The problems using iron liners for bore scoring
Discussion
I have been commenting for some time about the problems associated with recent practice of fitting steel liners to the M96 and M97 engines (to save a few quid over the cost of quality alloy Nikasil plated liners - that we use) and warned that we have received several fitted with steel liners elsewhere sent here for re-doing with Nikasil alloy liners due to various problems. These include the differential expansion causing them to sink and head gaskets leaking, twisting in the block, and mainly smoking through the need for excessive piston clearances (necessary with steel) and high wear rates.
These were the reasons most performance engines dropped this technology several decades ago (including Porsche). There can be a case for fitting them in smaller diameter bores if they are cast into the main block but fitting wet liners in steel as an after market solution has not been used in most applications for ages.
It seems to me that it must be a poor solution if after paying elsewhere for them to be rebuilt with steel the same engines soon come to us for a further rebuild - doing the job properly - and as our liners cost only £417 each (if fitted as a batch of 6) or £600 (just for one) the difference in cost compared to steel is relatively small compared to the whole rebuild cost for something that will last forever - but still they keep coming in - so someone somewhere is doing a lot of trade that isn't working.
As we also offer to re-round remaining cylinders and fit securing rings to keep them round (that costs much less than steel liners) or fit all 6 alloy Nikasil liners for a permanent solution - I am surprised so many people still fall for this options that costs more in the relatively short term (not even reaching the "long run").
So I wondered if people believed my posts or thought it was just to drum up business - so I asked the engine building technicians if they kept any of the steel liners we removed? Unfortunately most have been thrown away but we did find the most recent ones that I have photographed. These show three basic designs - all of which needed replacing. The block shows the top of some that have sunk as well.
Considering the numbers involved - there must also be plenty running around with high oil consumption etc and others that have not been sent to us yet to do properly - so as most of these liners came in as single fits or three on one bank - the pictures prove just how many are failing - be warned.
Pictures of the top of a block with a steel liner that has dropped, our alloy liner and a set of cylinder blocks we have not yet removed the liner from and a few different liners recently taken from other engines and replaced with alloy Nikasil alternatives (as Porsche themselves use in the GT3 and Turbo engines).
Baz
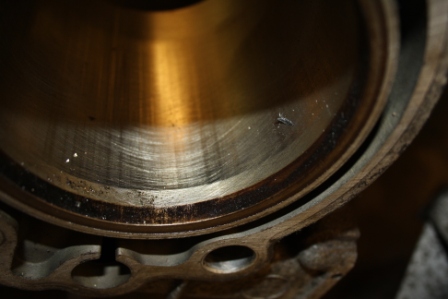

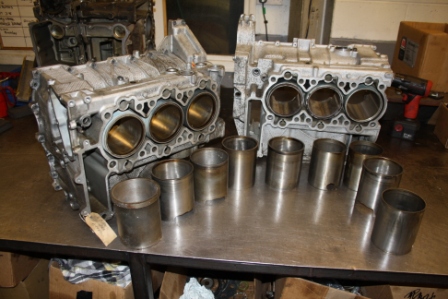
These were the reasons most performance engines dropped this technology several decades ago (including Porsche). There can be a case for fitting them in smaller diameter bores if they are cast into the main block but fitting wet liners in steel as an after market solution has not been used in most applications for ages.
It seems to me that it must be a poor solution if after paying elsewhere for them to be rebuilt with steel the same engines soon come to us for a further rebuild - doing the job properly - and as our liners cost only £417 each (if fitted as a batch of 6) or £600 (just for one) the difference in cost compared to steel is relatively small compared to the whole rebuild cost for something that will last forever - but still they keep coming in - so someone somewhere is doing a lot of trade that isn't working.
As we also offer to re-round remaining cylinders and fit securing rings to keep them round (that costs much less than steel liners) or fit all 6 alloy Nikasil liners for a permanent solution - I am surprised so many people still fall for this options that costs more in the relatively short term (not even reaching the "long run").
So I wondered if people believed my posts or thought it was just to drum up business - so I asked the engine building technicians if they kept any of the steel liners we removed? Unfortunately most have been thrown away but we did find the most recent ones that I have photographed. These show three basic designs - all of which needed replacing. The block shows the top of some that have sunk as well.
Considering the numbers involved - there must also be plenty running around with high oil consumption etc and others that have not been sent to us yet to do properly - so as most of these liners came in as single fits or three on one bank - the pictures prove just how many are failing - be warned.
Pictures of the top of a block with a steel liner that has dropped, our alloy liner and a set of cylinder blocks we have not yet removed the liner from and a few different liners recently taken from other engines and replaced with alloy Nikasil alternatives (as Porsche themselves use in the GT3 and Turbo engines).
Baz
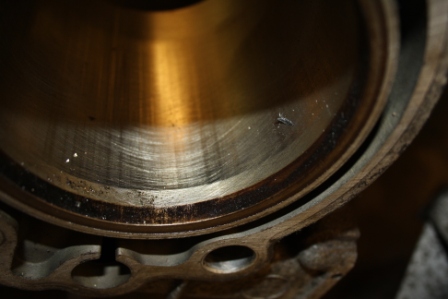

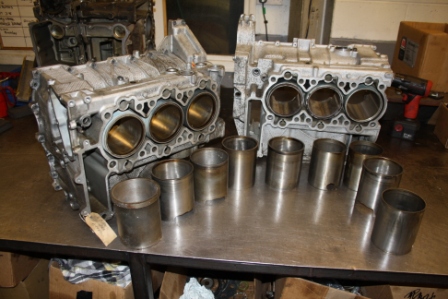
Edited by hartech on Friday 16th August 15:43
you pays your money and takes your chances,rebuilding with steel liners is a false economy but so many things are built like that today.
why didn't Porsche fit nikasil in the m96/7 in first place and in the 9A1 block ?I know they are more expensive but surely on a £60k+ car it wouldn't add that much.even my friends tuned lambretta has a nikasil bore and forged piston,he even tried expensive ceramic bores but they too weren't that good either.
why didn't Porsche fit nikasil in the m96/7 in first place and in the 9A1 block ?I know they are more expensive but surely on a £60k+ car it wouldn't add that much.even my friends tuned lambretta has a nikasil bore and forged piston,he even tried expensive ceramic bores but they too weren't that good either.
Edited by itsybitsy on Friday 16th August 16:11
It is an interesting subject - sorry if it comes over as a bit of a lecture explaining the issues - but they are actually not that challenging to understand.
Racing engines have less of a problem with differential expansion and clearances because the engines are only ever going to be used flat out and no one is interested in emissions at tickover.
Smaller domestic cars have small pistons and low temperature gradients to work with but powerful large sports car engines have quite a problem to overcome.
On the one hand they need tight piston clearances at low output (both for emission readings and driving in say town/city situations without high oil consumption or emissions) and tight clearances flat out (to stop the piston faces overheating from too much blow by). The difference in thermal rates between 30 mpg and 160 mph are massive.
Iron or steel has an expansion coefficient half to just over half that of aluminium – so does not expand as much. This can cause problems both with trying to keep close piston clearances for low and high speed runs and also for keeping the right surface contact when it is fitted inside an aluminium cylinder block that is expanding at different rates.
Similarly iron and steel have thermal conductivity rates about 1/3rd of aluminium – so do not transfer as much heat through them as aluminium does.
An iron or steel liner therefore expands at different rates to the piston and also does not dissipate as much heat.
In racing engines this heat transfer problem can be compensated for somewhat by the design of the coolant channels (often with holes drilled along the side of the liners to cool them closer to the inside reducing the wall thickness for the heat to transfer across). Similarly the clearances between the piston and cylinder bore can be set larger for the temperatures reached at racing speeds and coolant flow design can compensate somewhat. It is well known by racing engine engineers that one of the most important breakthroughs 4 stroke engine tuners made some decades ago when tuning standard production engines was to alter the coolant flows to equalise cylinder and piston temperatures by changing the flow design often with external pipework
High performance road engines suffer from having to perform at very light power outputs (actually for most of their life) while also being able to perform flat out at racing speeds and often actually on race tracks – and this creates difficulties over setting the right piston to cylinder wall clearances for both extremes. Manufacturers have for decades spent millions trying to get away from steel liners in engines as a consequence.
Engines with smaller diameter pistons (usually multi cylinder V8 or smaller 4 cylinder engines) have less of a problem that larger capacity engines with fewer cylinders -because the growth in size of the cylinders and pistons is greater in proportion in a larger bore than a smaller cylinder or piston at the same temperature range).
Some iron liners that are cast in overcome the expansion differential problem by ribs cast into the liner and aluminium to force the liner to expand at the same rate. This was OK in small bore engines but not so successful in larger bore ones.
The early 911’s had steel liners but soon converted to Nikasil plated alloy cylinders (that ran with closer clearances and didn’t wear out as quickly) and the 3 litre 944 S2 and 968 had at the time some of the biggest pistons fitted to similar sports cars and to solve this problem Porsche introduced a wholly alloy cylinder block and pistons with a homogeneous silicon particle mix (Alusil) and that worked brilliantly.
When we consider the M96 and M97 engines – they already have a weak open deck cylinder design and an unbalanced coolant flow that results in the thrust face of bank 2 cylinders (where all the problems are) running hotter than on bank 1 (where there are very few problems).
As liners cannot be retrospectively cast in the only option is to fit them to a machined cylinder bore.
This can be done 2 ways – fit the liner inside the alloy remaining (as most others do) – or completely machine away the upper alloy (where the coolant is) and fit a new solid liner therefore directly in contact with the coolant on one side and the cylinder bore on the other (as we do see photo) – and in the process make it sit inside the outer top diameter converting the cylinder block to a favoured closed deck design.
Furthermore you may notice the ribbed exterior which increases the contact area with coolant and increases heat dissipation even further (a great improvement over any other solution).
Heat transfer through 2 dissimilar materials is always reduced so even though steel transfers less heat this is exacerbated by connecting it to the alloy before it reaches the actual coolant. Our solution has the new alloy liner directly in contact with the coolant providing something like 4 times the ability to transfer heat away from the piston and combustion chamber.
Fitting a steel liner therefore has several disadvantages.
(1) The expansion of the alloy gradually reduces the interference fit so that the liner may even become loose (we have seen several rotate in the block) or it reduces the already much poorer heat transfer rates.
(2) The top deck height varies between the steel and aluminium and the head gaskets are solid triple layer steel with very little ability to adjust into changes in the sealing face.
(3) The wear rates of steel are well known to be poor compared to Nikasil (that is why previously manufacturers made oversized pistons for re-boring) but Porsche did not make any oversized pistons removing that option when they wear.
(4) The steel liners that are plated with Nikasil overcome that “wear rate” disadvantage but still have the problem of differential expansion and lower heat transfer and as the main cost is in the machining, rebuild labour costs and Nikasil plating – the minute difference in liner cost between steel and alloy is so small it seems hardly worth putting a recognised inferior product into the rebuild to save a few quid.
None of the steel liners we have had back to replace have Nikasil plated bores. Only time will tell if the extra cold clearances they must run with and the higher piston temperatures that must result will reduce longevity compared to an alloy Nikasil solution. This is particularly relevant since the original piston coating applied both to the first Lokasil engines and all the original Alusil engines – is not longer available as a process in the West resulting in even the Gen 2 engines running with a different “plastic” coating to the pistons that the previously successful Alusil 944 and 968 engines - and time will also tell if this is as good (which I have my doubts about).
It is no coincidence that Porsche themselves fit alloy Nikasil plated liners to their GT3 and Turbo engines and have reverted away from Lokasil to Alusil for their Gen 2 engines – nor that these engines have excellent longevity.
As we are expanding our engine rebuild facilities (now including CNC machining of the blocks) we have been reducing our prices as production efficiency increases (and this also allows us to machine a better coolant flow rate for the cylinders – all thrown into the job FOC).
I don’t know what the prices are for fitting steel liners and Nikasil plated steel liners (perhaps others could post that information) because I am frankly not interested in building an inferior engine and have such a huge success rate building far more engines than anyone else – any extra cost speaks for itself – in my opinion.
However there are always those that will want a rebuild at the lowest possible cost regardless of how short a time it works successfully and these will also be liable not to change other things to help the engines survive the longest – probably not a low temperature thermostat (that we pioneered), supported cylinder bores, etc etc.
Regardless of any other arguments others may like to raise or promote - It is clear from the number of engines we have had to rebuild to replace steel liners that for many it has not worked out for very long at all and was a false economy.
I am just trying to point out these issues and demonstrate that they a real and active problems. I have no axe to grind about anyone preferring steel liners and although steel liners with Nikasil plating may be OK for wear rates – they must still run with bigger cold and low speed running clearances than you can achieve with an alloy Nikasil plated liner. They may also be OK in engines designed for them with appropriate cooling changes and piston materials and especially for narrower applications.
We are trying our best to match prices with these to encourage customers to make the right choices technically in their own best interests. We are not stopping others offering similar alloy liners – so are not just promoting our own product – we are genuinely trying to make sure customers do not get led by the nose to a solution that possibly increases the supplying businesses profits or saves them a small amount if the short term only to cost more in the long run.
We fit these alloy Nikasil liners for many other independent businesses and are even setting up to do so Worldwide – because we believe in the quality of this solution and understand the short comings of many of the alternatives on the market.
For those struggling to afford such a repair we offer another alternative that is actually less expensive than three steel liners – just replacing the scored bore with an alloy Nikasil liner and then re-rounding the remaining good Lokasil cylinders (converting them to a closed deck in the process) and increasing the coolant flow there while fitting a low temperature thermostat – that is working out very wel and reliably – but it is not as good a fitting three or all six alloy Nikasil liners which we have heavily discounted to encourage uptake.
Compared to the cost of a replacement new engine (with the same faults that caused the original to fail) even one rebuilt with 6 Nikasil liners can be half the price and includes lots of other technical benefits.
We predicted the continual growth of failed engine numbers and really cannot cope with anymore than we presently handle – so this issue is not in any way to “drum up business” it is just that as an engineer that first was involved in the manufacture of Nikasil plated alloy cylinders over 40 years ago (with two stroke racing motorcycles) I happen to coincidentally know a lot more about the subject than most other specialists and this is the only proper solution. I am putting the technical arguments forward to counter those talked into a less satisfactory solution by engineers that either don’t know any better or are trying to get the business on the back of potentially a little less cost and don’t care about the long term consequences for the customer.
Our solution may be a little more expensive but we are trying to subsidise that as much as possible with more efficient production methods and quantity price reductions – and I don’t think there is much (if anything) in it any more. If things continue as planned we will one day be able to invest in an automatic multi tool change CNC machine and then we may even be able to beat the prices for inferior steel liner fitting – giving customers the best of both Worlds.
Arguments about what other manufacturers or racing cars do are irrelevant because the whole design is different and often so is the application.
There are not many road cars that can also reach 160mph or more and it is this technical problem that encouraged Porsche (and others) to find solutions that involved alloy cylinders. They seemed to go a little bit wrong with the Lokasil solution – but that hasn’t changed the principle – nor the best solution.
It seems that at some time in the near future most engines will have alloy blocks with plasma coated cylinder bores and this may well be the final solution but we have had to deal with an existing problem with an engine with other short comings and fitting steel liners into that already flawed scenario is in my view asking for trouble and the engines coming here to replace steel liners – seems to me – to confirm that totally. Meanwhile I do not believe that the difference in our alloy liner prices is significant compared to the whole cost of the job and not enough to risk the obvious consequences.
Baz
Racing engines have less of a problem with differential expansion and clearances because the engines are only ever going to be used flat out and no one is interested in emissions at tickover.
Smaller domestic cars have small pistons and low temperature gradients to work with but powerful large sports car engines have quite a problem to overcome.
On the one hand they need tight piston clearances at low output (both for emission readings and driving in say town/city situations without high oil consumption or emissions) and tight clearances flat out (to stop the piston faces overheating from too much blow by). The difference in thermal rates between 30 mpg and 160 mph are massive.
Iron or steel has an expansion coefficient half to just over half that of aluminium – so does not expand as much. This can cause problems both with trying to keep close piston clearances for low and high speed runs and also for keeping the right surface contact when it is fitted inside an aluminium cylinder block that is expanding at different rates.
Similarly iron and steel have thermal conductivity rates about 1/3rd of aluminium – so do not transfer as much heat through them as aluminium does.
An iron or steel liner therefore expands at different rates to the piston and also does not dissipate as much heat.
In racing engines this heat transfer problem can be compensated for somewhat by the design of the coolant channels (often with holes drilled along the side of the liners to cool them closer to the inside reducing the wall thickness for the heat to transfer across). Similarly the clearances between the piston and cylinder bore can be set larger for the temperatures reached at racing speeds and coolant flow design can compensate somewhat. It is well known by racing engine engineers that one of the most important breakthroughs 4 stroke engine tuners made some decades ago when tuning standard production engines was to alter the coolant flows to equalise cylinder and piston temperatures by changing the flow design often with external pipework
High performance road engines suffer from having to perform at very light power outputs (actually for most of their life) while also being able to perform flat out at racing speeds and often actually on race tracks – and this creates difficulties over setting the right piston to cylinder wall clearances for both extremes. Manufacturers have for decades spent millions trying to get away from steel liners in engines as a consequence.
Engines with smaller diameter pistons (usually multi cylinder V8 or smaller 4 cylinder engines) have less of a problem that larger capacity engines with fewer cylinders -because the growth in size of the cylinders and pistons is greater in proportion in a larger bore than a smaller cylinder or piston at the same temperature range).
Some iron liners that are cast in overcome the expansion differential problem by ribs cast into the liner and aluminium to force the liner to expand at the same rate. This was OK in small bore engines but not so successful in larger bore ones.
The early 911’s had steel liners but soon converted to Nikasil plated alloy cylinders (that ran with closer clearances and didn’t wear out as quickly) and the 3 litre 944 S2 and 968 had at the time some of the biggest pistons fitted to similar sports cars and to solve this problem Porsche introduced a wholly alloy cylinder block and pistons with a homogeneous silicon particle mix (Alusil) and that worked brilliantly.
When we consider the M96 and M97 engines – they already have a weak open deck cylinder design and an unbalanced coolant flow that results in the thrust face of bank 2 cylinders (where all the problems are) running hotter than on bank 1 (where there are very few problems).
As liners cannot be retrospectively cast in the only option is to fit them to a machined cylinder bore.
This can be done 2 ways – fit the liner inside the alloy remaining (as most others do) – or completely machine away the upper alloy (where the coolant is) and fit a new solid liner therefore directly in contact with the coolant on one side and the cylinder bore on the other (as we do see photo) – and in the process make it sit inside the outer top diameter converting the cylinder block to a favoured closed deck design.
Furthermore you may notice the ribbed exterior which increases the contact area with coolant and increases heat dissipation even further (a great improvement over any other solution).
Heat transfer through 2 dissimilar materials is always reduced so even though steel transfers less heat this is exacerbated by connecting it to the alloy before it reaches the actual coolant. Our solution has the new alloy liner directly in contact with the coolant providing something like 4 times the ability to transfer heat away from the piston and combustion chamber.
Fitting a steel liner therefore has several disadvantages.
(1) The expansion of the alloy gradually reduces the interference fit so that the liner may even become loose (we have seen several rotate in the block) or it reduces the already much poorer heat transfer rates.
(2) The top deck height varies between the steel and aluminium and the head gaskets are solid triple layer steel with very little ability to adjust into changes in the sealing face.
(3) The wear rates of steel are well known to be poor compared to Nikasil (that is why previously manufacturers made oversized pistons for re-boring) but Porsche did not make any oversized pistons removing that option when they wear.
(4) The steel liners that are plated with Nikasil overcome that “wear rate” disadvantage but still have the problem of differential expansion and lower heat transfer and as the main cost is in the machining, rebuild labour costs and Nikasil plating – the minute difference in liner cost between steel and alloy is so small it seems hardly worth putting a recognised inferior product into the rebuild to save a few quid.
None of the steel liners we have had back to replace have Nikasil plated bores. Only time will tell if the extra cold clearances they must run with and the higher piston temperatures that must result will reduce longevity compared to an alloy Nikasil solution. This is particularly relevant since the original piston coating applied both to the first Lokasil engines and all the original Alusil engines – is not longer available as a process in the West resulting in even the Gen 2 engines running with a different “plastic” coating to the pistons that the previously successful Alusil 944 and 968 engines - and time will also tell if this is as good (which I have my doubts about).
It is no coincidence that Porsche themselves fit alloy Nikasil plated liners to their GT3 and Turbo engines and have reverted away from Lokasil to Alusil for their Gen 2 engines – nor that these engines have excellent longevity.
As we are expanding our engine rebuild facilities (now including CNC machining of the blocks) we have been reducing our prices as production efficiency increases (and this also allows us to machine a better coolant flow rate for the cylinders – all thrown into the job FOC).
I don’t know what the prices are for fitting steel liners and Nikasil plated steel liners (perhaps others could post that information) because I am frankly not interested in building an inferior engine and have such a huge success rate building far more engines than anyone else – any extra cost speaks for itself – in my opinion.
However there are always those that will want a rebuild at the lowest possible cost regardless of how short a time it works successfully and these will also be liable not to change other things to help the engines survive the longest – probably not a low temperature thermostat (that we pioneered), supported cylinder bores, etc etc.
Regardless of any other arguments others may like to raise or promote - It is clear from the number of engines we have had to rebuild to replace steel liners that for many it has not worked out for very long at all and was a false economy.
I am just trying to point out these issues and demonstrate that they a real and active problems. I have no axe to grind about anyone preferring steel liners and although steel liners with Nikasil plating may be OK for wear rates – they must still run with bigger cold and low speed running clearances than you can achieve with an alloy Nikasil plated liner. They may also be OK in engines designed for them with appropriate cooling changes and piston materials and especially for narrower applications.
We are trying our best to match prices with these to encourage customers to make the right choices technically in their own best interests. We are not stopping others offering similar alloy liners – so are not just promoting our own product – we are genuinely trying to make sure customers do not get led by the nose to a solution that possibly increases the supplying businesses profits or saves them a small amount if the short term only to cost more in the long run.
We fit these alloy Nikasil liners for many other independent businesses and are even setting up to do so Worldwide – because we believe in the quality of this solution and understand the short comings of many of the alternatives on the market.
For those struggling to afford such a repair we offer another alternative that is actually less expensive than three steel liners – just replacing the scored bore with an alloy Nikasil liner and then re-rounding the remaining good Lokasil cylinders (converting them to a closed deck in the process) and increasing the coolant flow there while fitting a low temperature thermostat – that is working out very wel and reliably – but it is not as good a fitting three or all six alloy Nikasil liners which we have heavily discounted to encourage uptake.
Compared to the cost of a replacement new engine (with the same faults that caused the original to fail) even one rebuilt with 6 Nikasil liners can be half the price and includes lots of other technical benefits.
We predicted the continual growth of failed engine numbers and really cannot cope with anymore than we presently handle – so this issue is not in any way to “drum up business” it is just that as an engineer that first was involved in the manufacture of Nikasil plated alloy cylinders over 40 years ago (with two stroke racing motorcycles) I happen to coincidentally know a lot more about the subject than most other specialists and this is the only proper solution. I am putting the technical arguments forward to counter those talked into a less satisfactory solution by engineers that either don’t know any better or are trying to get the business on the back of potentially a little less cost and don’t care about the long term consequences for the customer.
Our solution may be a little more expensive but we are trying to subsidise that as much as possible with more efficient production methods and quantity price reductions – and I don’t think there is much (if anything) in it any more. If things continue as planned we will one day be able to invest in an automatic multi tool change CNC machine and then we may even be able to beat the prices for inferior steel liner fitting – giving customers the best of both Worlds.
Arguments about what other manufacturers or racing cars do are irrelevant because the whole design is different and often so is the application.
There are not many road cars that can also reach 160mph or more and it is this technical problem that encouraged Porsche (and others) to find solutions that involved alloy cylinders. They seemed to go a little bit wrong with the Lokasil solution – but that hasn’t changed the principle – nor the best solution.
It seems that at some time in the near future most engines will have alloy blocks with plasma coated cylinder bores and this may well be the final solution but we have had to deal with an existing problem with an engine with other short comings and fitting steel liners into that already flawed scenario is in my view asking for trouble and the engines coming here to replace steel liners – seems to me – to confirm that totally. Meanwhile I do not believe that the difference in our alloy liner prices is significant compared to the whole cost of the job and not enough to risk the obvious consequences.
Baz
One other way to look at the problem is that a small engine'd car (sat 1 or 0.4 litre) travelling at say 40mph is working its small pistons quite hard and they are quite hot and have already expanded quite a lot compared to fully expanded flat out at say 100 mph.
A big 3.6 litre 6 cylinder engine has piston area many time greater and a longer stroke and so the pressure force on each piston @ 40mph is very much less because it multiplies by the area of the top of the bigger piston (and all 6 of them) - so the temperature of the burning fuel is much lower and the area of the larger piston to dissipate that heat through the much larger cylinder walls is also much greater. This means the pistons in a larger engine @40mph will not have expanded as much (as a proportion of the full power expansion) as the much smaller engine at the same speed.
However when the big engine is flat out - the output needed to propel a car @ say 160mph compared to 100mph for the smaller engine is much higher and as the pistons are bigger the difference in the size of the small and large pitons between running at 40mph and flat out is much greater for the bigger engine. So piston clearances become more of an issue for the bigger engine.
This is why different solutions reach a technical limit of their suitability sooner with bigger more powerful sports car and why the introduction of all alloy blocks and cylinders became a solution to this difference in expansion rates managing to keep the piston clearances much closer at all levels of power than is mecessary with smaller engines and steel liners.
Baz
A big 3.6 litre 6 cylinder engine has piston area many time greater and a longer stroke and so the pressure force on each piston @ 40mph is very much less because it multiplies by the area of the top of the bigger piston (and all 6 of them) - so the temperature of the burning fuel is much lower and the area of the larger piston to dissipate that heat through the much larger cylinder walls is also much greater. This means the pistons in a larger engine @40mph will not have expanded as much (as a proportion of the full power expansion) as the much smaller engine at the same speed.
However when the big engine is flat out - the output needed to propel a car @ say 160mph compared to 100mph for the smaller engine is much higher and as the pistons are bigger the difference in the size of the small and large pitons between running at 40mph and flat out is much greater for the bigger engine. So piston clearances become more of an issue for the bigger engine.
This is why different solutions reach a technical limit of their suitability sooner with bigger more powerful sports car and why the introduction of all alloy blocks and cylinders became a solution to this difference in expansion rates managing to keep the piston clearances much closer at all levels of power than is mecessary with smaller engines and steel liners.
Baz
..Baz, Interesting reading here, I use to be involved with race engine development myself for TWR where we had considerable success on the track from group C to BTTC, and many others too.
I've seen (and measured) more bores/liners/pistons than I care to remember, and the different materials coefficients of expansion is something that you can never get away from it's always a compromise in mixed metal solutions.
Most OEM blocks I saw came in with cast iron liners pre-cast into alloy blocks, some race engines we would bore them out and fit machined cast iron liners into, I think we tried just about every variant on coated liners too, Nikasil was a frequently used one, some chromed bores too.
The problems I saw with the coated bores were that after honing there was often a lot of pitting in the surface, you can't see this until the bores are sized as the cavities are hidden in the coating until it's honed, it was often a reason why I sent liners back, I don't know how many rejects you get, maybe the process is a lot better now. The step height from location surface to gasket face tolerance was 20 microns and these were always hand selected to get uniform critical deck heights, are you using a stock head gasket or using machined rebates for Cooper rings or similar in your liners ..?
What is the thermal expansion rate for the Nikasil compared to your parent alloy liner..?, I've seen examples of flaking here too when the coating comes away, gets picked up and makes a big mess very shortly afterwards, so this solution does have potential downsides, compared to say a cast liner which is all the same material.
Are you using stock OEM rings..?
On a subnote, it still makes me chuckle that most people think pistons are round..
I've seen (and measured) more bores/liners/pistons than I care to remember, and the different materials coefficients of expansion is something that you can never get away from it's always a compromise in mixed metal solutions.
Most OEM blocks I saw came in with cast iron liners pre-cast into alloy blocks, some race engines we would bore them out and fit machined cast iron liners into, I think we tried just about every variant on coated liners too, Nikasil was a frequently used one, some chromed bores too.
The problems I saw with the coated bores were that after honing there was often a lot of pitting in the surface, you can't see this until the bores are sized as the cavities are hidden in the coating until it's honed, it was often a reason why I sent liners back, I don't know how many rejects you get, maybe the process is a lot better now. The step height from location surface to gasket face tolerance was 20 microns and these were always hand selected to get uniform critical deck heights, are you using a stock head gasket or using machined rebates for Cooper rings or similar in your liners ..?
What is the thermal expansion rate for the Nikasil compared to your parent alloy liner..?, I've seen examples of flaking here too when the coating comes away, gets picked up and makes a big mess very shortly afterwards, so this solution does have potential downsides, compared to say a cast liner which is all the same material.
Are you using stock OEM rings..?
On a subnote, it still makes me chuckle that most people think pistons are round..

Edited by RatBoy M3CSL on Sunday 18th August 12:48
Yes that's all correct Ratboy but of course all your work was it seems with racing engines and as I already explained that is not a problem because you only ever run at one temperature area and can apply clearances to suit.
It seems difficult to get over the reason why a road sports car with large capacity has a much greater problem over the range of pistons sizes it experiences during different uses - perhaps it needs reading again.
We have no problems with flaking nor pitting and the Nikasil is now recognised as the perfect solution (until the next one comes along I guess). Porsche thought it was Lokasil but it wasn't.
Nikasil is so well bonded in the liner it moves with it no problem there the only problem is if it ever badly overheats when it can come away but the engine would be finished by then any way.
The key to understanding this issue is to recognise that a large capacity road car piston goes through bigger size changes than a smaller one and therefore if you have a liner that doe not expand as much as alloy - you simply have to start out with greater clearances - even though this is the speed range the engine spends most of its life covering.
Baz
It seems difficult to get over the reason why a road sports car with large capacity has a much greater problem over the range of pistons sizes it experiences during different uses - perhaps it needs reading again.
We have no problems with flaking nor pitting and the Nikasil is now recognised as the perfect solution (until the next one comes along I guess). Porsche thought it was Lokasil but it wasn't.
Nikasil is so well bonded in the liner it moves with it no problem there the only problem is if it ever badly overheats when it can come away but the engine would be finished by then any way.
The key to understanding this issue is to recognise that a large capacity road car piston goes through bigger size changes than a smaller one and therefore if you have a liner that doe not expand as much as alloy - you simply have to start out with greater clearances - even though this is the speed range the engine spends most of its life covering.
Baz
..Interesting to know you have worked thro' your own solution, made the parts and have bought them to market. My 996 engine hasn't let go so far, seems to run cool and doesn't use any oil, but if it does I will come and see you..!
The principle of 'the bigger it is the more it expands' still stands and you can run out of clearance quickly thro' a temp range as you point out.
What bore distortion are you getting after assembly torque is applied..? if any ..?
We used to use a dummy honing plate, torque it up to assembly figures then hone the bores.
Take the plate off and they were not round any more, but on assembly they came back in very close.
All the best.
The principle of 'the bigger it is the more it expands' still stands and you can run out of clearance quickly thro' a temp range as you point out.
What bore distortion are you getting after assembly torque is applied..? if any ..?
We used to use a dummy honing plate, torque it up to assembly figures then hone the bores.
Take the plate off and they were not round any more, but on assembly they came back in very close.
All the best.
Edited by RatBoy M3CSL on Sunday 18th August 18:37
We do not suffer any distortion but how is our secret - sorry!
What a lot of people don't realise is that Porsche found a way to overcome this variation in piston and cylinder expansion for a large engine'd road sports car and the huge range of temperatures and size changes the piston would go thought) when they changed from an iron block with the 924 to an Alusil one for the 944 and the result was an outstanding car. It was a brilliant piece of engineering that would not have worked had they not also followed the lead from the USA in pioneering ferrous coated pistons to survive in the Alusil bores.
They managed to push those boundaries to a 3 litre version with 104mm pistons with the S2 and 968 versions but if they had done this with steel liners they would have encountered the very problems I have been discussing - it would not have worked out like it did with 944 and 968 engines having covered 200K or so still running great. Alusil proved to be so good some even ran for quite high mileages with a new type of "plastic" piston coating. But Alusil has silicon in the whole block and is hard to machine and expensive to produce as a result (but extremely strong and more stable than commercial cast aluminium).
They also succeeded in increasing the piston sizes with the 3.6 and then 3.8 996 and 997 but two very significant changes were made that have caused these problems.
(1) They change to Lokasil (which needs a ferrous piston coating - or something new yet to be identified - to survive) and Lokasil is less stable and less strong as is the aluminium they cast around it - resulting in the very migration to oval we speak about in the thrust direction. Running the engines at a higher temperature (to assist with emission control) didn't help the plastic coated piston material to last as long as it could have done if run cooler either.
(2) It seems they were unable or unwilling to use the original piston ferrous coating (I undertstand due to environmental health and safety limitations to the process).
They have now returned to Alusil in the Gen 2 engines but still are not using the original ferrous coated pistons that worked so well in Alusil in the 944 and 968. However they seem to have found a suitable new piston coating
The early M96 2.5 to 4.3 engines still used the ferrous coating with pistons supplied first by the block manufacturer (KS) and at the end by Mahle who then supplied pistons with a plastic coating. This combination in block 2 is the problem side (because the thrust face runs hotter and platics don't like excessive heat).
Nikasil (as I am sure you already know) provides such a good long life wear resistant coating that it can run with pistons with almost any coating or no coating at all - unfortunately it is relatively expensive - but so much so that they use it in the GT3 and turbo engines - because they know their stuff and can charge more for the end product to cover the extra costs.
Two cylinders inside each other never work as well, are as stable with temperature changes or transfer heat as well as one homogeneous material and we use a very high strength alloy and replace the whole original Lokasil and alloy block material so our new liner is totally in contact with the coolant.
I am extremely frustrated that the vast majority of people and specialists simply don't understand these issues or the significance of them and many are resorting to a solution that is never going to be as good or as reliable as ours - especially when the owners who chose steel have to get the engines done for a second time.
I wish I had the ability to explain this phenomenon better so everyone "got it". You would think the facts speak for themselves but unfortunately it seems they do not even for people with the engineering experience to know better.
I guess there is a limit therefore to what I can do to convince them and anyway we could not handle many more engine repairs than we do now without some major expansion and investment that is not currently planned.
It really is simple - if you want to use steel or iron there is a limit to how big the pistons can be to cover the whole range of temperatures they go through in a road car in road use. Hence if you want a bigger capacity with steel or iron liners you have to have more cylinders.
Porsche found a way to have large capacity engines with fewer cylinders thanks to this new alloy cylinder technology (and balance shafts) - but the change to Lokasil in the 6 cylinder engines just didn't work out for enough cars once the original piston ferrous coatings were replaced by plastic ones.
By lowering the cylinder temperatures and re-rounding the oval Lokasil cylinders - we have found a way to reduce the problem so in most instances they work OK with the original Lokasil - but a much better solution is obviously to replace them all with Nikasil - so we offer both solutions - one less expensive anyway than steel and so far working out very well indeed and the other the best you could possibly get with current technology.
The practice of using steel (even if it is Nikasil plated which we have not yet seen) is IMHO a flawed solution introduced to either save a small amount of money or increase the profit for those applying it on their customers behalf. It is a typical cheap solution and the usual consequences will follow.
The additional cost of ally Nikasil liners is a small additional price to pay for the best solution yet to be found or applied to engines with such large pistons and already proven by Porsche in their other trouble free models.
However in our research and development we have engines running around with LOkasil bores and new piston coatings - some of which have never been tried before (one of which looks very encouraging) but we should really not be trying to carry out such expensive and time consuming work form such a small business - and it is a huge financial and labour intensive task and unfortunately takes thousands of test miles and engines strips to asses - but we are trying. It should have been undertaken by the manufacturers but if someone like us didn't - it would be new engines for everyone at usually more than twice the price and with the same flawed technology.
Meanwhile we offer the best solution and are continually trying to bring the Nikasil cost down to match steel - and to find a new psiton coating that lasts well in Lokasil - to encourage even the most impecunious owners to choose the best solution for their rebuilds.
Baz
What a lot of people don't realise is that Porsche found a way to overcome this variation in piston and cylinder expansion for a large engine'd road sports car and the huge range of temperatures and size changes the piston would go thought) when they changed from an iron block with the 924 to an Alusil one for the 944 and the result was an outstanding car. It was a brilliant piece of engineering that would not have worked had they not also followed the lead from the USA in pioneering ferrous coated pistons to survive in the Alusil bores.
They managed to push those boundaries to a 3 litre version with 104mm pistons with the S2 and 968 versions but if they had done this with steel liners they would have encountered the very problems I have been discussing - it would not have worked out like it did with 944 and 968 engines having covered 200K or so still running great. Alusil proved to be so good some even ran for quite high mileages with a new type of "plastic" piston coating. But Alusil has silicon in the whole block and is hard to machine and expensive to produce as a result (but extremely strong and more stable than commercial cast aluminium).
They also succeeded in increasing the piston sizes with the 3.6 and then 3.8 996 and 997 but two very significant changes were made that have caused these problems.
(1) They change to Lokasil (which needs a ferrous piston coating - or something new yet to be identified - to survive) and Lokasil is less stable and less strong as is the aluminium they cast around it - resulting in the very migration to oval we speak about in the thrust direction. Running the engines at a higher temperature (to assist with emission control) didn't help the plastic coated piston material to last as long as it could have done if run cooler either.
(2) It seems they were unable or unwilling to use the original piston ferrous coating (I undertstand due to environmental health and safety limitations to the process).
They have now returned to Alusil in the Gen 2 engines but still are not using the original ferrous coated pistons that worked so well in Alusil in the 944 and 968. However they seem to have found a suitable new piston coating
The early M96 2.5 to 4.3 engines still used the ferrous coating with pistons supplied first by the block manufacturer (KS) and at the end by Mahle who then supplied pistons with a plastic coating. This combination in block 2 is the problem side (because the thrust face runs hotter and platics don't like excessive heat).
Nikasil (as I am sure you already know) provides such a good long life wear resistant coating that it can run with pistons with almost any coating or no coating at all - unfortunately it is relatively expensive - but so much so that they use it in the GT3 and turbo engines - because they know their stuff and can charge more for the end product to cover the extra costs.
Two cylinders inside each other never work as well, are as stable with temperature changes or transfer heat as well as one homogeneous material and we use a very high strength alloy and replace the whole original Lokasil and alloy block material so our new liner is totally in contact with the coolant.
I am extremely frustrated that the vast majority of people and specialists simply don't understand these issues or the significance of them and many are resorting to a solution that is never going to be as good or as reliable as ours - especially when the owners who chose steel have to get the engines done for a second time.
I wish I had the ability to explain this phenomenon better so everyone "got it". You would think the facts speak for themselves but unfortunately it seems they do not even for people with the engineering experience to know better.
I guess there is a limit therefore to what I can do to convince them and anyway we could not handle many more engine repairs than we do now without some major expansion and investment that is not currently planned.
It really is simple - if you want to use steel or iron there is a limit to how big the pistons can be to cover the whole range of temperatures they go through in a road car in road use. Hence if you want a bigger capacity with steel or iron liners you have to have more cylinders.
Porsche found a way to have large capacity engines with fewer cylinders thanks to this new alloy cylinder technology (and balance shafts) - but the change to Lokasil in the 6 cylinder engines just didn't work out for enough cars once the original piston ferrous coatings were replaced by plastic ones.
By lowering the cylinder temperatures and re-rounding the oval Lokasil cylinders - we have found a way to reduce the problem so in most instances they work OK with the original Lokasil - but a much better solution is obviously to replace them all with Nikasil - so we offer both solutions - one less expensive anyway than steel and so far working out very well indeed and the other the best you could possibly get with current technology.
The practice of using steel (even if it is Nikasil plated which we have not yet seen) is IMHO a flawed solution introduced to either save a small amount of money or increase the profit for those applying it on their customers behalf. It is a typical cheap solution and the usual consequences will follow.
The additional cost of ally Nikasil liners is a small additional price to pay for the best solution yet to be found or applied to engines with such large pistons and already proven by Porsche in their other trouble free models.
However in our research and development we have engines running around with LOkasil bores and new piston coatings - some of which have never been tried before (one of which looks very encouraging) but we should really not be trying to carry out such expensive and time consuming work form such a small business - and it is a huge financial and labour intensive task and unfortunately takes thousands of test miles and engines strips to asses - but we are trying. It should have been undertaken by the manufacturers but if someone like us didn't - it would be new engines for everyone at usually more than twice the price and with the same flawed technology.
Meanwhile we offer the best solution and are continually trying to bring the Nikasil cost down to match steel - and to find a new psiton coating that lasts well in Lokasil - to encourage even the most impecunious owners to choose the best solution for their rebuilds.
Baz
Hi Sump, We do not name competitors products and never have - life is difficult enough on the internet and people have different opinions and experiences - so we feel that is unfair to do so (and anyway the value of our contribution would be diminished by those assuming it was pure self promotion) so we always only refer to either our own products or purely technical considerations (as in this case).
Again the issue is not which steel/iron liner is used or who made or fitted it but a broader issue about the ability of pistons in large bore engines being able to fit into the bore with the correct clearances for very slow and very fast speeds the engines are capable of.
Try and imagine the amount of combustion pressure the engine has to create to push 6 relatively big pistons along so the car travels at say 30 to 40 mph (which if you refer to the hours running records and mileages covered is about the norm). That pressure pushes on the whole area of the piston creating a downward force - so the larger the piston the less the pressure has to be to be above it to achieve the same force (and the difference increases with the square of the diameter).
So big pistons running at modest power outputs are really relatively cool and have not expanded much. However the force neccessary to push a car along against air resistance at say 160mph is huge and once again is a factor of the square of the speed (or even more) greater than at a slower speed - so a car that will only do 100 mph needs a lot less force to get there than one capable of 160mph.
Making an engine that will run with the right clearances for both scenarios is therefore easier as the piston diameter is smaller and the top speed lower - so is the biggest problem technically for an engine with big pistons capable of 160 mph - like these engines.
Large pistons (and therefore less cylinders) means fewer parts to make (less cost) and less internal engine resistance at low revs/speed so makes a fuel and emission efficient engine - so is desirable.
The problem however in designing such an engine is in keeping the piston to cylinder bore clearances right for such very different thermal conditions (between the maximum potential top speed with can be up to say 60% different in different cars - and the minimum speed most cars drive around at all day long - which is much the same)and using materials with dissimilar expansion rates makes it a lot more difficult - especially in engines with accepted problems over unbalanced and reduced cylinder coolant flow.
That is why, many years ago, manufacturers tried lots of different ways to find pistons and coatings and cylinder finishes that would allow the cylinders to be made of materials with more similar expansion rates to the pistons - something that the practice of fitting steel/iron liners goes completely against for this type of applications.
Bearing in mind that there must be relatively few engines out there fitted with these liners, that it has only been a recent phenomenon and how much extra someone must be paying to remove and replace them so soon after rebuilding them - I am amazed and concerned about the numbers that we are getting through here and can only conclude that since there is such strong technical and historical evidence against their suitability and such high practical "real World" evidence at their failings - that it is not the best solution and as such I hope that explaining all this enables some owners or businesses to justify the better solution - for the sake of all involved.
Although we do use the better alloy Nikasil plated liners - please remember there is nothing to stop our competitors doing the same and in the same way that several have copied things (like our IMS solutions etc) - this technical warning is not about our product promotion but is a real absolute technical issue that we have got right - that others could follow - but that they seem not to do - for reasons no one yet has tried to defend (for rather obvious reasons).
Baz
Again the issue is not which steel/iron liner is used or who made or fitted it but a broader issue about the ability of pistons in large bore engines being able to fit into the bore with the correct clearances for very slow and very fast speeds the engines are capable of.
Try and imagine the amount of combustion pressure the engine has to create to push 6 relatively big pistons along so the car travels at say 30 to 40 mph (which if you refer to the hours running records and mileages covered is about the norm). That pressure pushes on the whole area of the piston creating a downward force - so the larger the piston the less the pressure has to be to be above it to achieve the same force (and the difference increases with the square of the diameter).
So big pistons running at modest power outputs are really relatively cool and have not expanded much. However the force neccessary to push a car along against air resistance at say 160mph is huge and once again is a factor of the square of the speed (or even more) greater than at a slower speed - so a car that will only do 100 mph needs a lot less force to get there than one capable of 160mph.
Making an engine that will run with the right clearances for both scenarios is therefore easier as the piston diameter is smaller and the top speed lower - so is the biggest problem technically for an engine with big pistons capable of 160 mph - like these engines.
Large pistons (and therefore less cylinders) means fewer parts to make (less cost) and less internal engine resistance at low revs/speed so makes a fuel and emission efficient engine - so is desirable.
The problem however in designing such an engine is in keeping the piston to cylinder bore clearances right for such very different thermal conditions (between the maximum potential top speed with can be up to say 60% different in different cars - and the minimum speed most cars drive around at all day long - which is much the same)and using materials with dissimilar expansion rates makes it a lot more difficult - especially in engines with accepted problems over unbalanced and reduced cylinder coolant flow.
That is why, many years ago, manufacturers tried lots of different ways to find pistons and coatings and cylinder finishes that would allow the cylinders to be made of materials with more similar expansion rates to the pistons - something that the practice of fitting steel/iron liners goes completely against for this type of applications.
Bearing in mind that there must be relatively few engines out there fitted with these liners, that it has only been a recent phenomenon and how much extra someone must be paying to remove and replace them so soon after rebuilding them - I am amazed and concerned about the numbers that we are getting through here and can only conclude that since there is such strong technical and historical evidence against their suitability and such high practical "real World" evidence at their failings - that it is not the best solution and as such I hope that explaining all this enables some owners or businesses to justify the better solution - for the sake of all involved.
Although we do use the better alloy Nikasil plated liners - please remember there is nothing to stop our competitors doing the same and in the same way that several have copied things (like our IMS solutions etc) - this technical warning is not about our product promotion but is a real absolute technical issue that we have got right - that others could follow - but that they seem not to do - for reasons no one yet has tried to defend (for rather obvious reasons).
Baz
.Thanks Baz, I'm sensing your frustration, but over time now you have a reliable fix, the best advertising for your product is always going to be durability in the field and customer referrals.
Thanks for typing your journey up to get here, a wet liner has better heat transfer properties, but requires some extra machining to make a space for it, and they do need to have thicker walls than a steel to withstand the cylinder pressures. Similarly making a round bore @ 20C is 1 thing, but keeping it round after it's torqued up and running hot is another thing altogether..!
I was head of the dept @ TWR responsible for measuring the results of all the variations of materials / coatings / processes used and resulting shapes achieved, and I know it was a long journey even with the resources and equipment we had back then to do it.
Interestingly we tried low friction piston coatings too, Xylan it was called and a green very slippery plastic, ultimately it wears off tho'.
We did a few road car engines too, notably the XJ220, and the prototype DB7 straight 6 supercharged one which I remember well, as we had some piston slap to figure out and the resulting rattle was not a good sound on the early engines..!
Thanks for typing your journey up to get here, a wet liner has better heat transfer properties, but requires some extra machining to make a space for it, and they do need to have thicker walls than a steel to withstand the cylinder pressures. Similarly making a round bore @ 20C is 1 thing, but keeping it round after it's torqued up and running hot is another thing altogether..!
I was head of the dept @ TWR responsible for measuring the results of all the variations of materials / coatings / processes used and resulting shapes achieved, and I know it was a long journey even with the resources and equipment we had back then to do it.
Interestingly we tried low friction piston coatings too, Xylan it was called and a green very slippery plastic, ultimately it wears off tho'.
We did a few road car engines too, notably the XJ220, and the prototype DB7 straight 6 supercharged one which I remember well, as we had some piston slap to figure out and the resulting rattle was not a good sound on the early engines..!
Edited by RatBoy M3CSL on Monday 19th August 10:05
That's very interesting Ratty and we too have tried Xylan (in green and orange - don't think that makes any difference) and the problem with the Lokasil is interesting - and I think you will be interested so I will explain it further - just for your benefit.
When the silicon was mixed in with the aluminium and cast in everywhere (as with Alusil) - it resulted in a very strong but difficult to machine block that was extremely stable. It had an open deck design but was so strong it only ever went oval and cracked if used in turbo applications at very high boost pressures and then only after a lot of use.
The Lokasil solution was thought to end up the same and was advertised and promoted technically as just the same. It was made from a preform cylinder that was explained as a porous moulding entrapping silicon in a porous matrix. This was then fitted into the metal moulds and molten aluminium was applied under pressure. The result was that the molten aluminium flowed into the porous spaces and burned off the original bonding agent leaving the silicon suspended in the aluminium in exactly the same way it was in Alusil. It was therefore claimed to be just the same but of course only entrapped the silicon content at the surface where it was needed hence it was called "localised silicon" or lokasil.
The block material was not as strong as the original Alusil and the Lokasil preform was even weaker than either - so the combination of the two resulted in a relatively weak and unstable open deck cylinder and no wonder it soon goes oval and eventually cracks.
This could have been improved if Porsche had increased the diameter of the outer alloy (but they reduced it instead) or secured the tops with a ring (but they didn't).
In reality the silicon particles in Lokasil are not IMHO as well secured in place as they are when mixed in with molten aluminium in the Alusil solution. I also do not expect the distribution to be as even nor the individual particle bonding to be as good. They also changed the sizes and concentration of the silicon from Lokasil 1 to Lokasil 2 but I cannot find out any more about why or when. I also cannot find out what the particle size is and the concentration % in the original Alusil - but it stands to reason that to make a porous preform there may not be as many particles - but that is just conjecture on my part.
Because the whole situation went pear shaped it is very difficult to find out as much as I would like. I did obtain a lot of help direct with the original engineers at KS but since things have gone worse and more in the public domain - that source has dried up!
What I do know is that the distribution of the silicon in Lokasil is not as even in the resulting cylinders and the positioning of the preform is not always perfectly central. I think the particles are not as securely fixed in the matrix as they are in Alusil giving rise to a random number falling out and this exposes new sharper particles to score the plastic coated pitons. After boring and honing the Lokasil with diamond cutters it is necessary to expose the silicon particles with a special material and this also reduces the sharpness of the edges of the silicon particles - but of course if they then fall out they expose new particles that have not been similarly treated. We have the surface measuring equipment to check all this and the manufacturing equipment to carry out the reboring, honing and exposing of the Lokasil to do this (and had the quality of the end result confirmed by KS as correct) but so far have failed to obtain a piston with a coating that will survive long enough.
For sure an aluminium piston will not survive in a Lokasil bore without a coating of some kind. The Mahle pistons have a screen printed material called Feroprint - but unlike the original Ferrous coated pistons they are not magnetic (as the ferrous coated ones were) so I am not sure what the coating material actually is (or where the ferrite is) - but I am sure it can flake off and rub off over time - resulting in a problem. In contrast Nikasil will run with anything. It is interesting that another specialist worked out that the earlier cast pistons were better than the later forged ones (and thought this was the explanation) but missed the fact that it was the change in coating that coincided with the change in pistons supplier and it was the coating that was the relevant issue not the method of production. As I said before - this level of research should not need to be undertaken by such small businesses as ours when such a large manufacturer gets things wrong and tries to wriggle out of responsibility by putting up smoke screens.
Like all plastics - temperature is important for the key to the piston surface and the unbalanced coolant flow results in bank two pistons running hotter on the side that scores than bank 1, so temperature comes into the problem (hence our increasing coolant flow through the block and fitting a lower temperature thermostat).
The new coatings we are testing will remain our secret for now but this has been part of a long term plan to enable us to overbore the Lokasil and provide oversized pistons. It has cost us a small fortune but will pay off for us and our customers if we can find something durable enough. Meanwhile the Nikasil solution works brilliantly - it is just more expensive than reboring the original Lokasil and fitting the alloy rings to the top to comvert the engine to a closed deck and prevent them going oval.
To help reduce this cost we have automated the machining out of the original block but until we can afford to invest in an auto tool changing CNC the result of the added cost of the Nikasil plating still makes us a little more expensive than steel or iron (although I believe our trade price is the same anyway).
There is very much more that we have researched and tested that I could explain but from your position I think you will already know from these responses that we are extremely competent at what we do and have carried out more research and development in a proper professional manner than you would expect inside our Independent Porsche sector - and basically - that we know what we are talking about.
It is a shame for those who are persuaded to resort to steel or iron (for possibly a very small saving) that they do not appreciate these issues in the same way you probably do! If they did I cannot imagine anyone going that route.
Baz
When the silicon was mixed in with the aluminium and cast in everywhere (as with Alusil) - it resulted in a very strong but difficult to machine block that was extremely stable. It had an open deck design but was so strong it only ever went oval and cracked if used in turbo applications at very high boost pressures and then only after a lot of use.
The Lokasil solution was thought to end up the same and was advertised and promoted technically as just the same. It was made from a preform cylinder that was explained as a porous moulding entrapping silicon in a porous matrix. This was then fitted into the metal moulds and molten aluminium was applied under pressure. The result was that the molten aluminium flowed into the porous spaces and burned off the original bonding agent leaving the silicon suspended in the aluminium in exactly the same way it was in Alusil. It was therefore claimed to be just the same but of course only entrapped the silicon content at the surface where it was needed hence it was called "localised silicon" or lokasil.
The block material was not as strong as the original Alusil and the Lokasil preform was even weaker than either - so the combination of the two resulted in a relatively weak and unstable open deck cylinder and no wonder it soon goes oval and eventually cracks.
This could have been improved if Porsche had increased the diameter of the outer alloy (but they reduced it instead) or secured the tops with a ring (but they didn't).
In reality the silicon particles in Lokasil are not IMHO as well secured in place as they are when mixed in with molten aluminium in the Alusil solution. I also do not expect the distribution to be as even nor the individual particle bonding to be as good. They also changed the sizes and concentration of the silicon from Lokasil 1 to Lokasil 2 but I cannot find out any more about why or when. I also cannot find out what the particle size is and the concentration % in the original Alusil - but it stands to reason that to make a porous preform there may not be as many particles - but that is just conjecture on my part.
Because the whole situation went pear shaped it is very difficult to find out as much as I would like. I did obtain a lot of help direct with the original engineers at KS but since things have gone worse and more in the public domain - that source has dried up!
What I do know is that the distribution of the silicon in Lokasil is not as even in the resulting cylinders and the positioning of the preform is not always perfectly central. I think the particles are not as securely fixed in the matrix as they are in Alusil giving rise to a random number falling out and this exposes new sharper particles to score the plastic coated pitons. After boring and honing the Lokasil with diamond cutters it is necessary to expose the silicon particles with a special material and this also reduces the sharpness of the edges of the silicon particles - but of course if they then fall out they expose new particles that have not been similarly treated. We have the surface measuring equipment to check all this and the manufacturing equipment to carry out the reboring, honing and exposing of the Lokasil to do this (and had the quality of the end result confirmed by KS as correct) but so far have failed to obtain a piston with a coating that will survive long enough.
For sure an aluminium piston will not survive in a Lokasil bore without a coating of some kind. The Mahle pistons have a screen printed material called Feroprint - but unlike the original Ferrous coated pistons they are not magnetic (as the ferrous coated ones were) so I am not sure what the coating material actually is (or where the ferrite is) - but I am sure it can flake off and rub off over time - resulting in a problem. In contrast Nikasil will run with anything. It is interesting that another specialist worked out that the earlier cast pistons were better than the later forged ones (and thought this was the explanation) but missed the fact that it was the change in coating that coincided with the change in pistons supplier and it was the coating that was the relevant issue not the method of production. As I said before - this level of research should not need to be undertaken by such small businesses as ours when such a large manufacturer gets things wrong and tries to wriggle out of responsibility by putting up smoke screens.
Like all plastics - temperature is important for the key to the piston surface and the unbalanced coolant flow results in bank two pistons running hotter on the side that scores than bank 1, so temperature comes into the problem (hence our increasing coolant flow through the block and fitting a lower temperature thermostat).
The new coatings we are testing will remain our secret for now but this has been part of a long term plan to enable us to overbore the Lokasil and provide oversized pistons. It has cost us a small fortune but will pay off for us and our customers if we can find something durable enough. Meanwhile the Nikasil solution works brilliantly - it is just more expensive than reboring the original Lokasil and fitting the alloy rings to the top to comvert the engine to a closed deck and prevent them going oval.
To help reduce this cost we have automated the machining out of the original block but until we can afford to invest in an auto tool changing CNC the result of the added cost of the Nikasil plating still makes us a little more expensive than steel or iron (although I believe our trade price is the same anyway).
There is very much more that we have researched and tested that I could explain but from your position I think you will already know from these responses that we are extremely competent at what we do and have carried out more research and development in a proper professional manner than you would expect inside our Independent Porsche sector - and basically - that we know what we are talking about.
It is a shame for those who are persuaded to resort to steel or iron (for possibly a very small saving) that they do not appreciate these issues in the same way you probably do! If they did I cannot imagine anyone going that route.
Baz
..Thanks Baz, I can see I will have to come and have a chat with you 1 day..!
I've worked extensively with Nikasil coated liners, steel/chrome plated ones, the cast iron liners we machined ourselves from centrifugally spun castings, which were about 90% scrap by weight by the time we had cut the finished liner out in several stages...!,
The solid billets are expensive for openers to get the shape as they are 1 piece, you will know this as you are paying for your billets..!
Most of our pistons were Mahle or Cosworth, sometimes Accralite or CP.
I was head of quality for Pankl a few years after TWR too, who know a little about making nice con-rods..! They took over an American company later and make cranks/pistons too now I believe.
Always been interested in the Porsche Alusil/Lokasil solutions, but never had the chance to get too close to the oppositions oily bits when we were in group 'C', or other racing, except the time someone who will remain nameless wheeled a complete RC45 Honda GP bike into my office and said have a look at that engine and see what we're doing wrong will you.. !, I really enjoyed the BTCC program for Volvo too, which we won, that 5 cylinder 2.0 litre on the dyno flat chat sounded lovely @ 8250rpm, we had a great battle with Cosworth as their 2.0 V6 wasn't as powerful and they didn't like it much..!
Good to talk to a guy who knows his Ra from his Rz, and what plateau honing is, good luck with your repair package sales moving forward after all your time invested in a fix, as the batch sizes go up the profitability will come back ..
Edited for clarity.. as pointed out, it was a '94 GP bike and defo a 2 stroke, not the RC45..!
I've worked extensively with Nikasil coated liners, steel/chrome plated ones, the cast iron liners we machined ourselves from centrifugally spun castings, which were about 90% scrap by weight by the time we had cut the finished liner out in several stages...!,
The solid billets are expensive for openers to get the shape as they are 1 piece, you will know this as you are paying for your billets..!
Most of our pistons were Mahle or Cosworth, sometimes Accralite or CP.
I was head of quality for Pankl a few years after TWR too, who know a little about making nice con-rods..! They took over an American company later and make cranks/pistons too now I believe.
Always been interested in the Porsche Alusil/Lokasil solutions, but never had the chance to get too close to the oppositions oily bits when we were in group 'C', or other racing, except the time someone who will remain nameless wheeled a complete RC45 Honda GP bike into my office and said have a look at that engine and see what we're doing wrong will you.. !, I really enjoyed the BTCC program for Volvo too, which we won, that 5 cylinder 2.0 litre on the dyno flat chat sounded lovely @ 8250rpm, we had a great battle with Cosworth as their 2.0 V6 wasn't as powerful and they didn't like it much..!
Good to talk to a guy who knows his Ra from his Rz, and what plateau honing is, good luck with your repair package sales moving forward after all your time invested in a fix, as the batch sizes go up the profitability will come back ..

Edited for clarity.. as pointed out, it was a '94 GP bike and defo a 2 stroke, not the RC45..!
Edited by RatBoy M3CSL on Tuesday 20th August 09:38
blade7 said:
RatBoy M3CSL said:
.someone who will remain nameless wheeled a complete RC45 Honda GP bike into my office and said have a look at that engine and see what we're doing wrong will you.. !
Calling a superbike a GP bike probably...What's even worse, back in the day of the RC45 it was a 4 stroke, the then GP bikes were 2 strokes.
I'm only a woodworker, its all castrol R to me. :-)
Gassing Station | Porsche General | Top of Page | What's New | My Stuff