New machine not doing what it is ment to.
Discussion
Mods...Sorry, no idea where to put this so please move if needed.
Amongst other things I own a company that refurbishes alloy wheels, and have just spent rather a lot of money on a CNC wheel lathe, kind of like the one below.
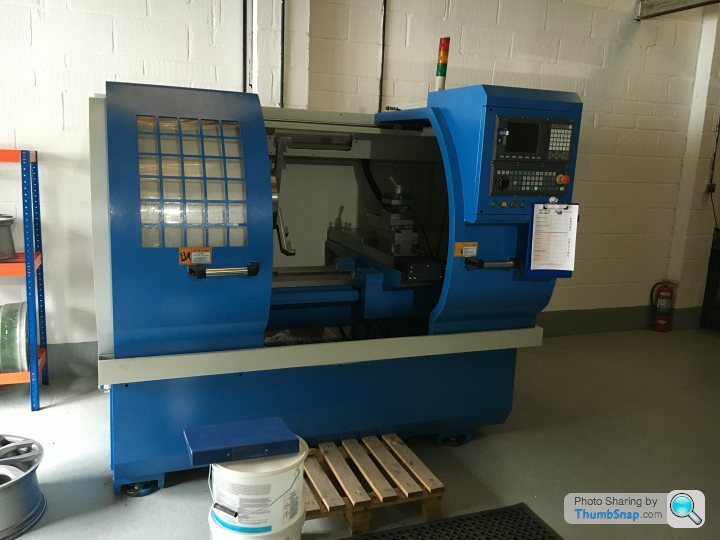
2 of my lads went on a training course, one passing with merit, the other with distinction, we also took 10+ alloys with us on training and they were done on an identical machine,musing the same cutting tip. They looked stunning.
On returning to our own machine things were looking good, we loaded in our first alloy and probed,plotted and optimised it no problem at all, then we cut it, ie machined the front face, removing the damage. And here lies the problem.
We just cannot get a good finish, we are getting marks on the face of the alloy wheel, see below.
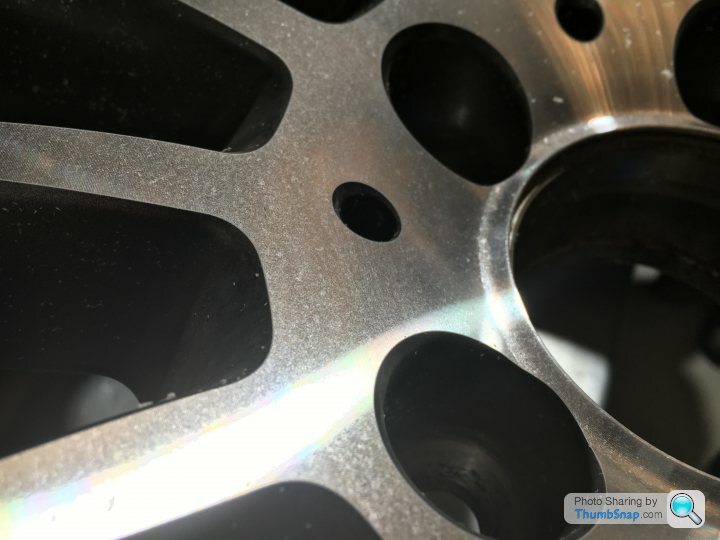
We are now 3 weeks in, having done approx 50-60 wheels, trying different speeds, cut depths, turret speed, yet still get this finish every time.
The company who supplied the machine and training are supposed to provide a yr back up service, yet are not interested, they say it's the tip, we have tried 3 in total, it's the tip they recommend, a tungsten diamond carbide insert tip. They say it's the type of alloy we are cutting, yes, some makes, BMW in particular are hard to get a good finish, but we have cut a mixture of BMW, Audi, Range Rover, Mercedes to name a few. All with the same result.
We have noticed the turret , which you turn by hand, when locked in place is not quite straight, we have told them this but they won't have it, say it's normal. We kind of think the tip, which is a 1.3 radius is not cutting central, so not clearing the swarf, could this be "catching" and causing the finish.
So, I ask the PH massive, anybody have experience of using a CNC and in particular on alloy wheels. We really are running out of ideas, and indeed wheels to practice on, I've a nice new machine yet for the moment are still sending this type of alloy away.
Welcome any thoughts, thank you.
Amongst other things I own a company that refurbishes alloy wheels, and have just spent rather a lot of money on a CNC wheel lathe, kind of like the one below.
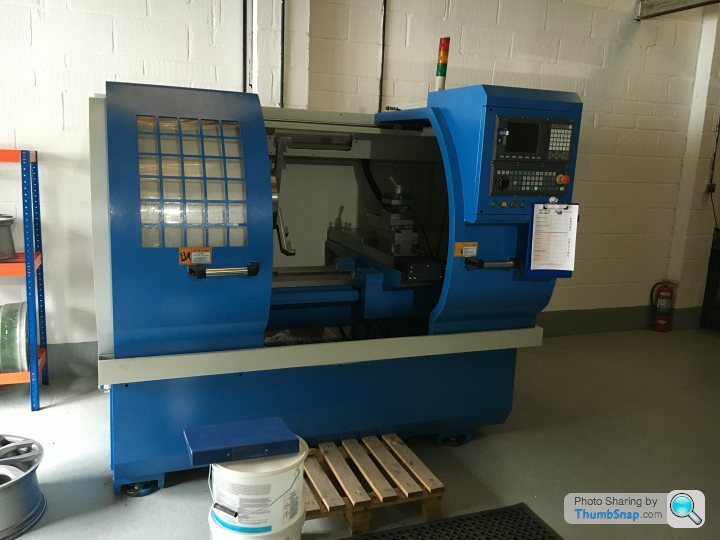
2 of my lads went on a training course, one passing with merit, the other with distinction, we also took 10+ alloys with us on training and they were done on an identical machine,musing the same cutting tip. They looked stunning.
On returning to our own machine things were looking good, we loaded in our first alloy and probed,plotted and optimised it no problem at all, then we cut it, ie machined the front face, removing the damage. And here lies the problem.
We just cannot get a good finish, we are getting marks on the face of the alloy wheel, see below.
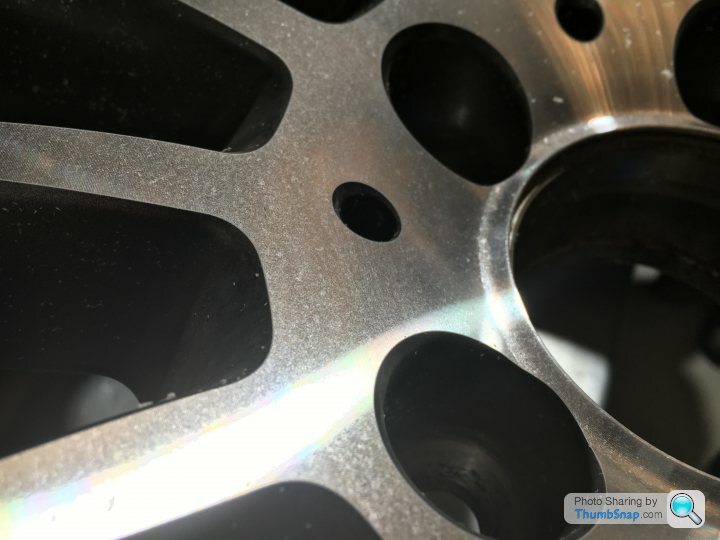
We are now 3 weeks in, having done approx 50-60 wheels, trying different speeds, cut depths, turret speed, yet still get this finish every time.
The company who supplied the machine and training are supposed to provide a yr back up service, yet are not interested, they say it's the tip, we have tried 3 in total, it's the tip they recommend, a tungsten diamond carbide insert tip. They say it's the type of alloy we are cutting, yes, some makes, BMW in particular are hard to get a good finish, but we have cut a mixture of BMW, Audi, Range Rover, Mercedes to name a few. All with the same result.
We have noticed the turret , which you turn by hand, when locked in place is not quite straight, we have told them this but they won't have it, say it's normal. We kind of think the tip, which is a 1.3 radius is not cutting central, so not clearing the swarf, could this be "catching" and causing the finish.
So, I ask the PH massive, anybody have experience of using a CNC and in particular on alloy wheels. We really are running out of ideas, and indeed wheels to practice on, I've a nice new machine yet for the moment are still sending this type of alloy away.
Welcome any thoughts, thank you.
dudleybloke said:
Have you clocked up the toolpost to see how far out of square it is?
And I'm not keen on your chucking arrangement, if I were turning something of a large diameter I would like a bigger chuck with jaws that don't stick out that far. But that's me being fussy.
Is the tip you're using a wiper tip? Another issue could be coolant.
Tool post is approx 6" sq, and is out by approx 4 mm on one endAnd I'm not keen on your chucking arrangement, if I were turning something of a large diameter I would like a bigger chuck with jaws that don't stick out that far. But that's me being fussy.
Is the tip you're using a wiper tip? Another issue could be coolant.
Edited by dudleybloke on Monday 30th May 16:31
Chuck/jaws are what came with the machine, and the same as the machine we were trained on.
Sorry, no idea if the tip is a "wiper tip", this is the tip in question, with a 1.2 radius
http://www.cutwel.co.uk/lathe-tools/iso-turning-in...
Ref coolant, don't use any, never been shown or told to, cut the wheel dry.
Thanks for the pointers so far folks.
mr.man said:
Describe in greater detail the imperfections on the machined finish. I can't really see the marks only that it's clearly not a diamond turned finish. Without seeing your set up myself it's difficult to help.
Basic facts. This machine using the same purpose made jaws, the same toolpost, the same grade and style of tool is capable of producing the required finish.
Basic things to check. Is there a tiny nick on the nose of the tool?.Are you clamping the tool with minimum overhang? Are you spinning it fast enough?. These tips are good for 3000m/min. What feed rate and depth of cut was recommended?
Looks like fine spray water marks.Basic facts. This machine using the same purpose made jaws, the same toolpost, the same grade and style of tool is capable of producing the required finish.
Basic things to check. Is there a tiny nick on the nose of the tool?.Are you clamping the tool with minimum overhang? Are you spinning it fast enough?. These tips are good for 3000m/min. What feed rate and depth of cut was recommended?
They say the tips are good for 250 wheels approx, we have tried 3 tips now with no visible damage on any.
Tool was clamped same distance as the one they were trained, though I think the lads have since moved it in up to 20mm to see if any change, there is a limit on how much it can be moved.
Training says RPM of 500, 0.1-0.2 cut depth and 0.1-0.2 feed speed across the wheel. we have tried 500,550,600,700 and 750 RPM with no luck, they say no more than 800 RPM. And tried just about every increment from 0.50-0.2 with still the same poor result.
I'm still leaning towards it being something to do with the tool post not locking straight, maybe the picture below may help in showing how far it's out.
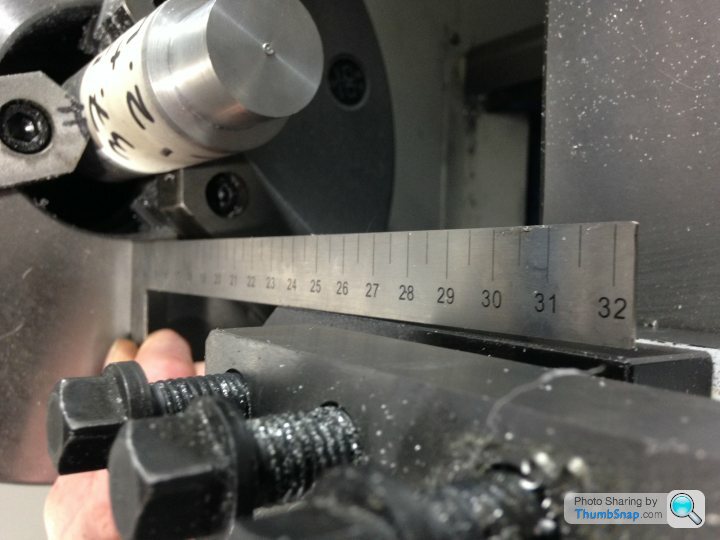
LDN said:
Surely; if they're not proving support and they said they would / it's included then you issue them a final demand for support or else you will take them to court...
The fact you've had to come onto a forum to ask the question means they've really left you up the creek with no paddle. It's not fair and I'm sure you'd win your case if it ever got that far.
It's heading down this route very very quickly, so far I've had 2 lads not machine a "paid" wheel in over 3 weeks, didn't expect to be doing 20 wheels a day from day one but it's becoming very frustrating.The fact you've had to come onto a forum to ask the question means they've really left you up the creek with no paddle. It's not fair and I'm sure you'd win your case if it ever got that far.
I know the machine can do a good job, I saw one in action last Nov when I went to take a look, plus of course my lads took wheels up to training.
Simpo Two said:
How about challenging them to come over, with a wheel of their choice, and show you how it works? Either you'll find the problem, or they'll be forced to admit it's dud. If they don't take up the challenge, wonder why. It will look good later...
Simpo, they are doing just this today, due at 11am, it's only taken them 3 weeks of asking, I posted on here to hopefully get a few more pointers, to throw at them, which I have, thanks for help so far folks. Guys, THANK YOU so much for all your help, the company sent down their trainer today, but it's a 4-5 hrs trip on a good run, due to the moody weather we had here in the south east today he was late arriving, so back tomorrow to finish off.
He did give the machine a once over and said things like the offsets, centres, tooling and such had all been set up correctly by my lads.
Will keep you all informed. Thanks again.
He did give the machine a once over and said things like the offsets, centres, tooling and such had all been set up correctly by my lads.
Will keep you all informed. Thanks again.
Whooh whooh whooh, calm down folks, I'm here, did try and post a reply on Weds night but PH appeared to be broken.
Ok, so Tuesday he was late arriving, but once here he checked that my lads had set the machine, probe and tip up correctly, which they had, all the offsets were good, he checked that they were optimising the data ok, no problems there.
He then plotted and cut 2 alloy wheels, and at last agreed that something was not right.
Back Weds am to continue looking, he just kept going over and over the same things, he upped the speeds, slowed the speeds, changed the tips, still no improvement at all.
He then made some phone calls to another company which has 4 lathes, 2 of which are the same as ours, and all of them use the same diamond carbide tips.
They said the tips need "bedding" in from new, up to 50 cuts, they said when they change a tip they put a scrap alloy in and do a min of 50 0.2 cuts, this dresses the tip to provide a good finish.
So, a scrap wheel was found, and 50+ cuts were made, I knew it probably was not this, but keen to try just about anything, I'll let you guys guess the rest.
The trainer, and I use that term loosely was kicked halfway back to Yorkshire, with instructions that its sorted with 7 days or the s
te really will hit the fan.
There is a massive trade show at the NEC next week, 3 day event, and I know these guys have a big trade stand there, if any body is going then come say hi, I will be the one standing right by their stand, wearing a t-shirt with "Don't buy this lathe, its not fit for purpose" printed all over it.
Maybe that will get results, or me thrown out by security.
Sorry not better news folks, we will either get to the bottom of it or the machine will be returned pronto.
Ok, so Tuesday he was late arriving, but once here he checked that my lads had set the machine, probe and tip up correctly, which they had, all the offsets were good, he checked that they were optimising the data ok, no problems there.
He then plotted and cut 2 alloy wheels, and at last agreed that something was not right.
Back Weds am to continue looking, he just kept going over and over the same things, he upped the speeds, slowed the speeds, changed the tips, still no improvement at all.
He then made some phone calls to another company which has 4 lathes, 2 of which are the same as ours, and all of them use the same diamond carbide tips.
They said the tips need "bedding" in from new, up to 50 cuts, they said when they change a tip they put a scrap alloy in and do a min of 50 0.2 cuts, this dresses the tip to provide a good finish.
So, a scrap wheel was found, and 50+ cuts were made, I knew it probably was not this, but keen to try just about anything, I'll let you guys guess the rest.
The trainer, and I use that term loosely was kicked halfway back to Yorkshire, with instructions that its sorted with 7 days or the s

There is a massive trade show at the NEC next week, 3 day event, and I know these guys have a big trade stand there, if any body is going then come say hi, I will be the one standing right by their stand, wearing a t-shirt with "Don't buy this lathe, its not fit for purpose" printed all over it.
Maybe that will get results, or me thrown out by security.
Sorry not better news folks, we will either get to the bottom of it or the machine will be returned pronto.
Heard a story today about a guy who had a wheel lathe, not sure of make, but he was producing outstanding work, except on a Thursday, and only a Thursday.
They spent almost 3 months trying to work out what was wrong, including setting up webcams so the company who built the lathe in the USA could watch him , still no luck.
It was then discovered that the next unit along from him was a printers, and their biggest machine was just the other side of the wall, I'll let you guess what day of the week they fired it up.
The concrete floors were so thin that the printing press was shaking the lathe, they lifted the lathe and sat it on 10mm rubber washers, problem solved.
Now, we don't have a printers next door, so I know it's not that, lol, but just goes to show how sensitive these machines can be, and as another previous poster said, you sometimes really need to think outside the box.
They spent almost 3 months trying to work out what was wrong, including setting up webcams so the company who built the lathe in the USA could watch him , still no luck.
It was then discovered that the next unit along from him was a printers, and their biggest machine was just the other side of the wall, I'll let you guess what day of the week they fired it up.
The concrete floors were so thin that the printing press was shaking the lathe, they lifted the lathe and sat it on 10mm rubber washers, problem solved.
Now, we don't have a printers next door, so I know it's not that, lol, but just goes to show how sensitive these machines can be, and as another previous poster said, you sometimes really need to think outside the box.
dudleybloke said:
Any joy?
Have another make of tip on the way. We did notice the tool holder wasn't level, levelled it up but made no difference.Got a company coming in to re-level the machine and check it's not twisted.
Have also managed to get in touch with the company who produce the lathe in China, sent him some program files and data and awaiting his reply.
Found a company in North London who have the same machine, awaiting a call to see if we can go and take a look at theirs in action.
Trade show in Birmingham today, I made myself quite vocal on the suppliers stand, I'm sure it didn't do any good at all but it made me feel better.
eliot said:
hornetrider said:
Oh yeah, it was this guy.
http://www.pistonheads.com/gassing/topic.asp?h=0&a...
Presume he bought from Yorkshire in the end, given he has guys from the supplier coming down to test it.
Indeed.http://www.pistonheads.com/gassing/topic.asp?h=0&a...
Presume he bought from Yorkshire in the end, given he has guys from the supplier coming down to test it.
Otherwise imagine trying to get the same support from china.
When in fact China could have just turned round and said " sorry, we didn't sell you the machine, Yorkshire did, go and ask them for help".
New cutting tips arriving tomorrow so going to give them a go, see where that gets us.
JKRolling said:
Sorry for trying to offer helpful advice and yes my username is a play on words between JK of jamiriqui and the author. The former being a car nut.
That has certainly taught me a lesson in not having an opinion to voice on here in future
I welcomed your advice pal, I did drop you an email via PH yesterday, did you get it. I was after some advice on tips, though since then we have tried some really cheap tips and got pretty much the same result as with the all singing, all dancing diamond carbide thingy ma jigs. So I don't think it's a problem with the tips.That has certainly taught me a lesson in not having an opinion to voice on here in future
D - day tomorrow, the Chinese are a coming.
Company in Yorkshire have had 3 guys over from the company who produce the machine in China, they have taken a look at the pictures I've been sending up and agree something is not right, so they are heading down tomorrow, with a translator in tow.
I sense an end in sight.
Company in Yorkshire have had 3 guys over from the company who produce the machine in China, they have taken a look at the pictures I've been sending up and agree something is not right, so they are heading down tomorrow, with a translator in tow.
I sense an end in sight.
garyhun said:
So what was the outcome of the visit from the Chineses OP?
Well, its taken 2 days of head scratching, but I think we are there, cut 7 wheels this morning and every single one looks fantastic.Appeared to be a mixture of two things, the "thing that auto tightens the drive belts" wasn't doing what it should have been, so the wheel, when being cut, wasn't turning at a regular speed.
Also the "software" was a bit messed up, they reloaded it, we had a good clear out of all the files we had stored on the machine, this was causing it to cut uneven.
There may have been other things wrong, the guys from China took every access panel off, just about every wire and switch off and lots lots more, it was hard to keep track of what they were doing as everything was done through the translator.
It does, for now appear to be doing what it is designed and built to do, so I am for now a happy wheel repairer.
As always huge thanks to the PH massive, for all your help, ideas and pointers. Yet again this place has come good.
honestbob said:
Glad it's now doing it's job properly. What speed, feed and depth of cut is now being used compared to what you were using? Any changes to the tooling and any other mechanical changes ?
Nope, no changes at all, same tip, holder and turret.Cutting between 500-600 rpm, between 0.1-0.2 depth, and feed speed dependant on what finish we want.
My 2 lads are like a dog with 2 cocks today, it was really getting them down, thinking they were not doing it right.
carlpea said:
I imagine a lot of programming goes into refurbishing those wheels since they aren't flat?
No more than most other alloys to be honest, approx 20 mins to plot/probe and optimise a wheel, then about 15 mins to cut it. Once we have built up a database of wheels I'm looking at 4-5 alloys per hr.
Gassing Station | Business | Top of Page | What's New | My Stuff