Interestingly this doesn't mean using the hardest metal possible as that will shatter when it fails, potentially taking the whole engine with it, so instead Nova use an M121 F1-standard steel supplies by Austrian firm Bohler. This steel pits when it wears, giving a warning that the gear needs changing rather than it suddenly failing with catastrophic results. This steel is supplied in blank discs as despite the fact Nova have some rods of it for prototype work, the billet steel is so tough that if they cut their own discs using their band saw for every gear it would take them ages and cost a fortune in blades!
The discs are put into a lathe that turns features such as the indents, edges and lips into the metal and produces a smooth round gear with no teeth. This blank is then milled to add pockets and engagement dogs if necessary and then has its teeth cut into it by the gear shaping machine at the rate of a tooth every minute - so about twenty minutes per complete gear. The cutter, or hobber, has rows of sharp cutting teeth that gradually nibble away at the disc to form the gear's teeth. Then, in a particularly violent act, a broacher pulls a vicious looking tool through the centre of the gear to cut in a spline before a four-axis mini mill cleans up the gear if necessary. Then, to harden the metal, every gear is heated to 800 degrees before being quenched in nitrogen or oil to give it a hard case before being tempered in an over at 300 degrees to relax its core to increase its strength further. A bit more machining to ensure there is no distortion due to the heat treatment and a quick blast in a super-finishing machine and you have a lovely new gear. Only another eleven plus a few shafts and a gear selector drum to go...
Gassing Station | Biker Banter | Top of Page | What's New | My Stuff