Manifold fitting - an alternative to slotting
Discussion
I'm considering alternatives to slotting the bottom bolt holes because I'm fitting ARP's with nordlocks and I'm worried that the smaller shoulder area of the ARP's will reduce clamping force if I cut the slots
I'm looking for thoughts from those who have struggled with this job. I can see the potential for this to go wrong by a bolt slipping off during fitting but it still looks good to me
Any thoughts?
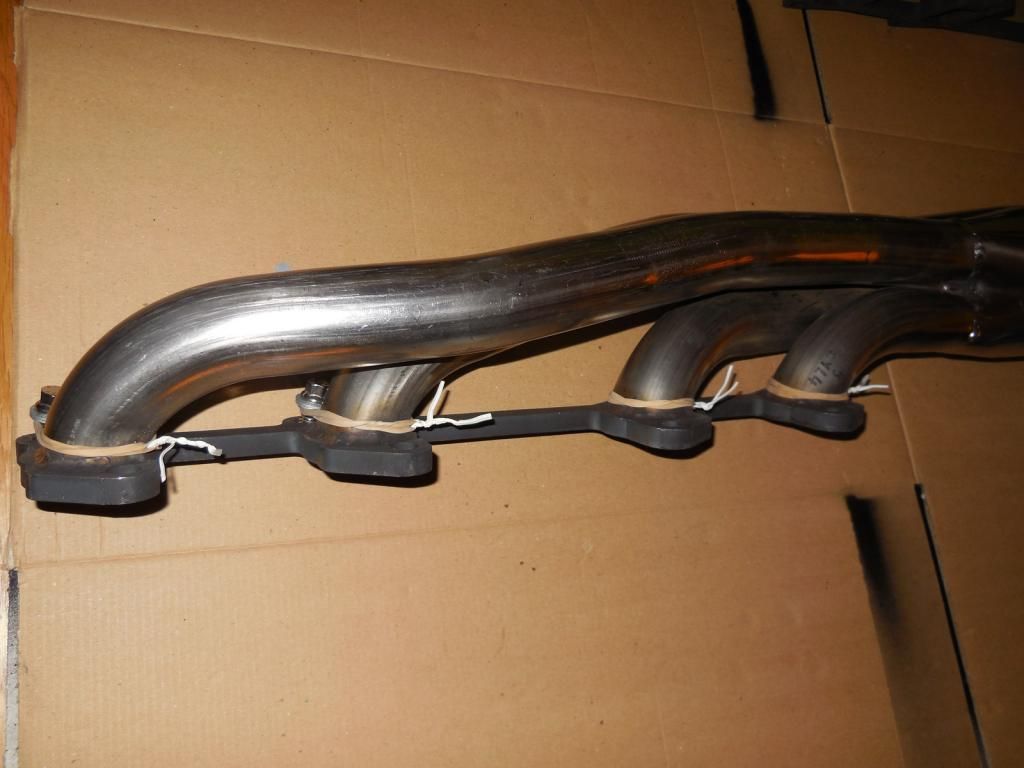
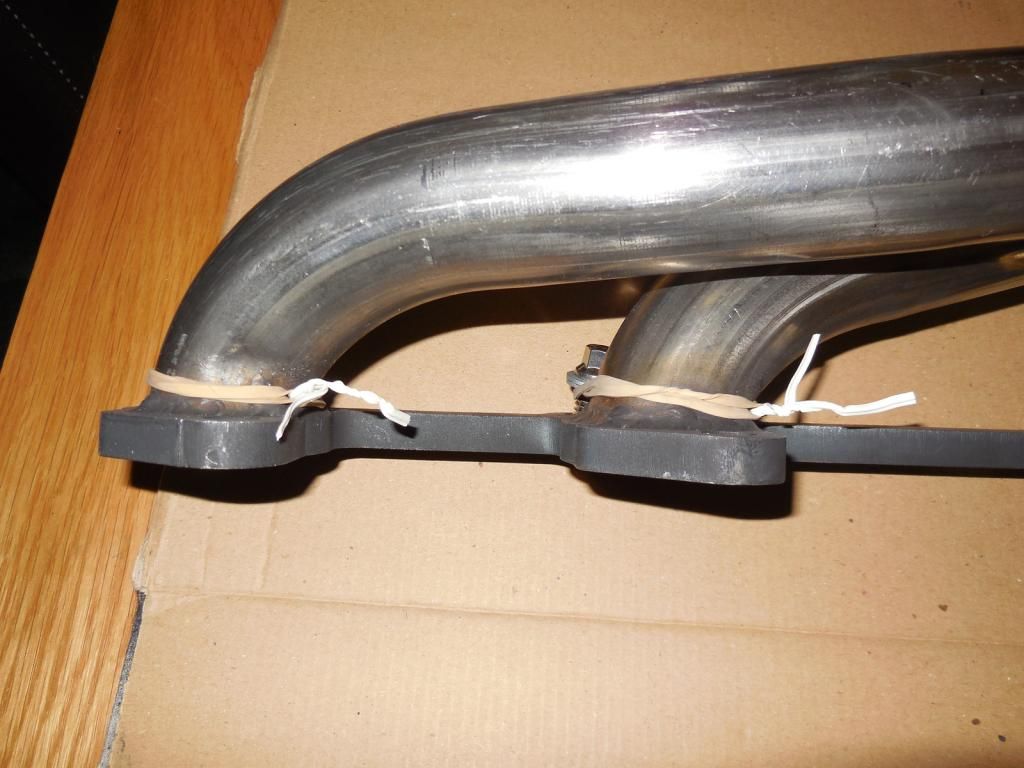
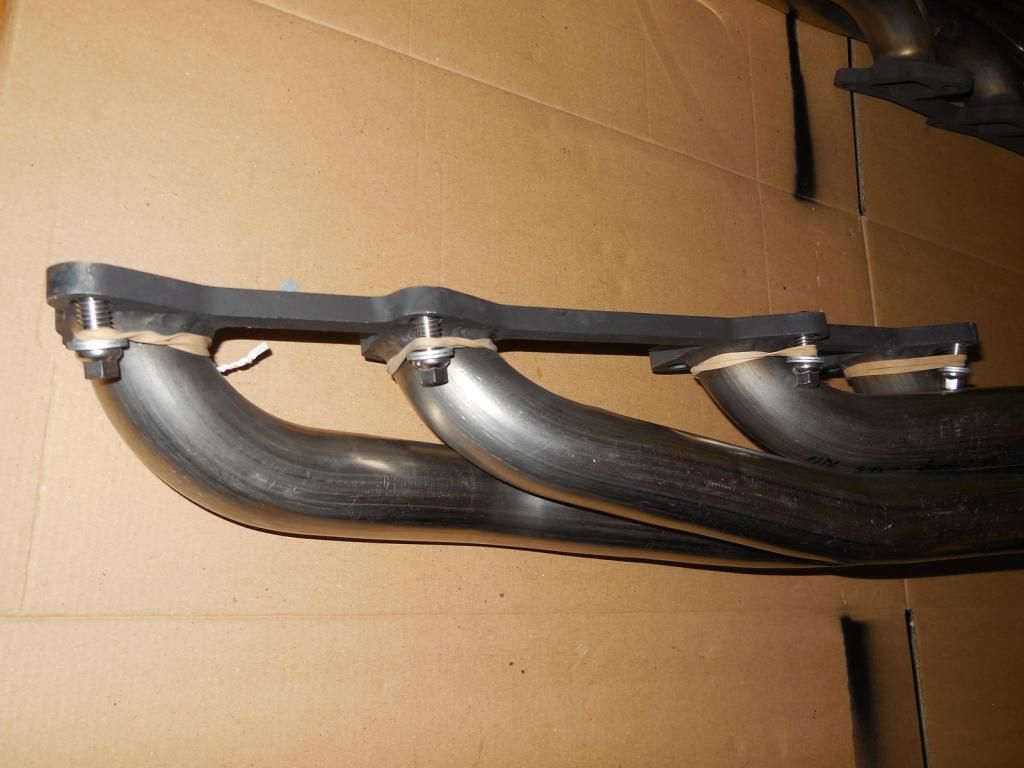
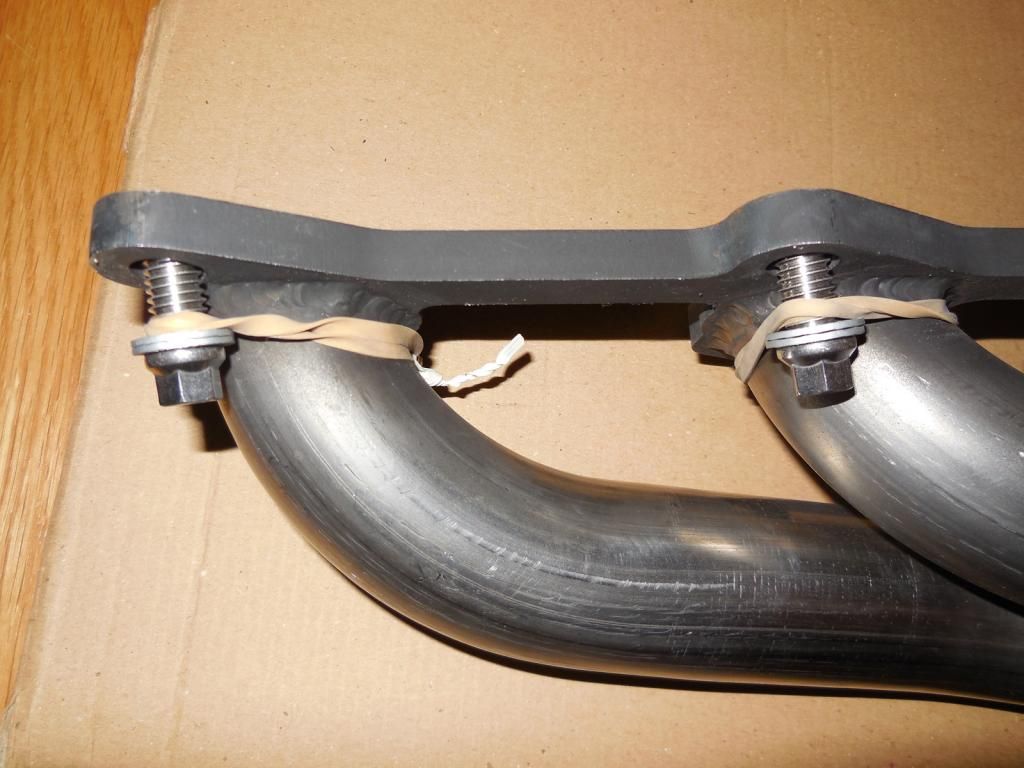
I'm looking for thoughts from those who have struggled with this job. I can see the potential for this to go wrong by a bolt slipping off during fitting but it still looks good to me
Any thoughts?
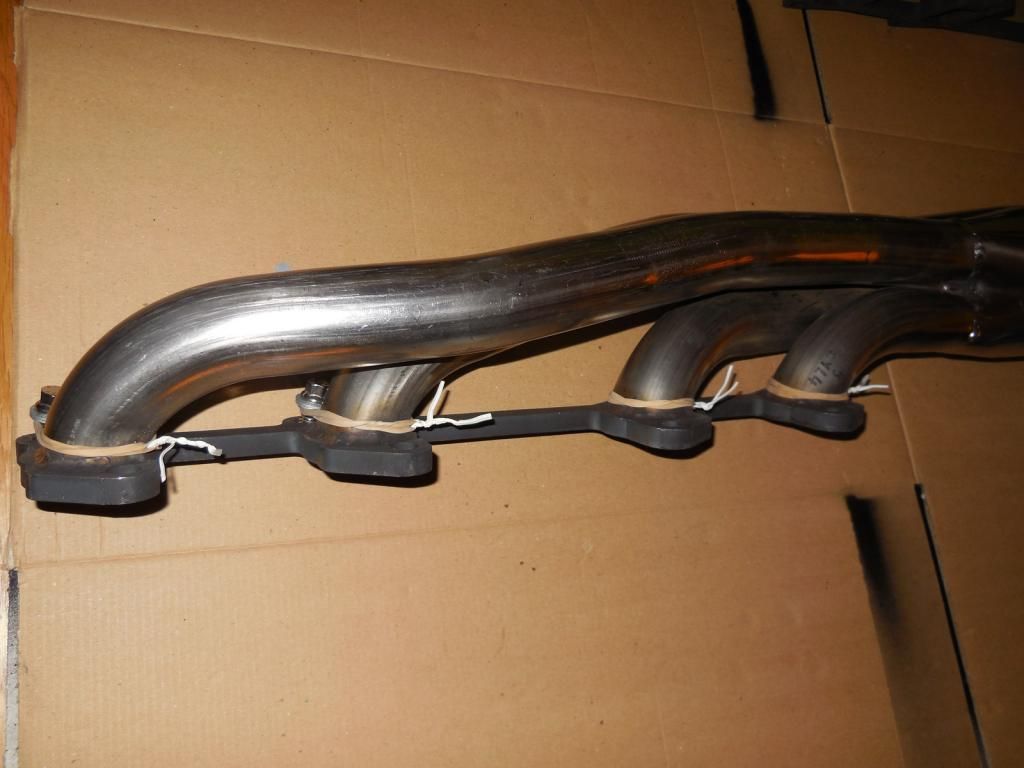
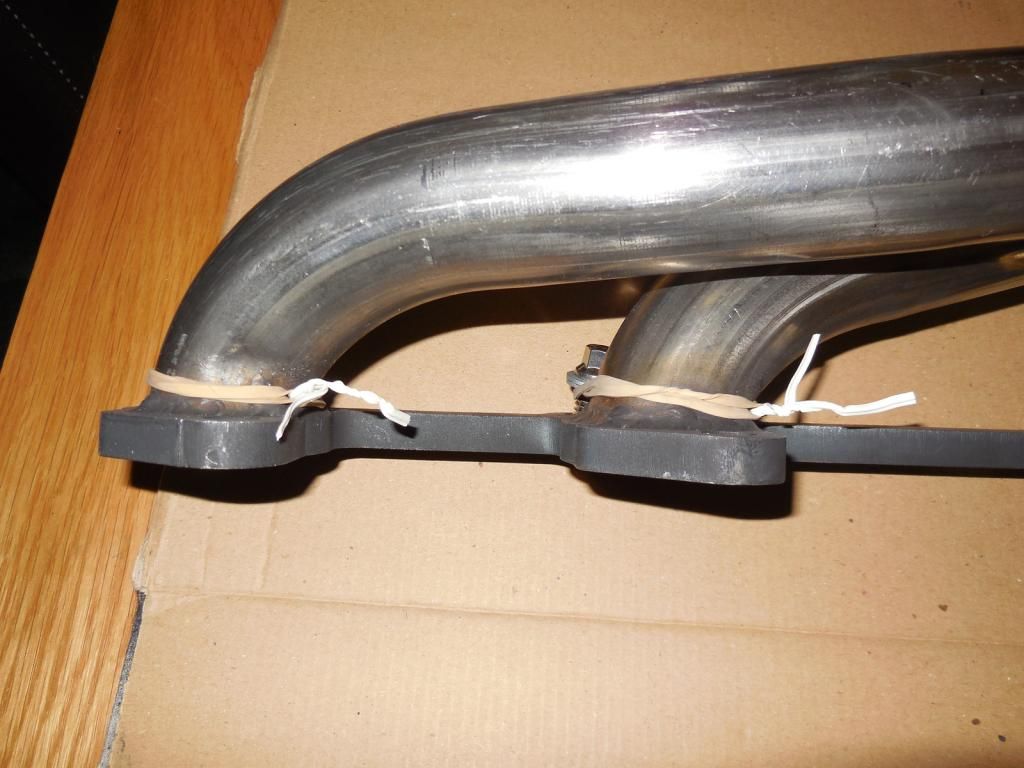
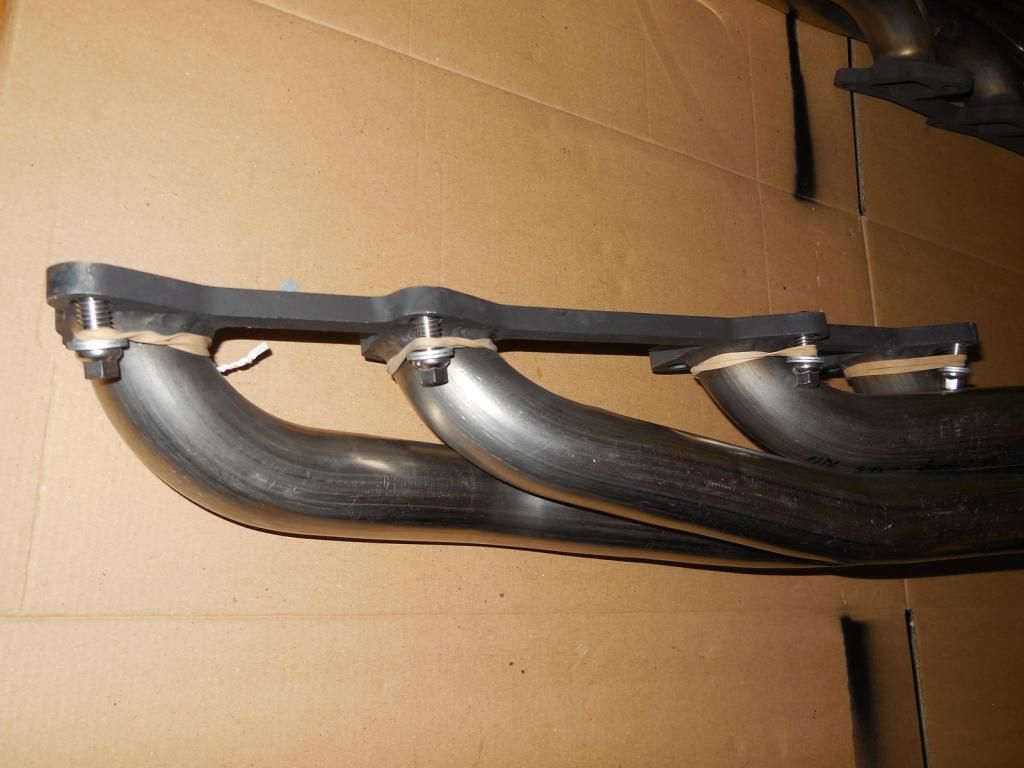
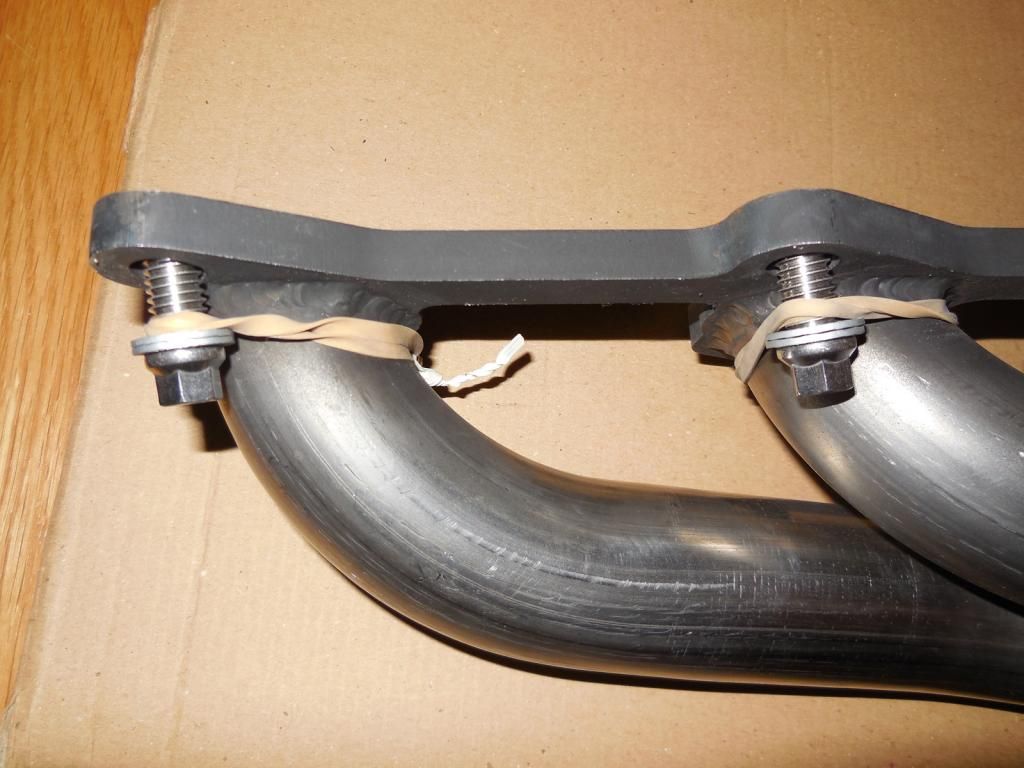
They look good. In hindsight I would have looked further rather than just buying what appeared to be popular and I think ACT selling the ARP/norlock combo gives a degree of undeserved credibility.
The ARP flange is too small and as you say the polished surface works counter to the nordlock process. I'm always wary of over tightening into an alloy block. I have had to run a tap down several of my bolt holes to enable the new ARP's to find a start, that also runs the risk of oversizing or otherwise weakening the female tread.
Perhaps the only true benefit on ARP's is the small AF size and corrosion resistance
The ARP flange is too small and as you say the polished surface works counter to the nordlock process. I'm always wary of over tightening into an alloy block. I have had to run a tap down several of my bolt holes to enable the new ARP's to find a start, that also runs the risk of oversizing or otherwise weakening the female tread.
Perhaps the only true benefit on ARP's is the small AF size and corrosion resistance
I can insert 2mm +/- 0.3mm on all but two. Those two are both 5mm. This measured at the point that the bolt can no longer be withdrawn
I therefore generally have 9mm with two at 6mm of engaged thread. Not much considering the weakness of alloy threads and the bolting force needed to create a flat gasket seal
I therefore generally have 9mm with two at 6mm of engaged thread. Not much considering the weakness of alloy threads and the bolting force needed to create a flat gasket seal
I still have my original mild steel bolts and can see from the point that corrosion stops that they didn't have much engaged thread either. If you consider the force that can be applied to a standard nut and bolt fastening and consider the length of engaged thread in the nut then we're 2 to 3 times more than that.
Gassing Station | Chimaera | Top of Page | What's New | My Stuff