Had my E46 M3 subframe strengthened! Yay!
Discussion
Further to all the threads on the dreaded subframe mounting panel cracks, like many I started to panic and inspected mine asap. Being a 1 previous owner (lady) with just 27 k miles I was pretty hopeful that all would be OK.
Luckily I have access to a car ramp, so a good inspection was easy enough. It was easy to inspect the rear mounts but to get a good look at the fronts was impossible as all you get is a peek at a couple of sections.
My car is a 2002 car that will be 10 years old in May; so I wanted to stop it cracking and so started surfing the net. It appeared that the way forward was to use the epoxy injection method from BMW to reinforce the rear left panel section to resist flex of the chassis and therefore stop any cracks. Apparently when/if BMW do a goodwill repair on the pre 10 year old cars they inject the resin as a preventative measure! I found that the following were needed:
Cavity foam to block off certain parts of the cavity inside the subframe panel
A 2 part foaming Epoxy resin (2off double cartridges)
Applicator gun for said Epoxy
A few drills, grommets and bits n’ pieces.
To reinforce just one side of the rear panel, the materials alone from BMW were around £220ish and the gun could be bought elsewhere for around £80 (BMW wanted £280 for the applicator gun but don’t sell it to the public as its a ‘special tool’) Although its primarily the rear left section that goes, I wanted both sides doing. So I was getting into £500 to do it myself. Plus it has to be done under controlled temperature conditions and must never dip below 5deg when curing or the resin won’t set correctly apparently - given that our climate is as predictable as the numbers for Euro Millions I felt it best to let a specialist do it for me! Plus I wanted proof of it being done properly for when I come to sell it.
I was pointed in to the direction of ‘MProve Solutions’ www.mprovesolutions.com via a BMWCC member. Long story short, I made contact and booked in at a price of £295 all in. They use the genuine BMW materials just the same and could lend me a car to use as it takes 24hrs to cure!
After a thorough inspection they confirmed there was indeed no cracks. To check, they loosened the rear mount bolts and lowered the frame by about 15mm and used a fancy camera on a long probe to get a picture of under the mount without taking off the frame! They also stuck the camera through an inspection hole in the boot to inspect the top of the mount from the inside! They also used the camera on the fronts also.
They mentioned another, more expensive option and that was to have some pre fabricated 2mm steel steel templates affixed to the chassis on the underside and have the resin reinforcement done also, but explained that was more usually for the preserve of cars that require cracks welding beforehand, then plating afterwards. A car that was maybe planning some serious power upgrades or heavy track use would also benefit. It was a good preventative measure but I decided to just stick with the cheaper option as I’m just a ‘regular’ driver. Bye Bye
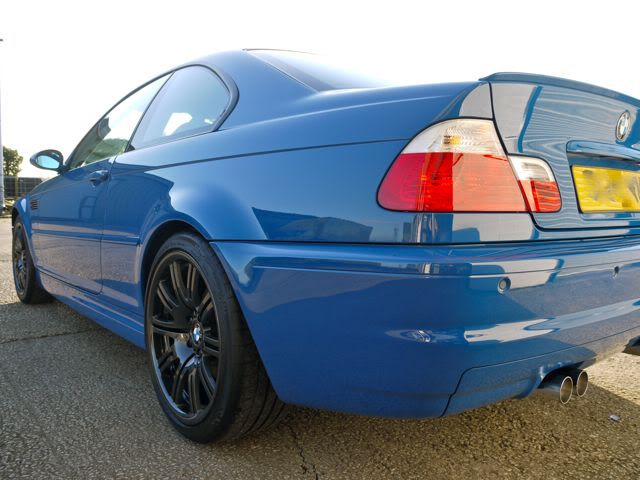
Anyway, I cleared off and let them get on with it. About an hour or so later I thought that I would go the whole hog and have the plates fitted as well just because i thought it would be a better selling point further down the line.
As the job would take a few days, I kept nipping over to get an update and also get some pics. They said they was OK with me doing.
This is how I left the car, wheels being slackened and the prop being undone. My heart was in my mouth lol
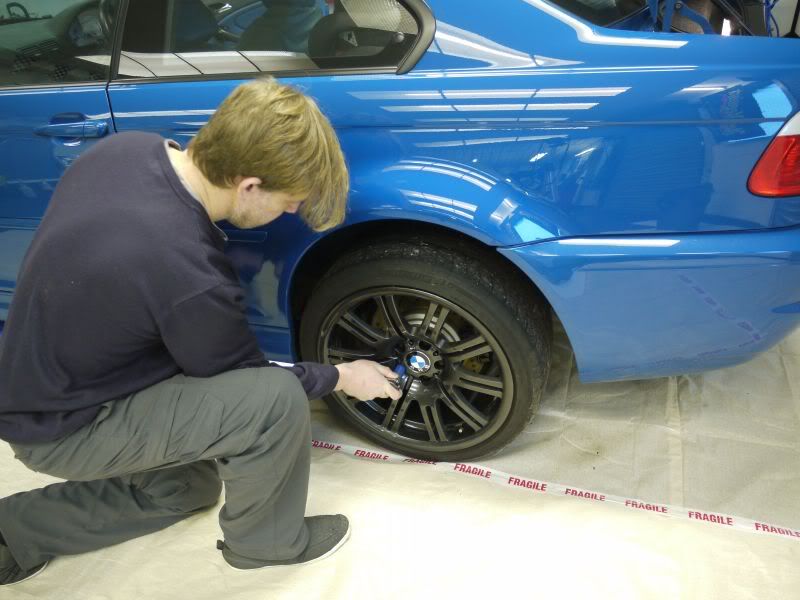
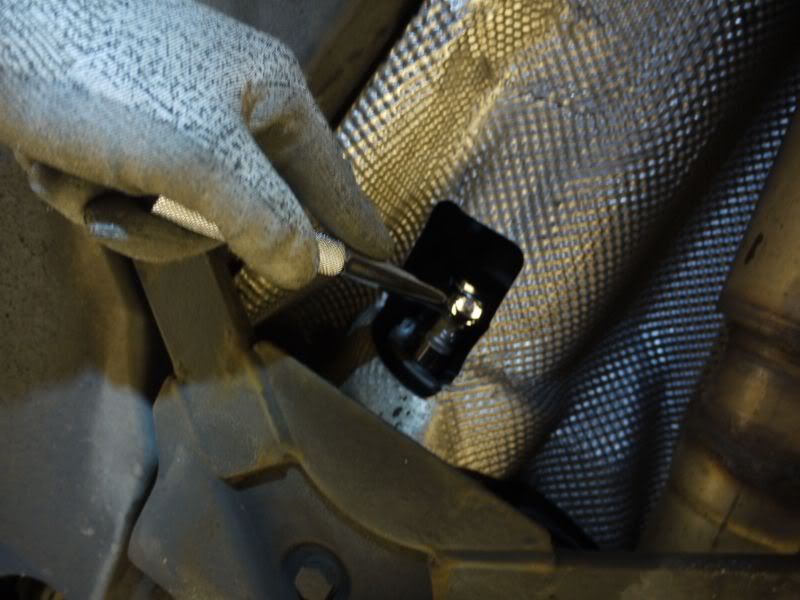
They explained they would remove the subframe, clean up the mount points and give me a bell. This is a pic of one of the front mount points - front right (a classic one for failing) The black semi circular marks are from the rubber subframe bushes. Apparently they have two lips that make contact with the floor. The pics show all the welds intact. Yay.
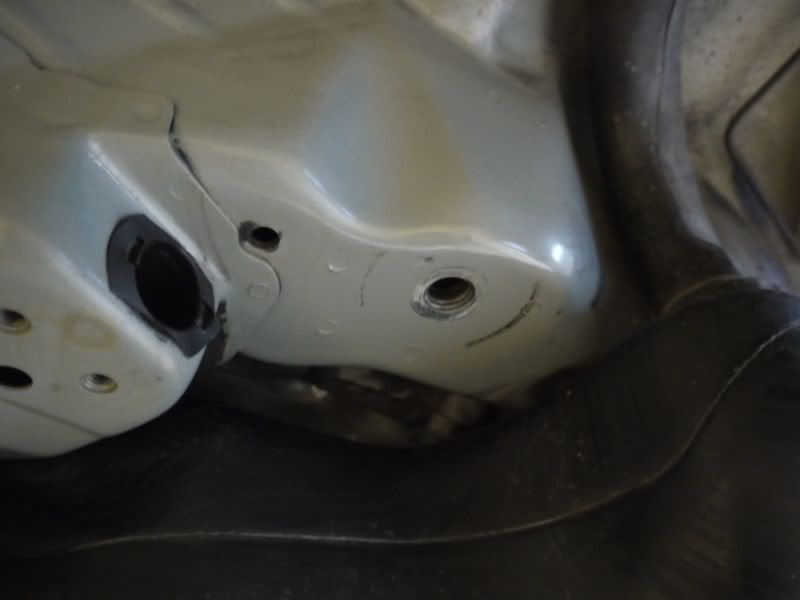
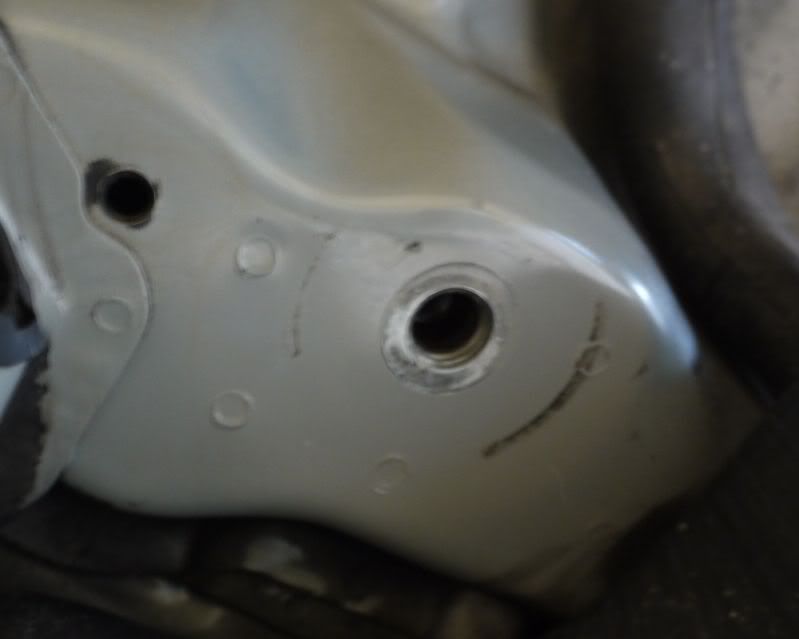
And the front left (usually always untouched)
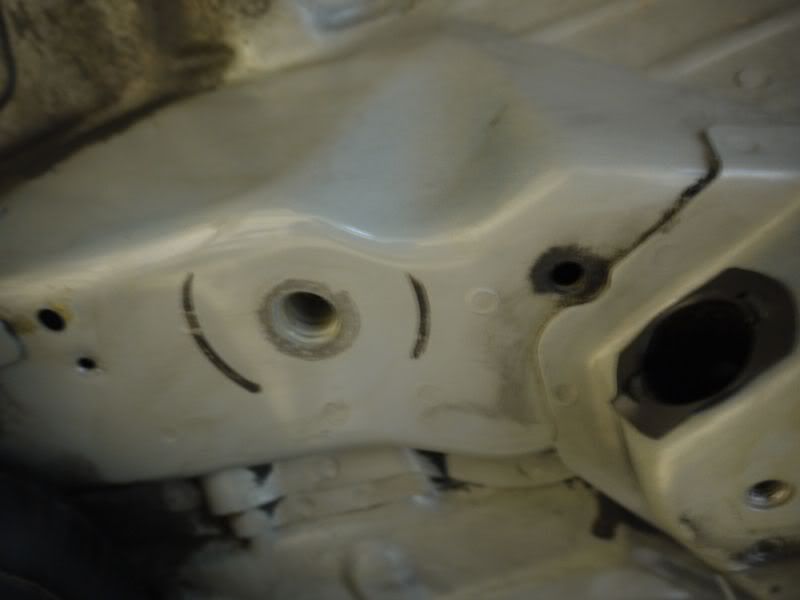
On a side note, It was explained that the rear left and the front right mounts are the ones that suffer. The rear left starts the flex and the paint on the spot welds comes off. Then they start to rust and weaken. This allows more flex and and then the spots fail. Once the spots fail even more movement and flex is allowed and a crack usually appears around the next weakest point - the formed/pressed radius section. Once the crack is there then so much flex allows problems to surface on the front right mount and the cracks begin there too! One of the guys is a Chartered Engineer and has performed some structural calculations, but I glazed over in seconds; but it sounded good.
I had the option of having the plates being welded in or bonded with some aerospace type resin. I went for the bonding option as they explained that when the plates are welded on the weld penetration burns off the protection on the inside of the floor section, plus the resin bonding was actually stronger than welding due to all the plate having a contact with the panel via the glue rather than just the weld around the perimeter. Bondage it was then!
It was safer too as I didnt like the idea of my mint car having welding done, plus they would have had to cut some metal from inside the boot to do a special weld from the inside then plate it.
Heres a pic of the rear left with most of the OEM e coat ground off - again the welds intact but there was evidence of straining apparently.
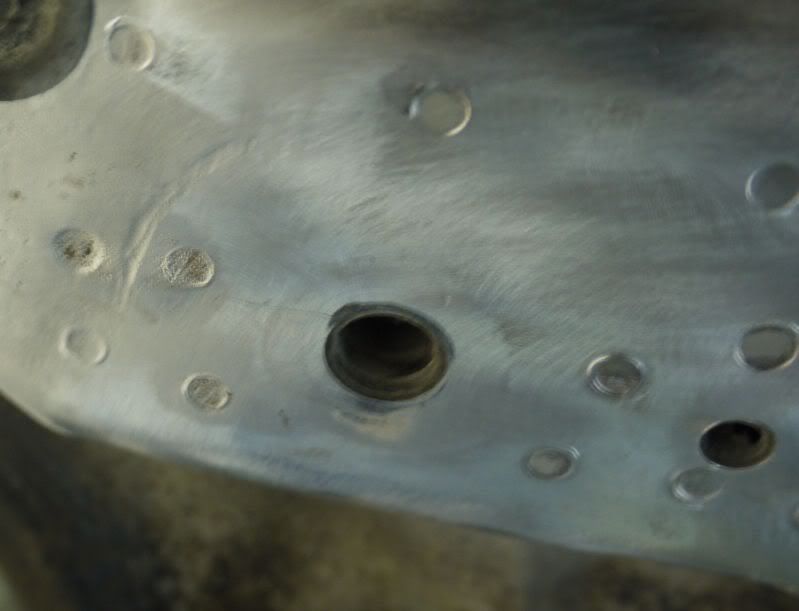
The bottom right weld had started to corrode! The very beginning of the process apparently.
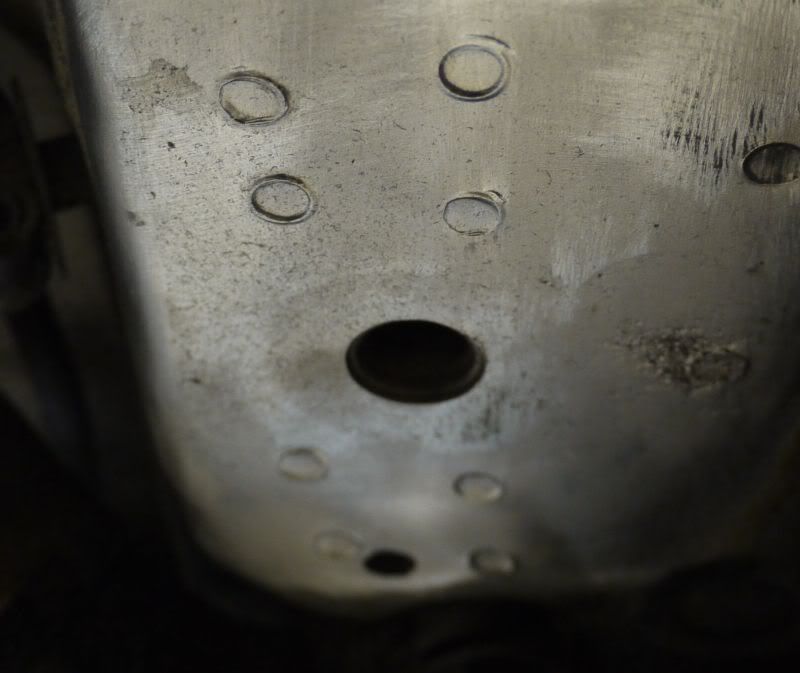
Here's a pic of the strengthening plate being roughed up to get a good key for the resin
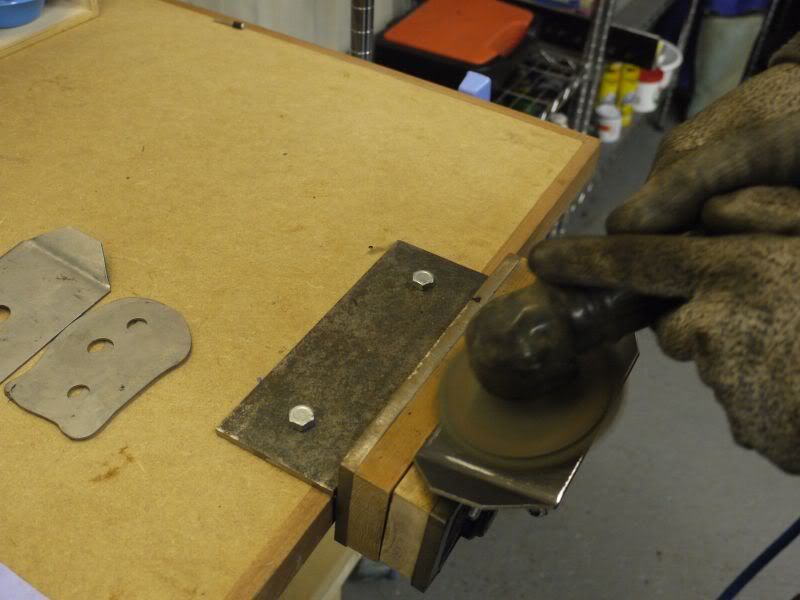
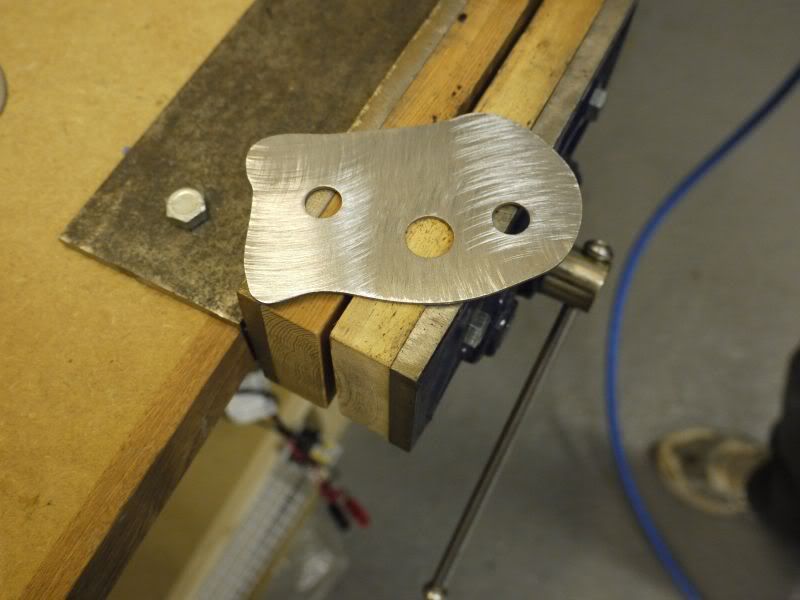
The surfaces on the floorpan were roughed up too, then the resin was applied to both the floor and the plates.
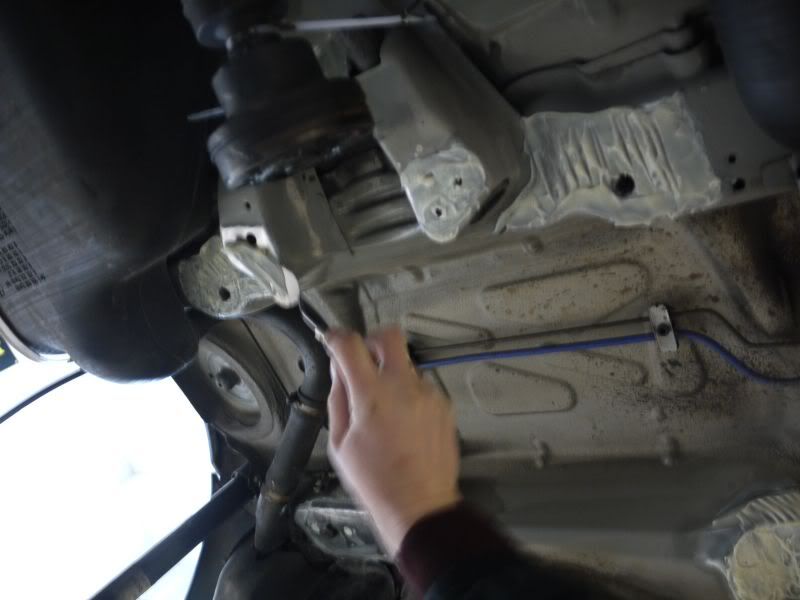
I never got round on the second day until after work but when I did the plates were bonded on, cured with infra red lamps and coated with etch primer and then painted with stonechip paint or something like that. Looks good to me!
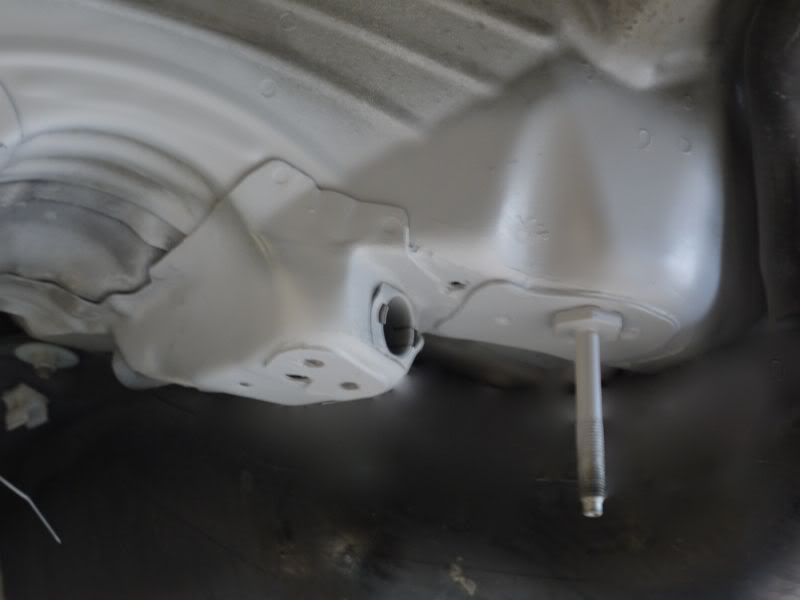
After that the frame was refitted - pretty much OEM looking!
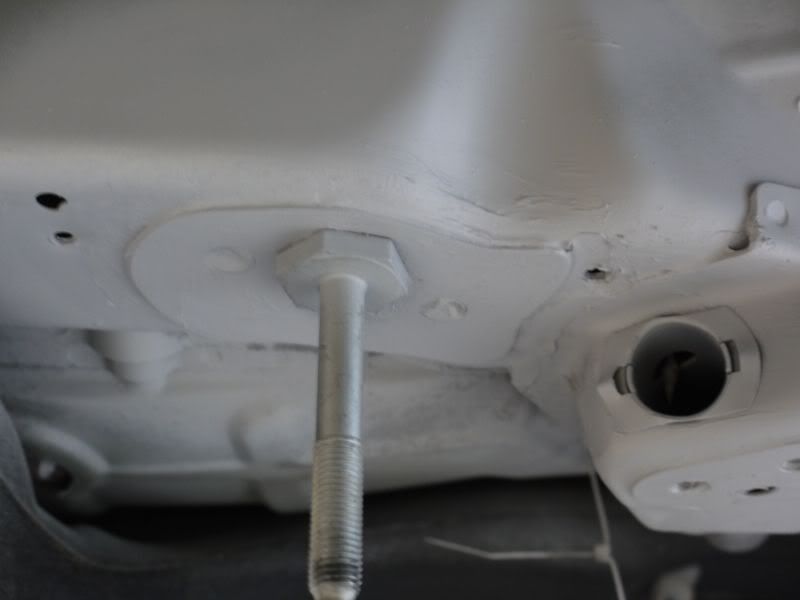
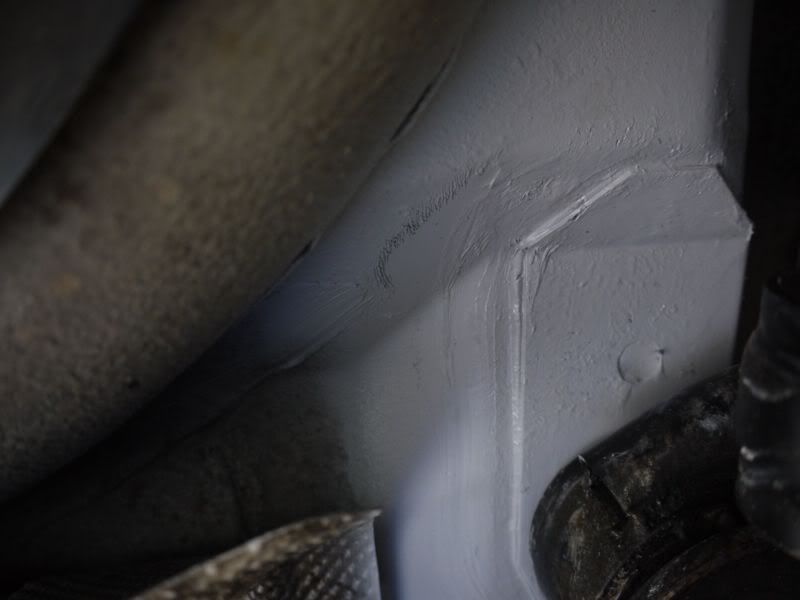
And then a resin based underseal
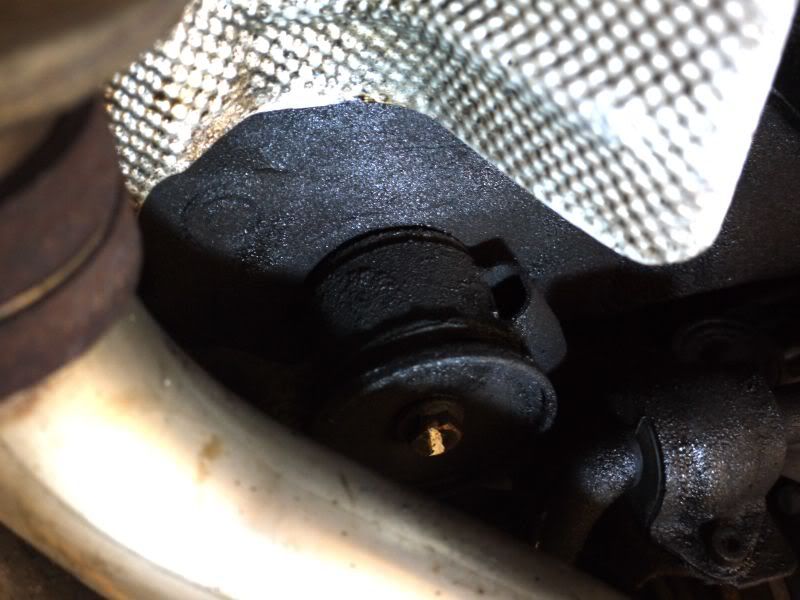
The final step was the resin injection inside the rear frame mount section to stop the twisting.
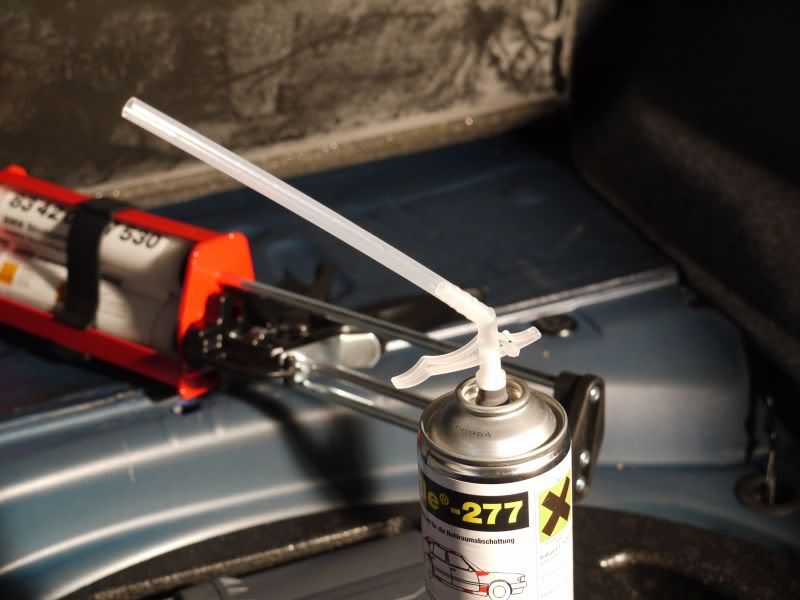
After 24 hours the resin had cured, job was done and car was cleaned and ready to drive home!
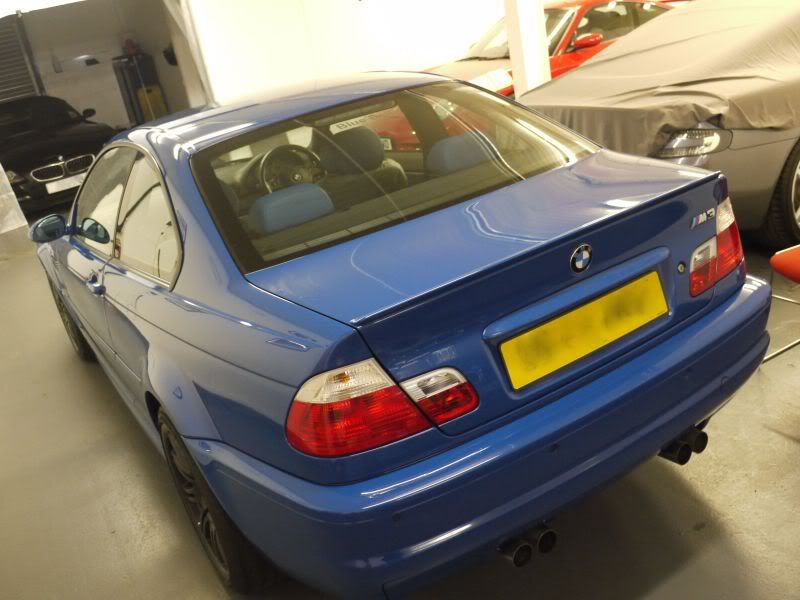

The car somehow felt tighter when under hard acceleration, like the power was going to the wheels rather than being absorbed with flex etc
So, Its a thumbs up from me! The whole process was worth the worry as now the work done makes my car stronger than it ever would be. I’m a pretty (well, very) critical character and can be demanding of garages largely due to me not trusting work to be done properly, but I must say I can wholeheartedly recommend MProve Solutions and thats why Iv’e taken the time and effort to write up in detail in the hope they get more work from people like me who worry about their car.
I run a small company myself and have our reputation on hard work and treating customers fairly and I am pleased to say these guys did exactly the same for me.
Luckily I have access to a car ramp, so a good inspection was easy enough. It was easy to inspect the rear mounts but to get a good look at the fronts was impossible as all you get is a peek at a couple of sections.
My car is a 2002 car that will be 10 years old in May; so I wanted to stop it cracking and so started surfing the net. It appeared that the way forward was to use the epoxy injection method from BMW to reinforce the rear left panel section to resist flex of the chassis and therefore stop any cracks. Apparently when/if BMW do a goodwill repair on the pre 10 year old cars they inject the resin as a preventative measure! I found that the following were needed:
Cavity foam to block off certain parts of the cavity inside the subframe panel
A 2 part foaming Epoxy resin (2off double cartridges)
Applicator gun for said Epoxy
A few drills, grommets and bits n’ pieces.
To reinforce just one side of the rear panel, the materials alone from BMW were around £220ish and the gun could be bought elsewhere for around £80 (BMW wanted £280 for the applicator gun but don’t sell it to the public as its a ‘special tool’) Although its primarily the rear left section that goes, I wanted both sides doing. So I was getting into £500 to do it myself. Plus it has to be done under controlled temperature conditions and must never dip below 5deg when curing or the resin won’t set correctly apparently - given that our climate is as predictable as the numbers for Euro Millions I felt it best to let a specialist do it for me! Plus I wanted proof of it being done properly for when I come to sell it.
I was pointed in to the direction of ‘MProve Solutions’ www.mprovesolutions.com via a BMWCC member. Long story short, I made contact and booked in at a price of £295 all in. They use the genuine BMW materials just the same and could lend me a car to use as it takes 24hrs to cure!
After a thorough inspection they confirmed there was indeed no cracks. To check, they loosened the rear mount bolts and lowered the frame by about 15mm and used a fancy camera on a long probe to get a picture of under the mount without taking off the frame! They also stuck the camera through an inspection hole in the boot to inspect the top of the mount from the inside! They also used the camera on the fronts also.
They mentioned another, more expensive option and that was to have some pre fabricated 2mm steel steel templates affixed to the chassis on the underside and have the resin reinforcement done also, but explained that was more usually for the preserve of cars that require cracks welding beforehand, then plating afterwards. A car that was maybe planning some serious power upgrades or heavy track use would also benefit. It was a good preventative measure but I decided to just stick with the cheaper option as I’m just a ‘regular’ driver. Bye Bye
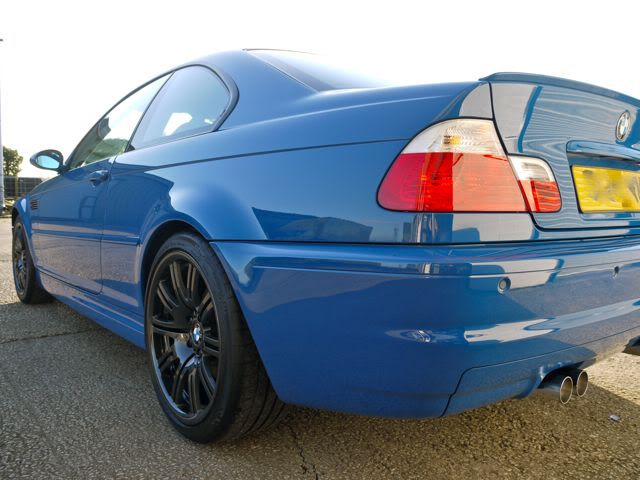
Anyway, I cleared off and let them get on with it. About an hour or so later I thought that I would go the whole hog and have the plates fitted as well just because i thought it would be a better selling point further down the line.
As the job would take a few days, I kept nipping over to get an update and also get some pics. They said they was OK with me doing.
This is how I left the car, wheels being slackened and the prop being undone. My heart was in my mouth lol
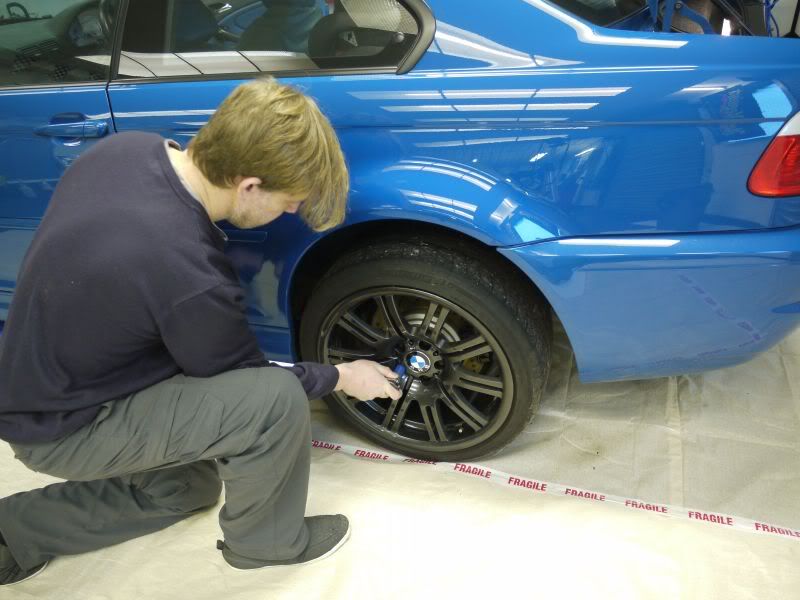
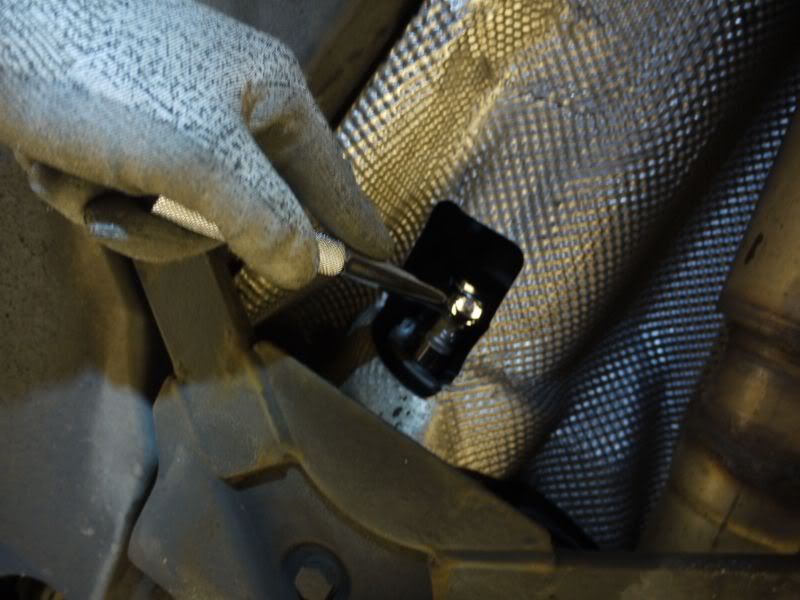
They explained they would remove the subframe, clean up the mount points and give me a bell. This is a pic of one of the front mount points - front right (a classic one for failing) The black semi circular marks are from the rubber subframe bushes. Apparently they have two lips that make contact with the floor. The pics show all the welds intact. Yay.
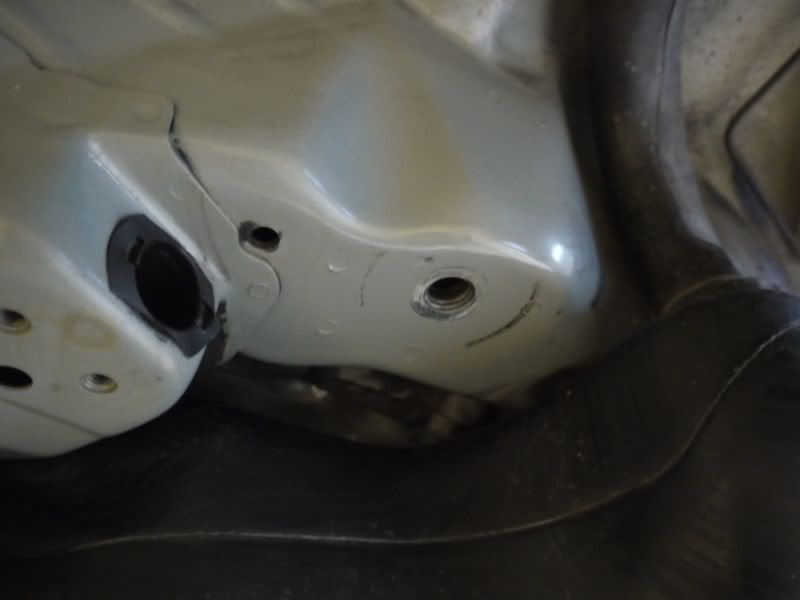
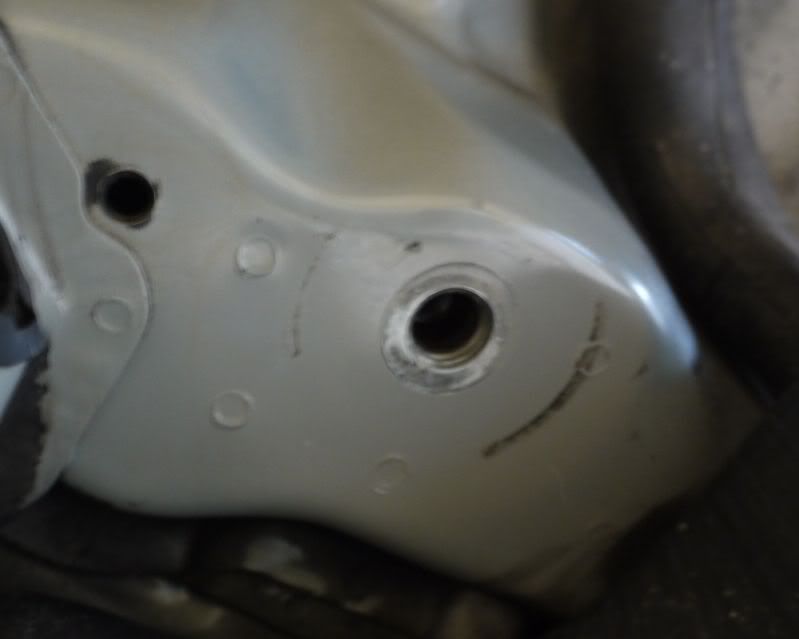
And the front left (usually always untouched)
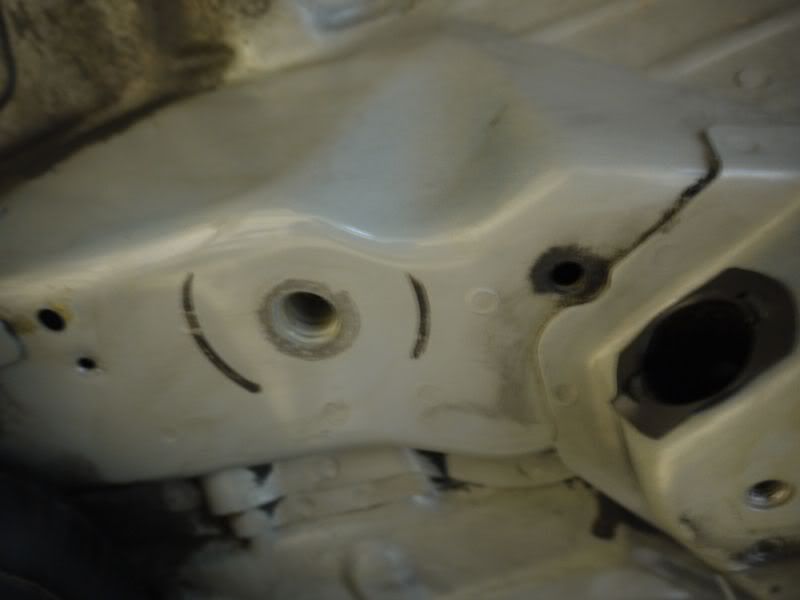
On a side note, It was explained that the rear left and the front right mounts are the ones that suffer. The rear left starts the flex and the paint on the spot welds comes off. Then they start to rust and weaken. This allows more flex and and then the spots fail. Once the spots fail even more movement and flex is allowed and a crack usually appears around the next weakest point - the formed/pressed radius section. Once the crack is there then so much flex allows problems to surface on the front right mount and the cracks begin there too! One of the guys is a Chartered Engineer and has performed some structural calculations, but I glazed over in seconds; but it sounded good.
I had the option of having the plates being welded in or bonded with some aerospace type resin. I went for the bonding option as they explained that when the plates are welded on the weld penetration burns off the protection on the inside of the floor section, plus the resin bonding was actually stronger than welding due to all the plate having a contact with the panel via the glue rather than just the weld around the perimeter. Bondage it was then!
It was safer too as I didnt like the idea of my mint car having welding done, plus they would have had to cut some metal from inside the boot to do a special weld from the inside then plate it.
Heres a pic of the rear left with most of the OEM e coat ground off - again the welds intact but there was evidence of straining apparently.
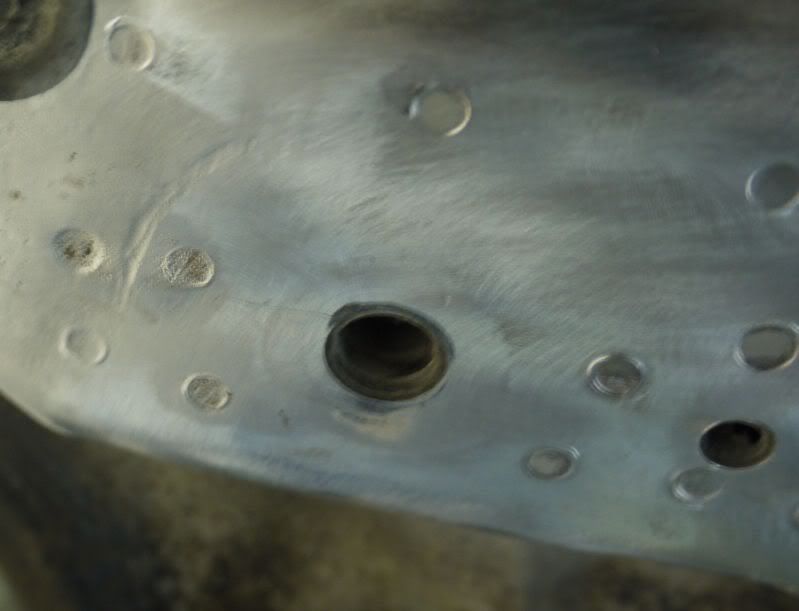
The bottom right weld had started to corrode! The very beginning of the process apparently.
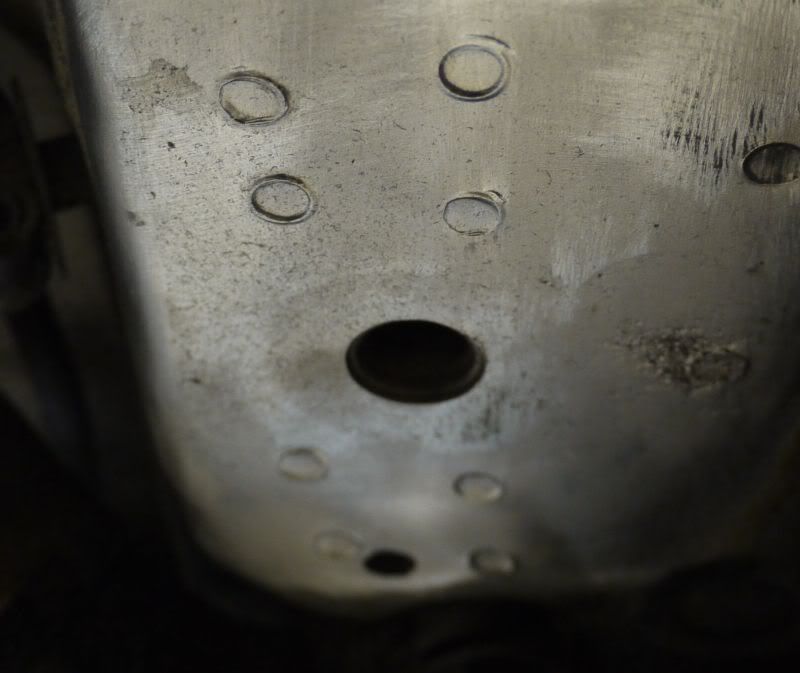
Here's a pic of the strengthening plate being roughed up to get a good key for the resin
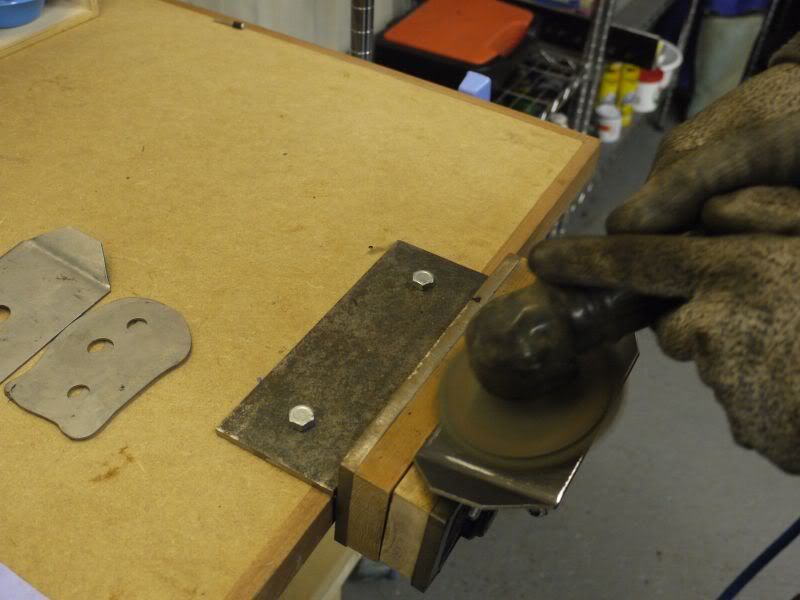
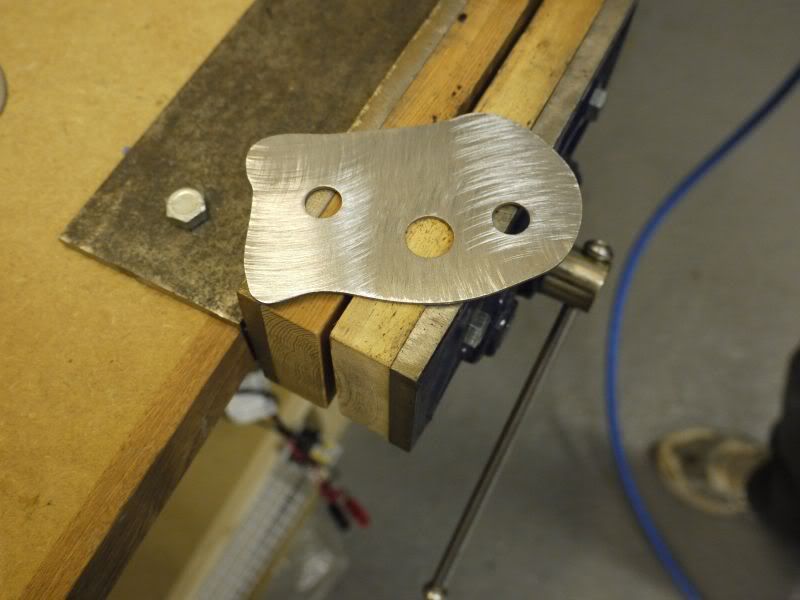
The surfaces on the floorpan were roughed up too, then the resin was applied to both the floor and the plates.
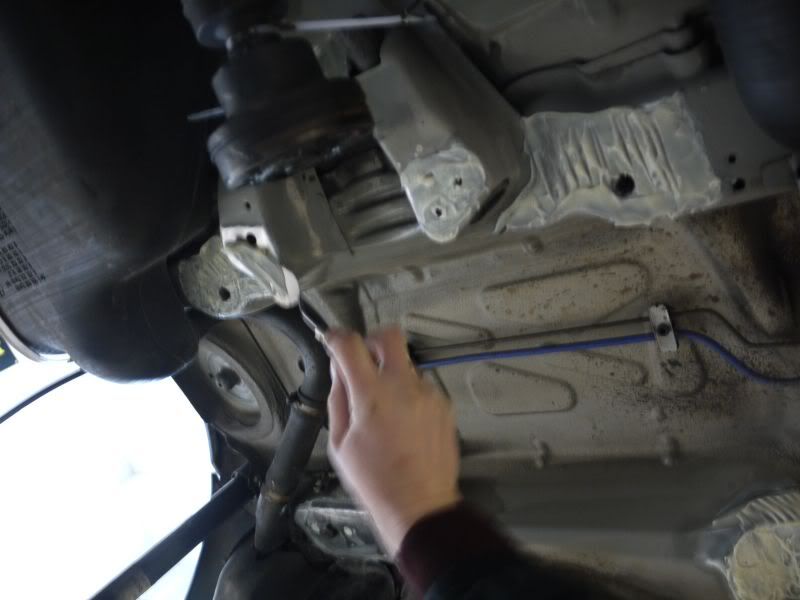
I never got round on the second day until after work but when I did the plates were bonded on, cured with infra red lamps and coated with etch primer and then painted with stonechip paint or something like that. Looks good to me!
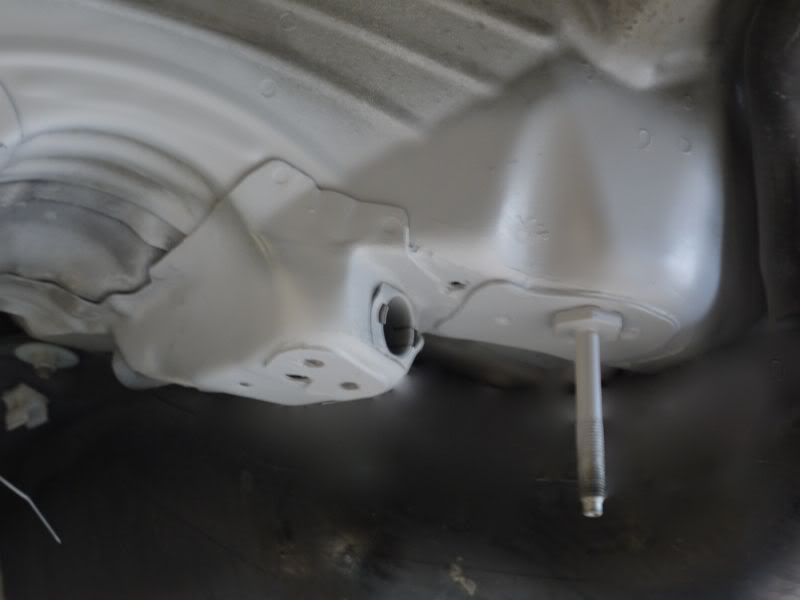
After that the frame was refitted - pretty much OEM looking!
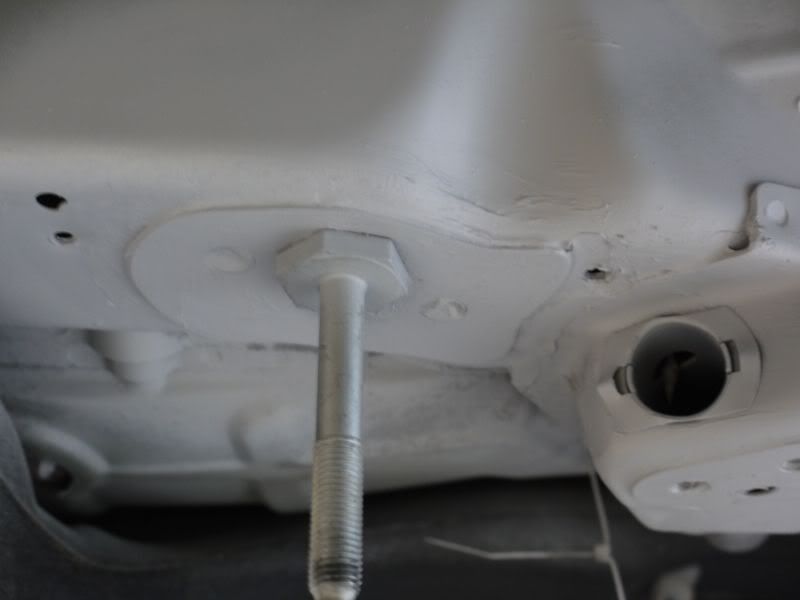
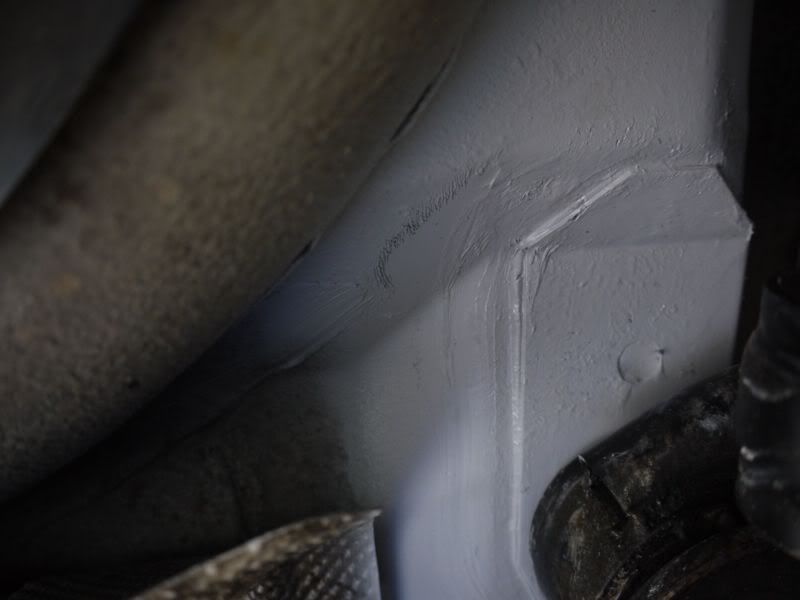
And then a resin based underseal
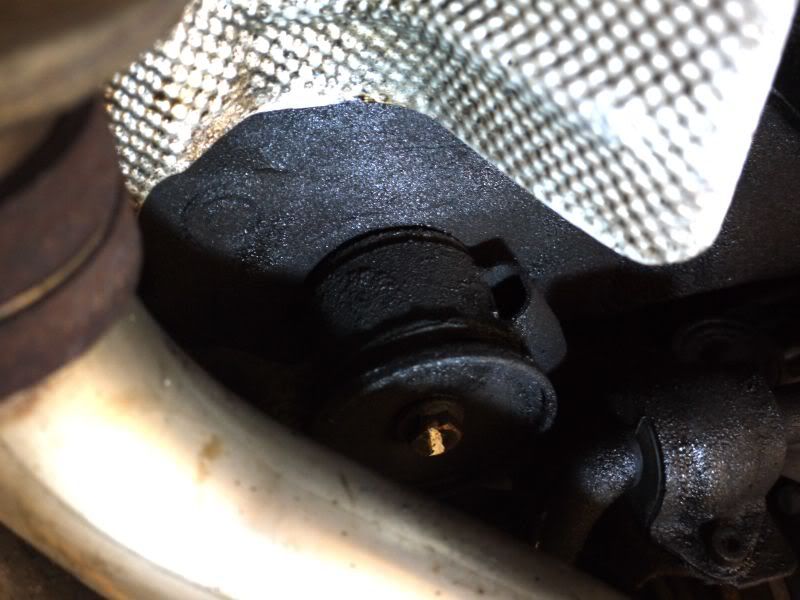
The final step was the resin injection inside the rear frame mount section to stop the twisting.
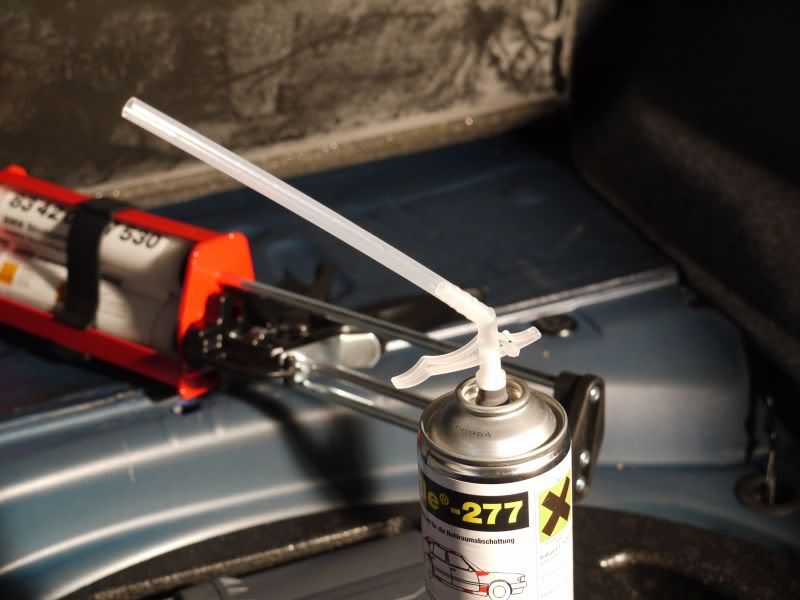
After 24 hours the resin had cured, job was done and car was cleaned and ready to drive home!
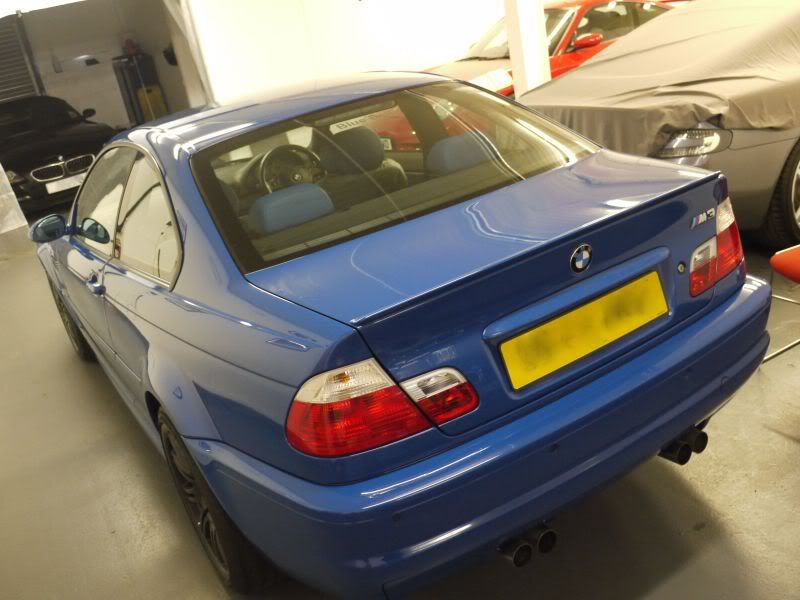

The car somehow felt tighter when under hard acceleration, like the power was going to the wheels rather than being absorbed with flex etc
So, Its a thumbs up from me! The whole process was worth the worry as now the work done makes my car stronger than it ever would be. I’m a pretty (well, very) critical character and can be demanding of garages largely due to me not trusting work to be done properly, but I must say I can wholeheartedly recommend MProve Solutions and thats why Iv’e taken the time and effort to write up in detail in the hope they get more work from people like me who worry about their car.
I run a small company myself and have our reputation on hard work and treating customers fairly and I am pleased to say these guys did exactly the same for me.
I was considering having this done myself, in light of deciding to use an M3 as a daily driver. Also having some sort of weatherproofing put on the underside of the car – is this a silly idea? I guess, back in the day, you’d call it underseal, is there a modern alternative that would be suitable for weatherproofing a car to use as a daily driver?
thanks
thanks
jaedba2604 said:
I was considering having this done myself, in light of deciding to use an M3 as a daily driver. Also having some sort of weatherproofing put on the underside of the car – is this a silly idea? I guess, back in the day, you’d call it underseal, is there a modern alternative that would be suitable for weatherproofing a car to use as a daily driver?
thanks
All cars are undersealed in the factory using some sort of wax oil, the M3 is n exception. You shouldnt have any issues what so ever using it as a daily driverthanks
philis said:
jaedba2604 said:
I was considering having this done myself, in light of deciding to use an M3 as a daily driver. Also having some sort of weatherproofing put on the underside of the car – is this a silly idea? I guess, back in the day, you’d call it underseal, is there a modern alternative that would be suitable for weatherproofing a car to use as a daily driver?
thanks
All cars are undersealed in the factory using some sort of wax oil, the M3 is n exception. You shouldnt have any issues what so ever using it as a daily driverthanks
Fascinating thread, and interesting to hear that people are bonding the plates on rather than welding them in place ... The designs of the plates in this thread appear to call for welding, and for a puddle weld in the drilled holes, however I can see that bonding could work ok.
I've just completed the repairs and associated strengthening to my chassis, and must get around to sharing the pictures of this, plus do a write up of the work we undertook.
Very interested to know what the cost of the labour content of this work was for the OP.
I've just completed the repairs and associated strengthening to my chassis, and must get around to sharing the pictures of this, plus do a write up of the work we undertook.
Very interested to know what the cost of the labour content of this work was for the OP.
Guys
Thanks for the comments, glad it may have helped someone.
The cost for the fitting of the plates and the reinforcing of the inner subframe mounting panel (both sides not just the LHS) and rear geometry reset was £795 all in. Given the time involved, materials used and the future benefits I would probably say it has been the best money ive ever spent on a car! Especially in the past when Ive w
ked £500 quid on a remap thats done nothing more than made it more 'drivable' lol
Thanks for the comments, glad it may have helped someone.
The cost for the fitting of the plates and the reinforcing of the inner subframe mounting panel (both sides not just the LHS) and rear geometry reset was £795 all in. Given the time involved, materials used and the future benefits I would probably say it has been the best money ive ever spent on a car! Especially in the past when Ive w

The bonding method has been known for years on the other side of the pond.
I debated it, but was put off by the temperatures the exhaust can get to, and the breaking temperature point of the bonding agent on two of them.
ETA did mine, albeit wedled. Like the OP, the car felt very different leaving. The only other thing I did was change the rear subframe bushes.
I debated it, but was put off by the temperatures the exhaust can get to, and the breaking temperature point of the bonding agent on two of them.
ETA did mine, albeit wedled. Like the OP, the car felt very different leaving. The only other thing I did was change the rear subframe bushes.
Gassing Station | M Power | Top of Page | What's New | My Stuff