Throttle bodies and forced induction
Discussion
I'm about to build a custom inlet manifold for my engine (J-Series Renault 2.0). It's got plenty of expensive forged bits inside, big cam, standalone and all that tosh.
While i'm messing about, i'm considering using ITB's instead of a single TB. I'm finding a lot of conflicting information out on the world wide web, so I thought i'd ask here which seems to be pretty reliable for tuning info (you clever barstewards, you
)
What am I looking for? BHP, of course, and something different for my old Renault. The current plan is to use 8 injectors (although I don't need to with current tech, but it fits with the era of the car, and it's cool). I would sacrifice this though to use ITB's with a single 1000cc injector per pot if I was up for a good chance of making a bit more power.
Opinions please, on using ITB's on a car with forced induction....(up to 2 bar boost)
Thanks!
While i'm messing about, i'm considering using ITB's instead of a single TB. I'm finding a lot of conflicting information out on the world wide web, so I thought i'd ask here which seems to be pretty reliable for tuning info (you clever barstewards, you

What am I looking for? BHP, of course, and something different for my old Renault. The current plan is to use 8 injectors (although I don't need to with current tech, but it fits with the era of the car, and it's cool). I would sacrifice this though to use ITB's with a single 1000cc injector per pot if I was up for a good chance of making a bit more power.
Opinions please, on using ITB's on a car with forced induction....(up to 2 bar boost)
Thanks!

http://www.theturboforums.com/smf/advanced-tech-se...
Here's an internet thing. Makes sense I guess - much denser air after the turbo, so the throttle bodies make much more of a restriction there.
Here's an internet thing. Makes sense I guess - much denser air after the turbo, so the throttle bodies make much more of a restriction there.
davepoth said:
http://www.theturboforums.com/smf/advanced-tech-se...
Here's an internet thing. Makes sense I guess - much denser air after the turbo, so the throttle bodies make much more of a restriction there.
Thanks for the responses - however i'm not talking about pre-turbo TB's, i'm talking about going from this>>Here's an internet thing. Makes sense I guess - much denser air after the turbo, so the throttle bodies make much more of a restriction there.
Single TB
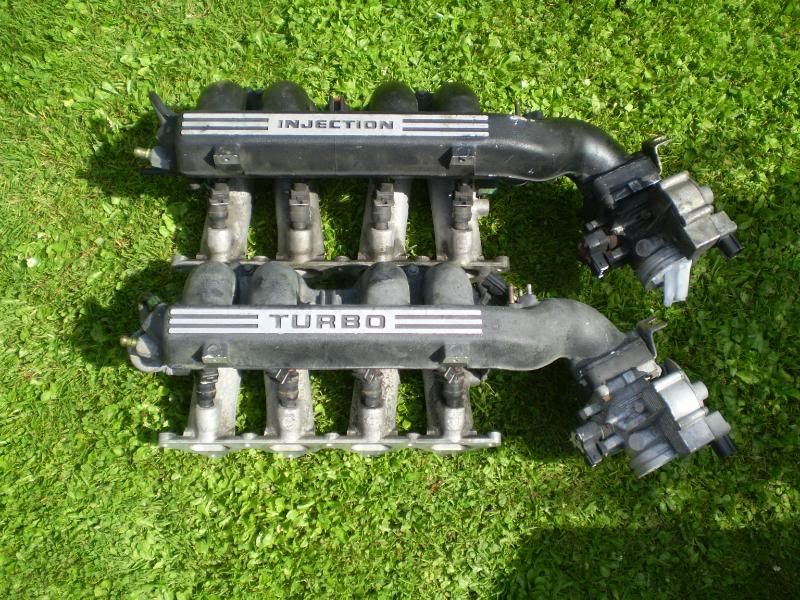
To this>>
Individual Throttle Bodies

not my pics, just random google images btw.
Firstly, engines don't care if they are turbocharged or not. The turbo does not "force air into the engine". (it just increases the manifold air density, in fact, the pressure ratio across the engine (and hence the Manifold volumetric efficiency) falls).
Hence, turbo engines respond to ITB's just like NA ones.
The biggest issue is one of robust "Load sensing". On a forced induction engine the intake massflow changes massively with both throttle position and manifold pressure. You cannot just use one or the other, you need to know both.
Regarding those pics, i suspect the lower one will flow signficantly worse than the normal manifold due to the tight (~1D) bend immediately upstream of the throttle plates. (means the hydraulic diameter of the system is massively reduced. (not to mention the hideous runner to "plenum" entry condition!)
Hence, turbo engines respond to ITB's just like NA ones.
The biggest issue is one of robust "Load sensing". On a forced induction engine the intake massflow changes massively with both throttle position and manifold pressure. You cannot just use one or the other, you need to know both.
Regarding those pics, i suspect the lower one will flow signficantly worse than the normal manifold due to the tight (~1D) bend immediately upstream of the throttle plates. (means the hydraulic diameter of the system is massively reduced. (not to mention the hideous runner to "plenum" entry condition!)
Max_Torque said:
The biggest issue is one of robust "Load sensing".
True....currently runs off a single 3-bar MAP sensor and TPS. The TPS will be easy enough to rig up....I guess the MAP sensor would either need bridging across the cylinders or maybe switch to a MAF....Max_Torque said:
Regarding those pics, i suspect the lower one will flow signficantly worse than the normal manifold due to the tight (~1D) bend immediately upstream of the throttle plates. (means the hydraulic diameter of the system is massively reduced. (not to mention the hideous runner to "plenum" entry condition!)
As stated not mine, just a visual example of what I meant. I'm using 3" pipework and 3" intercooler, so the intake to the plenum would match that too.This is mine when I was messing about fitting the intercooler-
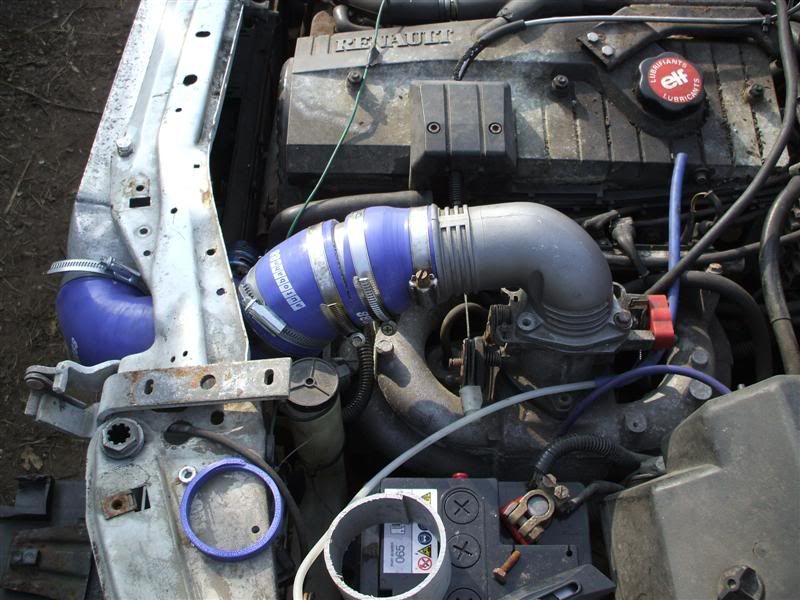
DaveL485 said:
I'm about to build a custom inlet manifold for my engine (J-Series Renault 2.0). It's got plenty of expensive forged bits inside, big cam, standalone and all that tosh.
While i'm messing about, i'm considering using ITB's instead of a single TB. I'm finding a lot of conflicting information out on the world wide web, so I thought i'd ask here which seems to be pretty reliable for tuning info (you clever barstewards, you
)
What am I looking for? BHP, of course, and something different for my old Renault. The current plan is to use 8 injectors (although I don't need to with current tech, but it fits with the era of the car, and it's cool). I would sacrifice this though to use ITB's with a single 1000cc injector per pot if I was up for a good chance of making a bit more power.
Opinions please, on using ITB's on a car with forced induction....(up to 2 bar boost)
Thanks!
Boost pressure is irrelevant. And TBH, if you cannot meet your power goals with a single throttle and boost, something is badly wrong.While i'm messing about, i'm considering using ITB's instead of a single TB. I'm finding a lot of conflicting information out on the world wide web, so I thought i'd ask here which seems to be pretty reliable for tuning info (you clever barstewards, you

What am I looking for? BHP, of course, and something different for my old Renault. The current plan is to use 8 injectors (although I don't need to with current tech, but it fits with the era of the car, and it's cool). I would sacrifice this though to use ITB's with a single 1000cc injector per pot if I was up for a good chance of making a bit more power.
Opinions please, on using ITB's on a car with forced induction....(up to 2 bar boost)
Thanks!

All ITB's will do is add cost, complication and hassle. Positives may be better throttle response and perhaps a small fraction more power if well designed with a decent plenum...Much like the OEM already has.
And even a single 60-65mm throttle blade will easily support 600+
Funnily enough i have a boosted Renault Engine:


2.0 F7r Turbo, with electronic "fly-by-wire" ITB's, custom carbon intake system, 8 injectors and ALS.
It also uses a pretty trick electronic "MAP sensor per runner" device, that measures the manifold pressure within each runner at a high freqency (approx 2kHz), but is linked (via a PPL) to the crank position sensor so it only looks at the sensor for the runner that is actually undergoing its intake stroke. By using a filtering algorythm, it calculates the average charge density individually for each firing event. In this fashion i am able to "recover" a genuine MAP signal with enhanced Signal to noise ratio under all load and speed conditions.
The absolute diameter of the upstream intake piping is actually fairly unimportant, however, "Area Rule " and "Efficient Pressure Recovery" are the watchwords of a decent intake system.


2.0 F7r Turbo, with electronic "fly-by-wire" ITB's, custom carbon intake system, 8 injectors and ALS.
It also uses a pretty trick electronic "MAP sensor per runner" device, that measures the manifold pressure within each runner at a high freqency (approx 2kHz), but is linked (via a PPL) to the crank position sensor so it only looks at the sensor for the runner that is actually undergoing its intake stroke. By using a filtering algorythm, it calculates the average charge density individually for each firing event. In this fashion i am able to "recover" a genuine MAP signal with enhanced Signal to noise ratio under all load and speed conditions.
The absolute diameter of the upstream intake piping is actually fairly unimportant, however, "Area Rule " and "Efficient Pressure Recovery" are the watchwords of a decent intake system.
The biggest gains on any engine (N/A or FI) with ITB's is the ability to retain decent driveability with more aggressive cam profiles. The smaller volume between intake valve and throttle plate means that at part throttle the throttle plate acts as a restriction and blocks pressure reversals during the overlap period that would otherwise fill the plenum with residuals when at light load / slow speed.
Benefits in response come from not having to wait for plenum filling, especially when moving between part throttle and boosted operation. This is especially true when using aggressive antilag strategies, where the plenum is maintained at "full" boost pressure during gear shifts / off throttle events etc.
Benefits in response come from not having to wait for plenum filling, especially when moving between part throttle and boosted operation. This is especially true when using aggressive antilag strategies, where the plenum is maintained at "full" boost pressure during gear shifts / off throttle events etc.
stevieturbo said:
Boost pressure is irrelevant. And TBH, if you cannot meet your power goals with a single throttle and boost, something is badly wrong.
1995cc, 4-pot 21 Turbo J-Series bottom end, 12v (from the NA TXi engine) head, billet cam with spec below.duration | duration | maximum lift | lift at TDC | parts | application |
---|---|---|---|---|---|
[0.1mm+cl] | [1.0mm+cl] | [cl=0] | [cl=0] | [-] | (TURBO) |
275 / 264° | 239 / 227° | 10.45 / 9.90mm | 2.45 / 3.80mm | custom | MECH: rally & cross |
Vernier, big Turbo, custom manifolds and standalone. Target 500 brake at 2bar. Obviously its a bit more extensive than that but they're the essentials.
stevieturbo said:
And even a single 60-65mm throttle blade will easily support 600+
Was planning a 70mm single, so that should be OK then! 
Max_Torque said:
Funnily enough i have a boosted Renault Engine:
2.0 F7r Turbo, with electronic "fly-by-wire" ITB's, custom carbon intake system, 8 injectors and ALS.
It also uses a pretty trick electronic "MAP sensor per runner" device, that measures the manifold pressure within each runner at a high freqency (approx 2kHz), but is linked (via a PPL) to the crank position sensor so it only looks at the sensor for the runner that is actually undergoing its intake stroke. By using a filtering algorythm, it calculates the average charge density individually for each firing event. In this fashion i am able to "recover" a genuine MAP signal with enhanced Signal to noise ratio under all load and speed conditions.
The absolute diameter of the upstream intake piping is actually fairly unimportant, however, "Area Rule " and "Efficient Pressure Recovery" are the watchwords of a decent intake system.
Christ, thats lovely. What sort of numbers is that running? Stunning bit of work I must say. The most powerful F7R i've seen so far is 749bhp so that can't be far off? I don't think i'm looking to be quite that advanced on the first build. Maybe in the future....or if I decide to invest in my 172 lump instead of the good old J7R....2.0 F7r Turbo, with electronic "fly-by-wire" ITB's, custom carbon intake system, 8 injectors and ALS.
It also uses a pretty trick electronic "MAP sensor per runner" device, that measures the manifold pressure within each runner at a high freqency (approx 2kHz), but is linked (via a PPL) to the crank position sensor so it only looks at the sensor for the runner that is actually undergoing its intake stroke. By using a filtering algorythm, it calculates the average charge density individually for each firing event. In this fashion i am able to "recover" a genuine MAP signal with enhanced Signal to noise ratio under all load and speed conditions.
The absolute diameter of the upstream intake piping is actually fairly unimportant, however, "Area Rule " and "Efficient Pressure Recovery" are the watchwords of a decent intake system.
Appreciate the input, I think i'll stick with the original plan for now then.
DaveL485 said:
Was planning a 70mm single, so that should be OK then!
Actually, 70mm would be excessive and offer a reduction in resolution under foot.Fitting a throttle that allows all the air the engine would ever need at say 60-70% opening just means instead of a useful 0-100% under your foot, you now only have 0-70% for the same engine output.
Always baffles me why people use such large throttles. Some even use throttles far far larger than their boost plumbing !
stevieturbo said:
Always baffles me why people use such large throttles. Some even use throttles far far larger than their boost plumbing !
Boost pipework & intercooler is 76mm, so I opted for 70 as it's the biggest thats under the pipework, IYSWIM.I'm in uncharted territory so half the work is based on gut feeling lol (I can almost feel Pumaracing trembling at that remark!)
It's easy, just follow the 1kPa or less rule of dynamic head!
(no that's not some sort of weird sexual fetish ;-)
Effectively you size your plumbing so that under maximum airflow conditions, no more than 1kPa of dynamic pressure exists. In that way, you only ever have 1 kPa to loose through poor pressure recovery in the inlet. I'll leave it to Google and you to research the necessary simple formulas to calculate dynamic air pressure !
(no that's not some sort of weird sexual fetish ;-)
Effectively you size your plumbing so that under maximum airflow conditions, no more than 1kPa of dynamic pressure exists. In that way, you only ever have 1 kPa to loose through poor pressure recovery in the inlet. I'll leave it to Google and you to research the necessary simple formulas to calculate dynamic air pressure !
Max_Torque said:
It's easy, just follow the 1kPa or less rule of dynamic head!
(no that's not some sort of weird sexual fetish ;-)
Effectively you size your plumbing so that under maximum airflow conditions, no more than 1kPa of dynamic pressure exists. In that way, you only ever have 1 kPa to loose through poor pressure recovery in the inlet. I'll leave it to Google and you to research the necessary simple formulas to calculate dynamic air pressure !
Oh go on, you know you want to do an example for us, what figures and specs do you need? I can't find anything on Google.(no that's not some sort of weird sexual fetish ;-)
Effectively you size your plumbing so that under maximum airflow conditions, no more than 1kPa of dynamic pressure exists. In that way, you only ever have 1 kPa to loose through poor pressure recovery in the inlet. I'll leave it to Google and you to research the necessary simple formulas to calculate dynamic air pressure !
DaveL485 said:
Boost pipework & intercooler is 76mm, so I opted for 70 as it's the biggest thats under the pipework, IYSWIM.
I'm in uncharted territory so half the work is based on gut feeling lol (I can almost feel Pumaracing trembling at that remark!)
If there are lots of twists/turns, oversizing the plumbing can make sense to accommodate for those bends etc.I'm in uncharted territory so half the work is based on gut feeling lol (I can almost feel Pumaracing trembling at that remark!)
But going large on the throttle size just makes little sense.
After all...what size is the discharge of the turbo ?
Although even my own TB is slightly oversized, although that's because the bigger versions were more readily available, and shiny, and cheap !
stevieturbo said:
If there are lots of twists/turns, oversizing the plumbing can make sense to accommodate for those bends etc.
But going large on the throttle size just makes little sense.
After all...what size is the discharge of the turbo ?
Although even my own TB is slightly oversized, although that's because the bigger versions were more readily available, and shiny, and cheap !
The sizing of boost pipes and throttle bodies is much talked about with some going small and some going big, there seem to be good arguments for either way.But going large on the throttle size just makes little sense.
After all...what size is the discharge of the turbo ?
Although even my own TB is slightly oversized, although that's because the bigger versions were more readily available, and shiny, and cheap !
I've never heard of anyone with any official qualification make comment on the matter, it would be good to see a back to back test done.
I'm a big pipe man myself (ooh er missus) (and TB) and I would like to put some questions forward for you to answer and some points I have noted on the subject, let's set a spec of a 4 cyl turbo engine making 500bhp:
Your comment on the small output nozzle of a turbo is good and I do wonder why then do we not keep all the pipework that size? It looks about 50mm on the good old GT3076R which will do around 500 - 600 bhp. So then why do most intercoolers which will handle that kind of power have 75mm inlet/outlets? You shouldn't mess with the air to keep it flowing well (keep diameters the same*, bends to a minimum).
- Apart from on a bend when a pipe which has a bigger bowl on the longside would be an advantage)
If you were using 75mm pipework then a 70mm TB the TB would cause a restriction in the system, not only from its smaller diameter, but also the reduction caused by the plate and spindle. An 85mm item would be more appropriate (roughly speaking) to keep the airflow something like constant.
UNLESS (for some reason) we are trying to speed up the air at this point on it's entry to the plenum where exactly the opposite happens. Substitute the word 'Plenum' for 'settling chamber'.
Your comments are welcome.
Of course you should keep bends to a minimum, but obviously that's impractical. There will always be bends.
There are rules where air velocity in the pipework needs to be kept below a certain level. The maths for that is way over my head, so back to keeping it simple.
So you want the pipework as small as possible without posing any major restriction ( again, no numbers )
So whilst it could make sense to retain that 50mm throughout, it doesnt. Adding bends regardless of them being mandrel bent will pose a restriction. SO for that reason alone it can make sense to increase diameter a little or a lot to accommodate for the restriction of the bends.
As for intercoolers. Core design is but a small part. Of equal importance are the end tanks. Most egay ones regardless of pipe size are crap for the simple reason the end tanks do not promote even flow through the core regardless of their inlet/exit size.
3" is normally used as it pretty much covers all options. 3" pipework is easily worked and readily available. It is still a size that most engine bays can accommodate and will support over 1kbhp.
but it will equally be at home at 500bhp. So it's just an easy and sensible size to use.
Although despite the egay IC failings, as they are generally fairly big and very very cheap, value for money they are pretty good.
As for pipe size changes/IC. The only time really I see a change being necessary is at the entry and exit of the IC core. In otherwords, a large smooth flowing, and if need be ducted flow path to the actual tubes of the core to promote even flow into and out of the core. Actual inlet and outlet pipe size are largely irrelevant.
So yes about TB size. In reality I cant see there being much, if any benefit from using a TB much larger ( as you say to accommodate for the blade/shaft itself ) than the outlet of the turbocharger.
Fitting a TB larger than the actual boost plumbing if it is already much larger than the turbo discharge just seems silly. At least in terms of throttle resolution.
As I say, if you fitted a huge TB to a turbo car you can and do see scenarios where say 60% upwards of opening makes no difference because it's already flowing all the air the engine can actually consume. So all you've done is give yourself horrible throttle control which often is also a pig to tune and drive at low openings.
For 500bhp, IMO 2.5" OD is quite adequate unless there are a huge amount of bends and say a 55-60mm TB
There are rules where air velocity in the pipework needs to be kept below a certain level. The maths for that is way over my head, so back to keeping it simple.
So you want the pipework as small as possible without posing any major restriction ( again, no numbers )
So whilst it could make sense to retain that 50mm throughout, it doesnt. Adding bends regardless of them being mandrel bent will pose a restriction. SO for that reason alone it can make sense to increase diameter a little or a lot to accommodate for the restriction of the bends.
As for intercoolers. Core design is but a small part. Of equal importance are the end tanks. Most egay ones regardless of pipe size are crap for the simple reason the end tanks do not promote even flow through the core regardless of their inlet/exit size.
3" is normally used as it pretty much covers all options. 3" pipework is easily worked and readily available. It is still a size that most engine bays can accommodate and will support over 1kbhp.
but it will equally be at home at 500bhp. So it's just an easy and sensible size to use.
Although despite the egay IC failings, as they are generally fairly big and very very cheap, value for money they are pretty good.
As for pipe size changes/IC. The only time really I see a change being necessary is at the entry and exit of the IC core. In otherwords, a large smooth flowing, and if need be ducted flow path to the actual tubes of the core to promote even flow into and out of the core. Actual inlet and outlet pipe size are largely irrelevant.
So yes about TB size. In reality I cant see there being much, if any benefit from using a TB much larger ( as you say to accommodate for the blade/shaft itself ) than the outlet of the turbocharger.
Fitting a TB larger than the actual boost plumbing if it is already much larger than the turbo discharge just seems silly. At least in terms of throttle resolution.
As I say, if you fitted a huge TB to a turbo car you can and do see scenarios where say 60% upwards of opening makes no difference because it's already flowing all the air the engine can actually consume. So all you've done is give yourself horrible throttle control which often is also a pig to tune and drive at low openings.
For 500bhp, IMO 2.5" OD is quite adequate unless there are a huge amount of bends and say a 55-60mm TB
stevieturbo said:
Of course you should keep bends to a minimum, but obviously that's impractical. There will always be bends.
There are rules where air velocity in the pipework needs to be kept below a certain level. The maths for that is way over my head, so back to keeping it simple.
So you want the pipework as small as possible without posing any major restriction ( again, no numbers )
So whilst it could make sense to retain that 50mm throughout, it doesnt. Adding bends regardless of them being mandrel bent will pose a restriction. SO for that reason alone it can make sense to increase diameter a little or a lot to accommodate for the restriction of the bends.
As for intercoolers. Core design is but a small part. Of equal importance are the end tanks. Most egay ones regardless of pipe size are crap for the simple reason the end tanks do not promote even flow through the core regardless of their inlet/exit size.
3" is normally used as it pretty much covers all options. 3" pipework is easily worked and readily available. It is still a size that most engine bays can accommodate and will support over 1kbhp.
but it will equally be at home at 500bhp. So it's just an easy and sensible size to use.
Although despite the egay IC failings, as they are generally fairly big and very very cheap, value for money they are pretty good.
As for pipe size changes/IC. The only time really I see a change being necessary is at the entry and exit of the IC core. In otherwords, a large smooth flowing, and if need be ducted flow path to the actual tubes of the core to promote even flow into and out of the core. Actual inlet and outlet pipe size are largely irrelevant.
So yes about TB size. In reality I cant see there being much, if any benefit from using a TB much larger ( as you say to accommodate for the blade/shaft itself ) than the outlet of the turbocharger.
Fitting a TB larger than the actual boost plumbing if it is already much larger than the turbo discharge just seems silly. At least in terms of throttle resolution.
As I say, if you fitted a huge TB to a turbo car you can and do see scenarios where say 60% upwards of opening makes no difference because it's already flowing all the air the engine can actually consume. So all you've done is give yourself horrible throttle control which often is also a pig to tune and drive at low openings.
For 500bhp, IMO 2.5" OD is quite adequate unless there are a huge amount of bends and say a 55-60mm TB
I initially agree with the larger TBs being a bit 'hair trigger', I've just fitted a 70mm one to a 2 litre turbo engine, BUT it has been fitted along with high lift race cams, a very light flywheel and paddle clutch so they all add up to a car which is a PITA to drive around town and manoeuvring. I can see how the big TB contributes - it's a bit like opening a huge barn door in a force 10 gale compared to a small toilet window, just a small crack open and you will get a heck of a lot of air going through.There are rules where air velocity in the pipework needs to be kept below a certain level. The maths for that is way over my head, so back to keeping it simple.
So you want the pipework as small as possible without posing any major restriction ( again, no numbers )
So whilst it could make sense to retain that 50mm throughout, it doesnt. Adding bends regardless of them being mandrel bent will pose a restriction. SO for that reason alone it can make sense to increase diameter a little or a lot to accommodate for the restriction of the bends.
As for intercoolers. Core design is but a small part. Of equal importance are the end tanks. Most egay ones regardless of pipe size are crap for the simple reason the end tanks do not promote even flow through the core regardless of their inlet/exit size.
3" is normally used as it pretty much covers all options. 3" pipework is easily worked and readily available. It is still a size that most engine bays can accommodate and will support over 1kbhp.
but it will equally be at home at 500bhp. So it's just an easy and sensible size to use.
Although despite the egay IC failings, as they are generally fairly big and very very cheap, value for money they are pretty good.
As for pipe size changes/IC. The only time really I see a change being necessary is at the entry and exit of the IC core. In otherwords, a large smooth flowing, and if need be ducted flow path to the actual tubes of the core to promote even flow into and out of the core. Actual inlet and outlet pipe size are largely irrelevant.
So yes about TB size. In reality I cant see there being much, if any benefit from using a TB much larger ( as you say to accommodate for the blade/shaft itself ) than the outlet of the turbocharger.
Fitting a TB larger than the actual boost plumbing if it is already much larger than the turbo discharge just seems silly. At least in terms of throttle resolution.
As I say, if you fitted a huge TB to a turbo car you can and do see scenarios where say 60% upwards of opening makes no difference because it's already flowing all the air the engine can actually consume. So all you've done is give yourself horrible throttle control which often is also a pig to tune and drive at low openings.
For 500bhp, IMO 2.5" OD is quite adequate unless there are a huge amount of bends and say a 55-60mm TB
On the other hand this 70mm TB came from an ordinary 2ltr production car, now I don't believe it was that bad to drive so I'm assuming it was down to the gearing between TB and throttle pedal. I've noticed some TBs which have very oval cable reels on the side which helps, but there is also some kind of ratio between TB and pedal which must overcome this problem, my next move is to create one of these oval type cable reel thingies.
Ultimately of course drive-by-wire is the way forward!
Another way of looking at it is this, if a performance production car (2ltr turbo, 200bhp) has a TB fitted of 56mm then you would presume they got their calcs right and wouldn't fit something which was oversized and cost more to produce. Therefore it will be no good at well over double the power output and trading up to 70mm is the sensible thing to do. AG Bells Turbo performance tuning book lists 70mm as good for 500bhp too and 56mm only good for 300bhp before becoming too much of a restriction.
In my mind and no doubt many others you are better going bigger than smaller and throwing potential power away.
Something else worth discussing is that hot air takes up more volume than cold, so does this mean the exit of an intercooler and the following pipework should be smaller than the entry? If so, to what degree?
Personally I agree with DaveLs choice of a 70mm Tb for his 500bhp target.
Whilst looking carefully at what the manufacturers are putting on their engines can be a good indicator, it's by no means the rule otherwise we wouldn't be finding 2ltr N/A engines with 70mm TBs and 4ltr engines with TBs I probably couldn't get my flaccid penis into. Maybe it's down to where in the rev range you want your torque and power too........
Cossies regularly make over 500bhp with their standard 58mm TB or whatever it is and it is not a restriction.
And you cannot compare n/a to a boosted engine when it comes to TB sizing.
As an example, even a boosted LS1 V8 can make in excess of 1000bhp on the standard 78mm TB and even at that it is not a restriction.
Ive worked on Subarus making over 600bhp with their standard 60mm TB and again I dont see it as a restriction.
But as stated, the negatives of too big as driveability and throttle resolution. If you can live with these compromises then that's fine. And as you've already suggested engine spec will define how much of an issue the large TB will be. Some you may notice no negative effects, others will be terrible.
But neither will alter the fact that if it flows all the air the engine can consume at say 60-70% opening, it has been a waste of money.
And you cannot compare n/a to a boosted engine when it comes to TB sizing.
As an example, even a boosted LS1 V8 can make in excess of 1000bhp on the standard 78mm TB and even at that it is not a restriction.
Ive worked on Subarus making over 600bhp with their standard 60mm TB and again I dont see it as a restriction.
But as stated, the negatives of too big as driveability and throttle resolution. If you can live with these compromises then that's fine. And as you've already suggested engine spec will define how much of an issue the large TB will be. Some you may notice no negative effects, others will be terrible.
But neither will alter the fact that if it flows all the air the engine can consume at say 60-70% opening, it has been a waste of money.
Gassing Station | Engines & Drivetrain | Top of Page | What's New | My Stuff